特种加工技术 (6)
6化学作用特种加工技术(删减版)

层叠叶片上的 孔加工
二、光化学腐蚀加工
光化学腐蚀加工简称光化学加工(Optical Chemical Machining 缩写OCM),是化学照相制版和光刻(化学 腐蚀)相结合的一种精密微细加工技术。
它与化学刻蚀(化学铣削)加工的主要区别在于: 它 不是靠人工刻形、划线,而是用感光照相来确定工件 表面要刻蚀的图形、线条。 (一)照相制版的原理和工艺 1、照相制版的原理
3)加工过程不产生应力、裂纹、毛刺等缺陷, Ra2.5~1.5
4)操作简单
化学铣削的缺点:
1)不适用于加工窄、深槽或型孔;
2)不能去除原零件的表面缺陷,划痕等
3)腐蚀液对设备、人有害,注意保护。
应用范围:1)大面积表面减薄加工,
2)在厚度小于1.5mm薄壁零件上加工孔
(二)化学铣削工艺过程
表面预处理: 去油污、氧化 膜;在相应腐 蚀液中预腐蚀; 喷砂处理,形 成一定的粗糙 度。 保护层:氯丁 橡胶、丁基橡 胶、丁苯橡胶。 0.2mm厚
1、光刻的原理、特点及应用范围 光刻,是利用光致抗蚀剂的光化学反应的特点,将掩 模板上的图形精确的复制在涂有光致抗蚀剂的衬底上, 再利用光致抗蚀剂的耐腐蚀特性,对衬底表面进行腐 蚀,获得所需的图形。精度可达:0.005mm。 使用于电路布线板、晶闸管元件等的制作。 2、光刻的工艺过程
1)原图和掩模板的制备,2)涂复光致抗蚀剂,3)曝 光,4)腐蚀,5)去胶。 应用:电路、多孔金属板、滤片、筛网、标牌、制版
照相制版将将图形摄影到底片上,经光化学反应,将图象复制 到涂有感光胶的铜板或锌板上,经坚膜固化处理,使感光胶具 有一定的抗蚀能力,经化学腐蚀,即可得到所需图形的金属板。
2、工艺过程
(1)原图和照相
特种加工技术

三、电火花加工的特点及应用 优 点
1.适于难切削材料的加工 1.适于难切削材料的加工 硬质合金、 硬质合金、淬火钢等 2.加工复杂形状或特殊零件 2.加工复杂形状或特殊零件 应用领域日益扩大
局限性
1.主要加工金属等导电材料 1.主要加工金属等导电材料 2.加工速度较慢 2.加工速度较慢 3.有电极损耗, 3.有电极损耗,影响加工精度
缺点: 缺点:
1) 加工精度(±0.03 mm)及稳定性不 ) 加工精度( ) 易提高 2) 小孔、窄缝及棱角清晰零件难加工 ) 小孔、 3) 电极设计制造较麻烦,需多次修整 ) 电极设计制造较麻烦, 4) 附属设备多,一次性投资大 ) 附属设备多, 5) 防腐蚀及电解泥渣、废液处理问题 ) 防腐蚀及电解泥渣、
• 电子束加工(简称EBM)和离子束加工 电子束加工(简称 ) 简称IBM)是近年来得到高速发展的 (简称 ) 新兴特种加工。 新兴特种加工。这两种加工主要用于精 细加工领域,尤其是微电子领域。 细加工领域,尤其是微电子领域。 1.电子束加工的原理 电子束加工的原理
6.电解倒棱去毛刺 6.电解倒棱去毛刺
机加工中去毛刺工作量 很大,电解去毛刺效率高, 很大,电解去毛刺效率高, 节省费用。 节省费用。 加工原理是尖角处电 加工原理是尖角处电 流密度最高。 流密度最高。 去毛刺时间与加工电 去毛刺时间与加工电 压、加工间隙及电解液参 数有关。 数有关。 智能控制的电化学齿轮修形工艺源于电解去毛刺和倒圆角 智能控制的电化学齿轮修形工艺源于电解去毛刺和倒圆角
三、激光加工的应用
1.激光打孔 1.激光打孔
金刚石拉丝模、宝石轴承、 金刚石拉丝模、宝石轴承、 化纤喷丝头、不锈钢板打孔。 化纤喷丝头、不锈钢板打孔。
2.激光切割 2.激光切割 3.激光焊接 3.激光焊接 4.激光表面处理 4.激光表面处理 5.激光快速成形 5.激光快速成形
特种加工技术第6章物料切蚀加工

(a) 锥 形
(b) 指 数 形
(c) 阶 梯 形
超声波加工规律
加工速度
加工精度
表面质量
加工精度:机床精度、夹具精度、磨料粒度、工具精度、工具磨损、工具 表面粗糙度一般为Ra0.1 -1 mm,
的横向振动、加工深度、工件材料性质等有关。一般孔的尺寸精度可达到 取决于每个磨粒每次撞击在工
±0.02-0.05 mm。
4)超声加工的生产率较低,加工面积不够大,工具损耗也大,这是超声波
加工的一大缺点。
超声波及其特性
超声加工原理与特点
超声波加工原理
超声波加工是利用超声振动的工具,在具有磨
当声波频率超出16000 Hz范围称为超声波。超声波可以在气体、液体和固 料的液体介质或磨料干粉中,产生冲击、抛磨
体介质中传递,由于超声波频率高、波长短、能量大,所以传播时反射、 等产生气蚀来去除材料,或是振动的能量转化
生波的反射和折射。
撞击作用,因此特别适合于硬脆材料的加工。
4)干涉和共振。在一定的条件下会产生干涉和共振现象。为了使弹性杆
处于最大振幅共振状态,应使弹性杆设计成半波长的整数倍,而固定弹性
杆的支撑点应该选在振动过程的波节处(没有振动的地方)。
超声波加工设备及其组成
超声波发生器
超声波振动系统
机床本体
工作液循环系统
