转炉除尘风机在线监测及故障诊断系统
风机状态监测与故障诊断

内燃机
阀或发射器故障, 散热管或油冷却器故障. 热
量分布过高的散热器进口/出口温度
重型设备 - 轮胎,轴承,刹车,液压,窑,
球蘑机,造纸机
刹车过热, 疲劳, 轴承, 滑轮, 齿轮, 齿轮或
滑轮未对中, 和液压系统阻塞
机械式涡轮驱动和小型涡轮发电单元,燃气
涡轮, 排气管道
高的润滑油温度, 高的轴承温度, 故障停机/
什么是状态监测与故障诊断?
故障是指机械设备丧失了原来所规定
的性能和状态。通常把机械设备在运
行中所发生的状态异常、缺陷、性能
恶化、以及事故前期的状态统统称为
故障,有时也把事故直接归为故障。
什么是状态监测与故障诊断?
状态监测是指通过一定的途径了解和掌握设
备的运行状态,包括利用监测与分析仪器
设备(定时的或非定时的,在线的或离线
各种电气设施;
电气开关、插头、插座、电工元器件
电气照明及装置
中央空调电气设施、电梯电气设施
控制电器和保护电器装置、接地装置
各种消防设备、设施的电气部分
电气系统预测性维护-外部故障
电力系统运行中,载流导体会因为电流效应产生电
阻损耗,而在电能输送的整个回路上存在数量繁多的连接
件、接头或触头。在理想情况下,输电回路中的各种连接
1.线路接头接触不良或氧化腐蚀
2.整体质量较差:线圈匝数不足、绝缘能力不够、线径过小、
铁芯面积过小、空间间隙太大、硅钢片插得不紧等等
3.供电网络问题。过载、谐波都会造成整流器内部温度过高
电气接头
电机控制中心
电气室
相不平衡
红外诊断的方法
表面温度判断法(参考国标)
相对温差判断法
风电场有功与无功功率控制的在线监测与故障诊断

风电场有功与无功功率控制的在线监测与故障诊断风电场是利用风能转化成电能的设施,其在能源产业中扮演着重要的角色。
然而,由于天气等自然因素的影响,风电场在实际运行中常常出现功率控制与故障诊断方面的问题。
为了确保风电场的有效运营和可靠性,需要进行在线监测与故障诊断。
风电场的功率控制主要包括有功功率和无功功率的控制。
有功功率是指风电机组通过转动风轮产生的机械能转化为电能的能力,而无功功率是指风电机组对电力系统的无效功率提供能力。
在线监测与故障诊断系统主要用于实时监测风电场的功率输出情况,并及时发现和诊断潜在的故障问题。
在线监测系统通过安装传感器和数据采集设备来获取风电场的关键参数,如风速、转速、电流、电压等。
这些参数可以反映风电场的运行状况和发电能力。
监测系统将实时采集的数据传输给中央控制室,并进行数据分析和处理,以便及时发现异常状况和故障。
在风电场的有功功率控制方面,在线监测系统可以通过监测风速和转速等关键参数来实时计算风电机组的有功功率输出。
通过分析这些数据,系统可以了解风电场的实时功率输出情况,并与预期功率进行比较。
如果功率输出异常,系统将发出警报,并通知操作人员进行处理。
这可以帮助风电场及时发现潜在的故障问题,确保功率输出稳定和高效。
在风电场的无功功率控制方面,在线监测系统可以监测风电机组的电流和电压参数,并实时计算无功功率。
通过分析电流和电压的波形和相位关系,系统可以评估风电机组对电力系统的无功功率支撑能力。
这样,系统可以检测到风电场无功功率异常,例如过低或过高的无功功率输出,以及电力系统的电压波动等。
通过及时诊断无功功率方面的问题,风电场可以避免对电力系统稳定性造成不利影响,并减少相关故障的发生。
故障诊断是在线监测系统的重要功能之一。
通过收集大量的风电场运行数据并进行分析,系统可以辨识故障的发生位置和类型。
例如,系统可以检测到风电机组闪变、偏位故障以及传动链路断裂等问题。
当故障发生时,系统会通过报警和通知操作人员,以便他们及时采取措施进行修复或维护。
基于可靠性的状态监控预知系统——转炉风机在线监测及诊断系统技术方案

振动传感器、 垂直方向安装 1 个振动传感器、 轴向安装 1 个振动传感器。 2 . 2电机本体安装 2 个冲击脉冲传感器: 两个轴承位各安装 1 个冲 击 脉冲传感器 。 2 . 3电机和风机 之 间安装 1 个转速 传感器 。 2 . 4电机控制柜上: 控制柜上电机电流y g -  ̄ - 接人 V C N。 3风机在线监 测系统功能 要求 3 . 1按照设备状态在线监测和故障诊断的需求 , 风机上实施在线监 测, 并 具有故 障诊断和故 障报警功 能 。 3 . 2利用传感器捕捉振动、 冲击脉冲、 转速 、 电流信号 ; 进行信号处 理、 模式识 别 、 预报 决策 , 及 计算机 技术 , 监测 机组 在运行 过程 中的振 动 参数及 有关 l 生 能参数 及其 动态变化 , 在机组运 行过程 中, 做 出是否 有故 障、 故障种类 、 故障部位 、 故障严重程度、 故障发展变化趋势等诊断结果 , 判断机 组性 能劣化 趋势 。 3 . 3通过振动准确监测风机系统的不平衡、 不对中、 松动等问题。 3 . 4通过冲击脉冲准确监测风机系统的轴承问题 , 做到准确预知与 诊断 。 3 . 5通过电机电流信号的监测 , 反映风机载荷的变化 , 提高系统诊
断 的准确性 。 4主要 系统硬件 的技术条件 4 . 1振动 监测 模块 ( v c M - 2 o ) 。V C M - 2 0是 连 续测 量单元 , 供 采用
1 . 2 . 3根据设 备的多棒 性, 有 时设备总体 振动不大 , 但 是短 时工作后 便 造成事故停 机现象 , “ E V A M ”根据 3 0多项参数 的趋势 变化可 以捕捉 设 备的故障原 因 , 并 报警提示 。 1 . 2 . 4根据设 备的基本参 数和正常状 态下 的参 量 ,形成适合 该设备 的企 业标准 , 从而 为设备后期更 准确判 断设备运行 状态 。 1 . 3轴承监测——冲击脉冲技术 冲击脉冲技术简单易用 , 只须在轴承座上安装冲击脉冲传感器 , 系 统会直接给出轴承运转状态值及国际标准的“ 绿、 黄、 红” 状态指示。 该技术的优势是其独特设计的冲击脉冲传感器, 仅对轴承运转、 齿 轮啮合时产生的瞬态冲击做出反应 ,而对其它低频振动的干扰不作反 应, 因此可以得到纯净的早期信号。对冲击脉冲信号进行频谱分析 , 即 专利 的 S P M S p e c t r u m T M, 具有其 它常规 带通滤 波 、 包络技 术无法 比拟 的优势 , 可得 到极为清 晰的频谱 图。 1 4通过企 业 内部 网络实现 网络共享 , - 同时支 持 5 个用 户 同时上 网 查看设备 目前 的工作 状况 。 1 _ 5系统内置 的 T I J T自检功能 , 自 动监 测 网络 系统的连接 质量和硬 件品质 , 保证采集数据的真实可靠。 l I 6本 系统 自 成 体系 , 不受 网络系统 的故 障干扰 。 1 . 7本 系统可 以同时接 收在线或离 线便携 式数采 器的数 据 , 进入 系 统 进行统一管 理。 1 . 8可以按企业内部的设备统一编号或 自己编排 的编号 ( 任意) 编
风机在线振动检测与故障诊断系统.

