瞬间液相扩散连接过程数值模拟的研究进展
速凝浆液裂隙动水注浆扩散数值模拟与试验验证
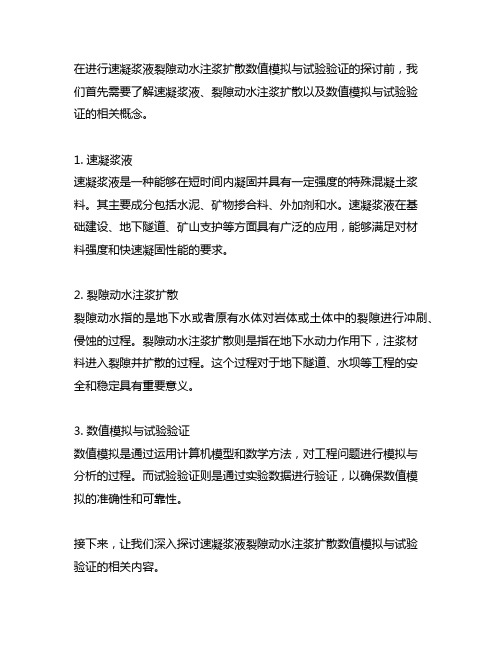
在进行速凝浆液裂隙动水注浆扩散数值模拟与试验验证的探讨前,我们首先需要了解速凝浆液、裂隙动水注浆扩散以及数值模拟与试验验证的相关概念。
1. 速凝浆液速凝浆液是一种能够在短时间内凝固并具有一定强度的特殊混凝土浆料。
其主要成分包括水泥、矿物掺合料、外加剂和水。
速凝浆液在基础建设、地下隧道、矿山支护等方面具有广泛的应用,能够满足对材料强度和快速凝固性能的要求。
2. 裂隙动水注浆扩散裂隙动水指的是地下水或者原有水体对岩体或土体中的裂隙进行冲刷、侵蚀的过程。
裂隙动水注浆扩散则是指在地下水动力作用下,注浆材料进入裂隙并扩散的过程。
这个过程对于地下隧道、水坝等工程的安全和稳定具有重要意义。
3. 数值模拟与试验验证数值模拟是通过运用计算机模型和数学方法,对工程问题进行模拟与分析的过程。
而试验验证则是通过实验数据进行验证,以确保数值模拟的准确性和可靠性。
接下来,让我们深入探讨速凝浆液裂隙动水注浆扩散数值模拟与试验验证的相关内容。
对速凝浆液裂隙动水注浆扩散数值模拟的过程进行模拟和分析。
在数值模拟中,需要考虑速凝浆液的性质、裂隙的形态和动水的作用,通过建立数学模型和运用计算机软件进行模拟计算,以预测速凝浆液在裂隙中的扩散情况和影响范围。
需要考虑工程实际中可能存在的不确定因素,如地质构造、地下水位变化等,以提高模拟结果的准确性。
进行速凝浆液裂隙动水注浆扩散试验验证。
通过在实际工程场地进行试验,注入速凝浆液并观测其在裂隙中的扩散情况,以验证数值模拟结果的准确性和可靠性。
在试验中,需要考虑速凝浆液的成分和性能、裂隙的形态及地下水的作用,以及试验过程中可能存在的干扰因素,如外界环境变化等。
综合以上两方面的内容,可以得出关于速凝浆液裂隙动水注浆扩散数值模拟与试验验证的综合结论。
通过数值模拟和试验验证的相互印证,可以获得关于速凝浆液裂隙动水注浆扩散的全面、深入和可靠的研究成果。
在这个过程中,我个人认为,需要特别关注速凝浆液的选择及其性能、裂隙动水对注浆扩散的影响机理,以及数值模拟与试验验证的互补作用。
瞬时液相连接
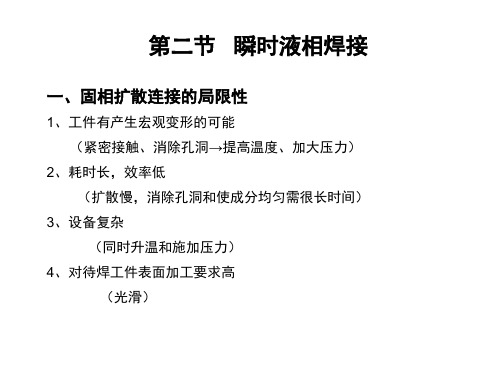
一、固相扩散连接的局限性
1、工件有产生宏观变形的可能 (紧密接触、消除孔洞→提高温度、加大压力)
2、耗时长,效率低 (扩散慢,消除孔洞和使成分均匀需很长时间)
3、设备复杂 (同时升温和施加压力)
4、对待焊工件表面加工要求高 (光滑)
二、瞬时液相扩散连接的基本特征
概念:中间层熔化形成液相,液态金属浸润母材表面填充毛细间隙。在 随后保温过程中借助液固相之间相互扩散使液相成分向高熔点侧变化, 最终发生等温凝固和成分均匀化,不会残留凝固铸态组织。
(3)等温凝固 固液界面B原子扩散进入母材,A扩散进入中间液相。 中间液相熔点提高,即导致液相凝固。(保温阶段)
(4)固相成分均匀化
temperature
接头中心区域与母材成分不一致, 进一步保温可继续均匀化,可得到成 分组织和母材几乎一致的接头。
需时间很长。
A
E
B
中间层分类: (1)低熔点合金中间层(与母材成分接近,添加少量能降低熔点的元素, 熔点低于母材) (2)能与母材发生共晶反应形成低熔点合金的中间层
初始阶段特征 (1)有液相参与,与钎焊相似。 (2)液相浸润作用,促进接触,连接压力可很小。 (3)降低了对表面加工精度的要求。
后期特征 (1)扩散使熔点提高,中间部分在保温阶段即发生等温凝固。(瞬时液 相:初期有液相) (2)钎焊温度高于使用温度。 (3)瞬时液相扩(1)中间层溶解或熔化
假设中间层能与母材发生共晶反应形
成低熔点合金。
ABA组装 (A母材,B中间层)
初期A/B界面浓差大,扩散迅速,
界面上形成共晶液相,并向母材和中 间层推移,使液相区加宽,中间层全 A 部溶解为液相。
瞬时液相扩散焊技术的研究进展
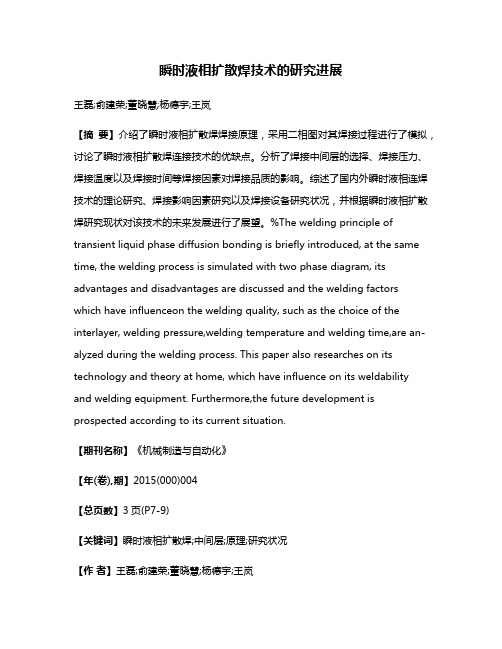
瞬时液相扩散焊技术的研究进展王磊;俞建荣;董晓慧;杨德宇;王岚【摘要】介绍了瞬时液相扩散焊焊接原理,采用二相图对其焊接过程进行了模拟,讨论了瞬时液相扩散焊连接技术的优缺点。
分析了焊接中间层的选择、焊接压力、焊接温度以及焊接时间等焊接因素对焊接品质的影响。
综述了国内外瞬时液相连焊技术的理论研究、焊接影响因素研究以及焊接设备研究状况,并根据瞬时液相扩散焊研究现状对该技术的未来发展进行了展望。
%The welding principle of transient liquid phase diffusion bonding is briefly introduced, at the same time, the welding process is simulated with two phase diagram, its advantages and disadvantages are discussed and the welding factors which have influenceon the welding quality, such as the choice of the interlayer, welding pressure,welding temperature and welding time,are an-alyzed during the welding process. This paper also researches on its technology and theory at home, which have influence on its weldabilityand welding equipment. Furthermore,the future development is prospected according to its current situation.