球铁冒口根部缩孔分析
铸铁缩孔、缩松的热分析测量与预防

铸铁缩孔、缩松的热分析测量与预防概述:铁水质量的热分析方法源于金属学中的相图理论,在发达国家早已广泛用于铁水的在线检测和控制,是高质量铸铁生产中依赖的检测手段,在提高资源利用率、节能减排中发挥着重要的作用。
随着我们对热分析技术的了解,能够改变我们以往仅从成分角度来进行材质控制的初级状态。
可以使我们对活性成分共晶度的概念、型核物质的作用、消除缺陷的机理从理念上发生质的飞跃。
为了使大家能够掌握热分析技术的优势,正确使用热分析解决生产中具体的质量问题,普遍提高我国的铸件材质水平和参与国际市场竞争的能力。
在此依个人之浅见就热分析测量和预防缩孔、缩松方面的作用,向大家做一个介绍。
1、热分析测量缩孔、缩松的方法取铁水浇入H-3QG样杯,用HF-08T型铁水质量热分析仪对孕育或球化后的铁水进行测量。
热分析仪首先记录下样杯内铁水的凝固温度曲线:铁水质量热分析仪通过对凝固温度曲线的解析,找出铁水凝固过程的各种相变特征参数。
将相变特征参数值带入数学模型,即可计算出铁水凝固组织中的:初生奥氏体生成量、再辉段石墨生成量、再辉后石墨生成量,进而可以计算出凝固组织的缩孔率和缩松率。
2、热分析测量缩孔概率的机理铁水降温到初晶温度点(TL),在铸型的激冷作用下首先凝固出一个的激冷壳。
从初晶温度点(TL)到共晶开始点(TEL)的凝固过程,是初生奥氏体晶芽生长成树枝状奥氏体枝晶的过程。
由于液态的铁水可以在树枝状枝晶间流动,降温、凝固收缩产生的体积空位,可由上部的液态铁水绕过枝晶进行填补。
因此在激冷壳内凝固产生的体积空位经流动铁水的补充后,在上部的中心合并成一个集中的体积空位,这就是缩孔的形成过程。
热分析能够测量出凝固铁水的初晶温度点(TL)和共晶开始点(TEL),可以通过测量凝固铁水在这个区间释放的热量,计算出初生奥氏体枝晶生成量和体积收缩率。
因此可以在浇注前预测铁水的缩孔率。
简而言之:共晶度越低,液-固两相区的温差越大,枝晶生成量越大、被测铁水的缩孔率越大。
10步解决解决球墨铸铁件缩孔、缩松问题
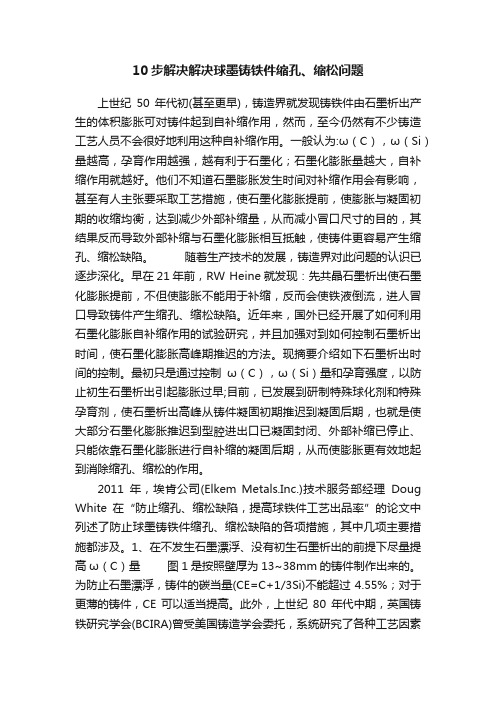
10步解决解决球墨铸铁件缩孔、缩松问题上世纪50年代初(甚至更早),铸造界就发现铸铁件由石墨析出产生的体积膨胀可对铸件起到自补缩作用,然而,至今仍然有不少铸造工艺人员不会很好地利用这种自补缩作用。
一般认为:ω(C),ω(Si)量越高,孕育作用越强,越有利于石墨化;石墨化膨胀量越大,自补缩作用就越好。
他们不知道石墨膨胀发生时间对补缩作用会有影响,甚至有人主张要采取工艺措施,使石墨化膨胀提前,使膨胀与凝固初期的收缩均衡,达到减少外部补缩量,从而减小冒口尺寸的目的,其结果反而导致外部补缩与石墨化膨胀相互抵触,使铸件更容易产生缩孔、缩松缺陷。
随着生产技术的发展,铸造界对此问题的认识已逐步深化。
早在21年前,RW Heine就发现:先共晶石墨析出使石墨化膨胀提前,不但使膨胀不能用于补缩,反而会使铁液倒流,进人冒口导致铸件产生缩孔、缩松缺陷。
近年来,国外已经开展了如何利用石墨化膨胀自补缩作用的试验研究,并且加强对到如何控制石墨析出时间,使石墨化膨胀高峰期推迟的方法。
现摘要介绍如下石墨析出时间的控制。
最初只是通过控制ω(C),ω(Si)量和孕育强度,以防止初生石墨析出引起膨胀过早;目前,已发展到研制特殊球化剂和特殊孕育剂,使石墨析出高峰从铸件凝固初期推迟到凝固后期,也就是使大部分石墨化膨胀推迟到型腔进出口已凝固封闭、外部补缩已停止、只能依靠石墨化膨胀进行自补缩的凝固后期,从而使膨胀更有效地起到消除缩孔、缩松的作用。
2011年,埃肯公司(Elkem Metals.Inc.)技术服务部经理Doug White在“防止缩孔、缩松缺陷,提高球铁件工艺出品率”的论文中列述了防止球墨铸铁件缩孔、缩松缺陷的各项措施,其中几项主要措施都涉及。
1、在不发生石墨漂浮、没有初生石墨析出的前提下尽量提高ω(C)量图1是按照壁厚为13~38mm的铸件制作出来的。
为防止石墨漂浮,铸件的碳当量(CE=C+1/3Si)不能超过4.55%;对于更薄的铸件,CE可以适当提高。
铸件冒口下面总是缩孔咋办?

铸件冒口下面总是缩孔咋办?
