砂轮硬度及砂轮硬度的选择
普通砂轮的材质,粒度,硬度,砂轮标示,代号
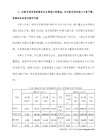
SiO2 % :≤0.45 Fe2O3%:≤0.10
CaO % :≤0.05 Na2O%:≤0.30
--平均晶粒尺寸:0.5MM
--成品率:大于92%;
--化学成份:TiO2(0.27%),SiO2(0.1%),Fe2O3(0.16%),Al2O3≥94%。
(2)高品级棕刚玉煅烧磨料
该产品具有化学成份高粒度形状好、清洁度高、堆积密度高等特点。广泛应用于飞机、汽车、轮船、机械制造等行业。主要技术性能指标处于国内领先地位。
二、砂轮粒度: ←粗……20#、24#、30#、……180#、220#、240#、…… 细 →
三、砂轮硬度: ←软 E、F、G、H、I、J、K、L、M、N、O、P、Q、R、S、T 硬→
四、砂轮标示: 例砂轮标示为:WA46L5V351A350×40×127其中各字母代号、数据各代表意义如下:WA→砂轮采用的磨料材质 35→砂轮使用线速度为35M/S 46→砂轮的粒度 1A→砂轮的形状 L→砂轮硬度 350→砂轮直径尺寸 5→砂轮组织号 40→砂轮厚度尺寸 V→砂轮为陶瓷制法砂轮子 127→砂轮内孔尺寸
1)单晶刚玉磨料
单晶刚玉磨料是Al203以物理刚玉的单晶形态自熔体中析出,经化学处理而得到的绝大多数磨粒为单晶体的磨料。它具有较高的韧性和硬度,切削能力强。用来加工工具钢、不锈钢、高钒钢等韧性大、硬度高的耐磨材料,比其它材料优秀。
主要技术性能指标:
--冶炼设备技术参数:1100KVA电弧炉,电极园:D=900MM;
--纯度:元素含量与原材料基本一致99.99%(氧除外);
--电弧额定功率:单级10kw,双级20kw,三级30kw;
--运行方式:连续运行≥8小时;
砂轮使用的选择范文

砂轮使用的选择范文砂轮是一种常见的研磨工具,广泛用于金属加工、木工、石材加工等领域。
正确选择合适的砂轮,对于保证加工质量、提高工作效率、延长工具寿命等方面起着至关重要的作用。
以下是砂轮使用的选择的相关知识。
1.砂轮材料选择砂轮的材料种类繁多,常见的有氧化铝砂轮、石英砂砂轮、黄金刚石砂轮等。
不同材料的砂轮适用于不同的工作对象和工作要求。
-氧化铝砂轮:适用于加工常用金属材料,如铁、钢、铸铁等,具有良好的耐磨性和切削性能。
-石英砂砂轮:适用于加工石材、陶瓷等非金属材料,具有较高的硬度和耐用性。
-黄金刚石砂轮:适用于加工硬质合金、玻璃、磁性材料等特殊材料,具有超强的切削性能和耐磨性。
2.砂轮粒度选择砂轮的粒度表示砂轮表面上磨粒的大小,常用的粒度标记为#,粒度越细,砂轮磨削效果越好,表面质量越高。
但同时也会降低砂轮的磨削效率。
一般来说,选择较细的粒度可用于对表面要求较高的精细加工,而选择较粗的粒度可用于对表面要求相对较低的粗加工。
在实际应用中,根据具体工件的要求和砂轮的特性进行选择,最佳粒度范围可根据实验确定。
3.砂轮形状选择砂轮的形状有平面砂轮、弧面砂轮、圆筒形砂轮、锥形砂轮等多种类型。
不同形状的砂轮适用于不同的加工任务。
-平面砂轮:适用于平面磨削、平面加工等任务。
-弧面砂轮:适用于对弧面、圆面等曲面进行加工。
-圆筒形砂轮:适用于内圆磨削、棒材修磨等任务。
-锥形砂轮:适用于锥面加工等特殊加工任务。
4.砂轮硬度选择砂轮的硬度是指砂轮结合剂的硬度,硬度越高,砂轮的抗磨削能力越强。
对于不同材料的加工需求,需要选择不同硬度的砂轮。
-软砂轮:适用于加工较硬材料,如高速钢、合金钢等。
-硬砂轮:适用于加工较软材料,如铸铁、黄铜等。
5.砂轮尺寸选择砂轮的尺寸一般由直径、宽度和孔径三个参数来确定。
选择合适的砂轮尺寸可以提高工作效率,并符合加工要求。
-直径:砂轮的直径应根据加工机床的规格来选择。
-宽度:较窄的砂轮适用于精细加工,而较宽的砂轮适用于快速去除大量材料。
砂轮的特性要素及选择标准

砂轮的特性要素及选择标准砂轮由磨料和结合剂经压坯、干燥、烧结而成的多孔体。
磨料、结合剂和气孔构成了砂轮的组成三要素。
砂轮的性能取决于磨料、粒度、结合剂、硬度和组织5个参数。
1.磨料承担切削任务,具有很高的硬度、耐磨性、耐热性和韧性,并有较锋利的棱角。
常用的磨料有氧化物系、碳化物系、高硬磨科系三类。
氧化物系磨料的主要成分是A1203,由于它的纯度不同和加入金属元素不同,而分为不同的品种。
碳化物系磨料主要以碳化硅、碳化硼等为基体,也是因材料的纯度不同而分为不同品种。
超硬磨料系中主要有人造金刚石和立方氮化硼。
立方氮化硼是一种很有前途的磨料。
耐热性(1400℃)比金刚石(800℃)高出许多,而且对铁元素的化学惰性高,所以特别适合于磨削既硬又韧的钢材。
2.粒度粒度表示磨粒的大小程度。
以磨粒刚能通过的筛网的网号来表示磨粒的粒度。
以每英寸长度上筛孔的数目表示粒度号,粒度号越大,颗粒越小;尺寸小于40μm的微粉,用其实际尺寸前加W 表示粒度号。
我国新标准中采用米制单位,磨粒的大小统一以磨粒最大尺寸方向上的尺寸来表示。
选择原则:(1)精磨用颗粒较细的磨粒;(2)粗磨用颗粒较粗的磨粒;(3)高速磨削用颗粒较粗的磨粒;(4)当工件材料软、塑性大和磨削面积大时,为避免堵塞砂轮,也可采用较粗的磨粒,精磨或磨硬脆性材料选用细磨粒。
