夹套冷却时间计算
化工课程设计--夹套反应釜课程设计 (2)

化工设备机械基础课程设计题目:1m3夹套反应釜设计学院: 化学与材料工程学院专业: 化学工程班级: 10化工姓名:学号: ***********指导老师:完成日期: 2012年6月1日夹套反应釜设计任务书设计者:班级:10化工学号:10111003101指导老师:日期:一、设计内容设计一台夹套传热式带搅拌的配料罐。
二、设计参数和技术特性指标见下表三、设计要求1.进行罐体和夹套设计计算;2.选择支座形式并进行计算;3.手孔校核计算;4.选择接管、管法兰、设备法兰;5.进行搅拌传动系统设计;(1)进行传动系统方案设计(指定用V带传动);(2)作带传动设计计算:定出带型,带轮相关尺寸(指定选用库存电机Y1322-6,转速960r/min,功率5.5kW);(3)选择轴承;(4)选择联轴器;(5)进行罐内搅拌轴的结构设计、搅拌器与搅拌轴的连接结构设计;6.设计机架结构;7.设计凸缘及安装底盖结构;8.选择轴封形式;9.绘制装配图;10. 绘传动系统部件图。
表1 夹套反应釜设计任务书简图设计参数及要求容器内夹套内工作压力,Mpa设计压力,MPa0.2 0.3工作温度,℃设计温度,℃<100 <150介质染料及有机溶剂冷却水或蒸汽全容积,m3 1.0操作容积,m30.8全容积传热面积,m2>3.5腐蚀情况微弱推荐材料Q235-A搅拌器型式推进式搅拌轴转速,r/min200轴功率,kW 4接管表符号公称尺寸DN连接面形式用途a 25 蒸汽入口b 25 加料口c 80 视镜d 65 温度计管口e 25 压缩空气入口f 40 放料口g 25 冷凝水出口h 100 手孔目录1. 夹套反应釜的结构 (5)1.1 夹套反应釜的功能和用途 (5)1.2 夹套反应釜的反应条件 (5)2. 设计标准 (6)3. 设计方案的分析和拟定 (6)4. 各部分结构尺寸的确定和设计计算 (7)4.1 罐体和夹套的结构设计 (7)4.1.1 罐体几何尺寸计算 (8)4.1.2 夹套几何尺寸计算 (10)4.2 夹套反应釜的强度计算 (12)4.2.1 强度计算(按内压计算强度) (12)4.2.2 稳定性校核(按外压校核厚度) (15)4.2.3水压试验校核 (21)4.3 反应釜的搅拌器 (23)4.3.1 搅拌装置的搅拌器 (23)4.3.2 搅拌器的安装方式及其与轴连接的结构设计 (23)4.3.3 搅拌装置的搅拌轴设计 (24)4.4 反应釜的传动装置设计 (26)4.4.1 常用电机及其连接尺寸 (26)4.4.2釜用减速机类型、标准及其选用 (26)4.4.3 V带减速机 (27)4.4.4凸缘法兰 (30)4.4.5安装底盖 (31)4.4.6机架 (31)4.4.7联轴器 (32)4.5 反应釜的轴封装置设计 (33)4.5.1 填料密封 (33)4.5.2 机械密封 (33)4.6反应釜的其他附件设计 (34)4.6.1 支座 (34)4.6.2 手孔和人孔 (35)4.6.3 设备接口 (35)5. 设计小结 (38)6. 参考文献 (39)设计说明书1. 夹套反应釜的结构夹套反应釜主要由搅拌容器、搅拌装置、传动装置、轴封装置、支座、人孔、工艺接管和一些附件组成。
产吨环氧树脂车间工艺设计蔡成云2

目录前言31.1产品介绍31.2、生产工艺31.2.1一步法工艺41.2.2二步法工艺41.3、主要原材料4第2章初步工艺流程设计52.1 工艺流程框图:52.2工艺流程:6第3章物料衡算63.1 计算条件与数据理:63.2 原料用量计算:73.3 缩合工段物料衡算:83.3.1 一次反应:83.3.3回收过量环氧氯丙烷:104.3.4 环氧树脂收集:10第4章热量衡算114.1计算依据:114.2 常用热力学数据计:134.3缩合工段热量衡算:144.3.1溶解岗位:144.3.2 反应岗位:14第5章设备选型165.1计算条件确定165.1.1 操作工时与生产周期地确定:165.1.2 日生产批次和反应釜个数地确定:175.2 缩合工段反应岗位地设备选型:175.2.1物料体积计算:175.2.2反应釜地选型:175.2.3校核传热面积:185.3 其它设备地选型21第6章厂区布置和车间布置设计226.1工厂设计地内容与规范:226.2 厂址地选择:236.3 车间地布置:236.3.1 辅助生产和行政-生活布置:236.3.2 厂房地布局:246.3.3 厂房地长、宽、高和层数确定:246.3.4 厂房内布置:24第7章“三废”处理及其综合利用248.1 废水地处理:258.2 套用和回收利用:25第8章环氧树脂安全生产和环境保护258.1环氧树脂安全生产和环境保护地重要性258.2环氧树脂生产安全注意事项与劳动保护措施258.2.1环氧树脂生产原料安全毒性258.2.2环氧树脂生产中劳动保护注意事项268.2.3环境保护措施26致谢26参考文献27年产3000吨环氧树脂车间工艺设计蔡成云摘要:环氧树脂生产工艺一般分为一步法和二步法.