工艺设计要点之反应器
化工设计-13 反应器
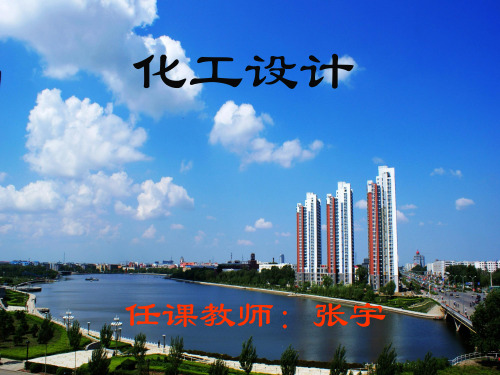
用途: 已知反应历程和平衡反应的反应方程式,
不考虑动力学可行性,计算同时达到化学 平衡和相平衡的结果。
REquil — 连接
REquil — 模型参数
REquil 模块有四组模型参数:
1、模型设定 (Specifications) 2、化学反应 (Reactions) 3、收敛 (Convergence)
△P代表选定组分 (selected) P的生成摩尔数; △A代表参照组分 (reference) A的消耗摩尔数; real 代表反应器内的实际情况; ideal 代表只有 A→P 一个反应发生时的情况。
RStoic — 示例(1)
甲烷与水蒸汽在镍催化剂下的转化反应为:
CH 4 2H2O CO2 4H2
原料气中甲烷与水蒸汽的摩尔比为14,流量为 100 kmol/hr。 若反应在恒压及等温条件下进行,系统总 压为0.1013 MPa,温度为 750 ℃,当反应器出 口处 CH4 转化率为 73% 时, CO2 和 H2 的产量是 多少?反应热负荷是多少?
RStoic — 示例(2)
反应和原料同示例 (1) ,若反应在恒压 及绝热条件下进行,系统总压为0.1013 MPa, 反应器进口温度为 950 ℃,当反应器出口处 CH4 转化率为 73% 时,反应器出口温度是多 少?
RYield — 产率
产率设置有四个选项: 1、组分产率 (Component yields) 2、组分映射 (Component mapping) 3、石油馏分表征 (Petro characterization) 4、用户子程序 (User subroutine)
RYield — 组分产率
RStoic — 化学反应
定义RStoic中进行的每一个化学反应的编 号、化学计量关系、产物生成速率或反应物转 化率。并指明计算多个反应的转化率时是否按 照串联反应方式计算。
化工厂装置中的反应器原理与设计要点

化工厂装置中的反应器原理与设计要点化工工业是现代工业的重要组成部分,而反应器作为化工厂装置中的核心设备,起着至关重要的作用。
反应器的原理和设计要点对于化工工业的发展和产品质量具有重要影响。
本文将探讨反应器的原理和设计要点,希望能够对相关领域的专业人士和学生有所帮助。
一、反应器的原理反应器是进行化学反应的装置,其原理主要包括反应动力学和传质过程。
反应动力学研究反应速率与反应物浓度之间的关系,以及反应速率与温度、压力等因素的关系。
传质过程则研究反应物在反应器中的传质现象,包括质量传递和热量传递。
在反应动力学方面,反应速率常常符合反应速率方程,该方程描述了反应速率与反应物浓度的关系。
在设计反应器时,需要根据反应速率方程确定反应物的投入量和反应时间,以达到预期的反应效果。
同时,反应速率还受到温度和压力等因素的影响,因此在设计反应器时需要考虑这些因素的控制。
在传质过程方面,反应物在反应器中的传质现象对反应速率和反应效果同样具有重要影响。
传质过程包括质量传递和热量传递,其中质量传递主要指反应物在相界面上的传递,而热量传递则指反应过程中的热量交换。
在设计反应器时,需要考虑传质过程的效率和速率,以确保反应物能够充分接触并发生反应。
二、反应器的设计要点1. 反应器的选择:根据反应物的性质和反应条件选择合适的反应器类型。
常见的反应器类型包括批式反应器、连续流动反应器和固定床反应器等。
不同类型的反应器适用于不同的反应条件和反应物种类,因此在设计反应器时需要充分考虑这些因素。
2. 反应器的尺寸和比例:反应器的尺寸和比例对于反应效果和生产能力具有重要影响。
反应器的尺寸需要根据反应物的投入量和反应速率来确定,同时还需要考虑传质过程的效率和速率。
反应器的比例则需要根据反应器的类型和工艺要求来确定,以确保反应物能够充分接触并发生反应。
3. 反应器的控制系统:反应器的控制系统对于反应过程的稳定性和安全性至关重要。
控制系统包括温度、压力和反应物投入量等参数的监测和调节。
化学工程中的反应器与工艺设计

化学工程中的反应器与工艺设计在化学工程中,反应器是一个关键的装置,用于制造化学物质和药品。
由于各种不同的物理和化学反应条件的影响,反应器的设计非常复杂。
化学工程师需要确保反应器能够正确地执行所需的反应,从而在制造过程中获得最高的效率和最佳的质量。
一、反应器的类型反应器的类型包括batch反应器、连续流反应器和半连续流反应器。
Batch反应器是将所有原料添加到反应器中,进行一次完整的反应,然后将产物分离出来。
连续流反应器是通过将原料连续添加到反应器中,以获得一个流通的反应。
半连续流反应器则将实验室规模的batch反应器与连续流反应器的设计结合起来,以使其具有一定程度的自动化功能。
二、反应器选择的重要因素反应器的设计与选择需要考虑多种条件,包括反应物的性质和浓度、反应物的读数和速率、反应器的能力和效率、反应的催化剂和溶剂、反应器的设计和尺寸、反应器的材料和使用环境等。
此外,重要的因素还包括反应器的成本、维护和操作复杂性、反应对环境的影响和群体的安全性。
因此,反应器的选择需要考虑到应用的需求、成本效益、环境安全和风险管理。