3.结合剂结合剂的作用是将磨粒粘合在一起,使砂轮具有必要的形状和强度。
常用的砂轮结合剂有:1)陶瓷结合剂(代号V)是由粘土、长石、滑石、硼玻璃和硅石等陶瓷材料配制而成。
特点是化学性质稳定,耐水、耐酸、耐热和成本低,但较脆。
除切断砂轮外,大多数砂轮都是采用陶瓷结合剂。
它所制成的砂轮线速度一般为35m/s。
2)树脂结合剂(代号B)其成分主要为酚醛树脂,但也有采用环氧树脂的。
树脂结合剂的强度高,弹性好,故多用于高速磨削、切断和开槽等工序。
但是树脂结合剂的耐热性差,当磨削温度达200—300℃时,它的结合能力便大大降低。
砂轮磨刀技巧

砂轮磨刀技巧一、砂轮的选择砂轮的硬度、粗细度、形状等特点,直接影响到了磨出的刃口的质量以及磨削的速度。
所以,在选择砂轮时,应该根据不同的需求选择相应的砂轮。
1、硬度硬度是指砂轮的硬度,通常用字母A、B、C、D、E、F、G、H依次表示,硬度越高,砂轮的抗磨性能越好,但磨削的速度却越慢。
因此,选择砂轮的硬度时,应根据磨削的材料以及磨切的需求来决定。
2、粗细度粗细度是指砂轮表面的磨粒大小,通常用数字表示,越小的数字表示磨粒越细。
在选择砂轮的粗细度时,应根据刀具的状态来选择,一般刀具刚磨或是切口较大时应该选择粗磨的砂轮,而磨完之后时需要使用细的砂轮进行抛光。
3、形状砂轮的形状种类繁多,如平面砂轮、圆弧砂轮、杯形砂轮、筒形砂轮等等。
而不同形状的砂轮适用于不同形状的刀具,因此,选择砂轮时还应根据具体的加工需求来选择不同形状的砂轮。
二、磨刀的方法在进行刀具的磨削时,正确的磨削方法也至关重要。
下面具体介绍如何使用砂轮磨刀。
1、准备工作首先,应将刀具彻底清洗干净,以防止磨削时因有杂质影响磨出的刃口质量。
然后,将砂轮安装到磨刀机上并调整到所需的粗细度。
2、调整砂轮在磨刀之前,必须将砂轮调整到合适的位置,以确保磨出的刃口的大小和角度都较为均匀,磨削效果良好。
通常,砂轮调整的范围为0.01mm左右,因此应该非常耐心仔细地调试。
3、磨刀开始磨刀之前,应根据刀具的形状选择合适的砂轮。
磨刀时,应该将砂轮靠近刀具,但不要使其直接接触,再启动磨刀机开始磨削。
磨削时应控制好砂轮的方向和速度,停止磨削后应用胶带或油来清洁刀具和砂轮,以便更好地检查成果。
总之,在砂轮磨刀的过程中,正确选择砂轮、合理调整砂轮,并按照正确的磨刀方法进行操作,都是非常重要的。
只有做到这些,才能磨出质量优良、锋利耐用的刀具,提高工作效率,保证产品的质量。
磨削加工砂轮的选择及使用

尺寸( 外径X 厚度X 内径)
规格 1
规格 2
备注
公制( 毫米)
英制( 英寸)
P
250X25X75
WA46-60K8VBE
PA46-60K8VBE
WA用于磨削普通碳钢工件
PA用于磨削合金钢和淬火钢工件粒度选择:
46 粒可达到Ra1.2-1.6
60 粒可达到Ra0.4-0.8
300X40X127
WA46-100K8VBE
微晶类(以矿石为基础的二次人工合成,强硬度介于传统与超硬之间)
SG
陶瓷烧结刚玉
NQ
新型陶瓷烧结刚玉
TG
特殊陶瓷刚玉
形状
国际标准
中国国标
平形
T1A
P
单面凹
T5A
PDA
双面凹
T7A
PSA
杯形
T6
B
碗形
T11
BW
碟形
T12
D
单面斜
T1C
PDX
双面斜
T4
PSX
3、砂轮的尺寸范围
外径尺寸20-1200mm
厚度3.2-305mm孔径根据不同机床要求配置
12X1-1/4X5
WA46-60K8VBE
PA46-60J8VBE
305X38X127
12X1-1/2X5
WA46-60K8VBE
PA46-60J8VBE
355X38X127
14X1-1/2X5
WA46-60K8VBE
PA46-60H8VBE
WA磨削普通碳钢工件
PA磨削合金钢和淬火钢工件粒度选择:
36-220
PA(25A)
铬刚玉,磨削性能同白刚玉,由于磨料具有一定的韧性且保持性好,对工件表面粗糙度的改善具有一定的作用,是WA的升级版。
砂轮的特性及选用
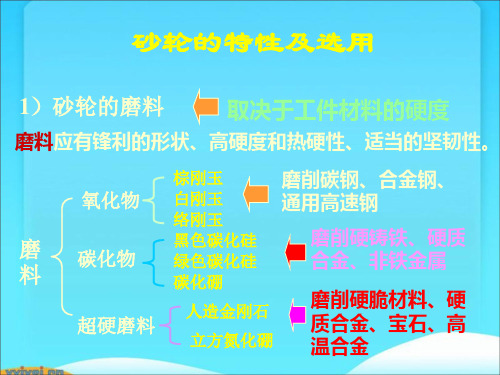
选择原则:
加工表面粗糙度值越大 →选用越粗的磨料 加工表面粗糙度值越小 →选用越细的磨料 砂轮速度高或与工件接触面大时用粗磨料 磨软材料用粗磨料,磨硬材料用细磨料
4)砂轮的结合剂
陶瓷结合剂
结 合 树脂结合剂 剂
橡胶结合剂
取决于磨削速度
价格便宜,耐酸、耐 碱,用的最多,使用 90%以上
VC>35m/s
砂轮的特性及选用
1)砂轮的磨料
取决于工件材料的硬度
磨料应有锋利的形状、高硬度和热硬性、适当的坚韧性。
棕刚玉
磨削碳钢、合金钢、
氧化物 白刚玉
通用高速钢
络刚玉
磨 料
Байду номын сангаас
碳化物
黑色碳化硅 绿色碳化硅 碳化硼
磨削硬铸铁、硬质 合金、非铁金属
人造金刚石
超硬磨料
磨削硬脆材料、硬 质合金、宝石、高
立方氮化硼 温合金
2)砂轮硬度
高速磨削或磨槽
5)砂轮的组织 取决于容屑空间
砂轮组织号用来表示砂轮结构紧密程度,是磨 粒在磨料中占有体积的百分数。
选择原则: 一般选用中等组织号的砂轮。