目前低分子量液体环氧树脂和中分子量固体环氧树脂,一般都采用一步法工艺;高分子量环氧树脂采用二步法.二步法工艺地优点:与一步法相比,它具有生产工艺简单、设备少、工时短、无三废排放和产品质量易调节控制等优点.以双酚A(BPA)为主要原材料,合成地环氧树脂称为双酚A(BPA)型环氧树脂,是目前产量最大、用途最广地环氧树脂,由于它地应用遍及国民经济地众多领域,因此又称为通用型环氧树脂.它属于缩水甘油醚型.本文介绍了年产3000吨地环氧树脂地车间设计,从技术、工程经济、生产管理等方面进行了详细地论述,内容主要包括:设计依据,工艺路线论证,工艺流程设计,全流程物料衡算,全流程能量衡算,工艺设备选型与计算,车间布置设计,三废处理及其综合利用,劳动组织,劳动保护与安全生产,工程经济,工艺细节改进设计等内容.关键词:环氧树脂;一步法;车间工艺设计Annual output of 3,000 tons of epoxy resin plant process designCaichengyunAbstract:Epoxy resin production process is generally divided into one-step and two-step. Present in low molecular weight solid epoxy resins and liquid epoxy resin, generally using one-step process。
均相液体机械搅拌夹套冷却反应器设计

均相液体机械搅拌夹套冷却反应器设计工艺计算书(工艺部分)上海工程技术大学 化学工程与工艺系均相液体机械搅拌夹套冷却反应器设计(工艺部分)一、设计任务1.处理能力:140000m 3/a 均相液体;2.设备型式:机械搅拌夹套冷却器。
二、操作条件1.均相液温度保持50℃;2.平均停留时间18min ;3.需移走热量105kW ;4.采用夹套冷却,冷却水进口温度20℃,出口温度30℃;5.50℃下均相液的物性参数:比热容C J/kg ︒⋅=1012p c ,导热系数C 0.622W/m ︒⋅=λ,平均密度3kg/m 930=ρ,粘度s Pa ⋅⨯=-2107332.μ。
6.忽略污垢热阻及间壁热阻;7.每年按300天,每天按24小时连续运行。
三、设计内容1.设计方案简介:对确定的工艺流程及设备进行简要论述;2.搅拌器工艺设计计算:确定搅拌功率及夹套传热面积;3.搅拌器、搅拌器附件、搅拌槽、夹套等主要结构尺寸的设计计算;4.主要辅助设备选型:冷却水泵、搅拌电机等;5.绘制搅拌器工艺流程图及设备设计条件图;6.对本设计的评述。
附:均相液体机械搅拌夹套冷却反应器设计——工艺计算书均相液体机械搅拌夹套冷却反应器设计——工艺计算书一、选定搅拌器的类型因为该设计所用搅拌器主要是为了实现物料的均相混合,故推进式、桨式、涡轮式、三叶后掠式等均可选择,本设计选用六片平直叶圆盘涡轮式搅拌器。
二、搅拌设备的设计计算确定搅拌槽的结构及尺寸,搅拌桨及其附件的几何尺寸及安装位置,计算搅拌转速及功率,计算传热面积等,最终为机械设计提供条件。
(一)搅拌槽的结构设计1. 搅拌槽的容积、类型、高径比 (1)容积与槽径对于连续操作,搅拌槽的有效体积为搅拌槽的有效体积=流入搅拌槽的液体流量×物料的平均停留时间35.833m =⨯⨯=601824300140000V根据搅拌槽内液体最佳充填高度等于槽内径,即D H =。
现以搅拌槽为平底近似估算槽直径,则有:m 95114383354433...πV H D =⨯=== 本设计取951.D =m 。
通用式厌氧发酵罐的设计
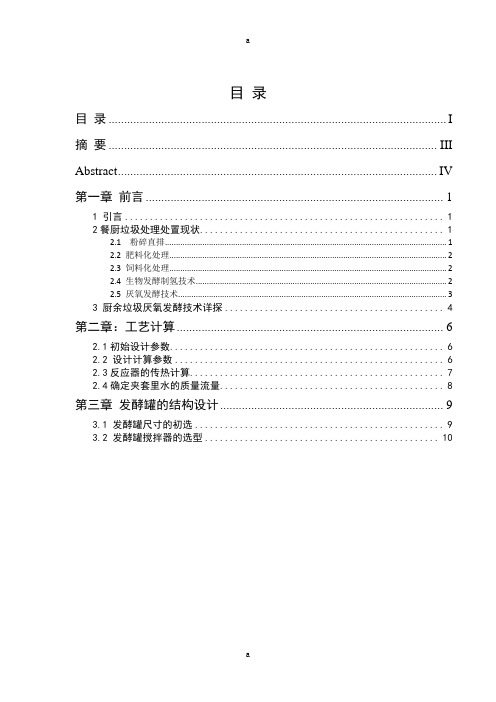
目录目录 (I)摘要 (III)Abstract (IV)第一章前言 (1)1 引言 (1)2餐厨垃圾处理处置现状 (1)2.1 粉碎直排 (1)2.2 肥料化处理 (2)2.3 饲料化处理 (2)2.4 生物发酵制氢技术 (2)2.5 厌氧发酵技术 (3)3 厨余垃圾厌氧发酵技术详探 (4)第二章:工艺计算 (6)2.1初始设计参数 (6)2.2 设计计算参数 (6)2.3反应器的传热计算 (7)2.4确定夹套里水的质量流量 (8)第三章发酵罐的结构设计 (9)3.1 发酵罐尺寸的初选 (9)3.2 发酵罐搅拌器的选型 (10)3.3 发酵罐传热元件的设计 (11)3.3.1 传热元件的选取 (11)3.3.2 夹套的尺寸及连接型式 (12)3.4 发酵罐的具体尺寸的设计计算 (13)3.4.1 发酵罐筒体厚度设计计算 (13)3.4.2 封头厚度计算 (14)3.4.3夹套的壁厚计算 (16)3.5 发酵罐搅拌功率计算及电机的选型 (16)3.5.1搅拌功率计算 (16)3.5.2 电机的选型 (16)3.6 传动装置及选型 (17)3.6.1减速器的选取 (17)3.6.2 联轴器的选择 (17)3.6.3 搅拌轴的设计 (18)3.6.3.1 搅拌轴强度预算 (18)3.6.3.2 按扭矩和弯矩合成计算轴强度 (19)3.6.3.3 搅拌轴临界转速的校核 (21)3.6.4 凸缘法兰的选型 (23)3.6.5 安装底盖的选型 (24)3.6.6螺栓强度的校核 (25)3.7 水压试验 (26)3.8接管及管法兰的设计 (27)第四章发酵罐的附件的选取 (29)4.1 视镜的选取 (29)4.2 温度计测量元件 (29)4.3 挡板的选型 (30)4.4 支座的选型 (30)4.5 转轴的密封 (32)4.6焊接结构设计 (33)结论 (35)致谢 (36)参考文献 (37)附录 (39)50L通用式厌氧发酵罐的设计摘要本设计介绍了餐厨垃圾的成分、特点,综述了目前处理厨余垃圾的基本方法:饲料化技术、堆肥化处理技术、生物厌氧发酵技术。
