圆钢生产设备及工艺(DOC 30页)
棒材车间生产工艺流程
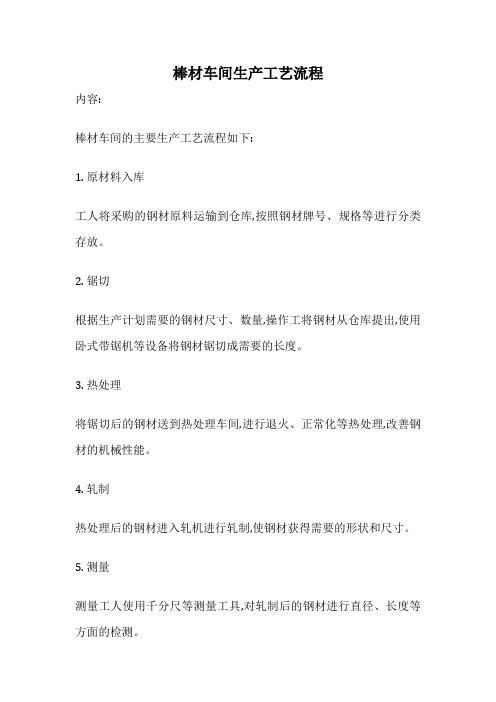
棒材车间生产工艺流程
内容:
棒材车间的主要生产工艺流程如下:
1. 原材料入库
工人将采购的钢材原料运输到仓库,按照钢材牌号、规格等进行分类存放。
2. 锯切
根据生产计划需要的钢材尺寸、数量,操作工将钢材从仓库提出,使用卧式带锯机等设备将钢材锯切成需要的长度。
3. 热处理
将锯切后的钢材送到热处理车间,进行退火、正常化等热处理,改善钢材的机械性能。
4. 轧制
热处理后的钢材进入轧机进行轧制,使钢材获得需要的形状和尺寸。
5. 测量
测量工人使用千分尺等测量工具,对轧制后的钢材进行直径、长度等方面的检测。
6. 标记
对检测合格的棒材进行打标,标明钢材牌号、规格、长度等信息。
7. 包装
工人使用牛皮纸等材料对标记完成的棒材进行包装。
8. 成品出库
按照产品编号、客户信息等对包装后的成品棒材进行堆放,然后使用叉车等设备运送到成品仓库。
以上是棒材车间从原材料入库到成品出库的主要生产工艺流程。
各环节的操作规范有利于保证棒材产品的质量。
圆钢生产设备及工艺
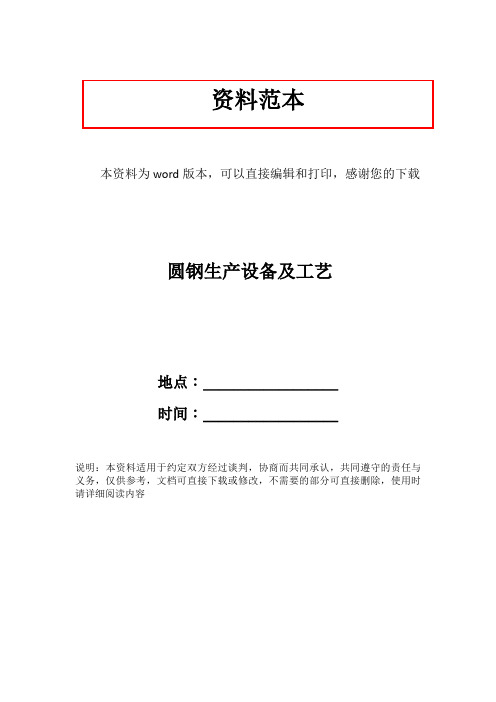
资料范本本资料为word版本,可以直接编辑和打印,感谢您的下载圆钢生产设备及工艺地点:__________________时间:__________________说明:本资料适用于约定双方经过谈判,协商而共同承认,共同遵守的责任与义务,仅供参考,文档可直接下载或修改,不需要的部分可直接删除,使用时请详细阅读内容1圆钢生产设备及工艺1.1坯料准备1.1.1 坯料的选择高速轧机圆钢材生产对钢坯的质量要求较高,其选择和验收的标准如1.1.1.1对钢种与化学成分的要求钢坯的牌号和化学成分应符合有关标准规定,对不同的钢种在钢的残余元素含量上有相应的要求。
1.1.1.2对钢坯尺寸和质量的要求(1)对钢坯的外形、尺寸、质量的要求有:钢坯断面形状及允许偏差、定尺长度、短尺的最短长度及比例、弯曲、扭转等。
这些要求是考虑了充分发挥轧机生产能力,保证加热与轧制顺利并考虑供坯的可能性和合理性等综合因素确定的。
方坯尺寸和边长允许偏差:方坯边长:130±mm(YB/T001-91)圆角半径:R>8mm(YB/T001-91)对角线长度差:≤6mm(YB/T001-91)连铸方坯和矩形坯标准: YB2011-83(2)钢坯标准长度为10000mm;短尺钢坯最短长度为8000mm;每批(炉)短尺钢坯的重量不大于全部钢坯重量的10%;长度允许偏差为10000+70,8000-0mm。
(3)钢坯的弯曲度在10000mm不大于100mm;但不允许在钢坯两端,两端最大50mm。
需莹光磁粉探伤的钢坯,如弹簧钢、轴承钢、冷镦钢等,每米弯曲不大于6mm。
(4)钢坯扭转在10000mm内最大为6°。
(5)钢坯端部因剪切变形而造成的局部宽展不大于边长的10%。
切头毛刺应清除。
端部因剪切变形造成的局部弯曲不得大于20mm。
剪切端面应与钢坯长度方向轴线垂直;端面歪斜量不得大于边长的6%。
1.1.1.3对表面质量与内部质量的要求(1) 钢坯对钢坯表面质量的要求是:钢坯端面不得有缩孔、尾孔和分层;钢坯表面应无裂缝、折叠、耳子、结疤、拉裂和夹杂等缺陷;钢坯表面缺陷必须沿纵向加工清除,清除处应圆滑、无棱角,清除宽度不得小于清除深度的5倍,表面清理深度不大于公称厚度的8%。
圆钢制造工艺

圆钢制造工艺一、圆钢的概述圆钢是一种常见的金属材料,通常用于制造机械零件、建筑结构、汽车零部件等领域。
在工业生产中,圆钢的质量和性能直接影响到产品的质量和使用寿命。
因此,圆钢制造工艺非常重要。
二、材料准备1.原材料:优质碳素结构钢、合金结构钢等。
2.加工设备:锅炉、轧机、切割机等。
3.检测设备:超声波探伤仪、磁粉探伤仪等。
三、生产流程1.热轧加工(1)原材料进入锅炉进行加热,使其达到适宜的温度。
(2)将经过加热的原材料送入轧机进行轧制。
在轧制过程中,通过不断调整轧辊间距和轧辊转速,使原材料逐渐变形成为所需直径的圆钢。