5)砂轮的组织 取决于容屑空间
组织反映砂轮中磨料、结合剂和气孔三者体积的比 例关系,即砂轮结构的疏密程度,分紧密、中等、疏 松三类13级。
紧密组织 成形性好,加工质量高,适于成形磨、 精密磨削和强力磨削。
砂轮硬度选择原则:
• 磨削硬材,选软砂轮;磨削软材,选硬砂轮; • 磨导热性差的材料,不易散热,选软砂轮以免工 • 件烧伤;磨有色金属,选较软的砂轮; • 砂轮与工件接触面积大时,选较软的砂轮; • 成形磨精磨时,选硬砂轮;粗磨时选较软的砂轮。
3)磨料粒度
超精密加工砂轮的选取原则

超精密加工砂轮的选取原则
超精密加工砂轮的选取原则如下:
1. 砂轮的磨料:超精密加工要求砂轮具有高的磨削效率和精度,因此应选择高硬度、高韧性、高耐磨性的磨料,如金刚石、CBN 等。
2. 砂轮的粒度:粒度越细,磨削表面的粗糙度越小,但磨削效率也会降低。
因此,应根据加工要求选择合适的粒度。
3. 砂轮的硬度:硬度越高,砂轮的耐磨性越好,但也会使磨削表面的粗糙度增加。
因此,应根据加工材料和加工要求选择合适的硬度。
4. 砂轮的组织:砂轮的组织结构对磨削性能有很大影响,应选择组织均匀、气孔率低的砂轮。
5. 砂轮的形状和尺寸:砂轮的形状和尺寸应根据加工零件的形状和尺寸来选择,以保证磨削效率和加工精度。
6. 砂轮的结合剂:结合剂的性能直接影响砂轮的硬度、强度和耐磨性,应选择性能稳定、结合强度高的结合剂。
7. 砂轮的修整:砂轮在使用过程中会磨损,需要定期修整。
应选择合适的修整工具和方法,以保证砂轮的磨削性能。
总之,超精密加工砂轮的选取应根据加工要求、材料特性和机床性能等因素综合考虑,选择合适的砂轮,以保证加工效率和加工精度。
砂轮的特性和选择

突出优点是粘 结力大,物理化学性能稳定,受温度和适度的影 响小,抗腐蚀性好,适于各种磨削液;其次是强 度较高,耐磨损,砂轮外形容易保持并易于修整。 其缺点是脆性大,弹性差,摩擦发热量大,不耐 冲击和振动,不适于制作薄片砂轮。 有机类结合剂的代表是树脂和橡胶。其中,树 脂的应用范围仅次于陶瓷,橡胶的应用范围较小。 有机结合剂的突出特点是强度高,韧性好,耐冲 击,自锐性好,制作的磨具不易破碎。其缺点是 粘结性差,磨具磨损快,外形不易保持;物理化 学性能不太稳定,高温下结合剂变软、老化、轻 度降低,甚至烧毁;抗腐蚀性差,树脂类不耐酸 和碱,橡胶类耐酸和耐油性均较差。
例1手动内径:P12X16X4A80MV60 手动内径:P12X16X4A80MV60 • 平行砂轮,外径12,厚度16,孔径4, 平行砂轮,外径12,厚度16,孔径4 棕刚玉磨料,粒度号80,硬度M 棕刚玉磨料,粒度号80,硬度M,陶瓷 结合剂,最高工作速度60m/s。 结合剂,最高工作速度60m/s。 例2沟道:P35X3X10A80LR35 沟道:P35X3X10A80LR35 平行砂轮,外径35,厚度3,孔径10, 平行砂轮,外径35,厚度3,孔径10, 棕刚玉磨料,粒度号80,硬度L 棕刚玉磨料,粒度号80,硬度L,橡胶 结合剂,最高工作速度35m/s。 结合剂,最高工作速度35m/s。
常用砂轮形状、代号和用途
• 砂轮的特性均标记在砂轮的侧面上,其顺 序是:形状代号、尺寸、磨料、粒度号、 硬度、组织号、结合剂、线速度。例如: 平行砂轮、外径 300mm,厚度50mm,孔 径75mm,棕刚玉磨料,粒度60,硬度L, 5号组织,陶瓷结合剂,最高工作线速度 35m/s的,其标记为:砂轮1-300 × 50 × 75-A60L5V-35m/s。
砂轮的硬度等级及代号
磨削砂轮的选择

砂轮的种类很多,并有各种形状和尺寸,由于砂轮的磨料、结合剂材料以及砂轮的制造工艺不同,各种砂轮就具有不同的工作性能。
每一种砂轮根据其本身的特性,都有一定的适用范围。
因此,磨削加工时,必须根据具体情况(如所磨工件的材料性质、热处理方法、工件形状、尺寸及加工形式和技术要求等),选用合适的砂轮。
否则会因砂轮选择不当而直接影响加工精度、表面粗糙度及生产效率。
下面列出砂轮选择的基本原则以供参考。
一、普通砂轮的选择1. 磨料的选择磨料选择主要取决于工件材料及热处理方法。
a. 磨抗张强度高的材料时,选用韧性大的磨料。
b. 磨硬度低,延伸率大的材料时,选用较脆的磨料。
c. 磨硬度高的材料时,选用硬度更高的磨料。
d. 选用不易被加工材料发生化学反应的磨料。
最常用的磨料是棕刚玉(A)和白刚玉(WA),其次是黑碳化硅(C)和绿碳化硅(GC),其余常用的还有铬刚玉(PA)、单晶刚玉(SA)、微晶刚玉(MA)、锆刚玉(ZA)。
棕刚玉砂轮:棕刚玉的硬度高,韧性大,适宜磨削抗拉强度较高的金属,如碳钢、合金钢、可锻铸铁、硬青铜等,这种磨料的磨削性能好,适应性广,常用于切除较大余量的粗磨,价格便宜,可以广泛使用。
白刚玉砂轮:白刚玉的硬度略高于棕刚玉,韧性则比棕刚玉低,在磨削时,磨粒容易碎裂,因此,磨削热量小,适宜制造精磨淬火钢、高碳钢、高速钢以及磨削薄壁零件用的砂轮,成本比棕刚玉高。
黑碳化硅砂轮:黑碳化硅性脆而锋利,硬度比白刚玉高,适于磨削机械强度较低的材料,如铸铁、黄铜、铝和耐火材料等。
绿碳化硅砂轮:绿碳化硅硬度脆性较黑碳化硅高,磨粒锋利,导热性好,适合于磨削硬质合金、光学玻璃、陶瓷等硬脆材料。
