热管在工业中的应用
电热管用途

电热管用途
电热管是一种将电能转化为热能的设备,通常由金属管、电阻丝和绝缘材料组成。
它的主要用途包括但不限于以下几个方面:
1. 加热液体:电热管常用于加热水、油、化学溶液等液体。
它可以用于热水器、热水壶、咖啡机、水族箱加热器等设备中,提供所需的热量。
2. 工业加热:在工业生产中,电热管可用于加热各种材料和工艺过程。
例如,它可以用于塑料加工、橡胶硫化、油漆固化、金属熔炼等领域,提供精确的温度控制。
3. 家用电器:电热管广泛应用于家用电器中,如电熨斗、电吹风、烤箱、取暖器等。
它们提供了方便、快捷的加热功能,满足人们日常生活的需求。
4. 暖通空调:在暖通空调系统中,电热管可用于加热空气或水。
它可以用于暖风设备、地暖系统、空气处理单元等,提供舒适的室内温度。
5. 实验室设备:电热管在实验室中也有应用,例如用于加热实验溶液、培养箱、烘箱等设备。
它能够提供精确的温度控制,满足实验要求。
6. 农业和园艺:电热管可用于农业和园艺领域,如温室加热、动物养殖场的取暖、植物生长灯等。
它为农作物和动物提供了适宜的生长环境。
总之,电热管具有广泛的用途,能够在各个领域提供可靠的加热功能。
它的优点包括高效能、易于控制、安装方便等,使其成为许多设备和应用中不可或缺的一部分。
热管制冷原理的应用

热管制冷原理的应用热管制冷概述热管制冷是一种利用热管的传热和传质特性来实现制冷的技术。
热管是一种热传递器件,由工作介质填充的密封通道组成。
它利用工作介质在管道内的汽化和冷凝过程来完成热量传递。
热管制冷技术以其高效、节能的特点,被广泛应用于航天器、电子设备以及工业制冷等领域。
热管制冷原理热管制冷的原理基于热管运载的工作介质的汽化和冷凝。
当热管的一端加热时,工作介质在热管内汽化成气体,从而产生大量的蒸汽。
蒸汽被压缩到热管的另一端,通过冷凝器将热量传递给外部环境。
冷凝后的工作介质液化成液体,被毛细力或重力送回到加热端,循环往复。
这样循环运行下去,实现了热量的传递和制冷效果。
热管制冷的优势热管制冷技术相比传统的制冷技术具有以下优势:•高效能:热管制冷技术利用工作介质的汽化和冷凝过程进行热量传递,具有很高的传热效率。
•节能环保:热管制冷过程中无需使用机械压缩制冷剂,没有动力设备产生噪音和振动,因此具有低能耗和环保的特点。
•可靠性高:热管制冷技术无机械运动部件,减少了故障发生的可能性,具有很高的可靠性。
•体积小巧:热管结构紧凑,适合小型化应用,可以节约空间。
•适应性广泛:热管制冷技术可适用于各种工况下的制冷需求,并且具有很好的稳定性和温度控制性。
热管制冷的应用领域热管制冷技术已经在许多领域得到了广泛的应用,下面列举了其中的几个典型应用领域:航天器制冷在航天器中,由于外部环境的极端温度条件,需要对设备和宇航员的生活空间进行冷却。
热管制冷技术可以高效地将热量传递给航天器表面,从而实现冷却效果。
而且,由于热管制冷技术的微重力适应能力,使其在航天器中得到了广泛应用,大大提高了航天器的工作效率和可靠性。
电子设备冷却电子设备的工作过程中会产生大量的热量,如果无法及时散热,会导致电子设备的性能下降甚至损坏。
热管制冷技术可以将电子设备内的热量传递给外部环境,实现设备的有效冷却。
与传统冷却技术相比,热管制冷技术可以提供更高的冷却效率和更静音的工作环境。
工程热力学热管技术在热力循环中的应用
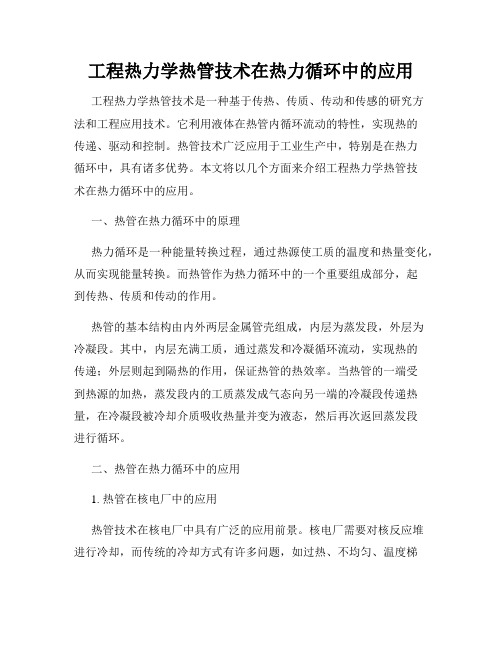
工程热力学热管技术在热力循环中的应用工程热力学热管技术是一种基于传热、传质、传动和传感的研究方法和工程应用技术。
它利用液体在热管内循环流动的特性,实现热的传递、驱动和控制。
热管技术广泛应用于工业生产中,特别是在热力循环中,具有诸多优势。
本文将以几个方面来介绍工程热力学热管技术在热力循环中的应用。
一、热管在热力循环中的原理热力循环是一种能量转换过程,通过热源使工质的温度和热量变化,从而实现能量转换。
而热管作为热力循环中的一个重要组成部分,起到传热、传质和传动的作用。
热管的基本结构由内外两层金属管壳组成,内层为蒸发段,外层为冷凝段。
其中,内层充满工质,通过蒸发和冷凝循环流动,实现热的传递;外层则起到隔热的作用,保证热管的热效率。
当热管的一端受到热源的加热,蒸发段内的工质蒸发成气态向另一端的冷凝段传递热量,在冷凝段被冷却介质吸收热量并变为液态,然后再次返回蒸发段进行循环。
二、热管在热力循环中的应用1. 热管在核电厂中的应用热管技术在核电厂中具有广泛的应用前景。
核电厂需要对核反应堆进行冷却,而传统的冷却方式有许多问题,如过热、不均匀、温度梯度大等。
而利用热管技术可以解决这些问题,提高核电厂的安全性和效率。
2. 热管在太阳能热能利用中的应用太阳能热能是一种绿色、清洁的能源,利用太阳能进行热能转换可以有效减少能源消耗和环境污染。
而热管技术可以提高太阳能的热能利用效率,将太阳能转化为实用的热能,广泛应用于太阳能热水器、太阳能空调等领域。
3. 热管在航空航天中的应用热管技术在航空航天领域中有着重要的应用价值。
在宇宙空间中,传统的传导和对流传热方式受到限制,而热管技术可以通过液体流动的方式实现热量的传输和均衡,提高航空航天器的散热效果,保证设备的正常运行。
4. 热管在工业生产中的应用热管技术在工业生产中有着广泛的应用。
例如,在钢铁冶炼过程中,热管技术可以用于冷凝和回收高温废气中的热能,提高能源利用效率。
此外,在工业热处理、电子设备制造等领域,热管技术也可以用于温度控制和热能回收。
热管技术在工业锅炉余热回收上的运用

热管技术在工业锅炉余热回收上的运用热管技术是一种基于热管原理的传热技术,利用热管的热导性能,将高温热源处的热能传递到低温处,实现了热能的有效利用。
在工业锅炉中,热管技术可以被用来回收排放出的高温烟气中的余热,将其转化为有用的热能,用于加热水或发电等用途。
下面我们将从热管技术在工业锅炉余热回收中的运用、优势及发展趋势等方面进行分析。
在工业锅炉中,热管技术可以应用在烟气余热回收系统中。
当工业锅炉燃烧燃料时,会产生大量的高温烟气,其中蕴含着大量的热能。
