主轴组件
《机械制造装备设计》2版 习题思考题解答 第3章 主轴组件设计

第3章主轴组件设计3.1 主轴组件的基本要求是什么?它们对加工精度有何影响?答:1) 旋转精度: 瞬时旋转中心线相对于理想旋转中心线在空间位置上的偏差,,其范围就为主轴的旋转精度,主轴组件的旋转精度是指专机在空载低速转动时,在主轴前端定位面上的测得的径向圆跳动、端面圆跳动和轴向窜动值的大小。
2) 静刚度: 是指在外加载荷作用下抵抗变形的能力。
3) 抗振性: 是指机器工作时主轴组件抵抗振动、保持主轴平稳运转的能力。
4) 热变形: 是指机器工作时,因各相对运动处的摩擦和搅油等耗损而发热造成的温差,使主轴组件在形状和位置上产生的畸变。
5) 耐磨性: 是指长期地保持其原始制造精度的能力,即精度的保持性。
由于各类机械装备的工艺特点的不同,主轴组件所传递的转速、承受的工作载荷等工作条件各异,故对主轴组件的要求也各有侧重,决不能强求一律。
3.2 主轴的轴向定位有几种?各有什么特点,适用何种场合?答:主轴的轴向定位,主要由推力轴承来实现。
推力轴承的配置型式有三种:1) 前端定位推力轴承安排在前支承处。
主轴发热后向后伸长,轴前端的轴向精度较高,但前支承结构复杂(表序号1、2和5)。
2) 后端定位推力轴承安排在后支承处。
主轴受热后向前伸长,影响轴前端的轴向位置精度和刚度,但这种结构便于轴承间隙调整(表序号3).3) 两端定位推力轴承分别安排在前后支承处。
支承结构简单,发热量小,但主轴受热,产生变形,会改变轴承间隙,影响主轴的旋转精度(表序号4、7和8)。
3.3 选择主轴材料的依据是什么?答:主轴材料的选择应根据耐磨性和热处理后变形的大小等来考虑。
因此,无需从强度、刚度角度来考虑主轴材料的选择。
3.4 为什么数控车床的前轴承常采用三联轴承组合,如何布置?为什么?答:如图所示。
数控车床主轴的前支承常采用三联轴承组合安装,即前两轴承为同向组合,接触线朝前(大口朝外),后轴承与之背靠背(反装),则支承点应在前面第一个轴承的接触线与轴线交点处,这样可以增加主轴的前支承支承宽度,缩短主轴前端悬伸量a。
数控机床模块化维修之主轴组件及故障
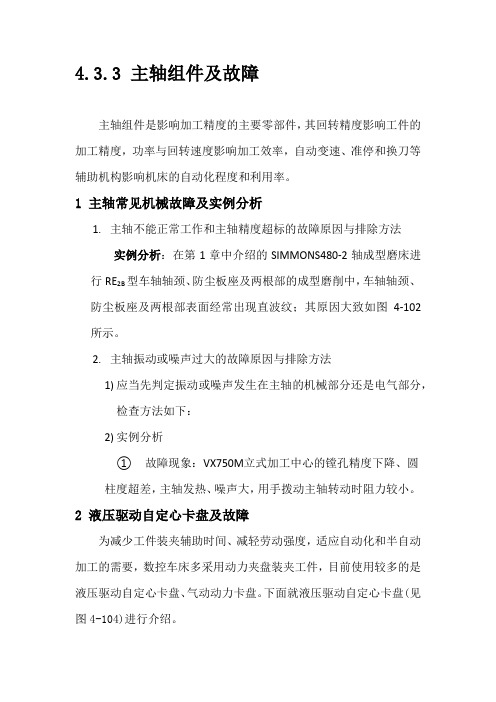
4.3.3 主轴组件及故障主轴组件是影响加工精度的主要零部件,其回转精度影响工件的加工精度,功率与回转速度影响加工效率,自动变速、准停和换刀等辅助机构影响机床的自动化程度和利用率。
1 主轴常见机械故障及实例分析1.主轴不能正常工作和主轴精度超标的故障原因与排除方法实例分析:在第1章中介绍的SIMMONS480-2轴成型磨床进行RE2B型车轴轴颈、防尘板座及两根部的成型磨削中,车轴轴颈、防尘板座及两根部表面经常出现直波纹;其原因大致如图4-102所示。
2.主轴振动或噪声过大的故障原因与排除方法1)应当先判定振动或噪声发生在主轴的机械部分还是电气部分,检查方法如下:2)实例分析①故障现象:VX750M立式加工中心的镗孔精度下降、圆柱度超差,主轴发热、噪声大,用手拨动主轴转动时阻力较小。
2 液压驱动自定心卡盘及故障为减少工件装夹辅助时间、减轻劳动强度,适应自动化和半自动加工的需要,数控车床多采用动力夹盘装夹工件,目前使用较多的是液压驱动自定心卡盘、气动动力卡盘。
下面就液压驱动自定心卡盘(见图4-104)进行介绍。
数控车床使用液压驱动自定心卡盘时,由于油管泄露、电磁换向阀阻滞或油泵损坏等机械故障,常导致液压卡盘动作不正常、甚至不动作。
除此之外还得现场分析(在线跟踪)图4-106的PMC梯形图中有关卡盘动作的信号逻辑关系:卡盘夹紧/松开指令是否输入PMC内部继电器R、保持型继电器K是否接通定时器的接通条件是否满足电磁阀线圈是否得电液压管路是否通畅电磁阀或回转液压缸等不良(手动状态时还得考虑到位检测开关)最终以“AL1006 CHUCK NOT OK”等报警呈现在LCD屏幕上。
