2。铸造简介及大铸件质量控制
铸造质量控制

铸造质量控制铸造质量控制是指在铸造过程中对产品质量进行管理和控制的一系列措施。
通过合理的质量控制措施,可以确保铸造产品的尺寸精度、表面质量、力学性能等指标达到设计要求,从而提高产品的质量和可靠性。
一、质量控制的目标和意义铸造质量控制的目标是确保产品质量达到设计要求,具体包括以下几个方面:1. 尺寸精度控制:通过控制铸件的收缩和变形,保证尺寸精度在允许范围内。
2. 表面质量控制:确保铸件表面光洁度、无气孔、夹杂物等缺陷。
3. 力学性能控制:保证铸件的强度、韧性等力学性能满足要求。
4. 成本控制:通过合理的质量控制措施,降低不合格品率,减少生产成本。
质量控制的意义在于:1. 提高产品质量:通过严格的质量控制,确保产品达到设计要求,提高产品的质量和可靠性。
2. 降低生产成本:通过减少废品率、减少返工率等手段,降低生产成本。
3. 提高企业竞争力:优质的产品能够提高企业的竞争力,赢得更多的市场份额。
二、质量控制的主要内容和方法1. 原材料控制:选择合适的原材料,确保其质量符合要求。
对原材料进行化学成分分析、物理性能测试等,确保铸件的化学成分和机械性能满足要求。
2. 铸型制备控制:控制铸型的制备工艺,确保铸型的密实性、耐火性等性能,避免铸型砂中的气孔、夹杂物等缺陷。
3. 浇注工艺控制:控制浇注温度、浇注速度、浇注时间等参数,确保熔融金属在铸型中充分填充,避免铸件出现冷隔、缩松等缺陷。
4. 熔炼工艺控制:控制熔炼温度、炉渣成分等参数,确保熔融金属的化学成分和纯净度符合要求。
5. 热处理工艺控制:对铸件进行热处理,提高其力学性能。
控制热处理温度、保温时间等参数,确保铸件的组织结构和性能达到设计要求。
6. 检测与检验:通过无损检测、化学成分分析、力学性能测试等手段,对铸件进行质量检测和检验,确保产品质量符合要求。
7. 过程控制:建立合理的工艺流程和操作规程,对每个工序进行严格控制,确保每一道工序的质量稳定可靠。
三、质量控制的指标和标准1. 尺寸精度指标:包括线性尺寸公差、平面度、垂直度等指标,根据产品设计要求和使用要求进行控制。
铸造工艺流程的质量控制方法
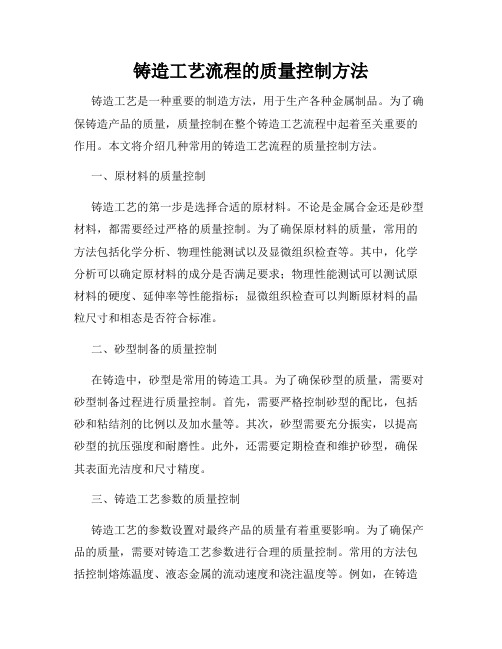
铸造工艺流程的质量控制方法铸造工艺是一种重要的制造方法,用于生产各种金属制品。
为了确保铸造产品的质量,质量控制在整个铸造工艺流程中起着至关重要的作用。
本文将介绍几种常用的铸造工艺流程的质量控制方法。
一、原材料的质量控制铸造工艺的第一步是选择合适的原材料。
不论是金属合金还是砂型材料,都需要经过严格的质量控制。
为了确保原材料的质量,常用的方法包括化学分析、物理性能测试以及显微组织检查等。
其中,化学分析可以确定原材料的成分是否满足要求;物理性能测试可以测试原材料的硬度、延伸率等性能指标;显微组织检查可以判断原材料的晶粒尺寸和相态是否符合标准。
二、砂型制备的质量控制在铸造中,砂型是常用的铸造工具。
为了确保砂型的质量,需要对砂型制备过程进行质量控制。
首先,需要严格控制砂型的配比,包括砂和粘结剂的比例以及加水量等。
其次,砂型需要充分振实,以提高砂型的抗压强度和耐磨性。
此外,还需要定期检查和维护砂型,确保其表面光洁度和尺寸精度。
三、铸造工艺参数的质量控制铸造工艺的参数设置对最终产品的质量有着重要影响。
为了确保产品的质量,需要对铸造工艺参数进行合理的质量控制。
常用的方法包括控制熔炼温度、液态金属的流动速度和浇注温度等。
例如,在铸造过程中,如果熔炼温度过高,易导致铸件内部存在气孔和夹杂物;如果浇注温度过低,易导致铸件的收缩缺陷。
因此,合理控制这些参数可以有效提高铸件的质量。
四、铸造产品的检测与测试在铸造工艺流程中,对铸造产品进行质量检测和测试是不可或缺的环节。
常用的方法包括无损检测、机械性能测试以及尺寸测量等。
其中,无损检测可以通过X射线、超声波等方法检测产品是否存在缺陷;机械性能测试可以测试产品的抗拉强度、硬度等力学性能;尺寸测量则可以验证产品的尺寸精度是否符合要求。
五、质量记录与反馈为了总结经验并改进铸造工艺流程,需要对质量进行记录和反馈。
对于每个铸造批次,应该记录原材料、砂型、工艺参数以及产品质量等关键信息。
铸造质量控制
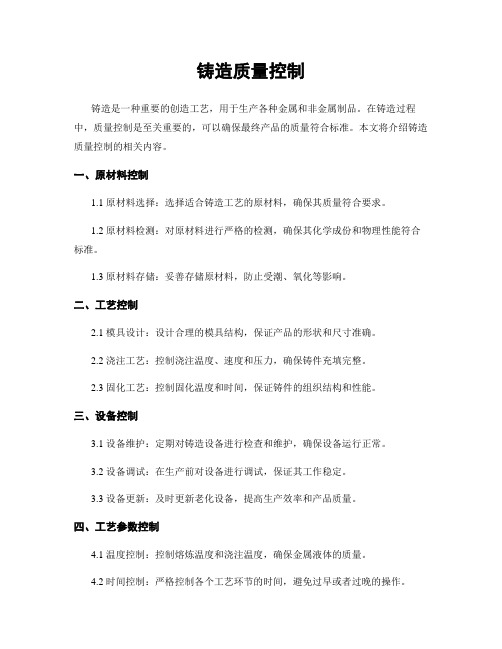
铸造质量控制铸造是一种重要的创造工艺,用于生产各种金属和非金属制品。
在铸造过程中,质量控制是至关重要的,可以确保最终产品的质量符合标准。
本文将介绍铸造质量控制的相关内容。
一、原材料控制1.1 原材料选择:选择适合铸造工艺的原材料,确保其质量符合要求。
1.2 原材料检测:对原材料进行严格的检测,确保其化学成份和物理性能符合标准。
1.3 原材料存储:妥善存储原材料,防止受潮、氧化等影响。
二、工艺控制2.1 模具设计:设计合理的模具结构,保证产品的形状和尺寸准确。
2.2 浇注工艺:控制浇注温度、速度和压力,确保铸件充填完整。
2.3 固化工艺:控制固化温度和时间,保证铸件的组织结构和性能。
三、设备控制3.1 设备维护:定期对铸造设备进行检查和维护,确保设备运行正常。
3.2 设备调试:在生产前对设备进行调试,保证其工作稳定。
3.3 设备更新:及时更新老化设备,提高生产效率和产品质量。
四、工艺参数控制4.1 温度控制:控制熔炼温度和浇注温度,确保金属液体的质量。
4.2 时间控制:严格控制各个工艺环节的时间,避免过早或者过晚的操作。
4.3 压力控制:根据产品要求控制浇注压力,确保铸件的密度和强度。
五、质量检验控制5.1 外观检验:对铸件的表面质量进行检查,包括气孔、裂纹等缺陷。
5.2 尺寸检验:测量铸件的尺寸和几何形状,确保符合设计要求。
5.3 化学成份检验:对铸件的化学成份进行分析,确保符合标准。
综上所述,铸造质量控制是确保铸件质量的关键环节,需要在原材料、工艺、设备、工艺参数和质量检验等方面进行全面控制。
惟独做好质量控制,才干生产出满足客户需求的优质铸件。
铸件质量控制计划
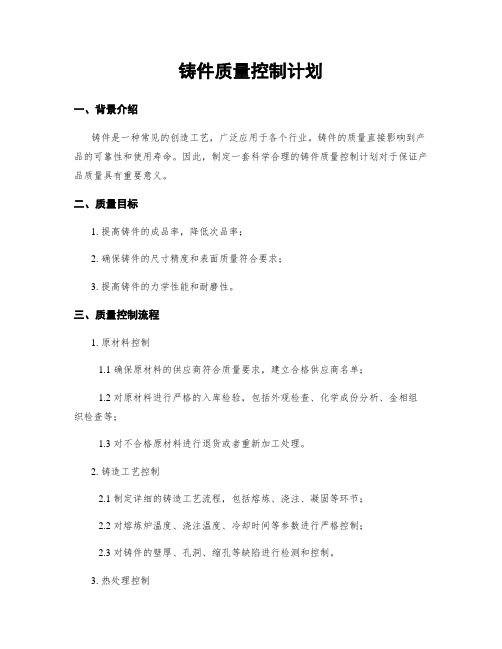