传统的余热回收设备多采用换热器,但常常存在换热效率低、结构复杂、维修成本高等问题。
而采用热管技术可以有效地解决这些问题。
热管技术可以将高温烟气中的余热迅速传递到工业锅炉需要加热的介质中,实现了热能的有效回收利用。
热管技术具有结构简单、传热效率高、维护方便等优点,能够有效地提高能源利用率,减少能源消耗。
热管技术还可以在工业锅炉烟气脱硫、除尘等设备中发挥重要作用。
利用热管技术将高温烟气中的余热用于辅助设备加热,不仅可以提高设备的效率,还可以降低设备运行成本,延长设备寿命。
热管技术的优势热管技术具有结构简单、体积小、重量轻的特点,可以方便地嵌入到现有的工业锅炉系统中,无需改变原有的结构。
这为工业锅炉的现场改造提供了便利。
热管技术工作稳定可靠。
热管内部没有运动部件,无需外部动力输入,因此工作稳定可靠,维护成本低。
热管技术适用于高温、高压等工况下的热能回收。
在工业锅炉中,热管技术可以适应高温高压的工作环境,具有很强的适用性和稳定性。
热管技术在工业锅炉余热回收中的发展趋势第一,热管技术的智能化发展。
随着传感技术和智能控制技术的不断成熟,热管技术的智能化水平将会不断提高,能够更好地根据工业锅炉的工况和需求进行自适应调整,提高系统的整体性能。
第二,热管技术的多元化应用。
热管技术不仅可以用于工业锅炉余热回收,还可以应用于石化、电力、冶金等多个行业的余热回收及传热领域,将会得到更广泛的应用。
热管技术的工作原理及在多领域中的应用
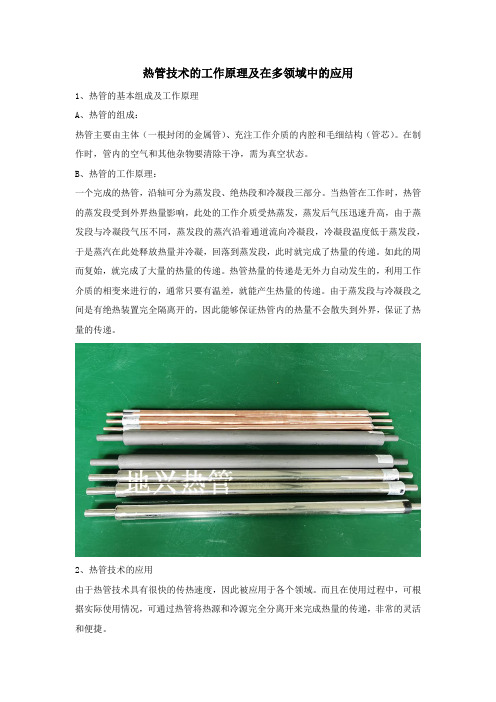
热管技术的工作原理及在多领域中的应用1、热管的基本组成及工作原理A、热管的组成:热管主要由主体(一根封闭的金属管)、充注工作介质的内腔和毛细结构(管芯)。
在制作时,管内的空气和其他杂物要清除干净,需为真空状态。
B、热管的工作原理:一个完成的热管,沿轴可分为蒸发段、绝热段和冷凝段三部分。
当热管在工作时,热管的蒸发段受到外界热量影响,此处的工作介质受热蒸发,蒸发后气压迅速升高,由于蒸发段与冷凝段气压不同,蒸发段的蒸汽沿着通道流向冷凝段,冷凝段温度低于蒸发段,于是蒸汽在此处释放热量并冷凝,回落到蒸发段,此时就完成了热量的传递。
如此的周而复始,就完成了大量的热量的传递。
热管热量的传递是无外力自动发生的,利用工作介质的相变来进行的,通常只要有温差,就能产生热量的传递。
由于蒸发段与冷凝段之间是有绝热装置完全隔离开的,因此能够保证热管内的热量不会散失到外界,保证了热量的传递。
2、热管技术的应用由于热管技术具有很快的传热速度,因此被应用于各个领域。
而且在使用过程中,可根据实际使用情况,可通过热管将热源和冷源完全分离开来完成热量的传递,非常的灵活和便捷。
A、在航空航天中的应用热管技术最早是应用于航天航空中的。
航天器在天空中时,向着阳光的一面温度高,背阴面温度较低,温差较大,而利用热管技术,热管的蒸发段从向阳的一面吸收热量,传递到背阴的一面,以此来实现两侧温度的平衡,避免两侧的温差过大,导致航天器出现故障。
B、工业领域中的热回收应用在工业领域,余热资源非常多,但能够再次进行利用的却很有限,由于技术或资金的原因,导致一些余热资源被浪费掉了。
如很常见的烘干或类似的工序,需要先将环境中的空气(即新风)送进反应炉中,经过加温,加热到符合条件的热度后,在进行下一步作业,为保证炉内空气的新鲜和维持一定的压力,需要将作业完后的空气排出,此时排除的空气会带有一定的热量;通过热管技术,对这部分热量进行回收,对新风进行预热,就减少了能源的投入,降低了成本。
热管换热器工作原理及特点-概述说明以及解释
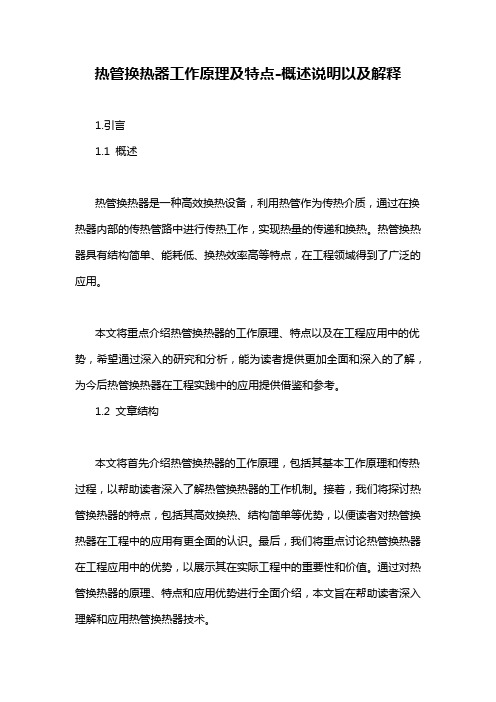
热管换热器工作原理及特点-概述说明以及解释1.引言1.1 概述热管换热器是一种高效换热设备,利用热管作为传热介质,通过在换热器内部的传热管路中进行传热工作,实现热量的传递和换热。
热管换热器具有结构简单、能耗低、换热效率高等特点,在工程领域得到了广泛的应用。
本文将重点介绍热管换热器的工作原理、特点以及在工程应用中的优势,希望通过深入的研究和分析,能为读者提供更加全面和深入的了解,为今后热管换热器在工程实践中的应用提供借鉴和参考。
1.2 文章结构本文将首先介绍热管换热器的工作原理,包括其基本工作原理和传热过程,以帮助读者深入了解热管换热器的工作机制。
接着,我们将探讨热管换热器的特点,包括其高效换热、结构简单等优势,以便读者对热管换热器在工程中的应用有更全面的认识。
最后,我们将重点讨论热管换热器在工程应用中的优势,以展示其在实际工程中的重要性和价值。
通过对热管换热器的原理、特点和应用优势进行全面介绍,本文旨在帮助读者深入理解和应用热管换热器技术。
1.3 目的:本文旨在深入介绍热管换热器的工作原理及特点,探讨其在工程应用中的优势。
通过对热管换热器的全面解析,旨在帮助读者全面了解该换热器的优点和适用领域,为工程实践提供参考和指导。
同时,通过对热管换热器未来发展前景的展望,进一步探讨该技术在换热领域的潜力和发展方向。
希望本文能为读者提供一份全面且深入的研究参考,促进热管换热器技术的不断创新与发展。
2.正文2.1 热管换热器的工作原理热管换热器是一种利用热管换热原理实现热量转移的换热设备。
其工作原理是通过热管内介质的相变过程来实现热量的传递。
热管换热器主要包括蒸发段和冷凝段两部分。
在蒸发段,工作介质(如液态水)受热后蒸发成为蒸汽,蒸汽通过热管的热传递作用被传输到冷凝段。
在冷凝段,蒸汽失去热量后冷凝成为液态介质,释放出的热量再次通过热管传递到冷却介质。
通过这样的过程,热管换热器实现了热量的高效传递,并具有一定的节能效果。
热管的应用及原理大全
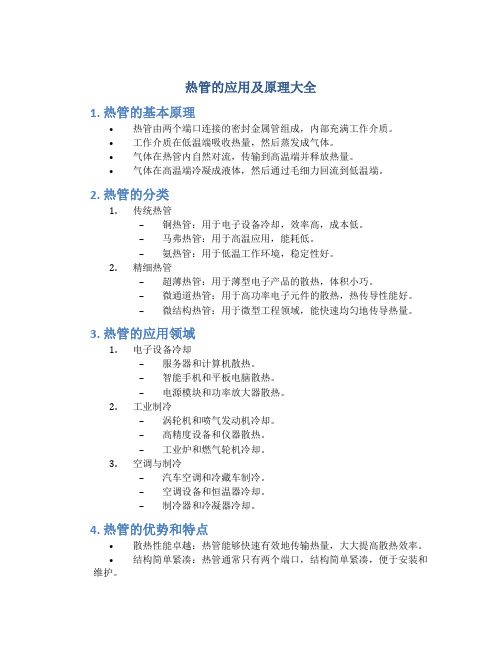
热管的应用及原理大全1. 热管的基本原理•热管由两个端口连接的密封金属管组成,内部充满工作介质。
•工作介质在低温端吸收热量,然后蒸发成气体。
•气体在热管内自然对流,传输到高温端并释放热量。
•气体在高温端冷凝成液体,然后通过毛细力回流到低温端。
