汽车企业TPS培训内容
面向一线生产管理人员的TPS培训
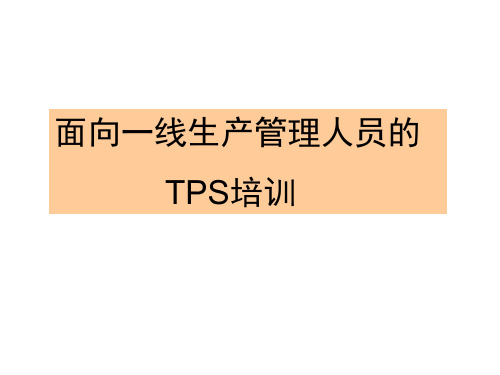
B)发生“制造过剩” 的原因 <管理缺失> ① 为应对机械故障、次品、缺勤、变更等「异常情况」 ② 负荷量不均匀 ③ 错误提高运转率 提高「直观」效率 ④ 认为停止生产线是「罪恶」的想法 ⑤ 作业人员过多 ⑥ 组织结构不好(工序的构造方式、批量・规格过大)
是否通过不断调整来减少不 必要的搬运距离?
是否进行了搬运工具自动 化的研究和改善?是否根 据需要实现了机器人化?
是否存在临时放置或者重复 堆放的现象?
产品·零部件等的容器,有特 殊要求的除外,是否统一了 规格,无论哪个箱子都可以 按照同样的方式堆放,而且 易于搬运?
是否研究过工序之间搬运 的自动化?
面向一线生产管理人员的 TPS培训
1、TPS是什么?
所谓TPS,即丰田生产方式 (Toyota Production System)的缩写
丰田生产方式的体系
基本构成与基本原则
基本骨架
JIT 准时生产
基本原則
①工序的流动化 ② 小批量化
③节拍生产 ④后工序引领方式
JIDOUKA
自働化
①工序内保证优质 ② 少人化
部件材料的放置场地、放置 方法、放置数量、向生产线 供应的方法、容器等方面的 对策,是否不断进行改进?
店铺的位置、大小、高度、 样式等是否合适?
地点编号、货架号码等的编 制是否简明易懂?无论何人 都能够非常容易地找到指定 地点么?
搬运的浪费②
容器箱每箱的“可容个数” 是否尽量减少?(小容量 化)
1TPS推进培训教材
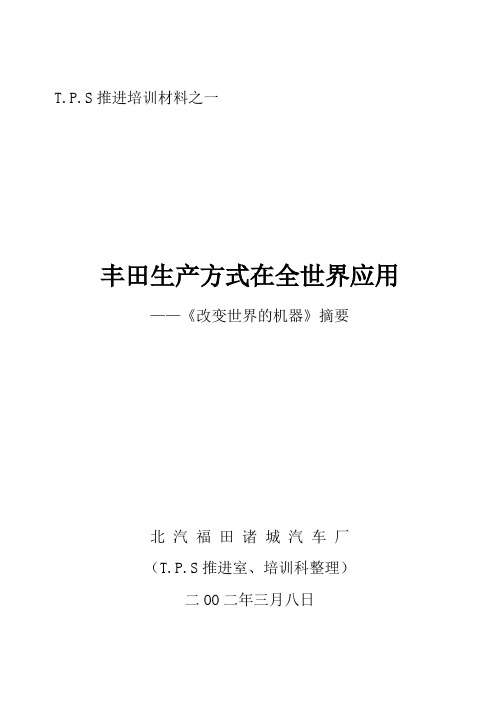
T.P.S推进培训材料之一丰田生产方式在全世界应用——《改变世界的机器》摘要北汽福田诸城汽车厂(T.P.S推进室、培训科整理)二OO二年三月八日前言本培训材料主要对《改变世界的机器》一书进行了摘要,通过大量图表、数据、文字说明丰田生产方式已在全世界应用,并将在不同领域企业中逐步代替大批量生产方式;丰田生产方式决非纯生产方式,而是一种将生产、管理与市场经营全环节结合的生产管理方式。
《改变世界的机器》一书作者花了五年时间,在一个庞大的工业中探索了大量生产方式与精益生产方式的差别。
精益生产方式的原理可以同样应用于全球每种工业。
向精益生产转变将会对人类社会产生深远影响,也就是说这一转变将真正的改变世界。
研究人之一约翰·克拉奇克是丰田—通用的合资公司新联公司雇佣的第一个美国工程师,长期工作在各丰田工厂中,在精益生产方式的发源地学到了这种生产方式的概念,他在麻省理工学院的斯隆管理学院取得了管理学硕士学位。
在攻读学位期间,调查了15个国家的90多家汽车厂。
我们相信这是一次在任何工业中没有进行过的全面的工业调查。
此书论述了人类社会在大量生产方式兴起的时期以及目前衰落的时期是如何从事生产的,而在进入精益生产方式时代的黎明时期,一些国家的某些公司如何率先采用了一种新的管理方法,最后描述了整个世界将如何进入这一新时代。
其叙述建立在国际汽车计划研究联络员的116篇专题报告基础上。
用典范的方式说明丰田的业务体系是怎样从这种创新发展起来,对美国和欧洲现存的生产都进行挑战的;以丰田公司的作为唤醒世界另外,我们相信精益生产方式的基本概念是通用的。
任何人,在任何地方都可以应用,而且很多非日本的公司已经在学习这一概念。
我们的注意力集中用在仔细解说精益生产的原理及技术,很少注意日本社会的特征,在采用精益生产方式时,既不必要也用不着去模仿,而是要做出特殊的努力在精益生产初期,从日本的应用中提炼出普遍的原则。
注:《改变世界T.P.S推进培训材料之一丰田生产方式在全世界应用的机器》作者:[美] 詹姆斯·P·沃迈克、丹尼尔·鲁斯目录一、丰田生产方式的认识 (1)二、丰田生产方式在全世界应用 (1)三、丰田生产方式的要素 (2)(一)管理工厂 (2)(二)产品开发和工程设计 (8)(三)协作环节 (13)(四)用户关系 (16)(五)管理精益企业 (20)四、丰田生产方式发展之未来 (23)1.发展进程中的三大障碍 (23)2.中国汽车工业 (24)3.丰田生产方式发展之未来 (24)一、对丰田生产方式的认识丰田生产方式是适应日益激烈的市场竞争和适时化、多元化的市场需要,在“多品种小批量”的市场需求制约下和大量生产方式的基础上发展起来的一种全新的生产方式。
TPS初级培训资料
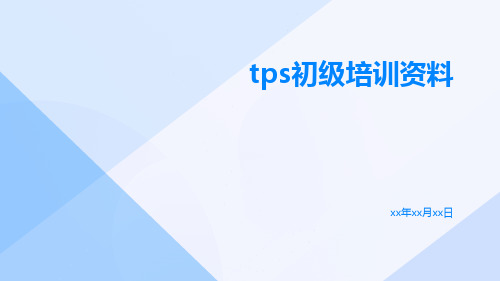
THANKS
按照tps的标准和方法进行实施,同时建立 监督机制,对实施过程进行监控和调整。
实施过程中的注意事项
注重细节
tps强调细节管理,在实施过程中要 注重每一个细节的把控。
强化沟通
及时有效的沟通是实施tps的关键, 员工之间、上下级之间要保持畅通 。
持续改进
实施tps是一个持续改进的过程,要 不断总结经验,优化流程和方法。
提升员工素质
TPS需要员工具备设备维护和保养 的技能和知识,通过培训和实践可 以提高员工的素质和能力。
02
tps标准与规范
日产生产模式
定义
日产生产模式是一种以减少浪费、提高生产力、降低成本为核心目标的生产方式 ,它强调在正确的时间、以正确的数量、用正确的方式、以最低的成本提供高质 量的产品。
特点
评估生产效率