超声波加工机床的本体一般很简单,包括支撑声学部件的机 架、工作台面以及使工具以一定压力作用在工件上的进给机 构等;图6-4是CSJ-2超声波加工机床。图中声学部件安装在一 根能上下移动的导轨上,导轨由上下二组滚动导轮定位,使 导轨能灵活精密地上下移动。工具的向下进给及对工件施加 压力靠声学部件的自重,为了能调节压力的大小,在机床后 部可以改变平衡重锤,也有采用弹簧或液压等其它方法改变 平衡砝码的重量。
特种加工技术---第六章:电子束和离子束加工

h
17
2 离子束加工在高真空环境下进行,所以污染少,特别适用于对易 氧化的金属、合金材料和高纯度半导体进行加工。
3 离子束加工是靠离子轰击材料表面的原子来实现的,是一种微观 作用,宏观压力很小,所以加工应力、热变形极小,加工质量高, 适合于加工各种材料和低刚度薄壁零件。
4 与电子束加工类似,离子束加工设备费用贵、成本高,应用范围 受到一定的限制。
h
4
三 电子束加工装置 一般说来,一套典型的电子束加工装置主要包括以下几个 主要组成部分
➢ 电子枪 ➢ 真空系统 ➢ 控制系统 ➢ 电源
h
5
1 电子枪 作用:发射电子束 组成:发射阴极,控制栅极、加速阳极
h
6
2 真空系统 真空系统的主要作用是保证电子束加工时维持1.33×10-21.33×10-4Pa的真空度,因为只有在真空中,电子才能高 速运动。此外,加工时产生的金属蒸汽会影响电子的发射 和运动,因此也需要不断地把加工中产生的金属蒸汽不断 抽走。
第六章 电子束和离子束加工
电子束加工-----Electron Beam Machining
离子束加工-----Ion Beam Machining
电子束加工主要用于打孔、焊接、切割、刻蚀、热处理和光刻 加工等方面。 离子束加工主要用于离子刻蚀、离子镀膜加工以及离子注入 加工等方面。
h
1
第一节 电子束加工
3 控制系统和电源
电子束加工设备控制系统主要包括:束流聚焦控制、束流位置 控制和束流强度控制。
束流的位置控制是为了改变电子束的方向,常用电磁偏转来控制
电子束焦点的位置。
电子束加工设备对电源电压的稳压性要求较高,因为电压波动
会影响电子束聚焦的稳定性。 h
§10-2 特种加工技术

加工时,工具以一定的静压力压在工件上, 加工区域送入磨粒悬浮液。超声波发生器产 生超声频电振荡,通过超声换能器将其转变 为超声频机械振动,借助于振幅扩大棒把振 动位移振动放大,驱动工具振动。材料的碎 除主要靠工具端部的振动直接锤击处在被加 工表面上的磨料,通过磨料的作用把加工区 域的材料粉碎成很细的微粒,从材料上碎除 下来。由于磨料悬浮液的循环流动,磨料不 断更新,并带走被粉碎下来的材料微粒,工 具逐渐伸入到材料中,工具形状便复现在工 件上,工具材料常用不淬火的45钢,磨料常 用碳化硼或碳化硅、氧化铝、金刚砂粉等。
(3)电化学加工 利用电能转化为化学能进行加工,如电解加 工、电镀、刷镀、镀膜和电铸加工等。 (4)激光加工 利用激光光能转化为热能进行加工。 (5)化学加工 利用化学能或光能转换为化学能进行加工, 如化学铣削和化学刻蚀(即光刻加工)等。 (6)复合加工 将机械加工和特种加工叠加在一起就形成复 合加工。如电解磨削、超声电解磨削等。
(2)超声波加工的特点和应用 超声波磨料流加工适宜加工各种硬脆材料,尤 其是电火花加工和电解加工无法加工的不导电 材料和半导体材料,如玻璃、陶瓷、半导体、 宝石、金刚石等。对于硬质的金属材料,如淬 硬钢、硬质合金等,虽可进行加工,但效率低。 近十几年来,超声波加工与传统的切削加工技 术相结合而形成的超声波振动切削技术得到迅 速的发展,并在生产实际中得以广泛的应用。 超声波车削、超声波磨削、超声波钻孔等在金 属材料,特别是难加工材料的加工中取得良好 的效果。加工精度、加工表面质量显著提高。
3)特种加工中,工具的硬度和强度可以低于工 件的硬度和强度,因为它主要不是靠机械力 来切削,同时工具的损耗很小,甚至无损耗, 如激光加工、电子束加工、离子束加工等。 适于加工脆性材料、高硬材料、精密微细零 件、薄壁零件、弹性零件等易变形零件。
第一节-特种加工技术

2.电火花加工的局限性:
(1)电火花加工生产效率低。 (2)被加工的工件只能是导体. (3)存在电极损耗,这就影响了成型精度。 (4)加工表面有变质层。 (5)加工过程必须在工作液中进行。电火花加工时 放电部位必须在工作液中,否则将引起异常放电。 (6)线切割加工有厚度极限。
60年代初,上海科学院电工研究所成功研制了我国第一台靠模仿形电 火花线切割 机床。随后又出现了具有我国特色的冷冲模工艺,即直接采用凸模打凹 模的方法,使凸凹模配合的均匀性得到了保证,大大简化了工艺过程。
60年代末,上海电表厂张维良工程师在阳极切割的基础上发明了我国 独有的高速走丝线切割机床。上海复旦大学研制出电火花线切割数控 系统。
电火花加工
一、加工原理
电火花加工是利用浸在工作液中的两极间脉冲放电时 产生的电蚀作用蚀除导电材料的特种加工方法,又称放电 加工或电蚀加工,英文简称EDM.