(3)经过初步轧制后,将圆钢送入精整区进行再次轧制。
这一步主要是为了进一步提高圆钢的表面光洁度和尺寸精度。
(4)完成轧制后,将圆钢送入冷却区进行自然冷却。
2.冷拉加工(1)将热轧成型的圆钢送入拉拔机进行拉拔。
在拉拔过程中,通过不断调整拉拔机的拉力和速度,使圆钢逐渐变细并提高其表面光洁度。
(2)经过多次拉拔后,将圆钢送入终轧机进行最后的加工。
这一步主要是为了进一步提高圆钢的尺寸精度和表面质量。
(3)完成冷拉加工后,将圆钢送入冷却区进行自然冷却。
3.切割加工(1)将经过热轧或冷拉加工的圆钢送入切割机进行切割。
在切割过程中,通过调整刀具和切割速度等参数,使得切割后的圆钢长度符合要求。
(2)对于需要特殊长度的圆钢,则需要在切割前进行定长处理。
四、质量控制1.外观检查:对于每批生产出来的圆钢都需要进行外观检查,包括表面质量、直径精度、长度精度等。
2.化学成分检测:对于每批生产出来的圆钢都需要进行化学成分检测,确保其符合相关标准要求。
3.机械性能检测:对于每批生产出来的圆钢都需要进行机械性能检测,包括拉伸强度、屈服强度、延伸率等。
五、包装和运输1.包装:将生产出来的圆钢按照规格和长度进行分类,并采用适当的包装材料进行包装,以保证在运输过程中不会受到损坏。
2.运输:将包装好的圆钢运往客户指定地点。
钢铁生产工艺流程及设备

钢铁生产工艺流程及设备目录1.钢铁生产工艺流程示意图A (2)2. 钢铁生产工艺流程示意图B (4)3.钢铁生产工艺流程示意图C (6)3.1钢铁生产工艺流程示详解C1 (8)3.1.1炼焦生产流程 (8)3.1.2烧结生产流程 (8)3.1.3高炉生产流程 (9)3.1.4转炉生产流程 (10)3.1.5连铸生产流程 (10)3.1.6热轧生产流程 (11)3.2钢铁生产工艺流程示详解C2 (12)3.2.1热轧生产流程>第一热轧钢带生产流程 (12)3.2.2热轧生产流程>热轧厚板剪切线布置图 (12)3.2.3热轧生产流程>热轧薄板剪切线布置图 (13)3.2.4热轧生产流程>一号调质重卷线布置图 (13)3.2.5热轧生产流程>二号调质重卷线布置图 (14)3.2.6热轧生产流程>酸洗涂油线设备布置图 (14)3.2.7热轧生产流程>第二热轧钢带生产流程 (15)3.2.8热轧生产流程>三号调质重卷线布置图 (15)3.2.9热轧生产流程>四号调质重卷线布置图 (16)3.3钢铁生产工艺流程示详解C3 (16)3.3.1小钢胚生产流程 (16)3.3.2条钢一场生产流程 (17)3.3.3条钢二场生产流程 (17)3.3.4线材生产流程 (18)3.3.5钢板生产流程 (18)3.4钢铁生产工艺流程示详解C4 (19)3.4.1第一酸洗冷轧线 (19)3.4.2第二酸洗冷轧线 (20)3.4.3热轧生产流程>热轧厚板剪切线布置图 (20)3.4.4连续热浸镀锌线 (21)3.4.5第一连续退火线 (21)3.4.6第二连续退火线 (22)3.4.7封盒退火炉 (22)3.4.8电解清洗线 (23)3.5钢铁生产工艺流程示详解C5 (23)3.5.1连续涂覆线 (23)3.5.2电磁钢片涂覆线 (24)3.5.3电气镀锌线 (24)3.5.4调质线 (25)3.5.5重卷线 (25)3.5.6往复式冷轧机 (26)3.5.7水平式退火涂覆线 (26)3.5.8张力整平线(TLL) (27)1.钢铁生产工艺流程示意图A2。
大棒厂生产工艺简介

850轧机
粗轧机主要参数
轧制压力:Pmax =6000 kN 轧制力矩:Mmax =650 kNm 轧制速度:V=0.5~4.5 m/s 轧辊直径:max:850mm, min:750mm 辊身长度:1900mm 辊颈直径:~480mm 上轧辊提升高度:~600mm 下辊调节范围:~150mm(垫片) 压下精度:~0.2mm 轴向调节行程:~±5mm
补热退火:主要消除产品残余应力、降低硬度、 改善组织性能的作用。
探伤:发现产品表面和内部的缺陷。现有涡流探 伤(表面)、超声波(内部)、磁粉探伤各一套
。
三 孔型系统介绍
3.1 孔型的概念
轧辊轴线: 轧辊的轴线。
轧 制 面: 通过两根轧辊轴线的平面称为轧制面。
