铸件表面清理--喷丸处理.
喷丸处理——精选推荐
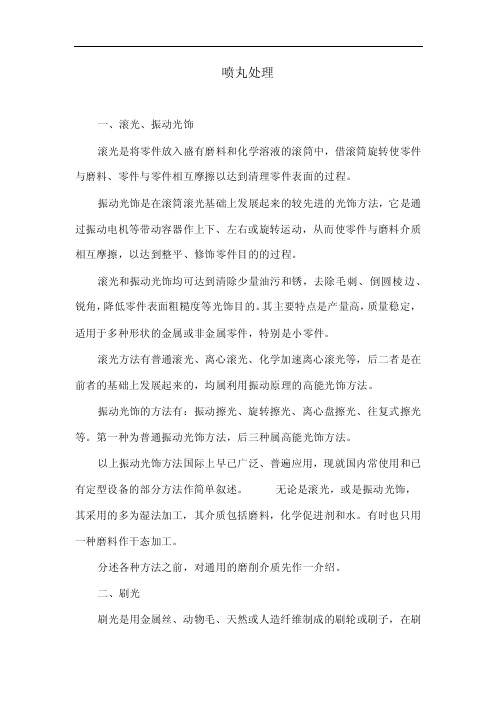
喷丸处理一、滚光、振动光饰滚光是将零件放入盛有磨料和化学溶液的滚筒中,借滚筒旋转使零件与磨料、零件与零件相互摩擦以达到清理零件表面的过程。
振动光饰是在滚筒滚光基础上发展起来的较先进的光饰方法,它是通过振动电机等带动容器作上下、左右或旋转运动,从而使零件与磨料介质相互摩擦,以达到整平、修饰零件目的的过程。
滚光和振动光饰均可达到清除少量油污和锈,去除毛刺、倒圆棱边、锐角,降低零件表面粗糙度等光饰目的。
其主要特点是产量高,质量稳定,适用于多种形状的金属或非金属零件,特别是小零件。
滚光方法有普通滚光、离心滚光、化学加速离心滚光等,后二者是在前者的基础上发展起来的,均属利用振动原理的高能光饰方法。
振动光饰的方法有:振动擦光、旋转擦光、离心盘擦光、往复式擦光等。
第一种为普通振动光饰方法,后三种属高能光饰方法。
以上振动光饰方法国际上早已广泛、普遍应用,现就国内常使用和已有定型设备的部分方法作简单叙述。
无论是滚光,或是振动光饰,其采用的多为湿法加工,其介质包括磨料,化学促进剂和水。
有时也只用一种磨料作干态加工。
分述各种方法之前,对通用的磨削介质先作一介绍。
二、刷光刷光是用金属丝、动物毛、天然或人造纤维制成的刷轮或刷子,在刷光机上或手工对零件表面进行加工的过程。
刷光轮上的弹性金属丝,其端面侧锋具有很好的切刮能力,工作时就是利用这种金属丝侧锋除去金属表面的锈皮、污垢、棱角毛刺等;或对零件基层表面进行装饰性底层加工,如丝纹刷光、缎面修饰等。
刷光可以湿刷,也可以干刷。
刷光不会改变零件的几何形状。
常用的刷轮一般由钢丝、黄铜丝等材料制成。
有时为了特殊的目的,也用其材料。
零件材料较硬时,应选择硬金属丝刷光轮;零件材料较软时,则选用软金属丝或人造纤刷光轮。
刷光轮的旋转速度一般在1200~2800r/min之间。
直径大的刷光轮,应采用较低的转速,硬质材料的零件,应选用较高的转速。
进行湿法刷光时,一般都用水作刷光液,黑色金属的镀前刷光,除用水外,如需去污,则宜采用具有除油功能的清洗剂。
喷丸处理的原理和作用
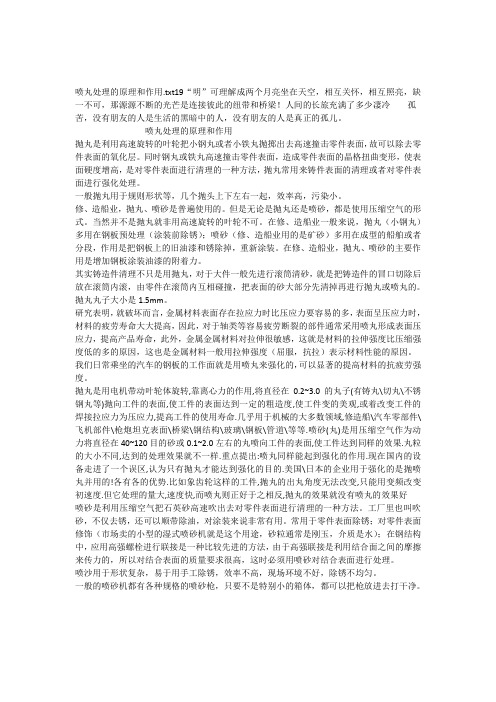
喷丸处理的原理和作用.txt19“明”可理解成两个月亮坐在天空,相互关怀,相互照亮,缺一不可,那源源不断的光芒是连接彼此的纽带和桥梁!人间的长旅充满了多少凄冷孤苦,没有朋友的人是生活的黑暗中的人,没有朋友的人是真正的孤儿。
喷丸处理的原理和作用抛丸是利用高速旋转的叶轮把小钢丸或者小铁丸抛掷出去高速撞击零件表面,故可以除去零件表面的氧化层。
同时钢丸或铁丸高速撞击零件表面,造成零件表面的晶格扭曲变形,使表面硬度增高,是对零件表面进行清理的一种方法,抛丸常用来铸件表面的清理或者对零件表面进行强化处理。
一般抛丸用于规则形状等,几个抛头上下左右一起,效率高,污染小。
修、造船业,抛丸、喷砂是普遍使用的。
但是无论是抛丸还是喷砂,都是使用压缩空气的形式。
当然并不是抛丸就非用高速旋转的叶轮不可。
在修、造船业一般来说,抛丸(小钢丸)多用在钢板预处理(涂装前除锈);喷砂(修、造船业用的是矿砂)多用在成型的船舶或者分段,作用是把钢板上的旧油漆和锈除掉,重新涂装。
在修、造船业,抛丸、喷砂的主要作用是增加钢板涂装油漆的附着力。
其实铸造件清理不只是用抛丸,对于大件一般先进行滚筒清砂,就是把铸造件的冒口切除后放在滚筒内滚,由零件在滚筒内互相碰撞,把表面的砂大部分先清掉再进行抛丸或喷丸的。
抛丸丸子大小是1.5mm。
研究表明,就破坏而言,金属材料表面存在拉应力时比压应力要容易的多,表面呈压应力时,材料的疲劳寿命大大提高,因此,对于轴类等容易疲劳断裂的部件通常采用喷丸形成表面压应力,提高产品寿命,此外,金属金属材料对拉伸很敏感,这就是材料的拉伸强度比压缩强度低的多的原因,这也是金属材料一般用拉伸强度(屈服,抗拉)表示材料性能的原因。
我们日常乘坐的汽车的钢板的工作面就是用喷丸来强化的,可以显著的提高材料的抗疲劳强度。
