注塑产品残留应力介绍
塑料件残余应力分析方法总结

塑料件残余应力分析方法总结PC/ABS的应用非常广泛,汽车内外饰零件,大家家中的液晶电视面框,智能手机的外壳,笔记本电脑的上下盖等等。
而其中多数产品的结构中都含有螺丝柱,卡扣的设计;另外,像一些二次加工工艺如喷漆,电镀,涂抹胶水等,这些结构和后加工工艺都可能诱发PC/ABS合金材料出现内应力开裂的现象,导致次品率很高。
为什么会有应力产生?这是由于材料的结构决定材料的性能。
PC/ABS在成型时,分子链被迫取向,但是由于分子链上含有苯环,所以解取向比较困难,而在成型后,被取向的分子链有恢复自然状态的趋势,但是由于整个分子链已经被冻结,从而造成制品存在残留应力。
那如何分析PC/ABS的残余应力呢,分析PC/ABS残余应力的手段:溶剂浸泡法1、将做好带有螺丝槽或柱的PC/ABS制件浸泡于冰醋酸中,持续30s或更长时间,取出后检查外观,如有细小致密的裂纹,说明此处有内应力存在,裂纹越多,则说明内应力越大;2、异丙醇与丙酮3:1的比例混合,加入红色染料,着色均一的说明内应力较小,不容易着色的部位应力较大,需要注意。
Moldflow模流分析模拟法通过模流分析软件,分析出速度/压力切换时的压力分布情况,压力越高的,参与的应力也就越大。
四分之一椭圆应力分析法选用四分之一椭圆夹具,试片尽量居中放置,将溶剂均匀涂覆在试片上,同一种原料试片最好做3-5组,涂覆完成后静止存放,(环境要求23℃,50%RH),观察试片裂纹情况,裂纹越多,残余应力越大。
螺丝孔实验法采用合适Size的螺丝进行攻螺丝实验,螺丝上可以涂覆一些常用的工业用黄油,必要的时候可以将攻好的螺丝放入高温环境,加速应力释放,出现开裂或者裂纹的说明参与应力大。
应力开裂是影响塑料制品质量的主要因素,为了提高产品质量,必须根据实际情况,在正确分析应力产生开裂的基础上,采取有效措施和手段,减小和避免产品内应力对制品的影响。
moldex 残余应力

moldex 残余应力残余应力是指在物体内部由于外部作用力消失后,仍然保留在物体内部的应力。
这种应力会导致物体的变形、裂纹扩展等不良现象,从而影响物体的使用寿命和性能。
Moldex是一款广泛应用于塑料注塑行业的模拟软件,可以对塑料制品的成型过程进行模拟分析,预测制品的残余应力分布情况,为优化成型工艺提供依据。
Moldex中的残余应力分析主要包括以下几个方面:1. 初始残余应力初始残余应力是指塑料制品在成型过程中,由于熔体的流动、冷却收缩等原因产生的应力。
在Moldex中,可以通过设置初始温度场、压力场等条件来模拟制品的成型过程,从而得到初始残余应力分布情况。
2. 熔体流动引起的残余应力熔体流动是塑料制品成型过程中的关键步骤,熔体的流动状态直接影响到制品的成型质量和残余应力分布。
在Moldex中,可以通过设置熔体的流动速率、温度、压力等参数来模拟熔体的流动过程,从而得到熔体流动引起的残余应力分布情况。
3. 冷却收缩引起的残余应力冷却收缩是塑料制品成型过程中的另一个重要环节,冷却过程中的收缩会引起制品内部的应力变化。
在Moldex中,可以通过设置冷却速率、温度梯度等参数来模拟制品的冷却过程,从而得到冷却收缩引起的残余应力分布情况。
4. 脱模引起的残余应力脱模过程中,制品与模具之间的摩擦力会导致制品产生额外的应力。
在Moldex中,可以通过设置脱模速度、摩擦系数等参数来模拟制品的脱模过程,从而得到脱模引起的残余应力分布情况。
5. 热膨胀引起的残余应力塑料制品在使用过程中,可能会受到温度的影响而发生热膨胀或收缩。
这种热膨胀或收缩会引起制品内部的应力变化。
在M oldex中,可以通过设置温度变化曲线、热膨胀系数等参数来模拟制品的热膨胀过程,从而得到热膨胀引起的残余应力分布情况。
通过对以上几个方面的残余应力进行分析,可以得到塑料制品在整个成型过程中的残余应力分布情况。
这对于优化成型工艺、提高制品质量具有重要意义。
注塑产品应力检查

塑料注射成形零件内应力检测方法塑料注射成形零件由于结构设计,模具设计和工艺的局限性,在注塑和冷却过程中总会同时伴有压力和拉力的产生,而较高的残余应力(表面拉力)将会导致零件过早失效。
为了有效规避零部件产生这种失效,更合理的设计和工艺是必需的。
同时,快速而有效的检测在研发和生产过程中可以帮助我们及时发现缺陷,并可避免问题的扩散。
目前评估塑料注射成形零件表面及附近区域残余应力的方法之一是溶剂沉浸测试法。
沉浸后,高应力集中区域会有相应的裂纹产生,以此我们就可以快速有效地对设计和工艺进行评估和改进。
以下部分是主要树脂生产商GE和Bayer推荐的适合于各自主要产品的溶剂测试法。
我们需要在供应商品质控制流程中加入该检测结果。
GEP Lexan/Cycoloy系列塑料Lexan 系列(PC):常用于手机镜片,导光板,机壳。
Cycoloy系列(PC+ABS):常用于手机机壳。
对于用Lexan和Cycoloy系列塑料成形的零件,内应力的检查都可以采用以下方法:
1.醋酸沉浸法:(1)将零件完全浸入24摄氏度的冰醋酸中30秒;(2)取出后立即清洗,后晾干检查表面;(3)仔细观察外观,若有细小致密的裂纹,说明此处有应力存在,裂纹越多,应力越大; (4)重复上述操作,在冰醋酸中浸2分钟,再检查零件,若有深入塑料的裂纹,说明此处有很高的内应力,裂纹越严重,内应力越大。
残余应力、粘度、缺陷处理、缺陷原因、解决方法

