连铸连轧生产技术讲义(概论)
连铸连扎一-绪论

连铸连轧-绪论 连铸连轧 绪论
第一章
Logo
Contents
1 2 3 4
连铸连轧简介
连铸连轧的优点
连铸技术存在的问题
连铸连轧存在与发展的意义
Company Logo
Logo
1.1 定义及分类
连铸连轧
定义:由连铸机生产出来 定义:
的高温无缺陷坯, 的高温无缺陷坯,无需清理 和再加热(但需经过短时均 和再加热( 热和保温处理) 热和保温处理)而直接轧制 成材,这样把“ 成材,这样把“铸”和“轧 ”直接连成一条生产线的工 艺流程。 艺流程。
连铸: 连铸:95 t 钢坯 模铸: 模铸:86 t 钢坯
Company Logo
Logo
3 连铸技术存在的问题
缺陷
要保证连铸坯直接轧制和热装, 要保证连铸坯直接轧制和热装,无缺 陷铸坯比率越高越好。 陷铸坯比率越高越好。 为保证铸坯有足够的轧制温度, 为保证铸坯有足够的轧制温度,一般 要保证温度在1000~1100℃以上, 要保证温度在 ~ ℃以上, 且断面温度要均匀。 且断面温度要均匀。
美国 中国 日本
英国
世界钢产量与连铸比的关系
我国钢产量与连铸比的关系
Company Logo
Logo
2 连铸连轧的优点
1、简化生产工艺流程。仅连铸工 、简化生产工艺流程。 序就取代了模铸工艺中的整模、 序就取代了模铸工艺中的整模、 铸锭、脱模、均热、开坯等工序。 铸锭、脱模、均热、开坯等工序。
英国
1979 新日铁大分厂建成世界第一个 最新型的钢铁联合企业, 最新型的钢铁联合企业,采用 大型转炉配连铸机, 大型转炉配连铸机,实现全连 铸。
1964 谢尔顿钢铁厂实现全连铸生产。 谢尔顿钢铁厂实现全连铸生产。
连铸连轧原理课件2

带钢直接连铸技术
单带式铸机 (图b)适合于生产5~15mm厚的带钢,并且期望与三机架 的在线热轧机联合生产薄带钢,该工艺中,液态钢水通过布流水口供 给旋转的带钢上。 铸带速度:相对较低的速度(15~60m/min)。
单辊式铸机和单带式铸机缺点:在铸机上很难保持融体流动的均匀, 导致带钢厚度明显不均。
双辊铸带——采用铸辊对称布置(图a) ——采用异径辊布(图b)
带钢直接连铸技术
单辊铸机 (图a) 适合于生产厚度<lmm的带材,不需要进一步的轧制。 原理:依靠转动辊的动量和液体表面张力,通过与转动辊相接触的“熔 体拉拔”来生产带材。
特点:生产率高
铸带速度:70~90m/min。 应用:包括锯条、剃刀刀片、包装材料及高硅电工钢带等。
带钢直接连铸技术
1. 连铸工艺与传统的模铸工艺比较,连续铸钢工艺 具有的优点:
ห้องสมุดไป่ตู้
2. 连铸机的组成
3. 双辊带钢连铸工艺优势: 4. 带钢连铸工艺方案的种类
习题:
1. 连铸工艺与传统的模铸工艺比较,连续铸钢工艺具有的优点: (1)铸坯表面细晶层; 钢水在结晶器内得到迅速而均匀的冷却凝固,形成较厚的细晶表面凝固层, 无充分时间生成柱状晶区。 (2)缺陷少; 连续浇铸可避免形成缩孔或空洞,同时无铸锭之头尾剪切。 (3)质量稳定; 整罐钢水的连铸自始至终的冷却凝固时间接近,连铸坯纵向成分偏差可控制 在10%以内,远比模铸钢锭为好; (4)节约能源、简化工艺、改善劳动条件、便于实现机械化和自动化等优点
习题:
第四章连续铸轧过程
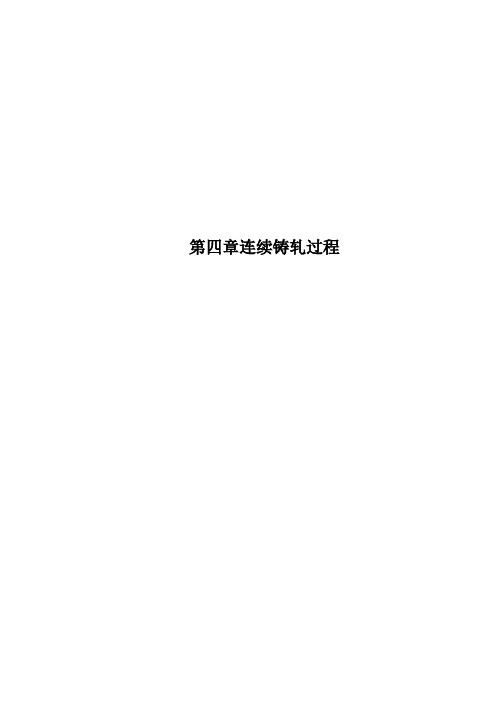
第四章连续铸轧过程第四章连续铸轧技术4.1 连续铸轧技术概论直接将金属熔体“轧制”成半成品带坯或成品带材的工艺称为连续铸轧。
这种工艺的显著特点是结晶器为两个带水冷系统的旋转铸轧辊,熔体在辊缝间完成凝固和热轧两个过程,而且在很短的时间内完成。
连续铸轧具有投资省、成本低、流程短等优点,目前,连续铸轧工艺已广泛的应用于铝合金等有色金属的生产中,在钢铁生产中的应用还处于试生产阶段。
连续铸轧技术不同于连铸连轧,后者实际上将薄锭坯铸造与热轧连续进行,即金属熔体在连铸机结晶器中凝固成厚约50-90mm 的坯后,再在后续的双机架(单机架、三机架)温连轧机上连续温轧成带坯或成品板带材,铸造和温轧是两道独立的工序。
而连续铸轧技术使连铸和轧制两个原先独立的工艺工程更加紧密地衔接在一起,已不再是一个纯粹的冶金和凝固过程,而是在连铸、凝固的同时伴随着轧制过程。
原来的全凝固压力加工规律和塑性变形规律也发生了相应的变化。
(一)铝带铸轧1951年,美国亨特一道格拉斯(Hunter—Douglas)公司首次铸轧成了铝带坯,制成了双辊式连续铸轧机。
随后,法国彼西涅(Pechiney)公司研制的3C水平式双辊铸轧机也获得成功,从那以后,铝带坯双辊连续铸轧技术和设备得到了迅速的发展。
