简述各设计院的分解炉
分解炉
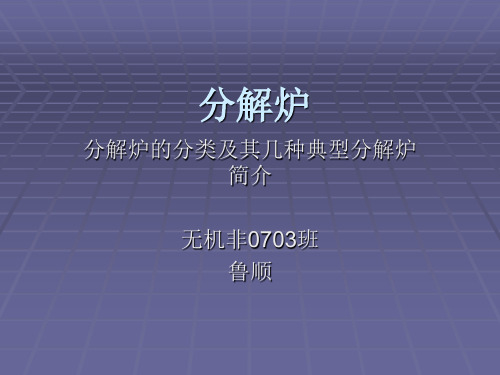
日本神户制钢与日本太平洋水泥株式会社的 DD分解炉及其三种改进型
N-MFC分解炉 N-MFC分解炉全称是:New Mitsubishi Fluidized Calciner。它由日本三菱水泥矿业 株式会社(Mitsubishi Cement Mine Inc.) 和三菱重工(MHI)联合研制开发,其窑系 统属于“流化+悬浮”。
Prepol系列分解炉与Pyroclon系列分解炉
Prepol(普列波尔)预分解窑与 Pyroclon(派洛克朗)预分解窑分别由德国 伯力休斯公司(Polysius AG)与德国洪堡 公司(KHZ)研制开发。 (1) Prepol预分解窑 Prepol预分解窑最早是德国伯力 休斯公司与德国罗尔巴赫(Rohrbach)公 司合作在多波尔(Dopol)型悬浮预热器窑 基础上,增设预分解装置而成。其全称是: Precalcining-Polysius。早期的Prepol分 解炉只有Prepol-AS(Air Separate,有单独 的三次风管)及Prepol-AT(Air Through,三 次风从窑内通过)这两种基本炉型。
下裂解、燃烧,生成H2、CO和CmHn等还 原性气体。然后在生料中的Al2O3及Fe2O3 作催化下,将空气中NOx还原为N2,使预 热器排出废气中NOx含量降低到100~ 150ppm。还原烧嘴燃烧约15%炉用燃料; 第四,三次风从Ⅱ区圆筒二侧径向入炉, 其后直接导入上喷的窑气中,所以炉内无 水平旋流,故其压损较小;第五,两个主 燃烧器在Ⅱ区的三次风管入口上部,燃料 喷入时形成涡流,这样便迅速受热着火且 在富氧条件下立即燃烧;第六,预热生料 通过Ⅲ区下部的下料管入炉,下料处有可 调式撒料箱;第七,在炉内缩口
FLS系列分解炉的三代“喷腾”型炉体结构
天津院TTF分解炉

天津水泥工业设计研究院有限公司(以下简称天津院)目前已有57条5000t/d级生产线相继投入运行,这些生产线均已达到或超过设计指标。
在工程实践、试验及理论研究的基础上,天津院对已投产的大量5000t/d生产线的预分解系统进行了归纳总结和不断的优化改进,在此基础上进行了新型低能耗型第三代5500t/d预分解系统的研究开发,并已应用于工程项目.2 5000t/d烧成系统运行现状天津院的第一条5000t/d预分解系统2002年6月于池州海螺1号生产线投产运行,2002年10月21-2413进行了烧成系统热工标定及考核验收工作,标定结果为产量:5518t/d、烧成热耗2963.62kJ /kg熟料、烧成系统电耗23。
68kWh/t熟料。
此套系统为国内第一条考核验收的国产化的5000t/d 系统,在当时的原燃料条件下,生产线完全达到设计的各项指标要求.随着5000t/d生产线大量的普及应用,很多生产线设计阶段的原燃料与实际使用的差别很大,部分生产线实际运行指标较池州考核指标有一定的差距.为此,天津院在大量实践反馈的基础上进行了针对性的优化改进。
从实践情况反映,改进后的生产线运行状况有一定幅度的改善。
表1为实测部分生产线在产量为5500t/d左右时预热器的出口温度及压力分布情况。
表1 部分5000t/d生产线预热器出口温度及压力3 第三代5500t/d预分解系统的研究开发及应用为了从根本上解决5000t/d烧成系统对原燃料的适应性较差的问题,天津院进行了新型低能耗型5500t/d烧成系统的研究开发,即在保持回转窑规格不变的前提下,通过采用优化改进的第三代预分解系统、高效篦冷机及燃烧器等烧成技术与装备使整个烧成系统能力达到额定5500t/d,性能指标达更优,其主要技术方案及特点如下:3.1 5500t/d系统设计指标烧成系统总体设计指标如下:烧成热耗:2967.8 kJ/kg熟料;预热器出口温度:305±15℃;出口压力:-4800±300Pa;预热器出口含尘浓度:〈65g/m3(标);预热器出口NOx:<500 mg/m3(标)(10%O2)。
分解炉的工作原理

分解炉的工作原理
分解炉是一种用于分解化学物质的设备,其工作原理基于高温和氧化条件下的热分解反应。
以下是分解炉的工作原理的详细说明:
1. 高温环境:分解炉内部设置了加热器,通过加热器提供高温环境。
高温是分解炉正常工作的基础,因为热分解反应需要足够高的温度才能进行。
2. 封闭空气供应:分解炉通常通过控制进气与出气的比例来控制内部气氛。
在分解炉工作期间,炉内通常会为了确保准确的反应条件而采用封闭空气供应系统,这有助于控制内炉气氛,以实现所需的分解反应。
3. 热分解反应:被投入到分解炉中的化学物质在高温环境中发生热分解反应。
热分解是一种化学反应,通过加热将化学物质分解成更简单的化学物质,通常伴随着生成气体、废渣或其他分解产物的释放。
4. 控制系统:分解炉通常配备有针对炉内温度、进气和出气流量、反应时间等参数的控制系统。
控制系统可以根据需要调整和维持适当的反应条件,以确保分解反应的效果和质量。
5. 产物收集和处理:分解炉将化学物质分解后,产生的气体、废渣或其他产物需要被收集和处理。
根据分解炉运行的具体需求,将副产物进行回收或进一步处理,以便达到生产要求或环保要求。
总结:分解炉通过提供高温和氧化条件,将化学物质加热至分解温度,然后进行热分解反应。
通过控制进气、出气、温度等参数,实现对分解反应的控制。
产物需要被收集和处理,以完成整个分解炉的工作过程。
分解炉

早期开发的分解炉,大多主要依靠 上述“四种效应”中的一种。后来,各 种类型的分解炉在技术上相互渗透,所 以目前的分解炉大都趋向于采用以上各 种效应的“综合效应”,以力求优化分 解炉内的热量传递、质量传递、动量传 递和化学反应过程(简称“三传一反” 过程)。即遵循“以物料的高度分散为 前提,以燃料的高效与完全燃烧为关键, 以生料的有效分解为目的,以环境保护 与社会责任为己任!”的原则来改进与 完善分解炉。
