连铸车间设备计算与设计
《年产432万吨连铸车间》设计说明书

内蒙古科技大学本科生毕业设计说明书(毕业设计)题目:设计年产量为432万吨合格连铸坯的连铸车间学生姓名:李震宇学号:0976102508专业:冶金工程班级:冶2011-5班指导教师:彭军副教授摘要本设计为年产量432万吨合格连铸坯的连铸车间,主要对连铸生产的工艺流程、车间组成和工艺布置进行设计,并对连铸机的几个主要工艺设备:钢包,中间包及其运载设备,结晶器及其振荡器,拉矫和引锭装置,切割装置进行了设计计算。
设计中对板坯连铸车间做了合理的布局。
并绘制了车间平面图和连铸机纵剖图。
为了提高连铸机生产率和提高产品质量,在设计中采用了一些新技术,新工艺和新设备。
设计中采用了直弧型连铸机,大容量和深熔池的中间包,电磁搅拌技术等。
本设计有2座210吨桶球型氧气顶吹转炉,转炉作业率85%,采用2吹2的吹炼制度。
冶炼时间需要38分钟。
车间设有2座RH炉,2座LF炉和2套板坯连铸机,预计年生产能力为432万吨良坯钢。
关键词:板坯连铸车间二次精炼炼钢AbstractThis paper is about the process design of the slab continuous casting plant of 4.32 million tons per year, it is mainly introduced the production process ,plant composition and the technological arrangement of the slab continuous casting plant. Also introduced and made the calculation about the important process and equipments of the slab caster: ladle and their delivery devices,tundish and their delivery devices, crystallizer and vibration device, straightening devices and dummy, cutting device.For improving the productivity of the continuous casting mill and product quality, some new technologies, and advanced equipment are taken.The straighten-arc casting mill, tundish with big capacity and deep pit, ,leaking prediction of the crystalizer, electromagetic stirring are selected, to make sure that the producing plan are scientific, adapting the demand of the present social development.There are two 210t silo-shape oxygen top-blown convertons both working with 85% operation rate.Two RH refining,two LF refining and two set of continous casing equipment , which are expected annual production capacity of 4.32 million tons steel billet.Key words: the slab continuous casting plant secondary refining continuous casting目录摘要.......................................................................................................................................... 第一章文献综述 . 01.1 连铸技术的发展概况 01.2 连铸技术发展趋势 (2)1.3 我国连铸技术发展 (4)1.4 国内连铸面临的问题 (5)1.5 连铸机总体设计的前提条件 (6)1.6 板坯连铸机主要技术特点 (6)第二章设计方案的确定和论证 (11)2.1 产品大纲的制定 (11)2.1.1 产品大纲制定的依据 (11)2.1.2 产品大纲 (12)2.1.3 各钢种的成分和生产工艺 (12)2.2 金属料流程图 (14)2.3 方案的选择与论证 (15)2.3.1 转炉容量与座数的确定 (15)2.3.2 钢包容量与尺寸的确定 (16)2.3.3 连铸方法的选择与论证 (20)第三章车间主体设备的设计 (27)3.1 连铸机的设计 (27)3.1.1 钢包允许的最大浇注时间 (27)3.1.2 铸坯断面的选择 (27)3.1.3 拉坯速度的确定 (28)3.1.4 冶金长度的计算 (29)3.1.5 连铸机弧形半径的计算 (30)3.1.6 连铸机的流数 (32)3.1.7 连铸机生产能力的确定 (32)3.2 连铸机的主要设备设计 (35)3.2.1 中间包的设计 (35)3.2.2 结晶器的主要设计参数 (39)3.2.3 二次冷却系统的设计 (41)3.2.4 喷水冷却系统 (42)3.2.5 喷嘴的选择与布置 (44)3.2.6 夹辊辊径、辊距及其布置 (44)3.2.7 拉坯矫直装置 (45)3.2.8 引锭装置 (46)3.2.9 铸坯的切割装置 (48)3.2.10 连铸机高度 (51)3.2.11 连铸机长度 (51)第四章车间主厂房的设计 (53)4.1 主厂房布置形式的选择与分析: (53)4.1.1 总体平面布置 (53)4.1.2 车间的工艺布置 (53)4.1.3 运输 (53)4.2 加料跨供应系统的选择 (53)4.2.1 转炉用铁水的供应 (53)4.3 连铸跨的布置 (56)4.3.1 浇注跨的标高、跨度 (56)参考文献 (58)第一章文献综述1.1 连铸技术的发展概况连续铸钢是钢铁冶金领域内发展最快、最受重视和最为成功的技术之一,其原因在于连铸技术具有显著的技术经济优越性,是钢铁生产流程中结构优化的重要环节。
毕业设计指导书连铸车间设计
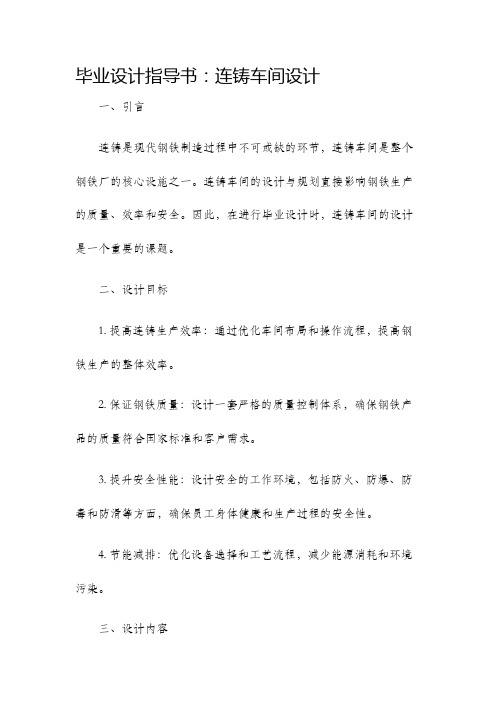
毕业设计指导书:连铸车间设计一、引言连铸是现代钢铁制造过程中不可或缺的环节,连铸车间是整个钢铁厂的核心设施之一。
连铸车间的设计与规划直接影响钢铁生产的质量、效率和安全。
因此,在进行毕业设计时,连铸车间的设计是一个重要的课题。
二、设计目标1. 提高连铸生产效率:通过优化车间布局和操作流程,提高钢铁生产的整体效率。
2. 保证钢铁质量:设计一套严格的质量控制体系,确保钢铁产品的质量符合国家标准和客户需求。
3. 提升安全性能:设计安全的工作环境,包括防火、防爆、防毒和防滑等方面,确保员工身体健康和生产过程的安全性。
4. 节能减排:优化设备选择和工艺流程,减少能源消耗和环境污染。
三、设计内容1. 连铸机布局:根据钢铁生产能力和市场需求确定连铸机的数量和类型,并合理安排连铸机的布局,以提高生产效率。
2. 冷却设备设计:设计一套高效的冷却设备系统,以确保连铸过程中钢水的快速冷却,使得钢铁产品具有理想的结晶组织。
3. 钢包设计:设计合理的钢包结构和钢包维护系统,确保钢水的顺利过渡和保持稳定的温度。
4. 水处理设备:设计适用于连铸车间的水处理设备,包括废水处理和循环水处理,以保护环境并节约水资源。
5. 环境控制:确保车间内的温度、湿度和清洁度达到要求,保证钢铁生产的稳定性和产品质量。
6. 周边设施:考虑到员工的工作环境和生活需求,设计合理的办公区、员工休息区、更衣室等周边设施。
四、设计方法1. 研究现有连铸车间的设计案例和经验,了解行业发展趋势和技术创新。
2. 布置车间:根据设备尺寸、工艺流程和人员活动等因素,对车间进行布局规划,遵循人机工程学原理。
3. 控制系统设计:设计合理的自动化控制系统,包括数据采集、监控和调控等方面,提高生产效率和质量控制水平。
4. 设备选择:根据连铸车间的生产能力、钢铁种类和产品要求,选择合适的连铸机、冷却设备、钢包等设备。
5. 安全设计:根据相关标准和法规,设计合理的安全措施,保障员工的人身安全和生产过程的安全性。
钢铁冶金-连铸机主要参数的确定

当铸机弧形半径大时,铸机高度 增加,重量增加;
当铸机弧形半径小时,铸机尺寸、 重量变小,但过
小的弧形半径在矫直时由于延伸 率过大而产生裂纹。
因此,铸机弧形半径大小应针对 不同的铸坯断面,浇
铸的钢种等因素,选择最佳半径, 其值大小可根据理
论计算来确定。
2
1.固相矫直时连铸机弧形半径计算
n G
T S v
式中:G: 钢包容量;t T:钢包允许的浇注时间;min S:铸坯断面积; m2 v:拉坯速度;m/min γ:铸坯比重;t/m3
二:弧形铸机参数计算
主要设计参数有: 铸坯断面、冶金长度、拉坯速度、 铸机弧形半径、连铸机流数等。
是铸机机械设备设计的主要依据,是决定设备性 能和尺寸的基本因素。
铸坯温度及对铸坯表面质 量多要求等。
普通碳钢、低碳钢:
将此值代入,则有:
1.5 ~ 2%
R 25 ~ 33.3 H
2) 校核铸坯是否完全凝固:.
Lc
01
2
R
H 2
lm 2
02
01 铸坯中线距离 Lc 有:
lm
02 ( :结晶器有效长度)
03
03
L >L 为使铸坯进入c矫直区e时全部
凝固,必须有:
t (H为铸坯厚
度)
e
Le v
若:拉坯速度 为v,全部凝固 所经历的时间 为:
L 2Hk v 则有:e
2Hale Waihona Puke 影响冶金长度 的因素有:铸 坯厚度、拉坯 速度、冷凝强
度
3.拉坯速度
拉坯速度:连铸机每分钟拉 出铸坯的长度。(m/min)
k t0
(mm)
lm
t 则: 0 lm / v
毕业设计指导书连铸车间设计

毕业设计指导书:连铸车间设计一、引言连铸车间作为钢铁生产过程中至关重要的环节,其设计直接关系到生产效率和产品质量。
本文旨在对连铸车间的设计进行指导,以确保其功能完备、安全高效。
首先,我们将介绍连铸工艺流程和其在钢铁生产中的重要性。
然后,我们将讨论连铸车间设计的基本原则和注意事项。
最后,我们将给出几个实用的设计建议。
二、连铸工艺流程1. 连铸工艺流程的基本原理连铸(Continuous Casting)是一种将钢水连续倾注到铸机中,并通过一系列工艺步骤将其冷却凝固成坯料的工艺。
该工艺相较于传统的离散式铸造具有许多优点,如高效率、节能、减少不良品产生率等。
2. 连铸工艺流程的步骤连铸工艺流程主要包括以下几个步骤:(1)钢水倾注:将冶炼好的钢水通过铸机倾注到浇注罐中。
(2)结晶器冷却:通过冷却水冷却结晶器,使钢水在结晶器中凝固成坯料。
(3)出坯:将凝固完成的坯料连续从结晶器中取出。
(4)切割:根据需要将连铸坯切割成合适的长度。
