压力容器厚板设备制造工艺
浅析厚板压力容器焊接工艺
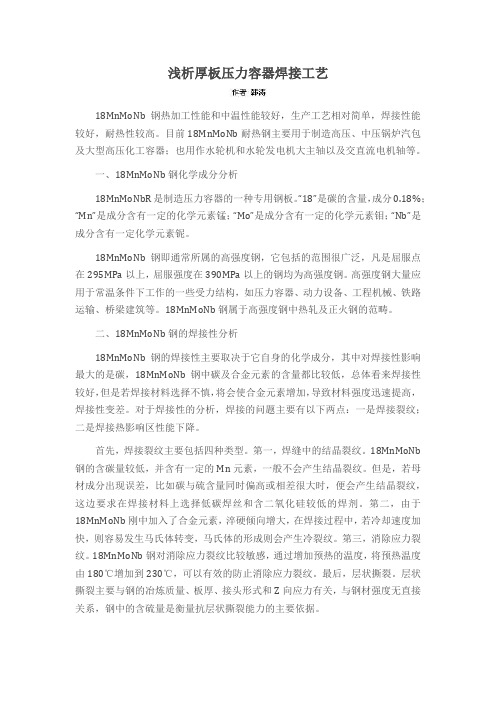
浅析厚板压力容器焊接工艺18MnMoNb钢热加工性能和中温性能较好,生产工艺相对简单,焊接性能较好,耐热性较高。
目前18MnMoNb耐热钢主要用于制造高压、中压锅炉汽包及大型高压化工容器;也用作水轮机和水轮发电机大主轴以及交直流电机轴等。
一、18MnMoNb钢化学成分分析18MnMoNbR是制造压力容器的一种专用钢板。
“18”是碳的含量,成分0.18%;“Mn”是成分含有一定的化学元素锰;“Mo”是成分含有一定的化学元素钼;“Nb”是成分含有一定化学元素铌。
18MnMoNb钢即通常所属的高强度钢,它包括的范围很广泛,凡是屈服点在295MPa以上,屈服强度在390MPa以上的钢均为高强度钢。
高强度钢大量应用于常温条件下工作的一些受力结构,如压力容器、动力设备、工程机械、铁路运输、桥梁建筑等。
18MnMoNb钢属于高强度钢中热轧及正火钢的范畴。
二、18MnMoNb钢的焊接性分析18MnMoNb钢的焊接性主要取决于它自身的化学成分,其中对焊接性影响最大的是碳,18MnMoNb钢中碳及合金元素的含量都比较低,总体看来焊接性较好,但是若焊接材料选择不慎,将会使合金元素增加,导致材料强度迅速提高,焊接性变差。
对于焊接性的分析,焊接的问题主要有以下两点:一是焊接裂纹;二是焊接热影响区性能下降。
首先,焊接裂纹主要包括四种类型。
第一,焊缝中的结晶裂纹。
18MnMoNb 钢的含碳量较低,并含有一定的Mn元素,一般不会产生结晶裂纹。
但是,若母材成分出现误差,比如碳与硫含量同时偏高或相差很大时,便会产生结晶裂纹,这边要求在焊接材料上选择低碳焊丝和含二氧化硅较低的焊剂。
第二,由于18MnMoNb刚中加入了合金元素,淬硬倾向增大,在焊接过程中,若冷却速度加快,则容易发生马氏体转变,马氏体的形成则会产生冷裂纹。
第三,消除应力裂纹。
18MnMoNb钢对消除应力裂纹比较敏感,通过增加预热的温度,将预热温度由180℃增加到230℃,可以有效的防止消除应力裂纹。
厚板UNS N08810材料压力容器监造检验控制

