2.精馏塔板型式和结构
精馏装置-板式塔的结构和原理
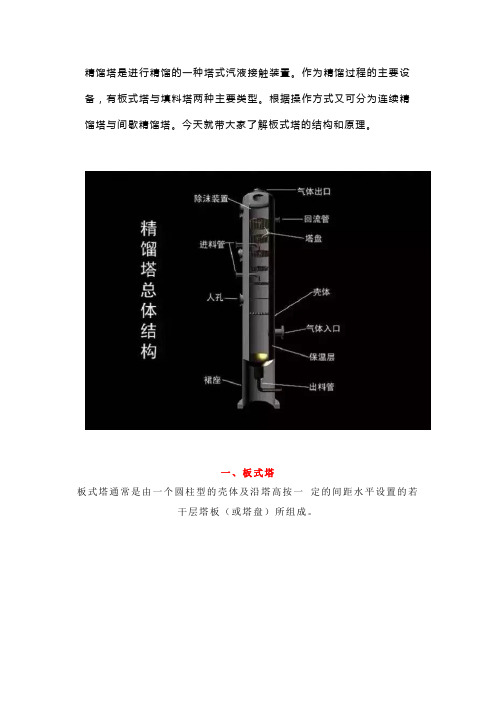
精馏塔是进行精馏的一种塔式汽液接触装置。
作为精馏过程的主要设备,有板式塔与填料塔两种主要类型。
根据操作方式又可分为连续精馏塔与间歇精馏塔。
今天就带大家了解板式塔的结构和原理。
一、板式塔板式塔通常是由一个圆柱型的壳体及沿塔高按一定的间距水平设置的若干层塔板(或塔盘)所组成。
板式塔实物图板式塔结构图二、板式塔塔板板式塔的塔板可分为有降液管及无降液管两大类。
有降液管的一般液体呈错流式,无降液管的液体呈逆流式。
板式塔由塔板不同可以分为泡罩塔、浮阀塔、筛板塔、舌型板和斜孔板等等。
其中以泡罩塔,浮阀塔和筛板塔在工业生产中使用最为广泛。
三、泡罩塔泡罩塔板是工业上应用最早的塔板,它由升气管及泡罩构成。
泡罩安装在升气管的顶部,分圆形和条形两种,以前者使用较广。
泡罩有f80、f100和f150mm三种尺寸,可根据塔径大小选择。
泡罩下部周边开有很多齿缝,齿缝一般为三角形、矩形或梯形。
泡罩在塔板上为正三角形排列。
泡罩边缘开有纵向齿缝,中心装升气管。
升气管直接与塔板连接固定。
塔板下方的气相进入升管,然后从齿缝吹出与塔板上液相接触进行传质。
由于升气管作用,避免了低气速下的漏液现象。
优点:该塔板操作弹性,塔效率也比较高,运用较为广泛。
缺点:是结构复杂,塔压降低,生产强度低,造价高。
四、筛板塔筛孔塔板简称筛板,其结构特点是在塔板上开有许多均匀小孔,孔径一般为3~8mm。
筛孔在塔板上为正三角形排列。
塔板上设置溢流堰,使板上能保持一定厚度的液层。
筛板塔的优点是结构简单、造价低,生产能力大,板上液面落差小,气体压降低,同时塔板效率较高。
缺点是操作弹性小,筛孔易堵塞,不宜处理易结焦、黏度大的物料。
五、浮阀塔浮阀是20世纪二战后开始研究,50年代开始启用的一种新型塔板,后来又逐渐出现各种型式的浮阀。
其型式有圆形、方形、条形及伞形等。
较多使用圆形浮阀,而圆形浮阀又分为多种型式。
其特点是浮阀取消了泡罩塔的泡罩与升气管,改在塔上开孔,阀片上装有限位的三条腿。
精馏塔的结构和工作原理
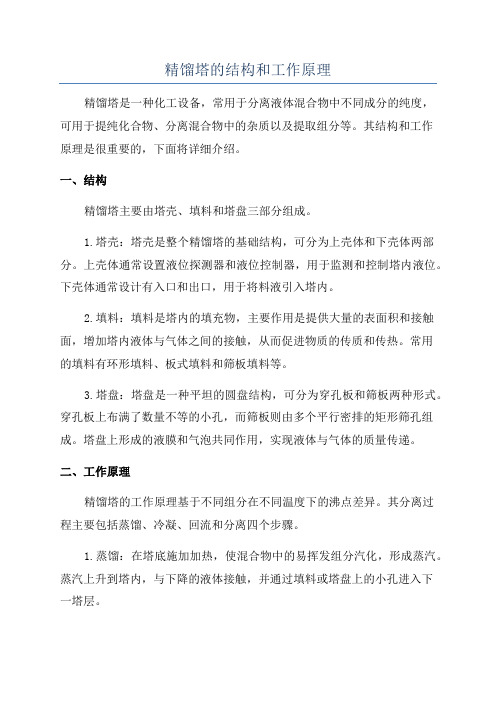
精馏塔的结构和工作原理精馏塔是一种化工设备,常用于分离液体混合物中不同成分的纯度,可用于提纯化合物、分离混合物中的杂质以及提取组分等。
其结构和工作原理是很重要的,下面将详细介绍。
一、结构精馏塔主要由塔壳、填料和塔盘三部分组成。
1.塔壳:塔壳是整个精馏塔的基础结构,可分为上壳体和下壳体两部分。
上壳体通常设置液位探测器和液位控制器,用于监测和控制塔内液位。
下壳体通常设计有入口和出口,用于将料液引入塔内。
2.填料:填料是塔内的填充物,主要作用是提供大量的表面积和接触面,增加塔内液体与气体之间的接触,从而促进物质的传质和传热。
常用的填料有环形填料、板式填料和筛板填料等。
3.塔盘:塔盘是一种平坦的圆盘结构,可分为穿孔板和筛板两种形式。
穿孔板上布满了数量不等的小孔,而筛板则由多个平行密排的矩形筛孔组成。
塔盘上形成的液膜和气泡共同作用,实现液体与气体的质量传递。
二、工作原理精馏塔的工作原理基于不同组分在不同温度下的沸点差异。
其分离过程主要包括蒸馏、冷凝、回流和分离四个步骤。
1.蒸馏:在塔底施加加热,使混合物中的易挥发组分汽化,形成蒸汽。
蒸汽上升到塔内,与下降的液体接触,并通过填料或塔盘上的小孔进入下一塔层。
2.冷凝:在塔顶设置冷凝器,冷却蒸汽,并将其转化为液体。
冷却过程中,蒸汽中的高沸点组分冷凝成液体,而低沸点组分保持挥发状态。
3.回流:冷凝后的液体通过回流管回流到塔顶,重新进入塔内。
回流液的作用是增加塔壁的液体,并通过填料或塔盘上的孔洞与上升的蒸汽混合。
4.分离:回流液与上升的蒸汽在塔内产生剪切力,使其彼此接触并进一步传质。
不同组分在塔内通过多次挥发和冷凝步骤的重复循环分离,逐渐提纯。
工作原理的关键在于塔内的物质传质和传热。
填料和塔盘提供了大量的表面积和接触面,使液体和气体之间能够充分接触。
高效的传质和传热能够促使组分之间相互转移,达到分离的目的。
总结:精馏塔的结构和工作原理是使得不同成分纯度提高的关键。
通过加热、冷凝和回流等步骤进行反复蒸发和冷凝,最终实现混合物中组分的分离。
精馏
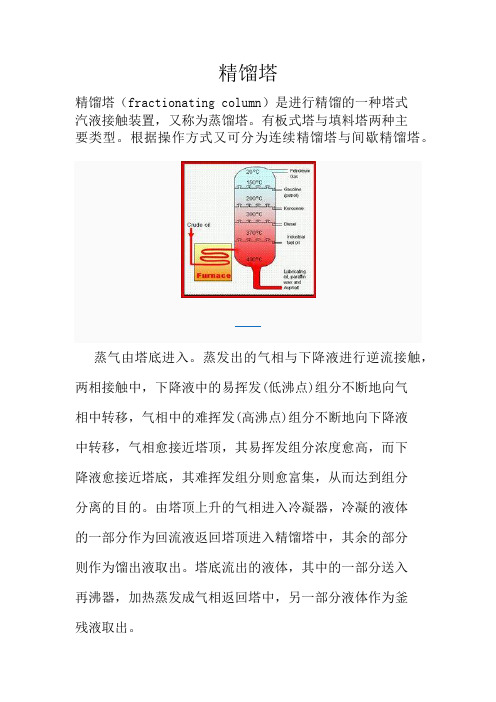
精馏塔精馏塔(fractionating column)是进行精馏的一种塔式汽液接触装置,又称为蒸馏塔。
有板式塔与填料塔两种主要类型。
根据操作方式又可分为连续精馏塔与间歇精馏塔。
蒸气由塔底进入。
