钢铁冶炼过程
炼钢生产过程以及流程图详解(全)
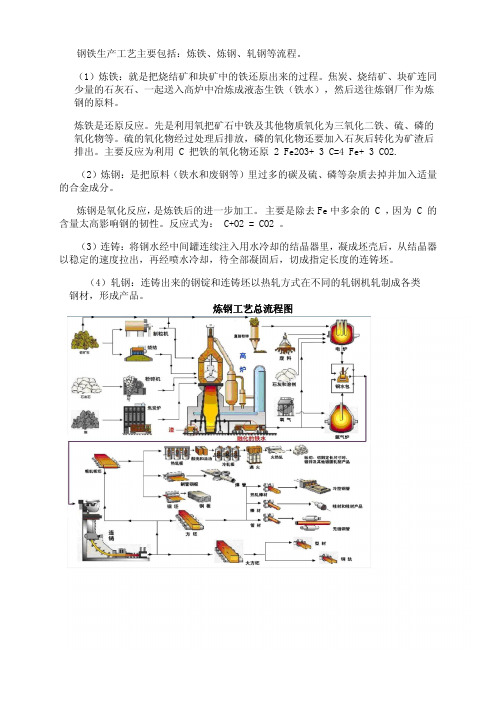
钢铁生产工艺主要包括:炼铁、炼钢、轧钢等流程。
(1)炼铁:就是把烧结矿和块矿中的铁还原出来的过程。
焦炭、烧结矿、块矿连同少量的石灰石、一起送入高炉中冶炼成液态生铁(铁水),然后送往炼钢厂作为炼钢的原料。
炼铁是还原反应。
先是利用氧把矿石中铁及其他物质氧化为三氧化二铁、硫、磷的氧化物等。
硫的氧化物经过处理后排放,磷的氧化物还要加入石灰后转化为矿渣后排出。
主要反应为利用 C 把铁的氧化物还原 2 Fe2O3+ 3 C=4 Fe+ 3 CO2.(2)炼钢:是把原料(铁水和废钢等)里过多的碳及硫、磷等杂质去掉并加入适量的合金成分。
炼钢是氧化反应,是炼铁后的进一步加工。
主要是除去Fe中多余的 C ,因为 C 的含量太高影响钢的韧性。
反应式为: C+O2 = CO2 。
(3)连铸:将钢水经中间罐连续注入用水冷却的结晶器里,凝成坯壳后,从结晶器以稳定的速度拉出,再经喷水冷却,待全部凝固后,切成指定长度的连铸坯。
(4)轧钢:连铸出来的钢锭和连铸坯以热轧方式在不同的轧钢机轧制成各类 钢材,形成产品。
炼钢工艺总流程图炼焦生产流程:炼焦作业是将焦煤经混合,破碎后加入炼焦炉内经干馏后产生热焦碳及粗焦炉气之制程。
烧结生产流程:烧结作业系将粉铁矿,各类助熔剂及细焦炭经由混拌、造粒后,经由布料系统加入烧结机,由点火炉点燃细焦炭,经由抽气风车抽风完成烧结反应,高热之烧结矿经破碎冷却、筛选后,送往高炉作为冶炼铁水之主要原料。
还原气体,还原铁矿石,产生熔融铁水与熔渣之炼铁制程。
转炉生产流程:炼钢厂先将熔铣送前处理站作脱硫脱磷处理,经转炉吹炼后,再依订单钢种特性及品质需求,送二次精炼处理站(RH真空脱气处理站、Ladle Injection盛桶吹射处理站、VOD真空吹氧脱碳处理站、STN搅拌站等)进行各种处理,调整钢液成份,最后送大钢胚及扁钢胚连续铸造机,浇铸成红热钢胚半成品,经检验、研磨或烧除表面缺陷,或直接送下游轧制成条钢、线材、钢板、钢卷及钢片等成品。
钢铁冶金学(炼铁部分)
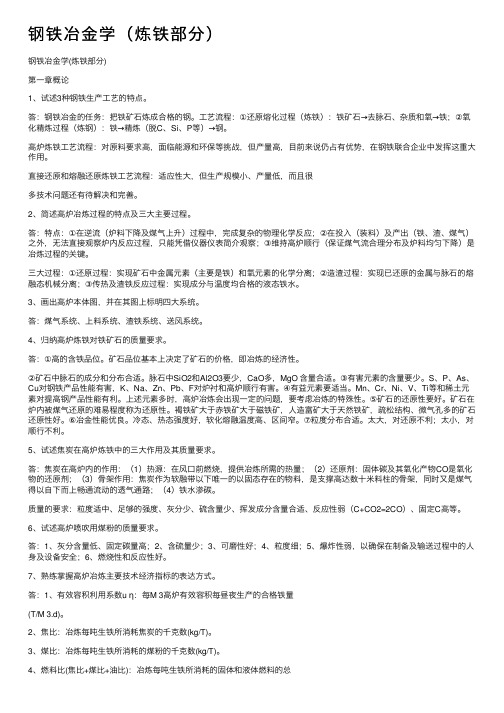
钢铁冶⾦学(炼铁部分)钢铁冶⾦学(炼铁部分)第⼀章概论1、试述3种钢铁⽣产⼯艺的特点。
答:钢铁冶⾦的任务:把铁矿⽯炼成合格的钢。
⼯艺流程:①还原熔化过程(炼铁):铁矿⽯→去脉⽯、杂质和氧→铁;②氧化精炼过程(炼钢):铁→精炼(脱C、Si、P等)→钢。
⾼炉炼铁⼯艺流程:对原料要求⾼,⾯临能源和环保等挑战,但产量⾼,⽬前来说仍占有优势,在钢铁联合企业中发挥这重⼤作⽤。
直接还原和熔融还原炼铁⼯艺流程:适应性⼤,但⽣产规模⼩、产量低,⽽且很多技术问题还有待解决和完善。
2、简述⾼炉冶炼过程的特点及三⼤主要过程。
答:特点:①在逆流(炉料下降及煤⽓上升)过程中,完成复杂的物理化学反应;②在投⼊(装料)及产出(铁、渣、煤⽓)之外,⽆法直接观察炉内反应过程,只能凭借仪器仪表简介观察;③维持⾼炉顺⾏(保证煤⽓流合理分布及炉料均匀下降)是冶炼过程的关键。
三⼤过程:①还原过程:实现矿⽯中⾦属元素(主要是铁)和氧元素的化学分离;②造渣过程:实现已还原的⾦属与脉⽯的熔融态机械分离;③传热及渣铁反应过程:实现成分与温度均合格的液态铁⽔。
3、画出⾼炉本体图,并在其图上标明四⼤系统。
答:煤⽓系统、上料系统、渣铁系统、送风系统。
4、归纳⾼炉炼铁对铁矿⽯的质量要求。
答:①⾼的含铁品位。
矿⽯品位基本上决定了矿⽯的价格,即冶炼的经济性。
②矿⽯中脉⽯的成分和分布合适。
脉⽯中SiO2和Al2O3要少,CaO多,MgO 含量合适。
③有害元素的含量要少。
S、P、As、Cu对钢铁产品性能有害,K、Na、Zn、Pb、F对炉衬和⾼炉顺⾏有害。
④有益元素要适当。
Mn、Cr、Ni、V、Ti等和稀⼟元素对提⾼钢产品性能有利。
上述元素多时,⾼炉冶炼会出现⼀定的问题,要考虑冶炼的特殊性。
⑤矿⽯的还原性要好。
矿⽯在炉内被煤⽓还原的难易程度称为还原性。
褐铁矿⼤于⾚铁矿⼤于磁铁矿,⼈造富矿⼤于天然铁矿,疏松结构、微⽓孔多的矿⽯还原性好。
⑥冶⾦性能优良。
冷态、热态强度好,软化熔融温度⾼、区间窄。
炼钢的工艺流程

炼钢的工艺流程:一、加料加料:向电炉或转炉内加入铁水或废钢等原材料的操作,是炼钢操作的第一步。
二、造渣造渣:调整钢、铁生产中熔渣成分、碱度和粘度及其反应能力的操作。
目的是通过钢铁高炉钢铁高炉渣--金属反应炼出具有所要求成分和温度的金属。
