电机定子铁心硅钢片的模具设计与制造
电机定子转子片套冲级模具设计

摘要设计题目来源于拥有七十多年电机生产历史的湖南湘电集团电机事业部生产现场。
冲压件——电机定子片与转子片采用的材料是电工用的硅钢片。
本设计对模具设计思路以及结构特点进行了较全面的论述。
结合模具发展现状以及冲压模具设计的主要技术,对定子片与转子片进行了较详细的工艺分析;进行了冲压力、压力中心、模具工作部分尺寸等冲压工艺计算;对卸料装置、定位装置、导料装置等模具结构形式进行了选择;根据工艺计算结果以及模具结构,对模具主要零部件进行了设计;对压力机进行了合理选择。
由于电机定子片、转子片结构复杂,对精密度要求较高,在设计过程中充分考虑了定子片叠装铆接孔与中心轴孔的对称度要求,以及材料的平整度和模具的工作强度。
采用了七工位排样设计:工位①为冲导正钉孔、定子片4个安装孔、转子片各槽孔及中间孔;工位②为校平工位;工位③为转子片外形落料;工位④为冲定子片内形槽孔;工位⑤为空工位; 工位⑥为定子片两端外形圆弧冲切;工位⑦为定子片与本体冲切分离。
该级进模的主要功能是将定子片与转子片同时冲出,并实现材料的高效利用。
在模具的结构方面主要有如下特点:一是模具导料系统设计了双侧导板机构和钢珠弹顶,带料在导板内侧连续送进,与钢珠弹顶中机构的钢珠成点接触,使带料在高速、连续的送进冲压中实现材料的平滑移动;二是模具中各凸模的导向精度由卸料板来保证。
为了保证卸料板的运动精度,在卸料板与凸模固定板之间设置了对称分布的4个辅助内导柱内导套;三是在模具底面转子片冲切落料型孔部位设计了4个螺孔,用以固定收集落料后的转子片装置,以避免与其他废料混合。
本模具与工步为80mm的辊式自动送料机进行配合送料,提高了生产自动化程度和送料定距的精度,从而实现了高质量、高效率的生产。
关键词:定子片转子片级进模多工位冲裁ABSTRACTThe design topic mainly originates from the production frontline in Generator Manufacturing Group of Xiangtan Electric Company, which has 70 years in the line of generator manufacturing. The material the stator and rotor plate use is electrical silicon steel sheet.The full text is to express the design idea and structural characteristics in detail;Here are the main context: Though Combining the current development situation of stamping die ,with the main technical of stamping die design; we focus on the motor stator and rotor plate to do the process analysis; doing the stamping process calculation, including the punching pressure, pressure center and so on; analyzing the reason of selecting the unloading device, positioning device, a material guide device of die structure and so on; describing the process of choose the right and reasonable press machine.Because of the stator and rotor plate are high complex and precise parts in the motor, so after careful and full consideration of the requirements of the place relationship between the stator lamination riveting hole and the hole of center axis, material flatness and die work intensity, we draw a seven station layout: Station 1—piercing pilot hole, 4 stator mounting holes, and the middle hole; Station 2—shool ping station; Station 3—rotor shape blanking station; Station 4—punching a stator inner slotted hole;Station 5—the air station ;Station 6—the outside shape arc of the stator cutting;Station 7—separation of stator plate and body. The main function of the progressive model is getting the motor stator and rotor plate out at one time,reaching the goal of the utter use of material.The main characters of the progressive mold structure:1.In the material guide system , bilateral plate mechanism and steel ball are included , with material in the plate medial continuous feeding, and the steel balls body point contacting with material, so that the strip can continuous to achieve smooth movement at high speed in the high punching stamping mold.2.The accuracy of each punching die in the mold can ensured by the stripper plate.In order to ensure the stripper plate motion accuracy , 4 auxiliary guide pillar and guide sleeve are distributed between the stripper plate and punching die fixing board .3.There are 4 screw holes in the bottom surface of the mold rotor punching blanking hole site , and the screw holes are used for fixing the collection after the blanking rotor device, in order to avoid mixing with other waste.The motor should be equipped with roller type automatic feeding machine in order to increase the automation level and feeding distance accuracy, realizing high quality, high efficient production.Keywords: stator plate rotor plate progressive punching die multi-station punching目录第一章前言...............................................................................................- 1 -1.1 概述........................................................................................................................ - 1 -1.2 冲压技术的进步.................................................................................................... - 1 -1.3 模具的发展与现状................................................................................................ - 2 -1.4 模具CAD/CAE/CAM技术 .................................................................................. - 4 -1.5 课题研究目标、拟解决的关键问题.................................................................... - 5 -1.6 课题创新................................................................................................................ - 6 - 第二章零件的工艺分析.............................................................................................................