蒸发出的气相与下降液进行逆流接触,两相接触中,下降液中的易挥发(低沸点)组分不断地向气相中转移,气相中的难挥发(高沸点)组分不断地向下降液中转移,气相愈接近塔顶,其易挥发组分浓度愈高,而下降液愈接近塔底,其难挥发组分则愈富集,从而达到组分分离的目的。
由塔顶上升的气相进入冷凝器,冷凝的液体的一部分作为回流液返回塔顶进入精馏塔中,其余的部分则作为馏出液取出。
塔底流出的液体,其中的一部分送入再沸器,加热蒸发成气相返回塔中,另一部分液体作为釜残液取出。
精馏原理 (Principle of Rectify)蒸馏的基本原理是将液体混合物多次部分气化和部分冷凝,利用其中各组份挥发度不同(相对挥发度,α)的特性,实现分离目的的单元操作。
蒸馏按照其操作方法可分为:简单蒸馏、闪蒸、精馏和特殊精馏等。
超重力精馏塔近年来出现的超重力精馏技术,利用高速旋转产生的数百至千倍重力的超重力场代替常规的重力场,极大地强化气液传质过程,将传质单元高度降低1个数量级。
从而使巨大的塔设备变为高度不到2米的超重力精馏机,达到增加效率、缩小体积的目的。
超重力精馏改变了传统的塔设备精馏模式,只要在室内厂房里就可以实现连续精馏过程。
对社会的发展而言可节省钢材资源,延长地球资源的使用年限;对企业的发展而言,可以节约场地与空间资源,减少污染排放,提高产品质量,改善经营管理模式,降低生产劳动强度,增加生产的安全性。
一、实验目的1. 熟悉精馏的工艺流程,掌握精馏实验的操作方法;2. 了解板式塔的结构,观察塔板上气-液接触状况;3. 测定全回流时的全塔效率及单板效率。
4. 测定全塔的浓度分布。
二、摘要在板式精馏塔中,由塔釜产生的蒸汽沿塔逐板上升与来自塔顶主板下降的回流液,在塔板上实现多次接触,进行传热与传质,使混合液达到一定程度的分离。
实验6 精馏塔(板塔)

精馏塔实验装置说明书一、实验目的1.了解板式塔的基本构造,精馏设备流程及各个部分的作用,观察精馏塔工作时塔板上的水里状况2.学会识别精馏塔内出现的几种操作状态,并分析这些操作状态对塔性能的影响3.学习精馏塔性能参数的测量方法,并掌握其影响因素。
4.研究开车过程中,精馏塔在全回流条件下,塔顶温度等参数随时间的变化情况5.测定精馏塔在全回流和某一回流比下连续精馏时,稳定操作后的全塔理论塔板数,总板效率。
二、实验原理对于二元物系,如果已知其气液平衡数据,则根据精馏塔的原料组成。
进料热状况、操作回流比及塔顶馏出液组成、塔底馏出液组成,可以求出该塔的理论板数以及总板效率。
全塔效率ηPtN N =t N —理论塔板数 p N —实际塔板数,10部分回流时,进料热状况参数的计算式为mmF B r r t t Cpm q +-⨯=)(q 线斜率=1-q q t F --进料温度; t B --泡点温度Cp m —进料液体在平均温度下的比热=()CKmol KJ x M c x M c p p ︒⋅+222111(乙醇ckg KJc p ︒⋅=07.31 、正丙醇c kg KJc p ︒⋅=85.22)r m —混合液体在泡点温度下汽化潜热=()KmolKJ x M r x M r 222111+(kgkJr kgkJr 680;81921==)三、装置和流程(一) 精馏塔(二) 物系 (乙醇─正丙醇)1. 纯度: 化学或分析纯.2. 平衡关系: 见表1.3. 料液浓度:15-25%(乙醇质量百分数).4. 浓度分析用阿贝折光仪.折光指数与溶液浓度的关系见表2. 表 1 常压下乙醇—正丙醇t-x-y 数据表( 均以乙醇摩尔分率表示,x-液相,y-气相 ,t/℃ )组成与泡点温度关系: 359.97861.271389.92+-=x x t (1) 式中: t —摄氏度,℃;x —乙醇在液相中的摩尔分率。
上列平衡数据摘自: J.Gmebling,U.onken •Vapor ─liquid•Equilibrium DataCollection ─Organic Hydro xy Compounds: Alcohols(p.336)。
板式精馏塔

板式精馏塔概述板式精馏塔是一种在化工工业中常用的设备,用于分离和纯化混合物。
它以其高效的分离效果和广泛的应用而被广泛采用。
本文将介绍板式精馏塔的工作原理、结构特点、应用领域以及一些常见的维护和安全注意事项。
一、工作原理板式精馏塔的工作原理基于物质的分馏和蒸馏。
内部设置有一系列的水平平板,称为分馏板。
原料在塔内加热,产生蒸汽。
当蒸汽通过分馏板时,会与冷却器接触,从而冷凝。
冷凝后的液体从板上回流,向下落入下一个分馏板。
这种逐级向下的流动使得组分在塔内逐渐分离。
在板式精馏塔中,分馏板是关键部件。
它可以分为两种类型:穿孔板和交互堆板。
穿孔板上设置有一些小孔,使得液体和蒸汽可以通过,而交互堆板上则有一些小柱子,用来阻碍液体的流动,增加接触面积,提高分离效果。
根据需要,可以选择不同类型的分馏板。
二、结构特点1. 塔体结构板式精馏塔的主体结构包括塔壳、塔盖和塔底。
