中华人民共和国机械工业部部标准
[机械制造]QCT563-1999转向盘试验国家标准
![[机械制造]QCT563-1999转向盘试验国家标准](https://img.taocdn.com/s3/m/c1e4016b03768e9951e79b89680203d8cf2f6a50.png)
中华人民共和国机械工业部部标准QC/T 563—1999汽车转向盘试验方法代替JB 3979—85本标准规定了转向盘试验方法,适用于金属骨架包覆塑料的汽车、拖拉机用转向盘。
1 试验项目转向盘试验项目如表1所示。
2 试验方法2.1 外观检查2.1.1 转向盘的外观用肉眼直接观察,尺寸及变形量用卡尺或直尺测量。
2.1.2 外观检查用的转向盘数量不得小于5个。
2.1.3 用卡尺和直尺测量转向盘尺寸,并对照图纸检查其几何尺寸及形状是否符合规定要求。
2.1.4 观察转向盘的表面光泽是否均匀,有无裂纹、凸起、凹陷、毛刺、探伤痕、熔接痕等。
2.1.5 观察轮毂孔内是否有毛刺,轮毂端面上是否有废余塑料。
2.1.6 用X光无损探伤法检查骨架在包覆塑料中的位置,并测出偏移量(mm)。
如X光无损探伤有困难,可以锯开轮辐和轮缘,直接测量偏移量(mm)。
注:锯开的位置及数量由供需双方确定。
2.2 热性能试验热性能试验包括耐热试验、耐寒试验、冷热交变试验。
其目的是转向盘在高温、低温以及高低温反复变化的条件下,检查其外观的变化。
2.2.1 耐热试验2.2.1.1 试样及数量耐热试验直接采用转向盘制品,其数量不得少于6个,其中一个保存在室内,作为标准试样用于评价变色程度。
2.2.1.2 试验设备恒温箱,温度波动不大于±2℃。
2。
2.1.3 试验条件耐热试验温度为90±2℃。
2.2.1.4 试验步骤恒温箱温度升高到90℃,把转向盘放入恒温箱中,并控制在90±2℃温度范围内,保持4h后取出,观察其外观变化。
2.2.2 耐寒试验2.2.2.1 试样及数量耐寒试验直接采用转向盘制品,其数量不得少于5个。
2.2.2.2 试验设备低温箱,温度波动不大于±2℃。
2.2.2.3 试验条件耐寒试验温度为-40±2℃。
2.2.2.4 试验步骤低温箱温度下降到-40℃,把转向盘放入低温箱中,并控制在-40±2℃温度范围内,保持7h,取出观察外观变化。
中华人民共和国机械行业标准

1主题内容 与适用范围
本标准 规定了热重一 差热分 析仪 ( T G-D T A) 的分 类、 技术要求 、 试验方 法 、 检验 规则 、 标志 、 包装 、
运输和贮存等。
本标 准适用 于常压 中温类 、 常压 高温类热重一差热分析仪 ( 以下 简称仪器 ) 本 标准 不适 用于常 压低温类 仪器。 2 引 用标 准 G B 2 8 2 9 A } 9 期检 查计 数抽 样程序及抽样 表 Z B Y 0 0 2 仪器仪表运输 、 运输贮 存基本环境条件 及试验 方法 Z B Y 0 0 3 仪器仪表 包装通 用技术条件 1 B 8 产品标牌 3 热重 一差热分析仪 分类 3 1 热 重一差热分析 仪分类 热重一 差热 分析仪分类 见表 1 0
1 . 5 . 2升、 降 温速率小于或等于 2 0 V/ m m时, 升、 降温曲 线应龙 滑。
4‘ 差热单元
4‘1放大器零点 漂移在 4 h 内不大于 1 . 5 p v 46三放大器噪吉不大于。2 . V ( 峰一峰值) 4 . 6 . 3量程 误差上 5 p v至士 5 即V档不超过 = 5 % , 其余档不超过- 3 % } 47差热基线 漂移
J B /T 6 85 6一 93
4 . 1 0 温度标 定 a 锢熔点 :
外推始点 1 5 4 1 4 1 ; ;
b 石英相 变点 : 5 外推始点 7 1 士3 C: c 铝熔 点: 外推始 点 6 5 8 . 8 - 4 ℃; d . 碳酸银相 变点二 9 外推始点 2 8 二 7 1 ; ; e 银熔 点 : 外 推始点 9 6 0 . 8 士 4 C ; , 4 . 1 1 静态 氮气中草酸钙 D T A 曲线 要求不 出现 一氧化碳燃烧放热峰 4 . 1 2 流动 氮气中草酸钙 T G (一 D T + : ) 一D T A 曲线 要求 T G曲线 漂移与静态常压空 气条件下相当 ; 不出现一氧 f 七 碳然 烧放热峰 4 . 1 3 石英一硫酸钾 分辩率
中华人民共和国机械工业部部标准(试验标准)
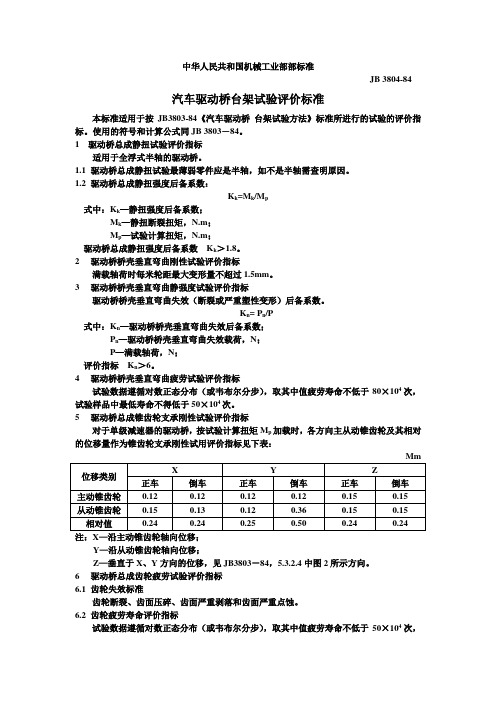
中华人民共和国机械工业部部标准JB 3804-84汽车驱动桥台架试验评价标准本标准适用于按JB3803-84《汽车驱动桥台架试验方法》标准所进行的试验的评价指标。
使用的符号和计算公式同JB 3803-84。
1 驱动桥总成静扭试验评价指标适用于全浮式半轴的驱动桥。
1.1驱动桥总成静扭试验最薄弱零件应是半轴,如不是半轴需查明原因。
1.2驱动桥总成静扭强度后备系数:K k=M k/M p式中:K k—静扭强度后备系数;M k—静扭断裂扭矩,N.m;M p—试验计算扭矩,N.m;驱动桥总成静扭强度后备系数K k>1.8。
2驱动桥桥壳垂直弯曲刚性试验评价指标满载轴荷时每米轮距最大变形量不超过1.5mm。
3驱动桥桥壳垂直弯曲静强度试验评价指标驱动桥桥壳垂直弯曲失效(断裂或严重塑性变形)后备系数。
K n= P n/P式中:K n—驱动桥桥壳垂直弯曲失效后备系数;P n—驱动桥桥壳垂直弯曲失效载荷,N;P—满载轴荷,N;评价指标K n>6。
4驱动桥桥壳垂直弯曲疲劳试验评价指标试验数据遵循对数正态分布(或韦布尔分步),取其中值疲劳寿命不低于80×104次,试验样品中最低寿命不得低于50×104次。
5驱动桥总成锥齿轮支承刚性试验评价指标对于单级减速器的驱动桥,按试验计算扭矩M p加载时,各方向主从动锥齿轮及其相对的位移量作为锥齿轮支承刚性试用评价指标见下表:Y—沿从动锥齿轮轴向位移;Z—垂直于X、Y方向的位移,见JB3803-84,5.3.2.4中图2所示方向。
6驱动桥总成齿轮疲劳试验评价指标6.1齿轮失效标准齿轮断裂、齿面压碎、齿面严重剥落和齿面严重点蚀。
6.2齿轮疲劳寿命评价指标试验数据遵循对数正态分布(或韦布尔分步),取其中值疲劳寿命不低于50×104次,试验样品中最低寿命不低于30×104次。
锅炉用钢材进厂检验标准
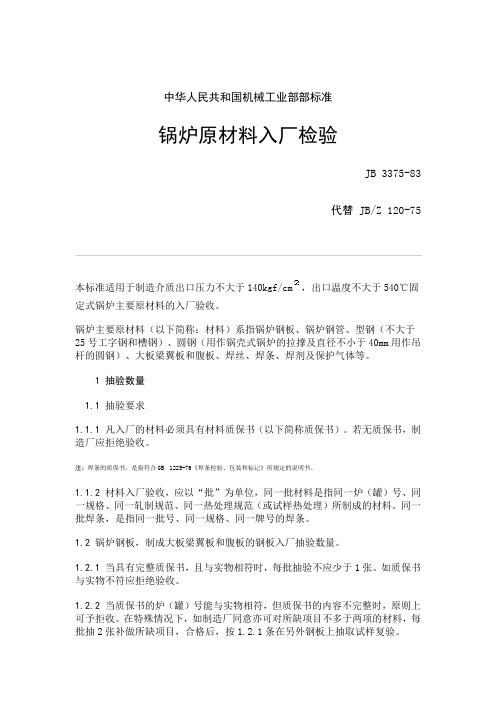
中华人民共和国机械工业部部标准锅炉原材料入厂检验JB 3375-83代替 JB/Z 120-75本标准适用于制造介质出口压力不大于140kgf/cm,出口温度不大于540℃固定式锅炉主要原材料的入厂验收。
锅炉主要原材料(以下简称:材料)系指锅炉钢板、锅炉钢管、型钢(不大于25号工字钢和槽钢)、圆钢(用作锅壳式锅炉的拉撑及直径不小于40mm用作吊杆的圆钢)、大板梁翼板和腹板、焊丝、焊条、焊剂及保护气体等。
1 抽验数量1.1 抽验要求1.1.1 凡入厂的材料必须具有材料质保书(以下简称质保书)。
若无质保书,制造厂应拒绝验收。
注:焊条的质保书,是指符合GB1225-76《焊条检验、包装和标记》所规定的说明书。
1.1.2 材料入厂验收,应以“批”为单位,同一批材料是指同一炉(罐)号、同一规格、同一轧制规范、同一热处理规范(或试样热处理)所制成的材料。
同一批焊条,是指同一批号、同一规格、同一牌号的焊条。
1.2锅炉钢板,制成大板梁翼板和腹板的钢板入厂抽验数量。
1.2.1当具有完整质保书,且与实物相符时,每批抽验不应少于1张。
如质保书与实物不符应拒绝验收。
1.2.2当质保书的炉(罐)号能与实物相符,但质保书的内容不完整时,原则上可予拒收。
在特殊情况下,如制造厂同意亦可对所缺项目不多于两项的材料,每批抽2张补做所缺项目,合格后,按1.2.1条在另外钢板上抽取试样复验。
