沉镍金流程
沉镍金制作流程(精)

沉镍金制作流程一、简介:通过化学反应在铜表面沉积较薄一层镍金、金层具有稳定的化学和电器特性,镀层具有优良的可焊性,耐蚀性等特点。
二、流程及作用:(1沉金前处理:①微蚀:除去烘烤绿油造成的铜面过度氧化物。
② 1200#磨刷幼磨:除去铜面杂物,清洁板面。
(2沉镍金流程:上板→除油→Ⅱ级水洗→微蚀→→Ⅱ级水洗→酸洗→Ⅱ级水洗→预浸→活化→Ⅱ级水洗→后浸酸→Ⅰ级水洗→沉镍→Ⅱ级水洗→沉金→金回收→水洗→热水洗→下板①除油:除去铜表面之轻度油脂及氧化物,使表面活化及清洁。
②微蚀:除去铜面氧化物及污染物,适度粗化铜面,增加镀层密着性、结合力。
③预浸:保护活化药液。
④活化:使用离子钯溶液使表面铜活化,可以只在铜面上沉积而基材的Pd化合物极易清洗,提供化学沉镍的启镀剂。
⑤化学镀镍:利用电子转移使溶液中的Ni2+还原在待镀铜面上而沉积出镍金属:但同时会有P析出,Ni层实际为Ni/P合金,Ni层厚度一般为100-200u〃。
⑥通过置换反应在新鲜镍面置换一层薄金,作为防止基体金属氧化和作为自身活化型镀金的底层,镍基体上覆盖一层金后金沉积就停止,所以厚度有一定了限制,Au层厚度一般为1-3 u〃。
(3沉金后处理:①草酸洗:除去金面氧化异物,,对金层疏孔处的镍底层作酸封孔处理,增加其耐蚀性。
②抗氧化清洗:防止镀层氧化,使焊锡维持更长的寿命。
三、流程控制注意事项:(1控制微蚀速率在0.6-0.8um,速率太低,镀层发亮,太高出现色差即金色不良。
(2活化缸Cu2+浓度≤200PPM需更换,且后期易出现渗金。
(3Ni缸温度不可太高,药水高温对绿油攻击较大,易出现甩S/M问题,槽液使用4.0MTD后需换槽。
(4金缸需控制Ni2+含量≤800PPM,Ni2+太高易出现金色不良及不上金问题。
四、常见问题介绍及处理方法:(1漏镀:①活化浓度温度过低,浴老化或活化后水洗过久。
②镍缸浓度、温度、PH值太低,或有不以纯物混入,成份失调。
③绿油冲板不净,有残渣附着铜面,需煲板返印。
PCB板化镍金工艺控制

PCB板化镍金工艺控制2008-10-14 18:19PCB板化镍金工艺控制文章来源:PCB采购网一、除油槽一般情况,沉镍金采用酸性除油剂来处理制板,其作用在于去除铜面之轻度油脂及氧化物,达到铜面清洁及增加润湿的效果,它应当具备不伤材料,低泡型易水洗的特点,后以二级市水洗或三级水洗更佳。
二、微蚀槽目的在于清洁铜面氧化及前工序遗留残渣,保持铜面新鲜及增加化学镍层的密着性,常用微蚀液为酸性SPS溶液。
沉镍金生产也有使用双氧水或酸性过硫酸钾微蚀液。
由于铜离子对微蚀速率影响较大,通常须将铜离子的浓度控制在5-25G/L,以保证微蚀速率处于0。
5-1。
5UM,生产过程中,换槽时往往保留1/5-1/3槽旧液,以保持一事实上的铜离子浓度,也有使用少量氯离子加强微蚀效果。
另外,由于带出的微蚀残液,会导致铜面在水洗过程中迅速氧化,所以微蚀后水持和流量以及浸泡时间都须特别考虑,否则,预浸槽会产生太多的铜离子,继而影响钯槽寿命,在条件允许的情况下,微蚀水洗后,再加入5%左右的硫酸浸洗后进入预浸槽。
三、预浸槽预浸槽在制程中没有特别的作用,只是维持活化槽的酸度以及使铜面在新鲜状态(无氧化)下,进入活化槽。
理想的预浸槽除了钯之外,其它浓度与活化槽一致,实际上,一般硫酸钯活化系列采用硫酸作预浸剂,盐酸钯活化系列采用盐酸作预浸剂,也有使用氨盐作预浸剂(PH值另外调节),否则,活化制程失去保护会造成钯离子活化液局部水解沉淀。
四、活化槽活化的作用是在铜面析出一层钯,作为化学镍起始反应之催化晶核,其形成过程则为钯与铜的化学置换反应。
从置换的反应来看,钯与铜的反应速度会越来越慢,当钯将铜完全覆盖后(不考虑浸镀的疏孔性),置换反应会停止,但实际生产中,不可能也不必要将铜面彻底活化,(将铜面完全覆盖),从成本上讲,这会使钯的消耗大幅上升,更重要的是,这样容易造成渗镀等严重品质问题。
由于钯的本身特性,活化槽存在着不稳定这一因素,槽液中会产生细微的钯颗粒,这些颗粒不但会沉积在板的PAD 上,而且沉积在基材、板面及槽壁上,当其累计到一定程度,就可能造成板渗镀及槽壁发黑等现象。
化学镍金
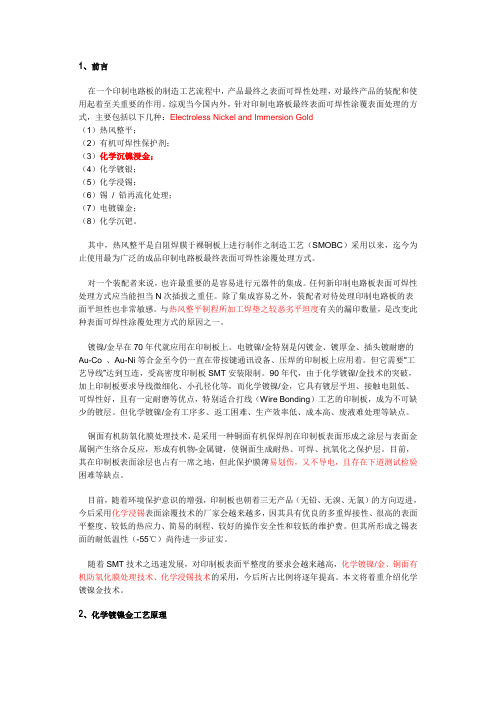
1、前言在一个印制电路板的制造工艺流程中,产品最终之表面可焊性处理,对最终产品的装配和使用起着至关重要的作用。
综观当今国内外,针对印制电路板最终表面可焊性涂覆表面处理的方式,主要包括以下几种:Electroless Nickel and Immersion Gold(1)热风整平;(2)有机可焊性保护剂;(3)化学沉镍浸金;(4)化学镀银;(5)化学浸锡;(6)锡/ 铅再流化处理;(7)电镀镍金;(8)化学沉钯。
其中,热风整平是自阻焊膜于裸铜板上进行制作之制造工艺(SMOBC)采用以来,迄今为止使用最为广泛的成品印制电路板最终表面可焊性涂覆处理方式。
对一个装配者来说,也许最重要的是容易进行元器件的集成。
任何新印制电路板表面可焊性处理方式应当能担当N次插拔之重任。
除了集成容易之外,装配者对待处理印制电路板的表面平坦性也非常敏感。
与热风整平制程所加工焊垫之较恶劣平坦度有关的漏印数量,是改变此种表面可焊性涂覆处理方式的原因之一。
镀镍/金早在70年代就应用在印制板上。
电镀镍/金特别是闪镀金、镀厚金、插头镀耐磨的Au-Co 、Au-Ni等合金至今仍一直在带按键通讯设备、压焊的印制板上应用着。
但它需要“工艺导线”达到互连,受高密度印制板SMT安装限制。
90年代,由于化学镀镍/金技术的突破,加上印制板要求导线微细化、小孔径化等,而化学镀镍/金,它具有镀层平坦、接触电阻低、可焊性好,且有一定耐磨等优点,特别适合打线(Wire Bonding)工艺的印制板,成为不可缺少的镀层。
但化学镀镍/金有工序多、返工困难、生产效率低、成本高、废液难处理等缺点。
铜面有机防氧化膜处理技术,是采用一种铜面有机保焊剂在印制板表面形成之涂层与表面金属铜产生络合反应,形成有机物-金属键,使铜面生成耐热、可焊、抗氧化之保护层。
目前,其在印制板表面涂层也占有一席之地,但此保护膜薄易划伤,又不导电,且存在下道测试检验困难等缺点。
目前,随着环境保护意识的增强,印制板也朝着三无产品(无铅、无溴、无氯)的方向迈进,今后采用化学浸锡表面涂覆技术的厂家会越来越多,因其具有优良的多重焊接性、很高的表面平整度、较低的热应力、简易的制程、较好的操作安全性和较低的维护费。
PCB沉金工艺介绍
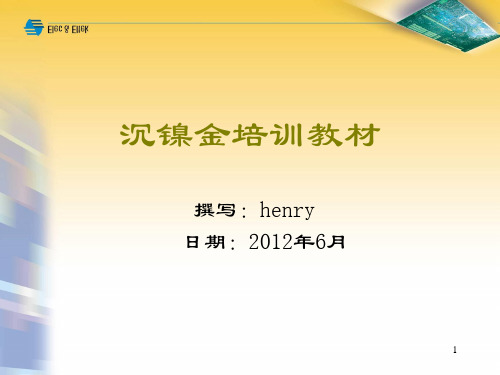
化学镍药水的分类:
按操作温度分可将镀液分成高温镀液(85950C)、中温镀液(65-750C)、低温 镀液(500C)以下
按其使用的还原剂又可大致分为次磷酸盐 型、硼氢化物型、肼型、胺基硼烷型4种。
26
按pH值分又可将其分为酸性镀液和碱性镀 液; 最常用的是次磷酸盐为还原剂的酸性高温 化学镀镍液,常称为普通化学镀镍液。
1.5 ±0.5min
搅拌:摆动及药液循环搅拌或空气打气
槽材质:PVC或PP
加热器:石英或铁弗龙加热器
15
铜浓度控制:
由于Cu2+对微蚀速率影响较大,通 常须将Cu2+的浓度控制在5-25g/l, 以保证微蚀速率处于0.5-1.5μm之间。 生产过程中,换缸时往往保留1/5-1/3 缸母液(旧液),以保持一定的Cu2+浓 度。
通常情况,不采用调节药水浓度或 升高温度来弥补因时间不足而引起的镍 厚不足,一定要根据客户镍层要求来设 置适当的镀镍时间。否则,可能引起活 性不稳定,会造成许多不良后果。
44
C、浓度: 不同供应商之不同系列药水,
其浓度控制范围各不相同。由于化 学镀镍的本身特点,其动态平衡的 控制难度远远大于化学镀铜,其控 制范围很窄则可说明这一点。因此, 尽可能使用自动补料器来控制药水 浓度,手动补料是很难保证每一个 制板的良品率。
• B、随着NaH2PO2和NiSO4浓度的增加, 沉积速度逐渐提高,而后趋于稳定或稍 有降低。但此时溶液的稳定性下降;
40
•C、化学镀镍层的厚度一般控制4~5μm, 最少要大于2.5μm厚的镍磷层才能起到 有效的阻挡层作用,防止铜的迁移,以免渗 出金面,氧化后导致导电性不良;
•D、镀覆PCB的装载量(裸铜面)应适 中,以0.1~0.5dm2/L为宜。负载太大会导 致镍缸活性逐渐升高,甚至导致反应失 控,造成严重后果;负载太低会导致镍 缸活性逐渐降低,造成漏镀等问题。
化学镍金基础知识
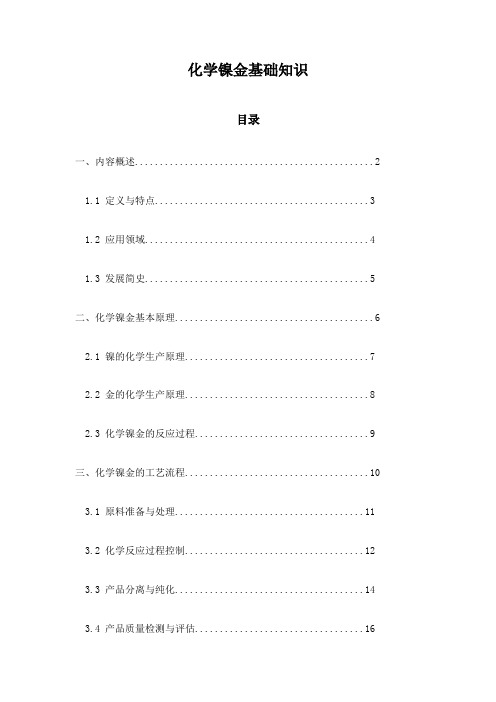
