陶瓷材料的显微结构
陶瓷材料显微结构与性能

1陶瓷烧结过程中影响气孔形成的因素有哪些?(1)煅烧温度过低、时间过低 (2)煅烧是时原料中的水碳酸盐、硫酸盐的分解或有机物的氧化 (3) 煅烧时炉内气氛的扩散 (4) 煅烧时温度过高,升温过快或窑内气氛不合适等。
夏炎2.影响陶瓷显微结构的因素有哪些?参考答案:(1) 原料组成、粒度、配比、混料工艺等(2) 成型方式、成型条件、制品形状等(3)干燥制度(干燥方式、温度制度、气氛条件、压力条件等)(4) 烧成制度(烧成方式、窑炉结构、温度制度、气氛条件、压力条件等)3. 提高陶瓷材料强度及减轻其脆性有哪些途径?参考答案:a.制造微晶、高密度、高纯度的陶瓷。
例如,采用热等静压烧结制成的Si3N4气孔率极低,其强度接近理论值。
b.在陶瓷表面引入压应力可提高材料的强度。
钢化玻璃是成功应用这一方法的典型例子。
c.消除表面缺陷,可有效地提高材料的实际强度。
d.复合强化。
采用碳纤维、SiC纤维制成陶瓷/陶瓷复合材料,可有效地改善材料的强韧性。
e.ZrO2与增韧。
ZrO2对陶瓷的强韧化的贡献有四种机理(相变增韧、微裂纹增韧、裂纹偏转增韧、表面残余应力增韧)罗念4.影响氧化锆相变增韧的因素是什么?简单叙述氮化硅陶瓷具有的性能及常用的烧结方法。
①晶粒大小。
当晶粒尺寸大于临界尺寸易于相变。
若晶粒尺寸太小,相变也就难以进行。
②添加剂及其含量使用不同的添加剂, t-ZrO2的可转变最佳晶粒大小、范围也不同。
③晶粒取向。
晶粒取向的不同而影响相变导致增韧的机制。
氮化硅陶瓷具有高强度、高硬度、耐磨、耐化学溶液和熔体的腐蚀、高电绝缘体、低热膨胀和优良抗热冲击、抗机械冲击等性能。
烧结方法:反应烧结氮化硅、无压烧结氮化硅、重烧结氮化硅、气氛加压氮化硅和热压烧结氮化硅。
——李成5.气孔对功能陶瓷性能的影响及降低功能陶瓷中的气孔量的措施?气孔均可使磁感应强度、弹性模量、抗折强度、磁导率、电击穿强度下降,对畴运动造成钉扎作用,影响了铁电铁磁性。
谈陶瓷显微组织与材料性能之间的关系

谈陶瓷显微组织与材料性能之间的关系陶瓷材料的物理性能在很大程度上取决于其显微结构,在某些情况下甚至是决定性的,掌握它们之间的内在关系可以有针对性地优化制备工艺,从而提高陶瓷的物理性能。
陶瓷是多晶多相的材料,其显微组织包括:多晶相的种类,晶粒的大小、形态、取向和分布,位错、晶界的状况,玻璃相的形态和分布,气孔的形态、大小、数量和分布,各种杂质、缺陷、裂纹存在的开式、大小、数量和分布,畴结构的状态和分布等。
在显微镜下研究陶瓷材料的显微组织,找出其物相组成、组织、性能之间的联系和规律是发展新型陶瓷材料的基础。
陶瓷材料主要组成相为晶体相、玻璃相和气相。
研究陶瓷显微组织与性能之间的关系,就是要研究晶体相、玻璃相和气相分别对材料性能的影响。
研究这个问题有着重要的意义,主要有以下几点:(1)当我们了解了陶瓷显微组织与材料性能之间的关系后,我们就可以通过研究陶瓷的显微组织结构而对材料的性能做出评价。
(2)通过对陶瓷的结构缺陷的检测分析,从显微组织上找出其缺陷原因,我们可以提出改善或防止结构缺陷的措施。
(3)通过材料的显微组织研究,从材料物理化学的基本原理出发,为新材料的设计或材料改性提供依据或参考。
(4)研究工艺条件对显微组织的影响,通过优化生产工艺,提高材料的性能。
一、晶体相对材料性能的影响晶相是由原子、离子、分子在空间有规律排列成的结晶相。
晶相是决定陶瓷材料性能呢个的主导物相。
由于陶瓷是多晶材料,故晶相又可分为主晶相、次晶相、析出相和夹杂相。
此时主晶相就成为主导陶瓷性能的主导晶相。
主晶相是材料的主要组成部分,材料的性能主要取决于主晶的性质。
次晶相是材料的次要组成部分。
例如Si3N4材料中的颗粒状的六方结构的相β-Si3N4为主晶相;针状的菱方结构的α-Si3N4为次晶相,含量较少。
析出相,由粘土、长石、石英烧成的陶瓷的析出相大多数是莫来石,一次析出的莫来石为颗粒状,二次析出的莫来石为针状,可提高陶瓷材料的强度。
实验4陶瓷材料的显微结构分析

主要设备:日立S-3000N扫描电镜、超声清洗仪 耗 材:Al2O3等多晶功能陶瓷材料、Au金靶、导电胶等
电子束与固体的相互作用
电子束
电子 电动势
阴极荧光 特征X-射线
二次电子 俄歇电子 背散射电子
样品
吸收 电流
透射电子
扫描电镜工作原理图
电子枪
高压电源
聚光镜 扫描线圈
透镜电源
M = As/Ac 由于扫描电子显微镜的荧光屏尺寸是固定不变的,电子束在样 品上扫描一个任意面积的矩形时,在阴极射线管上看到的扫描 图像大小都会和荧光屏尺寸相同。因此我们只要减少镜筒中电 子束的扫描幅度,就可以得到高的放大倍数,反之,若增加扫 描幅度们,则放大倍数就减小。90年代后期生产的高级扫描电 子显微镜放大倍数可以从数倍到80万倍左右。
思考题
(1) 扫描电镜使用时为何要抽真空? (2) 对于非金属样品,用扫描电镜观察前为何需在样品表面 喷镀一层金属?
