磨具的磨粒率CBN砂轮的浓度计算
CBN砂轮在磨削加工中的应用

CBN砂轮在磨削加工中的应用CBN材料除用来制作刀具外,其最大的应用领域还是制成CBN磨具,用于高速高效磨削和珩磨加工,可使磨削效率大大提高,其磨削精度和质量提高一个等级。
1.磨削汽车零件--凸轮轴和曲轴汽车发动机上的凸轮轴具有多个凸轮,淬火后的凸轮粗磨及精磨是影响凸轮质量的关键工序。
一般都是采用靠模仿形磨削,工件速度的提高受到限制,工件易产生磨削烧伤裂纹,采用靠模仿形磨削,其凸轮表面的轮廊曲线要受砂轮直径大小的影响,所以很难保证凸轮轮廊曲线的正确。
生产实践证明,当砂轮直径大时,磨出的凸轮瘦,当砂轮直径小时,磨出的凸轮胖,只有当砂轮直径接近或等于磨削靠模凸轮的滚轮直径时(一般为φ570mm),其仿形误差接近于零,即磨出的凸轮表面轮廊曲线接近于靠模凸轮。
在实际生产中,所用的砂轮直径一般都是从D600(或610)用到D500,与理想的砂轮直径(570)相差甚多,所以生产中总有大部分凸轮轴的凸轮曲线超标。
为解决这个问题,我们在靠模仿形凸轮磨床上采用CBN砂轮磨削,可把CBN砂轮直径制成D575,CBN磨料层厚为4~5mm,其磨轮的磨削最小直径是D565,磨削直径范围虽然只有10mm,但磨削零件数却相当于几十片普通砂轮,不仅可保证凸轮曲线正确,而且也不会产生磨削烧伤现象。
如Liton工业自动化公司用CBN砂轮磨削凸轮轴,其成本降低了50%,凸轮表面的疲劳强度提高了30%;东风汽车公司襄樊柴油发动机厂用陶瓷结合剂CBN砂轮粗磨冷激铸铁凸轮轴,其凸轮磨削余量t=4~5mm,υ砂=60m/s,工件转速n=100r/min,υf=0.1mm/s,采用高速磨削液,CBN砂轮的寿命基本相当于20片刚玉磨料砂轮。
2.CBN砂轮在内孔磨削中的应用内圆磨削的效率一直很低,其主要原因就是磨削速度、砂轮材质及磨杆的刚性问题。
生产过程中用在修整砂轮、更换砂轮的时间几乎占了单件工时的1/3~1/5。
如果内圆或沟槽磨削采用CBN电镀砂轮,并把砂轮速度提高,增大磨杆直径,便可适当提高工件转速与进给速度,不仅可保证孔(弧)径、槽宽尺寸与形位精度,表面粗糙度和避免烧伤,而且还可以成倍地提高加工效率,降低加工成本。
2018-2019-cbn砂轮知识-范文模板 (8页)
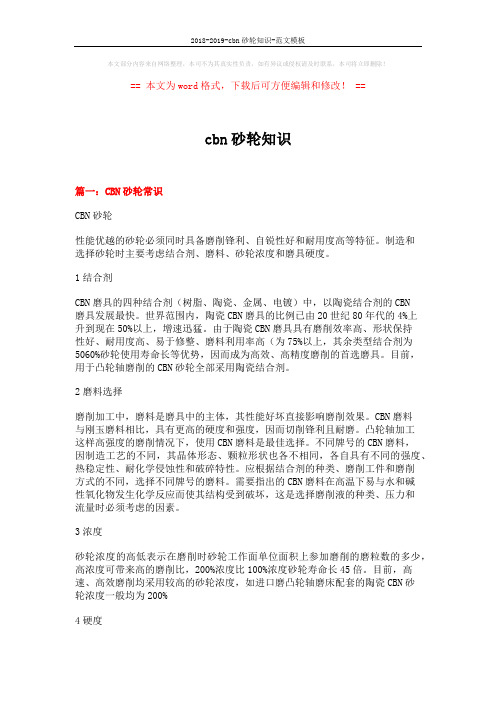
本文部分内容来自网络整理,本司不为其真实性负责,如有异议或侵权请及时联系,本司将立即删除!== 本文为word格式,下载后可方便编辑和修改! ==cbn砂轮知识篇一:CBN砂轮常识CBN砂轮性能优越的砂轮必须同时具备磨削锋利、自锐性好和耐用度高等特征。
制造和选择砂轮时主要考虑结合剂、磨料、砂轮浓度和磨具硬度。
1结合剂CBN磨具的四种结合剂(树脂、陶瓷、金属、电镀)中,以陶瓷结合剂的CBN磨具发展最快。
世界范围内,陶瓷CBN磨具的比例已由20世纪80年代的4%上升到现在50%以上,增速迅猛。
由于陶瓷CBN磨具具有磨削效率高、形状保持性好、耐用度高、易于修整、磨料利用率高(为75%以上,其余类型结合剂为5060%砂轮使用寿命长等优势,因而成为高效、高精度磨削的首选磨具。
目前,用于凸轮轴磨削的CBN砂轮全部采用陶瓷结合剂。
2磨料选择磨削加工中,磨料是磨具中的主体,其性能好坏直接影响磨削效果。
CBN磨料与刚玉磨料相比,具有更高的硬度和强度,因而切削锋利且耐磨。
凸轮轴加工这样高强度的磨削情况下,使用CBN磨料是最佳选择。
不同牌号的CBN磨料,因制造工艺的不同,其晶体形态、颗粒形状也各不相同,各自具有不同的强度、热稳定性、耐化学侵蚀性和破碎特性。
应根据结合剂的种类、磨削工件和磨削方式的不同,选择不同牌号的磨料。
需要指出的CBN磨料在高温下易与水和碱性氧化物发生化学反应而使其结构受到破坏,这是选择磨削液的种类、压力和流量时必须考虑的因素。
3浓度砂轮浓度的高低表示在磨削时砂轮工作面单位面积上参加磨削的磨粒数的多少,高浓度可带来高的磨削比,200%浓度比100%浓度砂轮寿命长45倍。
目前,高速、高效磨削均采用较高的砂轮浓度,如进口磨凸轮轴磨床配套的陶瓷CBN砂轮浓度一般均为200%4硬度磨具的硬度等级表示结合剂对磨料把持力的大小,制造商工艺控制的重要指标,也是用户选择磨具性能的主要参数。
砂轮硬度均匀和稳定及硬度高低的合理选择是保证磨削质量的重要前提。
砂轮线速度对CBN砂轮磨损影响的磨削试验研究
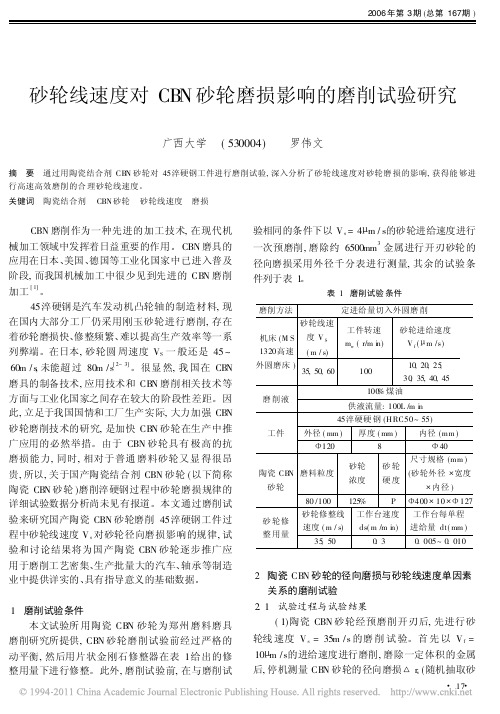
2006 年第 3 期 (总第 167期 )
3 结论 1 ) 为了解决测量精度和效率的矛盾, 提出在满
足测量精度要求的前提下, 测点的数目应尽可能的 少, 并用实例验证了曲面零件的测点自适应生成算 法的可行性。
2) 利用图形的质心和最小惯性主轴作为定位 基准, 可实现被测自由曲面与标准 CAD模型的自动 对齐。
参考文献 [ 1]李剑, 王文, 陈子辰. 自 由曲面零 件的寻 位自适 应检测 方法 研究
! 18!