抛丸是用电机带动叶轮体旋转,靠离心力的作用,将直径在0.2~3.0的丸子(有铸丸\切丸\不锈钢丸等)抛向工件的表面,使工件的表面达到一定的粗造度,使工件变的美观,或着改变工件的焊接拉应力为压应力,提高工件的使用寿命.几乎用于机械的大多数领域,修造船\汽车零部件\飞机部件\枪炮坦克表面\桥梁\钢结构\玻璃\钢板\管道\等等.喷砂(丸)是用压缩空气作为动力将直径在40~120目的砂或0.1~2.0左右的丸喷向工件的表面,使工件达到同样的效果.丸粒的大小不同,达到的处理效果就不一样.重点提出:喷丸同样能起到强化的作用.现在国内的设备走进了一个误区,认为只有抛丸才能达到强化的目的.美国\日本的企业用于强化的是抛喷丸并用的!各有各的优势.比如象齿轮这样的工件,抛丸的出丸角度无法改变,只能用变频改变初速度.但它处理的量大,速度快,而喷丸则正好于之相反,抛丸的效果就没有喷丸的效果好喷砂是利用压缩空气把石英砂高速吹出去对零件表面进行清理的一种方法。
镁合金表面喷丸处理
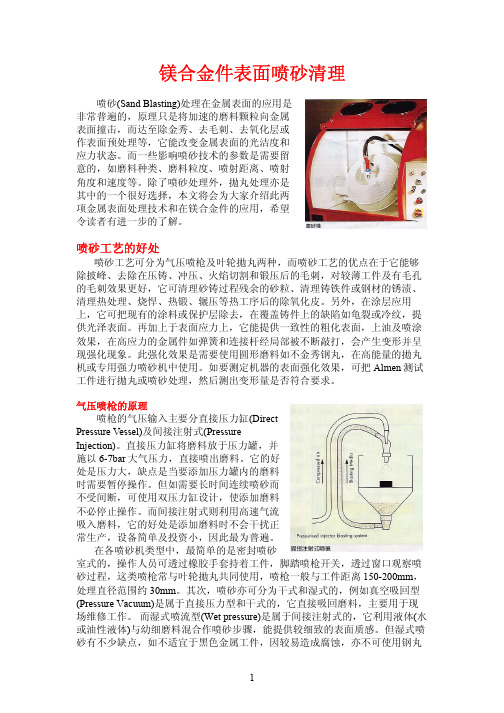
磨料的选择对工件表面效果有决定性的影响。磨料可分为固体或流体(如干 冰、水、油溶液),而固体磨料可分为金属(黑色与有色金属类)与非金属(矿物与 有机合成类),常用的包括: 高碳铸铁丸(Chill Cast Iron Grain)-属于高硬度材料,硬度约 60-68HRC,呈丸 状及砂砾状,直径约为 0.05-2.0mm,主要用于高强度要求的表面清理如去锈、 氧化皮和除涂层等。 低碳钢丸(Cast Steel Shot)-硬度约 55HRC,呈丸状及砂砾状,直径大约 0.052.8mm,它适中的硬度及损耗率,使其应用范围最广。 镍铬不锈钢丸(Rust & Acid Resistant Steel Shot)-主要是丸状,直径约 0.081.2mm,适用于高质量之有色轻金属铸件(除镁合金外)、重金属、贵金属及有色 重金属,能提供均匀及光泽的表面,提高工件抗酸及防锈性能。 锌、铝切丝丸-属于圆柱型的,因制造是从拉伸后再切成丝形,所以材质结构 较稳定,使用一段时间后会变圆,主要用于清理铝、镁、锌合金铸件。 銅铜-砂可用于清理铜铸件,或作电子零件除毛刺用。 氧化铝(Corundum)-因磨损性高的关系,使损耗率亦高。只适合表面粗化或作 喷涂前处理,而由于损耗性太强,只会用于气压喷枪。 陶瓷/玻璃砂(Ceramic/glass)-有丸状及砂砾状,直径约为 0.03-0.6mm,它可提 高工件的抗酸及防锈性能,而陶瓷多用于拋丸而玻璃砂多用于喷枪。 蜜胺/尼龙(Melamine/nylon)-主要用于电子产品,因需要严格控制清理力度。
镁合金件表面喷砂清理
喷砂(Sand Blasting)处理在金属表面的应用是 非常普遍的,原理只是将加速的磨料颗粒向金属 表面撞击,而达至除金秀、去毛刺、去氧化层或 作表面预处理等,它能改变金属表面的光洁度和 应力状态。而一些影响喷砂技术的参数是需要留 意的,如磨料种类、磨料粒度、喷射距离、喷射 角度和速度等。除了喷砂处理外,拋丸处理亦是 其中的一个很好选择,本文将会为大家介绍此两 项金属表面处理技术和在镁合金件的应用,希望 令读者有进一由一定尺寸范围的颗粒组成,在中位数的磨料砂砾 会占大多数,但当中亦含有少量较大或较小的颗粒,由于磨料在拋丸过程中损 耗,部分会经过回收再用而部份会过滤筛出,导致颗粒比例改变,所以要令喷 砂效果保持稳定,就要定时添加新磨料。如果添料时间相隔太长,磨料便明显 变小,令表面效果降低,延长清理时间。
喷砂与喷丸的区别

喷砂与喷丸的区别This model paper was revised by the Standardization Office on December 10, 2020喷丸与喷砂的区别1.喷丸是以金属弹丸,利用压缩空气或机械离心力为动力和摩擦力来除去金属锈蚀的方法。
弹丸直径在之间,压缩空气压力为,喷流与表面角度为30度-90度左右。
喷嘴系用T7或T8工具钢制成并淬火至硬度50-55HRC,每个喷嘴使用期限为15-20天。
喷丸是用来清除厚度不小于2mm的或不要求保持准确尺寸及轮廓的中型、大型金属制品以及铸锻件上的氧化皮、铁锈、型砂及旧漆膜。