化学镍金基础知识目录一、内容概述 (2)1.1 定义与特点 (3)1.2 应用领域 (4)1.3 发展简史 (5)二、化学镍金基本原理 (6)2.1 镍的化学生产原理 (7)2.2 金的化学生产原理 (8)2.3 化学镍金的反应过程 (9)三、化学镍金的工艺流程 (10)3.1 原料准备与处理 (11)3.2 化学反应过程控制 (12)3.3 产品分离与纯化 (14)3.4 产品质量检测与评估 (16)四、化学镍金的材料与技术 (17)4.1 镍的化合物与材料 (17)4.2 金的化合物与材料 (19)4.3 化学反应设备与工艺装置 (20)4.4 安全防护措施与环保要求 (22)五、化学镍金的性质与应用 (23)5.1 镍的性质与应用领域 (25)5.2 金的性质与应用领域 (26)5.3 化学镍金的应用实例分析 (27)六、化学镍金的实验方法与操作技巧 (28)6.1 实验设计与准备 (29)6.2 实验操作规范与注意事项 (30)6.3 数据记录与分析方法 (31)6.4 实验总结与改进建议 (33)七、化学镍金的前景与挑战 (34)7.1 发展前景展望 (34)7.2 面临的挑战与问题 (36)7.3 技术创新与产业升级建议 (37)一、内容概述化学镍金概念介绍:首先介绍了化学镍金的概念,以及其作为一种重要的表面处理技术,在现代工业和科技领域中的广泛应用。
化学镍金是通过化学反应在金属表面形成一层具有优异性能的镍金涂层的过程。
该涂层具有高导电性、良好的耐腐蚀性以及出色的耐磨性能等特点。
化学镍金的基本原理:详细阐述了化学镍金的基本原理,包括化学镀镍和电镀金的原理。
化学镀镍是通过化学反应在金属表面形成一层均匀且致密的镍涂层,而电镀金则是在已形成的镍涂层上通过电解方式沉积一层薄金层。
这些原理是化学镍金技术的基础,对于理解其工艺过程和应用具有重要意义。
化学镍金的工艺过程:介绍了化学镍金的工艺过程,包括表面处理、化学镀镍、电镀金等步骤。
(完整版)沉镍金流程

达到所需之镍层厚度。
• 化学反应: Ni2+ +2H2PO2- +2H2O
Ni
+2HPO32-+4H++H2
• 副反应: 4H2PO2+2P+2H2O+H2
2HPO32-
12
反应机理
• H2PO2- +H2O HPO32-+H++2H • Ni2++2H Ni+2H+ • H2PO2-+H OH-+P+H2O • H2PO2- + H2O HPO32-+H++H2
20
2、操作条件:
Na2S2O8: H2SO4: Cu2+ :
100±20g/l 20 ±10g/l 5~25g/l
温度:
30 ±2OC
时间:
1.5 ±0.5min
搅拌:摆动及药液循环搅拌或空气打气
槽材质:PVC或PP
加热器:石英或铁弗龙加热器
21
3、铜浓度控制:
由于Cu2+对微蚀速率影响较大,通 常 须 将 Cu2+ 的 浓 度 控 制 在 5-25g/l , 以保证微蚀速率处于0.5-1.5μm之间。 生产过程中,换缸时往往保留1/5-1/3 缸母液(旧液),以保持一定的Cu2+浓 度。
22
4、逆流水洗:
由于带出的微蚀残液,会导致铜 面在水洗过程中迅速氧化,所以微蚀 后水质和流量以及浸泡时间都须特别 考虑。否则,预浸缸会产生太多的 Cu2+,继而影响钯缸寿命。所以,在 条件允许的情况下(有足够的排缸), 微蚀后二级逆流水洗,之后再加入5% 左右的硫酸浸洗,经二级逆流水洗后 进入预浸缸。
线路板生产工艺流程
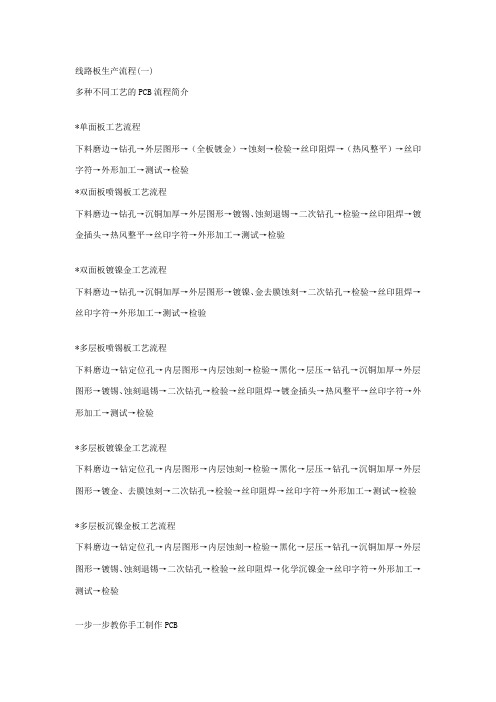
线路板生产流程(一)多种不同工艺的PCB流程简介*单面板工艺流程下料磨边→钻孔→外层图形→(全板镀金)→蚀刻→检验→丝印阻焊→(热风整平)→丝印字符→外形加工→测试→检验*双面板喷锡板工艺流程下料磨边→钻孔→沉铜加厚→外层图形→镀锡、蚀刻退锡→二次钻孔→检验→丝印阻焊→镀金插头→热风整平→丝印字符→外形加工→测试→检验*双面板镀镍金工艺流程下料磨边→钻孔→沉铜加厚→外层图形→镀镍、金去膜蚀刻→二次钻孔→检验→丝印阻焊→丝印字符→外形加工→测试→检验*多层板喷锡板工艺流程下料磨边→钻定位孔→内层图形→内层蚀刻→检验→黑化→层压→钻孔→沉铜加厚→外层图形→镀锡、蚀刻退锡→二次钻孔→检验→丝印阻焊→镀金插头→热风整平→丝印字符→外形加工→测试→检验*多层板镀镍金工艺流程下料磨边→钻定位孔→内层图形→内层蚀刻→检验→黑化→层压→钻孔→沉铜加厚→外层图形→镀金、去膜蚀刻→二次钻孔→检验→丝印阻焊→丝印字符→外形加工→测试→检验*多层板沉镍金板工艺流程下料磨边→钻定位孔→内层图形→内层蚀刻→检验→黑化→层压→钻孔→沉铜加厚→外层图形→镀锡、蚀刻退锡→二次钻孔→检验→丝印阻焊→化学沉镍金→丝印字符→外形加工→测试→检验一步一步教你手工制作PCB制作PCB设备与器材准备(1)DM-2100B型快速制板机1台(2)快速腐蚀机1台(3)热转印纸若干(4)覆铜板1张(5)三氯化铁若干(6)激光打印机1台(7)PC机1台(8)微型电钻1个(1)DM-2100B型快速制板机DM一2100B型快速制板机是用来将打印在热转印纸上的印制电路图转印到覆铜板上的设备,1)【电源】启动键一按下并保持两秒钟左右,电源将自动启动。
2)【加热】控制键一当胶辊温度在100℃以上时,按下该键可以停止加热,工作状态显示为闪动的“C”。
再次按下该键,将继续进行加热,工作状态显示为当前温度;按下此键后,待胶辊温度降至100℃以下,机器将自动关闭电源;胶辊温度在100℃以内时,按下此键,电源将立即关闭。
表面处理之化学沉镍金

化学沉镍金部分本公司EC-303系列为弱酸性镍/磷合金化学镍镀液,具有如下特性:、镀层磷含量稳定,镀层组成Ni93±1% P 7±1% 。
、适用于PCB/FPC沉镍金,FPC沉镍金时仅镍缸参数有所不同。
、操作温度范围宽,对绿油攻击极小。
、槽液稳定,管理简易方便,镍槽可使用自动加药装置。
、化学镍沉积速率稳定:PCB一般为10~13um/hr,FPC一般为8~11 um/hr。
、生产中前后制程对化学沉镍金的影响生产中前后制程对化学沉镍金的影响、板材:特殊板材吸附钯能力特强,在水洗不足或镍缸活性较强时,易出现渗镀现象。
如一些无卤素单面板材,孔及背面易上镍金。
一般采用过毒钯液处理或适当降低镍缸活性做板,即可避免。
、钻孔:钻孔进、退刀速率控制不良,钻咀刀锋前缘有损坏,导致钻孔后孔壁太粗糙,则化镍金时N-PTH孔易上镍金。
、图形制作/图形电镀:在线路制作工序,因板面显影不良易导致图形电镀时板面粗糙、发白。
此类缺陷是电镀铜后夹在铜层下面,经表面处理无法去除,而在化镍金时镍层无法掩盖此缺陷,最终的结果直接导致报废。
图形电铜面本身颗粒、针孔、发白、子弹孔等问题在化镍金时亦会呈现类似问题。
、蚀刻/退锡:蚀刻不净问题,在化镍金时可能会长胖或架桥,或N-PTH孔上镍金;有NPTH孔的化镍金板在蚀刻后、退锡前需做毒钯处理,否则NPTH孔容易上Ni/Au;剥锡不净问题,在化镍金时可能会出现白点或露铜甚至甩镍金现象。
丝印阻焊油:渗油(干绿油)、显影不净(感光绿油)等常见问题,在化镍金时极易出现发白、漏镀或甩镍金;油墨烘烤不够,曝光能量过低或者油墨厚度低于15um,在化镍金后极易出现掉油,油墨起泡。
曝光菲林上有垃圾时,化镍金后防焊油墨会点状上镍金。
若显影液残留板面未处理干净则化镍金时容易出现白点与阴阳色问题。
、化镍金前处理的刷磨:.最好使用800#以上或1000#、1200#磨辘细磨,磨辘太粗磨痕太深,化镍金时,金面可能会粗糙或发白,同时也会伤及阻焊油与保护膜,刷磨太轻太浅,则达不到应有的效果。
化金工艺

化学镍金工艺讲座pcb技术2010-05-20 09:43:11 阅读69 评论0 字号:大中小订阅化学镍金工艺讲座一、概述化学镍金又叫沉镍金,业界常称为无电镍金(Electroless Nickel Immersion Gold)又称为沉镍浸金.PCB化学镍金是指在裸铜面上化学镀镍,然后化学浸金的一种可焊性表面涂覆工艺.它既有良好的接触导通性,而且具有良好的装配焊接性能,同时它还可以同其它表面涂覆工艺配合使用.随着日新月异的电子业的民展,化学镍金工艺所显出的作用越来越重要.二、化学镍金工艺原理2.1 化学镍金催化原理2.1.1 催化作为化学镍金的沉积,必须在催化状态下,才能发生选择性沉积.Ⅷ族元素及Au等许多金属都可以作为化学镍的催化晶体.铜原子由于不具备化学镍沉积的催化晶种的特性,所以通过置换反应可使铜面沉积所需要的催化晶种.2.1.2 钯活化剂PCB业界大都使用PdSO4或PdCl2作为化学镍前的活化剂在活化制程中,其化学反应如下:Pd2++Cu→Pd+Cu2+2.2 化学镍原理2.2.1 化学镍在钯(或其它催化晶体)的催化作用下,Ni2+被NaH2PO2还原沉积在裸铜表面.当镍沉积覆盖钯催化晶体时,自催化反应将继续进行,直到达到所需要之镍层厚度.2.2.2 化学反应在催化条件下,化学反应产生镍沉积的同时,不但伴随着P的析出,而且产生氢气的逸出.主反应:Ni2++2H2PO2-+2H2O→N i+2HPO32-+4H++H2↑副反应:4H2PO2-→2HPO32--+2P+2 H2O+H22.2.3 反应机理H2PO2-+H2O→H++HPO32-+2HNi2++2H→Ni+2H+H2PO2-+H→H2O+OH-+PH2PO2-+H2O→H++HPO32-+H2↑2.2.4 作用化学镍的厚度一般控制在3~5μm,其作用同金手指电镀镍一样,不但对铜面进行有效保护,防止铜的迁移,而且具备一定硬度和耐磨性能,同时拥有良好的平整度.在镀件浸金保护后,不但可以取代拨插不频繁的金手指用途(如计算机内存条),同时还可以避免金手指附近连接导电处斜边时所遗留裸铜切口.2.3 浸金原理2.3.1 浸金是指在活性镍表面,通过化学置换反应沉积薄金.