球墨铸铁金相缺陷完整版
球墨铸铁常见缺陷的分析与对策
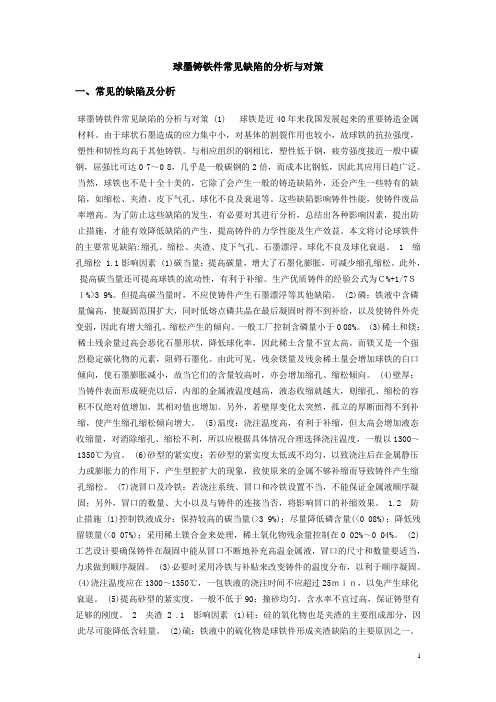
球墨铸铁件常见缺陷的分析与对策一、常见的缺陷及分析球墨铸铁件常见缺陷的分析与对策 (1) 球铁是近40年来我国发展起来的重要铸造金属材料。
由于球状石墨造成的应力集中小,对基体的割裂作用也较小,故球铁的抗拉强度,塑性和韧性均高于其他铸铁。
与相应组织的钢相比,塑性低于钢,疲劳强度接近一般中碳钢,屈强比可达0 7~0 8,几乎是一般碳钢的2倍,而成本比钢低,因此其应用日趋广泛。
当然,球铁也不是十全十美的,它除了会产生一般的铸造缺陷外,还会产生一些特有的缺陷,如缩松、夹渣、皮下气孔、球化不良及衰退等。
这些缺陷影响铸件性能,使铸件废品率增高。
为了防止这些缺陷的发生,有必要对其进行分析,总结出各种影响因素,提出防止措施,才能有效降低缺陷的产生,提高铸件的力学性能及生产效益。
本文将讨论球铁件的主要常见缺陷:缩孔、缩松、夹渣、皮下气孔、石墨漂浮、球化不良及球化衰退。
1 缩孔缩松 1.1影响因素 (1)碳当量:提高碳量,增大了石墨化膨胀,可减少缩孔缩松。
此外,提高碳当量还可提高球铁的流动性,有利于补缩。
生产优质铸件的经验公式为C%+1/7Si%>3 9%。
但提高碳当量时,不应使铸件产生石墨漂浮等其他缺陷。
(2)磷:铁液中含磷量偏高,使凝固范围扩大,同时低熔点磷共晶在最后凝固时得不到补给,以及使铸件外壳变弱,因此有增大缩孔、缩松产生的倾向。
一般工厂控制含磷量小于0 08%。
(3)稀土和镁:稀土残余量过高会恶化石墨形状,降低球化率,因此稀土含量不宜太高。
而镁又是一个强烈稳定碳化物的元素,阻碍石墨化。
由此可见,残余镁量及残余稀土量会增加球铁的白口倾向,使石墨膨胀减小,故当它们的含量较高时,亦会增加缩孔、缩松倾向。
(4)壁厚:当铸件表面形成硬壳以后,内部的金属液温度越高,液态收缩就越大,则缩孔、缩松的容积不仅绝对值增加,其相对值也增加。
另外,若壁厚变化太突然,孤立的厚断面得不到补缩,使产生缩孔缩松倾向增大。
球墨铸铁金相试样制备中的常见缺陷及其原因分析
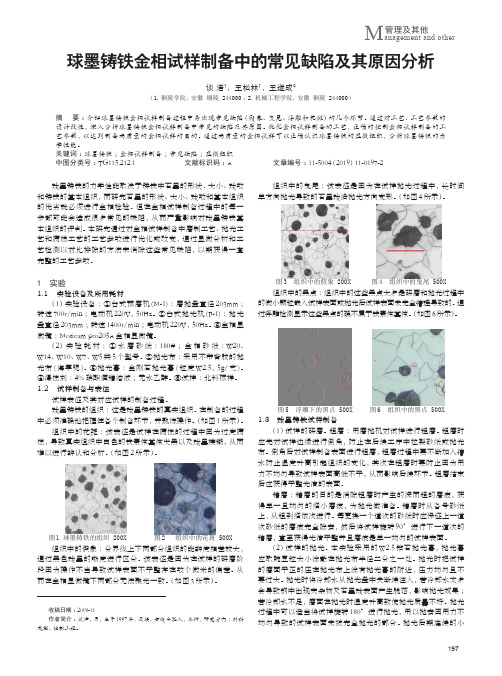
球墨铸铁金相试样制备中的常见缺陷及其原因分析
谈 浩¹,王松林¹,王继成²
(1. 铜陵学院,安徽 铜陵 244000 ;2. 机械工程学院,安徽 铜陵 244000)
摘 要 :介绍球墨铸铁金相试样制备过程中易出现常见缺陷(假象、曳尾、浮雕和花斑)的几个环节。通过对工艺、工艺参数的
收稿日期 :2019-11 作者简介 :谈浩,男,生于 19ห้องสมุดไป่ตู้7 年,汉族,安徽合肥人,本科,研究方向 :材料 成型、控制工程。
组织中的曳尾 :该表征是因为在试样抛光过程中,长时间 单方向抛光导致的石墨球沿抛光方向变形。(如图 4 所示)。
图 3 组织中的假象 200X 图 4 组织中的曳尾 500X 组织中的黑点 :组织中的这些黑点大多是研磨和抛光过程中 的微小颗粒嵌入试样表面或抛光后试样表面未完全清理导致的。通 过浮雕检测显示这些黑点的确不属于铁素体基体。(如图 6 所示)。
2 结果及讨论 2.1 球墨铸铁试样制备中常见的缺陷及应对措施
文献标识码 :A
文章编号 :11-5004(2019)11-0197-2
球墨铸铁的力学性能取决于铸铁中石墨的形状、大小、球数 和铸铁的基本组织,而研究石墨的形状、大小、球数和基本组织 的优劣就必须进行金相检验。但在金相试样制备过程中的每一 步都可能会造成很多常见的缺陷,从而严重影响对球墨铸铁基 本组织的评判。本研究通过对金相试样制备中磨制工艺、抛光工 艺和腐蚀工艺的工艺参数进行优化或改变,通过显微分析和工 艺检测以对比排除的方法来消除这些常见缺陷,以期获得一套 完整的工艺参数。
