DCS系统的应用与发展
DCS自动控制系统的应用

控制器一般分为硬件和软件两部分,硬件部分负责实现控制逻辑,软件部分则负 责接收输入信号、执行控制算法并输出控制信号。
输入/输出接口
输入/输出接口是DCS自动控制系统与外部设备进 行信息交互的桥梁。
通过输出接口,可以将控制信号输出到现场的各 种设备(如阀门、电机等),实现对设备的控制 。
网络安全与防护
总结词
网络安全、数据保密
VS
详细描述
随着网络技术的不断发展,DCS自动控制 系统面临着日益严峻的网络安全威胁。为 了保护系统的稳定性和安全性,需要采取 有效的网络安全措施,如数据加密、访问 控制、防火墙等,确保系统的数据安全和 保密性。
智能控制与优化
总结词
智能化、自动化
详细描述
随着工业自动化水平的不断提高,DCS自 动控制系统需要具备更高级别的智能化和 自动化功能。通过引入人工智能、机器学 习等技术,可以实现系统的智能控制和优 化,提高系统的控制精度和效率,减少人 工干预和操作失误。
开放性:DCS采用开放 式、标准化设计,支持 多种通信协议和总线系 统,方便与其他系统进 行互联互通。这使得 DCS能够适应不同的工 业应用场景,方便用户 进行系统集成和扩展。
灵活性:DCS提供丰富 的控制算法和工具,用 户可以根据实际需求灵 活选择控制策略。此外 ,DCS还支持多种操作 界面和组态方式,方便 用户进行系统配置和优 化。
高级功能
DCS自动控制系统支持多种高级功能,如网络通信、远程监控、数据分析等,可以满足不同用户的需 求。
04
DCS自动控制系统在工业 领域的应用案例
石油化工行业
总结词
重要应用领域
详细描述
DCS系统在化工工艺控制中的应用案例和创新展望

DCS系统在化工工艺控制中的应用案例和创新展望DCS系统(Distributed Control System,分散控制系统)是一种广泛应用于工业自动化控制领域的先进技术。
该系统通过将控制功能分布在多个节点上,并实现节点之间的数据交互和信息共享,有效提高了工艺控制的可靠性和稳定性。
在化工行业中,DCS系统的应用不仅改善了现有工艺的控制效果,还为创新工艺的发展提供了有力支持。
本文将通过介绍化工行业中DCS系统的应用案例,并展望其在创新工艺中的潜力,探讨DCS系统在化工工艺控制中的重要作用。
一、DCS系统在化工工艺控制中的应用案例1. 控制系统集成DCS系统通过集成多个子系统,实现对整个工艺流程的全面控制。
以炼油厂为例,DCS系统可以集成分离、转化、处理等多个子系统,并通过先进的控制算法和优化策略,实时调整操作参数,提高产品质量和生产效率。
2. 数据监测与分析DCS系统可以实时采集和监测诸如温度、压力、流量等工艺参数的数据,并进行实时分析。
通过与先进的数据分析算法相结合,DCS系统可以帮助工程师及时发现潜在故障和异常情况,并采取相应的措施,有效降低事故风险和生产成本。
3. 过程控制优化DCS系统通过模型预测控制、模糊控制和自适应控制等先进控制算法,实现对工艺过程的优化控制。
通过精确的控制和优化策略,DCS 系统可以降低能耗、减少废料排放、提高产品质量,进而提升整个生产过程的可持续性和环境友好性。
二、DCS系统在化工工艺创新中的展望1. 多元化生产随着市场需求的变化,化工工艺需要灵活多样的生产方式。
DCS系统具有良好的模块化和可扩展性,可以满足不同工艺的需求,支持多个产品同时生产。
未来,DCS系统将进一步发展,实现更加复杂的工艺控制和生产调度,以满足工艺创新的要求。
2. 智能化运维DCS系统可以通过集成人工智能和机器学习技术,实现对工艺过程的智能化运维。
通过大数据分析和模型建立,DCS系统可以预测工艺的变化趋势和故障潜在风险,并自动调整控制参数,实现智能化的运维管理。
DCS控制系统的发展趋势

DCS控制系统的发展趋势
随着科学和技术的不断发展,DCS控制系统的发展也不断改进,在工业现场应用中不断开发DCS控制系统,以满足工业自动化的需求。
DCS控制系统的发展方向,主要体现在下面几个方面:
一是增加功能。
随着多媒体技术的发展,DCS控制系统也增加了更多功能,可以支持较大的图形、视频和声音信息,实现远程监控和控制,更好地实现自动化管理目标。
二是改进性能。
目前DCS控制系统的性能也在不断提升,通过智能算法、软件模拟和其他技术,更好地改善性能,以期更好地满足用户的各种要求。
三是改进灵活性。
目前,DCS控制系统的灵活性也越来越强,可以满足不同的环境和用户,通过在线维护和远程检测等技术,系统的可用性可以得到显著提高。
四是改进数据安全性。
随着DCS控制系统的发展,数据安全性也得到了改进,采用加密技术、安全审计技术等,更好地保障DCS控制系统的安全。
DCs控制系统的发展,最终是为了更好地满足用户的要求,更好地满足工业自动化的要求,以提高效率,降低成本。
因此,DCS控制系统的发展趋势也会不断改善,贯彻以上几点发展方向,以满足客户的不断变化的需求。
DCS系统在电力行业中的应用