化学反应:2Au(CN)2-+Ni→2Au+Ni2++4CN-2.3.2 作用浸金的厚度一般控制在0.05~0.1μm,对镍面具有良好的保护作用,而且具备很好的接触导通性能.很多需按键接触的电子器械(如手机、电子字典),都采用化学浸金来保护镍面.三、化学镍金工艺流程3.1 工艺流程简介作为化学镍金流程,只要具备6个工作站就可满足其生产要求.3~7min1~2min0.5~4.5min2~6min20~30min7~11min除油微蚀预浸活化沉镍沉金3.2 工艺控制3.2.1 除油缸一般情况,PCB沉镍金采用酸性除油剂来处理制板,其作用在于去除铜面之轻度油脂及氧化物,达到铜面清洁及增加润湿效果的目的.它应当具备不伤Soider Mask(绿油),低泡型易水洗的特点.除油缸之后通常为二级市水洗,如果水压不稳定或经常变化,则将逆流水洗设计为三及市水洗更佳.3.2.2 微蚀缸微蚀的目的在于清洁铜面氧化及前工序遗留残渣,保持铜面新鲜及增加化学镍层的密着性,常用微蚀液为酸性过硫酸钠溶液.Na2S2O8:80~120g/L硫酸:20~50ml/L沉镍金生产也有使用硫酸双氧水或酸性过硫酸钾微蚀液来进行的.由于铜离子对微蚀速率影响较大,通常须将铜离子的浓度控制有5~25g/L,以保证微蚀速率处于0.5~1.5μm,生产过程中,换缸时往往保留1/5~1/3缸母液(旧液),以保持一定的铜离子浓度,也有使用少量氯离子加强微蚀效果.另外,由于带出的微蚀残液,会导致铜面在水洗过程中迅速氧化,所以微蚀后水质和流量以及浸泡时间都须特别考虑.否则,预浸缸会产生太多的铜离子,继而影响钯缸寿命.所以,在条件允许的情况下(有足够的排缸),微蚀后二级逆流水洗之后,再加入5%左右的硫酸浸洗,经二级逆流水洗之后进入预浸缸.3.2.3 预浸缸预浸缸在制程中没有特别的作用,只是维持活化缸的酸度以及使铜面在新鲜状态(无氧化物)下,进入活化缸.理想的预浸缸除了Pd之外,其它浓度与活化缸一致.实际上,一般硫酸钯活化系列采用硫酸作预浸剂,盐酸把钯活化系列采用盐酸作预浸剂,也有使用铵盐作预浸剂(PH值另外调节).否则,活化制程失去保护会造成钯离子活化液局部水解沉淀.3.2.4 活化缸活化的作用是在铜面析出一层钯,作为化学镍起始反应之催化晶核.其形成过程则为Pd与Cu的化学置换反应.从置换反应来看,Pd与Cu的反应速度会越来越慢,当Pd与Cu完全覆盖后(不考虑浸镀的疏孔性),置换反应即会停止,但实际生产中,人们不可能也不必要将铜面彻底活化(将铜面完全覆盖).从成本上讲,这会使Pd的消耗大幅大升.更重要的是,这容易造成渗镀等严重品质问题.由于Pd的本身特性,活化缸存在着不稳定这一因素,槽液中会产生细微的(5m滤芯根本不可能将其过滤)钯颗粒,这些颗粒不但会沉积在PCB的Pad位上,而且会沉积在基材、绿油以及缸壁上.当其积累到一定程度,就有可能造成PCB渗镀以及缸壁发黑等现象.影响钯缸稳定性的主要原因除了药水系列不同之外,钯缸控制温度和钯离子浓度则是首要考虑的问题.温度越低,钯离子浓度越低,越有利于钯缸的控制.但不能太低,否则会影响活化效果,引起漏镀发生. 通常情况下,钯缸温度设定在20~30℃,其控制范围应在±1℃,而钯离子浓度则控制在20~40ppm,至于活化效果,则按需要选取适当的时间.当槽壁及槽底出现灰黑色的沉积物,则需硝槽处理.其过程为:加入1:1硝酸,启动循环泵2小时以上或直到槽壁灰黑色沉积物完全除去为止.适当时可考虑加热,但不可超过50℃,以免空气污染. 另外,也有人认为活化带出的钯离子残液在水洗过程中会造成水解,从而吸附在基材上引起渗镀,所以,应在活化逆流水洗之后,多加硫酸或盐酸的后浸及逆流水洗的制程.事实上,正常情况下,活化带出的钯离子残液体,在二级逆流水洗过程中可以被洗干净.吸附在基材上的微量元素,在镍缸中不足以导致渗镀的出现.另一方面,如果说不正常因素导致基材吸附大量活化残液,并不是硫酸或盐酸能将其洗去,只能从根源去调整钯缸或镍缸.增加后浸及逆流水洗,其作用只是避免水中Pd含量太多而影响镍缸. 需要留意的是,水洗缸中少量的Pd带入镍缸,并不会对镍缸造成太大的影响,所以不必太在意活化后水洗时间太短,一般情况下,二级水洗总时间控制在1~3min为佳.尤其重要的是,活化后水洗不可使用超声波装置,否则,不但导致大面积漏镀,而且渗镀问题依然存在.3.2.5 沉镍缸化学沉镍是通过Pd的催化作用下,NaH2PO2水解生成原子态H,同时H原子在Pd催化条件下,将镍离子还原为单质镍而沉积在裸铜面上.作为化学沉积的金属镍,其本身也具备催化能力.由于其催化能力劣于钯晶体,所以反应初期主要是钯的催化作用在进行.当镍的沉积将钯晶体完全覆盖时,如果镍缸活性不足,化学沉积就会停止,于是漏镀问题就产生了.这种渗镀与镍缸活性严重不足所产生的漏镀不同,前者因已沉积大约20μ"的薄镍,因而漏镀Pad位在沉金后呈现白色粗糙金面,而后者根本无化学镍的沉积,外观至发黑的铜色.从化学镍沉积的反应看出,在金属沉积的同时,伴随着单质磷的析出.而且随着PH值的升高,镍的沉积速度加快的同时,磷的析出速度减慢,结果则是镍磷合金的P含量降低.反之,随着PH值的降低,镍磷含金的P含量升高.化学镍沉积中,磷含量一般在7~11%之间变化.镍磷合金的抗蚀性能优于电镀镍,其硬度也比电镀镍高.在化学沉镍的酸性镀液中,当PH6时,镀液很容易产生Ni(OH)2沉淀.所以一般情况,生产中PH值控制在4.5~5.2之间.由于镍沉积过程产生氢离子(每个镍原子沉积的同时释放4个氢离子),所以生产过程中PH的变化是很快的,必须不断添补碱性药液来维持PH值的平衡.通常情况下,氯水和氢氧化钠都可以用于生产维持PH值的控制,两者在自动补药方面差别不大,但在手动补药时就应特别关注.加入氨水时,可以观察到蓝色镍氨络离子出现,随即扩散时蓝色消失,说明氨水对化学镍是良好的PH调整剂.在加入氢氧化钠溶液时,槽液立即出现白色氢氧化镍沉淀粉末析出,随着药水扩散,白色粉末在槽液的酸性环境下缓慢溶解.所以,当使用氢氧化钠溶液作为化学镀的PH 调整剂时,其配制浓度不能太高,加药时应缓慢加入.否则会产生絮状粉末,当溶解过程未彻底完成前,絮状粉末就会出现镍的沉积,必须将槽液过滤干净后,才可以重新开始生产.在化学镍沉积的同时,会产生亚磷酸盐(HPO32-)的副产物,随着生产的进行,亚磷酸盐浓度会越来越高,于是反应速度受生成物浓度的长高而抑制,所以镍缸寿命末期与初期的沉积速度相差1/3则为正常现象.但此先天不足可采用调整反应物浓度方式予以弥补,开缸初期Ni2+浓度控制在4.60g/L,随着MTO的增加Ni2+浓度控制值随之提高,直至5.0g/L停止.以维持析出速度及磷含量的稳定,以确保镀层品质.影响镍缸活性最重要的因素是稳定剂的含量,常用的稳定剂是Pb(CH3COO)2或硫脲,也有两种同时使用的.稳定剂的作用是控制化学沉镍的选择性,适量的稳定剂可以使活化后的铜面发生良好的镍沉积,而基材或绿油部分则不产生化学沉积.当稳定剂含量偏低时,化学沉镍的选择性变差,PCB表面稍有活性的部分都发生镍沉积,于是渗镀问题就发生了.当稳定剂含量偏高时,化学沉积的选择性太强,PCB漏铜面只有活化效果很好的铜位才发生镍沉积,于是部分Pad位出现漏镀的现象.镀覆PCB的装载量(以裸铜面积计)应适中,以0.2~0.5dm2/L为宜.负载太大会导致镍缸活性逐渐升高,甚至导致反应失控;负载太低会导致镍缸活性逐渐降低,造成漏镀问题.在批量生产过程中,负载应尽可能保持一致,避免空缸或负载波动太大的现象.否则,控制镍缸活性的各参数范围就会变得很窄,很容易导致品质问题发生.镀液应连续过滤,以除去溶液中的固体杂质.镀液加热时,必须要有空气搅拌和连续循环系统,使被加热的镀液迅速传播.当槽内壁沉积镍层时,应该及时倒缸(将药液移至另一备用缸中进行生产),然后用25%~50%(V/V)的硝槽进行褪除,适当时可考虑加热,但不可超过50℃.至于镍缸的操作控制,在温度方面,不同系列沉镍药水其控制范围不同.一般情况下,镍缸操作范围86±5℃,有的药水则控制在81±5℃.在生产中,具体设定根据试板结果来定,不同型号的制板,有可能操作温度不同.通常一个制板的良品操作范围只有±2℃,个别制板也有可能小于±1℃.在浓度控制方面,采用对Ni2+的控制来调节其它组分的含量,当Ni2+浓度低于设定值时,自动补药器开始添加一定数量的药水来弥补所消耗的Ni2+,而其它组分则依据Ni2+添补量按比例同时添加.镍层的厚度与镀镍时间呈线性关系.一般情况下,200μ"镍层厚度需镀镍时间28min,150μ"镍层百度需镀镍时间21min左右.由于不同的制板所需的活性不同,为减轻镍缸控制的压力(即增大镍缸各参数的控制范围),可以考虑采用不同的活化时间,例如正常生产Pd缸有一个时间,容易渗镀的制板另设定活化时间.这样一来,则可以组合成六个程序来进行生产.需要留意的是,对于多程序生产,应当遵循一个基本原则,就是所有程序飞巴的起始位置必须保持一致,否则连续生产中切换程序容易造成过多的麻烦.镍缸的循环量一般设计在5~10turn over(每小时),布袋式过滤应优先选择考虑.