金属材料断口SEM图
(a) 沿晶断裂
(b) 穿晶断裂
掺硼金刚石薄膜SEM图
LiCoO2和Al,Zr掺杂LiCoO2材料SEM图
(a) 未掺杂
(b) 掺杂
人体组织SEM图
(a) 味 蕾
实验四 陶瓷材料的显微结构分析
一.实验目的与内容
1显微镜基本构造和使用方法
二.实验基本原理
电子枪发射并经过聚焦的电子束在样品表面逐点扫描,激发样 品产生二次电子、背散射电子、透射电子、特征X射线、俄歇电 子等各种物理信号。这些信号经检测器接收、放大并转换成调制 信号,最后在荧光屏上显示反映样品表面各种特征图像。
聚光镜:共有三对,前两对为强磁透镜,起缩小电子束光斑用, 第三对为弱磁透镜,又称物镜,焦距较长。扫描电镜中电子束直 径越小,成像单元的尺寸越小,相应的分辨率就越高。
陶瓷材料的显微组织作用及其功能

陶瓷材料的显微组织作用及其功能下载提示:该文档是本店铺精心编制而成的,希望大家下载后,能够帮助大家解决实际问题。
文档下载后可定制修改,请根据实际需要进行调整和使用,谢谢!本店铺为大家提供各种类型的实用资料,如教育随笔、日记赏析、句子摘抄、古诗大全、经典美文、话题作文、工作总结、词语解析、文案摘录、其他资料等等,想了解不同资料格式和写法,敬请关注!Download tips: This document is carefully compiled by this editor. I hope that after you download it, it can help you solve practical problems. The document can be customized and modified after downloading, please adjust and use it according to actual needs, thank you! In addition, this shop provides you with various types of practical materials, such as educational essays, diary appreciation, sentence excerpts, ancient poems, classic articles, topic composition, work summary, word parsing, copy excerpts, other materials and so on, want to know different data formats and writing methods, please pay attention!1. 引言陶瓷材料作为一类重要的工程材料,在各个领域中有着广泛的应用。
陶瓷的显微结构及性能课件

生物陶瓷 生物陶瓷具有良好的生物相容性和耐腐蚀性,在生物医疗 领域有广泛应用,如人工关节、牙齿等。
环保与可持续发展
1 2 3
降低能耗 陶瓷产业是高能耗产业,通过技术进步和产业升 级,降低陶瓷产业的能耗,有利于环境保护和可 持续发展。
陶瓷在医疗领域中用于制造人工关节、牙 科材料等,如人工关节置换材料、牙齿修 复材料等。
CHAPTER 02
陶瓷的显微结构
陶瓷的晶体结构
01
02
03
晶体结构定义
陶瓷的晶体结构是指陶瓷 内部质点的排列方式,包 括原子、分子的位置和排 列顺序。
晶体结构的分类
根据原子排列的规律性, 陶瓷的晶体结构可分为晶 体和玻璃相两大类。
原料处理
对原料进行破碎、混合、干燥等处 理,以保证其均匀性和稳定性。
成型工 艺
塑性成型
利用黏土的可塑性,通过压滤、 挤压、注浆等工艺成型。
干压成型
将粉末状原料在模具中加压成型, 适用于形状复杂的陶瓷部件。
热压成型
在加热条件下加压成型,适用于 热塑性陶瓷材料。
烧成工艺
烧成温度
控制烧成温度,以实现陶瓷的完全烧结和性能优化。
晶体结构的稳定性
晶体结构的稳定性决定了 陶瓷的力学性能、热学性 能和化学稳定性等。
陶瓷的显微组织
显微组织的定义
陶瓷的显微组织是指陶瓷中晶粒的大 小、形状、分布和晶界特征等。
显微组织与性能关系
陶瓷的显微组织对其力学性能、热学 性能、电学性能和磁学性能等均有影 响。
显微组织的影响因素
陶艺(第八章)-显微结构与性质1
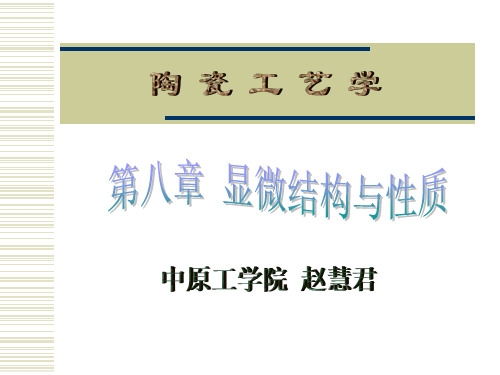
锡乳浊釉
公元前6~9世纪,中东地区就已经出现了应用在
内墙砖上的锡乳浊釉。
锡乳浊釉的显微结构是釉层中均匀分布着一定数
量的SnO(折射率高达1.99~2.09,比基础釉玻璃 的折射率要高出40%~50%)晶体。