【期刊名称】《机械制造与自动化》【年(卷),期】2015(000)004【总页数】3页(P7-9)【关键词】瞬时液相扩散焊;中间层;原理;研究状况【作者】王磊;俞建荣;董晓慧;杨德宇;王岚【作者单位】北京化工大学机电工程学院,北京100029;北京石油化工学院机械工程学院,北京102617;北京石油化工学院机械工程学院,北京102617;北京化工大学机电工程学院,北京100029;北京工业大学机械工程与应用电子技术学院,北京100022【正文语种】中文【中图分类】TG44近年来随着高新技术的发展,对新材料的需求越来越高,在现代材料结构中,不仅需要对大量同种材料进行焊接,有时也需要对异种金属材料进行焊接。
Si3N4陶瓷二次部分瞬间液相连接数值模拟
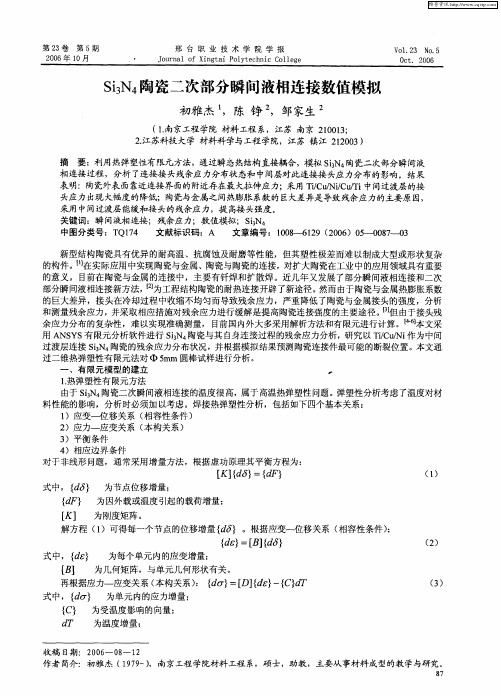
2 二次部分瞬间液相连接过程的计算模型 . 采用图 1 所示的接头形式。表 1 为母材和中间过渡层材料的基本性能。 表 1 各 种材 料物 性 参数 ’1 _
本试验用的中间过渡层 N 、C 和 T 的厚度分别为:10 a 、 1 0tn i u i 4 n 0 、8 t a
一
、
【 { ) d K】 ={F)
式中,{ 8 为节点位移增量; d }
() 1
{F) 为因外载或温度引起的载荷增量; d
[ 为刚度矩阵。 】 解方程 ()可得每一个节点的位移增量 {a 。根据应变—位移关系 ( 1 d} 相容性条件) : {c =[ ld ) d ) B {6
式中,{ } 如 为每个单元 内的应变增量;
( 2)
[】 B 为几何矩阵,与单元几何形状有关。 再根据应力一应变关系 ( 本构关系) {o} D]d }一C d : d -=[ {c _{ }T 式中,{o 为单元内的应力增量; d) - { ) 为受温度影响的向量; C
新型结构陶瓷具有优异 的耐高温 、抗腐蚀及耐磨等性能,但其塑性极差而难 以制成大型或形状复杂 的构件 。I在 实 际应用 中实现 陶瓷 与金属 、陶瓷 与 陶瓷 的连接 ,对扩 大 陶瓷在工 业 中 的应用 领域 具有 重要 J 】 的意义 。目 前在陶瓷与金属 的连接中,主要有钎焊和扩散焊 。近几年又发展了部分瞬间液相连接和二次 部分瞬间液相连接新方法 ,z 【 】 为工程结构陶瓷的耐热连接开辟了新途径 。 然而 由于陶瓷与金属热膨胀系数 的巨大差异,接头在冷却过程 中收缩不均匀而导致残余应力,严重降低了陶瓷与金属接头的强度 ,分析 和测量残余应力, 并采取相应措施对残余应力进行缓解是提高陶瓷连接强度的主要途径 。3 由于接头残 l J 但 余应力分布的复杂性 ,难以实现准确测量,目前国内外大 多采用解析方法和有限元进行计算 。[ 1 4 本文采 - 6 用 A S S有限元分析软件进行 s3 4 NY i 陶瓷与其 自身连接过程的残余应力分析, N 研究以 T C / i i u 作为中间 / N 过渡层连接 s N 陶瓷的残余应力分布状况 , i 3 并根据模拟结果预测陶瓷连接件最可能的断裂位置。 本文通 过 二 维热弹塑 性有 限元 法对 5 mm 圆棒 试样 进行 分析 。 有 限元模 型的 建立 1 弹塑性有 限元方法 . 热 由于 s3 i 陶瓷二次瞬间液相连接 的温度很高, N 属于高温热弹塑性 问题 。 弹塑性分析考虑 了温度对材 料 性 能的影 响 ,分 析 时必须加 以考 虑 。焊接 热弹 塑性分 析 ,包括如 下 四个 基本关 系 : 1 )应变—位移关系 ( 相容性条件) 2 )应力一应变关系 ( 本构关系) 3 )平衡 条件 4 )相应 边界 条件 对 于 非线形 问题 ,通常 采用 增量 方法 ,根据 虚功 原理其 平衡 方程为 :
关于扩散连接的文献综述

重庆理工大学本科生毕业设计(论文)文献综述论文题目:钛合金与不锈钢的瞬间液相扩散连接学院:材料科学与工程学院专业:焊接技术与工程姓名:学号:指导教师:完成日期:2015年1月20日瞬间液相扩散连接( TLP-DB) 方法以其独有的性能优势, 在先进材料连接领域得到广泛的重视和应用。
综述了瞬间液相扩散焊中接触熔化、液相均匀化、等温凝固以及固相成分均匀化阶段的理论模型及发展状况,并对现有模型进行了分析和讨论。
随着材料科学的发展,新材料不断涌现。
在生产应用中,经常遇到异种金属的连接问题。
焊接异种金属的方法有很多,主要有超声波焊接、熔焊、固相压力焊、熔焊、钎焊及瞬间液相扩散连接等。
钛合金与不锈钢的复合构件,能充分体现两种材料在性能与经济上的优势互补,在核动力装置、航空航天、武器装备、电子产业、医疗器械和机械制造等民用和军用行业,具有非常广阔的应用前景。
钛合金与不锈钢焊接时,由于两者的物理化学性能相差较大,且容易形成硬而脆的金属间化合物,使得接头性能难以提高。
瞬间液相扩散连接作为先进的焊接技术,特别适用于常规熔焊、接触焊、钎焊等难以解决的塑性差、熔点高和互不相溶的异种材料的连接。
在瞬间液相扩散连接的过程中加入超声波振动,对焊接件施加纵向超声波,能够提高焊接的质量,缩短焊接的时间,提高焊接的效率。