试样表征及其对应试样的制备过程。 球墨铸铁的组织 :这是球墨铸铁的真实组织。在制备的过程 中必须准确地把握住各个制备环节,并熟练操作。(如图 1 所示)。 组织中的花斑 :该表征是试样在腐蚀的过程中因为过度腐 蚀,导致真实组织中白色的铁素体基体发黑以及球墨模糊,从而 难以进行辨认和分析。(如图 2 所示)。
球墨铸铁件的缺陷和金相检验2012年

发挥。
共四十五页
球墨铸铁 的特性 (qiúmò-zhùtiě)
球墨铸铁可以像钢一样,通过热处理和 合金等措施来进一步提高其使用性能。比如, 处理过的球墨铸铁可以取得很好的韧性,延 伸率高达24%;抗拉强度可以高达1400MPa, 基本接近钢材(gāngcái),与钢材(gāngcái)相比,球墨 铸铁还有很多优点。比如铸造性能好,成本 相对较低。
60-70
球化分级
(f
6级
石墨呈聚集分布的蠕虫状、片状及球 状、团状、团絮状
小于60%
ē 共四十五页
石墨 大小 (shímò)
球墨铸铁石墨球的大小对力学性能的影 响很大,减小石墨球径,增加石墨球在单 位面积的个数可以明显地提高球墨铸铁的 强度、塑性和韧性。
石墨球径的减小,使单位面积上球墨铸铁数 量增多,可使抗疲劳强度提高,因此(yīncǐ),细 化石墨也是提高抗疲劳强度的一个要求。
因此,对球墨铸铁的金相研究,是我们了解球墨铸 铁,使用球墨铸铁的前提条件。
共四十五页
球状石墨 的形成 (shímò)
球状石墨的形成经历了形核与生长两个阶段。其 中的形核是石墨的首要过程,铁液在熔炼及随后的 球化、孕育处理中产生大量的非金属夹杂物,初生 的夹杂物非常小,在随后浇铸、充型、凝固过程相 互碰撞、聚合(jùhé)变大,上浮或下沉,成为石墨析 出的核心。
于焦炭含量较高等熔炼条件的限制,往往达不到这一标 准,应进一步改善熔炼条件,有条件可进行炉外脱硫, 一般要求小于0.06%。
共四十五页
典型缺陷(quēxiàn)——球化不良
球化不良和球化退化
特征:断口银灰色,分布(fēnbù)芝麻状黑 斑点。金相组织分布(fēnbù)大量厚片石墨。
球墨铸铁常见缺陷的分析与对策
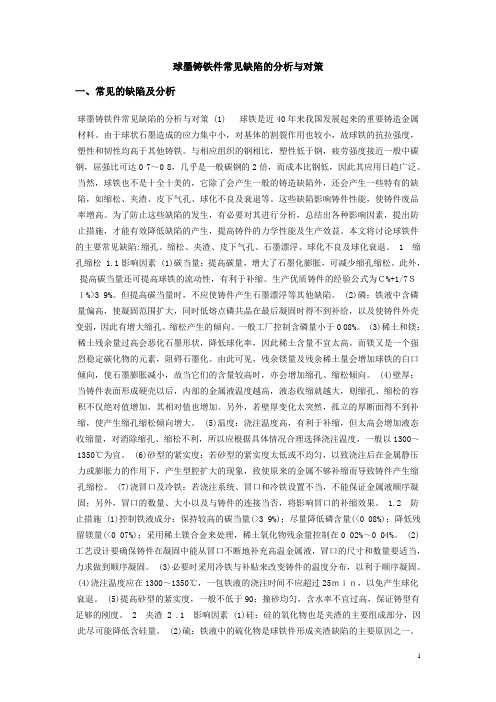
球墨铸铁件常见缺陷的分析与对策一、常见的缺陷及分析球墨铸铁件常见缺陷的分析与对策 (1) 球铁是近40年来我国发展起来的重要铸造金属材料。
由于球状石墨造成的应力集中小,对基体的割裂作用也较小,故球铁的抗拉强度,塑性和韧性均高于其他铸铁。
与相应组织的钢相比,塑性低于钢,疲劳强度接近一般中碳钢,屈强比可达0 7~0 8,几乎是一般碳钢的2倍,而成本比钢低,因此其应用日趋广泛。
当然,球铁也不是十全十美的,它除了会产生一般的铸造缺陷外,还会产生一些特有的缺陷,如缩松、夹渣、皮下气孔、球化不良及衰退等。
这些缺陷影响铸件性能,使铸件废品率增高。
为了防止这些缺陷的发生,有必要对其进行分析,总结出各种影响因素,提出防止措施,才能有效降低缺陷的产生,提高铸件的力学性能及生产效益。
本文将讨论球铁件的主要常见缺陷:缩孔、缩松、夹渣、皮下气孔、石墨漂浮、球化不良及球化衰退。
1 缩孔缩松 1.1影响因素 (1)碳当量:提高碳量,增大了石墨化膨胀,可减少缩孔缩松。
此外,提高碳当量还可提高球铁的流动性,有利于补缩。
生产优质铸件的经验公式为C%+1/7Si%>3 9%。
但提高碳当量时,不应使铸件产生石墨漂浮等其他缺陷。
(2)磷:铁液中含磷量偏高,使凝固范围扩大,同时低熔点磷共晶在最后凝固时得不到补给,以及使铸件外壳变弱,因此有增大缩孔、缩松产生的倾向。
一般工厂控制含磷量小于0 08%。
(3)稀土和镁:稀土残余量过高会恶化石墨形状,降低球化率,因此稀土含量不宜太高。