也有人认为在釉中除了含有SnO,还含有锡榍石
(CaO· SiO2),两者共同起作用。 SnO·
根据对釉层透光度的研究可知:釉的失透与乳浊相
折射率的大小,乳浊相粒子大小、数量、分布均匀程 度等有关。
根据乳浊剂的名字分类
锆乳浊釉 锡乳浊釉 钛乳浊釉
锆乳浊釉
在釉中残留或析出锆化合物晶体,使得釉层
失透,形成乳浊。
当锆釉中的乳浊相为锆石时,其乳浊效果最
佳;当锆釉中的乳浊相为锆英石与锆石时, 乳浊效果好;当锆釉中的乳浊相为锆英石时, 其乳浊效果较好。
显微结构中各物相的作用
莫来石:普通陶瓷的主晶相,是瓷坯内 部的骨架。莫来石的种类、大小、分布等 对瓷坯的强度有明显的影响。 瓷坯中的莫来石分别由粘土形成和从玻璃 相析出(针状,交织成网)。
显微结构中各物相的作用
玻璃相:环绕在石英颗粒周围的熔有石 英的高硅玻璃相,α小;中间生长有交织 成网的莫来石晶体的长石玻璃相;在粘土 分解产物区内,填充在粘土残骸(一次鳞 片状莫来石)间的玻璃相。
(一)气相乳浊釉
一般釉玻璃相的折射率为1.5左右,气体的
折射率一般为1.3左右,两者之间存在差距, 可以构成乳浊,直径小于0.1mm的釉泡会使釉 层混浊不透明。气泡尺寸大到肉眼能分辨时, 会使釉面产生暗哑的光泽而失去美感。要使 釉层中产生多而细小分布均匀的气泡在工艺 上较为因难,且会因气泡多影响釉面硬度。 一般不采用气体来实现釉面乳浊。
陶瓷材料的显微结构PPT课件
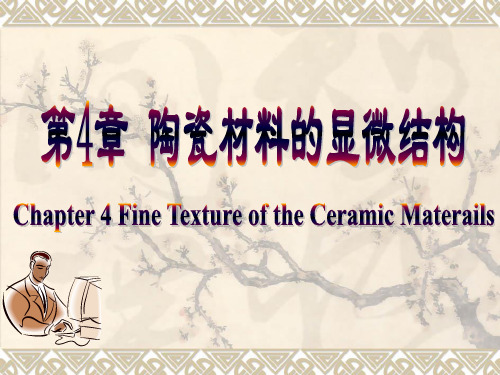
m-ZrO2
1150℃ 950℃
t-ZrO2
2370℃ c-ZrO2
➢ t-ZrO2 到 m-ZrO2 马 氏 体 相 变 伴 随 有 相 当 大 的 剪 切 应 变 ( 约 8%) 和体积增加(3%~5%)
➢ 施加压应力可抑止t-ZrO2的相变; ➢ 添加Y2O3、MgO和CeO2等稳定剂以降低相变温度,而使t-ZrO2
细孔
与
分
布
微孔
粒状
柱状
晶 柱粒状
粒 形
针状
态 网络状
特 征
斑状
树枝状
放射状 片状
对
陶 反应结构
瓷 中
定向结构
某 缺陷结构
些
特 欠烧或过烧结构
殊
结 壳芯结构
构 的
分相结构
综 复合结构
合
分 电(磁)畴结构
析
晶界与晶界相
§4.2 含缺陷陶瓷材料的显微结构
一、制备过程产生的缺陷
1、大孔径的孔隙 2、不纯原料 3、异常大晶粒 4、团聚 5、第二相夹杂物
由表面,直到材料断裂,从而提高了陶瓷的断裂韧性与强度。
②微裂纹分支增韧
主裂纹沿最大张应力的垂直方 向扩展,由于相变而受阻中断,裂 纹只能在偏离45o方向产生分支,也 相当于在剪应力方向再度扩展。
③微裂纹增韧
材料制备过程中,由高温降至 低 温 时 , 一 些 晶 粒 的 t-ZrO2 自 发 地 相变到m-ZrO2,产生微裂纹,使材 料增韧。
99%瓷→1700℃。
二次重结晶,导致局部晶粒 易于长大。
原料本身不均匀; 成型时的压力因素; 烧成温度偏高; 局部不均匀的液相存在。
异常显微结构,晶粒大小分 布显著不均匀。
陶瓷相的成分及其作用

陶瓷相的成分及其作用
陶瓷是把粘土原料、瘠性原料及熔剂原料经过适当的配比、粉碎、成型并在高温焙烧情况下经过一系列的物理化学反应后,形成的坚硬物质。
常用陶瓷材料主要包括:金属(过渡金属或与之相近的金属)与硼、碳、硅、氮、氧等非金属元素组成的化合物,以及非金属元素所组成的化合物,如硼和硅的碳化物和氮化物。
根据其元素组成的不同可以分为:氧化物陶瓷、氮化物陶瓷、碳化物陶瓷、硅化物陶瓷和硼化物陶瓷。
此外,近年来玻璃陶瓷作为结构材料也得到了广泛的应用。
陶瓷材料的显微结构:陶瓷主要由晶相(基本成分)、玻璃相(非晶态低熔点固体相,一般为20~40%,特殊20~60%)、气相(烧结过程中内部留下的孔洞,一般5~10%,特殊(多孔)~60%)组成。
晶相的结构、数量、形态和分布决定了陶瓷材料的主要性能和应用,晶相对陶瓷材料的物理性能有直接影响。
例如氧化铝陶瓷的性能与其主晶相刚玉(α-Al2O3)含量关系极大:晶粒的尺寸也是影响陶瓷材料性能的重要因素,一般细晶粒可以阻止裂纹的扩展,提高材料的导热系数,使材料绝缘性能下降。
玻璃相的作用:(1)起粘接剂和填充剂的作用,玻璃相是一种易熔相,可以填充晶粒间隙,将晶粒粘接在一起,使材料致密化;(2)降低烧成温度,加快烧结过程;(3)阻止晶型转变,抑制晶粒长大,使晶粒细化;(4)增加陶瓷的透明度等。
气相的多少、大小、形状、分布都会对陶瓷材料产生很大的影响,
除了多孔陶瓷外,气相的存在都是不利的,气孔的存在会使材料的密度、机械强度下降,直接影响材料的透明度,同时,大量气孔的存在会使陶瓷材料绝缘性能降低,介电性能变差,但是气孔多的陶瓷材料表面吸附性能及隔热性能好,利于涂层等。
