冲压工艺及模具设计
冲压工艺及模具设计
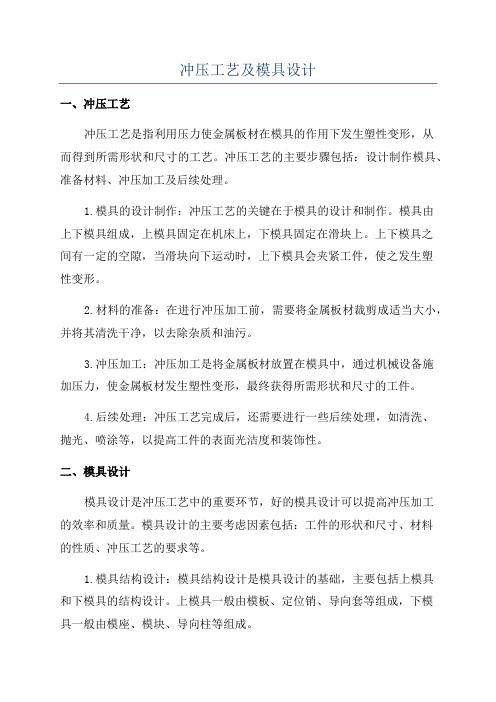
冲压工艺及模具设计一、冲压工艺冲压工艺是指利用压力使金属板材在模具的作用下发生塑性变形,从而得到所需形状和尺寸的工艺。
冲压工艺的主要步骤包括:设计制作模具、准备材料、冲压加工及后续处理。
1.模具的设计制作:冲压工艺的关键在于模具的设计和制作。
模具由上下模具组成,上模具固定在机床上,下模具固定在滑块上。
上下模具之间有一定的空隙,当滑块向下运动时,上下模具会夹紧工件,使之发生塑性变形。
2.材料的准备:在进行冲压加工前,需要将金属板材裁剪成适当大小,并将其清洗干净,以去除杂质和油污。
3.冲压加工:冲压加工是将金属板材放置在模具中,通过机械设备施加压力,使金属板材发生塑性变形,最终获得所需形状和尺寸的工件。
4.后续处理:冲压工艺完成后,还需要进行一些后续处理,如清洗、抛光、喷涂等,以提高工件的表面光洁度和装饰性。
二、模具设计模具设计是冲压工艺中的重要环节,好的模具设计可以提高冲压加工的效率和质量。
模具设计的主要考虑因素包括:工件的形状和尺寸、材料的性质、冲压工艺的要求等。
1.模具结构设计:模具结构设计是模具设计的基础,主要包括上模具和下模具的结构设计。
上模具一般由模板、定位销、导向套等组成,下模具一般由模座、模块、导向柱等组成。
2.模具材料选择:模具的材料选择直接影响到模具的使用寿命和加工质量。
一般情况下,模具材料应具有高硬度、高强度、良好的热导性和耐磨性等特性。
3.模具零件设计:模具零件的设计应考虑到工件的形状和尺寸,以及冲压工艺的要求。
模具零件的设计应尽量简化,减少加工难度,提高生产效率。
4.模具配合设计:模具零件之间的配合关系直接影响到模具的精度和稳定性。
模具配合设计应确保零件的定位准确、运动平稳,并充分考虑到热膨胀等因素。
综上所述,冲压工艺及模具设计是一项复杂的工程,它涉及到材料、结构、流程等多个方面。
通过合理的冲压工艺和精心的模具设计,可以实现高效、高质量的冲压加工,为生产制造提供有力支持。
冲压工艺及模具设计知识要点

冲压工艺及模具设计知识要点冲压工艺及模具设计知识要点冲压工艺是制造业中广泛应用的一种金属成形加工方式,它通过在金属材料表面施加压力,使其塑性变形,以达到所需的工艺和形状。
在冲压工艺中,模具的设计和制造是至关重要的一环。
因此,掌握冲压工艺及模具设计知识要点,对于提高冲压制造技术水平、提高产品质量和降低成本具有重要意义。
下面,将结合实际生产实践,总结一些关于冲压工艺及模具设计的知识要点。
一、冲压工艺的基本要素1.材料选择:冲压材料必须具备良好的塑性变形能力、疲劳寿命和均匀性,同时要满足在特定条件下的强度、硬度和耐磨性等要求。
2.模具设计:模具的设计必须充分考虑冲压材料的变形特性和受力条件,以及零件的加工要求和成本控制等因素。
模具的各个组成部分必须协调配合,且具备高精度、高刚度和耐用性等特点。
此外,模具的加工和装配需要注意细节化管理和工艺标准化。
3.加工工艺:冲压工艺过程需要严格控制各个工艺环节,特别是在模具定位、定量进料、开裂垫片等关键环节,需要特别加以关注。
此外,对于一些复杂形状或外观有要求的零件,可以考虑采用多道冲压或辅助模具等方式进行加工。
二、模具设计的基本原则1.要具备较好的适应性:模具应根据零件的形状、尺寸和材料特性等因素,合理选用模具结构类型和尺寸规格,以满足生产要求。
2.要具有高精度和稳定性:模具必须具备高精度、高刚性和高耐用性,以确保在大量生产过程中,始终保持稳定的加工质量。
3.要考虑冲压力分布均匀性:在模具设计时应充分考虑冲压时的力分布状况,特别是在切断底部的操作中,需要合理安排模具结构,使冲头的力能够均匀作用在零件的各个角落,避免切口不整齐等质量问题。
4.要注意保障安全性:模具设计时必须考虑操作安全和保护措施的设置,以避免操作工程师在工作中出现安全事故和模具损坏情况,同时还需要考虑环境保护和资源利用等问题。