是表面涂(镀)覆前的一种清理方法。
广泛用于大型造船厂、重型机械厂、汽车厂等。
用喷丸进行表面处理,打击力大,清理效果明显。
但喷丸对“骞ぜ的处理,容易使工件变形,且钢丸打击到工件表面(无论抛丸或喷丸)使金属基材产生变形,由于Fe3O4和Fe2O3没有塑性,破碎后剥离,而油膜与基材一同变形,所以对带有油污的工件,抛丸、喷丸无法彻底清除油污。
2.喷砂也是一种机械清理方法,但并喷砂不是喷丸,喷砂用的是砂粒如石英砂,喷丸用的是金属弹丸。
在现有的工件表面处理方法中,清理效果最佳的还数喷砂清理。
喷砂适用于工件表面要求较高的清理。
但是我国目前通用喷砂设备中多由铰龙、刮板、斗式提升机等原始笨重输砂机械组成。
用户需要施建一个深地坑及做防水层来装置机械,建设费用高,维修工作量及维修费用极大。
随着国家对环境保护和工业卫生的重视,由于喷砂过程有大量粉尘产生不仅严重污染环境,还及易导致操作者的职业病(矽肺),已大量将喷丸来代替喷砂。
3.抛丸是利用高速旋转的叶轮把小钢丸或者小铁丸抛掷出去高速撞击零件表面,故可以除去零件表面的氧化层。
同时钢丸或铁丸高速撞击零件表面,造成零件表面的晶格扭曲变形,使表面硬度增高,是对零件表面进行清理的一种方法,抛丸常用来铸件表面的清理或者对零件表面进行强化处理。
喷丸工艺流程
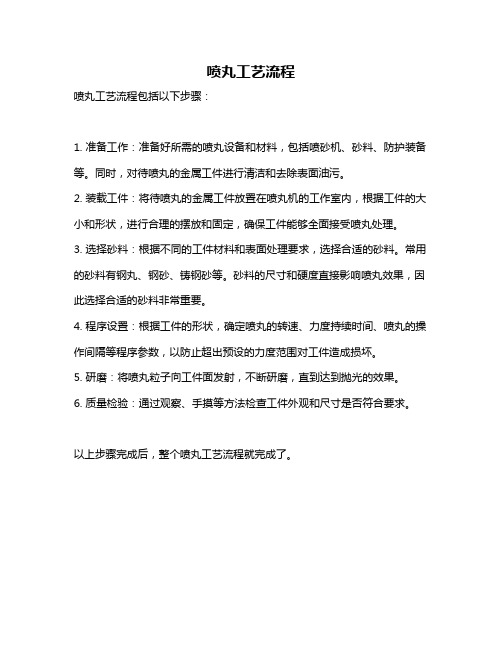
喷丸工艺流程
喷丸工艺流程包括以下步骤:
1. 准备工作:准备好所需的喷丸设备和材料,包括喷砂机、砂料、防护装备等。
同时,对待喷丸的金属工件进行清洁和去除表面油污。
2. 装载工件:将待喷丸的金属工件放置在喷丸机的工作室内,根据工件的大小和形状,进行合理的摆放和固定,确保工件能够全面接受喷丸处理。
3. 选择砂料:根据不同的工件材料和表面处理要求,选择合适的砂料。
常用的砂料有钢丸、钢砂、铸钢砂等。
砂料的尺寸和硬度直接影响喷丸效果,因此选择合适的砂料非常重要。
4. 程序设置:根据工件的形状,确定喷丸的转速、力度持续时间、喷丸的操作间隔等程序参数,以防止超出预设的力度范围对工件造成损坏。
5. 研磨:将喷丸粒子向工件面发射,不断研磨,直到达到抛光的效果。
6. 质量检验:通过观察、手摸等方法检查工件外观和尺寸是否符合要求。
以上步骤完成后,整个喷丸工艺流程就完成了。
喷砂和喷丸的作用和区别

喷砂和喷丸的作用和区别 This manuscript was revised by the office on December 22, 2012喷砂和喷丸的作用和区别(一)喷砂喷砂是用机械或净化的压缩空气,将砂流强烈地喷向金属制品表面,利用磨料强力的撞击作用,打掉其上的污垢物,达到清理或修饰目的的过程。
喷砂的主要用途有:(1)除掉零件表面的锈蚀、焊渣、积碳、旧油漆层和其它干燥了的油污;(2)除去铸件、锻件或热处理后零件表面的型砂及氧化皮;(3)除去零件表面的毛刺或方向性磨痕;(4)降低零件表面的粗糙度,以提高油漆和其它涂层的附着力;(5)使零件呈漫反射的消光状态。
喷砂分干喷砂和湿喷砂两种。
于喷砂加工的表面比较粗糙,湿喷砂的应用与干喷砂相似,但主要用于较精密的加工。
湿喷砂的优点是污染小。
1.干喷砂干喷砂又分机械喷砂与空气压力喷砂两种类型。
每一类型又可分为手工、半自动或连续自动等多种方式。
采用的喷砂机有自流式、离心式、吸入式和压力式等。
生产上常用的是吸入式和压力式。
吸入式设备简单,但效率低,适用于小零件。
压力式主要用于大、中型零件的大批量生产,适用性广,效率高。
国内广泛使用的是手工空气压力喷砂室,适用于各种形状复杂的中、小型零件。
干喷砂常用的砂料是氧化铝砂(含天然和人造两种)、石英砂(二氧化硅)、碳化硅(人造金刚砂)等。
以采用铝钒土(氧化铝砂)为最好。
因其不易粉化,劳动条件好,砂料还可以循环使用。
碳化硅砂虽也有上述优点,但因过于昂贵,很少使用。
国内应用最多的还是石英砂。
它虽易粉化,但有不污染零件的优点。
2.湿喷砂是在砂料中加入定量的水,使之成为砂水混合物,以减少砂料对零件表面的冲击作用,从而减少金属材料的去除量,使零件表面更光洁。
双层壁的钣金焊接件,因难防腐蚀,不宜采用湿喷砂。