三、反应器的设计要素在反应器的设计中,需要考虑多种因素。
例如:反应器的材料和形状、搅拌器和加热/冷却设备、反应器的容积和形状、管道和进出口设备和反应器的控制系统。
在考虑反应器的材料时,需要选择对所需反应物质质量和反应物质性质不敏感的材料。
在设定反应器的搅拌器和加热/冷却设备时,需要根据反应动力学和反应物质性质来优化设计。
反应器的容积和形状也需要根据应用来优化,以确保反应物质能够充分反应,而不会因为催化剂过多而造成浪费。
管道和进出口设备需要根据应用来优化,以确保反应物能够快速和有效地流过反应器。
控制系统可以自动调整反应器的参数以保证反应的佳效果,从而在生产多种不同的化学物质时降低成本并提高质量。
四、反应器的工艺设计反应器的工艺设计包括两个部分:物理设计和化学设计。
物理设计需要考虑反应器的结构、框架、埋地设备、运输布局,以及其他相关和次要设备等。
第六章_固定床反应器的工艺设计

第六章_固定床反应器的工艺设计固定床反应器是一种广泛应用于化工领域的反应设备,其工艺设计的主要目的是在满足反应物转化率和产品选择性的同时,考虑到反应器的稳定性、可操作性和经济性。
本文将从固定床反应器的工艺选择、反应器尺寸设计和操作条件优化三个方面进行详细讨论。
首先,在固定床反应器的工艺选择中,需要考虑反应物质的特性以及反应过程的要求。
例如,对于多相反应系统,可选择固液、固气或固液气等不同形式的反应器。
对于固液反应系统,通常采用固定床(如活性炭床)作为催化剂载体,而对于固气反应系统,常使用填充物(如陶瓷珠)来提供大表面积。
此外,还需要考虑反应物料的物理性质,如粘度、密度和颗粒大小等,以确定反应器的类型和结构。
其次,在固定床反应器尺寸设计中,主要考虑的是反应器的长径比、催化剂的活性、反应器的有效体积等因素。
反应器的长径比是一个重要的设计参数,过大的长径比会导致反应物料的流速过小,影响转化率;过小的长径比则会增加压力损失和催化剂层的温度梯度。
催化剂的活性直接影响反应速率,一般需要选择活性高、稳定性好的催化剂。
反应器的有效体积要足够大,以保证反应物集流时间足够,从而提高转化率。
最后,在操作条件优化方面,需要考虑反应温度、压力和流速等参数。
反应温度会直接影响反应速率和选择性,一般需要根据催化剂的特性和反应动力学进行调整。
反应压力主要考虑固定床压降和反应平衡的影响,需要在考虑反应速率和选择性的同时,保持固定床的稳定性。
流速则涉及反应物料的传质和传热问题,需要通过实验和模拟计算等方法进行优化。
综上所述,在固定床反应器的工艺设计中,需要综合考虑反应物质的特性、反应器尺寸和操作条件等因素,以达到高效、稳定、经济的反应过程。
在实际工程应用中,还需要结合实际生产中的具体要求和限制条件,进行合理的优化设计。
通过合理的工艺设计,可以提高产品的转化率和选择性,降低生产成本,提高生产效益。
化工工艺中的反应器设计原理

化工工艺中的反应器设计原理引言在化工领域中,反应器是实施化学反应的关键设备。
反应器的设计原理直接影响反应的效率、产品质量以及能源消耗等方面。
本文将从反应器的类型、反应动力学、传热与传质以及反应器的尺度放大等方面,探讨化工工艺中的反应器设计原理。
一、反应器的类型反应器的类型多种多样,常见的包括批量反应器、连续流动反应器以及半批量反应器等。
批量反应器适用于小规模生产和实验室研究,连续流动反应器适用于大规模连续生产,而半批量反应器则结合了两者的优点。
不同类型的反应器在设计原理上存在差异,需要根据具体情况选择合适的类型。
二、反应动力学反应动力学研究反应速率与反应物浓度、温度、压力等因素之间的关系。
了解反应的动力学特性对反应器的设计至关重要。
在反应动力学的基础上,可以确定反应的最佳温度、反应物的进料浓度以及反应器的体积等参数,从而提高反应效率和产品质量。
三、传热与传质在反应器中,传热与传质是不可忽视的因素。
传热与传质的效果直接影响反应速率和反应物的分布。
常用的传热方式包括对流传热、辐射传热和传导传热,而传质则通过扩散和对流等方式进行。
在反应器设计中,需要考虑传热与传质的方式和效果,选择合适的传热与传质设备,以提高反应的效率和产物的纯度。
四、反应器的尺度放大从实验室到工业生产,反应器的尺度放大是一个重要的过程。
在尺度放大过程中,需要考虑反应器的动力学特性、传热与传质效果以及设备的可行性等因素。
合理的尺度放大设计可以保证反应器在大规模生产中的稳定性和效率。
五、反应器的安全性设计反应器的安全性设计是化工工艺中的重要环节。
在设计中,需要考虑反应器的压力、温度、反应物的性质以及可能的副反应等因素,以确保反应器的运行安全。
采用合适的安全措施,如压力释放装置、温度控制装置和反应物泄漏检测装置等,可以有效降低事故风险。
六、反应器的优化设计反应器的优化设计旨在提高反应效率、降低能源消耗和改善产品质量。
常用的优化方法包括反应条件的调整、催化剂的选择以及反应器结构的优化等。
连续化反应器及工艺设计
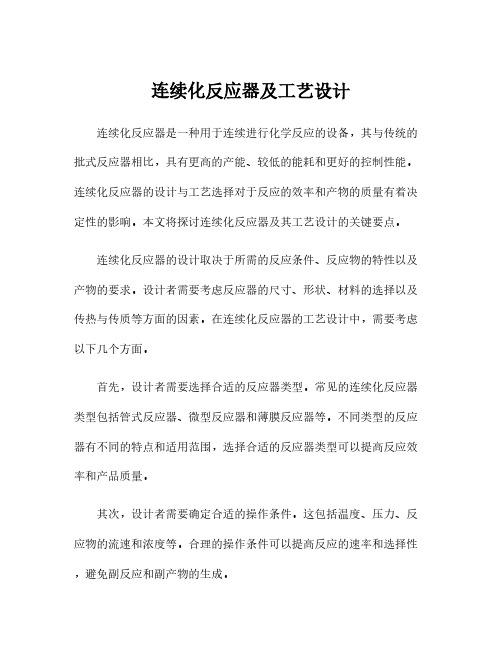
连续化反应器及工艺设计连续化反应器是一种用于连续进行化学反应的设备,其与传统的批式反应器相比,具有更高的产能、较低的能耗和更好的控制性能。
连续化反应器的设计与工艺选择对于反应的效率和产物的质量有着决定性的影响。