风机在线振动检测与故障诊断系统说明书中国华电南京农网城网工程有限公司2007.61、项目设计遵循标准及规范振动状态监测部分参照GB/T 19873.1-2005/ISO 13373-1:2002《机器状态监测与诊断振动状态监测》;有关电气装置的实施参照GB50255-96《电气装置安装工程施工及验收规范》;有关自动化仪表实施参照GB50093-2002《自动化仪表工程施工及验收规范》及DLJ 279-90《电力建设施工及验收技术规范》(热工仪表及控制装置篇);其余部分参照中国华电南京农网城网工程有限公司企业标准。
1.1 系统目标基于对钢铁企业现状的了解,并结合对未来在线监测系统的期望,我们拟订如下系统目标:1、实时监测以机组结构示意图、棒图、数据表格等方式实时显示所监测的数据和状态,并以不同颜色进行声光报警显示。
2、趋势分析对采集到的振动、轴位移等参数进行趋势分析,能根据标准值的限定范围实现劣化分析,并结合标准信息提供设备检修指导,同时劣化曲线应能导出成电子文档或图表形式。
3、振动分析包括时域分析(波形、幅值)、相关分析(自相关分析、互相关分析)、频谱分析(频谱、相位)、矢谱分析、矢功率谱分析、进动谱分析、全信息分析、轴心位置(稳态)、倒谱分析、时频分析等。
4、数据库管理系统能自动生成各种数据库,包括历史(分钟、小时、天、月、年)、启停机、报警、事件及特征数据库等,并能自动进行维护,对过期数据自动清理,对特殊数据进行保护和备份。
5、黑匣子功能系统设有黑匣子数据库,能追忆和分析报警前后有关的详细数据。
6、故障诊断能诊断机组的常见故障,包括不平衡、不对中、基础松动、油膜涡动、转子碰摩等十六种常见故障。
7、报表打印8、网络通讯公司及分厂的有关领导和技术人员都可以通过浏览器随时查看机组的运行状态和进行各种分析、诊断。
可与现场智能仪表、DCS系统和MIS系统通讯。
1.2 故障诊断的目的●确定机器继续运行的时间。
风机状态监测与故障诊断系统

逼混传碰 赘体友易 最小二乘法 神经网络
故障 诊断 中 图 分 类 号 碰 场渲 染近者念 床 轮
风电变流器的在线监测与故障诊断方法
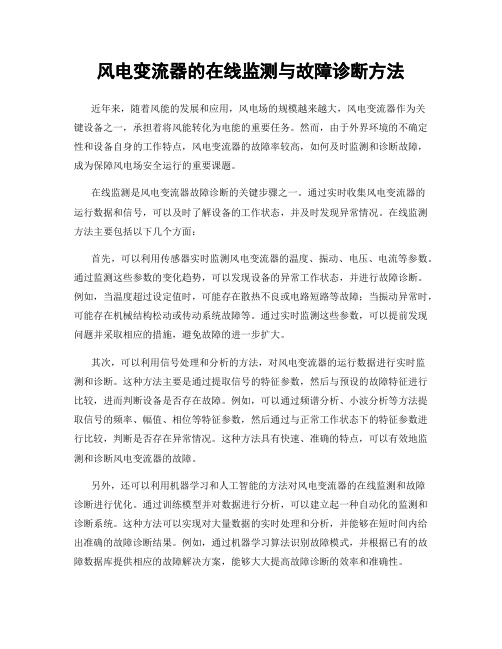
风电变流器的在线监测与故障诊断方法近年来,随着风能的发展和应用,风电场的规模越来越大,风电变流器作为关键设备之一,承担着将风能转化为电能的重要任务。
然而,由于外界环境的不确定性和设备自身的工作特点,风电变流器的故障率较高,如何及时监测和诊断故障,成为保障风电场安全运行的重要课题。
在线监测是风电变流器故障诊断的关键步骤之一。
通过实时收集风电变流器的运行数据和信号,可以及时了解设备的工作状态,并及时发现异常情况。
在线监测方法主要包括以下几个方面:首先,可以利用传感器实时监测风电变流器的温度、振动、电压、电流等参数。
通过监测这些参数的变化趋势,可以发现设备的异常工作状态,并进行故障诊断。
例如,当温度超过设定值时,可能存在散热不良或电路短路等故障;当振动异常时,可能存在机械结构松动或传动系统故障等。
通过实时监测这些参数,可以提前发现问题并采取相应的措施,避免故障的进一步扩大。
其次,可以利用信号处理和分析的方法,对风电变流器的运行数据进行实时监测和诊断。
这种方法主要是通过提取信号的特征参数,然后与预设的故障特征进行比较,进而判断设备是否存在故障。
例如,可以通过频谱分析、小波分析等方法提取信号的频率、幅值、相位等特征参数,然后通过与正常工作状态下的特征参数进行比较,判断是否存在异常情况。
这种方法具有快速、准确的特点,可以有效地监测和诊断风电变流器的故障。
另外,还可以利用机器学习和人工智能的方法对风电变流器的在线监测和故障诊断进行优化。
通过训练模型并对数据进行分析,可以建立起一种自动化的监测和诊断系统。
这种方法可以实现对大量数据的实时处理和分析,并能够在短时间内给出准确的故障诊断结果。
例如,通过机器学习算法识别故障模式,并根据已有的故障数据库提供相应的故障解决方案,能够大大提高故障诊断的效率和准确性。
针对风电变流器在线监测与故障诊断的方法,还需要注意以下几个问题:首先,数据采集和处理的可靠性是保证故障诊断准确性的基础。
除尘风机振动故障诊断与处理
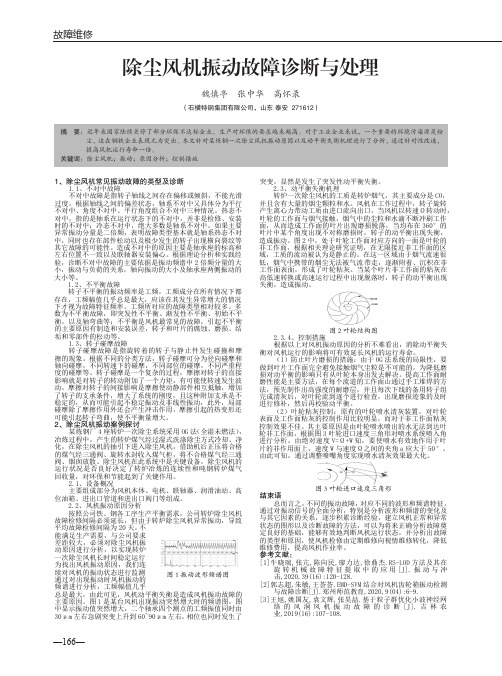
—166—故障维修摘..要:近年来国家陆续关停了部分环保不达标企业,生产对环保的要求越来越高。
对于工业企业来说,一个重要的环境污染源是粉尘,这在钢铁企业表现尤为突出。
本文针对某炼钢一次除尘风机振动原因以及动平衡失衡机理进行了分析,通过针对性改造,提高风机运行寿命一倍。
关键词:除尘风机;振动;原因分析;控制措施除尘风机振动故障诊断与处理魏慎亭 张中华 高怀录(石横特钢集团有限公司,山东 泰安 271612)1、除尘风机常见振动故障的类型及诊断1.1、不对中故障不对中故障是指转子轴线之间存在偏移或倾斜,不能光滑过度。
根据轴线之间的偏差状态,轴系不对中又具体分为平行不对中、角度不对中、平行角度组合不对中三种情况。
热态不对中,指的是轴系在运行状态下的不对中,并非是检修、安装时的不对中;冷态不对中,绝大多数是轴系不对中。
如果主要异常振动分量是二倍频,表明故障类型基本就是轴系热态不对中,同时也存在部件松动以及极少发生的转子出现横向裂纹等其它故障的可能性。
造成不对中的原因主要是轴承座的标高和左右位置不一致以及联轴器安装偏心。
根据理论分析和实践经验,诊断不对中故障的主要依据是振动频谱中2倍频分量的大小,振动与负荷的关系,轴向振动的大小及轴承座两侧振动的大小等。
1.2、不平衡故障转子不平衡的振动频率是工频,工频成分在所有情况下都存在,工频幅值几乎总是最大,应该在其发生异常增大的情况下才视为故障特征频率。
工频所对应的故障类型相对较多。
多数为不平衡故障,即突发性不平衡、渐发性不平衡、初始不平衡,以及轴弯曲等;不平衡是风机最常见的故障,引起不平衡的主要原因有制造和安装误差,转子和叶片的腐蚀、磨损、结垢和零部件的松动等。
1.3、转子碰摩故障转子碰摩故障是指旋转着的转子与静止件发生碰撞和摩擦的现象。
根据不同的分类方法,转子碰摩可分为径向碰摩和轴向碰摩,不同转速下的碰摩,不同部位的碰摩,不同严重程度的碰摩等。
转子碰摩是一个复杂的过程,摩擦对转子的直接影响就是对转子的转动附加了一个力矩,有可能使转速发生波动。
主通风机在线监测与故障诊断系统方案(修改)
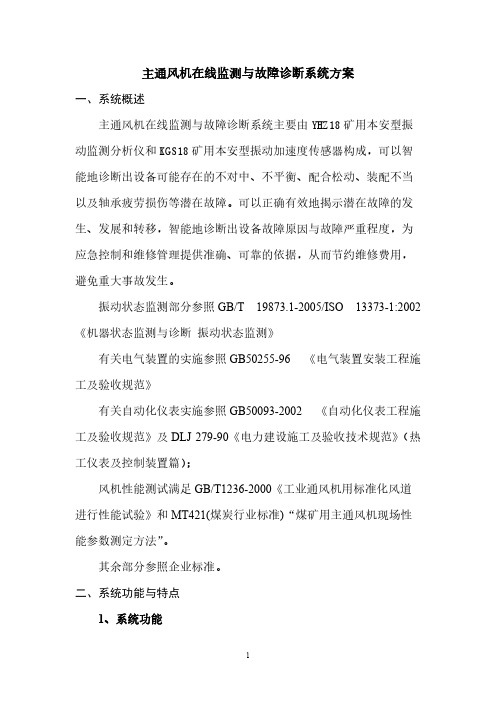
主通风机在线监测与故障诊断系统方案一、系统概述主通风机在线监测与故障诊断系统主要由YHZ18矿用本安型振动监测分析仪和KGS18矿用本安型振动加速度传感器构成,可以智能地诊断出设备可能存在的不对中、不平衡、配合松动、装配不当以及轴承疲劳损伤等潜在故障。