电火花加工的基本概念和特点
电火花加工的基本概念:
电火花加工又称放电加工(Electrical Discharge Machining 简称EMD)。它是在加工过程中,使工具和工件 之间不断产生脉冲性的火花放电,靠放电时产生的局部、瞬时 的高温将金属蚀除下来。这种利用火花放电产生的腐蚀现象 对金属材料进行加工的方法叫电火花加工。
国外电火花加工的发展
目前计算机技术广泛应用于工业领域,电火花加工实 现了数控化和无人化。美国、日本的一些电火花加工设 备生产公司依靠其精密机械制造的雄厚实力,通过两轴、 三轴和多轴数控系统、自动工具交换系统及采用多方向 伺服的平动、摇动方案,解决了电火花加工技术中一系列 实质性的问题。随着具有高精度、高刚度、高自动化、 高加工表面粗糙度的机床不断出现,使加工的功能及范围 不断扩大。如今,在国际上,电火花加工可以加工大至数十 吨重的模具和零件,小至只有几微米的微孔。
特种加工技术
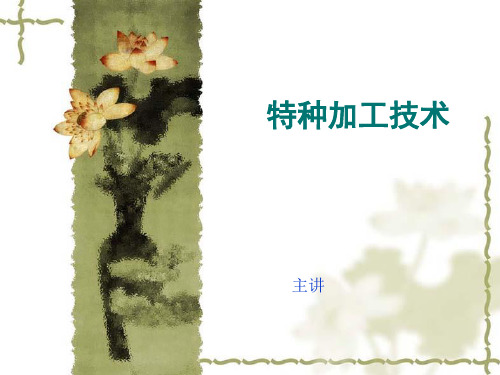
细微孔:直径小于0.2mm的孔。 国外目前可加工出深径比为5,直径为 0.015mm的细微孔。在我国一般可加工出深径 比为10,直径为0.05mm的细微孔。 但加工细微孔的效率较低,因为工具电极制 造困难,排屑也困难,单个脉冲的放电能量 须有特殊的脉冲电源控制,对伺服进给系统 要求更严。
电火花放电过程中如此 高的温度钼丝为何没有 熔断 ?
?
?
?
二、线切割加工的应用
(1)适用于各种形状的冲模。 (2)可以加工微细异形孔、窄缝和复杂形状的工件。 (3)加工样板和成型刀具。 (4)加工粉末冶金模、镶拼型腔模、拉丝模、波纹板 成型模。 (5)加工硬质材料、切割薄片,切割贵重金属材料。 (6)加工凸轮、特殊的齿轮。 (7)适用于小批量、多品种零件的加工。
工具电极材料
铜:制成各种精密复杂电极,可用于中小型腔加工 钨、钼:熔点和沸点较高、损耗少,但其机械加工 性能不好,价格较贵,一般仅用于线切割。 石墨:用于型腔加工 铜碳、铜钨和银钨合金等合金材料:导热性好,熔 点高,电极损耗少,价格较贵、制造成型困难,通 常只用于精密电火花加工。
2.影响加工精度的主要因仿形控制、光电跟踪控制、数字程序控制 以及微机控制等,前两种方法现已很少采用。 3)按脉冲电源形式分 有RC电源、晶体管电源、分组脉冲电源以及 自 适应控制电源等,RC电源现已基本不用。 4)按加工特点分 有大、中、小型,以及普通直壁切割型与锥度切割 型等。
数控线切割技术的发展趋势
(1)放电间隙的大小和一致性 (2)工具电极的损耗及“二次放电”
二次放电是指已加工表面上由于电蚀产物等 的介入而再次进行的非正常放电。 二次放电主要是在加工深度方向的侧面产生 斜度和使加工棱角边变钝。
特种加工技术
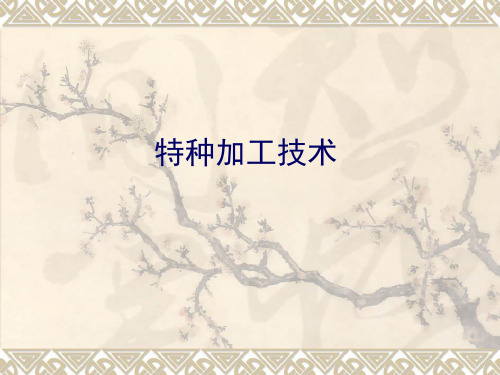
概述
特种加工:
研究的是将电、热、光、声、化 学等能量或其组合施加到被加工的部 位来去除材料的加工方法。
特种加工的特点
1、不是主要依靠机械能 2、加工过程中工具和工件之间不存在显著的机械切削力 3、工具硬度可以低于被加工材料的硬度
特种加工的分类
1、电火花加工 2、电化学加工 3、高能束加工
电火花加工原理
工件与工具电极分别连接到脉冲 电源的两个不同极性的电极上。当两 电极间加上脉冲电压后,当工件和电 极间保持适当的间隙,就会把工件与 工具电极之间的工作液介质击穿,形 成放电通道。放电通道中产生瞬时高 温,使工件表面材料熔化甚至气化, 同时也使工作液介质气化,在放电间 隙处迅速热膨胀并产生爆炸,工件表 面一小部分材料被蚀除抛,形成微小 的电蚀坑。脉冲放电结束后,经过一 段时间间隔,使工作液恢复绝缘。脉 冲电压反复作用在工件和工具电极上, 上述过程不断重复进行,工件材料就 逐渐被蚀除掉。伺服系统不断地调整 工具电极与工件的相对位置,自动进 给,保证脉冲放电正常进行。
高生产率和低电极损耗加工时,常采用负极性长脉宽加工。
电极材料的选用
电火花加工中如何选用电极材料: 主要考虑放电加工特性、价格、电极的切削加工性能。 目前主要采用的是紫铜和石墨
建立坐标系
G80 移动轴直到触感点 G82回到当前位置与零点的一半处 G92制定坐标原点 M05忽略接触感知 G80 X-; G92 G54 X0;/一般机床将G54工
找工件上的某一固定点