联合铸造联合铸造 2022-02-23 10:14
一、冒口颈缩孔产生的机理
冒口颈缩孔是指冒口中缩孔穿过冒口颈,侵入铸件中,形成二次缩孔(内缩孔)主要的原因是冒口颈凝固的比铸件早,堵塞了冒口至热节的补缩通道(凝固过程中从热节依次挪移至冒口颈、冒口的液相形成的通道),使冒口中的金属液不能对热节凝固时发生的体积亏损进行补偿(补缩),就产生冒口颈缩孔。
二、冒口颈缩孔引起的原因分析
1、过长的凝固时间 ;
2、过多的补缩口;
3、浇注温度;
4、过大的内浇口 ;
5、碳硅当量过高 ;
6、浇注系统的设计;
7、内浇口形状。
三、解决方案
1、过多的补缩口
图片
遇到这种情况,可以尝试改进浇注系统,均匀进水,用一个大的冒口补缩。
2、浇注温度
图片
解决方法:
在生产过程中控制好浇注温度,球铁温度控制在1360以上,灰铁控制在1400度以下。
3、浇铸系统的设计
解决方法:合理设计浇注系统,特别要注意铁水的流速及流向球铁浇注系统建议比例:直:横:内=1:1.2-2.0:0.75
免责声明:文章系转载,首先对原创作者表示感谢。
因转载次数过多,文章来源不甚清晰,因此未标明原创作者及文章来源,且文章的真实性有待核实。
文章角度不代表“联合铸造”平台立场,仅作交流信息所用,如有侵权,请在后台留言,经核实后小编会即时做出删除处理,不承担任何法律责任。
球墨铸铁常见缺陷的分析与对策
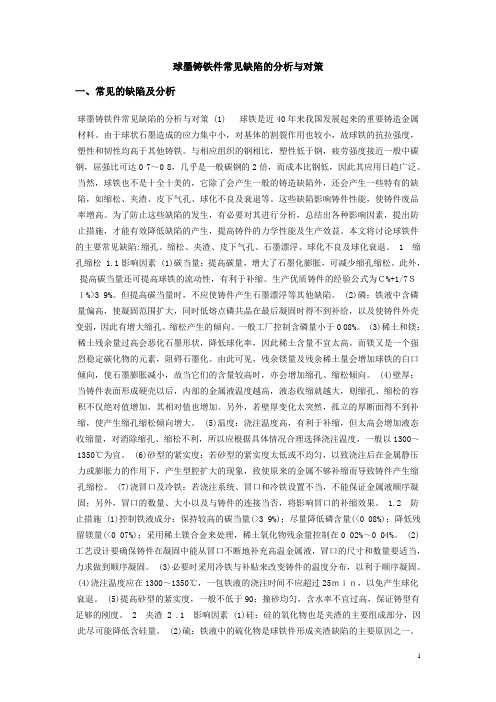
球墨铸铁件常见缺陷的分析与对策一、常见的缺陷及分析球墨铸铁件常见缺陷的分析与对策 (1) 球铁是近40年来我国发展起来的重要铸造金属材料。
由于球状石墨造成的应力集中小,对基体的割裂作用也较小,故球铁的抗拉强度,塑性和韧性均高于其他铸铁。
与相应组织的钢相比,塑性低于钢,疲劳强度接近一般中碳钢,屈强比可达0 7~0 8,几乎是一般碳钢的2倍,而成本比钢低,因此其应用日趋广泛。
当然,球铁也不是十全十美的,它除了会产生一般的铸造缺陷外,还会产生一些特有的缺陷,如缩松、夹渣、皮下气孔、球化不良及衰退等。
这些缺陷影响铸件性能,使铸件废品率增高。
为了防止这些缺陷的发生,有必要对其进行分析,总结出各种影响因素,提出防止措施,才能有效降低缺陷的产生,提高铸件的力学性能及生产效益。
本文将讨论球铁件的主要常见缺陷:缩孔、缩松、夹渣、皮下气孔、石墨漂浮、球化不良及球化衰退。
1 缩孔缩松 1.1影响因素 (1)碳当量:提高碳量,增大了石墨化膨胀,可减少缩孔缩松。
此外,提高碳当量还可提高球铁的流动性,有利于补缩。
生产优质铸件的经验公式为C%+1/7Si%>3 9%。
但提高碳当量时,不应使铸件产生石墨漂浮等其他缺陷。
(2)磷:铁液中含磷量偏高,使凝固范围扩大,同时低熔点磷共晶在最后凝固时得不到补给,以及使铸件外壳变弱,因此有增大缩孔、缩松产生的倾向。
一般工厂控制含磷量小于0 08%。
(3)稀土和镁:稀土残余量过高会恶化石墨形状,降低球化率,因此稀土含量不宜太高。
而镁又是一个强烈稳定碳化物的元素,阻碍石墨化。
由此可见,残余镁量及残余稀土量会增加球铁的白口倾向,使石墨膨胀减小,故当它们的含量较高时,亦会增加缩孔、缩松倾向。
(4)壁厚:当铸件表面形成硬壳以后,内部的金属液温度越高,液态收缩就越大,则缩孔、缩松的容积不仅绝对值增加,其相对值也增加。
另外,若壁厚变化太突然,孤立的厚断面得不到补缩,使产生缩孔缩松倾向增大。
球铁冒口根部缩孔分析

球铁冒口根部缩孔分析(总4页)-CAL-FENGHAI.-(YICAI)-Company One1-CAL-本页仅作为文档封面,使用请直接删除球铁冒口根部缩孔分析球墨铸铁大多数是共晶或过共晶成分,在凝固过程中受石墨膨胀及过冷的影响促使收缩值增大所以在凝固过程中就形成了缩孔缩松缺陷的产生,在球铁件铸造中除了利用石墨化膨胀进行自补缩之外必须进行外部补缩,无冒口铸造实际上是利用浇注系统进行补缩。
由于浇注系统的补缩能力往往不如冒口,因而无冒口铸造对铸型条件以及其他工艺条件的要求远远高于采用冒口补缩。
由于这个缘故,冒口补缩工艺仍然是目前球铁件的主要生产工艺。
然而,冒口补缩工艺在实际应用中遭遇失败的实例也甚多,致使不少铸造人员往往轻易认为某些球铁件不能采用冒口补缩工艺,只能采用无冒口工艺,实际上冒口补缩失败的原因往往是由于所采用的工艺不恰当所致。
因此,对引起冒口补缩失败的原因进行分析,将有助于认识球铁的工艺特性和正确掌握球铁件的铸造工艺。
根据笔者的实践,除铸型刚度、化学成分、原材料和铁水熔炼处理方面的因素之外,造成球铁件冒口补缩失败的铸型工艺因素(1)采用明冒口,导致石墨化膨胀压力松驰,使膨胀不能用于补缩。
(2)铁水先进入铸件型腔,加热型腔、温度降低后,再由铸件型腔进入冒口,因而后者温度始终低于铸件,故称为“冷冒口”;这种冒口由于其铁水先加热型腔,使型腔过热,冒口本身早于铸件凝固,不但不能起补缩作用,反而从铸件抽吸铁水,使铸件产生缩松、缩孔。
不少人企图通过加大冷冒口的尺寸希望能使其冷速减慢,起到补缩作用,结果是:冷冒口越大,铸件排放的冷铁水越多,型腔铁水流过量越大,过热也就越严重,“上冷下热”温差越大,缩孔、缩松越严重。
即使浇注后往冷冒口冲注热铁水,由于冲入铁水量有限,并不能扭转情况。
铁水经由冒口进入铸件,冒口温度高于铸件,故称为“热冒口”,冒口迟于铸件凝固,使轮毂部位直接得到补缩,而从轮毂流出的铁水在向周围的轮辐扩散、流入轮缘过程中,由于轮辐散热面积大,铁水温度迅速降低,完成部分凝固和收缩,及时从冒口吸取补缩液体,因而也有利于防止轮缘部位缩松。