例如氧气顶吹转炉造渣和吹氧操作是为了生成有足够流动性和碱度的熔渣,能够向金属液面中传递足够的氧,以便把硫、磷降到计划钢种的上限以下,并使吹氧时喷溅和溢渣的量减至最小。
三、出渣出渣:电弧炉炼钢时根据不同冶炼条件和目的在冶炼过程中所采取的放渣或扒渣操作。
如用单渣法冶炼时,氧化末期须扒氧化渣;用双渣法造还原渣时,原来的氧化渣必须彻底放出,以防回磷等。
四、熔池搅拌熔池搅拌:向金属熔池供应能量,使金属液和熔渣产生运动,以改善冶金反应的动力学条件。
熔池搅拌可藉助于气体、机械、电磁感应等方法来实现。
五、脱磷减少钢液中含磷量的化学反应。
磷是钢中有害杂质之一。
含磷较多的钢,在室温或更低的温度下使用时,容易脆裂,称为"冷脆"。
钢中含碳越高,磷引起的脆性越严重。
一般普通钢中规定含磷量不超过0.045%,优质钢要求含磷更少。
生铁中的磷,主要来自铁矿石中的磷酸盐。
氧化磷和氧化铁的热力学稳定性相近。
在高炉的还原条件下,炉料中的磷几乎全部被还原并溶入铁水。
如选矿不能除去磷的化合物,脱磷就只能在(高)炉外或碱性炼钢炉中进行。
铁中脱磷问题的认识和解决,在钢铁生产发展史上具有特殊的重要意义。
钢的大规模工业生产开始于1856年贝塞麦(H.Bessemer)发明的酸性转炉炼钢法。
但酸性转炉炼钢不能脱磷;而含磷低的铁矿石又很少,严重地阻碍了钢生产的发展。
1879年托马斯(S.Thomas)发明了能处理高磷铁水的碱性转炉炼钢法,碱性炉渣的脱磷原理接着被推广到平炉炼钢中去,使大量含磷铁矿石得以用于生产钢铁,对现代钢铁工业的发展作出了重大的贡献六、电炉底吹电炉底吹:通过置于炉底的喷嘴将N2、Ar、CO2、CO、CH4、O2等气体根据工艺要求吹入炉内熔池以达到加速熔化,促进冶金反应过程的目的。
炼钢工艺流程

炼钢工艺流程炼钢是钢铁冶炼过程中炼钢厂使用铁矿石、硅石等原料经过多道工序综合制备出含碳量和特定化学组份结构的钢铁制品的重要环节。
炼钢工艺流程是炼钢厂为达到特定的质量标准,满足不同类型钢铁制品的性能要求,确定出的一系列安排和操作步骤。
炼钢工艺流程包括五个主要环节:原料准备、热处理、冶炼、凝固以及加工。
首先,原料准备环节是炼钢过程的开始,包括矿石的抽样和分析、调节化学成份、优化元素组成、除杂筛选、铁矿石去矿化处理等。
经过对原料的系统分析和调节,以确保钢的成分和性能,其中最重要的是对碳和硅的调节,控制碳含量的同时,将硅含量控制在适当的范围内。
其次,热处理是为了提高特定加工动态性能要求而进行的热质量改性环节,最常用的有正火处理、回火处理、正回火处理以及其他多种热处理工艺,在此基础上进一步增强钢的耐蚀性、耐磨性和硬度等特性,以满足客户的要求。
接着,冶炼是将历经热处理的原料熔化,形成融合的熔池,按照特定的工艺标准,加入化学元素及添加剂进行淬火,以获得指定性能的钢铁材料,而在冶炼过程中,采用工艺一定,元素组成一致,温度恒定,层流及混合场强度适宜,满足工艺质量要求,防止杂质污染等要求。
凝固是冶炼不可缺少的环节,它可以使钢的组织结构稳定,缩小晶粒细度,改善钢的性能,还可以增加材料的硬度和抗磨性,并减少材料的冷弯变形率,从而使钢铁制品更为坚韧,再加上钢的化学含量特别是碳含量的控制,质量问题也就得到解决。
最后,加工是将炼钢得到的钢铁制品加工成各类零件和外观效果,根据客户的要求,一般分为热处理、机加工和表面处理三个环节。
而机加工技术包括传统加工和数控加工,数控加工技术可以提高工艺性能和生产效率,准确切削,有助于实现定位精度和产品精度。
炼钢工艺流程系统化,每一步要求都是严格的,只有按照标准的要求,才能保证生产的钢铁制品质量,从而达到质量要求。
因此,炼钢工艺流程非常重要,该流程不仅涉及钢铁制品的冶炼过程,还关乎到原料准备、热处理、加工等后续工序,只有将这些环节完善,才能更好的发挥钢铁制品的特性,满足客户的要求,确保产品的有效性和可靠性。
炼钢厂的工艺流程
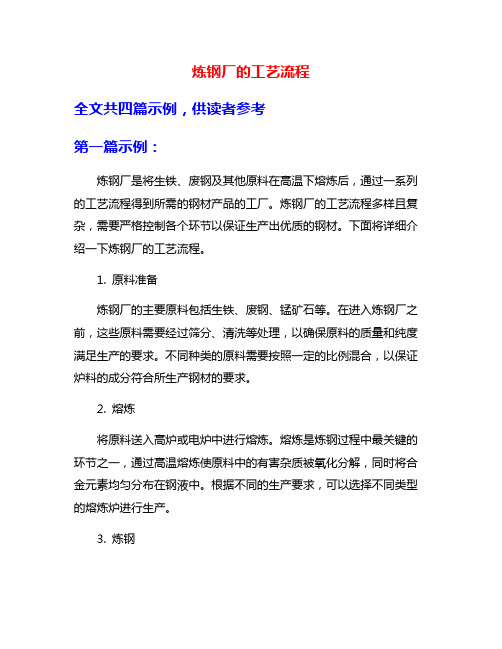
炼钢厂的工艺流程全文共四篇示例,供读者参考第一篇示例:炼钢厂是将生铁、废钢及其他原料在高温下熔炼后,通过一系列的工艺流程得到所需的钢材产品的工厂。
炼钢厂的工艺流程多样且复杂,需要严格控制各个环节以保证生产出优质的钢材。
下面将详细介绍一下炼钢厂的工艺流程。
1. 原料准备炼钢厂的主要原料包括生铁、废钢、锰矿石等。
在进入炼钢厂之前,这些原料需要经过筛分、清洗等处理,以确保原料的质量和纯度满足生产的要求。
不同种类的原料需要按照一定的比例混合,以保证炉料的成分符合所生产钢材的要求。
2. 熔炼将原料送入高炉或电炉中进行熔炼。