该操作的具体过程是: ①电极(设电极半径为R)碰AB边,直到接触感知
后停止时,将AB边坐 标清零; ②将电极移到BC边,碰BC 边,直到接触感知后停止时, 将BC边坐标清零; ③将电极移到坐标(100+R,80+R)即找到 O点的位置。
特种加工技术
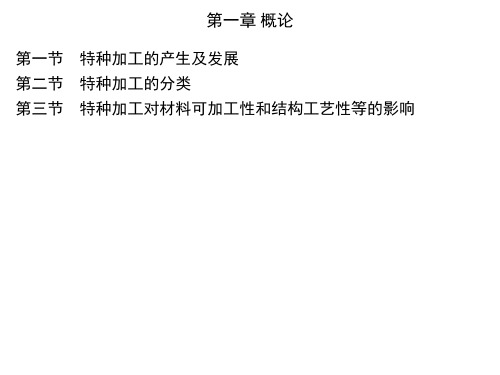
图2-4 极间放电电压 和电流波形
a) 电压波形 b) 电流波形
图2-5 放电间隙状况示意图 1—正极 2—从正极上熔化并抛出金属的区域 3—放电通道 4—气泡 5—在负极上熔
化并抛出金属的区域 6—负极 7—翻边凸起 8—在工作液中凝固的微粒 9—工作液 10—放电形成的凹坑
用途
备注
1.型腔加工: 约占电火花机
加工各类型腔模 床总数的30%,
及各种复杂的型 典型机床有D712
腔零件
5、D7140等电火
2.穿孔加工: 花穿孔成形机床
加工各种冲模、
挤压模、粉末冶
金模、各种异形
孔及微孔等
类别 Ⅱ
表2-1 电火花加工工艺方法分类
工艺方法
电火花线切割 加工
特点
1.工具电极 为顺电极丝轴线 方向移动着的线 状电极
可达到表 面粗 糙度/μm 平均/最高
主要适用 范围
超声加工
任何脆 0.1/10
1/50
性材料
0.03/0.0 05
0.63/0.1 6
加工、 切割脆硬 材料。如 玻璃、石 英、宝石、 金刚石、 半导体单 晶锗、硅 等。可加 工型孔、 型腔、小 孔、深孔 以及切割 等
表1-2 几种常用特种加工方法的综合比较
图2-3 电火花加工表面局部放大图
二、电火花加工的特点及其应用
1.主要优点 2.电火花加工的局限性
1.主要优点
(1) 适合于任何难切削导电材料的加工 由于加工中材料的去除是靠放电时的 电热作用实现的,材料的可加工性主要取决于材料的导电性及其热学特性, 如熔点、沸点、比热容、热导率、电阻率等,而几乎与其力学性能(硬度、强 度等)无关。 (2) 可以加工特殊及复杂形状的表面和零件 由于加工中工具电极和工件不直 接接触,没有机械加工宏观的切削力,因此适宜加工低刚度工件及作微细加 工。
特种加工技术

定义与概念
特种加工亦称“非传统加工”或“现代加工方法”,泛指用电 能、热能、光能、电化学能、化学能、声能及特殊机械能等能 量达到去除或增加材料的加工方法,从而实现材料被去除、变 形 、改变性能或被镀覆等。
特种加工技术是直接利用电能、热能、声能、光能、电化学能、 化学能及特殊机械能等多种能量或其复合能量以实现材料切除 的加工方法。其研究范围是电加工、高能束流(激光束、电子束、 离子束、高压水束)加工、超声波加工及多能源复合加工。
离子束加工技术
它是一种微细加工技术,成为航空电子设备和精密机载设备的 关键制造技术之一。它是应用离子蚀刻技术、离子溅射技术、 离子镀膜技术和离子注入技术完成精密零件的精密成形加工和 特殊表面层的制备。 离子束加工技术在航空电子设备和高精密机载设备的微细加工 和超精密加工中具有至关重要的作用,工业发达国家的航空工 业界高度重视此项技术的发展与应用。离子束加工技术主要发 展方向是实现计算机数控自动化、超精密化、经济与高效化。
特种技术的特点
加工范围不受材料物理 、机械性能的限制,能加工任何硬的、 软的、脆的、耐热或高熔点金属以及非金属材料。 易于加工复杂型面、微细表面以及柔性零件。 易获得 良好的表面质量,热应力、残余应力、冷作硬化、热影 响区等均比较小。 各域
特种加工技术在国际上被称为21世纪的技术 难加工材料,如钛合金、耐热不锈钢、高强钢、复合材料、工 程陶瓷、金刚石、红宝石、硬化玻璃等高硬度、高韧性、高强 度、高熔点材料。 难加工零件,如复杂零件三维型腔、型孔、群孔和窄缝等的加 工。 低刚度零件,如薄壁零件、弹性元件等零件的加工。 以高能量密度束流实现焊接、切割、制孔、喷涂、表面改性、 刻蚀和精细加工。
电加工技术
目前电解加工机床最大容量已达到5万安培,并已实现CNC控制 和多参数自适应控制。电火花加工气膜孔采用多通道、纳秒级 超高频脉冲电源和多电极同时加工的专用设备,加工效率2~3 秒/孔,表面粗糙度Ra0.4μm,通用高档电火花成型及线切割已 能提供微米级加工精度,可加工3μm的微细轴和5μm的孔。精 密脉冲电解技术已达10μm左右。电解与电火花复合加工,电 解磨削、电火花磨削已用于生产。
特种加工技术