3 液压尾座及故障为装夹具有一定长度的轴类零件,保证工件的表面加工质量,卧式数控车床出厂时一般配置标准尾座(见图4-107)。
数控车床使用液压尾座时,由于油管泄露、电磁换向阀阻滞或油泵损坏等机械故障,常导致液压尾座动作不正常、甚至不动作。
lzc7第四篇三章主轴组件
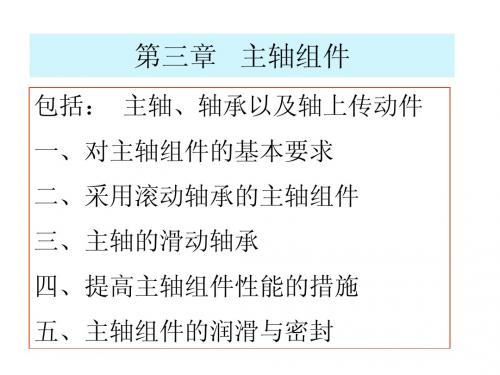
影响因素:
主轴、轴承、箱体孔的制造、装配和调整, 转速、支承设计,润滑剂,动平衡等
二、静刚度
静刚度:(刚度) 主轴组件抵抗静态外载荷变形的能力。 弯曲刚度K: 使主轴前端产生单位位移时,组位移方 向测量处所需施加的力。 即:K = F/δ (N/µm) ) 影响因素: 影响因素: 主轴尺寸形状 轴承型号数量 支承间距 传动件的布置方式 主轴前端悬伸量
车 床 主 轴 端 部
扭 定 矩 传 递 : 前 端 双 键 杆 从 后 端 拉 紧 孔 : 锥 位
铣 床 和 加 工 中 心 端 部
拉
7:24 7:24
短 锥 定 位 反 向 螺 母 锁 紧
外 圆 磨 床 主 轴 端 部
内圆磨床主轴 莫氏锥孔定位砂轮接杆并传递扭矩, 锥孔底部螺孔紧固接杆。
•
1.刚性支承、弹性主轴
L RB RA F a
δs
主轴前端受载F后,其挠度为: δs=( F a3 / 3 E I )(L/ a + 1 ) 柔度为:δs/ F=(a3 / 3 E I)(L/ a + 1 )
2. 刚性主轴、弹性支承
δk
RA
近似为线性变形 前后支承变形分别为δA 和 δB : δA =R A/KA δB =R B /K B 由于支承变形导致的主轴前端位移: δz =F/KA[(1+KA/KB)(a2/L2)+2a/L+1]
主轴结构之一:高刚度型
机床主轴结构之二:高速型
采用圆锥滚子轴承的主轴结构
多刀半自动车床主轴组件
磨床主轴
磨床主轴单元
内圆磨床主轴组件
第三节 主轴的滑动轴承
• 滑动轴承优点: 阻尼性能好 抗振性能好 • 分类: 液体滑动轴承 气体滑动轴承 支承刚度高 运动平稳 动压轴承 静压轴承
数控机床设计4主轴组件设计
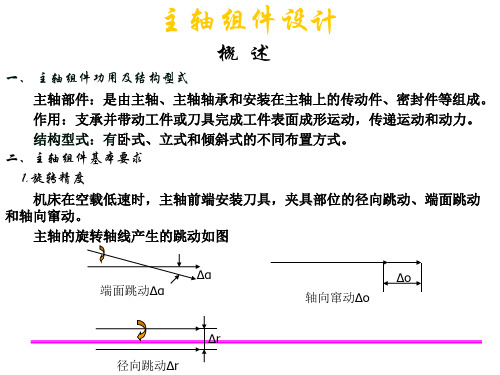
采用合理的轴承选配法,可在制造精度并非很高的情况下,也能使主轴组 件获得较高的旋转精度。
2)后轴承选配
对主轴组件前轴承选配之后再对后轴承选配,还可进一步提高主轴组件的 旋转精度。
把后轴承如同前轴承那样选配,可得到较小的轴端的偏心量。
综上所述,为了提高主轴组件的旋转精度,采用轴承选配法的几点结论是: (1)首先对前轴承进行选配(高点导向),使其偏心量δ A为最小。
常用中碳结构钢:优质结构钢,45。 合金结构钢,40Cr, 50Mn, 65Mn. 球墨铸铁也开始应用。 (2)热处理方法:滑动轴承支承,前端定位表面,淬硬HRC50~55; 低碳钢,渗碳淬火;合金可以化学处理。
三、主轴的技术条件 主轴的精度是根据机床的精度来提出技术要求,主轴的精度是:尺寸精 度,形状精度,以及支承轴颈与壳心表面之间的位置精度和光洁度。 支承轴颈为主轴基准,是工艺基准和测量基准,技术条件可以根据机床 手册和同等精度机床主轴图纸上的条件确定。
可用于要求不高的中速、普通精度机床的主轴(卧式车床、多刀车床、立式铣 床等)。
3)两端定位
两端定位结构其特点:
(1)支承结构简单,间隙调整方便; (2)主轴受热伸长会改变轴承间隙,
影响轴承的旋转精度及寿命;
(3)刚度和抗振性较差。 适用范围:(1)轴向间隙变化不影响正常工作的机床主轴,如钻床。
(2)支距短的机床主轴,如组合机床。
