氰化法提金工艺
氰化提金工艺及污水处理
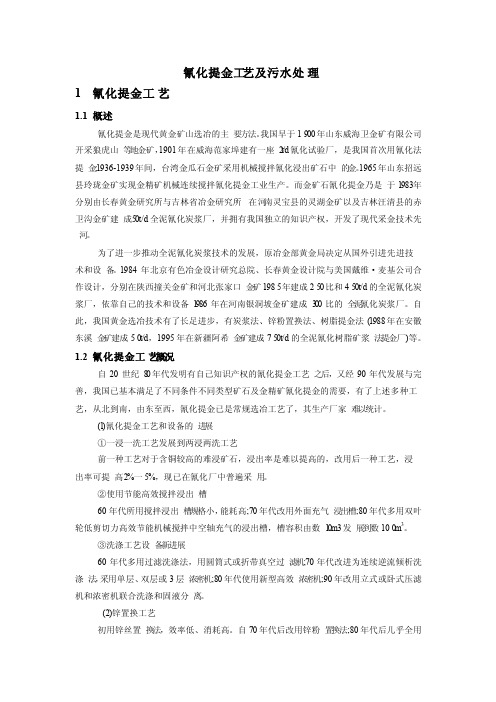
氰化提金工艺及污水处理1 氰化提金工艺1.1 概述氰化提金是现代黄金矿山选冶的主要方法。
我国早于1900年山东威海卫金矿有限公司开采狼虎山等地金矿,1901年在威海范家埠建有一座2t/d氰化试验厂,是我国首次用氰化法提金;1936-1939年间,台湾金瓜石金矿采用机械搅拌氰化浸出矿石中的金。
1965年山东招远县玲珑金矿实现金精矿机械连续搅拌氰化提金工业生产。
而金矿石氰化提金乃是于1983年分别由长春黄金研究所与吉林省冶金研究所在河南灵宝县的灵湖金矿以及吉林汪清县的赤卫沟金矿建成50t/d全泥氰化炭浆厂,并拥有我国独立的知识产权,开发了现代采金技术先河。
为了进一步推动全泥氰化炭浆技术的发展,原冶金部黄金局决定从国外引进先进技术和设备。
1984年北京有色冶金设计研究总院、长春黄金设计院与美国戴维·麦基公司合作设计,分别在陕西撞关金矿和河北张家口金矿1985年建成250比和450t/d的全泥氰化炭浆厂,依靠自己的技术和设备1986年在河南银洞坡金矿建成300比的全泥氰化炭浆厂。
自此,我国黄金选冶技术有了长足进步,有炭浆法、锌粉置换法、树脂提金法(1988年在安徽东溪金矿建成50t/d,1995年在新疆阿希金矿建成750t/d的全泥氰化树脂矿浆法提金厂)等。
1.2 氰化提金工艺概况自20世纪80年代发明有自己知识产权的氰化提金工艺之后,又经90年代发展与完善,我国已基本满足了不同条件不同类型矿石及金精矿氰化提金的需要,有了上述多种工艺,从北到南,由东至西,氰化提金已是常规选冶工艺了,其生产厂家难以统计。
(l)氰化提金工艺和设备的进展①一浸一洗工艺发展到两浸两洗工艺前一种工艺对于含铜较高的难浸矿石,浸出率是难以提高的,改用后一种工艺,浸出率可提高2%一5%,现已在氰化厂中普遍采用。
全泥氰化提金工艺简介
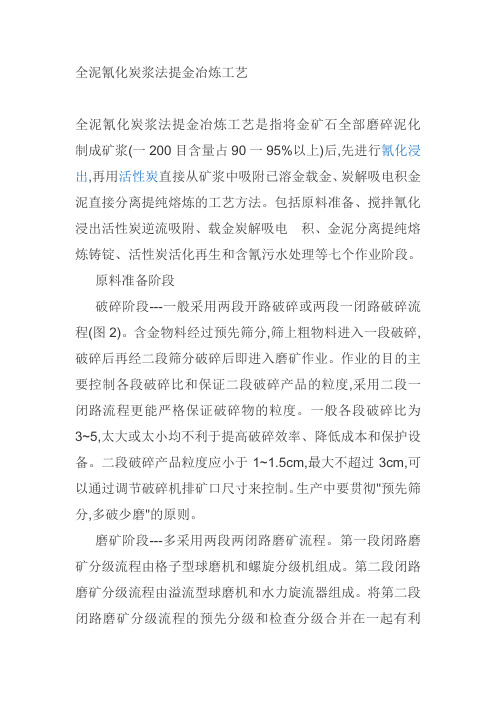
全泥氰化炭浆法提金冶炼工艺全泥氰化炭浆法提金冶炼工艺是指将金矿石全部磨碎泥化制成矿浆(一200目含量占90一95%以上)后,先进行氰化浸出,再用活性炭直接从矿浆中吸附已溶金载金、炭解吸电积金泥直接分离提纯熔炼的工艺方法。
包括原料准备、搅拌氰化浸出活性炭逆流吸附、载金炭解吸电积、金泥分离提纯熔炼铸锭、活性炭活化再生和含氰污水处理等七个作业阶段。
原料准备阶段破碎阶段---一般采用两段开路破碎或两段一闭路破碎流程(图2)。
含金物料经过预先筛分,筛上粗物料进入一段破碎,破碎后再经二段筛分破碎后即进入磨矿作业。
作业的目的主要控制各段破碎比和保证二段破碎产品的粒度,采用二段一闭路流程更能严格保证破碎物的粒度。
一般各段破碎比为3~5,太大或太小均不利于提高破碎效率、降低成本和保护设备。
二段破碎产品粒度应小于1~1.5cm,最大不超过3cm,可以通过调节破碎机排矿口尺寸来控制。
生产中要贯彻"预先筛分,多破少磨"的原则。
磨矿阶段---多采用两段两闭路磨矿流程。
第一段闭路磨矿分级流程由格子型球磨机和螺旋分级机组成。
第二段闭路磨矿分级流程由溢流型球磨机和水力旋流器组成。
将第二段闭路磨矿分级流程的预先分级和检查分级合并在一起有利于提高磨矿效率和保证产品细度。
破碎好的含金物料经过第一段闭路磨矿分级流程后,矿浆中一200目含量为55%一65%。
再经过第二段闭路磨矿分级流程后矿浆中一200目物料含量就可达90%一95%以上,符合全泥氰化工艺的细度要求。
本段作业主要控制磨矿浓度、溢流浓度和溢流细度。
一般磨矿浓度:第一段为75%一80%,第二段为60%~65%;溢流浓度:第一段为25%~30%,第二段为14%一20%;溢流细度(一200目含量):第一段为55%~65%,第二段为90写一95%以上。
磨矿浓度的控制主要通过调节给水量、给矿量和返砂比等,若磨矿浓度偏高,则增加给水量、减少给图3两段两闭路磨矿流程矿量,增大返砂比等,反之亦然。
氰化法提金工艺
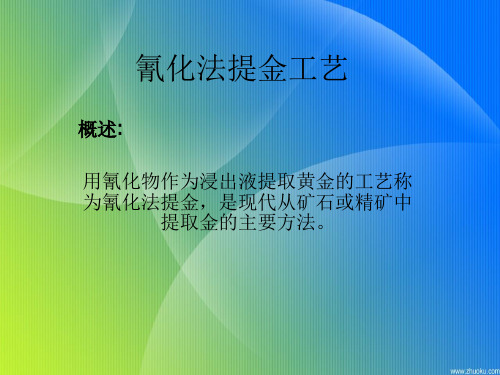
矿浆粘度的影响
• 氰化矿浆的粘度会直接影响氰化物和氧的扩散速度,当矿浆粘度较高时,对金粒与溶 液间的相对流动产生阻碍作用。
• 在矿浆温度等条件相同的情况下,矿浆浓度和含泥量是决定矿浆粘度的主要条件。因 为固体颗粒在液体中被水润湿后,在其表面形成一个水层,水层与固体颗粒之间,由 于吸附和水合等作用很难产生相对流动。
• 为达氰化浸出的最优效果,助浸剂除了能增加矿浆中的 “有效活性氧”含量外,一般还应具备如下功能:
• (1)分散作用:利用分散作用,使矿浆得到充分分散,增加氰化 物与金的有效接触机会。
• (2)除杂作用:利用除杂作用,消除或减弱矿浆中杂质对金矿 浸出的不利影响,提高金的浸出效果。
• (3)螯合作用:利用螯合作用,增加对金的溶出效果并消除影 响金浸出的杂质元素。[1]
氰化法提金工艺
概述:
用氰化物作为浸出液提取黄金的工艺称 为氰化法提金,是现代从矿石或精矿中
提取金的主要方法。
基本工序
• 氰化法提金工艺包括:氰化浸出、浸出矿 浆的洗涤过滤、氰化液或氰化矿浆中金的 提取和成品的冶炼等几个基本工序。
传统的氰化法提金工艺主要包括浸 出、洗涤、置换(沉淀)三个工序
• ①浸出——矿石中固体金溶解于含氧的
氰化物用量
• 氰化物浓度是决定金溶解速度的主要因素。 因此,在氰化浸出时,矿浆中必须确保一定的 游离CN-,保证金的氰化浸出。
温度的影响
• 金在氰化液中的溶解速度随着矿浆温度的升高而增大。当温度为80℃时,溶解速度达 到最大值
• (1)金的溶解速度随着温度的升高而增大,当80℃时,达到最大值,此后温度升高, 金溶解速度反而降低。
丹东虎山金矿试验成功后,相继在河南、河北、辽宁、云
南、湖北、内蒙古、黑龙江、吉林、陕西等省区推广应用,
贵金属选冶理论与技术第三章氰化法提金工艺.
