列管式换热器结构设计示例.
换热器设计案例
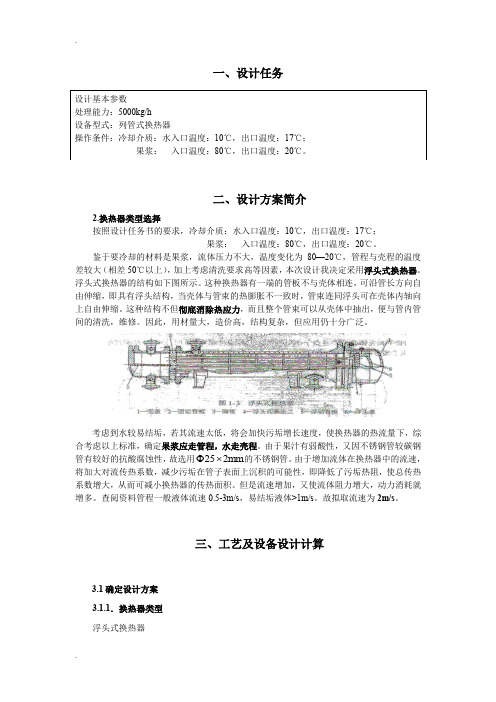
一、设计任务二、设计方案简介2.换热器类型选择按照设计任务书的要求,冷却介质:水入口温度:10℃,出口温度:17℃;果浆: 入口温度:80℃,出口温度:20℃。
鉴于要冷却的材料是果浆,流体压力不大,温度变化为80—20℃,管程与壳程的温度差较大(相差50℃以上),加上考虑清洗要求高等因素,本次设计我决定采用浮头式换热器。
浮头式换热器的结构如下图所示。
这种换热器有一端的管板不与壳体相连,可沿管长方向自由伸缩,即具有浮头结构,当壳体与管束的热膨胀不一致时,管束连同浮头可在壳体内轴向上自由伸缩。
这种结构不但彻底消除热应力,而且整个管束可以从壳体中抽出,便与管内管间的清洗,维修。
因此,用材量大,造价高,结构复杂,但应用仍十分广泛。
考虑到水较易结垢,若其流速太低,将会加快污垢增长速度,使换热器的热流量下,综合考虑以上标准,确定果浆应走管程,水走壳程。
由于果汁有弱酸性,又因不锈钢管较碳钢管有较好的抗酸腐蚀性,故选用mm 225⨯Φ的不锈钢管。
由于增加流体在换热器中的流速,将加大对流传热系数,减少污垢在管子表面上沉积的可能性,即降低了污垢热阻,使总传热系数增大,从而可减小换热器的传热面积。
但是流速增加,又使流体阻力增大,动力消耗就增多。
查阅资料管程一般液体流速0.5-3m/s ,易结垢液体>1m/s 。
故拟取流速为2m/s 。
三、工艺及设备设计计算3.1确定设计方案 3.1.1.换热器类型 浮头式换热器设计基本参数处理能力:5000kg/h设备型式:列管式换热器操作条件:冷却介质:水入口温度:10℃,出口温度:17℃;果浆: 入口温度:80℃,出口温度:20℃。
3.1.2.流体流动形式为了增大平均温差,节省操作费用,本次设计采用逆流的流动方式。
3.2确定物性数据定性温度:对于一般液体和水等低黏度流体,其定性温度可取流体进、出口温度的平均 值。
故:果浆的定性温度为 ℃5022080T =+=水的定性温度为 t = ℃13.521710=+果浆在50℃下的有关物性数据如下:密度 : 0ρ= 1058 kg/3m定压比热容: C po =3584 J/(kg·℃) 导热系数 : 0λ =0.61 W/(m·℃)黏度 : = 2×10-3 Pa·s水在13.5℃下的有关物性数据如下:密度 : i ρ = 999.7 kg/3m定压比热容:C pi = 4191 J/(kg·℃) 导热系数 : i λ= 0.58 W/(m·℃)黏度 : i μ= 1.2×10-3 Pa·s3.3计算总传热系数 3.3.1热负荷Kw h KJ 67.298/101.075220)-(803.5845000T C q Q 60P0m0T =⨯=⨯⨯=∆=3.3.2平均传热温差 所以m t ∆=2121ln t t t t ∆∆∆-∆=()()10-2017-80ln 10-201780--=28.8(℃)3.3.3水用量640P0i Q 1.075210 3.66510/C t 4.191(17-10)miq kg h ⨯===⨯∆⨯ μ 03.3.4总传热系数K (1)管程传热系数:43e 10499.3102.17.9992021.0R ⨯=⨯⨯⨯==-iii i u d μρ>4000 (湍流区) 对流传热系数:C/39.650458.0102.14191102.17.9992021.0021.058.0023.0)()(023.034.038.034.0ii 8.0i i i i i ︒⋅=⎪⎪⎭⎫⎝⎛⨯⨯⨯⎪⎭⎫⎝⎛⨯⨯⨯⨯⨯==--m w C u d d p i i λμμρλα(2)壳程传热系数:假设壳程的传热系数10000=α W/(2m ·℃)污垢热阻 Rso=0.0003(m 2·℃)/WRsi=0.0002(m 2·℃)/W管壁的导热系数 λ=17.4W/(m·℃)0000011αλα++++=s m i si i i R d bd d d R d d K℃∙=++⨯⨯+⨯+⨯=2W/m 53.541100010003.00229.04.17025.0002.0021.0025.00002.0021.075.3735025.013.4计算换热面积2m T 2.198.2853.541298670t K Q 'm A =⨯=∆=考虑15%的面积裕度:208.22'15.1m A A ==3.5工艺尺寸计算 3.5.1 管径和流速取mm 225⨯Φ的不锈钢管,流速u=2m/s. 3.5.2 管程数和传热管数依据传热管内径和流速确定单程传热管数2242860/(36001058)180.7850.02114v s i q n d uπ⨯==≈⨯⨯(根)按单管程计算,所需的传热管长度为: 传热管长:m n d A s 63.1518025.014.308.22L 00=⨯⨯==π按单程管设计,传热管过长,宜采用多管程结构。
列管式换热器的设计计算
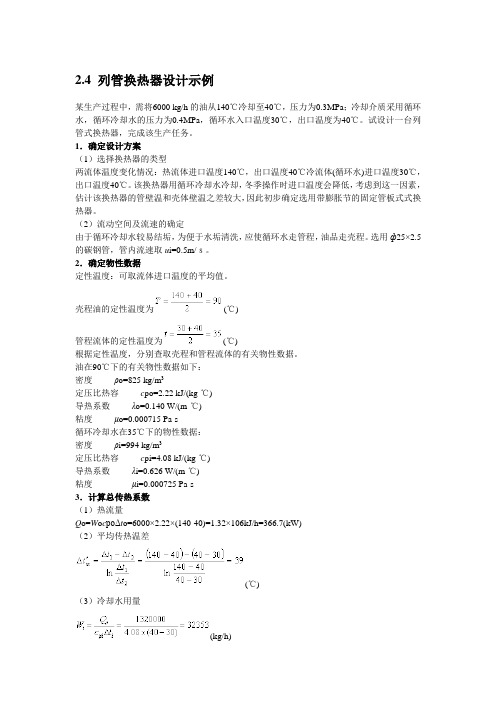
2.4 列管换热器设计示例某生产过程中,需将6000 kg/h的油从140℃冷却至40℃,压力为0.3MPa;冷却介质采用循环水,循环冷却水的压力为0.4MPa,循环水入口温度30℃,出口温度为40℃。
试设计一台列管式换热器,完成该生产任务。
1.确定设计方案(1)选择换热器的类型两流体温度变化情况:热流体进口温度140℃,出口温度40℃冷流体(循环水)进口温度30℃,出口温度40℃。
该换热器用循环冷却水冷却,冬季操作时进口温度会降低,考虑到这一因素,估计该换热器的管壁温和壳体壁温之差较大,因此初步确定选用带膨胀节的固定管板式式换热器。