铬刚玉砂轮:适于磨削刀具,量具、仪表,螺纹等表面加工质量要求高的工件。
单晶刚玉砂轮:适于磨削不锈钢、高钒高速钢等韧性大、硬度高的材料及易变形烧伤的工件。
微晶刚玉砂轮:适于磨削不锈钢、轴承钢和特种球墨铸铁等,用于成型磨,切入磨,镜面磨削。
如何选择合适砂轮硬度

磨软而韧的有色金属材料时,砂轮容易堵塞,为保持磨具自锐性,选得软一些的砂轮
磨削导热性差的工件材料时,选软一些的砂轮。
这类材料导热系数低,但硬度高,磨削区不容易散热,这时宜选用较软的砂轮
切入磨削外圆比纵向进给磨削外圆选用更软一些的砂轮
避免磨削时烧伤工件
磨削成和断续表面时,磨具选硬一些
砂轮硬度和磨粒硬度不是同一个概念。
砂轮硬度是指砂轮的磨粒在外力(一搬指磨削力)的作用下,从砂轮表面脱落下来的难易程度。
可以参照下表来选择砂轮的硬度。
选 择 原 则
选 择 理 由
磨硬材料的时候,选较软的磨具,磨软材料的时候,选较硬的磨具
硬材料难磨,磨粒比较容易磨钝,选软一些的砂轮;反之,选硬一些的砂轮
刃磨时工件不容易散热,易产生烧伤、裂纹,砂轮硬度一般选在H-L间。
高速磨削时,砂轮硬度应比普通磨削时选择的砂轮硬度低一、二级
砂轮在高速磨削状态下的“动力硬度”比普通磨削时高,故选软一、二级的砂轮。
干磨时要比用冷却液磨பைடு நூலகம்的砂轮硬度低些
干磨时工件发热更快,选择的砂轮硬度要比用冷却液磨削时软1-2级。
原文:江西冠亿砂轮
用硬一点的砂轮可以保证工作的正确几何形状。
平面磨削时、端面磨比圆周磨削时,砂轮选软些。工件与磨具的接触面较大及进给量较大时,砂轮应选软些
磨具与工件接触面积大时,砂轮磨粒容易钝,温度增高,工件易烧伤。
内圆磨较外圆、平面磨选砂轮时要选硬些的砂轮
磨削内圆时,砂轮工作的最高线速度低,硬度要选硬一些的砂轮。
选较软砂轮用来刃磨刀具等工件
砂轮硬度标准对照表

砂轮硬度标准对照表一、硬度单位转换砂轮硬度通常用“度”来表示,常用的硬度单位有布氏硬度(HB)、洛氏硬度(HR)和维氏硬度(HV)等。
不同硬度单位之间可以相互转换,转换公式如下:1. 布氏硬度(HB)与洛氏硬度(HR)之间的转换公式:HR = 100 - (1.234 ×log(HB) + 0.8)2. 布氏硬度(HB)与维氏硬度(HV)之间的转换公式:HV = 1000 ×log(HB) - 9003. 洛氏硬度(HR)与维氏硬度(HV)之间的转换公式:HV = 1300 ×log(HR - 0.16)二、砂轮种类与硬度不同种类的砂轮具有不同的硬度,常见的砂轮种类包括橡胶砂轮、陶瓷砂轮、玻璃纤维砂轮等。
一般来说,硬质砂轮的硬度较高,而软质砂轮的硬度较低。
三、砂轮硬度等级标准常见的砂轮硬度等级标准包括国际标准(ISO)和美国标准(ANSI)等。
不同标准的砂轮硬度等级命名方式略有不同,但都有一定的规律可循。
一般来说,数值越小,表示砂轮硬度越高。
四、不同硬度对应的应用场景不同硬度的砂轮适用于不同的应用场景。
一般来说,硬质砂轮适用于加工硬质合金、不锈钢等难加工材料,而软质砂轮则适用于加工较易切削的材料,如铝、铜等有色金属。
五、砂轮硬度与磨削性能关系砂轮硬度与磨削性能具有密切关系。
一般来说,砂轮硬度越高,磨削性能越好,能够获得更好的表面粗糙度和加工效率。
但是,过高的砂轮硬度可能导致工件表面烧伤或砂轮磨损加剧。
因此,选择合适的砂轮硬度对于提高磨削性能和保证工件质量至关重要。
六、砂轮硬度与使用寿命关系砂轮硬度与使用寿命之间也存在一定的关系。
一般来说,砂轮硬度越高,其使用寿命越短。
这是因为硬质砂轮在磨削过程中需要消耗更多的能量,导致其磨损速度较快。
因此,为了延长砂轮的使用寿命,通常会选择较低的砂轮硬度。
七、砂轮硬度与安全性关系砂轮硬度与安全性也有一定的关系。
在某些情况下,过高的砂轮硬度可能导致砂轮的自锐性不足,进而产生过多的热量和火花,增加火灾和人员伤害的风险。
砂轮的特性与选择

6.3.3 砂轮的特性与选择砂轮是磨削加工中最主要的一类磨具。
砂轮是在磨料中加入结合剂,经压坯、干燥和焙烧而制成的多孔体。
由于磨料、结合剂及制造工艺不同,砂轮的特性差别很大,因此对磨削的加工质量、生产率和经济性有着重要影响。
砂轮的特性主要是由磨料、力度、结合剂、硬度、组织、形状和尺寸等因素决定。
(1)磨料磨料是砂轮的主要组成部分,它具有很高的硬度、耐磨性、耐热性和一定的韧性,以承受磨削时的切削热和切削力,同时还应具备锋利的尖角,以利磨削金属。
常用磨料代号、特点及应用范围简表 6.6表 6.6 常用磨料代号、特性及适用范围(2)粒度粒度是指磨料颗粒尺寸的大小。
粒度分为磨粒和微粉两类。
对于颗粒尺寸大于 40 μm的磨料,称为磨粒。
用筛选法分级,粒度号以磨粒通过的筛网上每英寸长度内的孔眼数来表示。
如60 # 的磨粒表示其大小刚好能通过每英寸长度上有60孔眼的筛网。
对于颗粒尺寸小于40 μm的磨料,称为微粉。
用显微测量法分级,用W和后面的数字表示粒度号,其W后的数值代表微粉的实际尺寸。
如W20表示微粉的实际尺寸为20 μm。
砂轮的力度对磨削表面的粗糙度和磨削效率影响很大。
磨粒粗,磨削深度大,生产率高,但表面粗糙度值大。
