铸件化学成分的控制与配料
zg40cr25ni20si2耐热钢铸件 铬镍合金热处理工装 整体铸造工艺

zg40cr25ni20si2耐热钢铸件铬镍合金热处理工装整体铸造工艺ZG40Cr25Ni20Si2是一种耐热铬镍合金铸件材料,其主要成分包括约25%的铬(Cr)、20%的镍(Ni)以及2%的硅(Si),具有优良的高温抗氧化性、抗渗碳性和一定的耐腐蚀性能。
这种材料适用于制造需要在高温环境下长期稳定工作的工装部件,如炉内支撑梁、炉底板、耐热钢垫块、下料管、排渣管等。
整体铸造工艺流程大致如下:1. 熔炼与配料:-根据ZG40Cr25Ni20Si2的化学成分要求,进行精确的原材料准备和合金元素配比。
-采用中频感应电炉或其他先进熔炼设备对铁水进行冶炼,确保熔体纯净度高,合金元素均匀分布。
2. 浇注前准备:-制作合适的砂型或金属型腔,保证铸件形状准确,内部结构合理。
-对模具进行预热处理,减少铸件冷却时的热应力,并防止模具吸潮导致的缺陷。
3. 浇注成型:-在严格控制温度的情况下将熔融的合金液浇入型腔中,通过合理的浇注系统设计,确保合金液流动平稳且充满整个型腔,避免出现缩孔、气孔等铸造缺陷。
4. 凝固与冷却:-铸件在型腔中逐渐冷却并凝固,期间可能采取适当的冷却速率调控措施以优化铸件微观组织和力学性能。
5. 热处理工序:-铸件凝固后通常需要进行退火、正火或淬火+回火等热处理过程,以消除铸造应力、细化晶粒、改善机械性能和提高耐热稳定性。
6. 后续处理:-热处理完成后,根据需要进行精加工,如机加工、打磨抛光等,使铸件达到最终使用的技术要求和表面质量标准。
7. 检验验收:-完成以上所有步骤后,对铸件进行无损检测(如超声波探伤、磁粉探伤等)及金相组织分析,确认其内在质量和表面完整性符合规定标准。
总之,ZG40Cr25Ni20Si2耐热钢铸件的整体铸造工艺涉及到从原料选择到成品检验的多个环节,每个环节都需要精细化管理与控制,以确保铸件在高温环境下的优异性能和长寿命使用。
铜合金熔铸配料及化学成分调整的生产实践

河南江河 机械有限责任公司 ( 山 鲁 4 7 3 ) 于连顺 6 37 刘玉卿 胡 红利 杨小青 褚克辉
【 要 】 此文主要论述 了在铜合金熔铸生产 中怎样配料及化学成分的调整计算;并总结出了合金熔铸 摘
时 的调 整 配料 计算 及补偿 图和冲 淡 图的应用 ,给从 事铜 合 金熔 铸 技术 工 作者 提 供 一些 启 示 ,方便 铜合 金 熔铸
原 则。
、
铜合金熔炼 时配料应 遵守的基本原则
( )在 铜 合金 熔炼 过 程 中 ,要 生产高 品位 合金 产 1
品,就应选择高品位的金属原料。生产普通产品时, 在
保证产品质量的前提下 ,应选择低成本原料 。
按 照铜合金熔炼配料 原则 ,铜是 贵金属 ,在保 证其 化学成 分合格 的情 况下 ,应适 当降低 铜 的配料 比。H 8 6 黄铜 中 W =6 % ~ 1 ,在实 际工 作 中我 们 常把铜 的 7 7%
应对熔体 的化学成分进行 调整 。
=
2 77. kg。 8
2 .金属补偿计算
所谓元素补偿计算就是经 炉前分析结果 ,某种元素 含 量低 于所要 的化学成分范 围下限时 ,对该 来自素进行补 加 的计算 。
加 以修正 。初步确定 的配料 比 ,不可能 完全满 足合 金化 学成分要 求 ,还 可根 据 熔铸 出来 的成 分 结 果再 进行 调
按 国标采用  ̄ 0 m试 棒检 测铸 件组 织与性 能 具有代 表 bm 3
性。
( )成分调整后 ,金相组织明显改善 ,大 大降低 了 2
组织 中碳化物 的含量 ,并优 化了碳化物 的分布 形式 ,使
铸造配料计算
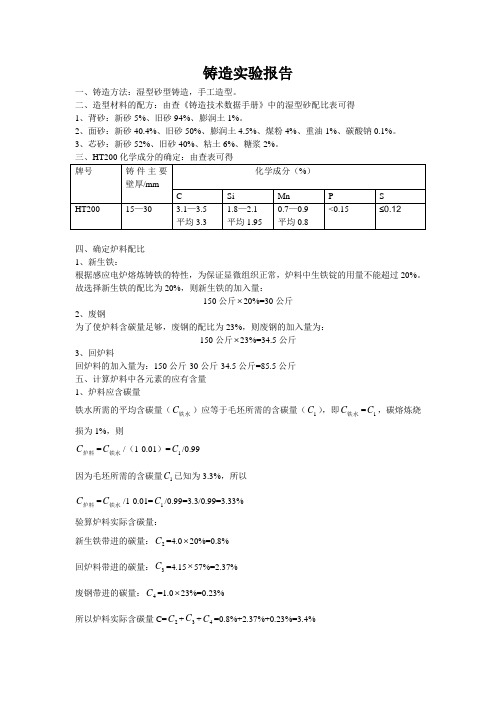
铸造实验报告一、铸造方法:湿型砂型铸造,手工造型。
二、造型材料的配方:由查《铸造技术数据手册》中的湿型砂配比表可得 1、背砂:新砂5%、旧砂94%、膨润土1%。
2、面砂:新砂40.4%、旧砂50%、膨润土4.5%、煤粉4%、重油1%、碳酸钠0.1%。
3、芯砂:新砂52%、旧砂40%、粘土6%、糖浆2%。
四、确定炉料配比 1、新生铁:根据感应电炉熔炼铸铁的特性,为保证显微组织正常,炉料中生铁锭的用量不能超过20%。
故选择新生铁的配比为20%,则新生铁的加入量:150公斤⨯20%=30公斤2、废钢为了使炉料含碳量足够,废钢的配比为23%,则废钢的加入量为:150公斤⨯23%=34.5公斤3、回炉料回炉料的加入量为:150公斤-30公斤-34.5公斤=85.5公斤 五、计算炉料中各元素的应有含量 1、炉料应含碳量铁水所需的平均含碳量(铁水C )应等于毛坯所需的含碳量(1C ),即铁水C =1C ,碳熔炼烧损为1%,则炉料C =铁水C /(1-0.01)=1C /0.99因为毛坯所需的含碳量1C 已知为3.3%,所以炉料C =铁水C /1-0.01=1C /0.99=3.3/0.99=3.33%验算炉料实际含碳量:新生铁带进的碳量:2C =4.0⨯20%=0.8% 回炉料带进的碳量:3C =4.15⨯57%=2.37% 废钢带进的碳量:4C =1.0⨯23%=0.23%所以炉料实际含碳量C=2C +3C +4C =0.8%+2.37%+0.23%=3.4%2、炉料应含硅量:铁水所需的平均含硅量(铁水Si )应等于毛坯所需的含硅量(1Si ),即铁水Si =1Si ,硅熔炼烧损为6%,则炉料Si =铁水Si /(1-0.06)=1Si /0.94因为毛坯所需的含硅量1Si 已知为1.95%,所以炉料Si =铁水Si /(1-0.06)=1Si /0.94=1.95/0.94=2.07%验算炉料实际含硅量:新生铁带进的含硅量:2Si =1.85%⨯20%=0.37% 回炉料带进的含硅量:3Si =1.5%⨯57%=0.855% 废钢带进的含硅量:4Si =0.26%⨯23%=0.05%所以炉料实际含硅量Si =2Si +3Si +4Si =0.37%+0.855%+0.06%=1.285% 炉料中尚缺硅量=炉料应含硅量-炉料中实际含硅量=2.07%-1.285%=0.785% 3、炉料应含锰量铁水所需的平均含锰量(铁水Mn )应等于毛坯所需的含锰量(1Mn ),即铁水Mn =1Mn ,锰熔炼烧损为8%,则因为毛坯所需的含锰量1Mn 已知为0.8%,所以炉料Mn =铁水Mn /(1-0.08)=0.8//0.92=0.87%验算炉料实际含锰量:新生铁带进的锰量:2Mn =0.03%⨯20%=0.006% 回炉料带进的锰量:3Mn =0.7%⨯57%=0.399% 废钢带进的锰量:4Mn =0.25%⨯23%=0.058%所以炉料中实际含锰量Mn =2Mn +3Mn +4Mn =0.006%+0.399%+0.058%=0.463%炉料中尚缺锰量=炉料应含锰量-炉料实际含锰量=0.87%-0.463%=0.407% 六、计算铁合金加入量 1、硅铁加入量补加含硅75%的硅铁的百分数=炉料中尚缺的硅量(%)/硅铁的含硅量(%)=0.785/75%=1.05% 即每100公斤炉料补加1.05公斤含硅75%的硅铁 则150公斤炉料补加含硅75%的硅铁量为: 1.5⨯1.05公斤=1.57公斤2、锰铁加入量补加含锰65%的锰铁的百分数=炉料中尚缺的锰铁(%)/锰铁的含量(%)=0.407%/65%=0.626%即每100公斤炉料补加0.626公斤含锰65%锰铁则则150公斤炉料补加含锰65的锰铁量为:1.5 0.626公斤=0.939公斤七、配料单炉料名称加入量(公斤)新生铁30废钢34.5回炉料85.5Si75(75硅铁) 1.57Mn2(65锰铁)0.939。
铸造铁配料比例