均相液体机械搅拌夹套冷却反应器设计
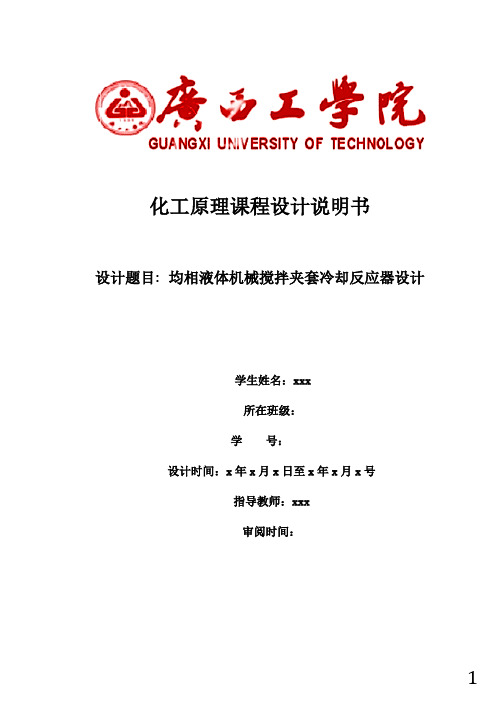
化工原理课程设计说明书设计题目:均相液体机械搅拌夹套冷却反应器设计学生姓名:xxx所在班级:学号:设计时间:x年x月x日至x年x月x号指导教师:xxx审阅时间:一、设计题目:均相液体机械搅拌夹套冷却反应器设计。
二、设计任务及操作条件1. 处理能力(140000+500X)m3/a均相液体。
〖注:X代表学号最后两位数〗2. 设备型式机械搅拌夹套冷却装置。
3. 操作条件①均相液温度保持50℃。
②平均停留时间18min。
③需要移走热量105kW。
④采用夹套冷却,冷却水进口温度20℃,冷却水出口温度30℃⑤50℃下均相液物性参数:比热容Cp=1 012J/(kg·)℃,导热系数λ=0.622W/(m·)℃,平均密度ρ=930kg/m3,粘度μ=2.733X10-2Pa·s。
⑥忽略污垢及间壁热阻。
⑦年按300天,每天24小时连续搅拌。
三、厂址:柳州地区。
四、设计项目(1)设计方案简介:对确定的工艺流程及设备进行简要论述。
(2)搅拌器工艺设计计算:确定搅拌功率及夹套传热面积。
(3)搅拌器、搅拌器附件、搅拌槽、夹套等主要结构尺寸设计计算。
(4)主要辅助设备选型:冷却水泵、搅拌电机等。
(5)绘图(3#图纸):带控制点的工艺流程图及设备设计条件图。
(6)对本设计评述。
五、参考文献柴诚敬,张国亮等.化工流体流动与传热.北京:化学工业出版社,2000化工设备设计全书编辑委员会.搅拌设备设计.上海:上海科学技术出版社,1985王凯,冯连芳.混合设备设计.北京:机械工业出版社,2000目录第一章设计方案简介 (4)1.1搅拌器的选型 (4)1.2搅拌器的安装选择 (5)1.3电动机的选型 (5)1.4减速机的选型 (6)1.5密封装置的选择 (6)1.6物料进口进口安置 (7)1.7夹套进出口安置 (7)1.8泵的选择 (7)1.9支座的选择 (7)1.10管子的选择 (7)1.11封头的选择 (7)第二章工艺流程图及说明 (8)第三章工艺计算及主要设备的计算 (9)3.1均相液体和冷却水的物性数据 (9)3.2搅拌槽的计算 (9)3.3搅拌器的功率计算 (12)3.4总传热面积 (12)3.4.1被搅拌液体侧的对流传热系数.. (13)3.4.2夹套测冷却水对流传热系数 (13)3.4.3总传热系数 (14)3.4.4夹套传热面积 (14)第四章设备的计算和选型 (15)4.1电动机的选型 (15)4.2支座的选择 (15)4.3泵的选型 (15)4.3.1 输料泵的选型计算 (15)4.3.2 冷水泵的选型计算 (15)第五章设计结果一览表 (18)第六章附图(另附搅拌器工艺流程图及设备设计条件图) (20)第七章设计心得 (20)第八章主要符号说明 (21)第九章参考文献 (22)设计方案简介搅拌设备在石油、化工、食品等工业生产中应用范围很广,尤其是化学工业中,很多的化工生产或多或少地应用着搅拌操作,化学工艺过程的种种物理过程与化学过程,往往要采用搅拌操作才能得到好的效果。
夹套反应釜设计计算

夹套反应釜设计计算首先,夹套反应釜的热传导方程是非常重要的设计依据。
热传导方程可以用来推导出夹套和反应体系之间的热传导系数,从而确定夹套的尺寸和设计条件。
热传导方程的基本形式可以表示为:Q=k*A*ΔT/Δx其中,Q是热通量,k是热传导系数,A是传热面积,ΔT是温度差,Δx是传热距离。
夹套反应釜的设计计算中还需要确定传热系数k。
传热系数与夹套和反应体系之间的传热面积、流体的导热性质有关。
传热系数的计算可以采用经验公式或者利用流体力学和传热学的计算方法。
对于常见的工艺流体,可以使用流体传热系数的经验公式进行计算。
在进行夹套反应釜的设计计算时,需要考虑到反应体系的热容和传热特性。
热容是指单位质量物质在单位温度变化下所吸收或放出的热量。
传热特性包括传热速率、传热强度等参数。
这些参数对于夹套反应釜的设计和操作都有很大的影响。
在设计夹套反应釜时,还需要考虑到反应体系的冷却方式。
冷却方式可以分为直接冷却和间接冷却两种。
直接冷却是指利用夹套内部的冷却介质来降低反应体系的温度,而间接冷却则是通过外部介质进行冷却。
直接冷却通常可以实现较高的冷却速率,但也会带来传热效果的不均匀性。