各种新型材料, 如金属间化合物具有耐高温、抗腐蚀、耐磨损等优点使其成为极具潜力的高温结构材料, 其中钛合金是潜在的航空航天材料,但是, 金属间化合物的共同缺点: 室温塑性低和高温强度差制约了它们在生产实践中的应用; 现代复合材料, 具有比强度高、比刚度大、抗疲劳性好、尺寸稳定、耐磨、抗震等优良性能, 其在航空、航天、军工等高技术领域具有极其广阔的应用前景, 但由于复合材料中基体与增强相之间物理、化学性能相差很大, 导致其焊接性很差, 很难获得理想的焊接接头; 陶瓷材料的塑性差, 冷加工困难, 难以制成大型或形状复杂的构件等, 因而这些材料都会不同程度受到实用化问题的挑战。
TP304H_12Cr1MoV异种钢管的瞬时液相扩散连接

第27卷 第2期2006年2月焊接学报TRANS ACTI O NS OF THE CH I N A W ELD I N G I N STI T UTI O NVol .27 No .2February 2006TP304H /12C r1MoV 异种钢管的瞬时液相扩散连接井晓天1, 陈思杰1,2, 卢俊峰1, 李辛庚3(1.西安理工大学材料科学与工程学院,西安 710048;2.河南理工大学材料科学与工程学院,河南焦作 454000;3.山东电力研究院,济南 250002)摘 要:用Fe N i CrSi B (A )合金作中间层,氩气保护,对12Cr1MoV 珠光体耐热钢和TP304H 奥氏体不锈钢管进行了瞬时液相扩散连接。
用正交试验的方法研究了工艺参数对接头组织和性能的影响,分析了T LP 连接接头的显微组织、断口形貌、力学性能和元素分布,确定出了合适的连接工艺参数。
研究结果表明,连接温度1240℃,等温凝固时间3m in,压力4MPa 时,接头的强度最高达到590MPa,其断口呈韧性断裂特征。
关键词:TP304H /12Cr1MoV;异种钢管;瞬时液相连接;显微组织中图分类号:TG151.1 文献标识码:A 文章编号:0253-360X (2006)02-97-05井晓天0 序 言火力发电机组随着各个部位工作温度的不同,相应地使用了不同化学成分和组织结构的钢材,因此必然会遇到异种钢的焊接问题。
其中许多部件及管道采用了12Cr1MoV 耐热钢与TP304H 不锈钢的异种钢接头。
12Cr1MoV 钢热强性和持久塑性较高,由于碳及合金元素含量较多,淬硬敏感性较大,在焊件刚性及接头应力较大时,易产生冷裂纹。
TP304H 是经固溶处理后供货的,其组织为单相奥氏体,具有高的抗蚀性、抗蠕变性和综合力学性能;但在450~850℃温度区间长时间停留,易发生晶间腐蚀。
12Cr1Mo V 与TP304H 焊接时,因接头化学成分的不均匀导致组织的不均匀,从而最终影响到接头的持久强度。
水泥浆液裂隙注浆扩散规律模型试验与数值模拟

水泥浆液裂隙注浆扩散规律模型试验与数值模拟一、本文概述本文旨在探讨水泥浆液在裂隙注浆过程中的扩散规律,通过模型试验与数值模拟相结合的方法,揭示水泥浆液在复杂裂隙网络中的扩散行为及其影响因素。
水泥浆液作为一种广泛应用的工程材料,在地下工程、岩土工程等领域具有重要的应用价值。
然而,由于裂隙网络的复杂性和不确定性,水泥浆液的扩散规律一直是工程实践中的难点问题。
因此,本文的研究具有重要的理论意义和实际应用价值。
本文将对水泥浆液的基本性质进行介绍,包括其成分、物理性能以及注浆过程中的基本原理。
在此基础上,通过设计合理的模型试验,模拟水泥浆液在裂隙网络中的扩散过程,观察浆液在不同条件下的扩散形态和分布规律。
同时,利用数值模拟方法,建立水泥浆液扩散的数学模型,对试验结果进行验证和补充。
本文将分析影响水泥浆液扩散的主要因素,包括裂隙网络的几何特征、浆液的物理性能、注浆压力以及注浆速率等。
通过对比分析不同条件下的试验结果和数值模拟结果,揭示各因素对水泥浆液扩散规律的影响机制和程度。
本文将对水泥浆液裂隙注浆扩散规律的研究进行总结,提出相应的工程应用建议。
指出目前研究中存在的问题和不足,为后续研究提供参考和借鉴。
通过本文的研究,有望为水泥浆液在裂隙注浆工程中的应用提供更为准确的理论指导和实践依据。
二、水泥浆液裂隙注浆扩散理论基础水泥浆液在裂隙中的注浆扩散是一个涉及多物理场耦合的复杂过程,包括流体力学、渗流力学、材料科学和断裂力学等多个学科的知识。
注浆过程中,水泥浆液在压力作用下通过注浆管进入岩体裂隙,并在裂隙中扩散、填充和固结,最终实现岩体的加固和封堵。
在理论基础上,水泥浆液在裂隙中的扩散行为可以通过渗流方程来描述。
渗流方程通常基于达西定律,考虑到浆液的粘性、裂隙的几何形状以及注浆压力等因素。
浆液在裂隙中的扩散还受到浆液与裂隙壁面间的相互作用影响,包括润湿角、浆液粘附力等。
这些因素共同决定了浆液在裂隙中的扩散范围和固结形态。
第七章扩散连接原理

固相扩散连接过程
目前,人们认为扩散连接包括以下三个过程 :()塑性 变形使连接表面接触;()晶界迁移和孔洞消失;()界面和 孔洞消失过程。下面分别叙述各阶段的过程和机理。 ()塑性变形使连接表面接触
固相扩散连接时,材料表面通常是进行机械加工后 再进行研磨、抛光(包括化学抛光)和清洗,加工后材料表 面在微观上仍然是粗糙的、存在许多一μ的微观凹凸,且 表面还常常有氧化膜覆盖。将这样的固体表面相互接触, 在不施加任何压力的情况下,只会在凸出的顶峰处出现接 触,如图(。初始接触区面积的大小与材料性质、表面加 工状态以及其它许多因素有关。
