挤出机机头
挤出机的基本知识

挤出机的基本知识塑料挤出机的主机是挤塑机,它由挤压系统、传动系统和加热冷却系统组成1.挤压系统挤压系统包括螺杆、机筒、料斗、机头、和模具,塑料通过挤压系统而塑化成均匀的熔体,并在这一过程中所建立压力下,被螺杆连续的挤出机头。
(1)螺杆:是挤塑机的最主要部件,它直接关系到挤塑机的应用范围和生产率,由高强度耐腐蚀的合金钢制成。
(2)机筒:是一金属圆筒,一般用耐热、耐压强度较高、坚固耐磨、耐腐蚀的合金钢或内衬合金钢的复合钢管制成。
机筒与螺杆配合,实现对塑料的粉碎、软化、熔融、塑化、排气和压实,并向成型系统连续均匀输送胶料。
一般机筒的长度为其直径的15~30倍,以使塑料得到充分加热和充分塑化为原则。
(3)料斗:料斗底部装有截断装置,以便调整和切断料流,料斗的侧面装有视孔和标定计量装置。
(4)机头和模具:机头由合金钢内套和碳素钢外套构成,机头内装有成型模具。
机头的作用是将旋转运动的塑料熔体转变为平行直线运动,均匀平稳的导入模套中,并赋予塑料以必要的成型压力。
塑料在机筒内塑化压实,经多孔滤板沿一定的流道通过机头脖颈流入机头成型模具,模芯模套适当配合,形成截面不断减小的环形空隙,使塑料熔体在芯线的周围形成连续密实的管状包覆层。
为保证机头内塑料流道合理,消除积存塑料的死角,往往安置有分流套筒,为消除塑料挤出时压力波动,也有设置均压环的。
机头上还装有模具校正和调整的装置,便于调整和校正模芯和模套的同心度。
挤塑机按照机头料流方向和螺杆中心线的夹角,将机头分成斜角机头(夹角120o)和直角机头。
机头的外壳是用螺栓固定在机身上,机头内的模具有模芯坐,并用螺帽固定在机头进线端口,模芯座的前面装有模芯,模芯及模芯座的中心有孔,用于通过芯线;在机头前部装有均压环,用于均衡压力;挤包成型部分由模套座和模套组成,模套的位置可由螺栓通过支撑来调节,以调整模套对模芯的相对位置,便于调节挤包层厚度的均匀性。
机头外部装有加热装置和测温装置。
双螺杆挤出机的结构及原理

双螺杆挤出机的结构及原理双螺杆挤出机是一种常用的塑料加工设备,广泛应用于塑料加工行业,本文将介绍双螺杆挤出机的结构及其原理。
结构双螺杆挤出机主要包括机头、料斗、螺旋输送机、缸体、螺杆组、电控系统等组件。
•机头:双螺杆挤出机的出料口,通过机头将挤出的熔融塑料进行成型。
•料斗:贮存塑料原料。
•螺旋输送机:将料斗中的塑料原料输送到缸体中。
•缸体:分为加热区和冷却区,加热区通过电热管加热,使塑料原料熔化并提高其流动性;冷却区通过水循环冷却,使塑料原料快速降温固化。
•螺杆组:可以分为驱动螺杆和被动螺杆,驱动螺杆由电机提供动力,通过传动装置带动被动螺杆旋转,将塑料原料在缸体中挤出。
•电控系统:控制双螺杆挤出机的启动、停止、加热、冷却和速度等参数。
原理双螺杆挤出机的工作原理是将塑料原料经过加热融化变成熔融塑料,通过螺杆的旋转将熔融塑料挤出机头形成管材、板材等形状。
具体工作过程如下:1.将塑料原料放入料斗中,由螺旋输送机将原料运送到缸体中。
2.缸体中的螺杆组由电机驱动旋转,将原料挤压向机头。
被动螺杆通过沟槽的作用将塑料原料送向驱动螺杆处。
3.加热区电热管的加热作用使塑料原料快速熔化变成熔融状态。
4.熔融塑料在螺杆的作用下,完全混合均匀后,通过机头挤出。
5.冷却区水循环制冷,使挤出的塑料快速降温固化成型。
6.控制系统可以实现对双螺杆挤出机的启停、加热、冷却、速度等参数的调节和控制。
总结双螺杆挤出机的结构及其原理相对简单,但具有高效、稳定、可靠的特点,广泛应用于塑料加工领域。
通过加热、挤出和冷却三个步骤,能够实现对塑料原料的自动化加工和成型,满足不同行业对塑料制品的需求。
挤出机机头设计
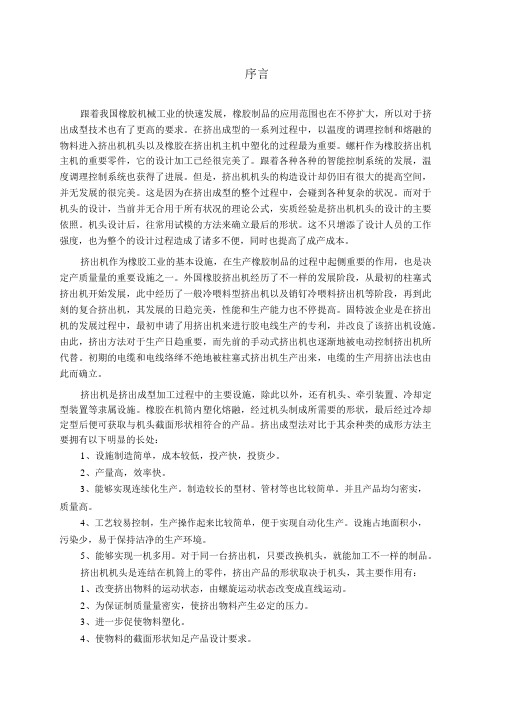
序言跟着我国橡胶机械工业的快速发展,橡胶制品的应用范围也在不停扩大,所以对于挤出成型技术也有了更高的要求。
在挤出成型的一系列过程中,以温度的调理控制和熔融的物料进入挤出机机头以及橡胶在挤出机主机中塑化的过程最为重要。
螺杆作为橡胶挤出机主机的重要零件,它的设计加工已经很完美了。
跟着各种各种的智能控制系统的发展,温度调理控制系统也获得了进展。
但是,挤出机机头的构造设计却仍旧有很大的提高空间,并无发展的很完美。
这是因为在挤出成型的整个过程中,会碰到各种复杂的状况。
而对于机头的设计,当前并无合用于所有状况的理论公式,实质经验是挤出机机头的设计的主要依照。