孔 型: 轧槽在轧制面上所形成的孔称为孔型,孔型 的尺寸指正在过钢时的尺寸。
广泛应用于棒材和线材连轧机上,适合生产
高合金钢和优质钢。
椭圆-圆孔型系统
从轧制的稳定性考虑,椭孔和圆孔中轧件的充满度应有一定的要求。 充满度的实质是轧件的宽高比,一般应大于1.5。 一般在圆孔型中轧制时,应控制轧件的宽度尺寸不大于高度尺寸。
酸洗
热处 理
检验
包装
入库
二、生产工艺流程
原料为连铸坯,连铸坯规格为: 220×220×9000~11000mm 250×300(350)×9000~11000mm 320×480×4500~5400mm 合格连铸坯由吊车运至上料台架入口段,逐根移送至入炉辊 道上,经人工目视检查、不合格钢坯剔除后,合格钢坯送入 加热炉加热。为节约能源,连铸坯可热送热装。
孔型设计:就是如何在轧辊上刻制形状正确、尺寸精确的 轧槽以达到生产出满足产品质量要求的产品。
3.2 我厂主要使用的孔型系统
钢铁工业全套生产工艺和设备分析
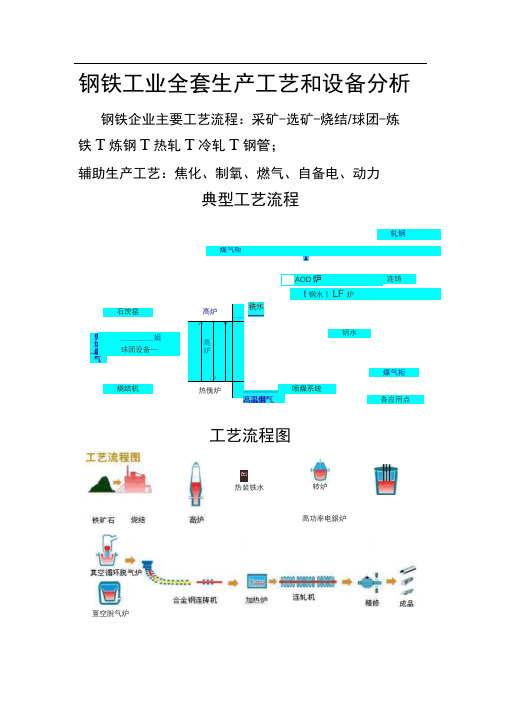
钢铁工业全套生产工艺和设备分析钢铁企业主要工艺流程:采矿-选矿-烧结/球团-炼铁T炼钢T热轧T冷轧T钢管;辅助生产工艺:焦化、制氧、燃气、自备电、动力典型工艺流程轧钢煤气柜AOD炉t钢水丨LF炉工艺流程图连铸石茨窑烧结机高炉—----J1高炉i1F1热傀炉钥水煤气柜喷煤系统各应用点fel热装铁水_________ 姐球团设备—转炉高功率电銀炉亶空脫气炉焦化厂主要是生产炼铁所需要的燃烧原料。
主要工艺是将原煤碳化。
生产工艺为:配煤、捣固、炼焦、湿熄焦及干熄焦、余热发电、回收、煤化工。
配煤:配煤前将原煤经过破碎清俗称:洗煤。
国内的煤炭有肥煤和瘦煤的说法、配煤是将两种煤按照一定燃烧值要求配比混匀捣固:将配比好的煤加入粘结剂用捣固机捣制成煤饼的形状。
炼焦:国内目前的焦炉主要有3米、4米、6米、7米和7.63米焦炉。
所谓的米数是指结碳室炉膛的高度。
一般一座焦炉的孔数在55 空左右。
现今主流的焦炉都在 6 米及以上。
焦炉技术最早由德国和日本引进,后为国内消化。
熄焦:湿熄焦是在焦炭出炉后由熄焦车运到熄焦塔通过低水分熄焦工艺将红焦迅速熄灭。
干熄焦是通过专门的熄焦工艺将红焦装入氮罐自然熄灭。
余热发电:为干熄焦的配套设备,通过鼓风机将碳罐中氮气引向蒸汽发电机。
回收及煤化工:炼焦过程中会产生大量的有毒气体及物质(硫磺、苯、氢、氖、煤焦油等),但是这些物质又是化工行业所不可缺少的原材料,所以为了环保和创收,回收及煤化工是焦化厂相当重要的一个环节。
特别要提出来的是五大车:装焦、推焦、拦焦、熄焦、旋转焦罐车也是我们需要相当重视的其中涉及到我们的产品为:大量的变频器、。
年产110万t高强度圆钢和螺纹钢生产线的工艺及设备

d ton ln i h — te t o nd a d s r w r wih a u l o t utof 1 m i i n t ns uc i i e of h g —sr ng h r u n c e ba t nn a u p .1 l o o . l Ke o ds hi y W r : gh— s r n t te g h: r u r;s r w r o nd ba c e ba ;pr e s;e ui m e t oc s q p n
总第 1l 8
2 1年 第 1期 01
河 北 冶金
2 1, u b r 1 01 N m e
Tl ol tl a 8
年 产 1 t 强 度 圆钢 1 0万 高 和 螺 纹 钢 生 产 线 的 工 艺 及 设 备
郝 利 强 侯 红 杰 何 滨 田 允 夏 志 军 , , , ,
鲁丽 集 团 10万 t 强度 和 螺 纹钢 生 产 线设 备 1 高