陶瓷工艺学试题库(完整版)
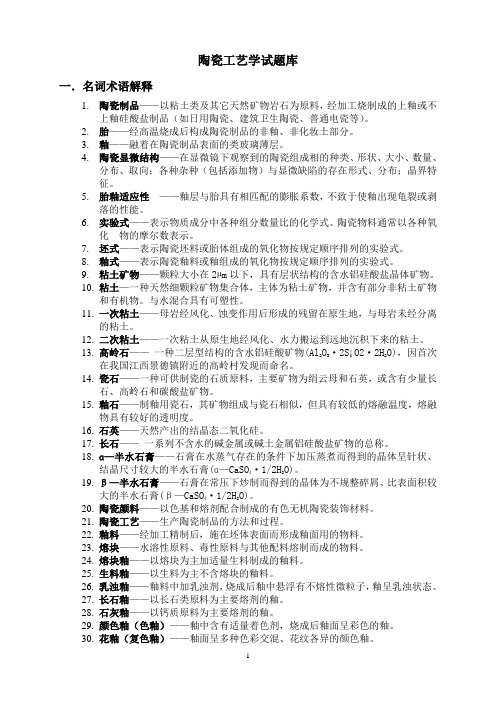
陶瓷工艺学试题库一.名词术语解释1.陶瓷制品——以粘土类及其它天然矿物岩石为原料,经加工烧制成的上釉或不上釉硅酸盐制品(如日用陶瓷、建筑卫生陶瓷、普通电瓷等)。
2.胎——经高温烧成后构成陶瓷制品的非釉、非化妆土部分。
3.釉——融着在陶瓷制品表面的类玻璃薄层。
4.陶瓷显微结构——在显微镜下观察到的陶瓷组成相的种类、形状、大小、数量、分布、取向;各种杂种(包括添加物)与显微缺陷的存在形式、分布;晶界特征。
5.胎釉适应性——釉层与胎具有相匹配的膨胀系数,不致于使釉出现龟裂或剥落的性能。
6.实验式——表示物质成分中各种组分数量比的化学式。
陶瓷物料通常以各种氧化物的摩尔数表示。
7.坯式——表示陶瓷坯料或胎体组成的氧化物按规定顺序排列的实验式。
8.釉式——表示陶瓷釉料或釉组成的氧化物按规定顺序排列的实验式。
9.粘土矿物——颗粒大小在2µm以下,具有层状结构的含水铝硅酸盐晶体矿物。
10.粘土—一种天然细颗粒矿物集合体,主体为粘土矿物,并含有部分非粘土矿物和有机物。
与水混合具有可塑性。
11.一次粘土——母岩经风化、蚀变作用后形成的残留在原生地,与母岩未经分离的粘土。
12.二次粘土——一次粘土从原生地经风化、水力搬运到远地沉积下来的粘土。
13.高岭石——一种二层型结构的含水铝硅酸矿物(Al2O3·2S¡O2·2H2O),因首次在我国江西景德镇附近的高岭村发现而命名。
14.瓷石——一种可供制瓷的石质原料,主要矿物为绢云母和石英,或含有少量长石、高岭石和碳酸盐矿物。
15.釉石——制釉用瓷石,其矿物组成与瓷石相似,但具有较低的熔融温度,熔融物具有较好的透明度。
16.石英——天然产出的结晶态二氧化硅。
17.长石——一系列不含水的碱金属或碱土金属铝硅酸盐矿物的总称。
18.ɑ—半水石膏——石膏在水蒸气存在的条件下加压蒸煮而得到的晶体呈针状、结晶尺寸较大的半水石膏(ɑ—CaSO4·1/2H2O)。
口腔材料学-陶瓷材料基本知识

2、物理性能和化学性能 (1) 热性能:陶瓷的熔点高。
(2)电性能:可用作绝缘材料。 (3)化学稳定性:结构稳定,对酸、碱、盐有良好的抗蚀 能力。 (4)美观性能:表面光泽度高,具有透明和半透明性,与 真牙极为相似,具有优秀的审美性。 3、生物性能 化学稳定性赋予陶瓷良好的生物惰性和生物相 容性,无毒、无味、无刺激,耐人体体液腐蚀。
金属烤瓷和全瓷透光性对比
二、白榴石增强长石质烤瓷 1、组成 组成上与金属烤瓷材料相似,含有更多的白榴
石增强晶相,体积含量为35%~45%,均匀分散。白榴石晶相 强度较高,可阻止玻璃相中裂纹的扩展或者使裂纹方向偏转, 增强强度。
2、性能 白榴石增强长石质烤瓷的弯曲强度可达 104MPa,断裂韧性为1.5MPa·m1/2,压缩强度也较高。白榴 石的线胀系数大,这种差异造成瓷在冷却时白榴石晶体周 围的玻璃基质中产生切向压缩应力,起到了裂纹挡板的作 用,可提高脆弱的玻璃相抗裂纹扩展的能力。
(3)低拉伸强度、弯曲强度和较高的压缩强度:陶瓷的 实际拉伸强度要比金属低很多。陶瓷在受压时,气孔等缺 陷不易扩展成宏观裂纹,压缩强度较高。对陶瓷表面进行 处理,减少表面缺陷或在表面造成残余压应力层,可以有 效地提高陶瓷强度。测定陶瓷的弯曲强度表示其强度,同 时反映拉伸强度和压缩强度。
(4)优良高温强度和低抗热震性:陶瓷的熔点高于金属。 陶瓷在高温下不仅保持高硬度,而且基本保持其室温下的 强度,具有高的蠕变抗力,同时抗氧化性能好。当温度剧 烈变化时容易破裂,烧结和使用时要加以注意。
2、玻璃晶化法 玻璃在高温熔化后具有良好的流动性, 可浇铸成任意形状的铸件,置于特定温度下进行结晶化处理, 使玻璃中析出大量的晶体而转变为陶瓷结构,这种制备陶瓷 的方法称为玻璃晶化法,陶瓷质地致密,具有较高的强度, 称为玻璃陶瓷(glass-ceramics)或微晶玻璃 (microcrystalling glass)。
陶瓷工艺学---第四章 陶瓷的显微结构与性质
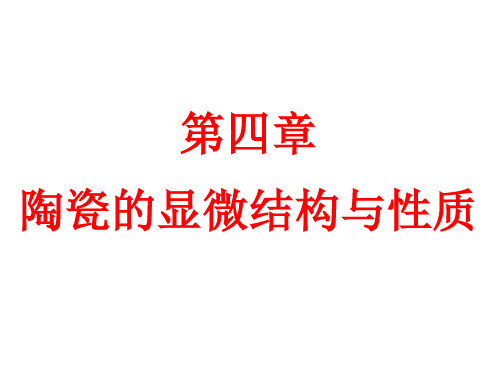
5.高温色釉 5.1 青釉 是我国历史上最早出现的颜色釉。各地青釉质感不同,原因 是釉层结构不同。 1)钧窑青釉 釉面乳浊 高硅质釉中含有磷酸盐,产生液-液分相乳浊。 2)龙泉青瓷、汝官窑青瓷、枢府青白瓷釉 3)临汝青釉瓷 透明 釉面乳浊 高铝低硅釉玻璃中含有小气泡和细小钙长石晶体产生乳浊。
釉层中无晶体析出,只有少量大气泡存在。