DCS系统在电力行业中的应用DCS(分散控制系统)是指通过网络连接的若干个可编程控制器及其周边设备组成的控制系统,它被广泛应用于电力行业中,为电力发电、输送、配送等环节提供了可靠高效的控制和管理手段。
本文将探讨DCS系统在电力行业中的应用与优势。
一、DCS系统在发电过程中的应用1. 发电机控制电力发电厂中的发电机是发电的核心设备,DCS系统通过实时监测发电机的运行状态,控制调节发电机的负荷、电压等参数。
同时,DCS系统能够自动检测发电机的故障,并进行相应的报警和保护,确保发电机的安全稳定运行。
2. 脱硫装置控制燃煤发电厂中常常需要通过脱硫装置减少烟尘和二氧化硫等污染物的排放量。
DCS系统可以实时监测脱硫装置的运行情况,调整氧气浓度、石膏浆液浓度等参数,以确保脱硫效果的稳定和达标。
二、DCS系统在输电过程中的应用1. 变电站控制电力输电环节中的变电站起着重要的作用,DCS系统能够对变电站进行自动控制和监测。
通过DCS系统,可以实现对变电站中断路器、变压器等设备的状态监测和控制,实时调节输电线路的电压等参数,提高输电效率和安全性。
2. 线路安全控制DCS系统可通过监测输电线路的状态和负荷情况,并实时调整电流的分配,避免输电线路过载和跳闸等问题。
同时,DCS系统还可以及时发现并处理线路故障,防止电力事故的发生。
三、DCS系统在配电过程中的应用1. 配电监控DCS系统能够实时监测配电系统的电流、电压、功率等参数,并根据需要进行相应的控制和调节。
它可以对配电系统进行远程监控,并能够自动控制配电设备的开关状态,提高配电系统的运行效率和可靠性。
2. 供电质量控制供电质量是指电力系统对用户提供的电能的稳定性和可靠性。
DCS 系统能够实时监测供电质量参数,如电压波动、谐波、电力因数等,并通过调节电力设备的运行状态来控制和改善供电质量,保证用户用电的稳定性。
综上所述,DCS系统在电力行业中的应用是不可或缺的。
它能够提高发电效率,减少污染物排放,确保输电安全稳定,提高配电质量,为电力行业的发展和运行提供有力的支持。
DCS控制系统及发展趋势

DCS控制系统及发展趋势摘要:DCS控制系统又称集散控制系统,它是计算机技术、控制技术和网络通信技术高度结合的产物。
本文分析了DCS控制系统及其发展的趋势。
关键词:DCS;控制系统;发展1 DCS控制系统简介集散控制系统(Distributed Control System)是相对于集中式控制系统而言的一种较新型的计算机控制系统,是利用计算机技术对生产过程进行集中监视、操作、管理和分散控制的一种全新的分布式计算机控制系统。
DCS从1975年诞生以来,经过多年的发展,其功能不断扩大,系统的规模、容量增加,数字化程度逐步提高,现已形成了数字化、信息化、集成化的分散控制系统。
现代的DCS 控制系统,不仅能够攻克常规模拟仪表和集中控制存在的致命缺陷(如控制能力单一,一个地方出问题导致全线停车等),还能通过各微处理机之间的相互连接,综合逻辑控制、顺序控制、程序控制、批量控制及配方控制,从而实现非常复杂的控制功能。
集散控制系统主要包括过程级、操作级和管理级,而任何一个集散控制系统的组成须具备以下几个要素:一台过程控制站、一台操作员站、一台工程师站、一条系统网络。
过程控制站是DCS的核心,系统主要的控制功能由它来完成。
现场控制站的硬件包含一个完整的工业计算机系统,当然包含CPU、存储器、网络接口,同时还包括I/O通道,一般是模块化的I/O,而同一个模块上可有多个I/O通道,连接这些现场测量设备和执行设备,其三是包含I/O单元,即用来摆放I/O模块的单元。
操作员站较简单,就是操作员通过工业计算机系统来完成控制过程。
但应注意增加屏幕或视野来增加操作员的观察范围,便于对全局有个系统的把握。
工程师站在DCS中可能不需要人员长期对其进行控制和操作,但它也是DCS系统中非常重要的环节。
它是对特定的DCS系统执行怎样的特定功能进行设置的一个特殊功能站,如在控制计算中参数的设定,对某节点是否需要人的监控和管理的选择等等,同时还包含如报警、记录历史数据等各个方面功能的定义。
DCS系统简介及应用
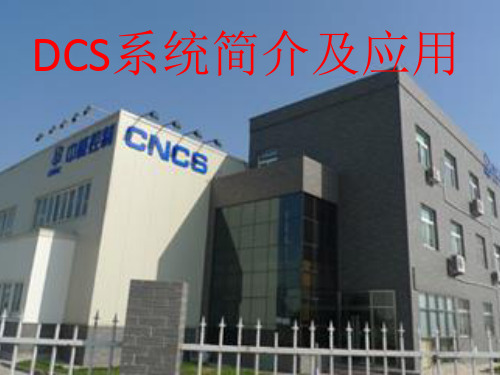
DCS应用情况
高桥石化公司炼油厂1#常减压装置采用SPECTRUM 系 统与FOX-300 上位机,除对全装置实现常规控制外,开 发了常压塔计算机集成优化系统,实现了基于动态内回 流的常压塔测线产品质量的在线计算、多测线产品质量 及收率的智能化协调控制与最佳回流取热分配控制,并 利用人工智能方法构造上级协调系统,开发了常压塔整 体智能决策与优化专家系统。该项目突破传统思维模式, 代之以信息流、物料流和能量流为主干分解方法,充分 发挥了DCS信息采集功能、通信功能和运算功能强的优 势,并以此为依托,开发和实施了高质量的数学模型和 优化控制软件。该系统在现场长时间投用以来,性能可 靠,提高轻油收率。
二、我国石油化工工业DCS应用情况
截止到1990年,中国石油化工总公司范围内 用于过程控制的大小不同规模的DCS共122套, 其中已投用的90 套,在建的32套。除4套为国产 外,其余均为国外引进产品。 石化总公司的122套DCS,用于炼油专业的27 套,化工专业的47套,化纤专业的18套,化肥专 业的13套,公用工程、三剂生产等系统14套,另 有3套用于中试装置。除此3套外,其余119套 DCS分别用在25个企业的71个生产厂。
缺点(与FCS比较)
• • • • • 浪费一次性投资 浪费安装费用 浪费维护费用 控制准确度与可靠性不高 用户的选择性不多
dcs自动控制系统
典型的dcs系统架构
DCS系统简介及应用
一、DCS控制系统应用概况
集散控制系统(Total Distributed Control System,DSC)是20世纪70年代中期发展起来 的以微处理器为基础的分散型计算机控制系 统。它是控制技术(Control)、计算机技术 (Computer)、通信技术(Communication)、 阴极射线管(CRT)图形显示技术和网络技术 相结合的产物。该装置时利用计算机技术对 生产过程进行集中监视、操作、管理和分散 控制的一种全新的分布式计算机控制系统。
dcs的应用场景