(5)过热处理:对切割后的连铸坯进行过热处理,以提高其应变能力。
(6)尺寸修整:对过热处理后的连铸坯进行尺寸修整,达到产品要求。
三、连铸车间设计的基本原则1. 安全性连铸车间工作环境应具备良好的安全性,包括防火、防爆、通风和紧急疏散设施等。
熟悉并遵守相关的安全操作规程和流程,有效减少事故的发生。
2. 空间布局合理的空间布局是连铸车间设计的关键。
要确保设备之间的间距足够,以便操作人员轻松进出及维修设备。
同时,为保证作业人员的视野和通道的畅通,需适当安排设备的位置。
3. 噪音和防护连铸车间通常会产生噪音,因此需要合理设计消声设备,降低噪音对工人的影响。
另外,还需设置适当的防护设施,如安全带、安全栏杆等,确保工人的人身安全。
4. 运输和搬运设备连铸车间需要合理规划运输和搬运设备,以保证钢坯的顺利流动。
需要考虑到设备的数量、容量和布局,使得整个运输和搬运过程高效可靠。
5. 环境保护钢铁生产过程中产生的废气、废水等污染物需要进行合理的收集和处理,以避免对环境造成污染。
毕业设计指导书连铸车间设计

毕业设计指导书一、毕业设计的性质及目的毕业设计是学生在学习了专业理论和毕业实习基础上进行的一次综合性专业工程设的基本训练,是对所学基础知识,特别是专业基础及准也理论知识的综合运用。
通过设计,学生应了解设计原则,初步掌握连铸及连铸车间的设计内容,设计步骤及设计法方法,了解连铸与炼钢及轧钢的配合,了解连铸机及连铸车间设计中的组要问题。
通过设计将较好的培养学生收集生产实际资料及查阅资料的能力并培养学生对采用新技术新工艺的考虑方式。
二、设计要求1.对设计任务的态度应严肃认真;2.设计应具有一定的合理性,计算准确,不应有原则性错误;3.设计方案要体现先进性,但设计中所采用的新技术、新工艺应是在生产上可行的。
对于技术经济指标,应选取国内先进水平。
1.设计依靠的计算数据应可靠,说明书应书写工整,条件清楚,文字简练,词意明确。
2.绘图应正确,尺寸标记完整,图面整齐清洁。
连铸设计内容第一章概述一、连铸机简介简单论述连铸特点及发展原因。
二、设计依据由设计任务书确定即题目三、(改建的)××厂现状及今后计划如扩容等包括铁水供应、炼钢、轧钢及炼钢厂房等情况。
四、设计指导思想设计的原则(如对有效、实用先进技术采用的考虑,对原有厂房和设备利用节约资金的考虑,分期的考虑等原则)一般在确定各主要指标时应取平均先进水平,在采用先进技术时,应用生产上可行的技术,在改建厂房时应尽量利用原有厂房的设备,并尽量减少影响原有的生产。
五、设计内容简介(在设计完成后总结)简单扼要的概述设计要点(包括连铸比,机型、产品类型、铸机产量、台数、设计的主要特点、车间布置的特点,工艺流程的特点,采用了那些新技术,今后发展的可能性及存在问题等)。
第二章连铸工艺§1 设计条件无论是新建或改造连铸车间作为设计的基本条件是生产计划和炼钢条件。
设计连铸机的能力要与计划浇注的品种和产量一致,而且要与炼钢能力匹配。
一、炼钢条件炉容量、座数、吹炼情况,平均出钢量,最大出钢量,冶炼周期,每天平均出钢炉数,年产钢量,厂房条件等。
连铸机主要设计参数的确定
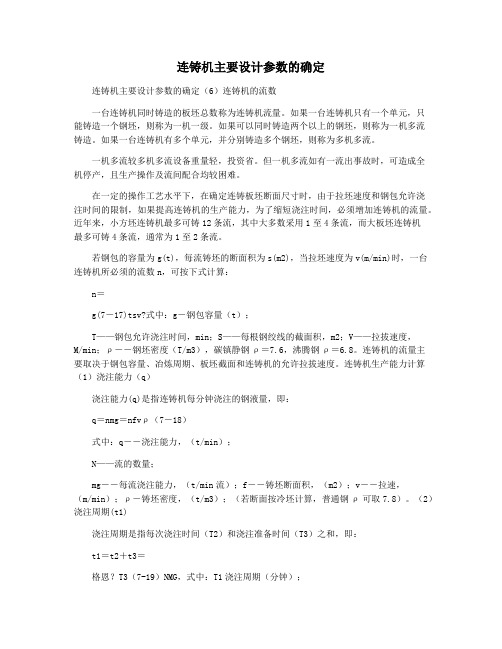
连铸机主要设计参数的确定连铸机主要设计参数的确定(6)连铸机的流数一台连铸机同时铸造的板坯总数称为连铸机流量。
如果一台连铸机只有一个单元,只能铸造一个钢坯,则称为一机一级。
如果可以同时铸造两个以上的钢坯,则称为一机多流铸造。
如果一台连铸机有多个单元,并分别铸造多个钢坯,则称为多机多流。
一机多流较多机多流设备重量轻,投资省。
但一机多流如有一流出事故时,可造成全机停产,且生产操作及流间配合均较困难。
在一定的操作工艺水平下,在确定连铸板坯断面尺寸时,由于拉坯速度和钢包允许浇注时间的限制,如果提高连铸机的生产能力,为了缩短浇注时间,必须增加连铸机的流量。
近年来,小方坯连铸机最多可铸12条流,其中大多数采用1至4条流,而大板坯连铸机最多可铸4条流,通常为1至2条流。
若钢包的容量为g(t),每流铸坯的断面积为s(m2),当拉坯速度为v(m/min)时,一台连铸机所必须的流数n,可按下式计算:n=g(7-17)tsv?式中:g―钢包容量(t);T——钢包允许浇注时间,min;S——每根钢绞线的截面积,m2;V——拉拔速度,M/min;ρ――钢坯密度(T/m3),碳镇静钢ρ=7.6,沸腾钢ρ=6.8。
连铸机的流量主要取决于钢包容量、冶炼周期、板坯截面和连铸机的允许拉拔速度。
连铸机生产能力计算(1)浇注能力(q)浇注能力(q)是指连铸机每分钟浇注的钢液量,即:q=nmg=nfvρ(7-18)式中:q――浇注能力,(t/min);N——流的数量;mg――每流浇注能力,(t/min流);f――铸坯断面积,(m2);v――拉速,(m/min);ρ―铸坯密度,(t/m3);(若断面按冷坯计算,普通钢ρ可取7.8)。
(2)浇注周期(t1)浇注周期是指每次浇注时间(T2)和浇注准备时间(T3)之和,即:t1=t2+t3=格恩?T3(7-19)NMG,式中:T1浇注周期(分钟);t2―浇注时间(从中间包开浇至中间包最后一流浇完为止的总时间,(min);T3——准备时间(从中间包浇注到下一个熔炉的假封头填充和浇注准备的总时间)间),(min);g――钢包钢液量,(t);N——每次连铸炉的平均数量。
连铸车间设备计算与设计

第六章 连铸车间设备计算与设计6.1连铸机的主要工艺参数连铸机的主要工艺参数是决定连铸机机械设备性能和尺寸的基本前提,也是连铸机车间工艺布置的主要依据,连铸机的主要工艺参数包括钢包允许的最大浇注时间、铸坯断面、拉坯速度、流速、冶金长度、弧形长度。