椭圆封头、 筒体 、 锥体和支座组成 。简体板厚 5 8 m 设 备 直径 0 20mm, m, 20 总长 200mm, 20 设备 结 构见图 1 。无论 从设 备 的规 格 还 是结 构 上 都 有相
Ke r s:h c l N0 0 al y; l i g; n f curn h a r ame t y wo d t ik wal 88 lo we d n ma u l t i g; e tte t n 1 a
当大 的制造难 度 , 此 , 投产 前期 监造 方就 介入 为 在
厚板 U SN 8 1 N 0 80材料压 力容器监造检验 控制
陈 亮
( 上海众深石化设备科技有限公司, 上海 2 10 ) 0 23
摘 要: 据 N81 根 0 80厚板 焊接 特 性及全 程 参 与某制 造厂设 备 制 造 监理 , N 8 1 对 0 80厚板 制造 压 力容 器 过 程 中 的焊 接 、 工 成 形 和 整 体 热处 理 等 难 点 , 订 了监 理 控 制 点 , 而 有 效 地 解 决 和 避 免 加 制 从 N 8 1 料焊 接过 程 中极 易 出现 的热裂 纹和 气孔 缺 陷 , 产 品最终 满足 客 户及 相 关标 准和 图样 要 080材 使
P HT.Thee y.i p o u e aina nd efc ie s l to o t o e fh tc a k a d g s p r W rb t r d c s a r to la fe tv ou in t he prblmso o r c n a o e
锅炉压力容器焊接方法及焊接工艺探讨
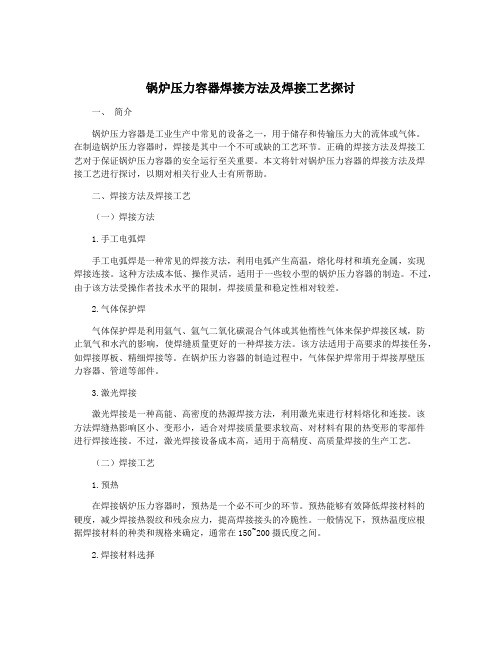
锅炉压力容器焊接方法及焊接工艺探讨一、简介锅炉压力容器是工业生产中常见的设备之一,用于储存和传输压力大的流体或气体。
在制造锅炉压力容器时,焊接是其中一个不可或缺的工艺环节。
正确的焊接方法及焊接工艺对于保证锅炉压力容器的安全运行至关重要。
本文将针对锅炉压力容器的焊接方法及焊接工艺进行探讨,以期对相关行业人士有所帮助。
二、焊接方法及焊接工艺(一)焊接方法1.手工电弧焊手工电弧焊是一种常见的焊接方法,利用电弧产生高温,熔化母材和填充金属,实现焊接连接。
这种方法成本低、操作灵活,适用于一些较小型的锅炉压力容器的制造。
不过,由于该方法受操作者技术水平的限制,焊接质量和稳定性相对较差。
2.气体保护焊气体保护焊是利用氩气、氩气二氧化碳混合气体或其他惰性气体来保护焊接区域,防止氧气和水汽的影响,使焊缝质量更好的一种焊接方法。
该方法适用于高要求的焊接任务,如焊接厚板、精细焊接等。
在锅炉压力容器的制造过程中,气体保护焊常用于焊接厚壁压力容器、管道等部件。
3.激光焊接激光焊接是一种高能、高密度的热源焊接方法,利用激光束进行材料熔化和连接。
该方法焊缝热影响区小、变形小,适合对焊接质量要求较高、对材料有限的热变形的零部件进行焊接连接。
不过,激光焊接设备成本高,适用于高精度、高质量焊接的生产工艺。
(二)焊接工艺1.预热在焊接锅炉压力容器时,预热是一个必不可少的环节。
预热能够有效降低焊接材料的硬度,减少焊接热裂纹和残余应力,提高焊接接头的冷脆性。
一般情况下,预热温度应根据焊接材料的种类和规格来确定,通常在150~200摄氏度之间。
2.焊接材料选择焊接材料的选择对于焊接质量和连接强度至关重要。
通常情况下,焊接材料的选择应考虑与母材的相容性、焊接操作性和焊接后的材料性能等因素。
在焊接压力容器时,应根据设计要求和使用环境来选择适当的焊接材料,以确保焊接接头的质量和可靠性。
3.焊接工艺控制焊接工艺控制是保证焊接质量的关键环节。
在焊接锅炉压力容器时,应根据设计要求和焊接材料的特性,合理选择焊接工艺参数,如焊接电流、电压、焊接速度等,保证焊接接头的质量和可靠性。
过程装备制造工艺学
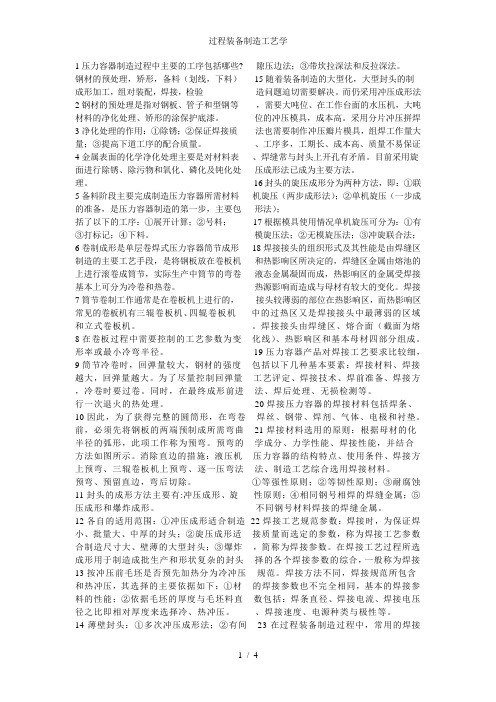
1压力容器制造过程中主要的工序包括哪些? 隙压边法;③带坎拉深法和反拉深法。
钢材的预处理,矫形,备料(划线,下料)15随着装备制造的大型化,大型封头的制成形加工,组对装配,焊接,检验造问题迫切需要解决。
而仍采用冲压成形法2钢材的预处理是指对钢板、管子和型钢等,需要大吨位、在工作台面的水压机,大吨材料的净化处理、矫形的涂保护底漆。
位的冲压模具,成本高。
采用分片冲压拼焊3净化处理的作用:①除锈;②保证焊接质法也需要制作冲压瓣片模具,组焊工作量大量;③提高下道工序的配合质量。
、工序多,工期长、成本高、质量不易保证4金属表面的化学净化处理主要是对材料表、焊缝常与封头上开孔有矛盾。
目前采用旋面进行除锈、除污物和氧化、磷化及钝化处压成形法已成为主要方法。
理。
16封头的旋压成形分为两种方法,即:①联5备料阶段主要完成制造压力容器所需材料机旋压(两步成形法);②单机旋压(一步成的准备,是压力容器制造的第一步,主要包形法);括了以下的工序:①展开计算;②号料;17根据模具使用情况单机旋压可分为:①有③打标记;④下料。
模旋压法;②无模旋压法;③冲旋联合法;6卷制成形是单层卷焊式压力容器筒节成形18焊接接头的组织形式及其性能是由焊缝区制造的主要工艺手段,是将钢板放在卷板机和热影响区所决定的,焊缝区金属由熔池的上进行滚卷成筒节,实际生产中筒节的弯卷液态金属凝固而成,热影响区的金属受焊接基本上可分为冷卷和热卷。
热源影响而造成与母材有较大的变化。
焊接7筒节卷制工作通常是在卷板机上进行的,接头较薄弱的部位在热影响区,而热影响区常见的卷板机有三辊卷板机、四辊卷板机中的过热区又是焊接接头中最薄弱的区域和立式卷板机。
焊接接头由焊缝区、熔合面(截面为熔8在卷板过程中需要控制的工艺参数为变化线)、热影响区和基本母材四部分组成。
形率或最小冷弯半径。
19压力容器产品对焊接工艺要求比较细,9筒节冷卷时,回弹量较大,钢材的强度包括以下几种基本要素:焊接材料、焊接越大,回弹量越大。
13MnNiMoR钢制容器的焊接工艺

焊 层 焊 接 方 法 1
牌 号 直 径 / 性 电 流 / mm 极 A
S MAW J0 R 6 7 H 4O .
反 接 5 一 7 2 ~ 6 1O1O 22 反 接 6 一 8 2 ~ 8 1 o 1 0 2 2
收 稿 日期 :2 1 一 1O 0 0 l一 8
器 焊 接 规 程 》 以及 等 强 匹 配原 则 ,焊条 电弧 焊 选 用
根 据 表 1可 知 ,1 Mn M0 钢 的 C,S及 P元 3 Ni R J0 R 焊条 .埋弧 焊焊 材选 用 H 8 2 A H 3 0 67 H 0 Mn Mo + J 5 。
素 的含 量 非 常低 ,Mn含 量 及 Mns较 高 , 因此 止冷 裂 纹 的 产 生 是 进行 焊接 工 艺 设 计 时首 要 考 虑
的 问题 。
1 Mn i R钢 属 于 中温 中压 锅 炉 和 压 力 容 器 用 3 N Mo
钢 ,供 货状 态 为正 火 + 回火 ,属 于 可焊 接 细 晶钢 ,热
强 性 能高 ,抗裂 纹 扩展 敏感 性好 ,被 广泛 用 以制造 高
2 焊 接 工艺 制订
压 锅炉 汽包 、核 能 容器及 其 他耐 高压 容器 等 。该 材料
的化学 成分 见表 l 。
21 焊 接方 法及 焊材 选择 .
根 据 实 际 产 品 的 规 格 . 拟 采 用 焊 条 电 弧 焊
( MA )和 埋 弧 焊 ( A )这 2种 焊 接 方 法 ,并 进 S W SW 行 工 艺 性 试 验 。参 考 J / 7 9 2 0 《 制压 力 容 BT4 0 - 0 0 钢
潘 伍 覃
( 武汉 一冶 钢结 构 有 限责 任 公 司 ,湖 北 武 汉 4 0 1 ) 3 4 5
Q245RRHIC厚壁容器制造

3. 2 筒体
下料展开长度按筒体中径计算 ,适当考虑厚板 展开的中径偏移量 ,控制展开长度误差为 ±2 mm , 对角误差为 ±2. 5 mm 。
验收条件 。
钢板需逐张进行超声波检测 ,符合 JB/ T 4730.
1~4730. 6 —2005《承压设备无损检测》标准规定 , Ⅱ
级为合格[8 ] 。
钢板应按 GB/ T 8650 —2006《管线钢和压力容
器钢抗氢致开裂评定方法》进行抗氢诱导裂纹 ( R2
H IC) 试验[9] ,采用 A 溶液 ,3 个试样裂纹长度敏感
2. 3 焊接材料
3. 1 封头
设备封头为标准椭圆封头 ,设计厚度为48 mm , 考虑加工减薄量 ,下料厚度取 54 mm 。采用整体热 压成形 ,加工工艺为 ,封头热压开始温度为 960 ℃, 终压温度为 860 ℃。母材验证试件随封头经历全部 受热史 (加热 、初压 、终压) 。由于热加工过程与板材 正火温度重叠 ,需要对封头 (带验证试件) 恢复正火
第 40 卷 第 5 期 石 油 化 工 设 备 Vol1 40 No1 5 2011 年 9 月 PETRO2C H EMICAL EQU IPM EN T Sept . 2011
小于 3 ,正火状态交货 。 ③锻件化学成分除应符合 文献[ 8 ]规定外 ,还应控制元素 S 的质量分数不大于
3 制造及检验
0. 003 % ,元素 P 的质量分数不大于 0. 015 %。 ④锻 件力学性能应为经正火 + 模拟焊后热处理后所得的 试验数据 。 ⑤锻件中脆性夹杂物 、塑性夹杂物不得 大于 2. 5 级 ,且两者总和不大于 4. 5 级 。 ⑥锻件的 抗氢诱导裂纹 ( R2H IC) 试验执行文献[ 9 ] ,抗硫化物 应力腐蚀试验执行文献[ 10 ] 。
厚板焊接