可以正确有效地揭示潜在故障的发生、发展和转移,智能地诊断出设备故障原因与故障严重程度,为应急控制和维修管理提供准确、可靠的依据,从而节约维修费用,避免重大事故发生。
振动状态监测部分参照GB/T 19873.1-2005/ISO 13373-1:2002 《机器状态监测与诊断振动状态监测》有关电气装置的实施参照GB50255-96 《电气装置安装工程施工及验收规范》有关自动化仪表实施参照GB50093-2002 《自动化仪表工程施工及验收规范》及DLJ 279-90《电力建设施工及验收技术规范》(热工仪表及控制装置篇);风机性能测试满足GB/T1236-2000《工业通风机用标准化风道进行性能试验》和MT421(煤炭行业标准)“煤矿用主通风机现场性能参数测定方法”。
其余部分参照企业标准。
二、系统功能与特点1、系统功能系统主要由在线监测、轴承实时诊断与状态预报、离线数据分析三部分组成。
(1)在线监测功能①在线监测通风机所在地点的环境大气参数,包括大气压力、大气温度、和大气湿度。
②在线监测通风机的流量、风压、轴功率、效率、振动等工况状态参数。
③在线监测电气设备的电气参数,包括电流、电压、功率因数,开关状态及系统保护信息。
④当运行中的通风机设备性能出现异常时,系统按照不同的故障类型,依据用户设定的模式进行提示、报警。
系统能够对于温度、振动等关键参数给出预警。
系统对各种故障点具有记忆功能,以对故障的分析提供帮助。
⑤系统具有运行状态实时数据显示、历史纪录查询、特性曲线或工况参数列表显示、报表打印及网络通讯传输等功能。
⑥系统与矿集中控制系统留有通讯接口,可接入矿局域网,在中央控制室内可实施对通风机设备的远程监测。
风机在线监测监控与故障诊断系统--设备自我诊断的分析

风机在线监测监控与故障诊断系统--设备自我诊断的分析随着矿山系统的内容及设备型式及数量规模越来越大,产品种类越来越多,所涉及的设备越来越复杂时,设备在运行中突然出现故障或问题的机会就越高,且若问题发生时单靠人为方式,一个一个的去检测排除,不仅费力耗时,也不一定能够实时准确发现设备异常和故障所在及原因。
这对监控系统在运行维护中造成了新的困难,进而会影响整个系统的正常运作。
实际上,监控系统中的设备在运行中都会由于主客观的环境因素而产生问题或故障,主观环境即自身状态,如存储空间不足等,以及设备由于受到电的、热的、机械的负荷作用,以及自然环境(气温、气压、湿度以及污秽等)的影响,长期工作引起的老化、疲劳、磨损,以致可靠性逐渐降低,出现异常。
设备运行状态出现问题和故障,客观环境如断电、断网、网络带宽等,因此必须对这些设备的运行状态进行必要的监测。
过去传统的检测方法是经常性的人工巡视、定期预防性检修,出现异常时只能逐个排查。
设备在运行中由值班人员巡视,凭外观现象、指示仪表等进行判断,发现可能的异常;此外定期对设备实行停止运行的例行检查,做预防性绝缘试验和机械动作试验,对结构缺陷及时作出处理等。
这种人工巡视只能作为平日设备的保养和预防,一旦设备出现问题,则会耗费大量的人力物力,特别是大型监控项目。
徐州中测电子成功研制开发的矿井主通风机性能在线监测监控与故障诊断系统,综合利用现代传感技术、微电子技术、自动控制技术、计算机技术、网络通讯技术,基于企业计算机网络实现主风机运行参数、通风数据的实时监测与风机主辅设备控制的一体化,监测内容丰富,控制功能完善,具有实时性强、安全可靠、操作方便、易学易用的特点。
随着传感技术与计算机技术的发展,监控状态监测方法向着自动化、智能化的方向发展,既不影响系统正常的运行,又能直接反映运行中的设备状态,有效、及时和可靠。
前端传感器设备运行状态监控系统服务器,大多是厂商自主研发的对监控系统的工作状态进行检测和监控的新型特色设备,是对监控系统的所有嵌入式设备进行工作状态监测的“智慧管家”。
转炉除尘风机在线监测及故障诊断系统

基于可靠性的状态监控预知系统------风机在线监测及诊断系统技术方案一、概况:监控设备:对于炼钢厂转炉风机,实施在线状态监测,精确了解设备运行状态,实施有计划的预知维修,同时根据运行状态与根源分析,进一步提高设备运行的可靠性,为合理安排设备维修和优化备件提供有力保障;实施目标:该系统通过建立关键设备在线监测体系,实时监控设备振动参量状态,及时报警,防止重大设备事故的发生;同时采用最先进的监控技术,最大程度延长设备的预警时间,从而实现预知维修,并通过智能的专家诊断,精确诊断故障源,实现精密维修,缩短维修用时,为检测维修制度合理化提供准确的数据基础;二、项目意义利用传感器捕捉振动、冲击脉冲、转速、电流信号;进行信号处理、模式识别、预报决策,及计算机技术,监测机组在运行过程中的振动参数及有关性能参数及其动态变化,在机组运行过程中,作出是否有故障、故障种类、故障部位、故障严重程度、故障发展变化趋势等诊断结果,判断机组性能劣化趋势;使运行、维护、管理人员能在维修之前做好有关准备,做到预知维修,并可根据监测诊断结果,进行技术改造,避免类似事故再次发生;实施本项目的意义在于:1、通过本项目实现对机组的连续在线监测和劣化趋势预测达到预知维修的目的,以保证无故障运行;2、利用监测诊断系统可以及时判别设备是否有故障,并且能够迅速查明故障原因、部位、预测故障影响;从而实现有针对性的按状态维修,那里坏了修那里,而不是大拆大卸,延长检修周期,缩短检修时间,提高检修质量,减少备件储备,提高设备的维修管理水平;3、向运行人员提供及时的信息,有效地支援运行,提高设备使用的合理性、运行的安全性和经济性,充分挖掘设备潜力,延长服役期限,以便尽量合理地使用设备;从而降低设备故障停机时间,减少计划检修时间和非计划检修时间;4、向维修管理人员及时提供设备运行情况,及时准备备品备件,及时处理有关故障,真正实现预知维修,以最少的代价发挥设备最佳的效益,做到最佳运行,使设备维修费用、设备性能劣化与停机损失费用最低;根据监测诊断结果确定维修时间、维修部位和维修方法,并根据诊断结果进行技术改造,可以降低设备故障停机时间,减少计划检修时间和非计划检修时间;提高开工率,增加产品产量,减少同类事故发生的次数;三、CMS在线监测系统功能说明:系统功能:1)本系统为瑞典SPM公司着名的CMS网络监控系统,在世界范围内拥有40年的历史,更为ABB、西门子、英格索兰、西马克、阿尔斯通等着名设备制造商应用,进行产品出厂配套或进行出厂质量校核;2) 全中文操作界面,提供WINDOWS 窗口形式和树状结构形式两种操作方式,真正做到会使用计算机就能操作软件;3) 在线监控设备振动指标,长期趋势监控,智能型“绿、黄、红”报警指示;4) 通过专利的“EVAM ”专利技术,实现:① 