dcs的应用场景摘要:一、DCS概述二、DCS的应用场景1.工业过程控制2.楼宇自控3.能源管理4.环保监测5.交通运输6.医疗设备7.智能家居三、DCS的发展趋势四、DCS在我国的应用案例正文:一、DCS概述分布式控制系统(DCS,Distributed Control System)是一种集散式工业控制系统,它采用分级、分布式、开放式的体系结构,通过对各种子系统的集成,实现对生产过程的监控、调度、控制和管理。
DCS具有高可靠性、易扩展性、易维护性和高度集成性等特点,广泛应用于各个行业。
二、DCS的应用场景1.工业过程控制DCS在工业过程控制中发挥着重要作用,可以实现对生产过程中的温度、压力、流量、液位等参数的实时监测和控制,确保生产过程的稳定运行。
同时,DCS还可以与其他系统如PLC、SCADA等配合使用,实现对整个工厂的集中管理和控制。
2.楼宇自控在楼宇自动化领域,DCS可以用于照明控制、空调控制、电梯控制、安防监控等系统,实现对建筑内部环境的智能调控,提高能源利用效率,降低能耗。
3.能源管理DCS在能源管理领域具有广泛应用,如电力系统、燃气系统、水务系统等。
通过实时监测和分析能源消耗数据,DCS可以有效地实现能源的合理调配和节约使用,为企业降低运营成本。
4.环保监测DCS在环保监测领域具有重要作用,可以用于监测大气污染、水污染、土壤污染等环境指标,为政府和企业提供决策依据,助力环境保护。
5.交通运输在交通运输领域,DCS可以应用于交通信号控制、地铁隧道通风、铁路牵引供电等系统,确保交通运输的安全、高效、顺畅。
6.医疗设备DCS在医疗设备领域具有广泛应用,如医疗影像设备、手术室净化系统、生物实验室等,为病患和医务人员提供安全、舒适、便捷的环境。
7.智能家居随着智能家居市场的快速发展,DCS也开始应用于家庭自动化系统,如智能照明、智能空调、家庭安防等,为消费者带来智能、舒适、便捷的生活体验。
DCS系统的发展历程与趋势展望

DCS系统的发展历程与趋势展望DCS(Distributed Control System,分布式控制系统)是一种用于监控和控制工业过程的自动化系统。
它的发展历程经历了几个重要的阶段,从最初的分散控制到现代的集成化实时控制系统,不断推动着工业自动化领域的发展。
本文将探讨DCS系统的发展历程,并对未来的趋势进行展望。
1. 第一阶段:分散控制系统在上世纪60年代,工业控制系统主要采用分散控制的方式。
这种方式下,每个设备或生产单元都有独立的控制器进行控制,互相之间缺乏通信与协调。
虽然这种系统可以满足简单工艺的需求,但对于复杂的生产过程来说,协调与集成的能力显得十分有限。
2. 第二阶段:中央集中控制系统为了解决分散控制系统的不足,上世纪70年代开始出现了中央集中控制系统。
这种系统将所有控制器集中在一个中央控制室,通过数据通信技术实现设备之间的信息交互。
这样一方面提高了控制系统的协调能力,另一方面也降低了系统的运行成本。
中央集中控制系统在许多工业领域获得了广泛应用,成为了当时工业自动化的代表性技术。
3. 第三阶段:分布式控制系统随着计算机和通信技术的发展,上世纪80年代起,DCS系统逐渐取代了中央集中控制系统。
分布式控制系统通过将控制器分布在各个生产单元中,实现了更强大的控制能力和更高效的信息交互。
此外,DCS系统还具备可靠性高、可扩展性强、维护方便等优点。
这使得它成为了工业自动化领域的主流技术,并广泛应用于石化、电力、制药等行业。
4. 当前阶段:集成化实时控制系统随着信息技术的不断发展,DCS系统正在向集成化实时控制系统的方向迈进。
这种系统不仅要求实时性高、可靠性好,还需要具备更强大的数据处理和分析能力。
同时,物联网、云计算、大数据等新技术的出现,为DCS系统的升级提供了更多可能性。
未来的DCS系统将更加注重信息的共享与互联,实现设备之间的智能协同和智能优化控制。
展望未来,随着工业自动化的智能化和数字化发展,DCS系统将继续朝着更高水平迈进。
DCS系统在电子制造业中的应用

DCS系统在电子制造业中的应用DCS(Distributed Control System,分布式控制系统)是一种广泛应用于电子制造业的自动化控制系统,它能够集中管理生产过程中的各种设备和系统,实现实时监控、调控和优化生产流程。
本文将介绍DCS系统在电子制造业中的应用,并探讨其带来的益处。
一、DCS系统在电子制造业中的应用在电子制造业中,DCS系统以其强大的功能和高效的性能被广泛应用于以下几个方面:1. 控制和监测生产过程:DCS系统能够连接和控制电子制造过程中的各种设备和机器,实时监测和调控生产参数,确保产品的质量和稳定性。
通过DCS系统,生产工艺可以实现自动化控制,从而提高生产效率和产品质量。
2. 数据采集和分析:DCS系统能够实时采集生产过程中的各种数据,包括温度、压力、流量等参数,同时也可以采集人员操作的数据,如参数调整和设备维护记录等。
通过对这些数据的分析和处理,企业可以了解生产过程的变化和趋势,从而进行合理的调整和优化。
3. 故障诊断和维护管理:DCS系统具备较强的故障诊断功能,当生产过程发生异常时,系统能够及时报警,并通过排除故障流程进行快速定位和处理。
此外,DCS系统还能进行设备状态监测、预测性维护等管理,提前发现潜在故障,避免因设备损坏而导致的生产事故和停工时间。
二、DCS系统在电子制造业中的益处DCS系统的应用给电子制造业带来了诸多益处,包括但不限于以下几个方面:1. 提高生产效率:通过自动化控制和优化管理,DCS系统能够实现生产过程中的流程优化和工艺改进,从而提高生产效率和生产能力。
同时,系统能够减少人为操作的错误,降低生产事故的发生率,提高生产线的稳定性和可靠性。
2. 优化产品质量:DCS系统能够实时监测和调控生产过程中的各种参数,确保产品在制造过程中的质量和一致性。
通过对生产数据的采集和分析,系统能够及时发现生产异常,并实施纠正措施,从而提高产品合格率和品质水平。
3. 降低生产成本:DCS系统的使用可以有效降低生产过程中的能源消耗和废品产生,减少原材料的浪费和人工的投入,从而降低生产成本。
DCS系统原理及应用情况