厚板焊接研究摘要:厚板是指厚度40.0-100.0mm的钢板,厚度的5-40mm称为中厚板,厚度超过100.0mm的为特厚板广泛用来制造各种容器、炉壳、炉板、桥梁及汽车静钢钢板、低合金钢钢板、桥梁用钢板、造般钢板、锅炉钢板、压力容器钢板、花纹钢板、汽车大梁钢板、拖拉机某些零件及焊接构件,本文论述了厚板的焊接工艺,从材料准备、预热、焊接过程的控制等,详细的分析厚板焊接过程所引起的一系列问题及造成质量差的原因,提出了相应的防止措施。
关键词:厚板焊接、预热、焊接过程、措施1、厚板焊接工艺由于材料为低合金结构钢,含有少量的合金元素,淬硬倾向大,焊接性差,焊缝中极易出现裂纹,因此厚板焊接是本工程的一大难题,为防止焊接缺陷的产生,除遵循上述“焊接通则”要求外,特制定如下工艺措施:(1)焊接材料①选择强度、塑性、韧性相同的焊接材料,并且焊前要进行工艺评定试验,合格后方可正式焊接,焊接材料选择低氢型焊接材料。
②CO2气体保护焊:选用药芯焊丝E71T-1或ER50-6。
CO2气体:CO2含量(V/V)不得低于99.9%,水蒸气与乙醇总含量(m/m)不得高于0.005%,并不得检出液态水。
③手工电弧焊时:选用焊条为E50型,焊接材料烘干温度如下所示:(2)焊前预热①为减少内应力,防止裂纹,改善焊缝性能,母材焊接前必须预热。
②预热最低温度:③T型接头应比对接接头的预热温度高25-50℃。
④操作地点环境温度低于常温时(高于0℃)应提高预热温度为15-25℃。
⑤预热方法采用电加热和火焰加热两种方式,火焰加热仅用于个别部位且电加热不宜施工之处,并应注意均匀加热。
电加热预热温度由热电仪自动控制,火焰加热用测温笔在离焊缝中心75mm的地方测温,测温点应选取加热区的背面。
(3)工艺参数选择为提高过热区的塑性、韧性,采取小线能量进行焊接。
根据焊接工艺评定结果,选用科学合理的焊接工艺参数。
(4)焊接过程采取的措施①由于后层对前层有消氢作用,并能改善前层焊缝和热影响区的组织,采用多层多道焊,每一焊道完工后应将焊渣清除干净并仔细检查和清除缺陷后再进行下一层的焊接。
厚板钢制压力容器焊接工艺要素分析

2 .焊接过程中工艺要素
焊பைடு நூலகம்过程 中的工艺要素主要是指 焊接参数 ,主要包
括焊接电流 、电弧 电压 、焊接速度 的控制与 匹配 、焊丝
( )在埋弧焊过程中,电流种类和极性要严格依据焊 7 接工艺规程进行选择,与焊接母材和焊剂进行合理匹配。
很 大影 响。焊丝干伸长度增加时 ,电阻热增加使焊 丝熔
( )焊件的厚度和散热条件也对焊缝成形产生一定 2
的影 响。在对薄板进行埋弧焊时 ,由于熔 深较小 ,板厚 及其散热情况的影响可以略去不计。但对厚板 进行埋 弧
焊时 ,由于厚度较大 ,熔深可因熔 池底部散热 条件 的变
化而发生明显变化 。
厚 板钢制压力容器在 中、高压压力容 器制造业 巾有
2 .气子超标 L
埋弧焊 由于熔池较深 ,对气孔敏感 性大 ,特别是在 厚板 的焊接和简体环缝 的焊接 过程 中 ,经常会 出现气孔
超标 ,甚至 出现贯穿性气孔 ,影 响焊接质量 ,给生产 带
来 很多麻烦。
着广泛 的应用 ,而压力容器厚板结构 的焊 接主要 以埋弧
焊为主。埋弧焊是在焊条电弧焊 的基础 上发展起来 的一 种高效率 的 自动焊接方法 ,这种 方法利用机械装置 自动 控制送丝 和移动电弧。电弧在焊 剂层 下燃烧 ,焊接过程 是通过操作控制盘上的按钮 开关来实现 自动控制 的。在 焊接过程 中,工件被焊处覆 盖一层 3 5 rm厚 的粒状 0~ 0 a 焊剂 ,连续送进 的焊丝在焊 剂层下 与焊 件问产 生 电弧 , 电弧的热量使焊丝、工件和焊剂熔化,形成金属熔池 ,使 它们与空气隔绝。随着焊机 自动向前移动 ,电弧不断熔化 前方的焊件金属 、焊丝及焊剂,而熔池后方的边缘开始冷
厚板的厚度标准

厚板的厚度标准厚板是一种常见的金属制品,广泛应用于建筑、船舶、桥梁等领域。
其厚度标准在不同行业和国家可能会有所不同,本文将以厚板的厚度标准为标题,介绍一些常见的厚板厚度标准及其应用。
一、厚板厚度标准的分类根据不同的使用领域和行业要求,厚板的厚度标准可以分为以下几类:1. 建筑用厚板:主要用于建筑结构的承重和支撑,常见的厚度标准有5mm、10mm、20mm等。
建筑用厚板通常采用热轧或冷轧工艺制造,具有较高的强度和耐久性。
2. 船舶用厚板:船舶用厚板的要求较高,主要用于船体的制造和维修。
常见的厚度标准有6mm、8mm、12mm等。
船舶用厚板通常采用特殊的船级社认证标准,如中国船级社(CCS)、德国劳氏(GL)等。
3. 桥梁用厚板:桥梁用厚板承担桥梁结构的荷载和振动,对材料的强度和韧性要求较高。
常见的厚度标准有16mm、25mm、40mm 等。
桥梁用厚板通常采用碳素结构钢或低合金高强度钢制造。
二、不同厚度标准的厚板应用1. 5mm厚板:适用于建筑内部隔墙、天花板等轻质结构的搭建,也可用于制作家具和装饰品。
2. 10mm厚板:常用于建筑结构的承重构件、屋面板等。
也可用于制作集装箱、铁路车辆的车身等。
3. 20mm厚板:适用于建筑结构的梁、柱等承重构件,也可用于制作大型机械设备的零部件。
4. 6mm厚板:常用于船舶的舱壁、甲板等部位,也可用于制作石油化工设备和压力容器。
5. 8mm厚板:适用于船舶的船体结构、船舶设备的支架等。
也可用于制作矿山机械、石油钻机等。
6. 12mm厚板:常用于船舶的船底、龙骨等部位,也可用于制作大型储罐、热交换器等。
7. 16mm厚板:适用于大型桥梁的主梁、桥塔等结构,也可用于制作锅炉、压力容器等。
8. 25mm厚板:常用于桥梁的桥面板、悬索桥主缆等部位,也可用于制作核电设备、化工容器等。
9. 40mm厚板:适用于大型桥梁的桥塔、桥墩等结构,也可用于制作海洋平台、风力发电机组等。
厚板生产工艺