三、模具加工工艺模具加工工艺是冲压工艺中的重要环节之一,是对模具设计的实际落地。
冲压工艺与模具设计课程设计
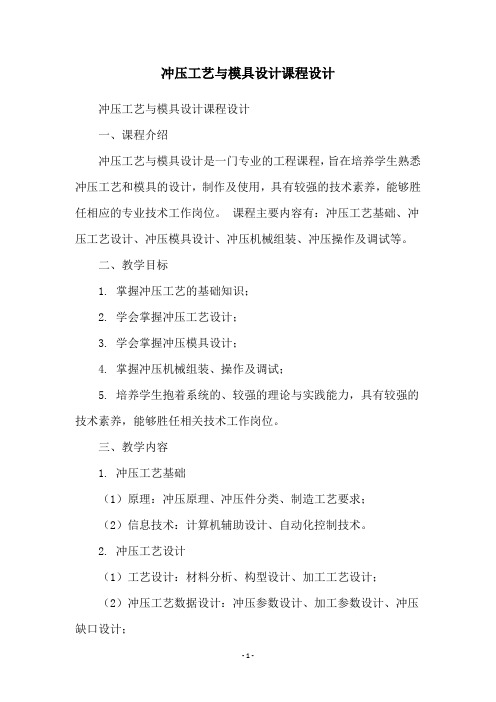
冲压工艺与模具设计课程设计冲压工艺与模具设计课程设计一、课程介绍冲压工艺与模具设计是一门专业的工程课程,旨在培养学生熟悉冲压工艺和模具的设计,制作及使用,具有较强的技术素养,能够胜任相应的专业技术工作岗位。
课程主要内容有:冲压工艺基础、冲压工艺设计、冲压模具设计、冲压机械组装、冲压操作及调试等。
二、教学目标1. 掌握冲压工艺的基础知识;2. 学会掌握冲压工艺设计;3. 学会掌握冲压模具设计;4. 掌握冲压机械组装、操作及调试;5. 培养学生抱着系统的、较强的理论与实践能力,具有较强的技术素养,能够胜任相关技术工作岗位。
三、教学内容1. 冲压工艺基础(1)原理:冲压原理、冲压件分类、制造工艺要求;(2)信息技术:计算机辅助设计、自动化控制技术。
2. 冲压工艺设计(1)工艺设计:材料分析、构型设计、加工工艺设计;(2)冲压工艺数据设计:冲压参数设计、加工参数设计、冲压缺口设计;(3)工艺过程设计:冲压过程设计、冲压加工组合设计。
3. 冲压模具设计(1)模具结构特性及原理:模具种类、模具结构特性、模具加工技术;(2)模具外形设计:模具尺寸设计、模具外形设计、模具开模方式设计;(3)模具细部设计:模具夹具设计、模具油道设计、模具放料口设计。
4. 冲压机械组装、操作及调试(1)机械组装:机床部件安装、工作台安装、冲程控制装置安装;(2)机械操作:调整冲程、挤压调节、调整冲头;(3)机械调试:机械功能调试、挤压参数调试、冲头快速调试。
四、教学安排本课程为2学期,每周3个小时,36学时。
主要采取实验操作和讨论报告的方式,在实验中锻炼学生的实践能力,在讨论中增强学生的专业综合能力。
五、教学考核及格考核和综合考核:成绩由实验操作50%、讨论报告50%组成。
冲压工艺及模具设计

冲压工艺及模具设计冲压工艺及模具设计是现代工业制造中常用的一种技术,它通过将金属板材或者其他形状的金属件置于模具中,然后通过冲压机的动作使得金属材料发生塑性变形以得到所需的形状和尺寸。
冲压工艺及模具设计是一门综合性强的工艺技术,以下将介绍其包括冲压工艺流程、模具设计原则、模具结构设计、模具构件选用等相关内容。
一、冲压工艺流程冲压工艺分为单道冲压和多道冲压两种。
单道冲压是指在一个冲压过程中完成产品的全体造型,多道冲压是指通过多次冲压工艺来完成产品的全体造型。
下面将以多道冲压为例介绍冲压工艺流程。
1.材料准备:选择合适的板材材料,进行剪切、铺料等准备工作。
2.模具设计:根据产品的形状和尺寸要求,设计合适的冲压模具。
3.上料:将材料板厚按照模具规格要求剪切成对应尺寸,然后放置在模具上。
4.开模:通过冲压机的动作,使得模具上的凸模与凹模对压,使材料发生塑性变形。
5.去杂及模具保养:在冲压过程中会产生一些杂质,需要及时清理,并对模具进行保养和维护。
二、模具设计原则模具设计是冲压工艺的核心环节,它直接影响着产品的质量和成本。
在进行模具设计时,需要遵循以下原则:1.合理性原则:模具结构要合理,能够满足产品的形状和尺寸要求,并且易于加工和调整。
2.稳定性原则:模具要具有足够的刚性和稳定性,能够承受冲压机的冲击力和振动。
3.高效原则:模具设计要考虑工作效率,设计出能够实现快速冲压的模具结构。
4.经济原则:模具的设计和制造成本要较低,以降低产品的制造成本。
三、模具结构设计模具的结构设计是模具设计的重要环节,它包括模具的整体结构、分段结构、导向结构等。
下面将介绍常用的模具结构设计方法:1.整体结构设计:将模具设计为一个整体结构,具有较好的刚性和稳定性。
2.分段结构设计:根据产品的形状和尺寸要求,将模具分为多个部分,通过连接件进行连接。