铸件质量控制计划一、背景介绍铸件是一种常见的创造工艺,广泛应用于各个行业。
铸件的质量直接影响到产品的可靠性和使用寿命。
因此,制定一套科学合理的铸件质量控制计划对于保证产品质量具有重要意义。
二、质量目标1. 提高铸件的成品率,降低次品率;2. 确保铸件的尺寸精度和表面质量符合要求;3. 提高铸件的力学性能和耐磨性。
三、质量控制流程1. 原材料控制1.1 确保原材料的供应商符合质量要求,建立合格供应商名单;1.2 对原材料进行严格的入库检验,包括外观检查、化学成份分析、金相组织检查等;1.3 对不合格原材料进行退货或者重新加工处理。
2. 铸造工艺控制2.1 制定详细的铸造工艺流程,包括熔炼、浇注、凝固等环节;2.2 对熔炼炉温度、浇注温度、冷却时间等参数进行严格控制;2.3 对铸件的壁厚、孔洞、缩孔等缺陷进行检测和控制。
3. 热处理控制3.1 制定合理的热处理工艺流程,包括加热温度、保温时间、冷却速率等;3.2 对热处理设备进行定期维护和校准,确保温度和时间的准确性;3.3 对热处理后的铸件进行硬度测试、金相组织观察等检验。
4. 机械加工控制4.1 制定详细的加工工艺流程,包括铣削、钻孔、车削等操作;4.2 对加工设备进行定期维护和保养,确保设备的精度和稳定性;4.3 对加工件进行尺寸测量和表面质量检查,确保符合要求。
5. 检验控制5.1 制定全面的检验计划,包括外观检查、尺寸测量、力学性能测试等;5.2 对检验设备进行定期校准和维护,确保准确可靠;5.3 对不合格品进行分类和处理,追溯问题原因并采取纠正措施。
四、质量控制指标1. 铸件成品率:目标为95%以上;2. 铸件次品率:目标为5%以下;3. 尺寸精度:符合产品图纸要求;4. 表面质量:无裂纹、气孔等缺陷;5. 力学性能:符合产品技术要求。
五、质量控制记录1. 原材料检验记录,包括供应商信息、检验结果等;2. 铸造工艺参数记录,包括熔炼温度、浇注温度、冷却时间等;3. 铸件缺陷记录,包括壁厚、孔洞、缩孔等情况;4. 热处理工艺参数记录,包括加热温度、保温时间、冷却速率等;5. 热处理后铸件的硬度测试记录;6. 机械加工工艺参数记录,包括铣削、钻孔、车削等操作;7. 加工件尺寸测量和表面质量检查记录;8. 检验结果记录,包括外观检查、尺寸测量、力学性能测试等;9. 不合格品处理记录,包括分类、原因分析和纠正措施。
铸件质量控制计划
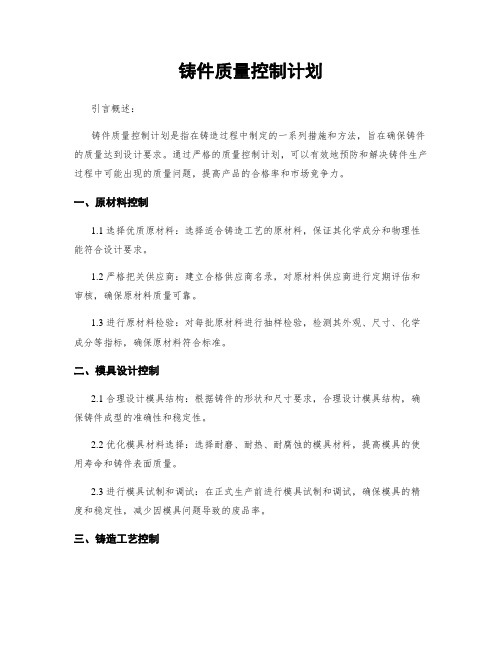
铸件质量控制计划引言概述:铸件质量控制计划是指在铸造过程中制定的一系列措施和方法,旨在确保铸件的质量达到设计要求。
通过严格的质量控制计划,可以有效地预防和解决铸件生产过程中可能出现的质量问题,提高产品的合格率和市场竞争力。
一、原材料控制1.1 选择优质原材料:选择适合铸造工艺的原材料,保证其化学成分和物理性能符合设计要求。
1.2 严格把关供应商:建立合格供应商名录,对原材料供应商进行定期评估和审核,确保原材料质量可靠。
1.3 进行原材料检验:对每批原材料进行抽样检验,检测其外观、尺寸、化学成分等指标,确保原材料符合标准。
二、模具设计控制2.1 合理设计模具结构:根据铸件的形状和尺寸要求,合理设计模具结构,确保铸件成型的准确性和稳定性。
2.2 优化模具材料选择:选择耐磨、耐热、耐腐蚀的模具材料,提高模具的使用寿命和铸件表面质量。
2.3 进行模具试制和调试:在正式生产前进行模具试制和调试,确保模具的精度和稳定性,减少因模具问题导致的废品率。
三、铸造工艺控制3.1 严格控制浇注温度:根据铸件材料和结构要求,控制浇注温度,避免因温度过高或过低导致铸件缺陷。
3.2 控制浇注速度和压力:合理控制浇注速度和压力,确保铸件充型充实,避免气孔和夹杂等缺陷。
3.3 采取适当的冷却措施:在铸造结束后,采取合适的冷却措施,避免因快速冷却或过慢冷却导致铸件内部应力过大。
四、热处理控制4.1 选择合适的热处理工艺:根据铸件的材料和使用要求,选择适合的热处理工艺,提高铸件的强度和硬度。
4.2 严格控制热处理参数:在热处理过程中,严格控制温度、时间和冷却速度等参数,确保热处理效果稳定可靠。
4.3 进行热处理质量检验:对热处理后的铸件进行硬度测试、金相分析等检验,确保热处理效果符合设计要求。
五、表面处理控制5.1 选择适合的表面处理方法:根据铸件的用途和要求,选择合适的表面处理方法,提高铸件的耐腐蚀性和美观度。
5.2 严格控制表面处理工艺:在表面处理过程中,严格控制处理时间、温度和液体浓度等参数,确保表面处理效果均匀一致。
铸件质量控制计划

铸件质量控制计划一、引言铸件是制造业中常见的零部件,其质量直接影响到产品的性能和可靠性。
为了保证铸件的质量,需要制定一套科学的质量控制计划。
本文将详细介绍铸件质量控制计划的制定过程,包括质量目标、质量控制流程、质量控制方法以及质量控制指标等方面。
二、质量目标1. 定义质量目标:根据产品的使用要求和客户的需求,确定铸件的质量目标。
例如,铸件的尺寸精度、力学性能、表面质量等方面的要求。
2. 制定质量指标:根据质量目标,制定相应的质量指标,以便对铸件的质量进行评估和控制。
三、质量控制流程1. 原材料采购:确保采购的原材料符合相关标准和要求,包括铸造合金、砂型材料等。
2. 铸造工艺控制:制定合理的铸造工艺参数,包括熔炼温度、浇注速度、浇注温度等,并通过实时监测和记录来控制铸造过程。
3. 砂型制备:选择适合的砂型材料和制备工艺,确保砂型的质量和准确性。
4. 铸件成型:严格按照工艺要求进行铸件的成型,包括浇注、冷却、脱模等过程。
5. 热处理控制:根据铸件材料的要求,制定合适的热处理工艺,并通过温度控制和冷却速率控制来保证铸件的力学性能。
6. 机械加工:对铸件进行必要的机械加工,包括铣削、钻孔、磨削等,以确保尺寸精度和表面质量。
7. 检测和检验:采用合适的检测方法对铸件进行检验,包括外观检查、尺寸测量、力学性能测试等。
8. 不合格品处理:对于不合格的铸件,制定相应的处理措施,如修复、返工或报废。