–
矫直速度是根据钢板的矫直温度、厚度及强度性能等因素确定的,速度范 围为0.8~2.0m/sec(通过最大2.5 m/sec),在使用快速冷却设备时, 须与快速冷却同步。 矫直压下量主要取决于钢板的矫直温度,一般在1.0~5.0mm的范围内选 取。
厚度大于80~250mm的钢板从矫直机中空过
–
–
冷却
轧后加速冷却(ACC)
在四辊精轧机和热矫直机之间布置有一套钢板加速冷却系统。 对于那些要求进一步提高强度或改善焊接性能和低温韧性的产品,以及那些要求抗氢致 裂纹(HIC)或抗硫化物应力腐蚀(SSCC)的产品,在完成控制轧制后即进入ACC装置进行加 速冷却。 根据不同的产品要求,这套冷却系统分为两部分:高压喷水冷却系统(DQ)、加速冷却系 统(ACC)。一旦两套冷却系统同时使用,就有可能采用两个不同的冷却速率对钢板进行冷 却,从而使钢板在厚度方向上的机械性能保持一致。但大多数情况下,一般只采用其中的 某一系统对钢板进行冷却。 加速冷却钢板的厚度一般在10~12mm以上。钢板在成品轧制的最后一个道次抛钢后, 由辊道运送,按照给定的速度直接进入ACC装置。钢板通过ACC装置时,上、下两面同时 喷水进行加速冷却,使钢板的温度由约700~800℃(即奥氏体区或双相区)快速下降至约 400~650℃。 根据成品钢板的不同长度,通过ACC装置冷却时可以采用两种方式:当长度26m时,钢 板可进行摆动冷却;当长度26m时,采用直通式冷却。钢板通过ACC装置的速度约0.5~ 2.5m/sec,考虑在上、下两面喷冷的同时,还有侧喷以清除板面的汽化层。 厚度在25mm以上的钢板,通过ACC装置的速度约在0.5~1.2m/sec之间;对厚度小于 25mm的钢板,通过速度最高可达2.5m/sec。 对其它控轧钢板,以及那些含碳量或合金含量较高的结构钢、工具钢等轧后不宜喷水降 温的钢板,在通过ACC装置时,不予喷水。
压力容器产品组装工艺规程

压力容器产品组装工艺规程(QB/SAR0303-2005)1.0总则1.1编制依据1.1.1《压力容器安全技术监察规程》;1.1.2《钢制压力容器》(GB150-1998);1.1.3《钢制卧式容器》(JB4731-2000);1.1.4《钢制塔式容器》(JB4710-2000);1.1.5《锅炉压力容器产品安全性能监督检验规则》;1.1.6本公司原有工艺方法。
1.2适用范围本规程适用于压力容器产品的壳体和其他零部件的组装过程。
1.3一般规定1.3.1产品组装前的零、部件均已完成规定的检验、试验项目并合格。
1.3.2压力容器必须按设计图纸进行加工制造,任何原因造成的需对原设计进行的变更,应取得原设计单位的认可。
1.3.3组装过程中各质量控制点必须按规定的控制类别,由相应级别的监检人员检验确认后,方可进行后续作业。
1.3.4压力容器产品质量应符合设计图纸和相关标准规定要求,须经授权的检验机构实施监检。
2.0壳体组装:2.1组对:2.1.1筒节加工完成并经检验合格后,即可进行壳体组装,组装前,应对各部件的标识和制作序号及组装中心线进行校核。
2.1.2相邻的筒节以及筒节与封头对接前,应对对接端的周长进行测量,换算成对接端的平均直径,以保证对接使的错边量均匀地分布在筒节或封头直边的全周上,避免对接端的直径差集中表现在局部圆弧上,而造成错边量超差。
2.1.3单层管钢板壳体环向对接焊缝的对口错边量b(见图2-1)应符合(表2-1)的允许值。
图2-1 图2-2表2-1 单层管钢板筒体环向对接错边允许偏差单位:mm 钢板厚度(δs) 对口错边允许偏差(b)δs≤12 ≤1/4δs12<δs≤20 ≤1/4δs20<δs≤40 ≤5.040<δs≤50 ≤1/8δsδs>50 ≤1/16δs.且不大于102.1.4复合钢板壳体的环向对接焊缝的对口错边量b(见图2-2)不得大于钢板复合层厚度5%,且不得大于2mm.2.1.5壳体组对时,要对壳体的直线度不断的进行测量和控制,以保证壳体组装完成后的直线度符合设计要求。
复合钢板压力容器设计

复合钢板压力容器设计作者:赵国锋刘清华来源:《中国科技博览》2019年第09期[摘要]由于不锈钢复合钢板比不仅具有不锈钢的良好的耐腐蚀性,还具有低合金钢的强度和加工性能。
与不锈钢容器相比,可大大降低设备造价,所以在压力容器中应用越来越广泛。
然而,复合钢板压力容器在设计中与不锈钢及碳钢压力容器并不相同。
本文总结复合钢板压力容器在设计及制造中的常见问题。
[关键词]复合钢板、热处理、焊接坡口中图分类号:G717 文献标识码:A 文章编号:1009-914X(2019)09-0327-011 概述随着工艺技术的不断发展,设备大型化逐步成为一种趋势。
为了降低设备的成本,提高经济效益,许多重要设备,越来越多采用不锈钢复合钢板来满足生产需要。
复合钢板具有单层金属材料所不具有的优异性能以及力学特性,能够满足高强度、耐腐蚀等性能。
压力容器行业应用最为广泛的为不锈钢不和钢板。
不锈钢复合钢板是以碳钢或低合金钢作为基层,以不锈钢作为复层同坐轧制、焊接、堆焊等方式制成的钢板。
基层材料主要用以满足设备安全的结构强度和刚度的要求,复层则用以满足盛装介质的腐蚀、磨削等特殊性能的要求。
不锈钢复合板比整体不锈钢板可节约铬、镍元素的70%~80%,复合板中不锈钢仅占1/5~1/6,可极大的节省不锈钢板材,成本仅为不锈钢板材的1/3,价格可降至整体不锈钢的3/4~2/3,有着巨大的经济及社会效益。
2 压力容器设计2.1材料选择2.1.1 复合钢板1)基层材料的选择基层材料选择主要根据设备的工作温度、工作压力、使用成本、加工性能,并通过计算比较后确定。
2)复层材料的选择复层材料的选择应根据介质的特性要求进行选择,如耐腐蚀、防污染和经济效果确定。
而部分设备需热加工或需进行焊后热处理,为了保证耐不锈钢复层耐晶间腐蚀,最好选用超低碳型不锈钢复层。
较为常见的不锈钢复层材料为S30403或S31603不锈钢钢板。
2.1.2 接管1)对于容器接管,小直径接管可直接采用与复层材料相同的不锈钢接管或锻件。
压力容器钢板,中厚板简介