2. 热管的分类1.传统热管–铜热管:用于电子设备冷却,效率高,成本低。
–马弗热管:用于高温应用,能耗低。
–氨热管:用于低温工作环境,稳定性好。
2.精细热管–超薄热管:用于薄型电子产品的散热,体积小巧。
–微通道热管:用于高功率电子元件的散热,热传导性能好。
–微结构热管:用于微型工程领域,能快速均匀地传导热量。
3. 热管的应用领域1.电子设备冷却–服务器和计算机散热。
–智能手机和平板电脑散热。
–电源模块和功率放大器散热。
2.工业制冷–涡轮机和喷气发动机冷却。
–高精度设备和仪器散热。
–工业炉和燃气轮机冷却。
3.空调与制冷–汽车空调和冷藏车制冷。
–空调设备和恒温器冷却。
–制冷器和冷凝器冷却。
4. 热管的优势和特点•散热性能卓越:热管能够快速有效地传输热量,大大提高散热效率。
•结构简单紧凑:热管通常只有两个端口,结构简单紧凑,便于安装和维护。
•体积轻巧:热管体积小巧,适用于薄型电子设备和微型工程。
•工作稳定可靠:热管通过自然对流工作,无需外部能源,工作稳定可靠。
•环保节能:热管可以提高能源利用效率,减少系统能耗。
5. 热管的发展趋势•进一步提高散热性能:改进热管材料和设计,提高热管的散热能力。
•发展微型热管技术:适应微型化及高功率集成电路的散热需求。
•探索新的应用领域:将热管技术应用于新兴领域,如军事航空等。
以上是关于热管的应用及原理的介绍,热管作为一种高效的热传导技术,正广泛应用于电子设备、工业制冷和空调制冷等领域。
通过不断创新和发展,热管将能够在更多领域展现其优势,并为人们的生活和工作带来更多的便利和舒适。
长效钢-水热管在石化行业的工业应用
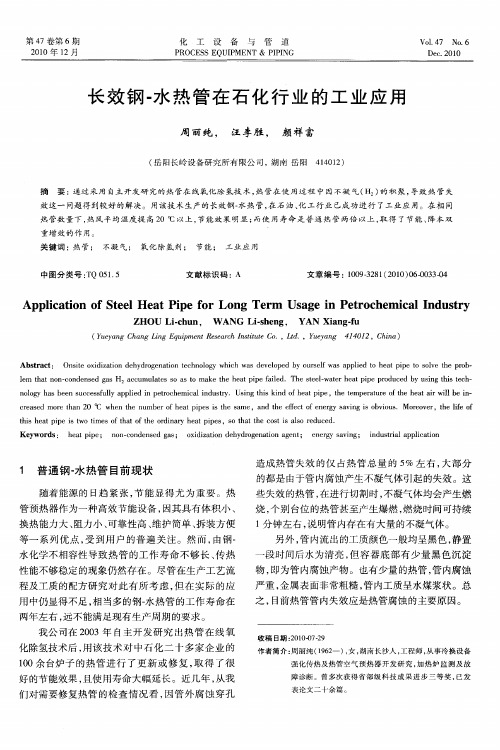
中 图分 类 号 :Q0 15 T 5 .
ZH O U - h Lic un , W AN G -h ng, YAN i n f Lis e X a g-u
( uy n h n i q i e t e ac nt u o , t. uy n 4 4 1 ,C ia Y e a g C a g Ln E u m n R s r Is tt C . Ld ,Y e a g 1 0 2 h ) g p e h i e n
1 普通钢- 水热管 目前现状
随着 能源 的 日趋 紧 张 , 能显 得 尤 为 重要 。热 节 管预 热器作 为一 种高效 节能设 备 , 因其具 有 体积小 、
造 成热 管失 效 的 仅 占热 管 总量 的 5 左 右 , 部 分 % 大
的都是 由于 管 内腐 蚀产 生不凝 气体 引起 的失效 。这 些 失效 的热 管 , 在进 行切 割时 , 不凝气 体均 会产 生燃 烧, 个别 台位 的热管 甚至 产生爆 燃 , 烧 时间可持 续 燃 1分钟 左右 , 明管 内存 在有 大量 的不凝气 体 。 说 另外 , 内流 出的工质 颜色 一般均 呈黑 色 , 置 管 静
( 阳长 岭 设 备 研 究 所 有 限 公 司 , 南 岳 阳 岳 湖 44 1 ) 102
摘
要 : 过 采 用 自主 开发 研 究 的热 管在 线 氧 化 除 氢技 术 , 管在 使 用 过 程 中 因不 凝 气 ( 2 的 积 聚 , 致 热 管 失 通 热 H ) 导
热管技术在热能工程中的应用分析
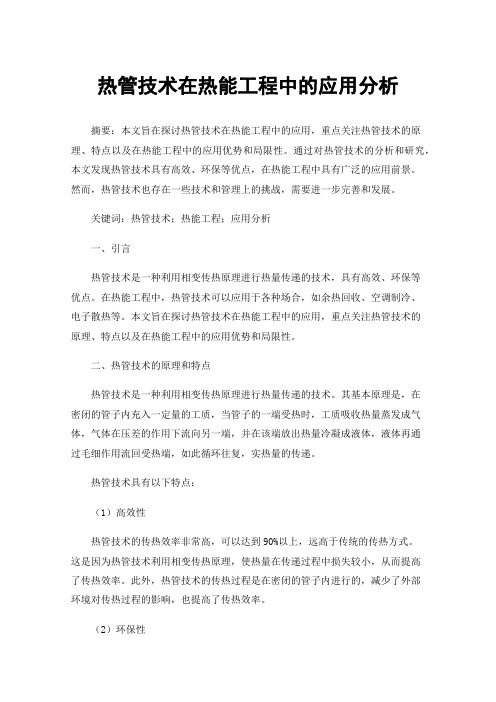
热管技术在热能工程中的应用分析摘要:本文旨在探讨热管技术在热能工程中的应用,重点关注热管技术的原理、特点以及在热能工程中的应用优势和局限性。
通过对热管技术的分析和研究,本文发现热管技术具有高效、环保等优点,在热能工程中具有广泛的应用前景。
然而,热管技术也存在一些技术和管理上的挑战,需要进一步完善和发展。
关键词:热管技术;热能工程;应用分析一、引言热管技术是一种利用相变传热原理进行热量传递的技术,具有高效、环保等优点。
在热能工程中,热管技术可以应用于各种场合,如余热回收、空调制冷、电子散热等。
本文旨在探讨热管技术在热能工程中的应用,重点关注热管技术的原理、特点以及在热能工程中的应用优势和局限性。
二、热管技术的原理和特点热管技术是一种利用相变传热原理进行热量传递的技术。
其基本原理是,在密闭的管子内充入一定量的工质,当管子的一端受热时,工质吸收热量蒸发成气体,气体在压差的作用下流向另一端,并在该端放出热量冷凝成液体,液体再通过毛细作用流回受热端,如此循环往复,实热量的传递。
热管技术具有以下特点:(1)高效性热管技术的传热效率非常高,可以达到90%以上,远高于传统的传热方式。
这是因为热管技术利用相变传热原理,使热量在传递过程中损失较小,从而提高了传热效率。
此外,热管技术的传热过程是在密闭的管子内进行的,减少了外部环境对传热过程的影响,也提高了传热效率。
(2)环保性热管技术在传递热量的过程中无需消耗额外的能源,是一种环保的传热方式。
这是因为热管技术利用相变传热原理进行热量传递,无需额外的能源驱动,减少了能源消耗和环境污染。
此外,热管技术的传热效率高,可以减少能源浪费和环境污染。
(3)灵活性热管技术可以应用于各种场合,如余热回收、空调制冷、电子散热等。
这是因为热管技术的传热原理简单,可以根据不同的应用场景进行定制化的设计和制造。
此外,热管技术的传热效率高,可以适用于不同的传热量和传热距离的需求。
(4)可靠性热管技术的传热过程是在密闭的管子内进行的,不易受到外部环境的影响,具有较高的可靠性。
热管技术在热能工程中的应用探究

热管技术在热能工程中的应用探究在科学技术不断发展的今天,热管技术的应用也更加普遍,受到了人们的广泛关注,在各个领域中都取得了很大的成就。
本文主要是对热管技术在热能工程中的应用做出简单的探究,从热管的组成部分、工作原理以及分类等方面出发,对热管技术的应用情况作出一系列的分析,为以后进一步的使用提供参考。
标签:热管技术;热能加工;应用0 引言热管一般是由管壳、吸液芯和端盖三个部分组成,它的工作过程是由液体的蒸发、蒸汽的流动、蒸汽的凝结和凝结液的回流组成的闭合循环。
这种结构使热管能够处于一种封闭的状态,并且能够承受外界较大的压力,同时保证了内部结构的稳定。