四、质量控制方法1. 统计过程控制(SPC):通过统计方法对铸件的关键质量特性进行监控,及时发现和纠正质量问题。
2. 全面质量管理(TQM):通过全员参与、持续改进的方式,提高铸件的整体质量水平。
3. 6σ管理:通过精确的数据分析和过程改进,将不合格品率控制在极低水平。
4. 设备维护管理:定期对铸造设备进行维护和保养,确保设备的正常运行和稳定性。
五、质量控制指标1. 尺寸精度:以尺寸偏差为指标,如直径偏差、平面度等。
2. 表面质量:以表面粗糙度、气孔和夹杂物等为指标。
铸件质量控制计划
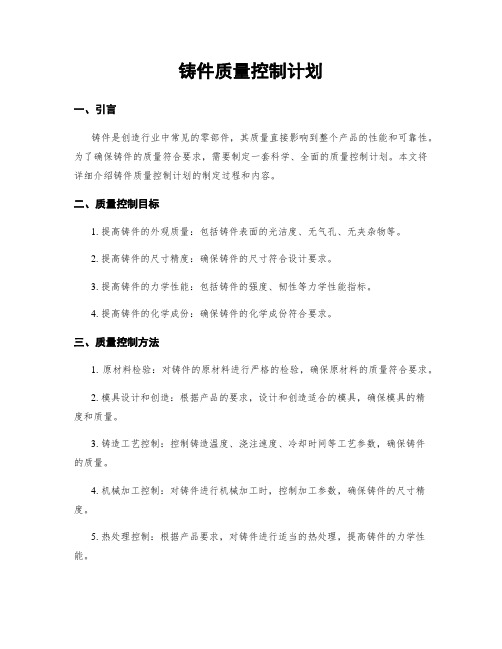
铸件质量控制计划一、引言铸件是创造行业中常见的零部件,其质量直接影响到整个产品的性能和可靠性。
为了确保铸件的质量符合要求,需要制定一套科学、全面的质量控制计划。
本文将详细介绍铸件质量控制计划的制定过程和内容。
二、质量控制目标1. 提高铸件的外观质量:包括铸件表面的光洁度、无气孔、无夹杂物等。
2. 提高铸件的尺寸精度:确保铸件的尺寸符合设计要求。
3. 提高铸件的力学性能:包括铸件的强度、韧性等力学性能指标。
4. 提高铸件的化学成份:确保铸件的化学成份符合要求。
三、质量控制方法1. 原材料检验:对铸件的原材料进行严格的检验,确保原材料的质量符合要求。
2. 模具设计和创造:根据产品的要求,设计和创造适合的模具,确保模具的精度和质量。
3. 铸造工艺控制:控制铸造温度、浇注速度、冷却时间等工艺参数,确保铸件的质量。
4. 机械加工控制:对铸件进行机械加工时,控制加工参数,确保铸件的尺寸精度。
5. 热处理控制:根据产品要求,对铸件进行适当的热处理,提高铸件的力学性能。
6. 检测与测试:使用适当的检测和测试方法,对铸件进行质量检验,确保铸件的质量符合要求。
四、质量控制流程1. 原材料检验流程:a. 对原材料进行外观检查,检查是否有明显的缺陷。
b. 进行化学成份分析,确保原材料的化学成份符合要求。
c. 进行物理性能测试,包括硬度、抗拉强度等指标的测试。
2. 模具设计和创造流程:a. 根据产品要求,设计模具的结构和尺寸。
b. 创造模具,并进行精度检验,确保模具的精度符合要求。
3. 铸造工艺控制流程:a. 设定铸造温度、浇注速度、冷却时间等工艺参数。
b. 进行铸造过程监控,记录关键参数,确保铸件的质量。
4. 机械加工控制流程:a. 设定机械加工参数,包括切削速度、进给量等。
b. 进行机械加工过程监控,记录加工参数和尺寸精度。
5. 热处理控制流程:a. 根据产品要求,选择适当的热处理工艺。
b. 进行热处理过程监控,确保铸件的力学性能符合要求。
铸造质量控制
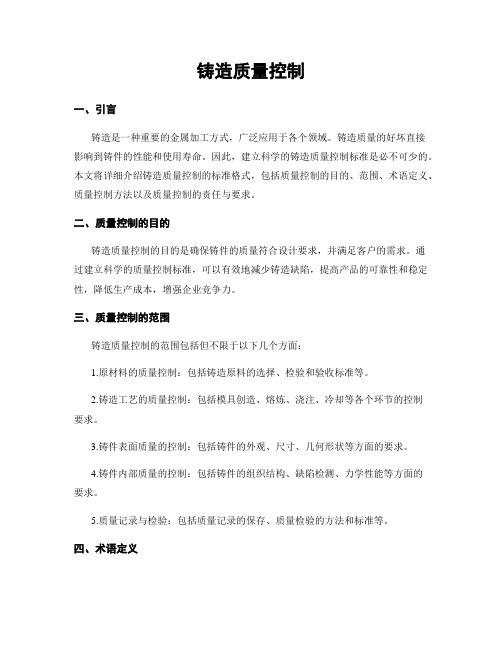
铸造质量控制一、引言铸造是一种重要的金属加工方式,广泛应用于各个领域。
铸造质量的好坏直接影响到铸件的性能和使用寿命。
因此,建立科学的铸造质量控制标准是必不可少的。
本文将详细介绍铸造质量控制的标准格式,包括质量控制的目的、范围、术语定义、质量控制方法以及质量控制的责任与要求。
二、质量控制的目的铸造质量控制的目的是确保铸件的质量符合设计要求,并满足客户的需求。
通过建立科学的质量控制标准,可以有效地减少铸造缺陷,提高产品的可靠性和稳定性,降低生产成本,增强企业竞争力。
三、质量控制的范围铸造质量控制的范围包括但不限于以下几个方面:1.原材料的质量控制:包括铸造原料的选择、检验和验收标准等。
2.铸造工艺的质量控制:包括模具创造、熔炼、浇注、冷却等各个环节的控制要求。
3.铸件表面质量的控制:包括铸件的外观、尺寸、几何形状等方面的要求。
4.铸件内部质量的控制:包括铸件的组织结构、缺陷检测、力学性能等方面的要求。
5.质量记录与检验:包括质量记录的保存、质量检验的方法和标准等。
四、术语定义1.铸造缺陷:指在铸造过程中产生的不符合设计要求的缺陷,如气孔、夹杂、砂眼等。
2.模具:用于创造铸件形状的工具,可以是金属模具、砂型、蜡模等。
3.熔炼:将金属原料加热至液态,并进行铸造准备的过程。
4.浇注:将熔融金属倒入模具中,使其冷却凝固成型的过程。
5.冷却:铸件在浇注后,通过自然冷却或者其他冷却方式使其降温凝固的过程。
五、质量控制方法1.原材料的质量控制方法:(1)选择合适的原材料供应商,并建立长期稳定的合作关系。
(2)对原材料进行严格的检验,包括外观、化学成份、物理性能等指标。
(3)制定原材料验收标准,明确合格和不合格的判定标准。
2.铸造工艺的质量控制方法:(1)制定详细的工艺流程和作业指导书,明确每一个环节的工艺参数和操作要求。
(2)对模具进行定期检查和维护,确保其精度和使用寿命。
(3)严格控制熔炼过程中的温度、时间、搅拌等参数,确保金属液的质量。
铸造质量控制

铸造质量控制一、概述铸造质量控制是指通过一系列的措施和方法,确保铸造件在制造过程中达到预期的质量要求。
本文将从铸造工艺、质量控制方法和质量控制指标三个方面详细介绍铸造质量控制的标准格式文本。
二、铸造工艺1. 铸型制备:铸造件的质量直接受到铸型的影响,因此应根据铸造件的形状、尺寸和材料特性,选择合适的铸型材料和制备工艺。
铸型制备应符合相关标准和规范,确保铸型的精度和表面质量。
2. 熔炼与浇注:熔炼是铸造过程中的关键环节,应严格控制熔炼温度、熔炼时间和熔炼材料的质量。
浇注过程中,应注意铸液的温度控制、浇注速度和浇注方式,以避免铸造缺陷的产生。
3. 凝固与冷却:凝固过程是铸造件形成的关键阶段,应根据铸件的结构特点和材料性能,合理控制凝固速度和冷却方式,以获得理想的组织结构和性能。
4. 除砂与清洁:铸件出模后,应进行除砂和清洁工作,以去除铸件表面的砂粒和杂质,确保铸件的表面光洁度和尺寸精度。
三、质量控制方法1. 工艺参数控制:通过对铸造工艺参数的控制,如熔炼温度、浇注速度、凝固时间等,来影响铸件的质量。
可以通过设定合理的参数范围、监测和调整参数数值,以达到质量控制的目的。
2. 检测与检验:采用合适的检测与检验方法,对铸件的尺寸、形状、组织结构和性能进行评估。