6.1.1钢包允许的最大浇注时间为了使钢包内的钢液不致因散热太多而形成包底柠壳,又能充分发挥其延长浇铸时间的潜力,保证浇铸的顺利进行,必须适当的确定不同容量的钢包允许的最大浇铸时间。
可按下列经验公式计算:max log 0.20.3G t f -=⨯ 其中: G —钢包容量,t ;t max —钢包允许浇注的最大时间,minf —质量系数,主要取决于对浇注温度控制的要求。
对要求严格控制中心偏析和疏松的钢种,钢水过热度要小,取f =10;max log 0.20.3G t f -=⨯ (m i n )60103.02.0100log =⨯-=6.1.2铸坯断面铸坯断面的形状和尺寸可依据下列因素确定:1)根据轧材品种和规格确定铸坯断面;2)不同钢种需要不同的压缩比;3)连铸机生产能力必须与炼钢能力相匹配。
综合以上所述,本设计大方坯连铸机尺寸,铸坯断面的尺寸为 280×325mm 、280×380、φ200~φ280。
6.1.3拉坯理论拉速与工作拉速1)理论拉速:实际上,连铸机的最大拉速取决于铸坯出结晶器时不致发生变形或拉漏所需的最小坯壳厚度。
V 理论=⎥⎦⎤⎢⎣⎡224D K •L 式中: V 理论—理论最大拉速,m/min ;L —冶金长度,本设计取L 为37.5m ;D —铸坯厚度,m ;K —综合凝固系数,一般取24~33本设计取为33。
V 理论=⎥⎦⎤⎢⎣⎡224D K •L=min /08.25.3728033422m =⎥⎦⎤⎢⎣⎡⨯⨯ 2)工作拉速:是指连铸机生产操作中能顺利浇铸,保证铸坯质量相对稳定的平均拉速。
在实际生产中,为改善铸坯质量,使用的工作拉速应小于最大理论拉速。
板坯连铸机结晶器的设计及计算

油缸卸压后 , 靠碟形弹簧的压力使窄边夹紧。 ( 6 ) 各种冷却水配管 结晶器冷却水及板坯二次冷却喷水配管, 通过振
动 台上 的平 面密封 使水路 自行接通 。 ( 7 ) 润滑及液 压
3 6 2 0 1 / m i n
5 0 5 1 / m i n
大连华锐重工集团股份有限公 司设计研 究院
摘 要: 通过 一 系列说 明 、 计算 , 概 述 了板 坯连 铸机结 晶器
张梁敬
辛
鑫
的型式 、 功能特点及设计 要点。
关键词: 板坯连铸 ; 结 晶器 ; 冷却水量 ; 调宽装置 ; 内腔尺寸
板整体拆除刨修。 水箱内设有供结晶器冷却用的水冷 通道 , 在与背板贴合 的铜板表面上开有水槽 , 连续铸 钢期 间与宽 面铜板 接触 的钢水 热量通 过 这些水 槽 中
流动 的冷 却水导走 。
l 概 述
结晶器是连铸机 中的铸坯成型设备。其作用是
将连续 不断 地 注入其 内腔 的钢 液通过 水冷 铜壁 强制
冷却 , 导出钢液的热量 , 使之逐渐凝固成为具有所要 求 的断面形状和一定坯壳厚度的铸坯 ,并使这种芯 部仍为液相的铸坯连续从结晶器下 口拉出,为其在 以后的二冷区域内完全凝固创造条件。文章围绕板 坯连铸机结晶器型式及功能予以阐述 ,并针对相关 应 用进行分 析计算 。
是通过长螺栓与内、 外弧水箱把合的, 在发生漏钢事 故或安装调整时操作方便 。用于冷却铸坯的喷水配 管分别安在内、外弧水箱 的底部通过喷嘴从两侧冷
却铸坯 。
( 3 ) 左、 右窄边及窄边导向装置 左、 右窄边铜 板与背板把合后通 过卡板 与螺栓与 压板连在一起, 冷却水从窄面压板进出。与宽面铜板 样, 窄边铜 板也开有冷却水槽 对铜板进行 冷却 。
连铸计算公式大全

连铸计算公式大全连铸(Continuous Casting)是一种金属加工工艺,用于生产连续长度的金属坯料。
在连铸过程中,液态金属被直接铸造成坯料,而不需要通过传统的浇铸过程。
连铸计算涉及到多个方面,包括熔炼过程、铸模设计、冷却和结晶过程等。
以下是一些可能涉及的连铸计算公式的示例:1. 铸坯截面积计算公式:A = L ×W其中:A -铸坯截面积L -铸坯长度W -铸坯宽度2. 铸坯体积计算公式:V = A ×H其中:V -铸坯体积A -铸坯截面积H -铸坯高度3. 结晶器截面积计算公式:A_mold = π×(D/2)²其中:A_mold -结晶器截面积D -结晶器直径4. 结晶器长度计算公式:L_mold = (8 ×V_mold) / (π×D_mold)其中:L_mold -结晶器长度V_mold -结晶器内腔体积D_mold -结晶器内腔直径5. 冷却水流量计算公式:Q = C ×A ×ΔT/Δt其中:Q -冷却水流量C -冷却水比热容A -冷却面积ΔT -冷却前后温度差Δt -时间间隔这些公式只是连铸计算中的一部分,实际生产中还需要考虑其他因素,如钢种、浇铸温度、浇铸速度等。
在实际应用中,需要根据具体生产情况选择合适的计算公式并进行相应参数的调整。
这只是连铸计算中的一小部分公式示例,实际的计算可能涉及到更多的参数和方程,具体取决于金属类型、连铸机型号、操作条件等因素。
在实际应用中,专业的冶金工程师通常会根据具体情况进行计算和优化。
连铸有关计算

径?
20
解:浇注速度
G=BDVc 7.60.280.151.2 0.38304t / min
22.98t / h
根据公式
d 2 375G = 375 22.98 =406mm2
H
450
d 406 20.16mm
21
3、结晶器的有关计算
2
1.1 坯壳厚度的计算 分析漏钢事故时,需要考虑出结晶器下口坯
壳厚度的厚薄。 例1 小方坯断面为150mmx150mm,拉坯速度Vc 2.5m / min 结晶器长度 Lm 750mm ,若浇注过程中结晶器液 面稳定在离上口50mm,结晶器凝固系数 K凝=20mm / min1/2
求出结晶器下口的坯壳厚度 ?