残余应力、粘度、缺陷处理、缺陷原因、解决方法。
一、制件残余应力1.模具和注塑条件对残余应力的影响:2. 制件残余应力开裂检查带有残余应力的制件是否会在使用环境中开裂,有几个方法可以进行预先诊断:对于聚苯乙烯,在室温下用煤油;对于高密度聚乙烯,在80℃下用2%的洗涤剂溶液;对于聚丙烯,在80℃下用63%(重量百分比)的三氧化铬与水的混合物。
3.退火处理某些有开裂倾向的制件,可以用退火热处理方法来消除内应力,从而减少裂纹的形成。
首先,将成形品加热(通常是在玻璃化温度附近)并保持一定时间,然后再让其缓慢地自然冷却,使发生裂纹处的大分子能自由活动、回复原来状态。
这种退火热处理法一般在成形后立即进行。
4.调湿处理对于尼龙塑件,为了改善内应力分布状况及塑料内的晶体结构,提高制件韧性,保持尺寸相对稳定,可以进行调湿处理,其效果比退火处理更佳。
方法是将制件浸入沸水或醋酸钾水溶液(比例为1.25:100, 沸点121℃)中,浸泡时间视制件最大壁厚而定,从2小时至16小时不等。
二、塑料的粘度1.定义:熔融塑料流动时大分子之间相互磨擦的性质称为塑料的粘性,这种粘性大小的系数即为粘度,粘度是熔融塑料流动性高低的直接反映。
2.粘度受哪些条件影响(1)分子量的影响同一种塑料可以有不同的分子和分子量分布,分子量愈大,分子间作用力愈强,反映出来的粘度愈大。
(2)低分子添加剂的影响低分子添加剂可以降低大分子链之间的作用力,因而使粘度减小,使之易于充模成形。
(3)外界温度的影响不同塑料对温度的敏感性不尽相同,PC、PA、PS等,在温度升高时粘度显著下降,加工时采用高温来达到降低粘度是有效的,但是象PE、PP就不应该着重采取升温的办法来达到降低粘度的目的。
(4)剪切速度的影响有效地增加塑料的剪切速度可使塑料熔体粘度下降,但不同的塑料受剪切速度的影响也不尽相同,如PC其粘度几乎不受螺杆转速的影响,而PS受的影响则很大。
(5)压力的影响虽然高的注射压力在注射过程能提高注射速度而获得大的剪切作用,似乎对降低粘度有利,但从压力的物理意义来说,增压反而会令熔融塑料粘度增大,原因很简单,塑料大分子链与链之间本身保持着岩距离,那是分子间作用力使然,压力的增加意味着分子距离的缩小,因而分子链间的错动显得更为困难,整体的流动粘度也就增大了。
塑料残留应力介绍

一、塑料残留应力介绍当一塑料成品在应用上发生破裂或破坏时,就材料力学的观点,即表示该塑料件在破坏区域上,其所承受之应力数值总合超过了材料本身之物性强度数值。
因此要解决成品在使用上的破坏或破裂问题,就必须要从如何增加材料物性强度或从如何减少成品应力值来着手。
塑料制品承受的应力作用通常可依应力来源区分为外部应力及内部应力两种,外部应力是成品在使用时所遭受之外力作用,此部分将视产品应用场合而定,通常是无法控制其程度,一般产品设计者会依照常态之外部应力值,乘上一安全系数值来设计产品之强度。
而内部应力通常是成品在加工成型过程中所产生而留存在成品内部。
所以要有效解决塑料成品之破坏问题,唯有降低应力作用或提高材料强度两种方法。
然而对于塑料成型加工业者而言,如何使用较适当之加工条件,来防止材料强度降低及避免在加工时产生过大残留内部应力则是最重要之议题。
所以就产品设计者或塑料成型加工者而言,通常需要了解塑料件发生破坏之成因与产生破坏之位置与破坏之型态,才能有效分析解决成型及设计上的问题点。
塑料材料由于具有高黏特性,所以一般在成型加工时都需要利用高温、高压、高剪切等加工条件,来有效降低塑料熔胶黏度至容易成型加工之范围,另外由于塑料具低的热传导系数,是热的不良导体,所以在高温成型后需要长时间方能达到均匀温度之冷却。
然而现代塑料射出成型加工,一般为求高效益快速生产,所以对于射出成型周期都尽量缩短,而所对应之射出成型条件就需要要求射速快、冷却时间短,而对于塑料成品而言过大之速度差或不均匀冷却,往往会造成成品内部形成应力。
所谓塑料残留应力就是指塑料成品在经过制造或成形过程后,在无外力作用下或无温度梯度存在时,物体内部仍维持承受应力之状况。
通常塑料件常见之内部应力可分为两种,一种是剪切流动造成之流动应力,另一种是冷却收缩所造成之热应力。
塑料材料在成型过程中会因为高剪切作用造成分子链接构的高度定向现象,此种是属于熔胶剪切流动所形成之应力,另外则是因不均匀之冷却造成成品内分子链的不均匀收缩,当成品温度快速冷却到塑料的Tg以下时,冷却收缩造成分子链间应力无法完全释放,此种是属于冷却所形成之应力。
注塑件残余应力的测试方法

高产品质量 、 降低废品 率意义重 大 介 铝 4种残余压力的测试 方法, 包括无损 测试 的双折 射 法、 x射 线衍射 法和有 损测试的剥层 法 、 钻孔 法、 力松驰 法。叙述 了不同测试 方法 的测试原理 、 算方法等 , 应 计 评进 了各种测试方 法的优缺
点。
关键 词
注塑件
残余应力
式 中 : .o— — 分别 为两束 平 面偏振 光 的平 面 内 主 o 、r r , 应力; Ⅳ. —— 分别 为 两 束 平 面 偏 振 光 的 主 应 力 , 方 向上 的折 射率 ;
被称为残余热应力。一般来说 残余热应力 比残余
流动应力 大一 个 数量 级 , 残 余 热应 力 分 布 可 以大 从 致 推算 出制 品翘 曲变形 的程 度
才是一 个 常数
±6 — 分 别表示 试样 没有 剥层 时的上 下 表 面 —
法将残余应力释放 , 测量残余应力释放产生的释放
应变, 如剥层 法 、 力松 弛法 和钻孔 法 。无损 测试是 应 利用材 料物理 性质 的变化或 晶体结 构 参数 的变化测
个 国家制造 业水平 高低 的标志 。对注 塑产 品形 状尺 寸、 使用性 能有 显 著影 响的 残余 应力 一 直 是制 约产 品质量 的重要 因素 , 何 减 小 注 塑件 的残 余 应 力是 如
塑 制 品的残余 应 力有 两个 来 源 : 一 个 是 残余 流 第 动 应力 。在充模 、 压过 程 中塑 料熔 体 在 模 腔 中做 保 非 等温 流动形 成 的 剪切 应 力 和法 向应 力 , 由于 冷却 过 程 中温度 的迅 速下 降 应 力 不 能完 全 松 弛 , 温度 当 降到玻 璃化温 度 以下 时 , 余 应力 被 “ 残 冻结 ” 固体 在
moldflow第一主方向残余应力

Moldflow第一主方向残余应力引言在注塑成型过程中,由于高温和高压的作用,塑料制品会产生应力。
在注塑成型结束后,材料在冷却过程中会发生收缩,这会导致残余应力的产生。
本文将重点探讨M ol df lo w模拟中的第一主方向残余应力。
残余应力的定义残余应力是指材料在成型过程结束后,在冷却和固化过程中由于收缩而产生的内部应力。
残余应力对制品的性能和稳定性有重要影响,因此对其进行准确的分析和预测具有重要意义。
Moldf low模拟及其应用M o ld fl ow是一种用于预测注塑成型过程中塑料流动和冷却过程的计算机模拟软件。
它可以模拟塑料在模具中的填充过程、冷却过程以及制品的收缩和变形情况。
通过Mo ld fl ow模拟,可以对产品的性能、变形和残余应力等进行预测和优化。
第一主方向残余应力的影响因素第一主方向残余应力是指沿着塑料制品形成方向的应力分量。
它受到以下因素的影响:1.材料特性:不同的塑料材料具有不同的热膨胀系数和收缩率,这会导致残余应力的差异。
2.模具设计:模具的结构和尺寸对于残余应力的分布有重要影响。
例如,模具的冷却系统设计合理与否将直接影响到材料的冷却速度和收缩程度。
3.工艺参数:注塑工艺中的温度、压力和冷却时间等参数也会对残余应力的形成产生影响。
第一主方向残余应力的分析方法为了准确分析第一主方向残余应力,可以采用以下方法:1.Mo ld fl ow模拟:通过Mo ld fl ow软件进行模拟,可以得到塑料制品在成型过程中的填充和冷却过程,以及残余应力的分布情况。
2.样品测量:可以通过在注塑成型后测量塑料制品的收缩率和变形程度,并结合力学性能测试,来分析残余应力的大小和分布情况。
3.数值模拟:通过有限元分析等数值模拟方法,可以将塑料材料进行离散化,进行残余应力场的计算和分析。
结论第一主方向残余应力是注塑成型过程中不可忽视的因素,对于产品的性能和稳定性具有重要影响。
通过合理的材料选择、模具设计和工艺参数控制,以及采用M old f lo w模拟和其他分析方法,可以准确预测和优化残余应力,提高塑料制品的质量和市场竞争力。
注塑件 残余应力

