模具设计计算公式
冲压件模具设计常用公式

冲压件模具设计常用公式1. 材料和工艺参数计算公式1.1 冲击力的计算公式冲击力是冲压件模具设计中重要的参考指标之一,它可以用于确定模具的强度和稳定性。
冲击力的计算公式如下:F = K × A × T × σ其中,F表示冲击力,K表示冲击系数,A表示冲压件的有效面积,T表示冲压时间,σ表示材料的抗拉强度。
1.2 冲床力的计算公式冲床力是指冲床在冲压过程中对工件所产生的压力。
冲床力的计算公式如下:P = F / A其中,P表示冲床力,F表示冲击力,A表示冲压件的有效面积。
1.3 冲压时间的计算公式冲压时间是指冲床一次冲压周期所需的时间。
冲压时间的计算公式如下:T = (L / V) + t其中,T表示冲压时间,L表示冲压件的长度,V表示冲床的下行速度,t表示冲程停留时间。
1.4 最大冲床力的计算公式最大冲床力是指冲床所能承受的最大压力。
最大冲床力的计算公式如下:P_max = K × A × σ其中,P_max表示最大冲床力,K表示冲击系数,A表示冲压件的有效面积,σ表示材料的抗拉强度。
2. 模具结构设计公式2.1 模具剪切强度的计算公式模具剪切强度是指模具在剪切过程中所能承受的最大剪切力。
模具剪切强度的计算公式如下:P_shear = F / A_shear其中,P_shear表示模具剪切强度,F表示冲击力,A_shear表示模具剪切面积。
2.2 模具挤压强度的计算公式模具挤压强度是指模具在挤压过程中所能承受的最大挤压力。
模具挤压强度的计算公式如下:P_extrusion = F / A_extrusion其中,P_extrusion表示模具挤压强度,F表示冲击力,A_extrusion表示模具挤压面积。
2.3 模具弯曲强度的计算公式模具弯曲强度是指模具在弯曲过程中所能承受的最大弯曲力。
模具弯曲强度的计算公式如下:P_bending = F / A_bending其中,P_bending表示模具弯曲强度,F表示冲击力,A_bending表示模具弯曲面积。
冲压件模具设计常用公式

冲压件模具设计常用公式1. 冲裁力计算公式冲裁力是模具在冲裁过程中对工件施加的力的大小,可以使用以下公式进行计算:$$ P = K \\cdot T \\cdot L \\cdot S $$其中: - P 是冲裁力〔单位:N〕 - K 是系数〔根据材料和冲裁方式进行选择〕 - T 是材料的厚度〔单位:mm〕 - L 是冲裁长度〔单位:mm〕 - S 是材料强度的保险系数2. 冲孔力计算公式冲孔是冲压件模具中常见的一个工序,为了计算冲孔力,可以使用以下公式:$$ F = K \\cdot T \\cdot L \\cdot S $$其中: - F 是冲孔力〔单位:N〕 - K 是系数〔根据材料和冲孔方式进行选择〕 - T 是材料的厚度〔单位:mm〕 - L 是冲孔孔径〔单位:mm〕 - S 是材料强度的保险系数3. 模具开孔面积计算公式在冲压件模具设计中,开孔面积对模具的设计和选择起着重要的作用。
开孔面积可以通过以下公式计算:$$ A = L \\cdot W $$其中: - A 是开孔面积〔单位:mm²〕 - L 是模具的长度〔单位:mm〕 - W 是模具的宽度〔单位:mm〕4. 模具强度计算公式模具强度的计算是冲压件模具设计中的关键步骤之一。
可以使用以下公式计算模具的强度:$$ P_t = P \\cdot S_f $$其中: - P_t 是模具的强度〔单位:N〕 - P 是冲裁力或冲孔力〔单位:N〕 - S_f 是平安系数5. 模具寿命计算公式模具寿命的计算是冲压件模具设计过程中需要关注的一个重要指标。
可以使用以下公式计算模具寿命:$$ N_m = \\frac{S_m}{f \\cdot V_c} $$其中: - N_m 是模具的使用寿命〔单位:次〕 - S_m 是模具材料的疲劳强度〔单位:MPa〕 - f 是载荷系数 - V_c 是模具的速度〔单位:m/s〕6. 模具热应力计算公式模具在使用过程中会受到热应力的影响,为了进行热应力的计算,可以使用以下公式:$$ \\sigma = \\frac{Q}{A} $$其中: - σ 是热应力〔单位:MPa〕 - Q 是热量〔单位:J〕 - A 是模具横截面积〔单位:mm²〕7. 模具变形计算公式模具在使用过程中会发生一定的变形,为了进行变形的计算,可以使用以下公式:$$ \\delta = \\frac{{F \\cdot L}}{{E \\cdot A}} $$其中: - δ 是变形量〔单位:mm〕- F 是施加在模具上的力〔单位:N〕 - L 是模具的长度〔单位:mm〕 - E 是弹性模量〔单位:MPa〕 - A 是模具的截面积〔单位:mm²〕总结在冲压件模具设计过程中,常用的公式可以帮助工程师快速准确地进行相关计算,从而确保模具的性能和可靠性。
模具设计计算公式
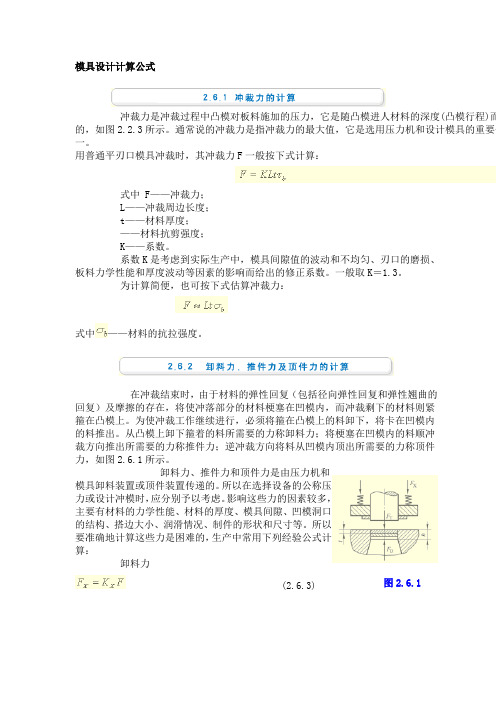
模具设计计算公式冲裁力是冲裁过程中凸模对板料施加的压力,它是随凸模进人材料的深度(凸模行程)而变化的,如图2.2.3所示。
通常说的冲裁力是指冲裁力的最大值,它是选用压力机和设计模具的重要依据之一。
用普通平刃口模具冲裁时,其冲裁力F一般按下式计算:式中 F——冲裁力;L——冲裁周边长度;t——材料厚度;——材料抗剪强度;K——系数。