特种加工技术特种加工亦称“非传统加工”或“现代加工方法”,泛指用电能、热能、光能、电化学能、化学能、声能及特殊机械能等能量达到去除或增加材料的加工方法,从而实现材料被去除、变形、改变性能或被镀覆等。
中文名特种加工外文名Special Machining 普及时间二十世纪四十年代目录一概述二发展三特点四运用领域五独到之处六加工工艺七加工技术1、电火花2、激光3、电子束4、离子束5、电加工6、超声波7、数控八发展方向一、概述:特种加工是指那些不属于传统加工工艺范畴的加工方法,它不同于使用刀具特种加工:特种加工、磨具等直接利用机械能切除多余材料的传统加工方法。
特种加工是近几十年发展起来的新工艺,是对传统加工工艺方法的重要补充与发展,目前仍在继续研究开发和改进。
直接利用电能、热能、声能、光能、化学能和电化学能,有时也结合机械能对工件进行的加工。
特种加工中以采用电能为主的电火花加工和电解加工应用较广,泛称电加工。
20世纪40年代发明的电火花加工开创了用软工具、不靠机械力来加工硬工件的方法。
50年代以后先后出现电子束加工、等离子弧加工和激光加工。
这些加工方法不用成型的工具,而是利用密度很高的能量束流进行加工。
对于高硬度材料和复杂形状、精密微细的特殊零件,特种加工有很大的适用性和发展潜力,在模具、量具、刀具、仪器仪表、飞机、航天器和微电子元器件等制造中得到越来越广泛的应用。
特种加工的发展方向主要是:提高加工精度和表面质量,提高生产率和自动化程度,发展几种方法联合使用的复合加工,发展纳米级的超精密加工等。
二、发展:特种加工是20世纪40年代发展起来的,由于材料科学、高新技术的发展和激烈的市场竞争、发展尖端国防及科学研究的急需,不仅新产品更新换代日益加快,而且产品要求具有很高的强度重量比和性能价格比,并正朝着高速度、高精度、高可靠性、耐腐蚀、高温高压、大功率、尺寸大小两极分化的方向发展。
为此,各种新材料、新结构、形状复杂的精密机械零件大量涌现,对机械制造业提出了一系列迫切需要解决的新问题。
特种加工技术
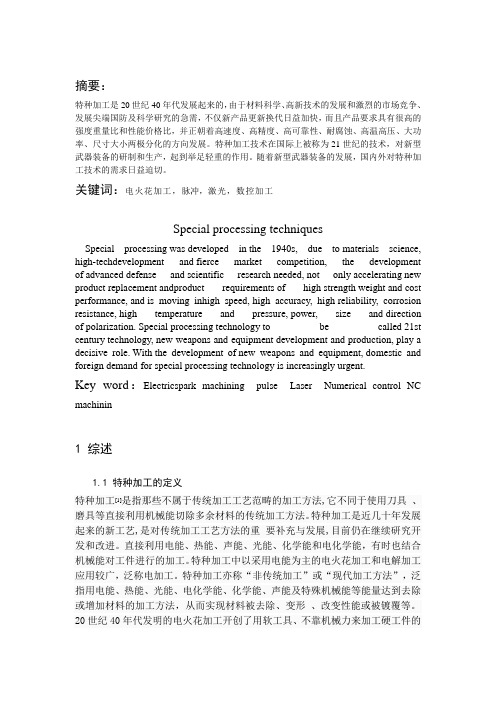
摘要:特种加工是20世纪40年代发展起来的,由于材料科学、高新技术的发展和激烈的市场竞争、发展尖端国防及科学研究的急需,不仅新产品更新换代日益加快,而且产品要求具有很高的强度重量比和性能价格比,并正朝着高速度、高精度、高可靠性、耐腐蚀、高温高压、大功率、尺寸大小两极分化的方向发展。
特种加工技术在国际上被称为21世纪的技术,对新型武器装备的研制和生产,起到举足轻重的作用。
随着新型武器装备的发展,国内外对特种加工技术的需求日益迫切。
关键词:电火花加工,脉冲,激光,数控加工Special processing techniquesSpecial processing was developed in the 1940s, due to materials science, high-techdevelopment and fierce market competition, the development of advanced defense and scientific research needed, not only accelerating new product replacement andproduct requirements of high strength weight and cost performance, and is moving inhigh speed, high accuracy, high reliability, corrosion resistance, high temperature and pressure, power, size and direction of polarization. Special processing technology to be called 21st century technology, new weapons and equipment development and production, play a decisive role. With the development of new weapons and equipment, domestic and foreign demand for special processing technology is increasingly urgent.Key word:Electricspark machining pulse Laser Numerical control NC machinin1 综述1.1 特种加工的定义特种加工[1]是指那些不属于传统加工工艺范畴的加工方法,它不同于使用刀具、磨具等直接利用机械能切除多余材料的传统加工方法。