注塑件 残余应力注塑件在制造过程中,由于塑料材料的流动性、填充、冷却、固化等过程,会产生残余应力。
残余应力是指在塑料件内部存在的未平衡的应力状态,这种应力可能导致注塑件在后续使用过程中出现变形、开裂等现象。
残余应力的产生主要原因有以下几点:1. 材料流动性:在注塑过程中,塑料熔体在模具中流动,由于分子间摩擦和分子取向的变化,会产生应力。
2. 填充过程:塑料熔体填充模具时,不同部位的填充速度和温度差异会导致内部应力的分布不均匀。
3. 冷却过程:注塑件在冷却过程中,内外部温度差异引起的收缩率不同,从而产生应力。
4. 固化过程:塑料件在固化过程中,分子链的交联会导致应力的产生。
5. 脱模过程:注塑件在脱模时,由于模具与塑料件之间的摩擦力和塑料件自身收缩,会产生应力。
为了降低注塑件的残余应力,可以采取以下措施:1. 选择合适的材料:选择流动性好、收缩率低、耐疲劳的塑料材料。
2. 优化模具设计:模具设计时,考虑塑料件的壁厚、冷却水道、模具材料等因素,以降低应力集中和冷却速度差异。
3. 控制注塑工艺:合理设置注塑参数,如注射速度、压力、保压时间等,以减小残余应力。
4. 采用后处理工艺:例如退火、喷涂、热处理等,以消除或降低残余应力。
5. 检测与评估:采用无损检测方法,如X射线、超声波等,对注塑件的残余应力进行检测和评估,以确保其在使用过程中的安全性。
总之,解决机械制造业残余应力与加工变形问题的企业,具备残余应力检测能力、数字化仿真能力、残余应力与加工变形解决能力、数字化工艺设计能力。
在残余应力与变形控制领域,应开发自主创新的产品、技术及先进的解决方案,尤其在轻型薄壁金属零件变形与控制方面处于世界领先地位。
【干货】塑料制品为何存在内应力,如何检测并解决?

【干货】塑料制品为何存在内应力,如何检测并解决?一、什么是内应力?塑料内应力是指在塑料熔融加工过程中由于受到大分子链的取向和冷却收缩等因素影响而产生的一种内在应力。
几乎所有塑料制品都会不同程度地存在内应力,尤其是塑料注射制品的内应力更为明显。
内应力的存在不仅使塑料制品在储存和使用过程中出现应力开裂和翘曲变形,也影响塑料制品的力学性能、光学性能、电学性能及外观质量等。
内应力的存在会出现以下常见危害:(1)开裂:因为应力的存在,在受到外界作用后(如移印时接触到化学溶剂或者烤漆后端时高温烘烤),会诱使应力释放而在应力残留位置开裂。
开裂主要集中在浇口处或过度填充处。
图:内应力导致的开裂(2)翘曲及变形:因为残留应力的存在,因此产品在室温时会有较长时间的内应力释放或者高温时出现短时间内残留应力释放的过程,同时产品局部存在位置强度差,产品就会在应力残留位置产生翘曲或者变形问题。
(3)产品尺寸变化:因为应力的存在,在产品放置或后处理的过程中,如果环境达到一定的温度,产品就会因应力释放而发生变化。
图:内应力导致的发亮、发白图:内应力集中处产生彩虹纹(透明产品)二、5种常见塑料测试应力开裂的方法材料名测试应力开裂方法称PMMA 制品用酒精:水=9:1溶液中浸15分钟后取出,放置1小时后观察,若开裂则存在应力。
应进行退火(韧化)处理:热风循环/除湿机器,在低于材料热变形温度10-15℃情况下进行约1h的处理。
红外线退火可在热变形温度基础上提高10℃,时间约10-15min即可。
PC 将PC制品浸入四氯化碳溶液中,以制品发生开裂破坏所需的时间来判断应力的大小,时间越长则应力越小。
如果浸5-15秒就开裂,说明应力很大;如果浸1-2分钟不出现裂纹,说明内应力很小POM 将经过热处理后的制品,放入30%盐酸溶液中浸渍30分钟,若不出现裂纹,说明制品中残存的内应力较小ABS 将制品浸入冰醋酸中,5-15秒内出现裂纹,则说明制品内应力大;而2分钟后无裂纹出现,则表明制品内应力小PA PA材料消除方法:小部件在沸水中泡煮约2h,尺寸大的部件应采用悬挂式,在蒸汽房里保持吸湿至水分平衡。
注塑件 残余应力
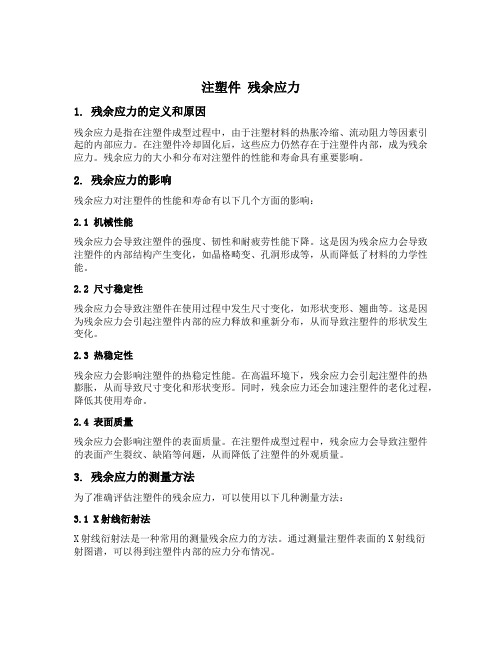
注塑件残余应力1. 残余应力的定义和原因残余应力是指在注塑件成型过程中,由于注塑材料的热胀冷缩、流动阻力等因素引起的内部应力。
在注塑件冷却固化后,这些应力仍然存在于注塑件内部,成为残余应力。
残余应力的大小和分布对注塑件的性能和寿命具有重要影响。
2. 残余应力的影响残余应力对注塑件的性能和寿命有以下几个方面的影响:2.1 机械性能残余应力会导致注塑件的强度、韧性和耐疲劳性能下降。
这是因为残余应力会导致注塑件的内部结构产生变化,如晶格畸变、孔洞形成等,从而降低了材料的力学性能。
2.2 尺寸稳定性残余应力会导致注塑件在使用过程中发生尺寸变化,如形状变形、翘曲等。
这是因为残余应力会引起注塑件内部的应力释放和重新分布,从而导致注塑件的形状发生变化。
2.3 热稳定性残余应力会影响注塑件的热稳定性能。
在高温环境下,残余应力会引起注塑件的热膨胀,从而导致尺寸变化和形状变形。
同时,残余应力还会加速注塑件的老化过程,降低其使用寿命。
2.4 表面质量残余应力会影响注塑件的表面质量。
在注塑件成型过程中,残余应力会导致注塑件的表面产生裂纹、缺陷等问题,从而降低了注塑件的外观质量。
3. 残余应力的测量方法为了准确评估注塑件的残余应力,可以使用以下几种测量方法:3.1 X射线衍射法X射线衍射法是一种常用的测量残余应力的方法。
通过测量注塑件表面的X射线衍射图谱,可以得到注塑件内部的应力分布情况。
3.2 激光光弹法激光光弹法是一种非接触式的测量方法。
通过激光光束的照射和接收,可以测量注塑件表面的应力分布情况。
3.3 数值模拟方法数值模拟方法是一种计算机辅助的测量方法。
通过建立注塑件的有限元模型,可以模拟注塑件成型过程中的应力分布情况。
4. 残余应力的消除和控制为了降低注塑件的残余应力,可以采取以下措施:4.1 优化注塑工艺参数通过调整注塑工艺参数,如注塑温度、注塑压力、注塑速度等,可以改变注塑件的冷却固化过程,从而减少残余应力的产生。
聚碳酸酯光学制品注塑成型的残余应力