- 7 -2.1 冲件尺寸.................................................................................................................. - 7 -2.2 工件材料分析.......................................................................................................... - 8 -2.3 工件结构分析.......................................................................................................... - 8 -2.4 工件精度分析.......................................................................................................... - 8 -2.5 确定工艺方案.......................................................................................................... - 8 -2.6 排样...................................................................................................................... - 9 -2.6.1 排样方案分析................................................................................................ - 9 -2.6.2 计算条料宽度.............................................................................................. - 10 -2.6.3 确定步距...................................................................................................... - 10 -2.6.4 材料利用率.................................................................................................. - 10 - 第三章冲压工艺计算...................................................................................................... - 12 -3.1 冲压力计算............................................................................................................ - 12 -3.1.1 冲裁力计算.................................................................................................. - 12 -3.1.2 卸料力计算................................................................................................ - 13 -3.1.3 冲压总力...................................................................................................... - 13 -3.2 压力中心计算........................................................................................................ - 13 -3.3 模具工作部分尺寸及公差.................................................................................... - 14 - 第四章模具结构形式的选择 .............................................................................................- 22 -4.1 模具类型及选择.................................................................................................. - 22 -4.2 卸料装置.............................................................................................................. - 22 -4.3 定位装置及精度.................................................................................................. - 23 -4.4 导料装置.............................................................................................................. - 23 -第五章主要零部件设计 ........................................................................................................- 25 -5.1 凹模的设计............................................................................................................ - 25 -5.1.1 凹模的结构.................................................................................................. - 25 -5.1.2凹模厚度H的计算 ...................................................................................... - 25 -5.1.3 凹模长度和宽度.......................................................................................... - 25 -5.1.4 凹模材料的选用.......................................................................................... - 25 -5.1.5 凹模的固定方法.......................................................................................... - 26 -5.1.6 切断轮廓线到凹模边缘的尺寸.................................................................. - 26 -5.1.7 螺孔到凹模孔、圆柱销孔到螺孔的尺寸.................................................. - 26 -5.1.8 螺孔间距[1]................................................................................................... - 26 -5.2 凸模的设计.......................................................................................................... - 26 -5.2.1 凸模的长度................................................................................................ - 26 -5.2.2 凸模的材料.................................................................................................. - 27 -5.2.3 凸模的固定.................................................................................................. - 27 -5.2.4 