熔炼是炼钢过程中最关键的环节之一,通过高温熔炼使原料中的有害杂质被氧化分解,同时将合金元素均匀分布在钢液中。
根据不同的生产要求,可以选择不同类型的熔炼炉进行生产。
3. 炼钢将熔炼后的熔铁进行炼钢处理。
炼钢是将熔铁中的碳含量、硫、磷等有害元素降低,同时添加适量的合金元素和脱氧剂,以调整钢液的成分和性能。
在炼钢过程中需要控制好炉温、时间、搅拌等参数,确保炼钢的过程充分、均匀。
4. 过程处理在炼钢过程中,会产生大量废气、废渣和废水等副产品。
为了减少环境污染,炼钢厂需要配备相应的废气处理设备、废渣处理设备等,对排放的废气、废渣进行处理,以达到环保标准。
5. 钢材成品经过炼钢处理后,钢水会被铸造成坯料,再通过轧制、淬火、酸洗、镀锌等工艺加工成成品钢材。
最终形成各种不同规格、用途的钢材产品,供应给不同行业的客户,如建筑、汽车制造、机械加工等领域。
炼钢厂的工艺流程经过原料准备、熔炼、炼钢、过程处理、成品制造等环节,全过程需要严格控制各个环节,确保生产出符合标准和客户需求的高质量钢材产品。
在生产过程中还需要关注环保问题,处理好废气、废渣等副产品,保护环境和人民的健康。
希望通过对炼钢厂工艺流程的介绍,让更多人了解钢铁行业的生产过程,关注环保和可持续发展。
第二篇示例:炼钢是将铁水经过一系列工艺处理,使其脱除杂质,提高纯度,最终得到符合要求的钢材的过程。
简述高炉炼铁的基本过程

简述高炉炼铁的基本过程高炉炼铁是一种产生高质量生铁的主要方法,在钢铁工业中得到广泛应用。
下面将对高炉炼铁的基本过程进行详细描述。
高炉炼铁基本过程分为三个步骤:准备工作、冶炼过程和处理产物。
一、准备工作高炉炼铁的准备工作包括矿石的选矿、破碎、筛分、混合和预处理,以及高炉的预热和点火。
1.选矿:选矿是将矿石中的有用成分以及杂质进行分离的过程。
通常会根据矿石的性质和要求,对矿石进行鉴别和分类。
2.破碎:矿石经过选矿后,需要进行破碎,以便更好地与其他原料混合。
3.筛分:破碎后的矿石需要通过筛分装置进行分级,从而得到不同粒径范围的矿石。
4.混合:将不同粒径范围的矿石按比例混合,从而保证高炉炉料的均匀性。
5.预处理:预处理包括烘干、预热和固硬。
烘干是为了去除矿石中的水分,预热是为了降低高炉内的燃料消耗,固硬是为了增加料柱的强度。
6.高炉预热和点火:在准备工作的最后,高炉需要进行预热和点火。
预热可以提高高炉的工作效率,点火是将高炉内的燃料点燃,开始冶炼过程。
二、冶炼过程高炉炼铁的冶炼过程主要包括五个部分:焦化、还原、熔融、炉渣形成和产铁。
1.焦化:焦炭是高炉冶炼的主要燃料之一、焦化是将煤炭通过加热、干馏和冷却等过程,得到含有高固定碳和较低灰分的焦炭的过程。
2.还原:高炉冶炼的核心过程是还原。
在高炉中,焦炭作为还原剂,将含氧化铁的矿石还原为铁金属。
还原反应产生的一氧化碳进一步与矿石中的铁氧化物反应,生成铁和二氧化碳。
3.熔融:矿石还原后的金属铁会逐渐熔化,形成称为铁水的液体金属铁。
铁水温度通常在1400℃以上。
4.炉渣形成:炉渣是由矿石中的非金属物质和冶炼过程中生成的氧化物等组成的。
炉渣具有良好的流动性,可以将冶炼过程中产生的杂质和不溶于金属铁的物质捕捉和分离。
5.产铁:在高炉的下部,金属铁和炉渣被分离。
金属铁通过开口孔流出高炉,进入铁水池中。
炉渣则从高炉的炉底排出。
三、处理产物产铁后,还需要进行一系列的处理工艺来得到高质量的生铁。
钢铁厂工艺流程

钢铁厂工艺流程
《钢铁厂工艺流程》
钢铁厂是生产钢铁产品的重要工业场所,其工艺流程十分复杂。
以下是钢铁厂的主要工艺流程:
1. 原料准备:钢铁厂的主要原料包括铁矿石、焦炭和石灰石。
这些原料会经过破碎、磨碎和混合等步骤进行准备,以便用于后续的冶炼工艺。
2. 炼铁工艺:炼铁是将铁矿石中的铁氧化物还原成金属铁的过程。
在高炉中,原料混合物经过预热后,加入高炉炉料层,并通过加热、还原和熔融等步骤,最终得到熔融的生铁。
3. 轧钢工艺:生铁需要经过轧钢工艺才能生产出可用的钢铁产品。
这一工艺包括熔炼、浇铸、轧制和淬火等步骤,可以生产出各种规格和形状的钢材。
4. 产品加工:钢铁产品在生产出来后,还需要进行一系列的加工和处理,例如切割、焊接、热处理等,以适应各种不同的用途。
5. 环保处理:钢铁厂的生产工艺也需要考虑环保因素。
废气、废水和固体废物的处理以及资源的循环利用,对于钢铁厂的可持续发展至关重要。
总体来说,钢铁厂的工艺流程是一个综合性的过程,需要各种
技术和设备的协同作用。
只有不断优化工艺流程,并且严格遵守环保法规,钢铁厂才能够生产出高质量的钢铁产品,并且保护环境。
高炉炼铁工艺流程