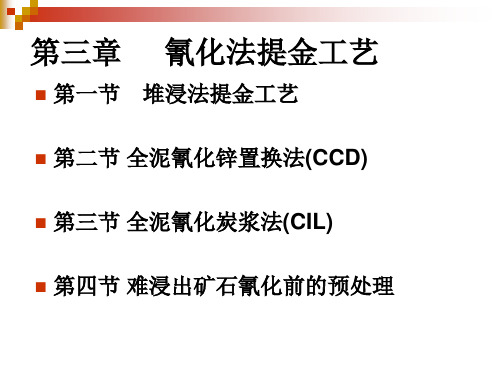
6、贵液中的杂质
溶液中所含杂质如铜、汞、镍及可溶性硫化物等都是置换金的 有害杂质。
(1)铜的络合物与锌反应时,铜被置换而消耗锌,同时铜在锌的 表面形成薄膜防碍金的置换,其反应式:
2Na2Cu(CN)3 + Zn = 2Cu + Na2Zn(CN)4 + 2NaCN (2)汞与锌发生反应生成的汞与锌合金使锌变脆,影响金的置换
一、堆浸法提金生产的主要经验
(1)破碎。根据矿石性质及工艺要求,实行不同的破 碎工艺流程。经过对堆浸矿山的调查,主要分三种 情况:废矿石堆浸一般不破碎(占30%),二段破 碎后矿石粒度为30~50mm(占53%),三段破碎后 矿石粒度为9~19mm(占17%)。
实践证明:破碎是保证矿石具有良好渗透性,提高 金的浸出率的关键技术环节之一。
锌粉置换:氰浓度为0.03~0.06%,碱浓度为0.01~0.03%。
2、氧的浓度
金在氰化物中溶解必须有氧参加,而置换是金溶解 的逆相过程,置换过程中的溶解氧对置换是有害的。 氧的存在会加快锌的溶解速度,增加锌耗,大量产 生氢氧化锌和氰化锌沉淀而影响置换。
溶氧量:生产中,一般控制溶液中的溶解氧时在 0.5mg/L以下。
(2)若溶液中CN-低浓度时,氰锌络合物分解并生成不溶解的氰 化锌(白色沉淀):
Zn(CN)2-4 + Zn(OH)2 = 2Zn(CN)2 +2OH总之:上述反应中生成的氢氧化锌和氰化锌沉淀会沉积在锌的
表面妨碍金的置换,所以在金的置换过程中,要保持溶液中 有一定的氰化物和碱的浓度,避免Zn(OH)2 和 Zn(CN)2的生 成,使金的置换过程顺利进行。
第三章 氰化法提金工艺
黄金矿石氰化工艺流程

黄金矿石氰化工艺流程
黄金矿石氰化工艺是一种常用的黄金提取方法,通常包括以下几个步骤:
1. 破碎和磨矿:将黄金矿石经过破碎和磨矿处理,使其细碎成适当的颗粒大小,便于后续的处理。
2. 浸矿:将磨碎的矿石放入浸矿槽(也称为浸矿池或浸没槽),并加入含有氰化物的溶液。
常用的氰化物是氰化钠(NaCN)。
3. 溶液搅拌:通过搅拌设备,使氰化物溶液与矿石充分接触,以促进黄金的溶解。
4. 氧化:为了加速黄金的氧化反应,可以向氰化槽中通入空气或氧气。
氧化有助于黄金的氧化还原反应,使黄金溶解速度增加。
5. 吸附:在溶液中,黄金以氰化物配合物(如Au(CN)2-)的形式存在。
为了将黄金从溶液中分离出来,使用活性炭吸附剂,将黄金配合物吸附到活性炭上。
6. 脱附:经过一段时间的吸附,活性炭上富集了大量的黄金。
然后,通过脱附过程,将黄金从活性炭上解吸下来。
通常使用热碱溶液(如氢氧化钠)或其他脱附剂进行脱附。
7. 脱氰:脱附后得到含有黄金的溶液,其中还含有氰化物。
为了回收氰化物,需要对溶液进行脱氰处理。
常用的方法是将溶液经过多级氧化处理,将氰化物转化为无害的氰酸盐。
8. 沉淀和纯化:经过脱氰处理后,得到的黄金溶液中含有金离子。
通过加入沉淀剂(如二硫化钠、水合硫酸亚铁等),使金离子还
原成金属黄金沉淀出来。
然后,对沉淀的黄金进行洗涤、过滤、干燥等工艺步骤,以得到纯净的黄金产品。
需要注意的是,黄金矿石氰化工艺涉及到氰化物的使用,氰化物具有一定的毒性,操作时需要严格控制环境和工艺条件,确保操作安全。
氰化法提金工艺

氰化法提金工艺嘿,朋友们!今天咱来聊聊氰化法提金工艺,这可真是个有趣又重要的玩意儿呢!你想想看,金子啊,那可是闪闪发光让人眼馋的宝贝呀!而氰化法就是能把金子从各种矿石里给弄出来的厉害手段。
就好像是一个神奇的魔法,能把隐藏起来的金子给变出来。
氰化法提金呢,简单来说,就是利用氰化物的特性来和金子发生反应。
这就好比是两个好朋友,一见面就紧紧拥抱在一起啦。
氰化物就像是个热情的小伙伴,紧紧抱住金子不撒手。
不过呢,这个过程可不能马虎。
就像做饭一样,得掌握好火候和调料的用量。
氰化物的浓度呀,反应的时间呀,温度呀等等,都得恰到好处。
不然,要么金子提不出来,要么可能会出啥岔子呢。
咱再打个比方,这氰化法提金就像是一场精密的手术。
医生得小心翼翼地操作,不能有一点差错。
在这个过程中,每一个环节都得精心照料,稍有不慎可能就前功尽弃啦。
而且呀,这氰化法提金可不是随随便便就能干的。
得有专业的设备和技术人员。
这可不是小孩子过家家,得认真对待才行呢!你说要是设备不行,那不就像是战士上战场没带好武器一样嘛,怎么能打胜仗呢?还有啊,安全问题可不能忽视。
氰化物可不是好惹的,要是不小心弄不好,那可是会出大问题的。
就像家里的电老虎,你不注意它就会咬你一口。
所以呀,操作的时候一定要万分小心,做好各种防护措施。
但是呢,一旦掌握好了这个工艺,那可就厉害啦!能把那些藏在矿石里的金子都给弄出来,那感觉,就像是发现了一个大宝藏!总的来说,氰化法提金工艺是个很有意思也很有挑战性的事情。
它就像是一个神秘的宝库,等待着我们去探索和发现。
只要我们认真对待,小心操作,就一定能从里面掏出大把大把的金子来!不是吗?。
氰化法提金工艺