凸模的强度计算.......................................................................................... - 27 -5.3 凸模固定板设计.................................................................................................... - 27 -5.4 卸料板设计............................................................................................................ - 28 -5.4.1 卸料板与凸模间隙.................................................................................... - 28 -5.4.2 卸料板尺寸................................................................................................ - 28 -5.4.3 卸料版台肩的高度.................................................................................... - 28 -5.5 导料和承料装置.................................................................................................... - 29 -5.5.1 导料板的尺寸.............................................................................................. - 29 -5.5.2 承料板.......................................................................................................... - 30 -5.6 模柄设计................................................................................................................ - 30 -5.6.1 模柄结构...................................................................................................... - 30 -5.6.2 模柄尺寸...................................................................................................... - 31 -5.7 卸料弹簧的设计.................................................................................................... - 31 -5.8 紧固件.................................................................................................................. - 32 -5.9 凹模固定板............................................................................................................ - 34 -5.10模架以及其他零部件的选用............................................................................... - 34 -5.10.1 模架设计.................................................................................................... - 34 -5.10.2 内导向装置设计........................................................................................ - 34 -5.10.3 模具零件的选材[7]..................................................................................... - 35 -5.10.4 零件的热处理工艺设计............................................................................ - 36 - 第六章校核模具闭合高度及压力机有关参数 ........................................................- 38 -6.1 冲压设备的选定.................................................................................................... - 38 -6.2 校核模具闭合高度.................................................................... 错误!未定义书签。
爪极型步进电机内部结构
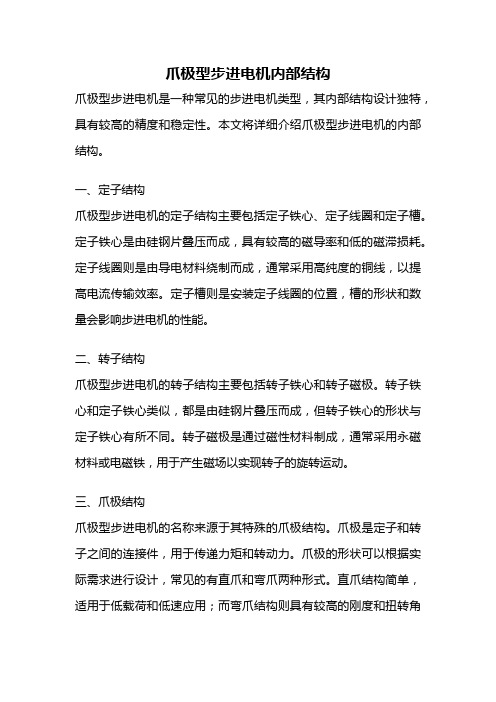
爪极型步进电机内部结构爪极型步进电机是一种常见的步进电机类型,其内部结构设计独特,具有较高的精度和稳定性。
本文将详细介绍爪极型步进电机的内部结构。
一、定子结构爪极型步进电机的定子结构主要包括定子铁心、定子线圈和定子槽。
定子铁心是由硅钢片叠压而成,具有较高的磁导率和低的磁滞损耗。
定子线圈则是由导电材料绕制而成,通常采用高纯度的铜线,以提高电流传输效率。
定子槽则是安装定子线圈的位置,槽的形状和数量会影响步进电机的性能。
二、转子结构爪极型步进电机的转子结构主要包括转子铁心和转子磁极。
转子铁心和定子铁心类似,都是由硅钢片叠压而成,但转子铁心的形状与定子铁心有所不同。
转子磁极是通过磁性材料制成,通常采用永磁材料或电磁铁,用于产生磁场以实现转子的旋转运动。
三、爪极结构爪极型步进电机的名称来源于其特殊的爪极结构。
爪极是定子和转子之间的连接件,用于传递力矩和转动力。
爪极的形状可以根据实际需求进行设计,常见的有直爪和弯爪两种形式。
直爪结构简单,适用于低载荷和低速应用;而弯爪结构则具有较高的刚度和扭转角度,适用于高载荷和高速应用。
四、传感器结构为了提高步进电机的控制精度和稳定性,常常在爪极型步进电机中加入传感器结构,用于检测转子的位置和运动状态。
常见的传感器包括霍尔元件、光电传感器等,通过与转子上的标志物相互作用,可以实时监测转子的位置信息,并根据需要进行调整和控制。
五、驱动电路爪极型步进电机的内部结构还包括驱动电路,用于控制电机的转动和运动。
驱动电路通常由逻辑电路和功率电路组成,逻辑电路负责接收和处理控制信号,将其转化为适合步进电机驱动的信号;功率电路则负责为步进电机提供足够的电流和电压,以实现电机的正常运转。
爪极型步进电机的内部结构包括定子结构、转子结构、爪极结构、传感器结构和驱动电路。
这些结构相互协作,使得步进电机能够实现精确的旋转运动。
掌握了步进电机的内部结构,可以更好地理解其工作原理和应用特点,为实际应用和故障排查提供参考和指导。
电动机定子铁芯冲压模具设计
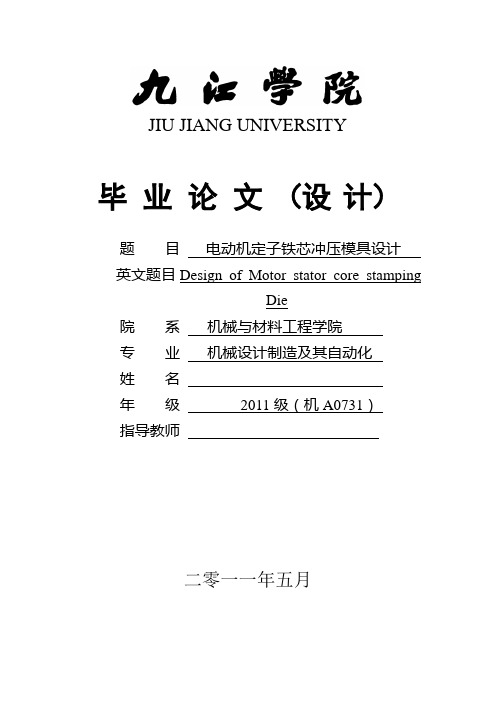
JIU JIANG UNIVERSITY毕业论文(设计)题目电动机定子铁芯冲压模具设计英文题目Design of Motor stator core stampingDie院系机械与材料工程学院专业机械设计制造及其自动化姓名年级2011级(机A0731)指导教师二零一一年五月摘要随着科学技术的不断进步和工业生产的迅速发展,冲压加工已成为机械制造也中先进高效的加工方法之一,其应用范围十分广泛,不仅可以加工金属材料,而且可以加工非金属材料,在现代制造业如汽车,拖拉机,农业机械,电机,电器,仪表,化工,玩具以及日常生活用品的生产方面,都占有十分重要的地位。
本文简单介绍了冲压模具的概念、基本特点、现状及发展方向,阐述了冲压模具的设计原理,并介绍了冲压模具的一般设计流程。
在模具设计过程中,首先通过对定子冲压片做工艺性分析,确定冲压工艺方案,初步确定模具的结构型式,进行凸、凹模刃口尺寸计算,对模具零部件的设计及选用,完成了定子冲压片冲压模具的设计。
在本文的设计过程中,主要详细介绍了本产品冲压工艺方案的分析确定、模具刃口尺寸的计算方法,以及模具非标准零部件的设计计算和标准零部件的设计及选用。
最后,通过计算机辅助设计软件,完成了定子冲压片的模具设计,绘制了定子冲压模具的总装图和模具的主要零部件图,并对主要零部件进行加工工艺的分析设计,最后还对本套模具进行装配设计,完成了该模具设计的一整套流程。