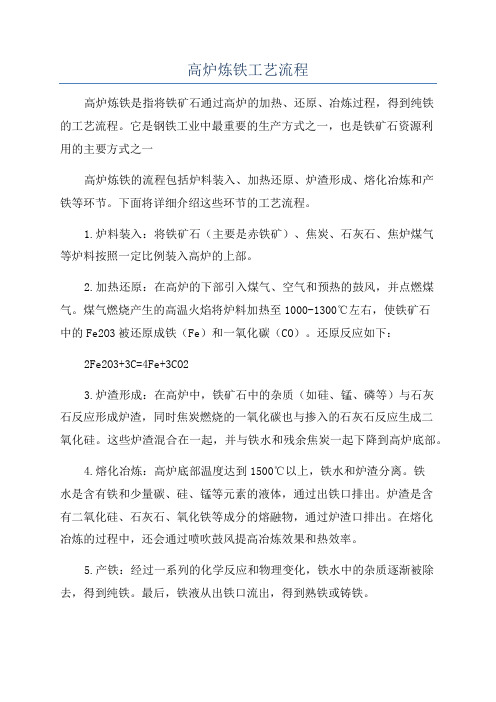
高炉炼铁工艺流程
高炉炼铁是指将铁矿石通过高炉的加热、还原、冶炼过程,得到纯铁
的工艺流程。
它是钢铁工业中最重要的生产方式之一,也是铁矿石资源利
用的主要方式之一
高炉炼铁的流程包括炉料装入、加热还原、炉渣形成、熔化冶炼和产
铁等环节。
下面将详细介绍这些环节的工艺流程。
1.炉料装入:将铁矿石(主要是赤铁矿)、焦炭、石灰石、焦炉煤气
等炉料按照一定比例装入高炉的上部。
2.加热还原:在高炉的下部引入煤气、空气和预热的鼓风,并点燃煤气。
煤气燃烧产生的高温火焰将炉料加热至1000-1300℃左右,使铁矿石
中的Fe2O3被还原成铁(Fe)和一氧化碳(CO)。
还原反应如下:2Fe2O3+3C=4Fe+3CO2
3.炉渣形成:在高炉中,铁矿石中的杂质(如硅、锰、磷等)与石灰
石反应形成炉渣,同时焦炭燃烧的一氧化碳也与掺入的石灰石反应生成二
氧化硅。
这些炉渣混合在一起,并与铁水和残余焦炭一起下降到高炉底部。
4.熔化冶炼:高炉底部温度达到1500℃以上,铁水和炉渣分离。
铁
水是含有铁和少量碳、硅、锰等元素的液体,通过出铁口排出。
炉渣是含
有二氧化硅、石灰石、氧化铁等成分的熔融物,通过炉渣口排出。
在熔化
冶炼的过程中,还会通过喷吹鼓风提高冶炼效果和热效率。
5.产铁:经过一系列的化学反应和物理变化,铁水中的杂质逐渐被除去,得到纯铁。
最后,铁液从出铁口流出,得到熟铁或铸铁。
炼铁工艺流程

炼铁工艺流程炼铁是一种将生铁矿石转化为钢铁的重要工艺过程。
这个过程经历了多个关键步骤和技术流程,涉及到多种设备和化学反应。
在本文中,我们将深入探讨炼铁工艺流程的各个方面,从焦化和还原到冶炼和精炼,以及最终的铁水浇铸过程。
首先,让我们从焦化和还原开始。
在炼铁工艺中,焦化是将高质量的煤进行加热处理,以去除其中的杂质,同时得到一种高碳含量的固体燃料,即焦炭。
这个过程主要发生在焦炉中,通过控制温度和其他参数来实现。
焦炭在后续的炼铁过程中起到了还原剂的作用,将矿石中的氧化物还原成金属铁。
接下来是冶炼过程。
在这个过程中,焦炭和矿石以及其他添加剂被放入高炉中进行氧化还原反应。
高炉是一个巨大的结构,有很强的耐火材料保护,能够承受极高的温度和压力。
在高炉中,焦炭与矿石共同产生强烈的反应,使矿石中的铁氧化物被还原为金属铁。
在冶炼过程中,还需要考虑矿石的种类和质量。
不同种类的矿石具有不同的化学成分和特性,因此对于不同的矿石,所采用的冶炼工艺和条件也会有所不同。
例如,高磷含量的矿石需要采取特殊的处理方法,以减少磷在最终产品中的含量。
因此,对矿石的分析和评估是炼铁工艺中非常关键的一步。
而后是精炼过程。
在冶炼过程中产生的生铁质量并不完全符合要求,还需进行精炼处理以去除其中的杂质和不纯物质。
一种常用的精炼方法是转炉法,即将冶炼好的生铁倒入转炉中,在高温下与氧气进行反应,从而将其中的碳和其他杂质氧化掉。
通过这个过程,可以得到更纯净的金属铁。
最后,是铁水浇铸过程。
在炼铁工艺中,冶炼好的金属铁被转化为铁水,即液态的铁。
这个过程通过将金属铁倒入特定的铁水包或铁水槽中来实现。
铁水可以直接用于铸造各种铁制品,如铁轨、钢板等。
在这个过程中,需要注意控制铁水的温度和流动性,以确保最终产品的质量。
综上所述,炼铁工艺流程涵盖了焦化和还原、冶炼、精炼以及铁水浇铸等多个步骤和过程。
每一个步骤都需要精确的操作、合适的设备和技术。
通过这些过程,生铁矿石最终被转化为高质量的钢铁产品。
钢铁生产工艺流程
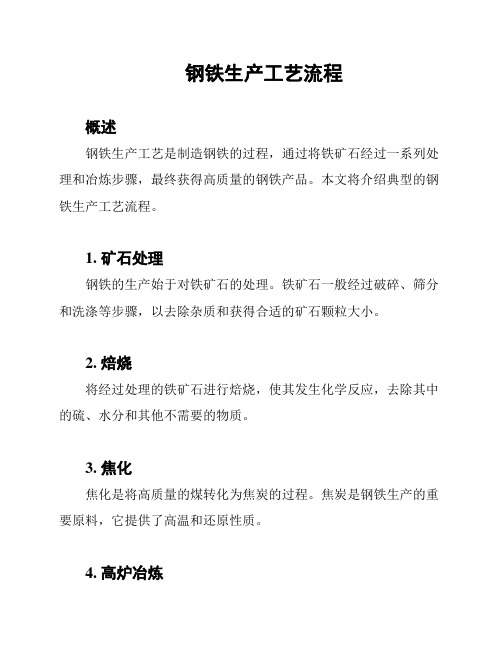
钢铁生产工艺流程概述钢铁生产工艺是制造钢铁的过程,通过将铁矿石经过一系列处理和冶炼步骤,最终获得高质量的钢铁产品。
本文将介绍典型的钢铁生产工艺流程。
1. 矿石处理钢铁的生产始于对铁矿石的处理。
铁矿石一般经过破碎、筛分和洗涤等步骤,以去除杂质和获得合适的矿石颗粒大小。
2. 焙烧将经过处理的铁矿石进行焙烧,使其发生化学反应,去除其中的硫、水分和其他不需要的物质。
3. 焦化焦化是将高质量的煤转化为焦炭的过程。
焦炭是钢铁生产的重要原料,它提供了高温和还原性质。
4. 高炉冶炼高炉是进行钢铁冶炼的关键设备。
在高炉中,将焙烧后的铁矿石、焦炭和添加剂等投入,经过高温下的还原和熔化反应,产生液态的铁。
5. 炼钢炼钢是将高炉产生的液态铁通过炼钢炉进行进一步的冶炼和精炼。
这个过程中,会加入合适的合金材料和调整熔炼温度,以获得所需的钢铁品质。
6. 连铸连铸是将炼钢炉中的钢液通过连续铸造过程转化为坯料或铸件。