热管技术现已广泛地应用于宇航、电子、动力、化工、冶金、石油、交通等许多部门,是一种新型的传热元件。
1 热管的工作原理根据热管的传热状况,可以将热管的工作过程分为蒸发段、输送段、凝结段三个工作阶段。
当热源對热管的一端进行加热时,工作液受热沸腾而蒸发,蒸气在压差的作用下高速地流向热管的另一端,在另一端放出潜热而凝结。
凝结液在吸液芯毛细抽吸力的作用下,从冷端返回热端。
如此反复循环,热量就从热端不断地传递到冷端,这种循环是快速进行的,热量可以被源源不断地传导开来。
在热量进行传递的过程中,要将两个部分的传递划分开来,这样做的好处是能够保证热量的有效传递,确保它在传递的过程中不会发生过多的热量损失。
2 热管的分类热管的类型很多,通常按照不同的划分标准有不同的分类方式。
按工作温度划分,热管一般分为极低温热管(工作温度低于-200℃)、低温热管(工作温度在-200℃~50℃)、常温热管(工作温度在50℃~250℃)、中温热管(工作温度在250℃~600℃)、高温热管(工作温度高于600℃)。
按工作液回流的原理划分,热管一般分为内装有吸液芯的有芯热管、两项闭式热虹吸管、重力辅助热管、旋转热管。
按形状划分,热管一般分为管形、板形、室形、L形、可弯曲形等。
3 热管技术的特点(1)安全性。
热管的原理和应用是什么
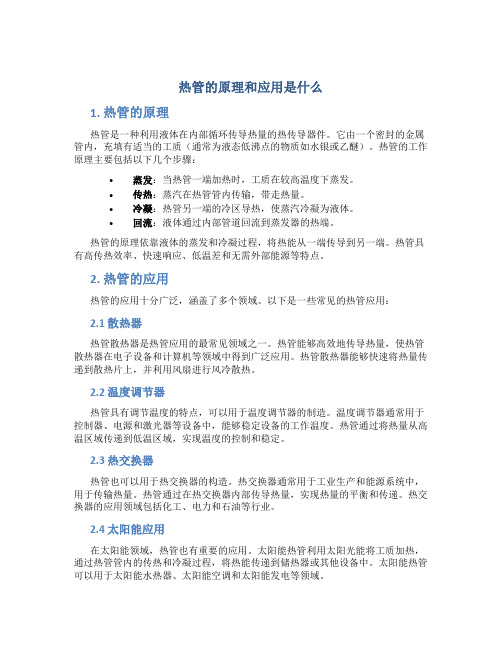
热管的原理和应用是什么1. 热管的原理热管是一种利用液体在内部循环传导热量的热传导器件。
它由一个密封的金属管内,充填有适当的工质(通常为液态低沸点的物质如水银或乙醚)。
热管的工作原理主要包括以下几个步骤:•蒸发:当热管一端加热时,工质在较高温度下蒸发。
•传热:蒸汽在热管管内传输,带走热量。
•冷凝:热管另一端的冷区导热,使蒸汽冷凝为液体。
•回流:液体通过内部管道回流到蒸发器的热端。
热管的原理依靠液体的蒸发和冷凝过程,将热能从一端传导到另一端。
热管具有高传热效率、快速响应、低温差和无需外部能源等特点。
2. 热管的应用热管的应用十分广泛,涵盖了多个领域。
以下是一些常见的热管应用:2.1 散热器热管散热器是热管应用的最常见领域之一。
热管能够高效地传导热量,使热管散热器在电子设备和计算机等领域中得到广泛应用。
热管散热器能够快速将热量传递到散热片上,并利用风扇进行风冷散热。
2.2 温度调节器热管具有调节温度的特点,可以用于温度调节器的制造。
温度调节器通常用于控制器、电源和激光器等设备中,能够稳定设备的工作温度。
热管通过将热量从高温区域传递到低温区域,实现温度的控制和稳定。
2.3 热交换器热管也可以用于热交换器的构造。
热交换器通常用于工业生产和能源系统中,用于传输热量。
热管通过在热交换器内部传导热量,实现热量的平衡和传递。
热交换器的应用领域包括化工、电力和石油等行业。
2.4 太阳能应用在太阳能领域,热管也有重要的应用。
太阳能热管利用太阳光能将工质加热,通过热管管内的传热和冷凝过程,将热能传递到储热器或其他设备中。
太阳能热管可以用于太阳能水热器、太阳能空调和太阳能发电等领域。
2.5 其他领域此外,热管在航空航天、医学设备、冷却系统和热管理等领域也有着广泛的应用。
在飞行器中,热管可以用于控制温度和传导热量;在医学设备中,热管可以用于控制温度并保持设备正常工作。
总之,热管通过其独特的工作原理,在多个领域中发挥着重要的作用。
电热管原理及应用特点

电热管原理及应用特点电热管是一种能够将电能转化为热能的装置,其原理是通过电流在热电阻丝中流动,产生电阻热效应,从而将电能转化为热能。
电热管主要由热电阻丝、加热底座、绝缘层、屏蔽层等组成。
热电阻丝是电热管的核心部件,一端固定在加热底座上,另一端与电源相连。
当电流通过热电阻丝时,由于热电阻丝的电阻率较大,电流在丝中流动时会产生较大的电阻热效应,将电能转化为热能。
热能会通过加热底座传导给需要加热的物体,实现加热的目的。
电热管具有以下几个应用特点:1. 高效能:电热管转化电能为热能的效率较高,可以将大部分的电能转化为热能,提高能源利用率。
2. 温度易控制:电热管的温度可以通过调节电流的大小来控制,可以根据需要调整加热的温度范围,实现精确的温度控制。
3. 可靠性高:电热管由于没有机械运动部件,因此结构简单,故障率低,使用寿命长,能够长时间稳定工作。
4. 加热均匀:电热管能够均匀地加热整个加热面积,避免了传统加热方法中加热不均匀的问题。
对于需要大面积加热的材料,使用电热管能够保证加热的均匀性。
5. 可控制加热区域:电热管可以根据需要进行分段控制,将加热区域分成不同的段,分别控制加热的温度和时间,以满足不同工艺流程的需求。
电热管在工业生产中有着广泛的应用,主要体现在以下几个方面:1. 加热:电热管可以用于各种工业加热需求,如加热热水器、加热锅炉、加热胶水等。
电热管具有高效、温度易控制、加热均匀等优点,能够满足不同加热需求的要求。
2. 干燥:电热管可以用于干燥设备中,通过将电热管安装在干燥设备中,产生的热能可以将湿气蒸发掉,实现干燥的目的。
电热管的温度易控制,能够根据不同材料要求调整温度,实现高效的干燥效果。
3. 热处理:电热管可以用于金属材料的热处理,在热处理过程中,可以通过电热管提供所需的加热温度和时间。
电热管能够均匀加热整个金属材料,避免了传统加热方法中的不均匀加热问题,提高热处理的质量。
4. 分析仪器:电热管可以应用于分析仪器中,如气相色谱仪、液相色谱仪等,用于加热样品。
热管技术及其工程应用
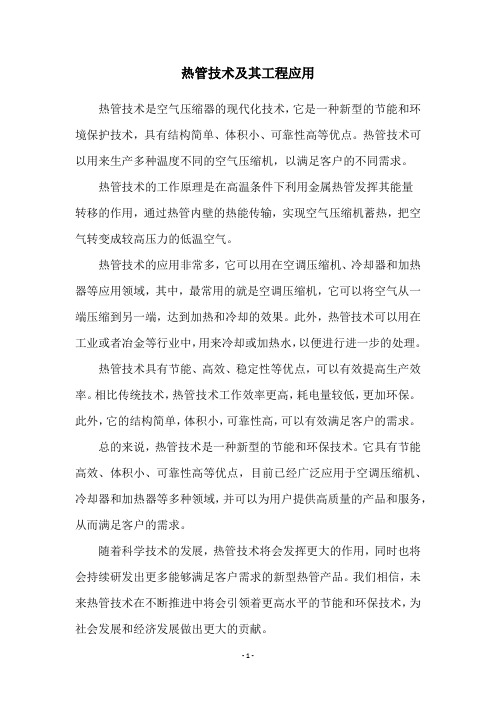
热管技术及其工程应用
热管技术是空气压缩器的现代化技术,它是一种新型的节能和环境保护技术,具有结构简单、体积小、可靠性高等优点。
热管技术可以用来生产多种温度不同的空气压缩机,以满足客户的不同需求。
热管技术的工作原理是在高温条件下利用金属热管发挥其能量
转移的作用,通过热管内壁的热能传输,实现空气压缩机蓄热,把空气转变成较高压力的低温空气。