截止到2007年底,亨特工程公司及意大利法塔亨特公司(FATA Hunter)的铸轧机已达153台,法国原普基工程公司(Pechiney Engineering)和现在的诺威力昔基工程公司(Novelis PAE)生产的3C式铸轧机,全球保有182台。
国外还有一些由其他公司和企业自制的双辊式铸轧机,主要是亨特式或3C式的变型,但产量不多,这一类铸轧机国外保有的总数也只有50多台。
我国铝带坯连续铸轧技术研究开发工作始于20世纪60年代。
1964年初进行了双辊下注式铝带坯连续铸轧模拟实验,并于同年铸轧出厚8mm,宽250mm 和400mm的铝板,1965年铸轧出宽700mm的铝带坯,1971年由东北轻合金加工厂研制成我国第一台8001Tim水平式下注式双辊铸轧机。
连铸概论

4. 中间包结构 包括包体、包盖、水口和塞棒及开闭装置级成。
( 一) 包体
包括外壳和内衬 外壳:(1)一般用12~20mm厚的钢板焊成,要求具有足够的刚性,长期在高温环境下浇注、搬 运、清渣和翻包时结构不变形。 (2)壳体外部有加固筋板,外壳设有钓钩或吊环以备换包体时用。 (3)外壳四周钻许多小孔通气,便于烘烤时内衬中水蒸汽的散发。 (4)包壳外壁有一定倒锥度。 内壁:有一定的锥度,以便于清渣、砌筑挤紧,耐火砖不易坍塌,斜度一般为8%~10%。 内衬:两种 (1)砌砖型:绝热层、永久层和工作层三层结构。 (2)打结型:整个中间包借助于专门的胎具,采用耐火混凝土浇灌打结成型,打结后的整 体包衬具有结构牢固,使用寿命长的优点。
第二节 中间包及中间包车
一、中间包 1.作用 (1)减压、稳流:避免钢流过大、过小引起钢水飞溅、散流以及结晶器液 面的过份波动。 (2)除渣:钢水在中间包内保持一定的停留时间,促使非金属夹杂物上浮,并均匀钢水温度 和化学成分。 (3)分流:当浇铸多流铸坯时,可进行分流。 (4)贮存:在多炉连浇过程中,中间包内贮存一定量的钢水,可以保证钢包在更换期间的顺 利浇铸,避免拉速的大幅度变化。 2.中间包结构的要求 (1)散热面积小,保温性能好。 (2)内衬耐材易于维护,便于清包、浇注、砌筑等操作。 (3)外形简单,长期高温作用下结构稳定可靠。 (4)钢水在中包内停留适当的时间,中包内的固体钢壳最少。 3.中间包形状 外壳力求简单,采用矩形(俯视),梯形(侧视),包壁有一定的倾斜度
(三)水口装置
三种水口控制方式:定径水口、滑动水口和塞棒水口。 本钢主要是塞棒控制。 1.作用:调节中间包到结晶器的钢水流量。 2.要求:灵活、可靠。在操作时能充分地观察和控制结晶器内的钢水液面高度。 3.控制方式:塞棒为整体结构,用于控制和精调从中间包到结晶器的钢流。它还可以在事故状态 下,立即阻断钢流。控制方式为液压机构,可手动也可自动。自动状态下,塞棒由结晶器液 位控制系统自动控制。 4.材质塞棒体:铝碳质 塞棒头:镁质材料 塞棒臂:碳素结构钢 5.特点 : 塞棒的控制可自动和手动,本钢是自动的液压控制,自动操作是通过结晶器液面控制仪根据液面 波动情况发出信号给位移跟踪指示器,通过液压随动系统由液压缸操作塞棒实现的。
连铸连轧技术
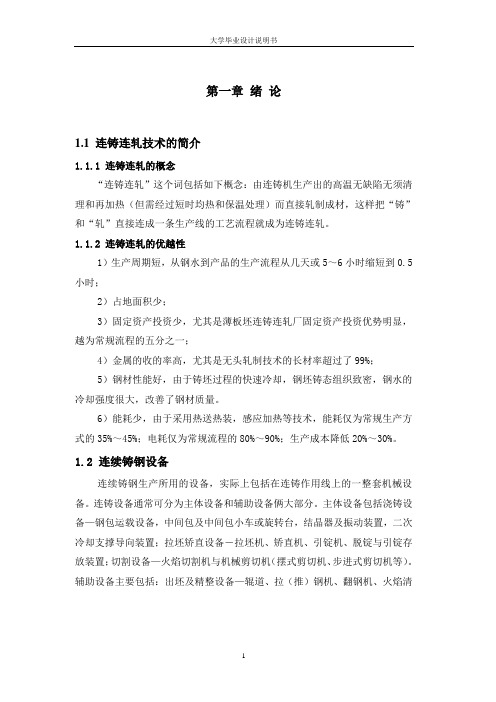
第一章绪论1.1 连铸连轧技术的简介1.1.1 连铸连轧的概念“连铸连轧”这个词包括如下概念:由连铸机生产出的高温无缺陷无须清理和再加热(但需经过短时均热和保温处理)而直接轧制成材,这样把“铸”和“轧”直接连成一条生产线的工艺流程就成为连铸连轧。
1.1.2 连铸连轧的优越性1)生产周期短,从钢水到产品的生产流程从几天或5~6小时缩短到0.5小时;2)占地面积少;3)固定资产投资少,尤其是薄板坯连铸连轧厂固定资产投资优势明显,越为常规流程的五分之一;4)金属的收的率高,尤其是无头轧制技术的长材率超过了99%;5)钢材性能好,由于铸坯过程的快速冷却,钢坯铸态组织致密,钢水的冷却强度很大,改善了钢材质量。
6)能耗少,由于采用热送热装,感应加热等技术,能耗仅为常规生产方式的35%~45%;电耗仅为常规流程的80%~90%;生产成本降低20%~30%。
1.2 连续铸钢设备连续铸钢生产所用的设备,实际上包括在连铸作用线上的一整套机械设备。
连铸设备通常可分为主体设备和辅助设备俩大部分。
主体设备包括浇铸设备—钢包运载设备,中间包及中间包小车或旋转台,结晶器及振动装置,二次冷却支撑导向装置;拉坯矫直设备-拉坯机、矫直机、引锭机、脱锭与引锭存放装置;切割设备—火焰切割机与机械剪切机(摆式剪切机、步进式剪切机等)。
辅助设备主要包括:出坯及精整设备—辊道、拉(推)钢机、翻钢机、火焰清理机等;工艺设备—中间包烘烤装置、吹氖装置、脱气装置、保护渣供给与结晶润滑装置等;自动控制与测量仪表—结晶器液面测量与显示系统、过程控制计算机、测温、测重、测长、测速、测压等仪表系统。
在连续铸钢的生产线上,出拉坯矫直机脱锭后的连铸坯需按用户或下部工序的要求,将铸坯切成定尺或倍尺。