铸造铁配料比例铸造铁的配料比例是一个复杂且重要的主题,涉及到多个因素和技术细节。
为了确保高质量的铸造产品,必须精确控制配料比例。
本篇文档将详细介绍铸造铁的配料比例,以期为相关行业提供有益的参考。
一、铁合金的种类与作用铸造铁中常用的铁合金主要包括生铁、废铁、回炉料和铁合金等。
这些铁合金在铸造过程中起着不同的作用。
生铁含有大量硅、锰、磷、硫等元素,能够提高铁的铸造性能和机械性能;废铁和回炉料可以降低成本;铁合金则可以调整铁的化学成分,提高其力学性能。
二、配料比例的计算铸造铁的配料比例计算是确保产品质量的关键环节。
根据铸造工艺要求和产品性能需求,需要精确计算各种铁合金的比例。
通常采用质量分数或重量比来表示配料比例,并考虑以下因素:1. 铸造产品的机械性能要求:根据产品用途,确定所需的最大强度、硬度和延伸率等指标,从而选择合适的铁合金种类和比例。
2. 铸造工艺要求:不同的铸造工艺对配料比例有不同的要求。
例如,砂型铸造与金属型铸造所需的配料比例不同,需根据实际情况调整。
3. 成本因素:在满足性能要求的前提下,应尽量降低成本。
通过合理搭配各种铁合金的比例,实现成本的有效控制。
三、实际操作中的注意事项在配料过程中,需注意以下几点:1. 确保原料质量:使用的各种铁合金应符合质量标准,避免因原料质量问题影响最终产品的性能。
2. 精确称量:采用高精度的称量设备,确保每种铁合金的比例准确无误。
3. 混合均匀:在配料过程中,需充分搅拌各种铁合金,确保混合均匀,以免因局部比例失调导致产品性能波动。
四、实验与调整完成配料比例的计算后,需进行实验验证。
通过制作实验样本,检测其各项性能指标,如力学性能、金相组织等。
根据实验结果,对配料比例进行调整,以满足实际生产需求。
在多次实验与调整后,最终确定最佳的铸造铁配料比例。
五、质量控制与标准化为确保铸造铁配料比例的稳定性和一致性,需建立严格的质量控制体系。
对配料过程进行标准化管理,制定详细的操作规程和工艺卡片。
铸铁件配料方法

铸铁件配料方法,及锰铁铬铁加入量配比HT250是珠光体灰铸铁。
化学成分:碳C :3.16~3.30硅Si:1.79~1.93锰Mn:0.89~1.04硫S :0.094~0.125磷P :0.120~0.170根据化学成分考虑原料的成分及烧损就可以知道配料了影响铸铁、铸钢件组织和性能的因素,有化学成分、孕育(变质)处理、冷却速度、炉料的“遗传性”、铁水过热温度等,在这几个因素中,化学成分含量的高低对铸件物理性能的影响相对更大些,而且是第一因素。
所以在生产过程中,根据铸件物理性能的要求,正确的配料或调料,严格控制材质的各化学成分含量尤为重要。
在生产实践中,作为冶炼技术人员和炉工来说,配料和调料应该是熟练掌握的一般性技术问题。
但是对予刚毕业的学生和大多数炉工来说,欲能系统、灵活的掌握,也确非易事。
要想控制铸件的化学成分与配料,必须事先了解以下几下问题:1、铸件的目标化学成分。
2、库存各种金属炉料的化学成分。
3、各种炉料在冶炼过程中化学成分的增减变化率。
4、配料方法。
一、目标化学成分现在大部分铸件,根据其牌号要求的不同,国标中已做出了相应的要求,从铸造手册中即可查到。
但是随着科技的进步,根据铸件的服役状况,市场需要更多物理性能各不相同的铸件,并对铸件的综合性能质量提出了更高的要求,科研单位也不断研究出新材质而取代旧材质,例如某水泥研究设计院研究的“中碳多元合金钢”,成功的代替了原需进口的球磨机衬板,代替了高锰钢,用该材质生产直径φ2.4甚至直径φ4.2的中大型球磨机衬板上,降低了生产成本,取得了良好的经济效益。
另外,如某厂生产出口国外石油钻井用的泥浆泵高铬双金属缸套及采石场600×900破碎机用的锤头,都是超高铬铸铁,这些材质的详细化学成分要求,在铸造手册中是查不到的。
在接受生产绪如上述产品时,如果自己没有完全掌握铸件化学成分要求,以及没有详细了解铸件的服役状况时,应让用户提供尽可能详细的化学成分要求范围及热处理工艺。
铁铸件制作配方介绍

铁铸件制作配方介绍全文共四篇示例,供读者参考第一篇示例:铁铸件在工业生产中扮演着非常重要的角色,它们被广泛应用于汽车、机械设备、建筑物以及其他领域。
铁铸件的制作过程需要严格遵循一定的配方,并且需要经过多道工艺流程来完成。
本文将介绍铁铸件制作的配方和工艺流程,帮助读者了解铁铸件的制作过程。
铁铸件的主要成分是铁和碳,其中碳的含量通常在2%~4%之间。
铁铸件通常通过熔铁炉熔炼铁水,然后倒入铸型中进行冷却凝固,最终制成所需形状的铁铸件。
下面将详细介绍铁铸件的制作配方和工艺流程。
1. 铁铸件的配方包括铁水、造型砂、脱模剂等材料。
铁水是最重要的原材料,其含有铁和碳,通过添加其他合金元素来改变铸件的性能。
造型砂是模具的主要材料,用于制作铸件的外形和内部结构。
脱模剂用于减少砂型和铸件之间的粘附力,便于取出铸件。
2. 制作铁铸件的工艺流程包括模具制作、熔炼铁水、浇铸、冷却凝固、清理等步骤。
首先在模具中制作出铸件的外形和内部结构,然后将铁水熔铸到模具中,待冷却凝固后取出铸件,最后清理表面和修整尺寸。
3. 铁铸件的制作过程需要严格控制制度参数,包括铁水的温度、流速和压力,模具的温度和湿度,冷却速度等。
这些参数直接影响铸件的质量和性能,需要经验丰富的操作人员进行控制。
4. 铁铸件的质量和性能受到许多因素的影响,如原材料、工艺流程、设备等。
在选择配方和制度参数时需要考虑这些因素,以确保铁铸件的质量达标。
铁铸件制作是一个复杂的工艺过程,需要严格遵循配方和工艺流程,并且需要经验丰富的操作人员来进行控制。
只有在掌握了铁铸件制作的技术要点和经验后,才能生产出质量优良的铁铸件,满足各种工业领域的需求。
希望本文能够为读者提供一些关于铁铸件制作配方和工艺流程方面的参考,帮助读者更好地了解铁铸件的制作过程。
【2000字】第二篇示例:铁铸件,又称为铸铁件,是一种由铁水铸造而成的金属零部件,它广泛应用于机械设备、汽车工业、建筑工程等领域。
铁铸件具有成本低廉、制造工艺简单、性能稳定可靠等优点,因此在工业生产中得到了广泛的应用。
球墨铸铁铸件配料实用技术