热管技术的应用非常多,它可以用在空调压缩机、冷却器和加热器等应用领域,其中,最常用的就是空调压缩机,它可以将空气从一端压缩到另一端,达到加热和冷却的效果。
此外,热管技术可以用在工业或者冶金等行业中,用来冷却或加热水,以便进行进一步的处理。
热管技术具有节能、高效、稳定性等优点,可以有效提高生产效率。
相比传统技术,热管技术工作效率更高,耗电量较低,更加环保。
此外,它的结构简单,体积小,可靠性高,可以有效满足客户的需求。
总的来说,热管技术是一种新型的节能和环保技术。
它具有节能高效、体积小、可靠性高等优点,目前已经广泛应用于空调压缩机、冷却器和加热器等多种领域,并可以为用户提供高质量的产品和服务,从而满足客户的需求。
随着科学技术的发展,热管技术将会发挥更大的作用,同时也将会持续研发出更多能够满足客户需求的新型热管产品。
我们相信,未来热管技术在不断推进中将会引领着更高水平的节能和环保技术,为社会发展和经济发展做出更大的贡献。
热管的应用及原理

热管的应用及原理1. 热管的应用热管是一种热传导和热控制装置,广泛应用于各个领域。
以下是热管的主要应用领域:1.电子器件散热:热管可以将电子器件产生的热量传导到远离器件的散热器上,提高散热效率,有效保护电子器件的工作稳定性。
2.航天航空工业:热管在航天航空领域中广泛应用,可以用于航天器的温度控制和热管理,提高航天器的可靠性和性能。
3.能源领域:热管在核能、太阳能和化学能等能源领域的转换和利用过程中起着重要的作用,可以提高能源转换效率和能量利用率。
4.家电电器:热管在家电电器中的应用也很常见,如电冰箱、空调、热水器等,可以提高设备的能效和使用寿命。
5.医疗器械:热管在医疗器械中被广泛应用,如医用激光设备、核磁共振设备等,可以提高设备的性能和稳定性。
2. 热管的原理热管是一种利用液体的相变和循环来传热的装置。
其基本原理如下:1.工作介质:热管通常由内部充满工作介质的密封管道组成,工作介质一般为易于相变的液体,如水、乙醇、铵等。
2.热力学循环:热管的工作过程是一个闭合的热力学循环过程。
首先,在热管的一端,工作介质吸收热量并蒸发成气体;然后,气体通过压力差的作用将热量传导到热管的另一端;最后,在热管的另一端,气体冷却并凝结成液体,释放热量。
3.热传导:在热管的工作过程中,热量通过工作介质的相变和循环传导,从而实现热量的传递。
4.热阻和热导率:热管的热传导效果主要由热阻和热导率决定。
热阻指的是热量在热管中传导过程中的阻碍程度,而热导率则指的是热量在工作介质中的传导性能。
3. 热管的优势热管具有以下几个优势,使其成为热传导和热控制领域中的重要装置:1.高热传导效率:热管内部的工作介质可以高效传导热量,因此热管具有很高的热传导效率。
2.无需外部动力驱动:热管通过工作介质的相变和循环实现热量的传递,无需外部动力驱动,省去了能源消耗和故障风险。
3.可靠性高:热管的结构简单,传热过程中无机械运动,因此具有较高的可靠性和稳定性。
热管技术及其工程应用

热管技术及其工程应用热管技术是一种先进的节能技术,它可以有效地降低用电量,减少能源消耗,从而改善和保护环境。
它的应用范围涉及汽车、建筑、制冷、供热、热水系统等多个领域,能有效改善能效,减少污染物的排放,提高能源利用率。
热管技术最早出现在20世纪50年代。
当时,它主要用于电力行业,以减少电力消耗。
随着科学技术的发展和人们对节能的重视,热管技术和热管工程得到了越来越多的应用。
汽车行业首先采用热管技术,其最突出的特征是体积小、重量轻、效率高。
它不仅可以减少发动机油耗,而且可以缩短发动机运行时间,减少排放,提高汽车性能。
热管技术还可以用于汽车空调系统,改善车辆内部环境,减少空调系统的耗电量。
在建筑行业中,热管技术的应用更加广泛。
它可以用于采暖和供热系统,可以改善房间的温度和湿度,减少用电量,延长设备的使用寿命。
热管技术还可以用于室外温控,改善外部建筑的热损失,保持室外环境的舒适度,减少能耗。
另外,热管技术也可以用于电子行业,如制冷系统、激光器、半导体芯片等。
它可以有效控制芯片的温度,降低元器件损坏的可能性,提高制冷系统的效率,减少制冷剂的排放量。
此外,热管技术在工业过程中也有重要应用。
热管可以有效控制工业设备的温度,维持运行环境的稳定,减少能源消耗,降低污染物排放。
比如,在石油化工、电镀、液体冶炼等领域,采用热管技术可以减少热能损失,提高能效,节约能源。
热管技术已经成为节能减排的重要解决方案。
热管工程应用可以大大减少用电量,同时还可以改善效率,提高能效,改善和保护环境,是21世纪最受欢迎的技术之一。
因此,决定采用热管技术的话,必须找到一个有经验的热管工程商来为系统定制布线方案,确保热管工程的顺利实施,实现节能减排的目标。
只有通过广泛采用热管技术和热管工程,才能推动绿色能源发展,实现节能减排,建设绿色家园。
总之,热管技术和热管工程的应用使能源资源有效利用,推动绿色能源发展,保障环境的健康发展,为构建美丽家园作出贡献。
热管技术在合成氨工业节能中的应用

和控 制合 成氨 生产 放 出的 热 量 , 不 仅 可 以 节 约 生产 中的 能 耗 , 降低 成 本 , 还 可 以提 高 C O 变换 率及 氨 的 合成 率 。 关键 词 : 热管技术 ; 合成氨 ; 节能 ; 应用 1上 、 下行 煤 气 余 热 回收 回收 的技 术 改 造 。 上、 下 行 煤 气 是 指 以煤 或煤 球 为原 料 的生 产 路 线 中煤 造 气 炉 所 2 . 2 中型 合 成 氨 吹 风气 燃 烧 热 的利 用 产生的上吹半水煤气及下吹半水煤气。 由于生产原料不 同, 上、 下行 中小合成氨不 同之处在于所有中型合成氨厂以煤造气的工段 , 煤气气体中所含尘粒及温度也不相同。 吹风气都经过燃烧室燃烧后再进入废热锅炉 回收余热 。 原有的列管 1 . 1小合成氨上 、 下行煤气余热 回收 式 废 热 锅 炉 都 是按 瞬时 最 大 吹 风 气 流 量 设 计 的 , 而 吹风 气 在 一个 循 小合成氨生产 大都使用煤球为原料造气 。 其特点是 由煤造气炉 环中只占 2 5 %~ 2 8 %的时间, 所 以设备 的利用率不 高。