元器件焊接检验规范
SMT检验标准(IPC-610F)

1目的为了提升SMT内产品焊接的品质,本文件规定了SMT内相关元件的焊接标准,使员工操作时有依据可寻,减少误判、错判。
2范围本规范适用SMT车间所有焊接后的产品。
3定义无4职责4.1工艺部4.1.1负责对本文件进行编制、修订等操作;4.1.2负责依据本标准对设备相关检验标准进行设定;4.1.3负责对操作员和品质人员无法进行判断的可疑品进行复判,并将结果告诉相关人员;4.2制造部4.2.1负责按照本标准对相关可疑品进行判定;4.2.2出现异常时及时报告相关人员;4.3品质部4.3.1监督员工是否按照本标准进行可疑品判定;4.3.2负责对操作员无法进行判断的可疑品进行复判,并将结果告诉操作员;5内容5.1矩形或方形端片式元件5.1.1尺寸要求最大元器件尺寸1206,注8端子元器件每端有3个或3个以上可润湿端子区域注1:不违反最小电气间隙。
注2:未作规定的尺寸参数或变量,由设计决定。
注3:润湿明显。
注4:最大填充可偏出焊盘和/或延伸至端帽金属镀层的顶部或侧面;但焊料不能接触到元器件的顶部或侧面。
注5:(C)是从焊料填充最窄处测量。
注6:这些要求是为组装过程中可能会翻转成窄边放置的片式元器件而制定。
注7:对于某些高频或高振动应用,这些要求可能是不可接受的。
注8:对于宽高比小于1.25:1及有5面端子的元器件可以大于12065.1.2侧面偏移5.1.3末端偏出目标:侧面无偏移现象可接受:侧面偏出(A)小于或等于元器件端子宽度(W)的25%,或焊盘宽度(P)的25%,取两者中的较小者不良:侧面偏出(A)大于元器件端子宽度(W)的25%,或焊盘宽度(P)的25%,取两者中的较小者目标:无末端偏出现象5.1.4末端焊接宽度不良:元件末端偏出焊盘目标:末端连接宽度等于元器件端子宽度或焊盘宽度,取两者中的较小者可接受:末端连接宽度(C)至少为元器件端子宽度(W)的75%或焊盘宽度(P)的75%,取两者中的较小者5.1.5最大爬锡高度5.1.6最小爬锡高度不良:小于可接受末端连接宽度下限目标:最大爬锡高度为焊料厚度加上元器件端子高度不良:焊料延伸至元器件本体顶部目标:最小爬锡高度(F)为焊料厚度(G)加上端子高度(H)的25%或焊料厚度(G)加上0.5mm[0.02in],取两者中的较小者5.1.7元件末端重叠5.1.8侧立5.1.9翻件不良:小于焊料厚度(G)加上端子高度(H)的25%或焊料厚度(G)加上0.5mm [0.02in],取两者中的较小者目标:元器件端子和焊盘之间至少有25%的重叠接触不良:元器件端子和焊盘之间小于25%的重叠接触不良:元器件不允许侧立目标:片式元器件的电气要素面朝上放置制程警示:片式元器件的电气要素面朝下放置5.1.10立碑不良:元器件不允许立碑5.2圆柱体帽形端⼦5.2.1尺寸要求参数尺寸要求最大侧面偏移 A 25% (W) 或25% (P),取两者中的较小者;注1末端偏出 B 不允许最小末端连接宽度,注2 C 50% (W) 或 50% (P),取两者中的较小者;最小侧面连接长度 D 75%(R)或75%(S),取两者中的较小者;注6最大爬锡高度 E 注5最小爬锡高度(末端与侧面) F (G) + 25%(W) 或(G) + 1mm[0.04in],取两者中的较小者焊料厚度G 注4最小末端重叠J 75%(R);注6焊盘宽度P 注3端子/镀层长度R 注3焊盘长度S 注3端子直径W 注3注1:不违反最小电气间隙。
SMT焊接推力检验标准
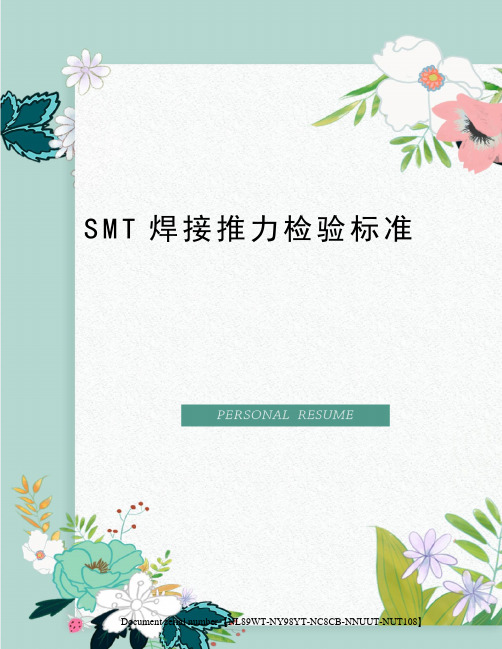
15
USB插座(按插拔方向推力)
1.消除阻碍USB插座边缘的其它元器件
2.选用推力计,将仪器归零,≤30度角进行推力试验;
3.当推力计达到推力标准时,检查元器件是否脱焊
≥
16
TF卡座
1.消除阻碍TF卡座边缘的其它元器件
2.选用推力计,将仪器归零,≤30度角进行推力试验;
3.当推力计达到推力标准时,检查元器件是否脱焊
≥
17
纽扣电池
1.消除阻碍电池边缘的其它元器件
2.选用推力计,将仪器归零,≤30度角进行推力试验;
3.当推力计达到推力标准时,检查元器件是否脱焊
≥
18
多脚芯片(8脚及以上)
1.消除阻碍芯片边缘的其它元器件
2.选用推力计,将仪器归零,≤30度角进行推力试验;
3.当推力计达到推力标准时,检查元器件是否脱焊
3.当推力计达到推力标准时,检查元器件是否脱焊
≥
9
晶体
1.消除阻碍晶体元器件边缘的其它元器件
2.选用推力计,将仪器归零,≤30度角进行推力试验;
3.当推力计达到推力标准时,检查元器件是否脱焊
≥
10
RF连接器
1.消除阻碍RF连接器边缘的其它元器件
2.选用推力计,将仪器归零,≤30度角进行推力试验;
3.当推力计达到推力标准时,检查元器件是否脱焊
3.当推力计达到推力标准时,检查元器件是否脱焊
≥
3
0805器件
1.消除阻碍0805元器件边缘的其它元器件
2.选用推力计,将仪器归零,≤30度角进行推力试验;
3.当推力计达到推力标准时,检查元器件是否脱焊
≥
4
1206器件
1.消除阻碍1206元器件边缘的其它元器件
SMT元器件焊接强度推力测试标准
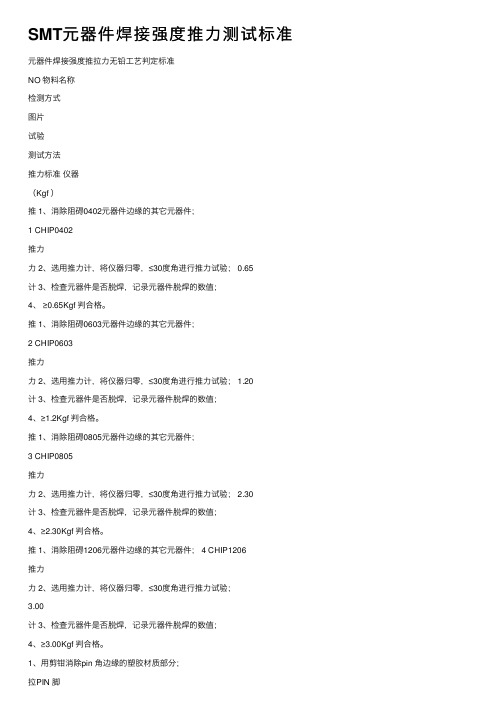
SMT元器件焊接强度推⼒测试标准元器件焊接强度推拉⼒⽆铅⼯艺判定标准NO 物料名称检测⽅式图⽚试验测试⽅法推⼒标准仪器(Kgf )推 1、消除阻碍0402元器件边缘的其它元器件;1 CHIP0402推⼒⼒ 2、选⽤推⼒计,将仪器归零,≤30度⾓进⾏推⼒试验; 0.65计 3、检查元器件是否脱焊,记录元器件脱焊的数值;4、 ≥0.65Kgf 判合格。
推 1、消除阻碍0603元器件边缘的其它元器件;2 CHIP0603推⼒⼒ 2、选⽤推⼒计,将仪器归零,≤30度⾓进⾏推⼒试验; 1.20计 3、检查元器件是否脱焊,记录元器件脱焊的数值;4、≥1.2Kgf 判合格。
推 1、消除阻碍0805元器件边缘的其它元器件;3 CHIP0805推⼒⼒ 2、选⽤推⼒计,将仪器归零,≤30度⾓进⾏推⼒试验; 2.30计 3、检查元器件是否脱焊,记录元器件脱焊的数值;4、≥2.30Kgf 判合格。
推 1、消除阻碍1206元器件边缘的其它元器件; 4 CHIP1206推⼒⼒ 2、选⽤推⼒计,将仪器归零,≤30度⾓进⾏推⼒试验;3.00计 3、检查元器件是否脱焊,记录元器件脱焊的数值;4、≥3.00Kgf 判合格。
1、⽤剪钳消除pin ⾓边缘的塑胶材质部分;拉PIN 脚拉 2、选⽤推⼒计,将仪器归零,使⽤专⽤拉⼒测试夹具,垂5 SIM 卡连接(六个⼒直成90度向上拉起,1.00器脚)计 3、检查元器件是否拉掉是否脱焊,记录元器件脱焊的数值;4、≥1.00kgf 判合格。
推⼒(六1、消除阻碍SIM 卡元器件边缘的其它元器件;推 2、选⽤推⼒计,将仪器归零,≤30度⾓(如图所⽰)进⾏SIM 卡连接个脚)6⼒推⼒试验;5.00器(左右⽅向)计 3、检查元器件是否破裂,记录元器件破裂的数值;4、≥ 5.00 Kgf 判合格。