机头设计后,往常用试模的方法来确立最后的形状。
这不只增添了设计人员的工作强度,也为整个的设计过程造成了诸多不便,同时也提高了成产成本。
挤出机作为橡胶工业的基本设施,在生产橡胶制品的过程中起侧重要的作用,也是决定产质量量的重要设施之一。
外国橡胶挤出机经历了不一样的发展阶段,从最初的柱塞式挤出机开始发展,此中经历了一般冷喂料型挤出机以及销钉冷喂料挤出机等阶段,再到此刻的复合挤出机,其发展的日趋完美,性能和生产能力也不停提高。
固特波企业是在挤出机的发展过程中,最初申请了用挤出机来进行胶电线生产的专利,并改良了该挤出机设施。
由此,挤出方法对于生产日趋重要,而先前的手动式挤出机也逐渐地被电动控制挤出机所代替。
初期的电缆和电线络绎不绝地被柱塞式挤出机生产出来,电缆的生产用挤出法也由此而确立。
挤出机是挤出成型加工过程中的主要设施,除此以外,还有机头、牵引装置、冷却定型装置等隶属设施。
橡胶在机筒内塑化熔融,经过机头制成所需要的形状,最后经过冷却定型后便可获取与机头截面形状相符合的产品。
挤出成型法对比于其余种类的成形方法主要拥有以下明显的长处:1、设施制造简单,成本较低,投产快,投资少。
2、产量高,效率快。
3、能够实现连续化生产。
制造较长的型材、管材等也比较简单。
并且产品均匀密实,质量高。
挤出成型机头的作用和用途
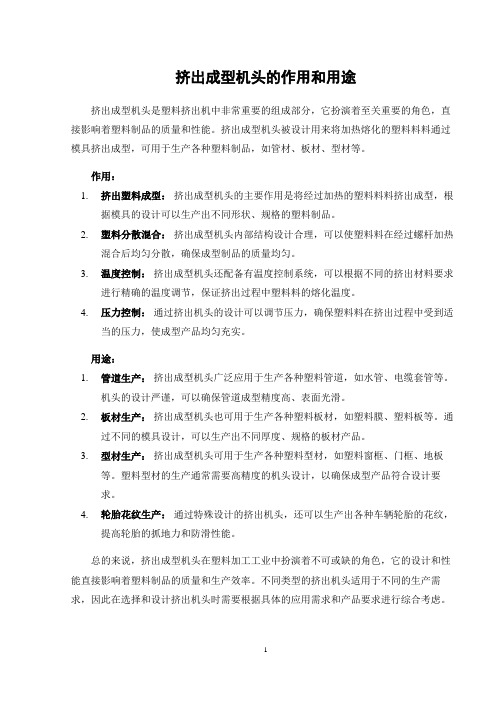
挤出成型机头的作用和用途挤出成型机头是塑料挤出机中非常重要的组成部分,它扮演着至关重要的角色,直接影响着塑料制品的质量和性能。
挤出成型机头被设计用来将加热熔化的塑料料料通过模具挤出成型,可用于生产各种塑料制品,如管材、板材、型材等。
作用:1.挤出塑料成型:挤出成型机头的主要作用是将经过加热的塑料料料挤出成型,根据模具的设计可以生产出不同形状、规格的塑料制品。
2.塑料分散混合:挤出成型机头内部结构设计合理,可以使塑料料在经过螺杆加热混合后均匀分散,确保成型制品的质量均匀。
3.温度控制:挤出成型机头还配备有温度控制系统,可以根据不同的挤出材料要求进行精确的温度调节,保证挤出过程中塑料料的熔化温度。
4.压力控制:通过挤出机头的设计可以调节压力,确保塑料料在挤出过程中受到适当的压力,使成型产品均匀充实。
用途:1.管道生产:挤出成型机头广泛应用于生产各种塑料管道,如水管、电缆套管等。
机头的设计严谨,可以确保管道成型精度高、表面光滑。
2.板材生产:挤出成型机头也可用于生产各种塑料板材,如塑料膜、塑料板等。
通过不同的模具设计,可以生产出不同厚度、规格的板材产品。
3.型材生产:挤出成型机头可用于生产各种塑料型材,如塑料窗框、门框、地板等。
塑料型材的生产通常需要高精度的机头设计,以确保成型产品符合设计要求。
4.轮胎花纹生产:通过特殊设计的挤出机头,还可以生产出各种车辆轮胎的花纹,提高轮胎的抓地力和防滑性能。
总的来说,挤出成型机头在塑料加工工业中扮演着不可或缺的角色,它的设计和性能直接影响着塑料制品的质量和生产效率。
不同类型的挤出机头适用于不同的生产需求,因此在选择和设计挤出机头时需要根据具体的应用需求和产品要求进行综合考虑。
1。
挤出机头的分类及特点有哪些机头设计的主要

挤出机头的分类及特点有哪些机头设计的主要
挤出机头是塑料挤出机中的关键部件,负责将加热融化的塑料通过模具的形状挤出成型。
根据挤出机头的不同设计和结构,可以将其分为多种分类,并且每种分类都具有其独特的特点和优势。
首先,从结构形式上来看,挤出机头可以分为光圈式机头、螺杆式机头和板式机头三种主要类型。
光圈式机头由针管和鞍座组成,适用于挤出螺纹、型材、带材等产品;螺杆式机头主要由挤出螺杆和机筒组成,适用于挤出管材、板材等产品;板式机头由板状合模和螺杆组成,适用于挤出薄膜、片材等产品。
不同类型的机头适用于不同的产品挤出加工,有着各自独特的特点和优势。
其次,从挤出成型方式上来看,挤出机头又可以分为单层机头、多层机头、中空机头等。
单层机头适用于一次性成型的产品,结构简单、生产效率高;多层机头可以实现多层产品挤出成型,产品层次丰富,适用于复合产品的生产;中空机头适用于中空结构产品的挤出,如管材、异形材等,具有独特的设计和挤出方式。
最后,挤出机头的特点还包括挤出均匀性、调节精准、耐磨耐高温等。