系数K是考虑到实际生产中,模具间隙值的波动和不均匀、刃口的磨损、板料力学性能和厚度波动等因素的影响而给出的修正系数。
一般取K=1.3。
为计算简便,也可按下式估算冲裁力:(2.6.2) 式中——材料的抗拉强度。
在冲裁结束时,由于材料的弹性回复(包括径向弹性回复和弹性翘曲的回复)及摩擦的存在,将使冲落部分的材料梗塞在凹模内,而冲裁剩下的材料则紧箍在凸模上。
为使冲裁工作继续进行,必须将箍在凸模上的料卸下,将卡在凹模内的料推出。
从凸模上卸下箍着的料所需要的力称卸料力;将梗塞在凹模内的料顺冲裁方向推出所需要的力称推件力;逆冲裁方向将料从凹模内顶出所需要的力称顶件力,如图2.6.1所示。
卸料力、推件力和顶件力是由压力机和模具卸料装置或顶件装置传递的。
所以在选择设备的公称压力或设计冲模时,应分别予以考虑。
影响这些力的因素较多,主要有材料的力学性能、材料的厚度、模具间隙、凹模洞口的结构、搭边大小、润滑情况、制件的形状和尺寸等。
所以要准确地计算这些力是困难的,生产中常用下列经验公式计算:卸料力 (2.6.3)图2.6.1推件力 (2.6.4)顶件力 (2.6.5)式中 F——冲裁力;图2.6.1 卸料力推件力和顶件力——卸料力、推件力、顶件力系数,见表2.6.1;n——同时卡在凹模内的冲裁件(或废料)数。
式中 h——凹模洞口的直刃壁高度;t——板料厚度。
注:卸料力系数Kx,在冲多孔、大搭边和轮廓复杂制件时取上限值。
压力机的公称压力必须大于或等于各种冲压工艺力的总和Fz。
Fz的计算应根据不同的模具结构分别对待,即采用弹性卸料装置和下出料方式的冲裁模时(2.6.6)采用弹性卸料装置和上出料方式的冲裁模时(2.6.7)采用刚性卸料装置和下出料方式的冲裁模时(2.6.8)为实现小设备冲裁大工件,或使冲裁过程平稳以减少压力机振动,常用下列方法来降低冲裁力。
冲压件模具设计的常用公式

冲压件模具设计的常用公式
一、材料力学公式
1.应力公式:σ=F/A,其中σ为应力,F为受力,A为受力面积。
2.应力应变关系公式:σ=E×ε,其中E为杨氏模量,ε为应变。
3.屈服强度公式:σs=F/A0,其中σs为屈服强度,F为屈服点所受力,A0为初始横截面积。
二、材料成形公式
1. 塑性变形公式:ε = ln (h0 / hn) ,其中ε为塑性变形,h0为初始厚度,hn为最终厚度。
2.变形力公式:F=S×σs,其中F为变形力,S为变形面积,σs为屈服强度。
3.针对特定形状的材料成形公式,如直冲材料成形公式、弯曲材料成形公式等。
三、模具设计公式
1.强度计算公式:F=σ×A,其中F为受力,σ为应力,A为受力面积。
2. 弯曲应力公式:σ = M / (W × yc),其中σ为弯曲应力,M为弯矩,W为截面模量,yc为弯曲轴心距离。
四、装配公式
1.装配公差公式:A=A1+A2+A3,其中A为总公差,A1为尺寸公差,
A2为形位公差,A3为相对公差。
五、切削力公式
1. 切削功率公式:P = F × V × kc,其中P为切削功率,F为切
削力,V为切削速度,kc为切削功率系数。
以上是冲压件模具设计中的常用公式,通过这些公式的运用,可以对
冲压件进行力学、成形、模具设计、装配以及切削力等方面的优化和设计。
当然,具体的设计中还需要根据实际情况和不同材料的特性来选择合适的
公式。
模具设计计算公式
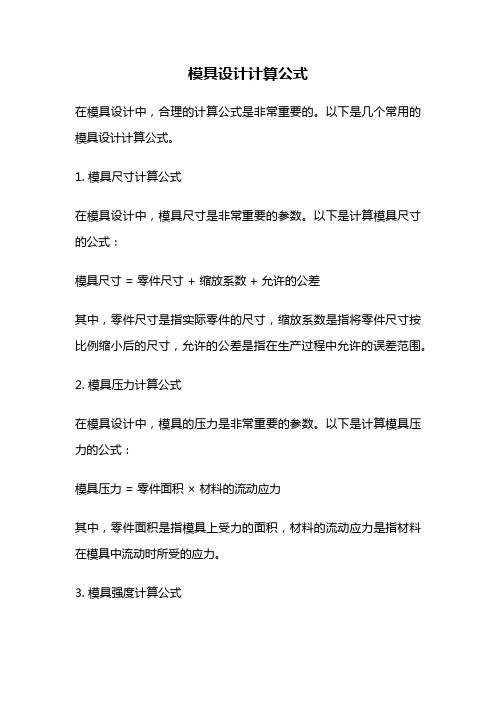
模具设计计算公式
在模具设计中,合理的计算公式是非常重要的。
以下是几个常用的模具设计计算公式。
1. 模具尺寸计算公式
在模具设计中,模具尺寸是非常重要的参数。
以下是计算模具尺寸的公式:
模具尺寸 = 零件尺寸 + 缩放系数 + 允许的公差
其中,零件尺寸是指实际零件的尺寸,缩放系数是指将零件尺寸按比例缩小后的尺寸,允许的公差是指在生产过程中允许的误差范围。
2. 模具压力计算公式
在模具设计中,模具的压力是非常重要的参数。
以下是计算模具压力的公式:
模具压力 = 零件面积× 材料的流动应力
其中,零件面积是指模具上受力的面积,材料的流动应力是指材料在模具中流动时所受的应力。
3. 模具强度计算公式
在模具设计中,模具的强度是非常重要的参数。
以下是计算模具强度的公式:
模具强度 = 材料的屈服强度× 模具截面面积
其中,材料的屈服强度是指材料在承受一定应力后开始产生塑性变形的应力值,模具截面面积是指模具在受力方向上的横截面积。
4. 模具温度计算公式
在模具设计中,模具的温度是非常重要的参数。
以下是计算模具温度的公式:
模具温度 = 热流量× 模具材料的热传导系数× 模具厚度
其中,热流量是指单位时间内通过模具表面的热量,模具材料的热传导系数是指材料传递热量的能力,模具厚度是指模具在受热方向上的厚度。
总结
以上是几个常用的模具设计计算公式。
在模具设计中,计算公式的正确性和合理性对于模具的质量和生产效率都非常重要。
因此,设计人员应该熟练掌握这些计算公式,以便更好地完成模具的设计工作。
冲压件模具设计常用公式

冲压件模具设计常用公式一、前言冲压件模具设计是冲压加工实现自动化、高效生产的关键环节,冲压件模具设计的好坏直接影响冲压品质和生产效益。
因此,在冲压件模具设计过程中,必须掌握一些常用公式,以便在实践中更加精准地解决模具设计中的各种问题。
本文将围绕冲压件模具设计常用公式进行阐述,以期为读者提供一些实用、有效的模具设计知识和技巧。