DD分解炉及其窑系统的主要特点为: DD分解炉及其窑系统的主要特点为: 第一,其内分为四个区段:Ⅰ 第一,其内分为四个区段:Ⅰ区为脱氮还 原区,Ⅱ区为生料分解及燃料燃烧区,Ⅲ 原区,Ⅱ区为生料分解及燃料燃烧区,Ⅲ 区为主燃烧区,Ⅳ 区为主燃烧区,Ⅳ区为完全燃烧区;第二, 上升烟道有缩口让窑气喷入炉内,缩口喷 速为30~40m/s,以获得窑气量与三次风量 速为30~40m/s,以获得窑气量与三次风量 之间的平衡,也能阻止生料直接落入窑中, 还可加速化学反应。其简单的结构与工艺 布置有利于减少漏风和减轻炉内结皮以及 排除其他障碍物;第三, Ⅰ区侧壁装设的 数个还原烧嘴,使燃料在缺氧的情况
日本神户制钢与日本太平洋水泥株式会社的 DD分解炉及其三种改进型
N-MFC分解炉 MFC分解炉 N-MFC分解炉全称是:New Mitsubishi MFC分解炉全称是:New Fluidized Calciner。它由日本三菱水泥矿业 Calciner。它由日本三菱水泥矿业 株式会社(Mitsubishi 株式会社(Mitsubishi Cement Mine Inc.) Inc.) 和三菱重工(MHI)联合研制开发,其窑系 和三菱重工(MHI)联合研制开发,其窑系 统属于“流化+ 统属于“流化+悬浮”。 社 日 本 三 菱 分 株 解 式 炉 会 N-MFC
分解炉工作原理

分解炉工作原理
分解炉是一种将有机物质快速分解为无机物质的设备。
其工作原理主要涉及两个过程,即热解和燃烧。
热解是指在高温下,通过热量作用使有机物质分解为较简单的无机物质的过程。
分解炉内部的温度可以达到数百摄氏度到千摄氏度,这种高温条件可以促使有机物质的分子键断裂。
在分解炉中,有机物质通常通过一个加热区域,被加热至热解温度。
在加热的同时,有机物质会发生热解反应,产生气体、液体和固体产物。
这些产物中的气体通常是能够被进一步利用的,如用作燃料或化学原料。
燃烧是指将产生的气体进一步燃烧,以提供所需的热量维持炉内的温度。
此过程有助于保持炉内温度的稳定,并提供维持热解反应所需的能量。
燃烧通常使用附加的燃料,例如天然气或燃油。
这些燃料通过燃烧与产生的气体混合,释放大量的热能。
这种热能可以用来保持炉内温度,并提供分解炉所需的热解反应。
综上所述,分解炉主要依靠热解和燃烧过程来将有机物质分解为无机物质。
通过高温的热解过程,有机物质的分子键断裂,产生气体、液体和固体产物。
而燃烧过程提供了分解炉所需的热能,维持炉内的温度并促进热解反应的进行。
第六章 窑外分解炉详解
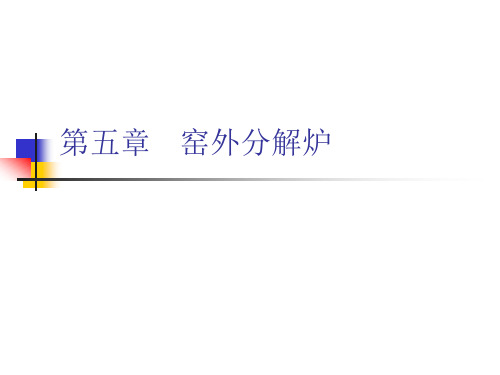
(4)、全燃烧区(Ⅳ区)炉顶部圆筒体,主 要作用是使未燃烧的10%左右的燃料继续燃烧 并促进分解。 气体和生料通过Ⅲ区和Ⅳ区间缩口向上喷腾直 接冲击到炉顶棚,翻转向下到出口,使气料搅 拌和混合,达到完全燃烧和热交换。 DD分解炉设置气料反弹室,有利于气料产生搅 拌和混合,增加了气料在炉内的停留时间,达 到完全燃烧和改善热交换,防止炉内的偏流现 象。炉下对称的三次风管以及顶部两根出风管, 都是向炉心径向安装,有利于产生良好的喷腾 运动和降低炉内压力。 此外4个主喷嘴,从三次风管上部两侧直接喷 入三次氧气流中,点火条件好,适合劣质煤。
在NF分解炉的基础上改进,二者对比如图 (1)、将喷油嘴下移至旋流室顶部,以一 定角度向下吹。直接吹入三次风中,其含氧 浓度高,易点火。 (2)、喂料口下移,分为两部分,一部分 在到窑尾的上升烟道内、炉内锥体下部。 (3)、取消了SF分解炉的缩口,采用加生 料来平衡窑与分解炉内的压力。
C-SF分解炉
二、喷腾效应
ห้องสมุดไป่ตู้
喷腾效应是分解炉或预热器内气流 作喷腾运动, 使物料滞后于气流的效应。 气流的喷腾作用造成了由炉中心向边缘的回旋 运动,在喷腾口,进入气流的物料及煤粉被气 流吹起、悬浮,有的被直接抛向炉壁,沿壁下 坠到喉口再被气流吹起而作大循环,较小的颗 粒,有的被气流带走,有的到达炉壁后进入滞 流层,处于炉上方直接被气流带走,处于炉下 方的再进入喷腾层而入气流,而使物料滞后于 气流 。
生料也分两路入炉。生料约有75%从炉 圆筒部分与三次风切线进口的交界处进 入,使生料和气体充分混合并在上升气 流作用下形成喷腾床。生料随气流流动 在喷腾床停留一定时间后,进入涡流室, 并通过排气口进入最低一级的旋风筒内。 同时为了防止入炉管道内的黏结堵塞, 有25%从烟道上部加入,以吸收烟气的 热,如果烟气温度不高,加入生料的量 可相应减少。
cdc分解炉
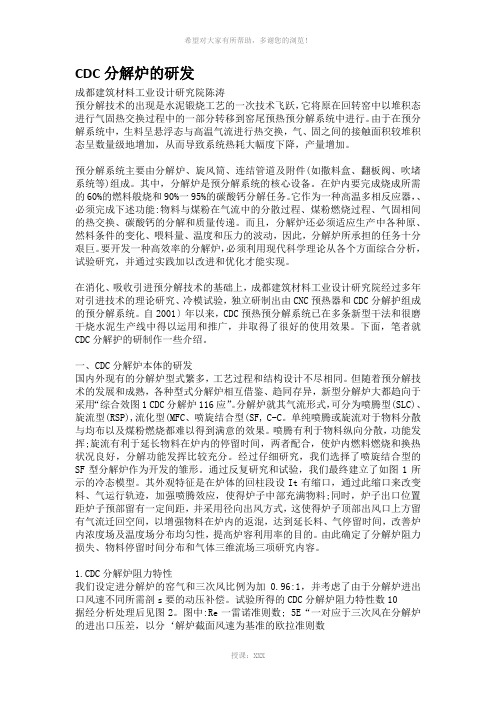
CDC分解炉的研发成都建筑材料工业设计研究院陈涛预分解技术的出现是水泥锻烧工艺的一次技术飞跃,它将原在回转窑中以堆积态进行气固热交换过程中的一部分转移到窑尾预热预分解系统中进行。
由于在预分解系统中,生料呈悬浮态与高温气流进行热交换,气、固之间的接触面积较堆积态呈数量级地增加,从而导致系统热耗大幅度下降,产量增加。
预分解系统主要由分解炉、旋风筒、连结管道及附件(如撒料盒、翻板阀、吹堵系统等)组成。
其中,分解炉是预分解系统的核心设备。
在炉内要完成烧成所需的60%的燃料般烧和90%一95%的碳酸钙分解任务。
它作为一种高温多相反应器,、必须完成下述功能:物料与煤粉在气流中的分散过程、煤粉燃烧过程、气固相间的热交换、碳酸钙的分解和质量传递。
而且,分解炉还必须适应生产中各种原、然料条件的变化、喂料量、温度和压力的波动,因此,分解炉所承担的任务十分艰巨。