好的挤出机头设计可以保证挤出产品的均匀性和一致性,提高生产效率和产品质量;精准的调节设计可以使挤出机头适应不同材料和产品的生产需求;耐磨耐高温的材质和表面处理则可以延长机头的使用寿命,减少维护成本。
综上所述,挤出机头作为塑料挤出机中的重要组成部分,其分类和特点根据不同的设计和结构而有所不同,每种类型都有其适用的领域和优势。
在实际生产中,选择合适的挤出机头设计将对产品的质量和生产效率产生重要影响,因此选择合适的挤出机头至关重要。
1。
挤出机机头设计原则和参数选择 韩兵
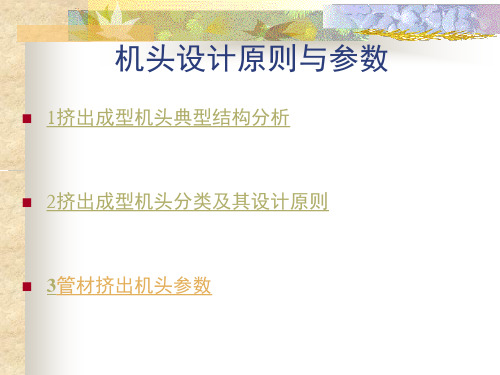
2.管材挤出机头零件的设计 (1) 口模
口模是成型管材外表面的零件,其 结构如图8-6所示。口模内径不等于塑料 管材外径,因为从口模挤出的管坯由于 压力突然降低,塑料因弹性恢复而发生 管径膨胀,同时,管坯在冷却和牵引作 用下,管径会发生缩小。这些膨胀和收 缩的大小与塑料性质、挤出温度和压力 等成型条件以及定径套结构有关,目前 尚无成熟的理论计算方法计算膨胀和收 缩值,一般是根据要求的管材截面尺寸, 按拉伸比确定口模截面尺寸。所谓拉伸 比是指口模成型段环隙横截面积与管材 横截面积之比。
L2=(1.5~2.5)D0
(8-4)
式中D0——栅板出口处直径。 芯模直径d1可按下式计算;
d1=d—2δ
(8-5)
式中δ—芯模与口模之间间隙;
d—口模内径。
由于如上所述塑料熔体挤出口模后的膨胀 与收缩,使δ不等于制品壁厚,δ可按下式计 算式:中k—经验系 数 ,kt k=1.(168~-61).20;
5.机头体 用来组装机头各零件及挤出机连接。 6.定径套 使制品通过定径套获得良好的表面粗糙度,正确 的尺寸和几何形状。 7.堵塞 防止压缩空气泄漏,保证管内一定的压力。
挤出成型机头分类及其设计原则
1.分类 由于挤出制品的形状和要求不同,因此要有相应
的机头满足制品的要求,机头种类很多,大致 可按以下三种特征来进行分类: (1)按机头用途分类 可分为挤管机头、吹管机头、挤板机头等;
2.设计原则
为了使挤出制品具有外观光洁性、尺寸准确性、形状与位置精确 准确性、单位长度的质量和物理力学性能等,一般遵循下面几个原 则:
(1)流道呈流线型 为使物料能沿着机头的流道充满并均匀地被挤 出,同时避免物料发生过热分解,机头内流道应 呈流线型,不能急剧地扩大或缩小,更不能有死 角和停滞区,流道应加工得十分光滑,表面粗糙 度应在Ra 0.4um以下。 (2)足够的压缩比 满足具体制品对机头压力的要求从而使制品密 实和消除因分流器支架造成的结合缝,根据制品 和塑料种类不同,应设计足够的压缩比。
挤出成型机头应设置适当的_装置
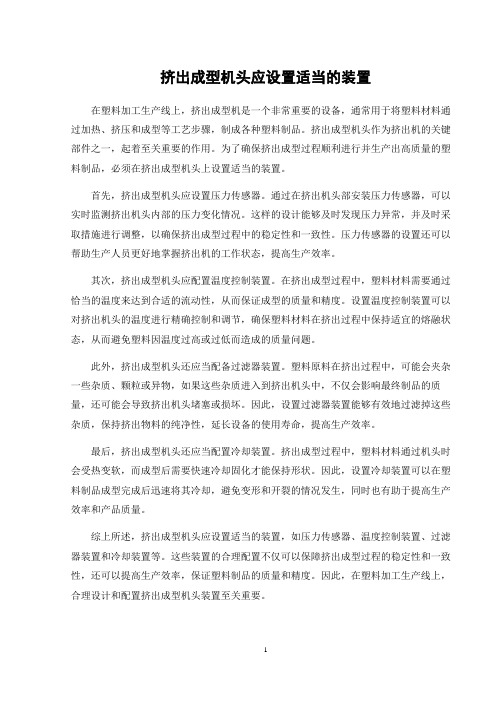
挤出成型机头应设置适当的装置在塑料加工生产线上,挤出成型机是一个非常重要的设备,通常用于将塑料材料通过加热、挤压和成型等工艺步骤,制成各种塑料制品。
挤出成型机头作为挤出机的关键部件之一,起着至关重要的作用。
为了确保挤出成型过程顺利进行并生产出高质量的塑料制品,必须在挤出成型机头上设置适当的装置。
首先,挤出成型机头应设置压力传感器。
通过在挤出机头部安装压力传感器,可以实时监测挤出机头内部的压力变化情况。
这样的设计能够及时发现压力异常,并及时采取措施进行调整,以确保挤出成型过程中的稳定性和一致性。
压力传感器的设置还可以帮助生产人员更好地掌握挤出机的工作状态,提高生产效率。
其次,挤出成型机头应配置温度控制装置。
在挤出成型过程中,塑料材料需要通过恰当的温度来达到合适的流动性,从而保证成型的质量和精度。
设置温度控制装置可以对挤出机头的温度进行精确控制和调节,确保塑料材料在挤出过程中保持适宜的熔融状态,从而避免塑料因温度过高或过低而造成的质量问题。
此外,挤出成型机头还应当配备过滤器装置。
塑料原料在挤出过程中,可能会夹杂一些杂质、颗粒或异物,如果这些杂质进入到挤出机头中,不仅会影响最终制品的质量,还可能会导致挤出机头堵塞或损坏。
因此,设置过滤器装置能够有效地过滤掉这些杂质,保持挤出物料的纯净性,延长设备的使用寿命,提高生产效率。
最后,挤出成型机头还应当配置冷却装置。
挤出成型过程中,塑料材料通过机头时会受热变软,而成型后需要快速冷却固化才能保持形状。
因此,设置冷却装置可以在塑料制品成型完成后迅速将其冷却,避免变形和开裂的情况发生,同时也有助于提高生产效率和产品质量。