定期评估生产效率,找出瓶颈和 浪费,采取相应的改进措施。
设定目标
设定明确的TPS目标和计划,并 确保所有员工都了解和参与实现 这些目标。
06
tps与其他管理方法
tps与jit生产方式
目标一致
TPS和JIT生产方式都以实现生产过程中的零浪费为目标,提高生 产效率和产品质量。
流程优化
两种方法都强调对生产流程的优化和改进,通过消除浪费、降低 成本和提高交货期来提高效益。
目的
TPS八大支柱帮助企业从各个方面全面提升生产管理 水平和效率,实现生产过程的优化和改进。
03
tps推行与实施
推行的关键步骤
制定推行计划
培训
明确tps推行的时间表、推行策略和责任人 等。
组织员工进行tps的培训,让员工了解tps的 理念、意义和实施方法等。
宣传推广
TPS(JIT) 生产方式培训资料

TPS(JIT) 生产方式培训资料TPS(JIT)生产方式培训资料(一)本文旨在介绍TPS(JIT)生产方式的培训资料,包括其基本概念、主要原则以及实施过程。
希望通过本文的阅读,能让读者对TPS(JIT)生产方式有更深入的了解,并能够在实践中应用这一生产方式,提高生产效率和质量。
一、什么是TPS(JIT)生产方式TPS(Toyota Production System,丰田生产方式),又称JIT (Just-in-Time)生产方式,是丰田汽车公司发展而来的生产方式,其核心理念是"同时制造,零库存"。
其主要目标是通过消除浪费、优化生产流程,以实现缩短生产周期、减少库存、提高质量和降低成本等效果。
二、TPS(JIT)生产方式的原则1. 浪费的消除TPS(JIT)生产方式强调消除各类浪费,包括过产、等待、运输、库存、过程中的损耗和不合格品等。
通过减少这些浪费,企业可以提高生产效率、降低成本、优化资源利用。
2. 拉动式生产TPS(JIT)生产方式以顾客需求为导向,采取拉动式生产,即按照订单来生产产品,避免过去的"推动式"生产方式中产生的过剩和库存。
拉动式生产可以提高生产的敏捷性,降低产出的滞后性。
3. 灵活性和变动适应性TPS(JIT)生产方式要求企业具备灵活性和变动适应性,即能够及时调整生产线,以适应市场需求的快速变化。
通过灵活的生产方式,企业可以减少因生产周期长、库存过多而导致的资源浪费。
4. 经济批量和小批量化生产TPS(JIT)生产方式倡导经济批量和小批量化生产,通过灵活的生产线布局和合理的生产计划,实现生产成本的最优化。
5. 高质量和持续改进TPS(JIT)生产方式注重产品质量,强调全员参与质量控制,通过改善生产工艺,提高产品质量。
同时,TPS(JIT)生产方式倡导持续改进,不断挑战和提高自身的生产能力和竞争力。
三、TPS(JIT)生产方式的实施过程1. 价值流分析价值流分析是TPS(JIT)生产方式实施的基础,通过对生产过程中每个环节的价值创造和浪费进行分析,找出存在的问题,确定改进方向。
TPS初级培训资料

详细描述
通过分析生产流程中的瓶颈环节,制定相应的改善措施,优化生产流程,实现 生产平衡,提高整体生产效率。
减少浪费活动
总结词
降低生产成本,提高资源利用效率。
详细描述
通过减少浪费活动,降低生产成本,提高资源利用效率。具体措施包括减少不良 品、减少库存、优化物流等。
05
TPS初级培训效果评估
TPS的五大原则
全员参与
TPS强调全员参与,包括管理层和一 线员工,每个人都应该对设备的维护 和保养负责。
目视管理
TPS采用目视管理方法,通过使用图 表、看板等工具,使设备管理信息一 目了然。
01
02
预防维修
TPS注重预防维修,通过定期检查和 预测设备故障,采取措施避免设备故 障的发生。
03
持续改进
TPS鼓励持续改进,不断优化设备维 护和保养的流程和方法,提高设备的 综合效率。
05
04
流程管理
TPS注重流程管理,通过制定和维护设 备管理流程,确保设备的维护和保养 工作有序进行。
TPS的三大支柱
自主维护
TPS的自主维护是指员工对自己 负责的设备进行日常检查、清洁、
调整和润滑等维护工作,确保设 备正常运行。
备异常情况。
维护与保养
根据设备特点和运行情 况,制定相应的维护和 保养计划,定期进行保
养和维修。
备件管理
建立备件管理制度,储 备必要的备件和易损件, 确保维修工作的及时性
和有效性。
快速换模
01
02
03
04
快速换模
通过优化换模流程和提高换模 效率,缩短换模时间,提高设
备利用率和生产效率。
10.TPS基础知识培训

问题点
3 、 搬
石子(问题点)
部品欠品 设备故障
(石:问题点) 计划未完
运
不良发生
的
浪
问题点
费
4 、 等 待 的 浪 费
加工的浪费一方面指在产品本身没有要求或要求不高时,却采取 了高于标准的加工而造成的浪费,另一方面是不合理的作业编排而造 成的浪费。
5 、 加 工 的 浪 费
6、动作的浪费
7 、 不 良 品 的 浪 费
根据后工序的领取状况推进工序的进展的机制。
平准化 拉式生产
一个流
目的:保证质量,缩短生产周期
前提条件
种类平准化 数量平准化
安排一上午的学习计划,半天全学外语和半天四小时
例 各学外语、数学、历史及语文的效果肯定是不一样的,
后者明显要好些。
非平准(不均衡)
AAAAAAAABBBBBBBCCCCC
平准化(均衡化)
必须根除浪费
生产过剩的浪费是最大的浪费
包含2层含义:
多了、快 了反而不