反之,则磨削深度均匀,表面粗糙度值小。
所以粗磨时,一般选粗粒度,精磨时选细粒度。
磨软金属时,多选用粗磨粒,磨削脆而硬材料时,则选用较细的磨粒。
粒度的选用见表 6.7。
表 6.7 磨料粒度的选用(3)结合剂结合剂是把磨粒粘结在一起组成磨具的材料。
砂轮的强度、抗冲击性、耐热性极耐腐蚀性,主要取决于结合剂的种类和性质。
常用结合剂的种类、性能及适用范围见表 6.8。
表 6.8常用结合剂的种类、性能及适用范围(4)硬度砂轮硬度是指砂轮工作时,磨粒在外力作用下脱落的难易程度。
砂轮硬,表示磨粒难以脱落;砂轮软,表示砂轮容易脱落。
砂轮的硬度等级见表 6.9。
砂轮的硬度与磨料的硬度是完全不同的两个概念。
硬度相同的磨料可以制成硬度不同的砂轮,砂轮的硬度主要决定于结合剂性质、数量和砂轮的制造工艺。
砂轮的基本知识
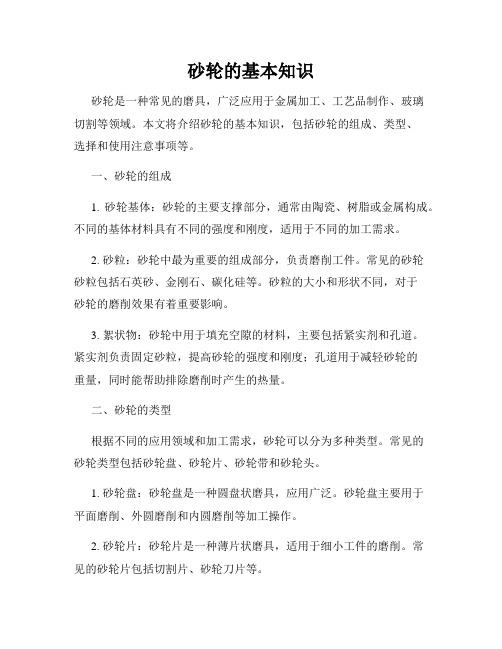
砂轮的基本知识砂轮是一种常见的磨具,广泛应用于金属加工、工艺品制作、玻璃切割等领域。
本文将介绍砂轮的基本知识,包括砂轮的组成、类型、选择和使用注意事项等。
一、砂轮的组成1. 砂轮基体:砂轮的主要支撑部分,通常由陶瓷、树脂或金属构成。
不同的基体材料具有不同的强度和刚度,适用于不同的加工需求。
2. 砂粒:砂轮中最为重要的组成部分,负责磨削工件。
常见的砂轮砂粒包括石英砂、金刚石、碳化硅等。
砂粒的大小和形状不同,对于砂轮的磨削效果有着重要影响。
3. 絮状物:砂轮中用于填充空隙的材料,主要包括紧实剂和孔道。
紧实剂负责固定砂粒,提高砂轮的强度和刚度;孔道用于减轻砂轮的重量,同时能帮助排除磨削时产生的热量。
二、砂轮的类型根据不同的应用领域和加工需求,砂轮可以分为多种类型。
常见的砂轮类型包括砂轮盘、砂轮片、砂轮带和砂轮头。
1. 砂轮盘:砂轮盘是一种圆盘状磨具,应用广泛。
砂轮盘主要用于平面磨削、外圆磨削和内圆磨削等加工操作。
2. 砂轮片:砂轮片是一种薄片状磨具,适用于细小工件的磨削。
常见的砂轮片包括切割片、砂轮刀片等。
3. 砂轮带:砂轮带是一种带状磨具,适用于长条状工件的磨削。
砂轮带的使用方便,能够满足不同形状工件的加工需求。
4. 砂轮头:砂轮头是一种球形或圆柱形的磨具,通常用于模具磨削和刀具修复等精密加工。
三、砂轮的选择正确选择适合的砂轮对于加工质量和效率至关重要。
以下几点是选购砂轮时需要考虑的要素:1. 加工材料:不同的工件材料需要不同的砂轮材料。
例如,对于金属材料的磨削,常用的砂轮为氧化铝砂轮;对于玻璃材料的切割,常用的砂轮为金刚石砂轮。
2. 砂粒尺寸:砂轮砂粒的尺寸直接决定了砂轮的磨削效果。
一般来说,粗砂粒适用于快速去除材料,细砂粒适用于精密磨削。
3. 砂轮硬度:砂轮硬度决定了砂轮的磨削效率和寿命。
选择适合的砂轮硬度有助于提高砂轮的使用寿命。
4. 砂轮形状:根据加工要求选择合适的砂轮形状,确保砂轮能够完整接触工件,避免加工不均或损坏工件。
磨削加工砂轮的选择及使用

磨削加工砂轮的选择及使用磨削加工砂轮是一种常见的磨削工具,用于金属加工、石材加工、木材加工等行业中。
它是通过磨削作用将材料表面的不平整部分削平,并达到所需的精度和光洁度。
选择适合的砂轮和正确的使用方法对于磨削加工的质量和效率至关重要。
在选择和使用砂轮时,需要考虑以下几个因素:1.砂轮材质:常见的砂轮材质包括氧化铝、氮化硅、碳化硅等。
不同材质的砂轮适用于不同的加工材料和工件硬度。
例如,氧化铝砂轮适用于加工钢铁材料,氮化硅砂轮适用于加工陶瓷材料。
2.砂轮粒度:砂轮的粒度越细,磨削表面越光滑,但磨削速度较慢。
粒度粗的砂轮磨削速度快,但表面光洁度较差。
根据加工要求选择合适的砂轮粒度,通常粗砂轮用于粗磨,细砂轮用于精磨。
3.砂轮硬度:砂轮硬度的选择取决于加工材料的硬度。
通常情况下,加工硬材料需要选择硬度较高的砂轮,而加工软材料需要选择硬度较低的砂轮。
硬砂轮磨削效率高,但易造成加工表面热损伤,软砂轮磨削表面质量好,但磨损较快。
4.砂轮尺寸:砂轮的直径和厚度需要根据加工机床的规格和加工要求来选择。
较大尺寸的砂轮用于大型工件的加工,而较小尺寸的砂轮用于小型工件的加工。
使用砂轮时,需要注意以下几点:1.安装正确:砂轮应正确安装在磨床上或电动工具上,确保砂轮转动平稳。
安装时要检查砂轮是否有裂纹或损坏,避免因砂轮损坏而引发事故。
2.控制加工参数:根据加工材料和加工要求,合理选择加工参数,如砂轮转速、进给速度、磨削深度等。
过高的转速和进给速度会导致砂轮过热和表面质量差,过深的磨削深度可能导致砂轮过载。
3.使用保护措施:在砂轮加工过程中,应戴上防护眼镜、戴耳罩和手套等安全防护装备,防止碎片、切屑和噪音对操作人员造成伤害。
4.定期保养:砂轮在使用过程中会磨损,需要定期检查和更换。
砂轮磨损严重会影响加工效果,并增加机床负荷。
同时,砂轮使用后应及时清洁干净并妥善存放,避免锈蚀和损坏。
总之,选择合适的砂轮和正确使用砂轮是磨削加工的重要环节。
高级磨工考试题及答案

高级磨工考试题及答案1. 磨床的工作原理是什么?- 磨床的工作原理是通过砂轮的高速旋转,利用砂轮与工件之间的相对运动,去除工件表面的多余材料,以达到所需的尺寸和表面光洁度。