晶相强度 > 普通玻璃相强度 减少玻璃相的含量,提高玻璃相的强度,瓷坯的强度提高。 特种陶瓷生产,对于添加剂形成的少量玻璃相进行晶化处理。
1.5 气相对强度的影响
通过对多孔陶瓷的研究,得到气孔率与强度的关系。
经验公式:
= 0 exp( p)
式中:P——气孔率,%;
0——P=0时的强度,Mpa;
铝质瓷中引入氧化镁0.5~1%。
3)晶型与晶粒形貌对强度的影响
常温下的晶型转变,导致瓷坯的强度降低;
一种晶体以不同的晶型存在时,晶体的形状不同,强度不同; 一种晶体以不同的形状(球形、柱状)存在,瓷坯强度不同;
4)晶界对强度的影响
晶界愈多,抑制裂纹的扩展,界面上如有气孔降低强度。
1.4 玻璃相对强度的影响
=Kd
式中:K——与晶体结构及材料显微结构有关的比例常数。
d——晶粒直径。
——与材料特性和实验条件有关的经验常数。 =1/8~1 随d的增大而增大。 P254~255表4-21、图4-32、4-33 各种陶瓷材料强度与粒径关系
细晶粒提高强度机理:
1. 晶粒愈细小,比表面积愈大,晶界愈多,裂纹扩展阻力愈大
第四章 陶瓷的显微结构与性质
主要内容
1.坯体的显微结构
2.釉层的显微结构 3.釉层的物理化学性质
4.陶瓷性能的控制
陶瓷材料的显微结构

②微裂纹分支增韧
主裂纹沿最大张应力的垂直方 向扩展,由于相变而受阻中断,裂 纹只能在偏离45o方向产生分支,也 相当于在剪应力方向再度扩展。 ③微裂纹增韧 材料制备过程中,由高温降至 低温时,一些晶粒的t-ZrO2 自发地 相变到m-ZrO2 ,产生微裂纹,使材 料增韧。
(2)影响相变增韧的因素
四、陶瓷复合材料
(1)颗粒弥散增强复合材料
ZrO2起相变韧化与裂纹转向韧化作用
(2)纤维补强增韧复合材料
①长纤维增韧
②短纤维(或晶须)增韧
热压方法制备,晶须排列有 一定的择优取向,界面结合 良好,晶须分布比较均匀
③颗粒与短纤维复合增韧
兼有ZrO2 粒子相变增 韧与短纤维韧化作用。
(3)陶瓷基复合材料的界面
m-ZrO2
1150℃ 950℃
t-ZrO2
2370℃
c-ZrO2
t-ZrO2 到m-ZrO2 马氏体相变伴随有相当大的剪切应变(约8%) 和体积增加(3%~5%) 施加压应力可抑止t-ZrO2的相变; 添加Y2O3 、MgO和CeO2 等稳定剂以降低相变温度,而使tZrO2在室温时处于亚稳定状态。
③复合材料的界面设计
目的:调整增强体与基体之间物理与化学的 相容性,充分地发挥增强体的增韧补强效应。 途径: a. 正确选择增强相与基体,使它们能够形成 一种热力学稳定的界面; b. 增强体的表面改性:表面涂层、酸洗、表 面热处理等。
表面涂层
合理的涂层能有效地调节界面 的残余应力,抑制界面的化学 反应,改善界面的结合状态
相同蠕变条件下:1300℃,250MPa,100h YL-a(晶界宽度1nm); YL-b(晶界宽度2.5nm) YL-b的蠕变量为YL-a的2.4倍
陶瓷材料的显微结构

相组成:晶相、玻璃相、气相
晶形:每一种晶体在形成、长大的过程中,往往习 惯地、自发地按一定的规律生长和发育成一 定的几何形态。
这种习惯称为结晶习性。
自形晶:先结晶的晶体在较好的环境下生长,即在有利于按其 本身的结晶习性的环境中生长发育的,而形成晶形完整 的晶体。
• Al2O3含量↑,玻璃相↓。 • Al2O3含量↑,烧成温度↑。95%瓷→1600℃;
99%瓷→1700℃。
二次重结晶,导致局部晶粒 易于长大。
原料本身不均匀; 成型时的压力因素; 烧成温度偏高; 局部不均匀的液相存在。
异常显微结构,晶粒大小分 布显著不均匀。
与添加剂的选用与加入量不 当有关
2、ZrO2陶瓷
与应力诱导相变不 同,后者在相变开 始点周围应力变化 较大处产生,因此 成核相变可能是应 力诱导相变的先兆。
1、大孔径的孔隙 2、不纯原料 3、异常大晶粒 4、团聚 5、第二相夹杂物
二、高温缺陷
温度↑,陶瓷的强度↓ ➢高温破坏:广泛分布的显微结构 损伤的积累过程; ➢室温破坏:已经存在的裂纹的突 然破坏所致。
高温下损伤的形成与材料承受蠕变或蠕 变破坏的能力有关。 与高温强度有关的重要因素— 晶界相
I. 烧结助剂如MgO等与Si3N4中的SiO2杂质 反应形成硅酸盐液相;
③微裂纹增韧
材料制备过程中,由高温降至 低 温 时 , 一 些 晶 粒 的 t-ZrO2 自 发 地 相变到m-ZrO2,产生微裂纹,使材 料增韧。
(2)影响相变增韧的因素
①晶粒大小
I. ZrO2相变增韧材料中存在临界晶粒尺寸; II. 晶粒尺寸大于临界尺寸时,易于相变,冷却过程中,伴随相
陶瓷材料力学性能.