(2)流动空间及流速的确定由于循环冷却水较易结垢,为便于水垢清洗,应使循环水走管程,油品走壳程。
选用ф25×2.5的碳钢管,管内流速取u i=0.5m/s。
2.确定物性数据定性温度:可取流体进口温度的平均值。
壳程油的定性温度为(℃)管程流体的定性温度为(℃)根据定性温度,分别查取壳程和管程流体的有关物性数据。
油在90℃下的有关物性数据如下:密度ρo=825 kg/m3定压比热容c po=2.22 kJ/(kg·℃)导热系数λo=0.140 W/(m·℃)粘度μo=0.000715 Pa·s循环冷却水在35℃下的物性数据:密度ρi=994 kg/m3定压比热容c pi=4.08 kJ/(kg·℃)导热系数λi=0.626 W/(m·℃)粘度μi=0.000725 Pa·s3.计算总传热系数(1)热流量Q o=W o c poΔt o=6000×2.22×(140-40)=1.32×106kJ/h=366.7(kW)(2)平均传热温差(℃)(3)冷却水用量(kg/h)(4)总传热系数K管程传热系数W/(m·℃)壳程传热系数假设壳程的传热系数αo=290 W/(m2·℃);污垢热阻R si=0.000344 m2·℃/W , R so=0.000172 m2·℃/W管壁的导热系数λ=45 W/(m·℃)=219.5 W/(m·℃)4.计算传热面积(m2)考虑15%的面积裕度,S=1.15×S′=1.15×42.8=49.2(m2)。
化工原理课程设计---列管式换热器的设计
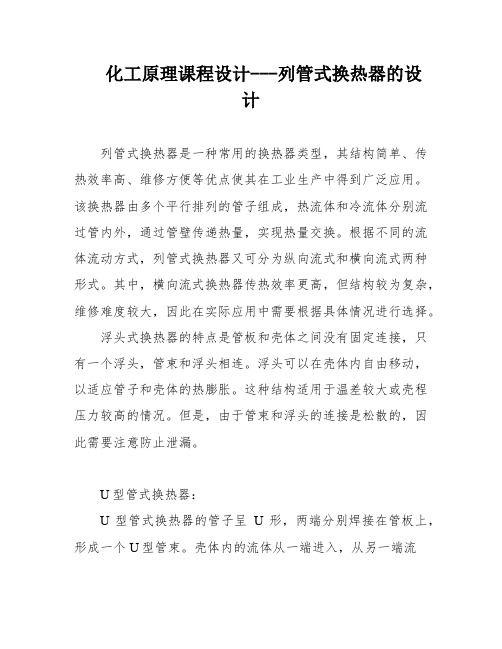
化工原理课程设计---列管式换热器的设计列管式换热器是一种常用的换热器类型,其结构简单、传热效率高、维修方便等优点使其在工业生产中得到广泛应用。
该换热器由多个平行排列的管子组成,热流体和冷流体分别流过管内外,通过管壁传递热量,实现热量交换。
根据不同的流体流动方式,列管式换热器又可分为纵向流式和横向流式两种形式。
其中,横向流式换热器传热效率更高,但结构较为复杂,维修难度较大,因此在实际应用中需要根据具体情况进行选择。
浮头式换热器的特点是管板和壳体之间没有固定连接,只有一个浮头,管束和浮头相连。
浮头可以在壳体内自由移动,以适应管子和壳体的热膨胀。
这种结构适用于温差较大或壳程压力较高的情况。
但是,由于管束和浮头的连接是松散的,因此需要注意防止泄漏。
U型管式换热器:U型管式换热器的管子呈U形,两端分别焊接在管板上,形成一个U型管束。
壳体内的流体从一端进入,从另一端流出,管内的流体也是如此。
这种结构适用于流体腐蚀性较强的情况,因为管子可以很容易地更换。
多管程换热器:多管程换热器是将管束分成多个组,每组管子单独连接到管板上,形成多个管程。
这种结构可以提高传热效率,但也会增加流体阻力。
因此,需要根据具体情况来选择多管程的数量。
总之,列管式换热器是一种广泛应用于化工及酒精生产的换热器。
不同的结构适用于不同的工艺条件,需要根据具体情况来选择合适的换热器。
在使用过程中,需要注意保养和维护,及时清洗和更换损坏的部件,以保证换热器的正常运行。
换热器的一块管板与外壳用法兰连接,另一块管板不与外壳连接,这种结构称为浮头式换热器。
浮头式换热器的优点是管束可以拉出以便清洗,管束的膨胀不受壳体约束,因此在两种介质温差大的情况下,不会因管束与壳体的热膨胀量不同而产生温差应力。
但其缺点是结构复杂,造价高。
填料式换热器的管束一端可以自由膨胀,结构比浮头式简单,造价也较低。
但壳程内介质有外漏的可能,因此不应处理易挥发、易燃、易爆和有毒的介质。
(完整版)列管式换热器设计

第一章列管式换热器的设计1.1概述列管式换热器是一种较早发展起来的型式,设计资料和数据比较完善,目前在许多国家中已有系列化标准。
列管式换热器在换热效率,紧凑性和金属消耗量等方面不及其他新型换热器,但是它具有结构牢固,适应性大,材料范围广泛等独特优点,因而在各种换热器的竞争发展中得以继续应用下去。
目前仍是化工、石油和石油化工中换热器的主要类型,在高温高压和大型换热器中,仍占绝对优势。
例如在炼油厂中作为加热或冷却用的换热器、蒸馏操作中蒸馏釜(或再沸器)和冷凝器、化工厂中蒸发设备的加热室等,大都采用列管式换热器[3]。
1.2列管换热器型式的选择列管式换热器种类很多,目前广泛使用的按其温度差补偿结构来分,主要有以下几种:(1)固定管板式换热器:这类换热器的结构比较简单、紧凑,造价便宜,但管外不能机械清洗。
此种换热器管束连接在管板上,管板分别焊在外壳两端,并在其上连接有顶盖,顶盖和壳体装有流体进出口接管。
通常在管外装置一系列垂直于管束的挡板。
同时管子和管板与外壳的连接都是刚性的,而管内管外是两种不同温度的流体。
因此,当管壁与壳壁温度相差较大时,由于两者的热膨胀不同,产生了很大的温差应力,以致管子扭弯或使管子从管板上松脱,甚至毁坏整个换热器。
为了克服温差应力必须有温度补偿装置,一般在管壁与壳壁温度相差50℃以上时,为安全起见,换热器应有温差补偿装置。
(2)浮头换热器:换热器的一块管板用法兰与外壳相连接,另一块管板不与外壳连接,以便管子受热或冷却时可以自由伸缩,但在这块管板上来连接有一个顶盖,称之为“浮头”,所以这种换热器叫做浮头式换热器。
这种型式的优点为:管束可以拉出,以便清洗;管束的膨胀不受壳体的约束,因而当两种换热介质的温差大时,不会因管束与壳体的热膨胀量的不同而产生温差应力。
其缺点为结构复杂,造价高。
(3)填料函式换热器:这类换热器管束一端可以自由膨胀,结构与比浮头式简单,造价也比浮头式低。
但壳程内介质有外漏的可能,壳程终不应处理易挥发、易爆、易燃和有毒的介质。
化工原理课程设计列管式换热器设计示例.