2. 简述磨削液的作用。
- 磨削液的作用主要有:降低磨削区域的温度,减少工件和砂轮的磨损,提高加工效率,以及带走磨削产生的金属屑和磨粒,防止工件表面划伤。
3. 磨削过程中,砂轮的硬度应如何选择?- 砂轮的硬度选择应根据工件材料的硬度、加工要求和砂轮的磨粒类型来决定。
一般来说,工件材料硬度越高,砂轮硬度应越低;加工要求光洁度越高,砂轮硬度应越高。
4. 磨削过程中,砂轮的速度应如何控制?- 砂轮的速度应根据工件材料、砂轮的类型和磨削要求来控制。
对于硬度较高的材料,砂轮速度应适当降低;对于要求光洁度较高的加工,砂轮速度应适当提高。
5. 磨床的维护保养主要包括哪些内容?- 磨床的维护保养主要包括:定期检查和更换砂轮,清洁机床表面和工作台,润滑导轨和传动部件,检查和调整机床的水平度和精度。
6. 磨削过程中,工件的夹紧方式有哪些?- 工件的夹紧方式主要有:使用三爪卡盘、四爪卡盘、吸盘、磁力台等。
选择夹紧方式时,应考虑工件的形状、大小和加工要求。
7. 磨削加工中,常见的缺陷有哪些?- 常见的磨削加工缺陷包括:表面烧伤、磨痕、尺寸超差、圆度和圆柱度误差、表面粗糙度不达标等。
8. 如何预防和解决磨削过程中的烧伤问题?- 预防和解决磨削过程中的烧伤问题,可以通过以下方法:使用合适的砂轮硬度和粒度,控制合适的磨削速度和进给速度,使用合适的磨削液,以及定期检查和更换砂轮。
9. 磨床的精度等级是如何划分的?- 磨床的精度等级通常按照国家标准或行业标准进行划分,主要依据机床的几何精度、运动精度和工作精度等指标。
10. 简述磨床的分类。
- 磨床的分类主要包括:平面磨床、外圆磨床、内圆磨床、无心磨床、工具磨床等。
每种磨床都有其特定的加工对象和加工范围。
名词解释砂轮的硬度

名词解释砂轮的硬度砂轮是一种常用的磨料工具,在工业领域有着广泛的应用。
它通过与工件之间的相对运动,使工件表面产生切削、磨削或抛光等作用,从而实现加工和修整的目的。
而砂轮的硬度则是评价砂轮质量和性能的重要指标之一。
本文将对砂轮的硬度进行详细解释,并探讨其影响因素和应用。
1. 硬度的概念与意义硬度是指砂轮材料抵抗硬物侵入或划伤的能力。
对于砂轮而言,硬度越高,抗磨损性和切削能力越强,但易产生脆性断裂。
相反,较低的硬度可提供较好的韧性和抗冲击性能,但其切削效率会降低。
因此,选择适当的硬度成为砂轮选用的重要因素。
2. 硬度的评价方法砂轮硬度的评价方法主要有洛氏硬度和布氏硬度两种。
洛氏硬度是通过对砂轮进行显微硬度测试,得到其硬度值。
而布氏硬度则是通过用布氏硬度计依次施加不同载荷,在相同时间内测量砂轮的印痕面积,并根据印痕面积与载荷之间的关系,计算出砂轮的硬度。
3. 影响砂轮硬度的因素砂轮硬度受多种因素影响,如砂轮材料、砂轮组分和烧结方法等。
首先,砂轮材料的硬度对整个砂轮的硬度有直接影响。
常见的砂轮材料有氧化铝、碳化硅和金刚石等。
其中金刚石的硬度最高,且耐高温性能好,因此具有较高的适应性和广泛应用价值。
其次,砂轮的组分也会对硬度产生影响。
组分中砂轮的磨料与粘结剂的比例以及磨料粒度均会直接影响硬度。
此外,不同的烧结方法也会影响砂轮的硬度。
常见的烧结方法有热压烧结和冷压烧结等,采用不同的烧结方法可以得到不同硬度的砂轮。
4. 硬度与砂轮的应用砂轮硬度的选择需要根据具体的加工要求和工件材料来确定。
对于较硬的工件材料,如钢铁和合金材料,需要选择较高硬度的砂轮,以保证切削效率和表面质量。
而对于较软的工件材料,如铝和铜材料,较低硬度的砂轮更适合,可以减少切削热和磨损。
此外,砂轮的硬度还会影响加工件表面的粗糙度和磨削热。
较高硬度的砂轮可实现更光滑的表面,但也容易产生热损伤。
因此,在实际应用中需要根据加工要求和工件材料的硬度来选择合适的砂轮硬度。
砂轮的硬度

砂轮的硬度砂轮的硬度是指砂轮工件表面上的磨粒受外力作用时脱落的难易程度。
磨粒容易脱落的砂轮,其硬度就低;反之,砂轮硬度就高。
因此,砂轮硬度并不是指磨粒或结合剂本身的硬度,它与金属硬度的概念不同。
同一种磨料,可以做出不同硬度的各种砂轮。
影响砂轮硬度的主要因素是结合剂的性质、数量,砂轮中结合剂的数里越多,它的硬度越高。
磨具成型时的密度也是影响磨具硬度的重要因素。
磨具成型厚度偏差、成型料的千湿、单重称量误差等因素都将使磨具成型密度产生偏差。
此外,磨具的烧结温度以及烧结时间也影响磨具的硬度。
在其他条件相同的悄况下,成型密度大,烧结时间长、温度高,磨具的硬度就商些;反之,硬度低。
砂轮的硬度对加工表面质量和磨削效率有显著的影响。
砂轮的硬度高,磨粒不易脱落,磨粒切削刃的等高性容易保持,所以加工的工件粗糙度低、精度高。
但如果太硬,磨钝了的磨粒仍然留在砂轮表面上掉不下来,不仅磨削效率降低,而且由于钝化了的磨粒在工件表面上摩擦挤压加剧,磨削力和磨削热显著增大,使工件表面粗糙度上升,还容易产生烧伤裂纹等缺陷。
相反,如果砂轮的硬度较低,磨钝了的磨粒容易脱落,砂轮工作表面上经常保持者锋利的磨粒,磨削效率提高,而且发热量少,可以避免工件表面烧伤,但工件精度和表面粗糙度就差些。
当硬度太低时,磨粒还处在锋利状态下就脱落,使砂轮很快失去iK确的几何形状,工件楮度难以控制,工件表面也容易被脱落的粒磨划伤,致使表面粗糙度升高,同时磨削效串也将下降。