常用的检测方法包括尺寸测量、金相分析、硬度测试、无损检测等。
3. 过程监控:通过实时监测铸造过程中的关键参数和指标,如铸液温度、浇注速度、凝固时间等,及时发现异常情况并采取相应措施,以确保铸件的质量稳定。
4. 环境管理:铸造过程中的环境条件对铸件的质量也有一定影响。
应通过控制环境温度、湿度和灰尘等因素,来减少外界环境对铸件质量的影响。
四、质量控制指标1. 尺寸精度:铸件的尺寸精度是衡量其质量的重要指标之一。
应根据铸件的设计要求和使用环境,制定合理的尺寸公差,并通过尺寸测量和检验来评估尺寸精度。
2. 表面质量:铸件的表面质量直接影响其外观和使用寿命。
应通过除砂、清洁和表面处理等措施,确保铸件表面的光洁度和无裂纹、气孔等缺陷。
铸造质量控制
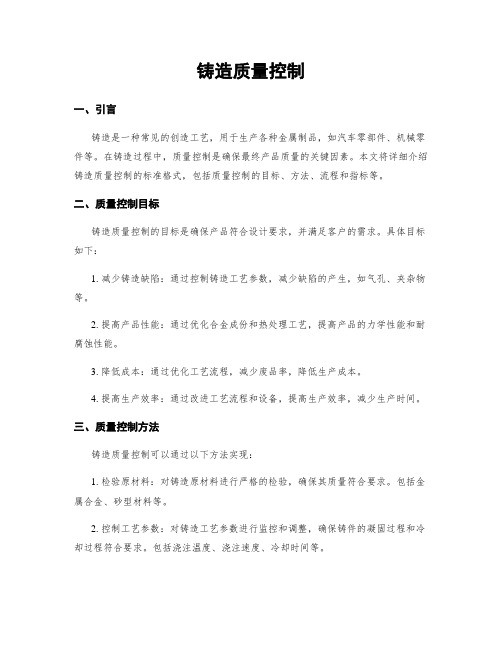
铸造质量控制一、引言铸造是一种常见的创造工艺,用于生产各种金属制品,如汽车零部件、机械零件等。
在铸造过程中,质量控制是确保最终产品质量的关键因素。
本文将详细介绍铸造质量控制的标准格式,包括质量控制的目标、方法、流程和指标等。
二、质量控制目标铸造质量控制的目标是确保产品符合设计要求,并满足客户的需求。
具体目标如下:1. 减少铸造缺陷:通过控制铸造工艺参数,减少缺陷的产生,如气孔、夹杂物等。
2. 提高产品性能:通过优化合金成份和热处理工艺,提高产品的力学性能和耐腐蚀性能。
3. 降低成本:通过优化工艺流程,减少废品率,降低生产成本。
4. 提高生产效率:通过改进工艺流程和设备,提高生产效率,减少生产时间。
三、质量控制方法铸造质量控制可以通过以下方法实现:1. 检验原材料:对铸造原材料进行严格的检验,确保其质量符合要求。
包括金属合金、砂型材料等。
2. 控制工艺参数:对铸造工艺参数进行监控和调整,确保铸件的凝固过程和冷却过程符合要求。
包括浇注温度、浇注速度、冷却时间等。
3. 检测铸件缺陷:使用无损检测技术,如X射线检测、超声波检测等,对铸件进行缺陷检测,及时发现和修复缺陷。
4. 进行力学性能测试:对铸件进行拉伸、弯曲等力学性能测试,确保产品的力学性能符合要求。
5. 进行化学成份分析:对铸件进行化学成份分析,确保合金成份符合要求。
6. 进行金相组织分析:对铸件进行金相组织分析,了解铸件的组织结构和缺陷情况。
四、质量控制流程铸造质量控制的流程包括以下步骤:1. 设计铸造工艺:根据产品要求和材料特性,设计合适的铸造工艺,包括模具设计、浇注系统设计等。
2. 检验原材料:对铸造原材料进行检验,确保其质量符合要求。
3. 控制工艺参数:根据设计要求,控制铸造工艺参数,如浇注温度、浇注速度等。
4. 监控铸造过程:通过实时监控铸造过程中的温度、压力等参数,确保铸造过程的稳定性。
5. 进行缺陷检测:对铸件进行缺陷检测,如X射线检测、超声波检测等,发现并修复缺陷。
铸件质量控制计划
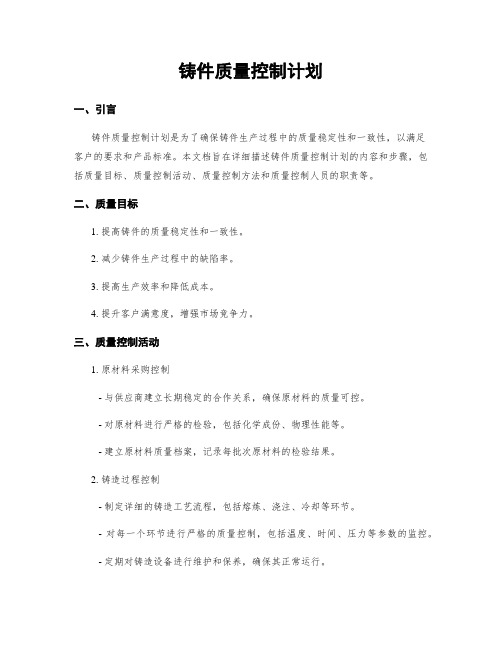
铸件质量控制计划一、引言铸件质量控制计划是为了确保铸件生产过程中的质量稳定性和一致性,以满足客户的要求和产品标准。
本文档旨在详细描述铸件质量控制计划的内容和步骤,包括质量目标、质量控制活动、质量控制方法和质量控制人员的职责等。
二、质量目标1. 提高铸件的质量稳定性和一致性。
2. 减少铸件生产过程中的缺陷率。
3. 提高生产效率和降低成本。
4. 提升客户满意度,增强市场竞争力。
三、质量控制活动1. 原材料采购控制- 与供应商建立长期稳定的合作关系,确保原材料的质量可控。
- 对原材料进行严格的检验,包括化学成份、物理性能等。
- 建立原材料质量档案,记录每批次原材料的检验结果。
2. 铸造过程控制- 制定详细的铸造工艺流程,包括熔炼、浇注、冷却等环节。
- 对每一个环节进行严格的质量控制,包括温度、时间、压力等参数的监控。
- 定期对铸造设备进行维护和保养,确保其正常运行。
3. 检验和测试控制- 制定详细的检验和测试方案,包括外观检查、尺寸测量、力学性能测试等。
- 对每批次铸件进行全面的检验和测试,确保其符合产品标准和客户要求。
- 建立检验和测试记录,保留至少五年的时间。
4. 缺陷分析和改进控制- 对铸件生产过程中的缺陷进行分析,找出根本原因。
- 制定改进措施,防止类似缺陷再次发生。
- 定期评估改进效果,对改进措施进行调整和优化。
四、质量控制方法1. 统计过程控制(SPC)- 通过采集和分析数据,监控铸件生产过程中的关键参数,及时发现和纠正异常。
- 利用控制图和过程能力指数等工具,评估铸件生产过程的稳定性和能力。
2. 全面质量管理(TQM)- 引入全面质量管理理念,将质量控制融入到整个铸件生产过程中。
- 建立质量管理体系,包括质量政策、质量目标、质量手册等。
- 实施质量培训,提高员工的质量意识和技能。
3. 5S管理- 实施5S管理,即整理、整顿、清扫、清洁、素质。
- 维护铸件生产现场的整洁和有序,提高工作效率和质量稳定性。
铸件质量控制计划
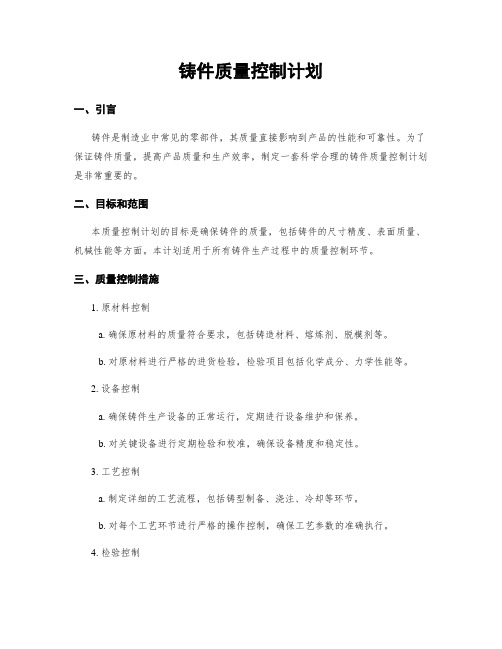
铸件质量控制计划一、引言铸件是制造业中常见的零部件,其质量直接影响到产品的性能和可靠性。
为了保证铸件质量,提高产品质量和生产效率,制定一套科学合理的铸件质量控制计划是非常重要的。
二、目标和范围本质量控制计划的目标是确保铸件的质量,包括铸件的尺寸精度、表面质量、机械性能等方面。
本计划适用于所有铸件生产过程中的质量控制环节。
三、质量控制措施1. 原材料控制a. 确保原材料的质量符合要求,包括铸造材料、熔炼剂、脱模剂等。
b. 对原材料进行严格的进货检验,检验项目包括化学成分、力学性能等。
2. 设备控制a. 确保铸件生产设备的正常运行,定期进行设备维护和保养。
b. 对关键设备进行定期检验和校准,确保设备精度和稳定性。
3. 工艺控制a. 制定详细的工艺流程,包括铸型制备、浇注、冷却等环节。
b. 对每个工艺环节进行严格的操作控制,确保工艺参数的准确执行。
4. 检验控制a. 制定全面的检验计划,包括原材料检验、首件检验、中间检验和最终检验等。