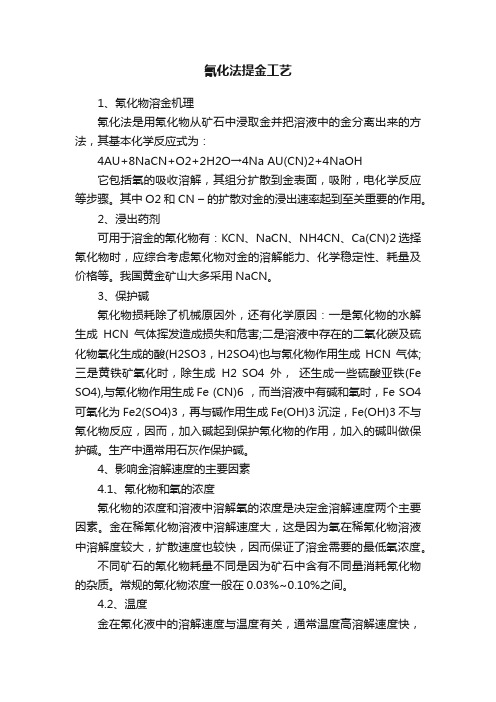
氰化法提金工艺1、氰化物溶金机理氰化法是用氰化物从矿石中浸取金并把溶液中的金分离出来的方法,其基本化学反应式为:4AU+8NaCN+O2+2H2O→4Na AU(CN)2+4NaOH它包括氧的吸收溶解,其组分扩散到金表面,吸附,电化学反应等步骤。
其中O2和CN –的扩散对金的浸出速率起到至关重要的作用。
2、浸出药剂可用于溶金的氰化物有:KCN、NaCN、NH4CN、Ca(CN)2选择氰化物时,应综合考虑氰化物对金的溶解能力、化学稳定性、耗量及价格等。
我国黄金矿山大多采用NaCN。
3、保护碱氰化物损耗除了机械原因外,还有化学原因:一是氰化物的水解生成HCN气体挥发造成损失和危害;二是溶液中存在的二氧化碳及硫化物氧化生成的酸(H2SO3,H2SO4)也与氰化物作用生成HCN气体;三是黄铁矿氧化时,除生成H2 SO4外,还生成一些硫酸亚铁(Fe SO4),与氰化物作用生成Fe (CN)6 ,而当溶液中有碱和氧时,Fe SO4可氧化为Fe2(SO4)3,再与碱作用生成Fe(OH)3沉淀,Fe(OH)3不与氰化物反应,因而,加入碱起到保护氰化物的作用,加入的碱叫做保护碱。
生产中通常用石灰作保护碱。
4、影响金溶解速度的主要因素4.1、氰化物和氧的浓度氰化物的浓度和溶液中溶解氧的浓度是决定金溶解速度两个主要因素。
金在稀氰化物溶液中溶解速度大,这是因为氧在稀氰化物溶液中溶解度较大,扩散速度也较快,因而保证了溶金需要的最低氧浓度。
不同矿石的氰化物耗量不同是因为矿石中含有不同量消耗氰化物的杂质。
常规的氰化物浓度一般在0.03%~0.10%之间。
4.2、温度金在氰化液中的溶解速度与温度有关,通常温度高溶解速度快,在无特殊工艺要求的条件下,使矿浆温度维持在150C~250C即可满足浸出的要求。
4.3、金粒的大小和形状金的溶解速度与金粒暴露的表面积成正比,因此氰化作业的磨矿粒度要比浮选更细一些。
4.4、矿浆浓度和矿泥矿浆浓度和矿泥含量直接影响溶剂的扩散速度和溶剂与金粒的接触。
提金技术工艺大全(专利)
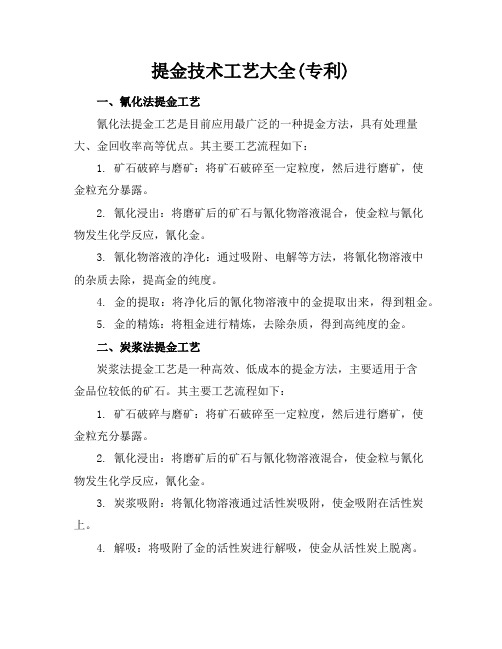
提金技术工艺大全(专利)一、氰化法提金工艺氰化法提金工艺是目前应用最广泛的一种提金方法,具有处理量大、金回收率高等优点。
其主要工艺流程如下:1. 矿石破碎与磨矿:将矿石破碎至一定粒度,然后进行磨矿,使金粒充分暴露。
2. 氰化浸出:将磨矿后的矿石与氰化物溶液混合,使金粒与氰化物发生化学反应,氰化金。
3. 氰化物溶液的净化:通过吸附、电解等方法,将氰化物溶液中的杂质去除,提高金的纯度。
4. 金的提取:将净化后的氰化物溶液中的金提取出来,得到粗金。
5. 金的精炼:将粗金进行精炼,去除杂质,得到高纯度的金。
二、炭浆法提金工艺炭浆法提金工艺是一种高效、低成本的提金方法,主要适用于含金品位较低的矿石。
其主要工艺流程如下:1. 矿石破碎与磨矿:将矿石破碎至一定粒度,然后进行磨矿,使金粒充分暴露。
2. 氰化浸出:将磨矿后的矿石与氰化物溶液混合,使金粒与氰化物发生化学反应,氰化金。
3. 炭浆吸附:将氰化物溶液通过活性炭吸附,使金吸附在活性炭上。
4. 解吸:将吸附了金的活性炭进行解吸,使金从活性炭上脱离。
5. 金的精炼:将解吸后的金进行精炼,去除杂质,得到高纯度的金。
三、树脂法提金工艺树脂法提金工艺是一种新型、高效的提金方法,具有处理量大、金回收率高等优点。
其主要工艺流程如下:1. 矿石破碎与磨矿:将矿石破碎至一定粒度,然后进行磨矿,使金粒充分暴露。
2. 氰化浸出:将磨矿后的矿石与氰化物溶液混合,使金粒与氰化物发生化学反应,氰化金。
3. 树脂吸附:将氰化物溶液通过树脂吸附,使金吸附在树脂上。
4. 解吸:将吸附了金的树脂进行解吸,使金从树脂上脱离。
5. 金的精炼:将解吸后的金进行精炼,去除杂质,得到高纯度的金。
四、生物法提金工艺生物法提金工艺是一种环保、低成本的提金方法,主要适用于含金品位较低的矿石。
其主要工艺流程如下:1. 矿石破碎与磨矿:将矿石破碎至一定粒度,然后进行磨矿,使金粒充分暴露。
2. 生物氧化:将磨矿后的矿石与生物氧化剂混合,使金粒与氧化剂发生反应,可溶性金。
几种氰化法提金介绍备课讲稿
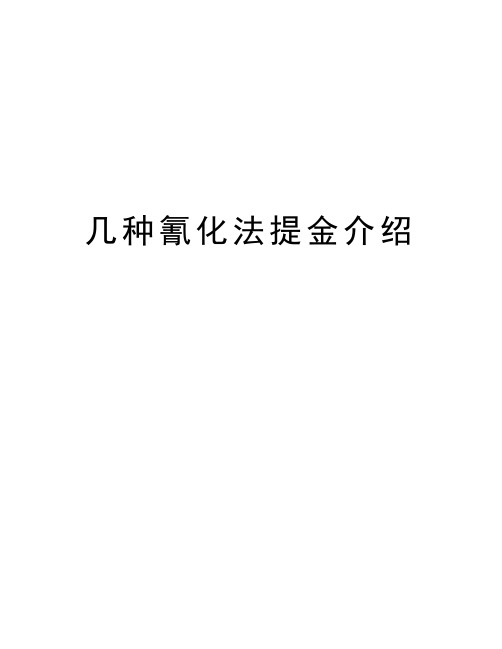
几种氰化法提金介绍2016-12-06 廖德华紫金矿业HOT全球矿业资讯1.氰化法提金概述氰化法提金是以氰化物的水溶液作溶剂,浸出含金矿石中的金,然后再从含金浸出液中提取金的方法。
氰化法提金主要包括如下两个步骤:(1)氰化浸出:在稀薄的氰化溶液中,并有氧(或氧化剂)存在的条件下,含金矿石中的金与氰化物反应生成一价金的络合物而溶解进入溶液中,得到浸出液以氰化钾为例,反应式为:4Au+8KCN+2H2O→4KAu(CN)2+4KOH氰化浸出金的工艺方法有槽浸氰化法和堆浸氰化法两类。