而镁又是一个强烈稳定碳化物的元素,阻碍石墨化。
由此可见,残余镁量及残余稀土量会增加球铁的白口倾向,使石墨膨胀减小,故当它们的含量较高时,亦会增加缩孔、缩松倾向。
(4)壁厚:当铸件表面形成硬壳以后,内部的金属液温度越高,液态收缩就越大,则缩孔、缩松的容积不仅绝对值增加,其相对值也增加。
另外,若壁厚变化太突然,孤立的厚断面得不到补缩,使产生缩孔缩松倾向增大。
铸铁缺陷原因介绍

6、适当增加加工余量
缩松
铸件内部有许多分散小缩孔,其表面粗糙,水压试验渗水
一般认为由于球铁凝固特性所决定的,其影响因素有
1、碳、硅含量低;磷含量高
2、残留镁量偏高
3、浇注温度低,影பைடு நூலகம்冒口补缩效果
4、铸型紧实度低
1、适当提高铁液碳、硅含量,尽量降低磷含量。铁液球化处理后应充分孕育保证石墨充分析出,提高自身补缩能力
球墨铸铁件缺陷分析
在球墨铸铁件生产中,常见的铸件缺陷除有灰铸铁件的一般缺陷外,还有球化不良、球化衰退、夹渣、缩松、石墨漂浮、皮下气孔等。通常,产生这些缺陷的原因不单是球化处理问题,有时还有造型制芯、熔炼浇注、配砂质量、落砂清理等许多工序的问题,因此必须具体分析、以便采取相应的合理措施加以解决。
球铁特有的缺陷分析
6、在铸型表面喷涂锭子油碳质材料,使铁液与铸型界面造成还原性气氛、在铁液表面或铸型表面撒上少量冰晶石粉或氟硅酸钠等能减少或消除皮下气孔
碎块状石墨
显微组织为少量大块石墨球周围共晶团边界均匀分布碎块状石墨和铁素体,石墨球也生长成连接成分枝石墨,其宏观断面为界限分明的暗灰色斑点,主要产生在大断面铸件热节部位或冒口颈下
铁液碳当量超过共晶点,初生的球状石墨从高温液态中析出,由于密度的差别和镁蒸汽泡上浮使部分石墨上浮至铸件上表面聚集,随后在共晶转变时迅速变大,形成石墨漂浮。因此碳当量越高、铸件越厚、铁液残留镁含量越低,浇注温度越高,越容易产生
1、严格控制碳当量,当壁厚大于70mm的铸件,碳当量必须小于4.55%,当壁厚小于30mm,碳当量必须小于4.70%,其余按这个范围适当调整
4、在铁液表面加覆盖剂,如石墨粉、木炭粉、冰晶石粉等
夹渣
球墨铸铁缺陷分析
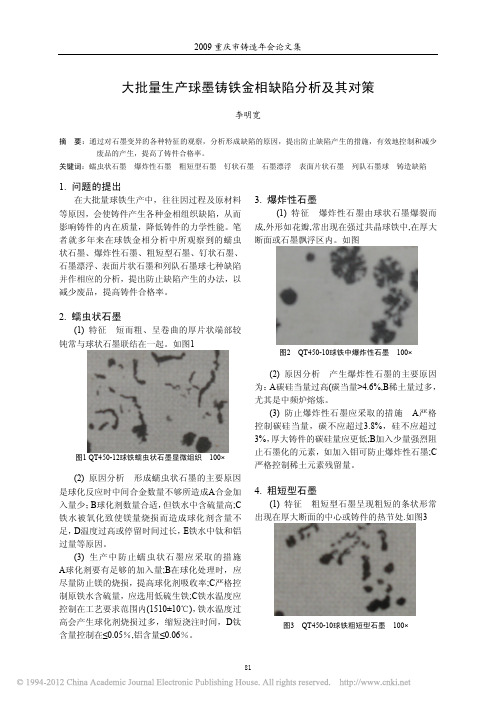
大批量生产球墨铸铁金相缺陷分析及其对策李明宽摘 要:通过对石墨变异的各种特征的观察,分析形成缺陷的原因,提出防止缺陷产生的措施,有效地控制和减少废品的产生,提高了铸件合格率。
关键词:蠕虫状石墨 爆炸性石墨 粗短型石墨 钉状石墨 石墨漂浮 表面片状石墨 列队石墨球 铸造缺陷1. 问题的提出在大批量球铁生产中,往往因过程及原材料等原因,会使铸件产生各种金相组织缺陷,从而影响铸件的内在质量,降低铸件的力学性能。
笔者就多年来在球铁金相分析中所观察到的蠕虫状石墨、爆炸性石墨、粗短型石墨、钉状石墨、石墨漂浮、表面片状石墨和列队石墨球七种缺陷并作相应的分析,提出防止缺陷产生的办法,以减少废品,提高铸件合格率。
2. 蠕虫状石墨(1) 特征 短而粗、呈卷曲的厚片状端部较钝常与球状石墨联结在一起。
如图1图1 QT450-12球铁蠕虫状石墨显微组织 100×(2) 原因分析 形成蠕虫状石墨的主要原因是球化反应时中间合金数量不够所造成A 合金加入量少;B 球化剂数量合适,但铁水中含硫量高;C铁水被氧化致使镁量烧损而造成球化剂含量不足,D 温度过高或停留时间过长,E 铁水中钛和铝过量等原因。
(3) 生产中防止蠕虫状石墨应采取的措施 A 球化剂要有足够的加入量;B 在球化处理时,应尽量防止镁的烧损,提高球化剂吸收率;C 严格控制原铁水含硫量,应选用低硫生铁;C 铁水温度应控制在工艺要求范围内(1510±10℃),铁水温度过高会产生球化剂烧损过多,缩短浇注时间,D 钛含量控制在≤0.05%,铝含量≤0.06%。