) * $ + ) * $’
) * $ + ) * $#
球化孕育处理时的操作要点:-)铁液处理温度应在 $,)). 以上,以保证球化及孕育
处理能顺利进行:/)选用球化剂时应注意到金属炉料中是否有干扰元素,原铁液温度和
硫含量多少,生产工艺和铸件要求如何?通常,当炉料中干扰元素较高时应选用稀土含
量较高的球化剂,用钒钛生铁生产球墨铸铁时应选用高稀土球化剂(如 012345 678$6
珠岩集渣剂等),冲入!" + #$的铁液,待球化剂反应趋于平稳时,补加其余铁液,并在出铁 槽里均匀地加入孕育剂,出完铁后要充分搅拌铁液,加脱硫剂和草灰,搅拌扒渣 ! + # 次,
而后取样检验,用覆盖剂或草灰保温。
四、球墨铸铁铁液质量的炉前控制(见表 ! " # " $&)
五、球墨铸铁的配料
$ * 热处理态球墨铸铁的配料 配料应用举例 # " 6 欲生产退火态高韧度球墨铸铁 ?@,)) " $6,成分(质量分数)要求为:9#A ’( + ,*)(、23!A )( + !*&(、4B!)*%(、C!)*)&、2!)*)#(,试计算出所用炉料的加入百分数?
表 ! " # " $% 球化孕育时硅铁(硅 &’)孕育的加入量
孕育处理方法
炉前孕育
二次孕育
浇口杯孕育
漏斗包外孕育 硅铁棒瞬时浇包孕育
加入量(质量分数) )*’ + $*%
(()
出铁槽 )*# + $*) 铁液表面 )*! + )*,
) * $ + ) * $’
注:熔制铸态铁索体球墨铸铁时孕育剂的加入量可取稍大值。
铸钢200-400化学成分

铸钢200-400化学成分
铸钢是一种用于铸造工艺的特殊钢材,通常用于制造零件和构件。
铸钢的化学成分可以因不同的标准和要求而有所不同,但一般来说,铸钢的化学成分主要包括碳、硅、锰、磷和硫等元素。
在铸钢的化学成分中,碳是最重要的元素之一,它的含量通常在0.2%到0.4%之间。
碳的含量会影响铸钢的硬度和强度,过高或过低的碳含量都会影响铸钢的性能。
除了碳以外,硅也是铸钢中常见的元素,它有助于提高铸钢的流动性和润滑性。
硅的含量通常在0.2%到0.5%之间。
另外,锰是一种常见的合金元素,它可以提高铸钢的强度和韧性。
铸钢中的锰含量通常在0.5%到1.2%之间。
此外,磷和硫是铸钢中的杂质元素,它们的含量应该尽量控制在较低的水平,因为过高的磷和硫含量会对铸钢的加工性能和机械性能产生不利影响。
总的来说,铸钢的化学成分会根据具体的生产要求和用途有所
不同,但以上提到的元素通常是铸钢中重要的组成部分。
在生产和使用铸钢时,需要根据具体情况对化学成分进行严格控制和调整,以确保铸钢具有所需的性能和质量。
铸件浇冒口和铸件本体成分

铸件浇冒口和铸件本体成分
摘要:
1.铸件浇冒口和铸件本体成分的定义与作用
2.铸件浇冒口和铸件本体成分的种类与选择
3.铸件浇冒口和铸件本体成分对铸件质量的影响
4.铸件浇冒口和铸件本体成分的控制方法
5.结论
正文:
一、铸件浇冒口和铸件本体成分的定义与作用
铸件浇冒口是指在铸造过程中,连接模具和浇注系统的短管道,它的作用是引导熔融金属从浇注系统进入模具,并在填充模具的过程中,为铸件提供足够的压力和速度。
铸件本体成分是指铸件的主要化学成分,它决定了铸件的性能和质量。
二、铸件浇冒口和铸件本体成分的种类与选择
铸件浇冒口的种类主要有直浇冒口、弯浇冒口和横浇冒口等,选择浇冒口的种类需要根据铸件的结构、尺寸和生产工艺来确定。
铸件本体成分的种类主要有铁素体、珠光体、马氏体和奥氏体等,选择铸件本体成分需要根据铸件的使用环境和性能要求来确定。
三、铸件浇冒口和铸件本体成分对铸件质量的影响
铸件浇冒口的设计不合理或质量不好,可能会导致铸件出现浇注不足、气孔、夹杂等缺陷,影响铸件的质量。
铸件本体成分的不合理,可能会导致铸件的强度、硬度、耐磨性等性能不佳,影响铸件的使用寿命。
四、铸件浇冒口和铸件本体成分的控制方法
对于铸件浇冒口,可以通过优化设计、严格控制浇注温度和压力、选择优质的材料和合理的制造工艺等方式来控制其质量。
对于铸件本体成分,可以通过合理的配料、精确的熔炼温度控制、严格的化学成分分析和质量检测等方式来控制其成分。
五、结论
铸件浇冒口和铸件本体成分是影响铸件质量的重要因素,需要对其进行科学的设计和严格的控制。
铸件化学成分的控制与配料(下)

铸件化学成分的控制与配料 ( ) 下
驻马店柴油机厂 ( 河南 4 30 ) 杨群收 6 00 4 3 0 ) 康晋 辉 6 00 崔 勇 驻马店高级技 工学校 ( 河南 姚 恩广
三 、配料
在配 料前 选 择 原 材 料 时 ,既 要 照 顾 到 铸 件 的质 量要 求 ,还 要 注 意 到 各 材 料 的 价 格 ,以及 库 存 量 , 尽 可能 多 地利 用 本 厂 的 回炉 料 、废 钢 和 废 铁 ,以 降
作为铸造熔炼技术工作者来说在实践中应把理论与实践结合起来掌握规律总结经验制订工艺只有这样工作起来才能得心应手游刃有根据铸件的服役状况对特定的铸件应取什么样的金相组织不同成分对组织影响能引起材质综合性能产生怎样的变化等都应做到心中有例如油田钻井用的泥浆泵高铬双金属缸套的内套和采石厂用的破碎机锤头其材质都是高铬铸铁由于工况条件各不相同在控制其化学成分的上下限时就存在差异
进 行选 取 。
4
配人量 ( ) % 4 5
4 0
例 如 :H 2 0牌号 灰铸 铁 的 叫 T5 =3 1 一3 4 , .% .% 新 生铁 的 W :3 8 ,回炉 料 的 W .% =3 2 ,废 钢 的 .%
Wc=0 4 。 .%
废 钢
I 5
累 积代 入 的成 分 :
O5 . 08 .
废 钢
O4 .
O 2 .7
05 .
配 料方 法及 公式 ,除 碳 的 配 料 计 算 方 法 是 两个 以上外 ,其 他元 素 的配 比计算均 是 累积 法 。
用上 述 原 材 料 并 配 用 7 SF 、6 Mn e 5 ie 5 F ,用 冲 天 炉生 产灰 铸铁 H 2 0 T 0 ,其 化学成 分要 求 如表 3所示 。
如何控制箱体类铸件的内在质量