磨损量分别为 24 m 和 22 m, 分别 是砂轮在 V s = 35m / s条件下 的径 向磨 损量 116 m 的 20. 69% 和 18. 97% 。
( 2)在 V s = 60m / s的条件下, 随着砂轮进给速度 Vf 的增大, 砂轮磨损缓慢且均匀地增大; 而当 Vs = 35m / s时, 随着 V f 的增大, 砂轮磨损呈跳跃式地增大。 所以, 陶瓷结合剂 CBN砂轮必须在高速下工作。
表 1 磨削试验 条件
磨削方法
定进给量切入外圆磨 削
砂轮线速 机床 (M S 度 V S 1320高速 ( m / s) 外圆磨床 )
35, 50, 60
工件转速 mw ( r/m in)
1 00
砂轮进给速度 Vf ( m /s)
10, 20, 25, 30, 35, 40, 45
磨 削液
100% 煤油 供液流量: 100L /m in
cbn砂轮磨削参数

cbn砂轮磨削参数今天咱们来唠唠CBN砂轮磨削参数这个超有趣(虽然听起来有点专业啦)的话题。
一、CBN砂轮是啥呢?CBN砂轮啊,它可是磨削界的一个小明星呢。
CBN就是立方氮化硼啦,这种材料超级硬,硬度仅次于金刚石哦。
所以用它做成的砂轮在磨削的时候就特别厉害。
它可以用来磨削好多硬度比较高的材料,像那些合金钢啊、高速钢之类的。
你想啊,要是普通的砂轮去磨削这些硬家伙,可能没几下就磨损得不成样子了,但是CBN砂轮就不一样啦,它能稳稳地把这些硬材料磨削得又精准又光滑。
二、磨削参数之砂轮转速。
说到CBN砂轮的磨削参数,砂轮转速可是个关键因素。
这个转速就像是砂轮工作时候的小节奏。
如果转速太快呢,虽然磨削的效率可能会提高,但是也会带来一些小麻烦。
比如说,砂轮可能会因为离心力太大而发生破裂,这可就危险啦,就像一个转得太快的小陀螺突然散架了一样。
要是转速太慢呢,磨削的效率就会变得很低,就像小蚂蚁搬家,慢悠悠的。
所以呢,要根据被磨削材料的硬度、砂轮的直径大小等因素来确定一个合适的转速。
一般来说,对于硬度比较高的材料,转速可以适当高一点,但是也要在安全的范围内哦。
三、磨削参数之进给量。
进给量这个东西呢,就像是给砂轮规定的每次向前走多少的小指令。
如果进给量太大,砂轮一次吃进去太多材料,就会让磨削变得很粗糙,就像一个人狼吞虎咽吃饭一样,肯定吃相不太好啦,而且还可能会让砂轮磨损得特别快。
要是进给量太小呢,虽然磨削出来的表面可能会比较光滑,但是效率就太低了,这就有点像吃饭的时候一粒一粒地吃米饭,太浪费时间啦。
所以啊,要找到一个合适的进给量,让砂轮既能高效地磨削,又能保证磨削的质量。
对于那些对精度要求比较高的零件,进给量可能就要稍微小一点,多花点时间来保证质量。
四、磨削参数之磨削深度。
磨削深度也是个很重要的参数呢。
这个就像是砂轮要在材料上挖多深的小坑一样。
如果磨削深度太大,那对砂轮的压力就很大,很容易让砂轮磨损,而且也可能会让被磨削的材料出现裂纹之类的问题。
用于高性能磨削的CBN砂轮

用于高性能磨削的CBN砂轮1前言在高性能磨削或高效深磨中,由于采纳极高的砂轮线速度(100m/s~250m/s左右)进行深磨(切深5mm~20mm),工件进给速度也相当高,因而无论对机床和砂轮都提出了很高的要求。
对于砂轮来说,必需具有很高的抗碎裂强度、很好的形状精度保持性以及尽可能高的耐用度,以削减转动时离心力的影响和缩短更换砂轮所需的时间。
传统的陶瓷和树脂结合剂砂轮已不能充足高性能磨削的需要,必需采纳新型的砂轮以适应高速和大切深。
目前国内外在金属材料的高性能磨削中重要采纳单层电镀CBN砂轮,另外为了解决单层电镀砂轮容屑空间比较小的问题,还开发出了一种金属单层CBN砂轮。
以下简要讨论一下高性能磨削砂轮的基本特征和两种不同结合剂形式砂轮的性能特点。
2高性能磨削砂轮的基特征本高性能磨削的效果与砂轮的合理设计和使用紧密相关,而用于高性能磨削的砂轮与一般砂轮有很大区分。
在正确的使用条件下,高性能磨削时砂轮的磨损特别小,即使在高效深磨的条件下,磨削比也可达到20000甚至更高,而且这种现象随砂轮速度的提高表现得愈加明显,而速度的提高对砂轮强度提出了极高要求。
高强度和半永久性是高性能磨削砂轮两个基本特征。
高性能砂轮设计应遵从三个原则:(1)安全性好;(2)加工精度高;(3)良好的磨削性能。
其中安全性是最重要的。
高性能砂轮的安全性很大程度上倚靠于基体强度,对磨料层强度、基体与磨料层结合强度也有很高要求。
由于磨料层厚度相对很小,砂轮的安全设计重要是基体综合设计,这也是与一般砂轮设计的紧要区分。
依据有关原则(最大切向应力、疲乏强度、砂轮全塑性变形)可以确定砂轮的临界失效转速。
另外还要考虑砂轮直径与主轴转速的合理匹配,对基体截型应考虑多种因素进行优化设计。
高性能磨削中极高的砂轮线速度和很高的工件进给速度相结合,有可能导致磨削系统振动,因而要求砂轮应具有肯定的阻尼减振特性,一般可通过在砂轮和主轴之间加入阻尼垫或采纳阻尼特性好的高分子或复合材料制作砂轮盘。
CBN及CBN砂轮磨削技术参数优化