3. 爆炸性石墨(1) 特征 爆炸性石墨由球状石墨爆裂而成,外形如花瓣,常出现在强过共晶球铁中,在厚大断面或石墨飘浮区内。
如图图2 QT450-10球铁中爆炸性石墨 100×(2) 原因分析 产生爆炸性石墨的主要原因为:A 碳硅当量过高(碳当量>4.6%,B 稀土量过多,尤其是中频炉熔炼。
球铁典型铸造缺陷极其防止

球铁典型铸造缺陷极其防止1、球化不良与球化衰退(1)球化不良:球化不良是指球化处理没有达到预期的球化效果。
球化不良的金相组织为:集中分布的厚片状石墨和少量球状、团状石墨;有时还有水草状石墨。
随着球化不良的程度的加剧,集中分布的厚片状石墨的数量逐渐增多、面积增大,球化不良将使球墨铸铁的力学性能达不到响应牌号要求的指标。
关于球化不良产生的原因极其防止措施分述如下:1、原铁液含硫高 硫是主要反球化元素,含硫高会严重影响球化,一般原铁液的硫的质量分数要小于等于0.06%。
为保证球化,当原铁液含硫量偏高时,必须响应地提高球化剂的加入量,含硫量越高,则球化剂的消耗量也越多。
2、球化元素残留量低 为使石墨球化良好,球铁中必须含有一定量的残余镁和稀土,在我国现今生产条件下,残余镁量的质量分数不得小于0.03%,残余稀土量的质量分数不得小于0.02%。
3、铁液氧化 原材料中铁锈、污染以及铁液在熔化与过热中的氧化,导致铁液中的FeO 含量增多,因而在球化过程中要消耗更多的镁,致使残余镁量过低。
4、炉料含有反球化元素 当反球化元素超出允许范围时,就会影响球化效果,要注意废钢中可能含有钛,还要注意电镀材料、铝销、铅系涂料进入冲天炉。
稀土有中和反球化元素的能力,根据我国原生铁中含有较多的反球化元素的情况,我国球铁中的残余稀土量比国外的要多。
5、 孕育效果差 由于孕育效果差,或者孕育衰退,均会造成石墨球数量少,使得石墨球不圆整。
6、型砂水分高、含硫量高 由于界面反应,铁液中的镁与铸型表面中的氧、硫发生作用,致使铸件表面的残余镁量不足,形成一薄层的片状石墨。
解决的措施就是提高残余镁量,减少型砂含水量,型砂硫的质量分数应小于0.1%,或采用能获得还原性气氛的涂料。
在使用含硫硬化剂的树脂砂铸型中,可采用含有MgO 、CaO 的涂料。
2、球化衰退球化衰退的特点时:炉前球化良好,在铸件上球化不好;或者同一浇包的铁液,先浇注的铸件球化良好,后浇注的铸件球化不好。
球墨铸铁缺陷的金相分析及防止措施

302020年第5期工艺试验与应用球墨铸铁缺陷的金相分析及防止措施球墨铸铁是近几十年才发展起来的高强度铸造金属材料。
与钢材相比,球墨铸铁还有很多优点。
比如铸造性能好,成本相对较低。
由于球墨铸铁产量的不断增加,性能不断开发, 现已成功地部分取代了锻钢和铸钢,成为前景广阔的金属结构材料。
力学性能与金属的金相组织密切相关,什么样的金相结构决定了什么样的力学性能。
球墨铸铁也不例外,因此,对球墨铸铁的金相研究,是我们了解球墨铸铁的先决条件[1]。
下面对我厂生产的材质为QT450-10A 铸件,在生产过程中出现的两种不同缺陷进行分析[2]。
1 显微缩松1.1 微观结构球墨铸铁的显微缩松在显微下观察类似呈片状、多角形,有时连续、有时断续,分布在共晶团边界,有时类似片状石墨(图1),往往我们会误认为该缺陷是由球化不良造成。
这样极大的影响判断问题的改进方向,同时有可能使问题更加突出[3]。
我们对同样试块的缺陷位置进行能谱分析,能谱图像显示该缺陷区域呈乳突状立体结构(图2)。
1.2 形成原因铸件凝固过程中,奥氏体支晶凝固后,残余的铁液则在支晶间最后凝固,因得不到补缩而形成显微缩松,这类显微缩松的形成原因有如下几种原因:(1)碳当量CE 值过低,使得石墨膨胀体积不足以补充凝固过程中的体积收缩;(2)合金成分如Cu、Mn、Cr、P 及残留Mg 过高,增大缩松倾向[4];(3)砂型强度偏低,在铸件凝固过程中铸件体积增大,在体积增大的部位得不到其他部位铁液的补充;(4)工艺设计不合理,热节处在凝固过程中周围没有足够的铁水补充收缩[5];(5)孕育不充分或孕育过量等。