要开发一种高效率的分解炉,必须利用现代科学理论从各个方面综合分析,试验研究,并通过实践加以改进和优化才能实现。
在消化、吸收引进预分解技术的基础上,成都建筑材料工业设计研究院经过多年对引进技术的理论研究、冷模试验,独立研制出由CNC预热器和CDC分解护组成的预分解系统。
自2001〕年以来,CDC预热预分解系统已在多条新型干法和很磨干烧水泥生产线中得以运用和推广,并取得了很好的使用效果。
下面,笔者就CDC分解护的研制作一些介绍。
一、CDC分解炉本体的研发国内外现有的分解炉型式繁多,工艺过程和结构设计不尽相同。
但随着预分解技术的发展和成熟,各种型式分解炉相互借鉴、趋同存异,新型分解炉大都趋向于采用“综合效图1 CDC分解炉116应”。
分解炉就其气流形式,可分为喷腾型(SLC)、旋流型(RSP),流化型(MFC、喷旋结合型(SF, C-C。
单纯喷腾或旋流对于物料分散与均布以及煤粉燃烧都难以得到满意的效果。
喷腾有利于物料纵向分散,功能发挥;旋流有利于延长物料在炉内的停留时间,两者配合,使炉内燃料燃烧和换热状况良好,分解功能发挥比较充分。
分解炉的工作原理与结构

分解炉的工作原理与结构分解炉是一种用于处理化学物质的装置,通过在高温高压下分解原料,将其中的成分分离出来。
分解炉能够广泛应用于各种领域,如石油化工、金属冶炼、电子工业等。
本文将详细介绍分解炉的工作原理与结构。
一、工作原理分解炉的工作原理是通过提高原料的温度和压力,使得原料分子间相互碰撞,产生裂解反应分解成小分子化合物,最终将其分离出来。
一般来说,分解炉使用碳、氧气、氮气等气体作为燃料,将其加热到高温高压状态,然后通过反应管将原料送入炉内进行分解。
分解后产生的气体通过分离器进行分离,便可得到所需要的成分。
二、结构组成1. 爆炸室爆炸室位于分解炉的中部,其结构一般为圆柱形或矩形,内部有一定的燃烧空间。
爆炸室的作用是将气体和固体处理物料进行混合并提高其温度和压力。
爆炸室一般由耐火材料制成,以防止它被爆炸所摧毁。
2. 进料系统进料系统用于将处理物料送入分解炉中。
它通常包括料斗、输送机、加热炉、进气管道、反应管等。
料斗和输送机用于将原料输送到加热炉中,加热炉则用于提高物料的温度和压力,以加速裂解反应。
进气管道将气体送入爆炸室,反应管则将处理物料输送到爆炸室中进行反应。
3. 分离系统分离系统用于将分解后的气体和固体分离出来。
它通常包括冷却器、分离器和收集器。
冷却器用于将高温的气体冷却成液态,以便于分离。
分离器一般采用物理或化学方法将气体或固体的成分分离。
收集器则用于收集所需要的产品。
4. 控制系统控制系统由自动控制器、传感器和执行器组成。
自动控制器负责对分解炉的工作状态进行监测和控制,传感器则将相关数据反馈给自动控制器进行处理,执行器负责执行自动控制器下达的指令。
三、总结分解炉是一种非常重要的化工装置,其工作原理和结构与炉型密切相关。
分解炉的主要作用是将原材料分解成所需的成分,并将不需要的成分进行分离。
分解炉的结构一般由爆炸室、进料系统、分离系统和控制系统组成。
通过对分解炉的工作原理和结构的深入了解,我们可以更好地运用和管理它,使其在化工领域中扮演更加重要的角色。
简述各设计院的分解炉

分解炉在窑外分解系统起着很重要的作用,自1971年第一台窑外分解系统投产,从而开始水泥工业大规模生产开始,分解炉的形式有很多。
从分解炉内的气流运动来看,可归纳为四种基本型式,即:涡旋式、喷腾式、悬浮式和流化床式。
早期开发的分解炉,多以上述四种运动型式之一为基础,使生料和燃料分别依靠“涡旋效应”、“喷腾效应”、“悬浮效应”和“流态化效应”分散于热气流中,利用物料颗料之间在炉内流场中的相对运动,实现高度分散、均匀混合和分布、迅速换热,以达到提高燃烧效率,传热效率和入窑生料碳酸盐分解率的目的。
分解炉按照设计单位国内有以下常见几种:RSP 来源与日本小野田TDF、TSD、TD、TSD、TWD、TTF、TFD天津院CDC成都院NST-I NC-SST南京院具体形式和特点如下:TDF型分解炉TDF分解炉是天津水泥院在引进日本DD炉技术的基础上,针对中国燃料特点,研制开发的一种双喷腾分解炉(Dual Spout Furnace),如下图1-1所示。
TDF炉技术特点如下:①分解炉坐落窑尾烟室之上,炉与烟室之间缩口在尺寸优化后可不设调节阀板,结构简单;②炉中部设有缩口,保证炉内气固流产生第二次“喷腾效应”;①三次风切线入口设于炉下锥的上部,使三次风涡旋入炉;炉的两个三通道燃烧器分别设于三次风入口上部或侧部,以便入炉燃料斜喷入三次风气流之中迅速起风燃烧;②在炉的下部圆筒体内不同的高度设置四个喂料管入口,以利物料分散均布及炉温控制。
⑤炉的下锥体部位的适当位置设置有脱氮燃料喷嘴,以还原窑气中的氮,满足环保要求;⑥炉的顶部设有气固流反弹室,使气固流产生碰撞反弹效应,延长物料在炉内滞留时间;⑦气固流出口设置在炉上椎体顶部的反弹室下部;⑧由于炉容较DD炉增大,气流、物料在炉内滞留时间增加,有利于燃料完全燃烧和碳酸盐分解。
TSD分解炉TSD型炉是带旁置旋流预燃室的组合式分解炉(Combination Furnace with spinpre-burning Chamber)见图1-2炉TSD炉技术特点如下:①设置了类似RSP型炉的预燃室;②将DD型炉改造为类似MFC型炉的上升烟道或RSP型窑的MC室(混合室),作为TSD型炉炉区的组成部分,并扩大了DD炉型的上升烟道容积,使TSD炉具有更大的适应性;③该炉可用于低挥发分煤及质量较差的燃料。
分解炉分类及发展
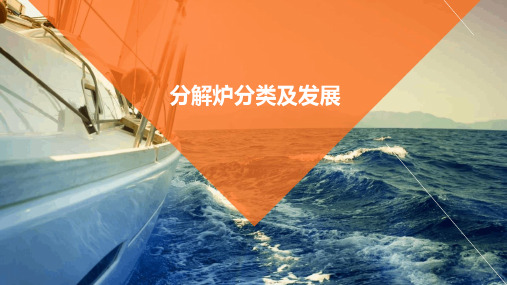
科研人员使用分解炉对样品进行高温分解,以获取纯净的物质或进行元素分析。
环保领域