槽浸氰化法是传统的浸金方法,又分渗滤氰化法和搅拌氰化法两种;堆浸法是近20年来才出现的新技术,主要用于处理低品位氧化矿。
自1887发现氰化液可以溶金以来,氰化法浸出至今已有近百年的生产实践,工艺比较成熟,回收率高,对矿石适应性强,能就地产金,所以至今仍是黄金浸出生产的主要方法。
(2)沉积提金:从氰化浸出液中提取金。
工艺方法有加锌置换法(锌丝置换法和锌粉置换法)、活性炭吸附法(炭浆法CIP和炭浸法CIL)、离子交换树脂法(树脂矿浆法RIP和RIL)、电解沉积法、磁炭法等。
锌粉(丝)置换法是较为传统的提金方法,在黄金矿山应用较多;炭浆法是目前新建金矿的首选方法,其产金量占世界产金量的50%以上;其余方法在黄金矿山也正日渐得到应用。
2.渗滤氰化法渗滤氰化法是氰化浸出的工艺方法之一,是基于氰化溶液渗透通过矿石层而使含金矿石中的金浸出的方法,适用于砂矿和疏松多孔物料。
渗滤氰化法的主要设备是渗滤浸出槽。
渗滤浸出槽通常为木槽、铁槽或水泥槽。
槽底水平或稍倾斜,呈圆形、长方形或正方形。
槽的直径或边长一般为5~12米,高度一般为2~2.5米,容积一般为50~150吨。
渗滤氰化法的工艺过程:(1)装入矿砂及碱:要求布料均匀,粒度一致,疏松一致。
有干法和湿法两种装法。
干法适于水分在20%以下的矿砂,可用人工或机械装矿。
湿法是将矿浆用水稀释后,用砂泵扬送或沿槽自流入槽内。
几种氰化法提金介绍
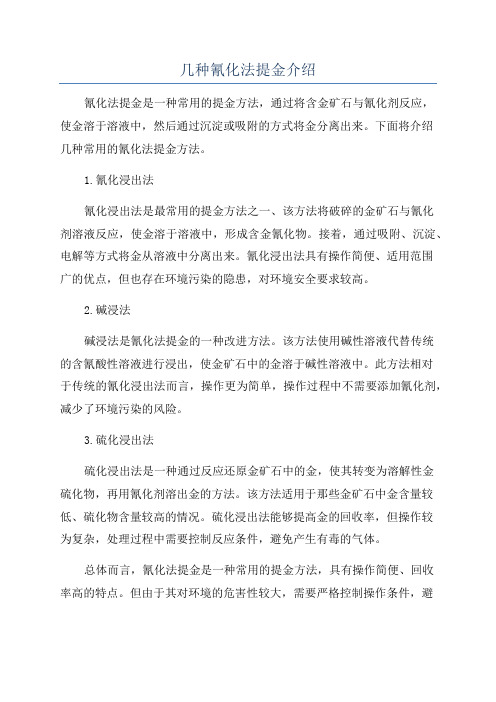
几种氰化法提金介绍
氰化法提金是一种常用的提金方法,通过将含金矿石与氰化剂反应,
使金溶于溶液中,然后通过沉淀或吸附的方式将金分离出来。
下面将介绍
几种常用的氰化法提金方法。
1.氰化浸出法
氰化浸出法是最常用的提金方法之一、该方法将破碎的金矿石与氰化
剂溶液反应,使金溶于溶液中,形成含金氰化物。
接着,通过吸附、沉淀、电解等方式将金从溶液中分离出来。
氰化浸出法具有操作简便、适用范围
广的优点,但也存在环境污染的隐患,对环境安全要求较高。
2.碱浸法
碱浸法是氰化法提金的一种改进方法。
该方法使用碱性溶液代替传统
的含氰酸性溶液进行浸出,使金矿石中的金溶于碱性溶液中。
此方法相对
于传统的氰化浸出法而言,操作更为简单,操作过程中不需要添加氰化剂,减少了环境污染的风险。
3.硫化浸出法
硫化浸出法是一种通过反应还原金矿石中的金,使其转变为溶解性金
硫化物,再用氰化剂溶出金的方法。
该方法适用于那些金矿石中金含量较低、硫化物含量较高的情况。
硫化浸出法能够提高金的回收率,但操作较
为复杂,处理过程中需要控制反应条件,避免产生有毒的气体。
总体而言,氰化法提金是一种常用的提金方法,具有操作简便、回收
率高的特点。
但由于其对环境的危害性较大,需要严格控制操作条件,避
免对生态环境造成污染。
在实际应用中,还可以结合其他方法,如浮选、压磨等,来提高金的提取率和回收率,降低环境风险。
氰化提金工艺

圆筒扎德拉电解槽:3槽串联,91×120cm;
阴极装:7.2 kg钢棉/个;
阳极:不锈钢圆筒形筛网;
金总回收率:~95%;
图 美国霍姆斯特克矿业公司莱德矿炭浆法生产工艺流程 黄金产量:~8 t/a
20
9.5 磁炭法
磁炭法:磁性炭浆法。
操作与炭浆法和炭浸法基本相同,但由于可采用弱磁选机回收浸出吸 附尾浆中的载金细粒炭,因此磁炭工艺可克服活性炭易磨损而造成细粒载 金炭损失的缺点。
小规模常采用吸附塔:装活性炭25-30 kg。
9
9.4 炭浆工艺
把氰化浸出槽排出的矿浆,送到吸附槽用活性炭吸附矿浆中的 金银的方法,称为炭浆法(CIP)。
把活性炭投入氰化浸出槽中,使氰化浸出金与炭吸附金在同一 槽中进行的方法,称为炭浸法(CIL)。
当前,它已成为新建金矿的首选方法,世界产金量一半以上是 用该法生产的。
1
18
0.72
11250
62.5
2
18
0.27
4500
85.9
3
24
0.06
2550
96.9
4
24
0.015
600
99.2
16
3、解吸 (1)常压解吸法
85 0C下,用1%氰化钠和1%氢氧化钠,24-60h解吸。 或95 0C下,用4%氰化钠和2%氢氧化钠,12-14h解吸。 (2)酒精解吸法 80 0C常压下,用0.1%氰化钠、1%氢氧化钠、20%体积 的酒精,5-6h解吸。缺点是易燃,费用高,需回收。 (3)高压解吸法 160 0C、3.5*105Pa下,用0.1%氰化钠、1%氢氧化钠、 2-9h解吸,或用含1%氰化钠和5%氢氧化钠溶液预处理后5倍 炭体积热水解吸 优点是试剂消耗少解吸时间短,但需高压,减压前需冷却。
全泥氰化提金工艺设计与生产实践

全泥氰化提金工艺设计与生产实践一、工艺流程设计泥氰化提金工艺是一种常用的金属提取工艺,主要用于提取含金废物中的金属成分。
下面是一个典型的泥氰化提金工艺流程设计:1.前处理:将含金废物进行粉碎与破碎,使其颗粒大小均匀,并去除其中的杂质和有机物。
2.浸泡:将经过前处理的含金废物浸入氰化溶液中,进行化学反应。
反应时间根据废物的性质和废物含金量而定,一般为24小时至72小时。