DCS系统原理及应用情况DCS(分散控制系统)是一种用于监控和控制工业过程的自动化系统。
它由许多分布式控制器组成,这些控制器分布在整个工厂或工艺系统中,通过网络连接在一起,可以实现对整个系统的实时监控和控制。
DCS系统的发展可以追溯到20世纪70年代,起初是用于大型化工厂的控制系统,后来逐渐广泛应用于各种工业领域,包括制造业、电力、石油化工、水处理等。
DCS系统的原理是基于分布式控制器的概念,即将整个系统划分为多个子系统,每个子系统由一个或多个控制器控制,这些控制器通过网络连接在一起,可以实现相互通信和数据交换。
每个控制器都可以独立运行,并具有自己的处理能力和存储空间,可以处理各种控制任务,并与其他控制器协调工作,从而实现对整个系统的集中控制和管理。
1.控制器:负责实时监控和控制各个子系统,通过传感器获取系统状态信息,通过执行器执行控制命令,以实现对系统的自动化控制。
2.人机界面(HMI):用于显示系统状态信息、操作界面和报警信息,供操作员进行监控和操作,通常使用图形界面或触摸屏显示。
3.数据通信网络:用于连接各个控制器、传感器和执行器,实现数据的传输和通信。
4.传感器和执行器:用于采集系统的各种参数信息(如温度、压力、流量等)和执行控制命令(如开关、调节阀等)。
1.制造业:在汽车制造、食品加工、电子制造等行业中,DCS系统可以实现生产线的自动化控制,提高生产效率和质量。
2.电力行业:在发电厂、输电站等电力系统中,DCS系统可以实现对发电设备、变电设备的远程监控和控制,确保电力系统的稳定运行。
3.石油化工:在炼油厂、化工厂等工艺系统中,DCS系统可以实现对生产过程的实时监控和控制,提高生产安全性和环保性。
4.水处理:在供水、污水处理等水处理系统中,DCS系统可以实现对水质、流量等参数的实时监测和调节,确保水质符合标准要求。
5.建筑自动化:在大型建筑、商业综合体等场所中,DCS系统可以实现对照明、空调、安防等设备的智能控制,提高能源利用效率和舒适性。
浅析DCS控制系统的特点与发展趋势

浅析 DCS控制系统的特点与发展趋势摘要:DCS控制系统可直译为“分散控制系统”或“分布式计算机控制系统”。
它采用控制分散、操作和管理集中的基本设计思想,采用多层分级、合作自治的结构形式。
其主要特征是它的集中管理和分散控制。
目前DCS在电力、冶金、石化等各行各业都获得了极其广泛的应用。
关键词:DCS控制系统;特点;发展趋势一、DCS控制系统的发展集散控制系统是1975年首先由美国霍尼威尔(Honeywell)公司推出的,当时DCS还在初创阶段,产品还是集散控制系统的雏形。
随着半导体技术、显示技术、控制技术、网络技术和软件技术等高新技术的发展,集散控制系统进入了第二代集散控制系统。
美国Foxboro公司在1987年推出的I/AS系统标志着集散控制系统进入了第三代。
它的主要改变是在局域网络方面,在符合开放系统的各制造厂产品间可以相互连接、相互通信和进行数据交换,第三方的应用软件也能在系统中应用,从而使集散控制系统进入了更高的阶段,同时第三代集散控制系统所提供的控制功能也有了增强。
目前,我国DCS控制系统已取得了显著的发展,有众多的国产品牌,并逐步掌握从操作系统到芯片在内的全国产技术。
原国产品牌DCS,其内部CPU(中央处理器)、AD/DA、MCU、 FPGA、千兆PHY芯片等核心芯片均采用进口;控制器嵌入式操作系统、上位机操作系统等多采用非开源进口操作系统。
随着近年来国家政策扶持和市场优胜劣汰发展,一批优质的国产软硬件品牌已经取得长足进步。
在选型调研中发现:适用于DCS系统的国产芯片、元器件、操作系统及软件,与同等级别进口产品在性能指标方面旗鼓相当。
二、DCS控制系统特点DCS控制系统能被广泛应用的原因是它具有优良的特性。
与模拟电动仪表比较,它具有连接方便、采用软连接的方法连接容易更改、显示方式灵活、显示内容多样、数据存储量大等优点;与计算机集中控制比较,它具有操作监督方便、危险分散、功能分散等优点。
DCS、FCS、PLC的应用及发展

PLC的产生 ◇ 1969年,美国数字设备公司(DEC公司)研制出了基于集 成电路和电子技术的控制装置,首次采用程序化的手段应 用于电气控制,这就是第一代可编程序控制器,称 Programmable Controller(PC),用于GM(通用汽车) 公司。
◇
◇
1971年,日本从美国引进了这项新技术,很快研制成了 日本第一台可编程控制器DSC-8;
国产PLC主要生产厂家
我国有许多厂家、科研院所从事PLC的研制与开发, 如中国科学院自动化研究所的PLC-0088,北京联 想计算机集团公司的GK-40,上海机床电器厂的 CKY-40,上海起重电器厂的CF-40MR/ER,苏州电 子计算机厂的YZ-PC-001A,原机电部北京机械工 业自动化研究所的MPC-00l/20、KB-20/40,杭州 机床电器厂的DKK02,天津中环自动化仪表公司的 DJK-S-84/86/480,上海自立电子设备厂的KKI系 列,上海香岛机电制造有限公司的ACMY-S80、 ACMY-S256,无锡华光电子工业有限公司(合资) 的SR-10、SR-20/21等。
浙大中控
中控科技集团有限公司(浙大中控)是中国领先的自动化信息化技术、 产品与解决方案供应商,业务涉及工厂自动化、公用工程信息化、装备自 动化等领域。 浙大中控自1993年进入自动化行业领域以来,始终致力于工厂自动化 领域前沿科技的研究与开发,经过十多年的积累,浙大中控在工厂自动化 领域已经成长为业内最知名的公司之一。
DCS系统在电子制造行业中的关键作用和应用案例