推 1、消除阻碍SOT23元器件边缘的其它元器件;7 SOT23推⼒⼒ 2、选⽤推⼒计,将仪器归零,≤30度⾓进⾏推⼒试验; 2.00计 3、检查元器件是否脱焊,记录元器件脱焊的数值;4、≥2.00Kgf 判合格。
电子元器件焊接质量检验标准

焊接质量检验标准焊接在电子产品装配过程中是一项很重要的技术,也是制造电子产品的重要环节之一。
它在电子产品实验、调试、生产中应用非常广泛,而且工作量相当大,焊接质量的好坏,将直接影响到产品的质量。
电子产品的故障除元器件的原因外,大多数是由于焊接质量不佳而造成的。
因此,掌握熟练的焊接操作技能对产品质量是非常有必要的。
(一)焊点的质量要求:对焊点的质量要求,应该包括电气接触良好、机械接触牢固和外表美观三个方面,保证焊点质量最关键的一点,就是必须避免虚焊。
1.可靠的电气连接焊接是电子线路从物理上实现电气连接的主要手段。
锡焊连接不是靠压力而是靠焊接过程形成牢固连接的合金层达到电气连接的目的。
如果焊锡仅仅是堆在焊件的表面或只有少部分形成合金层,也许在最初的测试和工作中不易发现焊点存在的问题,这种焊点在短期内也能通过电流,但随着条件的改变和时间的推移,接触层氧化,脱离出现了,电路产生时通时断或者干脆不工作,而这时观察焊点外表,依然连接良好,这是电子仪器使用中最头疼的问题,也是产品制造中必须十分重视的问题。
2.足够机械强度焊接不仅起到电气连接的作用,同时也是固定元器件,保证机械连接的手段。
为保证被焊件在受振动或冲击时不至脱落、松动,因此,要求焊点有足够的机械强度。
一般可采用把被焊元器件的引线端子打弯后再焊接的方法。
作为焊锡材料的铅锡合金,本身强度是比较低的,常用铅锡焊料抗拉强度约为3-4.7kg/cm 2,只有普通钢材的10%。
要想增加强度,就要有足够的连接面积。
如果是虚焊点,焊料仅仅堆在焊盘上,那就更谈不上强度了。
3.光洁整齐的外观良好的焊点要求焊料用量恰到好处,外表有金属光泽,无拉尖、桥接等现象,并且不伤及导线的绝缘层及相邻元件良好的外表是焊接质量的反映,注意:表面有金属光泽是焊接温度合适、生成合金层的标志,这不仅仅是外表美观的要求。
典型焊点的外观如图1所示,其共同特点是:① 外形以焊接导线为中心,匀称成裙形拉开。
SMT焊接检验标准及元器件推力标准
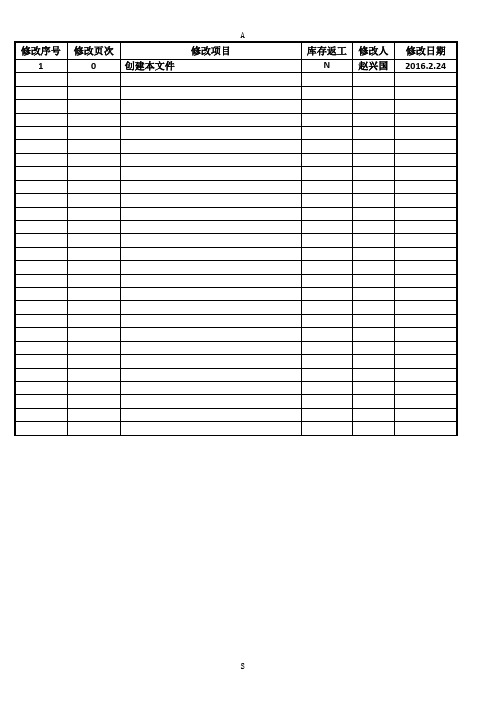
不合格图示合格图示2多件不需要的器件而有的。
多出不应该有多一顆零件不合格图示合格图示3错件不符合BOM 的料号或放错位置。
1k 正确1k101错误101错误不合格图示102正确合格图示4浮件(倾斜)器件浮起>0.3 mm ,不允许; 器件一端倾斜>0.3 mm ,不允许;0.3mm0.3mm<03mm不合格图示合格图示序号检查项目缺陷定义描述及图示参考图示5立碑1、应正面摆放变成侧面摆放的;2、应两端接触变成单边接触的;单边吃锡侧置不合格图示合格图示6空焊 应焊锡而未焊到的。
未吃锡不合格图示合格图示器件脚与锡未完全融合。
不合格图示合格图示不应导通而导通的。
不合格图示应导通而未导通的。
不合格图示缺陷定义描述及图示不合格图示以器件脚的宽度为准,偏移不可0.1mm0.3mm不合格图示合格图示<1/2W缺陷定义描述及图示<1/2W焊点四周及PCB板面上不得有锡球或其他焊锡残渣等。
合格图示不合格图示单面不允许>0.5mm,不合格图示合格图示序号检查项目缺陷定义描述及图示参考图示18 锡不足(锡少) 锡焊高度h不小于1/3H(器件高度)。
h≧1/ 3Hh器件高度H不合格图示合格图示19 极性反正负极性反向。
正确++错误黑线是负极不合格图示黑线是负极合格图示7.2插件类元器件检验标准序号检查项目缺陷定义描述及图示参考图示1 缺件应有器件而没有器件的。
缺件L8L8不合格图示合格图示2 多件不需要器件而有器件的。
L8正确L8多余不合格图示合格图示序号检查项目缺陷定义描述及图示参考图示3 错件不符合BOM料号要求或放错位置。
1Ω正确100Ω错误不合格图示合格图示4 浮件(倾斜1. 器件距PCB板面> 1.3 mm;2. 器件一端倾斜> 1.3 mm。
(a) 1.3mm浮件(b)hh>=1. 3mm倾斜不合格图示合格图示5 包焊表面造成气球状 (将器件脚整个包住)。
电子元器件焊接规范标准精选全文

可编辑修改精选全文完整版迪美光电电路板焊接标准概括---A手插器件焊接工艺标准一.没有引脚的PTH/ VIAS(通孔或过锡孔)标准的(1)孔内完整充满焊料。
焊盘表面显示优秀的湿润。
(2)没有可见的焊接缺点。
可接受的(1)焊锡湿润孔内壁与焊盘表面。
(2)直径小于等于的孔一定充满焊料。
(3)直径大于的孔没有必需充满焊料但整个孔内表面和上表面一定有焊锡湿润。
不行接受的(1)部分或整个孔内表面和上表面没有焊料湿润。
(2)孔内表面和焊盘没有湿润。
在两面焊料流动不连续。
二.直线形导线1、最小焊锡敷层(少锡)标准的(1)焊点圆滑、光亮体现羽翼状薄边,显示出优秀的流动和湿润。
(2)导线轮廓可见。
可接受的(1)焊锡的最大凹陷为板厚(W)的 25%,只需在引脚与焊盘表面仍体现出优秀的浸润。
不行接受的(1)焊料凹陷超出板厚( W)的 25%。
(2)焊接表现为由焊锡不足惹起的没有充满孔和/ 或焊盘没有完整湿润。
2、最大焊锡敷层(多锡)标准的(1)焊点圆滑、光亮体现羽翼状薄边,显示出优秀的流动和湿润。
(2)引脚轮廓可见。
可接受的(1)在导体与终端之间多锡,但仍旧湿润且联合成一个凹形焊接带。
(2)引脚轮廓可见。
不行接受的(1)在导体与终端焊盘之间形成了一个多锡的凸形焊接带。
(2)引脚轮廓不行见。
3、曲折半径焊接标准的(1)焊接带体现凹形,而且没有延长到元件引脚形成的曲折半径处。
可接受的(1)焊料没有高出焊盘地区且焊接带体现凹形。
(2)焊想到元件本体之间的距离不得小于一个引脚的直径。
不行接受的(1)焊料高出焊接地区而且焊接带不体现凹形。
(2)焊想到元件本体之间的距离小于一个引脚的直径。
4、弯月型焊接标准的(1)焊接带体现出凹形而且弯月型部分没有延长进焊猜中。
可接受的(1)元件弯月型部分能够插入焊接联合处(元件面),只需在元件和周边焊接接合处没有裂缝。
不行接受的(1)元件半月型部分进入焊接接合处,在元件本体与周边焊接接合处有破碎的迹象。
元器件焊接质量检验规范
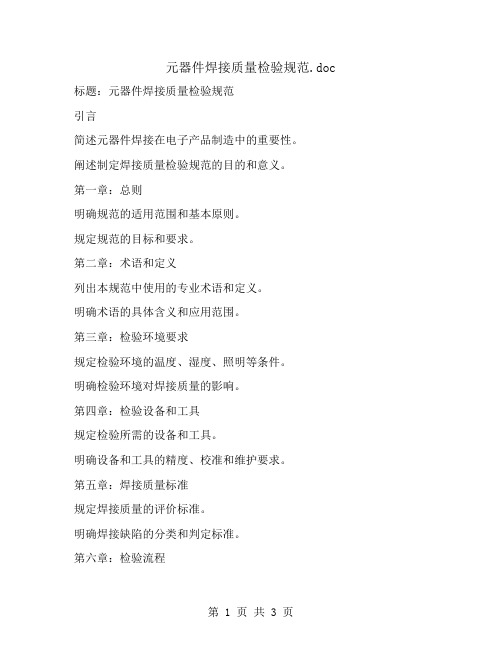
元器件焊接质量检验规范.doc 标题:元器件焊接质量检验规范引言简述元器件焊接在电子产品制造中的重要性。
阐述制定焊接质量检验规范的目的和意义。
第一章:总则明确规范的适用范围和基本原则。
规定规范的目标和要求。
第二章:术语和定义列出本规范中使用的专业术语和定义。
明确术语的具体含义和应用范围。
第三章:检验环境要求规定检验环境的温度、湿度、照明等条件。
明确检验环境对焊接质量的影响。
第四章:检验设备和工具规定检验所需的设备和工具。
明确设备和工具的精度、校准和维护要求。
第五章:焊接质量标准规定焊接质量的评价标准。
明确焊接缺陷的分类和判定标准。
第六章:检验流程描述焊接质量检验的流程。
明确各检验环节的操作要点。
第七章:外观检验规定外观检验的内容和方法。
明确外观缺陷的判定和记录要求。
第八章:机械性能检验规定机械性能检验的内容和方法。