智能诊断故障原因,对位移、加速度、速度、歪度、峭度、4个等级摩擦量以及不平衡、不对中、松动、轴承故障、转子断条等30多项参数与征兆独立评估,分别给出“绿、黄、红”状态指示,实现智能专家诊断;② 针对设备工况的复杂性,对于变速设备、载荷变化较大的设备,可根据转速和载荷的变化量预先设定设备不同工况下的不同标准;③ 根据设备的多样性,有时设备总体振动不大,但是短时工作后便造成事故停机现象,“EVAM ”根据30多项参数的趋势变化可以捕捉设备的故障原因,并报警提示;④ 根据设备的基本参数和正常状态下的参量,形成适合该设备的企业标准,从而为设备后期更准确判断设备运行状态;⑤ 内置的“专家系统”和庞大的轴承库,方便具有一定专业知识、习惯用频谱来分析设备故障的管理人员来判断如不平衡、不对中、松动、轴承故障、转子断条等等故障;5) 轴承监测 —— 冲击脉冲技术① 振动监测解决不了早期预警问题已是世界公认的事实,原因是轴承早期的问题如润滑不良,点蚀等所产生的是较弱的瞬态信号,常规振动传感器及振动分析方法根本无法捕捉得到;如下图实例中,振动未报警,但轴承冲击脉冲峰值LR 已远远超出报警值,损伤程度值COND 逐渐加大,说明轴承已经失效,继续运行将导致严重隐患;② “冲击脉冲技术”是完全不同于振动监测的技术,该技术已服务世界各国30多年,被公认为是解决滚动轴承、齿轮问题的最佳途径,因此应用极为广泛,仅在中国就已成功应用于上千家企业;绝大多数世界知名设备制造商,如ABB 、英格索兰、苏尔寿、GE,都已在其设备出厂前安装冲击脉冲传感器,或使用该技术进行出厂检验;为数众多的进口石化挤出机、造纸机、船用发动机的齿轮箱上,已经安装了冲击脉冲监测保护系统;③该技术简单易用,只须在轴承座上安装冲击脉冲传感器,系统会直接给出轴承运转状态值及国际标准的“绿、黄、红”状态指示,同时给出:专利的LR/HR 技术,给出强冲击与平均冲击指标;状态代码CodeA 为最佳,B 为干磨擦,C 为轻度损伤,D 为严重损伤;润滑状态代码LUB 油膜厚度:0,1,2,3,4…;损伤程度值Cond<30为轻度,30-40为中度,>40为重度;它包括一个庞大而丰富的轴承库,以及专利的 LUBMASTER 轴承润滑寿命分析模块;见下图④ 冲击脉冲技术的优势是其独特设计的冲击脉冲传感器,仅对轴承运转、齿轮啮合时产生的瞬态冲击做出反应,而对其它低频振动的干扰不作反应,因此可以得到纯净的早期信号;对冲击脉冲信号进行频谱分析,即专利的SPM Spectrum TM,具有其它常规带通滤波、包络技术无法比拟的优势,可得到极为清晰的频谱图;6) 通过企业内部网络实现网络共享,同时支持5个用户同时上网查看设备目前的工作状况; 轴承状态冲击脉冲LR/HR损伤程度COND 润滑指标LUB 水平振动VIB7)系统内置的TLT自检功能,自动监测网络系统的连接质量和硬件品质,保证采集数据的真实可靠;8)本系统自成体系,不受网络系统的故障干扰;9)本系统可以同时接收在线或离线便携式数采器的数据,进入系统进行统一管理;10)可以按企业内部的设备统一编号或自己编排的编号任意编辑测点名,方便查找;11)可以根据管理人员的职责范围来设定管理权限,真正做到职责分明;12)对于问题设备或检修过设备处理的过程、方法和结论可在当时的测定数据中加以注解,便于将来查阅、参考和制定恰当的处理方案;13)本系统采用WINDOWS自带的SQL SERVER 数据库,可以利用SQL SERVER 数据库自身的软件进行备份,也可以在客户端自行备份数据;14)数据可与企业EAM或ERP体系实现数据共享;15)本系统采用模块化的方式,可以根据用户的需求扩展功能,如:脉冲技术、油膜分析功能等更深层次的分析功能;16)可以通过网络系统,输入软件序列号,在互联网上免费升级软件;实施方法:1)安装振动传感器,监控设备的振动变化;2)安装冲击脉冲传感器,监控轴承的冲击变化和润滑的状况;3)安装转速传感器,实现转速监控,并实现变速设备智能诊断;4)通过现场监测单元多通道信号处理,将数据通过企业互联网传输;5)服务器运行监控软件与数据库,客户端实现有权限地数据共享与诊断分析;五、在线系统结VCM+BMU1、结构图2、风机测点分布测点说明如下:风机本体安装3个振动传感器:风机本体轴承位水平安装1个振动传感器、垂直方向安装1个振动传感器、轴向安装1个振动传感器,;电机本体安装2个冲击脉冲传感器:两个轴承位各安装1个冲击脉冲传感器;电机和风机之间安装1个转速传感器;电机控制柜上:控制柜上电机电流信号接入VCM;一、风机在线监测系统功能要求;1、按照设备状态在线监测和故障诊断的需求,风机上实施在线监测,并具有故障诊断和故障报警功能;2、利用传感器捕捉振动、冲击脉冲、转速、电流信号;进行信号处理、模式识别、预报决策,及计算机技术,监测机组在运行过程中的振动参数及有关性能参数及其动态变化,在机组运行过程中,做出是否有故障、故障种类、故障部位、故障严重程度、故障发展变化趋势等诊断结果,判断机组性能劣化趋势;3、通过振动准确监测风机系统的不平衡、不对中、松动等问题;4、通过冲击脉冲准确监测风机系统的轴承问题,做到准确预知与诊断;5、通过电机电流信号的监测,反映风机载荷的变化,提高系统诊断的准确性;6、有关诊断分析软件中能实现不同岗位人员的权限设定,并能在局域网内实现数据共享,以便提高各级专业人员利用系统及时了解所监测设备的能力和水平,以便提高此类重要设备管理的效率;二、主要系统硬件的技术条件1、振动监测模块VCM-20VCM-20 是连续测量单元,供采用 EVAM 专家方法进行振动分析;单元内部配有 CPU、硬盘和多路复用测量逻辑模块;VCM-20-8 配有 8个振动测量通道,8 个 RPM 测量通道;可插接4-20mA模拟量输入板,可扩充8-16通道模拟量,监控温度、压力等,也可通过负载电流监控,实现变载分析;VCM-20 可通过以太网与安装 Condmaster Nova 软件的计算机连接;测量设定值在软件中设置;通信程序 DBL 向 VCM-20 单元传送测量设定值,并读取这个单元的结果文件;处理器: 1GHz存储器: 256 Mb RAM硬盘容量: > 20 Gb通道:振动20,转速 8频率范围: 0 –20KHz包络频率: 100, 200, 500, 1000, 2000, 5000, 10 000 Hz检测窗口:矩形、汉宁、海明等分辩线数: 200, 400, 800, 1600, 3200, 64002、轴承监测模块BMU-07BMU-07配有7个测量滚动轴承冲击脉冲通道,与测量单元 VCM20连接,根据 VCM20的请求进行测量、传输数据;BMU 提供冲击振幅值和包络冲击脉冲信号,用于频谱分析;VCM20单元测量轴承转速,计算 SPM 频谱,评估轴承工作状态;测量条件在 Condmaster Nova 中设置,包括冲击脉冲方法、频谱类型、用于识别轴承故障的征兆及告警极限等;测量方法:冲击脉冲 LR/HR, 和 SPM 频谱测量范围: -19 到99 dBsv LR/HR测量通道: 7电源: 5 V DC ±10%温度范围: -10°到60° C尺寸: 139 x 145 x 46 mm3、冲击脉冲传感器42000测量范围:最大值100 dBsv机架基础:不锈钢SS 2382设计:密封温度范围:-30到+150° C外部压力:最大1 MPa 10 bar 扭矩:15 Nm, 最大20 Nm4、振动传感器SLD144B灵敏度:100 mV/m/s2,精度:1%工作环境温度:-50~125℃频率范围:~10KHz适用公制M8内螺纹孔,传感器垂直输出传输距离:400米以内。