【关键词】模具设计;工艺性分析;模具工艺方案论证;工艺计算;制造工艺AbstractWith the continuous progress of science and technology and the rapid development of industrial production, Stamping processing has become one of the advanced and efficient processing methods, whose application scope is very extensive. Not only can processes metal materials, but also non-metallic material, Stamping processing has becoming more and more important role in modern manufacturing industry such as automotive, tractors, agricultural machinery, motor, electric appliances, instruments, chemical, toys and daily production. This paper briefly introduced the stamping mould concept, basic characteristics, current situation and development direction, and also introduced the design principle of stamping mould, and general design process of stamping mould.In the design process, through anglicizing the process of stator, the structure of mold is determined tentatively. Convex and concave-edge size is calculated; the mold parts are designed and selected. At last, the design of the stator stamping die were completed. In the design process, mainly introduces to identify the product of stamping process program analysis, the calculation method of blade size mold and die non-standard parts design calculation and standard parts design and choose. Finally, through computer aided design software, completed the stator stamping mold design, draw a floor drain stamping mold assembly and the main parts drawing to carry on the processing technology of main componentanalysis and design, and finally designed this set of mold assembly , completed the mold design set of processes.【Key words】Mold design ;usability analysis;mould process scheme comparison;process calculation;manufacturingprocess目录摘要 (Ⅰ)Abstract (Ⅱ)前言 (1)第1章绪论 (2)1.1 冲压的概念、特点 (2)1.2 冲压技术的现状及发展方向 (3)1.3 冲压的基本工序及模具结构 (5)第2章冲压模具的设计 (7)2.1 零件的工艺性分析 (7)2.2 冲压工艺方案的确定 (8)2.3 模具结构式的初步确定 (9)2.4 主要设计计算 (12)2.5 主要零部件的设计计算与选 (18)2.6 绘制模具总装图和模具零部件图(附图) (22)2.7 小结 (22)第3章冲压模具主要零件的加工工艺设计及模具装配分析 (22)3.1冲压模具主要零件的加工工艺设计 (22)3.2模具装配分析 (23)结束语 (26)参考文献 (27)致谢 (28)前言现代模具工业有“不衰亡工业”之称。
电机定子铁心硅钢片的模具设计与制造

18D i e and M oul d Technol ogy N05.2008文章编号:1001—4934(2008)05—0018—03电机定子铁心硅钢片的模具设计与制造陈展(广州市高级技工学校,广东广州510410)摘要:针对电机定子铁心硅钢片的工艺特点,在分析级进模具与落料模具优缺点的基础上,设计了一套有弹性卸料装置的精密落料模;并介绍了该模具的结构特点、设计思路以及制造中应注意的问题。
关键词:定子铁心;硅钢片;落料模;模具结构中图分类号:TG386.2文献标识码:BA bst r ac t:A cc or di ng t o t he t echni cal charact er i s t i cs of m ot or s t at or co r e m ad e of s i l i con—s t e el pl at e,a s et of pr eci s e bl anki ng di e w i t h a f l exi b l e s t r i p per w as de si gne d t hr ough ana l y-zi ng t he adva nt a ge s a nd di sadvant age s of bo t h pr ogr e s s i ve di e a nd bl anki ng di e.T he char ac-t e ri st i c s of t he di e s t r uct ur e,t he des i gn i deas a nd m a t t er s ne e d at t en t i on i n t he m anu f act u ri ng pr oc es s w e r e al l i nt roduced.K e yw or ds:st at or cor e;s i l i con—s t eel pl a t e;b l anki ng di e;di e s t r uct ur e0引言电动机定子的作用是用来产生磁场和作电动机的机械支撑。
电动机定子铁芯冲压模具设计
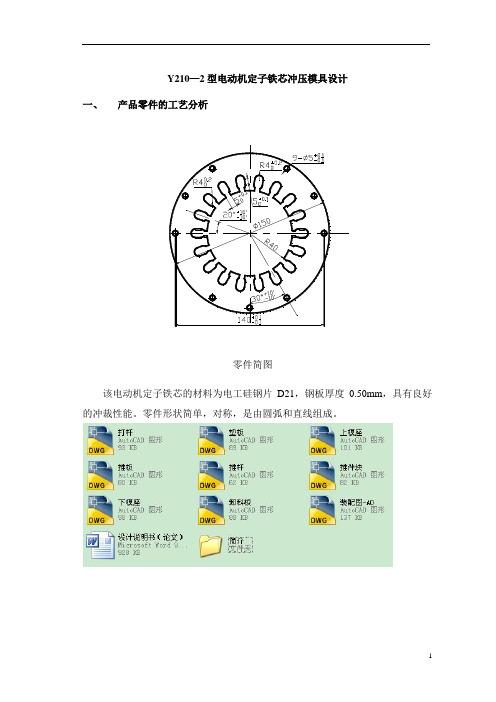
Y210—2型电动机定子铁芯冲压模具设计一、产品零件的工艺分析零件简图该电动机定子铁芯的材料为电工硅钢片D21,钢板厚度0.50mm,具有良好的冲裁性能。
零件形状简单,对称,是由圆弧和直线组成。
对于冲小孔Φ5,冲复杂圆孔Φ80,按照冲压手册一般冲孔模对该材料(钢 <400MPa)可以冲压的最小的孔径为d≧t=0.5mm,因而小孔符合工艺要求。
最小孔边距为b=3.5mm≧t,因而符合孔边距工艺要求,以上分析均符合冲裁工艺要求。
由表1、2 查出冲裁件内外所能达到的经济精度为IT11,孔中心与边缘距离尺寸公差为±0.6,对于孔心距公差为±0.1,将以上精度与零件简图中所标注的尺寸公差相比较,可认为该零件的精度要求能够在冲裁加工中得到保证,其他尺寸标准、生产批量等情况,也均符合冲裁的工艺要求,故决定采用冲孔落料复合冲裁模进行加工,且一次成形。
二、模具类型的确定常见的模具形式可分为单工序模、复合模和级进模三种。
确定模具形式,应以冲裁工件的要求、生产批量、模具加工条件为主要依据。
4冲压生产批量与合理模具形式见表3 ,单工序模、级进模和复合模的比较见表通过以上关系比较,此工件是大批量生产,故采用冲孔落料复合冲裁模进行加工,且一次冲压成行。
所谓复合模具结构,就是在冲床的一次行程内,完成两道以上的冲压工序。
在完成这些工序过程中,冲件材料无需进给移动。
复合模具结构的优点(1)制件精度高。
由于是在冲床的一次行程内,完成数道冲压工序。
因而不存在累积定位误差。
使冲出的制件内外形相对位置及各件的尺寸一致性非常好,制件平直。
适宜冲制薄料和脆性或软质材料。
(2)生产效率高。
(3)模具结构紧凑,面积较小。
复合模具结构的选用原则:只有当制件精度要求高,生产批量大,表面要求平整时,才选用复合模具结构。
三、冲裁间隙的选用在冲裁模的设计中,凸凹模间隙的合理选取,是保证模具正常工作、提高冲片质量、延长模具寿命的一个关键因素。
电机结构分析,零部件分解

后盖在耳朵上攻螺 孔用于安装风叶。
1.4 端盖
端盖多用铸铁铸成,材质一般为HT200,HT150;用螺栓固定在机座两端。 端 盖按照安装形式分为法兰和前端盖。 主页 目录 退出
2016/7/26
门盖
材质:HT150/HT200。 用于180及以上电机的安装。 可用于控制电机出现大的窜动。 开放式轴承油脂的密封,防止 泄漏到电机外部和转子内部。
主页
目录
退出
2016/7/26
1.2.4 引出线
1.2.5 绑扎带
具有优秀的耐热性、机械强度、 柔软性和易浸渍性能,以及良好 的耐氟、耐油性能,适用于电动
电机引出线组成: 镀锡铜结构导体 隔离层 橡皮绝缘体 丁橡皮护套层 (注:根据用户所需可制成黑,白 ,绿和红等多种颜色,色泽鲜艳,持久)
3.8.1 接线柱 3.8.2 连片 3.8.3 接地牌 3.8.4 冷压端子 3.8.5 接线图 3.8.6 电缆防水接头 3.8.7 波纹管 3.9 紧固件 3.9.1 波形片 3.9.2 挡圈 3.9.3 螺钉 3.9.4 螺母 3.9.5 平垫 3.9.6 弹性挡圈 3.9.7 铆钉 3.9.8 吊环
2016/7/26
2. 转子
1.铁心:由外周有槽的硅钢片叠成。 2.转子绕组:铁心槽内铸铝形成。 3.轴承:外购标准件。 4.转轴:买圆钢金属加工而成。 转子在旋转磁场作用下,产生感应电动势或电流。
主页 目录 退出
2016/7/26
2.1 转子铁心
2.2 转子绕组
鼠笼转子
由转子冲片叠压而成。转子 也叫鼠笼转子。 冲片也是用矽钢片冲压成型。 一般由铝 浇注入转子 铁心槽内并 由两端端环短接而成。