优质铁液的前提 。⑤进行低合金化处理 。如对高牌 号的铸铁件采取铁液孕育处理 ,以保证铸件的较高 性能 。⑥控制保温时间。铸型浇注后 ,控制合理的 保温时 间也是影响铸件加工性能的重要因素 。 ( )金 相组织 2 其组 织为 ≥9 %的珠光体基 0
体 及 4 级 A型 均 匀分 布 的 片 状 石 墨 ,应避 免 出现 ~5 D 的 过 冷石 墨 。 型
磷 常 以 低 熔 点 的 二 元 或 三 元 磷 共 晶 存 在 于 晶
界 ,有利 于提高 灰铸铁 的耐磨性 。但 因磷共 晶较 脆 ,箱体类铸件的热节点较 多,当磷量较高时 ,易 使铸件产生冷裂纹 ,故一般控制在W <01%。 . 5
总 之 ,对 于 箱 体 类 的 灰 铸 铁 件 ,其 化 学 成 分可
如何控制箱体类铸件的内在质量
山推股份 传动公 司 ( 山东 济宁 2 2 O ) 张西水 7 1 0
【 摘要】随着机械产品质量 的提升 ,对铸 件的
内在质 量 提 出 了更 高 的要 求 。在 铸 造 生产 中 ,要 获 得 优 质 铸 件 ,保 证 其 内在 质 量是 关键 。 内在 质 量 包 括 化 学成 分、 金 相 组 织 、 力 学性 能 、加 工 性 能 及 内 部 缺陷等。
元素 ,对铸铁的组织和性能起着决定性的影响。
碳 和 硅 :碳 是 产 生 、促 进 石 墨 化 的 基础 。在 一 定 条件 下 ,含 碳 量越 高 ,石 墨 片变 粗 ,数量 增 多 , 强 度和 硬 度 下 降 ;硅 是 强 烈 促进 石 墨 化 的元 素 ,它 的 作用 比碳 的 作 用 大 。 因此 ,在生 产 中常 用 碳 当量
的优化设计
一
汽 巴勒特 锻造 ( 春 )有 限公司 ( 长 吉林
铸件配料实用技术(生铁锭与废钢铁)

一、生铁锭生铁锭是熔制铸铁和铸钢的最主要金属炉料,约占配料重量的20%~100%,它的化学成分是否稳定、硫磷含量和有害杂质含量是否低,直接关系到所熔制铸铁和铸钢的质量。
合理的选用生铁锭也是获得低成本配料的有效方法之一。
生铁锭可分为铸造生铁、球墨铸铁专用生铁、炼钢生铁、高纯生铁和特种生铁等,均有标准,见表2-1-1至表2-1-7。
生产上常用生铁的化学成分和微量元素含量,见表2-1-8至表2-1-13。
通常:熔制灰铸铁时,应选用铸造生铁。
硅的质量分数为2.0%~3.0%的铸造生铁可用于熔制低牌号灰铸铁;硅的质量分数为1.2%~2.0%的铸造生铁可用于熔制高牌号灰铸铁。
熔制球墨铸铁时,应选用球墨铸铁专用生铁,但也可选用低硅、低锰和低磷硫的铸造生铁或炼钢生铁。
对于要求特别高的球墨铸铁也可选用高纯生铁。
球墨铸铁所用新生铁的硅的质量分数一般在0.8%~1.75%的范围内选择。
熔制大断面球墨铸铁件或铸态铁索体球墨铸铁件时,生铁的锰含量希望低于0.3%,不应超过0.5%,越低越好;熔制珠光体、贝氏体、退火铁索体球墨铸铁体时,生铁的锰的质量分数应小于0.6%;熔制正火珠光体球墨铸铁的中小型铸件时,生铁的锰的质量分数可适当放宽,一般也不要超过0.8%。
对于低温下工作的铁素体韧性球墨铸铁件和其他要求韧性较高的球墨铸铁件,应选用磷的质量分数小于0.07%的生铁。
一般球墨铸铁件用生铁磷的质量分数不应大于0.1%;硫的质量分数应限制在0.05以下;反球化元素不得过量ωTe<0.01%、ωTi<0.3%、ωSn<0.09%、ωSb<0.2%、ωPb<0.2%、ωBi<0.05%。
熔制蠕墨铸铁时,应参照熔制球墨铸铁的要求选用生铁。
熔制可锻铸铁时,一般只加入10%左右的生铁量,主要是为了提高碳含量,因此含磷、硫和铬低的铸造生铁、炼钢生铁和再生铁均能使用。
熔制特种铸铁时,应尽量选用含相应元素高的铸造生铁或特种生铁。
铁铸件制作配方介绍