间接冷却通常可以实现较好的传热效果,但需要更复杂的设备和操作。
在进行夹套反应釜的设计计算时,还需要考虑到夹套和反应体系之间的绝热性能。
绝热性能可以通过计算夹套和反应体系之间的热传导系数和传热面积来确定。
通过合理设计绝热层的材料和结构,可以减少热量的损失,提高反应体系的稳定性。
综上所述,夹套反应釜的设计计算是一个复杂的过程,需要考虑到反应体系的热传导、传热特性、冷却方式和绝热性能等多个方面的因素。
只有通过合理的设计和计算,才能确保夹套反应釜的安全和高效运行。
夹套反应器及搪玻璃反应器换热面积计算

夹套反应器及搪玻璃反应器换热面积计算
一、夹套反应器换热面积计算
夹套反应器主要由表面反应器、夹套和加热冷却等部件组成,它是目前应用最广泛的反应器之一。
夹套反应器可以分为两种类型:封闭式夹套反应器和开式夹套反应器。
封闭式夹套反应器的换热面积计算主要是根据夹套内表面温度的变化来计算的,具体公式:
换热面积A=(T2-T1)/K
其中,T2表示夹套内表面的最终温度,T1表示夹套内表面的初始温度,K表示单位面积的热传导系数。
开式夹套反应器的换热面积计算,主要是根据夹套的线热力学特性进行计算,具体公式:
换热面积A=(T2)/K
其中,T2表示夹套内表面的最终温度,K表示单位面积的热传导系数。
二、搪玻璃反应器换热面积计算
搪玻璃反应器是一种由搪玻璃组成的反应器,它具有耐腐蚀、耐温度高、耐久性强等特点,多用于高温高压反应,搪玻璃反应器的换热面积计算主要是根据搪玻璃表面温度的变化来计算的,具体公式:
换热面积A=(T2-T1)/K
其中,T2表示搪玻璃表面的最终温度,T1表示搪玻璃表面的初始温度,K表示单位面积的热传导系数。
发酵罐冷却夹套的有关配置问题

啤酒厂发酵大罐冷却夹套的有关配置问题(节录)1.冷却夹套的型式选择啤酒发酵罐有三种冷却夹套型式可供选择,即:螺旋半园管式、蜂窝式和米勒板式三种。
我国沈阳雪花啤酒厂早期引进的德国技术现场加工制造的发酵罐为半园管式冷却夹套;原北京华都啤酒厂从丹麦引进的发酵罐为蜂窝式冷却夹套;青岛啤酒二厂从法国引进的发酵罐为米勒板式冷却夹套。
这三种型式都采用液氨冷却效果较好,较使用酒精水、乙二醇水或丙二醇水作冷媒可节电20%左右,制冷压缩机吸气温度达-5℃即可。
(使用冷媒的制冷压缩机吸气温度必须低至-10℃)2.冷却夹套的传热特点发酵罐的直径从4000mm发展到现在的7200mm有效容积从130M3发展到650M3,甚至更大。
因各厂麦汁成分、酵母、发酵工艺不同,发酵过程中温度、时间、压力控制不同。
主酵开始时,一般先打开上部冷却带,发酵旺盛后再打开中部冷却带,发酵液的温度为下低上高,形成罐内对流循环。
一般主酵结束后要急速降温,开启上、中、下全部冷却夹套,将酒液从12℃降至4℃左右;回收酵母后要继续将酒液冷却至-1℃。
在后酵贮酒阶段一般只开启下部和锥底冷却夹套。
因为啤酒的密度在2.5℃时最大,酒液降至-1℃后,在发酵罐内呈现上部温度低于锥底温度的状态,此时冷却过程的对流和主发酵为相反方向循环。
后酵冷却过程也要防止啤酒在-2℃以下冻结,因而锥底冷却夹套的液氨蒸发温度必须控制在-2℃。
从以上分析冷却夹套必须采用多段控制,以利于使用过程灵活调控。
3.发酵过程产热分析首先算出发酵各个阶段罐内降糖产生的热量及热季罐外部散冷负荷。
1)主发酵过程是一个排热降温过程,浸出物形成的热量为163w/kg。
大约2/3左右的浸出物在主发酵时被消耗掉,100L麦汁的浸出物以12kg计,主发酵期放出的热量为:163×12×2/3=1304w这些热量必须通过冷却夹套排除,主发酵期间消耗浸出物是不均衡的,高泡期每天降糖2%,一般持续2~3天,按6天主发酵计,则每100L麦汁日最大排热量为(1304÷6)×2=434.66w/hl·d当罐内贮5000HL麦汁时,每小时必须消除热量为:(5000×434.66)÷24=90554w2)主发酵结束的温度一般控制在4℃以下,而整罐酒从12℃降至4℃耗冷也是相当大的,此时所需冷量为:Q=G×C×△t/T式中:Q—耗冷量wG—单罐贮酒量kg(L)C—酒的比热1.163w/kg△t—温度差℃T—冷却时间,一般24~36h如果罐内贮酒4800HL,要从12℃降至4℃,要求36h内完成,则所需冷量为:Q=480000×1×1.163×(12-4)/36=124053.3w3)热季发酵罐体向外界散冷量为:Q=K×F×△t式中:Q—散冷量wF—发酵罐保温后外表面积m2K—发酵罐保温后的传热系数W/m2·℃△t—发酵罐外界空气和冷却夹套内流动冷剂的平均温度差,因大罐昼间受太阳幅射热的影响,表面温度很高。
关于罐子夹套换热 冷冻水消耗量的计算

关于罐子夹套换热冷冻水消耗量的计算文章标题:深度探讨罐子夹套换热冷冻水消耗量的计算方法在工业生产中,罐子夹套换热技术是一种常见的换热方式,通过罐子夹套与罐体之间的热交换,实现在生产过程中对液体的加热或冷却。
而在这个过程中,冷冻水的消耗量是一个重要的计算参数。
本文将深度探讨罐子夹套换热冷冻水消耗量的计算方法,以帮助读者更好地理解这一复杂的过程。