特种加工技术
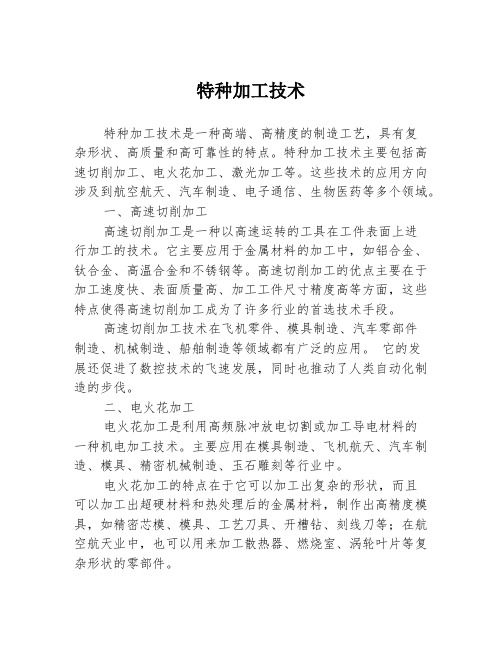
特种加工技术特种加工技术是一种高端、高精度的制造工艺,具有复杂形状、高质量和高可靠性的特点。
特种加工技术主要包括高速切削加工、电火花加工、激光加工等。
这些技术的应用方向涉及到航空航天、汽车制造、电子通信、生物医药等多个领域。
一、高速切削加工高速切削加工是一种以高速运转的工具在工件表面上进行加工的技术。
它主要应用于金属材料的加工中,如铝合金、钛合金、高温合金和不锈钢等。
高速切削加工的优点主要在于加工速度快、表面质量高、加工工件尺寸精度高等方面,这些特点使得高速切削加工成为了许多行业的首选技术手段。
高速切削加工技术在飞机零件、模具制造、汽车零部件制造、机械制造、船舶制造等领域都有广泛的应用。
它的发展还促进了数控技术的飞速发展,同时也推动了人类自动化制造的步伐。
二、电火花加工电火花加工是利用高频脉冲放电切割或加工导电材料的一种机电加工技术。
主要应用在模具制造、飞机航天、汽车制造、模具、精密机械制造、玉石雕刻等行业中。
电火花加工的特点在于它可以加工出复杂的形状,而且可以加工出超硬材料和热处理后的金属材料,制作出高精度模具,如精密芯模、模具、工艺刀具、开槽钻、刻线刀等;在航空航天业中,也可以用来加工散热器、燃烧室、涡轮叶片等复杂形状的零部件。
三、激光加工激光加工是利用激光束在工件表面切割、焊接、雕刻、打孔等加工过程中,具有非接触加工、非热接触、精度高、效率高、易自动化控制等优点。
激光加工的应用领域也非常广泛,如电子电器制造、机械制造、汽车制造、航空航天、医疗器械等。
激光加工可以对材料进行各种加工作业,从而满足生产的不同需求。
例如,激光切割技术可用于生产压缩机、汽车零件和航空零件。
激光焊接技术可用于电子零件、汽车制动系统和飞机的燃油泵等。
激光打孔技术可用于贵重石材、塑料制品和编织物等材料的加工中。
此外,激光打印技术也是目前3D打印技术中的一种先进的加工手段。
总之,特种加工技术的应用已经深入到我们生活的方方面面中,并且将持续发展,并为我们带来更多的便利和舒适。
特种加工技术

特种加工技术的发展及其应用特种加工是指那些不属于传统加工工艺范畴的加工方法,它不同于使用刀具、磨具等直接利用机械能切除多余材料的传统加工方法。
特种加工是近几十年发展起来的新工艺,是对传统加工工艺方法的重要补充与发展,目前仍在继续研究开发和改进。
直接利用电能、热能、声能、光能、化学能和电化学能,有时也结合机械能对工件进行的加工。
特种加工中以采用电能为主的电火花加工和电解加工应用较广,泛称电加工。
特种加工亦称“非传统加工”或“现代加工方法”,泛指用电能、热能、光能、电化学能、化学能、声能及特殊机械能等能量达到去除或增加材料的加工方法,从而实现材料被去除、变形、改变性能或被镀覆等。
20世纪40年代发明的电火花加工开创了用软工具、不靠机械力来加工硬工件的方法。
50年代以后先后出现电子束加工、等离子弧加工和激光加工。
这些加工方法不用成型的工具,而是利用密度很高的能量束流进行加工。
对于高硬度材料和复杂形状、精密微细的特殊零件,特种加工有很大的适用性和发展潜力,在模具、量具、刀具、仪器仪表、飞机、航天器和微电子元器件等制造中得到越来越广泛的应用。
特种加工技术的特点加工范围上不受材料强度、硬度等限制。
特种加工技术主要不依靠机械力和机械能去除材料,而是主要用其他能量(如电、化学、光、声、热等)去除金属和非金属材料,完成工件的加工。
故可以加工各种超强硬材料、高脆性及热敏材料以及特殊的金属和非金属材料。
以柔克刚。
特种加工不一定需要工具,有的虽使用工具,但与工件并不接触,加工过程中工具和工件间不存在明显的强大机械切削力,所以加工时不受工件的强度和硬度的制约,在加工超硬脆材料和精密微细零件、薄壁元件、弹性元件时,工具硬度可以低于被加工材料的硬度。