电机定转子片冲压工艺及模具设计讲解
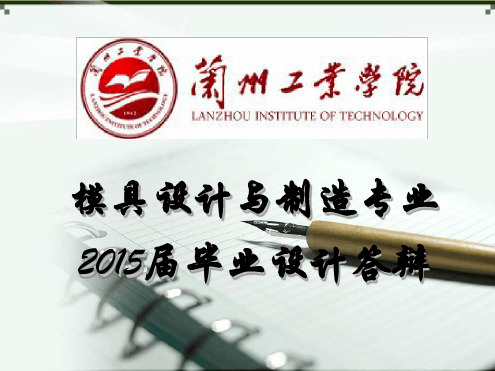
三、模具设计及主要的尺寸计算
1—下模座; 2、15—销钉; 3—凹模; 4—套;5—导柱; 6—导套; 7—上模座; 8—卸料 板9—橡胶; 10—凸模固定板; 11 —垫板; 12—卸料螺钉; 13—凸模; 14—模柄; 16、 17—螺钉
冲裁模典型结构与模具总体设计尺寸关系图
1.模具类型的选择
复合冲压是在压力机滑块的一次 行程中,在同一位置上,使材料顺 序完成几个冲压工序的方法,如落 料—冲孔、落料—拉深、落料—拉 深—冲孔、冲孔—翻边等复合工序, 该类模具称为复合模。生产现场应 用较多的有落料—冲孔复合模、落 料—拉深复合模和落料—拉深—冲 孔复合模等。
1)复合冲裁模的结构形式 复合冲裁模有倒装、顺装两种
结构形式。 倒装式复合模结构简单,使用
方便,应用较为广泛。 2)落料—拉深复合模
落料—拉深—冲孔复合模 3)带浮动模柄的落料—冲孔复合模
4)翻边复合冲模
2.工作部分的结构和尺寸的确定
工件的外形落料凹模采用整体 结构,直刃口形式。这种刃口强度 较好,孔口尺寸不随刃口的刃磨而 增大,适于形状复杂、精度高的工 件向上顶出的要求。
电机定、转子冲片工艺方案的种类
在冲裁工艺分析和技术经济分 析的基础上根据冲裁件的特点确定 冲裁工艺方案。冲裁工艺方案可分 为单工序冲裁、复合冲裁、级进冲 裁。
单工序冲裁是在压力机一次行 程,在模具单一的工位中完成单一 工序的冲压;复合冲裁是在压力机
一次行程中,在模具的同一工作位 置同时完成两个或两个以上的冲压 工序;级进冲裁是把冲裁件的若干 个冲压工序,排列成一定的顺序, 在压力机一次行程中条料在冲模的 不同工序位置上,分别完成工件所 要求的工序,在完成所有要求的工 序后,以后每次冲程都可以得到一 个完善的冲裁件,组合的冲裁工序 比单工序冲裁生产效率高,获得的
简述永磁同步电机的结构

简述永磁同步电机的结构永磁同步电机是一种使用永磁材料作为磁场源的电机,具有高效率、高功率密度和高控制精度等优点,被广泛应用于工业生产、交通运输和可再生能源等领域。
下面将对永磁同步电机的结构进行简述。
首先,永磁同步电机的主要组成部分包括定子、转子和永磁体。
定子是电机的静态部分,由定子铁心和绕组组成。
定子铁心是由硅钢片叠压而成的,以减小铁损和涡流损耗。
绕组则由多组线圈绕制而成,用于产生磁场。
定子线圈通电时产生的磁场与转子磁场相互作用,从而产生转矩。
转子是电机的动态部分,由转子铁心和永磁体组成。
转子铁心同样由硅钢片叠压而成,以减小铁损和涡流损耗,并提高电机的动态特性。
永磁体则是永磁同步电机的核心部件,用于产生稳定的磁场。
在永磁同步电机中,常见的永磁体材料有永磁铁氧体、钕铁硼和钴铁硼等。
这些材料具有高磁能积、高矫顽力和高磁导率等特点,使得电机具有较高的磁场强度和较低的磁场衰减。
除了定子和转子之外,永磁同步电机还包括电机的支承结构、端盖和轴等部件。
支承结构用于安装和支撑电机的各个部分,以保证电机的正常运转。
端盖则用于封装电机的内部部件,保护电机免受外界环境的影响。
轴则用于连接电机的转子和负载,传递电机产生的转矩。
关于永磁同步电机的结构参考内容,可以参考以下内容:1.《机械设计基础》(赵光华,机械工业出版社)2.《电机设计与制造》(林迈勇,机械工业出版社)3.《永磁同步电机技术及应用》(丁顺利,机械工业出版社)4.《永磁同步电机及其控制应用》(邓润树,机械工业出版社)5.《永磁同步电机理论与应用》(冉有华,中国电力出版社)这些参考内容在其中介绍了永磁同步电机的结构、工作原理、控制方法和应用等方面的内容,对于深入了解永磁同步电机具有较高的参考价值。
在具体选择参考内容时,可以根据自己的需求和背景选择相应的内容。
风力发电机定子冲片及铁心制作培训材料
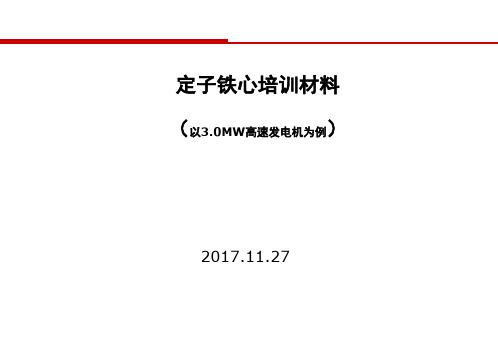
意义:保证高质量完成铁心叠装的必要条件
准备工作
内容: 叠装前各部件的检查 要点: 1、检查定子压圈合格证齐全,定子压圈编号记录齐全,检查压圈表面无气 孔、夹渣、裂纹及缺陷 。
2、检查齿压板合格证齐全,点焊牢固,外观检查无气孔、夹渣、裂纹及缺 陷。
3、检查通风槽板合格证齐全;平面度符合图纸要求;点焊牢固。
2. 片间压力符合图纸要求
3. 焊缝等级满足图纸要求
叠装现场准备
1、工艺文件和图纸(注意更新) 2、工具工装的准备和清理 3、操作者工作记录本
叠装现场清理
要点:所有进入叠装现场的冲片和工具、工装都必须是经过清理的,并保证叠 装周围环境的清洁,与叠装无 关的东西都要清出现场 后果:影响铁心的叠装速度和叠装质量
焊接
内容:焊接机座上筋和压圈及冲片的连接 要点:1、焊接前对机座筋焊接区域周围直线距离30mm范围内进行打磨作业,去 除油漆。
2、冲片和机座筋的连接焊接要对称焊接,机座筋端部与压圈焊接采用必要 的手段进行成型作业。
3、焊后要进行焊渣的彻底清理。 4、焊接时必须对铁芯进行保护。 后果:会产生应力变形或焊接不牢固,电机性能受到影响。
工艺准备 下料 落料
首件检查
铁芯冲片 YSZ20-
Hale Waihona Puke 去毛刺铁芯硅钢 技术B版
检查
涂漆:用涂漆机涂漆,需要检查漆膜厚度、绝缘电阻
附着力等参数 注意硅钢片搬运中的保护
首件检查 涂漆
铁芯硅钢 技术B版
准备工作
内容: 工艺准备 要点: 1、检查硅钢卷合格证齐全,确认牌号和图纸牌号一致 ; 2、检查热轧钢卷合格证齐全,确认牌号和图纸牌号一致 ; 3、模具确认,确认模具是落料成型模; 目的:避免不符合要求的材料流入,为下工序做准备 意义:完整的检测记录和报告是产品质量跟踪的依据,也是以后质量故障分析 的原始凭证
电机定、转子铁心自动叠装模设计

电机定、转子铁心自动叠装模设计1.引言铁心是电机、变压器等产品的重要零件之一,一般由导磁率高、低损耗的硅钢片制成,为了减少损耗,在铁心轴线方向上由厚度为0.35mm 或0.5mm的硅钢片组成。
因此,一台产品的铁心可由几片至几百片硅钢片组成;铁心冲片的生产用量非常大,同时,对铁心的质量要求也很高。
铁心叠装后要紧密,叠压力要求在100-150N,铁心叠装质量的好坏将直接关系到产品的性能。
随着模具技术的发展,铁心冲片的加工由单冲模、复合模的冲裁,发展到用高速级进模冲裁。
模具的结构形式从单列散片级进冲模,发展到双列、三列等多列自动叠片高速级进冲模。
冲裁速度可达280-400次/min ,模具一次刃磨寿命在300万次以上,模具总寿命高达亿次以上。
铁心叠装技术已由传统的手工理片,发展到自动叠片技术。
它去除了人工理片、加压、铆钉或螺钉联接、氩弧焊等工艺,使冲片在副模具中完成冲片叠装工艺。
大大减轻了工人的劳动强度,提高了劳动生产效率,保证铁心冲片的叠装质量。
自动叠片技术现已广泛应用于电机定、转子冲片铁心,变压器冲片铁心等产品中。
2.铁心自动叠装技术铁心自动叠装是在1副多工位级进冲模中实现。
叠装的原理是采用按扣的原理,通常由2次冲压来完成冲片的叠装。
冲裁时,先在条料上冲制出凸起,然后在落料的同时,后一冲片的凸起下部在铆紧凸模向下运动的冲压力作用下,扣入前一冲片凸起上部,即叠压。
为使铁心能完成叠装并承受一定的叠压力,铆合的上部压力来自落料凸模,下部支撑力则来自落料凹模下面的收紧套,利用落料冲片回弹造成的冲片外缘与收紧套内壁产生的挤压摩擦力,使冲片与冲片紧密地扣接在一起完成叠装铆紧。
另有种下部的支撑力来之于冲床垫板下部的液压缸。
冲裁过程中,液压缸上的托盘随着叠片的不断增高而逐步下移,当叠片达到设定片数时,液压缸驱动托盘迅速下降到与冲床垫板等高,模具下的横向气缸开始工作,将产品推出模外,然后复位,即完成一个工作循环。
3.铁心叠装形式(1)直铆接。
毕业设计论文:硅钢片的模具设计

冲压课程设计说明书机械工程系07级模具设计与制造专业一班题目:硅钢片的模具设计姓名:李卫民学号:200703220119指导老师:叶东老师2009年7月14日目录课程设计任务书 (3)前言 (4)第一部分设计题目 (5)第二部分冲裁工艺分析及方案确定 (5)一、零件的工艺分析 (5)二、确定工艺方案 (6)三、冲裁件的排样设计 (6)第三部分主要工艺参数计算 (7)一、冲裁力的计算 (7)二、模具压力中心的确定 (9)第四部分冲裁模主要零部件的结构设计与选择 (10)一、凸、凹模间隙值的确定 (10)二、计算各主要零件的尺寸 (10)第五部分设计体会和参考文献 (15)一、设计体会 (15)二、参考文献 (16)课程设计任务书一、本课程设计的目的1.学会具体运用《冲压工艺及模具设计》课程内容;2.了解并掌握冲压模具设计的一般程序;3.能够熟练的运用有关技术资料,掌握冲压工艺计算方法;4.能根据工件特点选择合适的冲压模具结构;5.训练设计冷冲压模具的能力,为以后的工作打下初步的基础。
二、本课程设计的任务及要求根据所设计工件的尺寸、形状、批量等原始数据和要求,每个人独立设计,电脑绘制完成一套冲压模具。
具体包括:1.模具装配图一张;2.非标准模具零件图各一张;3.设计说明书1份。
三、设计说明书内容要求设计说明书中应文图并茂,应包括:必要的分析,设计、计算及其依据出处、结构设计示意图等。
具体要求如下:1.设计依据、原始数据;2.冲压加工工艺性分析;3.冲压工艺计算;4.冲压工艺方案比较;5.模具结构设计计算;6.工艺力、零件强度较核等设计计算;7.设备选择计算。
前言冷冲压模具设计是在我们模具设计专业与制造专业学生在学完基础理论课、技术基础课以及大部分专业课的基础上,所设置的一个重要的实践性教学环节,这是我们在进行毕业设计之前对所学各课程的一次深入的综合性的总复习,也是一次理论联系实际的训练。
其目的是:1、综合运用本专业所学课程的理论和生产实际知识,进行一次冷冲压模具设计工作的实际训练,从而培养和提高学生独立工作的能力。
电机定子铁心硅钢片的模具设计与制造

电机定子铁心硅钢片的模具设计与制造电机的设计方式有很多种,但最主要的定子设计只有一种,电机定子当中三部分,第一部分为定子铁心,第二部分为绕组,第三部分为机座,这三部分链接在一起进行组装才能拼接成为最后的电机定子。