好
· 在规定的时间内多生产 · 提前生产出来
3 TPS的两大支柱
一、准时化
二、自働化
减少浪费、降低成本
准
自
时
働
化
化
持续改进
丰田佐吉的自働制造思想
TPS的基本思想是把发明王丰田佐吉的自働制 造思想与丰田汽车的实际创业者丰田喜一郎的 准时化思想结合起来,由大野耐一等人在生产 现场逐一具体化的产物。这种方式已被丰田公 司应用到一切经营领域,引起了全世界生产企 业的瞩目。
3-6 自働化
1、带人字旁的自働化
自働化:带有自动停止装置的机械(自停装 置、满负荷系统及防错装置),从而使机械具有 了人的智慧。
TPS现场改善培训资料
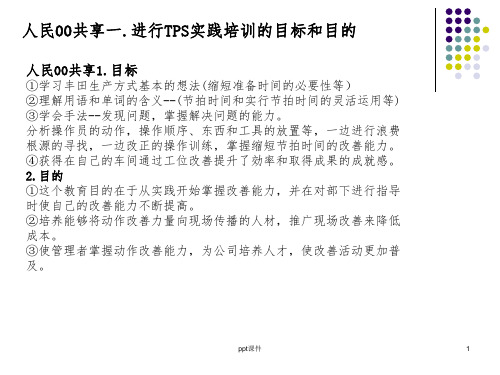
ppt课件
1
人民00共享 TPS现场改善技巧培训
培训人:川西实
ppt课件
2
二. TPS实践培训的主要内容
第一部分
第1章 丰田生产方式的体系 第2章 动作改善―――
1.根据现场观察分析标准作业的动作 2.缩短机器运转时间的次序 3.动作分析 4.动作经济的原则(单纯作业化的原则)
5.动作改善实践
第二部分
1.动作的大小
2.动作端的停止
3.能否往复的动作
4.加工以外的动作能否缩短
ppt课件
10
2-2
NO
<设备>
项目
缩短机械循环运转时间的次序
着眼点
考虑点
1 .能否尽快按下起动按钮
*作业组装后马上按下
.安全方面
2
.能否缩短装卸作业的手工 作业时间
*排除装卸动作的浪费、两手作业、废止换手作 业
.动作分析的实施
N0
动素
说明
例
1 组合
组合两个以上的物品
物品定点放置
2 分解
在一定的关系下分解装配物品物 从盒子里拿出物品
3 使用
为了有目的使用工具或装置的动作 切、打、弯曲
4 无目动作(空手移动)
针对目的物的前进或返回
伸手、返回
5 抓取
在控制目的物的状态下放置
握、抓、按押
6 搬运
改变目的物的位置
按押、拉拽、使滑动
人类的智慧是无穷无尽的
维持现状在将来看就是「退歩」
现在不总是最好的
必须要有「总是领先与他人」的思想准备。
ppt课件
8
2-1.现场观察后的动作改善...(关于人.设备)
1.目的
为了缩短人、设备的动作时间、 把握现状的动作浪费进行讨论,排除浪费 提升动作品质。(时间是动作唯一的影子) 使用以前的标准作业票,循环运作图、在现场进行观测、 能够抓住细小的现状动作的浪费。
TPS基础知识培训_标准作业
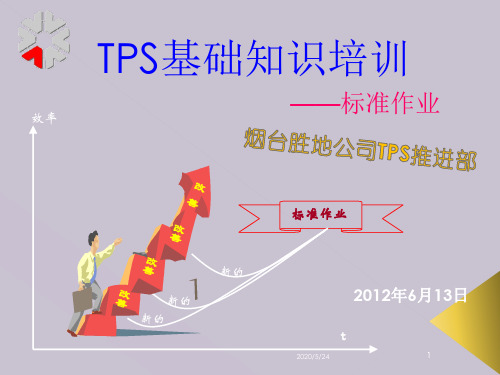
2013-8-2
14
1.节拍时间 T.T(Takt Time 标准工时): 2.作业顺序:
标准作业: 节拍时间
3.标准在制品:
作业顺 序
标准在制
2013-8-2
15
节拍时间(标准工时)‥‥生产一件产品应该使 用的时间值。
1班次的运转时间(定时) 节拍(T· T)=─────────── (秒) 1班次的必需生产数量 例如:精工二部工作时间为8.5小时,每生产线需要生 产500片满足产量要求,则: 节拍(T.T)=8.5*60*60/500=61.2(秒)
标准在制品 数量 设 备 中 1个 顺方向操作、无自动加工机械 0个
序号 1 2
条件 顺方向操作、有自动加工机械
材料、成品(装载在材料箱、成品筐的产品)不包 注意: 括在标准在制品内。
2013-8-2
20
编制标准作业
按照下列条件编制标准作业票、标准作业组合票。 一、条件: (1)需要数量550件/班次,每班次运转时间为460分钟 (2)生产型号:35372-1600 (3)产品名称:油泵 (4)装筐和取料时间分别为1秒 (5)2序、3序、4序需要检验,检验时间包含在手工作业内。 (6)生产线号:TPS--28 (7)取出数量:每台设备取1件 作业顺序如下:
2013-8-2
28
根据左边原题给的设备布局将标准作业票的 布局画出来
2013-8-2
29
1、根据布局图 将设备布局画出
5、为了能够实现用同 样顺序和动作进行作业, 在工序内保有的最低限 度在制品需要6个 。
3、返回时 需要用虚 线标识
2、根据作业顺序将标号 顺序标准在设备旁 三个图形分别表示 品质检验、安全、 标准在制品
tps计划培训

tps计划培训I. IntroductionToyota Production System, often referred to as TPS, is a world-renowned production system that focuses on continuous improvement and waste reduction. This training plan aims to provide a comprehensive understanding of TPS and equip employees with the knowledge and skills required to implement TPS principles in their work.II. Training ObjectivesThe main objectives of this TPS training plan are:1. To understand the core principles of TPS and how they