即使上行煤气 的上 、 下 行煤气 的温度较低 , 气体成分复杂含有大量粉尘及水蒸气 , 也通过废热锅炉 , 也只有 5 0 %一 6 0 %的利用率 , 何况上行 煤气 的流量 容易引起低温腐蚀及灰尘堵塞等一系列问题。 在设计此类设备 中应 仅是 吹风气瞬时流量的 1 / 3 ,所以合理的办法是将三台煤气炉的吹 重 点 考 虑 以下 问题 : 风气 通过一个燃烧室燃烧 ,燃烧后的烟气再进入一个废热锅 炉 , 这 ( 1 ) 由于气体 温度低 , 可利用传热温差 很小 , 要 回收一定热量必 就大大提 高了设备 的利用率 。 虽然利用原有 的列管式废 热锅 炉也可 须要有很大 的传热面积 , 传热面积过大不仅 占地大 、 金属耗量 大 , 成 做到这一点 , 但原有 的废热锅 炉设 计的气体流速均相 当高 , 锅炉进 本也高 ; 口处 的流速高达 2 0 m / s 以上。因此 , 高速磨损经常是管壁破坏 的原 ( 2 ) 上、 下行煤气含 有大量粉尘 和水 蒸气特别是下 行煤气含尘 因之一 。如果 三台煤气炉的吹风气都经过 同一锅炉 , 则 磨损 时间将 量最多 , 每标准立方米气体 的含 尘量估算在 3 0 g以上 ; 增大两倍 , 因而其磨损破坏概率也将增大两倍 。 ( 3 ) 这种成分的气体温度不宜降得过低 , 否则易达到露点 , 一旦 3 一段 转 化 炉 空 气 预 热器
热管技术在油田加热炉节能改造中的应用

1. 引言热管技术是一种利用热管在高温热源和工艺设备之间传递热量的先进技术,已经在许多领域得到了广泛应用。
其中,在油田加热炉节能改造中的应用尤为突出。
本文将从热管技术的基本原理、在油田加热炉中的应用、节能改造效果以及未来发展前景等方面展开探讨。
2. 热管技术的基本原理热管是一种利用液体的汽化和凝结来传递热量的装置。
其基本原理是利用液体在热管内部蒸汽化形成蒸气,然后在冷却段凝结成液体,从而完成热量的传递。
这种独特的传热方式使得热管技术在能源转换、热管理和节能领域具有广泛的应用前景。
3. 热管技术在油田加热炉中的应用在油田加热炉中,热管技术可以被应用于燃烧室、换热器和回收装置等部分。
通过将热管技术应用于油田加热炉中,可以实现燃料的高效利用和能量的有效回收,从而实现节能降耗的目的。
4. 节能改造效果经过热管技术的应用,油田加热炉的节能改造效果十分可观。
由于热管技术能够实现热能的高效传递和回收,因此可以大大减少能源的浪费。
通过热管技术的应用,油田加热炉的工作温度和燃烧效率都得到了有效提高,进一步实现了能源的节约和环境的保护。
5. 未来发展前景随着工业技术的不断发展和创新,热管技术在油田加热炉中的应用前景愈发广阔。
未来,我们可以预见热管技术将在油田加热炉的节能改造中发挥越来越重要的作用,为能源的可持续利用和环境的可持续发展提供更加坚实的技术支持。
6. 个人观点和理解作为一种先进的传热技术,热管技术在油田加热炉中的应用对于节能减排具有重要意义。
它不仅能有效提高油田加热炉的能源利用率,还能减少对环境的负面影响。
我对热管技术在油田加热炉中的应用前景充满信心,相信它将在未来发展中发挥越来越重要的作用。
7. 总结热管技术在油田加热炉节能改造中的应用已经取得了显著的成果,而且在未来发展中仍具有巨大的潜力。
通过深入探讨热管技术的基本原理、在油田加热炉中的应用、节能改造效果以及未来发展前景,我们可以更好地认识到热管技术在能源领域的重要作用,为其持续发展提供更好的技术支持和指导。
热管技术及其工程的应用

热管技术及其工程应用(1)Heat pipe Technology and Engineering Application什么是热管?热管从何而来?有什么作用?热管工作的原理是什么?有何特性?热管跟普通的“管”有什么区别?什么是热管换热器?常见的热管有哪些种类?如何设计热管换热器?我们日常生活中有哪些场合使用了热管换热器?热管换热器的研究发展前景如何?第一章绪论一.热管换热器的研究背景当今传热工程面临两大问题:研究高绝热材料和高导热材料。
具有良好导热性的材料有铝[(λ=202W/m•℃)]、柴铜[λ=385W/ m•℃]、和银:λ=410W/ m•℃)],但其导热系数只能达到102W/m•℃的数量级,远不能满足某些工程中的快速散热和传热需要,热管的发明就解决了这一问题。
热管的相当导热系数可达105 W/m•℃的数量级.为一般金属材料的数百倍乃至上千倍。
它可将大量热量通过很小的截面积远距离地传输而无需外加动力。
由于热管具有导热性能好、结构简单、工作可靠、温度均匀等良好性能.热管是传热领域的重大发明和科技成果,给人类社会带来巨大的实用价值。
热管的发展史· 热管的原理首先是由美国俄亥俄州通用发动机公司的R.S.Gaugler于1944年在美国专利中提出的。
· 1962年L.Trefethen再次提出类似于Gaugler的传热元件用于宇宙飞船,但因这种建议并未经过实验证明,亦未能付诸实施。
· 1967年一根不锈钢-水热管首次被送入地球卫星轨道并运行成功,从此吸引了很多科学技术工作人员从事热管研究。
· 1970年在美国出现了供应商品热管的部门,热管的应用范围从宇航扩大到了地面。
· 1980年美国Q-Dot公司生产了热管废热锅炉,日本帝人工程公司也成功地用热管做成锅炉给水预热器,解决了排烟的露点腐蚀问题。
· 1984年Cotter较完整地提出了微型热管的理论及展望,为微型热管的研究与应用奠定了理论基础。
热管工作原理

热管工作原理引言概述:热管是一种热传导设备,利用液体在低温端蒸发吸热,蒸汽在高温端凝结释放热量的原理,实现热量的传递。
热管在许多领域有着广泛的应用,如电子设备散热、航天器件冷却等。
下面将详细介绍热管的工作原理。
一、热管的基本结构1.1 热管由内管、外管和工作流体组成,内管和外管之间充满了工作流体。
1.2 内管表面通常采用特殊涂层,以增强表面张力,减小液滴的尺寸。
1.3 工作流体通常为高导热性的液体,如水、乙醇等。
二、热管的工作原理2.1 当热管的低温端受热时,工作流体在内管内蒸发,吸收热量,形成蒸汽。
