现场改善历程 PPT课件
合集下载
生产现场改善PPT课件
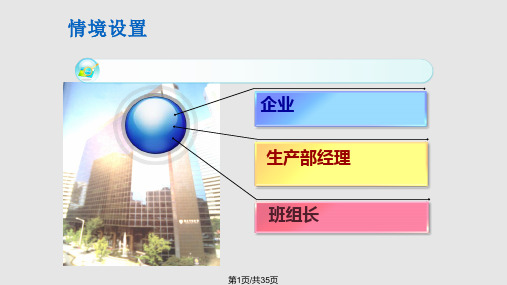
近视 近视
步骤三:思考可能的原因(问为什么)
环境
人为
常盯屏幕 先天近视
常揉眼睛 意外伤害
走路看书
近视
距离过近
躺着看书
看书方法不对
设备 材料 方法 步骤四:描述和排序真正原因
第12页/共35页
长时间看书不休息
步骤五:针对主要原因采取改进措施。
第13页/共35页
四、解决问题
对现状总怀疑的六何分析法
材料存放、搬运方式好不好?
材料成本如何,能否更便宜?
作业标准内容是否合适?
作业前后的准备工作是否经济高效?
前后工序的衔接好吗?
作业安全性如何?
第8页/共35页
统计数据 客户反馈 实际比较
红牌作战
在工厂内,找到问题点,并悬挂红牌,让大家都
明白并积极地去改善,从而达到整理、整顿的目
的。
第9页/共35页
材料成本如何,能否更便宜?
方法
作业标准内容是否合适?
作业前后的准备工作是否经济高效?
前后工序的衔接好吗?
作业安全性如何?第23页/共35页
运用统计数据、报告分析,找出问题点。
5.00% 4.50% 4.00% 3.50% 3.00% 2.50% 2.00% 1.50% 1.00% 0.50% 0.00%
第15页/共35页
第五级
现象:实际工作效率达到85%以上 库存是该行业中最低的 员工:新人也能很快跟上运营程序 全员主动地参与到改善活动中
第四级
现象:实际工作效率达到75%以上 设备:因故障而停线情况基本消除 管理者:天天研究如何再增加价值
第三级
现象:各环节均使用流程图管理 员工:具备多技能操作能力 现场:小组经常聚会讨论改善课题
现场改善方法PPT演示课件

3)标牌是否正确?
4)是否有杂质?
5)进货周期是否适当? 6)材料浪费情况如何?
7)材料运输有差错吗? 8)加工过程正确吗?
9)材料设计正确吗? 10)质量标准合理吗?
•14
Methods
1)工艺标准合理吗? 2)工艺标准提高了吗? 3)工作方法安全吗? 4)此方法能保证质量吗? 5)此方法是否高效? 6)工序安排合理吗? 7)工艺卡是否正确? 8)温度和湿度适宜吗? 9)通风和光照良好吗? 10)前后工序衔接好吗?
•12
Machine
1)设备能力足够吗? 3)是否正确润滑? 5)是否经常出现故障? 7)设备布置是否正确? 9)设备数量是否足够?
2)能否按工艺要求加工? 4)保养情况如何? 6)工作准确度如何? 8)噪音如何? 10)运转是否正常?
•13
Material
1)数量是否足够或过多? 2)是否符合质量要求?