第一节 陶瓷材料的结构
• 陶瓷材料的组成与结合键
负电性所体现的是一个原于吸住电子的能力,元素的负电性与其在 周期表中的位置有关,大约当负电性差∆X<0.4~0.5时,对形成固溶 体有利,当∆X增大时,则形成化合物的倾向增大。
• 陶瓷材料的显微结构
• 陶瓷材料由晶相、玻璃相和气孔组成。 • 如果玻璃相分布于主晶相界面,在高温下陶瓷材 料的强度下降,易于产生塑性变形。 • 气孔率增大,陶瓷材料的致密度降低,强度及硬 度下降。
第五节 陶瓷材料的断裂韧度与增韧
• 陶瓷材料的断裂韧度
1.单边切口梁法
• • • •
优点: (1) 数据分散性好; (2) 重现性好; (3) 试样加工和测定方法比较简单,是目前 广泛采用的一种方法。 • 缺点: • 测定的KIC值受切口宽度影响较大,切口宽 度增加, KIC增大,误差随之增大。 • 如果能将切口宽度控制在0.05~0.10mm以 下,或在切口顶端预制一定长度的裂纹, 可望提高KIC值的稳定性。
3.压痕法
• 测试过程:用维氏或显微硬度压头,压入 抛光的陶瓷试样表面,在压痕时对角线方 向出现四条裂纹,测定裂纹长度,根据载 荷与裂纹长度的关系,求出KIC值。
• 优点:测试方便,可以用很小的试样进行多点韧度测试, 但此法只对能产生良好压痕裂纹的材料有效。 • 缺点:由于裂纹的产生主要是残余应力的作用,而残余应 力又是因为压痕周围塑性区与弹性基体不匹配引起的。因 此,这种方法不允许压头下部材料在加载过程中产生相变 或体积致密化现象,同时压痕表面也不能有碎裂现象。
材料力学性能
第十章 陶瓷材料的力学性能
• 陶瓷材料广泛应用于我们的日常生活,它和金属材料、 高分子材料并列为当代三大固体材料之一。 • 传统的陶瓷制品以天然粘土为原料,通过混料、成型 烧结而成,性能特点是强度低、脆性高。 • 工程陶瓷的力学性能是耐高温、硬度高、弹性模量高、 耐磨、耐蚀、抗蠕变性能好。
陶瓷坯体的显微结构特征—陶瓷显微结构分析

(2010-08-06 11:44:39)
陶瓷坯体的显微结构特征
制品的坯体显微结构取决于原料颗粒的大小形状、各相的数量、性质和气孔率等。
经烧结而形成的制品坯体,是由晶相、玻璃及气相构成,这些相的数量比就是制品坯体的相组成,它决定着制品的物理性质。
瓷体玻璃相中,穿插着许多细小莫来石 晶体。在长石熔体分布区域中,针状莫来石长达10~12μm,在个别区域中可达20~40μm莫来石排成密网状,很少遇见凸粒状的。瓷器中玻璃莫来石的含量波动范围很宽:在软质瓷中可达80%;而在硬质瓷中则可降低到66%;在化学瓷中可降到45%;在精陶中则更少,主要是细小莫来石晶体,未见到针状莫来石晶体。
三、 气相
气相是瓷器坯体中第三个组成部分。瓷坯中总是会有闭口气孔的,所有这些气孔皆充满了气相。
气相的来源是:空隙中含有空气,脱水反应、离解反应和脱碳作用产生的气体,原料中经常存在的硫酸盐和硫化物及其他矿物成因分解产生的气体,原料中氧化还原以及原料中的有机残留物和空隙中炭黑经过氧化而产生的气体,坯体组分在熔融过程中及其他过程中释放出气体。
在950~1050℃烧成的彩陶制品中,玻璃相含量总共有8%~10%,未发现莫来石。
ቤተ መጻሕፍቲ ባይዱ
玻璃相对陶瓷坯体物理技术性质的影响,不仅取决于其数量及物理化学性质,而且还与玻璃相同晶相之间的比例有关。瓷器的基本性质,包括机械强度在内,主要取决于玻璃相中产生的应力;在较程度上,也与形成莫来石晶体的数量和大小有关。玻璃相能给瓷器以透光性,但也能降低其白度和热稳定性。当莫来石化程度较差、针状晶体较小、晶体交织程度较大时,瓷器坯体的机械强度就比较高。
精陶坯体中莫来石晶体不同于在瓷器中所见到的莫来石晶体,它们细而分散,只有通过X身线分析才能鉴别出来。
- 1、下载文档前请自行甄别文档内容的完整性,平台不提供额外的编辑、内容补充、找答案等附加服务。
- 2、"仅部分预览"的文档,不可在线预览部分如存在完整性等问题,可反馈申请退款(可完整预览的文档不适用该条件!)。
- 3、如文档侵犯您的权益,请联系客服反馈,我们会尽快为您处理(人工客服工作时间:9:00-18:30)。
相同蠕变条件下:1300℃,250MPa,100h YL-a(晶界宽度1nm); YL-b(晶界宽度2.5nm) YL-b的蠕变量为YL-a的2.4倍