连铸工艺可以生产各种形状和尺寸的钢铁产品。
7. 热轧热轧是将连铸坯进行加热和轧制形成具有所需尺寸和形状的钢材板。
热轧工艺可以提供高强度和良好的塑性性能。
8. 冷轧冷轧是将热轧钢材进行冷加工,提高钢材的表面光洁度和尺寸精度。
冷轧还可以改变钢材的力学性能和组织结构。
9. 其他加工和处理最后,钢材可以通过切割、焊接、热处理等工艺进行进一步加工和处理,以满足特定的需求和应用。
以上是钢铁生产的典型工艺流程。
实际的钢铁生产工艺可能因企业和产品的不同而略有差异,但总体流程通常类似。
这些过程需要精确的控制和高品质的原材料,以确保最终生产出符合要求的钢铁产品。
炼钢的工艺流程有几种
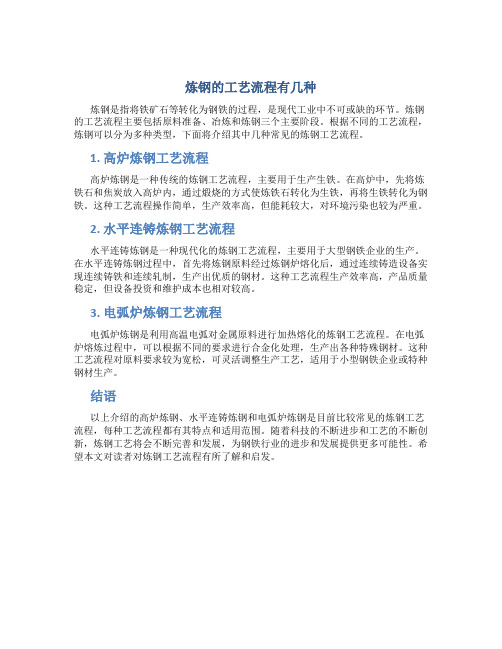
炼钢的工艺流程有几种
炼钢是指将铁矿石等转化为钢铁的过程,是现代工业中不可或缺的环节。
炼钢的工艺流程主要包括原料准备、冶炼和炼钢三个主要阶段。
根据不同的工艺流程,炼钢可以分为多种类型,下面将介绍其中几种常见的炼钢工艺流程。
1. 高炉炼钢工艺流程
高炉炼钢是一种传统的炼钢工艺流程,主要用于生产生铁。
在高炉中,先将炼铁石和焦炭放入高炉内,通过煅烧的方式使炼铁石转化为生铁,再将生铁转化为钢铁。
这种工艺流程操作简单,生产效率高,但能耗较大,对环境污染也较为严重。
2. 水平连铸炼钢工艺流程
水平连铸炼钢是一种现代化的炼钢工艺流程,主要用于大型钢铁企业的生产。
在水平连铸炼钢过程中,首先将炼钢原料经过炼钢炉熔化后,通过连续铸造设备实现连续铸铁和连续轧制,生产出优质的钢材。
这种工艺流程生产效率高,产品质量稳定,但设备投资和维护成本也相对较高。
3. 电弧炉炼钢工艺流程
电弧炉炼钢是利用高温电弧对金属原料进行加热熔化的炼钢工艺流程。
在电弧炉熔炼过程中,可以根据不同的要求进行合金化处理,生产出各种特殊钢材。
这种工艺流程对原料要求较为宽松,可灵活调整生产工艺,适用于小型钢铁企业或特种钢材生产。
结语
以上介绍的高炉炼钢、水平连铸炼钢和电弧炉炼钢是目前比较常见的炼钢工艺流程,每种工艺流程都有其特点和适用范围。
随着科技的不断进步和工艺的不断创新,炼钢工艺将会不断完善和发展,为钢铁行业的进步和发展提供更多可能性。
希望本文对读者对炼钢工艺流程有所了解和启发。
炼钢厂的工艺流程

炼钢厂的工艺流程全文共四篇示例,供读者参考第一篇示例:炼钢厂是将生铁或废钢通过高温熔炼、除杂质、合金和成型等工艺过程,生产出各种钢材产品的厂家。
炼钢厂的工艺流程包括原料准备、炼钢、连铸、轧钢等多个环节,下面就来详细介绍一下炼钢厂的工艺流程。
一、原料准备炼钢厂的原料主要包括铁矿石、煤炭、废钢和废铁等。
在炼钢的过程中,铁矿石是最主要的原料,其含铁量高低直接影响到生产效率和产品质量。
煤炭在高炉燃烧时提供热量,促使铁矿石还原为生铁。
而废钢和废铁则是通过熔融再生钢材的重要原料,对环保和资源循环利用起着重要作用。
二、炼钢炼钢是指将生铁或废钢加热至熔化状态,并通过除渣、除氧化物、合金和调节成分等工艺过程,生产出符合标准的钢材产品。
在炼钢过程中,生铁首先通过高炉冶炼得到熔融铁水,然后经过转炉、电炉或其他炼钢设备进行炼钢操作。
转炉炼钢是较常用的工艺,通过转炉炼钢可有效去除生铁中的杂质,调节成分,得到合格的钢材产品。
三、连铸连铸是将炼钢得到的熔钢直接注入到结晶器中,通过凝固成形,制成长方坯或圆坯等半成品,在后续的轧钢工艺中进行进一步加工。
连铸工艺具有生产效率高、能耗低的特点,对提高钢铁生产效率、减少能源消耗具有重要意义。
四、轧钢轧钢是将半成品坯料通过热轧、冷轧等工艺进行成形,生产出各种规格的钢材产品。
热轧是利用高温将坯料连续轧制,消除残余应力,得到粗毛坯的工艺;而冷轧是在室温下对热轧坯料进行轧制,得到较为平整光滑的表面,提高产品的表面质量。
炼钢厂的工艺流程是一个复杂的系统工程,需要各种设备、技术和人才协同作业,才能保证生产出高质量的钢材产品。
炼钢厂在生产过程中要注意环保、安全、节能等方面的要求,促进炼钢产业的可持续发展。
希望通过对炼钢厂工艺流程的介绍,让更多人了解炼钢产业的重要性和复杂性,支持和关注炼钢生产的发展。
第二篇示例:炼钢厂是生产钢材的重要工业设施,其工艺流程复杂且关键,涉及多个生产环节和工艺参数的控制。
本文将详细介绍炼钢厂的工艺流程,希望能够为读者提供更深入的了解。
钢铁企业工艺流程

钢铁行业工艺流程钢铁生产的工艺流程大致分为:选矿,烧结,焦化,炼铁,炼钢,连铸, 轧钢等过程;辅助系统有:制氧/制氮,循环水系统,烟气除尘及煤气回收 等。