35
(3) 浇注时间
t G钢 Gn
(4) 二冷水量 Q W BDVcn
36
(5) 铸机流数
n
G钢
BDVct
(6)水口直径
d 2 375G H
37
3、 结晶器的有关计算
(1) 结晶器倒锥度
l上 -l下 100%
l上
=S上口断S面上积-口断S面下积口断面积 100%
(mm) l上 -l下
出钢过程温降51℃,T1=51℃,钢水镇静10min,温 降为0.4 ℃/min,T2=10X0.4=4℃,所以出钢温度为
T(出钢)=T(进站)+T1+T2=1598+51+4=1653℃ 从上题可以看出,出钢温度是由浇注温度逆推得到
31
关于夹杂物上浮时间的计算和二冷区配水计算相 对比较复杂,我们在这里不作介绍。
所以
n G钢 Gt
年产量750万吨全连铸转炉车间设计(DOC)

年产750万吨转炉炼钢全连铸车间设计冶金工程0901 任人第二章生产规模及产品方案2.1 金属平衡计算图2.1 金属平衡表2.2 生产规模的确定该转炉车间的生产规模是年产合格铸坯750万吨。
2.2.1 转炉座数和大小的确定设计年产750万吨合格铸坯的转炉炼钢系统。
由金属平衡表计算可知,所需的转炉钢水年产量为819万吨。
每一座吹炼转炉的年出钢炉数N 为:112T 3651440T T 1440N η⨯=⨯=炉1003444%843651440=⨯⨯= (2-1)式中: T 1—每炉钢的平均冶炼时间,min ;T 2—一年的有效作业天数,d ; 1440—一天的日历时间,min ; 365—一年的日历天数,d ; η—转炉的作业率,取84%;转炉车间年产钢水量:W=n×N×q (2-2)式中: W —转炉车间年产钢水量,t ;n —转炉车间经常吹炼炉子座数; N —每一座吹炼炉的年出钢炉数; q —转炉公称容量,t 。
n×q=8190000÷10034=816吨 所以,取n= 2,则q=420t 所以:本设计选两座420吨的转炉进行炼钢。
3.1 转炉炉型选择及计算转炉炉型选筒球形,其中球缺体半径取R=1.1D 。
3.1.1 转炉主要尺寸参数的确定和计算(1)炉容比 炉容比取0.90m 3/t (2)熔池尺寸计算 ① 熔池直径D6554224200.51t G K D =⨯=⨯=㎜ (3-1) 式中: G —新炉金属装入量,取公称容量300t ;t —平均每炉钢纯吹氧时间,min ,(取16min ); K —系数(取1.50) D —熔池直径,mm ;② 熔池深度h)池3(m 76.16/6.8204G/T V === (3-2))池(mm 6.2201D 9.70D 46.00V h 23=+= (3-3)式中: V 池—转炉熔池有效容积,m 3 ;T —转炉内钢水密度,取6.8t/m 3 ;(3) 炉帽尺寸计算 ① 炉帽倾角θ:取θ=60◦ ② 炉口直径d 口:d 口=(0.43~0.53)D (3-4)本设计取d 口=0.43D=0.43×6554=2818.2mm ③ 炉帽高度H 帽:3.3535H tan d -D 21H =+=口口帽)(θ㎜ (3-5)式中H 口—炉口直线段高度,取H 口=300㎜: ④ 炉帽总容积V 帽:63.60H d 4d Dd D H H 12V 222=+++⨯-=口口口口口帽帽)()(ππm 3 (3-6)(4) 炉身尺寸计算 ① 炉身体积V 身:取炉容比为0.90m 3/tV T =0.80×T=0.90×420=378m 3 (3-7) V 身=V T -V 帽-V 池=255.61m 3 (3-8)式中:V T —转炉有效容积,m 3; ② 炉身高度H 身:6.7576D V V -V 4D V 4H 2T 2=-==ππ)(池帽身身㎜ (3-9)(5)出钢口尺寸的确定① 出钢口中心线水平倾角θ1:取θ1=0°; ② 出钢口直径d 出:49.282G 75.163d =+=出㎜ (3-10)(6)转炉有效高度H 内:H 内= h+H 身+H 帽=2201.6+7576.6+3535.3=13313.5㎜ (3-11)(7)转炉总高H 总:H 总=H 内+H 衬+δ底+δ帽=13313.5+1060+130=14503.5㎜ (3-12)(8)炉壳直径D 壳:D壳=D+D衬+2δ身=6554+2020+160=8734㎜(3-13)式中:δ身—炉身钢板厚度,取80㎜;D衬—炉身处两侧炉衬的厚度;(9) 高宽比核定:H总/D壳=14503.5/8734=1.65 (在1.35~1.65范围内)所以设计合格。
连铸机的设计

6结晶器的尺寸参数
项目 结晶器长度 结晶器的倒锥度 结晶器的水缝面积 结晶器拉坯阻力 水口直径
参数 619 mm 0.95% 13414mm2 34490 N 3.05cm
7 中间包主要工艺参数
项目 中间包容量 中间包高度 中间包长度 中间包的倾角 水口直径
参数 20.54 t 1200 mm 7100 mm 12° 3.05cm
3 主要工艺参数
参数 225 mm×1475 mm 9m 68.5 min 50 min 1.7 m/min 2.04 m/min 32.93 m 36.22 m 27.4 m 2 281 min 80% 98% 7231.8 t/d 211.15万吨/年 2台
4金属平衡图
5 钢包回转台
钢包回转台时是连铸机浇钢设备的重要组成部 分,它的作用是将位于受包位置的满载钢包 回转至浇钢位置,准备进行浇注。同时将浇 注完钢水的空包回转至受包位置,准备运走 。其转速为0.7~1.0转/min,换包时间为 0.5~2.0min。本设计采用的是蝶型钢包回转台 ,回转半径2.55m,升降行程0.56m。
一 连铸工艺流程图
ቤተ መጻሕፍቲ ባይዱ
2 连铸机型的选择
连铸机的分类: 立式﹑直弧形、弧形、多点矫 直弧形﹑超低头和水平式等连 铸机,几种机型都有采用,但 是弧形连铸机应用最多
项目 铸坯断面范围 连铸机弧形半径 最大浇铸时间 实际浇铸时间 拉坯速度 理论拉坯速度 冶金长度 铸机长度 液相长度 连铸机流数 浇铸周期时间 连铸机的作业率 连铸机铸坯收得率 连铸机平均日产量 连铸机的平均年产量 连铸机台数的确定
8 中间包车
本设计采用门型中间包车2台承重120吨,升降距离为 400mm,还采用新技术电子秤量系统、保护渣自动下 料装置,同时中间包小车上安装摆动溜槽。中间包车 的运行速度为10~20m/min,最高可达30 m/min,升降 速度为2m/min,中间包更换时间最快也为2~3min。