1. 罐子夹套换热技术简介罐子夹套换热技术是利用罐体内部夹套中的传热介质,通过外部的加热或冷却设备,对罐内液体进行加热或冷却的换热方式。
这种技术可以保持液体温度的均匀性,提高生产效率,同时也广泛应用于食品加工、化工生产等领域。
2. 冷冻水消耗量的计算方法在进行罐子夹套换热过程中,冷冻水的消耗量是一个需要精确计算的重要参数。
一般来说,冷冻水的消耗量与罐体的材质、夹套的结构、加热或冷却的温度差等因素都有密切关系。
计算冷冻水消耗量的方法可以通过以下步骤进行:步骤一:确定换热面积首先需要根据罐子夹套的尺寸、结构等参数,计算出换热面积。
换热面积的大小直接影响到冷冻水的消耗量,因此需要进行精确的测量和计算。
步骤二:计算传热系数传热系数是换热过程中的一个重要参数,它反映了热量在传递过程中的效率。
根据夹套材质、工作条件等因素,可以通过经验公式或实验测定的方法来计算传热系数。
步骤三:确定温度差在实际生产中,加热或冷却过程中液体的温度差是一个关键的参数。
根据工艺要求和设备性能,确定好温度差的范围,以便进行后续的计算。
步骤四:计算冷冻水的流量根据换热面积、传热系数和温度差等参数,可以利用传热方程来计算冷冻水的流量。
通过这一步骤,可以得到冷冻水的消耗量,从而为生产过程提供参考依据。
3. 个人观点和理解在实际生产中,罐子夹套换热冷冻水消耗量的计算需要考虑诸多因素,需要结合实际工艺参数和设备性能进行精确计算。
科学合理的计算方法可以帮助企业降低生产成本,提高生产效率,实现经济效益和环保效益的双赢。
味精工厂发酵车间的物料衡算

2 发酵罐及种子罐的设计与选型2.1 味精工厂发酵车间的物料衡算2.1.1 工艺技术指标及基础数据(1)查《发酵工厂工艺设计概论》P326表3 味精行业国家企业标准[5],选用主要指标如表1表1 味精发酵工艺技术指标指标名称单位指标数生产规模t/a 15000(味精)生产方法中糖发酵,一次等电点提取年生产天数d/a 300产品日产量t/a 50产品质量纯度% 99倒灌率% 1.0发酵周期h 48发酵初糖Kg/m3 150淀粉糖转化率% 95糖酸转化率% 48麸酸谷氨酸含量% 90谷氨酸提取率% 80味精对谷氨酸产率% 112(2)主要原材料质量指标淀粉原料的淀粉含量为80%,含水14%。
(3)二级种子培养基(g/L)水解糖25,糖蜜20,尿素3.5,磷酸氢二钾1.0,硫酸镁0.6,玉米浆5~10,泡敌0.6,硫酸镁0.002,硫酸亚铁0.002。
(4)发酵培养基(g/L)水解糖150,糖蜜4,硫酸镁0.6,氯化钾0.8,磷酸氢二钠0.2,硫酸亚铁0.002,硫酸锰0.002,尿素(总尿)40,泡敌0.6,植物油1.0。
(5)接种量为2% 。
2.1.2 谷氨酸发酵车间的物料衡算首先计算生产1000kg纯度为100%的味精需耗用的原辅材料及其他物料量。
(1)发酵液量V1式中150——发酵培养基初糖浓度(kg/m3)48%——糖酸转化率80%——谷氨酸提取率99%——除去倒灌率1%后的发酵成功率112%——味精对谷氨酸的精制产率(2)发酵液配制需水解糖量G1以纯糖算,(3)二级种液量V2(4)二级种子培养液所需水解糖量G2式中25——二级种液含糖量(kg/m3)(5)生产1000kg味精需水解糖总量G为:(6)耗用淀粉原料量理论上,100kg淀粉转化生成葡萄糖量为111kg,故理论上耗用的淀粉量G淀粉为:式中80%——淀粉原料含纯淀粉量95%——淀粉糖转化率(7)尿素耗用量二级种液耗尿素量为V3发酵培养基耗尿素为V4故共耗尿素量为627.5kg(8)甘蔗糖蜜耗用量二级种液耗用糖蜜量V5发酵培养基耗糖蜜量V6合计耗糖蜜69.9kg(9)氯化钾耗量GKCl(10)磷酸氢二钠(Na2HPO4•7H2O)耗量G3(11)硫酸镁(MgSO4•7H2O)用量G4(12)消泡剂(泡敌)耗用量G5(13)植物油耗用量G6(14)谷氨酸(麸酸)量发酵液谷氨酸含量为:实际生产的谷氨酸(提取率80%)为:2.1.3 15000t/a味精厂发酵车间的物料衡算结果由上述生产1000kg味精(100%纯度)的物料衡算结果,可求得15000t/a味精厂发酵车间的物料平衡计算。
夹套反应釜热传递选型计算方法

夹套反应釜热传递选型计算方法首先,计算热传导。
夹套反应釜的内外壁之间的热传导主要通过夹层介质进行。
夹层介质的导热系数是影响热传导速率的重要参数,可以通过实验或者查阅资料获得。
根据热传导定律,可以通过下式计算夹层介质的热传导速率:Q=λ*A*(T1-T2)/d其中,Q表示热传导速率,λ表示夹层介质的导热系数,A表示热传导的面积,T1和T2分别表示内外壁的温度,d表示夹层介质的厚度。
其次,计算对流传热。
对流传热是夹套反应釜中热传递的另一重要方式。
对流传热的计算需要考虑流体的热传导系数、速度和表面温度差等因素。
根据牛顿冷却定律,可以通过下式计算对流传热速率:Q=h*A*(T1-T2)其中,Q表示热传导速率,h表示对流换热系数,A表示热传导的面积,T1和T2分别表示内外壁的温度。
最后,计算辐射传热。
辐射传热是夹套反应釜中一种重要的热传递方式。