塔壳是一个高大的圆柱体,内部设置有一系列的分馏板。
塔盖在塔壳顶部覆盖,用于密封和连接装置。
塔底连接塔壳和下部的分离设备。
2. 分馏板结构分馏板一般由板板、横梁和支撑框架组成。
板板是水平平面,用于支撑液体和蒸汽的流动。
横梁用来加固板板,防止其过度变形。
支撑框架则起到支撑分馏板的作用。
3. 进出料装置板式精馏塔上设置有进料和出料装置。
进料装置通常位于下部,用于输入混合物。
出料装置则设置在上部,用于收集纯化后的产物。
三、应用领域板式精馏塔广泛应用于以下领域:1. 石油化工在石油化工过程中,板式精馏塔用于对石油原料进行分离和纯化,得到不同级别的馏分油。
它在原油炼制和石化产品生产中起到至关重要的作用。
2. 化学工业在化学工业中,板式精馏塔用于将化工原料进行分离和纯化,得到所需的产品。
它可以应用于有机溶剂的回收、催化剂的制备、酯化反应的分离等过程。
3. 制药工业在制药工业中,板式精馏塔被用于药物的提纯和分离。
它可以帮助去除杂质和不纯物质,确保药物的纯度和质量。
四、维护和安全注意事项1. 定期清洁板式精馏塔在使用过程中会积累一定的污垢和沉淀物,定期清洁是必要的。
板式精馏塔
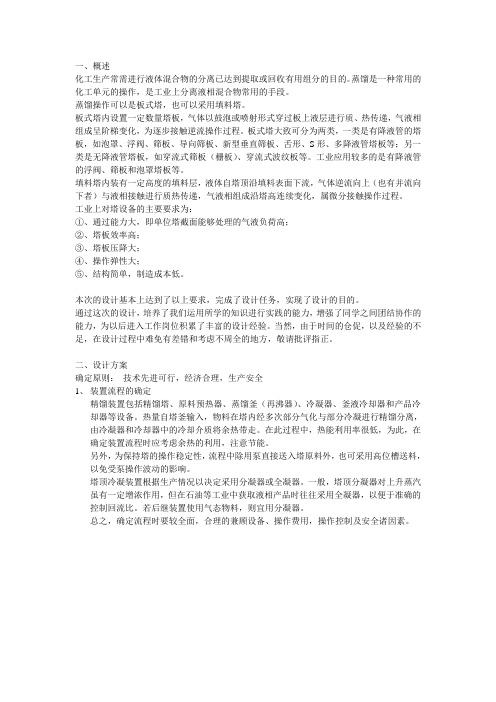
一、概述化工生产常需进行液体混合物的分离已达到提取或回收有用组分的目的。
蒸馏是一种常用的化工单元的操作,是工业上分离液相混合物常用的手段。
蒸馏操作可以是板式塔,也可以采用填料塔。
板式塔内设置一定数量塔板,气体以鼓泡或喷射形式穿过板上液层进行质、热传递,气液相组成呈阶梯变化,为逐步接触逆流操作过程。
板式塔大致可分为两类,一类是有降液管的塔板,如泡罩、浮阀、筛板、导向筛板、新型垂直筛板、舌形、S形、多降液管塔板等;另一类是无降液管塔板,如穿流式筛板(栅板)、穿流式波纹板等。
工业应用较多的是有降液管的浮阀、筛板和泡罩塔板等。
填料塔内装有一定高度的填料层,液体自塔顶沿填料表面下流,气体逆流向上(也有并流向下者)与液相接触进行质热传递,气液相组成沿塔高连续变化,属微分接触操作过程。
工业上对塔设备的主要要求为:①、通过能力大,即单位塔截面能够处理的气液负荷高;②、塔板效率高;③、塔板压降大;④、操作弹性大;⑤、结构简单,制造成本低。
本次的设计基本上达到了以上要求,完成了设计任务,实现了设计的目的。
通过这次的设计,培养了我们运用所学的知识进行实践的能力,增强了同学之间团结协作的能力,为以后进入工作岗位积累了丰富的设计经验。
当然,由于时间的仓促,以及经验的不足,在设计过程中难免有差错和考虑不周全的地方,敬请批评指正。
二、设计方案确定原则:技术先进可行,经济合理,生产安全1、装置流程的确定精馏装置包括精馏塔、原料预热器、蒸馏釜(再沸器)、冷凝器、釜液冷却器和产品冷却器等设备。
热量自塔釜输入,物料在塔内经多次部分气化与部分冷凝进行精馏分离,由冷凝器和冷却器中的冷却介质将余热带走。
在此过程中,热能利用率很低,为此,在确定装置流程时应考虑余热的利用,注意节能。
另外,为保持塔的操作稳定性,流程中除用泵直接送入塔原料外,也可采用高位槽送料,以免受泵操作波动的影响。
塔顶冷凝装置根据生产情况以决定采用分凝器或全凝器。
一般,塔顶分凝器对上升蒸汽虽有一定增浓作用,但在石油等工业中获取液相产品时往往采用全凝器,以便于准确的控制回流比。
精馏塔课程设计--苯-甲苯板式精馏塔的工艺设计

第一章绪论1.1精馏的特点与分类精馏是分离液体混合物的典型单元操作。
它是通过加热造成气液两相物系,利利用物系中各组分挥发度的不同的特性来实现分离的。
按精馏方式分为简单精馏、平衡精馏、精馏和特殊精馏。
1.1.1蒸馏分离具有以下特点(1)通过蒸馏分离,可以直接获得所需要的产品。
(2)适用范围广,可分离液态、气态或固态混合物。
(3)蒸馏过程适用于各种浓度混合物的分离。
(4)蒸馏操作耗能较大,节能是个值得重视的问题。
1.1.2平衡蒸馏将混合液在压力p1下加热,然后通过减压阀使压力降低至p2后进入分离器。
过热液体混合物在分离器中部分汽化,将平衡的气、液两相分别从分离器的顶部、底部引出,即实现了混合液的初步分离。
1.1.3简单蒸馏原料液在蒸馏釜中通过间接加热使之部分汽化,产生的蒸气进入冷凝器中冷凝,冷凝液作为馏出液产品排入接受器中。
在一批操作中,馏出液可分段收集,以得到不同组成的馏出液。
1.1.4连续精馏操作流程化工生产以连续精馏为主。
操作时,原料液连续地加入精馏塔内,连续地从再沸器取出部分液体作为塔底产品(称为釜残液);部分液体被汽化,产生上升蒸气,依次通过各层塔板。
塔顶蒸气进入冷凝器被全部冷凝,将部分冷凝液用泵(或借重力作用)送回塔顶作为回流液体,其余部分作为塔顶产品(称为馏出液)采出。