球墨铸铁缩松缺陷,都与哪些因素有关

球墨铸铁缩松缺陷,都与哪些因素有关墨铸件已广泛应用于大型模具铸造领域,是毛坯件最常用的生产工艺之一,随着汽车工业的迅速发展,裝备模具需求量逐年增长,铸造缺陷的影响也逐步凸显,常见缺陷有皱皮、变形、缩孔、夹砂和积碳等,本文主要针对球墨铸件缩孔缺陷进行研究。
1.缩孔的形成及危害(1)缩孔產生机理液态合金铁液由液态到固态过程中会出现体积变小現象,经历液态收缩、凝固收缩、固态收缩三个收缩过程。
当液态收缩量与凝固收缩量大于固态收缩量时便会产生缩孔,形状极不规则,孔壁粗糙并带有枝状晶,缩孔分为集中缩孔(简称缩孔)和分散缩孔(简称缩松)。
(2)缩孔特点缩孔主要集中在铸件的上部和最后凝固的部位,以及铸件壁厚悬殊处、凹角圆角半径小及内浇道附近等凝固较晚或凝固缓慢的部位(称為热节)。
缩孔表现出来的形式主要有4种,即明缩孔、夹角缩孔、芯面缩孔、内缩孔,如图1所示。
(a)明缩孔(b)夹角缩孔(c)芯面缩孔(d)内縮孔图1 缩孔形式(3)缩孔在模具中的危害主要有以下4个方面:一是减少铸件的有效承载截面积,甚至造成应力集中而大大降低铸件的物理和力学性能;二是铸件的连续性被破坏,使铸件的气密性、抗蚀性等性能显著降低;三是加工后铸件表面的粗糙度提高,致使制件拉毛;四是缩孔在球墨铸铁缺陷中占据很大比例,往往成为不可修复的缺陷,直接造成铸件报废,给企业带来巨大的經济损失。
2. 缩孔缺陷位置通过对以往铸件失效现象统计分析发现,球墨铸铁缩孔缺陷多发生于高牌号球墨铸铁的以下部位:铸件的热节和最后凝固部位;承重部位或使用麵部位;表面10mm以下部位。
如图2、图3所示。
图2图33. 原因分析(1)铸件热节和最后凝固部位的缩孔铸件热节部位多出现在铸件三面夹角、拐角、直径小的铸孔以及壁厚悬殊部位,热量散发缓慢或集中到某一点,铁液外层已凝固,但热节点位置仍处于液态,凝固层逐渐形成枝状晶并不断生长将尚存的铁液分割成若干个互不相同的熔池,随著温度的降低热节位置開始出现收缩,體积变小,此时不能得到铁液补充而凝固后的孔壁粗糙、排满树枝晶的疏松孔,形成大量分散缩孔。
铸铁件缩松、缩孔、凹陷缺陷的原因分析与防止方法
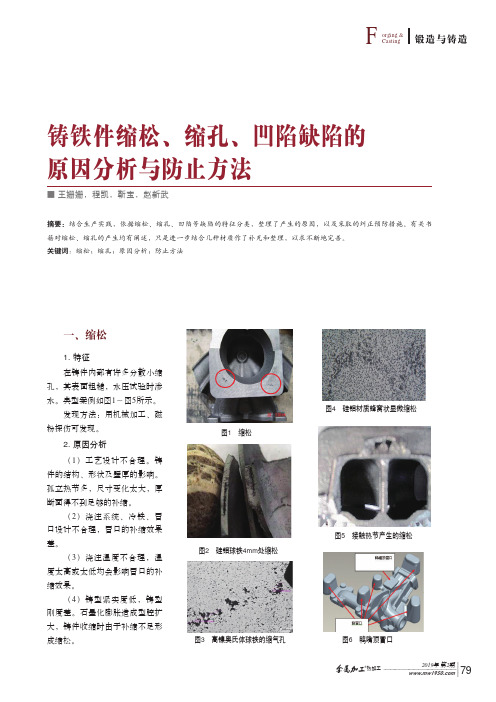
2019年第2期热加工79F锻造与铸造orging &Casting铸铁件缩松、缩孔、凹陷缺陷的原因分析与防止方法■王姗姗,程凯,靳宝,赵新武摘要:结合生产实践,依据缩松、缩孔、凹陷等缺陷的特征分类,整理了产生的原因,以及采取的纠正预防措施。
有关书籍对缩松、缩孔的产生均有阐述,只是进一步结合几种材质作了补充和整理,以求不断地完善。
关键词:缩松;缩孔;原因分析;防止方法一、缩松1. 特征在铸件内部有许多分散小缩孔,其表面粗糙,水压试验时渗水。
典型案例如图1~图5所示。
发现方法:用机械加工、磁粉探伤可发现。
2. 原因分析(1)工艺设计不合理。
铸件的结构、形状及壁厚的影响。
孤立热节多,尺寸变化太大,厚断面得不到足够的补缩。
(2)浇注系统、冷铁、冒口设计不合理,冒口的补缩效果差。
(3)浇注温度不合理,温度太高或太低均会影响冒口的补缩效果。
(4)铸型紧实度低,铸型刚度差。
石墨化膨胀造成型腔扩大,铸件收缩时由于补缩不足形成缩松。
图1 缩松图2 硅钼球铁4mm处缩松图4 硅钼材质蜂窝状显微缩松图3 高镍奥氏体球铁的缩气孔图5 接触热节产生的缩松图6 鸭嘴顶冒口2019年 第2期 热加工80F锻造与铸造orging &Casting(5)碳、硅含量低,磷含量较高;凝固区间大。
硅钼和高镍球墨铸铁对碳、硅含量和氧化铁液的敏感性特大,铁液严重氧化或碳、硅量低时,易出现显微缩松。
即便在薄壁处也容易出现缩松(见图2、图3、图4)。
(6)孕育不充分,石墨化效果差。
(7)残余镁量和稀土量过高。
钼含量较高时也会增加显微缩松。
(8)浇注速度太快。
(9)炉料锈蚀,氧化铁多。
(10)铁液在电炉内高温停放时间太长,俗称“死铁水”,造成严重氧化。
(11)冲天炉熔炼时底焦太底,风量太大,元素烧损大,铁液严重氧化。
(12)冒口径处形成接触热节产生缩松(见图5)。
(13)压箱铁不够(或箱卡未锁紧,箱带断裂等),浇注后由于涨箱造成缩松。
有关球铁铸件缩孔缩松形成及预防

有关球铁铸件缩孔缩松形成及预防摘要,阐述有关球墨铸铁凝固特性、凝固过程体积变化和缩孔、缩松形成机理以及本人就缩孔、缩松的预防提出了看法。
关键词,球墨铸铁件,缩孔,缩松,防止前言球墨铸铁具有较大的缩孔、缩松倾向,如何防止和消除一直是铸造工作者关注的问题。
由于球墨铸铁缩孔、缩松形成的复杂性,在缩孔、缩松的形成机理和防止措施方面,存在许多不一致甚至相互矛盾的看法。
为有助于对此问题进行更深的研究,本文讲述有关球墨铸铁铸件缩孔、缩松的形成及预防,并就缩孔、缩松的预防方法发表本人的看法。
1 定义球墨铸铁是通过球化和孕育处理得到球状石墨,有效地提高了铸铁的机械性能,特别是提高了塑性和韧性,从而得到比碳钢还高的强度 1.1成分球墨铸铁除铁外的化学成分通常为:含碳量3.6,3.8,,含硅量2.0,3.0,,含锰、磷、硫总量不超过1.5,和适量的稀土、镁等球化剂1.2性能球铁铸件差不多已在所有主要工业部门中得到应用,这些部门要求高的强度、塑性、韧性、耐磨性、耐严重的热和机械冲击、耐高温或低温、耐腐蚀以及尺寸稳定性等。