(3)重烧结Si3N4
反应烧结+更高温度烧结
低温氮化后,经1atmN2 压 力,1850℃,2h,室温抗 折强度550MPa
Si3N4烧结温度高,接近其挥发分解温度(1890℃); 常压下,提高烧成温度增加致密度比较困难; 发展了一种新工艺———气氛加压烧结工艺; 提高了烧成温度,抑制了烧成过程中的挥发与分解,制备出性能 优良的陶瓷材料
温度↑,陶瓷的强度↓ 高温破坏:广泛分布的显微结构 损伤的积累过程;
室温破坏:已经存在的裂纹的突 然破坏所致。
高温下损伤的形成与材料承受蠕变或蠕 变破坏的能力有关。 与高温强度有关的重要因素— 晶界相
I. 烧结助剂如MgO等与Si3N4中的SiO2 杂质 反应形成硅酸盐液相; II. 冷却过程中,这些促进烧结致密的液相形 成玻璃相驻留在晶界上,形成一层薄的非 晶态层(约1nm); III.材料在高温下(高于晶界玻璃相的转变温 度)受力时,由于蠕变裂纹的生长而破坏; IV.晶界玻璃相成为物质的快速传递区,导致 蠕变孔穴的迅速形成; V. 网状裂纹扩展并最终相互连接,导致材料 完全破坏。
他形晶:较迟结晶的晶体,在受抑制情况下生长发育,形成晶 形很不完整的晶体。
97瓷中刚玉半自形晶结构 莫来石陶瓷中莫来石 1、自形晶;2、半自形晶;3、他形晶 日用陶瓷中石英晶体受到熔 陶瓷自形晶的结构 蚀后呈他形晶结构
多晶体的晶形
§4.1 陶瓷显微结构类型
瓷 坯 中 晶 质 和 非 晶 质 的 含 量 全晶质 主 晶 相 的 晶 粒 尺 度
低温氮化后,经15atmN2 压 力,1950℃,2h,室温强度 750MPa,硬度HRA91~92
以Y2O3、AlN、Al2O3为添加剂, 室 温 强 度 850MPa , KIC 为 8.5MPa· 1/2 m
(4)热压Si3N4 热压Si3N4 是目前性能最好的Si3N4 材料,室温 强 度 950MPa , KIC 为 10MPa· 1/2 , 硬 度 m HRA93~94
注:在某些应力与应变速率条件下, 裂纹尖端后面的玻璃薄层未受损伤, 则可以限制裂纹的生长速率。
高温形变产生的孔穴和裂纹倾向 于沿所受应力的方向排列
高温下孔隙同样可以在没有外加应力 的作用下产生。 样品开始是完全致密的,但在氧化处 理过程中由于晶界孔隙的形成发生肿 胀。
孔隙的产生是由于扩散进入的氧与被 截留在晶界上的碳杂质反应生成CO 气体所致。
(5)自补强Si3N4
基体:1μm左右细小的β-Si3N4;
中间分布物:长须状α-Si3N4、四方相晶体(含La化合物)
三、多相复合陶瓷
当第二相TiC粒子从7μm下降到0.8 μm, 强度从418增加到586MPa
TiC与基体SiC之间存 在较大的热膨胀系数 与弹性模量差,在基 体中产生压缩应力; 裂纹扩展到TiC周围时, 与应力互作用造成裂 纹偏折或绕道,从而 提高断裂能。
四、陶瓷复合材料
(1)颗粒弥散增强复合材料
ZrO2起相变韧化与裂纹转向韧化作用
(2)纤维补强增韧复合材料
①长纤维增韧
②短纤维(或晶须)增韧
热压方法制备,晶须排列有 一定的择优取向,界面结合 良好,晶须分布比较均匀
③颗粒与短纤维复合增韧
兼有ZrO2 粒子相变增 韧与短纤维韧化作用。
(3)陶瓷基复合材料的界面
③复合材料的界面设计
目的:调整增强体与基体之间物理与化学的 相容性,充分地发挥增强体的增韧补强效应。 途径: a. 正确选择增强相与基体,使它们能够形成 一种热力学稳定的界面; b. 增强体的表面改性:表面涂层、酸洗、表 面热处理等。
表面涂层
合理的涂层能有效地调节界面 的残余应力,抑制界面的化学 反应,改善界面的结合状态
(2)无压烧结Si3N4 Si3N4 粉+烧结助剂→陶瓷材料(1800℃以上温度) 由长柱状和短柱状两种晶形组 成,晶粒发育完好,相互交织, 形成结构致密的材料,室温强 度达到600~700MPa。
由长柱状型和等轴状α型 两种晶粒组成
选择合适添加剂,形成具有高熔点、高耐火度的晶界玻璃相; 净化晶界,生成Si3N4固溶体; 通过氧化,改变晶界玻璃相组成以提高玻璃相耐熔度; 进行适当热处理,使晶界玻璃相析晶出具有高耐火度的晶体。