1-精馏塔 2-全凝器3-储槽 4-冷却器5-回流液泵 6-再沸器 7-原料液预热器图1连续精馏装置示意图1.2精馏塔的踏板分类1.2.1塔板的结构形式1.泡罩塔板泡罩塔板是工业上应用最早的塔板,它由升气管与泡罩构成。
泡罩安装在升气管的顶部,分圆形和条形两种,以前者使用较广。
泡罩有φ80mm、φ100mm和φ150mm三种尺寸,可根据塔径大小选择。
泡罩下部周边开有很多齿缝,齿缝一般为三角形、矩形或梯形。
泡罩在塔板上为正三角形排列。
它的优点是操作弹性适中塔板不易堵塞。
缺点是生产能力与板效率较低结构复杂、造价高。
图2泡罩塔板(a)操作示意图 (b)塔板平面图 (c)圆形泡罩2.筛孔塔板筛孔塔板简称筛板,其结构特点是在塔板上开有许多均匀小孔,孔径一般为3~8mm。
精馏塔操作
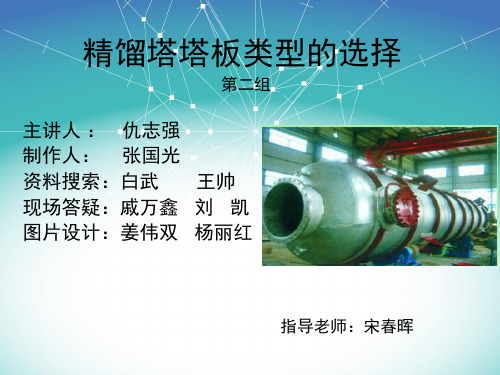
3.浮阀塔板——————浮阀形式
1-浮阀片;2-凸缘;3-浮阀”腿“;4-塔板上的孔
(a)F1型
(b)V-4型
(c)T型
浮阀塔板
• 优点:能适应气体流量在较大范围内
的波动,具有较大的操作弹性,生产 能力大,板效率高。
•缺点:是处理胶粘性和含固体颗
粒物料时,易导致阀片与塔板粘结 或被架起,同时在操作过程中可能 会发生阀片脱落或卡死等现象,使 塔板效率和操作弹性下降。
出料
• 精馏塔的内部原理:
液体靠重力作用由顶部逐板流向塔 底排出,并在各层塔板的板面上形成 流动的液层;气体则在压力差推动下 ,由塔底向上经过均布在塔板上的开 孔依次传播各层塔板由塔顶排出。
• 在有降液管式的塔板上,有专供液体流通 的降液管,每层板上的液层高度可以由适 当的溢流挡板调节。在塔板上气、液两相 成错流方式接触。 • 板式塔的溢流装置是指溢流堰和看、降液 管。降液管的布置规定了板上液体流动的 途径,一般有以下几种形式:
精馏塔板的选择:
• 层出不穷的新型塔板结构各具特点,应根 据不同的工艺及生产需要来选择塔型。不 是任何情况下都追求高的踏板效率,一般 来说,对难分离物系的高纯度分离希望得 到高的板效率,而对处理量大又易分离的 物系,往往追求高的生产能力,真空精馏 则需要低的压力降。
精馏塔常用的板型主要有四类:
(1)泡罩塔板; (2)筛板; (3)浮阀塔板; (4)喷射型塔板: ①舌形塔板 ②浮动喷射塔板 ③浮舌塔板 ④斜孔塔板 ⑤穿流栅孔塔板
1.泡罩塔板结构示意图
(a)泡罩塔板操作状态示意图
(b) 圆 形 泡 罩 结 构 图
1-升气管;2-泡罩;3-塔板
II----体由一系列平行的浮 动板组成,浮动板支承在支架的三 角槽内,可在一定角度内转动。
板式精馏塔的类型

板式精馏塔的类型板式精馏塔是一种常见的工业设备,用于分离液体混合物中的组分。
它的设计和操作方式会根据需要分离的物质以及工艺要求而有所不同。
在本文中,我们将深入探讨板式精馏塔的类型,并介绍它们在化工、石油等行业中的应用。
一、根据塔板结构分类1. 全开孔板式精馏塔:全开孔板式精馏塔是最简单的类型。
它的板面上布置了许多孔洞,使得液体和气体可以通过。
全开孔板式精馏塔主要用于处理易于分离的物质,如精馏水。
它的优点是操作简单,但对于较复杂的分离过程,效率可能较低。
2. 弗利斯塔式精馏塔:弗利斯塔式精馏塔采用更复杂的结构设计,可以提高分离效率。
它的板面上有许多小孔,通过这些小孔液体和气体进入阀流区,然后再进入孔板下的塔板。
弗利斯塔式精馏塔能够更好地分离液体混合物,使得不同组分的纯度更高。
3. 旁通式精馏塔:旁通式精馏塔也是常见的一种类型。
它的设计在塔板上有旁通管,使得液体在不同的塔板之间流动。
这种结构适用于处理较复杂和难分离的物质。
旁通式精馏塔可以提高塔内的混合物接触,增加分离效果。
4. 蛇形孔板式精馏塔:蛇形孔板式精馏塔的塔板上有许多弯曲的蛇形孔,使得液体和气体在塔板上形成多个旋涡流动的小区域。
这种结构使得液体和气体充分接触,提高了分离效果。
蛇形孔板式精馏塔常用于分离粘度较高的液体。
二、根据馏分进料方式分类1. 上进料精馏塔:上进料精馏塔是指精馏馏分从塔底进入塔体。
这种方式适用于处理重质组分。
一般情况下,重质组分易于液化,因此上进料精馏塔可以更好地控制液体的流动。
2. 下进料精馏塔:下进料精馏塔是指精馏馏分从塔顶进入塔体。
这种方式适用于处理轻质组分。
轻质组分易于气化,下进料精馏塔可以更好地控制气体的流动。
三、根据液体分布方式分类1. 平板式精馏塔:平板式精馏塔是指塔板上液体的分布是均匀的。
它的塔板上有许多小孔,液体通过这些小孔均匀分布在整个塔板上。
平板式精馏塔可以提高液体在塔内的均匀性,增加分离效率。
2. 管壳式精馏塔:管壳式精馏塔是指塔板上液体的分布是通过管壳系统实现的。
板式精馏塔塔板类型
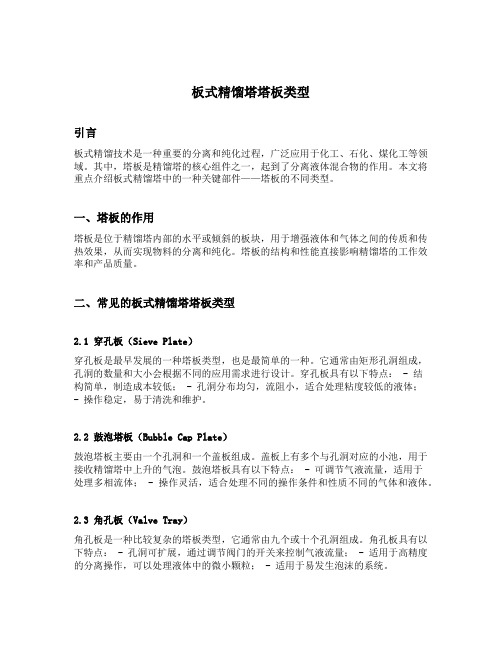