•
工序分析
工序分析是工序管理、搬运管理、布局研究、作业编制、顺序 规划等基础资料获取的必要手法。
步骤: 1.整理工序流程 2.工序流程中是否存在不均衡、不合理现象 3.工序顺序是否合理 4.工序流程是否顺畅,设备配置、搬运方法是否合理 5.工序中的作业是否必要,是否可以取消,是否有更好的作业方法
•15
改善的概念
全体员工在各自的工作区域内进行: 小规模的 持续的 增值的 改变以产生积极影响。
•16
改善的概念
-是否可以消除 -如果不能消除,可否减少 -如果消除和减少,会出现何种现象 -什么、有多少、怎样变好
改善使操作变得 更容易、更方便 更安全、更稳定
第五要素
第一要素
持续不断地变化 更容易地
•8
现场改善及案例分析ppt课件
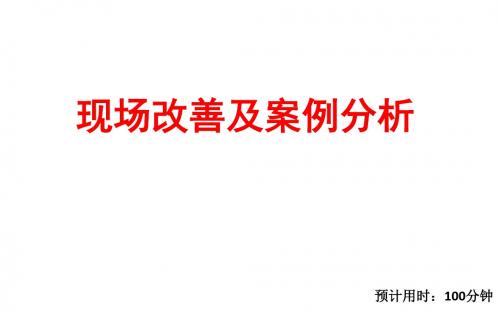
2 改善的着眼点
一、从现场的浪费中发现问题
过量生产的浪费
搬运的浪费
物
库存的浪费
不良品的浪费
现场的七大浪费
等待的浪费
人
动作的浪费
(即:现场中不产生附 加值的活动)
法 加工的浪费
图例:
搬运浪费
动作浪费
不良浪费
二、从现场的管理标准中发现问题 做事情的最佳方法。
现状与已确立的标准之间
必须解决的差距。
二、现场改善是谁的事情?
以降低库存的改善为例进行说明: 主责
原材料 采购部
次责 质管部
总库存
在制品 生产部
技术部、质管部
技 术成品 生销产售、部品质 采生购产、部仓、库、、
现场改善与各个部门息息相关。
三、现场改善为什么从生产开始?
• 生产是主线,通过生产过程中发生的问题,拉出 其他版块(采购、技术、人力等)存在的问题。
二、改善的基本步骤:
1.问题的发生、发现
要改善什么
2.现状分析
现状是怎样的(数据)
3.发现问题的重点
为什么会发生(真因)
4.改善方案的制定
怎样对策
5.实施、评价改善方案 对策是否有效(与目标对比)
6.跟踪处理改善方案
标准化
1. 问题的发生、发现 (要改善什么)
调查项目
调查重点
P:生产率、生产量
产量下降了吗/产量还能提高吗/人员过多或过少/ 设备正常吗
1.生产效率低(8个/挂)。 2.喷漆时油漆浪费大。
改善对策:重新设计制作一挂12只的挂具。
效果确认: FD110磁电4.1-4.15不良率为22.9%, 4.16-4.30不良率为20.4%,在不影响品质
现场问题解决及改善实践PPT课件

04 现场问题解决的案例分析
案例一:生产线故障解决
总结词
迅速响应、团队协作
详细描述
生产线突发故障导致生产中断,团队迅速响应,组织技 术专家进行故障诊断,各部门协同合作,短时间内恢复 生产。
案例二:产品质量问题解决
总结词
深入分析、持续改进
详细描述
产品出现质量问题,团队深入分析原因,针对性地制定改进措施,持续跟踪改进 效果,确保问题得到根本解决。
定有效的解决方案提供依据。
PDCA循环
要点一
总结词
PDCA循环是一种科学的问题解决方法,通过计划、执行、 检查和行动四个阶段的循环,不断优化和改进管理过程。
要点二
详细描述
PDCA循环包括Plan(计划)、Do(执行)、Check(检查) 和Act(行动)四个阶段,通过不断循环这四个阶段,可以逐 步优化管理过程,提高工作效率和质量。
案例三:设备维护问题解决
总结词
预防为主、定期维护
详细描述
设备维护不当导致运行故障,团队总结经验教训,加强设备日常巡检,制定定期维护计划,提高设备运行稳定性。
05 现场改善实践的策略和技 巧
5S管理
整理
识别现场需要的和不 需要的物品,将不需 要的物品移出工作区 域。
整顿
对留下的物品进行有 序摆放,明确标识, 方便查找和使用。
鱼骨图
总结词
鱼骨图是一种用于问题分析和解决的图形化工具,通过 将问题分解为若干个相关因素,帮助人们更好地理解和 解决复杂问题。
详细描述
鱼骨图由主干和分支组成,主干表示问题,分支表示与 问题相关的因素。通过逐一分析每个因素,可以找出问 题的根本原因,并制定相应的解决方案。鱼骨图有助于 人们系统地思考问题,避免遗漏重要信息。
现场改善经典培训讲义ppt课件

39
实例探讨
40
推荐书籍
内容简介: 本书内容适用如下读者:想掌握经营管理基础知识、
想知道管理改善的诀窍、想重新评估企业状况、想从陈 规中脱颖而出。
作者简介: 柿内幸夫,斯坦福大学工业工程学士和硕士,改善
顾问股份有限公司董事长、首席顾问兼工程师(经营工 程学)。1974年东京工业大学系毕业后,进入日产汽 车公司所属的横滨工厂生产科工作,历任生产管理部、 富士工厂工业程科长,于1991年辞职。
19
现场问题的发掘
方法的因素 加工方法是否依照工艺书? 生产工序是否有改进空间? 是否制定了明确的检验标准? 运输及包装是否存在问题? 工人的加工动作是否可以简化? 存储方式是否正确?