12 连铸机的形式及设计

连续铸钢是把钢水直接连续地浇铸成铸坯的新工艺, 简称连铸;
主要设备由钢包、中间包、结晶器、结晶器振动装 置、二次冷却和铸坯导向装置、拉坯矫直装置、切 割装置、出坯装置等部分所组成。
2
重要的连铸工艺技术:
• • • • • 高拉速技术: 均匀强冷结晶器、保护渣、液压振动、 电磁制动、拉漏预报、辊道冷却等; 优质洁净钢铸坯生产技术: 大包下渣监测、大容量中间包、保护浇铸、 中间 包多重堰、过滤器、浸入式水口防堵塞、结晶器 液面控制、防卷渣、电磁搅拌、中间包加热、亚 包晶钢铸坯表面裂纹防止、多点矫直技术、二冷 动态控制、喷嘴堵塞自动监测、二冷喷水宽度控 制、压缩铸造、轻压下等; • 近终型连铸取得成功 3
4—单带式连铸机;
1—双辊式连铸机;
2—单辊式连铸机
3—双带式连铸机;
• •
5—轮带式连铸机
同步运动结晶器 连铸机机型
7
连铸机规格的表示方法
弧形连铸机规格表示方法为:aRb-C a—组成1台铸机的机数,机数为1时可以省略; R—机型为弧形或椭圆形连铸机; b—连铸机的圆弧半径,m,若椭圆形铸机为多个 半径之乘积,也表示可浇铸坯的最大厚度: 坯厚= b/(30~36) mm C—表示铸机拉坯辊辊身长度,mm,还表示可容 纳铸坯的最大宽度: 坯宽=C-(150~200) mm
大包下渣检测系统
长水口自动安置
热中间包循环使用 滑板+步进液压缸控制 上装引锭杆 辊缝测量
80t密封中间包
垂直段3m
连浇自动操作(浇铸平台、搅拌站) 非正弦波振动 快速更换结晶器窄边改变浇铸铸坯厚度
钢包吹氩远程自动控制 10点弯曲 分节辊轻压下(17m) 气水喷雾二冷,喷嘴堵塞监测
北京科技大学课程设计连铸车间设计

北京科技大学专业课程设计题目:年产量200万吨板坯连铸生产工艺设计班级:材控XXX学号:XXXXXXXX姓名:XXX学院:材料科学与工程学院专业名称:材料成型及控制工程指导教师:XXX201X年XX月XX日目录一、绪论 (2)二、产品大纲及生产工艺流程 (4)1. 产品大纲 (4)2. 生产工艺流程 (4)三、连铸机设备参数的计算 (5)1. 连铸机类型选择 (5)2. 连铸机流数 (6)3. 中间包容量 (6)4. 设备清单 (7)四、连铸主要工艺参数 (11)1. 浇注温度 (11)2. 浇注时间 (11)3. 拉速 (12)4. 连铸机冶金长度 (12)5. 结晶器长度 (13)6. 铸机的弧形半径 (13)7. 匹配系数计算 (13)五、金属平衡图 (15)六、连铸机主要性能参数 (16)1. 连浇炉数 (16)2. 浇注周期 (16)3. 连铸机的作业率αp (16)4. 金属收得率 (17)5. 连铸机生产能力 (17)6. 生产能力校核 (18)七、参考文献 (19)工艺设计任务书一、学生姓名:XXX 学号:XXXXXXXX二、题目:年产量200万吨板坯连铸生产工艺设计已知:1. 某钢铁厂拟新建一板坯连铸车间,生产的典型钢种为压力容器用钢板16MnR、碳素结构钢板Q195,化学成分是:16MnR钢:C:≤0.20,Si:0.20~0.55,Mn:1.20~1.60,P:≤0. 035,S:≤0.030,Cr:≤0.,30,Ni:≤0.,30,Cu:≤0.30;Cr+Ni+Cu≤0.60;Q195钢:C:≤:0.06~0.12,Si:≤0.30,Mn:0.25~0.50,P:≤0.045,S:≤0.05,Cr:≤0.30,Ni:≤0.30,Cu:≤0.30。
2. 铸坯规格为:200,270mm×1800,2100mm(厚度×宽度)。
3.计划采用的转炉容量为100吨,冶炼时间为40分钟。
连铸工艺、设备--01连铸设备及主要工艺参数

连铸坯形状和尺寸: 小方坯: 70mm × 70mm ~200mm × 200mm 大方坯: 200mm ×200mm ~450mm × 450mm 矩形坯: 150mm × 100mm ~400mm × 630mm 板坯: 150mm × 600mm ~300mm × 2640mm 圆坯: Ф80 ~450mm
AA' A' C ' 0.5D 100 % 100 % 100 % CC ' OC R 0.5D
由于R>>D,故上式可近似写成:
ε=
0 .5 D ×100% R
ε ≤„ε‟ 则: R≥ 0.5 D (m) [ ]
式中 „ε‟:允许延伸率,它主要取决于浇铸钢种、铸 坯温度以及对铸坯表面质量的要求等。对普碳钢和 低合金钢 „ε‟=1.5 ~2.0%
×Vmax )-
2 h ] ∕π
②按铸坯矫直时允许最大延伸率计算铸机半径 原则: 矫直时内弧表面延伸率必须小于允许延伸率 值。 铸坯矫直时,内弧受拉,外弧受压,中心线 未发生变化,断面仍为平面,取C—C’段铸 坯,
铸坯矫直前后的延伸示意图: a—矫直前 b—矫直后
设外弧半径为R,铸坯厚度为D, 则内弧表面延伸率ε:
连铸机的实际作业时间=钢包开浇起至切割 完毕的时间+浇铸准备时间+正常开浇等待 的时间
五.金属收得率 η1=W1∕G1×100% η2 =W2∕W1×100% η = η1η2 = W2∕G1×100% η1—钢水收得率,%; W1—浇铸所得到的全部铸坯量,t; G1—钢水重量,t; η2— 铸坯合格率,% W2— 合格铸坯量,t; η— 金属收得率,%。
L 2
连铸连轧车间设计

摘要本设计首先介绍了薄板坯连铸连轧技术的发展过程,总结和分析了薄板坯连铸连轧生产的实质、特点、类型及关键技术,展望了薄板坯连铸连轧技术的发展趋势,并针对我国薄板坯连铸连轧的生产提出了一些尚待解决的问题和努力方向,接着对本设计做了可行性研究,并根据现有的国内外薄板坯连铸连轧生产线确定了本设计的生产方案、工艺流程及连铸机,加热炉,热连轧机的主要参数。
其次确定了本设计车间热轧部分的各个机架轧机的轧制力、力矩并校核了他们的轧辊、主电机,并均符合设计要求。
最后选择辅助设备,并对车间做了平面的布置、劳动组织及经济指标、环境保护与综合利用设计。
本设计是年产265万吨中薄板连铸连轧车间工艺设计。
车间的产品规格是(1.0~12.7)⨯(1000~1200)mm,产品钢种是合金结构钢、硅钢。
典型产品是30Mn2,4.0⨯1200mm,单卷重20T。