综上所述,挤出成型机头应设置适当的装置,如压力传感器、温度控制装置、过滤器装置和冷却装置等。
这些装置的合理配置不仅可以保障挤出成型过程的稳定性和一致性,还可以提高生产效率,保证塑料制品的质量和精度。
因此,在塑料加工生产线上,合理设计和配置挤出成型机头装置至关重要。
挤出机头的分类

(2)按挤出塑件的出口方向分类: 直通机头:熔体在机头内的挤出流向与挤 出机螺杆的轴线平行。
(图4.4 为直通式管材机头)
角式机头:熔体在机头内的挤出流向与 挤出机螺杆的轴线呈一定角度。
图4.6为直角式管材机头
(3) 按塑料熔体在机头内所受压力分类:
➢<
挤出机头的分类
➢ 按挤出成型的塑料制件分类 ➢ 按挤出塑件的出口方向分类 ➢ 按塑料熔体在机头内所受压力分类
(1) 按挤出成型的塑料制件分类:
挤出成型塑件:管材、棒材、板材、 片材、网材、单丝、粒料、各种异型材、 吹塑薄膜、带有塑料包覆层的电线电缆等。
相应的机头分别称为:管机头、棒机
塑料成型工艺与模具设计
2 单螺杆挤出机介绍
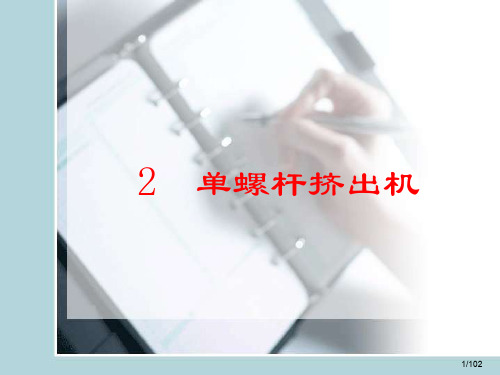
单螺杆挤出机的挤出过程
2.1.3.1 聚合物的三态变化
图2-5
聚合物三态变化图
31/102
图2-6
常规全螺纹螺杆的三个职能区
32/102
(1)加料段
功能主要是对塑料进行 压实和输送。
33/102
(2)熔融段或压缩段
是使塑料进一步压实和 塑化。
34/102
(3)计量段 塑料进入计量段后将进 一步塑化和均匀化,并使之 定压、定量和定温地从挤出 机头挤出。
2 单螺杆挤出机
1/102
2.1 概 述
挤出成型亦称挤压成型, 它是将物料加热熔融成粘流态, 借助螺杆的挤压作用,推动粘 流态的物料,使其通过口模而 成为截面与口模形状相仿的连 续体的一种成型方法。 所采用的设备称为挤出机。
2/102
塑料原料
加热 挤出机
塑料熔体 定型
加压
挤塑模具(机头)
初始形状的连续体
8/102
传动系统
其作用驱动螺杆,保证螺 杆在工作过程中所需要的扭矩 和转速。
9/102
加热冷却系统 它保证塑料和挤压系统在 成型加工中的温度控制要求。
10/102
加料系统
主要由料斗和自动上料装 置等组成。其作用是向挤压系 统稳定且(2)辅机
① ② ③ ④ ⑤ ⑥ ⑦ 机头 定型装置 冷却装置 牵引装置 切割装置 卷取装置 堆放装置
28/102
④螺纹螺距:用S表示 ⑤螺纹升角:用φ表示 ⑥螺纹头数:用P表示 ⑦螺槽轴向宽度:用B表示 B=S-b ⑧螺棱的轴向宽度:用b表示 ⑨螺槽的法向宽度:用W表示 ⑩螺棱的法向宽度:用e表示 11 螺纹外径与机筒内壁之间隙:用δ表示
29/102
φ
图2-4
挤出成型机头包括哪些部分组成

挤出成型机头包括哪些部分组成
挤出成型机是一种常用的塑料加工设备,用于将原料通过加热、压力和挤出机头的作用,将塑料原料挤出成型各种形状的制品。
而挤出机头是挤出成型机的关键部件之一,它由多个部分组成,包括进料系统、螺杆、筒体、模头以及冷却系统等。
首先是进料系统,用于将塑料原料从料仓中输送至螺杆区。
进料系统通常包括送料机构、送料口和螺杆进料口等部分,通过这些部分可以确保塑料原料被准确地送入挤出机。
接下来是螺杆,螺杆是挤出机头中最核心的部件之一,它在整个挤出过程中发挥着至关重要的作用。
螺杆可以根据加工的不同塑料原料以及成型的要求来设计不同的结构和参数,以确保挤出成型的效果。
紧接着是筒体,筒体是螺杆的外壳,用于容纳和固定螺杆。
在挤出成型过程中,塑料原料会在筒体内被加热、熔化,并受到一定的压力作用,从而变得柔软并容易挤出成型。
除了螺杆和筒体,挤出机头还包括模头。
模头是塑料挤出成型的关键部件,它的设计决定了最终成型制品的形状和尺寸。
模头可以根据产品的要求和设计图纸来定制,以确保最终挤出成型的产品符合要求。
最后是冷却系统,冷却系统用于降低挤出成型过程中塑料制品的温度,使其快速硬化和固化。
冷却系统通常包括冷却水管和风冷装置等部分,通过这些部分可以有效地控制塑料制品的成型温度和质量。
综上所述,挤出机头是挤出成型机中至关重要的部件之一,它由进料系统、螺杆、筒体、模头和冷却系统等部分组成,每个部分都发挥着不可或缺的作用,共同完成塑料挤出成型的工艺过程。
在实际生产中,合理设计和精心制造挤出机头的各个部分,对于提高生产效率和产品质量都起着至关重要的作用。
1。
管材挤出成型的机头结构及设计.