2 .60°接触角双向推力向心球轴承
这种轴承的优点是制造精度高,
允许转速高,温升较低,抗振性高 于推力球轴承8000型,装配调整简
单,精度稳定可靠。与双列圆柱滚
子轴承相配套,用于承受轴向载荷。 3.单列圆锥滚子轴承 普通单列圆锥滚子轴承(7000型),能同时承受径向和轴向载荷,承载 能力和刚度较高,价格便宜,支承简单,间隙调整方便。可用于中速、中载、 一般精度的主轴组件。
第10章 主轴组件PPT课件

金属切削机床
第三节 主 轴
主轴的结构 主轴材料与热处理方法 主轴技术要求
21
金属切削机床 主轴的结构 为了便于装配和满足轴承、传动件等轴向定位的需 要,主轴一般是阶梯形的轴。 有些主轴是空心的,如车床、铣床、加工中心等的 主轴。中孔用以通过棒料等。 d/D=0.7时,惯性矩下降约24%。为了不致使主轴 的刚度受太大的影响,孔径不宜超过外径的70%。
金属切削机床
a)
b)
常与双列圆柱滚子轴承配套使用
主轴轴承常用 轻系列、特轻系列、超轻系列
15
金属切削机床
主轴滚动轴承的精度 向心轴承: 0、6、5、4、2; 圆锥滚子轴承:0、6x、5、4、2; 推力轴承: 0、6、5、4
SP级和UP级作为补充;
旋转精度,相当于P4级和P2级;
(高)
内外圈的尺寸精度,则相当于P5级和P4级 (低)
轴承的工作精度主要决定于旋转精度
“成套轴承的内圈径向跳动”----Kia “成套轴承的外圈径向跳动”----Kea “轴圈滚道对底面的变动量”---Si(用于推力轴承)16
金属切削机床
表10-3
机床精度等级 前 轴 承
后轴承
普通精度级 精密级 高精度级
P5 或 P4(SP) P5 或 P4(SP)
主轴轴承在最高转速空转、连续运转至热稳态时允许温升为:
ቤተ መጻሕፍቲ ባይዱ
高精度机床 精密机床和数控机床 普通机床
810 ℃ 1520 ℃ 3040 ℃
滚动轴承温度不得超过 滑动轴承温度不得超过
70 ℃ 60 ℃
影响因素:
轴承间隙和预紧力的大小;润滑方式、散热条件等8
金属切削机床 5)耐磨性
长期保持原始精度的能力,即精度的保持性。 磨损后对精度有影响的部位首先是轴承。其次是安 装夹具、刀具或工件的定位面和锥孔, 还有如钻、镗床 的移动式主轴的内、外导向表面。
第10章-7-2 主轴组件的计算
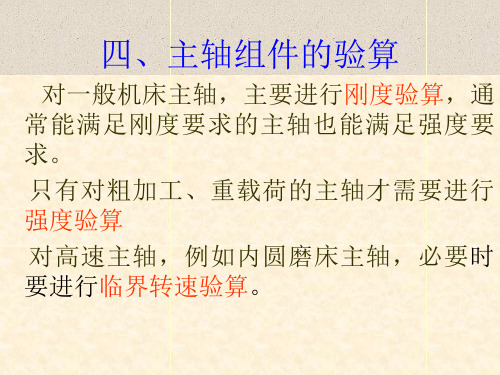
对粗加工机床,要验算传动件处的转角,
对齿轮传动,该齿轮处的主轴转角应满足
cF x rad 4 2 10 b
系数c= 5~15,齿轮宽度b较大或对主轴工
作性能要求较高时取小值, Fx 为齿轮圆周 力,单位为N。
2.主轴组件的扭转刚度验算
对钻床等以扭转变形为主的主轴,还要验
算其扭转刚度。 扭角在(20~25)D的长度内不超过1°
1.主轴组件的弯曲刚度验算
验算内容: 主轴轴端的位移Y
前轴承处的转角θ A。 如果切削力 F 和传动力 Q 不在同一平面内, 应将其分解在相互垂直的两个平面内分别 求出数值,再接向量进行合成,即
y
y
2 H
y
2 V
2 H
2 V
主轴轴端位移的允许值[y]根据机床所பைடு நூலகம்达
到的加工精度来确定 对精加工机床,取主轴轴端径向跳动允许 值的三分之一 对一般机床,取0.0002L,L为支承跨距 前支承处转角的允许值 [ θ A]与轴承类型 有关,可按表3-15选取 或者[θ A]=0.001rad
四、主轴组件的验算
对一般机床主轴,主要进行刚度验算,通
常能满足刚度要求的主轴也能满足强度要 求。 只有对粗加工、重载荷的主轴才需要进行 强度验算 对高速主轴,例如内圆磨床主轴,必要时 要进行临界转速验算。
主轴工作时,在切削力、传动力和支承反