本文将探讨连续化反应器及其工艺设计的关键要点。
连续化反应器的设计取决于所需的反应条件、反应物的特性以及产物的要求。
设计者需要考虑反应器的尺寸、形状、材料的选择以及传热与传质等方面的因素。
在连续化反应器的工艺设计中,需要考虑以下几个方面。
首先,设计者需要选择合适的反应器类型。
常见的连续化反应器类型包括管式反应器、微型反应器和薄膜反应器等。
不同类型的反应器有不同的特点和适用范围,选择合适的反应器类型可以提高反应效率和产品质量。
其次,设计者需要确定合适的操作条件。
这包括温度、压力、反应物的流速和浓度等。
合理的操作条件可以提高反应的速率和选择性,避免副反应和副产物的生成。
第三,设计者需要考虑反应器的传热与传质性能。
连续化反应器通常需要提供良好的传热条件,以保持反应物在适宜的温度范围内进行反应。
传质性能的优化可以提高反应物的溶解度和反应的速率。
第四,设计者需要选择适当的催化剂或催化剂载体。
催化剂在化学反应中起到催化作用,可以加快反应速率和提高选择性。
选择合适的催化剂和催化剂载体可以改善连续化反应器的性能。
最后,设计者还需要考虑反应器的控制策略和安全性。
连续化反应器需要实现对温度、压力、流量和浓度等参数的精确控制。
同时,反应器的安全性也是设计者需要重视的方面,包括防止反应失控、爆炸和环境污染等问题。
总之,连续化反应器及其工艺设计是一项复杂的工程任务。
设计者需要综合考虑多个因素,并进行合理的选择和优化。
通过合理的设计和工艺控制,连续化反应器可以实现高效、节能、安全和环保的化学反应过程。
化学工艺中的反应器设计与运行优化

化学工艺中的反应器设计与运行优化在化学工艺中,反应器设计与运行优化是非常重要的环节。
反应器是化学反应进行的场所,反应器的设计和运行质量直接关系到反应的效果和产品质量。
因此,在化学工艺中,反应器设计和运行需要特别重视。
一、反应器设计的重要性反应器设计是决定反应速率、选择性、收率以及产物成分和结构的关键因素。
好的反应器设计可以提高反应速率,增加反应废物的再利用率,减少反应废物的污染,提高反应的选择性和收率,保证生产中产物的质量。
反应器的设计需要考虑多种因素,例如反应废物的产生与再利用,催化剂的选择和使用,反应物的浓度,反应器的温度和压力等等。
这些因素的合理考虑和设计可以提高反应的效率和产物的质量,降低反应的能耗和废物的排放。
二、反应器运行的重要性在反应器运行中,需要考虑反应废物的处理,产品的分离、纯化和质量控制,以及反应率的控制和稳定性。
反应器的运行关系到反应的效果和产物的质量。
反应器的运行需要考虑多种因素,例如反应废物的处理技术,反应器的加热、冷却、搅拌和控制系统,产品的分离、纯化和质量控制技术等等。
这些技术的合理运用和优化可以提高反应的效率和产物的质量,降低能源的消耗和废物的排放。
三、反应器设计和运行的优化反应器设计和运行的优化需要考虑多种因素,并且需要我们从反应的整个过程中进行科学分析和仔细研究。
反应器设计的优化需要从反应器结构、催化剂的选择、反应器温度和压力的调节、反应器控制系统的优化等角度进行考虑和研究。
例如我们可以考虑采用多级反应器、流化床反应器、手性催化剂等方式来提高反应效率和产物的选择性。
同时可以考虑采用先进的反应器控制技术,例如模型预测控制和模糊控制等方式来提高反应器的稳定性和控制质量。
反应器运行的优化需要从反应器的控制程序、加热、冷却、搅拌等方面入手。
我们可以考虑采用优化化反应器运行程序、采用优化加热、冷却、搅拌等方式来提高反应器的效率和稳定性。
同时可以考虑采用先进的质量控制技术,例如在线反应检测监测和质量分析技术,保证生产过程的质量和稳定性。
连续化反应器及工艺设计

连续化反应器及工艺设计
连续化反应器是一种在工业生产过程中被广泛应用的化学反应器。
该反应器可以实现连续流动的反应物料。
与批量反应器相比,连续化反应器具有许多优点,如反应物料的持续供应、高反应速率、较低的能量消耗和较小的设备占地面积等。
在连续化反应器的工艺设计中,一般需要考虑以下几个方面:
1. 反应物料的选择:根据反应的性质和要求,选择合适的反应物料,包括催化剂、溶剂和辅助剂等。
2. 反应器的类型:根据反应过程的要求,选择适合的反应器类型,如管式反应器、塔式反应器、微反应器等。
3. 反应温度的控制:根据反应物料的热力学性质和反应速率,确定合适的反应温度,以实现较高的反应速率和较好的选择性。
4. 反应物料的流动方式:选择合适的流动方式,如稠化流动、湍流流动或混合流动等,以提高反应物料的混合程度和传质效果。
5. 反应物料的控制与分离:在连续化反应器中,需要考虑反应物料的控制和分离,以实现高纯度的产物和高回收率。
6. 反应器的尺寸与可扩展性:根据反应物料的产量要求和生产规模,确定合适的反应器尺寸,同时考虑反应器的可扩展性,以适应未来的生产需求。
总之,连续化反应器及工艺设计需要综合考虑反应物料的选择、反应器类型、反应温度控制、反应物料的流动方式、控制与分离、尺寸与可扩展性等方面的因素,以最大程度地实现反应过程的高效、高选择性和高产量。
化工工艺中的高效反应器设计与优化

化工工艺中的高效反应器设计与优化在化工工艺中,反应器是至关重要的设备,它在化学反应中起到催化和加热的作用,决定了反应的效率和产量。