20
现场问题的发掘
环境的因素 现场是否执行5S管理? 现场机台布局是否合理? 现场物料放置区域是否合理? 物料及产品是否有良好的存储环境? 现场及仓库是否有良好的区域划分?
21
第四部分
如何进行现场改善
22
现场的改善
消极的改善态度:
“我们一直这样做”、“以前试过,没用”、“可以试 试,但是不抱希望” “现在没时间,等下一次”、“晚点再做,没关系” “要花很多钱,很多时间,很多人力” “有问题很正常”、“人都会犯错的” “这次改掉就好了”、“已经做的不错了”、“差不多 就好”
12
附注:QCC
:英文全称QUALITY CONTROL CIRCLE, 中文译作“品管圈”。QCC就是由同一工作场所 的人们,自动自发地结成数人一圈的小团体(又 称QC小组),然后全体合作,活用品管的手法, 发掘工作现场所发生的问题,并自力自主地加以 解决的活动。
13
第三部分
如何发掘现场问题
实例探讨
40
推荐书籍
内容简介: 本书内容适用如下读者:想掌握经营管理基础知识、
想知道管理改善的诀窍、想重新评估企业状况、想从陈 规中脱颖而出。
作者简介: 柿内幸夫,斯坦福大学工业工程学士和硕士,改善
顾问股份有限公司董事长、首席顾问兼工程师(经营工 程学)。1974年东京工业大学系毕业后,进入日产汽 车公司所属的横滨工厂生产科工作,历任生产管理部、 富士工厂工业程科长,于1991年辞职。
19
现场问题的发掘
方法的因素 加工方法是否依照工艺书? 生产工序是否有改进空间? 是否制定了明确的检验标准? 运输及包装是否存在问题? 工人的加工动作是否可以简化? 存储方式是否正确?
20
现场问题的发掘
环境的因素 现场是否执行5S管理? 现场机台布局是否合理? 现场物料放置区域是否合理? 物料及产品是否有良好的存储环境? 现场及仓库是否有良好的区域划分?