3.导向结构设计:模具需要具有良好的导向性,避免材料在冲压过程中发生歪斜和偏移。
4.其他辅助结构设计:模具还需要考虑各种辅助结构,如剪断边缘结构、定位结构、脱模结构等。
冲压工艺与模具设计ppt课件
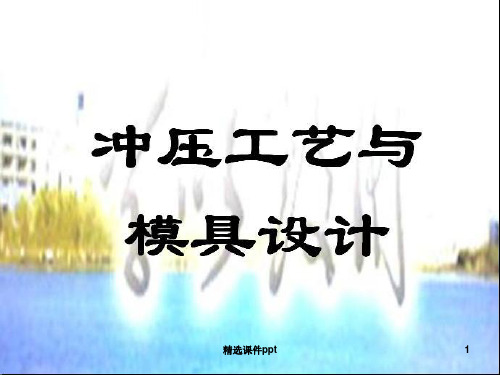
(7)大量生产时,产品成本低。
精选课件ppt
24
由此可见,冲压能集优质、高效、低能耗、 低成本于一身,这是其它加工方法无法与之相比拟的,
因此冲压的应用十分广泛,如汽车,拖拉机行业中,冲压 件占60%~70%,仪器仪表占到60~70%,还有日常生活中的 各种不锈钢餐具等等。从精细的电子元件,仪表指针到重 型汽车的覆盖件和大梁以及飞机蒙皮等均需冲压加工。
29
分离工序示意
D
D
D
落料
D
剪切
有分离现象发生,但不
改变空间形状
精选课件ppt
30
表1-1 分离工序
精选课件ppt
31
表1-1 分离工序(续)
精选课件ppt
32
(2)成形工序
冲压成形时,被加工材料在外力作用下,变形区材料所受 到的等效应力达到材料的屈服极限σs,但未达到强度极限σb, 使材料只产生塑性变形,从而得到一定形状和尺寸的零件。成 形工序主要有弯曲、拉深、翻孔、缩口、胀形等。
精选课件ppt
28
1.2 冲压工艺分类
1.按变形性质分类
➢分离工序 ➢成形工序
(1)分离工序
冲压成形时,被加工材料在外力作用下产生变形,当变 形区材料受到的剪切应力达到材料的抗剪强度,材料便产生 剪切而分离,从而形成一定形状和尺寸的零件。分离工序主 要有剪裁、冲孔、落料、切口、剖切等。
精选课件ppt
精选课件ppt
27
总之,模具工业是 一个国家的基础工业,模具设计与模 具制造水平的高低已成为衡量一个国家产品制造水平的高低。
发达国家非常重视模具的发展,日本认为:“模具就是进 入富裕社会的原动力”;德国:“金属加工业中的帝王”;罗 马尼亚:“模具就是黄金”;模具在国际上被认为是点石成金 的行业。不过这里的模具还包括塑模、锻模、压铸模、橡胶模、 食品模、建材模等等,但目前以冷冲模和塑料模的应用最广, 各占40%左右。
冲压工艺与模具设计
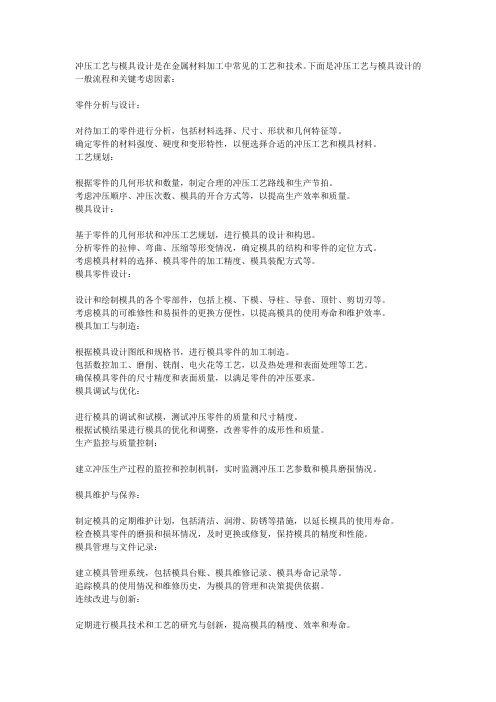
冲压工艺与模具设计是在金属材料加工中常见的工艺和技术。
下面是冲压工艺与模具设计的一般流程和关键考虑因素:零件分析与设计:对待加工的零件进行分析,包括材料选择、尺寸、形状和几何特征等。
确定零件的材料强度、硬度和变形特性,以便选择合适的冲压工艺和模具材料。
工艺规划:根据零件的几何形状和数量,制定合理的冲压工艺路线和生产节拍。
考虑冲压顺序、冲压次数、模具的开合方式等,以提高生产效率和质量。
模具设计:基于零件的几何形状和冲压工艺规划,进行模具的设计和构思。
分析零件的拉伸、弯曲、压缩等形变情况,确定模具的结构和零件的定位方式。
考虑模具材料的选择、模具零件的加工精度、模具装配方式等。
模具零件设计:设计和绘制模具的各个零部件,包括上模、下模、导柱、导套、顶针、剪切刃等。
考虑模具的可维修性和易损件的更换方便性,以提高模具的使用寿命和维护效率。
模具加工与制造:根据模具设计图纸和规格书,进行模具零件的加工制造。
包括数控加工、磨削、铣削、电火花等工艺,以及热处理和表面处理等工艺。
确保模具零件的尺寸精度和表面质量,以满足零件的冲压要求。
模具调试与优化:进行模具的调试和试模,测试冲压零件的质量和尺寸精度。
根据试模结果进行模具的优化和调整,改善零件的成形性和质量。
生产监控与质量控制:建立冲压生产过程的监控和控制机制,实时监测冲压工艺参数和模具磨损情况。
模具维护与保养:制定模具的定期维护计划,包括清洁、润滑、防锈等措施,以延长模具的使用寿命。
检查模具零件的磨损和损坏情况,及时更换或修复,保持模具的精度和性能。
模具管理与文件记录:建立模具管理系统,包括模具台账、模具维修记录、模具寿命记录等。
追踪模具的使用情况和维修历史,为模具的管理和决策提供依据。