因此,设计和优化高效的反应器对于提高化工工艺的经济效益具有重要意义。
本文将探讨化工工艺中的高效反应器设计与优化的相关内容。
一、反应器的分类与特点根据反应物与催化剂的接触方式和物料流动情况,反应器可以分为多种类型,如批量反应器、连续流动反应器、固定床反应器等。
每种反应器都有其独特的特点和适用范围。
批量反应器适用于小规模的生产和反应物质量要求较高的情况,其反应过程需要在一定时间内,将反应物料全部进料、反应、冷却、卸料。
连续流动反应器适用于大规模生产和连续供应的需求,它的特点是反应物料的连续进出,反应过程的控制更加稳定。
固定床反应器主要用于固体催化剂的反应,其催化剂通常填充在固定的反应器床层中,反应物料经过催化剂层进行反应。
二、高效反应器设计原则1. 催化剂选择与催化活性在反应器设计中,催化剂的选择对反应效率有着重要影响。
催化剂应具备高度的活性、稳定性和选择性,以满足所需的反应过程。
此外,催化剂的形态结构也对反应物质的接触和扩散起到重要作用,设计反应器时需要考虑催化剂的颗粒大小、形状和分布等因素。
2. 反应器的温度和压力控制温度和压力是控制反应速率和选择性的重要因素。
合理的温度和压力控制可以提高反应速率和避免副反应的发生。
在反应器设计中,应根据反应物的性质和需要的反应条件,设定适当的温度和压力范围,并采取相应的措施进行控制。
3. 反应物料的混合和传质反应物料的混合和传质对反应器的效率和产率起着至关重要的作用。
在设计反应器时,可以采用物料的循环、搅拌或加入填料等方式,促进反应物料的混合和传质,提高反应效果。
4. 反应器的流体力学设计反应器的流体力学设计是确保反应物料在反应过程中能够充分接触、扩散和混合的关键。
反应器内部的结构设计和流道构造应该合理,以保证反应物料的流动和传递过程的顺利进行。
IC反应器构造及设计要点

IC反应器构造及设计要点IC(集成电路)反应器是一种常见的电子元器件,用于控制和管理电路中的电流和信号传输。
在设计和构造IC反应器时,有一些关键要点需要注意。
本文将介绍IC反应器的构造和设计要点。
一、IC反应器的构造IC反应器的构造由以下几个主要组成部分组成:1. 电路基板:IC反应器通常安装在电路基板上。
电路基板是一块由绝缘材料制成的基座,上面有导线和连接点,用于安装和连接IC反应器的其他部件。
2. 元件:IC反应器包含了各种电子元件,如电容器、电阻器、电感器等。
这些元件用于调节和控制电路中的电流和信号传输,以满足特定的电路需求。
3. 焊接点:IC反应器上的元件通常通过焊接点固定在电路基板上。
焊接点是将元件连接到电路基板上的金属接头,通过焊接工艺将元件与电路基板牢固地连接在一起。
二、IC反应器的设计要点在设计IC反应器时,需要考虑以下几个关键要点:1. 尺寸和布局:IC反应器应根据电路的尺寸和布局进行设计。
尺寸应足够小,以便于安装在电路中,并满足其他组件的空间需求。
布局应合理,以便于各个元件之间的连接和电路的正常运行。
2. 热管理:IC反应器在工作过程中会产生一定的热量。
因此,设计中需要考虑热管理,以确保IC反应器在长时间工作时不过热。
可以采用散热片、风扇等散热设备来降低温度,并保持IC反应器的正常工作温度范围。
3. 电路保护:IC反应器所处的电路环境可能存在各种电压波动、电磁干扰等问题。
因此,在设计IC反应器时,需要考虑电路保护措施,以保护IC反应器免受电路环境的影响。
可以采用电压稳定器、滤波器等保护设备,以确保IC反应器的正常工作和寿命。
4. 电路性能:IC反应器的设计还需要考虑电路的性能要求。
根据电路的需求,选择合适的电容器、电阻器、电感器等元件,并进行合理的布局和连接,以确保电路具有良好的稳定性、可靠性和性能。
总结:IC反应器的构造和设计要点涉及电路的构成和组件选择、尺寸和布局、热管理、电路保护以及电路性能等方面。
固定床反应器的工艺设计

固定床反应器的工艺设计1. 引言固定床反应器是一种常见的化工设备,广泛应用于化学工业中的各种反应过程中。
它由一个固定的催化剂床和一个通过床上空隙流动的气体或液体组成。
通过适当的设计和调节,固定床反应器可以实现高效的反应转化率和产出。
本文将介绍固定床反应器的工艺设计,包括反应器的结构、催化剂选择、反应条件等方面的内容。
2. 反应器的结构固定床反应器一般由反应器本体、催化剂床层、进出料口、反应气体或液体的流动通道等组成。
其中,反应器本体一般采用合适的材料制成,以承受反应过程中的温度和压力。
催化剂床层通常由多层的填料或颗粒催化剂组成,以提供反应活性面积和流动通道。
为了实现高效的反应,固定床反应器通常还配备有预热器、冷却器、再生器等附属设备,以控制反应温度、催化剂活性和产物的分离等。
3. 催化剂的选择催化剂是固定床反应器中实现化学反应的关键组件。
在选择催化剂时,需要考虑反应的性质、反应温度和压力、催化剂的稳定性和活性等因素。
常见的催化剂包括金属催化剂、氧化物催化剂、酸碱催化剂等。
选择合适的催化剂可以提高反应的转化率和选择性,降低反应温度和压力,减少副反应和催化剂失活等问题。
4. 反应条件的确定反应条件的确定是固定床反应器工艺设计的重要环节。
反应条件包括温度、压力、反应物浓度、催化剂负荷量等因素。
在确定反应温度时,需要考虑反应的热力学平衡和动力学要求。