铁铸件制作配方介绍全文共四篇示例,供读者参考第一篇示例:铁铸件是一种常见的金属制品,具有良好的耐磨、耐腐蚀和强度高的特点,在机械制造、建筑工程、汽车制造等领域有着广泛的应用。
铁铸件的制作过程中关键的一步就是铁铸件制作配方的确定,这直接影响到铁铸件的质量和性能。
接下来,我们就来详细介绍一下铁铸件制作配方的相关知识。
一、铁铸件制作配方概述铁铸件的原料主要由铁和一定量的碳组成,碳的含量在2%-4%左右。
通常情况下,还会加入少量的硅、锰、磷等元素,以提高铁铸件的硬度、韧性和耐磨性。
铁铸件制作配方的选择取决于具体使用要求,不同的配方会影响铁铸件的材质和性能。
1. 铁料:铁是铁铸件的主要原料,可选用生铁、废钢等。
生铁主要包括灰口铸铁、球墨铸铁等,灰口铸铁具有优良的流动性和耐磨性,球墨铸铁则具有良好的韧性和强度。
废钢也是一种常用的铁铸件原料,主要包括废钢丝、废钢板等,可以降低成本。
2. 碳含量:碳是铁铸件中的重要元素,对铁铸件的硬度和强度有着重要影响。
通常情况下,铁铸件中的碳含量控制在2%-4%之间,过高或者过低都会影响铁铸件的性能。
3. 硅、锰等元素:硅和锰是常用的合金元素,可以提高铁铸件的硬度和强度,同时还可以改善铁的流动性和耐磨性。
磷是一种常见的杂质元素,过高的磷含量会导致铁铸件的脆性增加。
4. 其他合金元素:除了上述的元素外,还可以根据需要添加其他合金元素,如铬、钼等,以满足不同领域的使用要求。
确定铁铸件制作配方需要考虑以下几个方面:1. 使用要求:根据铁铸件的具体使用要求确定碳含量、硅含量、锰含量等元素的含量,以满足不同领域的需求。
2. 原料选择:根据铁料的品种和质量选择合适的原料,如生铁、废钢等。
3. 合金元素的选择:根据铁铸件的使用环境和要求选择合适的合金元素,以提高铁铸件的性能。
4. 配方调整:在确定了铁铸件的基本配方后,需要进行小规模试验,不断调整配方,以获得最佳的铁铸件制作配方。
四、铁铸件制作过程铁铸件的制作过程主要包括原料准备、熔炼、浇注、冷却、清理等步骤。
铸造配料计算
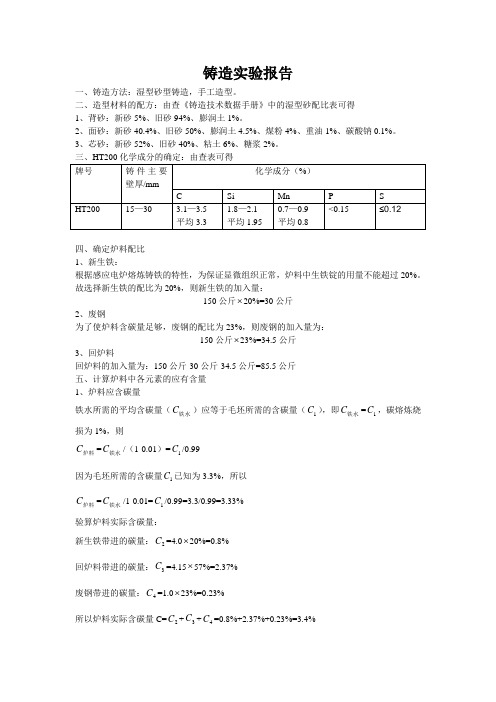
铸造实验报告一、铸造方法:湿型砂型铸造,手工造型。
二、造型材料的配方:由查《铸造技术数据手册》中的湿型砂配比表可得 1、背砂:新砂5%、旧砂94%、膨润土1%。
2、面砂:新砂40.4%、旧砂50%、膨润土4.5%、煤粉4%、重油1%、碳酸钠0.1%。
3、芯砂:新砂52%、旧砂40%、粘土6%、糖浆2%。
四、确定炉料配比 1、新生铁:根据感应电炉熔炼铸铁的特性,为保证显微组织正常,炉料中生铁锭的用量不能超过20%。
故选择新生铁的配比为20%,则新生铁的加入量:150公斤⨯20%=30公斤2、废钢为了使炉料含碳量足够,废钢的配比为23%,则废钢的加入量为:150公斤⨯23%=34.5公斤3、回炉料回炉料的加入量为:150公斤-30公斤-34.5公斤=85.5公斤 五、计算炉料中各元素的应有含量 1、炉料应含碳量铁水所需的平均含碳量(铁水C )应等于毛坯所需的含碳量(1C ),即铁水C =1C ,碳熔炼烧损为1%,则炉料C =铁水C /(1-0.01)=1C /0.99因为毛坯所需的含碳量1C 已知为3.3%,所以炉料C =铁水C /1-0.01=1C /0.99=3.3/0.99=3.33%验算炉料实际含碳量:新生铁带进的碳量:2C =4.0⨯20%=0.8% 回炉料带进的碳量:3C =4.15⨯57%=2.37% 废钢带进的碳量:4C =1.0⨯23%=0.23%所以炉料实际含碳量C=2C +3C +4C =0.8%+2.37%+0.23%=3.4%2、炉料应含硅量:铁水所需的平均含硅量(铁水Si )应等于毛坯所需的含硅量(1Si ),即铁水Si =1Si ,硅熔炼烧损为6%,则炉料Si =铁水Si /(1-0.06)=1Si /0.94因为毛坯所需的含硅量1Si 已知为1.95%,所以炉料Si =铁水Si /(1-0.06)=1Si /0.94=1.95/0.94=2.07%验算炉料实际含硅量:新生铁带进的含硅量:2Si =1.85%⨯20%=0.37% 回炉料带进的含硅量:3Si =1.5%⨯57%=0.855% 废钢带进的含硅量:4Si =0.26%⨯23%=0.05%所以炉料实际含硅量Si =2Si +3Si +4Si =0.37%+0.855%+0.06%=1.285% 炉料中尚缺硅量=炉料应含硅量-炉料中实际含硅量=2.07%-1.285%=0.785% 3、炉料应含锰量铁水所需的平均含锰量(铁水Mn )应等于毛坯所需的含锰量(1Mn ),即铁水Mn =1Mn ,锰熔炼烧损为8%,则因为毛坯所需的含锰量1Mn 已知为0.8%,所以炉料Mn =铁水Mn /(1-0.08)=0.8//0.92=0.87%验算炉料实际含锰量:新生铁带进的锰量:2Mn =0.03%⨯20%=0.006% 回炉料带进的锰量:3Mn =0.7%⨯57%=0.399% 废钢带进的锰量:4Mn =0.25%⨯23%=0.058%所以炉料中实际含锰量Mn =2Mn +3Mn +4Mn =0.006%+0.399%+0.058%=0.463%炉料中尚缺锰量=炉料应含锰量-炉料实际含锰量=0.87%-0.463%=0.407% 六、计算铁合金加入量 1、硅铁加入量补加含硅75%的硅铁的百分数=炉料中尚缺的硅量(%)/硅铁的含硅量(%)=0.785/75%=1.05% 即每100公斤炉料补加1.05公斤含硅75%的硅铁 则150公斤炉料补加含硅75%的硅铁量为: 1.5⨯1.05公斤=1.57公斤2、锰铁加入量补加含锰65%的锰铁的百分数=炉料中尚缺的锰铁(%)/锰铁的含量(%)=0.407%/65%=0.626%即每100公斤炉料补加0.626公斤含锰65%锰铁则则150公斤炉料补加含锰65的锰铁量为:1.5 0.626公斤=0.939公斤。
铸件化学成分的控制与配料(上)

温 度提 高 的同时 ,也 促使 碳 向铁 液 中 的溶 解 。 因此 , 底 焦高 度过 高时 ,铸铁 的增 碳量 也 大 。 如果 炉底 高度 垫 的高 ,铁 液 下 落 流经 的路 程 短 ,
院研 发 的 “ 中碳 多元合 金钢 ” ,成 功 地代 替 了原需 进
化规 律 ,将 是 一 个 较为 复杂 的 问题 。熔 炼 设 备 的 不
同 ,如 冲天 炉 ( 、冷 风 )三 节 炉 、中频 感 应 电 炉 热 等 ,其化学 成 分 的 变化 都 各 不 相 同。 即便 是 同 一个 炉子 ,因修 炉所 用材 料 的不 同 ,以及 操 作 方 法 的 不 同 ,熔 炼过 程 中化 学 成 分 的 变 化 也不 相 同。 以 冲天 炉 为例 ,热 风 与 冷 风 ,风 压 的 高 低 ,风 眼 直 径 的 大
泵 高铬双金 属 缸套 及 采 石场 6 0 0 m 破 碎机 0 mm X9 0 m 用 的锤 头 ,都是 超高 铬铸 铁 ( 要成 分 见 表 1 ,这 主 ) 些材 质 的详 细化 学 成 分要 求 ,在 铸 造 手 册 中 是查 不
到 的。
表 1 超 高 铬 铸 铁 化 学成 分 ( 量 分 数 ) 质
要想 掌握各 种 炉 料 在 熔炼 过程 中化 学 成 分 的 变
但 是随 着 科 技 的 进 步 ,根 据 铸 件 的 服 役 状 况 , 市 场需要 更 多 物理 性 能 各 不 相 同 的铸 件 ,并 对 铸 件 的综合性 能 提 出了更 高 的要 求 ,科 研单 位 也 不 断 研 究 出新材 质 来 取代 旧材 质 ,例 如 合 肥水 泥研 究 设 计
性 、中性或 是碱 性 ,其 材 质 化 学 成 分 的 变 化都 不 尽
(整理)铁水化学成分控制