21
第四部分
如何进行现场改善
22
现场的改善
消极的改善态度:
“我们一直这样做”、“以前试过,没用”、“可以试 试,但是不抱希望” “现在没时间,等下一次”、“晚点再做,没关系” “要花很多钱,很多时间,很多人力” “有问题很正常”、“人都会犯错的” “这次改掉就好了”、“已经做的不错了”、“差不多 就好”
12
附注:QCC
:英文全称QUALITY CONTROL CIRCLE, 中文译作“品管圈”。QCC就是由同一工作场所 的人们,自动自发地结成数人一圈的小团体(又 称QC小组),然后全体合作,活用品管的手法, 发掘工作现场所发生的问题,并自力自主地加以 解决的活动。
13
第三部分
如何发掘现场问题
《现场改善》PPT课件
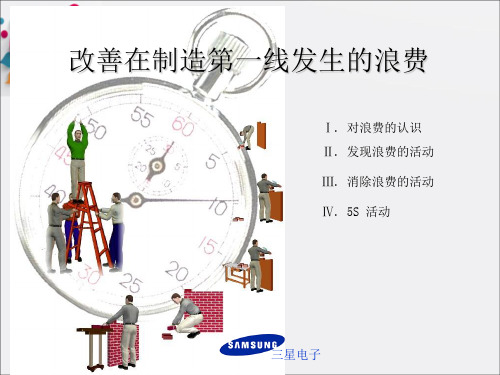
□ 价值
□ 浪费
⑤ 组合PCB
□ 价值
□ 浪费
⑧ 更换箱子
□ 价值 □ 浪费
□ 价值
□ 价值
□ 价值
□ 浪费
⑥ 把螺丝刀拿过来
□ 浪费
□ 浪费
⑨ 挑选出不良产品
Ⅰ. 对浪费的认识
4) 工作和活动
产生净附加价值的动作
• 组装 • 焊接 • 粉刷 • 加工
产生低附加价值的动作
[人] 手工拧紧 KNOW-HOW 工作 追加工作(设计变更) 不良生产
④ 加工本身导致的浪费
工作程序一旦被定下来,工作者就逐渐忘记工作的根本目标而只考虑“工作”
□ 试想在工作方法、环境、条件等方面是否做过多的工作。 □ 试想能否减少或消除现在做的工作。
Ⅰ. 对浪费的认识
⑤ 库存增多导致的浪费
应要抛件、组装品等工厂里的所有物品,也包括仓库和流程过 程的在产品。 ⑥ 动作导致的浪费
用力组装
□ 单纯动作 □ 附带动作 □ 附加价值(非效率性) □ 附加价值(效率性)
按电钮
□ 单纯动作 □ 附带动作 □ 附加价值(非效率性) □ 附加价值(效率性)
Ⅰ. 对浪费的认识
----?
搞不好会 败家的!
了解工作(Work)和活动(Move) ( 工作 ≠ 活动 )
一, 二,三。。
嘿呦 嘿呦
活 动
产生附加价值的动作 收款的动作(大)
非效率动作
收款的动作(小)
单纯动作
浪费钱的动作
附带动作
无法收款的动作
Ⅰ. 对浪费的认识
• 工作动作方面的浪费
由于一个工作由多种动作来完成,需要划分动作并找出各动作的浪费因素。
向零件箱子伸手 拿零件
现场改善(PPT 33页)(1)
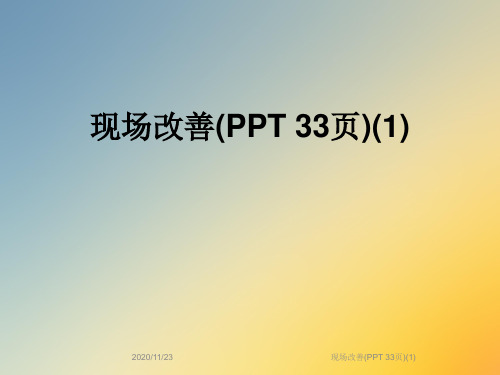
主題選定。
現況掌握及目標設定。
分析蒐集到的資料,以確定真正的原因。
依據資料分析,立定改善對策。
實施改善對策。
對改善對策做效果確認。
建立或修正標準,防止再發。
檢視上述步驟以及進行下一步驟。 现场改善(PPT 33页)(1)
UMAX
3rew
演讲完毕,谢谢听讲!