过高的温度可能导致副反应的发生和催化剂失活,而过低的温度则可能使反应速率过慢。
压力的选择取决于反应物的状态和反应的热力学平衡。
在固定床反应器中,通常会通过控制进料流量和床层压降来维持适当的压力。
反应物浓度对反应速率和选择性有直接影响。
合理选择反应物浓度可以提高反应转化率和产物选择性。
催化剂负荷量的确定需要考虑催化剂的活性和催化剂床层的透气性。
过高的催化剂负荷量可能导致流动阻力加大,而过低的负荷量则可能使反应活性降低。
5. 反应器的优化和改进固定床反应器的工艺设计是一个复杂的过程,通常需要通过试验和模拟来进行优化和改进。
第六章固定床反应器的工艺设计

第六章固定床反应器的工艺设计固定床反应器是一种常见的反应器类型,广泛应用于化工、石油化工等领域。
在固定床反应器的工艺设计中,需要考虑反应器的尺寸、材料选择、催化剂的选择和补给方式等因素。
本文将从这些方面介绍固定床反应器的工艺设计。
固定床反应器的尺寸设计包括反应器的长度、直径和体积等方面。
尺寸的选择应该根据反应物的性质、反应速率以及保持良好的传质和传热效果来确定。
通常情况下,反应器的直径在0.3-2米之间,体积在0.1-1000立方米之间。
反应器的长度一般要大于反应床的一层,以保证反应物在床层中有足够的停留时间和接触时间。
在材料的选择上,固定床反应器应选用耐高温、耐腐蚀和具有良好物理性能的材料。
常见的材料有不锈钢、镍基合金、钛合金等。
尤其对于高温反应和腐蚀性反应,选择合适的材料对保证反应器的使用寿命和安全性非常重要。
催化剂的选择对于固定床反应器的工艺设计来说也是至关重要的。
催化剂的性质直接影响着反应速率和产品选择性。
选用合适的催化剂可以提高反应效率和产物纯度。
常见的催化剂有金属催化剂、氧化物催化剂、分子筛催化剂等。
催化剂的选择要综合考虑反应物性质、反应条件以及经济因素。
对于固定床反应器的补给方式,常见的有逆流填料法、上升流填料法和下降流填料法等。
逆流填料法是指反应物和催化剂的进气方向相反,有利于反应物的分散和接触。
上升流填料法是指反应物和催化剂沿床层一同向上流动,适用于液相反应和气相-液相反应。
下降流填料法是指反应物和催化剂沿床层一同向下流动,适用于气相反应。
补给方式的选择要根据反应物的性质和反应条件来确定,以获得最佳的反应效果。
固定床反应器的工艺设计还需要考虑反应器的加热和冷却方式。
一般情况下,可以通过外部加热和冷却设备,如蒸汽、冷却水等来实现反应器的加热和冷却。
加热方式有直接加热和间接加热两种。
直接加热是指将加热介质(如蒸汽)直接送入反应器中进行加热,适用于高温反应。
间接加热是指通过换热器将加热介质与反应物进行热交换,适用于低温反应。
化学反应器的设计与控制

化学反应器的设计与控制一、引言化学反应器是化学反应工艺中最重要的部分之一,其设计与控制直接影响到反应的效率和产品的质量。
本文将从化学反应器的设计和控制两个方面进行讨论,以便更好地理解化学反应器的运作原理和调控方法。
二、化学反应器的设计化学反应器的设计是制造工艺中的首要环节之一。
设计阶段的失败可能导致生产线的整个停滞。
因此,在设计化学反应器时,需要考虑许多因素,如反应类型、反应条件和流体力学特性等。
下面将分别阐述这些因素并说明其设计中的重要性。
1. 反应类型在计划化学反应器时,应根据所需的反应类型选择适当的反应器。
例如,在发生氧化反应的情况下,应选择加热的自动加压反应器。
另一方面,友好环境反应可能需要较小的反应罐以减少生化风险。
因此确保选择适当的反应器类型是提交一个优秀反应器设计规划的重要组元。
2. 反应条件反应条件对化学反应器设计也极为重要。
这包括反应温度、反应压力和反应气相和液相之间的不同。
这些因素是影响反应器的操作因素,会生产不润滑环境之间的化学相互作用,并直接影响反应速率和产物质量。
3. 流体力学特性流体力学特性是决定化学反应器是否符合可行性的重要因素之一,相关特性包括相对粘度、气体液体体积流率等。
这些特性决定装置内部流体运动的性质和程度。
方案选择合理的搅拌强度和粘度范围都有助于使化学反应器稳定运行,从而避免冲击和不均匀现象。
三、化学反应器的控制一旦设计完成,化学反应器的控制则是生产化工反应的下一阶段。
反应过程中最重要的要素是实时监控,这种监测可以通过各种方法实现,包括自动化控制系统、传感器、控制算法和数据分析等。
下面将对每个方面展开讨论。
1. 自动化控制系统自动化控制系统是一套用于监控和控制化学反应器的计算机程序。
该程序自动采集并处理反应器数据,使系统能够对反应物添加量、温度、压力、搅拌率等参数进行调整。
系统可逐步开发以满足化学反应器控制要求。
2. 传感器传感器是化学反应器控制的重要组成部分,一般被用于测量参数从而实现测量数据的传输和分析。
化工工艺设计的要点探析
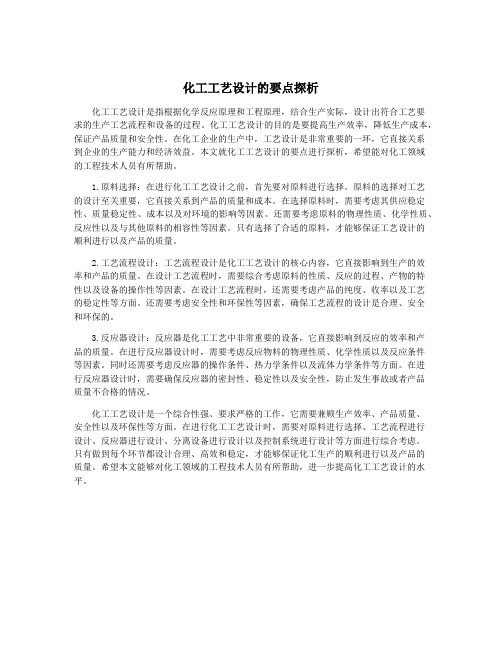
化工工艺设计的要点探析化工工艺设计是指根据化学反应原理和工程原理,结合生产实际,设计出符合工艺要求的生产工艺流程和设备的过程。
化工工艺设计的目的是要提高生产效率,降低生产成本,保证产品质量和安全性。
在化工企业的生产中,工艺设计是非常重要的一环,它直接关系到企业的生产能力和经济效益。
本文就化工工艺设计的要点进行探析,希望能对化工领域的工程技术人员有所帮助。