contribute to the overall success of a company.2. To identify waste and inefficiencies in the production process and develop strategies to eliminate them.3. To develop problem-solving skills and incorporate TPS principles into daily work routines.4. To create a culture of continuous improvement and innovation within the organization. III. Training ContentThe TPS training will be divided into several modules, each focusing on a specific aspect of the production system.Module 1: Introduction to TPS- Overview of TPS and its history- Key principles of TPS, including just-in-time production, continuous improvement, and respect for people- Case studies of companies that have successfully implemented TPSModule 2: Waste Reduction- Identification of the seven types of waste (muda) in production processes- Techniques for eliminating waste, such as value stream mapping, 5S, and standardized work- Practical exercises to identify and reduce waste in a simulated production environment Module 3: Problem-Solving Skills- Introduction to the A3 problem-solving methodology- Root cause analysis and the 5 Whys technique- Application of problem-solving skills to real-life production challengesModule 4: Kaizen and Continuous Improvement- The concept of kaizen and its role in TPS- Strategies for fostering a culture of continuous improvement within the organization- Practical examples of successful kaizen projects and their impact on business performance IV. Training MethodsThe TPS training will utilize a variety of interactive and experiential learning methods to ensure maximum engagement and retention of knowledge.- Lectures and presentations by TPS experts and practitioners- Group discussions and brainstorming sessions- Case studies and real-life examples of TPS implementation- Hands-on exercises and simulations of production processes- Gemba walks to observe TPS principles in action on the shop floorV. Training ScheduleThe TPS training will be conducted over a period of four weeks, with each module being covered in weekly sessions. The schedule will be as follows:Week 1: Introduction to TPS- Day 1: Overview of TPS and its key principles- Day 2: Case studies of successful TPS implementationWeek 2: Waste Reduction- Day 3: Identification of waste