连续改进与创新:定期进行模具技术和工艺的研究与创新,提高模具的精度、效率和寿命。
分析生产过程中的问题和不良品情况,提出改进措施,并进行试验验证。
在冲压工艺与模具设计过程中,需要综合考虑零件的形状复杂度、批量要求、成本效益等因素,确保模具的精度和稳定性,以实现高质量和高效率的生产。
冲压工艺与模具设计

冲压工艺与模具设计冲压工艺是一种通过对金属板材进行压制或冲剪,以改变其形状和尺寸的制造工艺。
在冲压过程中,需要使用模具来对金属板材施加确定的压力,使其发生塑性变形。
模具设计是冲压工艺的关键环节,合理的模具设计可以保证冲压过程的精度和效率。
一、金属材料的选择冲压工艺中常用的金属材料有钢板、铝板、铜板等。
不同金属材料的机械性能和加工性能不同,选择合适的金属材料对冲压工艺的成功至关重要。
二、冲压工艺的确定冲压工艺主要包括件的外形确定、孔位置的布置、切缘的设计等。
通过工艺确定,可以确定冲压工序的顺序、模具的需求以及操作要求。
三、模具设计要点1.模具结构的设计:模具结构设计要满足零件的加工要求,并在生产中方便拆卸、更换。
2.模具材料的选择:模具材料需要具有较高的硬度、强度和耐磨性,常用的模具材料有合金工具钢、硬质合金等。
3.模具配套设备的选择:根据冲压工艺的要求,选择合适的配套设备,如冲压机等。
4.压力分布的设计:模具在冲压过程中需要对板材施加一定的压力,合理的压力分布可以避免产生变形和裂纹。
5.模具的预紧力设计:预紧力是指模具在冲压过程中需承受的力量,需要合理设置预紧力以保证冲压过程的稳定性和精度。
6.附件的设计:模具附件是模具的辅助部件,如导向柱、定位销等,合理的设计可以提高模具的使用寿命和加工效率。
7.考虑模具的便于制造性和可维护性:在模具设计中,需要考虑到模具的制造难度和维护难度,合理的设计可以降低成本和提高效率。
总之,冲压工艺与模具设计是密不可分的,合理的模具设计可以保证冲压过程的精度和效率,最终提高产品的质量和生产效益。
在进行冲压工艺与模具设计时,需要考虑金属材料的选择、工艺的确定以及模具结构、材料等方面的要点。
只有全面考虑这些因素,才能设计出合理、高效的模具,实现优质的冲压加工。
冲压工艺及模具设计经典教材-冲压工艺及模具设计

数控压力机冲裁方式
(7) 模柄孔尺寸 模柄直径应略小于滑块内模柄安装孔的直径 。模柄的长度应小于模柄孔的深度。
(8) 压力机电动机功率 压力机电动机功率应大于冲压时所需 要的功率。
1.2.3 其他常用压力机简 介
(1) 偏心压力机 曲轴压力机的滑块行 程不能改变 ,而偏心 压力机的滑块行程是
可变的。 偏心压力机和曲
离合器
(3) 离合器 离合器是用来接通或断开大齿轮— 曲轴的运动 传递的机构 , 即控制滑块是否产生冲压动作, 由操作者操 纵 ,如图1.4所示。
制动 器
(4) 制动器 制动器是确保离合器脱开时 ,滑块比较准确地停止在曲 轴转动的上死点位置。 制动器的工作原理是 ,利用制动轮对旋转中心的偏心 ,使制动带对 制动轮的摩擦力随转动而变化来实现制动 。当曲轴转到上死点时 , 制动轮中心和固定销中心之间的中心距达到最大 。此时 ,制动带的 张紧力就最大 ,从而在此处产生制动作用 。转过此位置后 ,制动带 放松 ,制动器则不制动 。制动力的大小可通过调节拉紧弹簧来实现 。如图1.5所示。
(1)公称压力
压力机滑块 通过模具在 冲压过程中 产生的压力 就是压力机 工作压力。
2. (2) 滑块行 程 滑块行 程是指滑块 从上止点移 动到下止点 的距离。
3. (3) 滑块每 分钟冲压次 数。
1.2.2 曲柄压力机的主要技术参 数
压力机装模高度
(4) 压力机装模高度 压力机的装模高度是指滑块移动到下死点 时 ,滑块底平面到工作台垫板上平面的高度。
第1章 概 述
冷冲压加工概述