(4)机头体(模体)。机头 体相当于模架,用来安装 固定机头的各零部件。机 头体需与挤出机料筒紧密 连接,连接处应密封以防 塑料熔体泄漏。 (5)调节螺钉。调节螺钉用 来控制口模与芯模之间的 环隙大小和同轴度,以保 证挤出制品壁后均匀。通 常调节螺钉的数量4~8个, 视口模的尺寸而定。
(6)定径套。离开口模后的塑料熔体 虽已具有给定的截面形状,但因其 仍处于粘流状态从而产生变形,为 此需要用定径套对其进行冷却定型, 以使制品固化,并获得良好的质量、 准确的尺寸和几何形状。 (7)橡皮塞。橡皮塞的作用是防止压 缩空气泄漏,保证管内具有一定的 压力。
单管挤出机头实景
双管挤出机头实景
一. 管材挤出成型机头的作用
管材挤出机头主要有下述四种作用: (1)使物料由料筒内的螺旋运动变为直线运动。
(2)产生必要的成型压力,保证制品密实。
(3)使物料通过机头得到进一步塑化。
(4)通过机头成型所需断面形状的塑料制品。
二.管材挤出成型机头的结构组成
(1)口模和芯模。口模用 来成型制品的外表面, 芯模用来成型制品的内 表面。因此,口模和芯 模的定型部分决定了制 品的横载面形状和尺寸。
直角式机头
3.侧向机头(弯管式):来自挤出机的料流 (material flow)先流过一个弯形流道再进 入机头一侧,料流包芯棒后沿机头轴向方向 流出。这种设计可使管材的挤出方向与挤出 机呈任意角度,亦可与挤出机螺杆轴线相平 行。适合大口径管的高速挤出,但机头结构 比较复杂,造价较高。
侧向机头(弯管式)
五. 管材挤出成型机头的简单结构设计
2.1.2 口模内径
(1)经验公式: d1=D/BZ
(2)按拉伸比:
(BZ 为补偿系数)
I
挤出机模头积碳物处理方案

挤出机模头积碳物处理方案
挤出机是一种常用的工业设备,广泛应用于塑料加工行业。
然而,随着挤出机的使用时间的延长,机头内部会产生大量的碳物,严重影响机头的正常运行。
因此,如何有效处理挤出机模头积碳物成为了一个亟待解决的问题。
为了避免挤出机模头积碳物问题的发生,我们需要定期对机头进行清洗和维护。
清洗机头时,可以使用专门的清洗剂,将其喷洒到机头表面,并用刷子进行擦拭,以去除积碳物。
然后,再用清水冲洗干净,确保机头表面干净无残留。
此外,还可以使用高压水枪对机头进行冲洗,以彻底清除机头内部的碳物。
当挤出机模头出现严重积碳物时,需要采取更加强力的处理方法。
一种常用的方法是采用化学溶解剂进行清洗。
首先,将化学溶解剂倒入机头内部,然后将其加热至适当温度,使溶解剂能够溶解掉积碳物。
接着,使用专门的工具对机头进行刮擦,将溶解的积碳物彻底清除。
最后,用清水冲洗机头,确保机头表面干净无残留。
除了清洗和维护之外,还可以考虑使用一些特殊的涂层材料来预防挤出机模头积碳物问题的发生。
这些涂层材料具有抗黏附性和耐高温性能,可以有效降低积碳物的产生。
在机头表面涂覆这些材料后,积碳物会难以附着在机头表面,从而减少清洗和维护的频率。
针对挤出机模头积碳物问题,我们可以采取定期清洗和维护、使用
化学溶解剂清洗以及使用特殊涂层材料等多种处理方法。
这些方法能够有效解决挤出机模头积碳物问题,保证挤出机的正常运行。
通过合理的处理方案,我们可以延长挤出机模头的使用寿命,提高生产效率,为塑料加工行业的发展做出贡献。
第三章(挤出机)
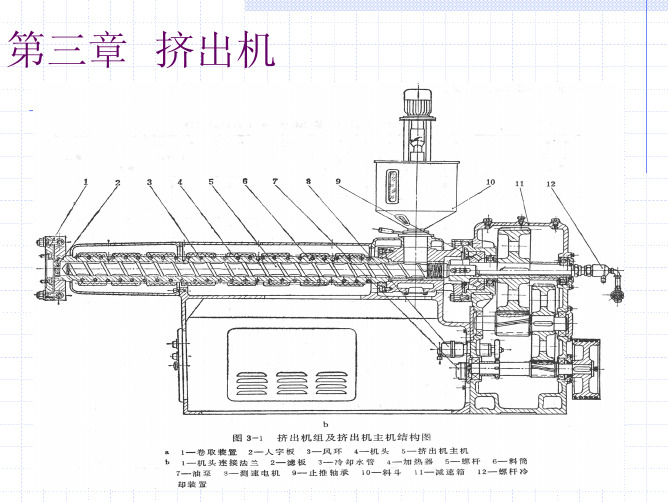
第一节 概述
一、挤出成型的过程 塑料原料
加热相变 挤出主机
塑料熔体
加压
挤出模具(机头) 切割 切割装置
初始形状的连续
定型 冷却(定型)装置
最终形状的连续体
一定规格的制品
二、挤出成型的特点
1、由于挤出过程具有连续性,故可生产任意长度的制品, 并且效率高、易实现生产过程的自动化。 2、应用范围广,能加工绝大多数的热塑性塑料和一些热固 性塑料。 制品成型:管材、板材、棒材、异型材、薄膜、丝、带 等; 原料准备工序:混合、塑化、脱水、着色、造粒、压延 喂料等; 半成品的加工:电缆料、色母料等。 3、由于挤出机结构简单,操作方便,成本低,故投资少, 收效快。
四、新型过滤器:长效,快换,不停机,多功能
五、静态混合器
在螺筒内加装分流、汇合混炼元件,让物料在流动的过 程中实现混 炼、均化的作用, 而不需要螺杆的 转动和螺棱的搅动。 ①Kenics静态混合器 ②Ross静态混合器 ③Sulzer静态混合器
第七节 加料装置
一、料斗的形式 圆形锥底、方形锥底、自热干燥料斗 二、上料方式 人工、鼓风、弹簧、真空(可以除去原料 中的空气和湿气) 三、强制加料结构 1、防止架桥 2、定量施压加料,有搅拌、螺旋、活塞等方式 四、加料装置的基本要求 1、有自动上料装置和计量器; 2、带有预热干燥或抽真空装置; 3、进料均匀; 4、如需混用两种或以上物料,需搅拌装置。
(一)固体输送理论
如计算固体输送流率,必把料筒转动线速度V= пDn, 该段的物料运动假设为理想化的物理模型。
流率Q = Vp1 F
= πD b n(tgφtgθ ) /( tgφ + tgθ ) F = ∫ (2πR − Pe / sin α )dR
异型材机头分类
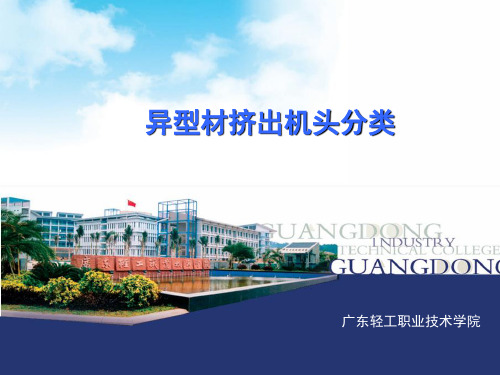
• 特点:结构简单,成本低,口模更换容易,适合多品种、小批量生产 • 缺点:横截面急剧变化,易形成局部滞料和死角,型材尺寸准确性不高 • 适用:聚烯烃,软聚氯乙烯的生产
2.流线型机头