CBN及CBN砂轮磨削技术参数优化CBN及CBN砂轮磨削技术参数优化CBN(Cubic Boron Nitride)是继人造金刚石问世之后,于1957年,由美国GE公司首先合成出的又一种超硬材料。
我国在1966年试制成功CBN,至今已有四十余年的历史了。
CBN的硬度仅低于金刚石,除了高硬度、高耐磨性、低摩擦系数等性质外,还具有比金刚石优越的耐热性和对铁族金属材料的化学惰性。
利用它这些优异的性能作研磨材料所制成的CBN磨具,特别适合于各类铁族金属材料的磨加工。
它和金刚石用于加工硬而脆的非铁系材料相互补充,使超硬材料的应用范围大大拓宽。
和普通磨料的磨具相比,CBN磨具具有高速、高效、高加工质量、长寿命、低成本的特点,可作为高速数控磨床高效、高精度磨削的首选工具。
在汽车、压缩机、机床、工具、轴承等工业领域有着广泛的应用。
1 CBN的性质1-1 CBN的晶体结构六方氮化硼(hBN)经高温高压合成,晶体结构由层状转变为立方结构,密度由2.25g/cm3增加到3.48g/cm3,各种性质都发生了突变。
1-2 CBN的主要特性在将CBN作研磨材料使用时,我们主要关注CBN的硬度、耐磨性、强度和导热性等性质。
1-2-1 硬度CBN的硬度仅次于金刚石,而远高于其它普通磨料。
高的硬度意味着切削能力更强、更锋利。
1-2-2 耐磨性CBN有高的耐磨性,意味着它比普通磨料更难磨损,保持磨粒形状的能力是CBN作为高性能磨料的主要特性之一。
1-2-3 抗压强度CBN的抗压强度很高,这意味着在高强度、大去除量磨削等恶劣条件下使用时,它能保持颗粒完整而不易破碎,因而使CBN磨具寿命更长。
1-2-4 导热性CBN有良好的导热性,在磨削时可实现冷切削。
从而大大减少被磨工件烧伤的可能性。
另外,CBN还有高的热稳定性和较低的热膨胀系数。
特别是CBN 与铁、碳没有明显的化学亲和力,决定着它在磨削铁族金属时的价值。
而金刚石在一定温度下与铁发生化学反应而使其结构破坏,这就是金刚石不能加工铁族金属材料的原因。
球面磨削中砂轮磨损量的理论和实验研究
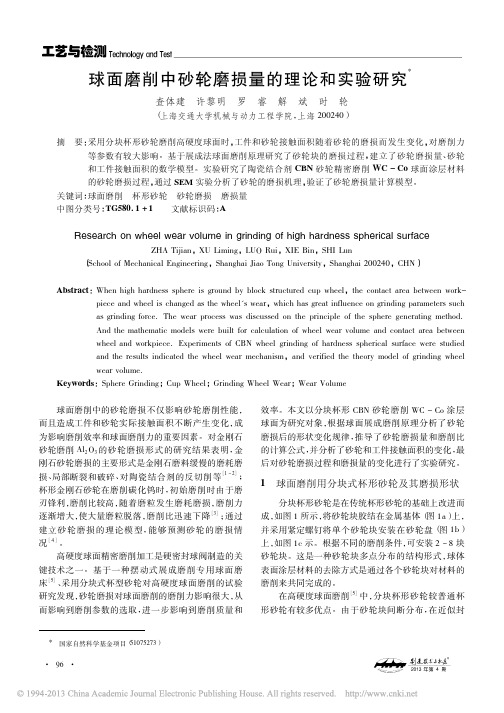
分块杯形砂轮是在传统杯形砂轮的基础上改进而 成, 如图 1 所示, 将砂轮块胶结在金属基体 ( 图 1a ) 上, 并采用紧定螺钉将单个砂轮块安装在砂轮盘 ( 图 1b ) 上, 如图 1c 示。根据不同的磨削条件, 可安装 2 ~ 8 块 砂轮块。这是一种砂轮块多点分布的结构形式, 球体 表面涂层材料的去除方式是通过各个砂轮块对材料的 磨削来共同完成的。
2 2 2 当 0 < re ≤l y / 2 - sy 时, 积分区域 D 为 x + y = re , 则:
( rp 槡
- rw )
2
- x2 - y2
X 方向经 的剖面图, 砂轮和工件的几何关系如图所示, 过 O 点垂直于 YOZ 平面。
V s = πn s ( 3 r p - s z ) r2 s /3 S ww = 2 πn s r p r s re 槡
2
Co 涂层。由于建立理论模型时假设砂轮块与工件的 - s2 y + sz - rp ) rp 槡
2
( 9) ( 10 )
S ww = 2 n s l y r p arcsin( l x / 2
- s2 y)
起始接触点为砂轮块中心, 因此在安装砂轮块时使砂 轮块平面与工件相切于砂轮块中心位置 。
y r p arcsin
- 当 r e > l x / 2 时, 积分区域 D 为 l x / 2 ≤x≤ - l x / 2 ,
· 97 ·
槡
1 -
l y / 2 + s y ≤y ≤l y / 2 + s y , 则: Vs = ns lx ly ( rp 槡
关键词: 球面磨削 杯形砂轮 砂轮磨损 磨损量 中图分类号: TG580. 1 + 1 文献标识码: A
陶瓷结合剂CBN砂轮的特性
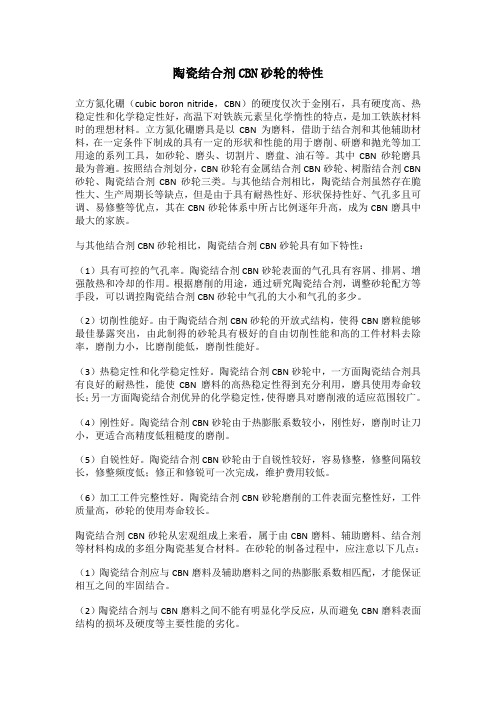
陶瓷结合剂CBN砂轮的特性立方氮化硼(cubic boron nitride,CBN)的硬度仅次于金刚石,具有硬度高、热稳定性和化学稳定性好,高温下对铁族元素呈化学惰性的特点,是加工铁族材料时的理想材料。
立方氮化硼磨具是以CBN为磨料,借助于结合剂和其他辅助材料,在一定条件下制成的具有一定的形状和性能的用于磨削、研磨和抛光等加工用途的系列工具,如砂轮、磨头、切割片、磨盘、油石等。
其中CBN砂轮磨具最为普遍。
按照结合剂划分,CBN砂轮有金属结合剂CBN砂轮、树脂结合剂CBN 砂轮、陶瓷结合剂CBN砂轮三类。
与其他结合剂相比,陶瓷结合剂虽然存在脆性大、生产周期长等缺点,但是由于具有耐热性好、形状保持性好、气孔多且可调、易修整等优点,其在CBN砂轮体系中所占比例逐年升高,成为CBN磨具中最大的家族。
与其他结合剂CBN砂轮相比,陶瓷结合剂CBN砂轮具有如下特性:(1)具有可控的气孔率。
陶瓷结合剂CBN砂轮表面的气孔具有容屑、排屑、增强散热和冷却的作用。
根据磨削的用途,通过研究陶瓷结合剂,调整砂轮配方等手段,可以调控陶瓷结合剂CBN砂轮中气孔的大小和气孔的多少。
(2)切削性能好。