而定子铁心的硅钢片在使用冲压后会形成细微的毛刺,这种毛刺会间接地影响到电磁场,降低电机的功率,更严重的是还会对设备产生破坏,最终导致设备故障,如何能够更好地生产设备这就需要我们在模具的设计和制造当中来着手进行考虑。
1 定子铁心技术要点(1)首先,对于定子铁心的冲片尺寸要把握精确,长度、通风槽等设备的尺寸要符合设计规定。
(2)其次,定子铁心的冲片表面应毫无瑕疵,最好选择无毛刺的冲片进行组成,而铁心的重量及各指标都要符合电机安装要求。
(3)最后,定子铁心的通同心轴距应当为0.025 mm左右,同时对设备进行压装后冲片不应该出现波浪形。
定子铁心的边缘以及齿部不能有明显的翘起,整体设计不能有明显的歪斜,进而保证其中心能够很好地对称。
2 明确设计方案初步进行研究根据上面的分析而得出结论,由于本部件自身的特点和需求量的原因,我们考虑应该采用级进模,这样能够提高生产效率。
级进模具就是将工件分别冲出若干个槽口以及销口,待冲出若干个槽口与销口后将剩余的条料进行冲外形,但级进模具看似便利,但还是有缺点存在的。
它的缺点:一是在进行出料与进料的过程当中由于级进模没有弹顶装置,非常容易造成在冲料后槽口的齿部回弹。
二是由于材料的硬度高,非常容易对凹凸模具产生破坏,减少使用寿命。
三是工件的本身对于同心度要求非常高,在采用了级进模设计和冲床后的安装与制造方面都有很大的困难,同时也不利于保证设计出的工件尺寸符合标准。
四是由于工件的自身尺寸比较大,在使用过后有可能超出压力机的安装尺寸,对后期的组装造成不便。
所以采用具有弹性的顶料和落料模才能更好地解决其带来的这些缺点。
3 模具各部位零件的设计在对模具设计的时候,一般因为工件的尺寸比一般规格的大,所以采用对角推送和弹性顶料的原理去进行设计,这样能最大程度上避免冲片回弹过程中对设备造成的损害。
定子铁心材料在电机性能中的作用

定子铁心材料在电机性能中的作用电机是现代社会中必不可少的电动机械设备,它能够将电能转化为机械能,广泛应用于各行各业。
其中,定子是电机的重要组成部分之一,而定子铁心材料的选用对电机性能起着重要作用。
本文将从定子铁心材料在电机性能中的作用角度进行探讨。
定子铁芯是电机中用于传递电磁能量的关键部件之一,其主要作用是提供一个磁路,使磁场能量能够顺利流动。
定子铁芯材料的选择直接关系到电机的性能和效率。
常见的定子铁心材料主要有硅钢片和铸铁。
硅钢片是一种特殊冷轧电工钢,由铁、硅、碳以及其他添加元素组成,其具有高磁导率、低磁滞损耗和低涡流损耗等特点。
这种材料的特殊结构使得磁场能够在其内部顺利传递,并且减少了磁能的损失。
因此,采用硅钢片作为定子铁心材料可以显著提高电机的效率和性能。
一方面,硅钢片具有较低的磁滞损耗,可以有效避免磁场能量在定子铁心中的损耗。
磁滞损耗是指材料在磁场作用下发生磁化反应时产生的能量损耗,它会导致电机的能量转化效率降低。
而硅钢片由于其特殊的晶粒结构和成分组成,能够减少磁滞损耗的发生,提高电机的效率。
另一方面,硅钢片的低涡流损耗也使得电机性能得到了明显提升。
涡流是指当导体在磁场中运动时,由于感应电动势的作用,形成的涡流。
在电机运行过程中,由于定子铁心处于强磁场中,导致定子铁心中涡流的产生。
这些涡流会产生磁场能量的损耗,从而降低电机的效率。
而硅钢片由于其特殊的导磁性能,可以有效降低涡流损耗的发生,提高电机的性能。
除了硅钢片之外,铸铁也是一种常用的定子铁心材料。
与硅钢片相比,铸铁成本较低,易加工,但其磁导率较低,容易产生涡流损耗和磁滞损耗。
因此,在一些对电机性能要求较低的场合,铸铁常常被作为定子铁心材料使用。
总结起来,定子铁心材料在电机性能中起着重要的作用。
硅钢片的选用能够有效提高电机的效率和性能,通过减少磁滞损耗和涡流损耗,提高能量转化效率。
而铸铁则成本较低,适用于对电机性能要求较低的场合。
在实际应用中,根据电机的具体要求和使用环境选择合适的定子铁心材料,不仅能够提高电机的性能,还能够节约能源,减少能源消耗。
硅钢片冲压模具设计

硅钢片冲压模具设计硅钢片冲压模具设计Silicon steel sheet stamping die design班级:学生姓名:学号:8指导教师:职称:导师单位:论文提交日期:课题名称:硅钢片冲压模具设计课题性质:设计,来源于生产实践系名称:机械工程系专业:班级:指导教师:学生姓名:毕业设计任务书一、课题名称:硅钢片冲压模具设计二、毕业论文(设计)主要内容:1、冲压工艺方案确定(冲压工艺性分析、工艺方案的确定)2、模具设计有关计算(冲裁力、压力中心、刃口尺寸);3、模具结构设计(凸凹模结构、标准模架、固定零部件、卸料零部件等);4、绘制模具装配图和非标准件的零件图(逐步完善和确定各零件的结构和尺寸、尽量选用标准组合结构和标准件);5、编写设计说明书;三、计划进度:第8周查阅资料,做好准备工作,冲压工艺方案确定第9周模具设计有关计算第10周模具结构设计;第11周选择标准模架,确定各个模板的尺寸;第12周绘制装配图、零件图,编写设计说明书;第13周论文答辩。
四、毕业论文(设计)结束应提交的材料:1、设计说明书(毕业论文)1份(5000字以上);2、装配图一份,非标准件的零件图2-3张。
指导教师教研室主任年月日年月日题目:冲压模具设计如下图所示,大批量生产,材料为DR510 ,t=1mm ,工件精度为IT9。
摘要在本次毕业设计中我的任务是硅钢片冲压模具设计,通过对零件的分析可知,该零件所用的材料是DR510,且为大批量生产,经过方案比较分析,选择复合冲压模具进行生产加工,既提高生产效率又经济实惠,而且模具设计和制造也相对于简单。
首先根据工件图算工件的展开尺寸,再根据展开尺寸算该零件的压力中心,材料利用率,画排样图,当所有的参数计算完后,对模具的装配方案,对主要零件的设计和装配要求都要进行分析。
在设计过程中除了设计说明书外,还包括模具的装配图,非标准件的零件图等等。
关键词:硅钢片;复合模;AbstractIn the graduation design in my choice of silicon steel, stamping mould design is based on the analysis of the components, it is known that the parts used materials is DR510, and for mass production, after scheme comparison and analysis choose compound stamping mould to process, which can improve the production efficiency and economic benefit, and mold design and manufacturing also relative to the simple. First of all, according to the workpiece figure calculate the workpiece expanded dimensions, and then based on the part of development size calculate pressure center, material utilization and painted strip layout diagram, when all the parameters are calculated to die after assembly scheme, the main parts of the design and assembly requirements are analyzed. In the design process in addition to the design specification outside, still include mold assembly drawings, non-standard parts graph, etc.Keywords:Silicon steel; Composite modulus;目录摘要 (6)Abstract (7)第一章绪论 (9)第二章冲压件工艺设计 (10)2..1冲裁工艺方案的确定 (11)2.2模具结构形式的确定 (12)第三章冲压工艺计算 (13)3.1排样设计 (13)排样方法的确定 (13)确定搭边值 (14)确定条料步距 (15)条料利用率 (15)3.2冲裁力的计算 (15)3.3冲压设备的初步选择 (17)3.4冲裁压力中心的确定 (17)3.5计算凸、凹模的刃口尺寸 (17)第四章主要零部件的设计 (20)4.1工作零部件的机构设计 (20)落料凹模 (20)冲孔凸模 (20)橡胶的设计与计算 (20)凸凹模 (21)4.2定位零件的设计 (21)卸料板的设计 (21)螺钉、销钉的选用 (21)模架及其他零部件的设计 (21)第五章校核模具闭合高度及压力机 (22)第六章绘制模具装配图及零件图 (23)附录 (26)致谢......................................... 错误!未定义书签。
电机铁心定转子片复合冲压工艺及模具设计
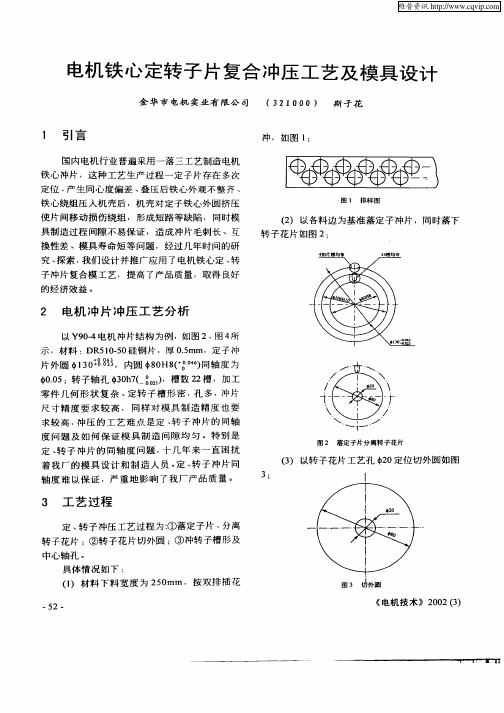
冲 ,如 图 1
铁 心 绕 组 压 入 机 壳 后 ,机 壳 对 定 子 铁 心 外 圆 挤 压 使 片 间 移 动 损 伤 绕 组 ,形 成 短 路 等 缺 陷 ,同 时 模 具 制 造 过 程 间隙 不 易 保 证 ,造 成 冲 片毛 刺 长 、互
出 ) 冲 裁 过 程 定 子 片 由弹 脱 料 装 置 采用 上 出料 方 ,
5 凸 凹模 l J 6 橡 胶 7 脱 料 板 8 定 子 脱 料 板 1 9 脱 料 板 1 凸 凹 摸 I 0 2J 1 下模 座 1
式 ,而 转 子 花 片 则 采 用 刚 性 打 料 在 冲床 上 行 时 通 过料杆 1 、打 料 板 2、脱 料 板 7打 落 ,并 由安 装在
中心轴孔 。 具体情况 如下 : () 材 料 下 料 宽 度 为 2 0 1 5 mm ,按 双 排 插 花
.
图 3
外 圆
52 .