二、冲压件模具设计常用公式分类1. 材料折弯空间S材料折弯空间S是指冲压时材料在弯曲过程中被拉长的长度,用于计算按照弯缘角度和弯曲半径计算成品长度。
公式如下:S=K*L*(180°-2α)/π 式中,L是材料长度,α是折弯角度,K 是常数,其值根据材料厚度和折弯角度而定。
2. 冲压件毛坯重量M冲压件毛坯重量M是指冲压件在未经加工之前的重量,用于计算材料消耗。
公式如下:M=ρ*L*w*t 式中,ρ是材料密度,L是边长,w是厚度,t 是数量。
3. 模具壁厚t模具壁厚t是指冲压件模具中金属材料的厚度,包括上、下、左、右四个方向的壁厚,一般与压力有关。
可按照最小切削层厚度取值,公式如下:t=K*H/24 式中,K是常数,一般为6~10,H是加工硬度。
4. 补料长度L补料长度L是指冲压件模具中需要加上的余量,保证成品尺寸精度和质量,公式如下:L=αt/K 式中,α是成品弯缘角度,t是壁厚,K是常数,一般为4~6。
5. 小孔冲孔孔距P小孔冲孔孔距P是指在被加工材料上,两相邻的小孔冲或冲孔之间的距离,用于计算模具孔距间距。
公式如下:P=p*t 式中,p是小孔冲孔孔距系数,t是壁厚。
6. 冲模的直径D冲模的直径D是指用以冲剪及压穿时所用的模具直径大小,用于计算冲模的耐用程度。
公式如下:D=0.7√t 式中,t是最薄材料厚度。
7. 冲孔直径d冲孔直径d是指冲剪和冲孔过程中冲头的直径大小,直接影响冲穿质量和模具的使用寿命。
公式如下:d=0.9√H 式中,H是加工硬度。
三、总结本文从材料折弯空间S、冲压件毛坯重量M、模具壁厚t、补料长度L、小孔冲孔孔距P、冲模的直径D和冲孔直径d等七个方面介绍了冲压件模具设计常用公式,并为读者提供了详细的公式计算方法和实用技巧。
模具面积计算重量计算公式
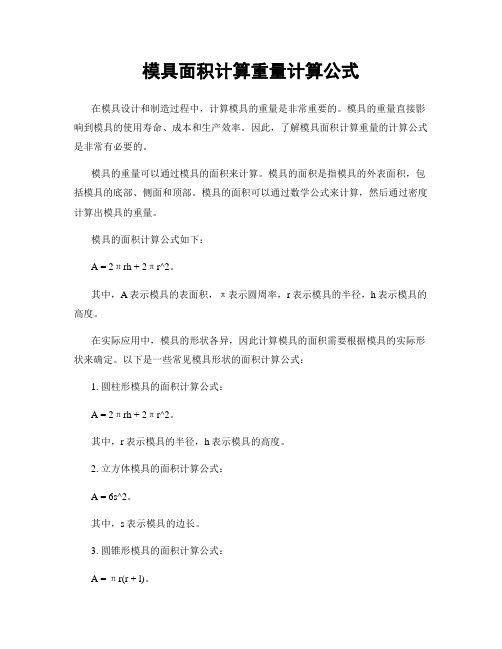
模具面积计算重量计算公式在模具设计和制造过程中,计算模具的重量是非常重要的。
模具的重量直接影响到模具的使用寿命、成本和生产效率。
因此,了解模具面积计算重量的计算公式是非常有必要的。
模具的重量可以通过模具的面积来计算。
模具的面积是指模具的外表面积,包括模具的底部、侧面和顶部。
模具的面积可以通过数学公式来计算,然后通过密度计算出模具的重量。
模具的面积计算公式如下:A = 2πrh + 2πr^2。
其中,A表示模具的表面积,π表示圆周率,r表示模具的半径,h表示模具的高度。
在实际应用中,模具的形状各异,因此计算模具的面积需要根据模具的实际形状来确定。
以下是一些常见模具形状的面积计算公式:1. 圆柱形模具的面积计算公式:A = 2πrh + 2πr^2。
其中,r表示模具的半径,h表示模具的高度。
2. 立方体模具的面积计算公式:A = 6s^2。
其中,s表示模具的边长。
3. 圆锥形模具的面积计算公式:A = πr(r + l)。
其中,r表示模具的底部半径,l表示模具的斜高。
通过以上公式,可以计算出模具的表面积。
一旦得到了模具的表面积,就可以通过模具的密度来计算模具的重量。
模具的密度一般是通过材料的密度来确定。
不同的模具材料有不同的密度,因此需要根据实际情况来确定模具的密度。
一般来说,模具的密度可以通过以下公式来计算:ρ = m/V。
其中,ρ表示模具的密度,m表示模具的质量,V表示模具的体积。
通过上述公式,可以计算出模具的密度。
然后,通过模具的面积和密度,就可以计算出模具的重量:W = ρA。
其中,W表示模具的重量,ρ表示模具的密度,A表示模具的表面积。
通过以上公式,可以很容易地计算出模具的重量。
这对于模具的设计和制造非常重要。
知道模具的重量可以帮助设计师选择合适的材料和结构,从而提高模具的使用寿命和生产效率。
此外,计算模具的重量还可以帮助制造商合理安排生产流程,提高生产效率。
知道模具的重量可以帮助制造商选择合适的设备和工艺,从而提高生产效率和降低成本。
模具设计计算公式

模具设计计算公式介绍如下:
1.模具尺寸计算公式
•模具长度L = 零件长度+ 拉料量+ 压头高度+ 开料量+ 模板厚度
•模具宽度W = 零件宽度 + 拉料量 + 压头宽度 + 开料量 + 2 x 壁厚
•模具高度H = 零件高度 + 拉料量 + 压头高度 + 开料量 + 2 x 壁厚
2.模具压力计算公式
•模具最大压力Fmax = (K x A x S x T) + (K x B x S x T) 其中,K为系数,A为零件的侧面积,B为零件的底面积,S为
材料抗拉强度,T为材料的厚度。
3.模具材料选择公式
•模具材料的选择应考虑到模具的使用寿命、成本、加工性能等因素。
一般来说,模具材料应具有高强度、高硬度、高韧性、
良好的热导性和耐磨性等特点。
常用的模具材料有工具钢、合
金钢、硬质合金等。
4.模具加工工艺公式
•模具加工过程中需要进行多项计算,如切削速度、进给速度、切削深度、切削力等。
这些参数的计算公式与加工工艺有关,
可根据具体情况进行选择和调整。
以上是一些常用的模具设计公式,但具体情况仍需根据实际情况进行
选择和调整。
在实际模具设计过程中,还需要考虑到多个因素的综合作用,如模具的结构、零件的形状和尺寸、生产批量等。
压铸模具设计公式试算REVA
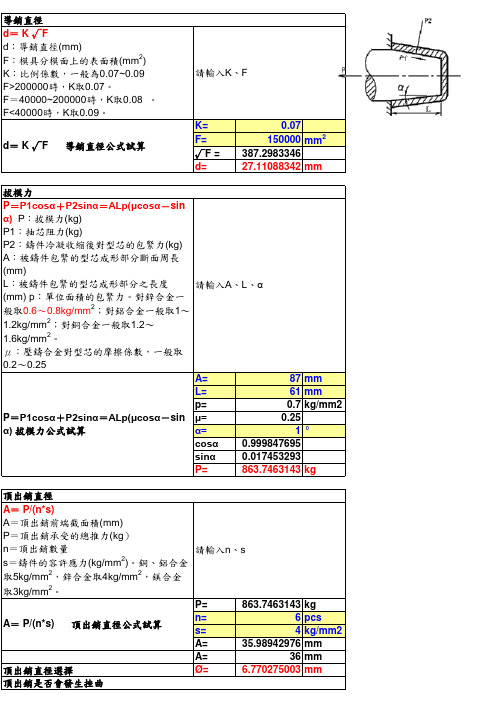
d = K √Fd :導銷直徑(mm)F :模具分模面上的表面積(mm 2)K :比例係數,一般為0.07~0.09F>200000時,K 取0.07。