为了满足使用条件的这些变化、球墨铸铁现有许多牌号,提供了机械性能和物理性能的一个很宽的范围。
如国际标准化组织ISO1083所规定的大多数球墨铸铁铸件,主要是以非合金态生产的。
显然,这个范围包括抗拉强度大于800牛顿/毫米,延伸率为2%的高强度牌号。
另一个极端是高塑性牌号,其延伸率大于17%,而相应的强度较低(最低为370牛顿/毫米勺。
强度和延伸率并不是设计者选择材料的唯一根,而其它决定性的重要性能还包括屈服强度、弹性模数、耐磨性和疲劳强度、硬度和冲击性能。
另外,耐蚀性和抗氧化以及电磁性能1对于设计者也许是关键的。
为了满足这些特殊使用,研制了一组奥氏体球铁,通常叫傲Ni一Resis亡球铁。
这些奥氏体球铁,主要用锌、铬和锰合金化,并且列入国际标准。
2球墨铸铁的凝固特点球墨铸铁有着与其它合金不同的凝固特点:(1)共晶凝固温度范围宽,呈糊状凝固(2)与灰铸铁相比,共晶团数多,共晶膨胀较大。
球铁缩松(厚大件)问题
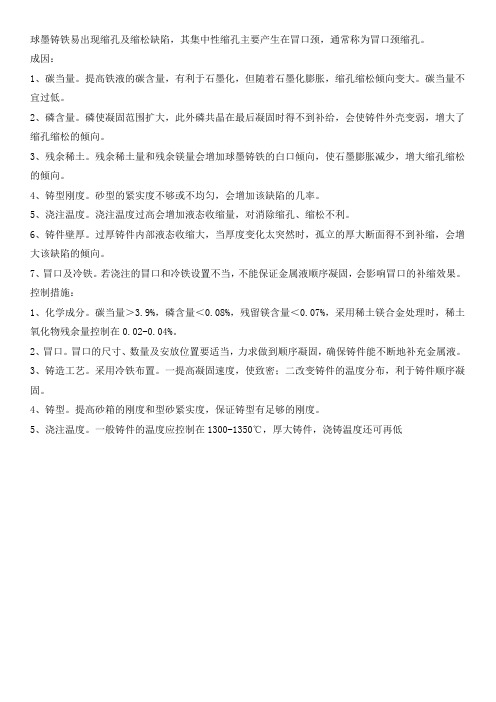
球墨铸铁易出现缩孔及缩松缺陷,其集中性缩孔主要产生在冒口颈,通常称为冒口颈缩孔。
成因:
1、碳当量。
提高铁液的碳含量,有利于石墨化,但随着石墨化膨胀,缩孔缩松倾向变大。
碳当量不宜过低。
2、磷含量。
磷使凝固范围扩大,此外磷共晶在最后凝固时得不到补给,会使铸件外壳变弱,增大了缩孔缩松的倾向。
3、残余稀土。
残余稀土量和残余镁量会增加球墨铸铁的白口倾向,使石墨膨胀减少,增大缩孔缩松的倾向。
4、铸型刚度。
砂型的紧实度不够或不均匀,会增加该缺陷的几率。
5、浇注温度。
浇注温度过高会增加液态收缩量,对消除缩孔、缩松不利。
6、铸件壁厚。
过厚铸件内部液态收缩大,当厚度变化太突然时,孤立的厚大断面得不到补缩,会增大该缺陷的倾向。
7、冒口及冷铁。
若浇注的冒口和冷铁设置不当,不能保证金属液顺序凝固,会影响冒口的补缩效果。
控制措施:
1、化学成分。
碳当量>3.9%,磷含量<0.08%,残留镁含量<0.07%,采用稀土镁合金处理时,稀土氧化物残余量控制在0.02-0.04%。
2、冒口。
冒口的尺寸、数量及安放位置要适当,力求做到顺序凝固,确保铸件能不断地补充金属液。
3、铸造工艺。
采用冷铁布置。
一提高凝固速度,使致密;二改变铸件的温度分布,利于铸件顺序凝固。
4、铸型。
提高砂箱的刚度和型砂紧实度,保证铸型有足够的刚度。
5、浇注温度。
一般铸件的温度应控制在1300-1350℃,厚大铸件,浇铸温度还可再低。
【坛友分享】球铁件七种常见缺陷原因分析

【坛友分享】球铁件七种常见缺陷原因分析热加工行业论坛热加工行业论坛昨天1、石墨球异化石墨球异化出现不规则石墨,如团块状、蝌蚪状、蠕虫状、角状或其他非圆球状。
这是由于球状石墨沿辐射方向生长时,局部晶体生长模式和生长速率偏离正常生长规律所致。
铸件中残余球化元素量超出应有范围时,如残余镁太高,超过了保持石墨球化所需的最低量时,也会影响石墨结晶条件,就容易产生蝌蚪壮石墨。
而残余稀土较多时,高碳当量铁水易产生碎块石墨,碎块石墨的集中区域一般称做“灰斑”。
而蠕虫状石墨的出现则是由于球化元素残余量不足或者含有超限的钛和铝。
2、石墨漂浮过共晶成分的厚壁球铁件中,在浇注位置顶部,常常出现一个石墨密集区域,即“始末漂浮”现象,这是由于石墨与铁水密度不同,过共晶铁水直接析出的石墨受到浮力作用向上所致。
石墨漂浮程度与碳当量、球化元素的种类及残留量、铸件凝固时间、浇注温度等因素有关系。
镁能使球铁的共晶含碳量提高,碳当量相同的铁水,提高其残余镁量就能减少石墨漂浮,残留稀土量过高,有助于爆裂状石墨的升成。
3、反白口一般铸铁件的白口组织容易出现在冷却较快的表层、尖角、披缝等处,反白口缺陷则相反,碳化物相出现在铸件中等断面心部、热节等部位。
球化元素残余量过多时,有促进反白口缺陷产生的作用,稀土元素强于镁,它们一般都能增加球铁组织形成时的过冷度。
4、皮下针孔皮下针孔内主要含有氢,也有少量一氧化碳和氮。
残余镁量过高时,也同时加强了从湿型中吸收氢的倾向,因而产生皮下针孔的几率增加。
另外,球化铁水停留时间长也能增加针孔的数量。
5、缩孔缩松缩孔常出现在铸件最后凝固部位(热节处、冒口颈与铸件连接处、内角或内浇口与铸件连接处),是隐蔽于铸件内部或与外表连通的孔洞。
缩松,宏观的出现在热节处,细微的收缩孔洞,大多是孔洞内部互相连通。
与球化元素有关的是,要控制残余镁和稀土不能过高,这对减少宏观和微观缩松都有明显效果,缩松倾向几乎与球化元素成正比。
6、黑渣它一般发生在铸件的上部(浇注位置),主要分为块状、绳索状和细碎黑渣。
球墨铸铁常见缺陷的分析与对策
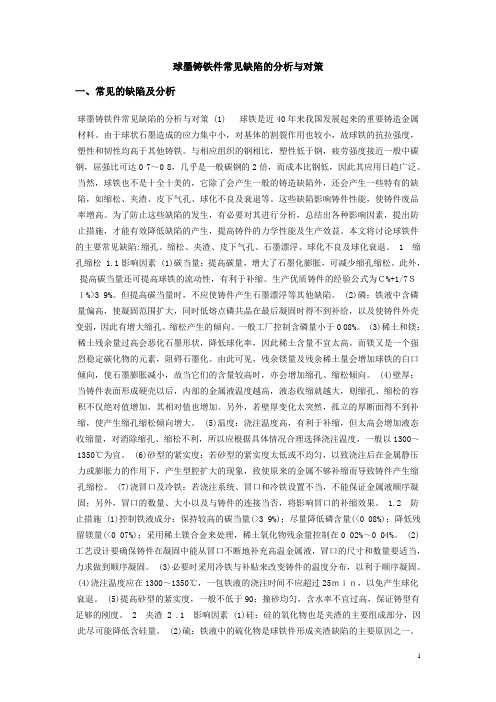
球墨铸铁件常见缺陷的分析与对策一、常见的缺陷及分析球墨铸铁件常见缺陷的分析与对策 (1) 球铁是近40年来我国发展起来的重要铸造金属材料。
由于球状石墨造成的应力集中小,对基体的割裂作用也较小,故球铁的抗拉强度,塑性和韧性均高于其他铸铁。
与相应组织的钢相比,塑性低于钢,疲劳强度接近一般中碳钢,屈强比可达0 7~0 8,几乎是一般碳钢的2倍,而成本比钢低,因此其应用日趋广泛。
当然,球铁也不是十全十美的,它除了会产生一般的铸造缺陷外,还会产生一些特有的缺陷,如缩松、夹渣、皮下气孔、球化不良及衰退等。