摇摆通常都是前后摆动设计,但对于laser盲孔板,镍缸和金缸设计为上下振动为佳.3.2.6 沉金缸置换反应形式的浸金薄层,通常30分钟可达到极限厚度.由于镀液Au的含量很低,一般为1~2g/L,溶液的扩散速度影响到大面积Pad 位与小面积Pad位沉积厚度的差异.一般来说,独立位小Pad位要比大面积Pad位的金厚度高100%也属正常现象.对于PCB的沉金,其金面厚度也会因内层分布而相互影响,其个别Pad位也会出较大的差异.通常情况下,沉金缸的浸镀时间设定在7~11分钟,操作温度一般在80~90℃,可以根据客户的金厚要求,通过调节温度来控制金厚.需要留意的是,金缸容积越大越好,不但其Au浓度变化小而有利于金厚控制,而且可以延长换缸周期.为了节省成本,金缸之后需加装回收水洗,同时也可减轻对环境的污染.回收缸之后,一般都是逆流水洗.四、关于生产线的设计4.1 沉镍金自动线4.1.1 排缸从生产线的角度来看,排缸数量越少越好,一方面可以减少不必要的天车运行距离和时间,另一方面,还可以节省投资成本以及占地空间. 关于排缸的顺序,一般情况应从产能、滴水污染、天车运行及操作方便等几个因素来考虑.镍缸由于保养费时,所以应当排放一备用缸.对于每天大约3KSF产能的生产线,设计一台天车则可以满足生产,建议排缸顺序如下:(1)上下料、(2)(3)(4)三级逆流水洗、(5)回收、(6)金缸、(7)(8)二级逆流水洗、(9)(10)双架位镍缸、(11)(12)备用双架位镍缸、(13)(14)二级逆流水洗、(15)活化缸、(16)预浸缸、(17)(18)二级逆流水洗、(19)酸洗缸、(20)(21)二级逆流水洗、(22)微蚀缸、(23) (24)(25) 三级逆流水洗、(26)除油缸对于每天大约4.5 KSF产能的生产线,需设计两台天车来满足生产需求,建议排缸顺序如下:(1)上下料、(2)(3)(4)三级逆流水洗、(5)回收、(6) (7)双架位金缸、(8) (9)二级逆流水洗、(10) (11)(12)三架位镍缸、(13)(14) (15)备用三架位镍缸、(16) 除油缸、(17)(18) (19)三级逆流水洗、(20)微蚀缸、(21)(22)二级逆流水洗、(23)酸洗缸、(24)(25)二级逆流水洗、(26) 预浸缸、(27)活化缸、(28)(29)二级逆流水洗对于每天大约6KSF的生产数,只需将三架位镍缸改为四架位镍缸即可.对于更大产能的生产线,则应考虑将缸的宽度和深度以及长度加大,以提高每架板的挂板数量.4.1.2 挂板设计关于挂窗尺寸,一般考虑最大板横挂.如18"×24"板则将24"边打横挂入,否则药水在板面滑落时间比横挂增加30%以上.因此,镍缸的有效宽度和有效深度一般为26"×21"左右,其它缸则参考镍缸的挂板空间.这样的设计,可以避免镍缸太深而导致药水交换不佳等问题.同时小尺寸生产则可以挂两排,以增加产量和弥补镍缸负载的不足.关于挂具的设计,应最大限度减少挂具在药液中浸泡的面积,降低药水带出以及挂具上沉积镍金的问题.同时,硝挂具一般采用王水,其操作的困难度较大,所以也应考虑保养的方便.建议使用PP夹板,每个挂具挂板15~20块,每块隔板的厚度以10mm 为佳.顶部以316不锈钢定夹板,下边以铁弗龙包胶U型相框来固定挂板.4.1.3 缸体材质由于镍缸和金缸操作温度在80~90℃,所以缸体不但须耐高温,而且须不易渗漏.所以一般使用316不锈钢做镍缸,缸壁最好采用镜面抛光.金缸一般使用耐热PP或不锈钢内衬铁弗龙.其它缸采用普通PP 材质即可.对于镍缸,如果仅生产单双面板,也可考虑使用耐热PP材质.但对于盲孔板,由于布线复杂,沉镍金生产过程中,线路间有可能出现相互影响而易产生漏镀,所以镍缸操作比单、双面板要高出5℃左右,甚至达到90℃以上.对采用PP材质的镍缸,不可避免产生大量的镍沉积在缸底,给操作带来很多问题.所以,镍缸及其缸内附件,包括加热和打气系统,如果使用不锈钢材质,则能够通过正电保护抑制上镍,不但使用镍缸操作变得容易,而且在成本方面避免不必要的浪费. 4.1.4 程序沉镍金生产,往往不可能只有一两种制板生产.由于每一种制板都有可能需要不同的活性,所以沉镍金生产线,最好有四个以上的程序段,来满足不同的生产需求.4.2 前后处理设备4.2.1 前处理由于沉镍金生产中"金面颜色不良"问题,通过调整系统活性以及加强微蚀速度等方式,虽然有时会凑效,但常常既费时又费力,而且这些措施很不安全,稍不注意就产生另一种报废.所以,在有条件的情况下,另设计一条水平线作为前处理,通过增加制程来拓宽沉镍金参数范围的控制.磨刷→水洗→微蚀→水洗→干板磨刷:通常采用500-1000#尼龙刷辘,在喷水装态下清洁铜面,以除去绿油工序残留的药液以及轻度的冲板不净剩余残渣.如果绿油工序制程稳定,或出现问题的可能性很小,则磨刷这个制程不需要设计.微蚀:通常使用80-120g/L的过硫酸钠与5%的硫酸配制槽液,通过调节温度,使微蚀率控制在1μm左右,它的作用是清洁铜面.去除前工序(主要指绿油)残留在板面的药水渍或严重氧化等铜面杂物,防止沉镍金出现由前工序引起的甩镍、金面颜色不良、渗镀等问题.需要注意的是,前处理若使用了水平微蚀剂,沉镍金制程中的微蚀缸仍需保留,但微蚀率达到0.5μm即可,否则易造成铜厚不足的问题.4.2.2 后处理由于沉镍金表面正常情况下光洁度和平整度很好,所以轻微的金面氧化或水渍都会使金面颜色变得很难看.而沉镍金生产线纵然控制到最佳,也只能杜绝金面氧化,对于烘干缸因水珠而遗留的水渍实在是无能为力.高压水洗机不但可以有效地清洗板面残留药水,防止金面氧化,而且干板过程有风力将水珠吹走,完全避免残留水珠而造成的水渍问题. 也有人在高压水洗机前加一段2%的酸洗段,以洗去因金缸后造成的金面氧化.这也是事后补救的一种可取的方法.因为金面残留的药水在短短的水洗过程中造成金面氧化,那说明它对金面的攻击作用是远远大于2%的盐酸或硫酸,而且水平酸洗过程也不足十秒,之后又有高压水洗和干板,其对于镍金面的影响应该可以忽略不计.但是,有的客户明确提出而且强烈反对沉金板酸洗,那也是没有办法的事,客户是上帝,他不喜欢的事最好别做.4.3 循环过滤泵、加热及打气装置4.3.1 循环过滤泵为保持槽液有一定的循环效果,除油、微蚀、活化、沉镍、沉金各缸都需要加装循环泵,除镍缸之外以上各缸还需加装过滤器,通过5μm 滤芯来过滤槽液.对于镍缸其循环不但要求均匀,有利于药液扩散和温度扩散,而且不能流速太快而影响化学镍的沉积,通常其循环量6-7turn over为佳.同时镍缸还需过滤,以除去槽液中杂物.由于棉芯容易上镍,所以应首先考虑布袋式过滤系统.关于镍缸的溢流问题,由主缸流入副缸,更有利于药水扩散和温度平衡.4.3.2 加热装置除油、微蚀、活化、沉镍、沉金各缸都需要加热系统,除镍金之外,均可使用石英或铁弗龙加热器.对于镍缸,最好采用不锈钢加热交换管,且须外接下电保护.因为自动补药器是在副缸加药,所以须留意加药口不可正对副缸中的加热器.4.3.3 打气装置微蚀和镍缸的主副槽以及各水洗缸都应加装打气系统.生产时通常是除油后第一道水洗、镍缸主槽、及镍缸后水洗处于打气关闭状态.对于镍缸,每一根加热管下方都应该保持强力打气状态.4.4 接口设备沉镍金生产线的周边附属设施中,首先需要的是DI水机,各药水缸配槽以及活化、沉镍、金回收之后的水洗缸,都需要使用DI水.有的厂采用中央DI水处理,半管道接入沉金线,那则是最理想的设计. 在生产过程中,由于活化缸和微蚀缸对温度要求很严格,所以应当购置冷水机来控制槽液温度.对于镍缸,有的人嫌降温过程太慢(由操作温度降至50℃以下),将冷水管(临时管道)接入镍缸,这也是充分利用现有资源的好方法.由于镍缸硝槽时使用硝酸数量较大,而且不便重复利用,所以,在镍缸底部连接一备用硝酸槽,通过一个抽水马达(须耐硝酸)以及换向阀,将硝酸抽到所需的槽中.须留意的是,管理槽(贮存硝酸)的容积要大于镍缸20-50%.沉镍金周边设施除DI水机、冷水机及管理槽,还须将生产线污浊空气抽出,送往化气塔净化.同时,生产线最好也加装送风装置,以保持操作环境的空气新鲜.五、工序常见缺陷分析5.1 漏镀5.1.1 主要原因体系活性(镍缸及钯缸)相对不足;铅、锡等铅面污染.5.1.2 问题分析漏镀的成因在于镍缸活性不能满足Pad位的反应势能,导致沉镍化学反应中途停止,或者根本未沉积金属镍.漏镀的特点是:如果一个Pad位漏镀,与其相连的所有Pad位都漏镀.出现漏镀问题,首先须区分是否由外界污染板面所致.若是,将该板进行水平微蚀或采用磨板方式除去污染.影响体系活性的最主要因素是镍缸稳定剂浓度,但由于难以操作控制,一般不采取降低稳定剂浓度来解决该问题.影响体系活性的主要因素是镍缸温度.升高镍缸温度,一定有利于漏镀的改善.如果不考虑外部环境以及内部稳定性,无限度的升高镍缸温度,应该能解决漏镀问题.影响体系活性的次要因素是活化浓度、温度和时间.延长活化的时间或提高活化浓度和温度,一定有利于漏镀的改善.由于活化的温度和浓度太高会影响钯缸的稳定性,而且会影响其它制板的生产,所以,在这些次要因素中,延长时间是首选改善措施.镍缸的PH值、次磷酸钠以及镍缸负载,都会影响镍缸的活性,但其影响程度较小;而且过程缓慢.