加工方法日新月异,向精密加工方向发展。
当前已出现了精密特种加工,许多特种加工方法同时又是精密加工方法、微细加工方法,如电子束加工、离子束加工、激光束加工等就是精密特种加工;精密电火花加工的加工精密度可达微米级0.51μm,表面粗糙度可达镜面 Ra0.02μm。
《特种加工技术》 习题答案

《特种加工技术》2017版习题参考答案【说明】:每章的第一大题是简答题,其答案基本在书中有描述,此处不再给出;部分章节的拓展题主要目的是启迪、开拓思路或展开应用,故没有统一或固定的答案。
第1章电火花成形加工(EDM SINKING)二、选择题1.电火花深小孔加工应当选择以下 C 作为工作液;A.自来水;B.煤油;C.去离子水(工业纯水) ;D.乳化液2.电火花共轭回转加工的最早发明人是:AA.中国人;B.美国人C.俄国人D.德国人3. 欲将小型交叉孔口毛刺去除彻底干净,最好采用D加工方法来完成。
A.锉刀;B.砂带磨削C.砂轮磨削D.电火花工艺4.欲保证最高的加工精度,电火花加工中工作液供给方式最好采用C。
A.静态淹没工件;B.侧面冲液C.工具电极内部抽吸D.工具电极内部射出5.对于象筛网零件有成千上万个小孔需要加工,为保证生产率,电火花加工宜采用以下D工具电极.A.单个实心电极逐个加工;B.单个空心电极逐个加工C. 实心群电极D.空心管群电极三、判断题1.电火花加工中的吸附效应都发生在正极上。
(F )2.电火花成型加工时,电极在长度方向上损耗后无法得到补偿,需要更换电极。
(T )3.电火花成型加工中的自动进给调节系统应保证工具电极的进给速度等于工件的蚀除速度;(T)4.电火花成型加工和穿孔加工相比,前者要求电规准的调节范围相对较小。
(F )5.电火花成型加工电极损耗较难进行补偿。
(T )6.在型号为DK7740的数控电火花线切割机床中,D表示电加工机床。
(T)7.弛张式脉冲电源电能利用率相当高,所以在电火花加工中应用较多。
(F)8.电火花成型加工属于盲孔加工,工作液循环困难,电蚀产物排除条件差。
(T)9.电火花加工的粗规准一般选取的是窄脉冲、高峰值电流。
(F)10.电火花加工的粗规准一般选取的是宽脉冲、高峰值电流。
(T)11.电火花加工的效率较低。
(T)12.煤油作为电火花液,冷却效果最好(F)13.紫铜又叫纯铜;(T)14.电火花机床没有主运动,只有进给运动。
- 1、下载文档前请自行甄别文档内容的完整性,平台不提供额外的编辑、内容补充、找答案等附加服务。
- 2、"仅部分预览"的文档,不可在线预览部分如存在完整性等问题,可反馈申请退款(可完整预览的文档不适用该条件!)。
- 3、如文档侵犯您的权益,请联系客服反馈,我们会尽快为您处理(人工客服工作时间:9:00-18:30)。
图7.1快速成形技术的原理图
图7-2 快速成形的基本过程
快速成形技术的不同称谓:
自由成形制造FFF(free form fabrication) 实体自由成形制造SFF(solid freeform fabrication) 分层制造LM(layered manufacturing)、 添加制造AM(additive manufacturing)或 材料增长制造MIM (material increase manufacturing) 直接CAD制造DCM(direct CAD manufacturing ) 即时制造IM(instant manufacturing)等等。
图7-7 叠层实体制造的系统原理图
LOM的成形工艺基于激光切割薄片材料、 由黏结剂黏结各层成形,其具体过程如 图7-8所示。
图7-8 LOM制造工艺过程
从叠层实体制造的工艺过程可以看出其具 有的特点: ① 用CO2激光进行切割; ② 零件交截面轮廓外的材料用打网格的办
法使之小的方块条,便于去除; ③ 采用成卷的带料供材; ④ 行程开关控制加工平面; ⑤ 热压辊对最上面的新层加热加压; ⑥ 先进行热压、黏结,再切割截面轮廓,
1. 成形精度高 2. 成形速度较快 3. 扫描质量好 4. 成形件表面质量好 5. 成形过程中需要添加支撑 6. 成形成本高
【应用实例7-1】 摩托罗拉公司手机手板制作
国外大公司已经广泛采用光固化快速成
形的方法加快产品的开发进程,下图为摩 托罗拉公司使用SLA成形工艺进行的手板 样件验证工作,大大缩短了开发周期。
【应用实例7-2】 冰箱内饰件快速制模