1选矿工序选矿是冶炼前的准备工作,从矿山开采下来矿石以后,首先需要将含铁、 铜、铝、锰等金属元素高的矿石甄选出来,为下一步的冶炼活动做准备。
选矿一般分为破碎、磨矿、选别三部分。
其中,破碎又分为:粗破、中破 和细破;选别依方式不同也可分为:磁选、重选、浮选等。
选矿工序原料:原矿石。
选矿工序产物:铁精矿。
选矿工序设备:矿石破碎设备:颚式破碎机、锤式破碎机。
磨矿工艺设备:球磨机、螺旋分级机。
选别工艺设备:浮选机、磁选机。
铁矿原料 钢成品原煤 粉状含铁原料 电、煤气焦化粗苯废气 焦油焦炉煤气 电 煤气 氧气 电氧气煤气块矿 辅料 废铁 水 废钢 水 电、煤气电、煤气 T 球团炉尘宣… 炉尘蒸汽高炉渣高炉煤气 转炉渣转炉煤气废气2烧结工序为了保证供给高炉的铁矿石中铁含量均匀,并且保证高炉的透气性,需要把选矿工艺产出的铁精矿制成10-25mm的块状原料。
铁矿粉造块目前主要有两种方法:烧结法和球团法。
铁矿粉造块的目的:♦去除有害杂质,回收有益元素,保护环境;♦综合利用资源,扩大炼铁用的原料种类;♦改善矿石的冶金性能,适应高炉冶炼对铁矿石的质量要求。
2.1烧结法烧结是钢铁生产工艺中的一个重要环节,它是将铁矿粉、粉(无烟煤)和石灰、高炉炉尘、轧钢皮、钢渣按一定配比混匀。
经烧结而成的有足够强度和粒度的烧结矿可作为炼铁的熟料。
烧结矿生产流程:烧结料的准备,配料与混合,烧结和产品处理;烧结矿生产原料:含铁原料、熔剂、燃料;烧结矿生产产物:烧结矿和球团矿;烧结矿生产设备:带式抽风烧结机。
电结矿 结矿精矿粉富矿粉 碎焦 高炉灰 无烟煤 轧钢皮 石灰石 白云石2.2球团法球团是把细磨铁精矿粉或其他含铁粉料添加少量添加剂混合后,在加水润湿的条件下,通过造球机滚动成球,再经过干燥焙烧,固结成为具有一定强度和冶金性能的球型含铁原料。
简述钢铁生产工艺流程

简述钢铁生产工艺流程
钢铁生产工艺流程一般包括以下几个步骤:
1. 炼铁:首先,通过高炉或直接还原法将铁矿石中的铁氧化物还原为铁。
矿石经过破碎、磨矿、浸出等处理后,与焦炭、石灰石等一起进入高炉,经过煅烧、冶炼、热平衡等过程,最终得到铁液。
2. 炼钢:将炼铁得到的铁液中的杂质进行进一步的去除和调整,得到所需要的合金成分和质量。
炼钢的方法可以采用氧气转炉、电弧炉、电渣炉等不同的设备。
3. 铸造:将炼钢得到的熔融金属倒入预先设计好的铸模中,让其冷却凝固成为不同形状的铁坯、铁锭或铸件。
铸造过程中需要注意铁液的温度、压力和冷却速度等因素,以确保所得到的铸件具有所需的结构和性能。
4. 轧制:铸造得到的铁坯或铸件需要经过轧机进行加工和成型。
通过热轧和冷轧等不同的轧制方法,可以得到不同规格和形状的钢材产品。
5. 热处理:通过加热和冷却的处理过程,对已经轧制成型的钢材进行去应力、改善组织结构和物理性能等。
常见的热处理方法有淬火、回火、正火等。
6. 表面处理:对钢材表面进行防腐、涂层或装饰性处理。
涂层可以包括镀锌、喷漆、喷塑等,以保护钢材不受氧化、腐蚀和
环境损害。
7. 检验和质量控制:对生产出的钢材进行检验和质量控制,包括化学成分分析、力学性能测试、金相组织观察等。
确保产品符合标准和客户的要求。
以上是钢铁生产工艺的基本流程,不同的钢铁厂家和产品可能会有一些差异和特殊步骤。
炼钢工艺及流程

1)高炉冶炼用的原料
主要由铁矿石、燃料(焦炭)和熔剂(石灰石)三部分组成。
通常,冶炼1吨生铁需要1.5-2.0吨铁矿石,0.4-0.6吨焦炭,0.2-0.4吨熔剂,总计需要2-3吨原料。为了保证高炉生产的连续性,要求有足够数量的原料供应。
2)工艺流程
生铁的冶炼虽原理相同,但由于方法不同、冶炼设备不同,所以工艺流程也不同。下面分别简单予以介绍。
f.上轧辊平衡装置:用于抬升上辊和防止轧件进出轧辊时受冲击的装置。形式有﹕弹簧式﹑多用在型材轧机上﹔重锤式﹐常用在轧辊移动量大的初轧机上﹔液压式﹐多用在四辊板带轧机上。
g.为提高作业率﹐要求轧机换辊迅速﹑方便。换辊方式有 C 形钩式﹑套筒式﹑小车式和整机架换辊式四种。用前两种方式换辊靠吊车辅助操作﹐而整机架换辊需有两套机架﹐此法多用于小的轧机。小车换辊适合于大的轧机﹐有利于自动化。目前﹐轧机上均采用快速自动换辊装置﹐换一次轧辊只需 5 ~ 8 分钟。
中国于1871 年在福州船政局所属拉铁厂( 轧钢厂 ) 开始使用轧机﹔轧制厚15mm 以下的铁板﹐ 6 ~ 120mm 的方﹑圆钢。 1890 年汉冶萍公司汉阳铁厂装有蒸汽机拖动的横列双机架 2450mm 二辊中板轧机和蒸汽机拖动的三机架横列二辊式轨梁轧机以及 350/300mm 小型轧机。随着冶金工业的发展﹐现已有多种类型轧机。
1、什么是轧机?