所以不宜作为改善漏镀问题的主要方法.5.2 渗镀5.2.1 主要原因体系活性太高外界污染或前工序残渣5.2.2 问题分析渗镀的主要成因在于镍缸活性过高导致选择性太差,不但使铜面发生化学沉积,同时其它区域(如基材、绿油侧边等)也发生化学沉积,造成不该出现沉积的地方沉积化学镍金.出现渗镀问题,首先须区分是否由外界污染或残渣(如铜、绿油等)所致.若是,将该板进行水平微蚀或其它的方法去除.升高稳定剂浓度,是改善体系活性太高的最直接的方法,但是,同漏镀问题改善一样,因难以操作控制而不宜采用.降低镍缸温度是改善渗镀最有效的方法.理论上,无限度的降低温度,可以彻底解决渗镀问题.降低钯缸温度和浓度,以及减少钯缸处理时间,可以降低体系活性,有效地改善渗镀问题.镍缸的PH值、次磷酸钠以及镍缸负载,降低其控制范围有利于渗镀的改善,但因其影响较小而且过程缓慢,不宜作为改善渗镀问题的主要方法.因操作不当导致钯缸或镍缸产生悬浮颗粒弥漫槽液,则应采取过滤或更新槽液来解决.5.3 甩金5.3.1 主要原因镍缸后(沉金前)造成镍面钝化镍缸或金缸杂质太多5.3.2 问题分析金层同镍层发生分离,说明镍层同金层的结合力很差,镍面出现异常而造成甩金.镍面出现钝化,是造成甩金出现的最主要因素.沉镍后在空气中暴露时间过长和水洗时间过长,都会造成镍面钝化而导致结合力不良,当然,水洗的水质出现异常,也有可能导致镍层钝化.至于镍缸或金缸是否为甩金出现的主要原因,可在实验室烧杯中做对比实验来确定,若是,则更换槽液.5.4 甩镍5.4.1 主要原因铜面不洁或活化后钯层表面钝化镍缸中加速剂失衡。
FPC工艺流程

溢流水洗 3
溢流水洗 4
清水洗 抗氧化
溢流水洗 5 溢流水洗 6 溢流水洗 7
清水洗 热风吹干 强风吹干
流程二.DES 线
显影
溢流水洗 1 溢流水洗 2
酸洗
溢流水洗 3
清水洗 Байду номын сангаас刻
溢流水洗 4 溢流水洗 5
清水洗 膨松 去膜
溢流水洗 6 溢流水洗 7
酸洗
溢流水洗 8
清水洗 强风吹干 热风吹干
6.1. 显影→溢流水洗 1→溢流水洗 2→酸洗→溢流水洗 3→清水洗→蚀刻→溢流水洗 4→溢 流水洗 5→清水洗→膨松→去膜→溢流水洗 6→溢流水洗 7→酸洗→溢流水洗 8→清水洗→强 风吹干→热风吹干
FPC 主生产流程图
流程(Process Flow) 覆铜板开料
钻孔 化学清洗
沉铜
镀铜
化学清洗
*请查看流程一
贴膜
曝光
显影 蚀刻
*请查看流程二 *请查看流程二
清洗
叠板
备注: 1.
压合
自动认位打孔
镀镍金 黄色
测试 补强 冲切 终检 包装 代表检查点
沉镍金 黄色
流程一.化学清洗线
酸性除油
溢流水洗 1 溢流水洗 2
沉镍金制作流程

沉镍金制作流程一、简介:通过化学反应在铜表面沉积较薄一层镍金、金层具有稳定的化学和电器特性,镀层具有优良的可焊性,耐蚀性等特点。
二、流程及作用:(1)沉金前处理:①微蚀:除去烘烤绿油造成的铜面过度氧化物。
② 1200#磨刷幼磨:除去铜面杂物,清洁板面。
(2)沉镍金流程:上板→除油→Ⅱ级水洗→微蚀→→Ⅱ级水洗→酸洗→Ⅱ级水洗→预浸→活化→Ⅱ级水洗→后浸酸→Ⅰ级水洗→沉镍→Ⅱ级水洗→沉金→金回收→水洗→热水洗→下板①除油:除去铜表面之轻度油脂及氧化物,使表面活化及清洁。
②微蚀:除去铜面氧化物及污染物,适度粗化铜面,增加镀层密着性、结合力。
③预浸:保护活化药液。
④活化:使用离子钯溶液使表面铜活化,可以只在铜面上沉积而基材的Pd化合物极易清洗,提供化学沉镍的启镀剂。
⑤化学镀镍:利用电子转移使溶液中的Ni2+还原在待镀铜面上而沉积出镍金属:但同时会有P析出,Ni层实际为Ni/P合金,Ni层厚度一般为100-200u〃。
⑥通过置换反应在新鲜镍面置换一层薄金,作为防止基体金属氧化和作为自身活化型镀金的底层,镍基体上覆盖一层金后金沉积就停止,所以厚度有一定了限制,Au层厚度一般为1-3 u〃。
(3)沉金后处理:①草酸洗:除去金面氧化异物,,对金层疏孔处的镍底层作酸封孔处理,增加其耐蚀性。
②抗氧化清洗:防止镀层氧化,使焊锡维持更长的寿命。
三、流程控制注意事项:(1)控制微蚀速率在0.6-0.8um,速率太低,镀层发亮,太高出现色差即金色不良。
(2)活化缸Cu2+浓度≤200PPM需更换,且后期易出现渗金。
(3)Ni缸温度不可太高,药水高温对绿油攻击较大,易出现甩S/M问题,槽液使用4.0MTD后需换槽。
(4)金缸需控制Ni2+含量≤800PPM,Ni2+太高易出现金色不良及不上金问题。
四、常见问题介绍及处理方法:(1)漏镀:①活化浓度温度过低,浴老化或活化后水洗过久。
②镍缸浓度、温度、PH值太低,或有不以纯物混入,成份失调。
化学镍金流程及注意
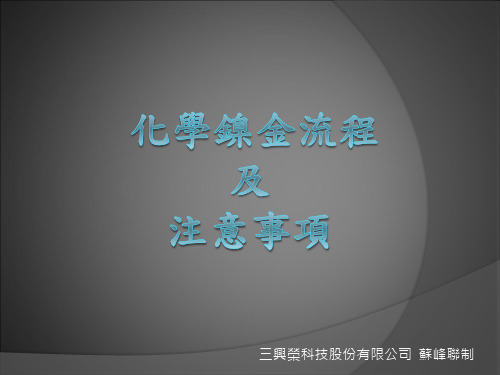
操作條件:濃度Pd 20ppm 範圍10~30ppm/L 時間1~2min 溫度25±5º C 注意事項:1.溫度對鈀附著影響甚大低於15℃時,易造 成鈀附著不足,形成無鍍層現象;高於 35℃時,鈀的附著量過多,易造成bridge ,並使無電解鎳浴的安定性變差。 2.在溫度固定下如藥液管控超出範圍之外, 就會産生酸度高,鈀濃度低,會造成SKIP (無電解鎳無法析出);相反的,酸濃度 低,鈀濃度高會造BRIDGE (擴散架橋)。
FPF-MC 建浴用(含錯化劑、還原劑、促進劑)。 FPF-1C 建浴補充用(每1L含100g鎳鹽)。 FPF-2CL 補充用(含還原劑、促進劑、安定劑、濕 潤劑)。 FPF-3C補充用(含PH調整劑)。 FPF-5建浴用,界面活性调整剂
錯 化 劑:防止PH迅速下降的緩衝劑,避免鎳離子與 亞磷酸根離子生成沈澱。 還 原 劑:Na(H2PO2)(磷的供應源)。
溫度較高
提升沈積速率 加快槽壁上鍍
溫度較低
降低沈積速率 無反應
易鎳厚不足 無鍍層
以上各項參數需控制于範圍內,其鎳:磷含量 最好控制于1:4~5,面積爲0.2dm2~0.8 dm2最爲
適當。
注意事項:1. FPF-3C主要爲調整PH值,若直接加入易 生成Ni(OH)2 之沈澱造成不良的産生,所 以需將其稀釋2倍後在攪拌處,徐徐加入 2.降低PH值可用H2SO4。 3.放入面積0.5dm2之裸銅板進行起鍍(dummy) 新建浴時間需1hr, 後起鍍30min即可。 4.須有陰極析出防止裝置,其控制電壓爲 1~2V,電流密度應在0.2~0.5A
參數變化的影響之性質:
補
充: (標準-分析)*槽體積/68.3 1.每添加100g K Au(CN)2時,約補充 1000ml GOLD—AD。 2. PH 下降時,可用試藥特級NH4OH調升 (添加時以純水稀釋1:1),調降時以試 藥特級的檸檬酸20%溶液調整。 注意事項:1.AD添加達3MTO 及鎳離子達800~1000PPM 時,應重新建浴。 2.因以高溫作業,其藥水蒸發量較大,需補 充純水。
沉镍金制作流程范文

沉镍金制作流程范文沉镍金是一种具有高精度、高硬度、高抗磨损性和耐蚀性的金属材料,广泛应用于电子器件、机械工具和汽车零部件等领域。
沉镍金的制作流程主要包括镀液制备、金属基材准备、沉镍金层的成型和后处理等环节。
以下是一个关于沉镍金制作流程的详细介绍。
一、镀液制备1.选择合适的化学品:镀液通常由羧酸镍、硫酸镍、草酸钠、硼酸和一些添加剂组成。
这些化学品具有良好的镀液稳定性和金属沉镍层的特性。
2.准备盛装器皿:选择一种能耐受镀液的器皿,如玻璃或聚丙烯材料制成的容器。
将容器清洗干净,并确保无存留的杂质。
3.称量化学品:根据制定的镀液配方,按照比例称取所需化学品,并严格控制各组分的配比。
4.配制镀液:将称取的化学品逐一加入容器中,按照特定的操作流程进行搅拌和配制,使其充分溶解和混合,形成均匀的镀液。
二、金属基材准备1.选择合适的基材:沉镍金可用于镀液重金属基材,如钢、铜、铝等。
选用基材需要根据实际使用环境和需求来确定。
2.基材的表面处理:首先,将基材进行清洗,去除表面的油污和杂质。
然后,通过酸洗、电解去氧等工艺,处理基材表面,以提高沉镍金层与基材的结合力和附着力。
三、沉镍金层的成型1.工艺参数设定:根据具体的工艺要求和所制备镀液的特点,设置适当的工艺参数,如温度、pH值、电流密度等。
2.浸泡基材:将经过处理的金属基材浸泡入镀液中,然后在规定的时间内进行电解反应。
镀液中的阳极引入电流,从而在基材上形成沉镍金层。
3.调整电流和工艺参数:根据实际观察和测量,适时调整电流密度和工艺参数,以确保沉镍金层的成型质量。
同时,根据需要,可以进行多次电镀,以增加金属层的厚度。
四、后处理1.水洗:将沉镍金层的基材进行水洗,以去除残留的镀液和杂质。
2.烘干:将水洗后的基材进行烘干处理,以去除水分。
3.烧结:为提高沉镍金层的致密性和硬度,将烘干的基材进行烧结处理,以达到金属层充分结合的目的。
4.研磨和抛光:对烧结后的沉镍金层进行研磨和抛光,以提高表面光洁度和平整度。
ElectrolessNickelandImmersionGold简称ENIG化镍沉金
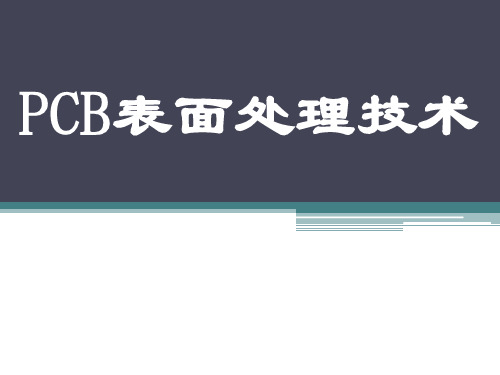