in production processes- Day 4: Techniques for eliminating wasteWeek 3: Problem-Solving Skills- Day 5: Introduction to the A3 problem-solving methodology- Day 6: Application of problem-solving skills to real-life challengesWeek 4: Kaizen and Continuous Improvement- Day 7: The concept of kaizen and strategies for fostering a culture of continuous improvement- Day 8: Hands-on kaizen project and wrap-upVI. Training EvaluationTo ensure the effectiveness of the TPS training, an evaluation process will be conducted at the end of each module. This will include quizzes, group discussions, and practical assessments to gauge the understanding and application of TPS principles by the participants.VII. ConclusionThe TPS training plan outlined above aims to provide a comprehensive understanding of Toyota Production System and equip employees with the knowledge and skills required to implement TPS principles in their work. By fostering a culture of continuous improvement and waste reduction, the organization will be able to achieve higher productivity and improved business performance.。
TPS精益生产方式培训

TPS精益生产方式培训◆讲课内容:TPS不能元样照搬的导入所有企业。
但是,结合「均衡化生产(JIT)「自働化」、「看板系统(无库存生产)」的基本思想,根据自身企业的特色・特征,建立起一套自成体系的「独自的生产方式」是有必有的。
从顾客,外部供应商的对应;到以批量生产为前提的工程对应等等各种各样的情况下,如果都能按「独自的生产方式」去做的话,就会建立起一个强大的制造工程。
◆课程大纲:1.开始●对制造部门的期待●改善过的制造工程部门所带来的效果2.「独自的生产方式」必要性3.丰田生产方式(以下称TPS)概要●TPS的概念●TPS的基本思想「卖价」、「原价」、「利润」的理论顾客第一的生产使人充满干劲的工作●TPS的目的●TPS的构成―两大支柱―◇均衡化生产(JIT)◇自働化●浪费与改善●看板(无库存生产)系统◇看板系统的直接作用◇看板系统的类型◇看板系统的使用例◇看板系统的效用●现地现物主义●维持与向上●生产工程中的主人公4.自社流生产方式(TPS)导入的实际●自社的情况●导入方法●导入事例◇顾客、外部供应商的对应◇从复数的单项工程到工厂的合理化看板系统机能的窍门外部供应零部件交货用看板系统的简单化9精益生产与6SIGMA管理课程目标:了解精益生产的基本概念及其改善的思想;如何认识现场的浪费及排除浪费;了解6σ的基本理念及运作模式;6σ的推进对企业的巨大收益;精益生产与6σ如何做到完美结合;课程纲要:Unit 1 精益生产的基本理念及基础了解企业竞争主题的改变精益的基本概念精益思想的基本理念精益思想的哲理性降低成本的思路以满足客户的需求为导向为什么库存是罪恶彻底消除一切浪费改善的基础Unit 2 精益生产方式的介绍如何降低成本真效率与假效率最大的浪费是什么挑战传统的生产方式拉动生产的方式实施条件供应链的管理精益生产的评价指标推动客户、供应商的良性循环理想的同期化生产模式Unit 3 六西格玛的介绍6σ的介绍6σ的哲理性6σ起源与成功开展6σ的流程改进方法如何推进6σ6σ成功的关键因素建立高效团队成功的项目管理6σ对未来的巨大挑战Unit 4精益生产与六西格玛的完美结合精益生产推行中的困惑为什么精益生产与6σ能够完美结合企业管理中的完美模式实现管理的层次变化生产力的增强提升企业的竞争体质Unit 5如何在你的工厂开始打造超级企业起步推行精益生产的要诀推行的基本步骤著名企业推行经验(二)工业工程篇工业工程(IE--Industrial Engineering)是对人员、物料、设备、能源和信息所组成的集成系统进行设计、改善的一门学科。
企业培训-TPS培训资料精品

企业可根据自身需求和员工特点,定制符合实际情况的TPS培训方案,提高培训的针对性 和实效性。
TPS培训对企业的价值