轧机是实现金属轧制过程的设备。泛指完成轧材生产全过程的装备﹐包括有主要设备﹑辅助设备﹑起重运输设备和附属设备等。但一般所说的轧机往往仅指主要设备。
2、轧机的发展史
据说在14 世纪欧洲就有轧机﹐但有记载的是1480 年意大利人 达 ' 芬奇 (Leonardo da Vinci) 设计出轧机的草图。1553 年法国人布律列尔 (Brulier) 轧制出金和银板材﹐用以制造钱币。此后在西班牙﹑比利时和英国相继出现轧机。1728 年设计的生产圆棒材用的轧机为英国设计的生产圆棒材用的轧机。英国于1766 年有了串行式小型轧机﹐19 世纪中叶﹐第一台可逆式板材轧机在英国投产﹐并轧出了船用铁板。1848 年德国发明了万能式轧机﹐ 1853 年美国开始用三辊式的型材轧机﹐并用蒸汽机传动的升降台实现机械化。接着美国出现了劳特式轧机。1859 年建造了第一台连轧机。万能式型材轧机是在1872 年出现的﹔20 世纪初制成半连续式带钢轧机﹐由两架三辊粗轧机和五架四辊精轧机组成。
炼钢生产过程及流程图详解 全

钢铁生产工艺主要包括:炼铁、炼钢、轧钢等流程。
(1)炼铁:就是把烧结矿和块矿中的铁还原出来的过程。
焦炭、烧结矿、块矿连同少量的石灰石、一起送入高炉中冶炼成液态生铁(铁水),然后送往炼钢厂作为炼钢的原料。
炼铁是还原反应。
先是利用氧把矿石中铁及其他物质氧化为三氧化二铁、硫、磷的氧化物等。
硫的氧化物经过处理后排放,磷的氧化物还要加入石灰后转化为矿渣后排出。
主要反应为利用 C 把铁的氧化物还原 2 Fe2O3+ 3 C=4 Fe+ 3 CO2.(2)炼钢:是把原料(铁水和废钢等)里过多的碳及硫、磷等杂质去掉并加入适量的合金成分。
炼钢是氧化反应,是炼铁后的进一步加工。
主要是除去Fe中多余的 C ,因为 C 的含量太高影响钢的韧性。
反应式为: C+O2 = CO2 。
(3)连铸:将钢水经中间罐连续注入用水冷却的结晶器里,凝成坯壳后,从结晶器以稳定的速度拉出,再经喷水冷却,待全部凝固后,切成指定长度的连铸坯。
(4)轧钢:连铸出来的钢锭和连铸坯以热轧方式在不同的轧钢机轧制成各类 钢材,形成产品。
炼钢工艺总流程图炼焦生产流程:炼焦作业是将焦煤经混合,破碎后加入炼焦炉内经干馏后产生热焦碳及粗焦炉气之制程。
烧结生产流程:烧结作业系将粉铁矿,各类助熔剂及细焦炭经由混拌、造粒后,经由布料系统加入烧结机,由点火炉点燃细焦炭,经由抽气风车抽风完成烧结反应,高热之烧结矿经破碎冷却、筛选后,送往高炉作为冶炼铁水之主要原料。
还原气体,还原铁矿石,产生熔融铁水与熔渣之炼铁制程。
转炉生产流程:炼钢厂先将熔铣送前处理站作脱硫脱磷处理,经转炉吹炼后,再依订单钢种特性及品质需求,送二次精炼处理站(RH真空脱气处理站、Ladle Injection盛桶吹射处理站、VOD真空吹氧脱碳处理站、STN搅拌站等)进行各种处理,调整钢液成份,最后送大钢胚及扁钢胚连续铸造机,浇铸成红热钢胚半成品,经检验、研磨或烧除表面缺陷,或直接送下游轧制成条钢、线材、钢板、钢卷及钢片等成品。
钢的冶炼过程

钢的冶炼过程钢铁,其实是两个名词——“钢”和“铁”的合称。
炼钢之前先要炼铁。
「铁」分为生铁和熟铁。
「钢」的含碳量介于生铁和熟铁之间。
「生铁」一般指含碳量在2~6.69%的铁的合金。
又称铸铁。
生铁里除含碳外,还含有硅、锰及少量的硫、磷等,它可铸不可锻。
「熟铁」是用生铁精炼而成的比较纯的铁。
含碳量在0.02%以下,又叫锻铁、纯铁。
纯铁要求碳、磷、硫等杂质元素含量很低,其冶炼难度较大,制造成本远大于生铁和钢。
一、铁的冶炼炼铁方法主要有高炉法、直接还原法、熔融还原法等,其原理是矿石在特定的气氛中(还原物质CO、H2、C;适宜温度等)通过物化反应获取还原后的生铁。
生铁除了少部分用于铸造外,绝大部分是作为炼钢原料。
「高炉炼铁」是现代炼铁的主要方法,钢铁生产中的重要环节。
由于技术经济指标良好,工艺简单,生产量大,劳动生产率高,能耗低,高炉法生产的铁占世界铁总产量的95%以上。
高炉是近似于圆柱形的炉子,它的外面包以钢板,内壁砌以耐火砖,整个炉子建筑在很深的混凝土基础上。
高炉生产时,从炉顶装入铁矿石、焦炭、造渣用熔剂(石灰石),从位于炉子下部沿炉周的风口吹入经预热的空气。
在高温下焦炭中的碳同鼓入空气中的氧燃烧生成的一氧化碳和氢气,在炉内上升过程中除去铁矿石中的氧,从而还原得到铁。
炼出的铁水从铁口放出。
铁矿石中不还原的杂质和石灰石等熔剂结合生成炉渣,从渣口排出。
产生的煤气从炉顶导出,经除尘后,作为热风炉、加热炉、焦炉、锅炉等的燃料。
原料:铁矿石、溶剂、燃料②溶剂矿石中的脉石和燃料中的灰分,都含有一些熔点很高的化合物(如SiO2熔点为1625℃,Al2O3熔点为2050℃),它们在高炉冶炼的温度下,不能熔化成液体,因而不能使它们很好地与铁液分离,同时也使炉子的操作发生困难。
加入熔剂的目的在于其与这些高熔点的化合物形成低熔点的炉渣,以便在高炉冶炼温度下完全液化,并保持相当的流动性,以达到很好地与金属分离之目的,保证生铁的质量。
- 1、下载文档前请自行甄别文档内容的完整性,平台不提供额外的编辑、内容补充、找答案等附加服务。
- 2、"仅部分预览"的文档,不可在线预览部分如存在完整性等问题,可反馈申请退款(可完整预览的文档不适用该条件!)。
- 3、如文档侵犯您的权益,请联系客服反馈,我们会尽快为您处理(人工客服工作时间:9:00-18:30)。
中文 电炉 废钢 氧-燃料烧嘴/喷枪 出钢至出钢的周期 钢水包/铁水包 板坯 方坯 石墨电极 高炉设计/专利公司名
英文 EAF scrap oxy-fuel burner tap-to-tap cycle ladle slab bloom/billet graphite electrode Paul Wurth
炼铁
炼钢
相同点
都是氧化还原反应
目的
把铁从铁矿石中还原出来
降低含碳量; 除硫磷等杂质; 调节合金元素的含量
不同点 原理 氧化-还原反应,还原剂还原出铁 氧化-还原反应,氧化剂氧化杂质除去
原料 设备
铁矿石、石灰石、焦碳、空气 炼铁高炉
生铁(废钢)、纯氧、氧化钙 转炉、平炉、电炉
14
炼钢
转炉结构图
15
转炉炼钢:
(氧气)
②除硅,锰,碳等杂质:Si+2FeO=SiO2+2Fe Mn+FeO=MnO+Fe C+FeO=CO+Fe
③造渣: CaO+SiO2=CaSiO3
(生石灰)
硫、磷杂质与生石灰作用形成炉渣被除去。
④脱氧: Si+2FeO=SiO2+2Fe (脱氧剂:硅铁,锰铁) 调节合金元素
13
炼铁和炼钢
炼铁和炼钢的比较
4
炼铁原料:铁矿石,焦炭,石灰石:
5
高炉构造:
6
7
炼铁:
3CO+Fe2O3 =2Fe+3CO2
CO2+C=2CO C+O2=CO2
8
9
炼铁生产工艺流程及下游产品处理:
10
炼铁
一 炼铁:铁矿石(化合态)→铁单质(游离态)
(1)基本反应原理:3CO+ Fe2O3=高==温==2Fe+3CO2
N2
Galvanising Line
Cold Rolled Products.