力的作用下, 承受弯矩和转矩的联合作用 除重型机床外,一般不考虑主轴组件和工 件的重量 另外还承受压力(或拉力)作用,但比起 弯矩和转矩来说则小得多,一般忽略不计 但对钻床等轴向力很大的机床,则不能忽 略。
MnL 180 1 GI R
Mn——主轴传递的最大扭矩,单位为N·cm;
第三章 主轴组件设计解析
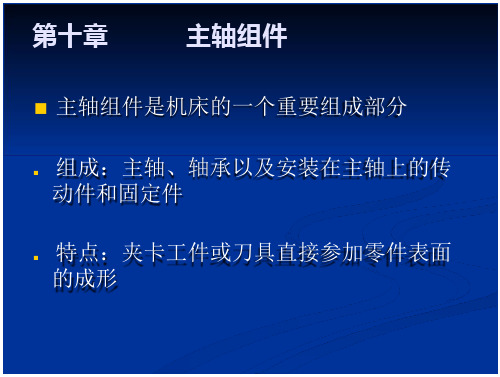
■ δa1、 δa2 可根据δa 计算得到 ■ 同 理 δb1、 δb2 也可根据δb计算得到
■ 一般情况下δ1等于δa1、δb1、δc1的均方根值 ■ δ2等于δa2、δb2、 δc2的均方根值
■ 据此,可算出δc1和δc2
■ 主轴的第⑶项公差就是根据2倍的δc1、 δc2 值
确定的
■ 4、短锥C对轴径A、B的径向圆跳动 ■ 短锥C是卡盘的定心轴颈。精度检验标准规
■ 二、轴承精度
■ 主轴轴承的精度主要采用P2、P4、P5 级
■ (B、C、D)相当于ISO 2、4、5 级
■ 此外,又规定了SP级和UP级作为补充
■ 结构对精度的影响:
■ a、向心轴承用于切削力方向固定的主轴, 对径向旋转精度影响最大的是“成套轴承的 内圈径向跳动” Kia
■ b、如用于切削力方向随主轴旋转而变化的 主轴,对轴承径向旋转精度影响最大的是 “成套轴承的外圈径向跳动” Kea
■ 轴瓦除了径向摆动外,也可轴向摆动
■ 轴瓦与球头螺钉接触面积要大于 80% 以保 证接触刚度
■ 轴承间隙靠螺钉调整 ■ 缺点是综合刚度低于固定多油楔轴承
■ 二、液体静压轴承
■ 静压轴承的油膜压 强由外界液压泵供 给
■ 油膜厚度对轴径和 轴承孔的圆度误差 起均化作用
■ 1、工作原理
■ 如图
■ 2、节流器
■ 型号:NN3000K(3182100) ■ NNU4900K(4382900)
■ 特点:内孔为 1:12 的锥 孔与主轴的锥形轴颈相配 合,只承受径向力
■ 间隙的调整: ■ 轴向移动内圈 ■ 适用场合: ■ 载荷较大、刚度要求较高,
中等转速
■ 2、双向推力角接触球轴承 ■ 型号:234400(2268100) ■ 特点:可承受双向的轴向载荷 ■ 它与双列圆柱滚子轴承配套使用
机床的主轴部件
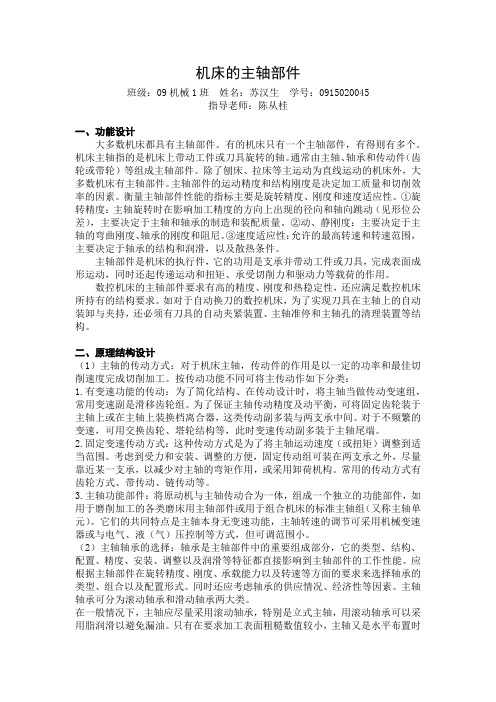
机床的主轴部件班级:09机械1班姓名:苏汉生学号:0915020045指导老师:陈从桂一、功能设计大多数机床都具有主轴部件。
有的机床只有一个主轴部件,有得则有多个。
机床主轴指的是机床上带动工件或刀具旋转的轴。
通常由主轴、轴承和传动件(齿轮或带轮)等组成主轴部件。
除了刨床、拉床等主运动为直线运动的机床外,大多数机床有主轴部件。
主轴部件的运动精度和结构刚度是决定加工质量和切削效率的因素。
衡量主轴部件性能的指标主要是旋转精度、刚度和速度适应性。
①旋转精度:主轴旋转时在影响加工精度的方向上出现的径向和轴向跳动(见形位公差),主要决定于主轴和轴承的制造和装配质量。
②动、静刚度:主要决定于主轴的弯曲刚度、轴承的刚度和阻尼。
③速度适应性:允许的最高转速和转速范围,主要决定于轴承的结构和润滑,以及散热条件。
主轴部件是机床的执行件,它的功用是支承并带动工件或刀具,完成表面成形运动,同时还起传递运动和扭矩、承受切削力和驱动力等载荷的作用。
数控机床的主轴部件要求有高的精度、刚度和热稳定性,还应满足数控机床所持有的结构要求。
如对于自动换刀的数控机床,为了实现刀具在主轴上的自动装卸与夹持,还必须有刀具的自动夹紧装置、主轴准停和主轴孔的清理装置等结构。
二、原理结构设计(1)主轴的传动方式:对于机床主轴,传动件的作用是以一定的功率和最佳切削速度完成切削加工。