由于陶瓷结合剂CBN砂轮的开放式结构,使得CBN磨粒能够最佳暴露突出,由此制得的砂轮具有极好的自由切削性能和高的工件材料去除率,磨削力小,比磨削能低,磨削性能好。
(3)热稳定性和化学稳定性好。
陶瓷结合剂CBN砂轮中,一方面陶瓷结合剂具有良好的耐热性,能使CBN磨料的高热稳定性得到充分利用,磨具使用寿命较长;另一方面陶瓷结合剂优异的化学稳定性,使得磨具对磨削液的适应范围较广。
(4)刚性好。
陶瓷结合剂CBN砂轮由于热膨胀系数较小,刚性好,磨削时让刀小,更适合高精度低粗糙度的磨削。
(5)自锐性好。
陶瓷结合剂CBN砂轮由于自锐性较好,容易修整,修整间隔较长,修整频度低;修正和修锐可一次完成,维护费用较低。
(6)加工工件完整性好。
陶瓷结合剂CBN砂轮磨削的工件表面完整性好,工件质量高,砂轮的使用寿命较长。
磨削加工凸轮表面粗糙度的数学模型

磨削加工凸轮表面粗糙度的数学模型韩赛宙;韩秋实;彭宝营;李启光;李忠刚【摘要】表面粗糙度是影响凸轮的耐磨性、配合的稳定性、疲劳强度的关键因素,因此提高凸轮表面粗糙度至关重要.对切屑的厚度进行了假设,考虑了特定磨粒形状对凸轮表面粗糙度的影响,研究了凸轮租糙度、砂轮转速、凸轮轮廓曲率、磨削点速度、磨削余量之间的关系,推导出凸轮表面粗糙度的数学模型,模型包括了砂轮线速度、曲率半径、磨削点线速度、磨削余量、砂轮相关系数、凸轮轮廓相关系数,这使得粗糙度模型可应用于不同的磨削条件.在数控非圆磨床上,根据X-C磨削凸轮模型加工某型号凸轮,磨削结果证明所推导的凸轮粗糙度模型是正确的.【期刊名称】《机械工程师》【年(卷),期】2016(000)004【总页数】4页(P77-80)【关键词】凸轮;磨削;粗糙度【作者】韩赛宙;韩秋实;彭宝营;李启光;李忠刚【作者单位】北京信息科技大学机电工程学院,北京100192;北京信息科技大学机电工程学院,北京100192;北京信息科技大学机电工程学院,北京100192;北京信息科技大学机电工程学院,北京100192;北京信息科技大学机电工程学院,北京100192【正文语种】中文【中图分类】TG596近年来,随着车辆、船舶、航天器等领域对机械零部件的加工要求的提高,对凸轮类非圆轮廓零件的加工质量——表面粗糙度也提出了更高的要求。
对于凸轮磨削,目前广泛采用X-C两轴联动加工。
X-C两轴联动加工是通过建立X-C联动位置与速度模型来加工凸轮,机床结构相对简单,因此X-C两轴联动具有效率高、精度高、成本低的特点。
表面粗糙度是指加工表面具有的较小间距和微小峰谷的不平度[1]。
其两波峰或两波谷之间的距离很小,它属于微观几何形状误差。
表面粗糙度越小,则表面越光滑。
Badger和Torrance[2]对磨粒进行了四棱锥体的假设,Shaw 和Lal[3]则认为,认为磨粒形状为球体更为合理,Hecker等[4]人根据磨削过程的随机性质建立了数学模型,该模型主要考虑了砂轮表面磨刃的随机几何形状和随机分布,Stepien[5]建立了一个磨削的概率模型,该模型考虑了磨粒顶尖在砂轮表面的随机排列,并对材料磨除过程进行了详尽的描述。
CBN砂轮常识

CBN砂轮性能优越的砂轮必须同时具备磨削锋利、自锐性好和耐用度高等特征。
制造和选择砂轮时主要考虑结合剂、磨料、砂轮浓度和磨具硬度。
1结合剂CBN磨具的四种结合剂(树脂、陶瓷、金属、电镀)中,以陶瓷结合剂的CBN磨具发展最快。
世界范围内,陶瓷CBN磨具的比例已由20世纪80年代的4%上升到现在50%以上,增速迅猛。
由于陶瓷CBN磨具具有磨削效率高、形状保持性好、耐用度高、易于修整、磨料利用率高(为75%以上,其余类型结合剂为5060%砂轮使用寿命长等优势,因而成为高效、高精度磨削的首选磨具。
目前,用于凸轮轴磨削的CBN砂轮全部采用陶瓷结合剂。
2磨料选择磨削加工中,磨料是磨具中的主体,其性能好坏直接影响磨削效果。
CBN磨料与刚玉磨料相比,具有更高的硬度和强度,因而切削锋利且耐磨。
凸轮轴加工这样高强度的磨削情况下,使用CBN磨料是最佳选择。
不同牌号的CBN磨料,因制造工艺的不同,其晶体形态、颗粒形状也各不相同,各自具有不同的强度、热稳定性、耐化学侵蚀性和破碎特性。
应根据结合剂的种类、磨削工件和磨削方式的不同,选择不同牌号的磨料。
需要指出的CBN磨料在高温下易与水和碱性氧化物发生化学反应而使其结构受到破坏,这是选择磨削液的种类、压力和流量时必须考虑的因素。
3浓度砂轮浓度的高低表示在磨削时砂轮工作面单位面积上参加磨削的磨粒数的多少,高浓度可带来高的磨削比,200%浓度比100%浓度砂轮寿命长45倍。
目前,高速、高效磨削均采用较高的砂轮浓度,如进口磨凸轮轴磨床配套的陶瓷CBN砂轮浓度一般均为200%4硬度磨具的硬度等级表示结合剂对磨料把持力的大小,制造商工艺控制的重要指标,也是用户选择磨具性能的主要参数。
砂轮硬度均匀和稳定及硬度高低的合理选择是保证磨削质量的重要前提。
国外陶瓷CBN砂轮一般有37个硬度等级可供选择,国内目前尚未制订CBN砂轮(包括金刚石磨具)硬度检验标准,制造商仅以配方硬度进行控制。