板式精馏塔塔板类型引言板式精馏技术是一种重要的分离和纯化过程,广泛应用于化工、石化、煤化工等领域。
其中,塔板是精馏塔的核心组件之一,起到了分离液体混合物的作用。
本文将重点介绍板式精馏塔中的一种关键部件——塔板的不同类型。
一、塔板的作用塔板是位于精馏塔内部的水平或倾斜的板块,用于增强液体和气体之间的传质和传热效果,从而实现物料的分离和纯化。
塔板的结构和性能直接影响精馏塔的工作效率和产品质量。
二、常见的板式精馏塔塔板类型2.1 穿孔板(Sieve Plate)穿孔板是最早发展的一种塔板类型,也是最简单的一种。
它通常由矩形孔洞组成,孔洞的数量和大小会根据不同的应用需求进行设计。
穿孔板具有以下特点: - 结构简单,制造成本较低; - 孔洞分布均匀,流阻小,适合处理粘度较低的液体;- 操作稳定,易于清洗和维护。
2.2 鼓泡塔板(Bubble Cap Plate)鼓泡塔板主要由一个孔洞和一个盖板组成。
盖板上有多个与孔洞对应的小池,用于接收精馏塔中上升的气泡。
鼓泡塔板具有以下特点: - 可调节气液流量,适用于处理多相流体; - 操作灵活,适合处理不同的操作条件和性质不同的气体和液体。
2.3 角孔板(Valve Tray)角孔板是一种比较复杂的塔板类型,它通常由九个或十个孔洞组成。
角孔板具有以下特点: - 孔洞可扩展,通过调节阀门的开关来控制气液流量; - 适用于高精度的分离操作,可以处理液体中的微小颗粒; - 适用于易发生泡沫的系统。
2.4 段叠板(Dual-flow Tray)段叠板是一种经典的塔板类型,具有双层结构,上层为雾区,下层为冷凝液区。
段叠板具有以下特点: - 分离效果好,操作稳定,适用于处理粘度较高的液体; - 操作灵活,适合处理污染物含量较高的流体; - 通过结构调整,可以适应不同的操作条件。
三、塔板的选择原则在选择板式精馏塔的塔板类型时,需要考虑以下几个因素: 1. 分离精度要求:选择适合的塔板类型以满足产品的纯度和回收率要求。
精馏塔的种类
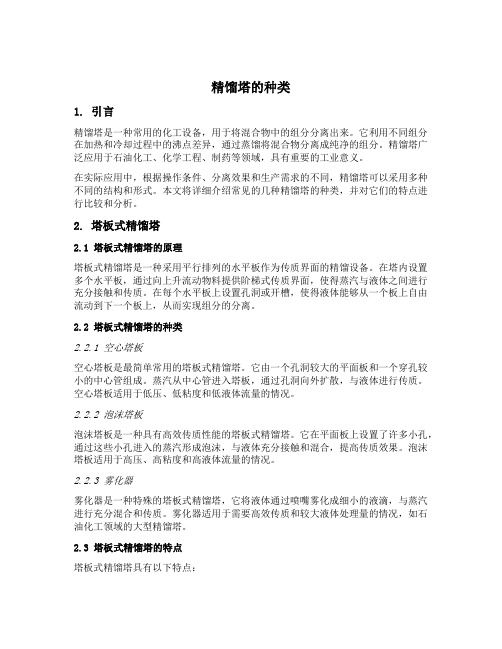
精馏塔的种类1. 引言精馏塔是一种常用的化工设备,用于将混合物中的组分分离出来。
它利用不同组分在加热和冷却过程中的沸点差异,通过蒸馏将混合物分离成纯净的组分。
精馏塔广泛应用于石油化工、化学工程、制药等领域,具有重要的工业意义。
在实际应用中,根据操作条件、分离效果和生产需求的不同,精馏塔可以采用多种不同的结构和形式。
本文将详细介绍常见的几种精馏塔的种类,并对它们的特点进行比较和分析。
2. 塔板式精馏塔2.1 塔板式精馏塔的原理塔板式精馏塔是一种采用平行排列的水平板作为传质界面的精馏设备。
在塔内设置多个水平板,通过向上升流动物料提供阶梯式传质界面,使得蒸汽与液体之间进行充分接触和传质。
在每个水平板上设置孔洞或开槽,使得液体能够从一个板上自由流动到下一个板上,从而实现组分的分离。
2.2 塔板式精馏塔的种类2.2.1 空心塔板空心塔板是最简单常用的塔板式精馏塔。
它由一个孔洞较大的平面板和一个穿孔较小的中心管组成。
蒸汽从中心管进入塔板,通过孔洞向外扩散,与液体进行传质。
空心塔板适用于低压、低粘度和低液体流量的情况。
2.2.2 泡沫塔板泡沫塔板是一种具有高效传质性能的塔板式精馏塔。
它在平面板上设置了许多小孔,通过这些小孔进入的蒸汽形成泡沫,与液体充分接触和混合,提高传质效果。
泡沫塔板适用于高压、高粘度和高液体流量的情况。
2.2.3 雾化器雾化器是一种特殊的塔板式精馏塔,它将液体通过喷嘴雾化成细小的液滴,与蒸汽进行充分混合和传质。
雾化器适用于需要高效传质和较大液体处理量的情况,如石油化工领域的大型精馏塔。
2.3 塔板式精馏塔的特点塔板式精馏塔具有以下特点:•结构简单、易于操作和维护;•分离效果好,能够实现高纯度的组分分离;•可以根据需要调整板间液体流量,适应不同的操作条件;•适用于多种物料和工艺要求。
3. 填料式精馏塔3.1 填料式精馏塔的原理填料式精馏塔是一种利用填料提供大量传质界面的精馏设备。
在填料层中,液体通过填料表面形成薄膜,并与下降的蒸汽进行接触和传质。
精馏塔
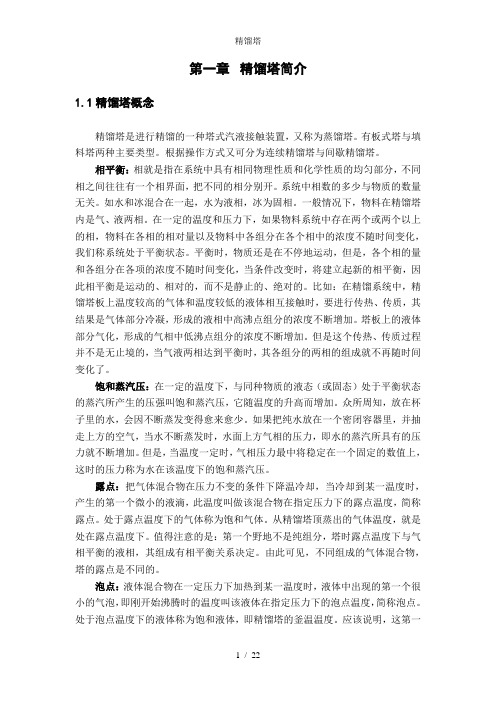
第一章精馏塔简介1.1精馏塔概念精馏塔是进行精馏的一种塔式汽液接触装置,又称为蒸馏塔。
有板式塔与填料塔两种主要类型。
根据操作方式又可分为连续精馏塔与间歇精馏塔。
相平衡:相就是指在系统中具有相同物理性质和化学性质的均匀部分,不同相之间往往有一个相界面,把不同的相分别开。
系统中相数的多少与物质的数量无关。
如水和冰混合在一起,水为液相,冰为固相。
一般情况下,物料在精馏塔内是气、液两相。