《 电机 技 术 》2 0 3 0 2()
维普资讯
() 以转 子 片 工 艺 孔 定 位 冲 槽 形 及 中心 轴 孔 4
。
巾 . ;转子轴孔  ̄0 7一 ∞) 05 0 3h( : . ,槽数 2 槽 ,加工 2
零 件 几何 形状 复 杂 、 定转 子槽 形 密 , 多 , 片 孔 冲
尺 寸 精 度 要 求 较 高 , 同 样 对 模 具 制 造 精 度 也 要 求 较 高 , 压 的 工 艺 难 点 是 定 、 子 冲 片 的 同 轴 冲 转 度 问 题 及 如 何 保 证 模 具 制 造 间 隙 均 匀 。特 别 是 定 、 子 冲 片 的 同 轴 度 问 题 , 几 年 来 一 直 困 扰 转 十 着 我 厂 的 模 具 设 计 和 制 造 人 员 。 、 子 冲 片 同 定 转 轴 度 难 以 保 证 ,严 重 地 影 响 了 我 厂 产 品 质 量 。
电机定子硅钢片复合模具设计

中文摘要本设计是落料、冲槽复合模的设计。
设计说明书中简要概述了冲压模具目前的发展状况和发展趋势。
然后对工件进行了详细工艺性分析以及冲压方案的确定。
按照冲压模具设计的一般步骤,计算并设计了本套模具上的主要零部件,如:凸模、凹模、凸凹模、凸模固定板、垫板、凹模固定板、卸料板、挡料销、推件板、顶件块等。
模架采用标准模架,选用了合适的冲压设备。
关键词:落料, 冲槽, 复合模, 冲压模具, 凸凹模AbstractThis is a design of dropping and Notching composite die. The design overview the current development status and development trends of stamping die briefly. Then I conduct a detailed analysis of the work piece and determine the Stamping program. After finishing the Stamping die design in accordance with the general steps,I also design and calculations the main parts of this mold .For example, Punch, Die, Die punch, punch plate, plate, Die plate and dump plates, block information, marketing pieces of boards, blocks and other top pieces . At last I use standard mold and choice the suitable Stamping equipment.Keywords : dropping; Notching ; compound die; stamping die; Die punch.目录中文摘要 (Ⅰ)英文摘要 (Ⅱ)第1章绪论 (1)1.1 模具发展的现状和趋势 (1)1.2 模具设计的意义 (4)第2章工艺分析和方案的确定 (5)2.1 工件工艺性分析 (5)2.1.1 工件尺寸和精度 (5)2.1.2 工件的粗糙度和毛刺 (6)2.2 确定工艺方案 (6)第3章模具结构形式的选择 (8)第4章工艺计算 (9)4.1 毛坯尺寸计算 (9)4.2 排样、搭边和料宽以及材料的利用率 (10)4.2.1 排样 (10)4.2.2 搭边和料宽 (11)4.2.3 材料利用率 (14)4.3 冲裁力、卸料力及推件力的计算 (16)4.3.1 冲裁力的计算 (16)4.3.2 卸料力及推件力的计算 (17)4.4 压力中心的计算 (18)4.5 冲裁间隙 (19)4.6 凸、凹模刃口尺寸计算 (20)第5章冲模主要零件的设计 (30)5.1 凸模、凹模的设计以及模架的选择 (30)5.1.1 凸模的设计 (30)5.1.2 凹模的设计 (33)5.1.3 模架的选择 (35)5.2 定位零件的设计 (36)5.3 卸料和推件、顶件零件的设计 (39)5.4 固定与紧固零件 (41)5.5 导向零件 (43)第6章冲压设备的选择 (44)6.1 设备类型的选择 (44)6.2 设备型号的选择 (45)第7章绘制模具装配图和部分零件图 (47)第8章设计总结 (49)参考文献 (51)致谢 (52)四川理工学院毕业设计(论文)第一章绪论1.1 模具发展的现状和发展1.1.1 冲压在工业生产中的作用近年来,随着飞机、汽车、电子、仪表、日用工业品等工业的发展及少无切屑加工技术的应用,冲压加工技术得到了高速的发展。
特大型精密汽轮发电机定子铁心冲片模具的开发

性, 葛洲坝电站首批机组 机 和。 3 1 4机组改造增容后 达到 16 W,9台机 组增容后每年 4M 1
可 多发 电 8 5亿 k 。 . Wh
葛洲坝电站是华 中电网的骨干电站之一 。装机 2 1台, 总容量 27 M 其 中 1 15 W, 9台机 组 为 15 2 MW ,9 8年 全 部 投 产 发 电后 至 今 已运 行 了 2 多年 , 均 年 运 行 小 时 数 达 到 18 O 平 6 0 h以上 。 当于其 它 一般 水 电站机 组运行 3 00 相 0多年 。 为提 高葛洲坝机组安全稳定运行可靠性 , 配合三峡 电站运行 , 增加发 电效益, 充分发 挥 三峡 、 葛洲坝 电站在 电 网枢 纽 中心 的作 用 , 三峡 总公 司站在 两坝 尽早 发挥 最 大效 益的 高 度, 决定对葛洲坝电站 1 9台 15 W 机组进行增容改造 , 2M 改造增容后可增加 出力 40 W。 0M 20 0 5年 l 1月 2 3日和 2 日,1 9 ‘4和 组增容改造 工程分 别 开始施 工。 经过 四个 多月 3机
,
I I
I
I
I
I
+ 、
萄
c坷 1 m
划 日
“一 —
享
i
j
二
。 ’ <
:
‘
/谕
1 } 『
一
甫
上模 示意 图
图 2
维普资讯
《东方 电机) 06年 第 4期 20
2 3 没 有变 化 , 定性 相 当好 , 且该模 具第 一 稳 而
次的刃 磨寿 命 达 到 了 5 2万 片 。这 一 套 模
4 结
论
该 型模 具 完 工 后 经 使 用 厂 家试 冲验 收 , 全达 到 了要 求 。 尺 寸精 度 和 尺 寸一 完 致性 , 毛刺 等 全 部 在 0 0 .2的要 求 范 围 内 。
定子与转子片的冲压模具设计与制造

定子与转子片的冲压模具设计与制造定子与转子片的冲压模具是一种广泛应用于电机、发电机、风力机、电动工具等领域的模具。
冲压模具的设计和制造对产品的质量和成本有着至关重要的影响。
在本文中,将详细介绍定子和转子片的冲压模具的设计流程、制造工艺和注意事项。
一、冲压模具设计冲压模具的设计是整个制造过程中最关键的部分,它直接影响到后续的模具制造和产品加工质量。
在定子和转子片的冲压模具设计中,主要包括以下几个步骤:1.产品分析产品分析是冲压模具设计的第一步。
要根据定子或转子片的形状、尺寸和工艺要求绘制三维图形。
一般来说,定子和转子片的轮廓都是曲线型,需要借助CAD等设计软件进行绘制。
同时还需要确定工艺要求,包括模具的结构形式、材料选用、凸台数量和位置、裁冲顺序等。
2.冲压模具结构设计在产品分析的基础上,需要设计冲压模具的结构。
冲压模具包括模板、凸台、挡料、弹簧、导柱等组成部分。
其中,凸台是冲压过程中起关键作用的部分。
凸台数量和位置、材料和硬度以及凸台高度都需要根据产品的特点来进行合理的设计。
3.模具结构成型设计模具的结构成型设计是模具制造的重点。
主要包括模具组合方式、各零部件之间连接方式、螺栓的数量、位置和规格等。
这一步需要考虑到模具的可靠性、稳定性和快捷性,同时要考虑材料的节约和使用寿命。
4.模具细节设计模具细节设计主要包括凸模、凹模、挡料、导柱、弹簧等零部件的设计。