聚碳酸酯光学制品注塑成型的残余应力介绍聚碳酸酯是目前应用最广泛的热塑性工程塑料之一,其具有良好的力学性能、耐热性和耐化学性,因此被广泛应用于光学、电子、汽车、医疗等领域。
而注塑成型是制造聚碳酸酯光学制品的主要工艺之一,但残余应力是注塑成型的一个重要问题。
本文将从聚碳酸酯的特性、注塑成型的原理和影响残余应力的因素三个方面来探讨聚碳酸酯光学制品注塑成型的残余应力问题。
聚碳酸酯的特性聚碳酸酯是一种透明、高强度、高韧性、耐热性、耐化学性、易加工的热塑性工程塑料。
它具有以下特点:1.高强度:聚碳酸酯的强度比普通塑料高出1.5倍以上。
2.高透明度:聚碳酸酯的光透明度比玻璃高出1.2倍。
3.耐热性:聚碳酸酯的耐热性比普通塑料高出20℃左右。
4.耐化学性:聚碳酸酯的耐化学性好,能耐受酸、碱、有机溶剂等化学物质的侵蚀。
5.易加工:聚碳酸酯易于成型、吹塑、注塑等加工方式。
注塑成型的原理注塑成型是将熔化的塑料通过注塑机的喷嘴注入到模具的腔中,然后在高压下冷却固化为成型品。
这是目前最常用的制造塑料制品的方法,它具有以下优点:1.生产成本低:注塑成型在制造大批量产品时效率高,生产成本较低。
2.高精度:注塑成型可以制造高精度、复杂的塑料制品。
3.材料选择范围大:注塑成型可以处理多种类型和品质的塑料。
然而,注塑成型也存在一些缺点,如制品易产生残余应力等。
影响残余应力的因素注塑成型的过程中,塑料的分子会因加压和冷却而产生应力。
残余应力是指人为造成的、材料在工艺加工过程中留下的,流程结束后未完全消失的应力。
残余应力一旦产生,会直接影响光学性能、形态稳定性及使用寿命,其产生原因主要有以下几个方面:1.注塑成型参数的设置:注塑机的压力和温度设置、注塑速度、压力保持时间等因素会直接影响注塑成型的质量和残余应力的产生。
2.模具设计:模具的结构、阀门位置、物料流动情况等都会影响注塑成型的质量和残余应力的产生。
3.塑料性质:塑料的性质差异也会对残余应力产生影响,比如聚酯的残余应力一般比聚碳酸酯大。
一文看懂注塑零件的残余应力-精

注塑制品的残余应力图解熔融塑料填充流动过程中的剪切应力是造成注塑件内应力的原因。
如果这种剪切应 力过大或分布不均匀,会造成尺寸变化、分子链断裂、局部残余应力过大、制品强度下降。
由于制品透明,可以通过透光程度的不同来观察残余应力的大小和分布。
图片内是 透明件的透光照片。
暗处是应力比较高的地带。
为了放大透光度反差,人们使用简单仪器来 进行观察。
另外,注塑技术人员们也经常利用这种现象来解决自己的难题。
比如,他们在试模 时先使用透明材料试验,然后观察试验制品的残余应力情况,据此判断流动情况,判断模具 是否合理。
改进后再用正常的塑料来进一步调试,直至模具验收合格。
透明注塑件因其优异的性价比得到越来越广泛的应用,但是残余应力的存在严重的 影响了它的使用性能,特别是机械性能和光学性能。
在注塑过程中,复杂的热力过程形成了残余应力,通常认为残余应力包括热应力与 流动应力两部分。
用光弹法测量了一系列从薄到厚的聚碳酸酯 PC 平板注塑件,发现随着产品厚度的增 加,残余应力的分布形态呈现出规律性的变化: 1.当平板厚度小于某一数值时,残余应力 沿熔体充填方向排布发展; 2.当厚度大于某一数值时,残余应力环绕产品形状排布发展; 3.当厚度介于两个临界值之间时,残余应力的分布同时存在上述两种趋势; 4.残余应力 分布形态发生变化时的厚度临界值与注塑材料有关,即残余应力的分布形态和构成是由产品 的材料和厚度决定的。
对于薄壁制品,主要为流动残余应力;对于厚壁制品,主要为热残余应力。
通过测量聚碳酸酯 PC 和聚苯乙烯 PS 平板不同成型条件下,制品上靠近浇口、产品中 部和充填末端三个典型位置的透光率和雾度,发现: 1.透光率基本上是材料固有的性能, 与成型条件和产品上的位置关系不大。
三种常用透明塑料透光率的大小顺序:PMMA>PS> PC. 2.雾度受到成型条件和位置的显著影响,但透明注塑件光学性能的大小随成型条件的变化对于产品是整体的,各位置一致。
塑胶产品残余应力的分析
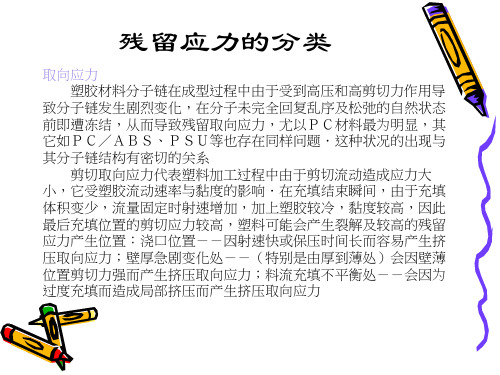
應力的危害
開裂:因為應力的存在,在受到外界作用後(如移印時接觸到化學溶劑或者烤漆後端時高溫烘烤),會誘使應力釋放而在應力殘留位置開裂。開裂主要集中在澆口處或過度填充處。翹曲及變形:因為殘留應力的存在,因此產品在室溫時會有較長時間的內應力釋放或者高溫時出現短時間內殘留應力釋放的過程,同時產品局部存在位置強度差,產品就會在應力殘留位置產生翹曲或者變形問題。產品尺寸變化:因為應力的存在,在產品放置或後處理的過程中,如果環境 達到一定的溫度,產品就會因應力釋放而發生變化。
模具設計及成型控制:在模具設計中,要注意避免尖角的存在而形成應力集中,要注意水路設計,保證冷卻均勻,避免因為冷卻不均而產生局部收縮應力,還要注意澆口位置的放置,避免流程太長導致不同位置壓力傳遞不同,而產生不同收縮程度導致應力翹曲變形。
THE END
9、静夜四无邻,荒居旧业贫。。10、雨中黄叶树,灯下白头人。。11、以我独沈久,愧君相见频。。12、故人江海别,几度隔山川。。13、乍见翻疑梦,相悲各问年。。14、他乡生白发,旧国见青山。。15、比不了得就不比,得不到的就不要。。。16、行动出成果,工作出财富。。17、做前,能够环视四周;做时,你只能或者最好沿着以脚为起点的射线向前。。9、没有失败,只有暂时停止成功!。10、很多事情努力了未必有结果,但是不努力却什么改变也没有。。11、成功就是日复一日那一点点小小努力的积累。。12、世间成事,不求其绝对圆满,留一份不足,可得无限完美。。13、不知香积寺,数里入云峰。。14、意志坚强的人能把世界放在手中像泥块一样任意揉捏。15、楚塞三湘接,荆门九派通。。。16、少年十五二十时,步行夺得胡马骑。。17、空山新雨后,天气晚来秋。。9、杨柳散和风,青山澹吾虑。。10、阅读一切好书如同和过去最杰出的人谈话。11、越是没有本领的就越加自命不凡。12、越是无能的人,越喜欢挑剔别人的错儿。13、知人者智,自知者明。胜人者有力,自胜者强。14、意志坚强的人能把世界放在手中像泥块一样任意揉捏。15、最具挑战性的挑战莫过于提升自我。。16、业余生活要有意义,不要越轨。17、一个人即使已登上顶峰,也仍要自强不息。
注塑件 残余应力