01
提高企业竞争力
通过TPS培训,企业能够提高生产效率、降低成本、提高产品质量,
从而增强市场竞争力。
02
塑造企业文化
TPS培训强调团队合作、精益生产等理念,有助于塑造企业文化,提
课程审核
邀请行业专家和公司领导对课程进行审核,确保 课程质量和效果。
培训实施与评估
实施准备
提前安排好师资力量、场地、 设备等,确保培训的顺利进行
。
培训实施
按照课程安排,组织员工参加培 训,并做好课堂管理和学员服务 。
效果评估
通过考试、问卷调查等方式,对培 训效果进行评估,及时总结经验教 训,为后续培训提供改进方向。
训计划的制定提供依据。
制定计划
02
根据调研结果和公司战略目标,制定详细的培训计划,包括培
训目标、内容、时间、地点等。
审批与公布
03
将培训计划提交给上级领导审批,经批准后向全体员工公布。
培训课程设置
课程设计
根据培训计划,设计针对不同岗位和层级的培训 课程,确保课程内容的针对性和实用性。
课程开发
组织开发团队编写教材、制作课件等,确保课程 内容的专业性和丰富性。
根据评估结果,向企业领导层汇报培训效果情 况,提供决策支持。
根据员工反馈和评估结果,对培训内容和方式 进行反思和改进,提高培训质量。
根据实际操作中的问题,针对性地开展后续培 训和辅导,提高员工的技能水平和应对能力。
05
TPS培训师资力量
师资来源与筛选
内部选拔
从公司内部选拔有经验的员工或管理者担任培训师,确保培训内 容与公司实际运营情况相符。
TPS相关培训资料
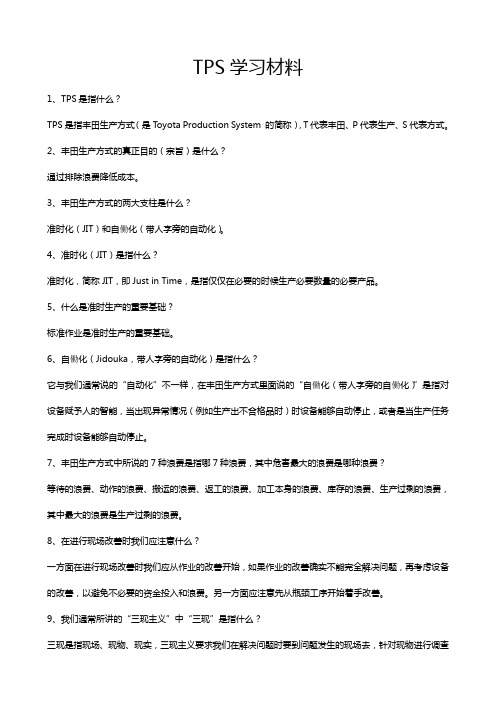
TPS学习材料1、TPS是指什么?TPS是指丰田生产方式(是Toyota Production System 的简称),T代表丰田、P代表生产、S代表方式。
2、丰田生产方式的真正目的(宗旨)是什么?通过排除浪费降低成本。
3、丰田生产方式的两大支柱是什么?准时化(JIT)和自働化(带人字旁的自动化)。
4、准时化(JIT)是指什么?准时化,简称JIT,即Just in Time,是指仅仅在必要的时候生产必要数量的必要产品。
5、什么是准时生产的重要基础?标准作业是准时生产的重要基础。
6、自働化(Jidouka,带人字旁的自动化)是指什么?它与我们通常说的“自动化”不一样,在丰田生产方式里面说的“自働化(带人字旁的自働化)”是指对设备赋予人的智能,当出现异常情况(例如生产出不合格品时)时设备能够自动停止,或者是当生产任务完成时设备能够自动停止。
7、丰田生产方式中所说的7种浪费是指哪7种浪费,其中危害最大的浪费是哪种浪费?等待的浪费、动作的浪费、搬运的浪费、返工的浪费、加工本身的浪费、库存的浪费、生产过剩的浪费,其中最大的浪费是生产过剩的浪费。
8、在进行现场改善时我们应注意什么?一方面在进行现场改善时我们应从作业的改善开始,如果作业的改善确实不能完全解决问题,再考虑设备的改善,以避免不必要的资金投入和浪费。
另一方面应注意先从瓶颈工序开始着手改善。
9、我们通常所讲的“三现主义”中“三现”是指什么?三现是指现场、现物、现实,三现主义要求我们在解决问题时要到问题发生的现场去,针对现物进行调查和分析,掌握现状,制定解决问题的对策,杜绝仅仅依靠主观想象进行判断。
10、丰田生产方式成功实施的前提条件是什么?全员参与改善是成功实施丰田生产方式的前提条件。
11、推行TPS的作用是什么?①彻底排除现场浪费,降低成本;②过程周期缩短带来资本效率提高和现金流增大;③企业内潜在能力的有效利用带来机会额度的扩大,经营资源的扩大;④人才锻造体系的确立和人才群体的培养,使企业确立持续竞争优势。
TPS初级培训资料[1]
![TPS初级培训资料[1]](https://img.taocdn.com/s3/m/ba51fac131b765ce050814fd.png)
等待浪费的原因和对策
对策:•采用均衡化生产
•制品别配置—一个流生产
•防误措施
原因:
•自动化及设备保养加强 •实施目视管理
•生产线布置不当,物流混乱
•加强进料控制
•设备配置、保养不当
•生产计划安排不当 •工序生产能力不平衡 •材料未及时到位 •管理控制点数过多 •品质不良
注意:
•均衡化生产
原因:
•生产流程调整顺畅 •看板管理的贯彻
•视库存为当然 •设备配置不当或设备能力差 •大批量生产,重视稼动 •物流混乱,呆滞物品未及时处理
•快速换线换模 •生产计划安排考虑库 存消化
注意:
•提早生产
•库存是万恶之源
•无计划生产
•管理点数削减降低安全库存
•客户需求信息未了解清楚
•消除生产风险降低安全库存
•设备余力并非一定是埋没成本
•生产浪费大
•生产能力过剩时,应尽量先考虑减
•业务订单预测有误
少作业人员,但并非辞退人员,而
•生产计划与统计错误 是更合理、更有效率地应用人员
TPS初级培训资料[1]
七大浪费—等待的浪费
双手均未抓到及摸到东西的时间
材料、作业、搬运、检查之所有等待
表现形式: •自动机器操作中,人员的“闲视”等待 •作业充实度不够的等待 •设备故障、材料不良的等待 •生产安排不当的人员等待 •上下工程间未衍接好造成的工程间的等待
是浪费的源头
表现形式:
•物流阻塞
•库存、在制品增加
•产品积压造成不良发生
•资金回转率低
•材料、零件过早取得
•影响计划弹性及生产系统的适应能力