再见,see you again
涵蓋了產品或服務之開發﹑設計﹑生產﹑ 銷售和服務
现场改善(PPT 33页)(1)
UMAX
源流管理
一.作業方式:
在現場生產之前之有關活動
是從管理階層的方針開始展開
依序確認改善上游之需求
必須建立企劃品質的標準
第一次就把企劃做正確
了解顧客之需求
將了解轉換為工程及設計上之需求
做好事前的準備
现场改善(PPT 33页)(1)
張樂聖
现场改善(PPT 33页)(1)
UMAX
標
準
※ 企業的日常事務,應依據某種已達成共識的程序來運作,
把這些程序清楚地寫下來,就成為標準。
維持和改進標準。
作業標準。
標準的主要特徵。
豐田工機公司。
改善事例(Kaizen Story)。
改善/ISO 9000/QS 9000。
现场改善(PPT 33页)(1)
2020/11/23
现场改善(PPT 33页)(1)
※標準:做事的最佳方法
现场改善(PPT 33页)(1)
UMAX
現場改善~今井正明三大理念
一﹒重視現場:任何問題都要到現場去了解,當場用最簡
單、最不花錢的方式來尋求「改善」,而
非以投入資金,從外界購買最新的科技設
现场IE改善(PPT47张)
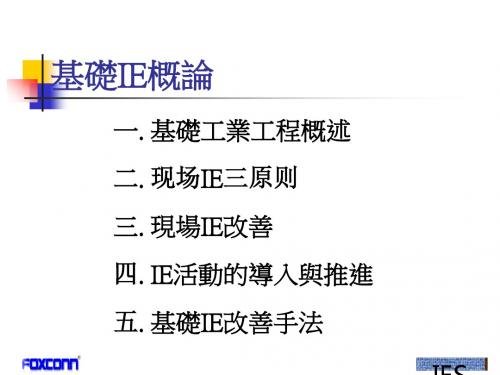
5、改善瓶颈岗位
(1)改善的4大原則
1)减少动作次数 2)同时使用双手 3)缩短移动距离 4)使动作变得轻松
(2) IE动作改善的4原则
ECRS原则 1、Eliminate 2、Combine 3、Rearrange 4、Simplify
——取消 ——合并 ——重排 ——简化
(3)ECRS法运用图示简介
四.基礎IE改善手法 1﹒何謂基礎IE手法
“基礎IE手法是以人的活動為中心 ﹐以事實為依據﹐用科學的分析方法對 生產系統進行觀察﹑記錄﹑分析﹐並對 系統問題進行合理化改善﹐最后對結果 進行標準化的方法”
IE手法一﹕動作改善法(作業標準化)
作業員須每隔28秒轉 身一次﹐取身后的膠 帶﹐這樣每小時須做 150次轉身無效轉身取 膠帶動作
3600<H> 节拍<TT>= 目标产量
二. 现场IE改善<3>
2.现场IE三原则 a、划节距线<25-30cm>,根据标准工时 调整拉速节拍<TT>。 b、保证每个节距有一个产品。 c、每个岗位不准堆积。
生产线平衡计算
平衡率=
(各工序的作业时间总和) * 100% 瓶颈岗位时间*人数<工位数>
改变观念
1、观念改变 2、行动改变 则 则 行动改变 习惯改变
3、习惯改变
则
命运改变
团队与集团的区别
集体
目标不一致
团队
目标一致
Q&A time
本課程到此告一段落﹐請大家就有疑問 的部分踴躍提問﹐謝謝﹗
• • • • • • • • • • • • • • • • • • • • • • • • • • • • • • • • • • • • • • • • • • • • • • • • • • • • • • • • • • • • • • • • • • • • • • • • • • • • • • • • • • • • • • • • • • • • • • • • • • • •
《现场改善技巧》课件
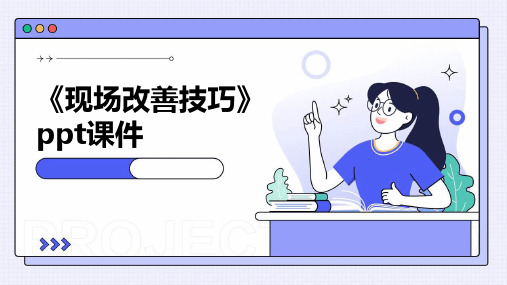
针对评估和审查中发现的问题,制定改进措施并组 织实施。
标准的更新与完善
根据改进效果和生产环境的变化,对作业标准进行 更新和完善,以保持标准的适用性和有效性。
05 目视化管理
目视化管理的定义和作用
01
目视化管理是一种利用视觉信息来管理和控制工作 场所的方法。
02