1.2.3 表面质量及尺寸偏差、每批抽查不应少于2张。
1.2.4 锅炉钢板当材料屈服强度不小于40kgf/mm或板厚S不小于60mm时,应作超声波检验,每批应按15%抽验,且不少于2张,当供货单位没有逐张超声波检验时,制造厂应逐张进行超声波检验。
1.2.5 当钢板长度不小于7m或重量不小于5000kg时,应在钢板两端各取一套试样。
1.3 锅炉钢管入厂抽验数量1.3.1 当具有完整的质保书,且与实物相符时,每批抽验不应少于2根,其中只需1根做化学分析。
4732标准释义

4732标准释义
4732标准全称为JB4732-1995《钢制压力容器—分析设计标准》,是中华人民共和国原机械工业部发布的行业标准。
该标准规定了钢制压力容器的设计、制造、检验、验收、操作、维修和报废等方面的内容,以确保其安全可靠运行。
JB4732标准与GB/T 150一起作为压力容器的设计标准并同时实施,但两者在某些方面存在差异。
例如,JB4732允许采用较高的设计应力强度,这意味着在相同设计条件下,容器的厚度可以减薄,重量可以减轻。
然而,由于设计计算工作量大、选材、制造、检验及验收等方面的要求较严,综合经济效益不一定高,一般推荐用于重量大、结构复杂、操作参数较高和超出GB/T150适用范围的压力容器设计。
技术条件
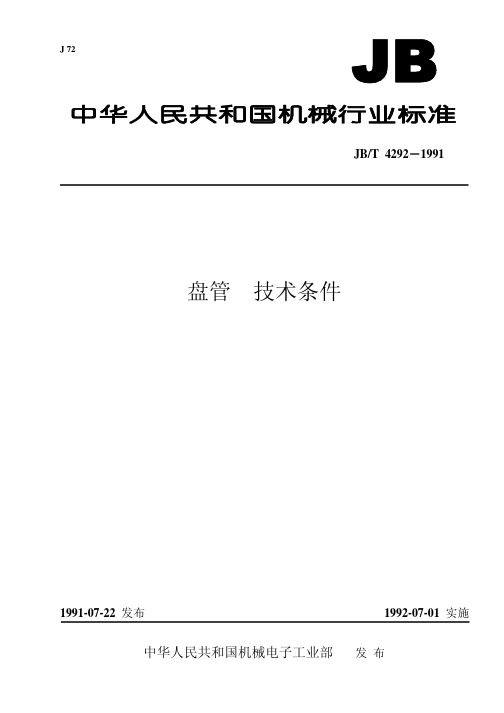
过 3 mm 的焊缝咬边深度应不超过 0.8 mm。 3. 1. 7
机械电子工业部 1991-07-22 批准
1992-07-01 实施
1
3. 1. 4
经热法浸镀或采用其他防腐及密隙处理的换热管镀层应均匀、光滑,肋片与换热光管间结合应 焊接接头基本型式与尺寸应符合 GB 985 的规定。 焊缝应无裂纹、气孔等缺陷,并圆滑向母材过渡。板厚不超过 3 mm 的焊缝应无咬边;板厚超 法兰连接孔中心距的尺寸允差应符合下图及表 2 的规定。
牢固,浸镀后换热管的倒片、迭片应修整。 3. 1. 5 3. 1. 6
J 72
Байду номын сангаас
JB/T 4292-1991
盘管
技术条件
1991-07-22 发布
1992-07-01 实施 发 布
中华人民共和国机械电子工业部
中华人民共和国机械行业标准
JB/T 4292-1991
代替 JB 4292—86
盘管
技术条件
1
主题内容与适用范围 本标准规定了盘管的技术要求、检验规则、标志、包装和贮存。 本标准适用于空调、通风、热风采暖等系统,最高工作压力不超过 1.3 MPa、介质为冷、热水和
型 绕 套 式 片 片 片 距 允 差 1)
手工电弧焊接接头的基本型式与尺寸 空气冷却器空气加热器性能试验方法 采暖通风与空气调节设备涂装技术条件 盘管 耐压试验与密封性检查 冷暖通风设备包装通用技术条件 采暖通风设备外观质量与清洁度 产品标牌
±4% ±2%
注:1)在 100 个片距长度上,片距总和的允差。
蒸汽的盘管。 2 引用标准 GB 985 GB 10223 ZB J72 017 ZB J72 021 ZB J72 026 ZB J72 029 JB 8 3 3. 1 3. 1. 1 3. 1. 2 3. 1. 3 技术要求 一般要求 盘管应符合本标准的要求,并按经规定程序批准的图样及技术文件制造。 所有的黑色金属制件表面应作防腐处理。 换热管肋片应整齐、平直、疏密均匀,与管子接触应紧密,其片距允差按表 1 规定。 表 1
中华人民共和国机械行业标准JB/T81-94凸面钢制管法兰盖

中华人民共和国机械行业标准 JB/T 86.1-94 凸面钢制管法兰盖 代替JB 86—59 1 主题内容与适用范围 本标准规定了公称压力PN为0.6,1.O,1.6,2.5,4.0 MPa的凸面钢制管法兰盖的型式和尺寸。
本标准适用于公称压力PN O.6~4.0 MPa的凸面钢制管法兰盖。
2 引用标准 JB/T 74 管路法兰 技术条件 3 法兰盖的型式和尺寸应符合图1及表1~表5的规定。
图1 4 法兰盖的技术要求按JB/T 74的规定。
5 法兰盖的公称压力和不同温度下的最大允许工作压力按JB/T 74附录B的规定。
6 标记示例 公称通径300 mm、公称压力4.0 MPa、尺寸为系列2的凸面钢制管法兰盖: 法兰盖300—40 JB/T 86.1—94 公称通径300 mm、公称压力4.0 MPa、尺寸为系列1的凸面钢制管法兰盖: 法兰盖300—40(系列1) JB/T 86.1—94 机械工业部1994—12—09批准 1995—10一01实施 1表1 PN0.6 MPa凸面钢制管法兰盖尺寸 mm 连接尺寸密封面尺寸螺栓、螺柱 公称 通径 DN法兰外径D 系列1/系列2螺栓孔中 心圆直径K 螺栓孔直径L 系列1/系列2数量 n 螺纹Th. 系列1/系列2df法兰 厚度 C法兰 理论 重量 kg10 15 20 25 32 40 50 65 80 100 125 150 (175) 200 (225) 250 300 350 400 450 500 600 700 800 900 100075 80 90 100 120 130 140 160 190/185 210/205 240/235 265/260 290 320/315 340 375/370 440/435 490/485 540/535 595/590 645/640 755 860 975 1075 117550 55 65 75 90 100 110 130 150 170 200 225 255 280 305 335 395 445 495 550 600 705 810 920 1020 112012 12 12 12 14 14 14 14 18 18 18 18 18 18 18 18 23 23 23 23 23 26/25 26/25 30 30 304 4 4 4 4 4 4 4 4 4 8 8 8 8 8 12 12 12 16 16 16 20 24 24 24 28M1O M10 M10 M10 M12 M12 M12 M12 M16 M16 M16 M16 M16 M16 M16 M16 M20 M20 M20 M20 M20 M24/M22 M24/M22 M27 M27 M2732 40 50 60 70 80 90 110 125 145 175 200 230 255 280 310 362 412 462 518 568 670 775 880 980 10802 2 2 2 2 3 3 3 3 3 3 3 3 3 3 3 4 4 4 4 4 5 5 5 5 512 12 12 12 12 14 14 14 14 14 16 16 16 16 16 16 18 18 20 22 24 28 32 36 40 44O.30 0.40 O.50 0.60 O.90 1.20 1.40 1.90 2.70 3.30 5.10 6.20 8.OO 9.20 11.10 12.80 19.40 24.00 34.00 46.OO 58.OO 92.00 141.00 202.OO 273.OO 315.OO表2 PN 1.0MPa凸面钢制管法兰盖尺寸 mm 连接尺寸 密封面尺寸螺栓、螺柱 公称 通径 DN法兰外径 D 系列1/系列2螺栓孔中 心圆直径 K 螺栓孔直径L 系列l/系列2数量 n 螺纹Th. 