• 设计要求:机头内流道必须为圆形过渡,各处不得有急剧过证挤出成型质量,适合大批量生产。
一、异型材机头分类
图9—6 板式机头 1—机颈座;2—口模板;3—夹持板
一、异型材机头分类
(2)流线型机头
在流线型机头中,当制品尺寸比挤出机出口尺寸小时,机头流道比较简单, 它由流道逐渐变化的过渡段和直接成型制品的口模(流道尺寸不变的平直部分) 所组成。当制品尺寸比挤出机出口处尺寸大时,流道可以由发散段、分流段、 压缩段和定型段组成。流入段的流道尺寸逐渐扩大,再到过渡段经压缩段进行 压缩,将机头的圆形截面逐步转变成口模的断面形状。这种转变应均匀而缓慢 地进行,熔融物料逐渐被加速,在整个断面上各部位的平均流速应基本相等, 防止流道内有任何死角和流速缓滞部分,避免造成物料过热分解。如图9—7所 示。
I段,成型部分流道,圆柱或圆锥形 II段,熔体分流与成型 III段,模头平行段,各流道均匀稳定流动
一、异型材机头分类
• (1)板式机头 板式机头的特点是结构简单,成本低, 制造快,调整及安装容易。其缺点是由于流道有急剧 变化,物料在机头内的流动状态不好,容易形成局部 物料滞流和流动不完全的死角。因此操作时间一长, 易引起该处物料分解,分解产物会严重影响产品质量, 故连续操作时间短,特别是热敏性塑料,如硬质聚氯 乙烯等。因此,板式机头多适用于聚烯烃,软质聚氯 乙烯制品的生产。图9-6为典型的板式机头,图中口模 板是成型带状产品的,当更换夹持在机颈和夹板间的 口模板时便可得到不同形状的制品,机颈是过渡部分, 它的内孔尺寸由挤出机的内孔逐渐过渡到与口模板成 型孔接近的尺寸,并比该孔稍大,由于在口模板入口 侧形成若干平面死点,设计时应尽量减少,以减少物 料分解的可能。
挤出成型机头的设计要点
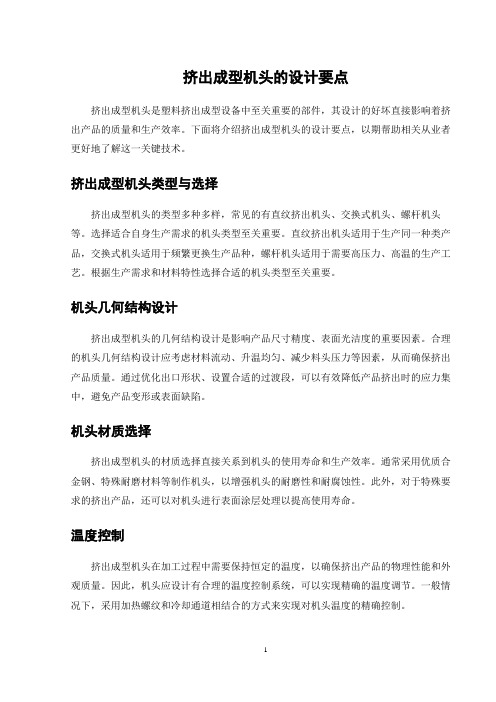
挤出成型机头的设计要点挤出成型机头是塑料挤出成型设备中至关重要的部件,其设计的好坏直接影响着挤出产品的质量和生产效率。
下面将介绍挤出成型机头的设计要点,以期帮助相关从业者更好地了解这一关键技术。
挤出成型机头类型与选择挤出成型机头的类型多种多样,常见的有直纹挤出机头、交换式机头、螺杆机头等。
选择适合自身生产需求的机头类型至关重要。
直纹挤出机头适用于生产同一种类产品,交换式机头适用于频繁更换生产品种,螺杆机头适用于需要高压力、高温的生产工艺。
根据生产需求和材料特性选择合适的机头类型至关重要。
机头几何结构设计挤出成型机头的几何结构设计是影响产品尺寸精度、表面光洁度的重要因素。
合理的机头几何结构设计应考虑材料流动、升温均匀、减少料头压力等因素,从而确保挤出产品质量。
通过优化出口形状、设置合适的过渡段,可以有效降低产品挤出时的应力集中,避免产品变形或表面缺陷。
机头材质选择挤出成型机头的材质选择直接关系到机头的使用寿命和生产效率。
通常采用优质合金钢、特殊耐磨材料等制作机头,以增强机头的耐磨性和耐腐蚀性。
此外,对于特殊要求的挤出产品,还可以对机头进行表面涂层处理以提高使用寿命。
温度控制挤出成型机头在加工过程中需要保持恒定的温度,以确保挤出产品的物理性能和外观质量。
因此,机头应设计有合理的温度控制系统,可以实现精确的温度调节。
一般情况下,采用加热螺纹和冷却通道相结合的方式来实现对机头温度的精确控制。
清洁与维护挤出成型机头在生产过程中容易受到塑料材料残渣的堵塞,因此需要定期清洁和维护。
清洁机头时应谨慎操作,避免损坏机头表面,影响其挤出产品的质量。
定期检查机头的磨损情况,并根据需要进行及时更换。
综上所述,挤出成型机头的设计要点包括机头类型选择、几何结构设计、材质选择、温度控制以及清洁与维护等方面。
只有全面考虑这些因素,合理设计和维护机头,才能确保挤出产品的质量和生产效率,提高生产制造的竞争力。
第6章 塑料挤出模具(机头)设计 6.4~6.5(第24讲)

第 24 讲 6.4 吹塑薄膜机头设计 一、吹膜机头的分类及特点 二、吹膜机头的结构设计
6.5 板材挤出机头设计 一、板片材挤出机头类型及特点 二、平缝式机头的设计要点
《塑料成型工艺与模具设计》 第6章 塑料挤出模具(机头)设计
6.4 吹塑薄膜机头设计
《塑料成型工艺与模具设计》 第6章 塑料挤出模具(机头)设计
1、芯棒式吹膜机头
(2)芯棒式机头设计要点 物料均匀分配问题 • 方法一:在芯棒上设置平衡流道, 方法一:在芯棒上设置平衡流道 设置平衡流道, 槽宽a等于机头进料口直径 等于机头进料口直径, 槽宽 等于机头进料口直径,深度为芯 棒侧原有间隙的1~1.5倍。 棒侧原有间隙的 倍
《塑料成型工艺与模具设计》
第6章 塑料挤出模具(机头)设计
3、螺旋式吹膜机头
螺旋槽数与芯棒直径关系
螺旋槽数与径向孔数相等;径向孔径取决于树脂种类、 螺旋槽数与径向孔数相等;径向孔径取决于树脂种类、温 度和挤出量,通常为φ8 φ16mm,螺槽起始深度16 20mm, φ8~φ16mm 16~20mm 度和挤出量,通常为φ8 φ16mm,螺槽起始深度16 20mm, 螺距16 22mm,口模平直段长度20 25mm,环隙0.8 1.2mm。 16~22mm 20~25mm 0.8~1.2mm 螺距16 22mm,口模平直段长度20 25mm,环隙0.8 1.2mm。 机头中心进料孔直径:过小阻力大, 机头中心进料孔直径:过小阻力大,过大则会在孔壁处滞 流引起熔体分解。 流引起熔体分解。
《塑料成型工艺与模具设计》
第6章 塑料挤出模具(机头)设计
3、螺旋式吹膜机头