列管式换热器设计说明书设计者:班级:姓名:学号:日期:指导教师设计成绩日期目录一、方案简介 (3)二、方案设计 (4)1、确定设计方案 (4)2、确定物性数据 (4)3、计算总传热系数 (4)4、计算传热面积 (5)5、工艺结构尺寸 (5)6、换热器核算 (7)三、设计结果一览表 (10)四、对设计的评述 (11)五、附图(主体设备设计条件图)(详情参见图纸)·································六、参考文献 (12)七、主要符号说明 (12)附图··········································································一、方案简介本设计任务是利用冷流体(水)给硝基苯降温。
列管式换热器(设计举例)
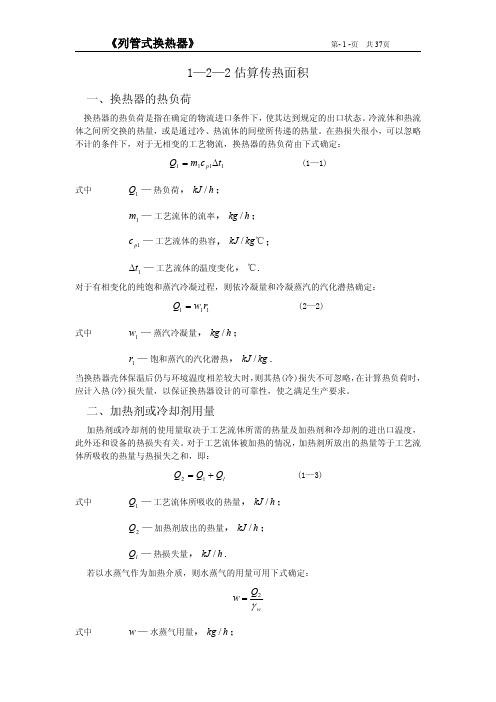
三、平均传热温差
平均传热温差是换热器的传热推动力。其值不但和流体的进出口温度有关,而且还与换 热器内两种流体的流型有关。对于列管式换热器,常见的流型有三种:并流,逆流,和折流
对于并流和逆流,平均传热温差均可用换热器两端流体温度的对数平均温差表示, 即:
《列管式换热器》
t m t1 t 2 t ln 1 t 2
R
热流体的温降 T1 T2 冷流体的温升 t 2 t1 t t 冷流体的温升 1 2 两流体最初温差 T1 T2
(1—13 a )
P
式中
(1—13 b )
T1、T2 — 热流体进、出口温度, ℃; t1、t 2 — 冷流体进、出口温度, ℃.
《列管式换热器》
第- 称为管心距。管心距的大小主要与传热管和管板的连接方式有 关,此外还要考虑到管板强度和清洗管外表面时所需的空间。 传热管和管板的连接方法有胀接和焊接两种,当采用胀接法时,采用过小的管心距,常 会造成管板变形,而采用焊接法时,管心距过小,也很难保证焊接质量,因此管心距应有一 定的数值范围。一般情况下,胀接时,取管心距 t 1.3~1.5d 0 ;焊接时,取 t 1.25d 0 ( d 0
共 37页
一般要求 t 的值不得低于 0.8,若低于此值,当换热器的操作条件略有变化时, t 的 变化较大,使得操作极不稳定。 t 小于 0.8 的原因在于多管程换热器内出现温度交差或温 度逼近。在这种情况下,应考虑采用多壳程结构的换热器或多台换热器串联来解决。所需的 壳程数或串联的换热器的台数可按下述方法确定: 首先,在坐标纸上作 Q ~ T 和 Q ~ t 线,由热衡算方程知,若两流体的热容量流率不变则
《列管式换热器》
第- 1 -页
列管式换热器设计
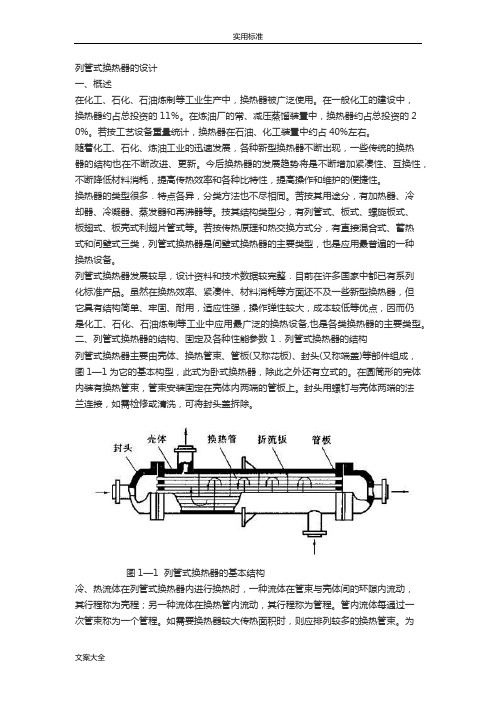
列管式换热器的设计一、概述在化工、石化、石油炼制等工业生产中,换热器被广泛使用。
在一般化工的建设中,换热器约占总投资的11%。
在炼油厂的常、减压蒸馏装置中,换热器约占总投资的2 0%。
若按工艺设备重量统计,换热器在石油、化工装置中约占40%左右。
随着化工、石化、炼油工业的迅速发展,各种新型换热器不断出现,一些传统的换热器的结构也在不断改进、更新。
今后换热器的发展趋势将是不断增加紧凑性、互换性,不断降低材料消耗,提高传热效率和各种比特性,提高操作和维护的便捷性。
换热器的类型很多.特点各异,分类方法也不尽相同。
苦按其用途分,有加热器、冷却器、冷凝器、蒸发器和再沸器等。
技其结构类型分,有列管式、板式、螺旋板式、板翅式、板壳式利翅片管式等。
若按传热原理和热交换方式分,有直接混合式、蓄热式和间壁式三类,列管式换热器是间壁式换热器的主要类型,也是应用最普遍的一种换热设备。
列管式换热器发展较早,设计资料和技术数据较完整.目前在许多国家中都已有系列化标准产品。
虽然在换热效率、紧凑件、材料消耗等方面还不及一些新型换热器,但它具有结构简单、牢固、耐用,适应性强,操作弹性较大,成本较低等优点,因而仍是化工、石化、石油炼制等工业中应用最广泛的换热设备,也是各类换热器的主要类型。
二、列管式换热器的结构、固定及各种性能参数 1.列管式换热器的结构列管式换热器主要由壳体、换热管束、管板(又称花板)、封头(又称端盖)等部件组成,图1—1为它的基本构型,此式为卧式换热器,除此之外还有立式的。
在圆筒形的完体内装有换热管束,管束安装固定在壳体内两端的管板上。
封头用螺钉与壳体两端的法兰连接,如需检修或清洗,可将封头盖拆除。
图1—1 列管式换热器的基本结构冷、热流体在列管式换热器内进行换热时,一种流体在管束与壳体间的环隙内流动,其行程称为壳程;另一种流体在换热管内流动,其行程称为管程。
管内流体每通过一次管束称为一个管程。
如需要换热器较大传热面积时,则应排列较多的换热管束。
列管式换热器设计举例

列管式换热器设计举例(一)一、设计任务书(一)已知条件 1. 气体工作压力: 管程:半水煤气 0.70MPa 壳程:变换气0.68MPa2. 壳、管壁温差 50℃,ta > ts 。
3. 由工艺计算求得换热面积为 130 2m 。
(二)设计任务1.列管热交换器结构及工艺尺寸;2.绘制列管热交换器结构图。