注塑件残余应力摘要:1.注塑件的概述2.残余应力的定义和产生原因3.残余应力对注塑件的影响4.减少残余应力的方法5.总结正文:一、注塑件的概述注塑件是通过注塑成型工艺制成的塑料制品,广泛应用于日常生活、工业生产等领域。
由于注塑件的制造工艺和材料性能等因素,其在使用过程中可能会产生一种现象,即残余应力。
二、残余应力的定义和产生原因残余应力是指在注塑件加工和使用过程中,由于内外应力不平衡而残留在制品内部的应力。
残余应力的产生原因主要有以下几点:1.注塑成型过程中的温度分布不均,导致内外冷却速度不同,从而产生应力。
2.注塑件的结构设计不合理,导致应力集中。
3.材料性能和工艺参数的波动,使得注塑件的应力分布不均。
4.后处理工艺不当,如焊接、热处理等,也会导致残余应力的产生。
三、残余应力对注塑件的影响残余应力对注塑件的性能和使用寿命产生重要影响,主要表现在以下几个方面:1.降低注塑件的强度和刚度,影响其使用性能。
2.促使注塑件变形和开裂,影响其外观和功能。
3.加速注塑件的老化,降低其使用寿命。
4.影响注塑件的疲劳性能和蠕变性能,可能导致在使用过程中出现意外损坏。
四、减少残余应力的方法为了提高注塑件的性能和使用寿命,需要采取措施减少残余应力:1.优化注塑件的结构设计,避免应力集中。
2.合理选择材料和工艺参数,保证注塑件的应力分布均匀。
3.控制注塑成型过程中的温度分布,使内外冷却速度趋于一致。
4.采用适当的后处理工艺,避免产生新的残余应力。
5.对注塑件进行热处理或退火处理,以消除残余应力。
五、总结注塑件残余应力是由于加工和使用过程中内外应力不平衡而产生的,对注塑件的性能和使用寿命具有重要影响。
注塑件应力痕详解

肉厚0.8
肉厚1.4
現行對策:將此面 加厚0.2mm.
現行對策:R角加大
現行對策:外觀面 送咬花.
應力痕問題改善方案(實際執行方案)
表面咬花HNDS-05
修改前 修改後(客戶設變改産品)
應力痕問題
制品外觀面應力痕
應力痕問題發生原因
外觀面應力痕的背面存在肉厚過渡不夠平緩.
應力痕問題改善方案
外觀面應力痕的背面存在肉厚過渡做到很平緩,基本OK.
應力痕問題發生原因(總結)
mm
1.0 mm
0.6 mm
分化過渡不夠 , 目前 1.4/(1.00.6)= 3.5 ( 太小 , 外加調機又
受限於 page1 肉厚問題 ) 建議 3d 結構修改加大分化 , 由
1.4 加到 2.8 即 2.8/(1.0-0.6)=7 , 或是盡可
能的做到最大至少 5 倍 分化過渡解應力痕問題依模廠經驗
慢速冷却,高结晶度,高收缩率
快速冷却,低结晶度,低收缩率
因不均勻冷卻造成成品內分子鏈的不均勻收縮,當成品溫度快速冷卻到塑膠的凝固 溫度以下時,冷卻收縮造成分子鏈間應力無法完全釋放,此種情況是屬於冷卻所形成
的應力.
(3)結晶作用或模內壓力產生的殘留應力
結晶性材料之不平衡結晶作用或是模穴壓力對不同位置分子鏈之不同影響都會形成 殘留應力
原因分析
(1)剪切流動造成的流動應力 (2)冷卻收縮造成的熱應力 (3)結晶作用或模內壓力產生的殘留應力
(1)剪切流動造成的流動應力
(1) 剪切流動(Shear Flow)
固定
移动
固定
固定
(2) 剪切速率(Shear Rate)
慢速移动
快速移动
注塑件 残余应力
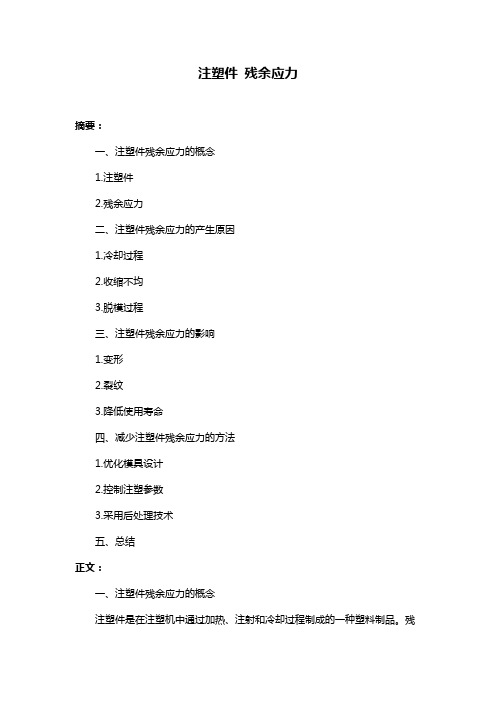
注塑件残余应力摘要:一、注塑件残余应力的概念1.注塑件2.残余应力二、注塑件残余应力的产生原因1.冷却过程2.收缩不均3.脱模过程三、注塑件残余应力的影响1.变形2.裂纹3.降低使用寿命四、减少注塑件残余应力的方法1.优化模具设计2.控制注塑参数3.采用后处理技术五、总结正文:一、注塑件残余应力的概念注塑件是在注塑机中通过加热、注射和冷却过程制成的一种塑料制品。
残余应力是指在注塑件生产过程中,由于冷却收缩、脱模等外力作用,使得塑料内部产生的一种潜在的应力。
这种应力在制品内部形成一个平衡状态,但如果受到外部因素的影响,可能会引发制品变形、裂纹等问题。
二、注塑件残余应力的产生原因1.冷却过程:在注塑件冷却过程中,由于塑料的热膨胀系数和冷却速度不同,容易产生收缩不均,从而导致内部应力的产生。
2.收缩不均:由于模具设计不合理、浇口位置不当等原因,使得塑料在冷却过程中收缩不均,从而形成残余应力。
3.脱模过程:在脱模过程中,如果脱模力过大或过小,都可能导致制品内部产生应力。
三、注塑件残余应力的影响1.变形:残余应力使制品在存放、使用过程中容易发生变形,影响制品的外观和使用性能。
2.裂纹:当残余应力超过制品的强度极限时,容易在制品表面形成裂纹,导致制品报废。
3.降低使用寿命:残余应力会降低制品的使用寿命,严重时可能导致制品在使用过程中突然损坏。
四、减少注塑件残余应力的方法1.优化模具设计:合理设置模具冷却水道,确保冷却速度均匀;选择合适的模具材料,提高模具刚性;合理设置浇口位置,减小收缩变形。
2.控制注塑参数:合理选择注射速度、压力、时间和温度等注塑参数,降低残余应力的产生。
3.采用后处理技术:通过热处理、时效处理等方法,消除或减小残余应力,提高制品的稳定性和使用寿命。
综上所述,注塑件残余应力对制品的质量、使用寿命和性能具有重要影响。
要减少残余应力,需要从模具设计、注塑参数控制和后处理技术等方面进行优化。
注塑产品应力痕解决方案