铁水化学成分控制1、正确的配料计算配料算是保证化学成分合乎要求的首要环节。
冲天炉的配料计算,就是根据铁水化学成分要求,考虑冲天炉在熔炼过程中元素的变化(增、减)和炉料的实际情况,计算出各种金属炉料的配合比例。
下面以HT200铸铁为例,说明配料计算方法。
1.1 配料计算的原始资料(1)铸铁的化学成分各种牌号铸铁要求的化学成分,随铸件壁厚和铸造方法而异。
HT200的化学成分范围为: C3.3~3.5%;Si1.5~2.0%;Mn0.5~0.8; S<0.12%;P<0.25。
(2)各种金属材料的化学成分用于配制HT200的金属炉料平均成分如下表。
炉料化学成分(%)名称 C Si Mn P SZ15生铁 4.19 1.56 0.76 0.04 0.036回炉料 3.28 1.88 0.66 0.07 0.098废钢 0.15 0.35 0.50 0.05 0.05注:所用铁合金为含硅45%硅铁,含锰75%锰铁。
(3)熔炼过程中元素的变化:在下表中列入了常见元素在冲天炉熔化过程中的增减率。
常见元素在冲天炉熔化过程中的增减率 %增减情况 C S Mn Si炉料中<3.2 炉料中>3.6极限范围 +(0/60) -(0/10) +﹛25/100) -(10/50) -(0/40)一般范围 +(5/40) -(3/8) +﹛40/80) -(15/25) -(10/20)增减情况 P Cr Mo Cu Ni V Ti-------------------------------------------------------------------------------------------- 极限范围 0 -(0/20) -(0/10) -(0/3) -(0/3) - -一般范围 0 -(8/12) -(3/4) -(1/2) -(1/2) -(30/40) -(40/50)熔炼HT200铸铁所用的冲天炉,经实际测定,熔炼过程中元素的变化为:Si –15%; Mn -20%; S +50%。
铸造配料计算
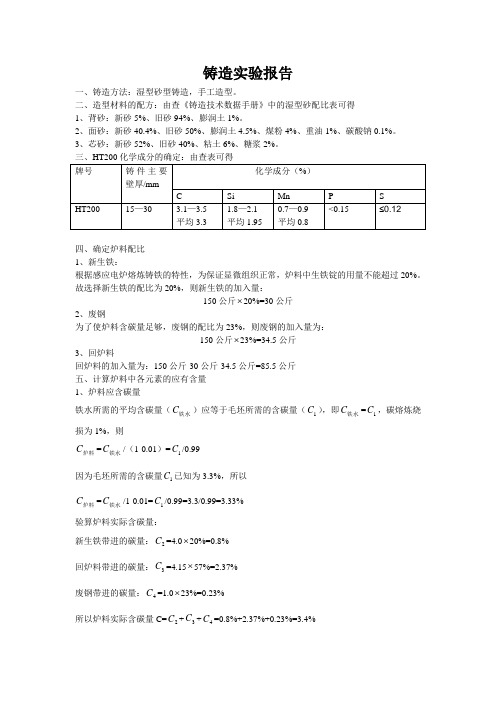
铸造实验报告一、铸造方法:湿型砂型铸造,手工造型。
二、造型材料的配方:由查《铸造技术数据手册》中的湿型砂配比表可得 1、背砂:新砂5%、旧砂94%、膨润土1%。
2、面砂:新砂40.4%、旧砂50%、膨润土4.5%、煤粉4%、重油1%、碳酸钠0.1%。
3、芯砂:新砂52%、旧砂40%、粘土6%、糖浆2%。
四、确定炉料配比 1、新生铁:根据感应电炉熔炼铸铁的特性,为保证显微组织正常,炉料中生铁锭的用量不能超过20%。
故选择新生铁的配比为20%,则新生铁的加入量:150公斤⨯20%=30公斤2、废钢为了使炉料含碳量足够,废钢的配比为23%,则废钢的加入量为:150公斤⨯23%=34.5公斤3、回炉料回炉料的加入量为:150公斤-30公斤-34.5公斤=85.5公斤 五、计算炉料中各元素的应有含量 1、炉料应含碳量铁水所需的平均含碳量(铁水C )应等于毛坯所需的含碳量(1C ),即铁水C =1C ,碳熔炼烧损为1%,则炉料C =铁水C /(1-0.01)=1C /0.99因为毛坯所需的含碳量1C 已知为3.3%,所以炉料C =铁水C /1-0.01=1C /0.99=3.3/0.99=3.33%验算炉料实际含碳量:新生铁带进的碳量:2C =4.0⨯20%=0.8% 回炉料带进的碳量:3C =4.15⨯57%=2.37% 废钢带进的碳量:4C =1.0⨯23%=0.23%所以炉料实际含碳量C=2C +3C +4C =0.8%+2.37%+0.23%=3.4%2、炉料应含硅量:铁水所需的平均含硅量(铁水Si )应等于毛坯所需的含硅量(1Si ),即铁水Si =1Si ,硅熔炼烧损为6%,则炉料Si =铁水Si /(1-0.06)=1Si /0.94因为毛坯所需的含硅量1Si 已知为1.95%,所以炉料Si =铁水Si /(1-0.06)=1Si /0.94=1.95/0.94=2.07%验算炉料实际含硅量:新生铁带进的含硅量:2Si =1.85%⨯20%=0.37% 回炉料带进的含硅量:3Si =1.5%⨯57%=0.855% 废钢带进的含硅量:4Si =0.26%⨯23%=0.05%所以炉料实际含硅量Si =2Si +3Si +4Si =0.37%+0.855%+0.06%=1.285% 炉料中尚缺硅量=炉料应含硅量-炉料中实际含硅量=2.07%-1.285%=0.785% 3、炉料应含锰量铁水所需的平均含锰量(铁水Mn )应等于毛坯所需的含锰量(1Mn ),即铁水Mn =1Mn ,锰熔炼烧损为8%,则因为毛坯所需的含锰量1Mn 已知为0.8%,所以炉料Mn =铁水Mn /(1-0.08)=0.8//0.92=0.87%验算炉料实际含锰量:新生铁带进的锰量:2Mn =0.03%⨯20%=0.006% 回炉料带进的锰量:3Mn =0.7%⨯57%=0.399% 废钢带进的锰量:4Mn =0.25%⨯23%=0.058%所以炉料中实际含锰量Mn =2Mn +3Mn +4Mn =0.006%+0.399%+0.058%=0.463%炉料中尚缺锰量=炉料应含锰量-炉料实际含锰量=0.87%-0.463%=0.407% 六、计算铁合金加入量 1、硅铁加入量补加含硅75%的硅铁的百分数=炉料中尚缺的硅量(%)/硅铁的含硅量(%)=0.785/75%=1.05% 即每100公斤炉料补加1.05公斤含硅75%的硅铁 则150公斤炉料补加含硅75%的硅铁量为: 1.5⨯1.05公斤=1.57公斤2、锰铁加入量补加含锰65%的锰铁的百分数=炉料中尚缺的锰铁(%)/锰铁的含量(%)=0.407%/65%=0.626%即每100公斤炉料补加0.626公斤含锰65%锰铁则则150公斤炉料补加含锰65的锰铁量为:1.5 0.626公斤=0.939公斤。
风力发电铸件的生产工艺

风力发电铸件的生产工艺风力发电的铸件包括叶片轮毂、齿轮箱、夹紧法兰和轴承座等,重量有的8-9t、3-4t,小的200-300kg,壁厚90~150mm,材质为QT400—18AL。
本文根据工厂的生产实况,对夹紧法兰和轴承座生产工艺作简要介绍。
1.化学成分及球化处理设计化学成分的原则是高碳、中硅、低锰、低磷和低硫,在力学性能达到的情况下,尽量不加入其它合金,炉料中带来的合金元素(在这里应看做杂质)之总量越低越好。
铸件重量大,壁厚,选用钇基重稀土球化剂。
炉料中首选低磷、低硫、低锰的Q10或Q12生铁,废钢为优质A3或槽钢、工字钢等,表1是化学成分的控制范围。
正常配料为:生铁Q10(C14.2 Si0.94)58%,废钢(C0.25 Si0.4)22%,回炉料(C3.5 Si2.1)20%,当温度达到1450℃~1460℃时,炉前用快速分析仪测定C E、C和Si,并根据实测情况加以调整。
出炉温度≥1480℃~1510℃,球化处理:钇基重稀土球化剂,用量1.5%。
一次孕育处理为75Si-Fe 0.5%~0.6%,在孕育剂上盖干净铁屑、覆盖剂和铁板,适当紧实。
当包内金属液达到容量的1/2时,进行二次孕育:Si-Ca-Ba0.2%,SiC0.2%,Y2重烯土孕育剂0.2%和增碳剂0.1%,随金属流冲入包内,粒度3~5mm。
三次孕育是用重稀土孕育剂Y4 0.2%,Si-Fe 0.1%,浇注时在浇口池随流孕育,粒度1.0mm。
为了更好地球化处理和增加石墨核心,在球化前做预处理,金属液首先在浇包的另一侧冲入预先置入的Si-Ba合金(0.2%~0.3%)和小苏打粉(0.3%)。
这对球化处理效果和铸件性能的提高大有裨益,处理过程如图1所示。
图1.铁液的予处理及球化孕育工艺浇包为细高状,H/D≥1.3。
包壁用耐火砖砌筑。
用前烘烤至400℃。
采用低温快速浇注。
浇注温度1290℃~1310℃。
浇注为大流量,15~45 kg/s。
铸造生产过程质量控制点