毛洪宇,勾洋洋,张 森(沈阳远大压缩机有限公司,辽宁 沈阳 110020)摘要:摘要:通过显微镜和能谱分析,观察球铁渣气孔和显微缩松的微观特征,找出种差别并分析了形成缺陷的原因;提出的防止缺陷产生的措施,能有效地控制和减少废品的产生,提高了铸件合格率。
关键词:关键词:渣气孔;缩松;预防措施中图分类号:中图分类号:TG245 文献标识码:文献标识码:B 文章编号:文章编号:1673-3320(2020)05-0030-03收稿日期:2020-04-16定稿日期:2020-08-10作者简介:毛洪宇(1986-),男,毕业于辽宁工业大学材料成型及控制工程专业,工程师,主要从事铸造工艺及材料、模具设计制造。
球墨铸铁金相组织缺陷原因及防止方法概述
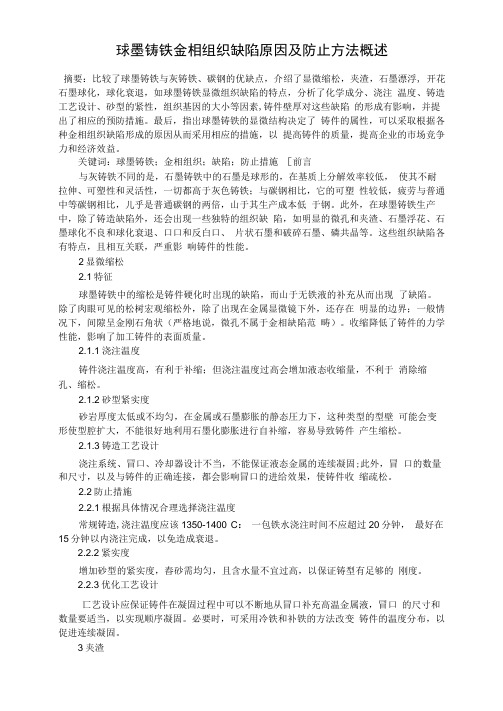
球墨铸铁金相组织缺陷原因及防止方法概述摘要:比较了球墨铸铁与灰铸铁、碳钢的优缺点,介绍了显微缩松,夹渣,石墨漂浮, 开花石墨球化,球化衰退,如球墨铸铁显微组织缺陷的特点,分析了化学成分、浇注温度、铸造工艺设计、砂型的紧性,组织基因的大小等因素,铸件壁厚对这些缺陷的形成有影响,并提出了相应的预防措施。
最后,指岀球墨铸铁的显微结构决定了铸件的属性,可以采取根据各种金相组织缺陷形成的原因从而采用相应的措施,以提高铸件的质量,提高企业的市场竞争力和经济效益。
关键词:球墨铸铁;金相组织;缺陷;防止措施[前言与灰铸铁不同的是,石墨铸铁中的石墨是球形的,在基质上分解效率较低,使其不耐拉伸、可塑性和灵活性,一切都高于灰色铸铁;与碳钢相比,它的可塑性较低,疲劳与普通中等碳钢相比,儿乎是普通碳钢的两倍,山于其生产成本低于钢。
此外,在球墨铸铁生产中,除了铸造缺陷外,还会出现一些独特的组织缺陷,如明显的微孔和夹渣、石墨浮花、石墨球化不良和球化衰退、口口和反白口、片状石墨和破碎石墨、磷共晶等。
这些组织缺陷各有特点,且相互关联,严重影响铸件的性能。
2显微缩松2.1特征球墨铸铁中的缩松是铸件硬化时岀现的缺陷,而山于无铁液的补充从而出现了缺陷。
除了肉眼可见的松树宏观缩松外,除了出现在金属显微镜下外,还存在明显的边界;一般情况下,间隙呈金刚石角状(严格地说,微孔不属于金相缺陷范畴)。
收缩降低了铸件的力学性能,影响了加工铸件的表面质量。
2.1.1浇注温度铸件浇注温度高,有利于补缩;但浇注温度过高会增加液态收缩量,不利于消除缩孔、缩松。
2.1.2砂型紧实度砂岩厚度太低或不均匀,在金属或石墨膨胀的静态圧力下,这种类型的型壁可能会变形使型腔扩大,不能很好地利用石墨化膨胀进行自补缩,容易导致铸件产生缩松。
2.1.3铸造工艺设计浇注系统、冒口、冷却器设计不当,不能保证液态金属的连续凝固;此外,冒口的数量和尺寸,以及与铸件的正确连接,都会影响冒口的进给效果,使铸件收缩疏松。
合成球墨铸铁金相组织缺陷产生原因及解决办法

2021年 第2期 热加工98铸造C a s t i n g合成球墨铸铁金相组织缺陷产生原因及解决办法曹琨1,2,胡克潮2,赵子文1,2,苏义祥31.兰州兰石能源装备工程研究院有限公司 甘肃兰州 7303142.甘肃省高端铸锻件工程技术研究中心 甘肃兰州 7303143.兰州理工大学材料科学与工程学院 甘肃兰州 730050摘要:采用光学显微镜、扫描电镜分析了合成球墨铸铁生产过程中常见金相组织缺陷,包括石墨漂浮、球化不良、球化失败、碳化物超标、缩松和缩孔等问题,并提出工艺控制要点及解决措施,为生产同类铸件提供了可借鉴经验。