(1)相变增韧机制
①应力诱导相变增韧
I. II. III. IV.
Y-TZP受外力时首先产生微裂纹; 裂纹尖端产生张应力,t-ZrO2产生应力松弛,则产生相变,成为m-ZrO2 ; 相变产生体积膨胀和剪切应变,引起的压应力抵消了外力造成的张应力, 从而阻止裂纹进一步延伸, t-ZrO2相变中止; 只有施加更大的外力才能使相变继续进行,裂纹继续扩展,形成新的自 由表面,直到材料断裂,从而提高了陶瓷的断裂韧性与强度。
界面的性质 物理相容性:基体与增强体之间的弹性模量与热膨胀系数是否匹配; 化学相容性:基体与增强体之间是否存在化学反应或界面反应层。
界 面 的 结 合 状 态
物理结合:结合力为弱化学键(氢键与范德华力), 键能8×102~2.1×104J/mol
化学结合:强化学键,8×102~2.1×104J/mol
显微结构:显微镜下所观察到物质的相种类、大小、 形态和物相之间的相互的结合状况。 相组成:晶相、玻璃相、气相
晶形:每一种晶体在形成、长大的过程中,往往习 惯地、自发地按一定的规律生长和发育成一 定的几何形态。 这种习惯称为结晶习性。
自形晶:先结晶的晶体在较好的环境下生长,即在有利于按其 本身的结晶习性的环境中生长发育的,而形成晶形完整 的晶体。 半自形晶:较迟结晶的晶体,在较差的生长环境下生长发育, 形成晶形部分完整的晶体。
①晶粒大小 I. II. ZrO2相变增韧材料中存在临界晶粒尺寸; 晶粒尺寸大于临界尺寸时,易于相变,冷却过程中,伴随相 变产生微裂纹,甚至大裂纹;
III. 晶粒尺寸太小,相变难以进行,起不到增韧作用;
IV. 因此控制晶粒大小成为获得性能优良的相变增韧材料的关键。
②添加剂及其含量
使用不同的添加剂,t-ZrO2的可转变最佳晶粒 大小、范围也不同。如12%CeO-TZP 的最佳晶粒 大小可证实为4-5μm
②微裂纹分支增韧
主裂纹沿最大张应力的垂直方 向扩展,由于相变而受阻中断,裂 纹只能在偏离45o方向产生分支,也 相当于在剪应力方向再度扩展。 ③微裂纹增韧 材料制备过程中,由高温降至 低温时,一些晶粒的t-ZrO2 自发地 相变到m-ZrO2 ,产生微裂纹,使材 料增韧。
(2)影响相变增韧的因素
m-ZrO2
1150℃ 950℃
t-ZrO2
2370℃
c-ZrO2
t-ZrO2 到m-ZrO2 马氏体相变伴随有相当大的剪切应变(约8%) 和体积增加(3%~5%) 施加压应力可抑止t-ZrO2的相变; 添加Y2O3 、MgO和CeO2 等稳定剂以降低相变温度,而使tZrO2在室温时处于亚稳定状态。
§4.3 陶瓷材料显微结构分析
一、氧化物陶瓷
1、Al2O3陶瓷
90瓷、95瓷、97瓷、 99瓷、透明氧化铝瓷
Al2O3 1200C Al2O3
95%瓷的主晶相α-Al2O3 呈柱状晶形;97%瓷 中的α-Al2O3 仍呈柱状晶形; 99%瓷和透明 Al2O3 瓷的晶形呈粒状,并且趋向于接近六 边形断面 Al2O3含量↑,玻璃相↓。 Al2O3含量↑,烧成温度↑。95%瓷→1600℃; 99%瓷→1700℃。
二次重结晶,导致局部晶粒 易于长大。 原料本身不均匀; 异常显微结构,晶粒大小分 布显著不均匀。 与添加剂的选用与加入量不 当有关
成型时的压力因素;
烧成温度偏高;
局部不均匀的液相存在。
2、ZrO2陶瓷
广泛应用的: 钇-四方氧化锆(Y-TZP); 镁-部分稳定氧化锆瓷(Mg-PSZ); 铈-四方氧化锆瓷(Ce-TZP); 复合陶瓷ZrO2-TiO2、ZrO2-Al2O3
同 一 材 料 中 添 加 剂 Y2O3 的分布不均匀 , 含Y2O3 少的 晶粒容易发生相变。
③晶粒取向
(3)成核相变
添加剂在同一晶粒 内的分布也可能不 是完全均匀的,相 变始于Y含量最少 处,即由杂质分布 不均匀而引起成核 相变
与应力诱导相变不 同,后者在相变开 始点周围应力变化 较大处产生,因此 成核相变可能是应 力诱导相变的先兆。
酸洗与热处理
对 陶 瓷 中 某 些 特 殊 结 构 的 综 合 分 析
反应结构 定向结构
缺陷结构
欠烧或过烧结构 壳芯结构 分相结构 复合结构 电(磁)畴结构
晶界与晶界相
§4.2 含缺陷陶瓷材料的显微结构
一、制备过程产生的缺陷
1、大孔径的孔隙 2、不纯原料 3、异常大晶粒 4、团聚 5、第二相夹杂物
二、高温缺陷
②界面的性质对材料力学性能的影响 a. 强的界面结合有利于载荷的传递,对提高材料的强度有利; b. 过强的界面结合将抑制断裂过程中界面的解离、裂纹的偏转 和桥接,对材料的韧性不利; c. 合适的界面结合强度是陶瓷材料得以有效强韧化的关键。
界面的物理相容性也影响复合材料的性能, 为了获得最佳的强韧化效果,增强相与基 体的基本匹配原则是: •增强相的弹性模量大于基体; •基体的热膨胀系数大于增强相。
①界面的结构类型
a. 无反应界面层:增强体与基体直接结合,形成共格、半共格 或非共格界面层。界面的结合力弱,有利于界面的解离,对 提高材料的韧性有利。 b. 反应层界面:增强体与基体之间存在一中间反应层或扩散层。 中间层紧密连接增强体与基体,增强界面的结合强度。 其形成及其性能与形成界面两相的化学相容性、原料粉体的 表面化学纯度和烧结添加剂的类型及含量等有关。