在一定的温度和压力下,如果物料系统中存在两个或两个以上的相,物料在各相的相对量以及物料中各组分在各个相中的浓度不随时间变化,我们称系统处于平衡状态。
平衡时,物质还是在不停地运动,但是,各个相的量和各组分在各项的浓度不随时间变化,当条件改变时,将建立起新的相平衡,因此相平衡是运动的、相对的,而不是静止的、绝对的。
比如:在精馏系统中,精馏塔板上温度较高的气体和温度较低的液体相互接触时,要进行传热、传质,其结果是气体部分冷凝,形成的液相中高沸点组分的浓度不断增加。
塔板上的液体部分气化,形成的气相中低沸点组分的浓度不断增加。
但是这个传热、传质过程并不是无止境的,当气液两相达到平衡时,其各组分的两相的组成就不再随时间变化了。
饱和蒸汽压:在一定的温度下,与同种物质的液态(或固态)处于平衡状态的蒸汽所产生的压强叫饱和蒸汽压,它随温度的升高而增加。
众所周知,放在杯子里的水,会因不断蒸发变得愈来愈少。
如果把纯水放在一个密闭容器里,并抽走上方的空气,当水不断蒸发时,水面上方气相的压力,即水的蒸汽所具有的压力就不断增加。
但是,当温度一定时,气相压力最中将稳定在一个固定的数值上,这时的压力称为水在该温度下的饱和蒸汽压。
露点:把气体混合物在压力不变的条件下降温冷却,当冷却到某一温度时,产生的第一个微小的液滴,此温度叫做该混合物在指定压力下的露点温度,简称露点。
处于露点温度下的气体称为饱和气体。
从精馏塔顶蒸出的气体温度,就是处在露点温度下。
值得注意的是:第一个野地不是纯组分,塔时露点温度下与气相平衡的液相,其组成有相平衡关系决定。
精馏塔
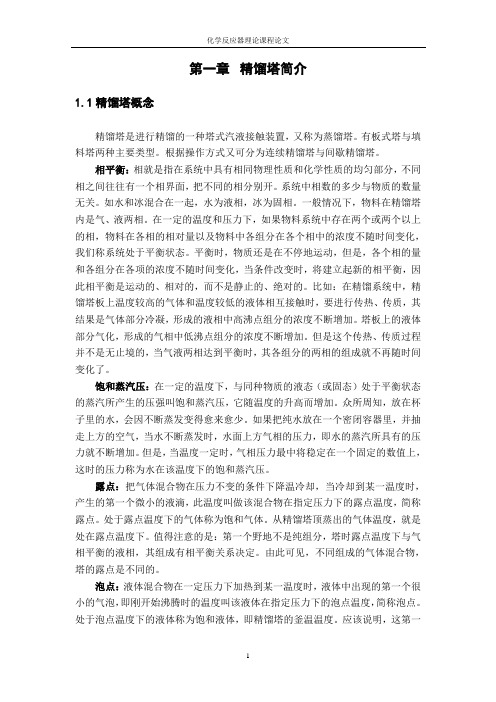
第一章精馏塔简介1.1精馏塔概念精馏塔是进行精馏的一种塔式汽液接触装置,又称为蒸馏塔。
有板式塔与填料塔两种主要类型。
根据操作方式又可分为连续精馏塔与间歇精馏塔。
相平衡:相就是指在系统中具有相同物理性质和化学性质的均匀部分,不同相之间往往有一个相界面,把不同的相分别开。
系统中相数的多少与物质的数量无关。
如水和冰混合在一起,水为液相,冰为固相。
一般情况下,物料在精馏塔内是气、液两相。
在一定的温度和压力下,如果物料系统中存在两个或两个以上的相,物料在各相的相对量以及物料中各组分在各个相中的浓度不随时间变化,我们称系统处于平衡状态。
平衡时,物质还是在不停地运动,但是,各个相的量和各组分在各项的浓度不随时间变化,当条件改变时,将建立起新的相平衡,因此相平衡是运动的、相对的,而不是静止的、绝对的。
比如:在精馏系统中,精馏塔板上温度较高的气体和温度较低的液体相互接触时,要进行传热、传质,其结果是气体部分冷凝,形成的液相中高沸点组分的浓度不断增加。
塔板上的液体部分气化,形成的气相中低沸点组分的浓度不断增加。
但是这个传热、传质过程并不是无止境的,当气液两相达到平衡时,其各组分的两相的组成就不再随时间变化了。
饱和蒸汽压:在一定的温度下,与同种物质的液态(或固态)处于平衡状态的蒸汽所产生的压强叫饱和蒸汽压,它随温度的升高而增加。
众所周知,放在杯子里的水,会因不断蒸发变得愈来愈少。
如果把纯水放在一个密闭容器里,并抽走上方的空气,当水不断蒸发时,水面上方气相的压力,即水的蒸汽所具有的压力就不断增加。
但是,当温度一定时,气相压力最中将稳定在一个固定的数值上,这时的压力称为水在该温度下的饱和蒸汽压。
露点:把气体混合物在压力不变的条件下降温冷却,当冷却到某一温度时,产生的第一个微小的液滴,此温度叫做该混合物在指定压力下的露点温度,简称露点。
处于露点温度下的气体称为饱和气体。
从精馏塔顶蒸出的气体温度,就是处在露点温度下。
值得注意的是:第一个野地不是纯组分,塔时露点温度下与气相平衡的液相,其组成有相平衡关系决定。
实验6 精馏塔(板塔)
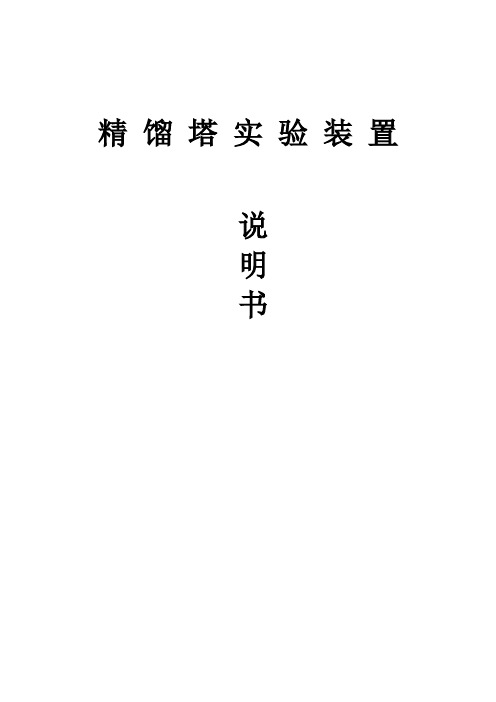
精馏塔实验装置说明书一、实验目的1.了解板式塔的基本构造,精馏设备流程及各个部分的作用,观察精馏塔工作时塔板上的水里状况2.学会识别精馏塔内出现的几种操作状态,并分析这些操作状态对塔性能的影响3.学习精馏塔性能参数的测量方法,并掌握其影响因素。
4.研究开车过程中,精馏塔在全回流条件下,塔顶温度等参数随时间的变化情况5.测定精馏塔在全回流和某一回流比下连续精馏时,稳定操作后的全塔理论塔板数,总板效率。
二、实验原理对于二元物系,如果已知其气液平衡数据,则根据精馏塔的原料组成。
进料热状况、操作回流比及塔顶馏出液组成、塔底馏出液组成,可以求出该塔的理论板数以及总板效率。