系列1/系列2 d f 法兰 厚度 C法兰 理论 重量 kg10 15 20 25 32 40 50 65 80 100 125 150 (175) 200 (225) 250 300 350 400 450 500 600 700 800 900 100090 95 105 115 140/135 150/145 165/160 185/180 200/195 220/215 250/245 285/280 310 340/335 365 395/390 445/440 505/500 565 615 670 780 895 1015/1010 1115/1110 1230/122060 65 75 85 100 11O 125 145 160 180 210 240 270 295 325 350 400 460 515 565 620 725 840 950 1050 116014 14 14 14 18 18 18 18 18 18 18 23 23 23 23 23 23 23 26/25 26/25 26/25 30 30 34 34 36/344 4 4 4 4 4 4 4 4 8 8 8 8 8 8 12 12 16 16 20 20 20 24 24 24 28M12 M12 M12 M12 M16 M16 M16 M16 M16 M16 M16 M20 M20 M20 M20 M20 M20 M20 M24/M22 M24/M22 M24/M22 M27 M27 M30 M30 M33/M3040 45 55 65 78 85 100 120 135 155 185 210 240 265 295 320 368 428 482 532 585 685 800 905 1005 11152 2 2 2 2 3 3 3 3 3 3 3 3 3 3 3 4 4 4 4 4 5 5 5 5 512 12 12 12 12 14 14 14 14 14 16 16 16 16 18 18 20 24 26 28 32 36 42 48 S4 58O.50 0.60 O.70 0.80 1.10 1.50 2.00 2.50 3.OO 3.60 5.50 7.00 9.10 lO.20 14.OO 15.70 22.00 34.00 47.00 61.00 85.00 127.OO 199.00 290.00 395.OO 525.00表3 PN 1.6 MPa凸面钢制管法兰盖尺寸 mm 连接尺寸密封面尺寸螺栓、螺柱 公称 通径 DN法兰外径D 系列1/系列2螺栓孔中 心圆直径K螺栓孔直径L 系列l/系列2数量 n螺纹Th. 系列1/系列2d f 法兰 厚度 C法兰 理论 重量 kg10 15 20 25 32 40 50 65 80 100 125 150 (175) 200 (225) 250 300 350 400 450 500 600 90 95 105 115 140/135 150/145 165/16d 185/180 200/195 220/215 250/245 285/280 310 340/335 365 405 460 520 580 640 715/705 840 60 65 75 85 100 110 125 145 160 180 210 240 270 295 325 355 410 470 525 585 650 770 14 14 14 14 18 18 18 18 18 18 18 23 23 23 23 26/25 26/25 26/25 30 30 34 36/41 4 4 4 4 4 4 4 4 8 8 8 8 8 12 12 12 12 16 16 20 20 20 M12 M12 M12 M12 M16 M16 M16 M16 M16 M16 M16 M20 M20 M20 M20 M24/M22 M24/M22 M24/M22 M27 M27 M30 M33/M36 40 45 55 65 78 85 100 120 135 155 185 210 240 265 295 320 375 435 485 545 608 7182 2 2 2 2 3 3 3 3 3 3 3 3 3 3 3 4 4 4 4 4 512 12 12 12 12 14 14 14 14 16 16 18 18 20 22 24 28 32 36 42 46 54 0.50 0.60 0.70 0.80 1.20 1.60 2.00 2.50 2.90 4.10 5.50 8.00 10.20 12.80 17.50 22.00 34.OO 49.00 70.00 99.60 133.00 220.00表4 PN 2.5 MPa凸面钢制管法兰盖尺寸 mm 连接尺寸密封面尺寸 螺栓、螺柱 公称 通径 DN法兰外径D 系列1/系列2螺栓孔中 心圆直径 K螺栓孔直径L 系列1/系列2数量 n 螺纹Th. 系列1/系列2d f 法兰 厚度 C法兰 理论 重量 kglO 15 20 25 32 40 50 65 80 100 125 150 (175) 200 (225) 250 300 350 400 90 95 105 115 140/135 150/145 165/160 185/180 200/195 235/230 270 300 330 360 395 425 485 555/550 620/610 60 65 75 85 100 110 125 145 160 190 220 250 280 310 340 370 430 490 550 14 14 14 14 18 18 18 18 18 23 26/25 26/25 26/25 26/25 30 30 30 34 36/34 4 4 4 4 4 4 4 8 8 8 8 8 12 12 12 12 16 16 16 M12 M12 M12 M12 M16 M16 M16 M16 M16 M20 M24/M22 M24/M22 M24/M22 M24/M22 M27 M27 M27 M30 M33/M30 40 45 55 65 78 85 100 120 135 160 188 218 248 278 302 332 390 448 505 2 2 2 2 2 3 3 3 3 3 3 3 3 3 3 3 4 4 4 12 12 12 12 12 14 14 16 18 20 22 24 24 26 28 30 34 38 42 O.50 0.60 0.70 O.80 l.10 1.50 2.00 2.80 3.80 5.80 8.60 1l.90 15.OO 18.70 25.10 30.00 45.00 66.OO 92.00表5 PN 4.O MPa凸面钢制管法兰盖尺寸 mm 连接尺寸密封面尺寸螺栓、螺柱 公称 通径 DN 法兰外径D 系列1/系列2螺栓孔中 心圆直径 K 螺栓孔直径L 系列1/系列2数量 n 螺纹Th. 系列1/系列2d f法兰 厚度 C法兰 理论 重量 kg10 15 20 25 32 40 50 65 80 100 125 150 (175) 200 (225) 250 300 350 40090 95 105 115 140/135 150/145 165/160 185/180 200/195 235/230 270 300 350 375 415 450/445 515/510 580/570 660/65560 65 75 85 100 110 125 145 160 190 220 250 295 320 355 385 450 510 58514 14 14 14 18 18 18 18 18 23 26/25 26/25 30 30 34 34 34 36/34 414 4 4 4 4 4 4 8 8 8 8 8 12 12 12 12 16 16 16M12 M12 M12 M12 M16 M16 M16 M16 M16 M20 M24/M22 M24/M22 M27 M27 M30 M30 M30 M33/M30 M3640 45 55 65 78 85 100 120 135 160 188 218 258 282 315 345 408 465 5352 2 2 2 2 3 3 3 3 3 3 3 3 3 3 3 4 4 416 16 16 16 16 16 18 20 22 24 28 30 34 38 40 44 50 56 64O.70 O.80 0.90 1.OO 1.60 1.80 2.60 3.60 4.70 7.10 10.50 15.00 23.40 29.00 39.00 46.OO 50.OO 74.OO 158.OO注:①表1~表5中系列1法兰连接尺寸与国标及德国法兰标准尺寸互换;系列2尺寸与原机标法兰尺寸互换;新产品设计应优先采用系列1尺寸。