转炉风机的故障诊断

状态监测与诊断 技术
中 闲彀给z o. 程22 o8
转 炉 风 机 的 故 障 诊 断
■ 陈 茂 华
【 摘 要 】结 合 现 场 实 际 ,运 用 大量 的 统 计 数 据 , 分析 转 炉 风 机 的 故 障 现 象 ,列 举 了一 些 经 故 障诊
断 实践 证 明 的 成 功 措 施 和 手 段 。
电 机 :J 0 —2,n 2 9 0 / n.P 5 0 W K5 0 = 7 r mi - = 0k
5 H、 6 H、2 V、5 V、6 分 别 为 初 始 值 的 4 1倍 、 32 V . . 倍 、49倍 、46倍 、32倍 、29倍 和 34倍 。 . . . . .
其 中 ,① 、⑤ 、⑥ 点 的水平 径 向振 动值 明显 增
【 关键词 】故 障诊 断技 术
1 通 过 振 动 分 析 判 断 设 备 基 础 松 动 故 障 . 我 公 司 西 洲 水 厂 的 罗 茨 风 机 ,型 号 及 基 本 参 数
为 , R 2 0, 3 0 E 5 8 V, 1 2 0 A, 5 k , 测 点 示 意 图 如 图 5W
准 ,处 于 带 病 工 作 状 态 。
虎 主 编 《 备 故 障 诊 断原 理 、技 术 及 应 用 》 表 24 , 设 中 .)
4月 2 日 的 测 值 均 小 于 28 7 .mm/ , 可 作 为 该 机 组 的 初 s 期值 。
40
D0 = 。
可匡 ⑤0 匡匡 ⑤ 啸0
维普资讯
加 , 比 初 始 值 高 4倍 以 上 , 已 处 于 危 险 区 , 很 可 能 是 叶轮不平衡所致 。 6 精 密 诊 断 .
旋 转 频 率 :4 .Hz 95
高炉风机轴振动在线监测与故障诊断系统的开题报告
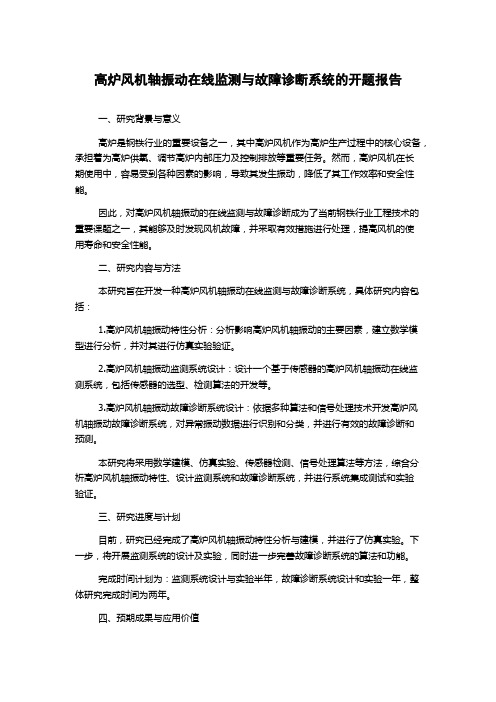
高炉风机轴振动在线监测与故障诊断系统的开题报告一、研究背景与意义高炉是钢铁行业的重要设备之一,其中高炉风机作为高炉生产过程中的核心设备,承担着为高炉供氧、调节高炉内部压力及控制排放等重要任务。
然而,高炉风机在长期使用中,容易受到各种因素的影响,导致其发生振动,降低了其工作效率和安全性能。
因此,对高炉风机轴振动的在线监测与故障诊断成为了当前钢铁行业工程技术的重要课题之一,其能够及时发现风机故障,并采取有效措施进行处理,提高风机的使用寿命和安全性能。
二、研究内容与方法本研究旨在开发一种高炉风机轴振动在线监测与故障诊断系统,具体研究内容包括:1.高炉风机轴振动特性分析:分析影响高炉风机轴振动的主要因素,建立数学模型进行分析,并对其进行仿真实验验证。
2.高炉风机轴振动监测系统设计:设计一个基于传感器的高炉风机轴振动在线监测系统,包括传感器的选型、检测算法的开发等。
3.高炉风机轴振动故障诊断系统设计:依据多种算法和信号处理技术开发高炉风机轴振动故障诊断系统,对异常振动数据进行识别和分类,并进行有效的故障诊断和预测。
本研究将采用数学建模、仿真实验、传感器检测、信号处理算法等方法,综合分析高炉风机轴振动特性、设计监测系统和故障诊断系统,并进行系统集成测试和实验验证。
三、研究进度与计划目前,研究已经完成了高炉风机轴振动特性分析与建模,并进行了仿真实验。
下一步,将开展监测系统的设计及实验,同时进一步完善故障诊断系统的算法和功能。
完成时间计划为:监测系统设计与实验半年,故障诊断系统设计和实验一年,整体研究完成时间为两年。
四、预期成果与应用价值本研究预计取得以下成果:1.高炉风机轴振动特性分析与建模研究成果。
2.基于传感器的高炉风机轴振动监测系统设计与实验成果。
3.基于多种算法和信号处理技术的高炉风机轴振动故障诊断系统设计与实验成果。
该研究成果可以为钢铁行业工程技术领域提供一个有效的高炉风机轴振动在线监测与故障诊断系统,增强了高炉风机的使用寿命和安全性能,提高了高炉生产效率和质量稳定性,有很大的应用价值和社会效益。
浅议风机状态监测与故障诊断

浅议风机状态监测与故障诊断【摘要】风机是我国对气体压缩和气体输送机械的习惯简称,是依靠输入的机械能,提高气体压力并排送气体的机械,它是一种从动的流体机械。
我国的企业中都在使用这种设备,因此风机的状态监测和故障诊断就成为了关系企业生产的重要环节。
本文以D350风机为例,来进行风机状态监测和故障诊断系统的相关介绍,将其设计思路和主要功能进行详述。
【关键词】旋转机械;状态监测;故障诊断;风机上个世界七十年代是计算机飞速发展的年代,随着计算机技术及其相关技术的快速发展,通过计算机来进行风机状态监测以及故障诊断技术开始得到了发展。
国外发达国家在这方面的水平要比我们先进很多,像是美国Bendy Nevada 公司的ADRE系统,Scientific—Atlanta公司的M6000系统等;我国最近几年在这方面也开始引起了重视,像是和一些高校以及研究所联合开展一些科研性的项目,自己开始研发监测和诊断系统,这些技术虽然和国际先进技术有差距,但是也没有以前那么大了。
本文以D350煤气排送机为例,进行风机状态监测和故障诊断系统的讲解,介绍其工作机制和一些技术方面的问题。
1、系统总体结构此系统是集合了许多功能的系统,例如数据收集、状态监测、振动分析、故障检查等等。
信号采集的时效性和准确性事确保监测和诊断系统是否精准的一个重要指标。
系统的结构是多个层次构成的,分为不同的子系统,状态监测子系统和故障诊断子系统并行工作。
为了提高系统可靠性,设计了仪表监测子系统和以计算机为中心的监测诊断子系统并行工作的系统。
其结构如图1所示。
2、传感器的选择与测点布置传感器负责收集和传递系统的往来信息。
因此传感器是否精确,决定着系统所收集到的信息以及对这些信息利用的可靠性。
相对于本系统而言,壳体振动选用压电式速度传感器。
这类传感器灵敏度高,安装方便,使用寿命长。
轴位移信号和键相信号采用电涡流传感器。
测量壳体振动一般测量3个方向的振动,即2个径向信号和1个轴向信号。