因此在所有的连铸设备中,切割设备是非常重要的一种设备。
由于连铸坯必须在连续的运动过程中实现切割,因而连铸工艺对切割设备提出了特殊的要求,既不管采用什么型式的切割设备都必须与连铸坯实行严格的同步运动。
连铸连轧知识点
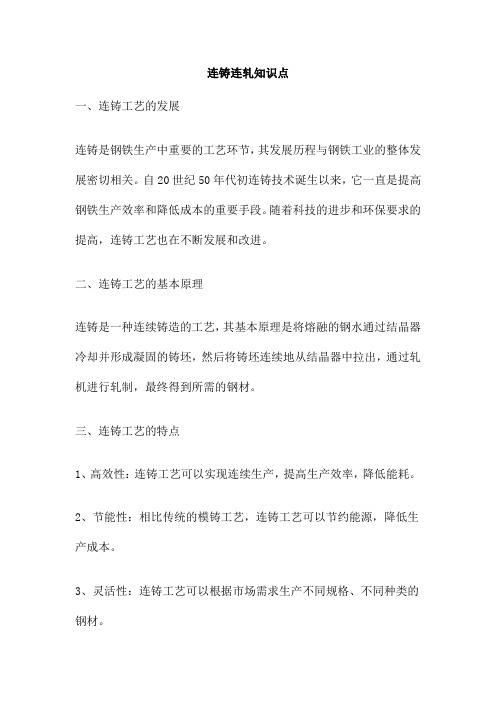
连铸连轧知识点一、连铸工艺的发展连铸是钢铁生产中重要的工艺环节,其发展历程与钢铁工业的整体发展密切相关。
自20世纪50年代初连铸技术诞生以来,它一直是提高钢铁生产效率和降低成本的重要手段。
随着科技的进步和环保要求的提高,连铸工艺也在不断发展和改进。
二、连铸工艺的基本原理连铸是一种连续铸造的工艺,其基本原理是将熔融的钢水通过结晶器冷却并形成凝固的铸坯,然后将铸坯连续地从结晶器中拉出,通过轧机进行轧制,最终得到所需的钢材。
三、连铸工艺的特点1、高效性:连铸工艺可以实现连续生产,提高生产效率,降低能耗。
2、节能性:相比传统的模铸工艺,连铸工艺可以节约能源,降低生产成本。
3、灵活性:连铸工艺可以根据市场需求生产不同规格、不同种类的钢材。
4、环保性:连铸工艺可以减少废弃物的产生,降低环境污染。
四、连铸工艺的应用范围连铸工艺广泛应用于各种钢铁产品的生产,包括板材、带材、型材、管材等。
随着技术的发展,连铸工艺也逐渐应用于有色金属、稀有金属等领域。
五、连铸工艺的未来发展方向随着科技的不断发展,连铸工艺的未来发展方向主要集中在以下几个方面:1、智能化:利用先进的自动化技术和智能化设备,提高生产过程的自动化水平和生产效率。
2、绿色化:进一步降低能耗和废弃物排放,实现生产过程的环保和可持续发展。
3、高效化:研发更高效的连铸技术,提高生产速度和产品质量。
薄板坯连铸连轧轧制区组织模拟薄板坯连铸连轧是一种高效、节能的钢材生产工艺,具有较高的生产效率和产品质量。
在轧制过程中,钢材的组织形态和性能特点对产品的质量和使用性能具有重要影响。
因此,薄板坯连铸连轧轧制区组织模拟成为了一个备受的研究领域。
通过组织模拟,可以深入了解轧制过程中材料的组织变化和性能特点,为工艺优化和产品性能提升提供理论支持和实践指导。
薄板坯连铸连轧轧制区背景及基础概念薄板坯连铸连轧是指将液态钢水倒入薄板坯连铸机中进行连续铸造,然后将连铸坯送入轧机进行连续轧制。
连铸连轧生产技术的讲义共40页

13、遵守纪律的风气的培养,只有领 导者本 身在这 方面以 身作则 才能收 到成效 。—— 马卡连 柯 14、劳动者的组织性、纪律性、坚毅 精神以 及同全 世界劳 动者的 团结一 致,是 取得最 后胜利 的保证 。—— 列宁 摘自名言网
15、机会是不守纪律的。——雨 特 67、今天应做的事没有做,明天再早也 是耽误 了。——裴斯 泰洛齐 68、决定一个人的一生,以及整个命运 的,只 是一瞬 之间。 ——歌 德 69、懒人无法享受休息之乐。——拉布 克 70、浪费时间是一桩大罪过。——卢梭
连铸连轧生产技术的讲义
11、战争满足了,或曾经满足过人的 好斗的 本能, 但它同 时还满 足了人 对掠夺 ,破坏 以及残 酷的纪 律和专 制力的 欲望。 ——查·埃利奥 特 12、不应把纪律仅仅看成教育的手段 。纪律 是教育 过程的 结果, 首先是 学生集 体表现 在一切 生活领 域—— 生产、 日常生 活、学 校、文 化等领 域中努 力的结 果。— —马卡 连柯(名 言网)
连铸连轧生产技术讲义(概论-1)

提高拉速措施:
•结晶器优化技术; •结晶器液面波动检测控制技术; •结晶器振动技术; •结晶器保护渣技术; •铸坯出结晶器后的支撑技术; •二冷强化冷却技术; •铸坯矫直技术; •过程自动化控制技术。
如果说提高拉速是小方坯连铸机高效化的核心,那么板坯连 铸机高效化的核心就是提高连铸机作业率。
目前提高连铸机作业率的技术主要有: (1)多炉连浇技术:异钢种多炉连浇;快速更换长水口;在线调宽;中 间包热循环使用技术;防止浸入式水口堵塞技术。 (2)连铸机设备长寿命技术:长寿命结晶器,每次镀层的浇钢量为20~ 30万t;长寿命的扇形段,上部扇形段每次维修的浇钢量100万t,下部扇 形段每次维修的浇钢量300~400万t。 (3)防漏钢的稳定化操作技术:结晶器防漏钢预报系统;结晶器漏钢报 警系统;结晶器热状态运行检测系统。 (4)缩短非浇注时间维护操作技术:上装引锭杆;扇形段自动调宽和调 厚技术;铸机设备的快速更换技术;采用各种自动检测装置;连铸机设 备自动控制水平。提高板坯连铸机设备坚固性、可靠性和自动化水平, 达到长时间的无故障在线作业,是提高板坯连铸机作业率水平的关键。
连铸的方法
根据铸坯与结晶器器壁间是否有相对运动可以分为:
有相对滑动-固定振动式结晶器 无相对滑动-移动式结晶器
连铸技术发展的四个阶段