关键词:合成铸铁;金相组织;球墨铸铁;工艺控制1 序言球墨铸铁件具备中高强度和韧性、优异的耐磨性和减振性以及良好的铸造工艺性能等特点,是目前最具发展潜力的“以铁代钢”的铸造材料[1,2]。
目前,许多铸造企业开始采用废钢增碳技术(即合成铸铁)替代铸造生铁生产球墨铸铁件的方法来降低成本。
用该方法熔炼的球墨铸铁力学性能十分优异,铸态下力学性能可达到QT700-2级别材料要求,无需进行正火处理(只进行去应力退火),能够减少一火次能源消耗,符合国家倡导的绿色可持续发展理念[3]。
与传统生铁熔炼方式不同,合成球墨铸铁熔炼过程中原铁液化学成分发生改变,生产过程中如果控制不当容易出现较多铸造缺陷。
目前,应用合成球墨铸铁技术的报道较多[4-12],但是对于合成球墨铸铁在生产过程中的自身特性、容易出现的质量问题及关键控制要点的报道甚少。
本研究主要从金相组织角度出发,针对生产过程中常见的金相组织缺陷进行分析并提出解决方案。
2 石墨漂浮合成球墨铸铁的核心是将废钢中的碳含量(w C 为0.2%左右)增至工艺要求范围(w C 为3.6%~3.9%),如果碳含量超标(w C ≥4.0%),则会出现石墨漂浮现象,如图1所示。
从图中可以看出石墨呈开花状、爆裂状,这种组织降低了球墨铸铁力学性能和表面质量。
腐蚀态金相照片显示,石墨周围铁素体组织呈破碎状,使珠光体含量达到95%,抗拉强度453~532M P a ,屈服强度431~477M P a ,伸长率1.5%~3%,硬度208~214HBW ,表明开花、爆裂状石墨对基体组织产生明显割裂作用,降低了产品力学性能。
球墨铸铁球化不良_石墨漂浮和夹渣缺陷的金相分析

第20卷增刊2010年11月 安徽冶金科技职业学院学报Journal of Anhui Vocational College of Metallurgy and TechnologyVol.20Nov.2010球墨铸铁球化不良、石墨漂浮和夹渣缺陷的金相分析凌云波(马钢股份公司重型机械设备制造公司 安徽马鞍山 243000)摘 要:通过对球化不良、石墨漂浮和夹渣三种常见缺陷的宏、微观特征的观察,分析了形成缺陷的原因,提出的防止缺陷产生的措施,能有效地控制和减少废品的产生,提高了铸件合格率。
关键词:球化不良;石墨漂浮;夹渣;铸造缺陷;宏观特征;微观特征中图分类号:TG255 文献标识码:A 文章编号:1672-9994(2010)增-0047-02收稿日期:2010-09-25作者简介:凌云波(1969-),男,重机公司质量管理部,高级工程师。
1 问题的提出在球铁生产中,往往因处理工艺及原材料等原因,会使铸件产生各种缺陷,从而影响铸件的内在质量,降低铸件的力学性能。
笔者就多年来在球铁金相图片中所观察到的球化不良、石墨漂浮和夹渣三种缺陷作以分析,提出防止缺陷产生的办法,以减少废品,提高铸件合格率。
2 球化不良(1)宏观特征 球化不良表现在铸件断面上出现芝麻点的黑斑,愈接近铸件中心,黑色斑点愈密集,随着球化不良的严重程度增加,黑点的直径也随之增大,数量也在增加。
(2)微观特征 金相观察为集中分布的厚片状石墨,极少量的球状石墨,且球状石墨特别圆,见图1。
在厚片状石墨周围出现铁素体组织,这种组织使球铁的力学性能急剧下降。
(3)原因分析 形成球化不良的主要原因是球化反应时中间合金数量不够所造成。
合金加入量少; 球化剂数量合适,但铁水中含硫量高;!铁水被氧化致使镁量烧损而造成球化剂含量不足等原因。
(4)生产中防止球化不良应采取的措施 球化剂要有足够的加入量; 在球化处理时,应尽量防止镁的烧损,提高球化剂吸收率;!严格控制原铁水含硫量,应选用低硫生铁;∀铁水温度应控制在工艺要求范围内,铁水温度过高会产生球化剂烧损过多,温度过低合金易#结死∃,均会产生球化不良。
球铁典型铸造缺陷极其防止

球铁典型铸造缺陷极其防止1、球化不良与球化衰退(1)球化不良:球化不良是指球化处理没有达到预期的球化效果。