• 应用:客户指定。在高频信号中,沉Ag板电性能良好。欧美不少用户要求作
沉Ag板。 9
3.5 电镀镍金
• 流程:除油-微蚀-酸洗-纯水洗-镀镍-纯水洗-镀金-回收金-水洗 • 镀层类型:
⑴镀硬金。
用在:PCB插头,按键上。 特点:·耐磨,接触良好,有硬度(120-190㎏/㎜²﹚ ·镍打底,Ni层厚度3-5微米;金厚度:0.1,0.25,0.5,0.8,1.0…微米。 ·金镀层含有钴(Co,0.5%﹚,或Ni锑等金属。 ⑵镀软金。 纯金,24K金。 用途:焊接用。
2
2. 0、 PCB无铅化
(1)、ROHS禁令: 禁6种物质:Pb,Hg,Cr6+ (六价铬),PBB(多溴联苯),PBDE(多溴联苯乙醚)。 其中一种就是铅。 (2)、铅的毒性: 智力下降,失眠,恶梦,无力,腹胀痛,头痛,食欲不振。 典型有害影响:贫血,中枢神经系统紊乱。 (3)、何为无铅? ·物质含量中的Pb≤1000ppm,即0.1%,为无铅。 ·只要不是故意在焊料中加铅就应是无铅。
·图形镀Ni/Au。板子在图形线路上镀Ni/Au,镍金作抗蚀层。蚀刻图形后,线路、
孔、焊盘覆盖Ni/Au。但图形线路和板边上镀金浪费,在金面上印阻焊剂附着力难 以保证。目前使用的产品已不多。
(6)、无铅焊料的配方。
4
·美国熔焊: 95.9 Sn-3.9 Ag- 0.6Cu 波焊:99.3 Sn-0.7 Cu ·欧盟:95.5 Sn-3.8 Ag-0.7 Cu ·日本:96.5 Sn-3.0 Ag-0.5 Cu ,即305配方(3.0%银,0.5%铜,其余为 锡,称之为305)。 ·上述配方,共熔点是217℃。比传统的铅锡合金183℃熔点提高了34℃。 ·无铅喷锡工艺,温度为265-270℃。有时候,板子喷得不平整,不合格,返 工1-2次,引起板子分层起泡,或阻焊剂起泡,板子报废。 ·据说,目前用得最广泛的是305焊料配方。SMT装配时用305,PCB厂喷锡往往 不使用305焊料。 “这是一筐烂苹果中找到的一个好苹果”学者这样评说。 ·在PCB厂作无铅喷锡,基于305焊料在使用过程中,Cu含量不断升高污染锡缸, 引起SMT装配时,锡面流动性差,散锡性不理想。在PCB厂作无铅喷锡,较多的 使用是这样的焊料:SCN,或SN100C,其焊料成份是:Sn-0.7Cu-0.05Ni(或锗 Ge替代Ni,0.05%Ge)。(Ni含量为0.02-0.05%)。 ·在Sn-0.7 Cu-0.05 Ni的焊料配方中,镍的存在减缓了铜在界面金属化合物 (IMC)的扩散速度。锗Ge的存在,目的是形成一层保护性的氧化膜。 5 ·当熔融焊料中Cu含量≥3%,涂覆的焊料层会发生粗糙,脆裂等问题。
FPC生产流程(全流程)

FPC生产流程(全流程)1. FPC生产流程:1.1 双面板制程:开料→ 钻孔→ PTH → 电镀→ 前处理→ 贴干膜→ 对位→曝光→ 显影→ 图形电镀→ 脱膜→ 前处理→ 贴干膜→对位曝光→ 显影→蚀刻→ 脱膜→ 表面处理→ 贴覆盖膜→ 压制→ 固化→ 沉镍金→ 印字符→ 剪切→ 电测→ 冲切→ 终检→包装→ 出货1.2 单面板制程:开料→ 钻孔→贴干膜→ 对位→曝光→ 显影→蚀刻→ 脱膜→ 表面处理→ 贴覆盖膜→ 压制→ 固化→表面处理→沉镍金→ 印字符→ 剪切→ 电测→ 冲切→ 终检→包装→ 出货2. 开料2.1. 原材料编码的认识NDIR050513HJY: D→双面, R→ 压延铜, 05→PI厚0.5mil,即12.5um, 05→铜厚18um, 13→胶层厚13um.XSIE101020TLC: S→单面, E→电解铜, 10→PI厚25um, 10→铜厚度35um, 20→胶厚20um.CI0512NL:(覆盖膜) :05→PI厚12.5um, 12→胶厚度12.5um. 总厚度:25um.2.2.制程品质控制A.操作者应带手套和指套,防止铜箔表面因接触手上之汗而氧化.B.正确的架料方式,防止皱折.C.不可裁偏,手对裁时不可破坏沖制定位孔和测试孔.D.材料品质,材料表面不可有皱折,污点,重氧化现象,所裁切材料不可有毛边,溢胶等.3钻孔3.1打包: 选择蓋板→組板→胶帶粘合→打箭头(记号)3.1.1打包要求: 单面板 30张 ,双面板 6张 , 包封15张.3.1.2蓋板主要作用:A: 防止钻机和压力脚在材料面上造成的压伤B::使钻尖中心容易定位避免钻孔位置的偏斜C:带走钻头与孔壁摩擦产生的热量.减少钻头的扭断.3.2钻孔:3.2.1流程: 开机→上板→调入程序→设置参数→钻孔→自检→IPQA检→量产→转下工序.3.2.2. 钻针管制方法:a. 使用次数管制 b. 新钻头之辨认,检验方法3.3. 品质管控点: a.钻带的正确 b.对红胶片,确认孔位置,数量,正确. c确认孔是否完全导通. d. 外观不可有铜翘,毛边等不良现象.3.4.常见不良现象3.4.1断针: a.钻机操作不当 b.钻头存有问题 c.进刀太快等.3.4.2毛边 a.蓋板,墊板不正确 b.靜电吸附等等4.电镀4.1.PTH原理及作用: PTH即在不外加电流的情況下,通过镀液的自催化(钯和铜原子作为催化剂)氧化还原反应,使铜离子析镀在经过活化处理的孔壁及铜箔表面上的过程,也称为化学镀铜或自催化镀铜.4.2.PHT流程: 碱除油→水洗→微蚀→水洗→水洗→预浸→活化→水洗→水洗→速化→水洗→水洗→化学铜→水洗.4.3.PTH常见不良状况之处理4.3.1.孔无铜 :a活化钯吸附沉积不好. b速化槽:速化剂浓度不对. c化学铜:温度过低,使反应不能进行反应速度过慢;槽液成分不对.4.3.2.孔壁有颗粒,粗糙: a化学槽有颗粒,铜粉沉积不均,开过滤机过滤. b板材本身孔壁有毛刺.4.3.3.板面发黑: a化学槽成分不对(NaOH浓度过高).4.4镀铜镀铜即提高孔内镀层均匀性,保证整个版面(孔内及孔口附近的整个镀层)镀层厚度达到一定的要求.4.4.1电镀条件控制a电流密度的选择b电镀面积的大小c镀层厚度要求d电镀时间控制4.4.1品质管控 1 贯通性:自检QC全检,以40倍放大镜检查孔壁是否有镀铜完全附着贯通.2 表面品质:铜箔表面不可有烧焦,脱皮,颗粒状,针孔及花斑不良等现象.3 附着性:于板边任一处以3M胶带粘贴后,以垂直向上接起不可有脱落现象.5.线路5.1干膜干膜贴在板材上,经曝光后显影后,使线路基本成型,在此过程中干膜主要起到了影象转移的功能,而且在蚀刻的过程中起到保护线路的作用.5.2干膜主要构成:PE,感光阻剂,PET .其中PE和PET只起到了保护和隔离的作用.感光阻剂包括:连接剂,起始剂,单体,粘着促进剂,色料.5.3作业要求 a保持干膜和板面的清洁, b平整度,无气泡和皱折现象.. c附着力达到要求,密合度高.5.4作业品质控制要点5.4.1为了防止贴膜时出现断线现象,应先用无尘纸粘尘滚轮除去铜箔表面杂质.5.4.2应根据不同板材设置加热滚轮的温度,压力,转数等参数.5.4.3保证铜箔的方向孔在同一方位.5.4.4防止氧化,不要直接接触铜箔表面.5.4.5加热滚轮上不应该有伤痕,以防止产生皱折和附着性不良5.4.6贴膜后留置10—20分钟,然后再去曝光,时间太短会使发生的有机聚合反应未完全,太长则不容易被水解,发生残留导致镀层不良.5.4.7经常用无尘纸擦去加热滚轮上的杂质和溢胶.5.4.8要保证贴膜的良好附着性.5.5贴干膜品质确认5.5.1附着性:贴膜后经曝光显影后线路不可弯曲变形或断等(以放大镜检测)5.5.2平整性:须平整,不可有皱折,气泡.5.5.3清洁性:每张不得有超过5点之杂质.5.6曝光5.6.1.原理:使线路通过干膜的作用转移到板子上.5.6.2作业要点: a作业时要保持底片和板子的清洁.b底片与板子应对准,正确.c不可有气泡,杂质.*进行抽真空目的:提高底片与干膜接触的紧密度减少散光现象.*曝光能量的高低对品质也有影响:1能量低,曝光不足,显像后阻剂太软,色泽灰暗,蚀刻时阻剂破坏或浮起,造成线路的断路.2.能量高,则会造成曝光过度,则线路会缩小或曝光区易洗掉.5.7显影5.7.1原理:显像即是将已经曝过光的带干膜的板材,经过(1.0+/-0.1)%的碳酸钠溶液(即显影液)的处理,将未曝光的干膜洗去而保留经曝光发生聚合反应的干膜,使线路基本成型.5.7.2影响显像作业品质的因素: a﹑显影液的组成 b﹑显影温度. c﹑显影压力. d﹑显影液分布的均匀性.e﹑机台转动的速度.5.7.3制程参数管控:药液溶度,显影温度,显影速度,喷压.5.7.4显影品质控制要点:a﹑出料口扳子上不应有水滴,应吹干净.b﹑不可以有未撕的干膜保护膜.c﹑显像应该完整,线路不可锯齿状,弯曲,变细等状况.d﹑显像后裸铜面用刀轻刮不可有干膜脱落,否则会影响时刻品质.e﹑干膜线宽与底片线宽控制在+/-0.05mm以内的误差.f﹑线路复杂的一面朝下放置,以避免膜渣残留,减少水池效应引起的显影不均.g﹑根据碳酸钠的溶度,生产面积和使用时间来及时更新影液,保证最佳的显影效果.h﹑应定期清洗槽内和喷管,喷头中之水垢,防止杂质污染板材和造成显影液分布不均匀性. i﹑防止操作中产生卡板,卡板时应停转动装置,立即停止放板,并拿出板材送至显影台中间,如未完全显影,应进行二次显影.j﹑显影吹干后之板子应有绿胶片隔开,防止干膜粘连而影响到时刻品质.5.8蚀刻脱膜5.8.1原理:蚀刻是在一定的温度条件下(45—50)℃蚀刻药液经过喷头均匀喷淋到铜箔的表面,与没有蚀刻阻剂保护的铜发生氧化还原反应,而将不需要的铜反应掉,露出基材再经过脱膜处理后使线路成形.5.8.2蚀刻药液的主要成分:酸性蚀刻子液(氯化铜),双氧水,盐酸,软水5.9蚀刻品质控制要点:5.9.1以透光方式检查不可有残铜, 皱折划伤等5.9.2线路不可变形,无水滴.5.9.3时刻速度应适当,不允收出现蚀刻过度而引起的线路变细,和蚀刻不尽.5.9.4线路焊点上之干膜不得被冲刷分离或断裂5.9.5时刻剥膜后之板材不允许有油污,杂质,铜皮翘起等不良品质。