(1) 冲裁 使板料分离来获得制件的工序。 (2) 弯曲 使板料由平变弯来获得制件的工序 。 (3) 拉深 使平板料变成开口壳体制件的工序。 (4) 成形 使板料或其他形状的半成品的局部产 生凸凹变形的工序。
冲压工艺与模具设计(第2版)

05
2.5冲裁模 的基本类型 与构造
2.8精密冲裁工艺 与模具设计
2.7冲裁模设计举 例
思考与练习题
1
3.1弯曲变形 过程分析
2
3.2弯曲件质 量分析及控制
3
3.3弯曲工艺 计算
4
3.4弯曲工艺 设计
5
3.5弯曲模具 设计
3.6弯曲模设计 举例
思考与练习题
1
4.1拉深变形 过程分析
2
4.2拉深件质 量分析及控制
设计方法与步 骤
3
8.3冲压模具 材料及热处理
4 8.4冲压工艺
与模具设计举 例
5
思考与练习题
作者介绍
同名作者介绍
这是《冲压工艺与模具设计(第2版)》的读书笔记模板,暂无该书作者的介绍。
读书笔记
读书笔记
这是《冲压工艺与模具设计(第2版)》的读书笔记模板,可以替换为自己的心得。
精彩摘录
精彩摘录
3
4.3拉深工艺 计算
4
4.4拉深工艺 设计
5
4.5拉深模具 设计
4.6拉深模设计 举例
思考与练习题
5.1多工位级 1
进模的排样设 计
2
5.2多工位级 进模典型结构
3 5.3多工位级
进模主要零件 设计
4 5.4多工位级
进模的图样绘 制
5
思考与练习题
01
6.1翻边
02
6.2缩口
03
6.3旋压
04
6.4胀形
06
思考与练习 题
05
6.5覆盖件 成形工艺与 模具
7.1冷挤压工 1
艺分类及冷挤 压金属变形特 点
7.2冷挤压原 2
冲压工艺与模具设计
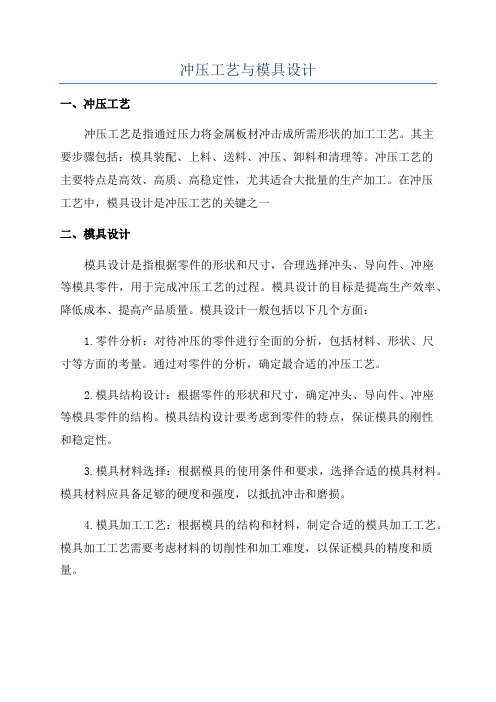
冲压工艺与模具设计一、冲压工艺冲压工艺是指通过压力将金属板材冲击成所需形状的加工工艺。
其主要步骤包括:模具装配、上料、送料、冲压、卸料和清理等。
冲压工艺的主要特点是高效、高质、高稳定性,尤其适合大批量的生产加工。
在冲压工艺中,模具设计是冲压工艺的关键之一二、模具设计模具设计是指根据零件的形状和尺寸,合理选择冲头、导向件、冲座等模具零件,用于完成冲压工艺的过程。
模具设计的目标是提高生产效率、降低成本、提高产品质量。
模具设计一般包括以下几个方面:1.零件分析:对待冲压的零件进行全面的分析,包括材料、形状、尺寸等方面的考量。
通过对零件的分析,确定最合适的冲压工艺。
2.模具结构设计:根据零件的形状和尺寸,确定冲头、导向件、冲座等模具零件的结构。
模具结构设计要考虑到零件的特点,保证模具的刚性和稳定性。
3.模具材料选择:根据模具的使用条件和要求,选择合适的模具材料。
模具材料应具备足够的硬度和强度,以抵抗冲击和磨损。
4.模具加工工艺:根据模具的结构和材料,制定合适的模具加工工艺。
模具加工工艺需要考虑材料的切削性和加工难度,以保证模具的精度和质量。
5.模具试验和修正:模具设计完成后,需要进行试验和修正。
通过试验,发现和解决可能存在的问题,确保模具的性能和稳定性。
修正包括进行冲击试验、模具调整、磨削等。
总的来说,冲压工艺与模具设计是相互关联的。
只有冲压工艺与模具设计相互配合,才能保证冲压工艺的高效、高质、高稳定性。
因此,对于冲压工艺与模具设计的研究和应用具有重要的意义。
冲压工艺及模具设计

冲压工艺及模具设计冲压工艺及模具设计是一种应用广泛的金属加工方法,它通过将金属材料置于模具中,施加外力使其产生塑性变形来实现加工目的。
冲压工艺及模具设计在日常生活中被广泛应用于汽车制造、家电制造、建筑结构等领域。
本文将详细介绍冲压工艺及模具设计的基本原理、流程以及注意事项。
一、冲压工艺的基本原理冲压工艺是利用模具的上下凸模与下模的活套孔进行压力传递,从而给金属材料施加一定的压力,使其发生塑性变形,最终获得所需形状的零件。
冲压工艺的基本原理包括:所需零部件的模具设计、材料的选用、设备的调整和操作、冲压力的控制等。
二、冲压工艺的流程1.设计模具:根据所需加工的零件形状和尺寸,设计相应的冲压模具。