结构: 结构:中心进料后沿径向பைடு நூலகம்成 3~6股料流,到达芯棒表面后, 6股料流,到达芯棒表面后, 进入各自的螺旋槽, 进入各自的螺旋槽,螺槽由深变 最终消失; 浅,最终消失;物料流动过程中 逐渐熔合,可有效消除熔接痕。 逐渐熔合,可有效消除熔接痕。
挤出机T型机头三维有限元模拟

2 () n 户 D
f 3 1 ( 4 )
采用 非牛 顿幂 律粘 度模 型 , 熔体 粘度 可 由下式 给 出 :
,=q ( 户 7 o )
1 边 界条 件 . 3
兰简: 军 , , 授主从高_ 工 篓 三 男 教 者介 ,蔓 c要 奠= 三麻 向 亍 边 包 壁 、口 出 、 面 固 壁 上 界 括 面入 和 口 称 。 体 面 对 华理大 “ 梯登划 K关文余。 采 量 入 边 和 南工学百 攀计K ,相论十篇 步 ” ̄ 目 资, .项 T -K - . 助 用 洁 边 ,所 速 。 口 界 … 界 。有 一 一 零 一… ~ 口 一 分 ~ … …
之 一 。迄今 为 止 , 于 流动 均 匀性 的研 究 主要 是 在 一 关 定 的简 化基 础 上进 行 数 学解 析 , 而熔 体 在 口模 中 的流 动是 复杂 的三 维流 动 。 随着 计 算流 体动 力学 ( F 和 C D) 计 算 机 软 硬件 技术 的发 展 , 来越 多 的计 算 流体 动 力 越 学软 件 用 于 聚合 物加 工 中各种 问题 的模 拟 分 析 , 而 进
维普资讯
l 试验 研 究l
挤 出机 T型 机头三维有 限元模拟
麻 向军 彭响方 孙树秋 童玉宝 赵 军
Байду номын сангаас
★
华 南 理 工大 学工 业 装 备 与控 制 工 程 学 院 广 州 5 0 4 1 60 摘 要 : 用 P l l 软 件对 一 种 T型 机头 内的 熔 体 流 动现 象进 行 了 三 维 有 限 元数 值 利 oy o fw 模 拟 。 果 表 明 。 拟计 算 得 到 的 流 动 均 匀性 指 数 与 解 析解 十 分 接 近 。 对 熔 体 在 机 头 结 模 并 中 的速 度场 和 压 力 场 进行 了分 析 。
挤出机机头压力范围

挤出机机头压力范围嘿,朋友们!今天咱来聊聊挤出机机头压力范围这个事儿。
你说这挤出机机头压力范围啊,就像是人跑步的速度一样。
要是跑太快了,那可能就喘不过气来,累得够呛;跑太慢了呢,又达不到锻炼的效果。
挤出机也一样啊,压力范围得合适才行。
想象一下,如果压力太小,那挤出来的东西是不是就软趴趴的,没个形状,就像面条没煮熟一样,软不拉几的。
可要是压力太大了呢,哎呀,那可不得了,就好像给气球吹太多气,说不定“嘭”的一下就爆了。
所以说啊,这个压力范围可得把握好,就跟做菜放盐似的,多了咸,少了没味。
咱平时用挤出机的时候,就得像了解自己的脾气一样了解它的压力范围。
你得知道啥时候该加点压力,啥时候得松一松。
这可不是随便说说的,得靠咱的经验和细心观察。
有时候可能就那么一点点的差别,出来的产品质量就完全不一样了。
比如说,在做一种塑料制品的时候,刚开始压力没调好,挤出来的东西要么有气泡,要么不光滑,那可不行啊!这就好比你去买衣服,看到一件到处是线头、皱皱巴巴的衣服,你会要吗?肯定不会嘛!所以啊,咱得把这挤出机的压力范围当回事儿。
那怎么才能找到最合适的压力范围呢?这就需要我们多尝试啦!就像学骑自行车一样,一开始可能会摔几跤,但慢慢就找到感觉了。
我们可以先从一个大概的范围开始试,然后一点点调整,看看哪种压力下出来的产品最让我们满意。
而且啊,不同的材料对压力范围的要求也不一样哦!这就跟不同的人有不同的性格一样。
有些材料比较“娇气”,压力稍微大一点就不行了;有些材料就比较“皮实”,压力大一点也能扛得住。
所以我们得根据材料的特点来调整压力范围,不能一概而论。
还有哦,机器的状态也会影响压力范围呢!要是机器用久了,可能就没那么灵光了,压力范围也可能会有点变化。
这时候我们就得更细心地去观察和调整了。
总之呢,挤出机机头压力范围这玩意儿,看似简单,实则暗藏玄机。
我们可得认真对待,好好琢磨,才能让挤出机乖乖地为我们生产出高质量的产品。
别小瞧了它,它可是能决定我们产品好坏的关键因素之一呢!这就是我对挤出机机头压力范围的一些看法,你们觉得呢?。
- 1、下载文档前请自行甄别文档内容的完整性,平台不提供额外的编辑、内容补充、找答案等附加服务。
- 2、"仅部分预览"的文档,不可在线预览部分如存在完整性等问题,可反馈申请退款(可完整预览的文档不适用该条件!)。
- 3、如文档侵犯您的权益,请联系客服反馈,我们会尽快为您处理(人工客服工作时间:9:00-18:30)。
上述三种机头的特征对比
管材机头尺寸设计
8、螺旋芯棒模头
优点: 1) 熔体能沿着口模的圆周均匀分布, 在制品上没有流动痕迹( 结合线) , 制品在圆 周方向上的厚度公差和各种性能均匀; 2) 压 力降和流动阻力较低, 在较高的产量下挤出物 的温度较低; 3) 机械应力和热应力较低,制品 有良好的机械强度; 4) 模头结构坚固, 适合高 粘度材料的吹塑成型, 同时, 机头的装拆操作
2.芯棒 1)芯棒的外径 芯棒的外径由管材的内径决定, 根据生产经验: d= D-2e 式中 d一芯棒的外径(mm); D一口模的内径(mm); e一口模与芯棒的单边间隙(mm), e =(0.83-0.94)t t一材料壁厚(mm)。