目视化管理能够提高工作效率,减少错误和浪费, 提升员工的安全意识。
认可和奖励
对积极参与改善活动的员工给予适当的认可和奖励,激发员工的积 极性。
团队合作与竞赛
组织跨部门的团队合作项目或竞赛,激发员工的团队合作精神和竞争 意识。
感谢您的观看
THANKS
作业标准的制定与实施
培训与教育
对员工进行作业标准的培训和教育,确保员工理解和 掌握标准。
监督与检查
建立监督检查机制,确保员工在实际工作中执行标准 。
反馈与改进
收集员工的反馈意见,对标准进行持续改进和优化。
作业标准的持续改进
定期评估与审查
定期对作业标准进行评估和审查,以发现存在的问 题和不足。
改进措施的实施
培养员工的问题意识
发现问题的能力
培养员工敏锐的观察力,能够及时发现现场存在的问题和改进空 间。
分析问题的能力
通过培训和引导,帮助员工学会分析问题产生的原因,并提出有 效的解决方案。
解决问题的能力
鼓励员工勇于承担责任,积极主动地解决问题,提高工作效率和 质量。
鼓励员工参与改善活动
提供培训和支持
为员工提供必要的培训和支持,使其具备参与改善活动的能力和信 心。
现场改善不仅关注单个环节的优化, 更强调整体流程的协同和整合。
现场改善的重要性
提高生产效率
标准的更新与完善
根据改进效果和生产环境的变化,对作业标准进行 更新和完善,以保持标准的适用性和有效性。
05 目视化管理
目视化管理的定义和作用
01
目视化管理是一种利用视觉信息来管理和控制工作 场所的方法。
02
目视化管理能够提高工作效率,减少错误和浪费, 提升员工的安全意识。
认可和奖励
对积极参与改善活动的员工给予适当的认可和奖励,激发员工的积 极性。
团队合作与竞赛
组织跨部门的团队合作项目或竞赛,激发员工的团队合作精神和竞争 意识。
感谢您的观看
THANKS
作业标准的制定与实施
培训与教育
对员工进行作业标准的培训和教育,确保员工理解和 掌握标准。
监督与检查
建立监督检查机制,确保员工在实际工作中执行标准 。
反馈与改进
收集员工的反馈意见,对标准进行持续改进和优化。
作业标准的持续改进
定期评估与审查
定期对作业标准进行评估和审查,以发现存在的问 题和不足。
改进措施的实施
培养员工的问题意识
发现问题的能力
培养员工敏锐的观察力,能够及时发现现场存在的问题和改进空 间。
分析问题的能力
通过培训和引导,帮助员工学会分析问题产生的原因,并提出有 效的解决方案。
解决问题的能力
鼓励员工勇于承担责任,积极主动地解决问题,提高工作效率和 质量。
鼓励员工参与改善活动
提供培训和支持
为员工提供必要的培训和支持,使其具备参与改善活动的能力和信 心。
现场改善不仅关注单个环节的优化, 更强调整体流程的协同和整合。
现场改善的重要性
提高生产效率
《IE现场优化改善》课件

展望
未来企业应进一步拓展IE现场优化改 善的领域,加强与其他管理方法的融 合,实现更高效、更灵活、更智能的 生产模式。
谢谢观看
《IE现场优化改善》PPT课件
目录
• IE现场优化改善概述 • IE现场优化改善方法 • IE现场优化改善案例分析 • IE现场优化改善的未来发展 • 结论与建议
01
IE现场优化改善概述
定义与目标
定义
IE现场优化改善是一种通过系统地分析和改进生产现场的布局、操作流程、设 备及工装夹具等,以提高生产效率、降低成本、提升质量的管理方法。
费,提升产品质量和客户满意度。
动作分析
01
动作分析的定义
通过对作业过程中动作的分析和研究,寻找最优的动作方法和顺序。
02
动作分析的工具
动素分析、动作经济原则。
03
动作分析在IE现场优化中的应用
通过动作分析,消除多余和无效的动作,提高作业效率和生产线的平衡