薄截面零件,因湿喷砂工作压力比干喷砂大,水的冲击易使其变形,故也不宜采用湿喷砂。
3.喷砂后零件的处理经喷砂的零件,应尽量减少触摸,并及时进行表面处理。
铝零件一些小问题铸铝白点霉变

铝零件一些小问题压铸铝铸件被水泡过后很多的铝灰和白点,用什么办法可以快速的处理干净?1你说的是铝质发生了霉变,要用专用的脱霉剂,用抛丸和其他方法可以暂时去除,但是过一段时间还会出现霉变;2有这样的清洗剂可以买一点,网上搜索一下很多的;彻底清除很难,如果允许的话,抛丸处理(严重的可能要刷光)。
3水中的盐分和酸腐蚀了铸件;用锌丸抛丸效果好一点,建议抛丸前做超音波清洗。
避免铝铸件阳极氧化膜染色后出现白斑的方法由于铝铸件产品组织疏松、孔隙率高,含有多种金属和非金属杂质,阳极氧化膜染色后极易出现白斑,铝铸件阳极氧化膜质量很难保证。
对此,有关专家表示,可以采用以下几种方法来避免这个问题:一、采用高电压大电流密度冲击法。
在阳极氧化初期采取高电压、大电流冲击,使原先被杂质分割的大小“岛屿”通过大电流冲击而连接成片。
二、铸件表面打磨法。
打磨可以使磨下来的铝末填充铸件的孔隙,起到连接被杂质隔离的块块“岛屿”的桥梁作用。
三、铸件表面喷丸法。
在喷丸法试用之前笔者采用圆头锤子敲的方法,原意是想使阻隔“岛屿”的缝隙通过敲打闭合,达到连接成片的目的,结果效果显著。
采用这几种方法就可有效避免铝铸件阳极氧化膜染色后出现白斑,从而保证其质量。
阳极氧化后的铝型材表面有密密麻麻的白点及白斑,是什么原因造成的?对整体防腐性能有影响吗?两个可能,染色後未封孔前, 工件於空气中熏到酸雾或碱雾, 染料呈点状退色所致. 此现象大都为细小星点状白点. 只要隔绝染色至封孔槽间的环境勿受酸碱物熏到, 即可改善. 此现象不会影响防腐性能.工件表面残馀污物尤其是残胶, 前处理未完全去除, 在阳极氧化过程中, 氧化不完全, 染色即无法完全上色, 改善前处理即可解决. 由於氧化膜不完全会影响防腐性能.。
不锈钢表面处理
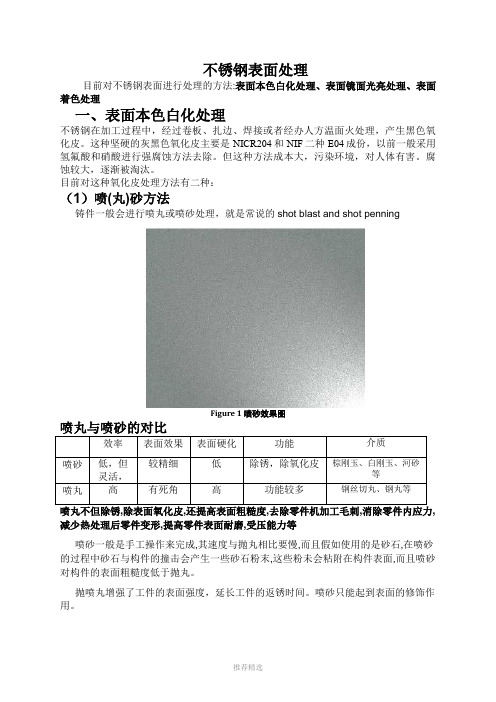
不锈钢表面处理目前对不锈钢表面进行处理的方法:表面本色白化处理、表面镜面光亮处理、表面着色处理一、表面本色白化处理不锈钢在加工过程中,经过卷板、扎边、焊接或者经办人方温面火处理,产生黑色氧化皮。
这种坚硬的灰黑色氧化皮主要是NICR204和NIF二种E04成份,以前一般采用氢氟酸和硝酸进行强腐蚀方法去除。
但这种方法成本大,污染环境,对人体有害。
腐蚀较大,逐渐被淘汰。
目前对这种氧化皮处理方法有二种:(1)喷(丸)砂方法铸件一般会进行喷丸或喷砂处理,就是常说的shot blast and shot penningFigure 1 喷砂效果图喷丸与喷砂的对比喷丸不但除锈,除表面氧化皮,还提高表面粗糙度,去除零件机加工毛刺,消除零件内应力,减少热处理后零件变形,提高零件表面耐磨,受压能力等喷砂一般是手工操作来完成,其速度与抛丸相比要慢,而且假如使用的是砂石,在喷砂的过程中砂石与构件的撞击会产生一些砂石粉末,这些粉未会粘附在构件表面,而且喷砂对构件的表面粗糙度低于抛丸。
抛喷丸增强了工件的表面强度,延长工件的返锈时间。
喷砂只能起到表面的修饰作用。
(2)化学法用一种无污染酸洗钝化膏和常温无毒害的带有无机添加剂的清洗液进行浸洗。
从而达到不锈钢本色的白化处理之目的。
基本上看上去是一目光的色泽。
这种方法对大型、复杂产品较适用,值得推广应用。
酸洗钝化方式根据操作方式不同,不锈钢酸洗钝化处理主要有浸渍法、膏剂法、涂刷法、喷淋法、循环法、电化学法等6种方法。
Figure 2 钝化前后效果图钝化机理:金属经氧化性介质处理后,其腐蚀速度比原来未处理前有显著下降的现象称金属的钝化。
其钝化机理主要可用薄膜理论来解释,即认为钝化是由于金属与氧化性介质作用,作用时在金属表面生成一种非常薄的、致密的、覆盖性能良好的、能坚固地附在金属表面上的钝化膜。
这层膜成独立相存在,通常是氧和金属的化合物。
它起着把金属与腐蚀介质完全隔开的作用,防止金属与腐蚀介质直接接触,从而使金属基本停止溶解形成钝态达到防止腐蚀的效果。
喷丸处理的原理和作用
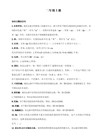