b. 使用先进的检测设备和方法,对铸件进行尺寸、表面质量、力学性能等方面的检验。
5. 过程控制a. 实施全面的过程控制,包括温度控制、浇注速度控制、冷却时间控制等。
b. 对每个工序进行数据采集和分析,及时发现问题并采取纠正措施。
6. 记录和文档控制a. 对每个质量控制环节进行详细的记录,包括原材料批次、工艺参数、检验结果等。
b. 确保文档的完整性和准确性,建立合理的文档管理体系。
四、质量控制指标1. 尺寸精度:铸件尺寸应符合设计要求,允许偏差应在允许范围内。
2. 表面质量:铸件表面应无明显缺陷,如气孔、夹渣、裂纹等。
3. 机械性能:铸件的强度、硬度、韧性等机械性能应符合设计要求。
五、质量控制流程1. 原材料进货检验a. 检验原材料的化学成分和力学性能。
b. 对不合格原材料进行退货或重新检验。
2. 铸件生产过程控制a. 控制铸造工艺参数,确保铸件的质量。
b. 定期对铸造设备进行检验和维护。
铸造生产过程质量控制点
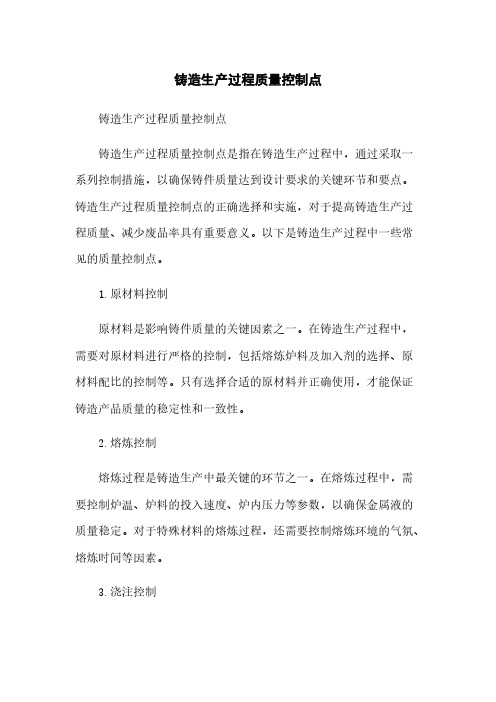
铸造生产过程质量控制点铸造生产过程质量控制点铸造生产过程质量控制点是指在铸造生产过程中,通过采取一系列控制措施,以确保铸件质量达到设计要求的关键环节和要点。
铸造生产过程质量控制点的正确选择和实施,对于提高铸造生产过程质量、减少废品率具有重要意义。
以下是铸造生产过程中一些常见的质量控制点。
1.原材料控制原材料是影响铸件质量的关键因素之一。
在铸造生产过程中,需要对原材料进行严格的控制,包括熔炼炉料及加入剂的选择、原材料配比的控制等。
只有选择合适的原材料并正确使用,才能保证铸造产品质量的稳定性和一致性。
2.熔炼控制熔炼过程是铸造生产中最关键的环节之一。
在熔炼过程中,需要控制炉温、炉料的投入速度、炉内压力等参数,以确保金属液的质量稳定。
对于特殊材料的熔炼过程,还需要控制熔炼环境的气氛、熔炼时间等因素。
3.浇注控制浇注过程是将熔融金属注入到型腔中的过程。
在浇注过程中,需要控制浇注速度、浇注温度、浇注方式等因素,以保证浇注质量和铸件的致密性。
还需要控制浇注过程中金属液的气体排出情况,避免气孔的产生。
4.型腔控制型腔是铸造中形成铸件形状和尺寸的关键部位,对铸件质量有着重要影响。
型腔控制包括型腔设计、制造和维护等环节。
必须确保型腔的准确尺寸和光洁度,避免型腔表面的破损和变形,以确保铸件的形状精度和表面质量。
5.冷却控制冷却过程是铸件从熔融状态到固态过程中的一个关键环节。
在冷却过程中,需要控制冷却速度、冷却介质、冷却时间等因素,以保证铸件组织的均匀性和致密性。
还需要控制冷却过程中的温度梯度,避免铸件产生应力和变形。
6.热处理控制对于某些特殊材料或要求较高的铸件,还需要进行热处理过程。
热处理过程包括加热、保温和冷却等环节。
在热处理过程中,需要控制温度、保温时间、冷却速度等参数,以确保铸件组织的改善和性能的提升。
7.表面处理控制铸件的表面处理是为了提高铸件的表面质量和耐腐蚀性。
表面处理包括喷砂、抛光、电镀等工艺。
在表面处理过程中,需要控制处理剂的使用和浸溶时间,以保证铸件表面的光洁度和处理效果。
铸件质量控制计划
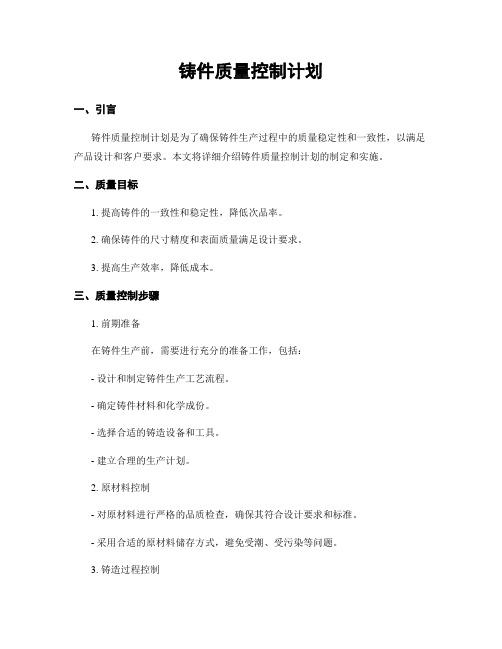
铸件质量控制计划一、引言铸件质量控制计划是为了确保铸件生产过程中的质量稳定性和一致性,以满足产品设计和客户要求。
本文将详细介绍铸件质量控制计划的制定和实施。
二、质量目标1. 提高铸件的一致性和稳定性,降低次品率。
2. 确保铸件的尺寸精度和表面质量满足设计要求。
3. 提高生产效率,降低成本。
三、质量控制步骤1. 前期准备在铸件生产前,需要进行充分的准备工作,包括:- 设计和制定铸件生产工艺流程。
- 确定铸件材料和化学成份。
- 选择合适的铸造设备和工具。
- 建立合理的生产计划。
2. 原材料控制- 对原材料进行严格的品质检查,确保其符合设计要求和标准。
- 采用合适的原材料储存方式,避免受潮、受污染等问题。
3. 铸造过程控制- 控制熔炼温度和时间,确保熔化的金属质量稳定。
- 严格控制铸造温度和速度,避免铸件浮现热裂纹温和孔等缺陷。
- 定期检查和维护铸造设备,确保其正常工作。
4. 后处理控制- 对铸件进行去毛刺、修整等工艺处理,确保其表面光洁度满足要求。
- 对铸件进行热处理、表面处理等工艺,提高其力学性能和耐腐蚀性能。
5. 检验与测试- 对铸件进行尺寸测量,确保其符合设计要求。
- 进行金相组织分析、硬度测试等,评估铸件的物理性能。
- 进行无损检测,发现和排除铸件内部缺陷。
6. 统计与分析- 对生产过程中的关键参数进行统计和分析,及时发现问题并采取措施进行改进。
- 建立合理的数据记录和档案管理系统,便于追溯和分析。
四、质量控制指标1. 尺寸精度:铸件尺寸与设计要求的偏差。
2. 表面质量:铸件表面的粗糙度、气孔、夹渣等缺陷。
3. 机械性能:铸件的强度、硬度等力学性能指标。
4. 化学成份:铸件材料的化学成份是否符合要求。
五、质量控制手段1. 工艺控制:通过控制铸造工艺参数,如温度、速度等,来保证铸件质量。
2. 设备控制:定期检查和维护铸造设备,确保其正常工作。
3. 检验与测试:对铸件进行尺寸测量、金相组织分析、硬度测试等,评估铸件质量。
铸造质量控制

铸造质量控制铸造质量控制是指通过一系列的措施和方法,确保铸造产品在生产过程中达到一定的质量标准。
铸造质量控制的目的是提高铸造产品的质量,减少缺陷率,提高生产效率,降低生产成本。
一、质量控制的前期准备在铸造质量控制的前期准备阶段,需要做好以下工作:1.确定质量标准:根据产品的要求和使用环境,确定铸造产品的质量标准。
包括材料的化学成分、力学性能、尺寸精度、表面质量等指标。
2.确定工艺参数:根据产品的要求和材料的特性,确定适当的工艺参数。
包括熔炼温度、熔炼时间、浇注温度、浇注速度等参数。
3.制定工艺流程:根据产品的要求和工艺参数,制定详细的工艺流程。
包括模具制作、熔炼、浇注、冷却、清理等工艺步骤。