只要知道晶胞参数,所有物质的密度都可以求得,计算有公式:密度= Z*M/(NA*V)其中,Z为晶胞中以化学式计量的单元数,如在立方氮化硼的晶胞中有4个N和4个B,因此Z=4M为化学式计算的摩尔质量g/mol,NA为阿氏常数,V为晶胞体积cm(3),通常晶胞参数用埃,换成cm,如立方氮化硼的晶胞参数为3.615埃,即3.615*10^(-8)cm据此求得立方氮化硼的密度:4*24.8/(6.023*10^23 * (3.615*10^(-8))^3 = 3.486 g/cm^3。
快速测定CBN砂轮质量

快速测定CBN砂轮质量在采用CBN 金刚石砂轮进行磨削作业时,除了砂轮使用寿命非常重要之外,对砂轮质量因素的认识也是至关重要的,以便达到对磨削流程和加工精度的高要求。
磨削加工工艺在刀具和部件加工中一直扮演着非常重要的角色。
与其他类型的切削技术相比,磨削工艺的长处在于其对硬质材料的良好的可加工性、较高的形位公差精度(IT5~6)和磨削表面的较小的波纹和粗糙度(Rz=1~3μm)。
由于电镀砂轮的基本外形可塑性极强,便于切削,因此这种工艺特别适合于要求较高的加工场合。
砂轮电镀层的特征在于,一方面需要通过高品质磨削颗粒物达到磨损极限范围要求,另一方面又需留出可以排放切屑的空间。
整体观察磨削流程由于加工工艺越来越复杂,因此必须对磨削流程进行整体观察。
这就意味着,要依据各种不同的应用场合,对所使用的砂轮的配置提出具体的要求。
这时往往会涉及表面形状(即刀盘的作用区域)问题。
为了能够对相关表面做具体特征化描述和评价,必须采用现代化的测量技术和方法。
这样即可在任意时间点上对带有颗粒物的刀具工艺流程的结果和质量水平做出客观的评定。
这也是确保稳定的加工质量的一个前提条件。
在电镀粘合时,砂轮颗粒通过电解液和镍或铬的沉淀,着床到导电盘上(图1)。
这种加工工艺具有随机特征,它会影响到所检测的质量特征。
为了对砂轮衬层进行特征化描述,采用了大量的各种不同的检测特征。
通过检测得到的重要特征有粘合硬度、颗粒大小和颗粒密度。
此外,也把刀刃静态数、刀刃动态数和刀刃动态间距等数据用于对刀具表面的评价上。
后两种参数已经包含了工艺的动态性,采用当今先进的测量技术,测量费用会比较高一些。
材料承重比例是重要的检测特征砂轮质量评判的另一重要的检测特征便是材料承重比例和材料比例曲线(Abbott 曲线),如图2 所示。
材料承重比例在一定数值上。
CBN砂轮

CBN砂轮(立方氮化硼砂轮)CBN grinding wheel最理想的高速、高效和高精度的磨削工具一、立方氮化硼(CBN)砂轮的特点:CBN作研磨材料使用时,我们主要研究CBN 的硬度、热稳定性、化学惰性、耐磨性和导热性等。
CBN的硬度远高于其它普通磨料。
高硬度意味着切削能力更强、更锋利;CBN有高的耐磨性,意味着它比普通磨料更难磨损;保持磨粒形状的能力是CBN作为高性能磨料的主要特性之一;CBN的抗压强度很高,这意味着在恶劣的条件下使用时它能保持颗粒完整而不易破碎;CBN有很好的导热性,在磨削时可实现冷切削。
1、高硬度、高韧性立方氮化硼(CBN)是人类合成的硬度仅次于金刚石的超硬材料远远高于普通刚玉与碳化硅磨料,因而具有更佳的切削能力、更锋利2、耐高温、热稳定性好。
立方氮化硼可以承受1250-1350摄氏度的高温,比金刚石的耐热性800摄氏度还要高;在研磨和切削铁质材料时,不会出现粘屑现象,在磨削淬火钢、高钒高速钢、铝高速钢等对磨削温度较为敏感的金属材料是最理想的砂轮。
3、化学惰性强。
立方氮化硼不易和铁族元素产生化学反应,所以对于各种高速钢、工具钢、模具钢、高合金淬硬钢、铬钢、镍合金、粉末冶金钢和高温合金等温度高、硬度高、热传导率低的材料的磨削非常适宜。
4、导热性好。
CBN热导率可达刚玉砂轮的几十倍到百倍,因而能将磨削热迅速导出,减少工件热变形。
对热传导率低的材料磨削非常适宜。
各种喷涂(焊)材料:镍基、铁基等;耐磨铸铁类材料:钒—钛铸铁、高磷铸铁、冷硬铸铁等;钛合金类:如TC45、磨削性能好、加工表面质量好。
由于立方氮化硼磨具能够长期保持磨粒微刃的锋利性,会使被加工工件加工精度和表面粗糙度值都达到较为理想的效果,因此可使工件的耐用度提高10%-30%。
所以即使批量加工的工件,也会始终获得较高的形状、精度及一致性。
CBN砂轮磨削能获得高的尺寸精度和低的表面粗糙度,加工表面不易产生裂纹和烧伤,残余应力小。
CBN及CBN砂轮磨削技术参数优化

CBN及CBN砂轮磨削技术参数优化CBN(Cubic Boron Nitride)是继人造金刚石问世之后,于1957年,由美国GE公司首先合成出的又一种超硬材料。
我国在1966年试制成功CBN,至今已有四十余年的历史了。
CBN的硬度仅低于金刚石,除了高硬度、高耐磨性、低摩擦系数等性质外,还具有比金刚石优越的耐热性和对铁族金属材料的化学惰性。
利用它这些优异的性能作研磨材料所制成的CBN磨具,特别适合于各类铁族金属材料的磨加工。
它和金刚石用于加工硬而脆的非铁系材料相互补充,使超硬材料的应用范围大大拓宽。
和普通磨料的磨具相比,CBN磨具具有高速、高效、高加工质量、长寿命、低成本的特点,可作为高速数控磨床高效、高精度磨削的首选工具。