1冷 坯 l 装 置 ;. 送辊 道 ;. 坯过 度 缓 冲装 置 ;. 坯 下 料装 置 ;. 炉辊 道 ;. 长 称 重 装 置 ;. 除 装 置 ;. 进 式 加 热 炉 ;. 压 水 除 磷 . 卜 料 2热 3热 4热 5入 6测 7剔 8步 9高 装 置 ;0 高频 焊机 ;1 出炉辊 道 ;2 卡 断 剪 ;3 粗 轧 机组 ;4 飞 剪 ;5 中 轧 机组 ;6 予 水 冷 装 置 ;7 飞 剪 ;8 精 轧机 组 ;9 减 定径 机 组 ;0 水 1. l. 1. 1. 1 1. 1. 1 1. l. 2. 冷装 置 ;1倍 尺 飞剪 ;2 冷床 上 料 装置 ;3 步 进式 冷 床 ;4 冷 飞剪 ;5 链 式移 钢 台 架 ;6 打捆 机 ;7 大捆 收 集装 置 ;8 短 尺 收集 装 置 2 2 2. 2. 2. 2. 2. 2.
钢筋加工的工艺流程与设备选择
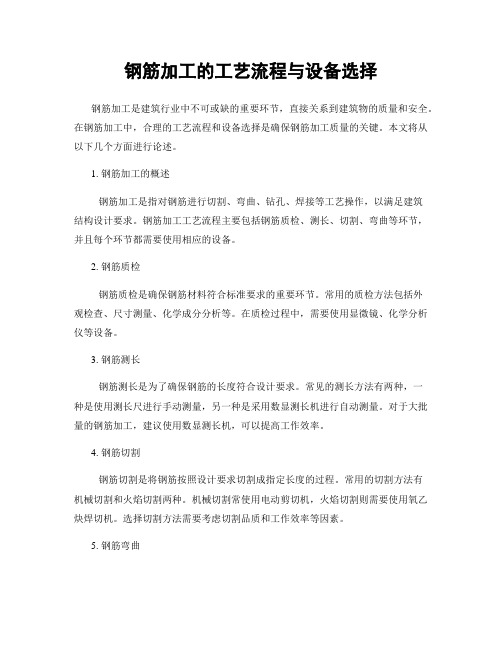
钢筋加工的工艺流程与设备选择钢筋加工是建筑行业中不可或缺的重要环节,直接关系到建筑物的质量和安全。
在钢筋加工中,合理的工艺流程和设备选择是确保钢筋加工质量的关键。
本文将从以下几个方面进行论述。
1. 钢筋加工的概述钢筋加工是指对钢筋进行切割、弯曲、钻孔、焊接等工艺操作,以满足建筑结构设计要求。
钢筋加工工艺流程主要包括钢筋质检、测长、切割、弯曲等环节,并且每个环节都需要使用相应的设备。
2. 钢筋质检钢筋质检是确保钢筋材料符合标准要求的重要环节。
常用的质检方法包括外观检查、尺寸测量、化学成分分析等。
在质检过程中,需要使用显微镜、化学分析仪等设备。
3. 钢筋测长钢筋测长是为了确保钢筋的长度符合设计要求。
常见的测长方法有两种,一种是使用测长尺进行手动测量,另一种是采用数显测长机进行自动测量。
对于大批量的钢筋加工,建议使用数显测长机,可以提高工作效率。
4. 钢筋切割钢筋切割是将钢筋按照设计要求切割成指定长度的过程。
常用的切割方法有机械切割和火焰切割两种。
机械切割常使用电动剪切机,火焰切割则需要使用氧乙炔焊切机。
选择切割方法需要考虑切割品质和工作效率等因素。
5. 钢筋弯曲钢筋弯曲是将直杆形态的钢筋弯成弯杆或弯件的过程,常用于梁、柱等构件的制作。
常见的钢筋弯曲设备有手动弯曲机和数控弯曲机。
手动弯曲机适用于小规模施工,而数控弯曲机则适用于大规模施工。
6. 钢筋焊接钢筋焊接是将两根或多根钢筋进行连接的工艺。
钢筋焊接设备主要包括电焊机和气焊设备。
在钢筋加工中,焊接是常见的连接方法,但需要注意焊接强度和焊接质量。
7. 钢筋钻孔钢筋钻孔是为了在钢筋上穿孔,用于固定连接件。
常用的钢筋钻孔设备有手持钻、电动钻和数控钻等。
选择钻孔设备需要考虑孔径大小、钻孔深度和钻孔精度等因素。
8. 设备选择的考虑因素在钢筋加工中,设备的选择直接影响到加工效率和质量。
因此,在选择设备时需要考虑以下几个因素:加工规模、加工工艺要求、设备价格和维护成本等。
钢筋加工的设备选择与工艺流程掌握
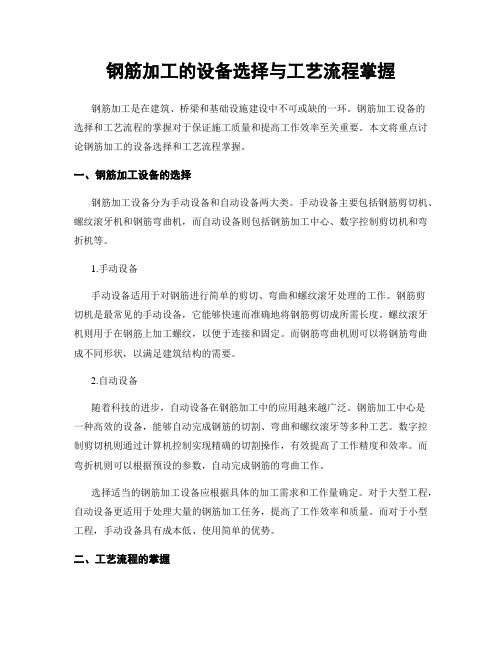
钢筋加工的设备选择与工艺流程掌握钢筋加工是在建筑、桥梁和基础设施建设中不可或缺的一环。
钢筋加工设备的选择和工艺流程的掌握对于保证施工质量和提高工作效率至关重要。
本文将重点讨论钢筋加工的设备选择和工艺流程掌握。
一、钢筋加工设备的选择钢筋加工设备分为手动设备和自动设备两大类。
手动设备主要包括钢筋剪切机、螺纹滚牙机和钢筋弯曲机,而自动设备则包括钢筋加工中心、数字控制剪切机和弯折机等。
1.手动设备手动设备适用于对钢筋进行简单的剪切、弯曲和螺纹滚牙处理的工作。
钢筋剪切机是最常见的手动设备,它能够快速而准确地将钢筋剪切成所需长度。
螺纹滚牙机则用于在钢筋上加工螺纹,以便于连接和固定。
而钢筋弯曲机则可以将钢筋弯曲成不同形状,以满足建筑结构的需要。
2.自动设备随着科技的进步,自动设备在钢筋加工中的应用越来越广泛。
钢筋加工中心是一种高效的设备,能够自动完成钢筋的切割、弯曲和螺纹滚牙等多种工艺。
数字控制剪切机则通过计算机控制实现精确的切割操作,有效提高了工作精度和效率。
而弯折机则可以根据预设的参数,自动完成钢筋的弯曲工作。
选择适当的钢筋加工设备应根据具体的加工需求和工作量确定。
对于大型工程,自动设备更适用于处理大量的钢筋加工任务,提高了工作效率和质量。
而对于小型工程,手动设备具有成本低、使用简单的优势。
二、工艺流程的掌握正确掌握钢筋加工的工艺流程对于保证施工质量和提高工作效率至关重要。