QC.T551-1999汽车发动机 飞轮壳安装尺寸
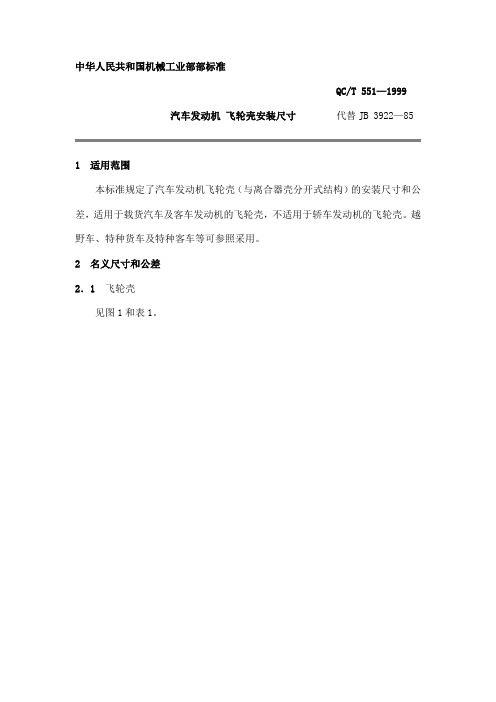
中华人民共和国机械工业部部标准QC/T 551—1999汽车发动机飞轮壳安装尺寸代替JB 3922—851 适用范围本标准规定了汽车发动机飞轮壳(与离合器壳分开式结构)的安装尺寸和公差,适用于载货汽车及客车发动机的飞轮壳,不适用于轿车发动机的飞轮壳。
越野车、特种货车及特种客车等可参照采用。
2 名义尺寸和公差2.1 飞轮壳见图1和表1。
2.2 螺孔的尺寸和间距2.2.1 尺寸和公差见图1和表2。
2.2.2 间距螺孔应在垂直和水平轴线两边均布,如图2所示。
3 飞轮壳与离合器定位孔的相互位置尺寸定位孔的深度(见图3的E)是指从飞轮壳端面到飞轮台阶或曲轴法兰盘端面或曲轴内部的一个台阶的距离,其尺寸见表3。
当多片离合器与特重型飞轮一起使用时,飞轮壳尺寸E还可选用括弧内尺寸。
4 相配件的安装尺寸4.1 相配件(如离合器壳)凸缘定位直径的公差与配合及形位公差均由该零件生产者自行决定。
4.2 相配件凸缘的通孔的位置应与2.2.2节中的规定相同,并符合GB 152—76《紧固件通孔及沉头座尺寸》的规定。
附录A孔的同轴度和端面圆跳动的测量程序(补充件)A.1 范围本附录适用于飞轮壳安装到发动机之后、测量其定位孔的同轴度及端面圆跳动的统一程序,孔的同轴度和端面圆跳动的公差由表1给定。
A.2 测量程序A.2.1 准备A.2.1.1 一只具有刚性加长杆的百分表。
A.2.1.2 被测表面不得有污物和毛刺。
A.2.1.3 一张如图 A1 所示的图表,以帮助确定孔的同轴度。
A.2.2 飞轮壳同轴度的测量A.2.2.1 将百分表的底座安在飞轮或曲轴的法兰盘上,并尽量靠近壳体定位孔,使误差减至最小。
A.2.2.2 将表调至与定位孔垂直,并在相当于时针6点钟位置处(硬性规定)置零。
A.2.2.3 缓慢地移动曲轴,并记录百分表在9点钟(a)、12点钟(b)、3点钟(c)位置时的读数及其相应的正负号。
*6点钟位置的读数应仍为零。
将读数记录在表A1的A行中,切记要带正、负号。
JB-2932-86 水处理设备制造技术条件

水处理设备制造技术条件
本标准适用于: a.设计压力p<1.569MPa(16kgf/cm2),不受《压力容器安全监察规 程》(以下简 称《容规》)监察的水处理设备的制造和检验。 b.设计压力0.098<p<1.569MPa(1<p<16kgf/cm2);容积V≥25L; 且p ×V≥19.6L·MPa(200L·kgf/cm2);设计温度高于标准沸点(指在 0.1MPa下的沸 点),介质为水和蒸汽,受《容规》监察的设备的制造和 检验。 各零部件的制造、装配和检验,除应符合本技术条件外,还应符合 设计图样、 工艺文件的要求。 1 技术要求 1.1 材料 1.1.1 制造设备的材料应符合部标《水处理设备原材料入厂检验》的规 定。 1.1.2 制造厂对首次采用的新材料应进行必要的工艺性试验。 1.1.3 容器材料的含碳量不得大于0.24%,焊后需热处理的容器,焊条含 钒量不得 大于0.05%。 1.1.4 设备的主要受压元件下料时,应按有关规定打上原材料移植标记。 1.1.5 设备的主要受压元件材料代用,必须征得原设计单位的同意,并 附证明文 件。 1.1.6 凡与容器相焊接的材料,其可焊性应良好。 1.1.7 焊接材料(包括焊条、焊丝、焊剂、保护气体金属粉末等)的选用, 按图样和工 艺文件的规定。 1.1.8 硬聚氯乙烯板应符合SG86—78《硬聚氯乙烯板材》的规定;管材 应符合 SG78—75《硬聚氯乙烯管材》的规定;焊条应符合相应标准的规 定。 1.1.9 设备所用锻件按JB755—73《压力容器锻件技术条件》中的Ⅰ级要 求规定。 1.1.10 设备上连接外管道的法兰和几何尺寸相类似的锻件按 JB74~85 —59《管 路法兰》1的规定。 1.1.11 设备容器法兰和几何尺寸相类似的锻件按JB1157~1164—82《压 力容器 法兰》的规定。 1.1.12 设备用灰铸铁件应符合JB2639—83《锅炉承压灰铸铁铸件技术条 件》及 JB2854—80《铸件机械加工余量、尺寸偏差和重量偏差》的规定。 1.2 冷热加工成形
中华人民共和国机械工业部部标准
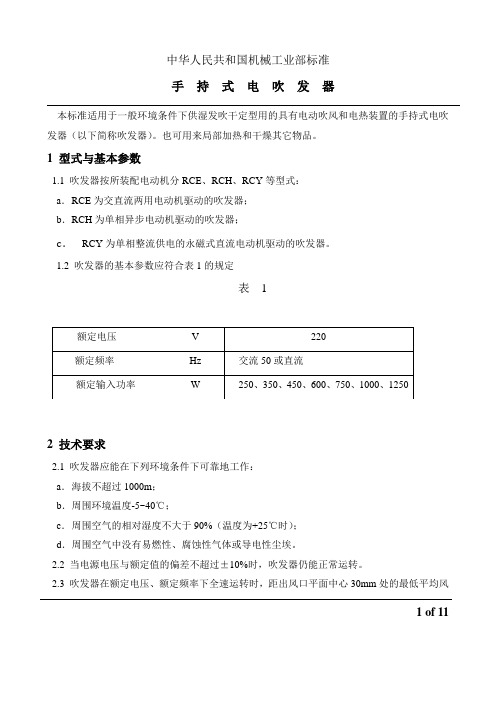
中华人民共和国机械工业部标准手持式电吹发器本标准适用于一般环境条件下供湿发吹干定型用的具有电动吹风和电热装置的手持式电吹发器(以下简称吹发器)。
也可用来局部加热和干燥其它物品。
1 型式与基本参数1.1 吹发器按所装配电动机分RCE、RCH、RCY等型式:a.R CE为交直流两用电动机驱动的吹发器;b.RCH为单相异步电动机驱动的吹发器;c.RCY为单相整流供电的永磁式直流电动机驱动的吹发器。
1.2 吹发器的基本参数应符合表1的规定表 12 技术要求2.1 吹发器应能在下列环境条件下可靠地工作:a.海拔不超过1000m;b.周围环境温度-5~40℃;c.周围空气的相对湿度不大于90%(温度为+25℃时);d.周围空气中没有易燃性、腐蚀性气体或导电性尘埃。
2.2 当电源电压与额定值的偏差不超过±10%时,吹发器仍能正常运转。
2.3 吹发器在额定电压、额定频率下全速运转时,距出风口平面中心30mm处的最低平均风1 of 11速、热风温升范围以及同型号产品温差范围应符合表2规定。
表 2中华人民共和国机械工业部1985—01—14发布1985—06—01实施2.4 吹发器在额定电压、额定频率下正常工作时,各部分的额定温升应不超过表3的规定。
表 32.5 吹发器在额定电压、额定频率下的实际消耗功率与额定输入功率的偏差不应大于+5%或小于-10%。
2.6 吹发器在85%额定电压下风叶在任一位置都应能起动至运转。
2.7 在稳定热态时Ⅰ类吹发器(一般绝缘有接地装置者)带电部分与外壳的绝缘电阻不低于2MΩ,Ⅱ类吹发器(双Ⅲ绝缘无接地装置者)不低于7MΩ。
出厂试验允许在冷态下进行。
2.8 吹发器的绝缘应承受历时1min的耐电压试验而不发生击穿及闪路现象,试验电压的频率为50Hz,波形为实际正弦波。
试验电压的有效值Ⅰ类吹发器为1500V,Ⅱ类吹发器为3750V。
2.9 吹发器的噪声以A计权声功率级表示,应不大于表4的规定。
中华人民共和国机械行业标准
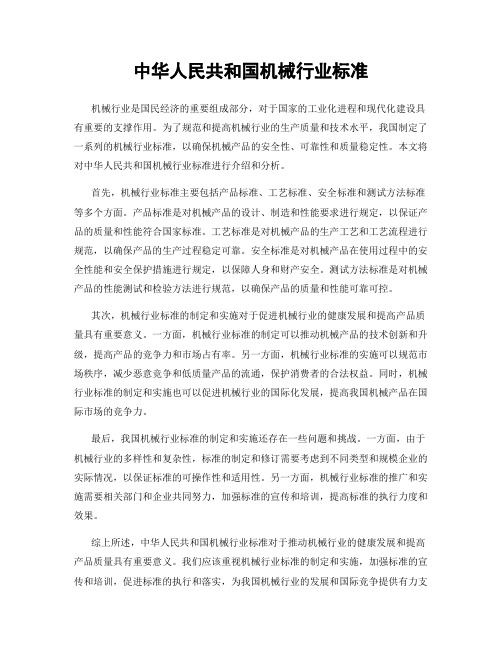
中华人民共和国机械行业标准机械行业是国民经济的重要组成部分,对于国家的工业化进程和现代化建设具有重要的支撑作用。
为了规范和提高机械行业的生产质量和技术水平,我国制定了一系列的机械行业标准,以确保机械产品的安全性、可靠性和质量稳定性。
本文将对中华人民共和国机械行业标准进行介绍和分析。
首先,机械行业标准主要包括产品标准、工艺标准、安全标准和测试方法标准等多个方面。
产品标准是对机械产品的设计、制造和性能要求进行规定,以保证产品的质量和性能符合国家标准。
工艺标准是对机械产品的生产工艺和工艺流程进行规范,以确保产品的生产过程稳定可靠。
安全标准是对机械产品在使用过程中的安全性能和安全保护措施进行规定,以保障人身和财产安全。
测试方法标准是对机械产品的性能测试和检验方法进行规范,以确保产品的质量和性能可靠可控。