第一阶段 (1840~1930年) 金属连续浇铸思想的启蒙阶段
1840年美国人塞勒斯(Sellers)获得连续铸铅的专利; 1856年英国人贝塞麦(Henry Bessemer)提出了采用双辊 连铸机浇铸出了金属锡箔、铅板和玻璃板,并获专利; 1887年德国人戴伦(R.M.Daelen)提出了与现代连铸机 相似的连铸设备的建议,在其开发的设备中已包括了上下敞 开的结晶器、液态金属注入、二次冷却段、引锭杆和铸坯切 割装置等。
连铸连轧知识点

连铸连轧知识点连铸和连轧是金属工业中常见的两个工艺过程。
连铸是指将液态金属连续铸造成坯料的过程,而连轧是指将坯料经过一系列压制和变形操作,连续地轧制成所需尺寸的金属板、带材或线材的过程。
本文将介绍连铸和连轧的基本概念、工艺流程和主要应用。
一、连铸连铸是一种高效的金属铸造技术,具有生产速度快、坯料质量好等优点。
连铸主要应用于钢铁、铜、铝等金属的生产中。
1. 连铸的基本原理连铸的基本原理是将熔融的金属通过连续浇注的方式,直接铸造成连续的坯料。
具体原理如下:首先,将金属熔融至液态,并通过加热设备保持在一定温度范围内;然后,通过连续浇注系统,将熔融金属均匀地注入到连铸结晶器中;在连铸结晶器中,通过冷却剂的作用,使金属迅速凝固,并形成坯料;最后,通过一系列传动装置,将连续产生的坯料送往下游的轧制设备或其他后续处理过程中。
2. 连铸的工艺流程连铸的工艺流程一般包括以下几个关键步骤:(1)冶炼:将矿石等原料经过熔炼处理,得到液态的金属合金;(2)调温:通过加热设备将金属保持在一定的液态温度;(3)连续浇注:通过连续浇注系统,将熔融金属注入到连铸结晶器中;(4)结晶与凝固:在连铸结晶器中,通过冷却剂的作用,使金属迅速凝固,并形成坯料;(5)切割和输送:将连续产生的坯料切割成合适的长度,并送往下游的加工设备。
3. 连铸的应用连铸广泛应用于钢铁、铜、铝等金属的生产中。
在钢铁工业中,连铸可以直接将炼钢铁水铸造成连续坯料,用于后续轧制成钢板和钢材。
在有色金属工业中,连铸可以将液态金属铸造成连续的板材、带材和线材,用于制造电线电缆、汽车零部件等产品。
二、连轧连轧是一种将金属坯料经过多道次的压制和变形操作,连续地轧制成所需尺寸的金属板、带材或线材的工艺过程。
连轧具有高效快速、坯料成形完整等特点,广泛应用于钢铁、有色金属等工业领域。
1. 连轧的基本原理连轧的基本原理是通过一系列的压制和变形操作,使金属坯料逐渐减小厚度、增大长度,并达到所需的尺寸要求。
讲义-连轧
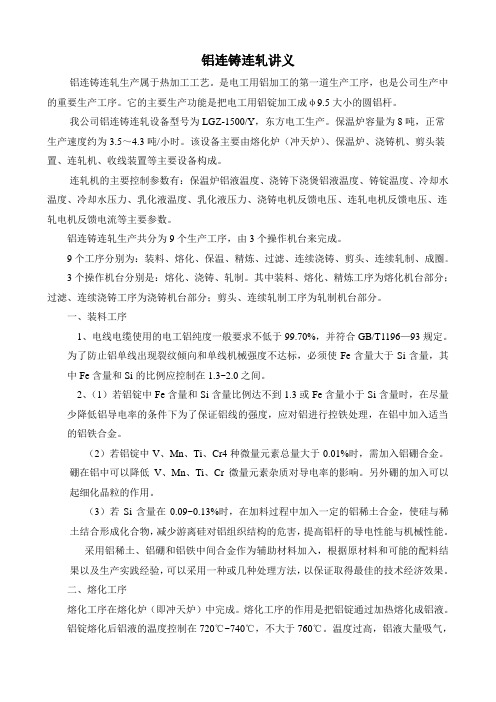
铝连铸连轧讲义铝连铸连轧生产属于热加工工艺。
是电工用铝加工的第一道生产工序,也是公司生产中的重要生产工序。
它的主要生产功能是把电工用铝锭加工成φ9.5大小的圆铝杆。
我公司铝连铸连轧设备型号为LGZ-1500/Y,东方电工生产。
保温炉容量为8吨,正常生产速度约为3.5~4.3吨/小时。
该设备主要由熔化炉(冲天炉)、保温炉、浇铸机、剪头装置、连轧机、收线装置等主要设备构成。
连轧机的主要控制参数有:保温炉铝液温度、浇铸下浇煲铝液温度、铸锭温度、冷却水温度、冷却水压力、乳化液温度、乳化液压力、浇铸电机反馈电压、连轧电机反馈电压、连轧电机反馈电流等主要参数。
铝连铸连轧生产共分为9个生产工序,由3个操作机台来完成。
9个工序分别为:装料、熔化、保温、精炼、过滤、连续浇铸、剪头、连续轧制、成圈。
3个操作机台分别是:熔化、浇铸、轧制。
其中装料、熔化、精炼工序为熔化机台部分;过滤、连续浇铸工序为浇铸机台部分;剪头、连续轧制工序为轧制机台部分。
一、装料工序1、电线电缆使用的电工铝纯度一般要求不低于99.70%,并符合GB/T1196—93规定。
为了防止铝单线出现裂纹倾向和单线机械强度不达标,必须使Fe含量大于Si含量,其中Fe含量和Si的比例应控制在1.3~2.0之间。
2、(1)若铝锭中Fe含量和Si含量比例达不到1.3或Fe含量小于Si含量时,在尽量少降低铝导电率的条件下为了保证铝线的强度,应对铝进行控铁处理,在铝中加入适当的铝铁合金。
(2)若铝锭中V、Mn、Ti、Cr4种微量元素总量大于0.01%时,需加入铝硼合金。
硼在铝中可以降低V、Mn、Ti、Cr微量元素杂质对导电率的影响。
另外硼的加入可以起细化晶粒的作用。
(3)若Si含量在0.09~0.13%时,在加料过程中加入一定的铝稀土合金,使硅与稀土结合形成化合物,减少游离硅对铝组织结构的危害,提高铝杆的导电性能与机械性能。
采用铝稀土、铝硼和铝铁中间合金作为辅助材料加入,根据原材料和可能的配料结果以及生产实践经验,可以采用一种或几种处理方法,以保证取得最佳的技术经济效果。
连铸连轧原理课件1

连铸机类型
厚板坯 薄板坯
断面形状 大方坯 小方坯 圆坯 异型坯 运行轨迹