3.选用适合并满足换热任务的标准型换热器。
二、换热器设计计算1.确定管子数n选5.225⨯φ的无缝钢管,材质为20号钢,管长 3 m 因 n l d F 均π= 所以 6133022********=⨯⋅⨯⋅==L d A n 均π 根其中因安排拉杆需减少6 根,实际近数为607 根。
2.管子排列方式、管间距确定采用正三角形排列,由表 查得层数为 13 层,查表 ,取管间距 mm 32=α。
3.换热器壳体直径的确定壳体内径为: ()l b D i 21+-=α 式中 i D —— 换热器内径;mb —— 正三角形对角线上的管子数;查表 ,取27=b ; l —— 最外层管子的中心到壳壁边缘的距离;取02d l =。
因此 ()mm D i 932252212732=⨯⨯+-⨯=圆整后取壳体内径 mm D i 1000=4. 换热器壳体壁厚的计算 材料选用20R 钢,计算壁厚为 []PPD S ti-=φσ2式中 P —— 设计压力;取MPa P 01⋅=; mm D i 1000=850⋅=φ []MPa 101300=σ (设壳壁温度为300℃); 换热器壳体壁厚为: mm S 865018501012100001⋅=⋅-⋅⨯⨯⨯⋅=取mm C 212⋅=,由表 ,得mm C 801⋅=圆整后实取 mm S n 8=5.换热器封头选择上下封头均选用标准椭圆形封头,根据JB1154—73 标准,封头为81000⨯Dg ,曲面高度mm h 2501=,直边高度mm h 402=,如图7-48所示,材料选用20R 钢。
列管式换热器课程设计(含有CAD格式流程图和换热器图)

X X X X 大学《材料工程原理B》课程设计设计题目: 5.5×104t/y热水冷却换热器设计专业: -—----———-——---—————-—-—---—-班级:—--——-——-—-—-学号: —--——-----—姓名: -—--日期:——-—-—-———-——--指导教师: —---—-----设计成绩: 日期:换热器设计任务书1.设计方案简介2.工艺流程简介3.工艺计算和主体设备设计4.设计结果概要5.附图6.参考文献1。
设计方案简介1.1列管式换热器的类型根据列管式换热器的结构特点,主要分为以下四种。
以下根据本次的设计要求,介绍几种常见的列管式换热器。
(1)固定管板式换热器这类换热器如图1—1所示。
固定管板式换热器的两端和壳体连为一体,管子则固定于管板上,它的结余构简单;在相同的壳体直径内,排管最多,比较紧凑;由于这种结构式壳测清洗困难,所以壳程宜用于不易结垢和清洁的流体。
当管束和壳体之间的温差太大而产生不同的热膨胀时,用使用管子于管板的接口脱开,从而发生介质的泄漏。
(2)U型管换热器U型管换热器结构特点是只有一块管板,换热管为U型,管子的两端固定在同一块管板上,其管程至少为两程。
管束可以自由伸缩,当壳体与U型环热管由温差时,不会产生温差应力.U型管式换热器的优点是结构简单,只有一块管板,密封面少,运行可靠;管束可以抽出,管间清洗方便。
其缺点是管内清洗困难;哟由于管子需要一定的弯曲半径,故管板的利用率较低;管束最内程管间距大,壳程易短路;内程管子坏了不能更换,因而报废率较高。
此外,其造价比管定管板式高10%左右.(3)浮头式换热器浮头式换热器的结构如下图1-3所示。
其结构特点是两端管板之一不与外科固定连接,可在壳体内沿轴向自由伸缩,该端称为浮头。
浮头式换热器的优点是党环热管与壳体间有温差存在,壳体或环热管膨胀时,互不约束,不会产生温差应力;管束可以从壳体内抽搐,便与管内管间的清洗。
列管式换热器课程结构设计

列管式换热器课程结构设计一、化工原理课程设计任务书某生产过程中,需用循环冷却水将有机料液从102℃冷却至40℃。
已知有机料液的流量为(2.5-0.01×24)×104 =2.26×104 kg/h,循环冷却水入口温度为30℃,出口温度为40℃,并要求管程压降与壳程压降均不大于60kPa,试设计一台列管换热器,完成该生产任务。
已知:定性温度下流体物性数据有机化合液 986 0.54*10-3 4.19 0.662水 994 0.728*10-3 4.174 0.626注:若采用错流或折流流程,其平均传热温度差校正系数应大于0.8 。
二、确定设计方案1.选择换热器的类型两流体的温度变化情况:热流体进口温度102℃,出口温度40℃;冷流体进口温度30℃,出口温度40℃,该换热器用循环冷却水冷却,冬季操作时,其进口温度会降低,考虑到这一因素,估计该换热器的管壁温度和壳体温度之差较大,故而初步确定选用带有膨胀节的管板式换热器。
2.管程安排已知两流体允许压强降不大于60kPa;两流体分别为有机料液和冷却水。
与有机料液相比,水的对流传热系数一般较大。
由于循环冷却水较易结垢,若其流速太低,将会加快污垢增长速度,使换热器的热流量下降,考虑到散热降温方面的因素,应使循环冷却水走管程,而使有机料液走壳程。
三、确定物性数据定型温度:对于一般低粘度和水等粘度低流体,其定性温度可取流体进出口的平均值。
故壳程有机料液的定性温度为℃71240102=+=T 管程流体的定性温度为℃3524030=+=T 根据定性温度,分别查取壳程和管程流体的有关物性数据。