【喷砂的主要应用范围】
(一)工件涂镀、工件粘接前处理喷砂能把工件表面的锈皮等一切污物清除,并在工件表面建立起十分重要的基础图式(即通常所谓的毛面),而且可以通过调换不同粒度的磨料,达到不同程度的粗糙度,大大提高工件与涂料、镀料的结合力。或使粘接件粘接更牢固,质量更好。
(二)铸锻件毛面、热处理后工件的清理与抛光喷砂能清理铸锻件、热处理后工件表面的一切污物(如氧化皮、油污等残留物),并将工件表面抛光提高工件的光洁度,能使工件露出均匀一致的金属本色,使工件外表更美观,达到美化装饰的作用。
其实铸造件清理不只是用抛丸,对于大件一般先进行滚筒清砂,就是把铸造件的冒口切除后放在滚筒内滚,由零件在滚筒内互相碰撞,把表面的砂大部分先清掉再进行抛丸或喷丸的。
抛丸丸子大小是1.5mm。
研究表明,就破坏而言,金属材料表面存在拉应力时比压应力要容易的多,表面呈压应力时,材料的疲劳寿命大大提高,因此,对于轴类等容易疲劳断裂的部件通常采用喷丸形成表面压应力,提高产品寿命,此外,金属金属材料对拉伸很敏感,这就是材料的拉伸强度比压缩强度低的多的原因,这也是金属材料一般用拉伸强度(屈服,抗拉)表示材料性能的原因。
我们日常乘坐的汽车的钢板的工作面就是用喷丸来强化的,可以显著的提高材料的抗疲劳强度。
抛丸是用电机带动叶轮体旋转,靠离心力的作用,将直径在0.2~3.0的丸子(有铸丸\切丸\不锈钢丸等)抛向工件的表面,使工件的表面达到一定的粗造度,使工件变的美观,或着改变工件的焊接拉应力为压应力,提高工件的使用寿命.几乎用于机械的大多数领域,修造船\汽车零部件\飞机部件\枪炮坦克表面\桥梁\钢结构\玻璃\钢板\管道\等等.喷砂(丸)是用压缩空气作为动力将直径在40~120目的砂或0.1~2.0左右的丸喷向工件的表面,使工件达到同样的效果.丸粒的大小不同,达到的处理效果就不一样.重点提出:喷丸同样能起到强化的作用.现在国内的设备走进了一个误区,认为只有抛丸才能达到强化的目的.美国\日本的企业用于强化的是抛喷丸并用的!各有各的优势.比如象齿轮这样的工件,抛丸的出丸角度无法改变,只能用变频改变初速度.但它处理的量大,速度快,而喷丸则正好于之相反,抛丸的效果就没有喷丸的效果好
喷砂和喷丸

五、磨料速度与清理效率的比较
工作压力MPa 磨料速度m*s-1 相对清理效率%
0.7 187.7 100
0.67 178.7 93
0.63 163.1 85
0.60 147.5 78
喷丸得到的铸件表面质量没有喷砂地好,但比喷砂经济。而且能够去除一些铸件难以清理的粘砂,而喷砂不行。
喷砂和喷丸是两种不同的表面硬化工艺,喷砂处理过的硬度比喷丸的低,所使用的工具也是不同的了!
喷砂喷丸根本就是两种喷射介质的差别,当然效果也有差别
喷砂比较精细,容易控制精度和平面度
喷丸比较经济实用,容易控制效率和成本,可以控制铁丸的直径来控制喷射效果
5 0.93 1.02 1.10 1.16 1.22 1.27 压缩空气m3*min-1
88.9 98 103 88.9 109.3 119.8 磨料Kg*h-1
11.24 12.6 13.1 13.75 14.30 15 清理效率m2*h-1
9.5 4.05 4.56 4.73 4.90 5.21 5.55 压缩空气m3*min-1
四、关于喷丸清理的喷嘴规格与压缩空气和磨料消耗相互关系
喷嘴
/mm 工作压力/MPa 项目
0.48 0.56 0.59 0.62 0.66
0.70
392 436 456 477 499 522 磨料Kg*h-1
16.1 17.8 18.7 19.5 20.4 21.4 清理效率m2*h-1
单位抛丸量所需功率比 1 8 30
达到同样清理效果的耗电量 KW*h/100m2 12.5 267 37.5
清理效率 40~150 15 6~10
11.1 5.50 6.14 6.45 6.79 6.96 7.19 压缩空气m3*min-1
喷丸处理

喷丸处理处理也称喷丸强化,是提高零件疲劳寿命的有效方法之一,喷丸处理就是将高速弹丸流喷射到弹簧表面,使弹簧表层发生塑性变形,而形成一定厚度的强化层,强化层内形成较高的残余应力,由于弹簧表面压应力的存在,当弹簧承受载荷时可以抵消一部分抗应力,从而提高弹簧的疲劳强度。