在这一步中,需要考虑以下几个方面:(1)凸模和凹模的配合度,包括毛坯的设计、修边和刀模的选用等。
(2)挡料的精度和调节方式,挡料是保证冲裁品质的重要部分。
(3)导柱的固定和调节方式,导柱主要起定位和锁定作用。
(4)弹簧的选用和布置方式,弹簧的作用是将模具保持稳定,并减小冲击力。
在弹簧的选择和布置过程中,需要考虑到模具重量、冲压力和工作环境等因素。
二、冲压模具制造完成冲压模具设计之后,就需要进行制造。
在制造过程中,需要根据设计要求进行材料选取、图纸制作和加工等工作。
- 1、下载文档前请自行甄别文档内容的完整性,平台不提供额外的编辑、内容补充、找答案等附加服务。
- 2、"仅部分预览"的文档,不可在线预览部分如存在完整性等问题,可反馈申请退款(可完整预览的文档不适用该条件!)。
- 3、如文档侵犯您的权益,请联系客服反馈,我们会尽快为您处理(人工客服工作时间:9:00-18:30)。
电机定子铁心硅钢片的模具设计与制造
作者:李俊
来源:《科技创新导报》2017年第15期
摘要:文章当中主要是根据电机定子铁心硅钢片所包含的特点对其进行研究,重点分析了模具与落料模具如何能更好地进行设计和配装。
同时设计了包含有卸料装置的精密落料模。
在这里还介绍了这种模具的结构构成和模具独有的特点,详细分析了在设计当中的思路以及在设计和后期制造当中所应当注意到的问题。
关键词:定子铁心电机硅钢片模具的构成
中图分类号:TG386 文献标识码:A 文章编号:1674-098X(2017)05(c)-0118-02
电机的设计方式有很多种,但最主要的定子设计只有一种,电机定子当中三部分,第一部分为定子铁心,第二部分为绕组,第三部分为机座,这三部分链接在一起进行组装才能拼接成为最后的电机定子。
而定子铁心的硅钢片在使用冲压后会形成细微的毛刺,这种毛刺会间接地影响到电磁场,降低电机的功率,更严重的是还会对设备产生破坏,最终导致设备故障,如何能够更好地生产设备这就需要我们在模具的设计和制造当中来着手进行考虑。
1 定子铁心技术要点
(1)首先,对于定子铁心的冲片尺寸要把握精确,长度、通风槽等设备的尺寸要符合设计规定。
(2)其次,定子铁心的冲片表面应毫无瑕疵,最好选择无毛刺的冲片进行组成,而铁心的重量及各指标都要符合电机安装要求。
(3)最后,定子铁心的通同心轴距应当为0.025 mm左右,同时对设备进行压装后冲片不应该出现波浪形。
定子铁心的边缘以及齿部不能有明显的翘起,整体设计不能有明显的歪斜,进而保证其中心能够很好地对称。
2 明确设计方案初步进行研究
根据上面的分析而得出结论,由于本部件自身的特点和需求量的原因,我们考虑应该采用级进模,这样能够提高生产效率。
级进模具就是将工件分别冲出若干个槽口以及销口,待冲出若干个槽口与销口后将剩余的条料进行冲外形,但级进模具看似便利,但还是有缺点存在的。
它的缺点:一是在进行出料与进料的过程当中由于级进模没有弹顶装置,非常容易造成在冲料后槽口的齿部回弹[1]。
二是由于材料的硬度高,非常容易对凹凸模具产生破坏,减少使用寿
命。
三是工件的本身对于同心度要求非常高,在采用了级进模设计和冲床后的安装与制造方面都有很大的困难,同时也不利于保证设计出的工件尺寸符合标准。
四是由于工件的自身尺寸比较大,在使用过后有可能超出压力机的安装尺寸,对后期的组装造成不便。
所以采用具有弹性的顶料和落料模才能更好地解决其带来的这些缺点。
3 模具各部位零件的设计
在对模具设计的时候,一般因为工件的尺寸比一般规格的大,所以采用对角推送和弹性顶料的原理去进行设计,这样能最大程度上避免冲片回弹过程中对设备造成的损害。
直接采用单向落料模能够有效地减少废弃材料的产生,在保证精度的同时能使模具自身的连接更加紧凑,进一步减少了模具的成本[2]。
同时在对这些主要工件进行设计的时候要考虑每种零部件都使用什么机床进行加工和制造,还要考虑制造后是否耐用以及便于安装。
分析各个模具的样式以及特点,对每一个不同的零件分批进行设计和组装,使其组装效果能够在最简单的前提下来完成。
3.1 慎重选择材料
由于硅钢片自身材料的原因,硅钢片自身密度比较大,同时冲裁出来的刃口也比较大,对各部件的性能要求都非常高,耐高温性强,而硅钢片的密度要比一般的材料强所以在这里就选择此类材料。
3.2 凸模与凹模的设计
在设计当中凸模可以直接用慢走丝线的方式对其材料进行切割,直接加工成凸模。
并在此基础上用稍钉进行定位,一般使用6~8个左右螺钉牢牢固定在垫板之中,凸模长度设计正常为卸料板自身的长度和橡胶加起来的总和再减去凸模凹入卸料板的1 mm为基准,而高度通常为50~60 mm,以这套模具的凹模为基准对凸模进行后期的配做。
在凹模当中利用整体的凹模对凹孔利用慢走丝线这种切割方式进行切割和加工。
待两种模具都设计完成后按数据测算结果,依次进行安装,安装中通常将压力中心与模柄中心相互重合。
3.3 对定位的零部件进行设计
定位零部件的设计与基础设计相同,都是采用导尺作为依据,材料之间的变化也没有太多的改变,预留出0.1 mm即可,在使用螺钉将导尺平稳地固定在凹模当中。
利用T10A的钢密度大的特性对其进行制作,而在热处理当中强度应保持在HRC50-60左右。
纵向挡销仍然留出3个档销的位置。
3.4 对于卸料装置的设计方式
在对定子铁心片进行冲裁以后大多数的工件都为封闭式曲线,这样非常容易在冲裁后使槽口慢性回弹甚至变形,其中特别是上文当中提到的齿部和外形翘起以引起设备故障,所以在对卸料装置进行设计的时候必须选择弹性卸料和弹性顶料的装置[3]。
一般在设计当中弹性顶料装置都是安装在下模的。
这样造成的结果就是,若是将橡胶放在凹模当中,会使凹模的模具厚度不断地增大,这样就会大大地加大投入的力度和模具的研究设计时间。
为了节省时间,将橡胶从内部移动到模具的外部,为了在达到一定寿命后便于更换,将其放在固定板下方。
弹性顶料板的厚度通常为25 mm以内,材料的热处理硬度选择HRC43~47左右,钢种则不可以再使用T10A种钢了,应该选择45#钢来使用。
在对顶料板安装过后对卸料板进行初步的研究,在进过研究发现卸料板使用厚度为30 mm 的厚度最为标准,材料的热硬度仍然是选择HRC43-47左右,钢种也用45#来代替普通钢。
3.5 对垫板进行材料选择和组装
在设计的结尾当中,在上垫板当中安装凸模,凸模的厚度一般选择30 mm左右。
下垫板对凹模起到了一个支撑的作用,厚度一般选择25 mm。
垫板与顶料和卸料板材料一样。
都选用45#钢以及热处理硬度为HRC43~47的材料。
这些步骤都完成后即可对整体的设备进行安装和调试了。
4 模具最重要的一点
此论文进行冲裁的是对硅钢片,所以这对外形和尺寸都有了很高的要求。
在对其冲裁后不能有毛刺的存在,这就给整个设计带来很大的难题。
首先要考虑的是在对凸模与凹模设计和制造当中尽可能地让二者使用一台线切割机床。
可以使用慢走丝多修两次,尽量做到在制成成品的尺寸与表面的粗糙度符合设计所需,设计过程当中减少机床所带来的影响,方便后期模具的安装与调配。
而最重要的是凸模与凹模在安装过后二者之间的缝隙必须均匀。
否则就会产生毛刺的存在。
所以在安装过程当中应先进行下模的安装,待下模安装好后对凸模进行调节,使凹凸模之间的缝隙均匀无误差后再对上模进行安装。
减少复装次数以免对模具造成损害。
5 结语
通过该方式设计的模具经后期检查符合设计理念,设计结构紧凑,同时既节省了材料、生产效率也得到了显著的提高。
经检验后设备在期维护以及设备调整方便有着显著的效果,生产大规模的定子铁心即便模具磨损了也非常容易进行更换,适合大范围的生产。
而利用此模具生产出来的定子铁心硅钢片在外形结构、尺寸重量当中完全符合现代所需的标准,在生产过后基本无毛刺或变形发生。
所以此种方式可行。
参考文献
[1] 黄豪杰,吴波,曹建树,等.电机定子硅钢片冲压模具设计及ANSYS有限元应力分析[J].模具技术,2015(1):40-46.
[2] 王旭.苏联对硅钢片硬质合金冲模寿命的探索[J].电机技术,1983(2):36.
[3] 陈国强.电机铁心定、转子片复合冲压工艺及模具设计[J].中小型电机,1999(1):44-45.。