二、质量控制的过程控制在铸造质量控制的过程中,需要进行以下控制措施:1.原材料控制:对原材料进行严格的检验和选择,确保原材料的质量符合要求。
包括金属材料、砂型材料、熔剂等。
2.熔炼控制:控制熔炼的温度、时间和熔炼剂的添加量,确保熔炼的金属合金成分和温度符合要求。
3.浇注控制:控制浇注的温度、速度和浇注口的位置,确保金属液能够充分填充模腔并且不产生气孔和缩孔。
4.冷却控制:控制冷却的速度和方式,确保铸件能够均匀冷却,避免产生应力和变形。
5.清理控制:对铸件进行清理和修整,去除表面的氧化皮、砂粒和毛刺,提高铸件的表面质量。
三、质量控制的检验和测试在铸造质量控制的过程中,需要进行以下检验和测试:1.化学成分分析:对铸件的材料进行化学成分分析,确保合金成分符合要求。
2.力学性能测试:对铸件进行拉伸、冲击、硬度等力学性能测试,确保铸件的强度和韧性符合要求。
3.尺寸精度检验:对铸件的尺寸进行测量和检验,确保尺寸精度符合要求。
4.表面质量检验:对铸件的表面进行检查和评估,确保表面质量符合要求。
5.无损检测:对铸件进行无损检测,如X射线检测、超声波检测等,发现和排除铸件的内部缺陷。
四、质量控制的记录和分析在铸造质量控制的过程中,需要做好记录和分析工作:1.记录工作:对质量控制的各项参数和检验结果进行记录,包括原材料的检验记录、工艺参数的记录、生产过程的记录、检验结果的记录等。
铸造质量管理
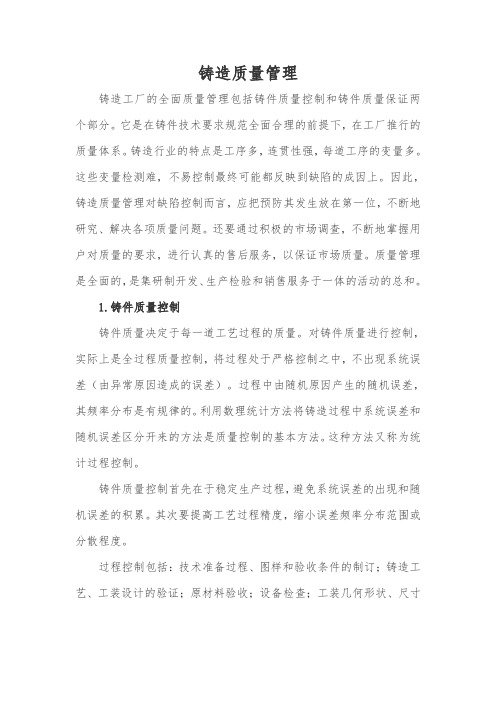
铸造质量管理铸造工厂的全面质量管理包括铸件质量控制和铸件质量保证两个部分。
它是在铸件技术要求规范全面合理的前提下,在工厂推行的质量体系。
铸造行业的特点是工序多,连贯性强,每道工序的变量多。
这些变量检测难,不易控制最终可能都反映到缺陷的成因上。
因此,铸造质量管理对缺陷控制而言,应把预防其发生放在第一位,不断地研究、解决各项质量问题。
还要通过积极的市场调查,不断地掌握用户对质量的要求,进行认真的售后服务,以保证市场质量。
质量管理是全面的,是集研制开发、生产检验和销售服务于一体的活动的总和。
1.铸件质量控制铸件质量决定于每一道工艺过程的质量。
对铸件质量进行控制,实际上是全过程质量控制,将过程处于严格控制之中,不出现系统误差(由异常原因造成的误差)。
过程中由随机原因产生的随机误差,其频率分布是有规律的。
利用数理统计方法将铸造过程中系统误差和随机误差区分开来的方法是质量控制的基本方法。
这种方法又称为统计过程控制。
铸件质量控制首先在于稳定生产过程,避免系统误差的出现和随机误差的积累。
其次要提高工艺过程精度,缩小误差频率分布范围或分散程度。
过程控制包括:技术准备过程、图样和验收条件的制订;铸造工艺、工装设计的验证;原材料验收;设备检查;工装几何形状、尺寸精度和装备关系检查等;另外,还包括熔炼、配砂、造型、制芯等工艺参数的控制。
控制方法是定期对记录工艺参数进行统计分析,判断车间参数误差频率分布及性质,对每一中间工序的结果进行检查。
以铸件车间的铸造工艺过程为例铸铁件生产过程质控站(质量控制站,QC)布置,如图0-1所示。
建立工艺过程质控站是质量管理中行之有效的措施。
质控站能为缺陷分析提供生产过程背景材料以及原始记录和统计资料,凡是对铸件质量特性有重大影响的工序或环节,一般都应设置质控站。
质控站的操作者应严格执行操作规程。
工厂考核铸件质量,按铸件产生缺陷的原因,追究个人或生产小组的责任。
由于铸件产生缺陷的原因是多方面的和复杂的,有些缺陷是由于多个因素引起的,故不容易划分各自应承担责任的百分比。
铸造质量控制

铸造质量控制铸造质量控制是指在铸造过程中对产品质量进行监控和管理,以确保铸件达到特定的质量要求和标准。
本文将详细介绍铸造质量控制的标准格式,包括质量控制目标、质量控制流程、质量控制方法和质量控制指标等方面。
一、质量控制目标铸造质量控制的目标是确保铸件的尺寸精度、化学成分、力学性能等符合设计要求,以提高产品的质量稳定性和可靠性。
具体目标包括:1. 尺寸精度控制:控制铸件的线性尺寸、角度、平面度等,确保满足设计要求。
2. 化学成分控制:控制铸件的化学成分,确保合金成分符合规定的范围。
3. 力学性能控制:控制铸件的硬度、强度、韧性等力学性能,确保满足使用要求。
4. 表面质量控制:控制铸件的表面光洁度、无缺陷、无气孔等,确保产品外观良好。
二、质量控制流程铸造质量控制的流程一般包括原材料检验、铸造工艺控制、铸件检验和铸件整理等环节。
1. 原材料检验:对铸造原材料进行检验,包括合金材料、砂型材料等。
检验项目包括化学成分、机械性能等。
2. 铸造工艺控制:控制铸造过程中的工艺参数,包括熔炼温度、浇注温度、浇注速度等。
确保工艺参数符合设计要求。
3. 铸件检验:对铸件进行尺寸检验、化学成分分析、力学性能测试等,以确保铸件符合质量要求。
4. 铸件整理:对铸件进行修整、除砂、表面处理等工序,以提高铸件的外观质量和尺寸精度。
三、质量控制方法铸造质量控制的方法主要包括可视检查、尺寸测量、化学分析和力学性能测试等。
1. 可视检查:通过目视观察铸件的外观质量,包括表面光洁度、无缺陷等。
2. 尺寸测量:采用测量仪器对铸件的尺寸进行测量,包括长度、宽度、高度等。
3. 化学分析:通过化学分析仪器对铸件的化学成分进行检测,确保合金成分符合要求。
4. 力学性能测试:采用万能试验机等测试设备对铸件进行硬度、强度、韧性等力学性能测试。
四、质量控制指标铸造质量控制的指标根据产品的具体要求和标准而定,常见的指标包括:1. 尺寸精度指标:包括线性尺寸公差、角度公差、平面度等。
铸件质量控制计划
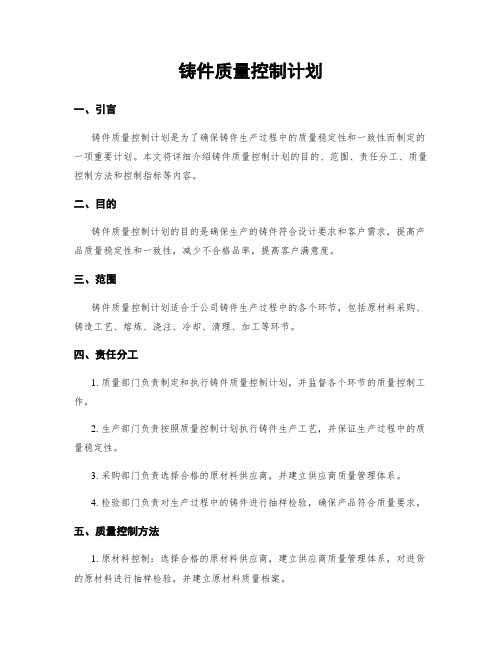
铸件质量控制计划一、引言铸件质量控制计划是为了确保铸件生产过程中的质量稳定性和一致性而制定的一项重要计划。
本文将详细介绍铸件质量控制计划的目的、范围、责任分工、质量控制方法和控制指标等内容。
二、目的铸件质量控制计划的目的是确保生产的铸件符合设计要求和客户需求,提高产品质量稳定性和一致性,减少不合格品率,提高客户满意度。