在汽车、压缩机、机床、工具、轴承等工业领域有着广泛的应用。
1 CBN的性质1-1 CBN的晶体结构六方氮化硼(hBN)经高温高压合成,晶体结构由层状转变为立方结构,密度由2.25g/cm3增加到3.48g/cm3,各种性质都发生了突变。
1-2 CBN的主要特性在将CBN作研磨材料使用时,我们主要关注CBN的硬度、耐磨性、强度和导热性等性质。
1-2-1 硬度CBN的硬度仅次于金刚石,而远高于其它普通磨料。
高的硬度意味着切削能力更强、更锋利。
1-2-2 耐磨性CBN有高的耐磨性,意味着它比普通磨料更难磨损,保持磨粒形状的能力是CBN作为高性能磨料的主要特性之一。
1-2-3 抗压强度CBN的抗压强度很高,这意味着在高强度、大去除量磨削等恶劣条件下使用时,它能保持颗粒完整而不易破碎,因而使CBN磨具寿命更长。
1-2-4 导热性CBN有良好的导热性,在磨削时可实现冷切削。
从而大大减少被磨工件烧伤的可能性。
另外,CBN还有高的热稳定性和较低的热膨胀系数。
特别是CBN与铁、碳没有明显的化学亲和力,决定着它在磨削铁族金属时的价值。
而金刚石在一定温度下与铁发生化学反应而使其结构破坏,这就是金刚石不能加工铁族金属材料的原因。
万向节球道磨用纳米陶瓷结合剂cBN砂轮的生产技术

本技术提供一种万向节球道磨用纳米陶瓷结合剂cBN砂轮及其制备方法。
所述纳米陶瓷结合剂由SiO2、V2O5、Na2O、Al2O3、K2O组成,添加5%~8%纳米ZrO2。
本技术提供的纳米陶瓷结合剂砂轮,所用结合剂与一般陶瓷结合剂的差别在于,用稀有金属氧化物V2O5替代常用的B2O3,同时添加纳米ZrO2,利用稀有金属氧化物能提高结合剂润湿能力的作用,提高砂轮的强度和硬度,使砂轮在保证较高的锋利性同时,具有更好的形状保持性,从而提升磨削速度和修整间隔,大大提升磨削效率和砂轮使用寿命。
权利要求书1.一种万向节球道磨用纳米陶瓷结合剂,其特征在于,所述万向节球道磨用纳米陶瓷结合剂含有基础结合剂以及纳米ZrO2;所述纳米ZrO2的用量为基础结合剂的5%~8%;所述基础结合剂包括SiO2、Al2O3、K2O、Na2O、V2O5;所述纳米ZrO2的粒径为30~50 nm;所述基础结合剂的重量百分数组成为,SiO2 45~60%、V2O5 20~30%、Al2O3 5~10%、Na2O 5~16%、K2O 5~10%;所述万向节球道磨用纳米陶瓷结合剂的制备方法为,将基础结合剂与纳米ZrO2混合均匀,然后加热至1500℃,然后快速水冷,再球磨3~5小时,然后干燥、过筛,选择600目至800目间的粉末,得到所述纳米陶瓷结合剂。
2.一种万向节球道磨用纳米陶瓷结合剂cBN砂轮,其特征在于,所述万向节球道磨用纳米陶瓷结合剂cBN砂轮由基体和磨料层组成;所述磨料层包括权利要求1所述纳米陶瓷结合剂;所述磨料层的重量百分数组成为,cBN磨料40~60%、Al2O3磨料20~30%、纳米陶瓷结合剂15~30%、造孔剂1~5%、临时粘结剂5~10%;万向节球道磨用纳米陶瓷结合剂cBN砂轮的制备方法包括以下步骤:(1)将基础结合剂与纳米ZrO2混合均匀,然后加热至1500℃,然后快速水冷,再球磨3~5小时,然后干燥、过筛,选择600目至800目间的粉末,得到纳米陶瓷结合剂;(2)将磨料、纳米陶瓷结合剂、造孔剂、临时粘接剂混合均匀,然后干燥、过120目标准筛,得到混合料;所述磨料含有cBN;(3)将混合料干压成型,得到生坯;所述生坯经过热处理得到磨料层;(4)将磨料层与基体结合,得到万向节球道磨用纳米陶瓷结合剂cBN砂轮。
CBN砂轮粗糙度研究
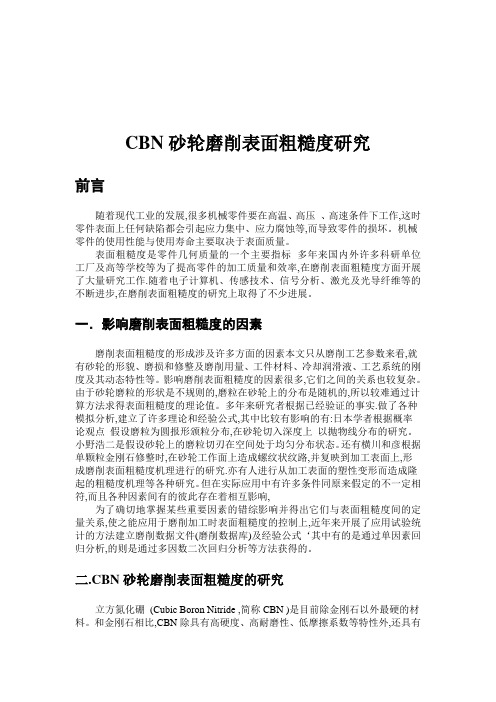
CBN砂轮磨削表面粗糙度研究前言随着现代工业的发展,很多机械零件要在高温、高压、高速条件下工作,这时零件表面上任何缺陷都会引起应力集中、应力腐蚀等,而导致零件的损坏。
机械零件的使用性能与使用寿命主要取决于表面质量。
表面粗糙度是零件几何质量的一个主要指标多年来国内外许多科研单位工厂及高等学校等为了提高零件的加工质量和效率,在磨削表面粗糙度方面开展了大量研究工作.随着电子计算机、传感技术、信号分析、激光及光导纤维等的不断进步,在磨削表面粗糙度的研究上取得了不少进展。
一.影响磨削表面粗糙度的因素磨削表面粗糙度的形成涉及许多方面的因素本文只从磨削工艺参数来看,就有砂轮的形貌、磨损和修整及磨削用量、工件材料、冷却润滑液、工艺系统的刚度及其动态特性等。
影响磨削表面粗糙度的因素很多,它们之间的关系也较复杂。
由于砂轮磨粒的形状是不规则的,磨粒在砂轮上的分布是随机的,所以较难通过计算方法求得表面粗糙度的理论值。
多年来研究者根据已经验证的事实.做了各种模拟分析,建立了许多理论和经验公式,其中比较有影响的有:日本学者根据概率论观点假设磨粒为圆报形颁粒分布,在砂轮切入深度上以抛物线分布的研究。
小野浩二是假设砂轮上的磨粒切刃在空间处于均匀分布状态。