其次,机械行业标准的制定和实施对于促进机械行业的健康发展和提高产品质量具有重要意义。
一方面,机械行业标准的制定可以推动机械产品的技术创新和升级,提高产品的竞争力和市场占有率。
另一方面,机械行业标准的实施可以规范市场秩序,减少恶意竞争和低质量产品的流通,保护消费者的合法权益。
同时,机械行业标准的制定和实施也可以促进机械行业的国际化发展,提高我国机械产品在国际市场的竞争力。
最后,我国机械行业标准的制定和实施还存在一些问题和挑战。
一方面,由于机械行业的多样性和复杂性,标准的制定和修订需要考虑到不同类型和规模企业的实际情况,以保证标准的可操作性和适用性。
另一方面,机械行业标准的推广和实施需要相关部门和企业共同努力,加强标准的宣传和培训,提高标准的执行力度和效果。
综上所述,中华人民共和国机械行业标准对于推动机械行业的健康发展和提高产品质量具有重要意义。
我们应该重视机械行业标准的制定和实施,加强标准的宣传和培训,促进标准的执行和落实,为我国机械行业的发展和国际竞争提供有力支持。
希望相关部门和企业能够共同努力,不断完善和提高机械行业标准体系,为我国机械行业的发展和繁荣做出更大的贡献。
中华人民共和国国家标准公告2016年第17号(机械工业部分)

2 0l 7 - 0 5 - 0l
1 一 业 车辆 稳定 验 证 第 8部 分 :在 门 前倾 l 5 G B f r 2 6 9 4 9 . 8 —2 0 J 6 和裁 荷 起 升 条 件下 堆 垛 作 、 J 的附 加 稳 定性 试 验 G B 厂 【 1 2 l 4 6 7 -2 0 0 8
2 0l 7 — 1 1 — 01 2 0l 7 - 0 5 - 0l
铸 造 合 金锭
7 : 2 4 1 嘲 锥 鲢 规 锰 基钎 料 检 验
GI j 厂 r 8 7 3 3 —2 0 0 7
GB , r 1 l 8 5 4 —2 0 0 3 Gl j , r l 3 6 7 9 一l 9 9 2
| I l
。
_
譬
。
农 林 拖 托 机 和 机 械 、草 坪 和 同 动 力 机 械 操 作 l ( ; B f l ’ 4 2 6 9 . 2 —2 0 l 6 臂操纵机 构乖 l 】 其 他 示 装 置 川 符 用 拖 拉机 币 I I 机 械 用 符
2 GB 厂 r 5l 8 4 —2 0I 6 3 ( B , r 6 4 0 6 —2 0 l 6 义 乍 挂 钩 型 货 叉和 货 叉 架 安 装 寸 超 硬磨 料 粒 度 榆 验 ( ; B / T 5 l 8 4 —2 0 0 8 ( B , r 6 4 0 6 一l 9 9 6
2 O I 7 — 0 5 一 O I
1 6 ( ; B / 1 " 2 6 9 4 9 . 1 l 一2 0 1 6 叉 乍
惶 车 辆 稳 定 性 验 证 第 l 1 5 - o1
1 业 车 辆 稳 定 r £ 验证 l 7 G B / i " 2 6 9 4 9 . 1 4 —2 O 1 6 缩臂式 叉乍
中华人民共和国机械工业部
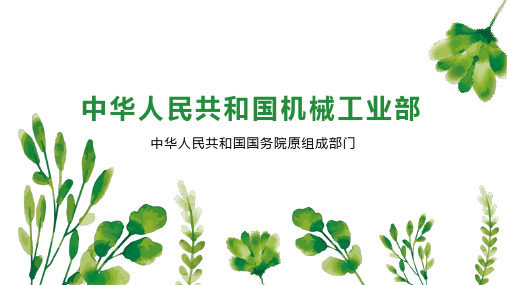
(四)指导机械行业高技术、通用技术及基础技术的研究、开发和应用,推进行业技术进步。组织制订行业 的技术标准、质量标准并对产品质量进行监督。
(五)组织协调机械行业重大技术装备及重点产品、军工产品的研制。
(六)管理部直属企事业单位,监督、检查、评价大型骨干机械企业的国有资产的保值增殖。参与国家有关 部门对机械行业的经济调节工作。
中华人民共和国机械工业部
中华人民共和国国务院原组成部门
01 历史沿革
03 机构设置 05 历任领导
目录
02 机构职责 04 人员编制
中华人民共和国机械工业部,为主管全国机械行业的中华人民共和国国务院原组成部门,成立于1982年5月, 其前身为原中华人民共和国第一机械工业部、中华人民共和国农业机械部、国家仪器仪表工业总局、国家机械设 备成套总局。
(一)制订振兴机械工业的方针、政策、法规,制定行业管理规章,指导行业体制改革、企业改革。
(二)制订机械行业的发展战略、总体布局及行业政策。组织编制行业中长期发展规划、年度计划。
(三)提出关于机械行业固定资产投资规模的意见,对行业重,存基本建设、技术改造、技术引进、利用外 资项目进行审查,提出立项建议。
历任领导
周建南(1982年4月—1985年8月) 何光远(1993年3月—1996年3月) 包叙定(1996年3月—1998年8月)
感谢观看
国家标准:汽车用螺纹紧固件拧紧扭矩规范

中华人民共和国机械工业部部标准中华人民共和国机械工业部1984-05-21发布 1984-12-01实施 JB3677-84汽车用螺纹紧固件拧紧扭矩规范本标准适用于碳素钢或合金钢制造的螺纹直径为6~20mm 、6级精度以上的汽车用一般螺栓、螺钉、螺柱和螺母的紧固。
其螺纹尺寸及公差按GB193-81《普通螺纹、直径与螺距系列》、GB196-81《普通螺纹、基本尺寸》和GB197-81《普通螺纹、公差与配合》标准的规定;螺栓、螺钉、螺柱和螺母机械性能、螺栓、螺钉、螺柱与螺母被拧入基本件强度级别的组合按GB3098-82《紧固件机械性能》标准的规定。
本标准不适用于承受交变载荷或加润滑剂装配的螺栓、螺钉、螺柱和螺母的紧固件,以及紧定螺钉和类似的不规定抗拉强度的螺纹紧固件。
1汽车用螺纹紧固件拧紧扭矩1.1机械性能为4.6级的螺栓、螺钉和螺柱,其拧紧扭矩按表1的规定。
表1拧 紧 扭 矩标 准 值 最 大 值最 小 值螺纹直径 mm螺距 mmN.m (Kgf.m)N.m (Kgf.m)N.m (Kgf.m)61 4.0 0.4 5.5 0.6 2.5 0.3 8 1.25 8.0 0.8 11.0 1.1 5.0 0.5 8 1 8.5 0.9 11.5 1.2 5.5 0.6 10 1.5 19.7 2.0 24.7 2.5 14.3 1.5 10 1.25 20.8 2.1 25.8 2.6 16.7 1.7 10 1 21.8 2.2 26.5 2.7 17.0 1.7 12 1.75 37.3 3.8 43.3 4.4 28.0 2.9 12 1.5 38.5 3.9 45.0 4.6 29.0 3.0 12 1.25 39.6 4.0 48.0 4.9 30.0 3.1 14 2 61.2 6.2 75.0 7.6 46.8 4.8 14 1.5 74.6 7.6 92.0 9.4 56.0 5.7 16 2 95.0 9.7 115.0 11.7 73.0 7.4 16 1.5 105.0 10.7 133.0 13.6 76.0 7.7 18 2.5 142.9 14.6 178.0 18.1 107.4 10.9 18 1.5 157.6 16.1 190.0 19.4 124.5 12.71.2机械性能为5.6级的螺栓、螺钉和螺柱,其拧紧扭矩按表2规定。
中华人民共和国机械工业部部标准
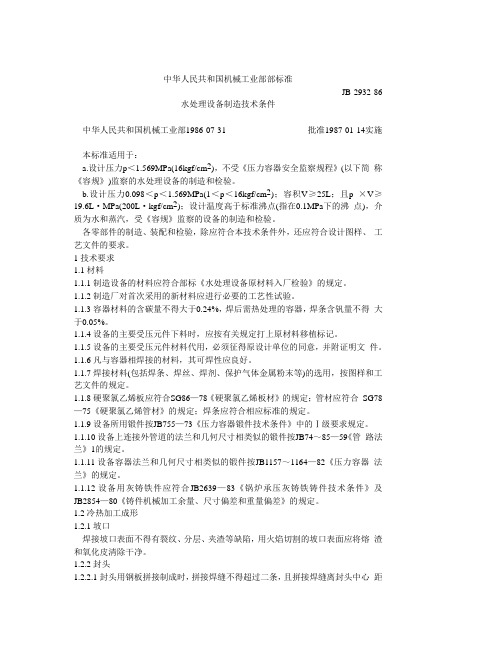
中华人民共和国机械工业部部标准JB-2932-86水处理设备制造技术条件中华人民共和国机械工业部1986-07-31 批准1987-01-14实施本标准适用于:a.设计压力p<1.569MPa(16kgf/cm2),不受《压力容器安全监察规程》(以下简称《容规》)监察的水处理设备的制造和检验。
b.设计压力0.098<p<1.569MPa(1<p<16kgf/cm2);容积V≥25L;且p ³V≥19.6L²MPa(200L²kgf/cm2);设计温度高于标准沸点(指在0.1MPa下的沸点),介质为水和蒸汽,受《容规》监察的设备的制造和检验。
各零部件的制造、装配和检验,除应符合本技术条件外,还应符合设计图样、工艺文件的要求。