模具的设计考虑要点包括:模具结构、零件加工顺序、模具寿命等。
2.材料选用:根据所需加工的零件的要求,选择合适的金属材料。
常用的金属材料有冷轧钢板、不锈钢板、铝合金板等。
3.材料切割:将金属材料按照所需零件的形状和尺寸切割成相应的板料。
4.模具调整:将上下模具安装在冲床上,并进行调整,使得上下模具对齐、平衡。
5.进料:将切割好的板料放置在模具上,通过上模的压力传递给下模,使金属材料发生塑性变形。
6.成型:通过上下模具的周期性运动,使金属材料依次进行冲击、拉伸、弯曲等工艺,最终获得所需形状的零件。
7.完成零件:将成型好的零件从模具中取出,并进行后续处理,如清洗、打磨、表面处理等。
三、冲压工艺及模具设计的注意事项1.模具的设计:模具的设计应符合所需零件的形状和尺寸要求,且要考虑模具的寿命和成本问题。
模具设计时,需注意加工顺序的合理性,以提高生产效率。
2.材料的选用:选择合适的金属材料是冲压工艺的关键,需考虑零件的材质要求、成本和加工性能等因素。
3.设备的调整和操作:正确调整冲床的压力、速度和行程等参数,保证冲压工艺的稳定进行。
操作时,需注意安全,确保操作人员的人身安全。
4.增加冲压辅助工艺:根据所需零件的形状和要求,可以增加冲压辅助工艺,如冲孔、拉伸、弯曲、压花等,以提高零件的加工质量和寿命。
冲压工艺及模具设计(3篇)

第1篇一、引言冲压工艺是一种常见的金属成形工艺,广泛应用于汽车、家电、电子、航空等行业。
冲压工艺具有生产效率高、成本低、精度高、尺寸稳定性好等优点。
模具是冲压工艺中的关键设备,其设计质量直接影响到冲压产品的质量和生产效率。
本文将对冲压工艺及模具设计进行简要介绍。
二、冲压工艺概述1. 冲压工艺原理冲压工艺是利用模具对金属板材施加压力,使其产生塑性变形,从而获得所需形状、尺寸和性能的零件。
冲压工艺的基本原理是金属的塑性变形,即金属在受到外力作用时,产生塑性变形而不破坏其连续性的过程。
2. 冲压工艺分类(1)拉深:将平板金属沿模具凹模形状变形,形成空心或实心零件的过程。
(2)成形:将平板金属沿模具凸模形状变形,形成具有一定形状的零件的过程。
(3)剪切:将平板金属沿剪切线剪切成一定形状和尺寸的零件的过程。
(4)弯曲:将平板金属沿模具凸模形状弯曲,形成具有一定角度的零件的过程。
三、模具设计概述1. 模具设计原则(1)满足产品精度和尺寸要求:模具设计应保证冲压产品具有高精度和尺寸稳定性。
(2)提高生产效率:模具设计应优化工艺流程,减少不必要的加工步骤,提高生产效率。
(3)降低生产成本:模具设计应选用合适的材料,降低模具成本。
(4)确保模具寿命:模具设计应考虑模具的耐磨性、耐腐蚀性等性能,延长模具使用寿命。
2. 模具设计步骤(1)产品分析:分析产品的形状、尺寸、材料等,确定模具设计的基本要求。
(2)工艺分析:根据产品形状和尺寸,确定冲压工艺类型,如拉深、成形、剪切、弯曲等。
(3)模具结构设计:根据工艺要求,设计模具结构,包括凸模、凹模、导向装置、压边装置等。
(4)模具零件设计:根据模具结构,设计模具零件,如凸模、凹模、导向装置、压边装置等。
(5)模具加工:根据模具零件设计,进行模具加工。
(6)模具调试:完成模具加工后,进行模具调试,确保模具性能符合要求。
四、冲压工艺及模具设计要点1. 冲压工艺要点(1)合理选择材料:根据产品形状、尺寸、性能要求,选择合适的金属材料。
冲压工艺与模具设计课程设计

冲压工艺与模具设计课程设计一、背景冲压工艺是一种常用的金属成形加工技术,广泛应用于汽车、电子、机械等行业。
模具设计是冲压生产过程中的核心环节,直接影响到产品的质量和成本,因此,冲压工艺与模具设计课程也成为机械、汽车等工科专业中不可或缺的一环。
二、课程目标本课程旨在使学生掌握冲压工艺与模具设计方面的基础理论和实践技能,能够进行简单冲压工艺的设计和工装的容易构思,掌握基本的模具加工工艺,提高学生对冲压行业的行业洞察力和工程实践能力。