喷丸是用来清除厚度不小于2mm的或不要求保持准确尺寸及轮廓的中型、大型金属制品以及铸锻件上的氧化皮、铁锈、型砂及旧漆膜。
是表面涂(镀)覆前的一种清理方法。
广泛用于大型造船厂、重型机械厂、汽车厂等。
喷丸强化是一个冷处理过程,它被广泛用于提高长期服役于高应力工况下金属零件,如飞机引擎压缩机叶片、机身结构件、汽车传动系统零件等的抗疲劳属性。
喷丸强化,是在一个完全控制的状态下,将无数小圆形称为钢丸的介质高速且连续喷射,捶打到零件表面,从而在表面产生一个残余压应力层。
因为当每颗钢丸撞击金属零件上,宛如一个微型棒捶敲打表面,捶出小压痕或凹陷。
为形成凹陷,金属表层必定会产生拉伸。
表层下,压缩的晶粒试图将表面恢复到原来形状,从而产生一个高度压缩力作用下的半球。
无数凹陷重叠形成均匀的残余压应力层。
最终,零件在压应力层保护下,极大程度地改善了抗疲劳强度,延长了安全工作寿命。
喷丸又分为喷丸和喷砂。
用喷丸进行,打击力大,清理效果明显。
但喷丸对薄板工件的处理,容易使工件变形,且钢丸打击到工件表面(无论抛丸或喷丸)使金属基材产生变形,由于Fe3o4和Fe2o3没有塑性,破碎后剥离,而油膜与基材一同变形,所以对带有油污的工件,抛丸、喷丸无法彻底清除油污。
在现有的工件表面处理方法中,清理效果最佳的还数喷砂清理。
喷砂适用于工件表面要求较高的清理。
但是我国目前通用喷砂设备中多由铰龙、刮板、斗式提升机等原始笨重输砂机械组成。
用户需要施建一个深地坑及做防水层来装置机械,建设费用高,维修工作量及维修费用极大,喷砂过程中产生大量的矽尘无法清除,严重影响操作工人的健康并污染环境。
喷丸强化分为一般喷丸和应力喷丸。
铸件清理工艺规程
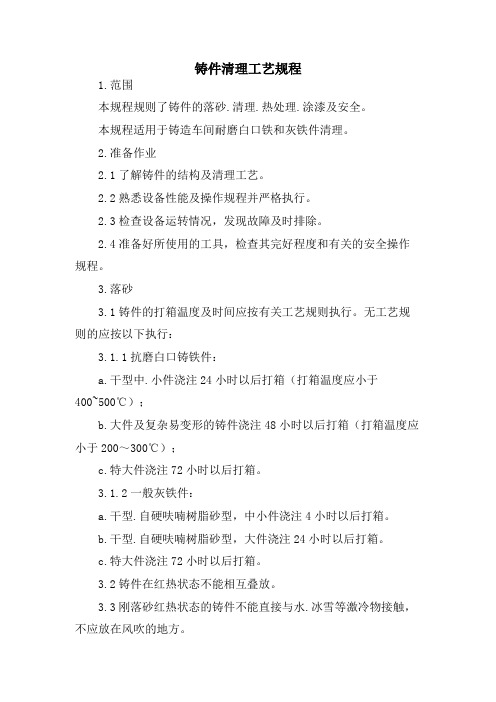
铸件清理工艺规程1.范围本规程规则了铸件的落砂.清理.热处理.涂漆及安全。
本规程适用于铸造车间耐磨白口铁和灰铁件清理。
2.准备作业2.1了解铸件的结构及清理工艺。
2.2熟悉设备性能及操作规程并严格执行。
2.3检查设备运转情况,发现故障及时排除。
2.4准备好所使用的工具,检查其完好程度和有关的安全操作规程。
3.落砂3.1铸件的打箱温度及时间应按有关工艺规则执行。
无工艺规则的应按以下执行:3.1.1抗磨白口铸铁件:a.干型中.小件浇注24小时以后打箱(打箱温度应小于400~500℃);b.大件及复杂易变形的铸件浇注48小时以后打箱(打箱温度应小于200~300℃);c.特大件浇注72小时以后打箱。
3.1.2一般灰铁件:a.干型.自硬呋喃树脂砂型,中小件浇注4小时以后打箱。
b.干型.自硬呋喃树脂砂型,大件浇注24小时以后打箱。
c.特大件浇注72小时以后打箱。
3.2铸件在红热状态不能相互叠放。
3.3刚落砂红热状态的铸件不能直接与水.冰雪等激冷物接触,不应放在风吹的地方。
3.4手工打箱落砂时,锤击砂箱应打在端面和箱壁的加强肋上,禁止敲击砂箱的箱带.箱把和箱耳。
3.5打箱前应把浇注溢出的铁块等收拾干净,把取下的压铁.箱卡.锁紧销.楔板等分别放在指定的地方。
3.6使用震动落砂机时应注意:a)落砂机禁止超负荷使用;b)避免铸件与砂箱碰撞造成损伤,薄壁易裂铸件应少震动;c)必须在排烟除尘装置启动后再行开震;d)铸件上的型砂应尽可震落干净,阻碍铸铁收缩的泥芯应及时除掉,将芯骨弄松;e)及时清除阻塞在落砂机栅格上的碎铁块和砂团;3.7打箱落砂后的砂箱不应残留干砂和铁块,并按不同规格平稳整齐地堆放在指定地点。
4.铸件清理的技术要求4.1清理后的铸件外表面,不允许有粘砂.氧化皮和影响零件装配及影响外面美观的缺陷。
4.2铸件内腔应无残留砂芯块.芯骨和飞翔.毛刺等多肉类缺陷。
4.3机械加工基准面(孔)或夹固面应光洁平整。
4.4铸件几何形状必须完整,非加工面上的清理损伤不应大于该处尺寸偏差,加工面上损伤不应大于该处加工余量的1/2。
抛丸、喷丸和喷沙的区别

• 喷丸 • 利用高速丸流的冲击作用
清理和强化基体表面的过 程。 • 用喷丸进行表面处理,打 击力大,清理效果明显。 但喷丸对薄板工件的处理, 容易使工件变形