三、范围铸件质量控制计划适合于公司铸件生产过程中的各个环节,包括原材料采购、铸造工艺、熔炼、浇注、冷却、清理、加工等环节。
四、责任分工1. 质量部门负责制定和执行铸件质量控制计划,并监督各个环节的质量控制工作。
2. 生产部门负责按照质量控制计划执行铸件生产工艺,并保证生产过程中的质量稳定性。
3. 采购部门负责选择合格的原材料供应商,并建立供应商质量管理体系。
4. 检验部门负责对生产过程中的铸件进行抽样检验,确保产品符合质量要求。
五、质量控制方法1. 原材料控制:选择合格的原材料供应商,建立供应商质量管理体系,对进货的原材料进行抽样检验,并建立原材料质量档案。
2. 铸造工艺控制:制定标准的铸造工艺流程,包括熔炼温度、浇注温度、冷却时间等参数的控制,确保铸件的内部组织和外观质量。
3. 检验控制:对生产过程中的铸件进行抽样检验,包括外观检验、尺寸检验、化学成份分析、力学性能测试等,确保产品符合设计要求。
4. 过程控制:建立生产过程中的监控点,对关键工艺参数进行实时监测和记录,及时调整工艺参数,确保产品质量的稳定性。
5. 不合格品处理:对不合格品进行分类、追溯和处理,包括修复、报废、返工等,确保不合格品不流入下道工序或者客户手中。
六、质量控制指标1. 外观质量:包括铸件表面的缺陷、气孔、夹渣等情况,要求无明显缺陷,表面光洁。
2. 尺寸精度:根据设计要求,对铸件的尺寸进行精确测量,确保尺寸误差在允许范围内。
3. 化学成份:根据客户要求和产品标准,对铸件的化学成份进行分析,确保符合要求。
4. 机械性能:对铸件进行拉伸、硬度等机械性能测试,确保产品的强度、韧性等性能符合要求。
铸造简介介绍

铸造简介介绍汇报人:日期:contents•铸造定义和历史•铸造工艺和分类目录•铸造材料和设备•铸造质量控制和检测01铸造定义和历史铸造的定义•铸造定义:铸造是一种通过将熔融的金属或其他材料倒入模具中,待其冷却凝固后形成具有预定形状、尺寸和表面质量的制品的成型工艺。
中世纪铸造中世纪时期,铸造技术进一步发展,出现了许多精美的艺术品和建筑构件,如铸铁雕塑和教堂钟楼。
古代铸造自古以来,人类就利用铸造技术制造各种工具、武器和生活用品。
例如,青铜器时代的铸造工艺就已经相当成熟。
现代铸造随着工业革命的到来,铸造技术迅速现代化,引入了新的设备、材料和工艺,使得铸造制品的精度、强度和耐久性得到显著提高。
铸造的历史发展铸造作为现代制造业的关键成型工艺之一,广泛应用于汽车、机械、航空航天、造船、建筑等领域。
重要成型工艺铸造技术的进步为现代工业的发展提供了有力支持,推动了产品设计、材料科学和制造工艺的创新与改进。
促进工业发展铸造行业在全球范围内创造了巨大的经济价值,提供了大量的就业机会,为社会经济发展做出了重要贡献。
创造经济价值铸造在现代工业中的地位02铸造工艺和分类砂型铸造是一种通过用砂型作为铸模的铸造方法。
定义工艺流程应用范围制作砂型、熔炼金属、浇注金属、冷却、除砂、清理和检验等步骤。
适用于各种大小、形状和复杂度的铸件,尤其对于大批量生产的铸件具有较高的经济性。
030201压力铸造是一种在高压下将熔融金属压入模具的铸造方法。
定义铸件尺寸精度高、表面质量好、生产效率高等。
优点广泛应用于汽车、航空航天、电子产品、家居用品等领域。
应用范围熔模铸造又称失蜡铸造,是一种通过蜡模熔化后形成空腔,再填充熔融金属进行铸造的方法。
定义精度高、设计自由度高、能制造复杂形状铸件等。
工艺特点适用于艺术品、珠宝、高端机械零件、航空航天组件等制造。
应用范围熔模铸造03铸造材料和设备•铸造是一种通过熔化金属或其他材料,并将其倒入模具中来制造物品的方法。
铸造质量控制程序
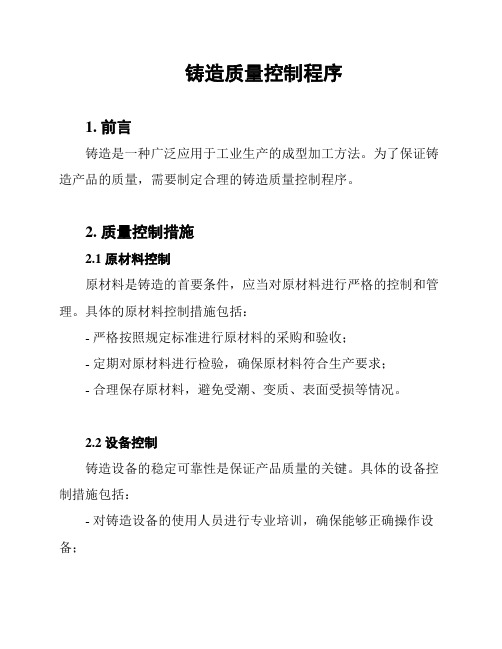
铸造质量控制程序
1. 前言
铸造是一种广泛应用于工业生产的成型加工方法。
为了保证铸造产品的质量,需要制定合理的铸造质量控制程序。
2. 质量控制措施
2.1 原材料控制
原材料是铸造的首要条件,应当对原材料进行严格的控制和管理。
具体的原材料控制措施包括:
- 严格按照规定标准进行原材料的采购和验收;
- 定期对原材料进行检验,确保原材料符合生产要求;
- 合理保存原材料,避免受潮、变质、表面受损等情况。
2.2 设备控制
铸造设备的稳定可靠性是保证产品质量的关键。
具体的设备控制措施包括:
- 对铸造设备的使用人员进行专业培训,确保能够正确操作设备;
- 定期对铸造设备进行检修和保养,确保设备处于良好的工作状态;
- 对铸造设备进行监控,及时发现故障并加以处理。
2.3 工艺控制
铸造工艺的控制直接关系到产品质量。
具体的工艺控制措施包括:
- 制定合理有效的铸造工艺;
- 按照规定程序操作,并严格执行工艺规程;
- 对铸件进行检测,并对有缺陷的铸件进行处理。
3. 质量管理要点
3.1 资源管理
确保足够的资金、设备、人员、物料等资源,为铸造质量的控制和提高奠定基础。
3.2 管理技能
提高管理人员的职业素养和意识,使其在铸造质量控制方面具备强有力的推动作用。
3.3 绩效评估
建立科学的绩效评估制度,对铸造质量的控制和提高进行有效的评估和指导。
4. 结语
铸造质量控制是保证产品质量的重要保障。
只有制定合理有效的铸造质量控制程序,并严格执行,才能生产出优质的铸造产品。
- 1、下载文档前请自行甄别文档内容的完整性,平台不提供额外的编辑、内容补充、找答案等附加服务。
- 2、"仅部分预览"的文档,不可在线预览部分如存在完整性等问题,可反馈申请退款(可完整预览的文档不适用该条件!)。
- 3、如文档侵犯您的权益,请联系客服反馈,我们会尽快为您处理(人工客服工作时间:9:00-18:30)。
铸造简介及大铸件质量控制
1.什么样是铸造:将金属加热熔化后倒入(或压入)模子(砂型或金属型)中,冷却后得到所需形状的物件,此种工艺称为铸造,获得的工件称为铸件。
2.常用的铸造金属材料:
2.1铸铁
1)铸铁是含碳量2%以上的铁碳合金,工业应用的铸铁含碳量一般为2.5%~4%。
除铁以外,铸铁中常存元素有碳、硅、锰、磷、硫。
其中碳是影响铸铁组织和性能的重要因素,硅和锰是调节铸铁组织和性能的有利因素;而磷和硫通常被视为有害杂质,应尽量降低其含量。