1.原料选择:在进行化工工艺设计之前,首先要对原料进行选择。
原料的选择对工艺的设计至关重要,它直接关系到产品的质量和成本。
在选择原料时,需要考虑其供应稳定性、质量稳定性、成本以及对环境的影响等因素。
还需要考虑原料的物理性质、化学性质、反应性以及与其他原料的相容性等因素。
只有选择了合适的原料,才能够保证工艺设计的顺利进行以及产品的质量。
2.工艺流程设计:工艺流程设计是化工工艺设计的核心内容,它直接影响到生产的效率和产品的质量。
在设计工艺流程时,需要综合考虑原料的性质、反应的过程、产物的特性以及设备的操作性等因素。
在设计工艺流程时,还需要考虑产品的纯度、收率以及工艺的稳定性等方面。
还需要考虑安全性和环保性等因素,确保工艺流程的设计是合理、安全和环保的。
3.反应器设计:反应器是化工工艺中非常重要的设备,它直接影响到反应的效率和产品的质量。
在进行反应器设计时,需要考虑反应物料的物理性质、化学性质以及反应条件等因素。
同时还需要考虑反应器的操作条件、热力学条件以及流体力学条件等方面。
在进行反应器设计时,需要确保反应器的密封性、稳定性以及安全性,防止发生事故或者产品质量不合格的情况。
化工工艺设计是一个综合性强、要求严格的工作,它需要兼顾生产效率、产品质量、安全性以及环保性等方面。
在进行化工工艺设计时,需要对原料进行选择、工艺流程进行设计、反应器进行设计、分离设备进行设计以及控制系统进行设计等方面进行综合考虑。
只有做到每个环节都设计合理、高效和稳定,才能够保证化工生产的顺利进行以及产品的质量。
反应器制造工艺方案
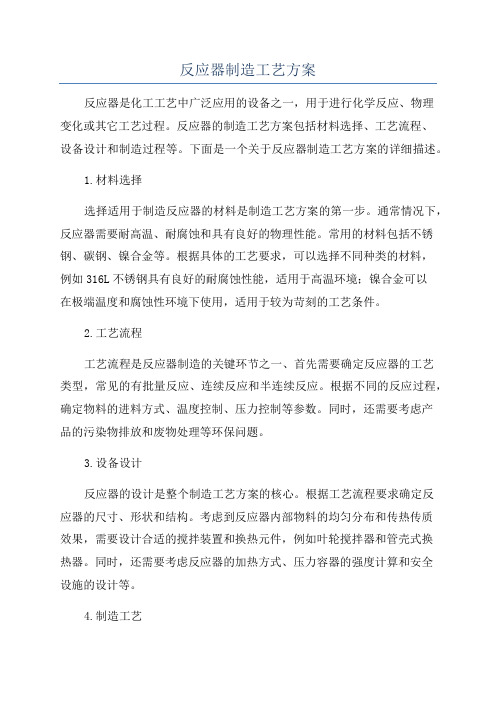
反应器制造工艺方案反应器是化工工艺中广泛应用的设备之一,用于进行化学反应、物理变化或其它工艺过程。
反应器的制造工艺方案包括材料选择、工艺流程、设备设计和制造过程等。
下面是一个关于反应器制造工艺方案的详细描述。
1.材料选择选择适用于制造反应器的材料是制造工艺方案的第一步。
通常情况下,反应器需要耐高温、耐腐蚀和具有良好的物理性能。
常用的材料包括不锈钢、碳钢、镍合金等。
根据具体的工艺要求,可以选择不同种类的材料,例如316L不锈钢具有良好的耐腐蚀性能,适用于高温环境;镍合金可以在极端温度和腐蚀性环境下使用,适用于较为苛刻的工艺条件。
2.工艺流程工艺流程是反应器制造的关键环节之一、首先需要确定反应器的工艺类型,常见的有批量反应、连续反应和半连续反应。
根据不同的反应过程,确定物料的进料方式、温度控制、压力控制等参数。
同时,还需要考虑产品的污染物排放和废物处理等环保问题。
3.设备设计反应器的设计是整个制造工艺方案的核心。
根据工艺流程要求确定反应器的尺寸、形状和结构。
考虑到反应器内部物料的均匀分布和传热传质效果,需要设计合适的搅拌装置和换热元件,例如叶轮搅拌器和管壳式换热器。
同时,还需要考虑反应器的加热方式、压力容器的强度计算和安全设施的设计等。
4.制造工艺制造反应器的过程中需要遵循一定的制造工艺。
首先需要对所选择的材料进行切割、加工和焊接等工艺。
随后进行材料的弯曲、成型和冷加工等加工操作。
在制造过程中需要进行严格的尺寸和质量控制,保证反应器的几何形状和内部结构的精度。
此外,还需要进行材料的表面处理,例如腐蚀处理和喷涂防腐等。
5.质量控制在反应器制造的整个过程中,质量控制是非常重要的。
通过严格的质量控制,可以保证反应器的使用安全和性能稳定。
质量控制包括原材料的检验、加工过程的控制、成品的检测和性能测试等。
常见的质量控制方法有材料化学成分分析、力学性能测试和无损检测等。
总结起来,反应器制造工艺方案涵盖了材料选择、工艺流程、设备设计和制造过程等多个方面,需要综合考虑反应器的工艺要求、使用环境和安全性能。
化工工艺中的反应器设计与生产流程
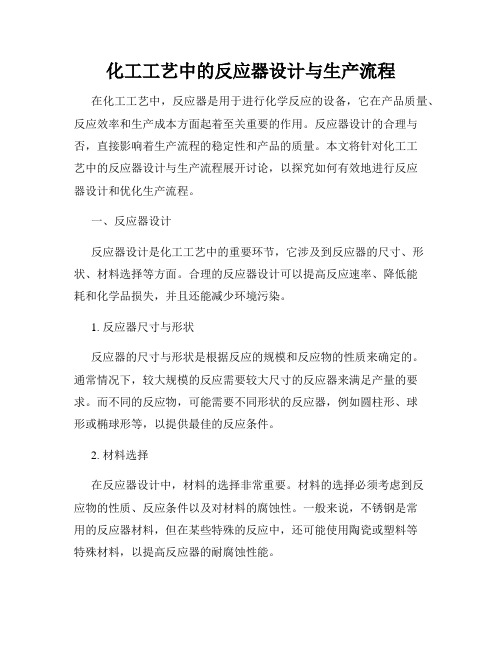
化工工艺中的反应器设计与生产流程在化工工艺中,反应器是用于进行化学反应的设备,它在产品质量、反应效率和生产成本方面起着至关重要的作用。
反应器设计的合理与否,直接影响着生产流程的稳定性和产品的质量。
本文将针对化工工艺中的反应器设计与生产流程展开讨论,以探究如何有效地进行反应器设计和优化生产流程。
一、反应器设计反应器设计是化工工艺中的重要环节,它涉及到反应器的尺寸、形状、材料选择等方面。
合理的反应器设计可以提高反应速率、降低能耗和化学品损失,并且还能减少环境污染。
1. 反应器尺寸与形状反应器的尺寸与形状是根据反应的规模和反应物的性质来确定的。
通常情况下,较大规模的反应需要较大尺寸的反应器来满足产量的要求。
而不同的反应物,可能需要不同形状的反应器,例如圆柱形、球形或椭球形等,以提供最佳的反应条件。
2. 材料选择在反应器设计中,材料的选择非常重要。
材料的选择必须考虑到反应物的性质、反应条件以及对材料的腐蚀性。
一般来说,不锈钢是常用的反应器材料,但在某些特殊的反应中,还可能使用陶瓷或塑料等特殊材料,以提高反应器的耐腐蚀性能。
3. 搅拌系统反应物在反应过程中需要获得均匀的混合,因此搅拌系统在反应器设计中起着关键作用。
常用的搅拌方式包括机械搅拌、气体搅拌和液体循环搅拌等,可以根据反应的需要选择相应的搅拌方式。