立式 立弯式 多点弯曲 弧形
椭圆形
连铸机类型
按铸坯断面分类
连铸机类型
连铸机示意图
机型的特点
(1)立式连铸机:
结晶器、二冷段、拉坯和剪切沿垂直方向排列
优点: - 无弯曲变形、冷却均匀,裂纹少。 - 夹杂物容易上浮。 缺点: ·设备高,建设费用大。 ·钢液静压大,容易产生鼓肚。
1.2 连铸的发展史
世界上第一台工业生产性连铸机是1951年在原苏联 红十月钢厂投产的立式半连续式装置。它是双流机, 断面尺寸180mm×600mm。 作为连续式浇铸的铸机是1952年建在英国巴路钢厂 的双 流立弯式铸机,其生产断面尺寸为 50mm×50mm 和90mm× 90 mm的小方坯。 宽板坯铸机于1959年建在原苏联的新列别茨克厂。 日本住友和罗西为新日铁光厂提供的世界上第一台不 锈钢宽板坯连铸机在1960年12月投产,宽度为 1050mm。 在整个50年代,连续铸钢技术尽管开始步入工业生 产,但产量很少,1960年的产量仅为115万吨,连铸 比仅为0.34﹪。
1.2 连铸的发展史
连续浇铸思想的启蒙阶段 (1840~1930年) 1840年美国 人塞勒斯(Sellers)获得了连续 铸铅的专利。
图1
图2
1856年英国人贝塞麦(Henry Bessemer) 采用双辊连铸机 浇铸出了金属锡箔、铅板和 玻璃板,并获专利。
1.2 连铸的发展史
1.2.1 早期尝试 美国亚瑟(B.Atha)(1866年)和德国工程师戴伦 (R.M.Daelen)(1877年)最早提出以水冷、底部敞口 固定结晶器为特征的常规连铸概念。前者采用一个底 部敞开、垂直固定的厚壁铁结晶器并与中间包相连, 施行间歇式拉坯;后者采用固定式水冷薄壁铜结晶器、 施行连续拉坯、二次冷却,并带飞剪切割、引锭杆垂 直存放装置。 1920~1935年间,连铸过程主要用于有色金属,尤其 是铜和铝的领域。
连铸连轧原理课件4
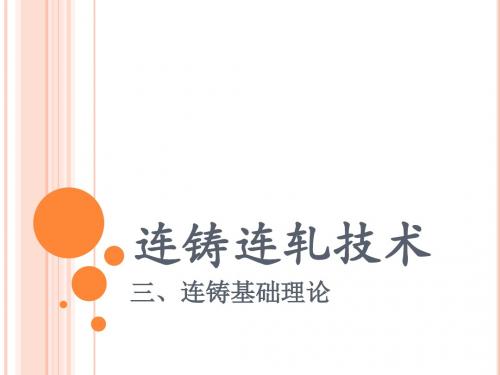
3.3 结晶器传热与凝固
结晶器弯月面渣子行为 在结晶器钢液面上加入保护渣,吸收 钢水热量渣子熔化,在结晶器钢液面 上形成液渣层、烧渣层和粉渣层的三 层结构的渣层。由于液渣与水冷铜壁 接触的温度梯度高。在结晶器周边形 成了固体渣围并黏附在结晶器壁上。
3.3 结晶器传热与凝固
渣圈的作用: 在浇注过程中一旦形成渣圈,由于液 渣和钢水与铜壁润湿程度有差异,在 结晶器四周弯月面渣圈与初生坯壳会 形成一个垂直向下的毛细管通道,由 于结晶器振动和毛细现象的作用,把 弯月面上的液体渣源源不断地吸人坯 壳与铜壁的气隙中形成渣膜,从而起 到润滑作用,结晶器振动的一个周期 内,液渣的渗漏量除了与钢液面液渣 层厚度有关外,还与结晶器周边形成 的渣圈形状有关。如果渣圈不断长大 ,会阻碍液渣的渗漏。渣圈可能破裂 ,特别是浸入式水口壁与铜板之间渣 圈有的可以搭桥,严重时会导致板坏 裂纹和漏钢。
3.3 结晶器传热与凝固
凝固钩(Hook),其形貌基本类似于弯月面形状,弧线自表面向钢液侧弯 曲深度达1.42mm,此时振痕深度0.26mm。
3.3 结晶器传热与凝固
在弯月面凝固形成的弧形凝固钩,其形状是由在弯月面区钢水表面张力和 钢水静压力的平衡决定的。凝固钩形成过程如图所示。
(a)弯月面钢水与铜板接触点是凝固钩 开始点,然后呈弧形线离开铜壁。凝 固沿弧形线横向生长,形成初生坯壳 厚度。 (b)结晶器向下运动处于负滑脱期间, 弯月面钢水溢出凝固钩弧线,此时流 体惯性力超过钢水表面张力,把弯月 面液渣泵入到坯壳与铜板气隙中作润 滑剂。同时溢过凝固钓弧线的钢水靠 近模壁迅速凝固。高温的钢水也把附 着铜壁的固体渣(0.16mm厚)再熔化, 使横向传热加快,坯壳增厚。
连铸连轧新技术培训
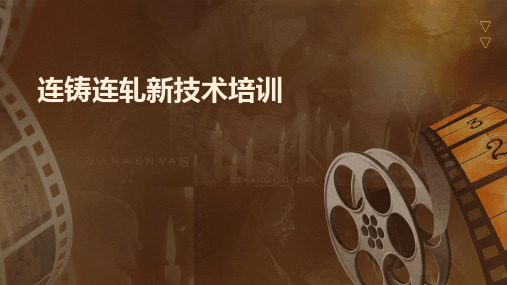
04
连铸连轧新技术的优势与挑战
连铸连轧新技术的优势
提高生产效率
节能减排
连铸连轧技术能够实现连续化生产, 提高了生产效率,降低了生产成本。
连铸连轧技术能够降低能源消耗和减 少废弃物排放,有利于实现绿色生产 。
优化产品质量
新技术能够更好地控制产品形状、尺 寸和性能,提高了产品质量和稳定性 。
连铸连轧新技术面临的挑战
01
02
03
技术更新成本高
新技术的引入需要投入大 量资金进行设备更新和技 术改造。
操作技能要求高
新技术的操作和维护需要 专业知识和技能,对操作 人员提出了更高的要求。
兼容性问题
新技术的引入可能需要对 原有生产系统进行改造和 调整,以实现与新技术的 兼容。
如何应对连铸连轧新技术的挑战
加强技术培训
对操作人员进行系统的技术培训 ,提高他们的专业知识和技能水
节能技术
采用先进的节能技术和设备,降低能耗和减少资源浪 费,实现绿色生产。
减排措施