下面将介绍常见的钢筋加工工艺流程。
1.预处理钢筋在加工之前需要进行清洁和修剪。
清洁钢筋可以去除表面的污物和锈蚀,以便于加工和使用。
修剪钢筋则是将长钢筋切割成所需长度。
2.剪切钢筋剪切是将钢筋切成所需的长度。
在进行剪切时要保证切口的光滑和准确,以避免影响后续加工和使用过程。
3.弯曲钢筋弯曲是根据建筑结构的需要将钢筋弯成不同的形状。
在进行弯曲时要注意控制弯曲角度和半径,以确保弯曲后的钢筋符合设计要求。
4.螺纹滚牙螺纹滚牙是为了方便钢筋的连接和固定。
轧钢厂棒材轧制工艺与装备
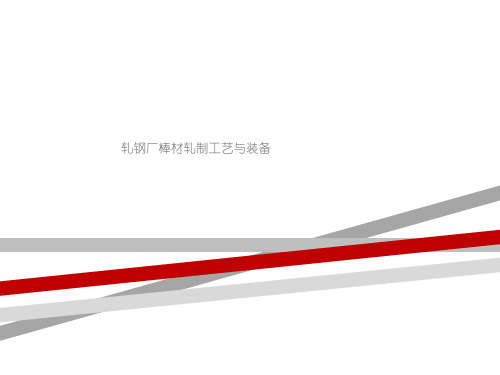
切头、尾及废品
t/a
%
20500
2.5
烧 损、氧化
t/a
%
12500
1.5
产品交货状态
棒材产品以直条成捆交货。
定尺长度:6~12m
每捆重量:1000-4000kg
打捆道次:
6m 棒 材 打 捆 3 道 ;
道;
7~9m 棒 材 打 捆 4
5道。
10~12m棒材打捆
二、工艺流程
1、工艺流程简图
工艺流程简图(续)
㈡ 轧制
结合阳春棒材厂系搬迁湘钢一棒材厂现有轧机的实际情况,本着能用的 轧机尽量利用的原则,并进行适当的改造,最终确定如下轧机布置方案:
更换原湘钢一棒材厂三辊可逆粗轧机为6架Φ550短应力线轧机,平/立 交替布置;中轧机组保留原有奇数道次Φ420水平轧机,将偶数道次三架水 平轧机更换成Φ420立式短应力线轧机;精轧机组保留原有6架Φ350短应力 线轧机,其中3架水平、1架立式、2架平立可转换轧机,另外再增加2架 Φ350短应力线立式轧机,形成精轧共8架短应力线轧机。正常轧制状态下, 全线最大轧制道次为18道。不切分轧制时,全线按18架平立布置进行生产, 无扭轧制,精轧机组平/立转换轧机空过;切分轧制时,精轧机组后2架立式 轧机空过。
生产工艺流程(续)
从精轧机组轧出的棒材产品,经一组辊道送至成品倍尺飞剪分段剪切(预留螺 纹钢穿水冷却工艺)。
分段剪切后的棒材由冷床输入辊道和带摩擦制动滑板的滑板辊道送入冷床,冷 床为步进齿条式,入口侧设有矫直板。棒材在冷床上矫直、冷却,经齐头辊道 齐头后,被送往排钢链式运输机,当运输机上积累了一定数量的棒材后,由卸 钢小车将一组成排的棒材送至冷床输入辊道,再由冷床输入辊道送往850T冷剪 剪切成6~12m定尺。
某钢铁厂主要生产流程及设备简介

钢铁厂主要生产工艺及设备简介烧结厂烧结厂目前有1#—6#烧结机(主要工艺流程如图),其中1#、2#的烧结机属于平烧,3#、4#、5#、6#属于带烧。
1、1#、2#烧结主要设备参数如下:10个原料料仓,一次混合机(Ø 2.8×12m×1台),二次混合机(Ø 2.8×12m×1台),平滚布料器(2台),烧结机(50m2×2台),助燃风机(4台),单辊破碎机(1台),链板机(IS125—15—M速比250×2台),1545振动筛(1.2×2.4m×2台)。
2、3#、4#、5#烧结主要设备参数如下:31个原料料仓,一次混合机(Ø 3.2×13m×2台),二次混合机(Ø 3.8×15m×2台),梭式布料器(48×1.2m×2台),烧结机(180m2×3台),助燃风机(9-19-7.1D×6台),抽风机(2台),单辊破碎机(2X3.74m×1台,3.23×1.8m×2台),环冷(170m2×48车×3台),椭圆等厚振动筛(IDLS3075×3台,IDLS 2060×3台)。
3、6#烧结主要设备参数如下:16个原料料仓,一次混合机(Ø 3.8×15m×1台),二次混合机(Ø 4.0×20m×1台),梭式布料器(41×1.2×1台),烧结机(265m2×1台),助燃风机(9-19-7.1D×2台),单辊破碎机(2X3.74m×1台),环冷(280m2×60车×1台),椭圆等厚振动筛(TDLS3090×2台)。
圆钢的制造工艺与要求

圆钢的制造工艺与要求圆钢是一种常用的钢材,具有广泛的应用领域。
在制造圆钢时,需要遵循特定的工艺流程和要求,以确保最终的产品具有良好的质量和性能。
本文将深入探讨圆钢的制造工艺与要求,并分享对该主题的观点和理解。
一、工艺流程1. 原料准备:圆钢的主要原料是熔铁和熔钢。