DCS系统在电子制造行业中的关键作用和应用案例DCS(分散控制系统)是一种广泛应用于电子制造行业的自动化控制系统。
它通过集成控制、监控和数据采集等功能,实现了生产过程的高效运行和优化控制。
本文将探讨DCS系统在电子制造行业中的关键作用,并通过几个应用案例来说明其具体应用。
一、DCS系统在电子制造行业的关键作用1. 实时监控和调度DCS系统可以实时监控电子制造过程中的关键参数,如温度、湿度、压力等。
凭借高精度的传感器和实时数据采集,DCS系统能够准确掌握生产设备的工作状态,以便及时调整生产参数,保证产品质量和生产效率。
此外,DCS系统还具备生产调度功能,可以根据实时数据分析和产能需求,智能调度生产计划,避免资源浪费和生产延误。
2. 过程优化和能源管理DCS系统采用先进的算法和模型,对电子制造过程进行优化控制,以最大程度地提高生产效率和产品质量。
通过对工艺参数的自动调整和优化,DCS系统能够减少生产过程中的能源消耗和废品产生,达到节能减排的目的。
这对于电子制造企业来说,不仅可以降低生产成本,还能提升产品竞争力,实现可持续发展。
3. 数据分析和决策支持DCS系统通过大数据分析和处理,可以将生产过程中的海量数据转化为有用的信息,提供给决策者参考。
通过对历史数据的挖掘和对比分析,DCS系统能够发现生产过程中的潜在问题和改进空间,为优化生产提供决策支持。
此外,DCS系统还可以与企业的ERP系统、MES 系统等进行无缝集成,实现全面的生产管控和资源协同。
二、DCS系统在电子制造行业的应用案例1. 半导体芯片制造半导体芯片制造是电子制造中最重要的环节之一,也是最复杂和关键的过程之一。
DCS系统在半导体芯片制造中的应用主要体现在设备集成控制、工艺调整和质量控制等方面。
通过DCS系统的集成控制,各个设备之间可以实现自动化的协同操作,避免了人工干预带来的误差和延误。
同时,DCS系统能够根据工艺参数的变化,实时调整工艺流程和设备参数,以保证芯片生产的一致性和稳定性。
浅谈发电厂DCS系统应用及发展

他技术不断的融合, 也将 出现某些功能在逐步被其他优秀 功能取代 。 新技术 就像注入新鲜的血液, 给火 电厂不断注入新的活力。一体化是DCS 系统 的发 展趋势, 将DCS 和S I S 有机的整合在一起, 把现场的数字化信号和管理系统整
产调度 、 过程监控与过程控制 强行分开 。但是, 在现实的 自 动化实施过程 中, 很难把各种功能准确的分 开。特别是现在第四代DC S 已经 实现 了五层功 能 中的许多功能 。 目 前看来, 许多 电厂应该大的提高。DCS 在 自动化技术 的不断发展的过程中, 在 与其
2 . DC S 系 统 发 展状 况
靠性 。 开环控制分为联锁保护 , 顺序控制, 选线控制等 。 火 电厂单元机组 中主 机和辅机设备都有联锁保护 , 如停机或停炉 , 一些 重要辅机的保护跳 闸, 备 用泵会 自动启动,成组设备 的顺序启停等 ,这些联锁保护现在一 一 般都在运
行。 4 . DC S 系统应用分析
科 学 进步
浅谈发 电厂 D C S系统 应用及发展
蒙冠霖
( 天津 市大唐 国际盘山发 电有 限责任 公司 设备部) 摘 要: 随着 科技 的迅猛 发展, 火 电厂热 工 自动化技 术也随之得到快速 发展, 随着单 机发 电容量 的增大和 电网容量 的迅速扩大 , 我 国已进入 了大 电 网、 大机 组、 高参数、 高度 自动化的 时代 。由于3 0 ∞ ^ , 、 6 o 0 Mw以及以上大容量、 高参数机组 的新技术发展迅速 , 装机数量 日益增 多, 机 组对热 工 自动化水 平 的要 求越 来越高。其中 , 具有代表性 的是8 0 年代 微机分散控制系统 ( D CS ) 的问世和 日益 完善, 并广 泛应用于大机组的 自动控制 。 关键 词: 自动 化 ; 控制 ; 电厂
dcs国内外发展现状

DCS(分布式控制系统)是工业自动化领域的一种重要技术,广泛应用于各种工业生产过程中。
本文将介绍DCS国内外发展现状,主要包含以下方面:1. 分散化和智能化随着工业生产过程的复杂性和集成度的不断提高,DCS系统逐渐向着分散化和智能化方向发展。
DCS系统的基本思想是将控制系统分散到不同的计算机节点上,每个节点只处理一部分任务,从而提高系统的可靠性和灵活性。
同时,随着人工智能技术的不断发展,DCS 系统也逐渐融合了各种智能化算法,实现了更加高效和精确的控制。
2. 系统构成的多样化DCS系统的构成逐渐向着多样化的方向发展。
传统的DCS系统通常由控制器、输入输出模块、通讯网络等部分组成,而现在,DCS 系统已经发展出了许多新的组成部分,如数据库服务器、工程师站、操作员站等,这些新组成部分使得DCS系统更加适合于处理复杂工业生产过程。
3. 综合自动化DCS系统逐渐向着综合自动化的方向发展。
传统的DCS系统主要关注的是控制功能,而现在的DCS系统则更加注重与现场设备、传感器、执行器等设备的集成,实现了更加高效和可靠的生产过程控制。
4. 集中管理DCS系统逐渐向着集中管理的方向发展。
传统的DCS系统通常采用分布式的管理方式,每个节点都有自己的管理软件和管理界面,这使得管理起来比较困难。
而现在的DCS系统则采用了集中管理的方式,将所有的节点都统一管理起来,从而提高了管理效率和管理质量。
5. 信息传递实时性高DCS系统的信息传递实时性比较高。
传统的DCS系统通常采用基于TCP/IP协议的通讯方式,这种通讯方式具有比较高的实时性。
而现在的DCS系统则采用了更加高效的通讯协议和通讯方式,如Ethernet/IP、Profinet等,这些通讯协议和方式具有更高的数据传输速率和更低的延迟,从而提高了系统的实时性。
6. 受制于系统厂商DCS系统的发展也存在着一些问题。
其中之一是DCS系统受制于系统厂商。
由于不同厂商的DCS系统架构和实现方式不同,这使得用户在选择DCS系统时存在一定的风险。
DCS系统原理及应用情况