三、课程内容1. 冲压工艺基础•冲压工艺概述•冲压件材料特性与材料成形性能•冲压机械结构和操作要领•冲压模具结构与分类•冲压工艺流程和工艺参数2. 冲压模具设计•冲压模具基础知识•冲压模具设计流程•冲压模具标准件与非标准件设计•冲压模具材料选择和热处理工艺•冲压模具的加工和品检标准3. 冲压工艺应用•冲压工艺的应用领域和特点•数控冲压工艺•自动化冲压生产线•冲压工艺优化和流程控制四、课程教学方法本课程既注重理论知识的讲解,又着重实践训练。
在理论授课中,采用互动式教学和案例分析方法,使学生能够理解和掌握所学知识,并能够将其应用到实际工程中。
在实践环节中,采用小组互动式实验、案例分析和研讨的方式,让学生通过模拟真实的冲压生产场景,让学生在模具设计和冲压工艺上得到更加全面和深入的锻炼。
五、课程考核与评估1. 考核形式•期中考试:笔试/上机考试•期末考试:笔试/设计作品结合考核•实习课程:实习报告/实习成果2. 评估标准根据学生的课堂表现、作业完成、实习情况等方面,评定学生的课程成绩。
具体评估标准如下:•课堂表现:包括出勤情况、人机互动、思维活跃程度等。
•作业完成:学生需要完成的课程作业,包括课堂笔记、设计案例、实验报告等。
•学术诚信:学生需要遵守作业的书写规范和学术道德规范,禁止抄袭、剽窃。
•实习成果:实习课程中学生需完成实际操作任务,提交实习报告,给出个人对实习经历的总结和感悟。
- 1、下载文档前请自行甄别文档内容的完整性,平台不提供额外的编辑、内容补充、找答案等附加服务。
- 2、"仅部分预览"的文档,不可在线预览部分如存在完整性等问题,可反馈申请退款(可完整预览的文档不适用该条件!)。
- 3、如文档侵犯您的权益,请联系客服反馈,我们会尽快为您处理(人工客服工作时间:9:00-18:30)。
(1)分类 外凸轮廓翻边: 压缩类,类似于局部浅拉深,
易起皱; 内凹轮廓翻边: 伸长类,类似于局部孔翻边,
易开裂。
(2)变形程度 外凸压缩类:εp=b/(R+b) 内凹伸长类:εd=b/(R-b). 允许变形程度可查表。(表5.3)
(3)外缘翻边力 F≈1.25·L·t·k·σb k=0.2~0.3
采用拉深→冲底孔→再翻边工序。
后续计算:
a.计算翻边能达到的最大高度: h=D(1-kmin)/2+0.57(r+t/2)
b.确定拉深高度: h’=H-h+r+t c.计算预制孔直径:
d0=D+1.14(r+t/2)-2h
实例:
⑤ calculation of flanging force 翻边力的计算 For cylindrical punch 圆柱形凸模: F=1.1π·t·σs·(D-d0)
圆弧相互之间 直线与圆弧之间互相影响。
(2)odd hole flanging 非圆孔的翻边
极限翻边系数k′
k′=(0.85~0.9)kmin,
预制孔 分别按弯曲,翻边,拉深展开; 光滑连接各部分;
翻边力 略小于圆孔翻边力。
3、 外缘翻边 沿毛坯的曲边,
使材料拉伸或压缩, 形成高度不大的竖边。
与弯曲的区别:
d0=dmax/ kmax
毛坯高度: L0=L[1+(0.3~0.4)δ]+b
b为修边余量=5~15mm,δ为延伸率,L为变形区母线长度
(2)胀形模 ①橡胶凸模胀形模 用聚氨脂做凸模。聚氨酯强度高、弹性好、
寿命长,工件尺寸精度高,外观质量好。
胀 形
(2)胀形模 ②分块式凸模胀形模 凸模为刚性,机械胀形,活动凸模可开合。
4、翻边模结构要点 结构与拉深模相似。
(1)凸凹模 凸模圆角半径较大,或成球形、圆锥型。
翻 以避免成为拉深。 凹模圆角半径影响不大,一般取工件圆角半径。
边 (2)凸凹模间隙 单边间隙Z Z≥t ——翻边力较小,精度不高; Z<t ——材料变薄,翻边竖壁垂直度要求较高。
一般为: Z=0.85t 也可查表。
切向拉长; 材料厚度变薄。
在孔的边缘处拉应力最大, 变形最大;
是开裂的危险区。