铸造生产过程质量控制点一、原料检验原料检验是确保产品质量的第一步,主要包括铸造用沙、金属材料和添加剂等的检验。
1.铸造用沙的检验:包括沙粒度检测、含水率检测、化学成分和矿物组成检测等。
沙粒度应符合设计要求,含水率应控制在一定范围内,化学成分和矿物组成应符合标准。
2.金属材料的检验:包括铁水、铝水、铜液等金属的化学成分检测、包括有害杂质的检测等。
金属的化学成分应符合设计要求,有害杂质应控制在合理范围内。
3.添加剂的检验:包括炭素稳定剂、铁矿粉、红土等添加剂的化学成分检测、水分检测等。
添加剂的化学成分应符合标准要求,水分应控制在合理范围内。
二、铸型制备铸型制备是铸造过程中至关重要的环节,主要包括模具制备和芯制备两个方面。
1.模具制备:模具制备的关键是模具材料的选择和加工工艺的控制。
模具材料应具有足够的强度和韧性,并且耐用性好。
加工工艺应控制模具尺寸的精度和表面质量,以及模腔的几何形状和位置精度。
2.芯制备:芯的制备需要控制芯盒尺寸的精度、芯材的化学成分和物理性能、芯粘结剂的配比和固化工艺等。
芯盒尺寸的精度直接影响最终铸件的尺寸精度,芯材的物理性能与化学成分直接关系到芯的强度和稳定性,芯粘结剂的配比和固化工艺决定芯的强度和表面质量。
三、铸造操作铸造操作是铸造生产中最关键的环节,主要包括浇注、冒口设置、冷却措施和除渣等。
1.浇注:控制浇注的速度、浇注的位置和浇注的角度等,以防止铸件内部出现夹渣、气孔等缺陷。
2.冒口设置:合理设置冒口位置和数量,以利于铸件内部的气体和夹渣排除,防止缩孔、砂眼等缺陷的产生。
3.冷却措施:采取适当的冷却措施,控制最终铸件的显微组织和性能。
包括调整浇注温度、铸件的冷却速率和冷却时间等。
4.除渣:及时清除铸件上的渣滓,防止渣滓对铸件品质的影响。
四、冷却处理冷却处理是铸件的重要环节,主要包括冷却速率、冷却时间和冷却介质等控制。
1.冷却速率:控制铸件的冷却速率,会影响到铸件的显微组织和力学性能。
- 1、下载文档前请自行甄别文档内容的完整性,平台不提供额外的编辑、内容补充、找答案等附加服务。
- 2、"仅部分预览"的文档,不可在线预览部分如存在完整性等问题,可反馈申请退款(可完整预览的文档不适用该条件!)。
- 3、如文档侵犯您的权益,请联系客服反馈,我们会尽快为您处理(人工客服工作时间:9:00-18:30)。
铸件化学成分的控制与配料河南省驻马店市解放路282号四号楼杨群收影响铸铁、铸钢件组织和性能的因素,有化学成分、孕育(变质)处理、冷却速度、炉料的“遗传性”、铁水过热温度等,在这几个因素中,化学成分含量的高低对铸件物理性能的影响相对更大些,而且是第一因素。
所以在生产过程中,根据铸件物理性能的要求,正确的配料或调料,严格控制材质的各化学成分含量尤为重要。
在生产实践中,作为冶炼技术人员和炉工来说,配料和调料应该是熟练掌握的一般性技术问题。
但是对予刚毕业的学生和大多数炉工来说,欲能系统、灵活的掌握,也确非易事。
要想控制铸件的化学成分与配料,必须事先了解以下几下问题:1、铸件的目标化学成分。
2、库存各种金属炉料的化学成分。
3、各种炉料在冶炼过程中化学成分的增减变化率。
4、配料方法。
一、目标化学成分现在大部分铸件,根据其牌号要求的不同,国标中已做出了相应的要求,从铸造手册中即可查到。
但是随着科技的进步,根据铸件的服役状况,市场需要更多物理性能各不相同的铸件,并对铸件的综合性能质量提出了更高的要求,科研单位也不断研究出新材质而取代旧材质,例如合肥水泥研究设计院研究的“中碳多元合金钢”,成功的代替了原需进口的球磨机衬板,代替了高锰钢,用该材质生产直径φ2.4甚至直径φ4.2的中大型球磨机衬板上,降低了生产成本,取得了良好的经济效益。
另外,如我厂生产出口国外石油钻井用的泥浆泵高铬双金属缸套及采石场600×900破碎机用的锤头,都是超高铬铸铁,其主要成分见表(一),这些材质的详细化学成分要求,在铸造手册中是查不到的。
表一:在接受生产绪如上述产品时,如果自己没有完全掌握铸件化学成分要求,以及没有详细了解铸件的服役状况时,应让用户提供尽可能详细的化学成分要求范围及热处理工艺。
当然作为生产厂家来说,必须尽多详细掌握自己产品所要求的化学成分范围及物理性能。
以便生产出用户满意的优质产品。
总之在生产配料之前,应了解所产铸件的目标化学成分,做到心中有数。
二、原材料的化学成分原材料的化学成分,指的是投炉所用的新生铁、废钢、回炉料的主要化学成分,以及硅铁、锰铁等铁合金的牌号或化学成分含量。
三、在冶炼过程中化学成分的增减变化要想掌握各种炉料在冶炼过程中化学成分的变化规律,将是一个较为复杂的问题。
冶炼设备的不同,如冲天炉(热、冷风)三节炉,中频感应电炉等,其化学成分的变化都各不相同。
即便是同一个炉子,因修炉所用材料的不同,以及操作方法的不同,冶炼过程中化学成分的变化也不相同。
以冲天炉为例,热风与冷风,风压的高低,风眼直径的大小,焦碳质量及块度的大小,修炉衬材料是酸性,中性或是碱性,对材质化学成分的变化都不尽相同。
1、碳量的变化碳量的变化大体上可分为四种:(1)炉料中含碳量高低的不同,碳量的增减率不同。
(2)炉料中硅、锰含量高低对碳量的影响。
(3)炉温高低和炉气氧化性强弱对碳量的影响。
(4)其它因素。
(1)炉料的平均含碳愈低,碳向金属中的溶解度愈大,铁水就会发生增碳,废钢用量越大,这种现象越明显。
炉料中平均含碳量愈高(例如在3.6%以上),铁水从焦炭中吸收碳量愈少,而碳的氧化烧损增加,铁水含碳量不仅不增加反而减少。
如果炉料中的含碳量高达3.6~3.8%时,冶炼中铁水的含碳量就基本不再变化了。
(2)铁水中含硅量越高,增碳量越少,这是因为硅可以溶解于铁内,降低了碳在铁中的溶解度。
锰则相反,含锰量增加时,铁水增碳量也有所增加。
(3)加大焦炭用量,或者使用的焦炭块度小,都会使增碳量加大,这是由于增加了铁水与焦炭的接触时间和接触面积。
铁料熔化成铁水滴下落,当流经赤热的底焦时,焦炭中的碳会慢慢溶到铁水滴中去,使铁水含碳量增加,这叫作增碳作用。
这种作用主要发生在过热区和炉缸区。
铁水与焦炭接触的时间越长,接触面积越大,温度越高,铁水增碳就越多。
冲天炉设有前炉,因为铁水能及时从炉缸中流入前炉,所以增碳较少。
搀炉无前炉缸,铁水只能存在炉锅内而与焦炭接触的机率多,所以增碳量就越较大。