1 技术要求1.1 材料1.1.1 制造设备的材料应符合部标《水处理设备原材料入厂检验》的规定。
1.1.2 制造厂对首次采用的新材料应进行必要的工艺性试验。
1.1.3 容器材料的含碳量不得大于0.24%,焊后需热处理的容器,焊条含钒量不得大于0.05%。
1.1.4 设备的主要受压元件下料时,应按有关规定打上原材料移植标记。
1.1.5 设备的主要受压元件材料代用,必须征得原设计单位的同意,并附证明文件。
1.1.6 凡与容器相焊接的材料,其可焊性应良好。
1.1.7 焊接材料(包括焊条、焊丝、焊剂、保护气体金属粉末等)的选用,按图样和工艺文件的规定。
1.1.8 硬聚氯乙烯板应符合SG86—78《硬聚氯乙烯板材》的规定;管材应符合SG78—75《硬聚氯乙烯管材》的规定;焊条应符合相应标准的规定。
1.1.9 设备所用锻件按JB755—73《压力容器锻件技术条件》中的Ⅰ级要求规定。
1.1.10 设备上连接外管道的法兰和几何尺寸相类似的锻件按JB74~85—59《管路法兰》1的规定。
1.1.11 设备容器法兰和几何尺寸相类似的锻件按JB1157~1164—82《压力容器法兰》的规定。
汽车螺栓拧紧力矩

有汽车螺栓拧紧力矩中华人民共和国机械工业部部标准QC/T 518—1999汽车用螺纹紧固件拧紧扭矩规范代替JB 3677—84本标准适用于碳素钢或合金钢制造的螺纹直径为6,20mm、6级精度以上的汽车用一般螺栓、螺钉、螺柱和螺母的紧固。
其螺纹尺寸及公差按GB 193 —81《普通螺纹直径与螺距系列》、GBI96一81《普通螺纹基本尺寸》和GB 197—81《普通螺纹公差与配合》标准的规定;螺栓、螺钉、螺柱和螺母机械性能、螺栓、螺钉、螺柱与螺母被拧入基体件强度级别的组合按GB 3098—82《紧固件机械性能》标准的规定,本标准不适用于承受交变载荷或加润滑剂装配的螺栓、螺钉、螺柱和螺母的紧固件,以及紧定螺钉和类似的不规定抗拉强度的螺纹紧固件。
1 汽车用螺纹紧固件拧紧扭矩1(1 机械性能为4.6级的螺栓、螺钉和螺柱,其拧紧扭矩按表1的规定。
1(2 机械性能为5.6级的螺栓、螺钉和螺柱,其拧紧扭矩按表2规定。
1(3 机械性能为8.8级的螺栓、螺钉和螺柱,其拧紧扭矩按表3规定。
1(4 机械性能为10.9级的螺栓和螺柱,其拧紧扭矩按表4规定。
附录A螺坟紧固件的拧紧扭矩(补充件)在拧紧螺母时、其拧紧扭矩M需要克服被旋合螺纹间的摩擦力矩和螺母与被联接件(或垫圈)支承面间的摩擦力矩,并使联接产生预紧力P0,它们的关系为要想得到规定的预紧力,应进行大量的试验求出拧紧扭矩系数的实际数值,通过以上的关系计算,把一定大小的扭矩施加到螺母上就能得到。
通过试验和数学分析得出,汽车用普通螺纹紧固件拧紧扭矩系数的平均值为0.284。
对于表1,4中未规定的各级机械性能的螺纹紧固件*的拧紧扭矩,可按(A2)、(A4)、(A5)经验公式计算确定。
附加说明:本标准由长春汽车研究所提出并归口。
本标准由长春汽车研究所负责起草。
本标准主要起草人王耀。
lycxgcs 2006-07-01 14:29 我有个表格。
螺栓强度级螺栓公称直径/mm6 8 10 12 14 16 18 20 22 24 27 30 36 42 48扭紧力矩/N.m4.64~5 10~12 20~25 35~44 54~69 88~108 118~147 167~206 225~284 294~370 441~519 529~666 882~1078 1372~1666 2058~24505.65~7 12~15 25~31 44~54 69~88 108~137 147~186 206~265 284~343 370~441 539~686 666~833 1098~1372 1705~2736 2334~25486.66~8 14~18 29~39 49~64 83~98 127~157 176~216 245~314 343~431 441~539 637~784 784~980 1323~1677 1960~2548 3087~38228.89~12 22~29 44~58 76~102 121~162 189~252 260~347 369~492 502~669638~850 933~1244 1267~1689 2214~2952 3540~4721 5311~7081 10.913~14 29~35 64~76 108~127 176~206 274~323 372~441 529~637 725~862 921~1098 1372~1617 1666~1960 2744~3283 4263~5096 6468~7742 12.9 15~20 37~50 74~88 128~171 204~273 319~425 489~565 622~830 847~1129 1096~1435 1574~2099 2138~2850 3736~4981 5974~7966 8962~11949 maf1971 2006-07-05 20:46 螺纹力矩标准为以螺栓强度的70%为标准计算的,值偏大,实际力矩主要与受力有关,均需计算.一般场合用标准也就是浪费点力气,但若是压力容器,预紧力太大则会使螺栓拉力太大而断裂.songwei 2006-07-10 09:50 通常规定,拧紧后螺纹联接件的预紧力不得超过其材料的屈服极限的80%对于一般联接用的钢制螺栓联接的预紧力,一般为:碳素钢制,0.6,0.7σ,A1;合金钢,0.5,0.6σSA1;扭矩T,0.2F0xd。
中华人民共和国机械工业部标准
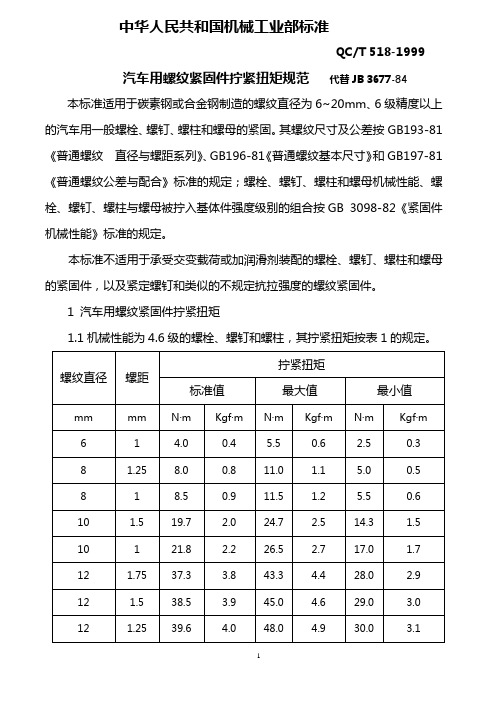
中华人民共和国机械工业部标准QC/T 518-1999 汽车用螺纹紧固件拧紧扭矩规范代替JB 3677-84本标准适用于碳素钢或合金钢制造的螺纹直径为6~20mm、6级精度以上的汽车用一般螺栓、螺钉、螺柱和螺母的紧固。
其螺纹尺寸及公差按GB193-81《普通螺纹直径与螺距系列》、GB196-81《普通螺纹基本尺寸》和GB197-81《普通螺纹公差与配合》标准的规定;螺栓、螺钉、螺柱和螺母机械性能、螺栓、螺钉、螺柱与螺母被拧入基体件强度级别的组合按GB 3098-82《紧固件机械性能》标准的规定。
本标准不适用于承受交变载荷或加润滑剂装配的螺栓、螺钉、螺柱和螺母的紧固件,以及紧定螺钉和类似的不规定抗拉强度的螺纹紧固件。
1 汽车用螺纹紧固件拧紧扭矩1.1机械性能为4.6级的螺栓、螺钉和螺柱,其拧紧扭矩按表1的规定。
1.2机械性能为5.6级的螺栓、螺钉和螺柱,其拧紧扭矩按表2规定。
1.3机械性能为8.8级的螺栓、螺钉和螺柱,其拧紧扭矩按表3规定。
1.4机械性能为10.9级的螺栓和螺柱,其拧紧扭矩按表4规定。
附录A螺纹紧固件的拧紧扭矩(补充件)在拧紧螺母时,其拧紧扭矩M需要克服被旋合螺纹间的摩擦力矩和螺母与被联接件(或垫圈)支承面间的摩擦力矩,并使联接产生预紧力,应进行大量的试验求出拧紧扭矩系数的实际数值,通过以上的关系计算,把一定大小的扭矩施加到螺母上就能达到。
M=KP0dx10-3〃〃〃〃〃〃〃〃〃〃〃〃〃〃〃〃[A1]式中:M---拧紧扭矩,N〃m;K---拧紧扭矩系数;P0---预紧力N;d---螺纹直径,mm。
通过试验和数学分析得出,汽车用普通螺纹紧固件拧紧扭矩系数的平均值为0.284。
对于表1-4中未规定的各级机械性能的螺纹紧固件的拧紧扭矩,可按(A2)、(A4)、(A5)经验公式计算确定。
螺纹紧固件最大拧紧扭矩为Mmax=0.170σs A S dx10-9〃〃〃〃〃〃〃〃〃〃〃〃〃〃〃〃[A2]式中:Mmax---最大拧紧扭矩,N〃m;σs---螺纹紧固件的屈服强度,N/mm2;A S------螺纹部分有效面积,mm2。
中华人民共和国第一机械工业部部标准

试 验 日期 : 室温 : 湿度 : 大气压:
℃ % mmHg
kc al/ h
标 10义 10'_ 准 散 热 量 Qn
H ,(7
风 阻 120
100 AP .
80 60
40
20
kcal/ m=hC
120
110 散
100 热 90 系
数 80 U
70
60
50
4 6 8 101 2 141 6 18 202 2 24 26k g/m's
. 壁必须 平整、光滑 ,各连接处必须 密封 ,不得漏气 。为了使 气流均匀稳 定 ,在散热器 的前后 风筒内 ,分 别设 置 b 招流 网及整流格。成品散热器及模型芯 子的风筒结 构分别见 图 3及图 40
z1巫W7
平托管
x 进 风
Hale Waihona Puke 干n.,D zw.co 地面
进风温 度计 r
—
岚阻侧最
> ID
> 2.S D
1标 0X 10} 准 散 热 量 Qn
::: 水困叭m m H,0 朋 60 40 20
致值
kcal/mphC 120 散 热 110 系 数
100
U 90 80
70 66' 50
水流f C,vk g/h
试验装置 796
试验者
图号
JB/T 2293- 1978
附录
1 整理计算时 ,所有的计算数据取 三位 有效 数字。 2 散热性能用水侧 散热量(Qw)进行计算 ,其正确度用风侧吸热量(Q,)进行验算。
79 1
Js/T2 293- 1978
加热 。加热水槽及热水 管道的外露部分必须隔热 。按所试 散热器的大小 ,水槽水容量为 。.5^-1m `,以保证 试验 时水温稳定 。 3.7 测量 风量用 的毕 托管装置在进风 集流器后的稳流段 内,毕托管轴应位 于风 道中心 ,与气流方 向的偏 斜度 不大于 500 3.8 风阻 的测定 点应在散热器前后 的风筒 的稳流段 内,且距散热器两侧各为 D。在每个测量 截面上装置 直径 为 5-8m m 的测压孔 ,测压孔应垂直于 风筒壁 面,并须平整、光滑,不得有突起和毛刺 。 3.9 水 阻的测定 点应在距 散热器进 、出水 口 100m m 内 ,测 压管必须垂 直于进 、出水管 ,其直径应 为 I- 5m m,测定 点处的管径等 于散 热器的进 、出水管管径 ,且管路不 得弯曲 ,个 别弯曲型进 、出水管 ,需单独进 行水 阻测量 。 3.10 进、出风温计的安装方式参见图 6,
QCT 566-1999 轿车的外部防护.
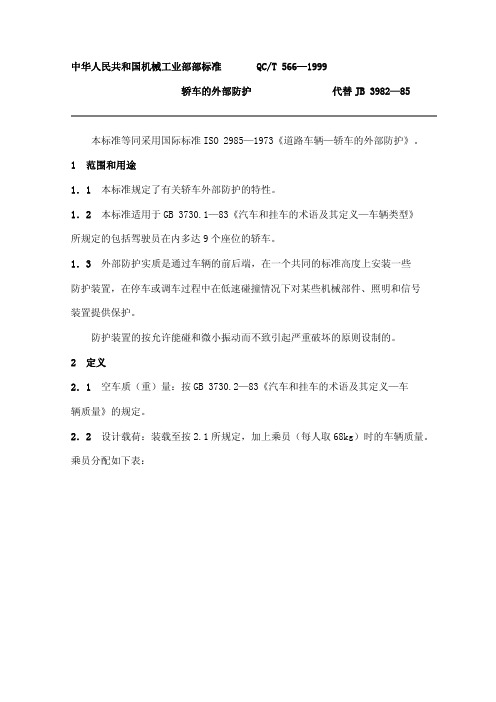
中华人民共和国机械工业部部标准 QC/T 566—1999轿车的外部防护 代替JB 3982—85本标准等同采用国际标准ISO 2985—1973《道路车辆—轿车的外部防护》。
1 范围和用途1.1 本标准规定了有关轿车外部防护的特性。
1.2 本标准适用于GB 3730.1—83《汽车和挂车的术语及其定义—车辆类型》所规定的包括驾驶员在内多达9个座位的轿车。
1.3 外部防护实质是通过车辆的前后端,在一个共同的标准高度上安装一些防护装置,在停车或调车过程中在低速碰撞情况下对某些机械部件、照明和信号装置提供保护。
防护装置的按允许能碰和微小振动而不致引起严重破坏的原则设制的。
2 定义2.1 空车质(重)量:按GB 3730.2—83《汽车和挂车的术语及其定义—车辆质量》的规定。
2.2 设计载荷:装载至按2.1所规定,加上乘员(每人取68kg)时的车辆质量。
乘员分配如下表:2.3 车辆角部:车辆与一个垂直平面接触的那部分,该垂直平面与车辆相切, 并与车辆的纵向对称平面成60°角。
2.4 标准高度:在空车质(重)量和设计载荷两种情况下的离地高度,在这高度上车辆应具有足够的防护装置。
此标准高度就是通过3.2条所述试验装置在基准线的水平面高度。
2.5 基准线:撞击突块的对称水平面与撞击装置本身的垂直平面A的交线(见图)。
3 试验条件3.1 总则3.1.1 车辆应停放在水平的硬实表面上。
3.1.2 两前轮平行于车辆的纵向对称平面。
3.1.3 各轮胎应按制造厂对规定装载条件所推荐的压力充气。
3.1.4 各制动器应放松,变速杆应处于空档位置。
3.1.5 外部照明和信号装置应能正常使用。
3.1.6 装备有液气,液力、空气悬架或按载荷情况自动调整高度装置的车辆,应按制造厂规定的正常行驶条件进行试验。
3.2 试验装置第4章规定的试验应采用具备下列条件特性的试验装置进行:3.2.1 试验装置的撞击表面应按图所示,其撞击突块由淬火钢材制成。
- 1、下载文档前请自行甄别文档内容的完整性,平台不提供额外的编辑、内容补充、找答案等附加服务。
- 2、"仅部分预览"的文档,不可在线预览部分如存在完整性等问题,可反馈申请退款(可完整预览的文档不适用该条件!)。
- 3、如文档侵犯您的权益,请联系客服反馈,我们会尽快为您处理(人工客服工作时间:9:00-18:30)。
中华人民共和国机械工业部部标准JB-2932-86水处理设备制造技术条件中华人民共和国机械工业部1986-07-31 批准1987-01-14实施本标准适用于:a.设计压力p<1.569MPa(16kgf/cm2),不受《压力容器安全监察规程》(以下简称《容规》)监察的水处理设备的制造和检验。
b.设计压力0.098<p<1.569MPa(1<p<16kgf/cm2);容积V≥25L;且p ×V≥19.6L·MPa(200L·kgf/cm2);设计温度高于标准沸点(指在0.1MPa下的沸点),介质为水和蒸汽,受《容规》监察的设备的制造和检验。
各零部件的制造、装配和检验,除应符合本技术条件外,还应符合设计图样、工艺文件的要求。
1 技术要求1.1 材料1.1.1 制造设备的材料应符合部标《水处理设备原材料入厂检验》的规定。
1.1.2 制造厂对首次采用的新材料应进行必要的工艺性试验。
1.1.3 容器材料的含碳量不得大于0.24%,焊后需热处理的容器,焊条含钒量不得大于0.05%。
1.1.4 设备的主要受压元件下料时,应按有关规定打上原材料移植标记。
1.1.5 设备的主要受压元件材料代用,必须征得原设计单位的同意,并附证明文件。
1.1.6 凡与容器相焊接的材料,其可焊性应良好。
1.1.7 焊接材料(包括焊条、焊丝、焊剂、保护气体金属粉末等)的选用,按图样和工艺文件的规定。
1.1.8 硬聚氯乙烯板应符合SG86—78《硬聚氯乙烯板材》的规定;管材应符合SG78—75《硬聚氯乙烯管材》的规定;焊条应符合相应标准的规定。
1.1.9 设备所用锻件按JB755—73《压力容器锻件技术条件》中的Ⅰ级要求规定。
1.1.10 设备上连接外管道的法兰和几何尺寸相类似的锻件按JB74~85—59《管路法兰》1的规定。
1.1.11 设备容器法兰和几何尺寸相类似的锻件按JB1157~1164—82《压力容器法兰》的规定。
1.1.12 设备用灰铸铁件应符合JB2639—83《锅炉承压灰铸铁铸件技术条件》及JB2854—80《铸件机械加工余量、尺寸偏差和重量偏差》的规定。
1.2 冷热加工成形1.2.1 坡口焊接坡口表面不得有裂纹、分层、夹渣等缺陷,用火焰切割的坡口表面应将熔渣和氧化皮清除干净。
1.2.2 封头1.2.2.1 封头用钢板拼接制成时,拼接焊缝不得超过二条,且拼接焊缝离封头中心距离应小于0.25D n,拼接板最小宽度应大于200mm(图1)。
1.2.2.2 封头由瓣片和顶圆板对接制成时,焊缝方向只允许是径向和环向的,径向焊缝之间最小距离应大于3S,且不小于100mm,中心顶圆板直径d应小于0.5D n,顶圆板由二块拼接时,焊缝应通过顶圆板中心(图2)。
1.2.2.3 椭圆形、碟形封头主要尺寸偏差按表1的规定(图3)。