为了适应不同加工条件的需要,砂轮有多种硬度等级。
CB/T2484-94规定磨只硬度代号由软至硬的顺序为:A,B,C,D,E,F,G,H,J,K,L,M,N,P,Q,T,Y表2-3是我国生产的砂轮硬度等级(国标)划分表。
- 1、下载文档前请自行甄别文档内容的完整性,平台不提供额外的编辑、内容补充、找答案等附加服务。
- 2、"仅部分预览"的文档,不可在线预览部分如存在完整性等问题,可反馈申请退款(可完整预览的文档不适用该条件!)。
- 3、如文档侵犯您的权益,请联系客服反馈,我们会尽快为您处理(人工客服工作时间:9:00-18:30)。
C(37C)―黑色碳化硅
碳化硅适用于铸铁、硬质合金、有色金属的磨削,也可用于玻璃、石材等非金属材料的磨削。
(3)SG磨料
SG磨料是圣戈班开发的经特殊引晶凝胶系统烧结而成,带有革命性的新一代氧化铝磨料,具有硬度高,
韧性好,锋利度强等优点。与普通刚玉磨料相比,SG具有磨耗比高,保形性强,工件表面加工质量好,砂轮修整量小,磨削效率高等优越性。SG砂轮特别适用于航空航天用合金、工具钢、淬火工件、硬铬、硬铸铁等的磨削。因SG磨料价格较贵,通常SG可以根据不同场合的磨削要求,以一定比例同白刚玉(或其它刚玉磨料)进行混合制成砂轮,以达到磨削效果和砂轮成本的最佳组合。
NORTON陶瓷结合剂产品介绍:
1、磨料种类
(1)刚玉类磨料:
A棕刚玉砂轮:适用于硬度较低的碳素钢、合金钢、可锻铸铁工件的普通磨削,如外圆磨、平面磨和无心磨,也可用于切断、打磨等场合。
WA(38A)―白刚玉砂轮:用于硬度较高的合金钢、高速钢、淬火工件的普通磨削,也多用于齿轮磨、螺纹磨、成型磨场合。
AWA(19A)―棕、白刚玉混合磨料:适用于硬度中等的碳素钢、合金钢工件的普通磨削。既可保证工件的表面粗糙度,又具有一定有磨削效率。
1.工件越硬,砂轮越软。
2.砂轮与工件接触面ቤተ መጻሕፍቲ ባይዱ大,砂轮选择越软。
3.精磨和成型磨削时应选择较硬的砂轮,以保持砂轮必要的形状精度。
4.砂轮硬度选择与粒度大小的关系:粒度越大的砂轮,为避免砂轮被磨屑阻塞,一般要选择较软的砂轮。
5.工件材料:磨有色金属、橡胶、树脂等较软材料时,应选用较软的砂轮。
砂轮选择及诺顿砂轮介绍
SA(32A)―单晶刚玉:适用于高速钢、奥氏体不锈钢、钛合金等高硬度、高强度金属材料的磨削。
ASA(23A)―单晶刚玉和棕刚玉的混合磨料:适用于球墨铸铁、冷激铸铁类材料的高效磨削,也用于轴承钢的普通磨削。
PA(25A)―铬刚玉,用于工具钢、不锈钢、淬火工件的内圆磨、工具磨、仿型磨及高光洁度磨削。
(2)碳化硅类磨料:
5、结合剂:
结合剂是砂轮的关键组成之一,其功能是将磨料颗粒接固成一体形成砂轮,以帮助其实现磨削功能。陶瓷结合剂一般是呈玻璃态的无机材料。结合剂的选择主要取决于砂轮的工作速度,工件的加工方式及加工精度的要求。圣戈班公司作为全球磨料磨具工业的先驱和领导者,积一百多年的砂轮制造、应用的经验,研制开发了近百种不同性能的结合剂。
使用树脂粘结的砂轮进行M2高速钢平面磨削试验。实验中,用ABN600和ABN800两种磨料制成的小砂轮的尺寸为125mm×6mm。实验结果表明,使用尖锐的磨料的砂轮寿命长,而磨削功率低。
众所周知,磨削过程中,在磨料和工件磨削面之间会产生瞬间界面高温。试验证明,与常用磨料相比,立方氧化硼产生的界面磨削温度更低。其中关键原因是立方氧化硼砂轮的比磨削能要比常用磨料的砂轮低。通过试验,可以看到,随着切削深度的提高,立方氧化硼砂轮之所以具有低的磨削能,主要得益于立方氧化硼具有高的热导率。
缓进给磨削中磨料特征的影响。在磨削过程中加在单个磨料粒子上载荷的种类与大小都将影响到磨粒的切削性能,进而影响到最佳磨料的选择。为说明这点,进行了台下的试验:使用端头半径为0.5mmr90°V型陶瓷粘结砂轮磨削M2高速钢,对两种ABN600和ABN800磨料进行测试,并对法向磨削力、功率和砂轮的磨损进行监测。可以看到,ABN800法向磨削力较低。当进给量提高时,切削率增加,磨削力也同时提高。但对于ABN800砂轮,磨削力的提高相对较小。而磨削功率随进给量的增加而提高的趋势与ABN600基本相同。尽管对于ABN800磨料制成的砂轮测出的磨削力和能量较低但曲率为0.5mm砂轮端面的磨损也同时减小。当进给量从而200mm/min提高到300mm/min时,三个参数增中的相对百分比,即切削功率提高50%。随着磨削条件的恶劣程度加剧,具有尖角状特征的磨粒的优点表现得更为突出。
实际上,对磨料合成条件控制得严格与否将会直接影响到磨粒的最终晶型和包括强度、热稳定性和断裂特征在内的物理性质,从而影响到它的使用性能。如De Beers公司生产的四种ABN产品,这四种产品每种都具有自己不同的特性。ABN200是脆性的黑色磨料,主要用于陶瓷粘结磨削工具和金属包敷树脂粘结的磨削工具。ABN300具有与ABN200相似的强度,但颜色为琥珀色,通常应用于金属和环氧树脂粘结的磨削工具。ABN600为黑色,是一种典型的具有特定晶面的高强立方氧化硼磨料,也是应用于金属和环氧树脂粘结的磨具。ABN800则是最新一代的高强单晶立方氧化化硼材料。ABN800具有与ABN600相似的强度,但是,可以看到两者存在着显著的不同,前者具有尖锐棱角和高热稳定性。