喷丸机
抛丸机
一、抛丸
• 抛丸是一种机械方面的表面处理工艺的名称,类似的工艺 还有喷砂和喷丸。抛丸的原理是用电动机带动叶轮体旋转 (直接带动或用V型皮带传动),靠离心力的作用,将直径 约在0.2~3.0的弹丸(有铸钢丸、钢丝切丸、不锈钢丸等 不同类型)抛向工件的表面,使工件的表面达到一定的粗 造度,使工件变得美观,或者改变工件的焊接拉应力为压 应力,提高工件的使用寿命。通过提高工件表面的粗糙度, 也提高了工件后续喷漆的漆膜附着力。抛丸这种工艺几乎 用于机械的大多数领域,如修造船、汽车零部件、飞机部 件、枪炮坦克表面、桥梁、钢结构、玻璃、钢板型材、管 道内外壁防腐甚至道路表面等等行业。
喷丸的优点
• 喷丸处理是工厂广泛采用的一种表面强化工艺,其设备简 单、成本低廉,不受工件形状和位置限制,操作方便,但 工作环境较差。喷丸广泛用于提高零件机械强度以及耐磨 性、抗疲劳和耐腐蚀性等。还可用于表面消光、去氧化皮 和消除铸、锻、焊件的残余应力等。
抛丸与喷丸的区别
• 喷丸使用高压风或压缩空气作动力,而抛丸一般为高速旋 转的飞轮将钢砂高速抛射出去。抛丸效率高,但会有死角, 而喷丸比较灵活,但动力消耗大。
• 丸的分类总共有3大类:铸钢丸 铸铁丸 玻璃丸
特别说明: 喷丸用玻璃丸和其他用途的玻璃丸是两个不同的概念。 喷丸玻璃丸最大的特 点是它的硬度最低不小于6—7莫氏而且有一定的韧性,成圆率最低不小于90%。而 道路反光玻璃丸对硬度无要求,一般普通玻璃作原材料即可,成圆率要求最低75%。 两种价格差别很大,但外观却相差无几,如果将普通玻璃丸用于喷丸加工,貌 似成本较低,而在喷丸加工时破碎率较高,且加工强度较高的工件时几乎是一次破
对付防腐材料阳极上的污垢小妙招
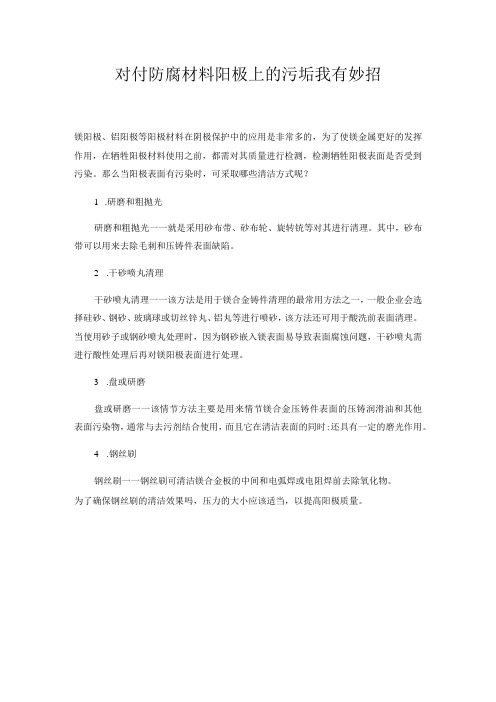
对付防腐材料阳极上的污垢我有妙招
镁阳极、铝阳极等阳极材料在阴极保护中的应用是非常多的,为了使镁金属更好的发挥作用,在牺牲阳极材料使用之前,都需对其质量进行检测,检测牺牲阳极表面是否受到污染。
那么当阳极表面有污染时,可采取哪些清洁方式呢?
1.研磨和粗抛光
研磨和粗抛光一一就是采用砂布带、砂布轮、旋转铳等对其进行清理。
其中,砂布带可以用来去除毛刺和压铸件表面缺陷。
2.干砂喷丸清理
干砂喷丸清理一一该方法是用于镁合金铸件清理的最常用方法之一,一般企业会选择硅砂、钢砂、玻璃球或切丝锌丸、铝丸等进行喷砂,该方法还可用于酸洗前表面清理。
当使用砂子或钢砂喷丸处理时,因为钢砂嵌入镁表面易导致表面腐蚀问题,干砂喷丸需进行酸性处理后再对镁阳极表面进行处理。
3.盘或研磨
盘或研磨一一该情节方法主要是用来情节镁合金压铸件表面的压铸润滑油和其他表面污染物,通常与去污剂结合使用,而且它在清洁表面的同时:还具有一定的磨光作用。
4.钢丝刷
钢丝刷一一钢丝刷可清洁镁合金板的中间和电弧焊或电阻焊前去除氧化物。
为了确保钢丝刷的清洁效果吗,压力的大小应该适当,以提高阳极质量。
抛丸处理后发黑的原因及对应措施
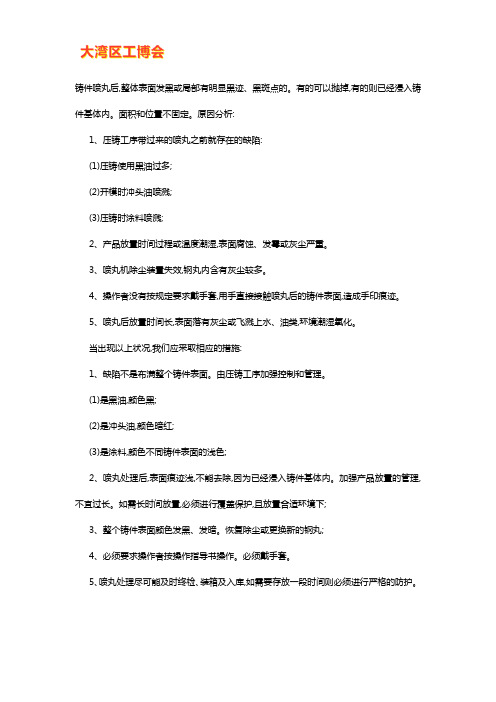
铸件喷丸后,整体表面发黑或局部有明显黑迹、黑斑点的。
有的可以抛掉,有的则已经浸入铸件基体内。
面积和位置不固定。
原因分析:
1、压铸工序带过来的喷丸之前就存在的缺陷:
(1)压铸使用黑油过多;
(2)开模时冲头油喷溅;
(3)压铸时涂料喷溅;
2、产品放置时间过程或温度潮湿,表面腐蚀、发霉或灰尘严重。
3、喷丸机除尘装置失效,钢丸内含有灰尘较多。
4、操作者没有按规定要求戴手套,用手直接接触喷丸后的铸件表面,造成手印痕迹。
5、喷丸后放置时间长,表面落有灰尘或飞溅上水、油类,环境潮湿氧化。
当出现以上状况,我们应采取相应的措施:
1、缺陷不是布满整个铸件表面。
由压铸工序加强控制和管理。
(1)是黑油,颜色黑;
(2)是冲头油,颜色暗红;
(3)是涂料,颜色不同铸件表面的浅色;
2、喷丸处理后,表面痕迹浅,不能去除,因为已经浸入铸件基体内。
加强产品放置的管理,不宜过长。
如需长时间放置,必须进行覆盖保护,且放置合适环境下;
3、整个铸件表面颜色发黑、发暗。
恢复除尘或更换新的钢丸;