明确机械性能缺陷的判定和记录要求。
第九章:电气性能检验规定电气性能检验的内容和方法。
明确电气性能缺陷的判定和记录要求。
第十章:破坏性检验规定破坏性检验的条件和方法。
明确破坏性检验的适用范围和记录要求。
第十一章:不合格品的处理规定不合格品的判定标准和处理流程。
明确不合格品的隔离、标识和处置要求。
第十二章:记录和文档管理规定检验记录的内容和格式。
明确记录的保存期限和管理要求。
第十三章:培训与考核规定检验人员的培训内容和考核标准。
明确培训和考核的周期和方法。
第十四章:监督与改进规定监督机制和持续改进的要求。
明确改进措施的实施和效果评估。
第十五章:附则规定本规范的解释权和修订权。
明确本规范的生效日期和相关法律法规的适用。
结语强调元器件焊接质量检验规范对于确保产品质量的重要性。
鼓励各方积极参与和支持规范的实施。
贴片焊接件检验规范书--贴片件

焊接件检验规范书焊接件名称:贴片件文件编号修改版本页次共两页生效日期序号检验项目描述图示或备注1 焊点标准1、焊缝表面总体光滑、无针孔,锡的流散性好2、焊料在被焊件上充分润湿,有光亮的、大致光滑的外观,并在被焊金属表面形成凹形的弯液面3、焊接件的轮廓清晰4、连接处的焊料中间厚边上薄,焊缝形状为凹型5、锡将整个上锡位及零件脚包围示意图:实物图:2 长方体元器件焊接位置1、元器件的引脚或焊点应在焊盘上,最大侧面偏移A不应超过0.1*W。
2、元器件禁止末端偏移出焊盘,也就是说B小于零。
3、元器件与焊盘接触面应大于50%*W。
3 长方体元器件焊接标准1、焊锡宽度C,超过元器件的宽度W或P的80%。
2、 焊锡高度H ,至少应超过元器件的50%。
3、 焊锡高度E ,可以超出焊盘或爬伸至金属镀层端帽可焊端的顶部,但不可接触元件体。
4、此标准同样适用于圆柱体焊接标准。
4IC 管脚焊接位置要求:最大侧面偏移A 小于等于0.1*W最大末端偏移B 小于零,禁止末端偏移 最小末端焊点宽度C 大于等于0.8*W 最小侧面焊接宽度D 大于等于W 最大焊接高度E 小于图中虚线所示 最小焊接高度F 大于G+T管脚在距离垫底以2倍管脚宽度焊接在中心上5IC 管脚焊接标准实物图实例: 示意图例:标准:1、元件脚呈良好的沾锡情形。
2、元件脚的表面呈洁净光亮。
3、焊锡在元件脚上呈平滑的下抛物线型。
4、元件脚前端上锡满足1/2元件脚厚度。
6检查方法 1、 用双手举板检查与放大镜检查。
2、 把板倾斜45°,并保持离眼睛30cm 距离,检查整体外观;放大镜抽检焊点。
3、 视觉上不容易检查的点,使用镊子,注意不要破坏和变形焊接点。
4、对于不很明确的焊点,有必要通过电洛铁进一步判断是否焊接完好。
编制: 审核: 批准:≤2W≤2W焊接件检验规范书焊接件不良品文件编号修改版本页次共三页生效日期序号检验项目图示及描述1 元件位置不正确1、偏差允许误差A超过了0.1*W,W为元器件宽度2、元器件两端靠近,且间隙小于了0.13mm3、可焊末端超出了焊盘1、最小末端焊接宽度(C)小于元件引脚宽度W的50%2、元器件脚趾延伸出焊盘,即B大于零3、临近的元器件引脚有连接现象2 焊锡过多或过少1、焊锡过多:焊锡覆盖到元器件体上2、焊锡过少:最小焊缝高度(F)小于焊锡厚度(G)加可焊端高度(H)的50%焊锡过多:锡已溢流至元件脚肩部3 空焊可焊件末端漏焊或翘起或焊锡量少4 拉尖1、焊接及修整时拉尖的长度或高度超过1.0mm以上,拉尖违反元器件组装高度的限制或引线伸出量的要求。
电子元器件贴片及接插件焊接检验标准

偏移
矩 形 元 件
异 形 元 件
1
审核: 审核 批准: 批准 XXXX 电子有限公司 发布时间: 发布时间 编 制
编号: 编号 页号: 页号 2 / 8 版本号: 版本号
电子元器件贴片及插件焊接检验标准 电子元器件贴片及插件焊接检验标准
翘起
立起
矩 形 元 件
异 形 元 件
2
1
2
审核: 审核 批准: 批准 XXXX 电子有限公司 发布时间: 发布时间 编 制
电子元器件贴片及插件焊接检验标准 电子元器件贴片及插件焊接检验标准
电容
电阻、电感、 电阻、电感、二极管
5
审核: 审核 批准: 批准 XXXX 电子有限公司 发布时间: 发布时间 编 制
编号: 编号 页号: 页号 6 / 8 版本号: 版本号
电子元器件贴片及插件焊接检验标准 电子元器件贴片及插件焊接检验标准
有 有 有
插 件 焊 接
有 有
有 有 间 有 有
8
元件引脚长度— 元件引脚长度—双面有元件
插件元件引脚弯度
焊锡量— 焊锡量—单面板
焊锡量— 焊锡量—双面板
7
审核: 审核 批准: 批准 XXXX 电子有限公司 发布时间: 发布时间 编 制
编号: 编号 页号: 页号 8 / 8 版本号: 版本号
电子元器件贴片及插件焊接检验标准 电子元器件贴片及插件焊接检验标准
三极管、三端集成块 三极管、
连接器
集成块
6
审核: 审核 批准: 批准 XXXX 电子有限公司 发布时间: 发布时间 编 制
编号: 编号 页号: 页号 7 / 8 版本号: 版本号
电子元器件贴片及插件焊接检验标准 电子元器件贴片及插件焊接检验标准
SMT焊接外观检查规范
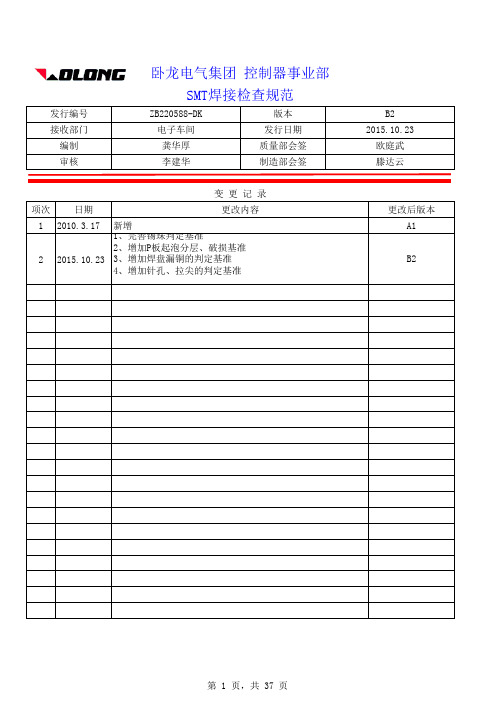
项次日期12010.3.1722015.10.23更改内容1、完善锡珠判定基准2、增加P板起泡分层、破损基准3、增加焊盘漏铜的判定基准4、增加针孔、拉尖的判定基准新增B2变 更 记 录更改后版本欧庭武滕达云A1编制审核版本发行日期质量部会签制造部会签ZB220588-DK电子车间龚华厚李建华卧龙电气集团 控制器事业部 SMT焊接检查规范发行编号接收部门B2 2015.10.231、片式元件侧面偏移标准:无侧面偏移允收:侧面偏移(A)小于或等于元件可焊端宽度(W)的1/3或焊盘宽度(P)的1/3,取其中较小者拒收:侧面偏移(A)大于元件可焊端宽度(W)的1/3或焊盘宽度(P)的1/3,取其中较小者P允收标准拒收拒收拒收标准:无纵向偏移允收:元件可焊端没有偏出焊盘,可焊端与焊盘的重叠部份清析可见。
拒收:可焊端偏出焊盘3、片式元件焊点宽度标准:末端焊点宽度大于或等于元件可焊端宽度或焊盘宽度,取其中较小者。
允收:末端焊点宽度(C)至少为元件可焊端宽(W)的75%或焊盘宽度(P)的75%,取其中较小者。
拒收:小于允收的末端焊点宽度。
2、片式元件纵向偏移标准拒收标准允收拒收允收4、片式元件焊点长度允收:焊点长度D大于元件可焊端长度R的75%或焊盘长度S的75%,取其中较小者。
拒收:焊点长度D小于元件可焊端长度R的75%或焊盘长度S的75%,取其中较小者。
5、片式元件与柱形元件焊点高度标准:焊点高度等于焊锡厚度加元件可焊端的高度。
允收:焊点高度F大于等于焊锡高度G加上可焊端高度H的25%或焊锡厚度G加0.5mm,取其中较小者。
允收:焊点高度延伸至可焊端金属体的顶部拒收:焊锡延伸至元件体的顶部拒收:焊点高度F小于锡锡高度G加可焊端高度H的25%或焊锡高度G加0.5mm,取其中较小者。