在制造过程中,首先需要将铁矿石经过炼焦和熔炼的过程得到铁水,然后与其他合金元素(如铬、镍等)进行合金化,最终得到熔钢。
2. 球团制备:将熔钢倒入连铸机中,通过冷却和结晶过程形成圆形铸坯,这个过程称为球团制备。
3. 球团热处理:球团需要进行热处理,以改善其内部结构和性能。
常见的热处理方法包括正火、退火、淬火等。
4. 热轧:将球团通过高温下的轧机进行加热和轧制,最终得到符合要求的圆钢。
5. 直径修整:通过机械或化学方法对热轧后的圆钢进行直径修整,以满足不同应用的要求。
6. 表面处理:为了提高圆钢的表面质量,常对其进行酸洗、机械抛光等表面处理。
7. 产品检验:对制造好的圆钢进行力学性能测试、化学成分分析以及外观检查等,以确保其符合相关标准和要求。
二、制造要求1. 化学成分控制:圆钢的化学成分对其性能具有重要影响。
制造过程中,需要严格控制熔钢的化学成分,包括碳含量、合金元素含量等。
2. 结晶控制:圆钢的内部结晶组织对其力学性能至关重要。
通过合适的热处理过程和控制冷却速率,在制造过程中要求圆钢具有细小、均匀以及连续的晶粒结构。
3. 尺寸精度:圆钢的尺寸精度对于一些特定的应用非常重要。
在制造过程中,需要根据具体的要求对其直径、长度等尺寸进行控制。
4. 表面质量:圆钢的表面质量直接影响到其使用寿命和外观效果。
在制造过程中,需要注意去除表面的氧化皮、裂纹等缺陷,并保证其平整度和光洁度。
5. 产品标识:为了方便管理和追溯,圆钢需要在表面进行标识,包括产品标准号、批号、生产日期等。
三、观点和理解圆钢作为一种重要的钢材,在工业生产和建筑领域具有广泛的应用。
在制造圆钢的过程中,工艺流程和制造要求是确保产品质量和性能的关键因素。
- 1、下载文档前请自行甄别文档内容的完整性,平台不提供额外的编辑、内容补充、找答案等附加服务。
- 2、"仅部分预览"的文档,不可在线预览部分如存在完整性等问题,可反馈申请退款(可完整预览的文档不适用该条件!)。
- 3、如文档侵犯您的权益,请联系客服反馈,我们会尽快为您处理(人工客服工作时间:9:00-18:30)。
圆钢生产设备及工艺(DOC 30页)1圆钢生产设备及工艺1.1坯料准备1.1.1 坯料的选择高速轧机圆钢材生产对钢坯的质量要求较高,其选择和验收的标准如1.1.1.1对钢种与化学成分的要求钢坯的牌号和化学成分应符合有关标准规定,对不同的钢种在钢的残余元素含量上有相应的要求。
1.1.1.2对钢坯尺寸和质量的要求(1)对钢坯的外形、尺寸、质量的要求有:钢坯断面形状及允许偏差、定尺长度、短尺的最短长度及比例、弯曲、扭转等。
这些要求是考虑了充分发挥轧机生产能力,保证加热与轧制顺利并考虑供坯的可能性和合理性等综合因素确定的。
方坯尺寸和边长允许偏差:方坯边长:130±mm(YB/T001-91)圆角半径:R>8mm(YB/T001-91)对角线长度差:≤6mm(YB/T001-91)连铸方坯和矩形坯标准: YB2011-83(2)钢坯标准长度为10000mm;短尺钢坯最短长度为8000mm;每批(炉)短尺钢坯的重量不大于全部钢坯重量的10%;长度允许偏差为10000+70,8000-0mm。
(3)钢坯的弯曲度在10000mm不大于100mm;但不允许在钢坯两端,两端最大50mm。
需莹光磁粉探伤的钢坯,如弹簧钢、轴承钢、冷镦钢等,每米弯曲不大于6mm。
(4)钢坯扭转在10000mm内最大为6°。
(5)钢坯端部因剪切变形而造成的局部宽展不大于边长的10%。
切头毛刺应清除。
端部因剪切变形造成的局部弯曲不得大于20mm。
剪切端面应与钢坯长度方向轴线垂直;端面歪斜量不得大于边长的6%。
进容易排列坯料,所以两种方式均有采用的。
连续式加热炉按钢坯在炉内运行方式分为推钢式和步进式。
步进式中又分为步进梁式炉、步进底式炉和步进梁底组合式炉。
最近几年所建方钢材轧机大都选用步进式连续加热炉,因为步进式加热方式更适合圆钢材生产工艺和产品质量要求。
1.3.3加热炉区设备组成1.3.3.1机械设备炉区机械设备包括:上料台架、分钢机、剔除装置、炉前辊道、两个升降挡板、称重装置、装料炉门、炉内装料悬臂辊道、对齐推钢机、炉底机械、出料炉门、炉内出料悬臂辊道、风机等。