按传动功能不同可将主传动作如下分类:1.有变速功能的传动:为了简化结构、在传动设计时,将主轴当做传动变速组,常用变速副是滑移齿轮组。
为了保证主轴传动精度及动平衡,可将固定齿轮装于主轴上或在主轴上装换档离合器,这类传动副多装与两支承中间。
对于不频繁的变速,可用交换齿轮、塔轮结构等,此时变速传动副多装于主轴尾端。
2.固定变速传动方式:这种传动方式是为了将主轴运动速度(或扭矩)调整到适当范围。
考虑到受力和安装、调整的方便,固定传动组可装在两支承之外,尽量靠近某一支承,以减少对主轴的弯矩作用,或采用卸荷机构。
机械制造装备设计介绍第三章主轴组件设计介绍

室温不是20οC时,温升Tt的许可值按下式计算
2021/5/11
T t T 2 0 K tt 2 0
主轴组件设计
主轴组件由主轴及其支承轴承、传动件、定位元 件等组成。
主轴组件是主运动的执行件,是机床重要的组成 部分。它的功用是缩小主运动的传动误差并将运动 传递给工件或刀具进行切削,形成表面成形运动; 承受切削力和传动力等载荷。
主轴组件直接参与切削,其性能影响加工精度和 生产率。因而是决定机床性能和经济性指标的重要 因素。
27
主轴组件设计主轴图
t
A
B
B
t
t1
t3 AB
?t4/300
AB
t2 B
A
t3 AB
t t1
?t4/300
AB
图3-8 车床主轴、箱体轴承孔简图及其技术要求
2021/5/11
28
主轴组件设计 主轴精度
轴承精度 公差名称 直径φ公差
圆度t、圆柱度t1
倾斜度t2 跳动t3 同轴度t4 Ra D、d≤80
10
主轴组件设计 滚动轴承
轴承的刚度与轴承的类型有关,线接触的滚子轴 承比点接触的球轴承刚度高,双列轴承比单列的刚 度高,且刚度是载荷的函数,适当预紧不仅能提高 旋转精度,也能提高刚度。
轴承的极限转速与轴承滚动体的形状有关,同等 尺寸的轴承,球轴承的极限转速高于滚子轴承,圆 柱滚子轴承的极限转速高于圆锥滚子轴承;同一类 型的轴承,滚动体的分布圆越小,滚动体越小,极 限转速越高。
主轴组件图库
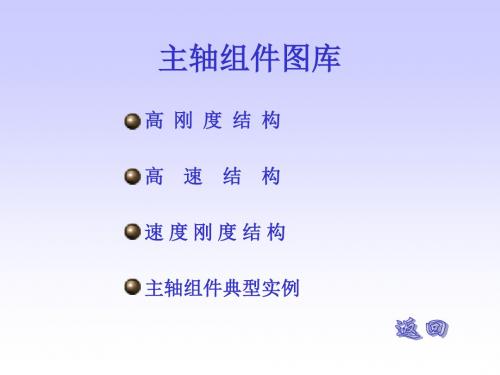
角接触球轴承具有良好的高速性能,但它 的承载能力较小,因而适用于高速轻载或精密 机床,如高速镗削单元、高速CNC车床等。
• 返回
典型高速结构
MNC 300
SKF 1
SS 125
NDM-40
76_300
返回
• MNC 300 该高速CNC车床主轴前后轴承都采用两 联角接触球轴承,具有较高的转速。
速度刚度结构
FNR 140 FNC 200 H2_077 SAG 101 BTA_B
HF2
SDNC 560
TNC 131
TS_15
返回
• FNR 140 返回
• FNC 200 返回
• H2_077
返回
• SAG 101
返回
• BTA_B返回• Fra bibliotekF2返回
• SDNC 560 返回
• TNC 131
主轴组件图库
高刚度结构 高速结构 速度刚度结构 主轴组件典型实例
高刚度结构
• 前支承用双列圆柱滚子轴承承受径向载 荷和60°角接触双列向心推力球轴承承 受轴向载荷,后支承采用双列短圆柱滚 子轴承。
这种轴承配置的主轴部件,适用于
中等转速和切削负载较大,要求刚度高 的机床。如数控车床主轴、镗削主轴单 元等。
返回
• TS_15
返回
机床主轴实例
• 返回
该图为具有一级转速的变速箱展开
图。最下面的轴是电动机轴或运动输入 轴,最上面的轴是机床主轴,主轴的位 置主要由车床的中心高确定。
• 返回
该图是采用圆锥滚子轴承的主轴部件,结 构比采用双列短援助滚子轴承简化,承载能力 和刚度比角接触球轴承高。但是因为圆锥滚子 轴承发热大、温升高,允许的极限转速要低些。 适用于载荷较大、转速不太高的普通精度的机 床主轴。
数控机床的主轴有哪些?