通过优化生产工艺和加强环保管理,降低污染物排放 ,保护环境。
THANK YOU
总结词
薄带连铸技术是一种新型的连铸技术,能够生产出厚度较薄的带坯。
详细描述
薄带连铸技术采用特殊的结晶器和冷却系统,通过控制钢液的凝固过程,生产 出厚度在50-200毫米之间的薄带坯。这种技术适用于生产不锈钢、碳钢、合金 钢等不同材质的薄带,具有节能、高效、环保等优点。
连铸坯热装热送技术
总结词
连铸坯热装热送技术能够提高钢铁生产效率,降低能耗和减少环境污染。
详细描述
连铸坯热装热送技术是指在连铸过程中,将刚出炉的铸坯通过保温和密封的运输装置直接送往轧机进行轧制,避 免了传统工艺中的冷却、再加热等环节。这种技术能够减少能源消耗和缩短生产周期,同时降低氧化和减少环境 污染。
薄板坯连铸连轧技术培训讲义

薄板坯连铸连轧技术培训讲义1. 引言薄板坯连铸连轧技术是一种先进的钢铁生产工艺,在钢铁制造过程中扮演着至关重要的角色。
本文档将介绍薄板坯连铸连轧技术的基本原理、流程和关键设备。
2. 基本原理薄板坯连铸连轧技术是将熔融的钢水通过连铸机连续铸造成为薄板坯,然后通过连轧机进行连续轧制,最终获得所需的薄板产品。
其基本原理如下:•连铸:钢水经过特殊的连铸机,在结晶器中快速冷凝,形成坯料,并通过辊道送至连轧机。
•连轧:坯料经过连轧机的一系列辊道,不断轧制变形,逐渐变薄并形成所需的薄板产品。
3. 工艺流程薄板坯连铸连轧工艺的主要流程包括连铸、坯料切割、连轧以及最终产品处理。
以下为具体步骤:3.1 连铸1.钢水预处理:熔融的钢水经过除杂、除气等预处理步骤,以提高钢水质量。
2.连铸开始:将预处理后的钢水注入连铸机的结晶器中,通过连续浇注形成连续的坯料。
3.结晶器冷却:结晶器中的冷却水快速冷凝坯料表面,促使坯料凝固和形成。
3.2 坯料切割1.坯料切割开始:连铸后的坯料通过切割机进行切割,得到所需长度的薄板坯。
2.切割方式:常见的切割方式为热切割和冷切割,根据材质和产品要求选择合适的方式。
3.3 连轧1.连轧机介绍:连轧机主要由多对辊道组成,用于将薄板坯逐渐轧制成所需的薄板产品。
2.轧制工艺:通过不断的轧制和辊道调整,使坯料逐渐变薄和延展,形成所需的薄板产品。
3.冷却处理:连轧后的薄板需要经过冷却设备进行冷却处理,以达到产品要求的硬度和性能。
3.4 最终产品处理1.张力控制:薄板产品在连轧过程中受到一定的拉力,需要通过张力控制系统进行控制,防止产生过大或过小的张力。
2.切边、打包:最后对薄板产品进行切边和打包,以便于运输和存储。
4. 关键设备薄板坯连铸连轧技术涉及到多种关键设备。
以下列举一些重要的设备:1.连铸机:用于将熔融的钢水连续浇注成坯料。
2.切割机:将连铸后的坯料按照所需长度进行切割。
3.连轧机:用于将坯料进行连续轧制,使其逐渐变薄并形成薄板产品。
连铸连轧原理课件3
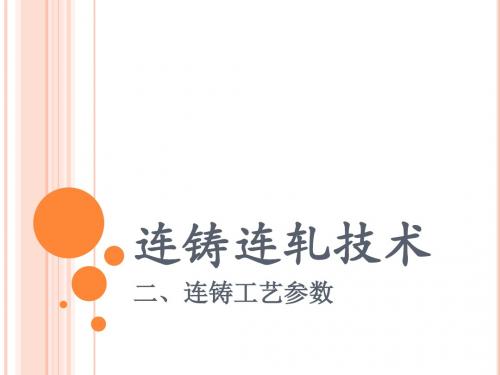
2.3 连铸钢水准备——钢水温度
2.3.1 连铸钢水传递过程温度变化规律 生产过程中,钢水进入钢包后,随着时 间的推移,其温度逐渐降低。要确定不 同钢种的合理浇注温度,必须确定出出 钢至浇注各个阶段的温度损失。
钢水过程总温降可用下式表示:
ΔT1为出钢时的温降。它主要取决于钢水的出钢温度、出钢时间,钢水包容量及 包衬材质,加入合金的种类及数量,包衬状态等。 ΔT2为出钢后到钢水炉外精炼站运输过程中的温降。它除与钢包容量、包衬材质 和钢包表面覆盖状态等因素有关外,还受等待时间和运输距离的影响。 ΔT3为钢水在钢包处理过程的温降,它取决于采用的炉外处理方法及处理时间。 ΔT4钢包运至中间包处的过程温降。 ΔT5钢水在中间包内的温降。钢水的热损失主要是中间包内衬吸热和钢水表面的 辐射散热。
2.3 连铸钢水准备——浇注温度
2.3.2 连铸钢水浇注温度的确定 连铸钢水的浇注温度,一般是指中间包内的钢水温度。钢水的 浇注温度应等于该钢种的液相线温度加上中间包钢水合适的过 热度。即:
液相线温度的计算 钢水的液相线温度是确定浇注温度的基础,它取决于钢水 中所含元素的性质和含量。根据文献材料,常用计算液相线温 度的经验公式有以下几种形式:
2.2 连铸机基本参数——拉坯速度
拉速是连铸机生产能力的重要标志。当铸饥浇注稳定以后,其 拉坯速度称为工作拉速。从提高生产率的要求出发,希望尽量 提高拉速。当铸坯的液心长度等于冶金长度时的拉速,即为最 大拉速,最大拉速一般为工作拉速的1.15~1.2倍。 连铸机最大拉速可按下式计算:
2.2 连铸机基本参数
液相线温度
过热度:20~40℃ 浇注温度为:1540~1550℃
- 1、下载文档前请自行甄别文档内容的完整性,平台不提供额外的编辑、内容补充、找答案等附加服务。
- 2、"仅部分预览"的文档,不可在线预览部分如存在完整性等问题,可反馈申请退款(可完整预览的文档不适用该条件!)。