这些缺陷影响铸件性能,使铸件废品率增高。
为了防止这些缺陷的发生,有必要对其进行分析,总结出各种影响因素,提出防止措施,才能有效降低缺陷的产生,提高铸件的力学性能及生产效益。
本文将讨论球铁件的主要常见缺陷:缩孔、缩松、夹渣、皮下气孔、石墨漂浮、球化不良及球化衰退。
1 缩孔缩松 1.1影响因素 (1)碳当量:提高碳量,增大了石墨化膨胀,可减少缩孔缩松。
此外,提高碳当量还可提高球铁的流动性,有利于补缩。
生产优质铸件的经验公式为C%+1/7Si%>3 9%。
但提高碳当量时,不应使铸件产生石墨漂浮等其他缺陷。
(2)磷:铁液中含磷量偏高,使凝固范围扩大,同时低熔点磷共晶在最后凝固时得不到补给,以及使铸件外壳变弱,因此有增大缩孔、缩松产生的倾向。
一般工厂控制含磷量小于0 08%。
(3)稀土和镁:稀土残余量过高会恶化石墨形状,降低球化率,因此稀土含量不宜太高。
而镁又是一个强烈稳定碳化物的元素,阻碍石墨化。
由此可见,残余镁量及残余稀土量会增加球铁的白口倾向,使石墨膨胀减小,故当它们的含量较高时,亦会增加缩孔、缩松倾向。
(4)壁厚:当铸件表面形成硬壳以后,内部的金属液温度越高,液态收缩就越大,则缩孔、缩松的容积不仅绝对值增加,其相对值也增加。
另外,若壁厚变化太突然,孤立的厚断面得不到补缩,使产生缩孔缩松倾向增大。
球铁缩孔缩松的影响因素
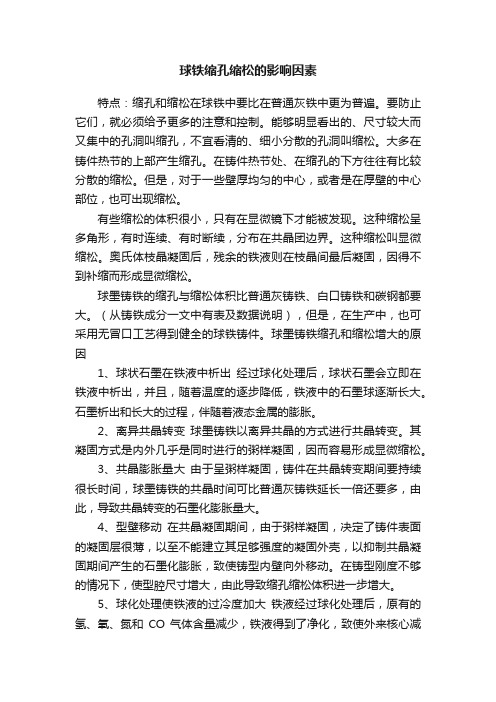
球铁缩孔缩松的影响因素特点:缩孔和缩松在球铁中要比在普通灰铁中更为普遍。
要防止它们,就必须给予更多的注意和控制。
能够明显看出的、尺寸较大而又集中的孔洞叫缩孔,不宜看清的、细小分散的孔洞叫缩松。
大多在铸件热节的上部产生缩孔。
在铸件热节处、在缩孔的下方往往有比较分散的缩松。
但是,对于一些壁厚均匀的中心,或者是在厚壁的中心部位,也可出现缩松。
有些缩松的体积很小,只有在显微镜下才能被发现。
这种缩松呈多角形,有时连续、有时断续,分布在共晶团边界。
这种缩松叫显微缩松。
奥氏体枝晶凝固后,残余的铁液则在枝晶间最后凝固,因得不到补缩而形成显微缩松。
球墨铸铁的缩孔与缩松体积比普通灰铸铁、白口铸铁和碳钢都要大。
(从铸铁成分一文中有表及数据说明),但是,在生产中,也可采用无冒口工艺得到健全的球铁铸件。
球墨铸铁缩孔和缩松增大的原因1、球状石墨在铁液中析出经过球化处理后,球状石墨会立即在铁液中析出,并且,随着温度的逐步降低,铁液中的石墨球逐渐长大。
石墨析出和长大的过程,伴随着液态金属的膨胀。
2、离异共晶转变球墨铸铁以离异共晶的方式进行共晶转变。
其凝固方式是内外几乎是同时进行的粥样凝固,因而容易形成显微缩松。
3、共晶膨胀量大由于呈粥样凝固,铸件在共晶转变期间要持续很长时间,球墨铸铁的共晶时间可比普通灰铸铁延长一倍还要多,由此,导致共晶转变的石墨化膨胀量大。
4、型壁移动在共晶凝固期间,由于粥样凝固,决定了铸件表面的凝固层很薄,以至不能建立其足够强度的凝固外壳,以抑制共晶凝固期间产生的石墨化膨胀,致使铸型内壁向外移动。
在铸型刚度不够的情况下,使型腔尺寸增大,由此导致缩孔缩松体积进一步增大。
5、球化处理使铁液的过冷度加大铁液经过球化处理后,原有的氢、氧、氮和CO 气体含量减少,铁液得到了净化,致使外来核心减少。
并且,铁液的过热温度越高,净化程度也越高,由此导致的过冷倾向也更加剧。
此外,球化元素镁和稀土均能与碳形成炭化物,由此减少了石墨化程度,加大了收缩倾向。
汽车球铁件冒口补缩设计方法及其评价_1_

16
2010 / 1
《现代铸铁》增刊
Casting Method and Process
收稿日期:2009-10-12
修定日期:2010-01-10
作者简介:金永锡(1943-),男,高工,主要从事铸造工艺及材料研究
工作。
限补缩原则指导工艺设计;但很遗憾,多年的实践 结果证明:该设计理论和方法并不适用汽车球铁 件,而且其与传统工艺设计的不同思路和方法,反 而引起更多的困惑和混乱。
因而,对于汽车球铁件的补缩工艺和设计方 法,需要重新思考和认识。
文章编号:1003-8345(2010)Z1-0015-11
Risering Methods for Feeding Automotive Nodular Iron Castings and Their Evaluation(Ⅰ)
JIN Yong-xi
(Shanghai Santman Automotive Casting Co. Ltd., Shanghai 201805, China)
由于球墨铸铁的凝固特点,缩孔、缩松往往是 球铁件的主要缺陷,质量要求较高的中小型汽车用 球铁件更是如此。
为此,十余年前笔者公司就试图通过引进凝固 模拟软件,进行缩孔、缩松缺陷的预测和分析。但多 年的实践表明,对汽车类球铁薄壁小件,收缩缺陷 的预测和模拟的准确性还有待提高。与此同时,笔 者公司曾通过项目合作,学习并应用均衡凝固和有