3.沉淀:将反应后的溶液经过沉淀处理,使其中的金属成分沉淀下来。
4.过滤:将沉淀后的溶液进行过滤,去除其中的固体杂质。
5.再溶解:将过滤后的固体沉淀添加到盐酸等溶液中进行再溶解,使其中的金属成分溶解于溶液中。
6.萃取:将再溶解后的溶液进行萃取处理,利用有机溶剂提取其中的金属成分。
萃取条件为温度控制在50-70摄氏度,时间控制在2-4小时。
7.还原:将经过萃取的有机溶剂中的金属成分进行还原处理,得到金属纯度较高的金属产品。
8.精炼:将还原后的金属产品进行精炼处理,提高其纯度。
以上是一个典型的泥氰化提金工艺流程设计,根据实际情况,工艺流程中的各个环节还可以进行调整,以提高提金效率和产品的纯度。
二、生产实践在实际生产过程中,需要注意以下几个方面:1.设备选择:根据生产规模和工艺流程要求,选择合适的设备,如破碎机、浸泡槽、沉淀槽、过滤设备、萃取塔等。
设备选择要考虑生产效率、产品质量、安全性和经济性等因素。
2.溶液控制:泥氰化提金工艺中的浸泡和萃取环节涉及到溶液控制,需要严格控制溶液的温度、浓度、pH值等参数,以提高金属提取率和产品纯度。
3.杂质处理:在泥氰化提金过程中,含金废物中通常会存在一些杂质,如铜、银、铅等,需要根据具体情况采取相应的处理方法,如溶解、沉淀、萃取等,以提高产品的纯度。
4.安全保护:在泥氰化提金生产中,由于涉及到氰化物的使用,需要加强安全保护工作,严格遵守操作规程,提供足够的通风和防护设施,确保操作人员和环境的安全。
5.产品质量检测:在生产过程中,需要对产品的质量进行检测,包括金属纯度、杂质含量、产品外观等指标的检测,以确保产品符合质量要求。
几种氰化法提金介绍
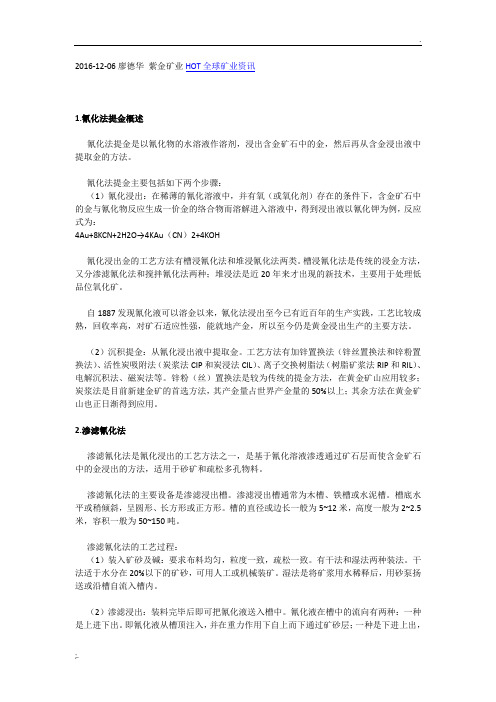
2016-12-06 廖德华紫金矿业HOT全球矿业资讯1.氰化法提金概述氰化法提金是以氰化物的水溶液作溶剂,浸出含金矿石中的金,然后再从含金浸出液中提取金的方法。
氰化法提金主要包括如下两个步骤:(1)氰化浸出:在稀薄的氰化溶液中,并有氧(或氧化剂)存在的条件下,含金矿石中的金与氰化物反应生成一价金的络合物而溶解进入溶液中,得到浸出液以氰化钾为例,反应式为:4Au+8KCN+2H2O→4KAu(CN)2+4KOH氰化浸出金的工艺方法有槽浸氰化法和堆浸氰化法两类。
槽浸氰化法是传统的浸金方法,又分渗滤氰化法和搅拌氰化法两种;堆浸法是近20年来才出现的新技术,主要用于处理低品位氧化矿。
自1887发现氰化液可以溶金以来,氰化法浸出至今已有近百年的生产实践,工艺比较成熟,回收率高,对矿石适应性强,能就地产金,所以至今仍是黄金浸出生产的主要方法。
(2)沉积提金:从氰化浸出液中提取金。
工艺方法有加锌置换法(锌丝置换法和锌粉置换法)、活性炭吸附法(炭浆法CIP和炭浸法CIL)、离子交换树脂法(树脂矿浆法RIP和RIL)、电解沉积法、磁炭法等。
锌粉(丝)置换法是较为传统的提金方法,在黄金矿山应用较多;炭浆法是目前新建金矿的首选方法,其产金量占世界产金量的50%以上;其余方法在黄金矿山也正日渐得到应用。
2.渗滤氰化法渗滤氰化法是氰化浸出的工艺方法之一,是基于氰化溶液渗透通过矿石层而使含金矿石中的金浸出的方法,适用于砂矿和疏松多孔物料。
渗滤氰化法的主要设备是渗滤浸出槽。
渗滤浸出槽通常为木槽、铁槽或水泥槽。
槽底水平或稍倾斜,呈圆形、长方形或正方形。
槽的直径或边长一般为5~12米,高度一般为2~2.5米,容积一般为50~150吨。
渗滤氰化法的工艺过程:(1)装入矿砂及碱:要求布料均匀,粒度一致,疏松一致。
有干法和湿法两种装法。
干法适于水分在20%以下的矿砂,可用人工或机械装矿。
湿法是将矿浆用水稀释后,用砂泵扬送或沿槽自流入槽内。
全泥氰化工艺
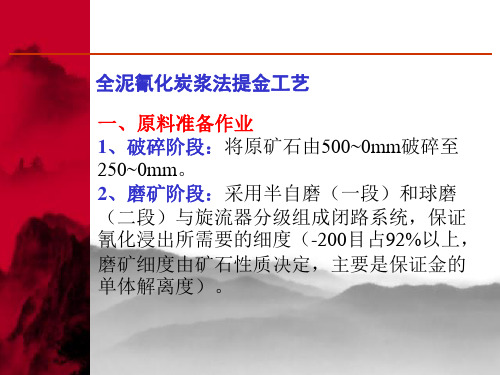
三、活性炭逆流吸附阶段 5、串炭量:为保持吸附系统金总量平衡和各 槽内槽间炭吸附性能,串炭量一般占槽内总 量的10~20%,通过调节串炭时间来控制。 6、炭载金量:为综合回银,控制炭载金量在 900~1000g/t,通过调节提炭量来控制。
三、活性炭逆流吸附阶段 7、尾液含金量:控制尾液含金量在0.07g/m3 以下,过高则说明活性炭吸附率降低了,可 通过增加底炭密度、降低载金炭含量和缩短 串炭时间等来控制。 8、尾矿品位:要求一厂小于0.24g/t、二厂小 于0.22g/t,原则上可通过提高磨矿细度、降低 矿浆浓度、减少处理量和延长浸出时间等来 控制。
全泥氰化炭浆法提金工艺 一、原料准备作业 1、破碎阶段:将原矿石由500~0mm破碎至 250~0mm。 2、磨矿阶段:采用半自磨(一段)和球磨 (二段)与旋流器分级组成闭路系统,保证 氰化浸出所需要的细度(-200目占92%以上, 磨矿细度由矿石性质决定,主要是保证金的 单体解离度)。