转炉一次除尘系统常见故障分析

转炉一次除尘系统常见故障分析1.1故障现象:炼钢时转炉炉口冒红烟,放散烟囱冒黑烟。
故障原因:风机转速低或机壳内积灰严重除尘系统管道积灰严重除尘水水温过高或流量低炉前下料溜槽氮封压力过高煤气回收系统管道积灰堵塞二次除尘系统停止运行处理措施:1.1.1提高风机转速,或清理机壳。
1.1.2清理除尘系统积灰。
1.1.3降低除尘水水温,调节水流量。
1.1.4调节炉前下料流槽氮封压力。
1.1.5清理煤气回收系统管道。
1.1.6运行二次除尘系统。
1.2 故障现象:一文水冷套异径管出现烧损、漏水故障原因:一文供水流量低供水管道堵塞一文水冷套异径管设计、安装不合格处理措施:1.2.1提高一文供水流量。
1.2.2疏通或更换供水管道。
1.2.3提高一文水冷套异径管设计、安装水平,保证材质、焊接质量。
1.3 故障现象:除尘风机无法正常工作故障原因:风机变频器出现故障风机转子振动强烈风机稀油站出现故障微机控制程序有故障高压配电室无法合闸。
处理措施:1.3.1处理变频器故障。
1.3.2切换备用风机,同时检修风机。
1.3.3处理风机稀油站。
1.3.4联系自动化部人员处理程序故障。
1.3.5检查处理配电室故障。
1.4故障现象:煤气回收或放散时,除尘风机机后三阀不工作。
故障原因:气源压力低汽缸出现故障换向阀出现故障电磁阀故障水封接近开关失效操作失误微机信号传输有误。
处理措施:1.4.1检查、调节气源压力。
1.4.2修复或更换汽缸。
1.4.3清理或更换换向阀。
1.4.4检修电磁阀。
1.4.5更换接近开关。
1.4.6加强炉前和风机房操作工操作水平和责任心。
1.4.7检查处理信号传输设备。
1.5故障现象:一次除尘系统供水压力低故障原因:供水泵运行故障管道堵塞或严重泄漏供水系统阀门阀板脱落处理措施:1.5.1维修除尘水供水泵。
1.5.2检查除尘水管道。
1.5.3检查更换供水阀。
(最新)煤矿大型机电设备在线监测与故障诊断系统

煤矿大型机电设备在线监测与故障诊断系统0背景介绍管好、用好煤矿大型关键设备,是煤矿稳产高产的前提,也是煤矿安全生产的保障,若能对设备进行状态监测与故障诊断,及时准确识别核心零部件故障的微弱特征信号,必将为潜在故障预示和演化、寿命预测和制定维修策略提供技术支持,从而提高煤矿关键装备整体运行安全性和可靠性,实现由“事后维修”到“预知维修”的转变,避免意外停机及恶性事故发生,具有巨大的经济效益和社会效益。
煤矿现行的设备维修方式基本上是通过维修工人凭直觉目测、敲击、触摸等手段判断,由于受人为因素的影响,其可靠性较差。
温度监测技术己广泛应用于煤矿设备状态监测,但设备在即将出现事故温度才会急剧上升,因此温度检测难以完成设备安全监测和早期预警的重任和及时报警的现场要求。
铁谱技术是现阶段煤矿行业设备状态监测与故障诊断常用技术,美国煤矿开展屑监测工作较早,然而,在应用铁谱分析技术属于离线监测,大多还是从设备现场采集油样,再在实验室制作谱片进行油液成分分析,分析周期相对较长,速度慢,降低了设备监测的实时性。
振动监测技术,利用振动信号对设备进行诊断,是设备故障诊断最常用、最有效的方法之一。
设备振动信号中包含了系统、零部件由于磨损、疲劳、老化等因素引起的劣化和失效等重要信息,通过对振动信号进行采集、分析和处理,可以监测设备的运行状态,识别机械设备的故障类型、故障来源,从而为设备的维修提供依据,以达到保障设备安全运行的目的。
设备在线监测诊断技术目的:1、概述传统的矿用机电设备在线监测系统仅仅局限于简单数据的采集与集中监测显示,这种方式虽然在设备运行状态监测中起到重要作用,但不能及时准确地诊断分析出机电设备可能出现的故障。
矿用机电设备在线监测与故障诊断系统主要由YHZ18矿用本安型振动监测分析仪和KGS18矿用本安型振动加速度传感器构成,可以智能地诊断出设备可能存在的不对中、不平衡、配合松动、装配不当以及轴承疲劳损伤等潜在故障,适用于煤矿通风机、皮带输送机、水泵等重要机电设备的运行状态监测与故障诊断分析。
风机远程振动监测与故障诊断系统
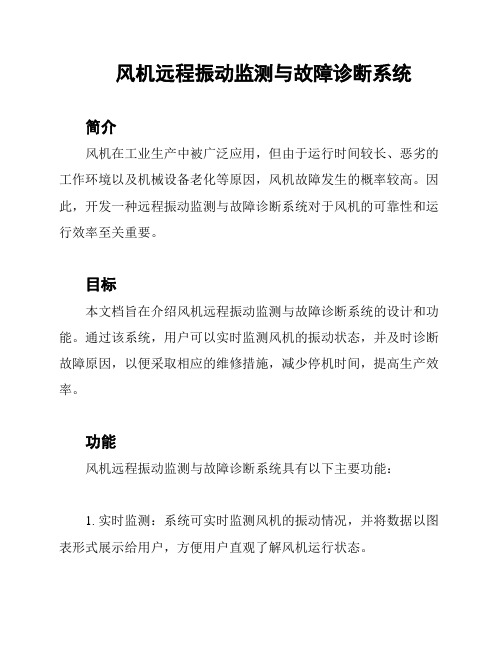
风机远程振动监测与故障诊断系统简介风机在工业生产中被广泛应用,但由于运行时间较长、恶劣的工作环境以及机械设备老化等原因,风机故障发生的概率较高。
因此,开发一种远程振动监测与故障诊断系统对于风机的可靠性和运行效率至关重要。
目标本文档旨在介绍风机远程振动监测与故障诊断系统的设计和功能。
通过该系统,用户可以实时监测风机的振动状态,并及时诊断故障原因,以便采取相应的维修措施,减少停机时间,提高生产效率。
功能风机远程振动监测与故障诊断系统具有以下主要功能:1. 实时监测:系统可实时监测风机的振动情况,并将数据以图表形式展示给用户,方便用户直观了解风机运行状态。
2. 数据分析:系统能对振动数据进行分析处理,检测振动频率、振动幅值等参数,从而诊断出可能存在的故障。
3. 故障诊断:基于振动数据的分析结果,系统能够自动诊断风机故障原因,为用户提供准确的故障诊断报告。
4. 历史记录:系统能够保存和管理风机振动数据的历史记录,方便用户进行数据对比和故障趋势分析。
5. 远程控制:用户可以通过系统远程监控和控制风机的运行状态,对故障进行处理或发出维修指令。
优势风机远程振动监测与故障诊断系统的优势在于:1. 实时性:用户可以随时随地通过系统监测风机振动情况,及时获取相关数据,做出迅速的决策。
2. 准确性:系统通过高精度的振动传感器和先进的数据处理算法,能够对风机故障进行准确诊断,避免人为误判。
3. 可远程控制:用户可以通过系统远程监控和控制风机的运行状态,无需现场操作,提高工作效率。
4. 维护成本低:系统能够提前发现潜在故障,及时采取维修措施,避免大量的停机时间和维修成本。
5. 数据分析能力强:系统具备强大的数据处理和分析能力,通过振动数据的分析,可以帮助用户更好地监测和管理风机运行情况。
总结风机远程振动监测与故障诊断系统通过实时监测和分析风机振动数据,能够帮助用户快速诊断风机故障,并采取对应的维修措施,提高风机的可靠性和运行效率。
四维度物联网式风机在线监测故障预警系统

四维度风机在线监测故障预警系统□国内外首创的多维度综合诊断专家预警系统□顺应潮流的物联网振动油液一体式采集分析监控方式□三级状态预警评价:极方便的整体控制和局部认知□有线和无线结合的传输方式:增强的兼容性和稳定性1、风电行业趋势:安全运行按需维护是趋势 (3)2、预警技术趋势:单一维度诊断分析存在缺陷....................................... 错误!未定义书签。
3、四维度综合诊断专家预警系统:全方位立体诊断............................... 错误!未定义书签。