一般工程用铸造碳钢
工程与结构用铸钢焊接结构用碳素铸钢
低合金高强度铸钢
抗磨铸钢
铸钢不锈、耐蚀铸钢
耐热铸钢
低温用铸钢
铸造工具钢
其它特种铸钢
2.3铸造非铁合金
2.3.1铸造铜合金
普通黄铜(铜锌合金)如H68,表示含铜量为68%的铜锌合金铸造黄铜特殊黄铜:在铜-锌系的基础上加入铝、锡、镍、锰、铁、硅等铸造铜合金元素
铸造青铜锡青铜(铜锡合金)如QSn10为含锡10%的锡青铜
特种青铜有铝青铜、硅青铜、铍青铜、铅青铜、磷青铜等2.3.2铸造铝合金分为铝-硅系、铝-铜系、铝-镁系和铝-锆系四大类。
3.金属熔炼设备简介:
3.1铸铁熔化设备:冲天炉、感应电炉
3.2铸钢熔炼设备:即炼钢设备包括粗炼和精炼
3.3非铁合金熔化炉:坩锅炉、感应电炉、电弧炉
4.常用铸造方法
砂型铸造:是最常用的铸造方法。
砂型铸造中,又以粘士砂型的使用为
最广。
用粘士砂型生产的铸件约占铸件产量的90%,特别是在
黑色金属的铸造中,应用更为广泛。
铸造方法金属型铸造:适用于批量生产和质量要求高的中、小型铸件
非铁合金铸件
压力铸造:生产效率高,光洁度高,力学性能高,适用于大特种铸造批量、中小型铸件
离心铸造:组织细密,没有浇冒口系统,便于制造双金属铸
件(如复合铸铁轧辊),生产效率较高;容易产生偏析
(比重偏析)
熔模铸造:尺寸精度高,光洁度可达R a6.3~2.5μm,可铸造形状
很复杂的铸件,浇注合金不受限制;过程复杂,周期长,
成本高,尺寸不能太大。
5.砂型铸造简介:
5.1砂型铸造简介:砂型铸造俗称“翻砂”,是用型砂造型的铸造方法。
主要过程为:1)制造模型:①用木材(或其它适用材料)制成与铸件外形基体相同的模型(要加上收缩量和拔模斜度)模型英文叫做Pattern,为了造型方便,模型往往要做成可以分合的两部分或几部分,见图3;
②用木材等材料打造“芯盒”,供制造砂芯或泥芯用。
见图5。
砂芯和泥芯的形状与铸件的内腔形状基本相同。
2)用“芯盒”当模子,制成砂芯或泥芯(Core),见图4。
砂芯或泥芯要有支撑用的芯头,芯子中往往要有钢筋骨架以提高强度。
芯子做好后,要用烘干或其它方法使之硬
化。
3)在砂箱中(大型的在地坑中)用模
型造出铸件的阴模即砂型(Mould),此
工序即为“造型”也叫“翻砂”(Moulding)。
同时要做出容纳芯头的槽(也叫芯头)。
通
常铸一个铸件都要用上下两个或更多的砂
箱。
砂箱中还要做出浇口(Gate)和冒
口(Riser)。
见图6。
(这里介绍的只是是原
理性的,实际上的工艺还要比这复杂一
些)。
4)将砂芯或泥芯下到砂型中(芯头架
在砂型的槽上),上下箱扣在一起。
称为合
箱,见图7。
这时,在砂型和芯子之间的
空间就是将来的铸件以及浇冒口系统。
5)浇注:将熔化的液体金属从浇口浇
入砂型
6)脱箱、落砂和清理:待铸件凝固后(按经验确定的保温时间),将铸件从砂型中取出,叫“脱箱”;清除砂子,叫落砂;去除表面粘砂、毛刺,割去浇冒口叫清理。
7)热处理、机械性能试验、探伤、焊补等。
5.2铸钢件的热处理:
铸钢件特别是大型铸钢件在铸造后都有较大的铸造应力,粗大的铸态金相组织,所以铸钢件一般都要经过热处理来消除应力,调整金相组织,改善机械性能。
铸钢件的热处理方法一般有退火、正火加回火、高温扩散退火、调质以及焊补后的去应力退火;高锰钢等奥氏体铸需要进行水韧处理。
铸铁件以及有色件的热处理请自学
5,3铸钢件的机械性能试块:
铸钢件的机械性能试块有单铸的(U形的、梅花形的),也有附在铸件上的。
重要铸件一般都要求附在铸件上的试块。
在试样缺失时,甚至有在铸件本体上割取试料,然后再将铸件焊补修复的。
试块如何取应按照合同和适用技术条件的规定。
试块应随铸件同炉热处理。
5.4铸钢件的焊补:
砂型铸造的铸钢件的常见缺陷有:粘砂,气孔,夹渣以及裂纹,疏松,缩孔,胀箱等等。
作为监督员,凡是尺寸超差,表面或内部有超标的不连续,均是要进行控制的。
对砂型铸造的大型铸钢件来说,挖除缺陷,焊补修复是一种通用的方法。
即使是马氏体不锈钢(如RCCM M3208)、铬-镍奥氏体铁素体不锈钢(如RCCM M3401)也是如此。
(根据RCCM M3406,冷却剂管道的奥氏体-铁素体不锈钢离心浇铸钢管,不允许焊补。
但在不得不面对时,还可以由供应商向承包商申请,作为例外,在有焊接工艺评定和能进行固溶热处理的基础上个案处理。
)缺陷挖补一般在性能热处理机械性能试验合格后进行,补焊合格后,仅进行消除应力热处理而不再进行性能热处理。
补焊要按补焊工艺(焊材、电参数、温度等)进行,补焊工艺要有补焊工艺评定报告支持。
补焊工人要经考试具有资格才能施焊。
焊材管理要符合相应规程的要求。
首先要将铸件表面清理打磨,去除表面缺陷,满足UT对表面的要求,经UT或RT之后,发现超标缺陷并将其位置、大小及深度记录下来(复杂重要的大铸件要画出缺陷地图),以后就根据此记录进行清除、PT或MT、焊补和检查。
清除、PT或MT、焊补和检查有可能反复进行,直到合格为止(见下面的流程图)。
6.大型重要铸钢件的质量控制——以某汽轮机缸体为例
6.1工艺流程
300MW汽轮机中压外缸制造工艺流程
造型1.高的尺寸精度,表面光滑的木质整体模型
2.铬铁矿自硬砂,喷涂锆英粉涂料,确保光滑的砂型表面
炼钢
钢包精炼炉(LF)精炼,确保钢水低P,S和钢水的纯净度,调整化学成分
附件1.化学成分和机械性能
表1 化学成分(%)
表2 机械性能(室温) 注 1.*系三个试样的平均值,其中一根试样允许最小值≥24J,其余试样高于平均值. 2.延伸率×抗
拉强度≥10500. 3.围绕铸件,按一定的间距打硬度(5吨以上铸件至少打5点)
附件2.高压外缸热处理工艺
℃
均匀化(软化)处理 ℃
调质(性能热处理)
附件3。
中压外缸取样及敷偶位置图
6.2质量计划
中压外缸上半质量计划概略
……………………………………………………………最新资料推荐…………………………………………………
最新精品资料整理推荐,更新于二〇二一年一月二十七日2021年1月27日星期三20:47:59。