一、原料准备作业 3、除屑作业:遵循由粗到细除屑的原则进行 多级除屑流程,破碎前人工捡出木屑杂物, 磨机出料口设圆筒筛,渣浆泵池前设细筛网 (一般20目),旋流器溢流设圆筒筛(24~28 目)。 4、调浆阶段:在浓密机中进行,满足氰化的 条件:控制浓度35%~38%、pH值10~11(浓 度由浓密机底流量和添加絮凝剂用量控制, pH值由原矿中石灰用量和浓密机中氢氧化钠 用量控制)。
二、搅拌氰化浸出阶段 矿浆在搅拌槽中进行预浸(3槽,氰化钠溶 液提前加入磨矿机中也属预浸)。关键是控 制CN-浓度(万分之5~5.5)和氧含量(充气 量0.02m3/m3· min和充气压力100kPa,调节各 气阀门),矿浆表面均匀弥散5~15mm直径气 泡为宜。
氰化提金工艺
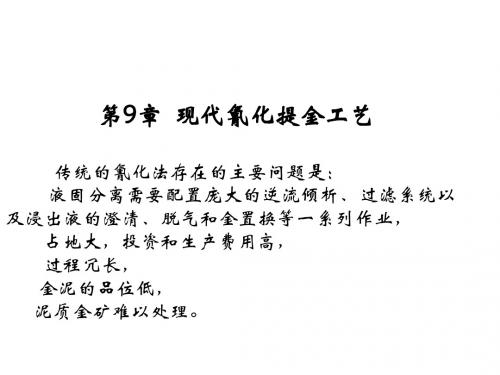
9.1.5 载金活性炭的解吸
从矿浆分离出来的载金活性炭,经洗涤和除去木屑等杂物 后送去解吸金(银)。载金活性炭的主要解吸方法有:
⑴常压解吸法
这一方法是最早在工业上应用的载金活性炭解吸方法,它是 由美国矿业局的Zadra研究成功的,因此,常称为扎德拉(Zadra) 法。 用0.1~0.2%的氰化钠和1%的氢氧化钠混合溶液,在 85~950C下从载金炭上解吸金。解吸液用电积法回收金。解吸 液与载金炭的体积比为8~15,并采用解吸液和电积溶液循环的 方式,解吸槽流出的含金贵液经预热并加热到所需的温度,以 每小时1~2柱床体积的流速给入解吸柱内,在常压下解吸 24~26h,即可将炭解吸到充分低的金品位。
8.1.2 活性炭吸附金的机理
⑴ 以金属形态被吸附 活性炭从金氯配合物(AuCl4-)溶液中吸附金后,可明显地看到 在炭的表面有黄色的金属金。以此推断金氰配合物也可被炭还 原。这种观点认为,炭上吸附的还原气体,如CO,可把金还原。
采用现代的分析技术X射线光电子能谱(XPS)对炭上被吸 附物中的金的价态的研究表明,被吸附的金的表观价态为 +0.3价。
0.7~0.8 97~99 1.16~2.35(14~8) 2~4 1~4
1050~1200 1000~1500 60~70 36~40
选用炭浆法活性炭最重要的条件,一是它对金应具有 良好的吸附性能,二是炭粒应当具有很强的耐磨性能。良好 的炭浆法活性炭,除了具备表9-1的性能外,通常还可用下列 三项技术指标来确定。 ⑴ 在含金1mg/L溶液中平衡吸附24h,活性炭的载金容 量应达25g/kg。 ⑵ 在含金10mg/L溶液中搅拌吸附1h,活性炭对金的吸 附率应达60%。 ⑶ 将活性炭臵于瓶中在摇滚机上翻滚24h,磨损率应小于 2%。
氰化法提金的工艺流程

氰化法提金的工艺流程氰化法提金呀,这可是个挺有趣的事儿呢。
一、氰化法提金的基础。
氰化法提金呢,就是利用氰化物能和金形成络合物这个特性。
一般来说,最常用的氰化物就是氰化钠啦。
金在矿石里可不会乖乖地自己出来,但是和氰化钠一接触,就会发生反应,生成一种叫金氰络合物的东西。
这就像是金和氰化钠交上了朋友,然后一起变成了一种新的形式,可以在溶液里存在啦。
矿石里的金可能是以很微小的颗粒存在的,或者和其他矿物混在一起,氰化法就能把它从那些“小伙伴”身边拉走,让它进入溶液里。
二、氰化浸出过程。
这个过程可重要啦。
要把含有金的矿石磨碎,磨得越细越好呢。
为啥呢?因为这样金就有更多的表面能和氰化物接触呀。
就像你要和很多人握手,你把手伸得越大,能握到的人就越多嘛。
把磨碎的矿石放到氰化钠溶液里,然后就开始浸出的过程啦。
这个过程需要一定的时间,就像炖菜一样,小火慢炖才能把味道都炖进去。
在这个过程中,金就慢慢地从矿石里跑到溶液里去了。
不过呢,这个过程也不是一帆风顺的,有时候矿石里的其他物质会捣乱,影响金和氰化物的反应,这就需要我们想办法去克服这些干扰啦。
三、金的回收。
金跑到溶液里之后,我们可不能就这么让它在溶液里待着呀。
接下来就要把金从溶液里回收出来。
有一种方法是用锌粉置换。
就像在一群小伙伴里,锌粉跑进去把金给换出来。
锌比金更活泼,它就把金从金氰络合物里挤出来了,金就又变回了自己的单质状态,然后就可以把它收集起来啦。
还有其他的回收方法呢,不过锌粉置换是比较常用的一种。
四、氰化法提金的注意事项。
这个氰化法提金虽然能把金提出来,但是也有很多要小心的地方。
氰化物可是有毒的东西呢,就像一个小恶魔,如果不小心处理,会对环境和人都造成很大的危害。
所以在整个过程中,对氰化物的储存、使用和废水处理都要特别特别小心。
废水里如果有残留的氰化物,可不能随便排放,得经过处理,把氰化物变成无毒的物质才行。
而且在操作的时候,工作人员也要做好防护措施,可不能让氰化物伤害到自己。
氰化法提金工艺

氰化法提金工艺(一)传统的氰化法提金工艺主要包括浸出、洗涤、置换(沉淀)三个工序。
①浸出——矿石中固体金溶解于含氧的氰化物溶液中的过程。
②洗涤——为回收浸出后的含金溶液,用水洗涤矿粒表面以及矿粒之间的已溶金,以实现固液分离的过程。
③置换——用金属锌从含金溶液中使其还原、沉淀,回收金的过程。
20世纪以来,从氰化矿浆中回收金是先进行矿浆的洗涤,然后进行贵液的澄清、除气。