1.3.3.2液压系统设备液压系统设备包括加热炉液压站、称重装置液压缸、推钢机液压钢、炉底机械平移与升降液压缸、相关液压管路等。
1.3.3.3炉子主要技术性能参数炉子主要技术性能参数为:炉子额定能力:90t/h有效炉底强度:500kg/(m2·h)加热钢种:Q235、20MnSi等普碳钢和低合金钢坯料尺寸:150mm×150mm×10m钢坯加热温度:1050~1080℃,最高1150℃空气:预热温度: 450℃工作压力: 4~6kPa最大空气消耗量(α=1.1): 29600m3/h燃料:高焦炉混合煤气设计发热值: 7531KJ/ m3车间煤气接点压力: 8000Pa最大燃料消耗量: 16000 m3/h炉底面积: 190.8m2排烟温度: 300~350℃单位燃耗:在装料温度20℃,出料温度1050~1150℃,产量90t/h,空气预热温度400~450℃,步进梁100%绝热情况下,炉子的单位热耗为1.34GJ/t(45.7kg标煤/t)1.2 轧机及相关设备1.2.1粗轧工艺和设备型式及参数粗轧的主要功能是使坯料得到初步压缩和延伸,得到温度合适、断面形状正确、尺寸合格、表面良好、端头规矩、长度适合工艺要求的轧件。
粗轧机多采用平-立交替轧机无扭轧制,机架数通常为4或6架,一般采用平箱—立箱,平均道次延伸系数为1.28~1.32。
在粗轧阶段普遍采用微张力或低张力轧制,因为此时轧件断面尺寸较大,对张力不敏感,设置活套实现无张力轧制十分困难也极不经济。
粗轧后的切头切尾工序是必要的。
轧件头尾两端的散热条件不同于中间部位,轧件头尾两端温度较低,塑性较差;同时轧件端部在轧制变形时由于温度较低,宽展较大,变形不均造成轧件头部形状不规则,这些在继续轧制时都会导致堵塞入口导卫或不能咬入。
为此在经过6道次粗轧后必须将端部切去。
通常切头切尾长度在70~200mm。
1.2.2 中轧及预精轧工艺和设备型式及参数中轧及预精轧的作用是继续缩减粗轧机组轧出的轧件断面,为精轧机组提供轧制成品线材所需要的断面形状正确、尺寸精确并且沿全长断面尺寸均匀、无内在和表面缺陷的中间料。
中轧机组的基本功能、使用条件及工艺要求和粗轧机组大体相同,因此在轧机的型式上除短中心距紧凑式轧机是适应粗轧特定条件而在中轧机组中使用外,中轧机组的设备型式基本和粗轧机组一样。
中轧采用的孔型系统一般是椭圆—圆—椭圆—圆孔型系。
中轧及预精轧的平均道次延伸系数一般在1.28~1.34之间。
轧机的技术参数见表2-1。
表2-1钢轧机主要技术性能一览表轧机序号No 公称直径/mm最大辊径/mm最小辊径/mm辊身长/mm辊颈直径/mm电机功率(D.C.)/kW转速/r·min-1轧机连续轧制载荷/t齿轮座中心距/mm1H 650 700 600 800 280 350 0~366 520H7 2V 650 700 600 800 280 350 0~366 580H7 3H 650 700 600 800 280 350 0~366 520H7 4V 650 700 600 800 280 350 0~366 460H7 5H 650 700 600 800 280 450 0~366 520H7 6V 650 700 600 800 280 450 0~366 460H7 7H 520 530 475 700 200 450 0~176 360H7 8V 520 530 475 700 200 450 0~176 360H7 9H 415 415 365 700 200 450 0~176 360H7 10V 415 415 365 700 200 450 0~176 360H7 11H 370 370 290 700 200 600 0~176 360H7 12V 370 370 290 700 200 600 0~176 360H7 13H 300 300 210 600 180 600 0~129 320H7 14V 300 300 210 600 180 600 0~129 320H71.3 剪切设备及工艺湘钢二棒材厂在整个轧线上共装配有1台剪切机和3台锯切机,剪切机位于精轧机组前,1号、2号、3号锯切机都位于精轧机组,剪切机,低速,剪力大,用于在方钢的切头、切尾及事故碎断。