注塑产品应力痕解决方案注塑产品在生产过程中容易出现应力痕,这是指产品表面或内部出现的细小裂纹或白化现象。
应力痕的存在会降低产品的质量,甚至影响产品的使用寿命。
因此,寻找有效的解决方案对于提高注塑产品的质量至关重要。
要解决注塑产品应力痕问题,就需要从原料的选择开始。
合适的原料能够减少产品在注塑过程中的收缩和变形,从而降低应力痕的产生。
在选择原料时,应根据产品的具体要求选择合适的塑料类型和牌号,并确保原料质量稳定可靠。
在注塑工艺的控制上也要下功夫。
注塑过程中,合理的注射速度、注射压力和注射温度等参数的控制,能够有效地减少应力痕的产生。
特别是在注射速度方面,过快的注射速度容易导致产品内部产生过大的应力,从而形成应力痕。
因此,在注塑工艺中需要根据产品的特点和要求,调整合适的注射速度,以确保产品的质量。
模具设计也是解决应力痕问题的重要环节。
合理的模具设计能够减少产品在注塑过程中的应力集中,从而降低应力痕的产生。
在模具设计中,应尽量避免产品出现过薄或过厚的部位,以及棱角过于尖锐的结构,这些都容易导致应力集中,产生应力痕。
同时,还应合理设置产品的排气系统,以避免气泡的产生对产品质量的影响。
合理的注塑温度控制也是降低应力痕的关键之一。
过高或过低的注塑温度都会导致产品在注塑过程中产生应力,从而引发应力痕。
因此,在注塑过程中,应根据原料的特性和产品的要求,控制好注塑温度,确保产品在注塑过程中能够充分熔融和流动,减少应力的产生。
适当的后处理也能够减少应力痕的产生。
例如,对于一些长条形或薄壁结构的产品,可以通过热处理或冷却处理等方式,降低产品内部的应力,减少应力痕的形成。
同时,在产品的后处理过程中,也要注意避免产生新的应力痕,例如避免过度切割或加工等操作。
注塑产品应力痕的解决方案主要包括原料选择、注塑工艺控制、模具设计、注塑温度控制和后处理等方面。
通过合理的控制和优化这些环节,可以有效地降低应力痕的产生,提高注塑产品的质量。
注塑塑件应力痕

注塑塑件应力痕
材料在成型过程中形成的不平衡构象,在成型之后不能立即恢复到与环境条件相适应的平衡构象,是注塑制品存在内应力的主要原因。
另外,外力使制件产生强迫高弹形变也会在其中形成内应力。
应力痕大多出现在靠近分型面的产品边缘上。
是由无数与料流方向垂直的拉伸取向分子和它们之间的微细距离组成的集合体。
在应力痕方向上尚存在高分子连接相,因而应力痕还不是裂缝,在适当的加热下,有可能使拉伸取向分子回复自然卷曲状态而使应力痕消退。
具体解决措施:
(1)生產過程注意保持模板分型面的緊密吻合,特別是型腔周圍區域,一定要處於真正充分的鎖模力下,避免縱向和橫向脹模。
(2)降低注射壓力、時間和料量,減少分子的取向。
(3)在模面應力痕位置塗油質脫模劑,一方面使這個位置不易傳熱,高溫時間維持多一些,另一方面使可能出現應力痕受到抑制。
(4)改進模具設計。
如採用彈性變形量較小的材料製作模具,加強型腔側壁和底板的機械承載力,使之足以承受注射時的高壓衝擊和工作過程溫度的急劇升高,對應力痕易發區給予較高的溫度補償,改變料流方向,使型腔內的流動分布合理。
(5)考慮換料。
残留应力的发生原因与解决方法

残留应力的发生原因与解决方法残留应力(residual stress)是指在物体内部出现的存在的应力。
这些应力可能是由于外部加载(如机械变形、热变形)或内部因素(如材料非均匀性、相变或相变消失)引起的。
残留应力对材料的物理和力学性能有着显著影响,因此了解残留应力的发生原因和解决方法对于确保产品质量、延长材料寿命以及保证安全至关重要。
1.加工变形:在材料的加工过程中,通常会涉及到冷加工、热加工或组合加工。
这些加工过程中,材料会发生塑性变形或热变形,从而导致残留应力的产生。
2.相变或相变消失:一些材料在加工或使用过程中会发生相变或相变消失,这一过程中会伴随着材料的体积变化,从而导致残留应力的生成。
3.高温冷却:在高温条件下制造或使用的材料,在冷却过程中由于不同部分的冷却速率不同,会导致残留应力的产生。
4.材料非均匀性:材料的组织结构或成分分布不均匀会导致局部性残留应力的产生。
对于残留应力的解决方法,可以采取以下几种措施:1.适当的材料选择和热处理:在材料设计和选材过程中,应考虑到材料的物理和化学性质,选择适合的材料和热处理方法,从而尽量减少残留应力的产生。
2.控制加工过程:在材料的加工过程中,应采取适当的措施,如合理选择加工方法、工艺参数和工艺流程,以减少材料的塑性变形或热变形,从而减小残留应力的产生。
3.应力释放和退火处理:对于已经产生的残留应力,可以通过应力释放或退火处理来减轻或消除这些应力。
应力释放是指在材料中引入一些切口或裂纹,以引发局部断裂来释放应力。
而退火处理则是通过加热材料使其达到临界温度,然后在合适的冷却速率下减小残留应力。
综上所述,残留应力的发生原因主要包括加工变形、相变或相变消失、高温冷却以及材料非均匀性等。
对于解决残留应力的方法,可以从材料选择和热处理、控制加工过程、应力释放和退火处理以及残留应力的测量和监测等方面进行考虑。
通过合理的方法和措施,可以减小或消除残留应力,从而提高材料的性能和使用寿命。
塑胶产品应力痕原因