辐射传热的计算需要考虑表面的发射率、温度和表面视为的辐射面积等因素。
根据斯特藩-玻尔兹曼定律,可以通过下式计算辐射传热速率:Q=ε*σ*A*(T1^4-T2^4)其中,Q表示热传导速率,ε表示表面的发射率,σ表示斯特藩-玻尔兹曼常数,A表示热传导的面积,T1和T2分别表示内外壁的温度。
在进行夹套反应釜热传递选型计算时,需要根据具体的工艺参数和操作要求进行合理选择。
一般来说,夹套反应釜的热传递选型应满足工艺需要,并保证安全、高效、经济地对反应进行加热或冷却。
此外,计算中还需要考虑其他因素,如夹套反应釜的耐压性能、材料的选择、使用寿命等。
对于高温、高压或特殊工艺要求的夹套反应釜,还需要对设备进行合理选择和设计。
总之,夹套反应釜热传递选型计算方法是一个复杂的过程,需要综合考虑热传导、对流传热和辐射传热等因素,并根据具体要求进行合理选择。
只有通过合理的选型计算,才能保证夹套反应釜在操作过程中的高效、安全和稳定性能。
发酵罐的工艺计算

第一节 发酵罐的化工设计计算一、发酵罐的容积确定需要选用V 全=30m 3的发酵罐 则V 有效= V 全*Φ=30*80%=24m 3二、基础参数选择1、D :H :选用D :H=1:42、锥角:取锥角为7003、封头:选用标准椭圆形封头4、冷却方式:选取槽钢盘绕罐体的三段间接冷却(罐体两段,锥体一段,槽钢材料为A 3钢,冷却价质采用20%、-4℃的酒精溶液5、罐体所承受最大压力:2.5kg/cm 3 外压:0.3kg/cm 36、锥形罐材质A 3钢外加涂料,接管均用不锈钢7、保温材料:硬质聚氨酯泡沫塑料,厚度200mm8、内壁涂料:环氧树脂三、D 、H 的确定由D :H=1:4,则锥体高度H 1=D/2tg350=0.714D 封头高度H 2=D/4=0.25D圆柱部分高度H3=(4.0-0.714-0.25)D=3.04D 又因为V 全=V 锥+V 封+V 柱=3π342414232XH D D H D⨯+⨯+⨯⨯ππ =0.187 D 3+0.13 D 3+1.60 D 3=30 得D=2.23m查JB1154-74《椭圆形封头和尺寸》取发酵直径D=2400mm 再由V 全=30m 3,D=2.4m 得径高比为: D :H=1:3.32由D=2400mm 查表: 椭圆形封头几何尺寸为: h 1=600mm h 0=40mm F=6.52m 2 V=2.00m 3筒体几何尺寸为: H=5654mmF=7.55*5.654=42.69m 2 V=4.524*5.654=25,58m 3 锥体封头几何尺寸为: h0=40mm v=360mm H=2215mmF=22204.1064.0sin )3.07.0(4/m a COSa d =⎥⎦⎤⎢⎣⎡⎢⎣⎡++-πV=[]32375.372.0/)cos 3.07.0(24/m tga a d =++π 则:锥形罐体总高: H=600+5654+40+40+2215=8549mm总容积:V=2+25.58+3.75=31.33m 3 实际充满系数%6.7633.31/24=:ψ 罐内液柱高:mm H 27034022151044.275.32422=++⨯⨯-=')(π 四、发酵的强度计算(一)罐体为内压容器的壁厚计算1、标准椭圆封头设计压力为1.1*2.5=2.75kg/cm 2[]C pPDgS t+-=ϕσ2 式中:P=2.75kg/cm 2[]t σ:A3钢工作温度下的许用力取1520.kgcm 2ϕ:焊接系数,本例采用双面对接焊作为局部无探伤0.9壁厚附加量:C=C 1+C 2+C 3查表得:C 1 :钢板厚度的负偏差取0.8mm 负偏差C 2:腐蚀裕量取2mmC 2:制造减薄量取0.3mm则:mm S 814.54.375.29.015202240075.2=+-⨯⨯⨯=取S O =8mm直边高H O =40mm 校核⎭⎬⎫⎩⎨⎧=h D s PD 24中中σ =[]tσ≤=++12.369900*2)82400(*6*4)82400(*75.22、筒体2/42.361.05.2*1.1)(1.1cmkg P p p =+=+⨯=)(静工作没[]mmC C C C PPDS 2.62.342.39.0*1520*22400*42.3)6.0,2,6.0(2322=+-===+-=取ψσ取S=7mm 校核 []tsPD σψσ≤==0.58822中3、锥形封头1)过渡区壁厚[]CPDg KP S t+-=5.02ψσ没[]mmC PDgKP S K cm kg P t43.5369.026.0)74.3*5.09.0*1520*2/(2400*14.3*75.05.0275.0)9.0(/74.39.05.2*1.12=+++-=+-===+=ψσ没没为静压)( (2)锥体[][]13.759.026.094.394.3)60.0(74.3*5.09.0*15202400*74.3*60.05.0*5.0*=+++=+==-=-=+-=C S S f PPDgf S C PPDgf S O t O