二、生产流程优化反应器的设计是化工生产流程优化的关键一环,而整个生产流程的优化涉及到原料选用、反应条件控制、能源利用和环境保护等多个方面。
1. 原料选用在化工生产中,原料的选择直接影响产品的质量和生产成本。
合理的原料选用可以提高反应效率和产能,并且减少废物和副产物的产生。
因此,在进行生产流程优化时,需要对原料进行综合评估,选择性能稳定、纯度高、价格适宜的原料,以达到最佳的生产效果。
2. 反应条件控制反应条件的控制对于反应的速率和选择性有着重要影响。
适当调节温度、压力、反应物浓度和催化剂的用量等参数,可以改善反应的效果并提高产品的纯度。
制药工艺中的反应器设计与优化研究

制药工艺中的反应器设计与优化研究制药工艺中的反应器设计是现代化药物生产中非常重要的一环。
一方面,好的反应器设计能够有效提高药物生产的质量和产量;另一方面,则直接影响到药物生产的成本和效益。
本文将从反应器的类型、反应器设计方法、反应器优化等角度探讨制药工艺中的反应器设计与优化研究。
反应器的类型生产药物时,反应器的类型多种多样。
目前在制药工艺中应用比较广泛的反应器主要有以下几种:一、批量反应器:批量反应器是一种常用的反应器,适用于小批量药物生产。
其特点是操作简便,能够有效控制反应物的质量和反应程度,但是不利于药物大规模生产。
二、连续式反应器:连续式反应器一般用于大规模药物生产,其输出比批量反应器准确高效,操作难度适中。
三、循环床反应器:循环床反应器主要应用于高密度发酵反应,可达到较高的产量和能量效率。
四、固定床反应器:固定床反应器主要适用于小分子物质的催化合成,在大规模生产时操作难度大,但适用于烷基化反应和脱氢反应等反应类型的制药。
反应器设计方法反应器设计的方法很多,通常包括反应器材料选择、反应器外形设计、反应器流体力学设计、反应器传热设计等多种因素。
下面分别探讨这些因素的影响。
一、反应器材料选择:反应器材料选择是反应器设计中的必要步骤,选错了材料会影响反应器的安全性和耐用性。
常用的反应器材料有玻璃钢、不锈钢、塑料等。
其中,玻璃钢价格便宜,但不耐压,适用于较小规模的药物生产。
不锈钢质地坚硬,强度高,用于大规模化药物生产较为适用。
塑料材料价格低廉,但其在制药生产中应用较少。
二、反应器外形设计:反应器外形设计包括反应器反应载体和反应器尺寸。
反应器载体的设计通常需要特定形状和表面质量,最好选用流线型和无孔质侵蚀的材质制造。
反应器尺寸则直接影响到反应器生产产量和费用。
一般而言,产品紧缩、温度升高或压力遭受过程,需要特殊炮举的滞后措施,制动反应器直接采取一定超越的容积和面积。
三、反应器流体力学设计:反应器流体力学的设计通常需要制定合适的流速方案,同时避免过度的湍流和不适当的边界层。
固定床反应器的工艺设计

固定床反应器的工艺设计固定床反应器是一种常见的化工设备,用于进行气体相催化反应,广泛应用于石油化工、化学工业等领域。
其工艺设计主要包括催化剂选择、反应器尺寸确定、流体力学设计和工艺参数确定等方面。
首先,催化剂的选择是固定床反应器工艺设计的核心之一。
催化剂的选择要考虑反应物的性质、反应条件和反应产物要求等因素。
常见的催化剂有贵金属系催化剂、氧化铝、硅负载催化剂等。
选择合适的催化剂不仅要考虑其催化性能,还要考虑催化剂的抗毒性、抗烧结性等因素。
接下来是反应器尺寸的确定。
固定床反应器的尺寸主要包括反应器直径、高度和床层厚度等。
反应器直径的确定要考虑气体分布均匀性和催化剂利用率等因素。
反应器高度的确定则要考虑反应物在反应过程中的转化率和反应物的停留时间。
床层厚度的确定要考虑反应物在固定床中的扩散速度和反应物的速度等因素。
流体力学设计是固定床反应器工艺设计的重要环节。
要保证流体在固定床中的均匀分布和床层内的有效接触,一般采用多孔介质来增加气流的接触面积。
此外,要考虑流体在固定床反应器中的压降,以确保反应过程中的稳定性。
通过合理设置入口和出口等设备,减少压降是流体力学设计的目标之一。
最后是工艺参数的确定。
固定床反应器的工艺参数包括反应温度、压力和空间速度等。
反应温度的确定要考虑反应物的活化能和热效应等因素。
反应压力的确定要考虑反应平衡和反应物的物性等因素。
空间速度则是反应物进入反应器的流量与催化剂床体积的比值,决定了反应物在固定床中的停留时间和转化率。
综上所述,固定床反应器的工艺设计涉及到催化剂选择、反应器尺寸确定、流体力学设计和工艺参数确定等方面。
只有在这些方面合理设计并综合考虑的基础上,才能实现固定床反应器的高效运行和优化生产。
固定床反应器的工艺设计是化工工程中的重要环节之一,其设计的合理与否直接影响到反应器的运行效果和生产效益。
在固定床反应器的设计中,首先需要选择合适的催化剂。
催化剂的选择应综合考虑反应物的性质、反应条件以及所要求的产物品质等因素。
连续化反应器及工艺设计

连续化反应器及工艺设计连续化反应器是一种反应器设计,可以在连续流动的条件下将原料转化为所需要的产物。
与传统的批量反应器相比,连续化反应器具有更高的产能和更好的反应控制性能。
本文将介绍连续化反应器的基本原理、工艺设计和应用。
连续化反应器的基本原理是将原料连续地引入反应器中,并将反应物与催化剂或反应溶液进行接触,以实现反应的进行。