有机料液在71℃下的有关物性数据如下: 密度 31986kg/m =ρ 定压比热容 ℃)/(19.41⋅=kg kj C P 热导率 ℃)/(662.01⋅=m W λ 粘度 s Pa ⋅⨯=-311054.0μ 循环水在35℃下的物性数据:密度 32994kg/m =ρ 定压比热容 ℃)/(174.42⋅=kg kj C P 热导率 ℃)/(626.02⋅=m W λ 粘度 s Pa ⋅⨯=-3110728.0μ四、估算传热面积1.热流量W h kJ t c m Q p 6600001063.1/1087.5)40102(19.422600⨯=⨯=-⨯⨯=∆=2.平均传热温差暂按单壳程、多管程进行计算。
列管式换热器设计(1)

工艺设计书列管式换热器设计摘要:首先,根据设计任务书的要求,结合换热介质的物性标准确定传热器的类型。
其次,根据流体流动及传热等章节中关于流动阻力、传热面积的计算,初步确定达到设计要求所要的传热面积,确定传热器的大致尺寸,尔后经过压降校核、传热校核,确定传热器尺寸。
最后,通过化工机械设计确定换热器各附件的尺寸。
关键词:列管式换热器设计任务书装配图The Design of Tubular Heat Exchanger Summary: First of all, according to the design plan requirements, we can combined with heattransfer medium of heat transfer properties of the standard to determine the type of device. Second, according to theories of fluid flow and heat transfer calculations on the flow resistance, heat transfer area, we can initially set tomeet the heat transfer area of the design requirements, and to determine the approximate size ,and then to determine size after checking the pressure drop, heat transfer. Finally , according to theories of chemical mechanicaldesign ,we can determine the size of all attachments of heat exchangers. Keywords: tube heat exchanger design plan assembly drawing第一部分化工设备设计任务书一、设计名称:列管式换热器的设计二、设计任务及操作条件:1、设计任务:处理能力:W S t/a煤油;19.8×105设备形式:卧式列管式换热器。
管式换热器结构设计参考

防冲板的安装形式(图4-15)
五、接管
1.接管的一般要求: 1)接管不应凸出壳体内表面。 2)接管应尽量沿径向或轴向布置。 3)设计温度在3000C以上时,用整体法兰。 4)对利用接管仍不能放气和排液,应设置放 气口。 5)操作允许时,接管与外部管线的连接也可 采用焊接。 6)必要时可设置温度计接口、压力表及液面 计接口。
2.标准法兰的选用 标准法兰有: JB4701 甲型平焊法兰 JB4702 乙型平焊法兰 JB4703 长颈对焊法兰
法兰标准有:GB9112~9125。 新的(容器)提出压力容器应优先推荐采 HG20592~ 20614以及HG20615~ 20635 换热器的接管法兰一般应选用管法兰,至于选 用哪一种标准,根据布管要求来选定
二、垫片
设备垫片标准有: JB4704 非金属软垫片 JB4705 缠绕垫片 JB4706 金属包垫片 1.垫片结构 2.垫片尺寸 3.垫片的选择
三、膨胀节
膨胀节依靠易变形的挠性构件对管子与壳 体的热膨胀差进行补偿,以此来缓解或降低壳 体与管子因温差而引起的温差应力。 1.结构形式: (1)波形膨胀节(U型膨胀节) (2)平板膨胀节 (3) Ώ形膨胀节 (4)夹壳膨胀节
2.膨胀节设置必要性判断 通过计算由温差产生轴向力和压力产生轴 向力共同作用,得到: 换热管最大应力 壳体最大应力 及管子拉脱力 当或或时应设置膨胀节 。 3.强度计算 包括: (1)温差引起的轴向力计算 (2)补偿量的计算 (3)膨胀节疲劳寿命计算
四、支座
(一)立式支座
公称直径的立式换热器,至少采用两个支座。 公称直径的立式换热器,采用四个支座。 支座在换热器上的位置,根据工艺安装的要求 确定。 立式支座的尺寸和要求,按JB/T4725B型、BN型 悬挂式支座规定。
化工原理课程设计列管式换热器

可用旳场合:
1)管程走清洁流体;
2)管程压力尤其高;
3)管壳程金属温差很大,固定管板换热器连设置膨胀节都无法 满足要求旳场合.