6、片式元件侧立拒收:贴片部品不可坚装 贴片部品不可侧装7、片式元件反白拒收:电阻元件不可反白8、片式元件立碑拒收:元件一端翘起9、元件漏贴、贴错、多贴拒收:不得有元件漏贴、脱落、错贴、多贴10、柱形元件侧面偏移允收:侧面偏移A小于或等于元件直径W 的25%或焊盘宽度P的25%,取其中较小者。
元器件焊接质量检验规范
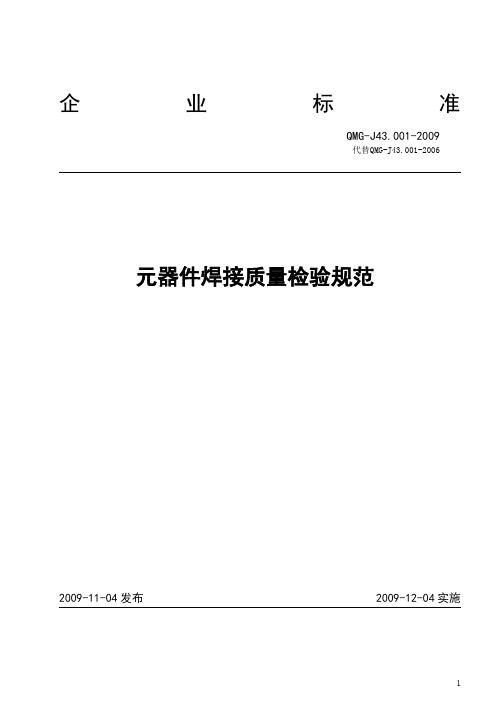
`
企
业
标
准
QMG-J43.001-2009
代替QMG-J43.001-2006
完整word版)电子元器件检验标准

完整word版)电子元器件检验标准目测、量测、比对、实物装配验证等。
三、差异检验项目差异检验项目清单中列出的部件,需按照规定的检验方法进行检验。
未列出的部件,按照通用检验项目执行。
四、不合格品处理4.1不合格品分类不合格品分为三类:重要不合格品、一般不合格品和提示不合格品。
4.2不合格品处理措施4.2.1重要不合格品重要不合格品指会影响产品的功能、可靠性、安全性的不合格品,必须全部退回或报废。
4.2.2一般不合格品一般不合格品指不会影响产品的功能、可靠性、安全性的不合格品,可由供应商改正后再次送检,或由本公司处理后再使用。
4.2.3提示不合格品提示不合格品指不符合技术规范或标准要求,但不影响产品的功能、可靠性、安全性的不合格品,可由供应商改正后再次送检,或在不影响产品质量的前提下使用。
改写:电子元器件来料检验标准文件编号:SW/QC-2015-2015-11-30A/0生效日期:2015年11月30日版本/版次:0页码/页数:第1页/共6页一、适用范围及检验方案1、适用范围本检验标准适用于PCBA上的贴片件或接插件。
具体下表清单列出了电子元器件的名称和序号。
2、检验方案2.1每批来料的抽检量(n)为5只,接收质量限(AQL)为:CR与MA=0,MI=(1,2)。
当来料少于5只时,则全检,且接收质量限CR、MA与MI=0.2.2来料检验项目=通用检验项目+差异检验项目。
差异检验项目清单中未列出的部件,按通用检验项目执行。
二、通用检验项目序号检验项目规格型号标准要求1 检查型号规格是否符合要求(送货单、实物、BOM表三者上的信息必须一致)2 包装检查包装是否符合要求(有防静电要求的必须有防静电袋/盒等包装,易碎易损的必须用专用包装或气泡棉包装等)3 外观外包装必须有清晰、准确的标识,明确标明产品名称、规格/型号、数量等。
或内有分包装则其上必须有型号与数量等标识。
4 贴片件盘料或带盘包装时,不应有少料、翻面、反向等。
直插元器件插装焊接检验标准

锡坑 锡尖
1、锡点表面不允许有 肉眼看见的锡坑
2、在焊盘的柱面内不 允许有高度≥1.0mm 的锡尖 3、超出焊盘柱面与邻 近焊盘或线路之间的锡 尖长度≤1/4空间距离 3.2.6 板面不允许有碎锡块等 碎锡 导电物不论是固定的或 是流动 固定的且不跨越线路 并没有导致短路可能的 流动的
MI 1.0mm MI
3、铝电解电容的外封 装塑料皮侧面不允许破 裂,顶面允许部分暴露 但暴露部分≤90%D D -- 电容的外直径 4、IC及三极管类的外 壳不允许有破裂或其它 明显的伤损
D MI
0 1
MA
5、连接插座(头)不 允许有外壳破伤现象
MA
插座内金属插针: a、簧片式不允许有扭 曲、陷进或高出绝缘体 固定槽等现象 b、直针式不允许有插 针高低不平、弯曲、针 体锈斑及损伤等现象 C、带绝缘皮的导线不 允许绝缘皮破伤
DXC通信
文件编号:
PG/QC-7.5-01
QA检验规范
成品检验
版 本 号: A 本页修改序号:00 页 码: 24外观检验
3.1 元器件自身外观检查 序号 项目 标准要求 1、元件引脚允许有轻 3.1.1 损伤 微变形、压痕及损伤, 但不可有内部金属暴露 损伤长度≤1/4D D -- 引脚的直径 2、玻璃管型元件不可 有外壳破裂现象
3.2.2
2、小于20%的焊盘不上 不上锡 锡,但在脚的周围360° 范围有锡均匀覆盖着 少锡 焊盘
MI
3、超过20%的焊盘不上 锡且在脚的周围360° 范围没有完全被锡覆盖
MA
4、双面板板面元件孔 上锡高度≤75%
MI
DXC通信
文件编号:
PG/QC-7.5-01
QA检验规范
成品检验
电子元器件贴片及其接插件焊接检验规范标准
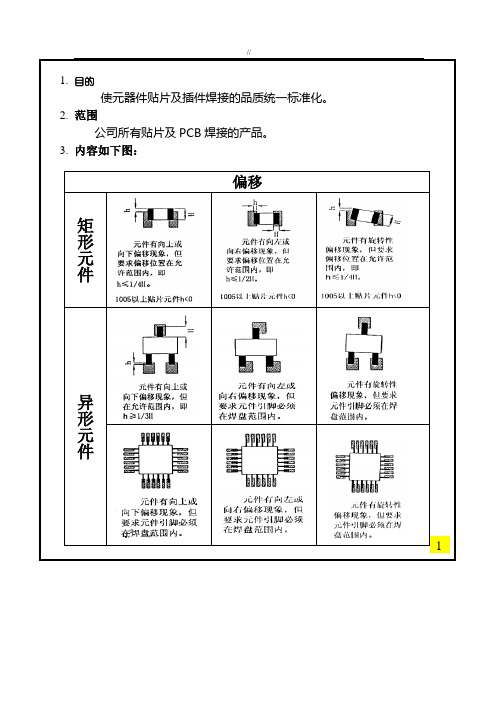
2 1贴片焊接包焊拉尖沾胶焊锡量明显太多,超出焊盘范围,且高出元件焊端。
焊接有拉尖现象。
焊盘有沾胶现象,但必须在规定范围内:h1≤0.2mm h ≤1/4H焊锡量明显太多,超出焊盘范围,且高出元件焊端。
焊接有拉尖现象。
少锡0805以下贴片矩形元件h<1/3H 判定为少锡. 1005贴片矩形元件h <1/4H 判定为少锡.H >2mm 以上贴片矩形元件 .h <0.5mm 判定为少锡.45678 电路板对应丝印识别:电路板焊接一、焊接流程1、焊接开始前,整理好桌面及周边环境,为电路焊接工作准备一个有条理、整洁的环境。
2、仓库领料,并依据元件明细表核对物料,确保物料正确无误,遇到生疏元件及时向相关负责人询问。
3、依据元件明细表进行电路板焊接。
4、电路板焊接完成后,依据元件明细表核对元件,以保证无错焊、虚焊、漏焊、假焊、桥接。
特别是确认多引脚元件和有极性元件焊接正确。
同样重要的是检查和优化焊点,一块合格的电路板是焊点光滑、过渡均匀、无毛刺、元件排列整齐美观。
二、对焊接点的基本要求1、焊点要有足够的机械强度,保证被焊件在受振动或冲击时不致脱落、松动。
不能用过多焊料堆积,这样容易造成虚焊、焊点与焊点的短路。
2、焊接可靠,具有良好导电性,必须防止虚焊。
虚焊是指焊料与被焊件表面没有形成合金结构。
只是简单地依附在被焊金属表面上。
3、焊点表面要光滑、清洁,焊点表面应有良好光泽,不应有毛刺、空隙,无污垢,尤其是焊剂的有害残留物质,要选择合适的焊料与焊剂。
三、焊接技术1、手工焊接的基本操作方法①焊前准备,准备好电烙铁以及镊子、剪刀、斜口钳、尖嘴钳、焊料、焊剂(我们这里是指焊锡丝,以下通指焊锡丝)等工具,将电烙铁及焊件搪锡,左手握焊料,右手握电烙铁,保持随时可焊状态。
②用烙铁加热备焊件。
③送入焊料,熔化适量焊料。
④移开焊料,当焊料流动覆盖焊接点,迅速移开电烙铁。
2、电子元器件焊接的顺序是由小到大,由低到高3、元器件焊接注意事项:1)批量将同侧的一端焊盘镀上适量焊锡(仅适用于贴装元器件)。
07.焊接检验规范-A1-1017
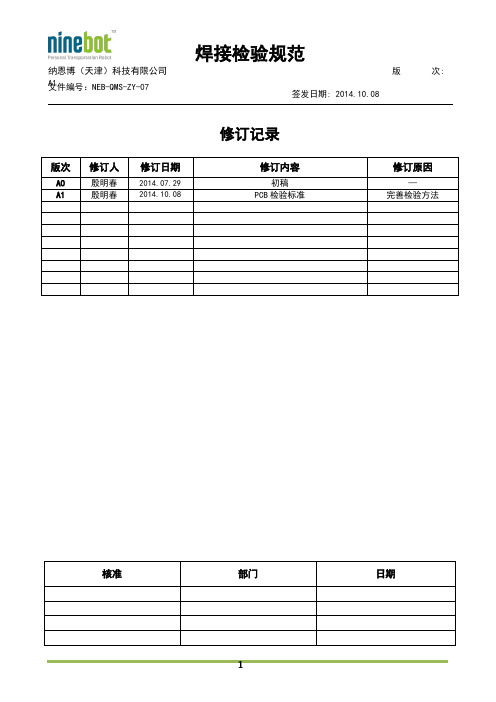
A1文件编号:NEB-QMS-ZY-07签发日期: 2014.10.08修订记录版次修订人修订日期修订内容修订原因A0 殷明春2014.07.29 初稿—A1 殷明春2014.10.08PCB检验标准完善检验方法核准部门日期A1文件编号:NEB-QMS-ZY-07签发日期: 2014.10.08产品信息:部件名称:V6 Charger Connector 中文名称:充电器接口印制板修订版本:A1 修订时间:2014.10.08 修订内容:焊接工艺说明和控制要点焊接工艺说明:1、元器件方向与印制板丝印方向对应;2、焊接完成后管脚焊点饱满,无虚焊、漏焊、连焊的现象;3、直插件、贴片件焊接完成后器件无浮高;4、焊接件歪斜程度零件本体不可超出位置框,零件管脚不可超出焊盘;5、直插件平面焊锡高度不得小于过孔直径的1/3;6、PCB板表面清洁不得有助焊剂、锡球、灰尘等污物。