关键词:薄板坯;连铸连轧;工艺设计;合金结构钢和硅钢AbstractThe development of continuous casting & rolling technology for thin slab is firstly introduced in this paper,and its essence,characteristics,types and key techniques are analyzed. The developing trend of continuous casting& rolling technology for thin slab is looked forward to and finally some unsettled problems in our county on continuous casting & rolling technology for thin slab are brought forward. After that has been doing the feasibility study to this design,and accortion to existing domestic and foreign the near net shape continuous casting & rolling production line to determine this design production plan,the technical process and conticastter,the heating furnace,hot company rolling mill patameter .Next had determined this workshop hot rolling partial each rolling mill main pressed the system ,the speed system,the temperature system,has calculated each rolling mill rolling strength,the moment of force and examined their roller,the host electrical machinery,also conformed to the design requirement. Finally selects the supporting facility,and has made the plane arrangement,the labor organization and the economical technical specification,the environmental protection and the comprehensive utilization design to the wordshop.This design is to produce 2.65 million tons of sheet metal continuous casting and rolling plant process design. Workshop product specifications are (1.0 ~ 12.7) (1000 ~ 1200) mm, of alloy steel products, structural steel, silicon steel. Typical products are 30Mn2, 4.0×1200mm, single coil weight 20T.Key word:thin slab, Continuous Casting and rolling, Process Design, Agencies just alloys and silicon steel目录1 综序 (1)1.1薄板连铸连轧技术发展的概况 (1)1.2薄板坯连铸连轧生产工艺 (1)1.3薄板坯连铸连轧工艺的发展及国内发展现状 (4)1.4我国薄板坯连铸连轧技术的发展目标与今后的工作方向 (6)1.5小结 (7)2 可行性研究 (10)2.1国内外钢材市场分析 (10)2.2原料要求 (10)2.3工程条件 (10)3 生产方案选择 (11)3.1选择产品方案的原则 (11)3.2生产规模 (11)3.3产品大纲 (11)3.4典型产品的选择 (12)3.5生产方案的选择标准 (13)3.6生产方案的选择 (13)4 生产工艺流程 (14)4.1指定工艺流程的主要依据 (14)4.2CSP生产线简述 (14)4.3CSP生产线技术参数 (17)5 主要生产设备选择 (18)5.1连铸机设备组成及性能 (18)5.2连铸机设备组成及性能 (18)5.3轧机的选择 (21)5.4加热炉的选择 (23)5.5连铸机生产能力的工程设计和计算 (26)6 工艺计算 (28)6.1压下规程 (28)6.2轧制力的确定 (35)6.3电机和轧辊强度校核 (42)6.4辊型的设计 (48)7辅助设备的选取 (51)7.1高压水除鳞机的选取 (51)7.2事故剪性能参数 (51)7.3热输出辊道和层流冷却设备的选取 (52)7.4卷取区设备的选取 (52)7.5平整分卷机组设备 (56)8 车间年产量计算 (57)8.1连铸机年产量的计算 (57)8.2轧机产量计算 (57)8.3计算板坯成材率 (59)9 车间平面布置 (60)9.1车间布置的原则 (60)9.2生产设备的布置 (60)9.3车间运输量的确定 (64)10 劳动组织及经济技术指标 (66)10.1车间劳动组织 (66)10.2车间技术经济指标 (67)10.3投资概算 (68)10.4盈利及投资回收 (70)11.环境保护与综合利用 (71)结论 (72)参考文献 (73)致谢 (74)1 综序1.1 薄板连铸连轧技术发展的概况薄板坯连铸连轧工艺问世10多年来发展迅速,CSP、ISP、FTSR为代表的各种工艺技术的发展各具特色。
- 1、下载文档前请自行甄别文档内容的完整性,平台不提供额外的编辑、内容补充、找答案等附加服务。
- 2、"仅部分预览"的文档,不可在线预览部分如存在完整性等问题,可反馈申请退款(可完整预览的文档不适用该条件!)。