连续化反应器通常由一系列连续的反应单元组成,每个单元都有一定的反应时间和反应条件。
通过调整每个单元中的反应条件,可以实现对反应的控制和优化。
在连续化反应器的工艺设计中,需要考虑以下几个关键因素:反应器类型、反应物的流量和浓度、反应温度和压力、催化剂的选择和循环、以及产物的分离和回收。
不同类型的反应器适用于不同的反应体系和目标产物。
例如,管式反应器适用于快速反应和高产能,而循环流化床反应器适用于催化剂循环和固体床反应。
反应物的流量和浓度对反应器性能和效果有重要影响。
较高的反应物流量可以提高产能,但过高的流量可能导致物料混合不均匀和反应物浓度不稳定。
反应物的浓度通常需要通过适当的稀释或浓缩来进行控制,以满足反应的要求。
反应温度和压力对反应物的转化率和选择性有重要影响。
适当的反应温度和压力可以提高反应速率和选择性,但过高的温度和压力可能导致副反应和催化剂的失活。
在工艺设计中需要仔细选择和控制反应温度和压力,以实现最佳的反应效果。
催化剂的选择和循环是连续化反应器设计中另一个重要考虑因素。
合适的催化剂可以提高反应速率和选择性,但催化剂的失活和污染可能会降低反应性能。
在连续化反应器中,催化剂通常需要循环使用,并采取适当的措施来清洁和再生。
循环催化剂可以有效减少催化剂的使用量和处理成本。
产物的分离和回收是连续化反应器工艺设计中非常重要的一部分。
高效的分离和回收技术可以提高反应器的效率和产物的纯度。
常用的分离技术包括蒸馏、萃取和膜分离等。
在反应器工艺设计中需要综合考虑反应物和产物的物性以及分离技术的适用性和经济性。
化工工程中的反应器设计与生产工艺
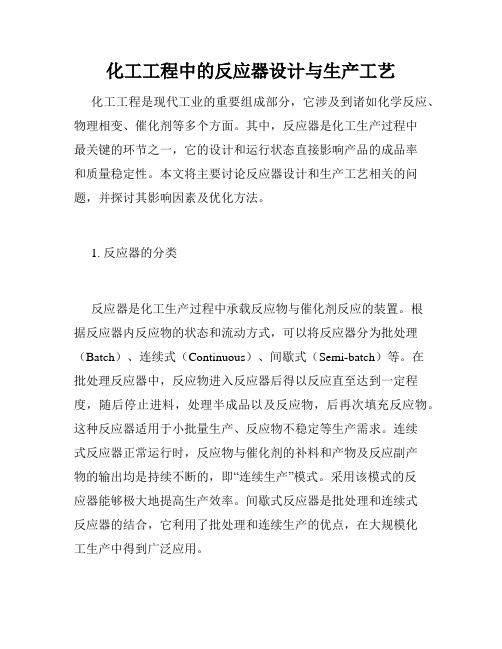
化工工程中的反应器设计与生产工艺化工工程是现代工业的重要组成部分,它涉及到诸如化学反应、物理相变、催化剂等多个方面。
其中,反应器是化工生产过程中最关键的环节之一,它的设计和运行状态直接影响产品的成品率和质量稳定性。
本文将主要讨论反应器设计和生产工艺相关的问题,并探讨其影响因素及优化方法。
1. 反应器的分类反应器是化工生产过程中承载反应物与催化剂反应的装置。
根据反应器内反应物的状态和流动方式,可以将反应器分为批处理(Batch)、连续式(Continuous)、间歇式(Semi-batch)等。
在批处理反应器中,反应物进入反应器后得以反应直至达到一定程度,随后停止进料,处理半成品以及反应物,后再次填充反应物。
这种反应器适用于小批量生产、反应物不稳定等生产需求。
连续式反应器正常运行时,反应物与催化剂的补料和产物及反应副产物的输出均是持续不断的,即“连续生产”模式。
采用该模式的反应器能够极大地提高生产效率。
间歇式反应器是批处理和连续式反应器的结合,它利用了批处理和连续生产的优点,在大规模化工生产中得到广泛应用。
2. 反应器设计的要素反应器的设计涉及到多个因素,如反应物的性质、产物的理化性质、催化剂的种类及其浓度、反应温度和压力等,因此反应器的设计需要考虑以下要素:(1)确定反应的类型和机理首先需要确定反应的类型和机理,例如区分非催化和催化反应。
针对不同的反应类型和不同的机理,需要采用不同的反应器设计方法。
(2)反应器的型式和尺寸根据反应物的属性,选择适宜的反应器型式。
例如,涉及到气液反应的场合,可以选择气体液体(G/L)反应器。
反应器的尺寸也是关键的设计参数之一,反应器内径、加热器功率、搅拌器功率等反应器设计参数的大小直接影响反应器所能承受的最大生产能力。
(3)反应器的催化剂和制备工艺催化剂的价格和制备工艺等往往存在着巨大的差异。
化学反应涉及到诸多反应物,必须在催化剂设计上进行合理的配合,否则,反应物或催化剂可能会被废弃。
- 1、下载文档前请自行甄别文档内容的完整性,平台不提供额外的编辑、内容补充、找答案等附加服务。
- 2、"仅部分预览"的文档,不可在线预览部分如存在完整性等问题,可反馈申请退款(可完整预览的文档不适用该条件!)。
- 3、如文档侵犯您的权益,请联系客服反馈,我们会尽快为您处理(人工客服工作时间:9:00-18:30)。
【MeiWei 81重点借鉴文档】
工艺设计要点之二十:反应器
1。
反应速率数据必须由实验室的研究工作得出,停留时间和空速数据的最终确定必须在试验台上取得。
2。
催化剂颗粒的尺寸:流化床一般为0.1 mm泥浆床一般为1mm 固定床一般为2~5mm
3。
对于均相全混釜反应器,输入搅拌浆的功率应该为0.1〜0.3kW/m3。
然而如果有传热发生,则所需功率应该三倍于上述数值。
4。
当平均停留时间达到组分均一所需时间的5~10倍时,就达到了CSTR的理想状态。
适当设计的搅拌约500〜20RR次旋转,才能达到组分均一。
5。
液体或者淤浆介质间相当慢的反应,通常最经济的配置应该采用3~5个全混釜反应器串联。
6。
平推流反应器的典型应用,在高流率产岀物及短停留时间,当需要明显的热量传递时选择它7。
当达到平衡条件下 95%的转化率时,一个5级全混釜反应器相当于一个活塞流反应器的性能。
8。
温度升高10o C,通常反应速率会加快一倍。
9。
非均相反应的反应速率经常是由传热或传质因素控制的,而不是化学动力学。
10。
有时,改善催化剂选择性能比增加反应速率更有效。
【MeiWei 81重点借鉴文档】。