t查表为ψσψσ取S=8mm h 0=40mm校核锥体所受最大应力处:[]tS PD σσ≤=+==14.68735cos *10*2)82400(*74.335cos 20中(二)、锥体为外压容器的壁厚计算1、标准椭圆封头 设S O =5mmR 内=0.9D g =0.9*2400=2160mm R 内/100S o =21600/100x5=4.32 查图表4-1及B=2.75[]220/3.0/64.02160/575.2/*cm kg cm kg R S B P =⨯==内满足要求取C 1=0.5mm , C 2=2mm C 3=0.5mm 则S= S O +C=8mm2、筒体设S O =6mm L/D=0.69D=2400/6=600 查图表4-1及B=210[]]/3.0/35.02400/6*21022cm kg cm kg P ==S O =6mm故可取C 1=6mm , C 2=2mm ,C 3=0.6 则S=S O +C=9.2mm 取S=10mm3、锥形封头因为:6050.2235 αα所以=按第四章发酵罐设计的中封头设计可知,加强圈间中锥体截面积最大直径为:mm tg 6.1918352/274020=⨯⨯取加强圈中心线间锥体长度为1370mm 设S O =6mmL/D=1370/2400=0.57 D/SO=2400/6=400 图表表4-1及B=320[]mmS C S S mm C mm C mm C mmS cm kg D BS P 102.92.366.0,2,66/3.080.02400/6*320/0321020==+=+========取所以故取综合前两步设计,取两者中较大的有生产经验确定 标准椭圆型封头厚度为8mm h o =40mm 圆筒壁厚 10mm标准形封头壁厚 10mm h o =40mm五、锥形罐的强度校核1、内压校核液压试验P 试=125P 设由于液体实验的存在,锥体部分为罐体受压最重之处即最危险 设计压力实验P=1.25p=4.68/cm 2查得A3钢3/2400cm kg =σ可见符合强度要求,试压安全2、外压实验以内压代替外压故可知试压安全内试试P cm kg P p cm kg P 22/8.225.1/25.2)2.13.0(*5.1*5.1===+=3、刚度校核本例中允许S=2*2400/1000=4.8mm而设计时取壁厚为S=10mm ,故符合刚度要求 (公式:10002内最小D S =)第二节 发酵罐热工设计计算[][]试试试)(σψσσ 2/19442400**9.0*9.09.0/52.640)2.312(2)2.312(240068.4)(2cm kg cmkg C S C S Dg P ===--+⨯=--+=一、计算依据计采用A 3钢作发酵材料,用8号槽钢做冷却夹套,分三段冷却,筒体二段,锥部一段,夹套工作压力为2.5kg/cmp 2 冷媒为20%(V/V )酒精溶液,,为出进C T C T 002,4--麦汁发酵温度维持120(主发酵5-6天,封头及筒体部分保温层厚度为200mm ,锥底部分为98mm )二、总发酵热计算Q=q*v=119*24=2856kg/hrQ 每立方米发酵麦汁在闰发酵期间每小时的放热量; V 为发酵麦汁量三、冷却夹套型号选择选取8号槽钢起截流面为A=hb —截面积=8*4-10.24=24.16cm 2 冷却剂流量为(三段冷却) 3*24.16*10-4*1=7.284*10-3=m 3/s查得20%(V/V )酒溶液△t 平=-30C 下的 P=976kg/m 3Cp=1.04kcal/kg ●0 C 冷却剂的冷却能力为:Q=7.248X103X976X1.041X2X2400 =34430.8kcal/hr>8330kcal/hr 故可选取8号槽钢为冷却夹套。
夹套冷却时间计算

夹套冷却时间计算首先,我们需要确定夹套材料的热传导性质。
夹套材料的热传导性质定义了物质传热的速率,通常用热传导系数(k)来表示。
夹套材料的热传导系数可以通过实验测量或者查阅相关的资料得到。
接下来,我们需要确定夹套与被冷却物质之间的传热系数。
传热系数表示了夹套与被冷却物质之间传热的效率,它可以通过实验或者经验公式来估算。
传热系数的大小通常取决于夹套的设计和被冷却物质的物性等因素。
然后,我们需要确定被冷却物质的初始温度和终温度。
这两个参数将决定夹套冷却时间的长短。
初始温度可以通过测量或者实验得到,而终温度可以根据工艺需求或者产品性质来确定。
根据以上参数,我们可以使用经验公式或者数值模拟的方法来计算夹套冷却时间。
经验公式是基于已有实验数据和经验的一种快速估算方法。
常见的经验公式包括牛顿冷却定律和四尔维定律。
牛顿冷却定律的数学表达式为:(q/A)=(h∆T)其中,q是夹套的传热量,A是夹套的表面积,h是传热系数,∆T是夹套与被冷却物质之间的温度差。
四尔维定律是一种修正牛顿冷却定律的方法,它引入了物质的热容能力(Cp)。
四尔维定律的数学表达式为:(t-t0)/(t-t∞)=exp{-3/2hA/CpV}其中,t是时刻t的温度,t0是初始温度,t∞是夹套的终温度,h是传热系数,A是夹套的表面积,Cp是物质的热容能力,V是物质的体积。