4、必须要求操作者按操作指导书操作。
必须戴手套。
5、喷丸处理尽可能及时终检、装箱及入库,如需要存放一段时间则必须进行严格的防护。
油箱防锈之酸洗磷化、喷丸、喷砂

磷化(Ⅱ)——磷化前的预处理一般情况下,磷化处理要求工件表面应是洁净的金属表面(二合一、三合一、四合一例外)。
工件在磷化前必须进行除油脂、锈蚀物、氧化皮以及表面调整等预处理。
特别是涂漆前打底用磷化还要求作表面调整,使金属表面具备一定的“活性”,才能获得均匀、细致、密实的磷化膜,达到提高漆膜附着力和耐腐蚀性的要求。
因此,磷化前处理是获得高质量磷化膜的基础。
1 除油脂除油脂的目的在于清除掉工件表面的油脂、油污。
包括机械法、化学法两类。
机械法主要是:手工擦刷、喷砂抛丸、火焰灼烧等。
化学法主要:溶剂清洗、酸性清洗剂清洗、强碱液清洗,低碱性清洗剂清洗。
以下介绍化学法除油脂工艺。
1.1 溶剂清洗溶剂法除油脂,一般是用非易燃的卤代烃蒸气法或乳化法。
最常见的是采用三氯乙烷、三氯乙烯、全氯乙烯蒸汽除油脂。
蒸汽脱脂速度快,效率高,脱脂干净彻底,对各类油及脂的去除效果都非常好。
在氯代烃中加入一定的乳化液,不管是浸泡还是喷淋效果都很好。
由于氯代卤都有一定的毒性,汽化温度也较高,再者由于新型水基低碱性清洗剂的出现,溶剂蒸汽和乳液除油脂方法现在已经很少使用了。
1.2 酸性清洗剂清洗酸性清洗剂除油脂是一种应用非常广泛的方法。
它利用表面活性剂的乳化、润湿、渗透原理,并借助于酸腐蚀金属产生氢气的机械剥离作用,达到除油脂的目的。
酸性清洗剂可在低温和中温下使用。
低温一般只能除掉液态油,中温就可除掉油和脂,一般只适合于浸泡处理方式。
酸性清洗剂主要由表面活性剂(如OP 类非离子型活性剂、阴离子磺酸钠型)、普通无机酸、缓蚀剂三大部分组成。
由于它兼备有除锈与除油脂双重功能,人们习惯称之为“二合一”处理液。
常见的酸性清洗剂配方及工艺参数见下表。
盐酸、硫酸酸基的清洗剂应用最为广泛,成本低,效率较高。
但酸洗残留的Cl-、SO42-对工件的后腐蚀危害很大。
而磷酸酸基没有腐蚀物残留的隐患,但磷酸成本较高,清洗效率低些。
对于锌件,铝件一般不采用酸性清洗剂清洗,特别锌件在酸中的腐蚀极快。
喷砂与喷丸的区别

喷砂与喷丸的区别集团公司文件内部编码:(TTT-UUTT-MMYB-URTTY-ITTLTY-1.喷丸是以金属弹丸,利用压缩空气或机械离心力为动力和摩擦力来除去金属锈蚀的方法。
弹丸直径在0.2-2.5mm之间,压缩空气压力为0.2-0.6Mpa,喷流与表面角度为30度-90度左右。
喷嘴系用T7或T8工具钢制成并淬火至硬度50-55HRC,每个喷嘴使用期限为15-20天。
喷丸是用来清除厚度不小于2mm的或不要求保持准确尺寸及轮廓的中型、大型金属制品以及铸锻件上的氧化皮、铁锈、型砂及旧漆膜。
是表面涂(镀)覆前的一种清理方法。
广泛用于大型造船厂、重型机械厂、汽车厂等。
用喷丸进行表面处理,打击力大,清理效果明显。
但喷丸对“骞ぜ的处理,容易使工件变形,且钢丸打击到工件表面(无论抛丸或喷丸)使金属基材产生变形,由于Fe3O4和Fe2O3没有塑性,破碎后剥离,而油膜与基材一同变形,所以对带有油污的工件,抛丸、喷丸无法彻底清除油污。
2.喷砂也是一种机械清理方法,但并喷砂不是喷丸,喷砂用的是砂粒如石英砂,喷丸用的是金属弹丸。
在现有的工件表面处理方法中,清理效果最佳的还数喷砂清理。
喷砂适用于工件表面要求较高的清理。
但是我国目前通用喷砂设备中多由铰龙、刮板、斗式提升机等原始笨重输砂机械组成。
用户需要施建一个深地坑及做防水层来装置机械,建设费用高,维修工作量及维修费用极大。
随着国家对环境保护和工业卫生的重视,由于喷砂过程有大量粉尘产生不仅严重污染环境,还及易导致操作者的职业病(矽肺),已大量将喷丸来代替喷砂。
3.抛丸是利用高速旋转的叶轮把小钢丸或者小铁丸抛掷出去高速撞击零件表面,故可以除去零件表面的氧化层。
同时钢丸或铁丸高速撞击零件表面,造成零件表面的晶格扭曲变形,使表面硬度增高,是对零件表面进行清理的一种方法,抛丸常用来铸件表面的清理或者对零件表面进行强化处理。
一般抛丸用于规则形状等,几个抛头上下左右一起,效率高,污染小。