化学镍金操作规范

目录壹,制程原理一,槽液功能贰,制程控制一,制程流程二,制程控制参数参,药液维护一,配槽浓度二,槽液,滤芯更换时间肆,镍控制器原理一,镍控制器面板二,镍控制器校正三,注意事项伍,镍槽的起镀步骤一,新配槽起镀操作步骤二,停机后起镀操作步骤三,假镀板数量之计算四,PH之设定陆,异常分析与对策柒,生产时注意事项捌,重工流程化学镍金操作规范(中文版)Rev.A1一,槽液功能:1.酸性清洁槽(Acid Cleaner):主要功能有二:(1)可移去板面油脂及氧化物:(2)润湿板面。
2.微蚀槽(Micro Etch): SPS/H2SO4 system , for these processes.主要功能:(1)移去污染物;(2)提供铜表面适当的粗糙度;(3)提供化学镍较佳的附着。
3.预浸槽(Pre-dip):主要功能:(1)避免污染物带入活化槽(保护钯槽);(2)提供酸性环境以避免不必要的副反应。
4.活化槽(Activator):靠铜和钯之间离子交换产生晶重层,以利镍的沉积。
反应式如下:Cu + Pd2+→Cu2+ + Pd5.化学镍槽(Electroless Nickel):(1)在铜表面镀上一层平坦而且均一可焊之镍层;(2)提供极佳的抗腐蚀性(保护铜面)。
6.浸金槽(immersion gold)靠金和镍之间的置换镀一层细密的金层。
反应式如下:2Au++ Ni →2Au + Ni2+贰,制程控制注意事项:1.以上条件视实际状况而定。
2.后浸槽做细线路时才使用。
3.◎:半开;○:1/4开。
4.微蚀量控制在60-100μ″。
5.预浸的时间必须在3分钟以上。
6.活化及镍槽之间水洗勿太久,以避免钯钝化,产生跳镀;镍槽及金槽之间水洗勿太长,以避免镍钝化,造成脱金。
7.微蚀槽以后水洗必须使用纯水。
注意事项:(1)操作条件视实际状况而定(2) H2SO4为CP级浓硫酸(3)Ni: 6.0g/L=100%; 5.7g/L=95%; 6.3g/L=105%参,药液维护(1)配槽时先加半槽纯水,再加药水。
10.第十讲-模具表面电镀及沉镍处理

第十节塑胶模具表面电镀及沉镍电镀(Electroplating):将金属零件作为阴极浸入含有欲镀金属的盐溶液中,通入电流,在直流电场的作用下,金属盐溶液中的阳离子在零件表面上沉淀成为牢固的镀层的工艺,称为电镀。
可以起到防止腐蚀,提高耐磨性、导电性、反光性及增进美观等作用。
化学镀:利用适当的还原剂,使一定成分溶液中的金属离子在经催化的金属表面上还原出金属镀层的一种化学方法。
常见的有化学镀镍与化学镀铜。
热浸镀:将金属零件浸入熔融的金属液体槽中,经一定时间取出然后冷却后,使其表面形成耐蚀覆盖层的工艺,称为热浸镀。
一、电镀的主要用途:◆提高金属制品或者零件的耐蚀性能。
如钢铁制品或者零件表面镀锌。
◆提高金属制品的防护装饰性能。
如钢铁制品表面镀铜、镀镍、镀铬等。
◆修复金属零件尺寸磨损和加工失误。
如轴、齿轮等零件使用后磨损,可采用镀铁、镀铬等弥补其尺寸。
◆赋予某种制品或零件某种特殊的功能。
如镀硬铬可提高其耐磨性能等。
就是利用电解原理在某些金属表面上镀上一薄层其它金属或合金的过程。
电镀的目的是在基材上镀上金属镀层,改变基材表面性质或尺寸。
电镀能增强金属的抗腐蚀性(镀层金属多采用耐腐蚀的金属)、增加硬度、防止磨耗、提高导电性、润滑性、耐热性、和表面美观。
二、电镀的金属类型:电镀分镀锌、镀铜、镀镍、镀金、镀银、镀钛、镀铬等。
镀硬铬得到耐磨抗腐表面;镀铜可防止局部渗碳。
利用电解作用在机械制品上沉积出附着良好的、但性能和基体材料不同的金属覆层的技术。
电镀层比热浸层均匀,一般都较薄,从几微米到几十微米不等。
◆镀层大多是单一金属或合金,如钛靶、锌、镉、金或黄铜、青铜等;◆也有弥散层,如镍-碳化硅、镍-氟化石墨等;◆还有覆合层,如钢上的铜-镍-铬层、钢上的银-铟层等。
电镀的基体材料除铁基的铸铁、钢和不锈钢外,还有非铁金属,如ABS、PP、聚砜PSU 和酚醛塑料,但塑料电镀前,必须经过特殊的活化和敏化处理。
三、电镀方式:电镀分为挂镀、滚镀、连续镀和刷镀等方式,主要与待镀件的尺寸和批量有关。
无电沉镍工艺流程

无电沉镍工艺流程
无电沉镍是一种常用的金属表面处理方法,主要用于给金属制品镀上一层具有良好耐蚀性和装饰性的镍层。
下面将介绍一下无电沉镍的工艺流程。
首先,准备金属工件。
将需要进行无电沉镍的金属工件进行表面清洁,去除表面的油污、尘土和氧化物等。
清洁方法可以采用化学清洗或机械清洗的方式。
其次,进行除油处理。
将已经清洁好的金属工件进行除油处理,以保证镍层的附着力和光泽度。
除油处理可以通过浸泡法或喷洒法进行,常用的除油剂有有机溶剂和碱性溶剂。
接着,进行活化处理。
活化处理的目的是去除金属表面的氧化物,以提高镍层的附着力。
活化处理可采用酸性活化液进行,常用的活化液有硫酸、盐酸和磷酸等。
然后,进行无电沉镍。
将已经完成活化处理的金属工件,放入含有镍离子的溶液中进行无电沉镍。
镍离子溶液中的镍离子将在金属工件表面还原成金属镍,并与金属工件表面的活化层发生反应,形成一层均匀致密的镍层。
镍离子溶液的配方根据需求的镍层厚度和镍层性能来确定。
最后,进行后处理。
无电沉镍完成后,需要进行后处理以提高镀层的亮度和光泽度。
后处理可采用酸洗或热处理的方式进行。
酸洗可去除镀层表面的杂质和氧化物,热处理可提高镀层的致密度和光泽度。
总结一下无电沉镍的工艺流程:金属工件清洁→除油处理→活化处理→无电沉镍→后处理。
这个流程简单明了,能够保证无电沉镍工艺的顺利进行,镀层的质量稳定可靠。
无电沉镍不仅可以提高金属工件的耐蚀性能,还可以美化金属表面,延长使用寿命。
因此,无电沉镍工艺在金属制品的制造和加工中得到了广泛应用。
浸镍工艺流程

浸镍工艺流程1.镍在化学品中的浓度是决定浸镀效果的重要因素。
Nickel concentration in the chemical solution is an important factor in determining the plating effect.2.浸镍工艺是一种常用的金属表面处理工艺。
Nickel plating process is a commonly used metal surface treatment process.3.浸镍工艺可以提高金属制品的耐腐蚀性能。
Nickel plating process can improve the corrosion resistance of metal products.4.在浸镍工艺中,首先要做好表面的预处理工作。
In the nickel plating process, the surface pre-treatment work should be done first.5.表面预处理包括去污、除油和激活等步骤。
Surface pre-treatment includes steps such as degreasing, deoiling, and activation.6.激活处理可以提高基材表面与镍层之间的结合力。
Activation treatment can improve the adhesion between the substrate surface and the nickel layer.7.激活后的基材要立即进行镍的浸镀以防止重新氧化。
The activated substrate should be immediately nickel-plated to prevent re-oxidation.8.镍的浸镀过程包括镍盐溶液的配制和电镀设备的操作。
The nickel plating process includes the preparation of nickel salt solution and the operation of electroplating equipment.9.浸镍工艺的电镀设备包括电镀槽、电源和附件等组成部分。
- 1、下载文档前请自行甄别文档内容的完整性,平台不提供额外的编辑、内容补充、找答案等附加服务。
- 2、"仅部分预览"的文档,不可在线预览部分如存在完整性等问题,可反馈申请退款(可完整预览的文档不适用该条件!)。
- 3、如文档侵犯您的权益,请联系客服反馈,我们会尽快为您处理(人工客服工作时间:9:00-18:30)。
3
一、什么是化学镀