球化不良的金相组织为:集中分布的厚片状石墨和少量球状、团状石墨;有时还有水草状石墨。
随着球化不良的程度的加剧,集中分布的厚片状石墨的数量逐渐增多、面积增大,球化不良将使球墨铸铁的力学性能达不到响应牌号要求的指标。
关于球化不良产生的原因极其防止措施分述如下:1、原铁液含硫高 硫是主要反球化元素,含硫高会严重影响球化,一般原铁液的硫的质量分数要小于等于0.06%。
为保证球化,当原铁液含硫量偏高时,必须响应地提高球化剂的加入量,含硫量越高,则球化剂的消耗量也越多。
2、球化元素残留量低 为使石墨球化良好,球铁中必须含有一定量的残余镁和稀土,在我国现今生产条件下,残余镁量的质量分数不得小于0.03%,残余稀土量的质量分数不得小于0.02%。
3、铁液氧化 原材料中铁锈、污染以及铁液在熔化与过热中的氧化,导致铁液中的FeO 含量增多,因而在球化过程中要消耗更多的镁,致使残余镁量过低。
4、炉料含有反球化元素 当反球化元素超出允许范围时,就会影响球化效果,要注意废钢中可能含有钛,还要注意电镀材料、铝销、铅系涂料进入冲天炉。
稀土有中和反球化元素的能力,根据我国原生铁中含有较多的反球化元素的情况,我国球铁中的残余稀土量比国外的要多。
5、 孕育效果差 由于孕育效果差,或者孕育衰退,均会造成石墨球数量少,使得石墨球不圆整。
6、型砂水分高、含硫量高 由于界面反应,铁液中的镁与铸型表面中的氧、硫发生作用,致使铸件表面的残余镁量不足,形成一薄层的片状石墨。
解决的措施就是提高残余镁量,减少型砂含水量,型砂硫的质量分数应小于0.1%,或采用能获得还原性气氛的涂料。
在使用含硫硬化剂的树脂砂铸型中,可采用含有MgO 、CaO 的涂料。
2、球化衰退球化衰退的特点时:炉前球化良好,在铸件上球化不好;或者同一浇包的铁液,先浇注的铸件球化良好,后浇注的铸件球化不好。
- 1、下载文档前请自行甄别文档内容的完整性,平台不提供额外的编辑、内容补充、找答案等附加服务。
- 2、"仅部分预览"的文档,不可在线预览部分如存在完整性等问题,可反馈申请退款(可完整预览的文档不适用该条件!)。
- 3、如文档侵犯您的权益,请联系客服反馈,我们会尽快为您处理(人工客服工作时间:9:00-18:30)。
球墨铸铁金相缺陷 HEN system office room 【HEN16H-HENS2AHENS8Q8-HENH1688】
从金相组织判断球铁牌号
从方面无法具体判别球铁的牌号,具体看看GB/T9441-2009和
GB/T1348-2009《就知道了,主要判别球铁牌号的依据还是力学性
能的数据,成分和金相都不作为标准,成分主要控制大概球铁的,
金相主要看球化率和珠光体的含量其实也还是看指标。
与铸铁的区别
球铁是的简称,是铸铁的一种
铸铁,含碳量在2%以上的。
工业用铸铁一般含碳量为2%~4%。
碳在铸铁中多以石墨形态存在,有时也以渗碳体形态存在。
除碳外,铸铁中还含有1%~3%的硅,以及锰、磷、硫等元素。
还含有镍、铬、钼、铝、铜、硼、钒等元素。
碳、硅是影响铸铁显微组织和性能的主要元素。
铸铁可分为:
①。
含碳量较高(%~%),碳主要以片状石墨形态存在,断口呈灰色,简称灰铁。
熔点低(1145~1250℃),凝固时收缩量小,抗压强度和硬度接近碳素钢,减震性好。
用于制造机床床身、汽缸、箱体等结构件。
②。
碳、硅含量较低,碳主要以渗碳体形态存在,断口呈银白色。
凝固时收缩大,易产生缩孔、裂纹。
硬度高,脆性大,不能承受冲击载荷。
多用作可锻铸铁的坯件和制作耐磨损的零部件。
③可锻铸铁。
由后获得,石墨呈团絮状分布,简称韧铁。
其组织性能均匀,耐磨损,有良好的塑性和韧性。
用于制造形状复杂、能承受强动载荷的零件。
④。
将铁水经后获得,析出的石墨呈球状,简称球铁。