钢板、中厚板简介关键字:中厚板一、中厚板定义:钢板厚度大于等于5.0mm,分普碳板、优碳板、低合金板、船板、桥梁板、锅炉板、容器板等。
二、用途:应用于建筑、机械、造船、桥梁、锅炉、压力容器等行业。
DIN标准:JIS标准:容器用钢板基础知识(一)压力容器用钢板压力容器用钢板是用于制造石油、化工、气体分离、气体贮运的容器或其他类似设备,如各种塔器、换热器、贮罐、罐车等的优质碳素结构钢和低合金高强度结构钢钢板,参见GB6654—1996。
1 尺寸、重量:按GB709的规定,常用厚度*宽度尺寸为6~120*600~3800(mm)。
2 常用牌号:20R、16MnR、15MnVNR、18MnMoNbR、13MnNiMoNbR、15CrMoR(其中13MnNiMoNbR、15CrMoR是旧标准GB6654—86中所没有的),牌号说明如下:数字平均碳含量的万分之几。
R “容”字的汉语拼音首位字母。
3 交货状态:20R、16MnR、15MnVR钢板以热轧、控轧或正火状态交货;15MnVNR钢板以正火状态交货;18MnMoNbR、13MnNiMoNbR、15CrMoR钢板以正火加回火状态交货。
4 使用情况:广泛用于制造各种中常温压力容器受压元件。
(二)低温压力容器用低合金钢钢板低温压力容器用低合金结构钢钢板是用于制造各种不大于-20℃低温压力容器的低合金钢板。
其标准参见GB3531—1996。
1 尺寸、重量:按GB709的规定,常用厚度*宽度尺寸为6~100*600~3800(mm)。
2 常用牌号:16MnDR、15MnNiDR、09Mn2VDR、09MnNiDR(其中15MnNiDR、09Mn2VDR是旧标准GB3531—83中所没有的;而旧标准GB3531—83中的09MnTiCuXtDR、06MnNbDR 因长期没有生产和订货量被取消了)。
牌号说明如下:数字平均碳含量的万分之几DR “低容”二字的汉语拼音首位字母,表示低温压力容器钢板用钢3 交货状态:钢板以正火或正火加回火状态交货。
中厚板生产工艺介绍
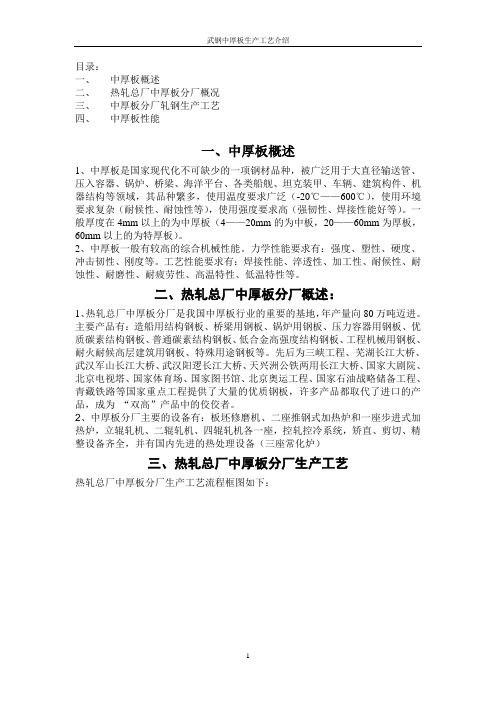
目录:一、中厚板概述二、热轧总厂中厚板分厂概况三、中厚板分厂轧钢生产工艺四、中厚板性能一、中厚板概述1、中厚板是国家现代化不可缺少的一项钢材品种,被广泛用于大直径输送管、压入容器、锅炉、桥梁、海洋平台、各类船舰、坦克装甲、车辆、建筑构件、机器结构等领域,其品种繁多,使用温度要求广泛(-20℃——600℃),使用环境要求复杂(耐候性、耐蚀性等),使用强度要求高(强韧性、焊接性能好等)。
一般厚度在4mm以上的为中厚板(4——20mm的为中板,20——60mm为厚板,60mm以上的为特厚板)。
2、中厚板一般有较高的综合机械性能。
力学性能要求有:强度、塑性、硬度、冲击韧性、刚度等。
工艺性能要求有:焊接性能、淬透性、加工性、耐候性、耐蚀性、耐磨性、耐疲劳性、高温特性、低温特性等。
二、热轧总厂中厚板分厂概述:1、热轧总厂中厚板分厂是我国中厚板行业的重要的基地,年产量向80万吨迈进。
主要产品有:造船用结构钢板、桥梁用钢板、锅炉用钢板、压力容器用钢板、优质碳素结构钢板、普通碳素结构钢板、低合金高强度结构钢板、工程机械用钢板、耐火耐候高层建筑用钢板、特殊用途钢板等。
先后为三峡工程、芜湖长江大桥、武汉军山长江大桥、武汉阳逻长江大桥、天兴洲公铁两用长江大桥、国家大剧院、北京电视塔、国家体育场、国家图书馆、北京奥运工程、国家石油战略储备工程、青藏铁路等国家重点工程提供了大量的优质钢板,许多产品都取代了进口的产品,成为“双高”产品中的佼佼者。
2、中厚板分厂主要的设备有:板坯修磨机、二座推钢式加热炉和一座步进式加热炉,立辊轧机、二辊轧机、四辊轧机各一座,控轧控冷系统,矫直、剪切、精整设备齐全,并有国内先进的热处理设备(三座常化炉)三、热轧总厂中厚板分厂生产工艺热轧总厂中厚板分厂生产工艺流程框图如下:1、原料选择原料是中厚板生产中的重要环节之一。
原料的选择是否合理,将影响轧机的生产率、成材率、钢板质量及成本。
原料表面缺陷一般可以采用表面清理的方法消除,然后再加热、轧制,否则会因原料缺陷在轧制过程中扩展造成废品。
高质量中厚板生产关键共性技术研发现状和前景

高质量中厚板生产关键共性技术研发现状和前景发布时间:2021-05-12T16:40:50.660Z 来源:《工程管理前沿》2021年4期作者:鲁建明胡志杰[导读] 中厚板,是指厚度4.5-25.0mm的钢板,厚度25.0-鲁建明胡志杰河钢集团邯钢公司中板厂河北邯郸 056015河钢集团邯钢公司品质管理部河北邯郸 056015摘要:中厚板,是指厚度4.5-25.0mm的钢板,厚度25.0-100.0mm的称为厚板。
由中厚板国际发展趋势和目前大量的市场需求来看,以绿色化、智能化、高质化、服务化为目标,确定主攻方向和突破口,加强全流程一体化创新,推进我国中厚板行业技术进步与发展。
下文主要论述了当前中厚板生产关键性技术和发展现状,同时研讨了高质量中厚板今后的发展方向。
关键词:高质量中厚板;生产关键共性技术;现状;前景1.高质量中厚板的主要用途中厚板主要应用于建筑工程、机械制造、容器制造、造船、桥梁建造等。
还可以用来制造各种容器、炉壳、炉板、桥梁及汽车静钢钢板、低合金钢钢板、造船钢板、锅炉钢板、压力容器钢板、花纹钢板、汽车大梁钢板、拖拉机某些零件及焊接构件等。
通中厚板用途:广泛用来制造各种容器、炉壳、炉板、桥梁及汽车静钢钢板、低合金钢钢板、桥梁用钢板、造般钢板、锅炉钢板、压力容器钢板、花纹钢板、汽车大梁钢板、拖拉机某些零件及焊接构件具体应用。
1.1桥梁用钢板用于大型铁路桥梁的钢板,要求承受动载荷、冲击、震动、耐蚀等,如:Q235q、Q345q等。
1.2造船用钢板用于制造海洋及内河船舶船体,要求强度高、塑性、韧性、冷弯性能、焊接性能、耐蚀性能都好。
如:A32、D32、A36、D36等。
锅炉钢板(锅炉板):用于制造各种锅炉及重要附件,由于锅炉钢板处于中温(350°C以下)高压状态下工作,除承受较高压力外,还受到冲击、疲劳载荷及水和气腐蚀,要求保证一定强度,还要有良好的焊接及冷弯性能,如:Q245R等。
中厚板热处理工艺技术规程
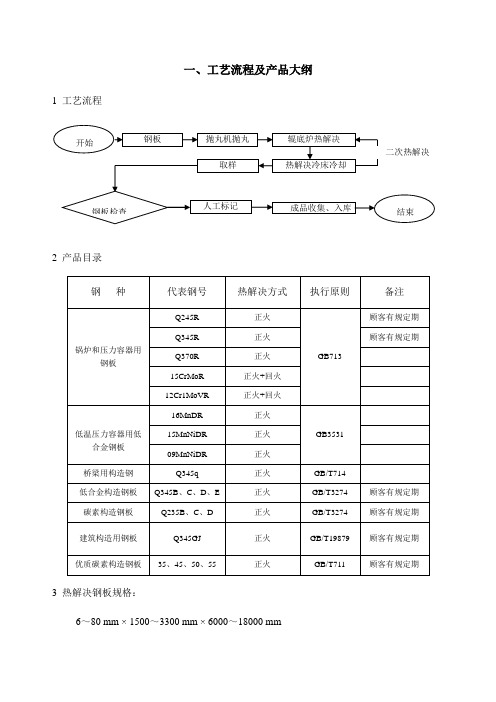
一、工艺流程及产品大纲1 工艺流程2 产品目录3 热解决钢板规格:6~80 mm × 1500~3300 mm × 6000~18000 mm最大单重:12.5 t4 热解决生产能力钢板旳正火或钢板旳高温回火,年解决量20.5万吨,其中正火钢板19万吨/年;回火钢板1.5万吨/年。
二抛丸清理区域工艺技术操作规程1、抛丸清理区域重要设备及性能1.1 抛丸清理机总体性能参数1.2 抛丸清理机前上料、机后输送辊道:1.3 抛丸室输送辊道:1.4 抛丸除锈系统1.5 丸料打扫系统对钢板旳清理采用二级打扫加二级风吹旳方式:一级滚扫采用老式旳高强度尼龙滚刷+收丸螺旋旳方式;二级横扫采用钢丝侧刷+压轮方式,打扫大量弹丸;一级风吹采用高压风机在打扫室内吹丸。
二级风吹采用高压空气在打扫室进行吹丸。
1.6 丸料循环系统1.7 抛丸器1.8 除尘系统1.9 气控系统1.10 起重设备2 抛丸清理机旳工艺操作规程2.1抛丸清理运营方式旳选择运营方式分为自动和手动两种方式。
自动方式为总操作台上“自动/手动”转换开关位于“自动”位置,按压自动起动按钮后,抛丸机按PC内预定程序顺序起动。
在进行结束时,按压自动停止按钮后,抛丸机旳电气设备将顺序关机。
手动方式为“自动/手动”转换开关位于“手动”位置,操作人员可按照预解决旳规定,分别按压有关旳起动停止按钮,来控制电气设备旳工作状态。
如从“手动”转为“自动”运营时,要保证抛丸机和辊道上没有钢板,然后将转换开关扳向“自动”位置,进入启动自动开机程序。
在“手动”和“自动”方式中,操作人员均可通过观测模拟屏上设备旳运营状态旳显示,来判断抛丸机旳工作状况。
2.2 钢板抛丸清理工艺规定2.2.1 按炉(批)进行钢板抛丸清理,严禁混炉混号。
2.2.2 钢板旳摆放吊板放在抛丸机前上料辊道上一定要放正,使其摆放在上料辊道旳中间位置。
钢板之间需保持一定旳距离。
当钢板是逐片进线时,间隔为相继钢板首尾之间旳距离。
压力容器筒体制造通用工艺守则102