•只是提前用掉了费用(材料费、人工费)而已,并无其它好处
TPS培训生产方式概述
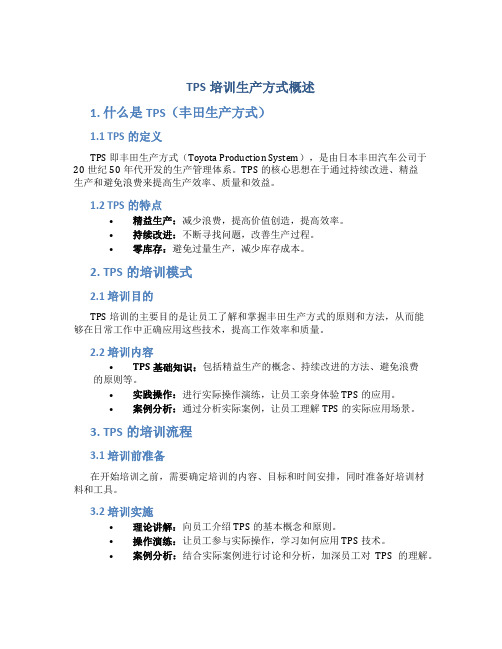
TPS培训生产方式概述1. 什么是TPS(丰田生产方式)1.1 TPS的定义TPS即丰田生产方式(Toyota Production System),是由日本丰田汽车公司于20世纪50年代开发的生产管理体系。
TPS的核心思想在于通过持续改进、精益生产和避免浪费来提高生产效率、质量和效益。
1.2 TPS的特点•精益生产:减少浪费,提高价值创造,提高效率。
•持续改进:不断寻找问题,改善生产过程。
•零库存:避免过量生产,减少库存成本。
2. TPS的培训模式2.1 培训目的TPS培训的主要目的是让员工了解和掌握丰田生产方式的原则和方法,从而能够在日常工作中正确应用这些技术,提高工作效率和质量。
2.2 培训内容•TPS基础知识:包括精益生产的概念、持续改进的方法、避免浪费的原则等。
•实践操作:进行实际操作演练,让员工亲身体验TPS的应用。
•案例分析:通过分析实际案例,让员工理解TPS的实际应用场景。
3. TPS的培训流程3.1 培训前准备在开始培训之前,需要确定培训的内容、目标和时间安排,同时准备好培训材料和工具。
3.2 培训实施•理论讲解:向员工介绍TPS的基本概念和原则。
•操作演练:让员工参与实际操作,学习如何应用TPS技术。
•案例分析:结合实际案例进行讨论和分析,加深员工对TPS的理解。
3.3 培训总结在培训结束后,进行总结与反思,让员工分享培训心得和体会,同时收集反馈意见,以便不断改进培训内容和方法。
4. TPS培训的效果4.1 生产效率提升通过TPS培训,员工可以更加高效地进行工作,减少浪费、提高生产效率,从而提升企业的竞争力。
4.2 质量改善TPS培训能够帮助员工更好地把握质量控制的关键点,提高产品质量,减少次品率。
4.3 创新能力提升TPS培训鼓励员工不断思考和改进现有生产方式,激发创新潜力,推动企业持续进步。
5. 结语通过对TPS的培训,员工能够全面了解丰田生产方式的核心理念,并能够在实际工作中灵活运用这些技术,不断改进、提高生产效率和质量。
TPS(JIT) 生产方式培训资料

TPS(JIT) 生产方式培训资料TPS(JIT)生产方式培训资料一、概述TPS(JIT)生产方式即"精益生产"或"零库存生产",是一种由丰田汽车公司创立的生产管理制度。
该制度旨在通过减少生产过程中的浪费,从而提高生产效率和质量,并缩短生产周期。
本文将从TPS (JIT)的定义、原则、实施步骤以及优势等多个方面,详细介绍这一生产方式。
二、TPS(JIT)的定义TPS(JIT)是基于精益生产原则的一种生产方式,目标是通过最小化库存,减少不必要的浪费和流程中的缺陷,提高生产效率并降低生产成本。
TPS(JIT)注重生产流程的优化、技术的创新和员工的参与,以实现高效的生产运作。
三、TPS(JIT)的原则1. 价值流分析:通过分析生产流程中的价值和非价值活动,确定生产过程中的浪费并采取相应措施进行改进。
2. 一体化生产系统:将生产流程中的所有环节进行整合,使之形成一个高效、稳定的产线。
3. 拉式生产:按需生产,根据客户需求进行生产,以减少库存和降低生产成本。
4. 稳定的生产节拍:通过对生产节拍进行稳定控制,实现高效率的生产。
5. 制造流动:实现从原材料采购到产品交付的流畅生产流程,减少等待时间和库存。
6. 质量第一:注重质量控制和质量改进,确保产品达到客户要求。
7. 持续改进:通过不断进行问题解决和流程改进,提高生产效率和质量水平。
四、TPS(JIT)的实施步骤1. 价值流分析:对生产流程进行详细分析,确定价值流和非价值流,通过价值流图找出浪费和瓶颈,制定相应改进措施。
2. 拉动生产:根据客户需求进行生产,并严格控制生产数量和周期,避免过量生产和库存积压。
3. 平衡生产:通过平衡生产节拍和资源利用,确保生产流程的稳定和高效。
4. 连续改进:持续进行问题解决和流程改进,推动生产效率和质量的不断提升。
五、TPS(JIT)的优势1. 降低库存成本:通过拉动生产和减少库存积压,降低了库存成本和堆积风险。
- 1、下载文档前请自行甄别文档内容的完整性,平台不提供额外的编辑、内容补充、找答案等附加服务。
- 2、"仅部分预览"的文档,不可在线预览部分如存在完整性等问题,可反馈申请退款(可完整预览的文档不适用该条件!)。
- 3、如文档侵犯您的权益,请联系客服反馈,我们会尽快为您处理(人工客服工作时间:9:00-18:30)。
长春一汽工艺装备有限公司
二、什么是TPS(含义)
长春一汽工艺装备有限公司
1、TPS的含义
TPS是Toyota Production System的缩写, 翻译为丰田生产方式。
TPS是丰田的工业工程,丰田专家讲TPS是赚钱 的管理技术。TPS是丰田人几十年管理经验的总 结,是战胜危机,战胜竞争对手的有力武器。 TPS的理念已经成为丰田人的基本理念,已成为 丰田的企业文化。
长春一汽工艺装备有限公司
3、TPS(丰田生产方式)的基本目的
追求利润是企业得以经营的前提条件之 一,为了产生效益,丰田生产方式将降 低成本作为基本的第一位目标。
长春一汽工艺装备有限公司
4、为降低成本消除一切浪费