图1图2图3图4表1mm表2mm1.2.2.4 椭圆形、碟形和折边锥形封头的最小壁厚不得小于图样厚度的90%。
当图样厚度大于40mm时,最小壁厚不得小于图样厚度的87%。
球形封头的最小壁厚不得小于图样厚度的85%。
1.2.2.5 椭圆形、碟形、折边锥形封头的直边部分上的纵向皱折深度不得大于1.5mm。
1.2.2.6 球壳或球形封头主要尺寸偏差按表2的规定(图4)。
1.2.3 筒节1.2.3.1 纵向焊缝条数见表3。
表31.2.3.2 两拼接纵向焊缝中心线间的弧长不小于300mm。
1.2.3.3 厚度相等的单层钢板纵焊缝的对口错边量(图5)b≤10%S,且不大于3mm. 1.2.3.4 厚度相等的复合钢板纵焊缝的对口错边量(图6)b≤10%S,且不大于2mm。
图5图6图7图81.2.3.5 对接纵焊缝处形成的棱角度E≤0.1S+2mm,且不大于5mm,用弦长等于16D n,且不小于300mm的内样板或外样板检查(图7)。
1.2.3.6 同一横截面上最大与最小直径之差,应不大于该截面直径的1%,且不大于25mm(图8),有开孔补强时应距补强圈边缘100mm以外的位置测量。
1.2.3.7 筒体的几何形状和尺寸偏差按表4的规定(图9)。
表4mm1.2.4 法兰1.2.4.1 管路法兰(或平盖)的加工按JB74~85—59《管路法兰》的规定。
1.2.4.2 受《容规》监察的设备的筒体法兰的加工按JB1157~1160—82《压力容器法兰》的规定。
图91.2.5 组装1.2.5.1 设备筒体可由数节对接而成,其中最短一节长度不得小于300mm。
1.2.5.2 厚度相等的钢板对接时,环向焊缝的对口错边量。
a.壁厚S≤6mm时,b≤25%S;b.壁厚6mm<S≤10mm时,b≤20%S;c.壁厚S>10mm时,b≤10%S+1mm,且不大于6mm(图10)。
1.2.5.3 厚度相等的复合钢板对接时,环向焊缝的对口错边量b≤10%,且不大于2mm(图11)。
图10图111.2.5.4 对接环焊缝处形成的棱角度E≤0.1S+2mm,且不大于5mm,用长度不小于300mm的检查尺检查(图12)。
1.2.5.5 厚度不相等的钢板对接时,当薄板厚度不大于10mm,且两板厚度差超过3mm;当薄板厚度大于10mm;且二板厚度差大于薄板厚度的30%或超过5mm时,则应将厚板边缘削薄,削薄长度L至少为削薄厚度b(厚板和薄板之差)的3倍,对接焊缝的对口错边量按第1.2.5.2款规定(图13)。
图12图131.2.5.6 当二板厚度差小于第1.2.5.6款规定的值时,则按第1.2.5.2款的规定,且焊缝的对口错边量b以较薄板厚度为基准确定。
在测量对口错边量时,不应计入钢板厚度的差值。
1.2.5.7 容器的组焊不应采用十字焊缝,组装对接时,相邻筒节间的纵缝及封头拼缝与相邻筒节的纵缝应错开,错开间距大于筒体厚度的3倍,且不小于100mm。
1.2.5.8 制造中应避免钢板表面的机械损伤,对深度大于0.5mm的尖锐伤痕应进行修磨,使其圆滑过渡,修磨处的深度不得超过钢板厚度的10%,且不大于2mm。
1.2.5.9 容器焊缝应尽量位于支座之处,设备内外件和筒体相焊接的焊缝,其边缘至筒体焊缝边缘距离应大于筒体厚度的3倍,且对于不受《容规》监察的设备应不小于30mm,受《容规》监察的设备不小于50mm。
图141.2.5.10 容器上凡被覆盖的焊缝,均应打磨至与母材齐平。
1.2.5.11 接管法兰螺栓孔不应和筒体主轴中心线重合,而应对称地分布在它的两侧,有特殊要求时应在图样上注明(图14)。
1.2.5.12 机械加工件表面的未注尺寸公差按GB1800~1804—79《公差与配合》规定的IT14级精度,非机械加工表面的未注尺寸公差按IT16级精度。
若未注公差尺寸为长度尺寸时,则长度尺寸公差按上述公差的 12 IT,1.3 开孔及装配1.3.1 容器焊缝上应尽量避免开孔如必须在焊缝上开孔,则不受《容规》监察的容器开孔周围不允许有缺陷存在。
受《容规》监察的容器被开孔中心两侧,各不少于 1.5倍开孔直径范围内的焊缝须经百分之百无损探伤。
1.3.2 在筒体或封头上开孔,开孔边缘与焊缝的距离不小于100mm。
1.3.3 当开孔有补强板时,板上应有一个M10的螺孔。
1.3.4 法兰面与主轴中心线的垂直度Δh不大于1%D w,且对于接管法兰面不大于3mm(图15a),对于筒体法兰不大于5mm(图15b)。
图151.3.5 90°弯头或三通、二法兰平面间的垂直度对于管子外径不大于108mm时,Δg 不大于1.5mm;当外径大于108mm时,Δg不大于2mm(图16)。
1.3.6 90°弯头或三通,其相对基准面至中心线的距离偏差为ΔL0-2mm(图17)。
1.3.7 装配时,当接管法兰螺栓孔直径为18mm时,其中心位置的偏移Δb不大于1.0mm;当螺栓孔直径大于18mm时,Δb不大于1.5mm(图18)。
图16图17图18图19图201.3.8 无人孔装置及焊接后无法进行内部清理的容器,在封头焊接之前,必须清除容器内的存水、电焊条、电焊药皮和铁屑等杂物。
1.3.9 设备内部的进水挡板、弓形多孔板和叠片式大水帽等集排水装置与筒体中心线的偏移不大于5mm,倾斜度为4mm,1.3.10支管中心线应垂直于母管中心线,其倾斜度和垂直度每米不大于3mm(图19)。
1.3.11 相邻二支管间的距离偏差为±2mm,任意二支管间的距离偏差不大于3mm。
1.3.12 除氧器内各种型式的散水槽应保持平直,散水槽的装配应保持水平,散水槽装配的平面度每米为4mm(图20)。
1.3.13 两散水槽(板)中心间的距离偏差为±1mm,任意二散水槽(板)中心间的距离偏差为±3mm(图21)。
1.3.14 散水托盘应保持平直,径向平面度每米为2mm,且总公差为5mm(图22)。
图21图22图23图241.3.15 散水托盘支承架应保持在同一水平面上,其平面度每米为2mm,且总公差为5mm(图23)。
1.3.16 接管和管夹的标高及方位偏差为±3mm(图24)。
1.3.17 内外接管伸出长度偏差为±3mm,其对筒体或封头的垂直度为1.5mm(图24)。
1.3.18 卧式容器鞍式支座的底板面到筒体中心高度偏差为δ0-6mm(图24)。
1.4 焊接和热处理1.4.1 水处理设备受压元件的施焊必须由考试合格的焊工承担,焊工考试遵照国家劳动总局关于《锅炉压力容器的焊工考试规则》进行。
1.4.2 水处理设备施焊前,应根据图样的技术要求以及施焊单位评定合格的焊接工艺,制订相应的焊接工艺规程,焊工必须严格遵守该规程。
1.4.3 施焊后,焊工应在焊缝附近的部位或按制造厂规定的部位打上焊工钢印。
1.4.4 凡施焊单位首次焊接的钢种、首先采用的焊接材料和焊接方法,以及改变已经评定合格的焊接工艺均应在容器施焊前进行焊接工艺评定,其评定要求按《容规》附件二的规定。
1.4.5 焊接接头基本型式和尺寸应参照GB985—89《手工电弧焊焊接接头的基本型式和尺寸》、GB986—80《埋弧焊焊接接头的基本型式和尺寸》的规定,或按制造厂的有关规定。
1.4.6 受《容规》监察的设备应按《容规》的规定。
制作焊接试板,试板要求、试样尺寸、取样部位、试验要求及评定标准均按JB1614—83《锅炉受压元件焊接接头机械性能检验方法》的规定。
当纵环焊缝焊接方法相同时,可只作纵缝试件一块。
1.4.7 焊缝内、外表面的外观应符合以下规定:a.焊缝和热影响区表面不得有裂纹、气孔、弧坑和夹渣等缺陷。
b.焊缝咬边深度不大于0.5mm,咬边连续长度不大于100mm,焊缝二侧咬边的总长不得超过该焊缝长度的10%。
c.角焊缝应有圆滑过渡至母材的几何形状。