但由于实际的材料表面不可能完全平整和清洁,因而 实际的扩散连接过程要比上述过程复杂得多。固体金属的 表面结构如图一所示,除在微观上表面呈凹凸不平外,最 外层表面还有~的气体吸附层,主要是水蒸气、氧、和。 在吸附层之下为 ~厚的氧化层,是由氧化物的水化物、 氢氧化物和碳酸盐等组成。在氧化层之下是 ~μ的变形层 。
扩散连接的定义及其特点
扩散连接是将两待连接工件紧压在一起,置于真空或 保护气氛中加热至母材熔点以下温度,对其施加压力使两 连接表面微观凸凹不平处产生微观塑性变形达到紧密接触 ,再经保温、原子相互扩散而形成牢固的冶金结合的一种 连接方法。
可见,扩散连接过程是在温度和压力的共同作用下完 成的,但连接压力不能引起试件的宏观塑性变形。
图一 几种材料扩散连接接头拉伸断口的微 观形貌
()钛 (℃ ); (}铁(℃ ); ()不锈钢钛 (℃ ,
); ()铝钛 (℃ )
()扩散、晶界迁移和孔洞消失 与第一阶段的变形机制相比,该阶段中扩散的作用
就要大得多。连接表面达到紧密接触后,由于变形引起的 晶格畸变、位错、空位等各种缺陷大量堆集,界面区的能 量显著增大,原子处于高度激活状态,扩散迁移十分迅速 ,很快就形成以金属键连接为主要形式的接头。由于扩散 的作用,可使大部分孔洞消失,也会产生连接界面的移动 。关于孔洞消失的机制阐述如下。
瞬时液相扩散焊在焊接修补中的应用研究
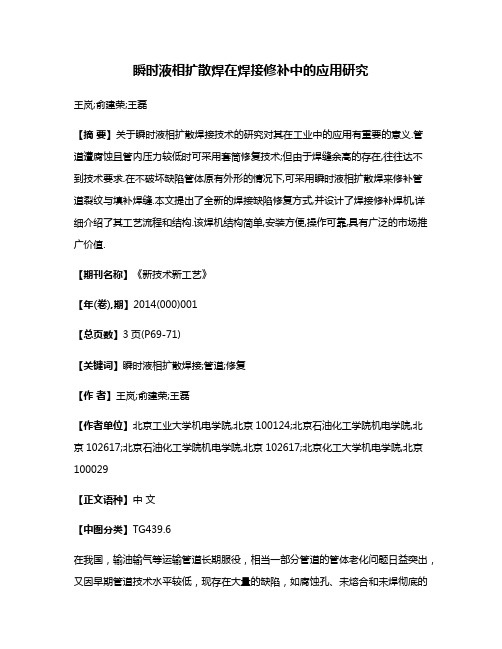
瞬时液相扩散焊在焊接修补中的应用研究王岚;俞建荣;王磊【摘要】关于瞬时液相扩散焊接技术的研究对其在工业中的应用有重要的意义.管道遭腐蚀且管内压力较低时可采用套筒修复技术;但由于焊缝余高的存在,往往达不到技术要求.在不破坏缺陷管体原有外形的情况下,可采用瞬时液相扩散焊来修补管道裂纹与填补焊缝.本文提出了全新的焊接缺陷修复方式,并设计了焊接修补焊机,详细介绍了其工艺流程和结构.该焊机结构简单,安装方便,操作可靠,具有广泛的市场推广价值.【期刊名称】《新技术新工艺》【年(卷),期】2014(000)001【总页数】3页(P69-71)【关键词】瞬时液相扩散焊接;管道;修复【作者】王岚;俞建荣;王磊【作者单位】北京工业大学机电学院,北京100124;北京石油化工学院机电学院,北京102617;北京石油化工学院机电学院,北京102617;北京化工大学机电学院,北京100029【正文语种】中文【中图分类】TG439.6在我国,输油输气等运输管道长期服役,相当一部分管道的管体老化问题日益突出,又因早期管道技术水平较低,现存在大量的缺陷,如腐蚀孔、未熔合和未焊彻底的焊缝等。
这些缺陷的存在严重威胁着管道的安全运行,多年来发生过很多原油和天然气泄漏等事故,给环境造成了很大压力。
在对这种管道进行修复的方法中,传统修复的方式往往会影响焊缝的质量,这是因为腐蚀孔、未熔合和未焊彻底的焊缝常发生在围绕焊缝的地方,当修复进行时,为了使焊缝处平整,会打磨焊缝,从而使焊缝处更薄,加重了裂纹焊缝的再一次泄漏[1]。
保证焊接质量的前提就是保证焊接管片与被修复管体的贴合度,在传统修复中,其也是影响焊接质量的重要因素;所以,要提高焊接质量,首先要保证焊接管片与管体的接合无缝隙。
特别是在修复管道缺陷为螺旋焊缝时,焊缝余高会直接影响焊件与管体外壁的贴合程度,这就会导致修复后焊缝处产生集中应力,从而降低疲劳强度,影响焊接修复的质量,如图1所示。
镍基高温合金瞬时液相扩散焊微观结构的研究
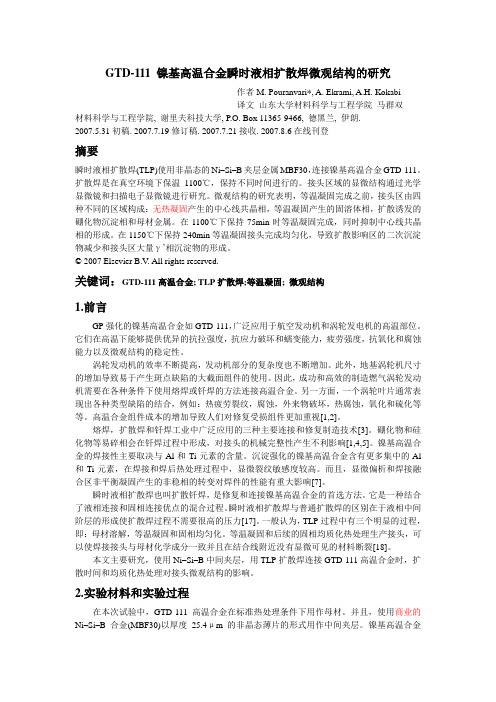
GTD-111 镍基高温合金瞬时液相扩散焊微观结构的研究作者M. Pouranvari∗, A. Ekrami, A.H. Kokabi译文山东大学材料科学与工程学院马群双材料科学与工程学院, 谢里夫科技大学, P.O. Box 11365-9466, 德黑兰, 伊朗.2007.5.31初稿. 2007.7.19修订稿. 2007.7.21接收. 2007.8.6在线刊登摘要瞬时液相扩散焊(TLP)使用非晶态的Ni–Si–B夹层金属MBF30,连接镍基高温合金GTD-111。
扩散焊是在真空环境下保温1100℃,保持不同时间进行的。
接头区域的显微结构通过光学显微镜和扫描电子显微镜进行研究。
微观结构的研究表明,等温凝固完成之前,接头区由四种不同的区域构成:无热凝固产生的中心线共晶相,等温凝固产生的固溶体相,扩散诱发的硼化物沉淀相和母材金属。
在1100℃下保持75min时等温凝固完成,同时抑制中心线共晶相的形成。
在1150℃下保持240min等温凝固接头完成均匀化,导致扩散影响区的二次沉淀物减少和接头区大量γ’相沉淀物的形成。
© 2007 Elsevier B.V. All rights reserved.关键词:GTD-111高温合金; TLP扩散焊;等温凝固; 微观结构1.前言GP强化的镍基高温合金如GTD-111,广泛应用于航空发动机和涡轮发电机的高温部位。
它们在高温下能够提供优异的抗拉强度,抗应力破坏和蠕变能力,疲劳强度,抗氧化和腐蚀能力以及微观结构的稳定性。
涡轮发动机的效率不断提高,发动机部分的复杂度也不断增加。
此外,地基涡轮机尺寸的增加导致易于产生斑点缺陷的大截面组件的使用。
因此,成功和高效的制造燃气涡轮发动机需要在各种条件下使用熔焊或钎焊的方法连接高温合金。
另一方面,一个涡轮叶片通常表现出各种类型缺陷的结合,例如:热疲劳裂纹,腐蚀,外来物破坏,热腐蚀,氧化和硫化等等。
高温合金组件成本的增加导致人们对修复受损组件更加重视[1,2]。
瞬时液相扩散焊TLP资料.