压力容器制造、检验通用工艺规程文件编号Q/PV-Q-3-102-2003第 1 版筒体制造通用工艺规程第0 次修改修改日期:第 1 页共8 页1总则1.1 本守则依据GB150—1998《钢制压力容器》和GB151—1999《管壳式换热器》标准,以及《压力容器安全技术监察规程》99版,结合我厂设备及技术力量,编制的压力容器筒体制造通用工艺守则。
1.2 由于压力容器种类较多,各种类型之间要求各不相同,因此,本守则若同产品设计或工艺文件有矛盾时,应以产品设计图样设计要求或工艺文件规定为准。
1.3 操作工人必须熟悉图样和工艺文件,对本岗位所使用的设备结构性能和操作规程必须了解。
1.4 筒体焊缝必须由持证合格焊工施焊。
2 材料2.1 制造筒体用的材料质量及规格应符合《容规》第10条国标、部标及相应的国家标准、行业标准有关的规定,并具有质量证明书,材料上明显部位有清晰、牢固的钢印标志或其他标志。
2.2 属下列之一的主要受压元件材料应复验2.2.1 设计图样要求复验的;2.2.2 用户要求复验的;2.2.3 制造单位不能确定材料真实性或材料的性能和化学成分有怀疑的;2.2.4 钢材质量证明书注明复印件无效或不等效的。
2.3 需要代用的材料,原则上应事先取得原设计单位出具的设计更改批准文件。
2.4 制造筒体的钢板表面不得有严重锈蚀或裂纹、斑疤、夹层等影响强度的缺陷。
2.5 严禁使用未经检验或检验不合格的材料。
3 筒体加工3.1 领料3.1.1 领料人员应根据领料单、图样、工艺过程卡,核对材料规格,材质标记,并在工艺过批准: 审核:编制: 2003.08.15实施压力容器制造、检验通用工艺规程文件编号Q/PV-Q-3-102-2003第 1 版筒体制造通用工艺规程第 0 次修改 修改日期: 第 2 页 共8 页程卡上作记录。
3.1.2 所领钢板平直度必须在允差范围内,其弧曲度与波浪度可根据具体产品图样要求确 定。
压力容器制造工艺介绍培训,一文看懂合成塔、交流器等制造工艺PPT

f. JB4708 — 2000 《钢制压力容器焊 接工艺评定》
13
g. JB4709 — 2000 《钢制压力容器焊接规程》 h. JB4710 — 92《钢制塔式容器》 i. JB4730 — 94《压力容器无损检测》 j. JB/T4744 — 2000《钢制压力容器焊接试 板的力学性能检测》 k. 锅炉压力容器压力管道焊工考试与管理规 则》(2002版)
c. 分离压力容器(代号S):主要是用于 完成介质的流体压力平衡缓冲和气体净化分离 的压力容器。如分离器、过滤器、集油器、缓 冲器、吸收塔、汽提塔、除氧器等。
8
d.储存压力容器(代号C,其中球罐代号 B):主要是用于储存、盛装气体、液体、液 化气体等介质的压力容器。如各型式的储罐。
⑶ 介质毒性程度的分级和易燃介质的划分 如下:
a. 压力容器中化学介质毒性程度和易燃 介质的划分参照HG20660《压力容器中化学介 质毒性危害和爆炸危险程度分类》的规定。
9
无规定时,按下述原则确定毒性程度:
------极度危害(Ⅰ级)最高允许浓度 < 0.1mg/m3 ------高度危害(Ⅱ级)最高允许浓度 0.1~ <1.0mg/m3 ------中度危害(Ⅲ级)最高允许浓度 1.0~ <10mg/ m3 ------轻度危害(Ⅳ级)最高允许浓度 ≥10mg/m3
3
二.核电站核岛主设备的制造过程管理 1.标识 2.制造过程管理
① 制造过程的文件和控制 ② 车间检查
4
三.核电站核岛主设备制造工艺 1.蒸汽发生器制造工艺简介 2.稳压器制造工艺简介 3.反应堆压力容器制造工艺简介
压力容器制作生产加工工艺