Galvanised Sheet and Coil.
25
人最宝贵的是生命。生命每个人只有一次 。 人的一生应当这样度过:当回忆往事的时候,他不会因为虚 度年华而悔恨,也不会因为碌碌无为而羞愧;。。。。。
保尔 柯察金 钢铁是怎么炼成的?
钢铁 是怎样 炼成的?
盈德气体应用技术讨论会
1
Objectives:
1。重温炼铁和炼钢的基础知识 2。了解炼铁和炼钢的流程和设备 3。通过学习加深对我们用户的了解 4。自学,互学,共同学习,一起成才
2
生铁和钢
生
炼钢生铁(白口铁)
铁
铸造生铁(灰口铁)
铁 合 金
钢
球墨生铁 合金生铁
碳素钢
低碳钢
中碳钢 高碳钢
Some useful approximations are:
✓ 0.5 to 0.6 ton of oxygen are consumed per ton of coal injected. ✓ At high coal injection rates 100 Nm3 or 150kg of oxygen are consumed per ton of hot metal. ✓ A large 10,000 TPD blast furnace utilising max. coal injection rates will result in an oxygen demand of 1400 to 1500 TPD O2.
中文 热风炉 干法息焦
出铁场 耐火砖网格 炉渣 直接还原铁
吹氧炼钢 (BOS)
吹氧枪 溅渣护炉
英文
stove
coke dry quenching (CDQ) cast house
refractory checkers
slag
Direct Reduced Iron, DRI Basic Oxygen Steelmaking lance
24
ห้องสมุดไป่ตู้
钢铁生产全流程中的气体供应和应用技术 Gas Supplies and Applications in Iron & Steel Making
Coal
Fluxes Iron Ore
N2
Coke Ovens
N2
Coke Sinter
Sinter Plant
Iron Ore
O2
Coke
Direct Reduction Fluxes Furnace
23
炼造钢铁时的供气 (二)
氧、氮、氩是炼钢企业不可缺少的工业气体,据报导,目前炼铁、炼钢、轧钢的综合氧耗已达 100~140m3/t,氮耗80~120m3/t,氩耗3~4m3/t。
目前,钢铁企业用的大型空分设备主要采用分子筛常温净、增压膨胀、填料塔和全精馏制氩的 外压缩流程和内压缩流程两种形式,同时考虑提取部分液体作为生产调峰用。
合金钢
生铁和钢的比较
铁的合金
生铁
钢
含碳的质量分数 2~4.3%
0.03~2%
杂质
硅锰(较多) 硫磷(较多)
硅锰(适量) 硫磷(较多)
机械加工
可铸不可锻
可铸,可锻,可压延
机械性能
硬而脆
硬而韧,有弹性
3
炼铁中的问题:
✓ 铁是以什么形态存在的? ✓ 铁的熔点是多少? ✓ 炼铁过程中需要哪些原料? ✓ 它们各自的作用的是什么? ✓ 炼铁是在什么设备里进行的? ✓ 炼铁需要什么样的条件? ✓ 焦炭是怎么制成的? ✓ 焦炭在炼铁过程中的作用是什么? ✓ 石灰石在炼铁过程中的作用是什么? ✓ 炼铁过程中产生了哪些有用的副产品?它们是怎么利用的? ✓ 怎样提高炼铁过程中的能源效率? ✓ 炼铁过程中的环保问题 ✓ 炼铁过程中的“休风”,“封炉”,“难行”,“悬料”,“崩料”?
高温
CaCO3===CO2+CaO
CaO+SiO2=CaSiO3 (熔剂:石灰石)
(5)炼铁产品:生铁
11
高炉物料平衡与气体消耗:(供参考)
✓ 通常冶炼 1 吨生铁需要1.5 – 2.0吨铁矿石,0.4 – 0.6 吨焦炭,0.2 – 0.4 吨石灰石。 ✓ 宝钢4063立方米高炉,日产生铁超过10,000吨,炉渣4000吨,日耗焦炭4000多吨。
利用氧化还原反应,在高温下,用还原剂(主要是CO)从铁矿石中还原出铁
(2)设备:高炉
(3)原料:铁矿石,焦炭,石灰石,空气(氧)
(4)炼铁的主要反应过程:
①产生还原剂: C+O2=CO2 CO2+C=2CO (空气,焦炭)
②还原铁矿石:
高温
Fe2O3+3CO==2Fe+3CO2
(铁矿石)
③造渣(除脉石):
16
电炉炼钢:
17
平炉炼钢示意图:
18
19
20
轧钢与轧辊:
21
轧钢:车轮,线材:
22
炼造钢铁时的供气 (一)
—空分设备主要是为冶炼工艺过程提供工业气体。 —氧、氮、氩是钢铁企业不可缺少的工业气体,空分设备为钢铁企业的连续生产源耕源不断地提 供着气体。在炼钢生产工艺过程中要用到氧气、氮气和氩气。 —氧气主要用于吹氧炼钢。吹氧炼钢的主要方式有:转炉纯氧顶吹或底吹炼钢、电孤炉炼钢和平 炉炼钢。转炉炼钢每吨钢耗氧50~60m3;电孤炉炼钢每吨钢耗氧10~25m3;平炉炼钢每吨钢耗耗 氧20~40m3。此外,轧钢每吨钢耗氧3~6m3、钢材加工、连铸坯火焰切割,火焰清除、炉衬火焰 每吨钢耗氧11.4~14.2m3。 —氮气在钢铁厂的应用主要是用作保护气,如轧钢、镀锌、镀铬、热处理(尤为薄钢片)连续铸 造等都要用氮气作保护气,而且氮气纯度要求99.99%以上。 —氩气在炼钢过程的作用:如向熔融的钢水中吹入氩气,使成份均匀,钢液净化,并可除掉溶解 在钢水中的氢、氧、氮等杂质,提高钢坯质量。吹氩还可以取消还原期,缩短冶炼时间,提高产 量,节约电能等。氩气吹炼和保护是提高钢材质量的重要途径。
O2
Blast Furnace
H2
DRI
Scrap Plain Carbon Steel
Electric Arc
N2 Furnace O2 Ar
O2 O2
Electric Arc Furnace
O2
Unrefined Stainless Steel
Ar
Stainless Steel Converter
Nitrogen may be used ➢ to pressurise lock-hoppers to prevent escape of furnace gas during charging ➢ to cool gearboxes associated with the charge distribution system Indicative figures expressed on a per ton of hot metal basis are:
✓ Inerting of coal systems 10Nm3/t ✓ Pnuematic transport of coal 1Nm3/t ✓ Other blast furnace uses 0.01 Nm3/t
12
炼钢
二 炼钢: 生铁 → 钢
(1)需要做到: ①降:降低含碳量 ②除:除去硫、磷等杂质 ③调:调节合金元素的含量
中文
英文
29
Unrefined Carbon Steel
O2
Secondary Refined Carbon or Steelmaking Stainless Steel
N2
O2
Reheat Furnace
Blooms, Billets, Bars