从澄清的贵液中沉淀金,一直沿用锌置换法。
20世纪60年代以来才发展起来的向矿浆中加入活性炭的“炭浆法”发展很快。
随着对离子交换剂应用的研究,采用离子交换树脂从氰化液或氰化矿浆中吸附金的方法亦具有重要的实用价值。
在氰化液的溶剂萃取提金方面也作过一些研究。
当往氰化含金液中加人硫酸时,可用异戊醇来萃取金,萃取率随硫酸浓度的升高而增加。
如在2mol/L的硫酸液中进行萃取,还可使金与砷、铁等杂质分离。
使用氧代烷氧基磷酸酯从氰酸盐碱性液中萃取金,萃取指标令人满意;使用亚硫酸钠反萃取也获得了较好的结果等等。
1.氰化浸金用含氧的氰化物溶液把矿石中的金溶解出来的过程叫氰化浸出。
目前,无论从工艺、设备、管理或操作等方面都已日臻完善。
如前所述,金在含有氧的氰化物溶液中的溶解,实质上是一个电化学腐蚀过程。
浸出过程中主要使用的药剂是氰化物和保护碱两种。
1)氰化物工业上用于氰化法浸出金的氰化物主要有氰化钾(KCN)、氰化钠(NaCN)、氰化钙[Ca(CN)2]和氰化铵(NH4CN)四种。
它们对金的相对溶解能力见表1。
表1 四种氰化物的性质对金的相对溶解能力在生产中常用的氰化物是氰化钠,它是一种剧毒的白色粉末,商品氰化钠一般压制成球状或块状。
工业上也有用氰熔体作为浸出药剂的。
它是将氰化钙、食盐和焦炭混合后在电炉中熔化而成的一种混合物。
除了含40%~45%的Ca(CN)2和NaCN以外,还含有一些对氰化过程有害的杂质,如可溶性硫化物、碳以及一些不溶性杂质等。
其特点是价格便宜,但用量大,约为氰化钠的2~2.5倍。
金矿选矿之氰化法提金法
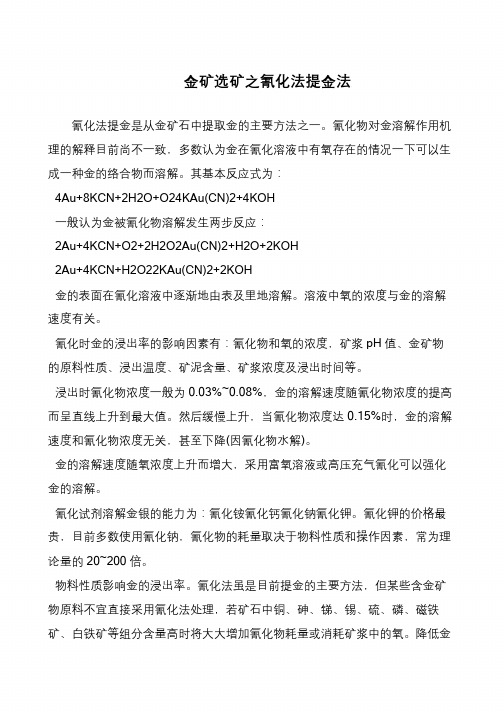
书山有路勤为径,学海无涯苦作舟
金矿选矿之氰化法提金法
氰化法提金是从金矿石中提取金的主要方法之一。
氰化物对金溶解作用机理的解释目前尚不一致,多数认为金在氰化溶液中有氧存在的情况一下可以生成一种金的络合物而溶解。
其基本反应式为:
4Au+8KCN+2H2O+O24KAu(CN)2+4KOH
一般认为金被氰化物溶解发生两步反应:
2Au+4KCN+O2+2H2O2Au(CN)2+H2O+2KOH
2Au+4KCN+H2O22KAu(CN)2+2KOH
金的表面在氰化溶液中逐渐地由表及里地溶解。
溶液中氧的浓度与金的溶解速度有关。
氰化时金的浸出率的影响因素有:氰化物和氧的浓度,矿浆pH 值、金矿物的原料性质、浸出温度、矿泥含量、矿浆浓度及浸出时间等。
浸出时氰化物浓度一般为0.03%~0.08%,金的溶解速度随氰化物浓度的提高而呈直线上升到最大值。
然后缓慢上升,当氰化物浓度达0.15%时,金的溶解速度和氰化物浓度无关,甚至下降(因氰化物水解)。
金的溶解速度随氧浓度上升而增大,采用富氧溶液或高压充气氰化可以强化金的溶解。
氰化试剂溶解金银的能力为:氰化铵氰化钙氰化钠氰化钾。
氰化钾的价格最贵,目前多数使用氰化钠,氰化物的耗量取决于物料性质和操作因素,常为理论量的20~200 倍。
物料性质影响金的浸出率。
氰化法虽是目前提金的主要方法,但某些含金矿物原料不宜直接采用氰化法处理,若矿石中铜、砷、锑、锡、硫、磷、磁铁矿、白铁矿等组分含量高时将大大增加氰化物耗量或消耗矿浆中的氧。
降低金。
- 1、下载文档前请自行甄别文档内容的完整性,平台不提供额外的编辑、内容补充、找答案等附加服务。
- 2、"仅部分预览"的文档,不可在线预览部分如存在完整性等问题,可反馈申请退款(可完整预览的文档不适用该条件!)。
- 3、如文档侵犯您的权益,请联系客服反馈,我们会尽快为您处理(人工客服工作时间:9:00-18:30)。
氰化法提金工艺—锌粉置换篇
传统的氰化法提金工艺主要包括浸出、洗涤、置换(沉淀)三个工序。
①浸出——矿石中固体金溶解于含氧的氰化物溶液中的过程。
②洗涤——为回收浸出后的含金溶液,用水洗涤矿粒表面以及矿粒之间的已溶金,以实现固液分离的过程。
③置换——用金属锌从含金溶液中使其还原、沉淀,回收金的过程。
20世纪以来,从氰化矿浆中回收金是先进行矿浆的洗涤,然后进行贵液的澄清、除气。
从澄清的贵液中沉淀金,一直沿用锌粉置换法。
20世纪60年代以来才发展起来的向矿浆中加入活性炭的“炭浆法”发展很快。
随着对离子交换剂应用的研究,采用离子交换树脂从氰化液或氰化矿浆中吸附金的方法亦具有重要的实用价值。
在氰化液的溶剂萃取提金方面也作过一些研究。
当往氰化含金液中加人硫酸时,可用异戊醇来萃取金,萃取率随硫酸浓度的升高而增加。
如在2mol/L的硫酸液中进行萃取,还可使金与砷、铁等杂质分离。
使用氧代烷氧基磷酸酯从氰酸盐碱性液中萃取金,萃取指标令人满意;使用亚硫酸钠反萃取也获得了较好的结果等等。
1.氰化浸金
用含氧的氰化物溶液把矿石中的金溶解出来的过程叫氰化浸出。
目前,无论从工艺、设备、管理或操作等方面都已日臻完善。
如前所述,金在含有氧的氰化物溶液中的溶解,实质上是一个电化学腐蚀过程。
浸出过程中主要使用的药剂是氰化物和保护碱两种。
1)氰化物