注塑加工生产时为什么会产生应力痕
注塑加工
在注塑加工生产的成品上,常见的ABS、PP、PC,我们会看到成型的产品表面会有发白、发亮的应力痕出现,也就是常称“光印、骨影”,这些就是内应力造成的结果,顶针应力痕、镶件应力痕、肉厚差应力痕,这些缺陷在放置一段时间后会有所消减。
但我们需要从源头看下究竟是什么样的原因造成了应力痕的出现。
1.成型产品的结构
(1)产品肉厚胶位的突然变化,而且壁厚相差过大,都会导致内应力的产生。
2、塑料注塑模具
(1)塑料注塑模具浇口附近会出现不规则应力痕,而顶针、斜顶应力痕形成的因素会更为多一点;
(2)镶件配合不紧,在高压的环境下填充时间过长,会导致镶件的松动,会产生应力;
(3)模具变形或模具装配问题,如注塑过程中顶针板变形,顶针、顶块稍微后退等,都有可能造成应力痕
(4)模具部分过热,冷却不均匀,冷却水道离应力痕产生部位太远。
3.成型工艺和使用材料
(1)随着保压压力和保压时间的增加,最先开始的是肉厚差应力痕、顶针斜顶应力痕、然后是肉厚差应力痕,最后是浇口附近不规则的应力痕;
(2)外观平面或弧面形成明显的应力痕,胶厚突变,致使塑胶件薄壁在冷却的过程中由于有从外到的冷却过程,使得冷却速率不一致,冷却的塑胶对先冷却的产生各种各样的作用应力;
(3)保压压力太高、模温太低、料温太低。
- 1、下载文档前请自行甄别文档内容的完整性,平台不提供额外的编辑、内容补充、找答案等附加服务。
- 2、"仅部分预览"的文档,不可在线预览部分如存在完整性等问题,可反馈申请退款(可完整预览的文档不适用该条件!)。
- 3、如文档侵犯您的权益,请联系客服反馈,我们会尽快为您处理(人工客服工作时间:9:00-18:30)。
一、塑膠殘留應力介紹當一塑膠成品在應用上發生破裂或破壞時,就材料力學的觀點,即表示該塑膠件在破壞區域上,其所承受之應力數值總合超過了材料本身之物性強度數值。
因此要解決成品在使用上的破壞或破裂問題,就必須要從如何增加材料物性強度或從如何減少成品應力值來著手。
塑膠製品承受的應力作用通常可依應力來源區分為外部應力及內部應力兩種,外部應力是成品在使用時所遭受之外力作用,此部分將視產品應用場合而定,通常是無法控制其程度,一般產品設計者會依照常態之外部應力值,乘上一安全係數值來設計產品之強度。
而內部應力通常是成品在加工成型過程中所產生而留存在成品內部。
所以要有效解決塑膠成品之破壞問題,唯有降低應力作用或提高材料強度兩種方法。
然而對於塑膠成型加工業者而言,如何使用較適當之加工條件,來防止材料強度降低及避免在加工時產生過大殘留內部應力則是最重要之議題。
所以就產品設計者或塑膠成型加工者而言,通常需要瞭解塑膠件發生破壞之成因與產生破壞之位置與破壞之型態,才能有效分析解決成型及設計上的問題點。
塑膠材料由於具有高黏特性,所以一般在成型加工時都需要利用高溫、高壓、高剪切等加工條件,來有效降低塑膠熔膠黏度至容易成型加工之範圍,另外由於塑膠具低的熱傳導係數,是熱的不良導體,所以在高溫成型後需要長時間方能達到均勻溫度之冷卻。
然而現代塑膠射出成型加工,一般為求高效益快速生產,所以對於射出成型週期都盡量縮短,而所對應之射出成型條件就需要要求射速快、冷卻時間短,而對於塑膠成品而言過大之速度差或不均勻冷卻,往往會造成成品內部形成應力。
所謂塑膠殘留應力就是指塑膠成品在經過製造或成形過程後,在無外力作用下或無溫度梯度存在時,物體內部仍維持承受應力之狀況。
通常塑膠件常見之內部應力可分為兩種,一種是剪切流動造成之流動應力,另一種是冷卻收縮所造成之熱應力。
塑膠材料在成型過程中會因為高剪切作用造成分子鏈結構的高度定向現象,此種是屬於熔膠剪切流動所形成之應力,另外則是因不均勻之冷卻造成成品內分子鏈的不均勻收縮,當成品溫度快速冷卻到塑膠的Tg以下時,冷卻收縮造成分子鏈間應力無法完全釋放,此種是屬於冷卻所形成之應力。
另外結晶性材料之不平衡結晶作用或是模穴壓力對不同位置分子鏈之不同影響都會形成殘留應力。
所以,所謂殘留應力就是指在塑膠成型過程中,造成分子結構不是處在最低能量之最穩定狀態,分子鏈受到流動定向影響或是受到週圍分子鏈之拘束,而呈現不穩定之高能態,所以一旦有外界能量給於此受應力作用之分子鏈,則此分子將極易釋放出應力而達到其最穩定之組態。
在一般塑膠射出成型加工過程中,由成品厚度方向來觀察,可以發現成品可依分子鏈之微觀結構差異,來區分不同之區域,如【圖一】所示。
其中A層示固化層,B層是流動高剪切層,C層是熔膠流動層,A層為塑膠充填時緊貼兩側模壁,瞬間冷卻固化的高分子鏈定向層,此部分會因為射出成型之噴流效應,而使分子鏈排向方向與流動方向相反,而B層是塑膠充填時緊靠A層固化層的高剪切區域所形成的分子鏈定向層,由於與A層具有最大之速度差,所以會形成最大之剪切流動應力效果,塑膠充填結束時本區定向層尚未完全凝固,而外層之A層固化定向層有絕熱效果,使B層熱散失不至過快,另外由於高剪切作用會產生剪切加熱作用,所以本區也是溫度最高之區域。
而C層因熔膠高溫及冷卻時間足夠,分子鏈有足夠時間鬆弛定向,故無高分子鏈定向行為,高分子鏈彼此之間較無剪切作用現象,若產品厚度有變化,則主要會影響C層厚度,若是薄件成品則C層的厚度將會變小。
【圖二】是沿厚度方向分子定向效果之分佈情況。
除了在成品厚度方向上下表面有一薄層固化層外,大部分區域是屬於熔膠流動層,而這區域主要之內部應力形成是由於不均勻冷卻造成,塑膠件厚度方向之冷卻是由與模壁接觸之成品表面開始向成品內部延伸,所以中心層是最慢冷卻之位置。
所以當塑膠成品成型後,開始進行冷卻階段時,在某一特定位置上之分子鏈會受到其外部已冷卻收縮之分子鏈牽引,所以會感受到早先冷卻收縮之分子鏈的拉伸應力。
所以嚴格來看在成品厚度方向靠近表面之區域,分子鏈是處在壓縮應力狀況,而內部區域是處於拉伸應力狀況。
【圖三】是射出成品厚度方向應力分佈情況。
【圖四】射出成品厚度方向剪切作用分佈情況。
二、殘留應力的影響塑膠成型過程所產生之殘留應力,除了會影響成品在使用上的強度外,尤其在某些二次後加工上都會造成問題。
殘留應力對塑膠成品的影響常見的有下列幾種:首先是成品的外觀尺寸變形及翹曲問題,由於剪切流動造成分子鏈的排向或是由於成品幾何造成流動的定向效果,在成品脫模時容易因應力鬆弛而造成尺寸發生變形,另外由於成品尺寸的不對稱性或在成品厚度方向冷卻收縮的不平衡性,所形成的熱應力都將造成成品在脫模後發生翹曲變形現象。