砂轮硬度及砂轮硬度的选择
砂轮磨具的硬度是反映磨粒在磨削力的作用下,从砂轮表面上脱落的难易程度。砂轮硬度用软硬表示,砂轮的硬度不同于磨粒的硬度。
砂轮选用的时候,要注意硬度适当,如果太硬,磨钝了的磨粒不及时脱落,会产生大量热量,烧伤工件;砂轮太软,则会使磨粒脱落过快而不能充分发挥作用。
[选择砂轮硬度的原则]
镍铬钢是一种较难磨削的材料。针对有尖锐棱角的磨料去屑率高的特点,用陶瓷粘结的砂轮对牌号为718的镍铬钢进行磨削试验。对两种高强磨料,ABN600和ABN800进行了如前的试验。可以看到,与ABN600相比,在工作台速度为150mm/min和200mm/min时,ABN800仍保持它的优点。当工作台速度进一步提高到300mm/min时,两种砂轮都表现出高的砂轮磨损速率。然而,试验结果表明,当使用尖锐磨料制成的砂轮磨削同样的材料时,在150mm/min和200mm/min的两种速度下,都可以得到合理的砂轮寿命。
4) 工件半径或孤度小的场合。
3、硬度
E F G H I J K L M N O P Q R
软 硬
砂轮的硬度是指磨料之间的结合度,砂轮中结合剂量的多少决定了砂轮的硬度高低。用户需要根据具体的磨削(如进刀量、粗糙度、材质)要求来灵活选择砂轮的硬度。
一般砂轮硬度选择的原则是:
•较软的硬度
1)进刀量大的粗磨。
6、可供砂轮直径尺寸:30―1200mm
7、可供线速度:35m/s―63m/s
9、产品订购要素:
订购表述:磨料•粒度•硬度•组织号•结合剂•线速度•形状•外径•厚度•孔径•数量
例:WA 46K 11 VBE 45m/s P 350401275片
近年来随着新技术的开发应用,高精度磨削技术的发展,使磨削尺寸达到0.1~0.3μm,表面粗糙度达到0.2~0.05μm,磨削表面变质层和残留应力均甚小,明显提高的加工质量。成形磨削,特别是高精度的成形磨削,经常是生活中的关键问题。成形磨削有两个难题:一是砂轮质量,主要是砂轮必须同时具有良好的自砺性和形廓保持性,而这二者往往是有矛盾的。二是砂轮修整技术,即高效、经济的获得所要求的砂轮形廓和锐度。因而为了提高磨削的效率和精度,特别是对于难加工材料的高效精加工,高效和强力磨削采用了CBN砂轮,使得强力磨突破传统磨削的限制,生产率成倍提高,有些零件的毛坯不需要经过粗加工,可直接磨削成为成品,这不仅提高了加工效率,同时还提高了加工质量。如SG磨料。它是一种新颖的陶瓷氧化铝磨料,以纯刚玉为原料,将其在水中与氧化镁之类媒介结合,产生块状胶凝物,干燥之后形成脆性物体。再将其碾碎至所需粒度,在1300℃到1400℃到温度下烧结而成。其硬度大大高于普通氧化铝,且韧性好,因此可以在较高速度和较大载荷条件下运转,金属磨除率比普通氧化铝高三倍以上。它最大的优点是磨削区温度低,砂轮始终具有锋利的磨削刃,砂轮形状保持性好、时间长。立方氮化硼磨削。它是一种坚硬而耐磨的磨料,并具有高的导热性和耐化学侵蚀等优异的性质。最新一代的磨料是以尖锐、高强和可用于无支撑切削为特征的,这些特征可降低磨削加工过程中的磨削力,从而减少对工件的损伤。
1)材质较软,延伸率大以及类似软铁和有色金属等材料。
2)进给量大,磨削效率要求高的场合。
3)表面粗糙度要求不高的场合。
4)磨削接触面大的场合。
•细粒度的磨料适用于磨削:
1) 硬度较高以及类似高碳工具钢,硬质合金一类的金属材料和玻璃等脆性材料。
2) 表面粗糙度及精度要求高的场合。
3) 磨削接触面小的场合。
常用形状代号:P(平形)、PDA(单面凹)、PSX(双斜边)、PDX(单斜边)、B(杯形)、PSA(双面凹)
美国NORTON诺顿砂轮规格参数及其使用用途
砂轮粒度选择
20 22 24 30 36 40 46 54 60 70 80 90 100 120 150 180 220 280 320 400
磨料依次由粗到细
在磨削过程中,块状或圆的磨粒可考虑采用与工件呈较大的负前角进行磨削。而对尖锐的多角状的粒子在多数情况下采用较大的正前角进行磨削。因此,在磨削碳化物含量较高的钢(如某些高速钢)时,最好选择具有负前角的磨料粒子。当加工更硬的强韧材料(如某些高速钢和表面硬化钢)时,具有较大的正前角的尖锐多角状磨粒具有潜在的优势。
综上所述,在不同材料和工艺条件的磨削中,合理选用砂轮,可降低磨削加工表面精度,提高磨削加工表面质量,能使磨削效率有成倍的提高,取得低成本加工的效果,并且砂轮寿命长,修整频率低,金属磨除率高,磨削力小冷却效果佳。
诺顿砂轮介绍
一、磨具磨料:
人类从新石器时代开始,就采用天然磨石打磨用具。伴随着蒸汽机的发明,磨具磨料开始进入机械制造领域,并成为不可替代的工艺方法越来越大量使用,是获得高精度产品的重要手段。缔属于圣戈班集团的NORTON(诺顿)品牌,创建于一八八五年,是世界最早从事磨具磨料研究、生产的专业工厂,一百多年来倾心为用户提供保证磨削质量,提高磨削效率、降低制造成本的优质产品,是全球最大的磨具磨料制造商。在中国五十年代出版的工具书中都可以见到该品牌的介绍,从圣戈班NORTON在国内设厂生产后,是目前在中国大陆能买到的最佳性价比的国外品牌。