F =40000~200000時,K 取0.08 。
F<40000時,K 取0.09。
K=0.07F=150000mm 2√F =387.2983346d=27.11088342mmP =P1cosα+P2sinα=ALp(μcosα-sin α) P :拔模力(kg)P1:抽芯阻力(kg)P2:鑄件冷凝收縮後對型芯的包緊力(kg)A :被鑄件包緊的型芯成形部分斷面周長(mm)L :被鑄件包緊的型芯成形部分之長度(mm) p :單位面積的包緊力。
對鋅合金一般取0.6~0.8kg/mm 2;對鋁合金一般取1~1.2kg/mm 2;對銅合金一般取1.2~1.6kg/mm 2。
μ:壓鑄合金對型芯的摩擦係數,一般取0.2~0.25A=87mm L=61mmp=0.7kg/mm2μ=0.25α=1°cosα0.999847695sinα0.017453293P=863.7463143kgA = P/(n*s)A =頂出銷前端截面積(mm)P =頂出銷承受的總推力(kg )n =頂出銷數量s =鑄件的容許應力(kg/mm 2)。
銅、鋁合金取5kg/mm 2,鋅合金取4kg/mm 2,鎂合金取3kg/mm 2。
P=863.7463143kg n=6pcss=4kg/mm2A=35.98942976mm A=36mm 頂出銷直徑選擇Ø= 6.770275003mmP =P1cosα+P2sinα=ALp(μcosα-sin α) 拔模力公式試算請輸入n 、sA = P/(n*s) 頂出銷直徑公式試算頂出銷是否會發生挫曲頂出銷直徑d = K √F 導銷直徑公式試算請輸入K 、F導銷直徑請輸入A 、L 、α拔模力K =n*E*I/(P*L 2)K :穩定安全係數,鋼取1.5~3n :穩定係數,其值取20.19E :楊氏模數,鋼取2x106(kg/cm 2)I :頂出銷最小截面積處之慣性矩(cm 4),對於圓形截面I =лd 4/64(d =頂出銷直徑)P :頂出銷承受之實際推力(kg)n=20.19E=2000000kg/cm 2d=1cm I=0.049087385cm 4P=863.7463143kg L=15cm L 2=225cmK=10.19923241K=1.5~3直徑核可角銷直徑d =(P*h/(3Cosα21/3d :角銷直徑(mm)h :滑塊端面至受力點的垂直距離(mm)P :拔模力(kg)Q :角銷承受的最大彎曲力(kg)P=863.7463143kg h=40mm α15°cosα0.965925826cosα20.933012702d=23.11066608mm 角銷直徑選擇Ø24mm結論請輸入h ,αd =(P*h/(3Cosα21/3角銷直徑公式試算請輸入d 、lK =n*E*I/(P*L 2) 頂針挫曲公式試算。
模具费用的计算方法

模具费用的计算方法:1.经验计算法模具价格=材料费+设计费+加工费与利润+增值税+试模费+包装运输费各项比例通常为:材料费:材料及标准件占模具总费用的15%-30%;加工费与利润:30%-50%;设计费:模具总费用的10%-15%;试模:大中型模具可控制在3%以内,小型精密模具控制在5%以内;包装运输费:可按实际计算或按3%计;增值税:17%2.材料系数法根据模具尺寸和材料价格可计算出模具材料费.模具价格=(6~10)*材料费锻模,塑料模=6*材料费压铸模=10*材料费模具报价估计1、首先要看客户的要求,因为要求决定材料的选择以及热处理工艺。
2、选择好材料,出一个粗略的模具方案图,从中算出模具的重量(计算出模芯材料和模架材料的价格)和热处理需要的费用。
(都是毛胚重量)3、加工费用,根据模芯的复杂程度,加工费用一般和模芯材料价格是1.5~3:1,模架的加工费用一般是1:1。
4、风险费用是以上总价的10%。
5、税()6、设计费用是模具总价的10%。
∙∙模具的报价策略和结算方式模具的报价与结算是模具估价后的延续和结果。
从模具的估价到模具的报价,只是第一步,而模具的最终目的,是通过模具制造交付使用后的结算,形成最终模具的结算价。
在这个过程里,人们总是希望,模具估价=模具价格=模具结算价。
而在实际操作中,这四个价并不完全相等,有可能出现波动误差值。
这就是以下所要讨论的问题。
当模具估价后,需要进行适当处理,整理成模具的报价,为签定模具加工合同做依据。
通过反复洽谈商讨,最后形成双方均认可的模具价格,签订了合同。
才能正式开始模具的加工。
一、模具估价与报价、报价与模具价格模具估价后,并不能马上直接作为报价。
一般说来,还要根据市场行情、客户心理、竞争对手、状态等因素进行综合分析,对估价进行适当的整理,在估价的基础上增加10-30%提出第一次报价。
经过讨价还价,可根据实际情况调低报价。
但是,当模具的商讨报价低于估价的10%时,需重新对模具进行改进细化估算,在保证保本有利的情况下,签订模具加工合同,最后确定模具价格。
冲压件模具设计的常用公式

冲压件模具设计的常用公式随着现代工业的发展,冲压件的应用越来越广泛,从家电到汽车、航空航天等领域都离不开冲压件的制造。
而冲压件的制造离不开模具的设计和制造。
在冲压件模具设计中,使用一些公式能够更好的指导设计过程,提高模具设计的效率和准确性。
本文将介绍一些冲压件模具设计中的常用公式。
1.冲压件的扁平公式在冲压件的设计中,往往需要先根据产品的图纸计算出其扁平尺寸。
用于判断冲压件的设计尺寸是否合理。