3.1、三级状况评价系统:风机从整体到细微一目了然.................... 错误!未定义书签。
3.1.1、服务器端应用..................................................................... 错误!未定义书签。
3.1.2、网页方式应用..................................................................... 错误!未定义书签。
3.2、早期预警:油液监测参量............................................................ 错误!未定义书签。
3.3、中期预警:振动监测参量............................................................ 错误!未定义书签。
3.4、晚期预警:红外监测参量............................................................ 错误!未定义书签。
3.5、趋势预警:效能监测参量............................................................ 错误!未定义书签。
回转窑风机远程监测及故障诊断系统

回转窑风机远程监测及故障诊断系统
杨波;段凤春
【期刊名称】《武钢技术》
【年(卷),期】2007(45)3
【摘要】根据回转窑风机运行的实际情况,对远程监测及故障诊断系统进行研究。
从测点及信息点布置,远程通信体系结构及接口设计,远程监测与故障诊断建模,网络数据库的建立及维护等方面进行深入研究。
实验及应用结果表明,该系统故障诊断率高,运行可靠。
【总页数】5页(P16-19)
【关键词】风机;监测;故障诊断
【作者】杨波;段凤春
【作者单位】武钢矿业公司乌龙泉矿
【正文语种】中文
【中图分类】TD464
【相关文献】
1.矿井主扇风机远程监测及故障诊断系统 [J], 孟凡丹;王柄燃;于文
2.矿井主扇风机远程监测及故障诊断系统 [J], 李朕;马晨峰;岳强;
3.基于Internet与风机故障诊断技术的机组远程监测及故障诊断系统综述 [J], 战阳;史清丽
4.矿井主扇风机远程监测及故障诊断系统 [J], 王怀新;张东阳;薛鹏程;
5.矿井主扇风机远程监测及故障诊断系统 [J], 李朕; 马晨峰; 岳强
因版权原因,仅展示原文概要,查看原文内容请购买。
- 1、下载文档前请自行甄别文档内容的完整性,平台不提供额外的编辑、内容补充、找答案等附加服务。
- 2、"仅部分预览"的文档,不可在线预览部分如存在完整性等问题,可反馈申请退款(可完整预览的文档不适用该条件!)。
- 3、如文档侵犯您的权益,请联系客服反馈,我们会尽快为您处理(人工客服工作时间:9:00-18:30)。
基于可靠性的状态监控预知系统------风机在线监测及诊断系统技术方案一、概况:[监控设备]:对于炼钢厂转炉风机,实施在线状态监测,精确了解设备运行状态,实施有计划的预知维修,同时根据运行状态与根源分析,进一步提高设备运行的可靠性,为合理安排设备维修和优化备件提供有力保障。
[实施目标]:该系统通过建立关键设备在线监测体系,实时监控设备振动参量状态,及时报警,防止重大设备事故的发生;同时采用最先进的监控技术,最大程度延长设备的预警时间,从而实现预知维修,并通过智能的专家诊断,精确诊断故障源,实现精密维修,缩短维修用时,为检测维修制度合理化提供准确的数据基础。
二、项目意义利用传感器捕捉振动、冲击脉冲、转速、电流信号;进行信号处理、模式识别、预报决策,及计算机技术,监测机组在运行过程中的振动参数及有关性能参数及其动态变化,在机组运行过程中,作出是否有故障、故障种类、故障部位、故障严重程度、故障发展变化趋势等诊断结果,判断机组性能劣化趋势。
使运行、维护、管理人员能在维修之前做好有关准备,做到预知维修,并可根据监测诊断结果,进行技术改造,避免类似事故再次发生。
实施本项目的意义在于:1、通过本项目实现对机组的连续在线监测和劣化趋势预测达到预知维修的目的,以保证无故障运行。
2、利用监测诊断系统可以及时判别设备是否有故障,并且能够迅速查明故障原因、部位、预测故障影响。
从而实现有针对性的按状态维修,那里坏了修那里,而不是大拆大卸,延长检修周期,缩短检修时间,提高检修质量,减少备件储备,提高设备的维修管理水平。
3、向运行人员提供及时的信息,有效地支援运行,提高设备使用的合理性、运行的安全性和经济性,充分挖掘设备潜力,延长服役期限,以便尽量合理地使用设备。
从而降低设备故障停机时间,减少计划检修时间和非计划检修时间。
4、向维修管理人员及时提供设备运行情况,及时准备备品备件,及时处理有关故障,真正实现预知维修,以最少的代价发挥设备最佳的效益,做到最佳运行,使设备维修费用、设备性能劣化与停机损失费用最低。
根据监测诊断结果确定维修时间、维修部位和维修方法,并根据诊断结果进行技术改造,可以降低设备故障停机时间,减少计划检修时间和非计划检修时间。
提高开工率,增加产品产量,减少同类事故发生的次数。
三、CMS在线监测系统功能说明:系统功能:1)本系统为瑞典SPM公司着名的CMS网络监控系统,在世界范围内拥有40年的历史,更为ABB、西门子、英格索兰、西马克、阿尔斯通等着名设备制造商应用,进行产品出厂配套或进行出厂质量校核;2)全中文操作界面,提供WINDOWS窗口形式和树状结构形式两种操作方式,真正做到会使用计算机就能操作软件;3)在线监控设备振动指标,长期趋势监控,智能型“绿、黄、红”报警指示;4)通过专利的“EVAM”专利技术,实现:①智能诊断故障原因,对位移、加速度、速度、歪度、峭度、4个等级摩擦量以及不平衡、不对中、松动、轴承故障、转子断条等30多项参数与征兆独立评估,分别给出“绿、黄、红”状态指示,实现智能专家诊断;②针对设备工况的复杂性,对于变速设备、载荷变化较大的设备,可根据转速和载荷的变化量预先设定设备不同工况下的不同标准;③根据设备的多样性,有时设备总体振动不大,但是短时工作后便造成事故停机现象,“EVAM”根据30多项参数的趋势变化可以捕捉设备的故障原因,并报警提示;④根据设备的基本参数和正常状态下的参量,形成适合该设备的企业标准,从而为设备后期更准确判断设备运行状态;⑤ 内置的“专家系统”和庞大的轴承库,方便具有一定专业知识、习惯用频谱来分析设备故障的管理人员来判断如不平衡、不对中、松动、轴承故障、转子断条等等故障。
5) 轴承监测 —— 冲击脉冲技术① 振动监测解决不了早期预警问题已是世界公认的事实,原因是轴承早期的问题(如润滑不良,点蚀等)所产生的是较弱的瞬态信号,常规振动传感器及振动分析方法根本无法捕捉得到。