全塔效率ηPtN N =t N —理论塔板数 p N —实际塔板数,10部分回流时,进料热状况参数的计算式为mmF B r r t t Cpm q +-⨯=)(q 线斜率=1-q q t F --进料温度; t B --泡点温度Cp m —进料液体在平均温度下的比热=()CKmol KJ x M c x M c p p ︒⋅+222111(乙醇ckg KJc p ︒⋅=07.31 、正丙醇c kg KJc p ︒⋅=85.22)r m —混合液体在泡点温度下汽化潜热=()KmolKJ x M r x M r 222111+(kgkJr kgkJr 680;81921==)三、装置和流程(一) 精馏塔(二) 物系 (乙醇─正丙醇)1. 纯度: 化学或分析纯.2. 平衡关系: 见表1.3. 料液浓度:15-25%(乙醇质量百分数).4. 浓度分析用阿贝折光仪.折光指数与溶液浓度的关系见表2. 表 1 常压下乙醇—正丙醇t-x-y 数据表( 均以乙醇摩尔分率表示,x-液相,y-气相 ,t/℃ )组成与泡点温度关系: 359.97861.271389.92+-=x x t (1) 式中: t —摄氏度,℃;x —乙醇在液相中的摩尔分率。
上列平衡数据摘自: J.Gmebling,U.onken •Vapor ─liquid•Equilibrium DataCollection ─Organic Hydro xy Compounds: Alcohols(p.336)。
板式精馏塔塔板类型
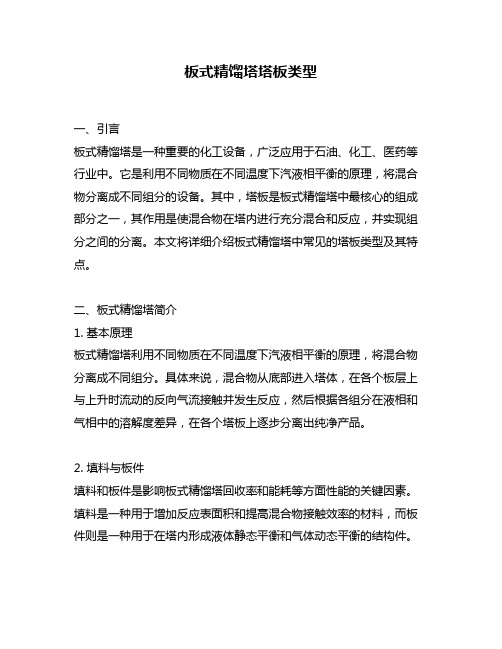
板式精馏塔塔板类型一、引言板式精馏塔是一种重要的化工设备,广泛应用于石油、化工、医药等行业中。
它是利用不同物质在不同温度下汽液相平衡的原理,将混合物分离成不同组分的设备。
其中,塔板是板式精馏塔中最核心的组成部分之一,其作用是使混合物在塔内进行充分混合和反应,并实现组分之间的分离。
本文将详细介绍板式精馏塔中常见的塔板类型及其特点。
二、板式精馏塔简介1. 基本原理板式精馏塔利用不同物质在不同温度下汽液相平衡的原理,将混合物分离成不同组分。
具体来说,混合物从底部进入塔体,在各个板层上与上升时流动的反向气流接触并发生反应,然后根据各组分在液相和气相中的溶解度差异,在各个塔板上逐步分离出纯净产品。
2. 填料与板件填料和板件是影响板式精馏塔回收率和能耗等方面性能的关键因素。
填料是一种用于增加反应表面积和提高混合物接触效率的材料,而板件则是一种用于在塔内形成液体静态平衡和气体动态平衡的结构件。
3. 塔板类型塔板是板式精馏塔中最核心的组成部分之一,其作用是使混合物在塔内进行充分混合和反应,并实现组分之间的分离。
常见的塔板类型有:三、常见的塔板类型及其特点1. 空心筒板空心筒板又称为筒型孔板,是一种较早出现的塔板类型。
它由一个中空的圆柱形筒体和若干个等距离排列的孔洞组成。
混合物从下部进入筒体内部,在上升过程中通过孔洞与上方气流接触进行反应,并逐步分离出纯净产品。
优点:结构简单,制造工艺容易掌握;缺点:不适用于高速气流条件下,易发生液膜撕裂现象;2. 波纹状大孔板波纹状大孔板是一种具有波纹状结构的板件,其上分布着大量的孔洞。
混合物从下部进入板内,在波纹状结构上形成液膜,然后通过孔洞与上方气流接触进行反应,并逐步分离出纯净产品。
优点:具有较高的传质效率和分离效率;缺点:制造难度较大,易发生液膜撕裂现象;3. 圆孔板圆孔板是一种平面结构的塔板类型,其上分布着若干个等距离排列的圆形孔洞。
混合物从下部进入塔内,在圆孔板上形成液膜,然后通过孔洞与上方气流接触进行反应,并逐步分离出纯净产品。
- 1、下载文档前请自行甄别文档内容的完整性,平台不提供额外的编辑、内容补充、找答案等附加服务。
- 2、"仅部分预览"的文档,不可在线预览部分如存在完整性等问题,可反馈申请退款(可完整预览的文档不适用该条件!)。
- 3、如文档侵犯您的权益,请联系客服反馈,我们会尽快为您处理(人工客服工作时间:9:00-18:30)。
一、塔板效率
2.单板效率EM
单板效率EM,它是以气相(或液相)经过实 际板的组成变化值与经过理论板的组成变化 值之比来表示。
(1) 以气相组成表示的单板效率
以气相组成表示的单板效率与理论板上下气 相组成有关,如图1所示。 y y n 1 (2) E MV n * yn y n 1 式中: EMV——以气相组成表示的单板效率; yn——离开第n板的气相组成,摩尔分率; yn*——与第n板的液相组成xn构成平衡的气 相组成,摩尔分率; yn+1——从下一板(n+1板)进入第n板的气 相组成,摩尔分率。
图2 一个精馏过程图解法求得理论板数结果
三、实际塔板数
例1 对于一个精馏过程,用图解法求 解理论板数的结果,如图2所示。 解: (2)实际板数 根据全塔效率ET=50%。 实际板数NP= NT/ET=6/0.5=12(不包 括再沸器); 精馏段实际板数=3/0.5=6; 提馏段实际板数=3/0.5=6(不包括再 沸器); 加料板在实际板中位置为从上往下数 第7块塔板(精馏段实际板数+1)。
一、塔板效率