充电借口板正面图示控制要点:1、无线接收模块焊接时需要检查管脚有无氧化发黑现象,接收模块上是否有连焊,空焊。
2、FFC管脚容易虚焊,焊接时要求管脚透锡不低于80%。
部件名称:V6 Foot Switch 中文名称:脚踏开关印制板修订版本:A1 修订时间:2014.10.08 修订内容:焊接工艺说明和控制要点A1签发日期: 2014.10.08 文件编号:NEB-QMS-ZY-07焊接工艺说明:1、元器件方向与印制板丝印方向对应;2、焊接完成后管脚焊点饱满,无虚焊、漏焊、连焊的现象;3、直插件焊接完成后器件无浮高,器件管脚需剪短,外露管脚长度小于1mm ;4、P1位置线序不可焊错;5、PCB控制要点:1、白色3P 信号线红线对应P1位置;2、焊接红外检测开关时要注意管脚有无发黑氧化现象;3、焊接白色3P 信号线时要检查信号线有无漏铜、线序错;4、PCB 表面无划伤,无漏铜。
产品信息:部件名称: V6 LED Pad中文名称: 中舱LED 灯板 修订版本: A1修订时间: 2014.10.08修订内容:焊接工艺说明焊接工艺说明:红外检测开关 白色3P 信号线A1文件编号:NEB-QMS-ZY-07签发日期: 2014.10.081、元器件方向与印制板丝印方向对应;2、焊接完成后管脚焊点饱满,无虚焊、漏焊、连焊的现象;3、焊接件歪斜程度零件本体不可超出位置框,零件管脚不可超出焊盘;4、PCB板表面清洁不得有助焊剂、锡球、灰尘等污物。
电子元器件安装及焊接工艺设计规范方案精选全文

可编辑修改精选全文完整版电子元器件安装与焊接工艺规范电子元器件安装与焊接工艺规范1范围本规范规定了设备电气盒制作过程中手工焊接技术要求、工艺方法和质量检验要求. 2引用标准以下文件中的有关条款通过引用而成为本规范的条款.凡注日期或版次的引用文件,其后的任何修改单<不包括勘误的内容>或修订版本都不适用于本规范,但提倡使用本规范的各方探讨试用其最新版本的可能性.凡未注日期或版次引用文件,其最新版本适用于本规范.HB 7262.1-1995 航空产品电装工艺电子元器的安装HB 7262.2-1995 航空产品电装工艺电子元器的焊接QJ 3117-1999 航天电子电气产品手工焊接工艺技术要求IPC-A-610E-2010 电子组件的可接收性3技术要求与质量保证3.1一般要求3.1.1参加产品安装和检验的人员必须是经过培训合格的人员.环境温度要求:20℃-30℃.相对湿度要求:30%-75%.照明光照度要求:工作台面不低于500lx.工作场地应无灰尘,及时清除杂物<如污、油脂、导线头、绝缘体碎屑等>工作区域不得洒水.3.2安装前准备把安装所用的器材备齐,并放在适当位置,以便使用;所有工具可正常使用,无油脂,按以下要求检查工具:切割工具刃口锋利,能切出整齐的切口;绝缘层和屏蔽剥离工具功能良好.按配套明细表检查和清点元器件、印制板、紧固件、零件等的型号规格及数量.凡油封的零件或部件,在安装前均应进行清洗除油,并防止已除过的零件再次糟受污染.4元器件在印制板上安装4.1元器件准备4.1.1安装前操作人员应按产品工艺文件检查待装的各种元器件、零件及印制板的外观质量.4.1.2元器件引线按以下要求进行了清洁处理:a、用织物清线器轻轻地擦拭引线,除去引线上的氧化层.有镀层的引线不用织物清线器处理;b、清洁后的引线不能用裸手触摸;c、用照明<CDD>放大镜检验元器件引线清洁质量.4.2元器件成型须知a、成型工具必须表面光滑,夹口平整圆滑,以免损伤元器件;b、成型时,不应使元器件本体产生破裂,密封损坏或开裂,也不应使引线与元器件内部连接断开;c、当弯曲或切割引线时,应固定住元器件引线根部,防止产生轴向应力,损坏引线根部或元器件内部连接;d、应尽量对称成型,在同一点上只能弯曲一次;e、元器件成型方向应使元器件装在印制板上后标记明显可见;f、不允许用接长元器件引线的办法进行成型;g、不得弯曲继电器、插头座等元器件的引线.4.3元器件成型要求4.3.1轴向引线元器件引线弯曲部分不能延长到元器件本体或引线根部,弯曲半径应大于引线厚度或引线直径;见图1:图1 轴向引线元器件引脚折弯要求水平安装的元器件应有应力释放措施,每个释放弯头半径R至少为0.75mm,但不得小于引线直径.图2 元器件应力释放弯头处理要求4.3.2径向引线元器件反向安装径向引线元器件成型要求见图3:图3 径向引线元器件弯角要求4.3.3扁平封装元器件引线成型时就有防震或防应力的专门工具保护引线和壳体封接;用工具挪动扁平组件时,只允许金属工具与外壳接触;装配扁平组件时,工作台面上应垫有弹性材料.4.3.4用圆嘴钳弯曲元器件引线的方法如下:a、将成型工具夹持住元器件终端封接处到弯曲起点之间的一点上;b、逐渐弯曲元器件引线.图44.4元器件在印制板上安装的一般要求4.4.1按装配工序,将盛开好的元器件由小到大依次安装,先安装一般元器件最后再安装电敏感元器件.4.4.2当具有金属外壳的元器件需要跨接印制导线安装时,必须采取良好的绝缘措施.4.4.3安装元器件时,不应使元器件阻挡金属化孔.4.4.4质量较重的元器件应平贴在印制板上,并加套箍或用胶粘接.4.5元器件在印制板上的安装形式4.5.1贴板安装元器件与印制板安装间隙小于1mm,当元器件为金属外壳面安装面又有印制导线时,应加绝缘衬垫或绝缘管套,如图5:图5 贴板安装要求4.5.2悬空安装元器件与印制安装距离一般为3~5mm,如图6.该形式适用发热元器件的安装.图6 悬空安装要求4.5.3垂直安装元器件轴线相对于印制板平面的夹角为90°±10°,见图7.该形式适用于安装密度高的印制板俣不适用于较重的细引线的元器件.图7 元器件垂直安装要求4.5.4支架固定安装用金属支架将元器件固定在印制板上见图8:图8 元器件支架安装要求4.5.5粘接和绑扎安装对防震要求较高的元器件,巾板安装后,可用粘合剂将元器件与印制板粘接在一起,也可以用绵丝绑扎在印制板上,见图9:图9 元器件绑线安装要求4.5.6反向埋头安装反向埋头安装形式见图10:图10 元器件反向埋头安装要求4.5.7接线端子和空心铆钉的安装4.5.7.1接线端子和空心铆钉的安装要求如下:a、安装接线端子和空心铆钉时应满足正常指力下,既不转动,也不轴向移动,没有缺损或印制板基材脱落现象;b、接线端子杆不得打孔、切口、切缝和其它间断点,以免焊料和焊剂漏入孔内;c、铆接后的接线端子或空心铆钉不得有切口、切缝和其它间断点,铆接事,铆接面周围的豁口或裂缝小于90角分开,且延伸不超过铆接面时,允许有三个弧状豁口或裂缝;d、接线端子应垂直安装于印制板,倾斜角应不大于5°.4.5.7.2按以下步骤安装接线端子和空心铆钉:a、将印制板置于夹具上,将清洁的接线端子或空心铆钉从印制板的元件面插入相应的孔内,将印制板翻转,翻转时,接线端子或空心铆钉应紧靠住底板;b、用铆接器<铆压工装>接线端子或空心铆钉铆接到印制板上,应控制好压力.4.6焊接面上元器件引线处理4.6.1弯曲元器件引线焊接面上元器件引线可采用全弯曲、部分弯曲和直插式.a、全弯曲引线:引线弯曲后,引线端与印制板垂线的夹角在75°~90°之间;b、部分弯曲:引线弯曲后,引线端与印制板垂线的夹角在15°~75°之间,见下图,引线伸出长度为0.5mm~1.5mm;c、直插引线:引线端与印制板垂线的夹角在0°~15°之间,见图11,引线伸出长度为0.5mm~1.5mm.