废物处理
分解炉可用于处理工业废物和城市垃圾,通过高温分解将有害物质转化为无害物 质或降低其毒性。
有机废弃物资源化
利用分解炉高温分解有机废弃物,将其转化为可再利用的资源和能源,如生物燃 气、生物炭等。
04 分解炉的未来发展趋势
按功能用途分类
水泥分解炉
用于水泥熟料的生产,将 原料高温分解成氧化钙、 二氧化硅等物质。
钢铁分解炉
用于钢铁冶炼过程中,将 铁矿石高温分解成铁水和 渣。
化工分解炉
用于化工生产过程中,将 原料高温分解成所需的化 学品。
02 分解炉的发展历程
ቤተ መጻሕፍቲ ባይዱ
早期阶段
分解炉的雏形
这一阶段主要是分解炉的初步探 索和试验阶段,技术尚未成熟, 主要应用于小型实验和初步工业 应用。
节能化
节能化
随着环保意识的提高和能源价格的上涨,节能已成为工业领域的重要发展方向。分解炉作为工业生产中的重要设 备,其节能化改造势在必行。新型分解炉将采用先进的节能技术和设备,如余热回收、高效燃烧器等,以降低能 耗和减少能源浪费。
节能化
节能化的发展趋势要求企业在生产过程中注重节约能源和资源,提高能源利用效率。这不仅有助于降低生产成本, 还有利于减少环境污染和促进可持续发展。
03 分解炉的应用领域
工业领域
工业生产
分解炉在工业生产中主要用于分解各 种物质,如矿石、废塑料等,以提取 有价值的成分或进行废物处理。
化工合成
分解炉也可用于化工合成领域,如合 成新材料、高分子化合物等,通过分 解原料来制备所需物质。
科研领域
实验研究
窑外分解窑分解炉种类和结构
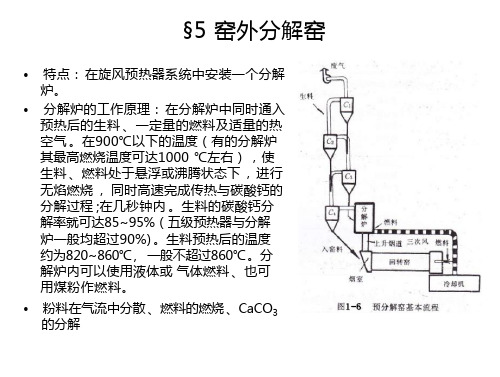
• (7)Pyroclon型与Prepol型分解炉 • PyrocIon系Pyro(高温)与Cyclon (旋风筒)两字缩写的组合 。系德国洪堡公司所开发。
Prepol系Precalcining (预分解)与Polysu is(公司)两字缩写的组合,为德国伯力鸠斯 司所开发。
• 这两种分解炉基本上大同小异,其共同的特点是 :
• ① 不设专门的分解炉,利用窑尾与最低一级旋风筒之间的上升烟道,适当延长加高而 作为分解炉用 。因此结构简单, 阻力小。
• ② 燃料与经预热后生料均自上升烟道下部喂入,力求在气流中充分分散, 因此最好沿 管道面能形成旋涡流动。
• ① 分解 底部设有一截面不大的多孔板,用3~5kPa高压风机鼓入流化风(占 总风量8 10%), 建立生料与燃料的密相流化床区 ; 煤粉喷咀设在流化床上 部,C4来的生料自流化床侧面加入,混合非常均匀,燃烧 、换热 、分解反应 开始进行,物料在床内停留时间达2min之久。
• ② 三次风在分解炉下锥底部分,送入到流化料层上部,切向进入,形成一定的 旋转流,携带流化生料形成了涡流床区 。充足的空气,使反应激烈进行。
• (4)RSP分解炉
• RSP分解炉(见图1- 10)是日本小野田公司开发 , 其主要特点是: • ① 分解炉由三部分组成 : 即
• 旋流燃烧室(SB) ——三次风呈旋流运动进入,主要是使燃料分散和部分 燃烧 ;
• 旋流分解室(SC) ,三次风吹送来的热生料和煤粉在此室也呈旋流运动 , 使煤粉进一步燃烧 、生料受热和部分分解 ;
分解炉

四、常见故障与处理办法
现象 产生原因 处理方法 注意事项 1、检修期间认 真检查炉内各部 位形状及尺寸 2、一些重要部 位如溜管、撒料 箱修补后一定要 拆模验收 3、有燃烧器的 分解炉一定要根 据情况定期更换 1、分解炉内部 1、合理调整分料挡板,让物 有局部高温现象 料均匀分布在炉内 2、煤质变化大、 2、适当煤质变化及时调整用 全硫高、挥发份 风比例,通常可关小三次风挡 高、发热量大 板和燃烧器用风 3、各部位结构 3、检查各撒料箱和溜管形状 发生变化、物料 及时按图恢复 分散度不好或分 4、操作上炉内温度应不大于 料挡板卡死 900℃,炉出口温度应小于 4、操作原因, 880℃,只要入窑分解率在92长期高温 95%之间温度越低越好。
4、分解炉用煤调节控制
预分解窑的发热能力来源于两个热源,即窑 头和分解炉,对物料的预烧主要由分解炉完成, 熟料的烧结主要由回转窑来决定。因此在操作中 必须做到以炉为基础,前后兼顾,炉窑协调,确 保预分解窑系统的热工制度的合理与稳定。调节 分解炉的喂煤量,控制分解炉出口温度在900℃ 左右,确保炉内料气的温度范围,保证入窑生料 的分解率。
炉温控制
由于回转窑内燃料燃烧是受扩散控制的,增减10~ 20℃对于燃料的燃烧影响是甚微的。但在分解炉内则明 显不同,如有的分解炉容积偏小,煤粉燃烬时间不足,以 至还原气氛重,而降低分解炉的温度,减少分解炉用煤量, 以图改变煤粉燃烧不完全、还原气氛的问题,但往往是 事与愿违。因在不减产量的情况下,分解炉用煤减少,分 解炉温度降低,煤的燃烧速度随温度降低而迅速下降,煤 粉始终是燃烧不完全。适当增大分解炉的容积已成为一 个发展动向。在分解炉偏小煤质差的情况下,可适当降 产量,而不宜降低分解炉的温度。
二 、 分 解 炉 的 主 要 设 计 参 数
分解炉的工作原理与结构(二)

分解炉的工作原理与结构(二)引言:分解炉作为一种常见的工业设备,在化工、石油、能源等领域具有广泛的应用。
本文将进一步介绍分解炉的工作原理与结构,以帮助读者更好地了解和应用分解炉。
正文:1. 燃料供给系统:- 燃料输送管道:用于输送燃料到燃料预处理设备。
- 燃料预处理设备:对燃料进行预处理,包括脱硫、脱氮等过程。
- 燃料喷嘴:将燃料导入燃烧室,确保燃料均匀燃烧。
2. 空气供给系统:- 空气进气管道:将空气引入燃烧室,与燃料进行充分混合。
- 空气预处理设备:对空气进行预处理,包括除尘、降温等处理。
- 风机:提供足够的风力将空气送入燃烧室。