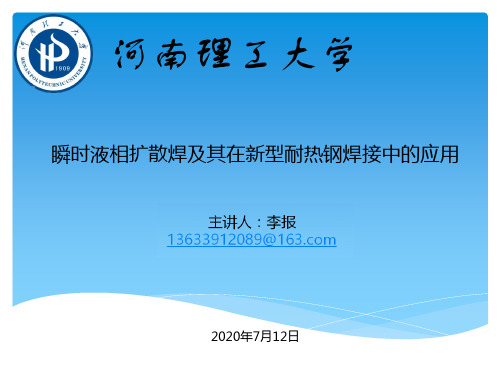
2 瞬时液相扩散焊(TLP)
a)
b)
c)
d)
e)
a)形成液相 b)低熔点元素向母材扩散 c)等温凝固 d)等温凝固结束 e)成分均匀化
2 瞬时液相扩散焊(TLP)
固态扩散连接与瞬时液相扩散对比
2 瞬时液相扩散焊(TLP)
扩散连接参数选择
扩散连接参数主要有温度、压力、时间、气氛环境和 试件的表面状态,这些因素之间相互影响、相互制约, 在选择焊接参数时应统筹考虑。此外,扩散连接时还
用液态钎料润湿母材,填充接头间隙并与母材相互扩
散实现连接焊件的方法。
1 焊接
1 焊接
目录
1 焊接 2 瞬时液相扩散焊(TLP) 3 TLP焊接新型耐热钢实例
目录
1 焊接 2 瞬时液相扩散焊(TLP) 3 TLP焊接新型耐热钢实例
2 瞬时液相扩散焊(TLP)
扩散焊
定义:在一定的温度和压力下,被连接表面相互接 触,通过使局部发生微观塑性变形,或通过被连接 表面产生的微观液相而扩大被连接表面的物理接触, 然后结合层原子间经过一定时间的相互扩散,形成 整体可靠连接的过程。
2 瞬时液相扩散焊(TLP)
原理:在金属不熔化的情况下,要形成焊接接头就必须使两待
焊表面紧密接触,使之距离达到(1~5)×10−6mm以内,在这种 条件下,金属原子间的引力才开始起作用,才可能形成金属键, 获得有一定强度的接头。实际上,金属表面无论经什么样的精 密加工,在微观上总还是起伏不平的。
2 瞬时液相扩散焊(TLP)
1 焊接
熔化焊:将两个工件连接处加热至熔化状态,连接处的
金属经历一个熔合—冷却—结晶的过程,形成焊缝,成
为一体。
焊
接
压力焊:利用焊接时施加一定压力而完成焊接的方法,
TLP扩散连接的动力学模型
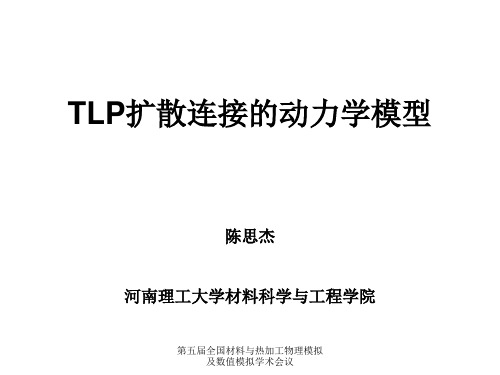
➢2、TLP等温凝固的的传统模型
第五届全国材料与热加工物理模拟 及数值模拟学术会议
图1 TLP连接的 传统模型
➢3、TG-TLP连接模型中过冷度的形成
C0-远离界面的液体成分 k-溶质分配系数 V-界面移动速度 D-液体中 溶质扩散系数
图2、TG-TLP连接模型过冷度形成示意图
第五届全国材料与热加工物理模拟 及数值模拟学术会议
➢4、 TLP 与TG-TLP连接过程比较
TLP 与TG-TLP
图3 TLP 与TG-TLP连接过程示意图
第五届全国材料与热加工物理模拟 及数值模拟学术会议
➢ 5、存在的问题及双温TLP连接模型的提出
TLP扩散连接过程中,中间层熔化阶段和液相均匀化阶段都是接 头区域(母材和中间层)熔化为液相的过程,从扩散本质上讲,是溶 质在固相区的扩散过程,受固相扩散速度的控制。中间层熔化后,有 害的难溶氧化物颗粒和杂质混在液相中,在等温凝固过程中,由于溶 质的重新分布,这些杂质分布在凝固界面的前沿。等温凝固完成后, 大部分杂质在接头中心处聚集,影响金属之间的连接。因此,接头的 剪切强度比相应母材的要低。另外,氧化物杂质分布形成的平滑连接 线降低接头的强度[23]。在凝固过程中,通过凝固理论和技术,研究 控制液固界面的形状和推进方式是改善接头性能的重要研究课题。在 传统的TLP扩散连接理论和模型的基础上,建立新的TLP扩散连接模 型,对于TLP扩散连接理论的发展具有重要的意义。TG-TLP连接工 艺模型取得了很大的突破,但存在温度梯度难于控制的问题。
第五届全国材料与热加工物理模拟 及数值模拟学术会议
➢四 结束语
1、瞬时液相扩散连接的本质就是中间层的熔化 与结晶的过程,其中的动力是溶质或降低熔点元素 (MPD)的扩散,对于一定的连接材料,首先要选择 合适的中间层,用母材加入MPD元素形成低熔点的 共晶合金做连接的中间层,对有效缩短连接时间, 提高接头的性能是十分有利的。
镍钛形状记忆合金与不锈钢异种材料焊接的研究进展
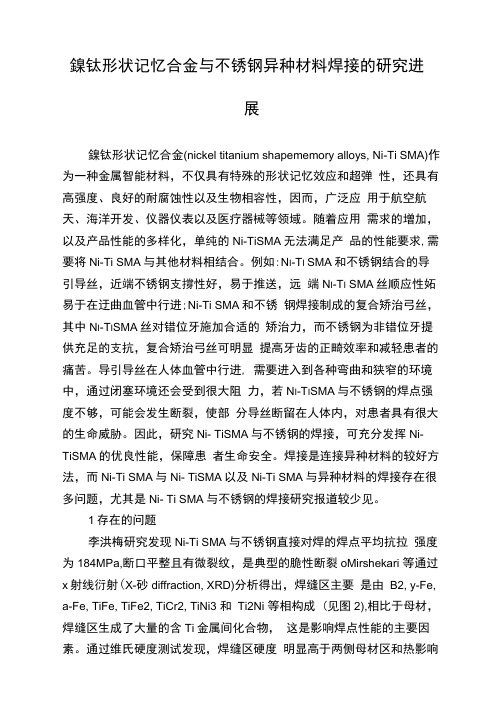
鎳钛形状记忆合金与不锈钢异种材料焊接的研究进展鎳钛形状记忆合金(nickel titanium shapememory alloys, Ni-Ti SMA)作为一种金属智能材料,不仅具有特殊的形状记忆效应和超弹性,还具有高强度、良好的耐腐蚀性以及生物相容性,因而,广泛应用于航空航天、海洋开发、仪器仪表以及医疗器械等领域。
随着应用需求的增加,以及产品性能的多样化,单纯的Ni-TiSMA无法满足产品的性能要求,需要将Ni-Ti SMA与其他材料相结合。
例如:N I-T I SMA和不锈钢结合的导引导丝,近端不锈钢支撐性好,易于推送,远端N I-T I SMA丝顺应性妬易于在迂曲血管中行进;Ni-Ti SMA和不锈钢焊接制成的复合矫治弓丝,其中N I-T I SMA丝对错位牙施加合适的矫治力,而不锈钢为非错位牙提供充足的支抗,复合矫治弓丝可明显提高牙齿的正畸效率和减轻患者的痛苦。
导引导丝在人体血管中行进, 需要进入到各种弯曲和狭窄的环境中,通过闭塞环境还会受到很大阻力,若N I-T I SMA与不锈钢的焊点强度不够,可能会发生断裂,使部分导丝断留在人体内,对患者具有很大的生命威胁。
因此,研究Ni- TiSMA与不锈钢的焊接,可充分发挥Ni-TiSMA的优良性能,保障患者生命安全。
焊接是连接异种材料的较好方法,而Ni-Ti SMA与Ni- TiSMA以及Ni-Ti SMA与异种材料的焊接存在很多问题,尤其是Ni- Ti SMA与不锈钢的焊接研究报道较少见。
1存在的问题李洪梅研究发现Ni-Ti SMA与不锈钢直接对焊的焊点平均抗拉强度为184MPa,断口平整且有微裂纹,是典型的脆性断裂oMirshekari 等通过x射线衍射(X-砂diffraction, XRD)分析得出,焊缝区主要是由B2, y-Fe, a-Fe, TiFe, TiFe2, TiCr2, TiNi3 和Ti2Ni 等相构成 (见图2),相比于母材,焊缝区生成了大量的含Ti金属间化合物,这是影响焊点性能的主要因素。