DCS系统原理及应用情况DCS(分布式控制系统)是一种广泛应用于工业控制领域的先进控制系统。
它是由多个分布式控制器组成的网络系统,用于监测和控制工厂中的各种工序和设备。
DCS系统具有高可靠性、可扩展性和灵活性,广泛应用于化工、电力、石油、冶金等领域。
DCS系统的原理是通过以太网或现场总线将各个分布式控制器连接起来,形成一个网络。
每个分布式控制器负责监测和控制一组特定的设备或工序,通过网络通信实现数据传输和共享。
所有的控制器都可以通过一个中央控制台进行集中管理和监控。
DCS系统的关键组成部分包括分布式控制器、输入/输出模块、以太网或现场总线、传感器和执行器等。
分布式控制器是系统的核心,负责处理数据和执行控制算法。
输入/输出模块用于与现场设备进行数据交换,传感器用于监测设备的状态,执行器用于控制设备的操作。
DCS系统的应用主要包括过程控制、设备控制和数据管理。
在过程控制方面,DCS系统可以实现对连续或离散工序的监测和调节,如温度、压力、液位等参数的控制。
在设备控制方面,DCS系统可以对各种设备进行监测和控制,如泵、阀门、电机等。
在数据管理方面,DCS系统可以实现数据采集、存储和分析,为企业管理和决策提供支持。
DCS系统的应用案例非常广泛。
在化工领域,DCS系统可以实现对化工生产过程的控制和优化,提高生产效率和产品质量。
在电力领域,DCS 系统可以实现电厂发电设备的运行控制和监测,确保电网的稳定和安全。
在石油领域,DCS系统可以实现油气生产过程的控制和调节,提高采收率和利润。
在冶金领域,DCS系统可以实现钢铁生产过程的控制和优化,提高生产效率和产品质量。
总之,DCS系统是一种先进的工业控制系统,具有高可靠性、可扩展性和灵活性。
它在过程控制、设备控制和数据管理领域都有广泛的应用。
随着工业自动化的不断发展,DCS系统的应用前景将更加广阔。
dcs的应用场景
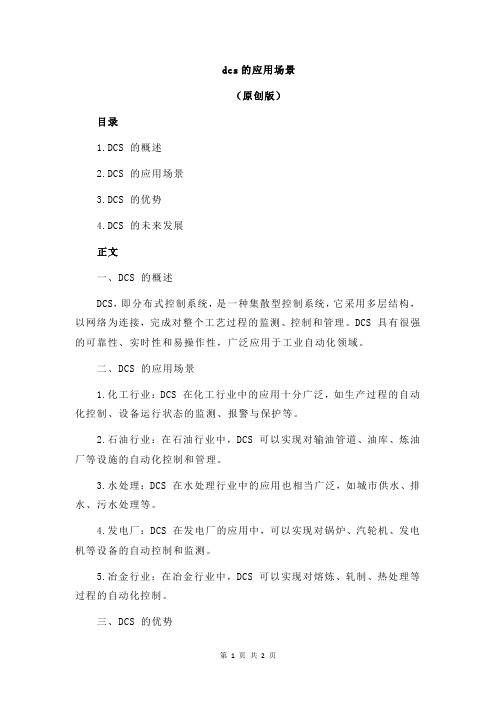
dcs的应用场景(原创版)目录1.DCS 的概述2.DCS 的应用场景3.DCS 的优势4.DCS 的未来发展正文一、DCS 的概述DCS,即分布式控制系统,是一种集散型控制系统,它采用多层结构,以网络为连接,完成对整个工艺过程的监测、控制和管理。
DCS 具有很强的可靠性、实时性和易操作性,广泛应用于工业自动化领域。
二、DCS 的应用场景1.化工行业:DCS 在化工行业中的应用十分广泛,如生产过程的自动化控制、设备运行状态的监测、报警与保护等。
2.石油行业:在石油行业中,DCS 可以实现对输油管道、油库、炼油厂等设施的自动化控制和管理。
3.水处理:DCS 在水处理行业中的应用也相当广泛,如城市供水、排水、污水处理等。
4.发电厂:DCS 在发电厂的应用中,可以实现对锅炉、汽轮机、发电机等设备的自动控制和监测。
5.冶金行业:在冶金行业中,DCS 可以实现对熔炼、轧制、热处理等过程的自动化控制。
三、DCS 的优势1.高度集成:DCS 采用分散与集中相结合的控制方式,具有高度集成的特点,可以减少设备投资和维护费用。
2.系统稳定性:DCS 采用多层结构,具有良好的系统稳定性和可靠性,能够满足工业生产过程中对自动化控制的需求。
3.易操作性:DCS 的操作界面直观、友好,方便操作人员进行监控和管理,提高生产效率。
4.系统扩展性:DCS 具有良好的系统扩展性,可以根据生产需要进行灵活扩展和配置。
四、DCS 的未来发展随着科技的进步和工业自动化水平的提高,DCS 在未来将会有更广泛的应用和更大的发展空间。
未来的 DCS 将会更加智能化、网络化和一体化,以满足不断变化的市场需求。
DCS技术的应用与发展趋势分析
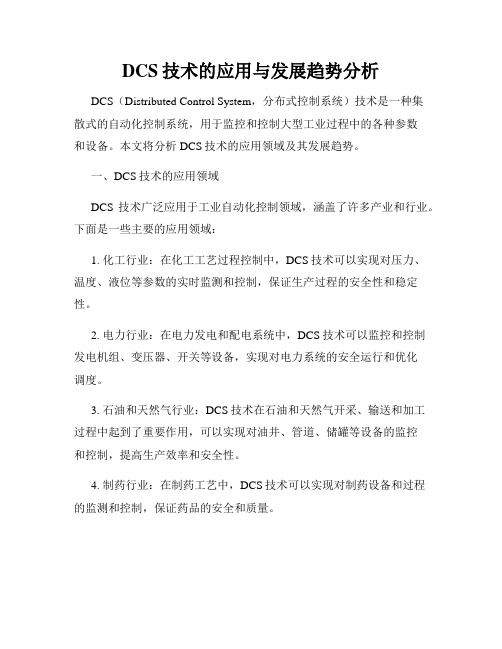
DCS技术的应用与发展趋势分析DCS(Distributed Control System,分布式控制系统)技术是一种集散式的自动化控制系统,用于监控和控制大型工业过程中的各种参数和设备。
本文将分析DCS技术的应用领域及其发展趋势。
一、DCS技术的应用领域DCS技术广泛应用于工业自动化控制领域,涵盖了许多产业和行业。
下面是一些主要的应用领域:1. 化工行业:在化工工艺过程控制中,DCS技术可以实现对压力、温度、液位等参数的实时监测和控制,保证生产过程的安全性和稳定性。
2. 电力行业:在电力发电和配电系统中,DCS技术可以监控和控制发电机组、变压器、开关等设备,实现对电力系统的安全运行和优化调度。
3. 石油和天然气行业:DCS技术在石油和天然气开采、输送和加工过程中起到了重要作用,可以实现对油井、管道、储罐等设备的监控和控制,提高生产效率和安全性。
4. 制药行业:在制药工艺中,DCS技术可以实现对制药设备和过程的监测和控制,保证药品的安全和质量。
5. 食品和饮料行业:DCS技术在食品生产中的应用越来越广泛,可以实现对温度、湿度、pH值等参数的实时监控,保证食品的生产过程符合卫生标准。
6. 污水处理行业:DCS技术可以实现对污水处理设备和过程的监控和控制,提高污水处理的效率和环保指标。
二、DCS技术的发展趋势随着科技的不断进步和应用需求的不断增加,DCS技术也在不断发展和演进。
下面是一些DCS技术的发展趋势:1. 高可靠性和安全性:随着工业系统的规模越来越大,对系统的可靠性和安全性要求也越来越高。
未来的DCS技术将着重提高系统的稳定性和防护能力,确保系统不受外部攻击和故障的影响。