3. 反应炉:- 燃烧室:燃料和空气混合燃烧的区域,产生高温高压的气体。
- 反应室:气体在此处进行分解反应,产生所需的产物。
- 冷却室:将分解后的气体冷却至适宜的温度,以便后续处理。
4. 热交换系统:- 冷却水系统:通过冷却水对炉体进行冷却,同时回收部分热量。
- 加热系统:通过燃料燃烧产生的热量对炉体进行加热,保持反应温度。
- 废热回收系统:对废气进行热回收,提高能源利用效率。
5. 控制系统:- 温度控制:监测和调节反应炉内的温度,确保反应过程的稳定性。
- 压力控制:监测和调节反应炉内的压力,确保操作的安全性。
- 流量控制:对燃料和空气的流量进行控制,保证燃烧和反应的平衡。
总结:通过对分解炉的工作原理与结构进行详细介绍,我们了解到燃料供给系统、空气供给系统、反应炉、热交换系统和控制系统五个大点对于分解炉的工作起到重要作用。
深入了解和熟练运用分解炉,将为化工、石油、能源等领域的生产提供更高效的工具和技术支持。
分解炉的热工性能
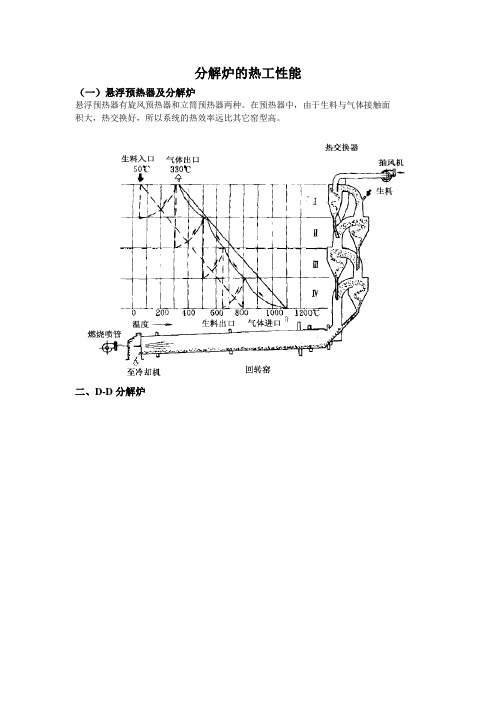
分解炉的热工性能(一)悬浮预热器及分解炉悬浮预热器有旋风预热器和立筒预热器两种。
在预热器中,由于生料与气体接触面积大,热交换好,所以系统的热效率远比其它窑型高。
二、D-D分解炉由主燃烧区排出的废气在后续的燃烧区内完全燃烧后进入四级或五级旋风筒。
经预热的生料从三级或四级旋风筒进入D-D 炉的燃料分解、燃烧区,经过预热分解后通过五级旋风筒进入窑内。
与窑尾直接连接的D-D炉喉部是个调节平衡的装置,可使回转窑的燃烧气体量和通过三次风管的高温空气达到平衡。
同时,由于向D-D炉喂入的生料在还原区内形成喷腾层,D-D 炉下部气体中的生料浓度增高,因而使进入炉内的窑尾废气温度急剧下降,防止炉底形成结皮。
窑尾气中的No x通过喉部进入还原区,在辅助喷咀喷入的燃料所产生的还原气氛中被还原。
在燃料分解、燃烧区和主燃烧区内,辅助燃烧喷咀是装在三次空气入口附近,燃料在炉内旋流中瞬间进行分解、气化和燃烧。
此时,燃料燃烧产生的热量由于被悬浮在D-D炉内的高浓度生料所吸收,使生料迅速进行分解反应。
因此,热交换性能极高,并且没有一般辉焰燃烧时出现的高温区,炉内温度均匀,能保持800-900℃较低温度。
由于这种燃烧机理,D-D 炉本身产生的No x量相当低,特别是由于主燃烧区和后燃烧区之间的缩口部的节流作用和通过喉部的上升气流喷腾到后燃烧区的顶盖后而翻转进入四级或五机旋风筒的作用,故能使夹带于气体中的生料与气体混合,搅拌的效果显著提高。
在较低的过剩空气下就能使燃料完全燃烧。
D-D炉和回转窑用燃料比例仍为6:4,生料在炉内予热分解后,分解率可达90%-95%。
三分解炉的工艺性能分解炉所担任的工艺过程主要是碳酸盐的分解过程。
在实际生产过程中,影响生料碳酸盐分解的因素很多,情况也很复杂。
但主要因素是炉内的分解温度,物料在炉内均匀分布程度和停留时间以及生料的物理性能。
(1)生料中碳酸盐反应的特性CaCO3的分解反应方程式为:这一过程是可逆的反应过程,根据系统温度和周围介质中的CO2的分压不同,反应可向任何一个方向进行。
分解炉的工作原理与结构
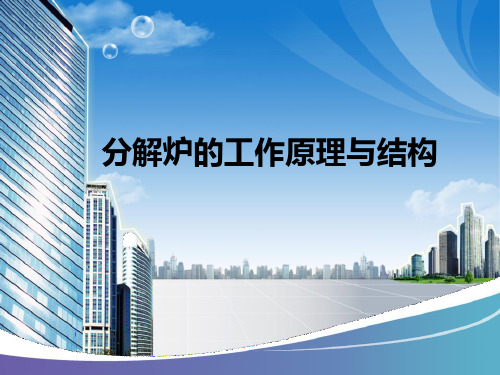
2.1旋流式分解炉
• 旋流式分解炉的结构比较简单.典型的旋流式分解炉其结 构如图,它是由上旋流室、下旋流室和反应室所构成的。 内表面镶砌有耐火混凝土与耐火砖,反应室中部设有l~3 个燃料喷嘴,成30°角向下喷射燃料。
2.1旋流式分解炉
• 四平型分解炉,以重油为燃料,分解炉用油量占总耗油 量的50%左右,炉内平均气体温为900℃左右。经过预热 分解后物料入窑温度可达860~895℃,入窑生料分解率则 达80~90%,热耗为4810千焦/公斤熟料左右。产量比同 规格带悬浮预热窑增加一倍多。 • 日本SF型分解炉,其结构与生产流程,与四平型分解炉 基本相同,不过其窑尾废气温度较高(约1100℃)和三次空 气温度较高(750~780℃),热利用情况较好,所以熟料单 位热耗较低,仅为3140~3280千焦/公斤熟料。 • 这种分解炉的主要缺点是:物料与燃料在炉内分布不均 匀,涡流室两侧易于结皮等。
2.新型分解炉介绍
• 分解炉自七十年代问世以来,得到了迅速的发展,到目前为止已经出 现了很多种型式,根据其结构与工作原理的不同,大致可以分为以下 四种类型。 • a.旋流式分解炉 • 这种分解炉的特点是炉内的气体与物料作旋流运动。如我国的四平 型和日本的SF型、NSF型分解炉属于这一类型。 • b.喷腾式分解炉 • 这种分解炉内物料的悬浮和运动,是靠气体的喷吹而形成的。我国 的本溪型和日本的KSV型,丹麦的史密斯型等分解炉属于这一类型。 • c.沸腾式分解炉 • 这种炉的特点是:物料在流化床上处于沸腾状态。日本的MFC型分 解炉属于这一类型。 • d.带预热室的分解炉 • 我国太原型分解炉和日本的RSP型分解炉属于这一类型。
2.4带预燃室的分解炉
• 为了使分解炉燃烧更加稳定,有的分解炉带有预燃室 。RSP型分解炉就是其中的一种。这种分解炉的构造较 为复杂,它是由分解炉(简称S炉)和混合室所组成。
分解炉的分类

分解炉的分类按分解炉与窑的连接方式大致分为三种类型1.同线型分解炉这种类型的分解炉直接坐落在窑尾烟室之上。
这种炉型实际是上升烟道的改良和扩展。
它具有布置简单的优点,窑气经窑尾烟室直接进入分解炉,由于炉内气流量大,氧气含量低,要求分解发炉具有较大的炉容或较大的气、固滞留时间长。
这种炉型布置简单、整齐、紧凑,出炉气体直接进入最下级旋风筒,因此它们可布置在同一平台,有利于降低建筑物高度。
同时,采用“鹅颈”管结构增大炉区容,亦有利于布置,不增加建筑物高度。