新型高温合金IC10的焊接研究进展_罗晓娜
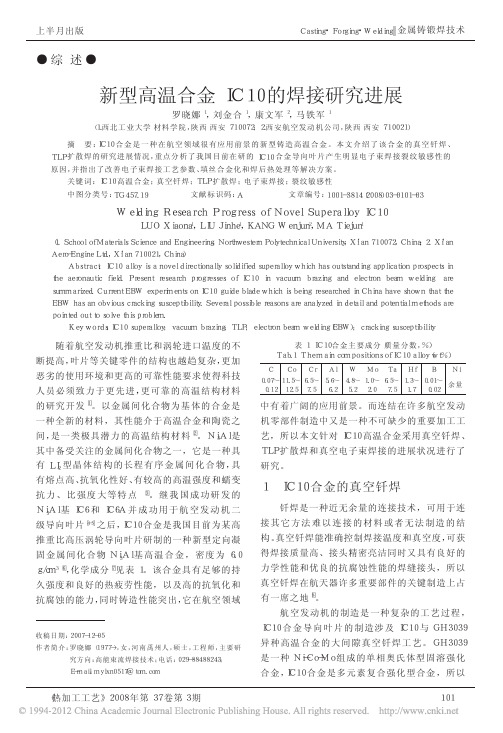
随着航空发动机推重比和涡轮进口温度的不 断提高, 叶片等关键零件的结构也越趋复杂, 更加 恶劣的使用环境和更高的可靠性能要求使得科技 人员必须致力于更先进, 更可靠的高温结构材料 的研究开发[1]。以金属间化合物为基 体的合金是 一种全新的材料, 其性能介于高温合金和陶瓷之 间, 是一类极具潜力的 高温结构材 料[2]。Ni3Al 是 其中备受关注的金属间化合物之一, 它是一种具 有 LI2 型 晶体 结 构 的 长 程 有 序 金 属 间 化 合 物 , 具 有熔点高、抗氧化性好、有较高的高温强度和蠕变 抗 力 、 比 强 度 大 等 特 点 [3]。 继 我 国 成 功 研 发 的 Ni3Al 基 IC6 和 IC6A 并 成 功 用 于 航 空 发 动 机 二 级导向叶片[4-5] 之后, IC10 合金是我国目前为某高 推重比高压涡轮导向叶片研制的一种新型定向凝 固金属间化 合物 Ni3Al 基 高 温 合 金 , 密 度 为 6.0 g/cm3 [6], 化学成分[7]见表 1。该合金具有足够的持 久强度和良好的热疲劳性能, 以及高的抗氧化和 抗腐蚀的能力, 同时铸造性能突出, 它在航空领域
航空发动机的制造是一种复杂的工艺过程, IC10 合 金 导 向 叶 片 的 制 造 涉 及 IC10 与 GH3039 异种高温 合金的大间 隙真空钎焊 工艺。GH3039 是一种 Ni-Co-Mo 组成的单相奥氏体型固溶强化 合金, IC10 合金是多元素复合强化型合金, 所以
《热加工工艺》2008 年第 37 卷第 3 期
TLP焊接技术的研究

TLP焊接技术的研究作者:李悦来源:《科学与财富》2016年第28期瞬时液相扩散焊(TLP)是扩散焊的一种连接方法,它是指在被焊母材之间放入含有降熔元素的中间层合金,依靠中间层合金的直接熔化或中间层和母材之间的扩散共晶反应产生液相,随后通过等温凝固和成分均匀化形成焊接接头的连接工艺。
就本质而言,TLP连接中的扩散在狭义上讲就是降低熔点的元素(Melting point depressant elements,简称MPD元素)的扩散,MPD元素的充分扩散是TLP焊接成败的命脉;而合理选定中间层则是起内因方面的首要前提。
扩散的目的就在于试图使中间层中MPD元素的浓度降至足够低,以达到如提高接头的重熔温度,消除中间层中的脆性相使其改变成固熔体等目的,中间层成分的这种显著且合理的质的变化乃至中间层的消失正是该方法中“过渡”(或“瞬时”)一词的含义所在。
上世纪五十年代,Lynch等人在连接Ti时采用一种合金做中间层,从中发现经过高温保温过程,获得接头成分与母材接近的接头现象。
1961年Owczarski在连接Zr合金和304不锈钢两种材料时,把这两种材料直接对接在一起,形成具有较高强度和抗蚀性的接头,并首先提出了近似于TLP扩散连接的概念。
20世纪70年代初Hoppin和Berry在连接镍基耐热合金时率先使用了MPD(Melting point depressant element),并提出了活性扩散连接的概念。
1974年D.S.Duvall在Udimet700材料的扩散连接中采用Cu-Ni做中间层,并获得了无脆性相的接头,他把TLP扩散连接的应用进行了汇总,并论述了其连接原理,提出了瞬时液相扩散连接的概念。
TLP连接过程如图1-2所示。
将一特殊成分和熔化温度的TLP中间层合金(厚度约25~100μm)作为钎料,放置于装配好的工件间,并施加不大的压力,然后在真空或氩气保护下加热到连接温度。
在连接温度下中间层首先熔化,润湿母材,在工件的配合面之间形成一薄层液体(图1-2b)。
焊接数值分析大纲

焊接过程数值模拟教学大纲开课单位:焊接任课教师:柯黎明职称:教授授课学时数:40 学分数: 2 授课方式: 讲授一、授课对象:焊接专业研究生。
二、教学要求和目的:了解数值分析方法的基本原理及在焊接领域的应用前景,基本掌握差分法及有限元法的原理及在平面问题中的应用,能用数值方法来求解二维热传导问题、热应力及变形问题,能用数值方法模拟焊接工艺过程。
了解数值分析方法的基本原理及在焊接领域的应用前景,基本掌握差分法及有限元法的原理及在平面问题中的应用,能用数值方法来求解二维热传导问题、热应力及变形问题,能用数值方法模拟焊接工艺过程。
三、课程内容:1、概述1.1数值分析在焊接中的应用1、数值分析方法简介2、基本应用:焊接现象的计算机模拟焊接结构使用过程中的强度和性能1.2焊接过程数值模拟的发展方向1、焊接热过程的数值模拟:实际焊接接头中的三维温度场分布2、焊缝金属凝固和焊接接头相变过程的数值模拟3、焊接应力和应变发展过程的数值模拟4、非匀质焊接接头的数值模拟5、焊接熔池形状尺寸的数值模拟2、数学物理方程简介2.1 基本概念:数理方程研究问题的一般程序:1、对物理问题,根据有关定律,建立相应的数学模型2、对数学问题,运用数学方法进行求解2.2 波动方程(双曲线方程):1、弦振动方程的导出2、定解条件:三类边界条件2.3 热传导方程(抛物线方程):1、方程的导出2、定解问题的提法2.4 拉普拉斯方程(椭圆方程):1、方程的导出2、定解条件2.5 定解问题的适定性存在性、唯一性、稳定性3、数值分析方法概述3.1 差分法(求解过程和原理)1、差分方程:(以一维对流方程为例)2、截断误差3、稳定性与收敛性3.2 有限元法1、基本步骤2、特点4、焊接热传导问题的差分解法4.1 稳态热传导问题的差分解法1、偏微分方程替代法2、能量平衡法4.2 不稳定热传导的差分解法1、差分格式2、差分格式的稳定性及步长的选取3、边界条件的处理4.3 温度场的计算实例:1、一维焊接热传导的差分计算(电弧焊)2、电阻焊温度场计算4.4 