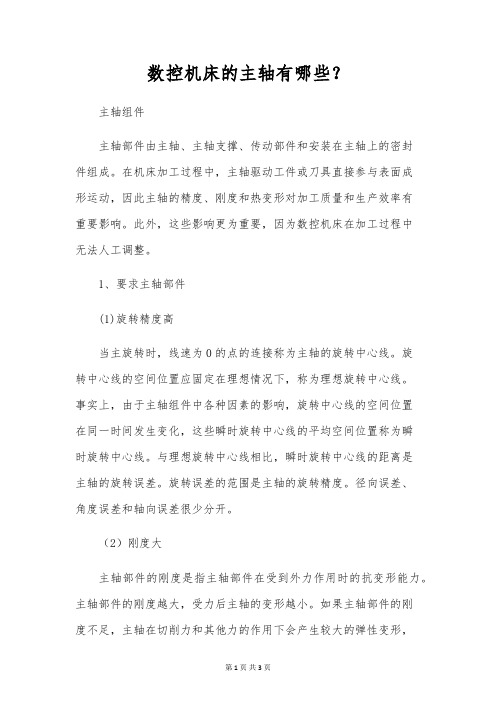
数控机床的主轴有哪些?主轴组件主轴部件由主轴、主轴支撑、传动部件和安装在主轴上的密封件组成。
在机床加工过程中,主轴驱动工件或刀具直接参与表面成形运动,因此主轴的精度、刚度和热变形对加工质量和生产效率有重要影响。
此外,这些影响更为重要,因为数控机床在加工过程中无法人工调整。
1、要求主轴部件(1)旋转精度高当主旋转时,线速为0的点的连接称为主轴的旋转中心线。
旋转中心线的空间位置应固定在理想情况下,称为理想旋转中心线。
事实上,由于主轴组件中各种因素的影响,旋转中心线的空间位置在同一时间发生变化,这些瞬时旋转中心线的平均空间位置称为瞬时旋转中心线。
与理想旋转中心线相比,瞬时旋转中心线的距离是主轴的旋转误差。
旋转误差的范围是主轴的旋转精度。
径向误差、角度误差和轴向误差很少分开。
(2)刚度大主轴部件的刚度是指主轴部件在受到外力作用时的抗变形能力。
主轴部件的刚度越大,受力后主轴的变形越小。
如果主轴部件的刚度不足,主轴在切削力和其他力的作用下会产生较大的弹性变形,这不仅会影响工件的加工质量,还会破坏齿轮和轴承的正面。
正常工作条件,加快磨损,降低精度。
主轴部件的刚度与主轴的结构尺寸、支撑跨度、所选轴承类型及其配置形式、轴承间隙的调整、主轴上传动部件的位置等有关。
抗振能力强(3)主轴组件的抗振能力是指切割时主轴保持稳定运行而不振动的能力。
如果主轴组件抗振能力差,工作时容易产生振动,不仅会降低加工质量,还会限制机床生产率的提高,降低刀具的耐久性。
为了提高主轴的抗振能力,必须提高主轴组件的静刚度。
因此,经常使用阻尼比较大的前轴承,必要时应安装阻尼器,使主轴组件的固有频率远大于激振能力的频率。
(4)温升低主轴组件运行中温升过高会造成两个不良结果:一是主轴组件和箱体因热膨胀而变形,主轴的旋转中心线与机床其他组件的相对位置发生变化,直接影响加工精度;二是轴承等部件会因温度过高而改变调整间隙,破坏正常润滑条件,影响轴承的正常运行,严重时甚至会出现“抱轴”现象。
- 1、下载文档前请自行甄别文档内容的完整性,平台不提供额外的编辑、内容补充、找答案等附加服务。
- 2、"仅部分预览"的文档,不可在线预览部分如存在完整性等问题,可反馈申请退款(可完整预览的文档不适用该条件!)。
- 3、如文档侵犯您的权益,请联系客服反馈,我们会尽快为您处理(人工客服工作时间:9:00-18:30)。
加工中心主轴组件分析报告一、主轴组件概述1.主轴组件定义加工中心主传动系统是由主轴电动机、主轴传动系统以及主轴组件组成,而主轴组件是加工中心的主传动部分的主要组成部分,在机床上,主轴主要作用是夹持工件或刀具旋转,提供足够的驱动功率或输出转矩,能在整个速度范围内提供切削所需功率和转矩,以满足机床强力切削时的要求,直接参加表面成形运动。
(应附图)主轴被比喻为“机床的心脏”,这是再恰当不过了,人们期望它输出更高的转速、更大的扭矩、更强劲的功率、更小的主轴跳动、更低的磨损率、更少的故障及更低的价格。
目前国内机床主轴的水平还未满足用户的要求。
2.国内外主轴现状比较在国外,主轴单元的设计大多是可以公开的,一些大轴承公司甚至公开出版书籍,教人们如何设计适合的主轴单元具体到使用什么轴承、轴承的精度等级、相应的配合公差、形位公差、主轴单元可以达到的精度、润滑方式、润滑油、密封方法、动平衡精度等,有的公司还会介绍如何装配,应在什么环境下装配等。
设计可以公开,但加工工艺就很少见诸文献。
大多数公司对工艺都严守秘密,好多出国考察的人士就反映主轴单元零件的精加工场所,甚至装配场所几乎都不允许参观。
因此很难叙述目前国外的工艺水平,只能从一些间接的现象来评估。
例如有时我们采用相同的设计、相同的材料、用同一轴承公司的型号、精度等级相同的轴承,而做不出相同精度或相同速度的主轴单元来。
对铣削加工中心,主轴跳动在1um已经是国内用户购买高精度机床的一个标淮,这对于国外的机床来说,也已经是一个非常普通的参数,甚至于价位很低的机床,反观我们国内的情况,还没有哪个厂家明确地在产品样本上标明主轴跳动为lum,而实际的情况更糟糕,机床的主轴指标往往是5um。
情况为什么会是这样呢?原因主要的还是主轴的结构设计、加工工艺、热处理工艺、装配工艺的问题。
这个也是以后开发主轴的技术难点。