1号锯切机用于切头、2号锯切机用于倍尺剪切功能。
最后一台锯切机用于切尾。
1.4 QTB控制冷却工艺及设备1.4.1 钢材轧后控制冷却技术的理论基础作为钢的强化手段在轧钢生产中常常采用控制轧制和控制冷却工艺。
这是一项简化工艺、节约能源的先进轧钢技术。
它能通过工艺手段充分挖掘钢材潜力,大幅度提高钢材综合性能,给冶金企业和社会带来巨大的经济效应。
由于它具有形变强化和相变强化的综合作用,所以既能提高钢材强度又能改善钢材的韧性和塑性。
圆钢材轧后冷却的目的主要是得到产品所要求的组织与性能,使其性能均匀和减少二次氧化铁皮的生成量,为了减少二次氧化铁皮量,要求加大冷却速度。
要得到所要求的组织和性能,则需根据不同品种,控制冷却工艺参数。
一般圆钢材轧后控制冷却过程可分为三个阶段,第一阶段的主要目的是为相变作组织准备及减少二次氧化铁皮生成量。
一般采用快速冷却,冷却到相变前温度,此温度称为吐丝温度;第二阶段为相变过程,主要控制冷却速度;第三阶段相变结束,除有时考虑到固溶元素的析出采用慢冷外,一般采用空冷。
按照控制冷却的原理与工艺要求,线材控制冷却的基本方法是:首先让轧制后的圆钢材在冷床上进行冷却,再由吊车把钢材吊入缓冷坑中进行缓冷,最后以较快的冷却速度冷却到适当的温度进行打印、运输和打捆等。
1.4.2 设备组成QTB的工艺设备组成如下:(1)淬水线小车(2)旁路辊道(3)液压缸(4)高温计(5)控制阀(6)水系统(7)压缩空气系统(8)液压系统(9)干油系统1.4.3 技术参数淬水线小车外观尺寸 3819mm×18600mm×2194mm质量 24500kg热处理棒材范围Φ10~Φ40mm螺纹钢淬火线小车行程 1700mm液压缸行程 1700mm阀台的外观尺寸 12300mm×4750mm×2300mm水系统压力(max/min) 1.2Mpa/0.8Mpa压缩空气流量(标准状态下) 90m3/h(干燥器用)200m3/h(仪器用)压缩空气压力 0.5Mpa增压泵数量 3旁路辊道数量级 201.4.4 冷床区设备和工艺冷床区设备包括冷床入口设备、冷床、冷床出口设备等。
1.4.4.1冷床入口设备冷床入口设备包括输入辊道、重叠装置、升降裙板辊道、分钢器、安全挡板等。
A 输入辊道输入辊道的作用是输送轧件,并分离前后轧件的头尾。
B 重叠装置在裙板辊道的前端采用了专用于切分产品的重叠装置。
其作用是在切分生产中,将切开的轧件重叠起来,因为切分轧制后,若两根轧件并行输送,特别是在分钢器分头尾时,由于轧件断面小头部容易“发飘”,出现上冷床困难的现象,通过重叠装置将两根轧件重叠运送到冷床上,可较好地解决以上问题。
C 升降裙板辊道裙板辊道是一系列可在垂直方向上下运动的板。
它的作用是对轧件进行输送和制动并将轧件卸到冷床上。
D 分钢器在裙板辊道的入口处有1气动分钢器,它的作用是将准备卸到冷床上的轧件尾部与后1根轧件头部分开,避免前后轧件头尾相接,无法卸料,影响生产。
E 安全挡板安全挡板固定在裙板辊道的末端,防止轧件由于制动失效造成轧件倍尺过长而形成的跑条。
1.4.4.2冷床设备冷床使轧件在空气中冷却并将轧件输送到冷剪工作区。
为了保证断面较小、长度较大的细长轧件不至于因冷却过程而造成弯曲和扭转,并防止轧件表面擦伤,圆材一般都采用步进齿条式冷床、摆式冷床。
冷床由冷床床体、对齐辊道、固定挡板及水冷系统组成。
1.4.4.3冷床的出口设备冷床出口设备包括带有棒层输送小车的辊道和棒层形成装置。
1.5圆钢材的精整、运输与成品库1.5.1圆钢的修整圆钢的修整主要是对它的头、尾修剪。
相对地说,圆钢材头、尾部分容易产生缺陷,且头、尾处轧件宽展量偏大,容易造成尺寸超差。
为此,在圆钢打捆之前要进行修整,将圆钢头尾的缺陷剪除。
1.5.2成品检查圆钢成品检查包括圆钢材外观质量检查和组织性能检验。
组织性能检验是按照国家或企业标准规定以及合同中用户提出的技术要求进行的。
外面质量检查是检查圆钢材的形状、尺寸和表面缺陷是否符合标准规定。
1.6 打捆机的工艺操作自动打捆机是近年来为提高作业率、降低劳动强度而发展起来的。