为了实现增大利润的目的,必须彻底消除企业பைடு நூலகம்的一 切浪费,也就是消除企业中所有的不合理现象,实现 “零浪费”。
长春一汽工艺装备有限公司
自働化与自动化的区别
自働化
一旦发生异常,机械自行判断停 机。
即使出现不良,机械、模具、夹 具不会破损。
机械因异常而停机,所以,问题 点显而易见。
可实现节省人力。
自动化
人不切断开关,机械就一直运转
易发生残次品和大的机械故障。
由于依赖人手保护,因而难以防 止再发生。
仅限于省力。
如果只是单纯地摆放,那只不过是排列而已。
所谓整顿,是把已整理过的东西、即需要的东西 整齐地摆放,以便于使用。
即使是需要的东西,如果杂乱堆放或所属地不明 确,也会由于不便使用而增加查找作业量,从而使问 题严重化。
长春一汽工艺装备有限公司
所谓清扫,是指机械设备因切屑或油脂而严重 污染、地面上散乱摆放不需要的零部件或切屑较多 时,难以作业,并且不能充分发挥机械设备及人的 能力,因此需要清扫干净。
生产过剩的浪费 是最大、最严重的浪费。
产过剩有两种 一种是在所规定的时间内产生了数量过剩的产品; 一种是比规定的时间提前完成了生产任务。(从市场经
长春一汽工艺装备有限公司
TPS培训内容
2004年2月
长春一汽工艺装备有限公司
目录
一、为什么要组织学习TPS 二、什么是TPS 三、TPS提供的方法 四、结合工装公司实际推行TPS
长春一汽工艺装备有限公司
一、为什么要组织学习TPS
长春一汽工艺装备有限公司
1、2003年底竺总提出了向轿车公司学习的要求, 轿车公司、解放公司推行TPS都已经收到了比较 好的效果。
长春一汽工艺装备有限公司
1、TPS的含义
是彻底消除浪费。支撑这种思想的两大支柱是 准时化、 自働化。 丰田生产方式是关于生产系统设计和运作的综 合体系,它包含着“制造产品”的思路、“生 产 管理”的思路和“物流”的思路。
长春一汽工艺装备有限公司
2、TPS的精髓:
准时化、 自働化。
准时化的概念 将必需的产品,仅按必需的数量,在必需的时候生产。
整顿、清扫、清洁、素养(顺序不能乱)。
看板方式是实现准时生产的管理手段。
支撑准时化的六项措施生产的均衡化、作业转换
时间的缩短、设备布局的筹划、作业的标准化、自动 化、改善活动。
长春一汽工艺装备有限公司
5S管理(是实现准时化生产的前提和基
础)
整理 整顿 清扫 清洁 素养
长春一汽工艺装备有限公司
所谓整理,就是把不需要的东西与需要的东西区 分开,马上处理不需要物品。换句话说,现在摆放的 零部件或坯料应该全是真正需要的东西,否则,必须 改善。
准时化的基本原则 依据需求量制定节拍 后工序领取(后工序的人按照必需的数量,在必需的时候 到前工序去领取所必需的零部件) 按流程生产
长春一汽工艺装备有限公司
准时化
准时化的前提是平准化所谓平准化,不只是把生
产量平均化,而是把生产量、种类、时间、工时综合 起来平均化。
准时化的必要条件是具备5S管理的基础整理、
请记住这样一句名言:减少一成的浪费等于增加一倍 的销售额。
试想一下,假设在商品售价中成本占90%,利润占 10%,如果一切生产经营活动维持现状,想把利润提高 一倍,就必须把销售额增加一倍。这是非常困难的事 情。然而从占商品售价90%的总成本当中部剥离出 10%的不合理因素及无畏的浪费,就相对容易得多了。
2、集团公司党委在2004年、2005年的工作纲要中 都相继提出了深化TPS工作的要求,而且把推进 TPS作为党委工作与经济工作的融合点。
长春一汽工艺装备有限公司
3、 TPS是丰田人的管理方式,这种管理方式得到 了世界的公认。美国的通用公司连续12年位居 世界500强之首,是全球汽车行业的老大。就是 这样的美国通用大公司,也想通过与丰田公司合 资的方式,深入分析研究丰田的生产经营方式; 而丰田公司也想通过与美国通用公司的合资,直 接进入美国的劳动力市场,并可以更多地了解到 丰田公司在美国面临的种种难题。正是双方利益 的要求,促使丰田与通用这两个远隔重洋的世界 汽车巨人历史性地结合起来。1984年,丰田与 通用公司正式合资,名为新联合汽车制造公司经 美国联邦贸易委员会核准成立。
所谓清洁,指维持整理、整顿、清扫3S的成果。 所谓素养,是具有经常地遵守已经决定了的事 情的习惯。
长春一汽工艺装备有限公司
自働化
带有自动停止装置的“智能”自动 化。丰田人把它称之为“带人字旁的自 働化”。
就是防止不合格品从前工序流 入后工序,不使后工序造成混乱, 并以此保证准时生产。(不接受不合
格品,不制造不合格品,不转移不合格品。)
长春一汽工艺装备有限公司
4、推行TPS生产方式,要求企业的管理具有一定 的基础,象工装公司现有的管理水平或者说基础 比较差,要推行TPS应该说难度是很大。公司 领导班子已经做出决定,TPS要推,要通过学习、 引进TPS的思想和先进方法,结合我们的实际, 把实现降成本、提高质量、缩短交货期作为目标, 最终达到实现企业高效益的目的。因此说推行 TPS是我们公司今年的一项重点工作。
长春一汽工艺装备有限公司
5、不同的生产方式存在不同的浪费
普通的生产方法
材料
A
成品
B
C
流水化工序的生产方法
材料 A B C
成品
长春一汽工艺装备有限公司
6、生产现场浪费的7种现象
生产过剩的浪费 停工等待浪费 搬运的浪费 加工过程本身的浪费 库存的浪费 动作的浪费 制造不良的浪费
长春一汽工艺装备有限公司