- 3、如文档侵犯您的权益,请联系客服反馈,我们会尽快为您处理(人工客服工作时间:9:00-18:30)。
第六章 连铸车间设备计算与设计
6.1连铸机的主要工艺参数
连铸机的主要工艺参数是决定连铸机机械设备性能和尺寸的基本前提,也是连铸机车间工艺布置的主要依据,连铸机的主要工艺参数包括钢包允许的最大浇注时间、铸坯断面、拉坯速度、流速、冶金长度、弧形长度。
6.1.1钢包允许的最大浇注时间
为了使钢包内的钢液不致因散热太多而形成包底柠壳,又能充分发挥其延长浇铸时间的潜力,保证浇铸的顺利进行,必须适当的确定不同容量的钢包允许的最大浇铸时间。
可按下列经验公式计算:
max log 0.20.3
G t f -=⨯ 其中: G —钢包容量,t ;
t max —钢包允许浇注的最大时间,min
f —质量系数,主要取决于对浇注温度控制的要求。
对要求严格控制
中心偏析和疏松的钢种,钢水过热度要小,取f =10;
max log 0.20.3
G t f -=⨯ (m i n )60103
.02.0100log =⨯-=
6.1.2铸坯断面
铸坯断面的形状和尺寸可依据下列因素确定:
1)根据轧材品种和规格确定铸坯断面;
2)不同钢种需要不同的压缩比;
3)连铸机生产能力必须与炼钢能力相匹配。
综合以上所述,本设计大方坯连铸机尺寸,铸坯断面的尺寸为 280×325mm 、280×380、φ200~φ280。
6.1.3拉坯理论拉速与工作拉速
1)理论拉速:实际上,连铸机的最大拉速取决于铸坯出结晶器时不致发生变形或拉漏所需的最小坯壳厚度。
V 理论=⎥⎦
⎤⎢⎣⎡224D K •L 式中: V 理论—理论最大拉速,m/min ;
L —冶金长度,本设计取L 为37.5m ;
D —铸坯厚度,m ;
K —综合凝固系数,一般取24~33本设计取为33。
V 理论=⎥⎦⎤⎢⎣⎡224D K •L=min /08.25.3728033422m =⎥⎦
⎤⎢⎣⎡⨯⨯ 2)工作拉速:是指连铸机生产操作中能顺利浇铸,保证铸坯质量相对稳定的平均拉速。
在实际生产中,为改善铸坯质量,使用的工作拉速应小于最大理论拉速。
计算工作拉速:
s
l f V = 式中: V —工作拉速,m/min
l —铸坯横断面周边长,mm
S —铸坯横断面面积,mm
f —速度换算系数m •mm/min ,其值与钢种、铸坯形状、结晶器长度和结构、冷却制度等因素有关,本设计取f=80m •mm/min 。
所以
s l f
V ==80×min /0.1325
2804280m =⨯⨯ 6.1.4连铸机的流数 当一台连铸机只浇注一种断面时,其流数N 的计算公式:
G
=tF υρN
式中: G —钢包容量,t ; t —钢包浇注时间,min 一般t ≤t max ,本设计取t=50min
F —铸坯断面面积,m 2;
ν—该断面的工作拉速,m/min ;
ρ—铸坯的密度,一般取7.6t/ m 3。
流0.389.26
.70.1325.028.050100≈=⨯⨯⨯⨯==ρtFv G N ,因此本设计连铸机为两机3流。
6.1.5铸坯的液相深度和冶金长度
1)铸坯的液相深度:L 1=2max 24K
V D ⨯⨯ 式中: L 1—液相深度,m;
D —铸坯厚度,mm;
V max —最大拉速即理论拉速,m/min;
K —综合凝固系数,mm/min 。
所以 L 1=44.3733408
.228022=⨯⨯m
2)冶金长度:铸机的冶金长度是指以最大拉速浇铸某一断面的铸坯从结晶器的钢液面到钢液完全凝固时的长度。
L ≥L 1 ,本设计L=37.5m
6.1.6连铸机圆弧(外弧)半径的计算R
连铸机的圆弧半径主要是指铸坯弯曲时的外弧半径,
按矫直时铸坯允许的表面延伸率计算:
/2[]R D ε≥ 其中碳素钢可取[]ε=1.5%~2% ,本设计取[]ε=1.5%,
所以,/2[]R D ε≥=,3.9%
5.128.05.0m =⨯ 本设计取弧形半径R=10m 。
6.2 连铸机生产能力的计算
6.2.1连铸机浇注周期计算
连铸浇注周期时间包括浇注时间和准备时间,如下式:
T= t 1+nt 2
式中: T —浇注周期时间,min;
t 1—准备时间,本设计取30;
n —平均连浇炉数,本设计取5炉;
t 2—单炉浇注时间,min;
单炉钢浇注时间由公式:=
N
BD G ρυ计算 式中 N —铸机流数 ; v —工作拉速,m/min;
ρ—铸坯密度,t/3m ;
B —铸坯宽度,m ;
D —铸坯厚度,m;
G —平均每炉产钢水量,t 。
t 2=min 483
0.16.7325.028.0100=⨯⨯⨯⨯ 所以,T= t 1+nt 2=30+5×48=270min 。
6.2.2连铸机生产能力的计算
①连铸机年作业率
η==⨯+%100021T T T %1000
30⨯-T T T 式中: η —连铸机年作业率, %;
T 1—连铸机年准备时间, h;
T 2—连铸机年浇铸时间, h;
T 3—连铸机年非作业时间,h;
T 0—年日历时间,为8760h;
在本设计中选取连铸机年作业率为85% 。
②连铸机铸坯收得率
计算如下:
Y 1 =%1001⨯G
W Y 2 =
%10012⨯W W Y =Y 1Y 2 =%1002⨯G
W
式中:Y 1—铸坯成坯率,%;
W 1—未经检验精整的铸坯量,t;
G —钢水质量,t;
Y 2—铸坯合格率,%;
W 2—合格铸坯量,t ;
Y—连铸坯收得率,%。
本设计中取Y=98%
③连铸机的平均日产量
T
G n Y A 1440==27098551001440⨯⨯⨯=3613t/d 式中:A — 连铸机平均日产量,t/d ;
1440—一天的时间,min;
G — 每炉的平均出钢量,t ;
n — 平均连浇炉数;
Y — 连铸坯的收得率,%;
T — 浇注周期,min 。
④连铸机的平均年产量
P=365A η=365×3613×85%=112万吨/年
⑤连铸机台数的确定 78.110
1121022044
=⨯⨯≈2台 因此,需要两台连铸机 6.3钢包载运设备
本设计连铸作业中运送并承载钢包进行浇注的方式选择双臂式叠型回转台和钢包加盖技术,有如下优点:
①占用浇注平台极小,易于定位,
②钢包更换迅速,便于远距离控制,
③有利于实现多炉连浇和漏钢事故的处理。