过渡液相扩散连接过程的数值模拟5、泛函及变分5.1 引论1、泛函的概念2、变分法1)最速降线问题2)短程线问题3)等周问题5.2 在不动边界问题中的变分方法1、变分及其特性2、欧拉方程3、依赖于较高阶导函数的泛函4、依赖于含多个自变量的函数的泛函5.3 极值的充分条件5.4 可动边界的变分问题5.5 条件极值的变分问题5.6 变分问题的直接解法1、直接法的概念2、欧拉有限差分法3、里兹法4、康托罗维兹法5、求解变分问题的有限元法6、平面弹性问题的有限元分析1、离散化2、单元分析3、整体分析及边界条件7、焊接热传导问题的有限元法计算6.1 各种温度场的变分问题6.2 稳态热传导问题的有限元解法6.2 不稳定热传导的有限元解法6.3 热源、边界条件、熔化潜热等的处理方法四、主要参考书:1、武传松:焊接热过程数值分析(哈尔滨工业大学出版社)2、陈楚等:数值分析在焊接中的应用(交通大学出版社)3、陈丙森:计算机辅助焊接技术4、复变与数理方程5、变分法。
- 1、下载文档前请自行甄别文档内容的完整性,平台不提供额外的编辑、内容补充、找答案等附加服务。
- 2、"仅部分预览"的文档,不可在线预览部分如存在完整性等问题,可反馈申请退款(可完整预览的文档不适用该条件!)。
- 3、如文档侵犯您的权益,请联系客服反馈,我们会尽快为您处理(人工客服工作时间:9:00-18:30)。
第17卷第6期2003年12月 华 东 船 舶 工 业 学 院 学 报(自然科学版)Journal of East China Shipbuilding Institute(Natural Science Edition)Vo1117No16Dec.2003文章编号:1006-1088(2003)06-0042-06瞬间液相扩散连接过程数值模拟的研究进展初雅杰,翟建广,邹家生,陈 铮(华东船舶工业学院材料与环境工程系,江苏镇江212003)摘 要:综述了近年来国内外关于瞬间液相扩散连接数值模拟的研究现状,内容涉及了异种材料接头元素的扩散与反应层形成的模拟,接头变形与应力行为的模拟,并提出了要解决的问题,为今后的研究提供了一定的借鉴。
关键词:瞬间液相连接;数值模拟;元素扩散;残余应力中图分类号:TG453 文献标识码:AProgress of the R esearch in the Area of Numerical Simulation ofT ransient Liquid Phase Diff usion BondingCHU Y a2jie,ZHA I Jian2guang,ZO U Jia2sheng,CH EN Zheng(Dept.of Material and Environment Eng.,East China Shipbuilding Institute,Zhenjiang Jiangsu212003,China) Abstract:Reviews the present progress in numerical simulation of transient liquid phase diffusion bonding in recent years.The simulation of element diffusion and formation of reaction layers are discussed in detail. At the same time the simulation of residual stress of the bonding is involved.The problems to be solved are pointed out.It could be useful for the future research.K ey w ords:transient liquid phase bonding;numerical simulation;element diffusion;residual stress0 引 言 近年来,随着高温合金、陶瓷、复合材料等新材料的迅速发展,这些新材料的连接技术也越来越引起人们的关注。
虽然活性钎焊和固相扩散连接以各自的优点成为近年来新材料连接领域的研究热点,但这两种连接方法均有一定的局限性。
Peaslee和Boam于1952年首次提出了瞬间液相扩散连接(Tran2 sient Liquid Phase Diffusion Bonding,简称TL P扩散连接)方法[1]。
1974年,Duvall成功地进行了Ni基耐热合金的TL P扩散连接,随后TL P扩散连接方法在航空航天等领域得到了广泛的应用。
但是由于TL P扩散连接涉及材料、扩散、相变、界面反应、接头应力应变等方面,工艺参数多,虽然已进行了大量的实验研究,但对各种材料的连接机理认识尚不深入[2~4]。
一般认为,瞬间液相扩散连接过程的完成受中间层成分、厚度以及保温温度等因素的控制,元素的扩散起主要的作用,由于元素扩散是一个极缓慢的过程,实际构件中接合面间隙又并非一致,因此,为焊接一定的材料,从中间层合金元素的选择、成分的设计到最佳焊接工艺的确定,是一项工作量极大的工作,人们常使用计算机模拟瞬间液相扩散连接收稿日期:2003-04-11基金项目:江苏省自然科学基金项目(B K2002602)作者简介:初雅杰(1979-),男,山东烟台人,华东船舶工业学院硕士研究生。
过程来分析各种因素的影响。
本文试图对此进行综述,讨论界面元素扩散及反应层形成、接头残余应力分布数值模拟的研究现状及其发展趋势,为进一步研究提供理论指导。
1 瞬间液相扩散连接元素扩散及反应层形成的数值模拟瞬间液相扩散连接实际上提供了一种用钎焊的方法,获得具有固相扩散连接接头耐热特性的连接方法。
研究表明,TLP 扩散连接工艺可分为5个步骤:①中间层材料熔化并填充接合面;②固液界面处基体熔化,液相层增厚;③固态基体向液相中生长,发生等温凝固过程,液相层减薄;④等温凝固完成,形成固相接头;⑤接头区域成分均匀化。