- 3、如文档侵犯您的权益,请联系客服反馈,我们会尽快为您处理(人工客服工作时间:9:00-18:30)。
20世纪70年代中期后,在线同步轧制停止发展。
连铸连轧生产技术
RAL
带液芯铸坯的直接轧制 含义 指铸坯未经切断的在线轧制,它除了具有上述在 线同步轧制的主要优缺点外,还有其自己特点。 优点
可减少铸坯中心部位的偏析,消除内部缩裂、
中心疏松及缩孔等缺陷;
显著降低单位轧制力,有利于节能;
铸坯潜热得到充分利用,通过液芯复热更容易 保证连铸连轧过程中所需要的较高铸坯温度。
RAL
连铸连轧生产技术
主讲人:张晓明
东北大学
轧制技术及连轧自动化国家重点实验室
连铸连轧生产技术
RAL
1 概论
• 1.1连铸技术的发展概况 • 1.2厚板坯连铸与轧制的衔接模式 • 1.3连铸坯热装及直接轧制技术的发展概况
1.4薄板坯连铸连轧技术的发展概况
1.5
带钢直接连铸技术的发展概况
连铸连轧生产技术
连铸连轧生产技术
RAL
连铸过程控制钢洁净度主要对策有:
•保护浇注; •中间包冶金技术,钢水流动控制; •中间包材质碱性化(碱性复盖剂,碱性包衬); •中间包电磁离心分离技术;
•中间包热循环操作技术;
•中间包的稳定浇注技术;
•防止下渣和卷渣技术;
•结晶器流动控制技术; •结晶器EMBR技术。
连铸连轧生产技术
RAL
1.1 连铸技术的发展概况
连铸的概念
所谓连铸是将钢水连续注入水冷结晶器中,凝固成 硬壳后从结晶器出口连续拉出或送出,经喷水冷却, 完全凝固后切成坯料或直送轧制的铸造工艺。 连铸的方法
根据铸坯与结晶器器壁间是否有相对运动可以分为:
有相对滑动-固定振动式结晶器 无相对滑动-移动式结晶器
连铸连轧生产技术
•结晶器优化技术; •结晶器液面波动检测控制技术; •结晶器振动技术; •结晶器保护渣技术; •铸坯出结晶器后的支撑技术;
•二冷强化冷却技术;
•铸坯矫直技术; •过程自动化控制技术。 如果说提高拉速是小方坯连铸机高效化的核心,那么板坯连 铸机高效化的核心就是提高连铸机作业率。
连铸连轧生产技术
RAL
模的连铸连轧试验机组。 20世纪70年代中期以前,工业性试验研 究和初步应用阶段。
在线同步轧制
所采用 的主要 实验研 究方案 带液芯轧制 热装炉轧制 直接轧制
主要方式连铸连轧生产技术 Nhomakorabea RAL
连铸-在线同步轧制 含义 连铸与轧制在同一作业线上,铸坯出连铸机后,
不经切断即直接进行与铸速同步的轧制。
特点 先轧制后切断,铸与轧同步,铸坯一般要进行 在线加热均温或绝热保温,每流连铸需配置专 用轧机(行星轧机或摆锻机和连锻机),轧机 数目1~13架。
RAL
连铸技术发展的四个阶段
第一阶段 (1840~1930年) 金属连续浇铸思想的启蒙阶段
1840年美国人塞勒斯(Sellers)获得连续铸铅的专利;
1856年英国人贝塞麦(Henry Bessemer)提出了采用双辊
连铸机浇铸出了金属锡箔、铅板和玻璃板,并获专利; 1887年德国人戴伦(R.M.Daelen)提出了与现代连铸机
相似的连铸设备的建议,在其开发的设备中已包括了上下敞
开的结晶器、液态金属注入、二次冷却段、引锭杆和铸坯切 割装置等。
连铸连轧生产技术
RAL
第二阶段 (1940~1949年) 连铸特征技术的开发阶段
1943年德国人永汉斯 (S.Junghans)建成了 第一台试验连铸机,提出 了振动水冷结晶器、浸入 式水口、结晶器保护剂等
连铸连轧生产技术
RAL
高效连铸
概念 通常是指以高拉速为核心,以高质量、无缺陷铸坯生 产为基础,实现高连浇率、高作业率的连铸技术。
日本: • 最高板坯铸速:3.2m/min;月产量:20~45万吨; • 连浇炉数:超过100炉,最高达10000炉; • 作业率达92%。
连铸连轧生产技术
RAL
提高拉速措施:
NNSC(Next Net Shape Casting)接近最终成品形状的 浇注技术,其实质是在保证成品钢材质量的前提下,尽量 减小铸坯的断面尺寸以减少甚至取代压力加工。
连铸连轧生产技术
RAL
近终形连铸技术包含的主要内容
•薄板坯连铸-TSCC(Thin Slab Continuous Casting) •带钢直接连铸-DSC(Direct Strip Casting)
RAL
铸坯表面质量好坏是热送热装和直接轧制的前提条件。铸坯 表面缺陷的产生主要决定于钢水在结晶器的凝固过程。 要清除铸坯表面缺陷,应采用以下技术: •结晶器钢液面稳定性控制; •结晶器振动技术; •结晶器内凝固坯壳生长均匀性控制技术; •结晶器钢液流动状况合理控制技术; •结晶器保护渣技术。
连铸连轧生产技术
连铸连轧生产技术
RAL
1.3连铸坯热装及直接轧制技术发展概况