Abstract: The risering methods for feeding nodular iron castings used popularly at present in China and abroad were summarized, and, with practical examples, various design methods were commented. It was considered that the principal key points for riser feeding design of nodular iron automotive castings produced with green sand mould are as follows: (a)Any casting must be fed from outside feeding source;(b)Because both the open riser and cold riser has no or very poor feeding effect, the hot riser should be used to feed castings; (c)The hot risers should be set at hot spots of castings, and the both riser and riser neck must be enough large;(d) The ingate entering the riser must freeze in time when pouring finished; (e)The effective covering scope of both the riser and riser neck should be expanded as possible; (f)Local chilling measures must be adopted for the isolated hot spots which can’t be fed by risers. Key words: automotive castings; riser; design
球铁飞架缩孔原因分析及解决对策
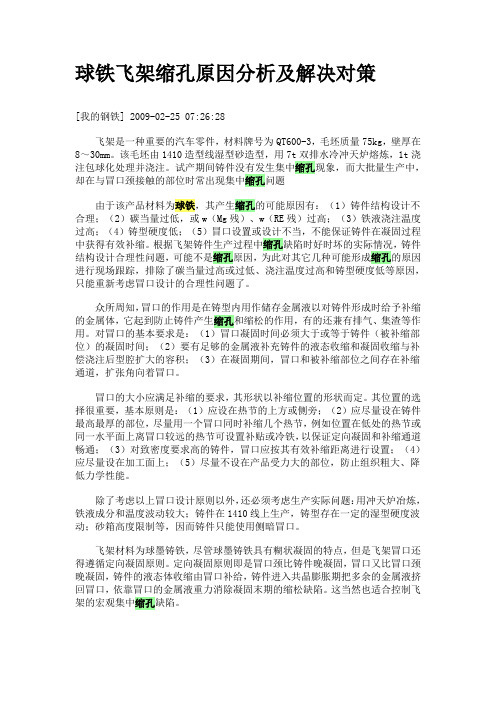
球铁飞架缩孔原因分析及解决对策[我的钢铁] 2009-02-25 07:26:28飞架是一种重要的汽车零件,材料牌号为QT600-3,毛坯质量75kg,壁厚在8~30mm。
该毛坯由1410造型线湿型砂造型,用7t双排水冷冲天炉熔炼,1t浇注包球化处理并浇注。
试产期间铸件没有发生集中缩孔现象,而大批量生产中,却在与冒口颈接触的部位时常出现集中缩孔问题由于该产品材料为球铁,其产生缩孔的可能原因有:(1)铸件结构设计不合理;(2)碳当量过低,或w(Mg残)、w(RE残)过高;(3)铁液浇注温度过高;(4)铸型硬度低;(5)冒口设置或设计不当,不能保证铸件在凝固过程中获得有效补缩。
根据飞架铸件生产过程中缩孔缺陷时好时坏的实际情况,铸件结构设计合理性问题,可能不是缩孔原因,为此对其它几种可能形成缩孔的原因进行现场跟踪,排除了碳当量过高或过低、浇注温度过高和铸型硬度低等原因,只能重新考虑冒口设计的合理性问题了。
众所周知,冒口的作用是在铸型内用作储存金属液以对铸件形成时给予补缩的金属体,它起到防止铸件产生缩孔和缩松的作用,有的还兼有排气、集渣等作用。
对冒口的基本要求是:(1)冒口凝固时间必须大于或等于铸件(被补缩部位)的凝固时间;(2)要有足够的金属液补充铸件的液态收缩和凝固收缩与补偿浇注后型腔扩大的容积;(3)在凝固期间,冒口和被补缩部位之间存在补缩通道,扩张角向着冒口。
冒口的大小应满足补缩的要求,其形状以补缩位置的形状而定。
其位置的选择很重要,基本原则是:(1)应设在热节的上方或侧旁;(2)应尽量设在铸件最高最厚的部位,尽量用一个冒口同时补缩几个热节,例如位置在低处的热节或同一水平面上离冒口较远的热节可设置补贴或冷铁,以保证定向凝固和补缩通道畅通;(3)对致密度要求高的铸件,冒口应按其有效补缩距离进行设置;(4)应尽量设在加工面上;(5)尽量不设在产品受力大的部位,防止组织粗大、降低力学性能。
除了考虑以上冒口设计原则以外,还必须考虑生产实际问题:用冲天炉冶炼,铁液成分和温度波动较大;铸件在1410线上生产,铸型存在一定的湿型硬度波动;砂箱高度限制等,因而铸件只能使用侧暗冒口。
球铁铸件缩孔、缩松的成因与防止
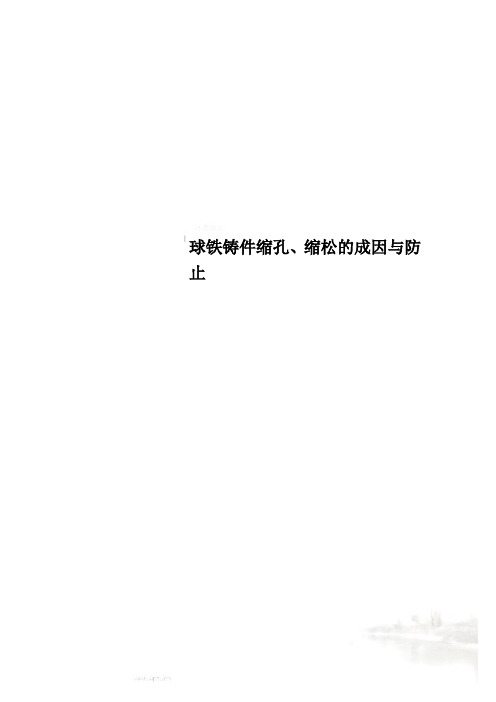
球铁铸件缩孔、缩松的成因与防止球铁铸件缩孔、缩松的成因与防止摘要:球墨铸铁大多数是共晶或过共晶成分,其糊状凝固方式使铸件外壳没有抵抗石墨化膨胀能力,因而铸型产生型壁迁移,增大铸件体积,极易产生内部缩孔、缩松。
球墨铸铁凝固时,在枝晶和共晶团间的最后凝固区域,收缩的体积得不到完全补充,留下的空洞形成宏观及微观缩松。
La 有助于消除缩松倾向。
分析缩孔缩松形成原因并提出相应的防止办法,有助于减少由此产生的废品损失。
关键词:球墨铸铁、收缩、缩孔、缩松1 前言1.1 缺陷形成原因球墨铸铁生产技术日臻完善,多年技术服务的实践表明,生产中出现的铸造缺陷,完全可以用成熟的经验予以消除。
据介绍:工业发达国家的铸造废品率可以控制在1%以下[1],国内先进水平也在2%左右,提高企业铸造技术水平,对减少废品十分重要。
1。
显微缩松显微镜观察微细连续缺失空间多角形疏松枝晶间、共晶团边界间众所周知,灰铸铁是逐层凝固方式,球墨铸铁是糊状凝固方式。
逐层凝固可以使铸件凝固时形成一个坚实的封闭外壳,铸件全封闭外壳的体积收缩可以减小壳体内的缩孔容积。