此处至少应就主轴类技术指标、材料及热处理的差距列表,差距比较是表现技术水平高低的重要形式,必须有数据,国外在主轴方面的发展方向是什么,必须在文中有回答(并提供一些参考资料作为支持)二主轴组件的分类、功能、性能要求以下以铣加工中心作为例子介绍(1)主轴组件的分类:皮带式主轴、直结式主轴、内藏式主轴(电主轴)(应附图)三类主轴使用环境:皮带式主轴广泛用于小型机床上,并能满足机床对转矩特性的要求;直结式主轴虽然简化了主轴结构,有效地提高了主轴刚度,但主轴输出转矩小,电动机发热对主轴精度影响大;内藏式主轴是集皮带式主轴和直结式主轴优点,具有高速度,高精度,以及良好的稳定性能等多项优点,广泛用于数控钻铣设备,精密雕刻、雕铣、木工机械、精密磨床及其他数控高速机械。
三类主轴发展趋势:从当前机床行业看,大多立式加工中心还是采用皮带式主轴,主要满足机床对转矩的要求,直结式的较少,因为电主轴已经有取代直结式主轴的趋势了。
主轴组件功能:1.调速功能为了适应不同工序、各种工件材料及刀具等各切削工艺要求,主轴必须具有一定的调速范围并实现无级变速,以保证加工时选用合理的切削用量,从而获得最佳切削效率、加工精度和表面质量;调速范围的指标主要由各种加工工艺对主轴最低转速和最高转速的要求来确定。
目前加工中心主轴基本实现无级变速。
2.刀具自动夹紧功能加工中心突出的特点是自动换刀功能,为保证加工过程的连续实施,加工中心主轴系统与其他主轴系统相比,必须具有刀具自动夹紧功能。
3.主轴定位功能要求主轴准停功能又称主轴的定位功能,即当主轴停止时,控制主轴停在固定的位置,这是自动换刀所必须的功能。
在自动换刀时,切削转矩通常通过刀杆的端面键来传递的,这就是要求主轴具有准确定位于圆周上的特定角度的功能。
主轴组件主要参数:机床主传动系统的参数有动力和运动参数。
动力参数是指主运动驱动电机的功率,运动参数是指主运动的变速范围。
(1)主传动功率通过查阅搜集的主轴相关资料,主轴功率分以下几种:30(BT30,DIN30,CAT30)锥孔规格的主轴电机功率大部分为3Kw或5Kw;40锥孔规格的主轴电机功率大部分为7.5Kw或11Kw,50锥孔规格的主轴电机功率大部分为15Kw或18.5Kw。
(2)主轴组件的最高转速以下是台湾主轴专业生产厂家的主轴转速范围主要有以下几种:键椿工业股份有限公司、普森精密主轴工业有限公司、矩将科技有限公司、台湾旭泰精密主轴公司:6000rpm 8000rpm 10000rpm 12000rpm;但从上可以看出,现在加工中心机械主轴的转速大部分是6000、8000、10000、12000,在往上走就是电主轴转速范围了。
日本、德国的呢?主轴组件性能要求:(1)回转精度主轴组件的回转精度,是指机床在空载低速旋转时,主轴前端安装工件或刀具部位的径向和轴向跳动值满足要求(其值可参考有关机床精度标准)。
目的是保证加工零件的几何精度和表面粗糙度。
当主轴做回转运动时,线速度为零的点的连线称为主轴的回转中心线。
回转中心线的空间位置,在理想的情况下应是固定不变的。
实际上,由于主轴组件中各种因素的影响,回转中心线的空间位置每一个瞬间多是变化的,这些瞬时回转中心的平均空间位置称为理想回转中心线。
瞬时回转中心线相对于理想回转中心线在空间的位置距离,就是主轴的回转误差,回转误差的范围就是的回转精度。
纯径向误差、角度误差和轴向误差它们很少单独存在。
当径向误差和角度误差同时存在时,构成径向跳动,而轴向误差和角度误差同时存在时构成端面跳动。
在加工过程中这些误差直接影响到工件的表面形状等加工质量。
因此,在设计主轴组件是必须对回转精度加以控制。
一般回转精度指标是多少?(国外,国内?)(2)刚度主轴组件的刚度是指受外力(例如切削力)作用时,主轴组件抵抗变形的能力。
通常以主轴前端产生单位位移量时,在位移方向上所施加的作用力大小来表示。
主轴组件的刚度越大,主轴受力的变形就越小。
主轴组件的刚度不足,在切削力及其他力的作用下,主轴将产生较大的变形,不仅影响工件的加工质量,还会破坏承的正常工作条件,使其加快磨损,降低精度。
可见主轴的刚度直接影响到主轴组件的性能。
主轴部件的刚度与主轴结构尺寸、支承跨距、所选用的轴承类型及配置形式、轴承间隙的调整、主轴上传动元件的位置等有关。
刚度一般采用有限元分析,指标情况如何呢?(3)抗振性主轴组件的抗振性是指切削加工时,主轴保持平稳地运转而不发生振动的能力。