2.离线型分解炉这种类型的分解炉自成体系。
采用这种方式时,窑尾设有两列预热器,一列通过窑气,一列通过炉气,窑列物料流至窑列最下级旋风筒后再进入分解炉,同炉列物料一起在炉内加热分解后,经炉列最下级旋风筒分离后进入窑内。
同时,离线型窑一般设有两台主排风机,一台专门抽吸窑气,一台抽吸炉气,生产中两列工况可以单独调节。
在特大型窑,则设置三列预热器,两个分解炉。
3.半离线型分解炉这种类型的分解炉设于窑的一侧。
这种布置方式中,分解炉内燃料在纯三次风中燃烧,炉气出炉后可以在窑尾上升烟道下部与窑气会合(如RSP、MFC等),亦可在上升烟道上部与窑气会合(如N-MFC. SLC-S等),然后进入最下级旋风筒。
这种方式工艺布置比较复杂,厂房较大,生产管理及操作亦较为复杂。
其优点在于燃料燃烧环境较好,在采用“两步到位”模式时,有利于利用窑气热焰和防止粘结堵塞。
中国新研制的新型分解炉亦有采用这种模式的。
分解炉内的气流运动,有四种基本型式:即涡旋式、喷腾式、悬浮式及流化床式。
在这四种型式的分解炉内,生料及燃料分别依靠“涡旋效应”、“喷腾效应”、“悬浮效应”和“流态化效应”分散于气流之中。
由于物料之间在炉内流场中产生相对运动,从而达到高度分散、均匀混合和分布、迅速换热、延长物料在炉内的滞留时间,达到提高燃烧效率、换热效率和入窑物料碳酸盐分解率的目的。
分解炉作为预分解窑的“第二热源”,承担着繁重的燃料燃烧和换热任务。
分解炉

日本小野田RSP分解炉炉型结构:由预燃室SB,分解室SC和混合室MC组成;与窑联接方式:离线旁置型,SC室单独设置,MC室通过缩口与烟室联接;特点:SB:10~15%三次风进上部旋流腔,作为煤粉燃烧的外风,与煤粉混合着火,起助燃和稳火作用;SC:85~90%三次风吹送热生料,将C3喂入的热生料分散到SC室内,在旋流的作用下,SC室边壁形成防止过热引起粘料的低温保护区,中心形成高温的强化燃烧区。
SC室操作不合适,会引起局部过热导致粘结或烧坏设备。
混合室MC从SC室下端以旋转气流夹带生料进入混合室,与窑尾的喷腾窑气相混合,分解率达90%以上。
该炉对燃煤适应性较强,可烧劣质煤及无烟煤,但结构复杂,阻力较高。
天津院设计的TSD分解炉是带旁置预燃室分解炉,旁置预燃室类似于RSP的SC室,预燃室可以高温操作,低挥发份煤能较好地着火、稳燃和快速燃,大大缩短煤粉燃尽所需的时间。
该炉适合于烧低挥发份的无烟煤。
1、DD、TD、TDF属于同一类,一代更比一代好,双喷腾,脱硝。
2、RSP、TSD相似,都是由预燃室SB,分解室SC和混合室MC组成。
是唯一明焰燃烧的分解炉。
以前RSP炉的MC室设计太小了,对MC的混合作用认识不足,后来国内天津院的TSD的主炉TD比MC合理多了。
3、CSF、TWD、CDC相似。
都是涡流喷腾型。
4、NMFC、TFD都是采用流态化床。
两步到位,一般是离线型布置。
5、Prepoel和Pyroclon都是属于管道式分解炉,旋喷结构。
6、KSV与DD炉相似,但三次风入炉方式不同,一是切线,一是轴线CDC是属于涡旋喷腾(双喷腾)结合型分解炉。
有两种型式,一种是在线,适合烧烟煤,还有一种是半离线型,就是在CDC主炉旁加了一个旁置预燃炉,适合烧无烟煤。
不管怎样说,成都院的CDC炉设计还是非常合理的,物料与气体的停留时间都比较长,石灰石的分解效率还是比较高的。
CDC炉就是NSF炉的变形,把出口改成的U形管,从而解决了用低质煤时反应时间问题。
分解炉

预分解技术一.预分解技术的发展预分解窑自20世纪70年代初期诞生以来,至今已经历了四个发展阶段。
⑴第一阶段。
20世纪70年代初期到中期。
为预分解技术的诞生和发展阶段。
德国多德豪森(Dottenhausen)水泥厂于1964年用含可燃成分的油页岩作为制造水泥原料的组分。
为了避免可燃成分在低温部分过早挥发,他们在悬浮预热器的中间喂入含油页岩的生料,提高生料的入窑分解率,开创了预分解技术的先例。
但是真正使用高级燃料在分解炉内作为第二热源的预分解窑,则是从1971年开始。
因此,预分解窑的诞生,应是日本IHI公司和秩父水泥公司共同开发的第一台SF窑(Suspension Preheater-Flash Furnacel)。
第一台SF窑诞生以后,日本各种类型的预分解窑相继出现(三菱公司的MFC炉-1971年;小野田水泥公司的RSP炉-1972年;川崎与宇部水泥公司共同开发的KSV炉-1974年等等)。
分解炉都是以重油为燃料。
⑵第二阶段。
20世纪70年代中、后期,为预分解技术的完善、提高阶段。
1973年国际爆发石油危机之后,油源短缺,价格上涨,许多预分解窑以煤代油。
原来以石油为燃料的分解炉难以适应,从而通过总结、改进,各种第二代、第三代的改进型分解炉应运而生。
例如:高径比(H/D)增加的MFC炉及N-MFC炉等的出现即为典型代表。
这些改进型炉不仅增加了炉容,在结构上也有很大改进。
为了提高燃料燃尽率,延长物料在炉内的滞留时间,许多分解炉结构采用了迭加效应,改善分解炉的功效。
⑶第三阶段。
20世纪80年代至90年代中期,为悬浮预热器和预分解技术日臻成熟,全面提高阶段。
中国科研、设计和生产人员已经比较成熟熟练地掌握了新型干法水泥生产技术,对中国水泥工业地发展和科技进步发挥了巨大作用。
如:LZ日产3200t预分解系统地技术改造工程。
⑷20世纪90年代中期至今,为水泥工业向“生态环境材料型”产业迈进阶段。
五大标志:一是产品质量提高,满足高性能混凝土地耐久性要求;二是尽力降低熟料热耗及水泥综合电耗,节约一次资源和能源;三是大力采用替代性原料和燃料,提高替代率;四是实行“清洁生产”,三废自净化;五是降解利用其它工业产生地废渣、废料,生活垃圾及有毒、有害地危险废弃物,为社会造福。
各型分解炉的结构及特点.