糊状凝固的特点是金属凝固时晶粒在金属液内部整个容积内形核、生长,固相与液相混合存在有如粥糊。
大多数球墨铸铁是共晶或过共晶成分,其糊状凝固方式使铸件外壳没有抵抗石墨化膨胀的能力,铸型产生型壁迁移,增大铸件体积,极易产生内部缩孔、缩松缺陷。
铸型冷却能力强,有利于铸件的容积凝固转变成逐层凝固,使铸件的分散缩松转变成集中缩孔。
然而,批量生产中湿砂型铸造很难被金属型或干砂型取代。
球墨铸铁凝固有以下三个特点,决定球墨铸铁是糊状凝固方式:①球化和孕育处理显著增加异质核心,核心存在于整个熔体,有利于全截面同时结晶。
②石墨球在奥氏体壳包围下生长,生长速度慢,延缓铸件表层形成坚实外壳;而片状石墨的端部始终与铁液接触,生长速度快,凝固时间短,促使灰铁铸件快速形成坚实外壳。
③球墨铸铁比灰铸铁导热率小 20%-30%,散热慢,外壳生长速度降低[3]。
球墨铸铁件缩孔和缩松问题的解决措施
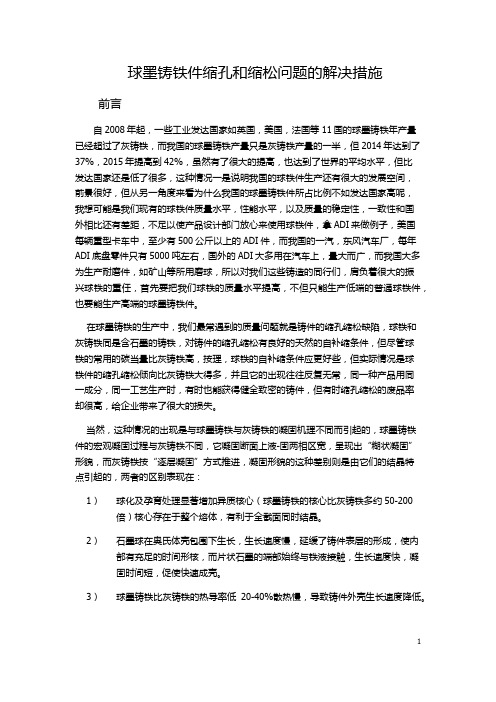
球墨铸铁件缩孔和缩松问题的解决措施前言自2008年起,一些工业发达国家如英国,美国,法国等11国的球墨铸铁年产量已经超过了灰铸铁,而我国的球墨铸铁产量只是灰铸铁产量的一半,但2014年达到了37%,2015年提高到42%,虽然有了很大的提高,也达到了世界的平均水平,但比发达国家还是低了很多,这种情况一是说明我国的球铁件生产还有很大的发展空间,前景很好,但从另一角度来看为什么我国的球墨铸铁件所占比例不如发达国家高呢,我想可能是我们现有的球铁件质量水平,性能水平,以及质量的稳定性,一致性和国外相比还有差距,不足以使产品设计部门放心来使用球铁件,拿ADI来做例子,美国每辆重型卡车中,至少有500公斤以上的ADI件,而我国的一汽,东风汽车厂,每年ADI底盘零件只有5000吨左右,国外的ADI大多用在汽车上,量大而广,而我国大多为生产耐磨件,如矿山等所用磨球,所以对我们这些铸造的同行们,肩负着很大的振兴球铁的重任,首先要把我们球铁的质量水平提高,不但只能生产低端的普通球铁件,也要能生产高端的球墨铸铁件。
在球墨铸铁的生产中,我们最常遇到的质量问题就是铸件的缩孔缩松缺陷,球铁和灰铸铁同是含石墨的铸铁,对铸件的缩孔缩松有良好的天然的自补缩条件,但尽管球铁的常用的碳当量比灰铸铁高,按理,球铁的自补缩条件应更好些,但实际情况是球铁件的缩孔缩松倾向比灰铸铁大得多,并且它的出现往往反复无常,同一种产品用同一成分,同一工艺生产时,有时也能获得健全致密的铸件,但有时缩孔缩松的废品率却很高,给企业带来了很大的损失。
当然,这种情况的出现是与球墨铸铁与灰铸铁的凝固机理不同而引起的,球墨铸铁件的宏观凝固过程与灰铸铁不同,它凝固断面上液-固两相区宽,呈现出“糊状凝固”形貌,而灰铸铁按“逐层凝固”方式推进,凝固形貌的这种差别则是由它们的结晶特点引起的,两者的区别表现在:1)球化及孕育处理显著增加异质核心(球墨铸铁的核心比灰铸铁多约50-200倍)核心存在于整个熔体,有利于全截面同时结晶。
大型球铁管件缩孔和缩松的防治
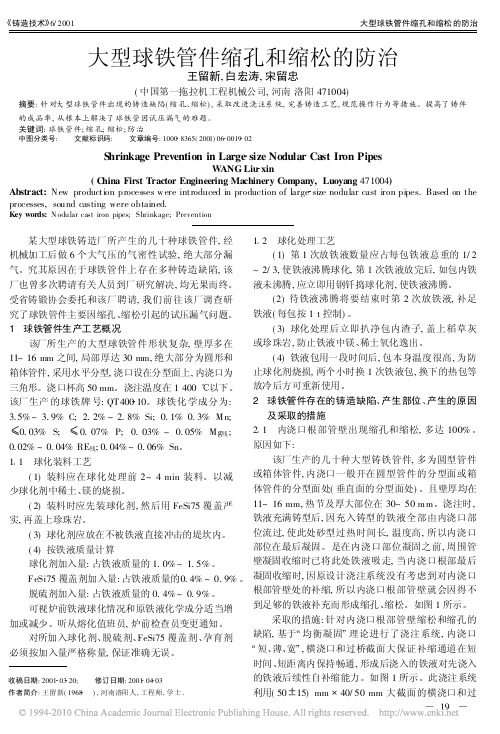
F eSi75 覆盖剂加入量 : 占铁液质量的 0. 4% ~ 0. 9% 。 凝固收缩时, 因原设计浇注系统没有考虑到对内浇口 根部管壁处的补缩, 所以内浇口根部管壁就会因得不 脱硫剂加入量: 占铁液质量的 0. 4% ~ 0. 9% 。 可视炉前铁液球化情况和原铁液化学成分适当增 加或减少。听从熔化值班员, 炉前检查员变更通知。 对所加入球化剂、 脱硫剂、 FeSi75 覆盖剂、 孕育剂 必须按加入量严格称量, 保证准确无误。
( 中国第一拖拉机工程机械公司, 河南 洛阳 471004)
摘要 : 针对大型球铁管件出现的铸造缺陷 ( 缩孔 、 缩松 ) , 采取改进浇注系统 , 完善铸造工艺 , 规范操作行为等措施 。 提高了铸件 的成品率 , 从根本上解决了球铁管因试压漏气的难题 。 关键词 : 球铁管件 ; 缩孔 ; 缩松 ; 防治
图1 典型零件图 1 F ig. 1 T y pical part 1 for casting
桥形成热节补缩区, 过桥的宽度前部同内浇口的宽度 相同, 内浇口截面一般采用厚 5 mm ∃ 宽 30~ 50 mm, 后部向两边斜, 比前边加宽 10 mm 与横浇口相接。内 浇口长 6~ 7 mm, 内浇口设置的多少根据零件品质和 具体位置而定。一般地 150 kg 的球铁管件设置 5 个 厚 5 m m ∃ 50 mm 的内浇口即可。 2 2 管件上箱法兰根部热节部位 100% 有缩松现象, 严重的竟呈蜂窝状 , 有的还夹杂着石墨漂浮。如图 2 ( A) 处所示。原因分析:
中图分类号 : 文献标识码 : 文章编号 : 1000 8365( 2001) 06 0019 02
Shrinkage Prevention in Large size Nodular Cast Iron Pipes
- 1、下载文档前请自行甄别文档内容的完整性,平台不提供额外的编辑、内容补充、找答案等附加服务。
- 2、"仅部分预览"的文档,不可在线预览部分如存在完整性等问题,可反馈申请退款(可完整预览的文档不适用该条件!)。
- 3、如文档侵犯您的权益,请联系客服反馈,我们会尽快为您处理(人工客服工作时间:9:00-18:30)。
球铁冒口根部缩孔分析