如下图实例中,振动未报警,但轴承冲击脉冲峰值LR 已远远超出报警值,损伤程度值COND 逐渐加大,说明轴承已经失效,继续运行将导致严重隐患。
② “冲击脉冲技术”是完全不同于振动监测的技术,该技术已服务世界各国30多年,被公认为是解决滚动轴承、齿轮问题的最佳途径,因此应用极为广泛,仅在中国就已成功应用于上千家企业。
绝大多数世界知名设备制造商,如ABB 、英格索兰、苏尔寿、GE ,都已在其设备出厂前安装冲击脉冲传感器,或使用该技术进行出厂检验;为数众多的进口石化挤出机、造纸机、船用发动机的齿轮箱上,已经安装了冲击脉冲监测保护系统。
③ 该技术简单易用,只须在轴承座上安装冲击脉冲传感器,系统会直接给出轴承运转状态值及国际标准的“绿、黄、红”状态指示,同时给出:专利的LR/HR ? 技术,给轴承状态冲击脉冲LR/HR损伤程度COND 润滑指标LUB水平振动VIB出强冲击与平均冲击指标;⏹状态代码Code(A为最佳,B为干磨擦,C为轻度损伤,D为严重损伤);⏹润滑状态代码LUB(油膜厚度:0,1,2,3,4…);⏹损伤程度值Cond(<30为轻度,30-40为中度,>40为重度);⏹它包括一个庞大而丰富的轴承库,以及专利的LUBMASTER 轴承润滑寿命分析模块。
(见下图)④冲击脉冲技术的优势是其独特设计的冲击脉冲传感器,仅对轴承运转、齿轮啮合时产生的瞬态冲击做出反应,而对其它低频振动的干扰不作反应,因此可以得到纯净的早期信号。
对冲击脉冲信号进行频谱分析,即专利的SPM Spectrum TM,具有其它常规带通滤波、包络技术无法比拟的优势,可得到极为清晰的频谱图。
6)通过企业内部网络实现网络共享,同时支持5个用户同时上网查看设备目前的工作状况;7)系统内置的TLT自检功能,自动监测网络系统的连接质量和硬件品质,保证采集数据的真实可靠;8)本系统自成体系,不受网络系统的故障干扰;9)本系统可以同时接收在线或离线便携式数采器的数据,进入系统进行统一管理;10)可以按企业内部的设备统一编号或自己编排的编号(任意)编辑测点名,方便查找;11)可以根据管理人员的职责范围来设定管理权限,真正做到职责分明;12)对于问题设备或检修过设备处理的过程、方法和结论可在当时的测定数据中加以注解,便于将来查阅、参考和制定恰当的处理方案;13)本系统采用WINDOWS自带的SQL SERVER 数据库,可以利用SQL SERVER 数据库自身的软件进行备份,也可以在客户端自行备份数据;14)数据可与企业EAM或ERP体系实现数据共享;15)本系统采用模块化的方式,可以根据用户的需求扩展功能,如:脉冲技术、油膜分析功能等更深层次的分析功能;16)可以通过网络系统,输入软件序列号,在互联网上免费升级软件。
实施方法:1)安装振动传感器,监控设备的振动变化;2)安装冲击脉冲传感器,监控轴承的冲击变化和润滑的状况;3)安装转速传感器,实现转速监控,并实现变速设备智能诊断;4)通过现场监测单元(多通道信号处理),将数据通过企业互联网传输;5)服务器运行监控软件与数据库,客户端实现有权限地数据共享与诊断分析。
五、在线系统结1、结构图VCM+BM2、风机测点分布测点说明如下:◆风机本体安装3个振动传感器:风机本体轴承位水平安装1个振动传感器、垂直方向安装1个振动传感器、轴向安装1个振动传感器,。
◆电机本体安装2个冲击脉冲传感器:两个轴承位各安装1个冲击脉冲传感器。
◆电机和风机之间安装1个转速传感器。
◆电机控制柜上:控制柜上电机电流信号接入VCM。
一、风机在线监测系统功能要求;1、按照设备状态在线监测和故障诊断的需求,风机上实施在线监测,并具有故障诊断和故障报警功能。
2、利用传感器捕捉振动、冲击脉冲、转速、电流信号;进行信号处理、模式识别、预报决策,及计算机技术,监测机组在运行过程中的振动参数及有关性能参数及其动态变化,在机组运行过程中,做出是否有故障、故障种类、故障部位、故障严重程度、故障发展变化趋势等诊断结果,判断机组性能劣化趋势。
3、通过振动准确监测风机系统的不平衡、不对中、松动等问题;4、通过冲击脉冲准确监测风机系统的轴承问题,做到准确预知与诊断;5、通过电机电流信号的监测,反映风机载荷的变化,提高系统诊断的准确性;6、有关诊断分析软件中能实现不同岗位人员的权限设定,并能在局域网内实现数据共享,以便提高各级专业人员利用系统及时了解所监测设备的能力和水平,以便提高此类重要设备管理的效率。
二、主要系统硬件的技术条件1、振动监测模块(VCM-20)VCM-20 是连续测量单元,供采用EVAM? 专家方法进行振动分析。
单元内部配有CPU、硬盘和多路复用测量逻辑模块。
VCM-20-8 配有8个振动测量通道,8 个RPM 测量通道。
可插接4-20mA模拟量输入板,可扩充8-16通道模拟量,监控温度、压力等,也可通过负载电流监控,实现变载分析。
VCM-20 可通过以太网与安装Condmaster Nova 软件的计算机连接。
测量设定值在软件中设置。
通信程序DBL 向VCM-20 单元传送测量设定值,并读取这个单元的结果文件。
●处理器:1GHz●存储器:256 Mb RAM●硬盘容量:> 20 Gb●通道:振动20,转速8●频率范围:0 –20KHz●包络频率:100, 200, 500, 1000, 2000, 5000, 10 000 Hz●检测窗口:矩形、汉宁、海明等●分辩线数:200, 400, 800, 1600, 3200, 64002、轴承监测模块(BMU-07)BMU-07配有7个测量滚动轴承冲击脉冲通道,与测量单元VCM20连接,根据VCM20的请求进行测量、传输数据。
BMU 提供冲击振幅值和包络冲击脉冲信号,用于频谱分析。
VCM20单元测量轴承转速,计算SPM 频谱,评估轴承工作状态。
测量条件在Condmaster Nova? 中设置,包括冲击脉冲方法、频谱类型、用于识别轴承故障的征兆及告警极限等。
●测量方法:冲击脉冲LR/HR, 和SPM 频谱●测量范围:-19 到99 dBsv (LR/HR)●测量通道:7●电源:5 V DC ±10%●温度范围:-10°到60°C●尺寸:139 x 145 x 46 mm3、冲击脉冲传感器(42000)●测量范围:最大值100 dBsv ●机架基础:不锈钢SS 2382●设计:密封●温度范围:-30到+150° C●外部压力:最大1 MPa (10 bar)●扭矩:15 Nm, 最大20 Nm4、振动传感器(SLD144B)●灵敏度:100 mV/m/s2,精度:1%●工作环境温度:-50~125℃●频率范围:0.5~10KHz●适用公制M8内螺纹孔,传感器垂直输出●传输距离:400米以内。