2、流动空间旳选择
3、流速旳拟定
4、流动方式旳选择
除逆流和并流之外,在列管式换热器中冷、 热流体还能够作多种多管程多壳程旳复杂 流动。当流量一定时,管程或壳程越多, 表面传热系数越大,对传热过程越有利。 但是,采用多管程或多壳程必造成流体阻 力损失,即输送流体旳动力费用增长。所 以,在决定换热器旳程数时,需权衡传热 和流体输送两方面旳损失。
5、流体出口温度旳拟定
若换热器中冷、热流体旳温度都由工艺条件所要求,则不存在 拟定流体两端温度旳问题。若其中一流体仅已知进口温度,则 出口温度应由设计者来拟定。例如用冷水冷却一热流体,冷水 旳进口温度可根据本地旳气温条件作出估计,而其出口温度则 可根据经济核实来拟定:为了节省冷水量,可使出口温度提升 某些,但是传热面积就需要增长;为了减小传热面积,则需要 增长冷水量。两者是相互矛盾旳。一般来说,水源丰富旳地域 选用较小旳温差,缺水地域选用较大旳温差。但是,工业冷却 用水旳出口温度一般不宜高于45℃,因为工业用水中所含旳部 分盐类(如CaCO3、CaSO4、 MgCO3和MgSO4等)旳溶解度 随温度升高而减小,如出口温度过高,盐类析出,将形成传热 性能很差旳污垢,而使传热过程恶化。假如是用加热介质加热 冷流体,可按一样旳原则选择加热介质旳出口温度。
取管长应根据出厂旳钢管长度合理截用。 我国生产系列原则中管长有1.5m,2m, 3m,4.5m,6m和9m六种,其中以3m和 6m更为普遍。同步,管子旳长度又应与管 径相适应,一般管长与管径之比,即L/D约 为4~6
管式换热器结构设计参考

第二节 列管式换热器机械结构设计
一、传热管与管板的连接 二、管板与壳体及管箱的连接 三、管箱
一、传热管与管板的连接 造成连接处破坏的原因主要有: (1)高温下应力松弛而失效 (2)间隙腐蚀破坏 (3)疲劳破坏 (4)由于热补偿不好引起的破坏 管子与管板的连接形式:强度胀接、强度焊接 与胀焊接混合结构。 应满足以下两个条件: 连接处保证介质无泄漏的充分气密性; 承受介质压力的充分结合力。
(二)纵向隔板 在壳侧介质流量较小的情况 下,在壳程内安装一平行于传热
管的纵向隔板。如图4-2
防止短路的方式: 如图4-3所示: (a)为隔板直接与筒体内壁焊接,但必须 考虑到焊接的可能性; (b)纵向隔板插如导向槽中; (c)、(d)分别是单双向条形密封,防止间 隙短路,对于需要将管束经常抽出清洗者,采 用此结构。
1、分程隔板结构 分程隔板应采用与封头、管箱短节同等材 料、除密封面外,应满焊于管箱上。设计时要 求管箱隔板的密封面与管箱法兰密封面,管板 密封面与分程槽面必须处于同一几基面。结构 如图4-1。 2、分程隔板厚度及有关尺寸 当承受脉动流体或隔板压差很大时,隔板 的厚度应适当增厚,当厚度大于10mm的分程隔 板,在距端部15mm处开始削成楔形,使端部保 持10mm。
(二)弓形折流板排列方式确定(图4-8)
1.水平切口(图a、b,缺口上下布置) 2.垂直切口(图c,缺口左右布置) 3.倾斜切口(图4-5a,缺口倾斜布置) 4.双弓形缺口与双弓形板交替(图4-5b) (三)折流板与壳程间隙 折留板与壳程间隙依据制造安装调节, 在保证 顺利的装入前提下,越小越好,一 般浮头式和U型 管式换热器可允许比固管板 式大1mm,折流板外圆直径和下偏差见表4-2。
(2)管箱最小长度计算 管箱最小长度计算涉及几何尺寸见图。 A型管箱 见图4-35(a), 按流通面积计算
列管式换热器课程设计(含有CAD格式流程图和换热器图)

检查并调整图纸中的线条、颜色、字体等细节,确保图纸清晰易读, 符合规范要求。
关键节点参数设置与调整
设备参数设置
根据换热器、泵等设备的性能参 数,设置相应的CAD图纸中的属 性,如设备尺寸、处理能力、扬 程等。
管道参数调整
根据工艺流程需求和管道设计规 范,调整管道的直径、壁厚、材 质等参数,确保管道系统的安全 性和经济性。
阀门与控制点设置
在关键位置设置阀门以控制物料 流动,并根据控制需求设置相应 的控制点,如温度传感器、压力 传感器等。
流程图在课程设计中的作用
明确工艺流程
通过流程图可以清晰地展示物料在换热器中的流动过程, 帮助学生理解工艺流程和设备的相互关系。
指导设备布局与管道设计
流程图可以作为设备布局和管道设计的依据,有助于优化 设备布局和减少管道长度,提高系统的效率。
方式和换热器图纸中的局部结构。
建议措施
03
加强CAD制图技能的训练,提高图纸的准确性和规范
性。
经验教训分享与未来展望
经验教训
在课程设计过程中,应注重团队协作,合理分配任务,及时沟通交流,确保设计进度和 质量。
未来展望
随着CAD技术的不断发展,应积极探索新的设计理念和方法,提高课程设计的创新性 和实用性。同时,鼓励学生参与实际工程项目,将理论知识与实践相结合,提升综合素
流程图绘制步骤及规范
确定流程图的类型和范围
根据课程设计需求,明确要绘制的流程图类型(如工艺流程图、控制 流程图等)和所涵盖的范围。
绘制主要设备和管道
使用CAD软件中的绘图工具,按照比例和规范要求,绘制出换热器、 泵、阀门等主要设备以及连接它们的管道。
添加流向箭头和标注
化工原理设计主要部分列管式换热器的设计

列管式换热器的设计炼油某厂拟用原油在换热器中回收柴油的热量,已知原油流量为40000㎏/h,进口温度70℃,要求其出口温度不高于110℃,柴油流量为34000㎏/h,进口温度为175℃。
试选仪态适当型号的列管式换热器或设计一台列管式换热器,已知物性数据如下:1﹑确定设计方案1.1选择换热器的类型选择固定管板式换热器,固定管板式换热器的两端和壳体连为一体,管子则固定于管板上。
它的结构简单,在棚泵体直径内排管最多,比较紧凑。
由于这种结果使壳体内侧清洗困难,所以原油走管束,柴油走壳体。
由于管束和壳体之间温差太大而产生热膨胀时,会使班子和管板间接脱开,从而发生介质泄露,为此要在外壳上装一个膨胀节。
1.2流动空间的选择在管板式换热器计算中,首先要决定任何流体走管程何种流体走壳程,这需遵循一些一般原则:1 不清洁或易结垢的流体宜走管间,因为管程清洗较方便。
2 腐蚀性流体宜走管程,以免管子和壳体同时被腐蚀,且管子便于维修和更换。
3 压力高的流体宜走管程,以免壳体受压,以节省壳体金属消耗量。
4 被冷却的流体宜走壳程,便于散热,增强冷却效果。
5 饱和蒸汽走壳程,便于及时排除冷凝水,且蒸汽较清洁,一般不需清洗。
6 有毒流体走管程,以减少泄漏量7 黏度大的液体或流量小的流体宜走壳程,因为折流挡板的作用,流速与流向不断改变,在较低Re(Re>100)的情况下即可达到湍流,以提高传热效果。