1.旋流式分解炉又称旋风式分解炉
• C-SF分,研制出C-SF分解炉,其结构原理如图 所示。
2 . KSV分解炉
• KSV分解炉是由日本川崎重工业公司研制。KSV分 解炉工艺流程和结构分别如图3-6和图3-7所示。
• FLS改进型分解炉如图3—18(b)所示,炉顶由原来的倒锥形改为平 顶,含有悬浮生料的气流从炉的圆柱形筒体上部以切线方向导出, 进入最低级旋风筒进行分离。
• 改进型分解炉使用后发现,炉内产生偏流、短路和特稀浓度区,影 响炉内气料的热交换。
• FLS常用的炉型
• SLC离线分解炉。SLC分解炉工艺流程如图3—19所示
1.旋流式分解炉又称旋风式分解炉
• 以SF型为代表 • 现已发展为N-SF型,原
理已发展为旋流-喷腾式 分解炉类型。
1.旋流式分解炉又称旋风式分解炉
• N-SF分解炉
• N-SF分解炉是在SF分解炉的基础上改进的,二者的结构对比如图。 • N-SF分解炉的不足之处在于分解炉以侧面出口,出口高度大,占分
7.普列波尔(Prepol)炉系列
• Prepol是Precalcining-Polysius的缩写,伯力休斯公司分解炉是 在该公司多波尔悬浮预热器基础上设置1条整体烟道分解炉。如 图3—28所示为伯力休斯分解炉系列。
8.TC分解炉系列
• 图3—36是根据国内燃料 的燃烧特性在DD分解炉基 础上研制开发的TDF分解 炉。
TC分解炉改进型
NC分解炉系列
• NC分解炉系列是南京院开发研制的,图3—38是在ILC分解炉、 Prepol及Pyroclon分解炉的基础上开发的NST-I同线分解炉(同线炉), 图3—39所示NST-S半离线炉
第12章 各类预分解窑简介
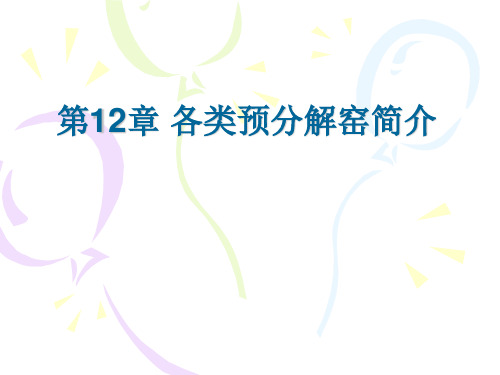
一、SF分解炉系列
• 1. SF分解炉(Suspension PreheaterFlash Furnace)
• 2. NSF分解炉 。
• 1)将燃料喷入点由原来喷入反应室锥体下部改为 喷入涡流室顶部,燃料燃烧条件改善,延长了在 炉内的停留时间,提高了燃烧效率;
• 2)改变窑气与三次风混合入炉的流程,三次风仍 以切线方向进入涡流室,窑气则单独通过上升管 道向上流动,使三次风与窑气在涡旋室形成叠加 湍流运动,强化了料粉的分散混合;
• 5)不足主要在于炉气侧向排出,且出口高度大,易 产生偏流、短路和稀薄生料区。
• 3. CSF分解炉
• 将NSF炉侧面出口改 为顶部涡室出口。
• 涡室下设置缩口,产 生喷腾效果,克服气 流偏流和短路。
• 增设连接管道,使生 料停留时间达到15s 以上,入窑生料分解 率提高到90%以上。
二、 KSV分解炉系列
• 3)在炉底喷腾层中部,增加了燃料喷嘴,使燃料在 低氧状态下燃烧,可使窑烟气中的NOX还原,有利 于减少环境污染。
• 4)从上一级旋风筒下来的生料,一部分从三次风入 口上部,使生料能够与气流均匀混合 和热交换。出炉气体温度为860~880℃,入窑生 料分解率为85~90%。
• 燃料喷入Ⅱ区富氧区立 即在炉内湍流中裂解和 燃烧。产生的热量迅速 传给生料,气料进行高 效热交换,生料迅速分 解。也称混合区。
• 3.主要燃烧区(Ⅲ区)
• 燃烧燃料、热量传递, 生料吸热分解。炉温保 持在850~900℃,生 料和燃料混合、分布均 匀,没有明亮火焰的过 热点,区内温度较低, 且分布均匀。
• 对RSP 分解炉的分析
• 特点:
• ⑴ RSP分解炉的三次风先以切线方向进入涡 流分解室,造成炉内的旋风运动,形成旋风效 应,有利于炉内燃烧、传热和分解的进行。
- 1、下载文档前请自行甄别文档内容的完整性,平台不提供额外的编辑、内容补充、找答案等附加服务。
- 2、"仅部分预览"的文档,不可在线预览部分如存在完整性等问题,可反馈申请退款(可完整预览的文档不适用该条件!)。
- 3、如文档侵犯您的权益,请联系客服反馈,我们会尽快为您处理(人工客服工作时间:9:00-18:30)。
分解炉在窑外分解系统起着很重要的作用,自1971年第一台窑外分解系统投产,从而开始水泥工业大规模生产开始,分解炉的形式有很多。
从分解炉内的气流运动来看,可归纳为四种基本型式,即:涡旋式、喷腾式、悬浮式和流化床式。
早期开发的分解炉,多以上述四种运动型式之一为基础,使生料和燃料分别依靠“涡旋效应”、“喷腾效应”、“悬浮效应”和“流态化效应”分散于热气流中,利用物料颗料之间在炉内流场中的相对运动,实现高度分散、均匀混合和分布、迅速换热,以达到提高燃烧效率,传热效率和入窑生料碳酸盐分解率的目的。
分解炉按照设计单位国内有以下常见几种:RSP 来源与日本小野田
TDF、TSD、TD、TSD、TWD、TTF、TFD天津院
CDC成都院
NST-I NC-SST南京
院
具体形式和特点如下:TDF型分解炉
TDF分解炉是天津水泥院在引进日本DD炉技术的基础上,针对中国燃料特点,研制开发的一种双喷腾分解炉(Dual Spout Furnace),如下图1-1所示。
TDF炉技术特点如下:
①分解炉坐落窑尾烟室之上,炉与烟室之间缩口在尺寸优化后可不设调节阀板,结构简单;
②炉中部设有缩口,保证炉内气固流产生第二次“喷腾效
应”;
①三次风切线入口设于炉下锥的上部,使三次风涡旋入炉;炉的两个三通道燃烧器分别设于三次风入口上部或侧部,以便入炉燃料斜喷入三次风气流之中迅速起风燃烧;