还有横川和彦根据单颗粒金刚石修整时,在砂轮工作面上造成螺纹状纹路,并复映到加工表面上,形成磨削表面粗糙度机理进行的研究.亦有人进行从加工表面的塑性变形而造成隆起的粗糙度机理等各种研究。
但在实际应用中有许多条件同原来假定的不一定相符,而且各种因素间有的彼此存在着相互影响,为了确切地掌握某些重要因素的错综影响并得出它们与表面粗糙度间的定量关系,使之能应用于磨削加工时表面粗糙度的控制上,近年来开展了应用试验统计的方法建立磨削数据文件(磨削数据库)及经验公式‘其中有的是通过单因素回归分析,的则是通过多因数二次回归分析等方法获得的。
二.CBN砂轮磨削表面粗糙度的研究立方氮化硼(Cubic Boron Nitride ,简称CBN )是目前除金刚石以外最硬的材料。
磨削参数分析

砂轮与磨削参数DCT工厂现场工程师(主管工程师)周鹏摘要:磨削加工广泛的被机加工行业运用,我厂在齿轴热后精加工中经常使用磨削加工。
砂轮的选择和磨削参数的选择直接影响零件的加工精度。
关键词:磨料粒度结合剂硬度组织线速度轴向进给径向进给一、概论磨削是齿轴热后精加工的主要方式,零件的尺寸精度、形状公差及表面精度主要通过砂轮的选择和机床的加工参数决定。
下文主对砂轮规格参数与机床加工参数进行了分析。
二、砂轮的选择砂轮的特性由下列五个因素来决定:磨料、粒度、结合剂、硬度和组织。
常用的磨料有氧化物系(Al203)、碳化物系(SiC 、BC)、高硬磨科系(CBN、金刚石)三类。
下图为常用磨料的名称和代号。
其中CBN砂轮在生产中越来越多的被运用,第一、CBN的硬度比金刚石略低,但其耐热性(1400℃)比金刚石(800℃)高出许多,而且对铁元素的化学惰性高,特别适合于磨削既硬又韧的钢材。
第二、CBN的磨粒切削刃锋利,在磨削时可减小加工表面材料的塑性变形,因此,磨出的表面粗糙度比用一般砂轮小。
第三、CBN砂轮加工所得的表面层为残余压应力,而Al203砂轮加工的表面层为残余张应力,残余张应力是形成表面裂纹的主要原因。
如右图所示。
粒度表示磨粒的大小程度,磨粒的直径大于40μm时,称为砂粒,磨粒的直径小于40μm 时,称为微粉。
磨粒粒度对磨削生产率和加工表面粗糙度有很大的影响。
结合剂的作用是将磨粒粘合在一起,使砂轮具有必要的形状和强度,它直接影响砂轮的强度、耐热性和耐用度。
常用的结合剂有四种:陶瓷结合剂(V),它的特点是化学性质稳定,耐水、耐酸、耐热和成本低,但较脆,它所制成的砂轮线速度一般为35m/s。
树脂结合剂(B),它的强度高,弹性好,多用于高速磨削、切断和开槽等工序,但在使用时要注意切削液的含碱量不宜超过1.5%,砂轮也不宜长期存放,存放太久可能会变质而使结合强度降低。
橡胶结合剂(R),多用于制作无心磨床的导轮和切断、开槽及抛光砂轮。
砂轮的磨削效率计算公式

砂轮的磨削效率计算公式一、砂轮的磨削效率计算公式。
砂轮的磨削效率可以用以下公式来计算:磨削效率 = 磨削去除的材料量 / 磨削时间。
其中,磨削去除的材料量可以用磨削前后工件的质量差来表示,磨削时间则是指单位时间内的磨削时间。
磨削去除的材料量和磨削时间都是可以直接测量得到的,因此可以通过这个公式来计算砂轮的磨削效率。
二、影响磨削效率的因素。
1. 砂轮的材料。
砂轮的材料对磨削效率有着很大的影响。
一般来说,硬度较高的砂轮可以更好地抵抗磨损,因此具有更高的磨削效率。
常见的砂轮材料有氧化铝、碳化硅、金刚石等,它们的硬度和耐磨性各不相同,因此对磨削效率也有着不同的影响。
2. 砂轮的结构。
砂轮的结构包括砂轮的粒度、结合剂等因素。
粒度越细的砂轮可以获得更光滑的表面,但磨削效率通常会降低。
而结合剂的选择也会影响砂轮的磨削效率,不同的结合剂对磨削的稳定性和效率都有着影响。
3. 磨削参数。
磨削参数包括磨削速度、进给量、磨削深度等。
这些参数的选择会直接影响砂轮的磨削效率。
一般来说,提高磨削速度和进给量可以提高磨削效率,但同时也会增加砂轮的磨损和发热,因此需要在磨削参数的选择上进行平衡。
三、提高磨削效率的方法。
1. 选择合适的砂轮材料和结构。
根据工件的材料和要求选择合适的砂轮材料和结构是提高磨削效率的关键。
对于硬度较高的工件,可以选择硬度较高的砂轮;对于需要较光滑表面的工件,可以选择粒度较细的砂轮。
2. 合理选择磨削参数。
在进行磨削时,需要根据工件的材料和形状合理选择磨削参数,包括磨削速度、进给量、磨削深度等。
合理选择磨削参数可以提高磨削效率,同时也可以减少砂轮的磨损和发热。
3. 定期修整砂轮。
砂轮在使用过程中会逐渐磨损,如果砂轮表面出现不均匀磨损或者磨削效率下降的情况,需要及时进行修整。
定期修整砂轮可以保持砂轮的磨削效率,并延长砂轮的使用寿命。
4. 选择合适的冷却液。
在进行高速磨削时,砂轮和工件会产生大量的热量,如果不能及时散热会影响磨削效率。
- 1、下载文档前请自行甄别文档内容的完整性,平台不提供额外的编辑、内容补充、找答案等附加服务。
- 2、"仅部分预览"的文档,不可在线预览部分如存在完整性等问题,可反馈申请退款(可完整预览的文档不适用该条件!)。
- 3、如文档侵犯您的权益,请联系客服反馈,我们会尽快为您处理(人工客服工作时间:9:00-18:30)。