,降低成本和浪费,提升产品质量和客户满意度。
制定标准、宣传培训、执行落实、检查考 核、持续改进。
通过5S管理,优化现场布局,提高作业效 率和生产线的平衡,减少浪费和不良品, 保障员工安全和健康。
流程优化
流程优化的定义
对现有流程进行分析、改进和优化,提高流程效率和效果。
流程优化的原则
明确目标、关注瓶颈、整体优化、持续改进。
流程优化的方法
流程图绘制、流程分析、流程改进、流程再造。
时间研究
时间研究的定义
通过对作业过程中所需时间的分析和研究,制定标准作业时间。
时间研究的工具
时间测量表、工作抽样。
时间研究在IE现场优化中的应用
通过时间研究,制定合理的生产计划和排程,提高生产效率和产能,降低成本和浪费,提 升产品质量和客户满意度。
未来企业应进一步拓展IE现场优化改 善的领域,加强与其他管理方法的融 合,实现更高效、更灵活、更智能的 生产模式。
谢谢观看
《IE现场优化改善》PPT课件
目录
• IE现场优化改善概述 • IE现场优化改善方法 • IE现场优化改善案例分析 • IE现场优化改善的未来发展 • 结论与建议
01
IE现场优化改善概述
定义与目标
定义
IE现场优化改善是一种通过系统地分析和改进生产现场的布局、操作流程、设 备及工装夹具等,以提高生产效率、降低成本、提升质量的管理方法。
费,提升产品质量和客户满意度。
动作分析
01
动作分析的定义
通过对作业过程中动作的分析和研究,寻找最优的动作方法和顺序。
02
动作分析的工具
动素分析、动作经济原则。
03
动作分析在IE现场优化中的应用
通过动作分析,消除多余和无效的动作,提高作业效率和生产线的平衡
,降低成本和浪费,提升产品质量和客户满意度。
制定标准、宣传培训、执行落实、检查考 核、持续改进。
通过5S管理,优化现场布局,提高作业效 率和生产线的平衡,减少浪费和不良品, 保障员工安全和健康。
流程优化
流程优化的定义
对现有流程进行分析、改进和优化,提高流程效率和效果。
流程优化的原则
明确目标、关注瓶颈、整体优化、持续改进。
流程优化的方法
流程图绘制、流程分析、流程改进、流程再造。
时间研究
时间研究的定义
通过对作业过程中所需时间的分析和研究,制定标准作业时间。
时间研究的工具
时间测量表、工作抽样。
时间研究在IE现场优化中的应用
通过时间研究,制定合理的生产计划和排程,提高生产效率和产能,降低成本和浪费,提 升产品质量和客户满意度。
精益生产现场改善PPT课件

物料
工具
第10页/共15页
物流距离
物流布局应以总物流负载 最小为最佳方案(总物 流负载=距离*对应的物 流量的总和)。
十二 设备优化与摆放
1>按工序布置 2>“U”形、逆时针布置 3>设备布置“三不”原则(不落地生根,不寄人篱下, 不离群索居) 4>设备间距小 5>设备功能够用就好(不追求大而全)
第11页/共15页
十三 产线布局优化
第12页/共15页
传统流水线
适合大订单,大 批量生产。
单元生产线
适合大小订单, 小批量生产。
精简CELL线 适合少量多样,
柔性生产。
十四 现场员工关系管理的秘诀
和谐的员工关系
• 员工工作责任心强 • 工作积极性高 • 企业生产效率高 • 员工稳定,流失率低 • 管理层和员工有效沟通
提高流程的效率,改善平面布置图 去掉时间浪费,缩短生产周期
第9页/共15页
加工 搬运 检查
停滞
十一 物流距离的优化原则
传统物流
供货商
大仓库
IQC
线边仓
生产线
物料员
成品仓
客户
精益物流 供货商
供货商端驻点IQC
生产线
成品仓
客户
三角形原理
物料或工具的放置点、产 品组装点、操作者的 位置形成的三角形的 边长越小越好。