连铸连轧技术的起源 传统轧 钢工序 能源消 耗情况
加热炉-57.5%
电能-38.6% 其他-3.9%。
节能的潜力
20世纪50年代初期,开始实验研究工作,先
后建立了一些连铸连轧试验性机组进行探讨。
连铸连轧生产技术
RAL
20世纪60年代后期,出现了工业生产规
(3)防漏钢的稳定化操作技术:结晶器防漏钢预报系统;结晶器漏钢报 警系统;结晶器热状态运行检测系统。
(4)缩短非浇注时间维护操作技术:上装引锭杆;扇形段自动调宽和调
厚技术;铸机设备的快速更换技术;采用各种自动检测装置;连铸机设 备自动控制水平。提高板坯连铸机设备坚固性、可靠性和自动化水平, 达到长时间的无故障在线作业,是提高板坯连铸机作业率水平的关键。
我国常统称类型1和2两类工艺为连铸连轧工艺。
连铸坯热装热送轧制工艺
类型2、3、4需入正式加热炉加热,故亦可统称为连铸 坯热装热送轧制工艺。
连铸连轧生产技术
RAL
CC-DR和HCR工艺的主要优点
1. 节约能源消耗 节能量与热装或补偿加热入炉温度有关,入炉温度越高, 则节能越多;
直接轧制比常规冷装炉轧制工艺节能80~85%。
连铸连轧生产技术
RAL
类型3、4为铸坯冷至A3甚至A1线以下温度装炉,称为低
温热装轧制工艺,简称HCR(Hot Charge Rolling)
特点:装炉温度一般在400~700℃之间。而低温热装 工艺,则常在加热炉之前还有保温坑或保温箱等,即 采用双重缓冲工序,以解决铸、轧节奏匹配与计划管 理问题。 类型5即传统的连铸坯冷装炉轧制工艺,简称CCR (Cold Charge Rolling) 特点:连铸坯冷至常温后,再装炉加热后轧制,一般连 铸坯装炉的温度在400℃以下。
连铸连轧生产技术
RAL
连铸-连轧工艺,简称CC-CR(Continuous Casting-Continuous Rolling)
类型1和2都属于铸坯热轧前基本无相变的工艺,其所面临 的技术难点和问题也大体相似,只是DHCR有加热炉缓冲, 对连铸坯温度和生产连续性的要求有所放宽,但它们都要
求从炼钢、连铸到轧钢实现有节奏的均衡连续化生产。故
传统连铸技 术成熟阶段
应用于工业生产 5000多项专利 代表性的技术
钢包回转台
弧形连铸机 电磁搅拌 结晶器保护渣
结晶器在线调宽
渐进弯曲矫直 浸入式水口浇注 中包塞棒控制
连铸连轧生产技术
RAL
第四阶段 (20世纪80~90年代) 传统连铸技术的优化发展阶段
特点是连铸比不断上升,连铸生产效率不断提高(表现为 铸机作业率、浇铸速率、拉坯速度、连浇炉数等主要指标 的不断提高),浇铸品种逐渐扩大,生产成本大大降低。
连铸连轧生产技术
RAL
连铸坯的质量逐年提高,连铸坯的质量包括:铸坯洁净度 (钢中非金属夹杂物数量,类型,尺寸,分布,形态);铸 坯表面缺陷(纵裂纹,横裂纹,星形裂纹,夹渣);铸坯内 部缺陷(中间裂纹,角部裂纹,中心线裂纹,疏松,缩孔, 偏析)。 连铸坯质量控制战略是:铸坯洁净度决定于钢水进入结晶器 之前的各工序;铸坯表面质量决定于钢水在结晶器的凝固过 程;铸坯内部质量决定于钢水在二冷区的凝固过程。
技术,取得工业规模的成
功,奠定了现代连铸机结 构的基础,结晶器振动成
为连铸机的标准操作。
图1-2 S.Junghans专利原理
1—中间包;2—保护剂加入装置;3—进水口;4—结晶器; 5—铸坯;6—拉辊;7—出水口;8—压缩机;9—钢包;10—振动机构
连铸连轧生产技术
RAL
第三阶段 (1950~1976年)
RAL
铸坯内部缺陷的产生主要决定带液芯的铸坯在二冷区的凝 固过程。要消除铸坯内部缺陷,可采用以下技术措施: •低温浇注技术;
•铸坯均匀冷却技术;
•防止铸坯鼓肚变形技术;
•轻压下技术;
•电磁搅拌技术; •凝固末端强冷技术; •多点或连续矫直技术; •压缩铸造技术。
连铸连轧生产技术
RAL
近终形连铸
钢铁 生产 的短 流程 工艺 技术 概念 电炉炼钢 直接还原 (DRI) 熔融还原 (如Corex) 近终形连铸
目前提高连铸机作业率的技术主要有: (1)多炉连浇技术:异钢种多炉连浇;快速更换长水口;在线调宽;中 间包热循环使用技术;防止浸入式水口堵塞技术。 (2)连铸机设备长寿命技术:长寿命结晶器,每次镀层的浇钢量为20~ 30万t;长寿命的扇形段,上部扇形段每次维修的浇钢量100万t,下部扇
形段每次维修的浇钢量300~400万t。
连铸连轧生产技术
RAL
优点
生产过程连续化程度高,可实现无头轧制,增大轧材卷重,
提高成材率及大幅度节能等。
缺点
操作复杂,对工艺装备和自动控制要求高,增大了技术实 现的难度;
连铸速度太慢,一般只为轧制速度的10%左右,铸-轧速 度不匹配,严重影响轧机能力的发挥,在经济上并不合算; 轧制速度太低使轧辊热负荷加大,使辊面灼伤和龟裂,影 响了轧辊的使用寿命,增加了换辊的次数。