图11 焊接面元器件引脚处理要求全弯曲引线一般要求:a、引线弯曲部分的长底不得短于焊盘最大尺寸的一半或0.8mm,但不大于焊盘的直径<或长度>;b、向印制导线方向弯曲引线;c、引线全弯曲后与印制板平面允许的最大回弹角为15°;d、引线弯曲后相邻元器件的间隙不小于0.4mm;e、不许弯曲硬引线继电器、电连接器插针或工艺文件规定的其它元器件引线.4.6.2切割引线用切割器切除引线,不许损坏印制制导线;不许切割直插式集成电路、硬引线继电器插针或工艺文件规定的其它元器件引线.4.6.3固定引线用玻璃纤维焊接工具压倒已切割过的引线.4.7各类元器件在印制板上的安装4.7.1轴向引线元器件安装a、轴向引线元器件应按工艺文件规定进行近似平行安装;b、将引线穿过通孔,弯曲并焊到印制板的焊盘上.弯曲部分应满足要求.4.7.2径向引线元器件安装4.7.2.1金属壳封装的元器件反向埋头安装要求见条的要求.4.7.2.2伸出引线的基面应平行于印制板的表面,且有一定的间隙.4.7.2.3引线应从元器件的基点平直地延长,引线的弯头不应延伸到元件的本体或焊点处.4.7.2.4当元器件每根引线承重小于3.5g时,元器件可不加支撑面独立安装,此时,元器件的基面和印制板表面间距为1.3mm~2.5mm.基准面应平行印制板表面,倾斜角在10度以内.4.7.2.5当元器件每根引线承重大于3.5g时,元器件基面将平行于印制板表面安装,元器件应以以下方式加支撑:a、元器件本身所具备的弱性支脚或支座,与元器件形成一个整体与底板相接;b、采用弹性或非弹性带脚支架装置,支座不堵塞金属化孔,也不与印制板上的元器件内连;c、当弹性支座或非弹性带脚支座的元器件安装到印制板时,元器件每个支脚都应与印制板相连,支脚的最小高度为0.25mm,当使用一个分离式弹性支座或分离式弹性无脚支座时,元器件基面与印制板表面平行安装的要求, 使用非弹性支座连接元器件基面并平行安装于印制板表面时,则基面应与支座完全接触,支脚应与印制板完全接触.4.7.2.6侧面或端部安装的元器件应与印制板粘接或固定住,以防因冲击或震动而松动.4.7.2.7引线带有金属涂层的元器件安装,涂层与印制板表面焊盘处距离不得小于0.25mm.禁止修整引线涂层.4.7.3双引线元器件安装要求:距印制板表面最近的元器件本体边缘与印制板表的平行角度在10度以内,且与印制板间距在1.0mm~2.3mm以内,元器件与印制板垂线成最大角度为±15°.4.7.4扁平封装元器件安装扁平封装元器件的安装要求见条.4.7.5双列直插式集成电路的安装双列直插式元器件基面应与印制板表面隔开,其间距为0.5mm~1mm或引线的凸台高度.4.8焊接方法4.8.1单面印制板的焊接图12 单面印制板的焊接4.8.2金属化孔双面印制板的焊接金属化孔双面印制板的焊接应符合图要求.对有引线或导线插入的金属孔,通孔就充填焊料,焊料应从印制电路板一侧连续流到另一侧的元器件面,并覆盖焊盘面积90%以上,焊料允许凹缩进孔内,凹缩量如图13:图13 元器件在金属化孔双面印制板上的焊接4.8.3多层印制板的焊接多层印制板的焊接应符合图14要求.严禁两面焊接以防金属化孔内出现焊接不良.图14 元器件在多层印制板上的焊接4.8.4扁平封装集成电路的焊接采用对角线焊接方法,并符合以下规定:扁平应沿印制导线平直焊接,元器件引线与印制板的焊盘应匹配;引线最小焊接长度为1.5mm且引线在焊盘中间;元器件的型号规格标识必须在正面,严禁反装;扁平封装集成电路未使用的引线应焊接在相应的印制导线上;焊点处引线轮廓可见.图15 扁平封装元器件的焊接4.8.5断电器的焊接焊接时非密封继电器应防止焊济、焊料渗入继电器内部,在接线端子之间应塞满条形吸水纸带,焊接时继电器焊接面倾斜不大于90°.焊接密封继电器时,要防止接线端子根部绝缘子受热破裂,可用蘸乙醇的棉球在绝缘子周围帮助散热.4.8.6开关元器件的焊接焊接时可采用接点交叉焊接的方法,使加热温度分散,减少损坏.5元器件焊接判定标准元器件焊接质量判定可根据附表1~附表16内的图示.附表 2 有引脚的支撑孔-焊接主面目标 可接受不可接受和孔壁润湿角=360° 焊锡润湿覆盖率=100%•引脚和孔壁润湿角≥270° •焊盘焊锡润湿覆盖率≥0•引脚和孔壁润湿角<270°附表3 有引脚的支撑孔-焊接辅面目标可接受不可接受和孔壁润湿角=360° 焊锡润湿覆盖率=100%•引脚和孔壁润湿角≥330° •焊盘焊锡润湿覆盖率≥75%•引脚和孔壁润湿角<330° •焊盘焊锡润湿覆盖率<75%附表4 焊点状况目标可接受不可接受附表1 焊点润湿目标可接受不可接受1焊点表层总体呈现光滑和与焊接零件由良好润湿;部件的轮廓容易分辨;焊接部件的焊点有顺畅连接的边缘;2表层形状呈凹面状.可接受的焊点必须是焊接与待焊接表面,形成一个小于或等于90度的连接角时能明确表现出浸润和粘附,当焊锡量过多导致蔓延出焊盘或阻焊层的轮廓时除外.1不润湿,导致焊点形成表面的球状或珠粒状物,颇似蜡层面上的水珠;表面凸状,无顺畅连接的边缘;2移位焊点; 3虚焊点.洞区域或表面瑕疵;和焊盘润湿良好;形状可辨识;周围100%有焊锡覆盖;覆盖引脚,在焊盘或导薄而顺畅的边缘. •焊点表层是凹面的、润湿良好的焊点内引脚形状可以辨识.•焊点表面凸面,焊锡过多导致引脚形状不可辨识,但从主面可以确认引脚位于通孔中;•由于引脚弯曲导致引脚形状不可辨识.附表5 有引脚的支撑孔-垂直填充目标可接受不可接受润湿角度=360°焊锡润湿覆盖率=100% •周边润湿角度≥330°•焊盘焊锡润湿覆盖率≥75%•周边润湿角度<330°•焊盘焊锡润湿覆盖率<75% 附表6 焊接异常-暴露基底金属目标可接受不可接受露基底金属·基底金属暴露于:a〔导体的垂直面b〔元件引脚或导线的剪切端c〔有机可焊保护剂覆盖的盘·不要求焊料填充的区域露出表面涂敷层·元件引脚/导体或盘表面由于刻痕、划伤或其它情况形成的基底金属暴露不能超过对导体和焊盘的要求附表7 焊接异常-针孔/吹孔目标可接受不可接受良好、无吹孔·润湿良好、无吹孔·针孔/吹孔/空洞等使焊接特性降低到最低要求以下附表8 焊接异常-焊锡过量-锡桥目标可接受不可接受·**桥·横跨在不应相连的两导体上的焊料连接·焊料跨接到非毗邻的非共接导体或元件上附表9 焊接异常-焊锡过量-锡球目标可接受不可接受现象·锡球被裹挟/包封,不违反最小电气间隙注:锡球被裹挟/包封连接意指产品的正常工作环境不会引起锡球移动·锡球未被裹挟/包封·锡球违反最小电气间隙附表10 引脚折弯处的焊锡目标可接受不可接受折弯处无焊锡·引脚折弯处的焊锡不接触元件体·引脚折弯处的焊锡接触元件体或密封端附表11 焊接异常-反润湿目标可接受不可接受良好、无反润湿现象·润湿良好、无反润湿现象·反润湿现象导致焊接不满足表面贴装或通孔插装的焊料填充要求附表12 焊接异常-焊料受拢目标可接受不可接受料受拢·无焊料受拢·因连接产生移动而形成的受拢焊点,其特征表力纹附表13 焊接异常-焊料破裂目标可接受不可接受料破裂·无焊料破裂·焊料破裂或有裂纹附表14 焊接异常-锡尖目标可接受不可接受圆润饱满没有锡尖·焊锡圆润饱满没有锡尖·锡尖违反组装的最大高度要求或引脚凸出要求1.5毫米·锡尖违反最小电气间隙附表15 镀金插头目标可接受不可接受插头上无焊锡·镀金插头上无焊锡·在镀金插头的实际连接区域有焊锡、合金以外其它金属附表16 焊接后的引脚剪切目标可接受不可接受·引脚和焊点无破裂·引脚凸出符合规范要求·引脚和焊点无破裂·引脚凸出符合规范要求·引脚与焊点间破裂。