扩散连接接头的模拟[5],主要有3个方面,但TLP 扩散连接过程中形成了液态合金,起到了类似钎料的作用,能够填充缝隙。
由于有液相参与,故大大加速了连接过程,降低了对连接表面加工精度的要求,有效地消除了固相扩散连接中难以消除的界面空洞,使扩散得以充分进行。
它的优点之一就是降低了材料表面制备要求,因此对界面空洞消失过程的机理模拟并不关键。
TLP 扩散连接的数值模拟主要是接头元素扩散及反应层形成的模拟和接头变形及应力行为的模拟。
目前,接头元素扩散及反应层形成的模拟主要针对异种材料进行。
异种材料扩散连接接头中往往会出现与基体材料性能不同的各种新相,脆性金属间化合物相的产生会弱化接头性能。
因此,研究扩散连接过程中脆性金属间化合物的形成和长大机理,进而对它进行控制,是异种材料连接的重要内容。
对于一个特定的陶瓷/金属接合体,人们从技术上广泛地研究了连接条件(温度、时间和压力等)对接头强度的影响规律,并发现这种影响往往是由于界面相互作用的不同所致。
一般而言,在热力学上,通常表现为形成不同的反应产物;在动力学上,则主要表现为界面反应层厚度的影响。
中尾等人则认为,控制反应层厚度是改善连接强度的关键。
影响陶瓷与金属之间的连接强度的因素很多,但主要是界面反应和残余应力的影响。
文献[6]曾根据合金元素扩散的理论,对接头元素分布进行了模拟,它们采用试验材料为耐热合金K5与耐热刚2Cr12NiMoV 进行扩散连接。
扩散的工艺参数:连接温度T =1273K 和1373K ,连接压力P =10MPa ,连接时间t =15min 。
各元素扩散系数见表1,实际元素浓度分布曲线与理论计算的分布曲线如图1所示。
T =1273K T =1373Ka )实际元素分布b )模拟元素分布图1 扩散连接元素浓度分布曲线Fig.1 Element distribution curve of diffusion由图1可以看出,模拟曲线与实际探针曲线较为接近,此扩散连接过程中的元素浓度分布模拟,能够较好反应元素的分布规律,可以为扩散连接工艺制定及中间层厚度的选择提供一定参考。
34第6期 初雅杰等:瞬间液相扩散连接过程数值模拟的研究进展表1 元素扩散系数Tab.1 Diffusion coefficient of element扩散系数Fe Al Ni D 1273K 3.6×10-118.43×10-12 4.96×10-10D 1373K 3.27×10-10 6.2×10-111.03×10-9Tien 和Yuning J 对Al -Cu 合金TL P 连接过程中的溶质分布做了详细的模拟[7~9],并建立了一维的数值模型。
柯黎明等人也作了相关的模拟[10],他们用计算机模拟了过渡液相扩散连接过程。
以纯镍为基体,以镍2硼合金作为中间夹层材料,进行了部分的计算。
在加热速度500K/s 的情况下,焊接温度、中间层厚度、硼含量对熔化及凝固的影响。
结果表明:①焊接温度上升,最大液相层厚度d 、稳态凝固速度均增加;在不同温度下完成等温凝固所需时间存在峰值(见图2)。
②随中间层厚度h 的提高,熔化速度、液相层最大厚度、等温凝固时间t s 均提高,但稳态凝固速度V p 下降(见图3)。
图2 温度对最大液相层厚度、凝固速度和时间的影响Fig.2E ffect of temperature on thickness ofliquid layer ,solidification rate and time 图3 中间层厚度对最大液相层厚度、凝固速度和时间的影响Fig.3 E ffect of interlayer thickness on thickness of liquid layer ,solidification rate and time这些研究初步表明,反应层厚度是影响陶瓷/金属间界面强度的重要参数。
因此,理想的耐热连接方法必须能控制高温使用时,反应层厚度不会明显增大。
扩散连接工艺是极其复杂的,影响接头的因素很多,特别是中间层厚度、连接温度、保温时间等,通过数值模拟可以找出各个因素对接头质量的影响。
2 接头变形与应力行为的模拟异种材料(包括异种金属、金属与陶瓷等)扩散连接后从高温冷却时,由于材料热膨胀系数不同且界面上存在相互约束,就会形成残余热应力。
这种热应力使得连接后在界面上形成裂纹,甚至导致断裂。
为了缓和残余应力,人们普遍采用在两材料之间插入一定厚度的中间层。
瞬间液相扩散连接正是采用了这种方法,如陶瓷/陶瓷和陶瓷/金属的瞬间液相扩散连接时,插入软质中间层效果非常显著[11~14]。
近年来,有限元法和边界元法已被广泛用于计算异种材料连接的界面残余应力和中间层选择与设计,但在如何评价残余应力的影响方面还很不完善,界面力学的建立和发展对解决陶瓷/金属连接中强度和残余应力方面的问题将起到不可忽略的作用。
在80年代末就有人用有限元法对带有中间层的接头应力进行了分析[15~18]。
Kuo 和Chen 用其它方法对此也进行了计算[19]。
Toyada 等用有限元法对于不同材料连接接头热应力问题作了系统、完整的分析和讨论。
而Munz D 等认为仅仅用有限元计算对于接头自由边缘的点不够精确。
1995年,他们把应力分布描述和有限元计算相结合,分析接头自由边缘热应力状况。
文献[20]采用非线性有限元程序包MARC7.2作为有限元数值模拟的软件环境,以TiAl 、Cu 作为母材,W 、Mo 、Ti 、Nb 等作为中间层进行接头残余应力分析,并提出了中间层的残余应力因子R f ,R f =Δα・E ・σ0.2・ω和中间层厚度因子T f ,T f =E σ0.2ωΔα1Δα2。
Δα是材料的热膨胀系数,E 44华东船舶工业学院学报(自然科学版)2003年为材料的弹性模量,σ0.2为材料的屈服极限,ω为材料的加工硬化系数,Δα1、Δα2,分别为中间层与两端母材的热膨胀系数差。