8 若两流体温度差较大,对流体热系数较大的流体走壳程,因为壁温接近于α较大的流体温度,以减小管子和壳体的温差,减少热应力。
根据以上原则,这样原油走管程,柴油走壳程。
1.3流体流速的选择流体流速的选择涉及传热系数流体阻力及换热器的结构方面,增大流速,不仅对流体传热系数增大,也可以减少杂质沉淀;但流体阻力也相应增大,故应选择适宜的流速。
根据黏度的不同选择原油的流速u2=1.8m/s,柴油流速uo=1.5m/s.1.4管子的规格和排列方法a﹑选择Φ25×2.5mm标准规格管子。
列管式换热器设计示例

列管式换热器设计试自行设计一台固定管板式换热器以完成苯车间用冷水冷却变换气的任务。
已知操作条件下变换气方面的数据:(1)根据任务要求,确定设计方案①类型的选择。
根据设计要求,采用固定管板式换热器②流动路径的选择。
由于变换气被冷却且要求压力降不允许超过30kpa ,按变换气走管内考虑;而冷却水为处理过的软水,结垢不严重,安排走管间(即壳程)③冷却介质的选用及其物性。
按已知条件给出,冷却介质为处理过的软水,根据全年最高温度设定为冷却水进口温度t 1=30℃,冷却水出口温度t 2=38℃,因此平均温度下冷却水物性如下:密度ρ=994.3kg/m 3粘度μ2=0.743Χ10-3Pa.s 导热系数λ=62.5Χ10-2 W/(m.K) 比热容Cpc=4.174 kJ/(kg.K) ④流速的选择,变换气在管内的流速取U=0.65m/s (2)初算换热器的传热面积So①热负荷及冷却介质消耗量的计算标准状况下变换气的质量流量Ws 1=3000t/day=125000kg/h热负荷 Q=WhCph(T 1-T 2)=125000Χ1.81Χ(80.1-40)=9072625kJ/h=2520KW 冷却水的消耗量 Ws 2=)(12t t C Q pc -=)3038(1000174.410009072625-⨯⨯⨯=271.7t/h②计算平均温度差Δtm ,并确定管程数。
选取逆流流向,先按单壳程单管程考虑,计算出平均温度差Δtm ’: Δtm ’=1212t t INt t ∆∆∆-∆=)3040()381.80()3040()381.80(-----IN =22.33℃ 有关参数 R=1221t t T T --=3038401.80--=5.01 ,P=1112t T t t --=301.803038--=0.16根据R,P 值,查《化工原理》上册P232可读得,温度校正系数Φw=0.88>0.8,可见用单壳程合适,因此平均温度差Δtm=Δtm ’Χ0.88=19.65℃③按经验数值初选总传热系数Ko (估),选取Ko (估)=480W/(m 2.K)④初算出所需传热面积So ’:So ’=tm o K Q ∆=65.1948010002520⨯⨯=267.18 m2(3)主要工艺及结构基本参数的计算①换热管规格及材质的选定。
列管换热器设计实例
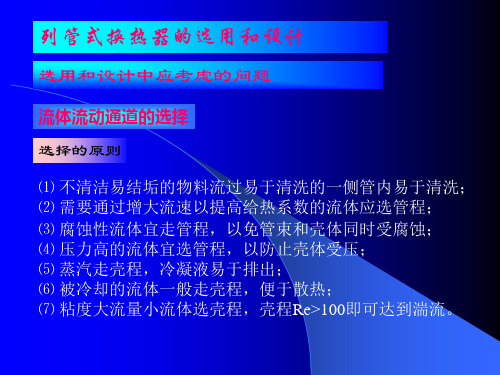
列管换热器的选用和设计的步骤
⑴ 确定流动路径,根据任务计算传热负荷,确定流体进、出的温度,选定 换热器形式,计算定性温度,查取物性,计算平均温差,根据温度校正系 数不小于0.8的原则,确定壳程数。
管子正方形排列,取F=0.3, Nc=1.1·n0.5=1.1×1920.5=15
p1'
0.3 0.8 15
20
795
0.567 2
2
9201
N/m2
l
6
N B h 1 0.3 1 19
p2
N
B
3.5
2h D
u0
2
2
19 (3.5
2 0.3 795 0.5672
)
0.6
2
6070
用热管制成的热管换热器对给热系数很小的气-气换热过程特别 有效,我们已经知道,当液体和气体换热时,常将管外表面翅 化以强化气体与管壁的传热,但对气-气传热的情况,管内的传 热强化则比较困难,热管是把管内的对流传热巧妙地转化为管 外表面的传热,从而可以采用加装翅片的方法进行强化。近年 来,利用热管换热器回收锅炉排出的烟气余热,以预热燃烧所 需要的空气,取得良好效果。
折流挡板
流体流经换热器的阻力 管程流体阻力 管程总阻力用下式计算
pi p1 p2 Ft Ns N p
⊿P1—流体流经直管的压力降,N/m2;
⊿p2—流体流经回弯管时的压力降,N/m2;
Ft—结垢修正系数,φ25×2.5mm,1.4,φ19×2mm,1.5 Ns—串联的壳程数; Np—管程数。
K Q 2778000 275 W/(m2·K)
- 1、下载文档前请自行甄别文档内容的完整性,平台不提供额外的编辑、内容补充、找答案等附加服务。
- 2、"仅部分预览"的文档,不可在线预览部分如存在完整性等问题,可反馈申请退款(可完整预览的文档不适用该条件!)。
- 3、如文档侵犯您的权益,请联系客服反馈,我们会尽快为您处理(人工客服工作时间:9:00-18:30)。
三、传热计算基本方程
5、传热膜系数的计算(续) 4)过渡流区域 当Re =2300~10000
'
1
6 105 Re 1.8
式中 α’——过渡流区域管程传热膜系数; α——由前面式求得
三、传热计算基本方程
5、传热膜系数的计算(续) (2)壳程传热膜系数 当换热器内无挡板时,壳程流体可按平行管束流动
du
0.8
c
1
3
w
0.14
式中
(μ/μw)0.14——考虑热流方向的校正项
液体被加热时, (μ/μw)0.14 =1.05;
液体被冷却时, (μ/μw)0.14 =0.95;
对于气体,不论是加热还是冷却, (μ/μw)0.14 =1
5、传热膜系数的计算(续)
定性温度:除μ w取壁温外,其余均取流体进出口 的算术平均温度。
2)湍流流动区域
对于低粘度流体(小于水的粘度的两倍),当Re>
10000,Pr= 0.7~120,d/L>60时
0.023
d
du
0.8
c
n
式中流体被加热时,n=0.4;流体被冷却时n=0.3。
二、操作条件的确定
1、换热器内流体通入空间的选择(续) (3)有腐蚀性的流体应走管程,这样,只有管子、管
板和管箱需要使用耐腐蚀的材料,而壳体及管外空间的 其他零件都可以使用比较便宜的材料。
(4)压力高的流体走管程,因为管子直径小,承受压 力的能力好,还避免了采用高压壳体和高压密封。
(5)有毒的流体走管程,减少泄漏的机会。 (6)饱和蒸汽一般走壳程,便于冷凝液的排出 (7)被冷却的流体走壳程,便于散热。