球墨铸铁大多数是共晶或过共晶成分,在凝固过程中受石墨膨胀及过冷的影响促使收缩值增大所以在凝固过程中就形成了缩孔缩松缺陷的产生,在球铁件铸造中除了利用石墨化膨胀进行自补缩之外必须进行外部补缩,无冒口铸造实际上是利用浇注系统进行补缩。
由于浇注系统的补缩能力往往不如冒口,因而无冒口铸造对铸型条件以及其他工艺条件的要求远远高于采用冒口补缩。
由于这个缘故,冒口补缩工艺仍然是目前球铁件的主要生产工艺。
然而,冒口补缩工艺在实际应用中遭遇失败的实例也甚多,致使不少铸造人员往往轻易认为某些球铁件不能采用冒口补缩工艺,只能采用无冒口工艺,实际上冒口补缩失败的原因往往是由于所采用的工艺不恰当所致。
因此,对引起冒口补缩失败的原因进行分析,将有助于认识球铁的工艺特性和正确掌握球铁件的铸造工艺。
根据笔者的实践,除铸型刚度、化学成分、原材料和铁水熔炼处理方面的因素之外,造成球铁件冒口补缩失败的铸型工艺因素
(1)采用明冒口,导致石墨化膨胀压力松驰,使膨胀不能用于补缩。
(2)铁水先进入铸件型腔,加热型腔、温度降低后,再由铸件型腔
进入冒口,因而后者温度始终低于铸件,故称为冷冒口”;这种冒口由于其铁水先加热型腔,使型腔过热,冒口本身早于铸件凝固,不但不能起补缩作用,反而从铸件抽吸铁水,使铸件产生缩松、缩孔。
不少人企图通过加大冷冒口的尺寸希望能使其冷速减慢,起到补缩作用,结果是:冷冒口越大,铸件排放的冷铁水越多,型腔铁水流过量越大,过热也就越严重,上冷下热”温差越大,缩孔、缩松越严重。
即使浇注后往冷冒口冲注热铁水,由于冲入铁水量有限,并不能扭转情况。
铁水经由冒口进入铸件,冒口温度高于铸件,故称为热冒口”,冒口迟于铸件凝固,使轮毂部位直接得到补缩,而从轮毂流出的铁水在向周围
的轮辐扩散、流入轮缘过程中,由于轮辐散热面积大,铁水温度迅速降低,完
成部分凝固和收缩,及时从冒口吸取补缩液体,因而也有利于防止轮缘部位缩松。
均衡凝固技术推荐采用飞边冷冒口”、鸭嘴冷冒口”耳冒口”和冒口颈设冷铁的冷颈冒口”,企图通过使冒口颈在浇注结束时尽快凝固,减少冷冒口从铸件抽吸铁水来防止冒口颈处缩孔、缩松,但实践证明,冒口颈加快凝固顶多能减少铸件被冷冒口抽吸的铁水量,略微减轻其危害性,并不可能使冷冒口有补缩作用,而且由于型腔仍会因铁水流过量大而过热,因而仍然容易引起缩孔、缩松。
此外,有人以为,增大冷铁水排放量可以更换铸件顶部铁水,提高顶面温度,利于气体排出,并使冒口起集渣作用,实践证明:这种方法由于提高铸件顶面铁水温度,使铁水相对不太容易结氧化膜,有时确实能稍微减少顶面气孔,然而,由于液流路线固定(内浇道T冒口),能更换铁水的只限于顶部的局部区域,而气孔和夹渣浮到顶面后,由于型壁激冷作用,使它们与铁水一起很快凝固或半凝固而丧失流动性,因而总是黏附在铸型顶面,不可能被更换而听从人意进入冒口,而靠排放冷铁水提温,即使顶部局部区域温度提高了,本来偏咼的下部温度更加提咼,更加重上低下咼”的温度分布状况,不但使缩
孔、缩松更严重,而且顶面大部分区域仍旧是先冷却结皮或形成夹渣,阻止气体排出。
因此,采用冷冒口底注工艺并不能彻底解决夹渣、气孔问题。
笔者的实践证明,与采用底注和冷冒口相比较,采用热冒口顶注更有利于提高顶面温度、提高铁水压力以及延长传递冒口压力的液态通道的畅通时间,因而更有利于防止气孔和一次及二次夹渣缺陷。
采用明冒口铸造工艺只是在具有较高的静压值时才能起到一定的作用,否则作用将相反,当铁液进入冒口时由于它过早的冷却于铸件不但不起补缩作用,反而从抽吸铸件中的铁液使铸件产生缩孔缩松,在这一阶段的冒口为冷冒口,即铸件排放的冷液就越多,故上冷下热即温差就越大,则缩孔缩松倾向就愈严重。
采用冷明冒口时,应加大冒口高度增加静压值,浇注后往冒口注入热铁液这样将有效的提高冷冒口的温度,从而使缩孔缩松率降低,加大冷明冒口冷液的排放量,从而提高温度使上下温差降低从而减少和降低缩孔和缩松,提高工
艺出品率。
磷;在铁液中含量高时使凝固范围扩大,同时低熔点磷共晶在最后凝固时得不到补给,以及使铸件外壳变弱,因此有增大缩孔缩松倾向并使过冷增大出现偏析等。
球化剂和孕育剂牌号及加入量是影响球墨铸铁凝固时的收缩倾向,而收缩倾向又是与石墨球数和白口数量密切相关,所以使用不同的的稀土元素对球墨铸铁凝固后的金相组织有着重要的相关影响,也是促使缩孔缩松的关键之一,同时过高会恶化石墨形态,降低球化率,对于易缩孔的铸件尽可能使用低稀土(Rev)但要根据原铁水含硫量及熔炼工艺而定,中频炉含硫量<%时应该选用低于%的稀土,必要时可采用La 系球化剂及孕育剂。
无冒口一般用于平均模数大于的铸件,当冶金质量非常好时模数小于铸件也可以应用,采用无冒口工艺要求遵循;
( 1 )铁液的冶金质量高,铸型刚度大,采用低温浇注,(浇注温度低,减少液态收缩)铁液进入铸型后体积立即膨胀,避免收缩缺陷产生的可能性,尽管以后的共晶膨胀率小,但因模数大可以得到很高的膨胀内压,在坚固的铸型内克服二次收缩的缺陷。
(2)浇注温度控制在1340-1380°C 如果璧薄可控制在1380-1420°C 采用扁平内浇口,快速分散进入铁液促进快速凝固,应提高铸型的刚度,紧固螺栓。
(3)铸型设计8-16mm 的明出气孔和排气通道,据结构必要时设计中空排气通道,浇注引气。
(4)生产中无冒口工艺一般要求采用干型,可设一个暗冒口,质量不超过铸件总重量的2-3%当铸件呈现轻微液态收缩时,暗冒口可以补充铸件收缩,在以后的膨胀期间这个冒口将会被回填满,因此仍属于无冒口补缩
工艺
2016-5-15 常纪立。