封头的生产加工工艺1、整板、拼板封头制作采用冲压、旋压、卷制以及分瓣成型的压力容器用半球形、椭圆形、蝶形、球冠形、平底形和锥形封头应符合,同时应符合钢制压力容器、钢制化工容器制造技术要求的有关规定。
2、椭圆封头、球形封头、锥段均至少自然加厚,具体投料厚度由制造方确定,确保压制成形后的最小厚度不得低于图纸技术要求给出的最小成形厚度或图样标示厚度。
3、拼板焊缝坡口外表不得有裂纹、分层、夹杂等缺陷,标准抗拉强度下限值﹥的钢材及低合金经火焰切割的坡口外表,应用砂轮打磨平滑,并应对加工外表进展磁粉或渗透检测。
4、先拼板后成型的封头,拼板的对口错边量不应大于材料厚度的,且不大于,拼接复合钢板的对口错边量不大于覆层厚度的,且不大于。
5、椭圆封头、球形封头瓜瓣、锥段瓜瓣外表不得有裂纹、气泡、结疤、折叠、夹杂和分层。
6、封头放样。
分片过渡段分为正锥壳和偏心锥壳,为方便加工成型一般分成两半下料加工,成型后的过渡段需经预组装,预组装要求在刚性平台上进展,下口外基准圆直径确定时须考虑每道拼缝预留3mm收缩余量,预组装错边≤2mm,拼缝焊前棱角≤(),\ ())。
正锥壳放样方样方法如下:(放样尺寸均以中径为准)如下左图所示正圆锥大端直径为、小端直径为、高为,圆锥顶角α[()] (*α) α。
正锥壳展开后其扇形中,△为等腰三角形,,⌒π*,而在排板下料时需根据板料情况排料,下右图中θ°*,那么2L*(θ).画的中垂线,使,那么就找出圆心,再以点为圆心为半径画圆弧就可得到展开的两半正锥壳。
偏心锥壳需用三角形展开法画出,偏心锥壳根本采用整体外委加工,验收时必需检查上下口平行度。
三角形展开画法:在右边图的右(或左)半边两圆周上均分一样的等分,再在大圆周上每个点连接小圆周上相邻的两个点。
画一直角三角形其高度为,斜边为偏心锥壳的最长边。
在直角三角形的底边上分别以垂足为圆心右图的连线为半径画上对应的点。
在钢板上以为长度确定一条直线的两点,再以此两点为基准,直角三角形上顶点到底边的各对应点的距离及各自圆周上的弦长(这些长度尺寸均可用方便的标出)为半径确定在展开图上的各对应点,圆滑的连接这些点即可。
sa240 304h奥氏体不锈钢丙烷脱氢反应器的制造技术