考虑,仍可用上述管程传热膜系数关联式进行计算, 需将式中管内径用壳程管子当量直径de代替即可
de D2 nd02 D nd0
三、传热计算基本方程
5、传热膜系数的计算(续)
(2)壳程传热膜系数(续)
当换热器内有挡板时,对于弓形挡板,当Re=3~
20000时
0.22 d0
d0u
选择时,除要考虑流体物性和操作条件外,还应考虑 换热器的类型。
三、传热计算基本方程
三、传热计算基本方程
2、总传热系数的计算 注意: 在通常的操作过程中,传热系数是个变量,由于
污垢热阻是变化的,因此设计中选择污垢热阻时,应 结合清洗周期来考虑。
若污垢热阻选得太小,清洗周期会很短,所需传热 面积会较小;
膜系数,W/(m2·K)
三、传热计算基本方程
2、总传热系数的计算(续)
Ri、R0——分别为管程和壳程的污垢热阻,K/W; A、A0、Am——分别为管程、壳程及管壳平均的传 热面积,m2; A——任一选定的作为计算K值的基准传热面积,m2; λm——管壁的导热系数,W/(m·K); b——管壁的厚度,m。
1
1
PR 1 m
P 1
R
三、传热计算基本方程
3、有效平均温差(续)
当R=1时 其中
t
2
y
1
y
ln ( 2
y) 2
2
2
y2
2
y P m mP P
反之,所需传热面积会较大,所以应该全面衡量, 作出选择。
三、传热计算基本方程
2、总传热系数的计算(续) 总传热系数的计算公式为
1 1 1 b Ri R0
KA iAi 0 A0 mAm Ai A0
式中 K——总传热系数,W/(m2·K); αi、 α0——分别为管程和壳程流体的传热
二、操作条件的确定
4、换热终温的确定(续) 如果超出上述数据,应通过技术经济比较来决定
换热终温。 (3)冷却水的出口温度不宜太高,否则会加快水垢
的生成。 对于经过良好净化的新鲜水,出口温度可达到
45℃或稍高一些; 对于净化较差的冷却水,出口温度建议不要超
过40℃。
三、传热计算基本方程
1、传热速率方程 在稳态下,当总传热系数随温度变化不大时 Q=KAΔtm
二、操作条件的确定
二、操作条件的确定
3、载热体的选择(续) 在选择时应考虑以下几个原则: (1)载热体能满足工艺上的要求达到的加热(冷却)温度 (2)载热体的温度易于调节; (3)载热体的饱和蒸汽压小,加热过程不会分解; (4)载热体的毒性小.对设备的腐蚀性小; (5)载热体不易爆炸; (6)载热体的价格低廉,来源充分。
T1、T2——热流体的进出口温度,K或℃; t1、t2——冷流体的进出口温度,K或℃; Cph、Cpc——热、冷流体的换热系数。
三、传热计算基本方程
2、热负荷(续) 有相变时
Q= W·r
式中 W——热或冷流体的流量,kg/s r——冷凝或蒸发潜热,J/kg
三、传热计算基本方程
3、有效平均温差
ห้องสมุดไป่ตู้
在无相变的纯粹逆流或并流换热器中,或一侧为恒温
二、操作条件的确定
3、载热体的选择(续) 工业上常用的载热体及其适用场合列于表3,供选用
时参考。
二、操作条件的确定
二、操作条件的确定
二、操作条件的确定
4、换热终温的确定 另外在决定换热终温时,一般不希望冷流体的出口
温度高于热流体的出口温度,否则会出现反传热现象, 当遇到达种情况时,可采用几个换热器串联的方法解 决。
三、传热计算基本方程
5、传热膜系数的计算(续)
当d/L<60时,必须考虑进口效应,可用下式进行
校正
am 1 d 0.7
a
L
三、传热计算基本方程
5、传热膜系数的计算(续)
3)高粘度液体
当Re>10000,Pr= 0.7~16700,d/L>60时
0.023
d
三、传热计算基本方程
3、有效平均温差(续) 各种流动情况x下的校正系数可根据R和P两个参数查图
得到,也可以用数学解析法计算得到
R T1T2 t2 t1
P t2 t1 T1 t1
三、传热计算基本方程
3、有效平均温差(续)
对应m壳程,2mn管程(m=l,2,3……)换热器的温差
三、传热计算基本方程
4、总传热系数 基本条件(设备型号、雷诺数、流体物性等)相同时,
总传热系数可直接采用经验数据,否则应用传热膜系数的 关联式,并选择合适的热阻值计算得到总传热系数。 (1)总传热系数的经验值
总传热系数的经验值见表4,有关手册中也列有其他 情况下的总传热系数经验值,可供设计时参考。
5、传热膜系数的计算(续) (1)管程传热膜系数 1)层流流动区域 当雷诺数Re<2300,普朗特数Pr=0.6—6700,
Re/Pr d/L>100时,传热膜系数α为
1
1
1
0.14
1.86
d
du
3
cu
3
d L
3
w
式中 Q——热负荷,W; K——总传热系数,W/(m2·K); A——与K对应的基准传热面积,m2 Δtm——有效平均温差,K.
三、传热计算基本方程
2、热负荷
无相变时
式中
Q= WhCph(T1 -T2)=WcCpc(t1- t2) Wh——热流体的流量,kg/s; Wc——冷流体的流量,kg/s;
校正系数为
当R≠1时
t
(
R R
2 1 1)
ln
(1 y) (1 y)R
(
2
)
1
R
R2 1
ln y
2 y
1
R
R2
1
其中
y
(
PR 1) P 1
1 m
二、操作条件的确定
1、换热器内流体通入空间的选择 在列管式换热器中,哪一种流体走管程,哪一种流体
走壳程,一般可从下列几方面考虑: (1)不洁净的或易结垢的流体走易于清洗的一侧;对
于固定管板式换热器一般走管程;U形管换热器,一般走 壳程。
(2)粘性大的或流量小的流体,宜走壳程,因流体在 有折流板的壳程流动时,一般在雷诺数(Re<l00)以下, 即可达到湍流,有利于提高传热系数。
三、传热计算基本方程
5、传热膜系数的计算 传热膜系数的关联式与传热过程是否存在相变、
换热器的结构及流动状态等因素有关; 关于传热膜系数的关联式很多,在选用时应注意
其适用的范围,对传热膜系数的关联式在此不作详细 的介绍,只列出常用的无相变的传热膜系数关联
其他形式的传热膜系数关联式可参考相关文献。
三、传热计算基本方程
第三章 列管换热器设计示例
一、设计计算基本步骤(续)
一、设计计算基本步骤(续)
(8)计算管子数和管长,对管子进行排列,确定壳体 直径
(9)根据管长与壳体直径的比值,确定管程数: (10)计算管程和壳程压力降,若压力降不符合要求, 调整流速,再确定管程数或折流板的间距,或选择另一 规格的换热器,重新计算压力降直至满足要求为止;
的其他流向的换热器中,其有效平均温差采用对数平均温
差
tm
t1 t 2 ln t1
t 2
三、传热计算基本方程