2. 大数据和云计算:DCS系统中生成的数据量庞大,传统的数据存储和处理方式已经无法满足需求。
未来的DCS技术将引入大数据和云计算技术,实现对数据的实时处理和分析,提高系统的智能化和效率。
3. 智能化和自动化:未来的DCS技术将越来越智能化和自动化,通过引入人工智能和机器学习算法,实现对系统的自动优化和决策,提高生产过程的效率和质量。
- 1、下载文档前请自行甄别文档内容的完整性,平台不提供额外的编辑、内容补充、找答案等附加服务。
- 2、"仅部分预览"的文档,不可在线预览部分如存在完整性等问题,可反馈申请退款(可完整预览的文档不适用该条件!)。
- 3、如文档侵犯您的权益,请联系客服反馈,我们会尽快为您处理(人工客服工作时间:9:00-18:30)。
DCS结构与组成
DCS控制站
• 1.DCS控制站 • DCS系统中,控制站继承了DDC技术,它是一个完整的计算 机,实际运行中可以在不与操作站及网络相连的情况下, 完成过程控制策略,保证生产装置正常运行。 • 控制站作为一个完整的计算机,它的主要I/O设备为现场的 输入、输出处理设备,以及过程输入/输出(P I/O)量, 包括信号变换与信号调理,A/D、D/A转换等。它在第二代 和第三代产品中已陆续采用了嵌入式技术,并采用单片机 等完成量程调整、远程I/O数据传输、小型化及减少P I/O 卡硬件规格等功能,直至连接智能化的现场变送器或接受 采用现场总线提供的数字信号。
• 2. 第二代DCS(成熟期) • 第二代DCS是在1980~1985年推出的各种系统,其中 包括Honeywell公司的TDGC-3000、Fisher公司的 PROVOX、Taylor公司的MOD300及Westinghouse公司的 WDPF等系统。
引入局域网作为系统骨干 摆脱仪表,靠近计算机 增加顺序控制、逻辑控制 可以实现优化控制和管理功能 显示技术得到提高,出现光标操作
DCS系统的发展历程
• 从1975年第一套DCS诞生到现在,DCS经历了3个大的 发展阶段,或者说经历了三代产品。 • 1. 第一代DCS (初创期) – 第一代DCS是指从其诞生的1975~1980年间所出现的第 一批系统,控制界称这个时期为初创期或开创期。这 个时期的代表是率先推出DCS的Honeywell公司的 TDC—2000系统,同期的还有Yokogawa(即横河)公司 的Yawpark系统、Foxboro公司的Spectrum系统、Bailey 公司的Network 90系统、Kent公司的P4000系统、 Siemens公司的Teleperm M系统及东芝公司的TOSDIC 系统等。注重功能的实现;使用专用软、硬件,价格 昂贵;没有统一标准,开放性差。
DCS系统的应用与发展
介绍内容
• • • • • • • • • • 前言 过程控制的发展概况 过程控制的主要内容 DCS系统的发展历程 DCS结构与组成 DCS系统的特点 DCS系统在中国的应用 DCS系统品牌 DCS VS PLC FCS VS DCS
前言
DCS系统的含义是集散型控制系统,也称为分 布式计算机控制系统(Distributed Control Systems),它紧密依赖于自动控制技术、计算 机技术、通信技术和CRT显示技术(4C)。
过程控制的主要内容
• 3.自动操纵及自动开停车系统 • 自动操纵系统:根据预先规定的步骤自动地对生产设备进 行某种周期性操作 • 如:合成氨造气车间煤气发生炉,按吹风、上吹、下吹、 吹净等,步骤周期性地接通空气和水蒸汽 • 自动开停车系统:按预先规定好的步骤将生产过程自动的 投入运行或自动停车
DCS系统的出现背景
I/O设备(模块)
• I/O设备提供数字量I/O ,模拟量I/O和智能变送 器信号的转换。允许相 应的信号与分散处理单 元DPU通讯。宽量程的 I/O转换模件可以执行各 种类型的信号转换使分 散处理单元与现场传感 器和执行机构接口。
DCS控制站的系统软件
• 关于DCS控制站的系统软件,原则上也有实时操作系统、编 程语言及编译系统、数据库系统、自诊断系统等,只是完 善程度不同而己。 • 第一代DCS控制站的功能更近似于多回路调节器,而且每个 控制站都可以配置人机界面和备用操作器; • 第二代DCS控制站的实时操作系统及程序编译系统比较完整 ,编程语言有面向过程语言和高级语言,控制策略的组态 由操作站或工作站在与控制站联机的情况下,完成编译和 下载; • 第三代DCS控制站的系统软件齐全,操作站或工程师站可以 完成离线组态及在线修改控制策略。
控制站是整个DCS的基础
• 控制站是整个DCS的基础,它的可靠性和安全性最为重要 ,死机和控制失灵的现象是绝对不允许的,而且冗余、掉 电保护、抗干扰、防爆系统构成等方面都应有很高的可靠 性,才能满足用户要求。多年的实践经验证明,绝大多数 厂家的DCS控制站都能够胜任用户要求。
分散处理单元(DPU)
过程控制的主要内容
• 1.自动检测系统—利用各种检测仪表对工艺参数进行测量 、指示或记录,如:加热炉温度、压力检测 • 2.自动信号和联锁保护系统 • 自动信号系统:当工艺参数超出要求范围,自动发出声光 信号 • 联锁保护系统:达到危险状态,打开安全阀或切断某些通 路,必要时紧急停车 • 如:反应器温度、压力进入危险限时,加大冷却剂量或关 闭进料阀
过程控制的发展概况