冲压件的扁平公式为:S=π(D+d)/2×√((D-d)/2)×F其中,S表示冲压件的扁平尺寸,D和d分别为模具的上模和下模的直径,F为强度系数。
2.模具的强度公式在冲压过程中,模具需要承受很大的压力和撞击力,因此模具的强度是非常重要的。
冲压件模具的强度公式为:σ= (K×(F×L))/((a-b)×b)其中,σ为应力,K为强度试验样本的应力系数,F为金属材料的屈服极限,L为冲压件的长度,a和b分别为上模和下模的外径。
3.折弯件的受载公式在冲压件的制造中,折弯件的制作也是非常重要的一个过程。
折弯件的受载公式为:M=W×L/2×sinα×t^2其中,M为折弯件的扭矩,W为载荷,L为支撑距离,α为折弯角度,t为材料的厚度。
4.齿轮的模数公式在冲压齿轮的设计中,需要根据参数计算出齿轮的模数。
齿轮的模数公式为:m=D/Z其中,m为模数,D为齿轮的直径,Z为齿轮的齿数。
5.模具内角的计算公式在冲压件模具的设计中,模具内角的大小和形状是非常重要的。
模具内角的计算公式为:Ψ=2arctan(0.5B/L)其中,Ψ为内角,B为压头直径(冷模),压头直径补偿(热模),L为模具凸部的长度。
以上就是冲压件模具设计中的一些常用公式。
通过使用这些公式,能够更好地指导冲压件模具的设计,提高冲压件的生产效率和质量。
模具简单计算公式是什么
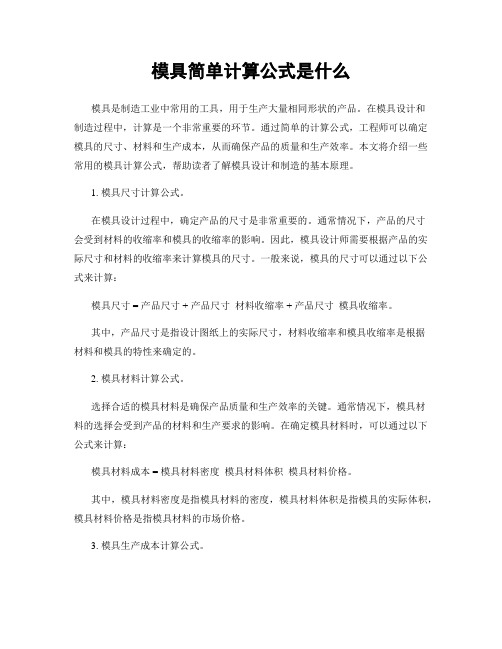
模具简单计算公式是什么模具是制造工业中常用的工具,用于生产大量相同形状的产品。
在模具设计和制造过程中,计算是一个非常重要的环节。
通过简单的计算公式,工程师可以确定模具的尺寸、材料和生产成本,从而确保产品的质量和生产效率。
本文将介绍一些常用的模具计算公式,帮助读者了解模具设计和制造的基本原理。
1. 模具尺寸计算公式。
在模具设计过程中,确定产品的尺寸是非常重要的。
通常情况下,产品的尺寸会受到材料的收缩率和模具的收缩率的影响。
因此,模具设计师需要根据产品的实际尺寸和材料的收缩率来计算模具的尺寸。
一般来说,模具的尺寸可以通过以下公式来计算:模具尺寸 = 产品尺寸 + 产品尺寸材料收缩率 + 产品尺寸模具收缩率。
其中,产品尺寸是指设计图纸上的实际尺寸,材料收缩率和模具收缩率是根据材料和模具的特性来确定的。
2. 模具材料计算公式。
选择合适的模具材料是确保产品质量和生产效率的关键。
通常情况下,模具材料的选择会受到产品的材料和生产要求的影响。
在确定模具材料时,可以通过以下公式来计算:模具材料成本 = 模具材料密度模具材料体积模具材料价格。
其中,模具材料密度是指模具材料的密度,模具材料体积是指模具的实际体积,模具材料价格是指模具材料的市场价格。
3. 模具生产成本计算公式。
确定模具的生产成本是制造企业的重要任务之一。
通常情况下,模具的生产成本会受到材料成本、加工成本和人工成本的影响。
在计算模具的生产成本时,可以通过以下公式来计算:模具生产成本 = 模具材料成本 + 模具加工成本 + 模具人工成本。
其中,模具材料成本是指模具材料的成本,模具加工成本是指模具的加工费用,模具人工成本是指模具的制造人工费用。
通过以上的简单计算公式,工程师可以快速准确地计算模具的尺寸、材料和生产成本,从而为模具设计和制造提供了重要的参考依据。
同时,这些公式也可以帮助企业降低生产成本,提高生产效率,提升产品质量。
因此,掌握模具计算公式是非常重要的,可以为制造企业带来巨大的经济效益。
模具费和加工费计算方法

模具费和加工费计算方法一、模具费计算方法:模具费是指制造模具所需的费用,通常包括模具设计费、制造费和试模费等三个方面。
1.模具设计费:指设计师完成模具产品的设计所需的费用。
模具设计费的计算一般根据设计工时和设计师的工资水平来确定。
具体计算方式可以采用以下公式:模具设计费用=设计师工资*设计工时2.制造费:指制造模具所需的原材料成本和制造工人的工资等费用。
制造费的计算比较复杂,涉及到模具的复杂程度、规模和材料等因素。
一般来说,制造费可以按照以下方式计算:制造费用=模具材料费+模具加工费+模具组装费+模具试模费3.试模费:指模具制造完成后进行试模的费用,包括试模设备的费用和试模工人的工资等。
试模费的计算方法也比较灵活,可以根据试模时间、试模设备和试模工人的工资来确定。
一般来说,试模费用可以采用以下公式计算:试模费用=试模设备费用+试模工人工资二、加工费计算方法:加工费是指产品在加工过程中所产生的费用,主要包括人工费、材料费和设备费等。
加工费的计算可以根据产品的设计、加工工序和材料耗费等因素来确定。
1.人工费:指产品在加工过程中所需的人工工资。
人工费的计算一般可以按照工序的复杂程度、工人数量和工资水平等因素来确定。
一般来说,人工费可以采用以下公式计算:人工费用=总工资*加工工时2.材料费:指产品在加工过程中所使用的原材料的费用。
材料费的计算可以根据产品的设计要求和加工工序来确定。
一般来说,材料费可以按照以下公式计算:材料费用=单位材料成本*加工数量3.设备费:指产品加工过程中所使用的设备的折旧费用。
设备费的计算可以根据设备的购买成本、使用年限和折旧率等因素来确定。
一般来说,设备费可以按照以下公式计算:设备费用=设备购买成本*(1-折旧率)^使用年限综上所述,模具费和加工费是制造业中常用的两个费用指标,其计算方法主要涉及到模具设计费、制造费、试模费、人工费、材料费和设备费等方面。