反应器的主要设计参数见表 1,结构形式见图 1。 该设备总高约 34.7 m,筒体最大直径 φ4 700 mm, 主要由封头、筒体、锥体、接管法兰、人孔、设备法兰、 裙座、内件等组成。
表 1 主要设计参数 Table 1 Main design parameters
项目
设计压力 /kPa 工作压力 /kPa 设计温度 /℃ 工作温度 /℃
stainless steel
成分材料 C
Ni Cr Mn Si S
P
304H 0.04~0.10 8~10.5 18~20 2 0.75 0.030 0.045
表 3 SA240 304H 奥氏体不锈钢的主要力学性能 Table 3 The mechanical property of SA240 304H austenitic
stainless steel
性能 屈服(N · mm-2) 硬度 (HB)/(N · mm-2)
值范围 ≥ 205 ≥ 40 ≥ 515
201
求只能用细丝焊接,且对焊道宽度有要求,主要原 因是热输入大导致的热裂纹产生机率高,容易出现 问 题。
第 56 卷第 6 期 2019 年 12 月
化 工 设 备 与 管 道 PROCESS EQUIPMENT & PIPING
Vol. 56 No. 6 Dec. 2019
SA240 304H奥氏体不锈钢丙烷脱氢反应器的 制造技术
袁世东,刘扣森
(森松(江苏)重工有限公司上海分公司,上海 201323)
(1)上、下封头成型、接管与封头的焊接 ; (2)筒体的制作、接管与筒体的焊接、设备法 兰的焊接 ; (3)中间锥体的成型、内件的组对 ; (4)裙座的制作与筒体 Y 型锻件的焊接 ; (5)设备法兰机加工 ; (6)整体内外附件的组焊 ; (7)整体热处理及局部热处理 ; (8)压力试验(气压); 由于厚壁的 304H 不锈钢强度高,有一定的热裂 纹倾向性的特点,必定在封头制造,焊接,热处理, 无损检测方面带来难度,其中对厚壁下封头的成型、 304H 的 焊 缝 铁 素 体 含 量 控 制, 无 损 检 测 荧 光 PT, 890 ℃整体及局部热处理等关键工艺进行控制是反应 器在制造过程中的关键技术,需要对这些难点进行分 析和研究,进行详尽的技术准备,才能确保产品质量。
- 1、下载文档前请自行甄别文档内容的完整性,平台不提供额外的编辑、内容补充、找答案等附加服务。
- 2、"仅部分预览"的文档,不可在线预览部分如存在完整性等问题,可反馈申请退款(可完整预览的文档不适用该条件!)。
- 3、如文档侵犯您的权益,请联系客服反馈,我们会尽快为您处理(人工客服工作时间:9:00-18:30)。
厚板设备制造工艺规程厚板设备:用厚板制造的设备,一般为中、高压设备。
基本组成结构:筒体、球形封头或锥体。
一.材料1.壳体用钢板一般为正火状态供货,容器用钢板材料应符合GB713-2008的规定,并逐张超声波检测;合格级别按材料相关标准的要求或图纸中的要求。
2.对于疲劳设备,材料还需满足JB4732要求,且满足分析设计标准中的各项要求;3.壳体用基钢板一般需逐张进行拉伸和夏比(V型缺口)冲击试验。
冲击温度和冲击功值一般需符合图纸或协议的要求,但不得低于GB713-2008 的要求; 4.图纸或技术附件中有要求时,基板按GB/T5313的规定进行Z向(厚度方向)拉伸试验;5.复合板复层材料按图纸或协议规定进行晶间腐蚀等试验;6.材料厚度需注意是成型前的厚度还是成型后的最薄壁厚;筒体材料的排版起码孔不得开在焊缝上。
组对时需注意开孔接管的焊接接头与设备的主体纵、环焊接接头的距离需大于3倍的壳体厚度,不得小于100mm。
主要连接件(如:支座、支承环、轴耳等),次要连接件(如:内部支撑筋板等)与压力容器相关焊接接头之间距离至少为50mm。
7.对复合板有晶间腐蚀要求的,其接管,内件需提交晶间腐蚀要求。
二.复合板制作工艺和交货状态1. 制作工艺:复合板的复层金属应与基层金属结合牢固,其复合方法爆炸复合或爆炸+轧制复合。
其复合级别需满足图纸或协议中的较高级;2.交货状态:复合板交货状态应与基层板的状态一致,复合板需经热处理、校平、切边后交货,复层表面应喷丸(砂)或酸洗处理;复合板热处理后不允许补焊。
三. 产品焊接试板如果图纸或技术协议中没要求,产品焊接试板要求需按《容规》或相关的行业标准制作;产品试板所使用的材料和厚度应与所代表的工件相同并与代表的工件的材料为同一热处理炉号。
四. 复验用料壳体复验用料应逐张提供试样。
复验的力学性能取样一般垂直于轧制方向,特别是拉伸试验要求的长度一般在250~300mm之间,所以提供的复验用料一定要足够宽,并且要考虑双倍复验可能性,所以要足够长。
复验料所使用的材料和厚度应与所代表的工件相同并与代表的工件的材料为同一热处理炉号。
五.法兰、接管锻件1. 接管、法兰锻件首先需满足材料对应的标准;2. 法兰、接管锻件,一般要求表面堆焊不锈钢或其他耐腐蚀层的,所以锻件需逐件进行超声波检测,合格级别按锻件标准或图纸和技术协议中提出的要求合格;3. 对于要求表面堆焊接管、法兰组对的环焊缝在未要求RT的情况下,能够进行UT 的焊缝尽量做UT检查,这样就会减少堆焊后该环焊缝返修的可能性;4. 待堆焊表面,首先需清理油脂、铁锈等影响焊接质量的缺点,然后在被堆焊表面进行磁粉检测确认无缺陷时,再进行表面堆焊:1).根据焊艺要求先堆焊过渡层,堆焊要求厚度均匀,表面平整;2).堆焊过渡层后,将表面修磨平整,对堆焊表面进行100%PT,按JB/T4730-2005 I级合格;3).堆焊工件按焊接工艺热处理工艺整体热处理;4).对堆焊表面清理干净,再对堆焊表面进行100%PT,按JB/T4730-2005 I级合格;5).堆焊面层,要求堆焊厚度均匀,表面平整;堆焊的厚度需能够车加工见平。
堆焊后,最好对堆焊表面进行UT,这样就会减少堆焊成本;6).车加工堆焊层至工艺要求后,堆焊表面进行100%PT+100%UT,这样即可检查表面的缺陷,又可以检查所有堆焊的厚度有无未焊透或气孔等缺陷。
六.球形封头成型封头的成型,分为整体(或拼焊后)整体冲压或瓜瓣拼接成型。
1. 有晶间腐蚀要求的封头,考虑到安全性最好采用瓜瓣组拼。
对于瓜瓣拼接成型的封头,组对的错边量不得大于1.5mm,且封头端部直径偏差和不圆度需小于6mm;2. 拼焊后的整板进行冲压的厚板封头:1).封头下料后,刨加工的坡口表面需100%MT/PT,按JB/T4730-2005 I 级合格;坡口边缘横向50mm范围内需100%UT,按复合板的复合标准和级别要求检查贴合率;2).按焊接工艺焊接基层,焊缝需打磨与母材平齐,且内表面的焊缝需与母材圆弧过渡。
焊缝进行100%RT+UT,合格级别按图纸要求;3).在冲压前,基板的表面焊缝处,增加加强连接板,以增加焊缝的强度,防止在封头冲压时从焊缝处裂开;4).厚板封头成型,一般分为三次成型,上模为定型磨具。
下模采用2个磨具,变换内口尺寸,具体尺寸由压制工艺决定。
冲压时采用三次成型,第三次包括校型的冲压过程进行。
成型的一般过程图示如下:5).封头在正火状态供货时冲压时温度在940~980°C ,终压温度不小于850°C 左右,二次入炉温度在600°C 左右,如此循环三次(加热、冲压热曲线图如下):封头在正火+回火温度供货时,冲压成型后需进行一次回火热处理;6).封头成型后,表面人工不易处理,所以基层和复层表面需进行喷砂处理。
表面喷砂后,复层表面酸洗钝化;7).封头成型后外观及尺寸检查合格后,需进行无损检查。
封头基层表面需100%MT,按JB/T4730-2005 I级合格;封头成型后的复合板需100%UT,检查贴合率;焊缝需进行100%UT+RT检查,合格级别按图纸要求;8).封头车加工定尺。
在样板检封头成型符合标准范围时,封头车加工以展长为基准进行车加工。
车加工定尺后,先测量封头端口的展长,再加工坡口。
坡口的检查按上述坡口检查方法执行。
七.筒体成型筒体下料尺寸根据封头的展长,以内平齐为准,同时考虑厚板卷制时延长,再进行定尺。
1. 材料复验、板材UT合格后,对复合板的基层进行检查,确认无裂纹、明显划伤等缺陷。
2. 筒体划线时对角线的偏差控制在±2mm,采用火焰切割下料,切割时要求对复层表面进行保护;3. 刨加工坡口前,先刨/铣去氧化及硬化层,再刨/铣加工坡口至工艺要求;4. 打磨焊缝坡口以及坡口与母材的交界处的棱角、凹槽并圆滑过渡,同时去除硬化层,打磨的方向必须与卷制的方向一致。
这样减少了卷制过程中产生的集中应力;5. 对所有坡口(包括边缘100mm范围内)按JB/T4730进行MT、P T、UT等检测,确认无超标缺陷。
6. 对坡口和剔边附近区域进行仔细检查,确认复层已经全部去除,并将各种沟槽、突起打磨圆滑过渡,避免棱角过渡,避免在卷制过程中由于坡口棱角原因引起应力集中发生裂纹等现象。
7. 对母材做硬度检测,一张筒体料检测不少于15点。
(两端预弯区域各6点,中间位置检测3点),硬度值HV(10)≤240。
并做好记录。
8. 预弯。
清理材料表面和卷板机上辊表面,无杂物和凸起;板材与卷板找正后预弯,开始每次下压量5毫米左右,变形超过1/2后,下压量3毫米左右。
预弯变形量超过1/2和达到要求时,分别在原位置对硬度进行测试,观察硬度变化情况。
母材按理论硬度值不得超过240HV。
9. 卷制1).卷制前应检查板料的基层侧,确认无裂纹和明显划伤。
2).板材与卷板机找正后卷制,下压量的控制5mm;3).卷制合口后,不允许出现焊缝处外桃形情况;4).样板检测10. 焊接。
按照焊接工艺执行,保证预热温度、焊接电流、层间温度、后热温度和时间。
外焊缝余高尽量与母材平齐,要求小于2毫米。
特别是预热和焊后消氢要满足规范要求,避免出现煤气燃烧不充分使加热区严重污染的情况。
同时进行焊接层间的敲击消应力处理。
在碳弧气刨后,要将熔渣和硬化层,彻底清理干净,并对表面需进行MT检测;焊缝焊接完后,进行焊缝表面的修整,使外焊缝与母材圆滑过渡,待堆焊处基层修磨与母材平齐,并同时与母材圆弧过渡,避免应力集中;11. 检测。
焊缝外观检测合格后,对焊缝进行100%RT+UT+PT检测,待堆焊面进行100%MT,合格级别按图纸要求;12. 消应力热处理。
根据板厚、材质、卷曲直径、测量硬度值、技术要求等综合问题在校圆前增加一次热处理。
在筒体壁厚与设备内径比值大于3%时,对纵焊缝(包括焊缝两侧母材各250mm处)进行消应力退火处理。
如果有特殊情况再根据特殊要求采取其他的消应力处理。
具体见热处理,焊艺需出具具体的热加工工艺。
14. 校圆。
清理材料表面和卷板机上辊表面,无杂物和凸起。
再校圆,校圆顺序如下:1).先对存在的直边段进行小范围校圆,校圆前在焊缝处垫板条,要求板条与复层平齐,或者略微低于复层0.5毫米。
开始校圆时上辊不得下压,先来回进行蠕动,等工件与卷板机的三辊找正后,上辊再下压,每次压下量不大于3毫米。
校圆程度到1/2时进行硬度测试,观察硬度值变化情况。
2).整体校圆,每次下压量不超过3毫米。
在校圆过程中随时观察筒体的情况,发现问题立即停止;3).筒体校圆合格后,再进行焊缝RT+UT检测。
对于所有的环焊缝基层焊接完后,就可以对焊缝进行RT检测,过渡层和面层堆焊后不再进行RT,但必须UT+PT检查。
15. 按照图纸和工艺要求进行焊缝的各项检测。
八.锥体成型先按锥体尺寸进行硬纸板放样,按放样的尺寸划线,在展长方向两端各留50mm预弯直边段(或焊接拖头板),在油压机上采用压制模具进行折弯,并用测量样板进行尺寸检验。
压制合格后划出最终的工艺尺寸线,剔去复层后,用半自动气割割去多余的部分。
用手工打磨对接坡口。
坡口的检验同上要求。
九.设备组装。
筒体之间、筒体与封头或锥体之间都是以内平齐为基准组对,且错边量不得大于复层厚度的1/2。
1. 组对时不得有强力组对现象;2. 组对时需注意开孔接管的焊接接头与设备的主体纵、环焊接接头的距离需大于3倍的壳体厚度,不得小于100mm;3. 主要连接件(如:支座、支承环、轴耳等),次要连接件(如:内部支撑筋板等)与压力容器相关焊接接头之间距离至少为50mm;4. 不锈钢或其他有耐晶间腐蚀要求接管/补强管与壳体之间的焊接,在热处理前只对开孔处的过渡层堆焊好,等设备整体热处理后再焊接不锈钢接管法兰与壳体。
耐晶间腐蚀的法兰接管组合件有支撑筋板结构的,需热处理前在相应位置施焊一过渡垫板。
这样避免设备热处理后筋板与设备直接施焊;5. 对于封头上的耐蚀面层堆焊,考虑到封头组对后施焊的困难性,可以在设备整体热处理前施焊好,但是产品焊接试板施焊必须与封头拼缝一致。
其余耐蚀面层的堆焊尽量在热处理后进行;6. 其余的组对应符合设备设计的相关标准。
十.热处理厚板设备一般都需要热处理,热处理时必须携带产品试板或其他需与设备同炉热处理的试样。