简化(Simplify):经过取消、合并、重组之后,再对该项工作作进一步更深
入的分析研究,使现行方法尽量地简化,以最大限度地缩短作业时间,提高工作效率。
第6页/共15页
八 动作经济的16原则
1
关于人体动作方面: 1 双手并用原则 2 对称反向原则 3 排除合并原则 4 降低动作等级原则 5 减少动作限制原则 6 避免动作突变原则 7 保持轻松节奏原则 8 利用惯性原则 9 手脚并用原则
现场改善培训课件(PPT 69页)

利用聲音、顏色、燈號來降低作業者 的頭部擺動,眼睛飄動和精神負荷。 •注意作業者的工作舒適性有安全性,例如燈 光、座椅等﹔防爆、防火、防割傷等裝置。
7
現場作業的步驟
步驟5 省力化
←最省時、省力、快
工作的設計盡可能使工作者用手 指、手腕的動作等級
8
現場作業的步驟
步驟6 順暢化
• 觀察作業是否順暢。例如下圖開關的位置
留意點
•1.次只拿一套套裝材料, 原則上要依據產距時間
•安排的方式要使水蜘蛛 容易取材料
•倉庫盡量靠近生產線
•作業員要能容易地取得 材料
•只有在標准在制品改變 時才改變時間差
•人選必須是下一次的班 長合格候選人
17
水蜘蛛
❖水蜘蛛的實施
• 逐漸的減少水蜘蛛的人數和擴充其工作范圍。 • 改善水蜘蛛的動作經濟性,使他到達每個供料
5
現場作業的步驟
步驟3 手離化→ 人離化(人、機分離)
• 利用夾具、治具,消除手的扶持加工物動作。 • 利用機器加工的時間同時執行其他的作業(人、機作業的分離) • 作業者有空手步行嗎? • 作業者只是站著或坐著監控機器碼?
機器作業
機器作業
人的作業
人的作業
6
現場作業的步驟
步驟4 舒適化
• 頭部動作左右、上下擺動? • 眼睛要左右移動,或一直注意加工狀態?
2.決定作業改善方向
--進行A.B.C.D之間工作的調整;也就是作業的 消除、合并、重組、簡化(E.C.R.S),使A.B.C. 的工作內容和T/T平衡。 --消除D的12‘‘ --消除所的的浪費、不均勻、勉強
3
現場作業的步驟
3.現場改善作業
步驟1
作業分類:將沒有規則性、偶發性的作業分 離,例如領取材料、整理材料
7
現場作業的步驟
步驟5 省力化
←最省時、省力、快
工作的設計盡可能使工作者用手 指、手腕的動作等級
8
現場作業的步驟
步驟6 順暢化
• 觀察作業是否順暢。例如下圖開關的位置
留意點
•1.次只拿一套套裝材料, 原則上要依據產距時間
•安排的方式要使水蜘蛛 容易取材料
•倉庫盡量靠近生產線
•作業員要能容易地取得 材料
•只有在標准在制品改變 時才改變時間差
•人選必須是下一次的班 長合格候選人
17
水蜘蛛
❖水蜘蛛的實施
• 逐漸的減少水蜘蛛的人數和擴充其工作范圍。 • 改善水蜘蛛的動作經濟性,使他到達每個供料
5
現場作業的步驟
步驟3 手離化→ 人離化(人、機分離)
• 利用夾具、治具,消除手的扶持加工物動作。 • 利用機器加工的時間同時執行其他的作業(人、機作業的分離) • 作業者有空手步行嗎? • 作業者只是站著或坐著監控機器碼?
機器作業
機器作業
人的作業
人的作業
6
現場作業的步驟
步驟4 舒適化
• 頭部動作左右、上下擺動? • 眼睛要左右移動,或一直注意加工狀態?
2.決定作業改善方向
--進行A.B.C.D之間工作的調整;也就是作業的 消除、合并、重組、簡化(E.C.R.S),使A.B.C. 的工作內容和T/T平衡。 --消除D的12‘‘ --消除所的的浪費、不均勻、勉強
3
現場作業的步驟
3.現場改善作業
步驟1
作業分類:將沒有規則性、偶發性的作業分 離,例如領取材料、整理材料