这些费用的计算需要结合产品的设计要求、加工工序、材料成本和设备折旧等因素进行综合考虑,以便更准确地计算出模具费和加工费。
模具斜顶底座长度计算公式

模具斜顶底座长度计算公式模具设计是制造业中非常重要的一环,而模具斜顶底座长度的计算是模具设计中的一个关键步骤。
模具斜顶底座长度的准确计算可以保证模具的精度和稳定性,从而保证产品的质量。
本文将介绍模具斜顶底座长度的计算公式及其应用。
模具斜顶底座长度的计算公式通常是根据模具的具体形状和尺寸来确定的。
一般来说,模具的斜顶底座长度是由模具的底座长度、斜顶角度和模具的高度来决定的。
下面我们将介绍一些常见的模具斜顶底座长度计算公式。
首先,我们来看一下模具底座长度的计算公式。
模具底座长度通常是根据模具的尺寸和形状来确定的,一般来说,模具的底座长度可以通过以下公式来计算:底座长度 = 模具长度 + 斜顶高度 tan(斜顶角度)。
其中,模具长度是指模具的实际长度,斜顶高度是指模具斜顶的高度,斜顶角度是指模具斜顶的角度。
通过这个公式,我们可以计算出模具的底座长度。
接下来,我们来看一下模具斜顶底座长度的计算公式。
模具斜顶底座长度通常是由模具的底座长度和斜顶角度来决定的,一般来说,模具的斜顶底座长度可以通过以下公式来计算:斜顶底座长度 = 底座长度 / cos(斜顶角度)。
通过这个公式,我们可以计算出模具的斜顶底座长度。
这个公式的核心是利用了三角函数的性质,通过斜顶角度的余弦值来计算斜顶底座长度,从而保证了模具的稳定性和精度。
模具斜顶底座长度的计算公式在模具设计和制造中具有非常重要的应用价值。
通过这个公式,我们可以根据模具的具体形状和尺寸来确定斜顶底座长度,从而保证模具的稳定性和精度。
在实际的模具设计和制造中,我们可以根据这个公式来确定模具的斜顶底座长度,从而保证产品的质量。
除了模具斜顶底座长度的计算公式,模具设计和制造中还有许多其他的重要内容,比如模具的材料选择、结构设计、加工工艺等。
这些内容都对模具的质量和性能有着重要的影响。
因此,在进行模具设计和制造时,我们需要综合考虑这些因素,从而保证产品的质量和性能。
总之,模具斜顶底座长度的计算公式是模具设计和制造中的一个重要内容,它可以帮助我们确定模具的斜顶底座长度,从而保证模具的稳定性和精度。
冲压模具设计用公式表
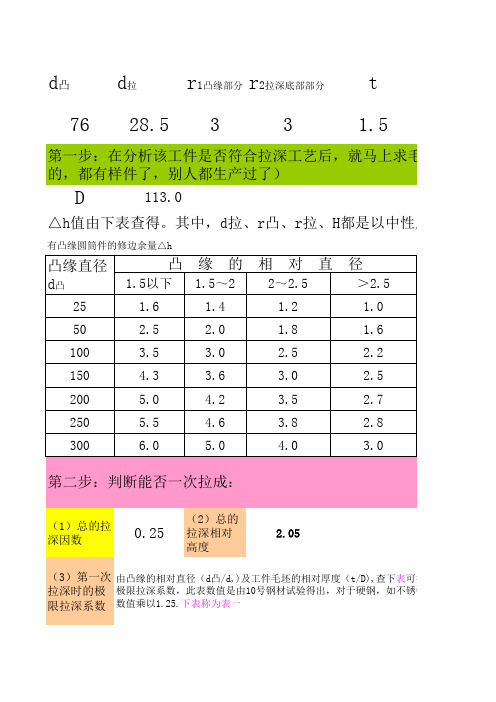
d凸d拉r1凸缘部分r2拉深底部部分t 7628.533 1.5第一步:在分析该工件是否符合拉深工艺后,就马上求毛坯的,都有样件了,别人都生产过了)D113.0△h值由下表查得。
其中,d拉、r凸、r拉、H都是以中性层计有凸缘圆筒件的修边余量△h<1.0~0.6<0.6~0.31.1以下0.510.530.550.571.30.490.510.530.541.50.470.490.500.511.80.450.460.470.482.00.420.430.440.452.20.400.410.420.422.50.370.380.380.382.80.340.350.350.353.00.320.330.330.33凸/d说明:1、表中数值适用于10号钢,对于比10号钢塑性更大的金属取接近于大的数值、对金属,取接近于小的数值;2、表中较大的数值适用于圆角半径较大的工件,较小值适用于圆角半径较小的工件毛坯相对厚度(t/D)*10012、第一次拉深时的凹模圆角半径初次决定r 凹7.1这个7.1是初次计算值,还要作如下处理:r1=7.1+t/2=7.85,圆整取8,填入右边栏82.0~1.0<1.0~0.3<03~0.1无凸缘(4-6)*t(6-8)*t(8-12)*t有凸缘(8-12)*t (12-15)*t (15-20)*t3、第一次拉深时的凸模圆角半径初次决定r 凸7.1这个7.1是初次计算值,还要作如下处理:r2=7.1+t/2=7.85,圆整取8,填入右边栏8最后确定r凸11.1第三步:试确定首次拉深因数右边的11.1可以灵活处理为:9.5-12之间的数,但不能比等,并把所确定的值填入右栏以上所确定的“再次确定r凸”是由经验公式计算得出的最小值,实际工作中,应该对前面由表均值那这样子说来,坯料直径就应该比当初所确定的113要大,大多少呢?见下面的D'初选第一次拉深完成后,凸缘相对直径(d凸/d1)=1.1,则由前面表一可知d1=m1*D=0.53*113=59.89(圆整到61,把此圆整数值填入右边一栏)为了首次拉深后的各次拉深过程中,不至于使前面加工出来的凸缘产生变形,必须在首拉入材料量的5%。
YQ-注塑模具设计-各类计算公式
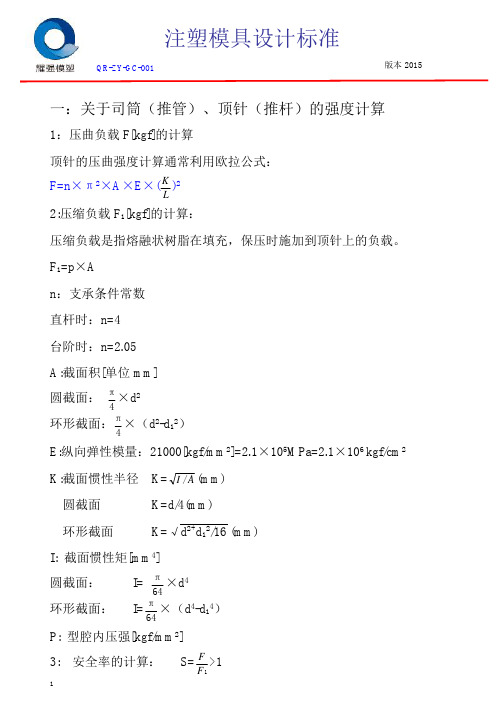
注塑模具设计标准QR-ZY-GC-001 版本 2015一:关于司筒(推管)、顶针(推杆)的强度计算1:压曲负载 F[kgf]的计算 顶针的压曲强度计算通常利用欧拉公式: F=n×π2×A×E×( K )2L2:压缩负载 F1[kgf]的计算: 压缩负载是指熔融状树脂在填充,保压时施加到顶针上的负载。