SLS技术
硅胶模具
硅橡胶翻制
塑料件
浇注树脂
图7-6 加工流程及加工零件
7.1.2.3叠层实体制造的工艺过程及技术性能
叠层实体制造LOM(laminated object manufacturing)工艺是快速原型技术中具 有代表性的技术之一,在我国也称为分 层实体制造SSM(slicing solid manufacturing)。其系统原理如图7-7所示:
7.1.2.2激光选区烧结快速成形工艺
一.激光选区烧结基本原理 激光选区烧结SLS(selected laser
sintering)工艺,又称选择性激光烧结, 它是采用红外激光作为热源来烧结粉末 材料,并以逐层堆积方式成形三维零件 的一种快速成形技术。图7-5即为SLS的工 艺原2.根据工艺要求,按照一定的规律将该模型离散为
一系列有序的单元,通常在Z向将其按一定厚度进 行离散(分层、切片),把原CAD三维模型变成一系 列的层片的有序叠加;
• 3.根据每个层片的轮廓信息,输入加工参数,自动 生成数控代码;
• 4.由成形机完成一系列层片制造并实时自动将它们 联接起来,得到一个三维物理实体。
以防止定位不准和错层问题。
7.1.2.4熔融挤出快速成形技术
熔融挤出快速成形工艺MEM(melted extrusion modeling),又称熔融沉积成形工 艺FDM(fused depositon modeling technology),是一种利用喷头熔融、挤出 丝状成形材料,并在控制系统的控制下, 按一定扫描路径逐层堆积成形的一种快速 成形工艺。其工艺原理图如图7-9所示。
第七章 特种加工新技术
• 7.1 特种加工与快速成形技术 • 7.2 微细加工技术 • 7.3 微机电系统应用
如何加工如下图所示套接在一起的连环?
7.1 特种加工与快速成形技术
• 7.1.1 快速成形技术的概念 • 7.1.2 快速成形工艺 • 7.1.3 激光快速制造技术
7.1.1 快速成形技术的概念
【应用点评7-1】快速成形技术的发展
快速成形技术是当今世界上发展最快的材 料成型技术,经过多年的发展,目前已形成了 多种先进的工艺技术,各种方法均具有自身的 特点和适用范围。 比较成熟的工艺有:光固化快速成形(SL)
激光选区烧结(SLS) 三维打印快速成形工艺(3DP) 熔融挤出快速成形工艺(FDM)
成形等,是一种采用激光束逐点扫描液态 光敏树脂使之固化的RP成形工艺。其工 艺的基本原理如图7-3所示。
图7-3 光固化成形的基本原理
二.光固化快速成形工艺的特点 光固化快速成形工艺作为快速成形技
术的一种,所依据的仍然是离散-堆积成 形原理。但是,由于层片成形机理的特点, 导致光固化快速成形工艺具有如下特点:
(1)铺粉
(2)激光烧结
成形后的零件 (3)活塞下降
(a)SLS成形的工作原理
图7-5 SLS工艺原理示意图
二.SLS工艺特点 与其他RP工艺相比,SLS工艺具有如下特 点:
1. 可以成形几乎任意几何形状结构的零件 2. SLS工艺无需支撑 3. SLS工艺可使用的成形材料范围广 4. 可快速获得金属零件 5. 未烧结的粉末可重复使用,材料浪费极小 6. 应用面广
快速模具制造(RMM—rapid mold manufacturing )
快速生物模具制造(RBM— rapid bio-model manufacturing )
快速支架制造(RSM—rapid scaffold manufacturing )
其基本过程是: • 1.完成被加工件的计算机三维模型(数字模型、
快速成形即快速制造,是指由CAD模型直接驱动 的快速制造任意复杂形状三维实体的技术总称。
快速成形(RM---rapid manufacturing) 即快速成形或快速 成形制造
快速原形制造( RPM—rapid prototyping manufacturing)
快速工具制造(RTM—rapid tooling manufacturing )
叠层实体制造(LOM)等。
7.1.2 快速成形工艺
1. 光固化快速成形工艺的定义 2. 激光选区烧结快速成形工艺 3. 叠层实体制造的工艺过程及技术性能 4. 熔融挤出快速成形技术 5. 三维打印快速成形工艺 6. 其他快速成形工艺简介
7.1.2.1光固化快速成形工艺的定义
一.光固化快速成形工艺 光固化快速成形,又称立体光刻、光