焊接检验标准及元器件推力标准

1.0 目的本标准建立目的在于控制表面贴装的印刷电路板及提供器件脚成型、点焊的电路板的外观,以确保产品品质达到规定要求。
2.0 参考文件1.GB2828-2003抽样程序3.0 AQL标准MA : 2.5 MI : 4.0主缺:可能会引起产品预定用途的失效或降低其本质上的可用性(功能、性能不良)次缺:与已建立的标准有背离却又对产品单元的有效作用或操作几乎无影响(外观不良)4.0 适用范围适用于各类SMT焊接及插件类器件焊接后的半成品及进料检验的质量控制。
5.0 使用工具5.1 游标卡尺5.2 放大镜5.3 塞规6.0 注意事项1.检查时必须正确佩带静电手环。
2.必须佩带手套或指套。
3.PCBA必须放置于有良好照明的工作台上,从距离30cm处以45度目视7.0 检查项目(见下页)7.1 贴片类元器件检验标准序号检查项目缺陷定义描述及图示参考图示PCB板上应有的器件而没有的。
漏打零件1 缺件不合格图示合格图示多一顆零件不合格图示101错误不合格图示102正确合格图示器件浮起>0.3 mm,不允许;器件一端倾斜>0.3 mm0.3mm 0.3mm<03mm不合格图示合格图示不合格图示合格图示不合格图示合格图示器件脚与锡未完全融合。
不合格图示合格图示不合格图示应导通而未导通的。
不合格图示缺陷定义描述及图示不合格图示以器件脚的宽度为准,偏移不可0.1mm0.3mm不合格图示不合格图示合格图示<1/2W<1/2W不合格图示合格图示焊点四周及PCB板面上不得有锡球或其他焊锡残渣等。
不合格图示合格图示不合格图示单面不允许>0.5mm,不合格图示19 极性反正负极性反向。
正确++错误黑线是负极不合格图示黑线是负极合格图示7.2插件类元器件检验标准序号检查项目缺陷定义描述及图示参考图示1 缺件应有器件而没有器件的。
缺件L8L8不合格图示合格图示2 多件不需要器件而有器件的。
L8正确L8多余不合格图示合格图示序号检查项目缺陷定义描述及图示参考图示3 错件不符合BOM料号要求或放错位置。
pcb焊接质量判定标准

PCB焊接质量判定标准在电子行业中,PCB(Printed Circuit Board)焊接质量对于产品的稳定性和可靠性具有重要影响。
本文将详细介绍PCB焊接质量判定标准,主要包括偏位、少锡、浮高、锡珠、外观和物理测试等方面。
1. 偏位定义:焊接完成后,元器件位置偏移。
判定标准:可以通过目视或使用工具进行测量。
焊接位置应与PCB板上的标记对齐,不得出现明显的偏移。
2. 少锡定义:焊接过程中,焊盘或电路板表面氧化或损伤,导致焊接不完整。
判定标准:用手触摸或使用工具测量焊接面积和重量。
焊接面积应足够,焊接点应牢固,无虚焊、漏焊等现象。
3. 浮高定义:元器件顶端高度超出电路板平面。
判定标准:使用工具测量浮高值是否超出允许范围。
一般情况下,元器件高度应控制在一定范围内,不得高于电路板平面。
4. 锡珠定义:焊接过程中,焊盘或电路板表面氧化或损伤,导致锡珠形成。
判定标准:通过目视或使用工具进行测量,观察是否符合要求。
锡珠应无裂缝、无气泡,大小均匀,不得影响元器件的连接和电路的正常工作。
5. 外观定义:焊接完成后,电路板和元器件的外观表现。
判定标准:应符合公司品控要求,保持美观整齐。
焊点应圆润、光亮,无毛刺、尖角等现象。
6. 物理测试定义:通过一系列物理测试,检验焊接质量的稳定性、耐用性等。
判定标准:应符合公司品控要求,达到指定寿命。
常见的物理测试包括拉力测试、扭力测试、耐高温测试等。
焊接点应能承受一定的拉力、扭力和高温,以保证产品的稳定性和可靠性。
总为了保证PCB焊接质量,我们需要严格控制各个方面的标准。
从偏位、少锡、浮高到锡珠和外观,都需要密切关注并按照规定进行检测。
此外,通过物理测试的严格把控,确保焊接质量的稳定性和耐用性。
只有经过所有这些环节的严格把关,才能生产出高质量的PCB 焊接产品,满足客户的需求和市场的品质要求。
- 1、下载文档前请自行甄别文档内容的完整性,平台不提供额外的编辑、内容补充、找答案等附加服务。
- 2、"仅部分预览"的文档,不可在线预览部分如存在完整性等问题,可反馈申请退款(可完整预览的文档不适用该条件!)。
- 3、如文档侵犯您的权益,请联系客服反馈,我们会尽快为您处理(人工客服工作时间:9:00-18:30)。
美的家用空调国内事业部企业标准元器件焊接质量检验规范1适用范围本规定采用电烙铁手工锡焊的焊接质量检验规范和基本要求,适用于电子整机生产和检验。
不适合于机械五金结构件和电器的特种焊接。
本规范适用于美的家用空调国内事业部。
3.2连焊:两个或以上的不同电位的相互独立的焊点,被连接在一起的现象;2009-04-07发布2009-04-10实施美的集团家用空调国内事业部发布3.3空焊:元件的铜箔焊盘无锡沾连;3.4冷焊:因温度不够造成的表面焊接现象,无金属光泽;3.5虚焊:表面形成完整的焊盘但实质因元件脚氧化等原因造成的焊接不良;3.6包焊:过多焊锡导致无法看见元件脚,甚至连元件脚的棱角都看不到;3.7锡珠,锡渣:未融合在焊点的焊锡残渣。
3.8锡尖:指在组装板经过波峰焊后,板子焊锡面上或元件引脚端部所出现的尖锥状的焊锡。
3.9脱焊:由于受外力等因素导致已焊接好的焊点端部焊锡与焊盘部分或完全脱离。
4合格性判断:4.1本标准执行中,分为三种判断状态:“最佳”、“合格”和“不合格”。
4.1.1最佳——它是一种理想化状态,并非总能达到,也不要求必须达到。
但它是工艺部门追求的目标。
4.1.2合格——它不一定是最佳的,但在其使用环境下能保持PCBA的完整性和可靠性。
(为允许工艺上的某些更改,合格要求要比最终产品的最低要求稍高些)4.1.3不合格——它不足以保证PCBA在最终使用环境下的形状、配合及功能要求。
应根据工艺要求对其进行处置(返工、修理或报废)。
4.2焊接可接受性要求:所有焊点应当有光亮的,大致光滑的外观,并且呈润湿状态;润湿体现在被焊件之间的焊料呈凹的弯月面,对焊点的执锡(返工)应小心,以避免引起更多的问题(锡珠、包焊等故障),而且应产生满足验收标准的焊点。
4.2.1可靠的电气连接;4.2.2足够的机械强度;4.2.3洁整齐的外观。
焊点分析图5焊接检验规范:5.1连焊:相邻焊点之间的焊料连接在一起,形成桥连(图1)。
在不同电位线路上,桥连不可接受;在相同电位线路上,可有条件接受连锡,对于贴片元件,同一铜箔间的连锡高度应低于贴片元件本体高度。
图15.2虚焊:元器件引脚未被焊锡润湿,引脚与焊料的润湿角大于90o(图2);焊盘未被焊锡润湿,焊盘与焊料的润湿角大于90o(图3)。