F1=p×A n:支承条件常数 直杆时:n=4 台阶时:n=2.05 A:截面积[单位 mm] 圆截面:π ×d2 4 π 环形截面: ×(d2-d12) 4E:纵向弹性模量:21000[kgf/mm2]=2.1×105MPa=2.1×106 kgf/cm2 K:截面惯性半径 圆截面 环形截面 K=I / A (mm)K=d/4(mm) K=√d2+d12/16 (mm)I: 截面惯性矩[mm4] 圆截面: 环形截面:π ×d4 64 I= π ×(d4-d14) 64I=P: 型腔内压强[kgf/mm2] 3: 安全率的计算:1S=F >1 F1注塑模具设计标准QR-ZY-GC-001 版本 2015二:关于悬臂梁结构的最大挠度(δmax)计算公式 1:型芯前端有集中负载 δmax=Fl3/3EI δmax:最大挠度(cm) F: E: I: 集中负载(kgf/cm2) 纵向弹性模量 截面抗弯惯量(cm4)[惯性矩]Fl此公式同样可以计算斜顶杆的直径注:δ:斜顶杆变形量(cm);F:斜顶头的重力(kgf);E:纵向弹性模量 2.1x106(kgf/cm2);I:截面抗弯 惯性矩(cm4)。
2:型芯侧面有均布负载 δmax=ql4/8EI q: E: I: = Fl3/8EI q×l=F δmax:最大挠度(cm) 均布负载(kgf/cm); l 指型芯悬于模板的长度 纵向弹性模量 截面抗弯惯量(cm )[惯性矩]4ql实际上,熔化树脂会瞬间流向型芯的周围,因此只受单方向压力作用的可 能性极小。
冲压件模具设计的常用公式
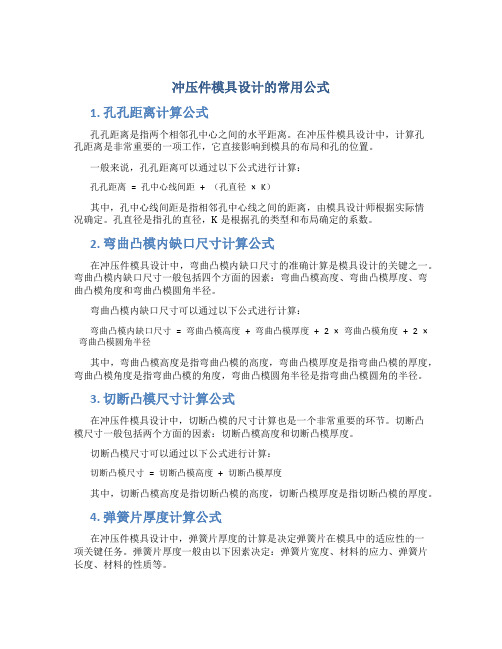
冲压件模具设计的常用公式1. 孔孔距离计算公式孔孔距离是指两个相邻孔中心之间的水平距离。
在冲压件模具设计中,计算孔孔距离是非常重要的一项工作,它直接影响到模具的布局和孔的位置。
一般来说,孔孔距离可以通过以下公式进行计算:孔孔距离 = 孔中心线间距 + (孔直径 × K)其中,孔中心线间距是指相邻孔中心线之间的距离,由模具设计师根据实际情况确定。
孔直径是指孔的直径,K是根据孔的类型和布局确定的系数。
2. 弯曲凸模内缺口尺寸计算公式在冲压件模具设计中,弯曲凸模内缺口尺寸的准确计算是模具设计的关键之一。
弯曲凸模内缺口尺寸一般包括四个方面的因素:弯曲凸模高度、弯曲凸模厚度、弯曲凸模角度和弯曲凸模圆角半径。
弯曲凸模内缺口尺寸可以通过以下公式进行计算:弯曲凸模内缺口尺寸 = 弯曲凸模高度 + 弯曲凸模厚度 + 2 × 弯曲凸模角度 + 2 ×弯曲凸模圆角半径其中,弯曲凸模高度是指弯曲凸模的高度,弯曲凸模厚度是指弯曲凸模的厚度,弯曲凸模角度是指弯曲凸模的角度,弯曲凸模圆角半径是指弯曲凸模圆角的半径。
3. 切断凸模尺寸计算公式在冲压件模具设计中,切断凸模的尺寸计算也是一个非常重要的环节。
切断凸模尺寸一般包括两个方面的因素:切断凸模高度和切断凸模厚度。
切断凸模尺寸可以通过以下公式进行计算:切断凸模尺寸 = 切断凸模高度 + 切断凸模厚度其中,切断凸模高度是指切断凸模的高度,切断凸模厚度是指切断凸模的厚度。
4. 弹簧片厚度计算公式在冲压件模具设计中,弹簧片厚度的计算是决定弹簧片在模具中的适应性的一项关键任务。
弹簧片厚度一般由以下因素决定:弹簧片宽度、材料的应力、弹簧片长度、材料的性质等。
弹簧片厚度可以通过以下公式进行计算:弹簧片厚度 = (弹簧片宽度 × 弹簧片宽度 × 弹簧片长度 × 弹簧片长度)/ (16 × 弹簧片宽度 × 材料的应力)其中,弹簧片宽度是指弹簧片的宽度,弹簧片长度是指弹簧片的长度,材料的应力是指材料的屈服应力。
- 1、下载文档前请自行甄别文档内容的完整性,平台不提供额外的编辑、内容补充、找答案等附加服务。
- 2、"仅部分预览"的文档,不可在线预览部分如存在完整性等问题,可反馈申请退款(可完整预览的文档不适用该条件!)。
- 3、如文档侵犯您的权益,请联系客服反馈,我们会尽快为您处理(人工客服工作时间:9:00-18:30)。
模具设计计算公式
冲裁力是冲裁过程中凸模对板料施加的压力,它是随凸模进人材料的深度(凸模行程)而变化的,如图2.2.3所示。
通常说的冲裁力是指冲裁力的最大值,它是选用压力机和设计模具的重要依据之一。
用普通平刃口模具冲裁时,其冲裁力F一般按下式计算:
式中F——冲裁力;
L——冲裁周边长度;
t——材料厚度;
——材料抗剪强度;
K——系数。
系数K是考虑到实际生产中,模具间隙值的波动和不均匀、刃口的磨损、板料力学性能和厚度波动等因素的影响而给出的修正系数。
一般取K=1.3。
为计算简便,也可按下式估算冲裁力:
(2.6.2)
式中——材料的抗拉强度。
在冲裁结束时,由于材料的弹性回复(包括径向弹性回复和弹性翘曲的回复)及摩擦的存在,将使冲落部分的材料梗塞在凹模内,而冲裁剩下的材料则紧箍在凸模上。
为使冲裁工作继续进行,必须将箍在凸模上的料卸下,将卡在凹模内的料推出。
从凸模上卸下箍着的料所需要的力称卸料力;将梗塞在凹模内的料顺冲裁方向推出所需要的力称推件力;逆冲裁方向将料从凹模内顶出所需要的力称顶件力,如图2.6.1所示。
卸料力、推件力和顶件力是由压力机和模具卸料装置或顶件装置传递
的。
所以在选择设备的公称压力或设计冲模时,应分别予以考虑。
影响这些力
的因素较多,主要有材料的力学性能、材料的厚度、模具间隙、凹模洞口的结
构、搭边大小、润滑情况、制件的形状和尺寸等。
所以要准确地计算这些力是
困难的,生产中常用下列经验公式计算:
卸料力(2.6.3)
图2.6.1
推件力(2.6.4)
顶件力(2.6.5)
式中F——冲裁力;图2.6.1 卸料力推件力和顶件力
——卸料力、推件力、顶件力系数,见表2.6.1;
n——同时卡在凹模内的冲裁件(或废料)数。