炉内温度升高会促使碳更快更多地溶解在铁水中,使增碳显著。
因此,如果其它条件不变而采用热风冲天炉,就会因为提高了炉内温度,使增碳量加大。
在炉内还存在着使碳减少的因素,如铁水滴接近风口,或者风量很大,风压很高时,炉气中的氧会氧化铁水而使含碳量减少(或称脱碳)。
增加风量,提高铁水温度,也会促使增碳。
但是增加风量后,由于加强了铁水氧化,又有促使脱碳的作用,不过,在这种状态下,脱碳作用大于增碳作用。
(4)除以上因素之外,还有其它具体因素也影响着碳量。
提高底焦高度,铁水的过热路程延长,铁水温度提高的同时,也促使了碳向铁水中的溶解。
因此,底焦高度过高时,铸铁的增碳量也大。
如果炉底高度垫的高,铁水下落流经的路程短,铁水及时流入前炉缸,减少了与焦炭的接触时间,增碳率就小。
反之增碳量就大。
炉料过碎小而且配用量大时,易出现熔化速度快、铁水下落快、增碳量很小的现象。
伴随着这种现象的同时,铸铁件也易出现白口缺陷。
在用冲天炉冶炼时,增碳和减碳这两个矛盾着过程,是同时进行的,影响含碳量的因素太多,很难精密的确定。
用中频感应电炉冶炼时,无论是酸性、中性、或者是碱性炉,对碳量均有烧损。
如果操作不当,碳量的烧损更大,当炉温达到浇注温度时,应及时降低功率,保温浇注。
金属液在炉内随着高温时间的延长,碳的烧损量增大,自发晶核减少,应添加增碳剂并加入接力脱氧剂。
2、硅量的变化硅量的变化,主要取决于两个因素,(1)炉衬的属性(酸性、中性或碱性)。
(2)炉温的高低以及在炉内的停留时间。
用石英砂(SiO2)作修炉料,即用酸性炉冶炼钢铁时。
硅量的烧损不明显,如果颗粒细小的石英砂或石英粉用量大时,硅量不但不减少,反而会增加。
用镁砂(碱性)或铝钒土(中性)修炉衬时,硅的烧损量就大,其烧损率一般可按10—15%计算,硅铁合金中硅的烧损率还要更高一些。
3、锰量的烧损无论在任何炉中冶炼,锰量均有烧损,炉温越高,金属液在炉中的停留时间越长,铁水含硫量越高,锰的烧损率就越高,其烧损率一般按15—25%计算,锰铁合金中锰的烧损率还要更高一些。
在冶炼过程中,除铜、钼等元素烧损量极少,在配料时可以不考虑其烧损率,其它元素都有不同程度的烧损。
四、配料配料前在选择原材料时,即要照顾到铸件的质量要求,还要注意到各材料的价格,以及库存量,尽可能多的利用本厂的回炉料、废钢、废杂铁,以降低库存积压和降低铸件的生产成本。
配料方法及工式,除碳的配料计算方法是两个以上外,其它元素的配比计算方法,均是累积法。
1、碳的计算工式一、C=1.8%+CL 2式中C——铁水的含碳量(%)C L——炉料中的平均含碳量(%)1.8%——在用冲天炉冶炼时,炉料经预热、熔化、过热、还原过程中,脱碳量和增碳量的(估算)中间值。
该式只适应用于冲天炉碳量的计算,不适用于电炉配料的计算,且为了计算结果符合本单位设备的冶炼情况,1.8%系数须根据多次熔炼经验的修正选取。
例如:HT250牌号灰铸铁的含碳量为3.1—3.4%,所用新生铁的含碳量3.8%,回炉料的含碳量3.2%,废钢的含碳量0.4%。
估算配比,新生铁加入量40%,回炉料加入量35%,废钢加入量25%。
C=1.8%+3.8×0.4+3.2×0.35+0.4×0.25×100%2=3.17%2、累积计算法就是将按比例投入的各种炉料,各自代入成分的量,相加在一起,把冶炼过程中的增减率计算在其中,再调整到目标成分的范围,该计算方法适应于冲天炉的配料,也适应于电炉的配料。
使用原材料的化学成分含量如表二所示:表二用上述原材料并配用硅铁75#、锰铁65#,用冲天炉生产HT200牌号的灰铸铁,其化学成分要求如表三所示。
表三:根据实践经验应考虑到,增碳率为10%,炉料中硅的烧损为15%,硅铁中硅的烧损为20%。
炉料中锰的烧损为20%,锰铁中锰的烧损为25%。
经调整后材料配比如表四所示:表四累积代入的成分:碳C=(3.5%×0.45+3.2%×0.4+0.4%×0.15)×1.1(增碳率)≈3.2%硅Si=1.8%×0.45%+1.9%×0.4+-0.27%×0.15)×(1-0.15)(烧损率)≈1.37%锰Mn=(0.7% ×0.45+0.8%×0.4+0.5%×0.15)(烧损率)≈0.568%当然每次配料,不可能一次配料计算成功,需多次调整配料比,方能达到理想,对于初掌握者来说,尤其是这样。
3、碳的计算方法三,列方程式该配料方法的优点是,在掌握了冲天炉增碳率之后,可一次配料成功,不需要试调配几次。
原材料的化学成分含量如表二所示;铸件材质HT200,各化学成分要求范围如表三所示;冲天炉增碳率为10%。
先确定回炉料的加入量为40%,回炉料代入碳:3.2%×0.4=1.28%总入炉料应代入碳(即未增碳10%以前的量):3.2%(要求碳量中线)≈2.91%1+10%(增碳量)生铁和废钢共需代入碳:2.91%-1.28%=1.63%列方程式:设生铁加入量为 x3.5%(生铁含碳量)×x+0.4%(废钢含碳量)×[(1-40%)-x]=1.63% x=45%废钢加入量:(1-40%)-45%=15%以上配料,碳达到了预期目的,但硅、锰仍达不到要求,需要补加硅铁和锰铁,补加硅铁、锰铁及其它任何铁合金,均可用下式求得。
×100%补加量(%)=要求%合金含量%×收得率%目标中线硅含量是1.95%,炉料中代入硅是1.37%,还差0.58%的硅量,需要添加硅铁来补充其差,硅铁的需补加量即可用上式算出。
硅铁75#补加量(%)=0.58%×100%75%×0.8≈1%目标中线锰含量应是0.8%,炉料代入的锰是0.568%,还差0.232的锰量,需添加锰铁来补充。
×100%锰铁65#补加量(%)=0.232%65%×0.75≈0.5%在生产普通铸铁或者普通钢时,掌握了以上方法基本可以指导生产了,但是,在生产合金钢,特别是高合金钢时,还要考虑到,为保证材质有足够的合金成分含量,在添加铁合金时,随之而代入的其它成分,另外还要考虑到如何降低生产成本。
例如用电炉生产合肥水泥研究设计院研究的“中碳多元合金钢”时。
中碳多元合金钢的主要化学成分含量如表一所示,常用的铬铁化学成分如下表所示:在配料过程中,铬含量取中线5%,就需要加入上表两类铬铁共计8%(因为低碳铬铁和高碳铬铁的含铬量接近,所以先混在一起计算其加入量),才能接近中线要求。
由于铬铁中含有一定量的碳和硅,加入8%铬铁的同时,势必引起碳和硅的增加。