以上二种情况均不可接受。
图2 图3合格合格不合格不合格5.3空焊:基材元器件插入孔全部露出,元器件引脚及焊盘未被焊料润湿(图4)。
不可接受。
图45.4半焊:元器件引脚及焊盘已润湿,但焊盘上焊料覆盖分部1/2,插入孔仍有部分露出(图5),不可接受。
图55.5多锡:引脚折弯处的焊锡接触元件体或密封端(图6),不可接受。
图65.6包焊:过多焊锡导致无法看见元件脚,甚至连元件脚的棱角都看不到(图7),不可接受。
图75.7锡珠、锡渣:直径大于0.2mm或长度大于0.2mm的锡渣黏在底板的表面上,或焊锡球违反最小电气间隙(图8),均不可接受;每600mm2多于5个直径小于0.2mm的焊锡珠、锡渣不可接受。
图85.8少锡、薄锡:引脚、孔壁和可焊区域焊点润湿小于270o(图9),或焊角未形成弯月形的焊缝角,润湿角小于15o(图11),或焊料未完全润湿双面板的金属孔,焊锡的金属化孔内填充量小于50%(图10、12),或贴片元件焊盘焊锡润湿面积小于85%,均不可接受。
图9 图10图11 图125.9锡尖:元器件引脚头部或电路板的铺锡层有焊锡拉出呈尖形(图13),锡尖高度大于安装高度要求或违反最小电气间隙,均不可接受。
图135.10锡裂:焊点和引脚之间有裂纹(图14),或焊盘与焊点间或焊点本身有裂纹,不可接受。
图145.11针孔/空洞/气孔:焊点内部有针眼或大小不等的孔洞(图15)。
孔直径大于0.2mm;或同一块PCB板直径小于0.2mm的气孔数量超过6个,或同一焊点超过2个气孔均不可接受。
图15注:如果焊点能满足润湿的最低要求,针孔、气孔、吹孔等是允许的。
(制程警示)合格合格合格5.12焊盘起翘:在导线、焊盘与基材之间的分离一个大于焊盘的厚度(图16),不可接受。
图165.13断铜箔:铜箔在电路板中断开,不可接受。
5.14冷焊:焊点表面不光滑,有毛刺或呈颗粒状(图17),不可接受。
图175.15焊料结晶疏松、无光泽,不可接受。
5.16受力元件及强电气件焊锡润湿角小于30o或封样标准,不可接受。
5.17焊点周围存在焊剂残渣和其他杂质,不可接受。
5.18贴片元件:上锡高度不能超过元件本体、没有破裂、裂缝、针孔、连焊等不良现象。
5.18.1片式元件:焊接可靠,横向偏移不能超过可焊宽度的50%;纵向偏移不能超过可焊宽度的25%可焊宽度指元件可焊端和焊盘两者之间的较小者。
见下图。
图185.18.2圆柱体元件:焊接可靠,横向偏移不能超过元件直径和焊盘宽度中较小者的50%,纵向偏移不能超过元件直径和焊盘宽度中较小者的25%,横面和侧面焊接宽度至少为可焊宽度的50%,见下图。
图195.19IC:依据管脚的形状对应片式元件的要求来检验。
其中IC管脚偏移不超过可焊宽度1/3,见下图。
图205.20功率器件,包括7805、7812、1/2W以上电阻、保险丝、可控硅、压缩机继电器,焊点高度应于1mm,焊点应饱满,不允许焊点有空缺的地方。
5.21对于交流电磁继电器,单插片、强电接插件及大功率电容等受外力器件,要求能承受10公斤拉(压)纵向力不会脱焊,裂锡和起铜皮现象。
5.22拨动检查:目视检查时发现可疑现象可用镊子轻轻拨动焊位确认。
5.23电路板铺锡层、上锡线厚度要求在0.1mm-0.8mm。
应平整,无毛边,不可有麻点﹑露铜﹑色差﹑孔破﹑凹凸不平之现象,不可有遗漏未铺上之不正常现象。
5.24贴片电路板的焊盘部分不可有遗漏未铺锡、露铜现象。
5.25板底元件脚要求清晰可见,长度在不违反最小电气间隙、不影响装配的条件下,在1.0mm-2.8mm范围内可接受;强电部分引脚直径大于或等于0.8mm,在不影响电气可靠性的情况下可放宽到3.1mm;5.26焊接后元器件浮高与倾斜判定5.26.1受力元件(插座、按钮、交流电磁继电器、风机电容、插片、互感器、散热片及发光二极管)、大元器件浮高不能超过板面0.8mm,见下图;图215.27非受力器件(直流电磁继电器、跳线、非浮高电阻、二极管、色环电感、连接线等)浮高在不违反最小电气间隙、不影响装配的条件下不能大于2mm,元器件装配焊接判定:6无铅焊与有铅焊元器件焊点检验规范一些区别:6.1.1无铅焊由于其焊点湿润性差,焊点四周容易产生一些微小裂缝。
6.1.2无铅焊接其焊接温度较高,在温度过高时容易产生过热焊接,焊点周围有一层明显的氧化现象,见图22。
图227PCBA检验过程注意项:7.1检验前需先确认所使用的工作平台清洁;7.2ESD防护:凡接触PCBA半成品必需配带良好静电防护措施﹝配带防静电手环接上静电接地线或防静电手套,具体参照工厂防静电工艺规范﹞;7.3要握持板边或板角执行检验,不允许直接抓握线路板上线组和元器件;7.4检验条件: 室内照明 800LUX(流明)以上,即40W日光灯下,离眼睛距离30CM左右,必要时以(五倍以上)放大照灯检验确认;7.4.1PCB分层/起泡: 不可有PCB分层( DELAMINATION )/起泡( BLISTER );7.4.2弯曲: PCB板弯或板翘不超过长边的%,此标准使用于组装成品板;7.4.3刮伤: 刮伤深至PCB纤维层不被允收,刮伤深至PCB线路露铜不被允收。
7.5连接插座、线组或插针: 倾斜不得触及其它零件,倾斜高度小于0.8mm与插针倾斜小于 8度内 (与 PCB 零件面垂直线之倾斜角),允许接收。
7.6带有IC插座的主IC: 主IC插入插座时,力度应均匀,与插座之间保持良好接触,且间隙均匀一致,不可出现左右前后间隙大小不一,出现松动等现象;7.7热熔胶7.7.1在工艺文件规定的元器件根部打胶,保证胶与元器件及PCB板充分接触,覆盖根部大于或等于270o,胶不可覆盖需要散热的元器件,如:大功率电阻;7.7.2所有需要连接的元器件部位,不可有多余的热熔胶,影响连接和安装的,不被接受。
7.7.3胶不可堵塞PCB上的爬电间隙孔。
7.7.4为避开爬电间隙孔,在经产品工程师评估无质量隐患前提下可以允许个别位置取消打胶;7.8防潮油、三防漆、高浓度防潮油:扫防潮油、三防漆、高浓度防潮油不可触及轻触开关、插座、连接线组等,如触及,但不属于金属体连接位置且不影响电气通断性能则可以允许接收。
7.9检验标记:合格PCBA的检验标贴上的相应工序必须做检验标记。
本标准由家用空调事业部武汉工厂工程部提出。
本标准由家用空调事业部技术研发中心标准化部归口。
本标准由家用空调事业部武汉工厂工程部负责起草。
本标准主要起草人:姜斐、蒋品强、范兴权。
本标准于2006年9月第一次修订,主要修订人:姜斐、丘稳胜、杨付礼。
本标准于2009年3月第二次修订,主要修订人:刘栋智、章春光。
2006年9月第一次修订说明:增加一些元器件焊接时偏移的尺寸标准,以及配图和检验过程注意项。
并参照IPC-A-610和电子行业焊接质量检验标准,增加焊点润湿质量判断,完善焊点合格性判断定义及可接受性要求;主要对能满足润湿最低要求的针孔、气孔、吹孔焊点合格性重新定义。
杨付礼丘稳胜姜斐 2006年9月7日2009年3月第二次修订说明:增加对锡尖、脱焊的定义,将直流电磁继电器和交流电磁继电器的浮高标准的区分,对少锡、锡裂内容的补充,PCBA检验过程注意项中增加检验标记项目。
刘栋智、章春光 2009年3月。