化学镀是在金属的催化作用 下,通过可控制的氧化还原 反应产生金属沉积的过程。
4
化学镀应具备的条件:
1、氧化还原电位应显著低于金属 还原电位; 2、溶液不产生自发分解,催化时 才发生金属沉积; 3、PH值、温度可以调节镀覆速度; 4、具有自催化作用; 5、溶液有足够寿命。
5
镀液成分:
9
第二部分
沉镍金原理及工艺流程
10
一、沉镍金原理 催化 化学镀镍 浸金
(一)、催化(活化) • 作用:为化学镍提供催化晶体 • 反应式:Pd2++Cu Pd+Cu2+
11
(二)、化学镍 • 作用:在钯的催化作用下,Ni2+在NaH2PO2的还
原条件下沉积在裸铜表面。当镍沉积覆盖钯催 化晶体时,自催化反应将继续进行,直至达到 所需之镍层厚度。
21
3、铜浓度控制:
由于Cu2+ 对微蚀速率影响较大, 通常须将Cu2+的浓度控制在5-25g/l, 以保证微蚀速率处于0.5-1.5μm之间。 生产过程中,换缸时往往保留1/5-1/3 缸母液(旧液),以保持一定的Cu2+ 浓 度。
22
4、逆流水洗:
由于带出的微蚀残液,会导致铜 面在水洗过程中迅速氧化,所以微蚀 后水质和流量以及浸泡时间都须特别 考 虑 。否 则 ,预 浸 缸会 产 生太 多 的 Cu2+ ,继而影响钯缸寿命。所以,在 条件允许的情况下(有足够的排缸), 微蚀后二级逆流水洗,之后再加入5% 左右的硫酸浸洗,经二级逆流水洗后 进入预浸缸。
1、微蚀药剂组成:
过硫酸钠Na2S2O8 硫酸H2SO4 H 作用: 酸性过硫酸钠微蚀液用于使铜面微 粗糙化,增加铜与化学镍层的密着性。 沉镍金生产也有使用硫酸双氧水或酸性 过硫酸钾微蚀液来进行的。
20
2、操作条件:
Na2S2O8: 100±20g/l H2SO4: 20 ±10g/l Cu2+ : 5~25g/l 温度: 30 ±2OC 时间: 1.5 ±0.5min 搅拌:摆动及药液循环搅拌或空气打气 槽材质:PVC或PP 加热器:石英或铁弗龙加热器
沉镍金技术培训教材
撰写:徐喜明 日期:2001年10月
1
目
• • • • • • •
录
3 10 16 50 63 95 95
2
1、沉镍金工序的概念 2、沉镍金原理及工艺流程 3、药水特性 4、沉镍金工序设备简介 5、沉镍金工序常见缺陷分析 6、生产应急措施及重工 7、沉镍金工艺应用
第一部分 沉镍金工序的概念
37
4、操作条件
A、温度 不同系列的沉镍药水其控制范围不 同。一般情况下,镍缸的操作范围是 86±50C,有的药水则控制在81±50C。 具体操作温度应根据试板结果来定, 不同型号的制板,有可能操作温度不同。 一个制板的良品操作范围一般情况下只 有±20C,个别制板也有可能小于±10C.
38
B、时间条件 镍层厚度与镀镍时间呈线形关系。 一般情况下,200µin镍层需镀镍时间 28min左右,而150µin镍层则需镀镍时间 21min左右。 通常情况,不采用调节药水浓度或 升高温度来弥补因时间不足而引起的镍 厚不足,一定要根据客户镍层要求来设 置适当的镀镍时间。否则,可能引起活 性不稳定,会造成许多不良后果。
27
4、工艺维护
• 影响钯缸稳定性的主要因素除了药水系 列不同之外,钯缸控制温度和Pd2+浓度则 是首要考虑的问题。温度越低、Pd2+浓度 越低,越有利于钯缸的控制。但不能太 低,否则会影响活化效果引起漏镀发生。 • 通常情况下,钯缸温度设定在20-300C, 其控制范围应在±10C,而Pd2+浓度则控 制在20-40ppm,至于活化效果,则按需 要选取适当的时间。
17
3、操作条件
温度:50±10oC 时间:6 ±2min 过滤:5μmPP滤芯连续过滤 搅拌:摆动及药液循环搅拌 槽材质:PP或SUS 加热器:石英或铁弗龙加热器
18
4、逆流水洗
除油缸之后通常为二级市水洗,如 果水压及流量不稳定或经常变化,则将 逆流水洗设计为三级市水洗更佳。
19
(二)、微蚀缸
25
2、操作条件
温度:27±3OC 时间:4 ±2min 槽材质:PVC或PP 温控:铁弗龙包覆加热器或冷却盘管 过滤 :5µmPP滤芯连续过滤 搅拌:摆动及药液循环搅拌
26
3、消槽处理
当槽壁及槽底出现灰黑色钯的沉积 物,则须消槽处理。其过程如下: 加入1:1硝酸,启动循环泵2h以上 1:1 2h 或直到槽壁会黑色沉积物完全除去为 止(如有必要,可加热至40~50OC), 硝酸排出后,加水循环10~20min,排 放后用水循环洗涤二次以及DI水循环 洗涤一次。
• 化学反应:
Ni2+
+2H2PO2 +2H2O
-
Ni
+2HPO32-+4H++H2 • 副反应: 4H2PO2-
2HPO32-+2P+2H2O+H2
12
反应机理
• HPO32-+H++2H • Ni+2H+ • H2PO2 +H OH-+P+H2O • H2PO2- + H2O HPO32-+H++H2
其含义是: 其含义是
在裸铜面进行化学镀镍,然后化学浸金。
7
四、沉镍金工艺的目的 沉镍金工艺的目的 • 沉镍金工艺既能满足日益复杂的PCB装配、 焊接的要求,又比电镀镍金的成本低,同 时还能对导线的侧边进行有效的保护,防 止在使用过程中产生不良现象。 • AU • Ni • CU •
8
五、沉镍金工艺的用途 沉镍金工艺的用途
39
C、浓度: 不同供应商之不同系列药水, 其浓度控制范围各不相同。由于化 学镀镍的本身特点,其动态平衡的 控制难度远远大于化学镀铜,其控 制范围很窄则可说明这一点。因此, 尽可能使用自动补料器来控制药水 浓度,手动补料是很难保证每一个 制板的良品率。
40
•D、循环量: • 5~~10 turn over per hour(每小时 循环抽液量所占开缸体积的倍数)。 •E、过滤: • 优先考虑布袋式过滤,棉芯过滤需监 控流量(发现堵塞及时更换)。 •F、摇摆: • 根据做板类型的需要决定采用上下摇 摆或前后摇摆方式
23
(三)、预浸缸
1、预浸剂:
维持活化缸的酸度及使铜面在新鲜状 态(无氧化物)的情况下,进入活化缸。
2、操作条件:
温度: 时间: 搅拌: 槽材质: 室温 1±0.5min 摆动及药液循环搅拌 PVC或PP
24
(四)、活化缸
1、活化剂
其作用是在铜面析出一层钯,作为化 学镍起始反应之催化晶核。 PCB沉镍金工序之活化剂一般为硫酸 型和盐酸型两种,现较多使用硫酸型钯活 化液。行业中也有使用Ru(Ruthenium) 做催化晶核,效果也较为理想。
H2PO2 +H2O Ni2++2H
13
(三)、
浸金
• 作用: 是指在活性镍表面通过化学置换 反应沉积薄金。 • 置换反应形成的浸金薄层,通常20-30分 钟时间就可达到极限厚度。 • 化学反应:2Au++Ni 2Au+Ni2+
14
二、工艺流程
除油 4~8min 活化 2~6min
水
微蚀 1~2min
化学镍的厚度一般控制在4-5μm,其作用 同金手指电镀镍一样,不但对铜面进行有效保 护,防止铜的迁移,而且具备一定硬度和耐磨 性能,同时拥有良好的平整度。浸金的厚度一 般控制在0.05-0.1μm,其对镍面具有良好的 保护作用,而且具备很好的接触导通性能。在 镀件浸金保护后,不但可以取代拨插不频繁的 金手指用途(如电脑内存条),同时还可以避 免金手指附近连接导电线处斜边时所遗留裸铜 切口。很多需按键接触的电子器械(如手机、 电子字典),都采用化学浸金来保护镍面。
水
预浸 0.5~1.5min
水
水
化学镀镍 22~29min沉金 7~Biblioteka 1min15第三部分
药水特性
16
(一)、除油缸
1、除油剂:
一般情况下,PCB沉镍金工序的除 油剂是一种酸性液体物料,用于除 去铜面之轻度油脂及氧化物,使铜 面清洁及增加润湿性。
2、特性:
A:不损伤solder mask B:低泡型,水洗容易
34
•C、柠檬酸、羟基乙酸、琥珀酸、苹果 酸、乳酸及其盐、氯化铵、焦磷酸盐、 乙二胺、三乙醇胺等均为结合剂,其中 某些药品还起缓冲剂作用; •D、锡、锌、铅、镉、锑等金属离子, 某些有机或无机含硫化合物如硫脲以及 三氯化钼都是化学镀镍的催化剂毒物。 但如含量很少时,对镀液有一定的稳定 作用。若含量过高会使镀液失效导致镍 不能沉积出来。
36
•G、镀液应连续过滤,以除去溶液中的 固体杂质。镀液加热时,必须要有空气 搅拌或连续循环系统,使被加热的镀液 迅速扩散开。当槽内壁镀有镍层时,应 及时用硝酸(1:3)褪除,适当时可考虑加 热,但不可超过50OC, 以免污染空气。 •H、镀液寿命一般控制在4MTO(即Ni离 子添补量累积达到4倍开缸量),超过此 限主要问题是镍厚不足。
32
•D、硬度高,显微硬度约为500~600HV, 400OC处理后则大于1000HV; •E、易钎焊,但熔焊性较差; •F、镀层密度约为8.0g/cm3 ; •G、熔点约为890OC
33
3、工艺维护
• A、在酸性溶液中,PH<3时镍不会被还 原析出。随着PH值的提高,沉积速度加 快。当PH>6时,很容易产生Ni(OH)2沉 淀。一般PH控制在4.5~5.0; • B、随着NaH2PO2和NiSO4浓度的增加, 沉积速度逐渐提高,而后趋于稳定或稍 有降低。但此时溶液的稳定性下降;