2)定型段、压缩段L2和收缩角 a、芯棒定型段的长度与L1相等或稍长。 b、L2可按下面经验公式计算: L2=(1.5-2.5)D0 式中 L2一芯棒的压缩段长度(mm); D0一塑料熔体在过滤板出口处的流道 直径(mm)。 c、芯模收缩角: 低粘度塑料 =45°-60° 高粘度塑料 =30°-50°
的环隙截面积之比,反映出塑料熔体的压实
程度。 低粘度塑料ε =4-10 高粘度塑料 ε =2.5-6.0
7管材挤出机的机头
分类
1)直通式机头
2)直角式机头
3)旁侧式机头
1)直通式机头 结构简单、制造容易、成本低、料流阻 力小等优点;但这种机头的缺点是在生产外 径 大的管材时芯模加热困难,分流器支架 造成的接缝处管材强度低。适用于加工RPVC、 SPVC、 PA、PC、PE和PP等塑料管材,一般 用于挤小口径的管材。
3、挤出机头设计原则
1.内腔呈流线型 :为了使塑料熔体能沿着机
头中的流道均匀平稳地流动而顺利挤出 (表面粗
糙度应小于1.6-3.2m );
2.足够的压缩比 :为使制品密实和消除因分
流器支架造成的结合缝 ;
3.正确的截面形状和尺寸 :要对口模进行适
当的形状和尺寸补偿;
4.合理的选择材料:为提高机头的使用寿命,
机头材料应选择耐磨、耐腐蚀、硬度高的钢 材或合金钢。
4、挤出机机头的结构组成
挤出模的主要零件:
口模、芯棒、过滤板、过滤网、分
流器、分流器支架、调节螺钉、定型套
和机头体。
主要结构的作用:
1)口模和芯模分别成型制品内外表面,定型 部分决定了制品的横截面形状 和尺寸; 2)分流器是使通过它的熔体变成薄环状,平 稳地进入成形区。同时,进一步加热和塑化 塑料 ; 3)定型套对成形管材进行冷却定型,以保证 制品良好质量,正确的尺寸和几何形状; 4)调节螺钉用来控制成形区内的口模和芯棒 之间的间隙及同轴度,以保证挤出塑件壁厚 的均匀 。
1、挤出机机头分类 2、挤出机机头的作用 3、挤出机机头的设计原则 4、挤出机机头的组件 5、工艺参数计算 6、管材挤出的机头介绍
1、挤出机头的分类 :
(1) 按挤出成型的塑料制件分类:有管材、棒材、板
材、片材、网材、单丝、粒料、各种异型材、吹塑薄
膜、电线电缆等。 (2) 按制品出口方向分类:有料流方向与挤出机螺 杆轴向一致的直向机头如硬管机头和料流方向与 挤出机螺杆轴向成某一角度横向机头如电缆机头。
工艺参数的确定
1.口模 1)口模外径:
D=d/k 式中 D-口模的内径(mm)。 D-管材的外径(mm) K-补偿系数,见表5-4
表5-4 补偿系数k值
2)定型段长度L1 a、按管材外径计算: L1=(0.5—3)D 通常当管子直径较大时定型长度取小值,因为 此时管子的被定型面积较大,阻力较大,反 之就取大值。同时考虑到塑料的性质,一般 挤软管取大值,挤硬管取小值。 b、按管材壁厚计算:L1=nt 式中 t一管材壁厚(mm); n一 系数,见表5-5。
3.分流器
(1)分流锥的角度(扩张角):
低粘度塑料 =30°-80° 高粘度塑料 =30°-60° 扩张角>收缩角过大时料流的流动阻力 大,熔体易过热分解;过小时不利于机头对其 内的塑料熔休均匀加热,机头体积也会增大。
(2)分流锥长度L5 L5=(1-1.5)D0 式中 D0一头于过滤板相连处的流道直径 (mm),如图5-6所示。 (3)分流锥尖角处圆弧半径R: R=(0.5-2) mm R不易过大, 否则熔体容易 在此处发 生滞留
(3) 按机头内压力大小分类 :有低压机头(料流压力
小于4MPa)、中压机头(料流压力为4—1OMPa)和
高压机头(料流压力大于1OMPa).
2、挤出机头主要作用:
(1)使物料由螺旋运动 变为直线运动。 (2)产生必要的成型压 力,保证制品密实。 (3)使物料通过机头得 到进一步塑化。 (4)通过机头成型所需 要的断面形状的塑料 制品。
(4)分流器表面粗糙度Ra Ra<0.4-0.2m (5)栅板与分流锥顶间隔L6 L6=(10-20)mm 或L5<0.1D1 式中 D1一 杆直径,如图5-8所示。
拉伸比和压缩比
拉伸比和压缩比是与口模和芯棒尺寸相关 的工艺参数。根据管材断面尺寸确定口模环 隙截面尺时,一般尚凭拉伸比确定 (1)拉伸比I 所谓管材的拉伸比是口模和芯棒的
5、口模、芯模定型部分长度的选择
为消除熔接缝, 使物料压力稳定且均匀 挤出, 口模、芯模定型部分长度通常为 口模间隙宽度的15 倍以上, 定型段长度
为分流处芯棒直径的2 倍以上。
6、压缩比
压缩比ε即流道最大截面积与挤出口模环隙面 积之比, ε值体现了压力降的大小。ε值过小, 易造成 泡膜挤压不实, 膜厚不均; ε值过大, 则熔料在流道中 易过热且在出口发生熔胀。一般取1.5~ 3 为宜。
环隙截面积与管材成型后的截面积之比,其
计算公式如下:
I
式中
D1 D2 d1 d 2
2
2
2
2
I一拉伸比; D1一口模内径(mm); D2一芯棒外径(mm); d1一 塑料管材的外径(mm); d2一塑料管材的内径(mm)。
(2)压缩比ε
所谓管材的压缩比是机头和
多孔板相接处最大进料截面积与口模和芯棒
2)直角式机头 这种结构芯模一端为支承端。不存在 分流器支架,熔料从机头一端进人芯模对 面汇集,只可能生一条接缝线。定径精度 较髙,而且管材的内外壁同时进行冷却, 出料均勻,管材质量好,产量高。
3)旁侧式机头
来自挤出机的料流先流过一个弯形流道再 进入机头一侧,料流包芯模后沿机头轴向流 出。这种设计可使管材的挤出方向与挤出机 呈任意角度,亦可与挤出机螺杆轴线相平行。 但机头结构比较复杂,造价较髙。