② flanging coefficient 翻边系数
翻边变形程度的大小,用翻边系数k来衡量。
k=d0/D δ= 1/k -1
翻边系数k越小,变形程度越大, 变形区拉伸变形量越大,孔的边缘 越容易开裂。
③ Minimum flanging coefficient
For cone or spheric punch圆锥形或球形凸模: F=1.2π·t·D·m·σs
m=0.05~0.25
无预制孔翻边 F′=(1.33~1.75)·F
(2)odd hole flanging 非圆孔的翻边 characters 变形特点
直线部分:视为弯曲变形; 凸圆弧部分:视为拉深; 凹圆弧部分:视为内孔翻边。
极限翻边系数kmin 孔边缘临界开裂的最小翻边系数。
To be determined by material properties, hole conditions, relative thickness, and punch shape.
kmin 取决于材料的性能、孔的状况、毛坯相对厚度、凸模工 作部分的形状等。
2、起伏成形 通过材料局部拉伸变形,形成局部凹进或凸起。
用于: 加强工件刚度(加强筋); • 工件表面造形(浮雕、压字等)
(1)起伏成形的极限延伸率 起伏成形变形程度的计算: δmax=(L1-L0)/L0 若δmax ≤(0.7 ~ 0.75)δ许用 可以一次成形,否则增加工序。
大深度起伏方法: 方法一:先大范围聚料,再整形;
翻边模
内外缘翻边复合模
翻 边
落料冲孔翻边复合 注意凸凹模的壁厚。
翻 边
§5-2 胀形
利用模具使坯料局部 塑性变形,材料变薄, 表面积增大的冲压方法。
主要有起伏成形 和凸肚两类。
起伏成形:加工对象为平板毛坯; 凸肚:加工对象为空心毛坯。
1、变形特点 外部材料不进入变形区。 变形区材料受两向拉应力, 产生拉伸变形,材料变薄。
1、hole flanging 内孔翻边 在预先冲孔的毛坯上,
依靠毛坯拉伸,孔沿周边 翻成竖直边缘的冲压工序。
内孔翻边过程
预先冲孔, 毛坯拉伸, 周边形成竖直边缘。
(1)round hole flanging 圆孔的翻边 ① Forming characters 变形特点
变形区材料,切向与径向 均受拉应力作用。
胀 形
(2)胀形模 ③液体凸模胀形模
液体受压缩后,产生高压,将坯料胀大。
CHAPTER 5
Formation
成形工艺
用各种局部变形来改变毛坯或半成品形状的冲压工序。
成形方法:
flaring & hole flanging 翻边
bulging
胀形necΒιβλιοθήκη ing缩口sizing
整形
flattening
校平
§5-1 Flaring 翻边
在成型毛坯的平面或曲面部分,沿一定曲线形成竖立边缘的冲 压方法。
•足够的压边力(压边面积); •更大的凸模圆角半径。
④ Calculation for flanging 翻边工艺计算 根据工件尺寸,计算预制孔直径: d0=D-2(H-0.43r-0.72t) 计算翻边系数: k=d0/D
判断:
如果 k≥kmin 可以由平板一次翻边成形。
如果 k < kmin ,竖边高度不能一次翻出。
方法二:扩孔成形,利用孔边材料的流动、补充。
3、凸肚胀形
将圆柱形毛坯件,依靠材料径向拉伸,在半径方向向外扩张, 形成凸起曲面的冲压方法。
(1)凸肚胀形变形程度
胀形系数: k=dmax/d0
k越大,变形量越大。
极限胀形系数kmax与许用伸长率δ许用的关系: kmax =δ许用 +1
由此,可计算:
毛坯直径:
材料塑性越好, kmin越小 ; 预制孔质量越高,kmin越小 ; 毛坯相对厚度越大, kmin越小 ; 球形凸模,材料流动阻力小, kmin小 。
为保证完成翻边工序,应确保变形时预制孔周围为变形弱区。 为此应有: •工件外径及内孔直径足够大;
( D0/ dp>2.5; d0/ dp > 0.2~0.3 )