对于一个实际操作的精馏塔,衡量精馏塔塔板分离效率 指标有两个,即全塔塔板效率(全塔效率)和单板效率。 1.全塔效率ET
在实际操作中,由于塔板上气液接触的时间及面积都很有限,因而任何形 式的塔板上气液两相都难以达到平衡状态,在实际分离过程中理论塔板是 不存在的,完成一定的分离任务所需的实际塔板数总是比理论塔板数多。 全塔塔板的分离效率,可以用全塔效率来表示。 全塔效率又称总板效率,是完成一定的分离任务所需的实际塔板数与相应 分离任务需要的理论塔板数之比,其值恒小于1。 全塔效率: (1 ) NT ET 100% 式中: N
xn 1
n * xn
理论板上两相组成示意图
二、塔板效率的影响因素
塔板效率主要受到混合物气液两相的物理性质、精馏塔 型式和结构,以及操作条件等因素影响。
1.混合物气液两相的物理性质
主要有黏度、相对挥发度、扩散系数、表面张力和密度等物理性质。
2.精馏塔板型式和结构
塔板型式主要有泡罩塔板、筛板、浮阀塔板、斜孔塔板等;塔板结构主 要涉及塔径、板间距、出口堰高度、液体在板上的流程长度、降液部分 大小及结构,还有阀、筛孔或泡帽的结构、排列与开孔率。
P
——全塔效率; N T ——理论塔板数(不包括再沸器); N P ——实际塔板数(不包括再沸器)。 全塔效率可反映全塔中各层板上分离传质过程所进行的程度。
ET
一、塔板效率
对于一个实际操作的精馏塔,衡量精馏塔塔板分离效率 指标有两个,即全塔塔板效率(全塔效率)和单板效率。 1.全塔效率ET
问题1 全塔效率如何确定? 回答——先根据实际生产中测定的数据(进料组成xF,进料状态和 温度,实际回流比R,以及分离结果xD和xW),求得精馏所需要的理 论塔板数(不包括再沸器),再结合实际塔板数(不包括再沸器), 可计算出全塔效率。
图1 理论板上两相组成示意图
一、塔板效率
2.单板效率EM
(2)以液相组成表示的单板效率
以液相组成表示的单板效率与理论板上下液相组 成有关,如图1所示。 (3 ) x x
EML
n 1
式中: EML——以液相组成表示的单板效率; xn——离开第n板的液相组成,摩尔分率; xn*——与第n板的气相组成yn构成平衡的液相组 成,摩尔分率; xn-1——从上一板(n-1板)进入第n板的液相组成, 摩尔分率。 图1 单板效率可由实验测定。
NP
式中: ET ——经验塔的全塔效率; N T ——理论塔板数(不包括再沸器); N P ——实际塔板数(不包括再沸器)。
T ET
三、实际塔板数
例1 对于一个精馏过程,用图解法求 解理论板数的结果,如图2所示。试 问: (1)该精馏过程需要的理论板数、精 馏段理论板数、提馏段理论板数各是 多少?加料板在理论板中处于什么位 置?图2 一个精馏过程图解法求得理 论板数结果
图2 一个精馏过程图解法求得理论板数结果 (2)若该精馏过程经验塔的全塔效率 为50%,则该精馏过程需要的实际板 数、精馏段实际板数、提馏段实际板 数各是多少?加料板实际在什么位置?
三、实际塔板数
例1 对于一个精馏过程,用图解法求 解理论板数的结果,如图2所示。 解: (1) 理论板数 根据图2可知。 该精馏过程需要的理论板数 NT=7-1=6 (不包括再沸器); 精馏段理论板数=3; 提馏段理论板数=7-3-1=3(不包括再 沸器); 加料板在理论板中位置为从上往下数 第4块塔板(该塔板跨过d点)。
知识点编号:ZYKC20112902040704
塔板效率与实际塔板数
理论塔板是指当气液两相在塔板上充分接触,有足够长的时间进行传热传 质,气体离开塔板时与下降的液体达到相平衡的塔板。
生产实际中,由于塔板上气液两相接触的时间及面积均有限,因而任何形 式的塔板上气液两相都难以达到平衡状态,也就是说实际塔板的分离效果 不可能达到理论塔板的效果,实际塔板与理论塔板在分离效果上存在差异。 同时,生产实际中不同塔板际塔板分离效率的概念,来衡量 实际塔板分离效果高低。 本知识点介绍塔板效率,以及在设计型项目中确定实际塔板数的方法。
3.操作条件
主要有气液两相的流量、回流比、温度及压力等。 影响塔板效率的因素多而复杂,很难找到各种因素之间的定量关系。
三、实际塔板数
对于设计型项目,在计算出理论塔板数后,需要求出相应的实际 塔板数,才能符合生产实际,完成工艺要求的加工任务。
1.实际塔板数 对于物系组成和性质、塔板型式和结构、操作条件初步确定的设 计型精馏塔计算中,可以找到物系组成和性质相近、塔板型式和 结构相似、操作条件接近的经验精馏塔,并通过测定和计算获得 经验塔的全塔效率,当计算出理论塔板数NT后,参照经验塔的全 塔效率ET,可求出相应的实际塔板数NP。 (4) N
图2 一个精馏过程图解法求得理论板数结果
三、实际塔板数
2.实际塔板数的意义 实际塔板数、板间距、塔径等,都属于精馏塔设计的重要工艺数 据。