另一种计算夹套冷却时间的方法是数值模拟。
数值模拟可以利用计算机进行模拟计算,可以更加精确地预测夹套冷却时间。
数值模拟通常使用传热学的基本方程,如热传导方程和对流传热方程。
这些方程可以通过有限元法、有限差分法或者其他数值方法进行求解。
除了以上方法,还可以通过实验测量夹套冷却时间。
实验可以在实际的生产线中进行,通过测量被冷却物质的温度随时间的变化来确定夹套冷却时间。
实验方法是最直接和可靠的,但同时也是最耗时和耗费资源的方法。
综上所述,夹套冷却时间的计算涉及多个参数和方法。
工程师可以根据具体的应用需求选择合适的计算方法,从而确定合理的夹套设计参数和运行条件,提高生产效率和产品质量。
关于反应釜夹套交替通入蒸汽和冷却水的注意事项

关于反应釜夹套交替通入蒸汽和冷却水的注意事项
反应釜夹套交替通入蒸汽和冷却水是一种常见的工业生产过程中的加热和冷却方式。
但是,在实际操作中,需要注意以下几点: 1. 确保安全。
在操作前,必须检查设备的安全性,确保夹套、管路等没有漏气、漏水等情况。
操作时必须严格遵守操作规程和安全措施,以免发生事故。
2. 控制加热和冷却速度。
在夹套交替通入蒸汽和冷却水时,需要控制加热和冷却速度,以免对设备造成损伤或者温度过高或过低影响产品质量。
3. 确保夹套内无水。
在反应釜夹套交替通入蒸汽和冷却水时,必须确保夹套内没有水,否则会引起爆炸或者设备损坏。
因此,在操作前要将夹套内的水排干净。
4. 控制压力和温度。
在操作过程中,必须控制好蒸汽和冷却水的压力和温度,以免导致设备压力过高或温度过低,影响设备的使用寿命和产品质量。
5. 定期检查设备。
反应釜夹套交替通入蒸汽和冷却水是一种常见的加热和冷却方式,但是设备长时间使用后会出现一些问题,因此需要定期检查设备,及时清洗和维修设备,以保证设备的正常运行和产品质量。
总之,在反应釜夹套交替通入蒸汽和冷却水的操作中,必须严格遵守操作规程和安全措施,控制好加热和冷却速度、压力和温度,保证设备的安全和产品质量。
搪瓷夹套的蒸汽计算公式

搪瓷夹套的蒸汽计算公式搪瓷夹套是一种常用的加热设备,用于在化工、医药、食品等行业中对液体进行加热或蒸发。
在使用搪瓷夹套进行加热时,需要对蒸汽进行计算,以确保加热效果和安全性。
本文将介绍搪瓷夹套的蒸汽计算公式及其应用。
搪瓷夹套的蒸汽计算公式可以通过以下步骤进行推导:1. 首先,我们需要确定搪瓷夹套的加热面积。
加热面积是指搪瓷夹套与被加热物料接触的表面积,通常以平方米为单位。
加热面积可以通过搪瓷夹套的尺寸和形状来计算得出。
2. 然后,我们需要确定被加热物料的温度变化。
被加热物料的温度变化是指被加热物料的初始温度和最终温度之间的差值,通常以摄氏度为单位。
3. 接下来,我们需要确定蒸汽的温度和压力。
蒸汽的温度和压力是影响加热效果的重要参数,可以通过蒸汽表或蒸汽表格来获取。
有了以上的基本参数,我们就可以使用以下的计算公式来计算搪瓷夹套的蒸汽需求:Q = m c ΔT。
其中,Q表示加热量,单位为焦耳(J)或千焦(kJ);m表示被加热物料的质量,单位为千克(kg);c表示被加热物料的比热容,单位为焦耳/千克·摄氏度(J/kg·°C);ΔT表示被加热物料的温度变化,单位为摄氏度(°C)。
通过上述公式,我们可以计算出搪瓷夹套所需的蒸汽量。
在实际应用中,我们还需要考虑到搪瓷夹套的传热效率、蒸汽的压力损失等因素,以确保加热效果和安全性。
除了计算搪瓷夹套的蒸汽需求外,我们还可以通过以下的公式来计算蒸汽的流量:G = Q / (λΔT)。
其中,G表示蒸汽的流量,单位为千克/小时(kg/h);λ表示蒸汽的焓值,单位为焦耳/千克(J/kg);ΔT表示被加热物料的温度变化,单位为摄氏度(°C)。
通过上述公式,我们可以计算出搪瓷夹套所需的蒸汽流量,以满足加热需求。
在实际应用中,我们还需要考虑到蒸汽的供应能力、输送管道的热损失、阀门的调节等因素,以确保蒸汽的稳定供应和加热效果。
总之,搪瓷夹套的蒸汽计算公式是加热过程中的重要工具,通过合理计算蒸汽需求和流量,可以确保加热效果和安全性。
水夹套工作原理

水夹套工作原理
水夹套是一种常用于化工、制药、食品等行业的加热或冷却设备,其工作原理是通过在容器外部套上一层密闭的管道,将流体(通常是水或其他冷却剂)流过管道,从而实现对容器内部物质的加热或冷却。
具体来说,水夹套的工作原理如下:
1. 加热:将加热介质(如蒸汽或电加热棒)引入水夹套内,使其加热,然后通过水夹套内的管道将热量传递给容器内的物质,从而实现加热作用。
2. 冷却:将冷却介质(如冷水或冷却剂)引入水夹套内,使其流过管道,从而吸收容器内物质的热量,然后将热量带走,实现冷却作用。
3. 温度控制:通过控制加热介质或冷却介质的流量、温度等参数,可以实现对水夹套内温度的精确控制,从而满足不同物质的加热或冷却需求。
总之,水夹套的工作原理是通过在容器外部套上一层密闭的管道,将流体流过管道,从而实现对容器内部物质的加热或冷却。