2.2 蒸汽在热管中向高温端传输,并在高温端凝结释放热量,将热量传递给外部环境。
2.3 凝结后的液体由于表面张力的作用,会沿着内管壁流回低温端,完成热量传递循环。
三、热管的优点3.1 热管具有高效的热传导性能,能够快速传递热量。
3.2 热管结构简单、可靠,使用寿命长。
3.3 热管可以实现热量的定向传递,适用于复杂的热传导环境。
四、热管的应用领域4.1 电子设备散热:热管可以有效地将电子设备产生的热量传递到散热器中,提高散热效率。
4.2 航天器件冷却:在太空环境中,热管可以帮助航天器件快速散热,确保器件正常工作。
4.3 工业生产:热管在工业生产中也有着广泛的应用,可以用于加热、冷却等工艺。
五、热管的发展趋势5.1 热管的材料和结构不断改进,提高了热传导效率。
5.2 热管在微型化和集成化方面有着更广阔的应用前景。
5.3 随着技术的不断进步,热管将在更多领域得到应用,为人类社会的发展做出更大的贡献。
总结:热管作为一种高效的热传导设备,具有许多优点和广泛的应用领域。
通过不断的技术改进和创新,热管将在未来发展中发挥更加重要的作用,为各行各业提供更好的热传导解决方案。
- 1、下载文档前请自行甄别文档内容的完整性,平台不提供额外的编辑、内容补充、找答案等附加服务。
- 2、"仅部分预览"的文档,不可在线预览部分如存在完整性等问题,可反馈申请退款(可完整预览的文档不适用该条件!)。
- 3、如文档侵犯您的权益,请联系客服反馈,我们会尽快为您处理(人工客服工作时间:9:00-18:30)。
1热管在工业中的应用——使用热管进行余热回收上、下行热管蒸汽发生器上置式热管余热锅炉性能特点应用范围广——适用于气-气(汽),气液或液-液等等多介质间热交换;换热效率高——热管换热器当量传热系数K比列管式换热器要提高5~10倍,换热效率高;流动阻力小——两种介质均在管外流动,流程短且介质流动方向与散热片方向一致,降低了流动阻力;结构简单紧凑——由加肋片的热管制成的换热器结构紧凑,设备体积小,质量轻,节省钢材和安装空间;不易产生露点腐蚀——可通过调节冷热介质间的换热面积比来调节热管表面温度,避免发生露点腐蚀和低温腐蚀;不易结垢、阻塞——设计时可将介质流速调整到自清灰以上,并调整热管的安装位置即可达到自清灰的目的,且结灰后便于清理;良好的可拆卸性——热管间彼此独立工作,并可与设备使用法兰连接,适于分别拆卸和单独更换;使用寿命高——热管使用寿命在10年以上,单根热管破坏,不影响整体运行,保证设备长期稳定运行;维护费用低——无需传动部件,设备正常操作期间不需维护。
适用范围化工及石油化工合成氨工业——上、下行煤气余热回收流程;吹风气燃烧气余热回收流程;一段转化炉空气预热器;变换工段气-气换热器;二段转化炉高温高压蒸汽发生器;绝热化学反应器级间热管换热器及其它换热、余热回收设备。
硫酸工业——沸腾焙烧炉沸腾层内的余热回收;沸腾焙烧炉矿渣余热回收;SO2炉气余热回收;SO3气体冷却器;热管SO2转化器;热管开工预热器及其它换热、余热回收设备。
盐酸、硝酸工业——盐酸炉余热回收;氨氧化炉热管蒸汽发生器及其它换热、余热回收设备。
石油化工——热管裂解炉;热管乙苯脱氢反应器;环己醇脱氢化学反应器;热管氧化反应器;催化裂化再生取热器;热管化学反应釜;苯酐热熔冷凝箱;加热炉余热回收及其它换热、余热回收设备。
建材及轻纺工业高岭土喷雾干燥热风炉;十二醇硫酸钠喷雾干燥热风炉;玻璃窑炉的余热回收;水泥工业中窑尾冷却机的余热利用及窑尾废气的余热利用;纺织工业中热定型机、沙浆机烘干机等余23热回收设备。
冶金工业加热炉和均温炉、烧结工序、高炉热风炉等设备的余热回收。
动力工程油、汽混烧电站锅炉、劣质煤料锅炉空气预热器;工业锅炉;柴油机排气余热回收等。
余热回收的几种流程用热管换热器从工业炉的排气中回收余热以加热空气,余热后的空气返回工业炉为助燃空气使用。
流程如图1所示:用热管散热器从排气中回收余热以加热空气,使之成为热风可作为供房的热源。
流程如图2所示:图2:热管热风炉将热管换热器回收的余热用来加热水,使之成为锅炉给水,或使水产生蒸汽供其他方面使用。
其流程如图3、图4所示:图3:热管余热锅炉烟囱烟囱 烟囱4图4:热管省煤器将热管换热器从排气中回收来的余热再次加热排气自身,使得经洗涤过的气体温度升高,以免腐蚀排烟设备。
流程如图5所示:图5:热管换热器余热回收流程图6:热管在工业中的应用现场照片热管在工业锅炉中的运用工业锅炉容量较小,参数低,故此运行效率较低,一般为65%左右,其节能潜力较大。
炉子烟囱加热器加热器洗涤塔热管换热器热管省煤器给水给水燃料烟囱锅炉除了改善燃烧、降低灰渣含碳量以外,降低排烟温度减少热量损失是提高工业锅炉效率的重要措施。
工业锅炉的省煤器和空气预热器的效率不高,因之热管技术在工业锅炉尾部的应用显得非常重要。
我们在国内数百家单位使用热管余热回收起到很好的效果。
表1列出了工业锅炉改装热管空气预热器前后的参数对比,可以看出改装后锅炉的效率提高了10%,表2列出了工业锅炉尾部热管空气预热器的参数。
表2. 热管换热器主要参数5应用实例:某化工厂一台6.5T/h的蒸汽锅炉,由于省煤器及空气预热器效率不高,锅炉出口排烟温度在220℃左右。
回收这部分低温余热可以获得较大的经济效益。
其流程如下:6余热回收流程图在锅炉出口的烟道中装设热管蒸汽发生器,出锅炉温度为220℃左右的烟气经过热管的蒸发段,降至140℃以下,经引风机送入烟筒。
给水温度为90℃左右,产生0.25Mpa (绝压)饱和蒸汽送给工艺工段使用。
运行6个月后,检查热管基本无积尘、无腐蚀现象,由于锅炉操作负荷的变动,该蒸汽发生器进口温度一直在180~220℃之间波动,但出口温度始终在140℃以下。
运行3个月、6个月的测试结果如表3:由此可见:在长期运行过程中,烟气的出口温度始终保持140℃左右,该装置的平均热负荷(以产生蒸汽量计)为7.15ⅹ105KJ/hr,相当于节约标准煤35Kg/h(标准煤按104KJ/Kg,锅炉效率按70%计),年节省标准煤277.2吨,每吨150元计,年收益为4.158万元。