比普通有较高强度、较好韧性和塑性。
用于制造内燃机、及农机具等。
⑤蠕墨铸铁。
将灰口铸铁铁水经蠕化处理后获得,析出的石墨呈蠕虫状。
力学性能与球墨铸铁相近,铸造性能介于灰口铸铁与球墨铸铁之间。
用于制造汽车的零部件。
⑥。
普通铸铁加入适量合金元素(如硅、锰、磷、镍、铬、钼、铜、铝、硼、钒、锡等)获得。
合金元素使铸铁的基体组织发生变化,从而具有相应的耐热、耐磨、耐蚀、耐低温或无磁等特性。
用于制造矿山、化工机械和仪器、仪表等的零部件。
球墨铸铁金相缺陷
1、球化不良
球化不良是稀土镁经常遇到的问题之一。
球化不良是指浇铸过程中因加入量不足等原因而形成的铸铁石墨未充分球化的现象。
铸
件中的石墨多呈团块状、开花状、枝晶状、蠕虫
状、厚片状。
(1)宏观特征
银白色的断口上分布有黑色斑点,破断铸件
在其整个断面上分布有明显可见的小黑点,愈往
中心愈密。
球化不良的程度越严重,黑斑直径越
大数量越多,甚至全部断口为黑灰色,类似灰铸
铁的断口。
金相微观分析能发现有集中分布的厚
片状石墨或晶间石墨以及少量球状、团状石墨,严重时还出现片状石墨。
球化不良使力学性能急剧下降,不能达到牌号所规定的性能指标。
主要是因为和的残留量不足造成的。
(2)微观特征
金相观察为集中分布的厚片状石墨,极少量的球状石墨,且球状石墨特别圆,见图1:
在厚片状石墨周围出现铁素体组织,这种组织使球墨铸铁的力学性能大幅下降。
(3)原因分析
①合金加入量少
②球化剂数量合适,铁水中含硫量高
③铁水氧化致使镁量烧损而造成球化剂含量不足
(4)应采取的措施
①球化剂加入要足量
②尽量防止镁的烧损,提高球化剂的吸收率
③严格控制铁水中的含硫量,应选用低硫生铁
④铁水温度应控制在工艺要求范围内,温度过高,造成球化剂烧损过多。
过低合金易“结死”都会造成球化不良。
2、石墨飘浮
(1)宏观特征
石墨漂浮常出现于铸件上表面、试块边缘及冒口底部,在断口上表面出现一层界限明显且平整的黑斑。
(2)微观特征
其石墨聚集,呈开化状或荔枝状,有的完全爆裂,见图2,这种组织严重削弱了球铁的力学性能,使材料的强韧性指标明显下降。
(3)原因分析
产生石墨飘浮的主要原因为碳硅当量
过高,(碳当量>%)。
当碳硅当量超过共
晶成分,因浇铸温度高,铁水在凝固前就
析出石墨,若液态停留一段时间,此时石
墨聚集并长大,由于石墨的密度远比铁水
轻,聚集石墨易上浮,有时夹杂物也被带
到铸件的上表面,从而在铸件表面产生石
墨飘浮。
在同等条件下(碳当量相同),
铸件愈大,浇铸温度愈高,冷却速度越
慢,则铁水在铸型内保持高温液态时间长,石墨有足够的上浮时间,因而石墨飘浮愈严重。
(4)防止石墨飘浮应采取的措施
①严格控制碳硅当量,碳不应该超过4%,硅不应该超过3%,厚大铸件的碳硅含量应更低。
②提高冷却速度,在壁厚处应放置冷铁
③加入少量强烈阻止石墨化的元素,如加入钼
④严格控制稀土元素残留量
3、夹渣
(1)宏观特征
夹渣分布于铸件的上表面和铸件的死角处,夹渣在断面上呈连续的暗黑色区域或斑点,无金属光泽。
(2)微观特征
有硫化物(MgS和FeS)和氧化物(MgO、SiO
2、FeO、Al
2
O
3
)在夹渣处除有球状石
墨外,还有类片状石墨,见图3。
夹渣的出现大大地降低了球铁的力学性能,特别是伸长率及冲击韧性下降更明显。
(3)原因分析
铁水中硫含量及残余镁量过高,加之浇铸温
度过低,形成了夹渣缺陷。
(4)防止产生夹渣的措施
可降低铁水中硫含量(硫含量应控制在)及
残留镁量≤%;控制足够的稀土量,提高浇铸温
度(≥1300℃),使熔渣易于上浮,减少夹渣。
球
化处理后需多次扒渣,以免非金属夹杂物留在铁
水中形成夹渣。
此外,在浇铸时,应减少铁液在
空气中停留的时间,以免铁液流在浇铸时产生氧化而生成二次渣的机会。