此現象對於尺寸精密度有要求或有組裝搭接性需求之塑膠射出成品,將會是一大問題。
再則塑膠件在使用上比例最高的破壞型式,當屬環境應力破壞(Environment Stress Cracking,ESC)─例如太陽UV光照射破壞、老化破壞、氣候性乾溼冷熱循環破壞等等,對此塑膠殘留應力也會造成環境應力破壞的加速。
其他像塑膠件的蠕變性破壞、疲勞性破壞等,都會因為殘留應力存在而加速加快其破壞產生。
另外塑膠件在成型過程中所產生的殘留應力,容易因為外界給於能量或驅動力來產生應力鬆弛效果,所以在塑膠成型業中最常見用來消除塑膠內部殘留應力之方法,即是退火(annealling)程式,即是將塑膠成品放入烘箱中或給於所需熱量,使定向分子鏈獲得能量而能再次去相互重排以達到最低能量之穩定結構,而應力鬆弛的驅動力除了熱能外,機械能、光能、化學能(溶劑作用)都可以達到同樣效果,然而在應力鬆弛同時也要考量成品尺寸變形之嚴重性。
一般殘留內部應力常常會造成成品在使用上或二次加工上發生問題,例如表面接著、表面電鍍或表面塗裝等工法,都會因為成品表面高度分子定向之高應力情況,而產生介面的不相容性。
另外如接觸到溶劑、化學品等也會造成在應力區域的加速劣化。
三、應力偏光檢測之理論基礎光同時具有粒子及波動之特性,所以光波可在真空中傳遞是屬於電磁波之一種,光的產生是藉由電荷振動所釋放之輻射波。
然而由於光可以向四面八方照射,所以若以自然光來做一些如干射、繞射等分光光譜觀測時,將會因為各方向光波的互相干擾而無法辨識。
因此為方便於光譜觀測及便於以簡單數學方程式來表示,所以一般常用單方向之光波來作為光源,而所謂單方向光源則是利用將白光光源,通過一單方向之光學偏光片,使其通過之光波都固定在一特定方向上。
我們可以簡單拿兩片光學偏光片依前後放置在一白光光源前,當白光通過第一片偏光片時已成一單方向光波,若旋轉第二片偏光片觀察時,將會發現當兩片偏光片成平行時,可見到白光通過;但若兩片成垂直時,則呈黑暗無光線通過,如【圖五】所示。
在存有應力之塑膠材料中,在特定平面上可將應力分成兩個主軸應力,此不均勻之應力將使材料產生兩個不同的折射率。
因此光要通過此材料時,沿二個主應力方向振動的光波彼此有不同的速率,穿出材料時,則會有相對速度差產生。
而此相位差將正比於平面上的兩個主軸應力之差值。
所謂應力光學定律是指一透明塑膠材料當受應力時,其折射率會隨著所受應力變化而改變,當物體的應力狀態和光交互作用,則可由光彈條紋可推知物體的應力狀態。
光彈性量測應力的方法其主要優點在於可瞭解外力作用瞬間或成形定型後,測試品整體的應力場分佈,可實際用於產品QC檢測上。
透明塑膠材料遭受應力時將產生雙折射現象,當光線穿透具雙折射率材料時,光在材料內進行的速度也會不同。
當偏極光進入有應力作用之雙折射材料時,光線會分為較快速及較慢速兩光束,其速度差相對距離則稱為相位差或遲延(retardation,R)。
在單色的光彈條紋中,粗線的地方代表該點之主應力方向與x軸(或y軸)平行。
因此兩道光之相位差為整數波長,因而造成光場之明暗條紋,光場之條紋可以肉眼觀察,條紋越密集的地方,表示應力愈大,亦即是應力集中的地方,也是材料發生破壞時最先開始之處,【圖六】是應力偏光儀量測觀察應力之原理。
式(1)及式(2)是應力偏光觀測主要之理論計算公式,式中Dn表示透明材料之雙折射率,s1與s2表示材料之兩主軸應力值,A是材料之光學應力常數,t是光前進之材料厚度距離,R則是兩不同速度光線之相位差。
Dn=(n1-n2)=A(s1-s2) (1)R=(s1-s2)′t′A=Dn′t=nl (2)由應力偏光觀測所得之干涉光譜條紋,可利用式(1)及式(2)計算出材料之雙折射率及應力值。
當射出模溫接近或超過塑膠之Tg溫度時,可有效消除雙折射現象,此既是由於流動所誘發之分子定向現象,可藉由使用較高模溫來使得分子有足夠動能及足夠時間來鬆弛分子應力。
此可藉由將透明試片置於兩片正交之偏光板間,可觀察到較無散射之彩色光環,既有較多區域呈現黑暗顏色,既分子結構較無殘留應力存在。
四、應力偏光儀觀測透明塑膠件殘留應力隨著產業的不斷進步,台灣塑膠成型業已從早期低層次民生用品發展到近年來蓬勃發展的電子電器業產品,然而現階段由於傳統產業大量外移,整個經濟大環境已迫使台灣塑膠成型業者,必須思考如何開創更高附加價值之產品。
近幾年來在政府及業者共同努力下,光電產業已成為一項明星產業,舉凡平面顯示器、導光板、背光板、光纖連接器、光波導、塑膠光學鏡片、精密微小射出成型產品等,都有許多廠商爭先投入。
在蓬勃發展的塑膠光電產業中,透明性塑膠材料佔了相當大的比重,例如PMMA、PC、mCOC 等都是經常被使用到的透明性塑膠,然而對於透明性塑膠在成型過程中,因加工條件設定所衍生殘留應力問題也越來越受加工業者注重,此主要是因會殘留應力除了會影響塑膠件尺寸精度要求,同時也會造成光學特性的改變,另外對於後續加工,例如塗佈、電鍍等製程都會造成嚴重影響。
所以如何觀測塑膠光學產品之內部殘留應力,是目前光電產業上相當重要之技術。
對於光電產業常使用之透明性塑膠材料而言,目前最簡易可用來觀察材料內部殘留應力之方法,就是使用穿透式應力偏光儀,如【圖七】所示。
此方法是一種非破壞性定性觀測方法,此主要是利用塑膠受應力作用下之光彈特性,來觀測材料的雙折射率變化情形。
此由Brewster的光彈性定律理論中可知,對於受應力作用而產生應變之高分子材料,其在空間中對光線的折射率將會有方向性的不同,換言之,也就是說塑膠材料在不同方向所受之應力分量不同,其在這些方向所表現之折射率也會不同,而其折射率之差異會與所受之應力程度成正比。
塑膠是由長度很長之高分子鏈所組成,所以就微觀角度而言,在分子鏈平行與垂直方向所表現之物性並不一致,此就是高分子鏈的異方向特性(anisotropic),然而就整體高分子材料而言,因分子鏈間相互糾結成一團狀結構,所以單一分子鏈之異方向特性將不易被察覺;然而若因塑膠材料在加工時所形成之應力,將造成分子鏈之高度定向作用,則塑膠材料之異方向性將會顯現,利用材料內部應力產生之雙折射率,可用來觀察入射光因前進速度之差異所產生之相位差干涉條紋,藉此來反推內部應力之分佈情形。