热管蒸气发生器应用实例表3. 应用热管的余热锅炉热负荷测试结果7热管在水泥、陶瓷、冶金工业中的运用8工业窑炉(冶炼炉)是耗能大户,且窑炉的种类十分繁多,炉子的热效率国内平均水平为国外先进水平的一半,总计年耗标准煤一亿多吨,有很大的节能潜力,其排烟温度较高,往往超过300℃,有的达到500~600℃甚至更高,作为余热回收方案而言,较多采用空气预热器(当然也可采用余热锅炉),对于烟气温度在400℃以下的中低温余热,主要采用空气预热器,热管换热器在此能够大显身手。
我国机械工业部标准《机械工业节能设计技术规定》中提到:工业炉窑排烟温度为400℃以下时,宜采用热管换热器。
工业炉窑中有相当大一部分没有装引风机,要求余热设备阻力小,同时因地位狭小,而要求设备紧凑,特别适合应用热管空气预热器。
主要应用以下几种布置方式:⑴、窑炉+热管空气预热器⑵、窑炉+热管热水器+热管空气预热器(适用于排烟温度很高时)⑶、窑炉+喷流或渗铝管空气预热器+热管空气预热器(适用于较高的预热空气温度时)⑷、窑炉+各种型式空气预热器+热管热水器或热管开水器与热水器复合装置⑸、窑炉+热管余热锅炉⑹、窑炉+其它换热器+热管余热锅炉⑺、窑炉+热管余热锅炉+其它换热器一、空气预热器或余热锅炉热管换热器型式的确定,应当从以下几个方面考虑:1、根据企业的需要,如果工业窑炉需要助燃,应尽可能选用空气预热器。
工艺需要蒸汽时,用余热锅炉。
2、根据余热回收的可能性,余热锅炉只有在排烟温度大于300℃的工业炉中才有可能。
3、可靠性,如果采用碳钢一水热管,其管内工质最高工作温度为300℃,以保证安全;热管外侧最低壁面大于酸露点,以避免腐蚀。
这些限制对换热器式的选择也会有直接的影响。
4、经济性,型式的选择在有多种方案可能时,需进行经济性比较,根据具体情况选用上述几种方式。
二、气-气及气-水组合型热管换热器由于工业窑炉的排烟温度往往较高,有时超过400℃,可达到500~600℃,甚至更高。
9作为气—气型热管换热器,最高允许的烟气入口温度在一般情况下仅为350~400℃,此时采用气—水及气—气组合型热管换热器是一种很好的方案,即为烟气温度高于350~400℃的区域应用气—水式换热器,而在烟气温度较低的区域应用气—气型热管换热器。
以上的划分温度是以应用碳钢一水热管为依据的,其工质的最高允许温度为300℃,具体属于上述形式⑵。
三、热管换热器的匹配工业窑炉有时需要300~400℃或更高温度的热空气助燃。
当热空气温度超过250℃时,只用热管空气预热器会使碳钢一水热管的最高工作温度超过300℃,因此空气从进口温度加热到250℃时采用热管空气预热器,而从250℃上升到更高值时采用常规空气热器,这是一种合理的布置方式,如上述形式⑶。
常规空气预热器可以选用渗铝钢管式或喷流式,因为它们可以与热管空气预热器很好地匹配在一起。
四、热管余热锅炉的不同类型热管余热锅炉可以分为二大类型:单管型及联箱型,前者适用于小容量的余热锅炉,热管放段直接插入汽包内,我们研制的最大容量为2t/h(蒸发量);后者适用于大容量的余热锅炉,热管放热段插入垂直的大直径管中,这些大直径管由联箱再引出管子通至汽包,我们研制的容量为1—10t/h(蒸发量)。
这二种形式蒸汽侧的结构是不同的。
由于受至碳钢-水热管工质最高工作温度为300℃的限制,余热锅炉蒸汽工作压力不会超过1MPa,烟气入口温度一般也不能太高,如450~500℃为最高值。
当烟气进口温度很高时,可采用上述形式⑹。
五、工业窑炉中的气—水型热管换热器在工业窑炉中,由于生活的需要或生产工艺的需要,有时需要应用上述形式⑷,不少情况下,为热管热水器与开水器复合装置,它有相当广泛的应用前景,特别是在乡镇企业。
热管在化工及石油化工中的应用一、热管技术在合成氨工业生产中有以下几种应用类型:101、回收低温余热预热助燃空气,或生产低压蒸汽作为生产原料;2、回收高温余热产生中压蒸气作原料蒸汽的补充,或生产高压蒸汽作为生产的动力源;3、控制固定床催化反应器的化学反应温度,使其向最佳反应温度曲线无限逼近,从而提高CO变换反应器的CO变换率及合成氨塔内氨的合成率。
以上三种应用类型,在不同的生产规模及不同的原料工艺路线中应用的方式及设计思路均不同,必须针对不同的实际条件采用不同的结构设计才能才能收到良好的效果。
以上、下行煤气余热回收为例:上、下行煤气余热回收的热管蒸汽发生器,如图1、2所示,体积紧凑、占地面积,气体流动方向为从上到下,减少灰尘附着于管壁的可能性;热管的蒸发段全部采用轴向直翅片,一方面可以扩展传热表面,另一方面可消除热管背部的涡流区,不使灰尘在此停聚,减少流动阻力损耗。
适用于小合成氨生产。
热回收流程表1.是某工段采用热管蒸汽发生器与原列管式余热锅炉的参数对比表。
从中可以看出热管蒸汽发生器的优越性。
中合成氨因工艺的不同,煤造气炉的下行煤气(200℃左右)不经过废热锅炉而直接去洗气塔,造成低温余热的浪费,而且列管式废热锅炉容易损坏,设备利用率不高。
根据这些情况,采用热管技术可有两种途径。
表1. 两种蒸汽发生器参数对比1、原有废热锅炉后加一台热管低温余热回收装置,将废热锅炉出口270℃的气体降至140℃,同时将下行煤气也经过热管装置。
热管装置可以是气-气式的,即用回收的低温余热加热进入煤气炉的空气或过热低压水蒸汽;也可以是热管省煤器的形式,加热废热锅炉的给水。
其流程如图3。
图3:低温余热回收流程2、为充分考虑设备利用率及余热回收率,可在每一台煤造气炉后加一台热管蒸汽发生器专供上、下行煤气余热回收,而将三台煤气炉的吹风气通过一个燃烧室燃烧后进入一台热管废热锅炉,可使设备的利用率达75%~84%。
二、热管技术在硫酸工业中的应用由于硫酸生产是连续性生产,生产过程中的高温,矿尘磨损,高、低温腐蚀等因素常使设备受到侵害,致使整个生产停顿造成损失。
热管设备的个别管件损坏不会影响整体设备效能,因之不需要停工检修,故热管技术在硫酸生产中具有广阔的应用远景。
热管技术在硫酸生产中可以应用在以下几个工序中。
1、沸腾焙烧炉沸腾层内的余热回收2、沸腾焙烧炉矿渣余热回收3、SO2炉气余热回收4、SO3气体冷却器5、热管SO2转化器6、热管开工预热器以沸腾焙烧炉沸腾层内的余热回收为例。