工业上用于氰化法浸出金的氰化物主要有氰化钾(KCN)、氰化钠(NaCN)、氰化钙
[Ca(CN)2]和氰化铵(NH4CN)四种。
在生产中常用的氰化物是氰化钠,它是一种剧毒的白色粉末,商品氰化钠一般压制成球状或块状。
工业上也有用氰熔体作为浸出药剂的。
它是将氰化钙、食盐和焦炭混合后在电炉中熔化而成的一种混合物。
除了含40%-45%的Ca(CN)2和NaCN以外,还含有一些对氰化过程有害的杂质,如可溶性硫化物、碳以及一些不溶性杂质等。
其特点是价格便宜,但用量大,约为氰化钠的2-2.5倍。
为了消除有害杂质的影响,使用氰熔体时应进行预先处理。
处理方法是通入空气强烈搅拌或往溶液中加入适量的铅盐。
在理论上,溶解1gAu只需消耗0.5g氰化钠,但在实际生产中,氰化物的消耗值为理论量的20-200倍,甚至更高一些。
消耗量的多少主要取决于矿石中能与氰化物起反应的其他成分的含量。
2)保护碱
保护碱主要是为了保持氰化物溶液的稳定性,减少氰化物的水解损失。
使碱在氰化浸出中的加入保持在浸出槽或者是氰化原矿的磨矿过程中。
当矿石成分复杂,含有一些诸如磁黄铁矿之类对氰化过程有害的矿物时,保护碱在磨矿过程中加入,有利于这些有害矿物氧化或形成沉淀除去。
保护碱可以是氢氧化钾和氢氧化钠,但更常用的是价格便宜的石灰(氢氧化钙)。
如若处理含金碲矿这类需要强碱度的矿石时,还是用氢氧化钠为好。
保护碱的加入量应当适量,一般维持矿浆的pH为10-11即可。
此时,矿浆中CaO质量分数约为0.01%-0.02%。
过低不利于防止氰化物水解,过高尽管能促使带负电荷的硅泥絮凝,有利于矿浆沉淀和液体净化,但对金的浸出速度有明显的不利影响。
用石灰作保护碱时,最好以石灰乳的形式加入,有利于过程的控制。
2.固液分离
矿石经氰化浸出后,产出由含金溶液和尾矿组成的矿浆。
为了使含金溶液与固体尾矿分离,需进行洗涤和过滤。
通常使用的分离流程包括:氰化矿浆的浓缩、过滤,再用脱金贫液或水在过滤机上洗涤滤渣后将含金较低的固体,即尾矿废弃或再处理,而将含金溶液用于金的置换沉淀。
在固液分离时,要加入洗涤水,洗涤水一般用置换作业排放的贫液或清水。
当处理的矿石中有害氰化的杂质较少时,可采用贫液全部返回到浸出作业的流程中,此时一般使用清水作为洗涤水,这样既可提高洗涤效率,又可使氰化尾矿溶液中氰化钠浓度降低,减少氰化钠的损失,简化污水处理作业。
当处理的矿石中有害氰化的杂质较多时,贫液一般不返回浸出流程中去,而使用部分贫液作洗涤水;此时如使用清水作为洗涤水,虽然洗涤效率有所提高,但因贫液排放量增加,使贫液中金的损失量增大,降低了总置换率,增加氰化物消耗量,并使污水处理量和成本增高。
目前洗涤方法有多种,从矿浆中分离含金溶液和尾矿的洗涤方法有倾析洗涤法、过滤洗涤法和流态化洗涤法等。
在生产实践中,选择什么样的洗涤方法和洗涤设备,是关系到能否提高洗涤效率及降低生产成本的关键
1)倾析洗涤法
倾析洗涤法广泛使用于北美,它可以分为间歇倾析洗涤法和连续倾析洗涤法。
①间歇倾析洗涤法。
间歇倾析洗涤法通常与间歇搅拌氰化配合使用。
它的作业方法之一是氰化矿浆于澄清槽中澄清后,用带有浮子的虹吸管抽出上层含金澄清液送置换回收金,余下的浓浆抽回搅拌浸出槽加NaCN稀溶液再次进行浸出。
方法之二是将氰化矿浆给入浓密
机中浓缩,溢流产出的含金溶液送置换金,浓密机中的浓浆抽至搅拌浸出槽加NaCN稀溶液再次进行浸出。
然后将二次浸出的矿浆送澄清槽或浓密机再处理。
如此反复几次,直至洗液中含金达微量为止。
第二次浸出作业产出的含金溶液,通常含金较少,可用作下批原料的一次浸出用,第三次浸出液用作下批原料的二次浸出用,这些溶液经不断使用,直至含金达规定浓度后送沉淀金。
浓密洗涤就是采用浓密机对浸出矿浆进行洗涤的过程,将浸出矿浆或待洗矿浆在给人浓密机的同时,用大量的洗水冲稀洗涤,固体颗粒在浓密机内自行沉降。
浓缩后的矿浆耙到排矿口随底流排走(或排到下台浓密机再次洗涤),上部清液中的已溶金随溢流进人金的沉淀工序而被回收,或作为上一级的洗涤水。
目前国内外氰化厂用于洗涤的浓密机种类较多,若按浓密机的层数可分为单层和多层;若按传动方式又可分为中心传动式和周边传动式。
近年来,国内还引进和仿制了一种新型浓密机,即高效浓密机。
无论脱水或洗涤,高效浓密机的效果都要比同规格的单层浓密机高出2-3倍。
如果加絮凝剂之后,其效果要高出5倍以上。
无论选用什么类型的浓密机,只要用于洗涤,就很少用单层单台,一般都是多台单层串联或多层浓密机组成的多级逆流洗涤。
间歇倾析洗涤法由于作业过程时间长,所用溶液数量多,设备占地面积大等缺点,在工业上应用很少。
②连续倾析洗涤法。
连续倾析洗涤法是国内外广泛使用的方法之一。
它是以矿浆和洗液呈逆向运动的原理进行的,在国外称连续逆流倾析洗涤法。
此法是将矿浆和洗(贫)液从相对的方向供入浓密机中并对流进入一级浓密机,以实现矿浆的洗涤和固液分离。
故浓密机是连续逆流倾析作业的主要设备。
为此,国外已使用的最大浓缩机直径达150-180m。
使用
的浓密机有单层的和多层的。