• 20世纪40年代末~50年代(仪表化与局部自动化阶段): • 过程控制系统:多为单输入、单输出简单控制系统 • 过程检测:采用基地式仪表和部分单元组合仪表(多数是 气动仪表) ;部分生产过程实现了仪表化和局部自动化。 • 控制理论:以反馈为中心的经典控制理论
过程控制的发展概况
• 分散处理单元(DPU)是一种 集智能化、高可靠、低功耗 以及硬件软件易升级等众多 先进技术于一体的高性能控 制单元,是过程控制系统的 核心。总线CPU通过SBUS 总线完成IO信息和状态信息 的交换,运算CPU完成相 应的控制运算以及通过以太 网与工作站进行数据信息交 换。双CPU协调工作,确 保DPU可靠高效的工作。
访问电源——为现场检测回路供电,变送器回路为24VDC, 开关量回路电压等级较多,一般使用24VDC、48VDC较多
•为保证DCS系统的高可靠性和高可用性,电源系统都为冗余配 置: 1+1冗余:使用两个开关电源,加一个两极管模块并联;
N+1冗余:使用多个开关电源并联;
接地系统
•接地系统是DCS的一个重要组成部分,接地系统的不 完善将直接导致DCS系统不能正常、稳定工作,甚至 导致安全事故。 •DCS系统机柜内一般分为三个地:
过程控制的发展概况
• 过程控制系统-----指自动控制系统的被控量是温度、压力 、流量、液位成分、粘度、湿度以及PH值(氢离子浓度)等 这样一些过程变量时的系统。
• 20世纪40年代(手工阶段):手工操作状态,只有少量的检 测仪表用于生产过程,操作人员主要根据观测到的反映生 产过程的关键参数,人工来改变操作条件,凭经验去控制 生产过程,劳动生产率很低。
过程控制的发展概况
• 20世纪70~80年代(全盘自动化阶段) : • 过程控制系统:最优控制、非线性分布式参数控制、解耦 控制、模糊控制 • 过程检测:新型仪表、智能化仪表、以微处理器为主要构 成单元的智能控制装置。单回路调节器KMM。 • 集散控制系统(DCS)、可编程逻辑控制器(PLC)、工业PC 机、和数字控制器等,已成为控制装置的主流,实现了控 制分散、危险分散,操作监测和管理集中。 • 控制理论:形成了大系统理论和智能控制理论。模糊控制 、专家系统控制、模式识别技术
DCS操作站
• DCS操作站具有操作员功能、工程师功能、通信功能 和高级语言功能等,其中工程师功能中包括系统组态 、系统维护、系统通用(Utility)功能。主要的类 型有工程师站、操作员站、历史站、数据接口站等。
数据通信及网络
• 在DCS系统诞生时,主要解决一个生产装置中几个控制站和 一个或几个操作站之间的数据通信问题;第二代DCS则解决 多个装置的DCS互联问题;第三代DCS则解决一个工厂的多 个车间互联及与全厂计算机管理网络互联的问题,这是总 的设计思想。
• 仪表控制的缺点
–监控和操作的要求越来越高 –功耗高、体积大、故障率高 –难实现先进控制,无法实现过程优化
• 仪表控制的优点
–局部故障不影响全局
DCS系统的出现背景
• 70年代初,有人用如DEC公司的PDP11/24这样的小型机代 替原来的集中安装的模拟仪表控制。安装在中央控制室的 PDP11/24,用电缆把现场仪表的信号传到中央控制室。小 型机既作为控制器、同时把连接小型机的CRT又作为显示 设备(即人机界面)。一台小型机需接收几上千台变送器 或别的传感器来的信号,完成几百个回路的运算。很显然 其危险有点集中。一旦小型机坏了,控制和显示都没有了 。当时数字控制没有达到预期的目的。当时有一个比喻, 称为把所有的鸡蛋放在一个篮子内。篮子坏了,所有鸡蛋 也都坏了。
ቤተ መጻሕፍቲ ባይዱ
过程控制的发展概况
• 20世纪90年代至今:信息技术飞速发展 • 过程控制系统:管控一体化现场,综合自动化是当今生产 过程控制的发展方向。 • 自动化仪表:总线控制系统的出现,引起过程控制系统体 系结构和功能结构上的重大变革。现场仪表的数字化和智 能化,形成了真正意义上的全数字过程控制系统。各种智 能仪表、变送器、无纸纪录仪 • 人工智能、神经网络控制
DCS操作站
• 实际的DCS操作站是典型的计算机,它与控制站不同,有 着丰富的外围设备和人机界面。70年代中期,CRT显示器 技术已成熟,以外部存储器为特征,第二代DCS操作站还 具有如下特点:操作站和工程师站(或称工作站)分开 ,也有公司将操作站的历史数据存储用硬盘(历史模件 )和高级语言应用站(应用模件)分别独立挂在通信网 络上;操作系统除采用DOS系统以外,有的产品采用Unix 等操作系统;实时数据库储存性能逐渐完善;在人机界 面方面,逐渐过渡为以GUI图形用户界面为平台并采用鼠 标、组态时制作流程图和控制回路图等方法,采用菜单 、窗口、CAD等技术,使人机界面友好。
“分散”指: 1、工艺上各种设备地理位置的分散。
2、功能分散。 “集”:集中监视、集中管理。
• DCS系统=分散式控制系统=集散控制系统= 分布控制系统 • DCS的基本思想是: 分散控制 集中操作 分级管理 配置灵活 组态方便。
当前DCS结构特点
• 典型的DCS网络系统可分为控制级、监控级、管理级三个 分级。 • 第一层控制级,主要以分散处理单元DPU(Distributed Processing Unit)和I/O模块通过现场总线构成对现场设备 的基本控制; • 第二层是监控级,即以监控计算机通过工控网络与DPU或 I/O模块相连,实现对流程设备的上位机监控; • 第三层为管理级,即以文件服务器、管理计算机及其工业 局域网与监控计算机相连,随时读取现场信息实现上层的 生产管理。