②在炉的下部圆筒体内不同的高度设置四个喂料管入口,以利物料分散均布及炉温控制。
⑤炉的下锥体部位的适当位置设置有脱氮燃料喷嘴,以还原窑气中的氮,满足环保要求;
⑥炉的顶部设有气固流反弹室,使气固流产生碰撞反弹效应,延长物料在炉内滞留时间;
⑦气固流出口设置在炉上椎体顶部的反弹室下部;
⑧由于炉容较DD炉增大,气流、物料在炉内滞留时间增加,有利于燃料完全燃烧和碳酸盐分解。
TSD分解炉
TSD型炉是带旁置旋流预燃室的组合式分解炉(Combination Furnace with spin pre-burning Chamber)见图1-2炉
TSD炉技术特点如下:
①设置了类似RSP型炉的预燃室;
②将DD型炉改造为类似MFC型炉的上升烟道或RSP型窑的MC室(混合室),作为TSD型炉炉区的组成部分,并扩大了DD炉型的上升烟道容积,使TSD炉具有更大的适应性;
③该炉可用于低挥发分煤及质量较差的燃料。
TFD分解炉
TFD型炉是带有旁置流态化悬浮炉的组合型分解炉(Combination Furnace with
Fluidized led)它是半离线型,见图1-3
其技术特点如下:
①将N-MFC炉结构作为该炉型的主炉区,其出炉气固流经“鹅颈管”经入窑尾DD炉型上升烟道的底部与窑气混合。
②该炉型实际为N-MFC炉的优化改造,并将DD炉结构用作上升烟道。
由于其炉区容积大,适用于老厂技术改造及使用无烟煤燃料。
③该炉型主要适用于老窑技术改造。
它同TSD型炉的区别主要在于上升烟道采用了新设DD炉结构形式还是采用老窑原有的上升烟道,同时,流态化悬浮炉亦可根据需要确定炉容大小与结构形式。
三喷腾型TTF分解炉
见图1-4
TTF炉固气停留时间比(tm/tg=4.8)大,炉流场大大优化,物料停留时间长,有利于煤粉的充分燃烧及生料充分分解;喂料方式:上下料点合理分料,分解炉中部局部温度可达~1300℃,可大幅提高煤粉燃烧效果,高温区间设计~1.5s,可保证劣质煤及无烟煤的充分燃烧;物料置于三次风正上方,可充分分散,分解炉物料分布均匀,流场更合理,同时可减少锥部塌料,分解炉的压损可大幅减少,系统阻力相应降低;喂煤方式:单通道对称四点喷入,优化分解炉温度场。
该分解炉有一个较长鹅颈管到达c5,更进一步物料的反应时间,分解率一般比较
高。
,CDC分解炉
CDC型炉是成都院研制开发的。
该炉型分为同线型及离线型两种,见图1-5,
其技术特点如下:
①CDC型是在分析研究N-SF型炉实用经验基础上研发,炉底部采用蜗壳型三次风入口,坐落在窑尾短型上升烟道之上,并在炉中部设有“缩口”形成二次喷腾,上部设置侧向气固流出口。
②炉内燃煤点有两处,一处在底部蜗壳上部;另一处设在炉下锥体处。
可根据煤质状况调整。
③炉内下料点有两处,一处在炉下部锥体处;另一处在窑尾上升烟道上,可用于预热生料,调节系统工况。
④CDC型炉最大特点是可根据原燃料需要,增大炉容,亦可增设“鹅颈管道”,满足燃料燃烧机物料分解需要。
⑤CDC型离线炉则是在原CDC型同型炉基础上增设类似
RSP型炉的预燃室(SC室),以满足使用低质燃料的需要。
这样,原设置CDC 炉部位已改为类似RSP型炉的混合室(MC室)或称上升烟道,并在上升烟道中部设有缩口使之形成二次喷腾。
NC-SST型分解炉
NC-SST型炉是由南京院研发的。
该炉系列由NC-SST-1型同线管道炉及
NC-SST-S型半离线型,同线管道炉见图1-6。
其技术特点:
NC-SST-1型同线型炉,安装与窑尾烟室之上,为涡旋、喷腾迭加式炉型。
其特色在于:一是扩大了炉容,并在炉出口至最下级旋风筒之间增设了“鹅颈管”,进一步增大了炉区空间,由于温度高,煤、料入口装设合理,即使低挥发份煤粉进入炉后亦可迅速起火燃烧。
同时,在单位时产10m3/(t·h)的巨大炉容内,可以保证煤粉完全燃烧。
NC-SST-S型炉为半离线炉。
主炉结构与同线炉相同。
见图1-7。
其技术特点如下:
出炉气固流经“鹅颈管”与窑尾上升烟道相连。
即可实现上升烟道的上部连接,又可采取“上升到
位”模式将“鹅颈管”连接于上升烟道下部。
研发者认为,由于固定碳的燃烧温度受温度影响很大,因此使低挥发燃料在炉下高温三次风及更高温度的窑尾烟气混合气流中起火燃烧,可以抵消气氧含量较低的影响,所以NC-SST-1型炉可以适应低挥发份煤的使用,而不必选用NC-SST-S 型炉。
研发者认为选用结构简单的大炉容积的优点,一是系统阻力低,二是可相应放宽燃料细度到20%(4900空筛余)以上。
两者均为降低生产电耗的重要举措。
NC-SST-1型炉在ILC炉、Prepol及Pyyoclon型管道炉的基础上开发创新。
其设计特色十分值得重视。
通过实践考验,如能够适应低挥发份煤及无烟煤的应用,达到研发目标,将会是一个很具有竞争力的炉型。
对于这几种国内常用的炉型,个人接触过TFD、TDF、TTF、TSD,综合起来这三种天津院的炉型,个人觉得TTF是一个暂时集大成者,它融合南京院NC-SST炉和TDF炉的精华,但是该种炉型在运用实际中需要根据煤种情况对于分解炉燃烧器进行调整。
TFD炉大家一般比较陌生些,其现在运用比较多的地方就是河南,其是河南建材院和洛阳院经常采用的炉型,其比较适合无烟煤,也是现在比较多见的半离线型炉。
实际现实照片如下:
未命名_conew5.bmp(189.9 KB, 下载次数: 3)。