主轴组件抗振性差,工作时容易产生振动,不仅降低加工质量,而且限制了机床生产率的的提高,使刀具耐用度下降。
提高主轴抗振性必须提高主轴组件的静刚度,采用较大的阻尼比的前轴承,以及在必要时安装阻尼消振器。
另外主轴固有频率应远远大于激振力频率。
抗振性如何测定?(4)温升和热变形主轴组件在运转过程中,温升过高会引起两方面的不良结果:一是主轴组件和箱体因热膨胀而变形,主轴的回转中心与机床其他件的相对位置发生变化,直接影响加工精度;其次是轴承等元件会因温度过高而改变已调好的间隙和破坏正常的润滑条件,影响轴承的正常工作。
严重时甚至会发生抱轴现象。
所以要提高主轴组件的性能,必须控制主轴温升。
大部分主轴厂家的控制温升为+10°C、+15°C、+20°C。
国内外有什么差距?国外在控制这个指标方面有什么新的对策和措施?(5)耐磨性主轴组件必须有足够的耐磨性,以便能长期保持精度。
主轴上易磨损的地方是刀具或工件的安装部位以及移动式主轴的工件部位。
为了提高耐磨度,主轴的上述部位应该淬硬,或者经过氮化处理,以提高其硬度增加耐磨性。
主轴轴承也需有良好的润滑,提高其耐磨性。
以上所述各项要求,要综合考虑,例如高刚度与高速,高速与低温升,高速与高精度等方面的矛盾就要具体问题具体分析。
这个指标非常关键和重要,有无具体指标数据方面的资料(国内外对比),包括材料、热处理的特殊手段、新手段?三、主轴产品技术分析1.主轴结构示意图:应附以表现某种型号主轴单元的完整结构图2.主轴组件零件分析一套完整的主轴组件离不开以下零件:端面键、刀柄、拉钉、主轴前端盖、拉杆、拉刀爪、前端轴承、主轴、隔环、主轴套、同步皮带和皮带轮、密封件、蝶形弹簧、拉刀气缸、撞块、行程开关、冷却系统、浮动退刀装置及紧固件。
端面键、刀具、刀柄、拉钉、拉刀爪、轴承、同步皮带和皮带轮、蝶形弹簧、拉刀气缸、行程开关、紧固件已经标准化,所以主轴需要自己独立设计的就只有主轴前端盖、拉杆、主轴、隔环、主轴套、同步带轮内孔和结构可根据需要特制、撞块、冷却系统的布局,浮动退刀装置(其实就是一种卸荷装置,相关资料见附件1)。
(一)标准件:(1)主轴前端有7:24的锥孔,用于装夹BT40刀柄或刀杆,再用拉杆从主轴后端拉紧,主轴端面有一端面键.既可通过它传递刀具的扭矩,又可用于刀具的周向定位.相关标准见GB3837·2—83机床工具7:24圆锥联结主轴端面键。
(2)刀柄:GB10944.1-2006T自动换刀用7:24圆锥工具柄部—40、45和50号柄第1部分尺寸及锥角公差;GB10944.2-2006T自动换刀用7:24 圆锥工具柄部—40、45和50号柄第2部分技术条件;日本BT刀柄标准见B6339-1998。
(3)拉钉:GB10945.1-2006-T自动换刀用7:24 圆锥工具柄部-40、45和50 号柄用拉钉第1部分:尺寸及机械性能GB/T 10945.2-2006自动换刀用7:24圆锥工具柄部第2部分技术条件日本BT拉钉标准见B6339-1998(4)拉刀爪:刀杆尾部的拉紧机构分2大类:四瓣爪和钢球式①四瓣爪②钢球式比较2种拉紧结构,各有优点,但从可靠性方面四瓣爪要强,因为钢球式由于钢球表面很硬,拉刀的力也比较大,受力方式是点接触,如果时间长了很容易将钢球边缘压凹或者将拉钉端部拉坏,而四瓣爪通过面接触,不会出现钢球式那种情况,论成本钢球式当然比四瓣爪便宜,但是在拉紧机构的可靠稳定性方面,四瓣爪比钢球式强很多,现在国内加工中心基本上采用四瓣爪拉紧结构。
(5)轴承:经查阅大量主轴相关资料及前面已介绍,主轴轴承采用的是角接触球轴承或双列圆柱滚子轴承(用于大中型卧式加工中心主轴和强力切削机床主轴),主轴轴承主轴采用轴承的内径为60,65,70(用于BT40型号),80,100(用于BT50型号)mm,台湾几家专业主轴厂家的主轴前轴承采用的德国FAG公司的高精度精密主轴轴承或(NSK)轴承或SKF轴承,且前后轴承精度等级都为P4级。
(6)同步皮带和皮带轮:同步皮带和皮带轮很有采用的是美国盖茨或日本UNITTA公司的精确圆弧齿同步带5GT和圆弧齿同步带8YU,皮带式主轴基本上采用如上同步皮带,相应地也会采用如上的带轮。
(7)蝶形弹簧:德国专业的蝶形弹簧供应商;(8)拉刀气缸:台湾专业的拉刀气缸生产商;(9)行程开关:选用欧姆龙的,作用是提供松刀完成及拉刀完成的信号。