普通磨具的配方一般有三种表示方法,一种是以磨料为100% ,其他材料都以占磨料的百分数表示,如表1:
表1A F46陶瓷结合剂配方表(%)
这种表示方法的优点是:调整配方中任何一项数据时不直接影响其他数据的数值。
例如表1中,硬度H的结合剂量由9%变为10%时,糊精、润湿剂和成型密度仍然可以是2%、2.5%2.15g/cm3。
我国70年代以前的配方大多都不标组织号,但确定组织号的磨粒率可以由配方
数据计算出来,如表1中硬度H的配方点磨粒率为:
u=γ/d×ΣW
u—毛坯磨粒率
γ—成型密度
d—磨料颗粒密度
ΣW—配方百分重量总合
u=2.15/3.92×(100+9+2+2.5)%=0.4832≌48%
毛坯组织号按磨粒率48%换算:
N=(62-48)/2=7
即硬度为H的配方点毛坯组织号,N=7
陶瓷结合剂磨具配方的另一种表示方法为:磨料百分数与结合剂百分数之和为100%,配方如表2:
表2A F60陶瓷结合剂磨具配方表
配方表毛坯磨粒率的计算与前例略有不同,如表2中硬度H 配方点的毛坯磨粒率为:
u=γ×91.5% /3.92×(91.5+8.5+3+2.8)%
=0.4765≌48%
由毛坯磨粒率换算成毛坯组织号,N=7
此外还有一种配方表是:将不同材质不同粒度的磨具的结合剂量、成型密度、润湿剂等分别列表,结合起来使用。
磨具的成品磨粒率计算比较复杂,参见《陶瓷结合剂砂轮配方》1991。
超硬磨具(金刚石和CBN 磨具)与普通磨具不同的是磨粒率被称为浓度,其含义为在超硬磨具的体积中超硬磨料的体积占25%时,浓度为100% ;超硬磨料的质量以“克拉”为单位,每0.2克为1克拉。
其浓度与质量的关系,见表3:
表3 超硬磨料的浓度
超硬磨料比较贵重,所以超硬磨具制品的浓度高低对成本和磨削加工都有着明显的影响,一般说浓度高,磨料密度大,耐用度高,磨削效率低;浓度低磨削效率高,耐用度低;但过低的浓度磨料稀疏,磨粒易脱落,效率反而下降,甚至不能正常使用。
陶瓷结合剂超硬磨具的浓度通常在75%~150%之间。
超硬磨具的配方也有多种表示方法,比较便于计算的是以超硬磨料量为100%,其他成分按占磨料的百分数计算。
以表4的CBN磨具配方为例,
表4 陶瓷结合剂CBN磨具配方
表4中成型密度为2.63g/cm3,其计算过程如下:
浓度为125%时,每cm3成型料内有CBN磨料1.087克(见表3),
辅助磨料CF150 1.0875g×70%=0.7613g
结合剂 1.0875g×60%=0.6525g
糊精量 1.0875g×5%=0.05438g
润湿剂量 1.0875g×7%=0.07613g
成型密度γ=(1.0875+0.7613+0.6525+0.05438+0.07613)g/cm3
=2.63g/cm3
若毛坯体积为5cm3,制作10块坯料,混料余量为5%时配料量计算如下:
CBN 量 1.0875g×[5×10×(1+5%)]=57.09g
辅助磨料量57.09g×70%=39.96g
结合剂量57.09g×60%=34.25g
糊精量57.09g×5%=2.85g
水量57.09g×7%=4.00g
成型单重 2.63g/cm3×5cm3=13.15g
整理配料单,见表5:
表5 陶瓷结合剂CBN磨具配料单
另一种配方的表示方法是:用超硬磨料和辅助磨料之和为100%来计算,见表6:
表6 陶瓷结合剂金刚石磨具配方表
按表6的数值计算配方的成型密度γ,
超硬磨具的浓度为125%时,每cm3型料中含金刚石为1.1g (见表3),
辅助磨料C F120 为1.1g
总磨料量=(1.1+1.1)g=2.2g
结合剂量=2.2g×28%=0.616g
糊精量=2.2g×3%=0.066g
水量=2.2g×4.5%=0.099g
成型密度=(1.1+1.1+0.616+0.066+0.099)g/cm3
=2.98g/cm3
其混配料计算过程同陶瓷结合剂CBN磨具(参见表4)
有的超硬磨具的生产工艺是以糊精液做润湿剂混料的,配方给出的是每Kg干料所用的润湿剂的ml数,其成型密度的计算与前略有不同,某CBN磨具的配方见表7,
表7 陶瓷结合剂CBN磨具配方表
按表7数据计算成型密度,
配方中CBN浓度为100%时,每型料中CBN含量为0.87g(见表3),
辅助磨料量=0.87g
总磨料量=(0.78+0.78)g=1.74g
结合剂量=1.74 g×26%=0.4524g
糊精液每Kg干料用35ml,每克干料用糊精液量为:35 ml/1000 g=0.035 ml/g
每cm3干料的质量为:(1.74+0.4524)g=2.1924g
每cm3干料用糊精液量为:0.035 ml/g×2.1924 g=0.0767ml
设:使用的糊精液的浓度为30% 其相对密度为1.10,见表8
表8 糊精液的相对密度
所以每cm3型料中糊精液的质量为:0.07673×1.100=0.0844g
所以表7 中配方的成型密度为:γ=0.87+0.87+0.4524+0.0844=2.2768≌2.28g/cm3 其配混料计算过程同前,从略。