式中h——凹模洞口的直刃壁高度;
t——板料厚度。
注:卸料力系数Kx,在冲多孔、大搭边和轮廓复杂制件时取上限值。
压力机的公称压力必须大于或等于各种冲压工艺力的总和Fz。
Fz的计算应根据不同的模具结构分别对待,即
采用弹性卸料装置和下出料方式的冲裁模时
(2.6.6)
采用弹性卸料装置和上出料方式的冲裁模时
(2.6.7)
采用刚性卸料装置和下出料方式的冲裁模时
(2.6.8)
为实现小设备冲裁大工件,或使冲裁过程平稳以减少
压力机振动,常用下列方法来降低冲裁力。
1.阶梯凸模冲裁
在多凸模的冲模中,将凸模设计成不同长度,使工作端
面呈阶梯式布置,如图2.6.2所示,这样,各凸模冲裁力
的最大峰值不同时出现,从而达到降低冲裁力的目的。
图2.6.2 凸模的阶梯布置法
在几个凸模直径相差较大,相距又很近的情况下,为能避免小直径凸模由于承受材料流动的侧压力而产生折断或倾斜现象,应该采用阶梯布置,即将小凸模做短一些。
凸模间的高度差H与板料厚度t有关,
即t<3mm H=t
t>3mm H=0.5t
阶梯凸模冲裁的冲裁力,一般只按产生最大冲裁力的那一个阶梯进行计算。
2.斜刃冲裁
用平刃口模具冲裁时,沿刃口整个周边同时冲切材料,故冲裁力较大。
若将凸模(或凹模)刃口平面做成与其轴线倾斜一个角度的斜刃,则冲裁时刃口就不是全部同时切人,而是逐步地将材料切离,这样就相当于把冲裁件整个周边长分成若干小段进行剪切分离,因而能显著降低冲裁力。
斜刃冲裁时,会使板料产生弯曲。
因而,斜刃配置的原则是:必须保证工件平整,只允许废料发生弯曲变形。
因此,落料时凸模应为平刃,将凹模作成斜刃,如图2.6.3a、b所示。
冲孔时则凹模应为平刃,凸模为斜刃,如图2.6.3c、d、e所示。
斜刃还应当对称布置,以免冲裁时模具承受单向侧压力而发生偏移,啃伤刃口,如图2.6.3a~e所示。
向一边斜的斜刃,只能用于切舌或切开,如图2.6.3f所示。
斜刃冲模虽有降低冲裁力使冲裁过程平稳的优点,但模具制造复杂,刃口易磨损,修磨困难,冲件不够平整,且不适于冲裁外形复杂的冲件,因此在一般情况下尽量不用,只用于大型冲件或厚板的冲裁。
最后应当指出,采用斜刃冲裁或阶梯凸模冲裁时,虽然减低了冲裁力,但凸模进入凹模较深,冲裁行程增加,因此这些模具省力而不省功。
a)、b)落料用c)、d)、e)冲孔用f)切舌用
图2.6.3 各种斜刃的形式
3.加热冲裁(红冲)
金属在常温时其抗剪强度是一定的,但是,当金属材料加热到一定的温度之后,其抗剪强度显著降低,所以加热冲裁能降低了冲裁力。
但加热冲裁易破坏工件表面质量,同时会产生热变形,精度低,因此应用比较少。
模具的压力中心就是冲压力合力的作用点。
为了保证压力机和模具的正常工作,应使模具的压力中心与压力机滑块的中心线相重合。
否则,冲压时滑块就会承受偏心载荷,导致滑块导轨和模具导向部分不正常的磨损,还会使合理间隙得不到保证,从而影响制件质量和降低模具寿命甚至损坏模具。
在实际生产中,可能会出现由于冲件的形状特殊或排样特殊,从模具结构设计与制造考虑不宜使压力中心与模柄中心线相重合的情况,这时应注意使压力中心的偏离不致超出所选用压力机允许的范围。
1.简单几何图形压力中心的位置
(1)对称冲件的压力中心,位于冲件轮廓图形的几何中心上。
(2)冲裁直线段时,其压力中心位于直线段的中心。
(3)冲裁圆弧线段时,其压力中心的位置,如图2.6.4,按下式计算:
式中:b ——弧长。
其他符号意义见图。
图2.6.4
2.确定多凸模模具的压力中心
确定多凸模模具的压力中心,是将各凸模的压力中心确定后,再计算模具的压力中心(见图2.6.5)。
计算其压力中心的步骤如下:
(1)按比例画出每一个凸模刃口轮廓的位置。
(2)在任意位置画出坐标轴线x ,y 。
坐标轴位置选择适当可使计算简化。
在选择坐标轴位置时,应尽量把坐标原点取在某一刃口轮廓的压力中心,或使坐标轴线尽量多的通过凸模刃口轮廓的压力中心,坐标原点最好是几个凸模刃口轮廓压力中心的对称中心。
(3
)分别计算凸模刃口轮廓的压力中心及坐标位置
和
(4
)分别计算凸模刃口轮廓的冲裁力
或每一个凸模刃口轮廓的周长。
(5)对于平行力系,冲裁力的合力等于各力的代数和。
即
图2.6.5
(6)根据力学定理,合力对某轴之力矩等于各分力对同轴力矩之代数和,则可得压力中心坐标( )计算公式。
(2.6.10)
(2.6.11)
因为冲裁力与周边长度成正比,所以式中个冲裁力可分别用冲裁周边长度
(2.6.12)
(2.6.13)
3.复杂形状零件模具压力中心的确定
复杂形状零件模具压力中心的计算原理与多凸模冲裁压力中心的计算原理相同(见图2.6.6)。
其具体步骤如下:
(1)选定坐标轴x和y。
(2)将组成图形的轮廓线划分为若干简单的线段,求出各线段长度
(3)确定各线段的重心位置和.
(4)然后按公式(2.6.13)、(2.6.14)算出压力中心的坐标.
图2.6.6
冲裁模压力中心的确定,除上述的解析法外,还可以用作图法和悬挂法。
但因作图法精确度不高,方法也不简单,因此在应用中受到一定限制。
悬挂法的理论根据是:用匀质金属丝代替均布于冲裁件轮廓的冲裁力,该模拟件的重心就是冲裁的压力中心。
具体作法是:用匀质细金属丝沿冲裁轮廓弯制成模拟件,然后用缝纫线将模拟件悬吊起来。
并从吊点作铅垂线;再取模拟件的另一点,以同样的方法作另一铅垂线,两垂线的交点即为压力中心。
悬挂法多用于确定复杂零件的模具压力中心。