挤出成型及机头设计
挤出机机头设计
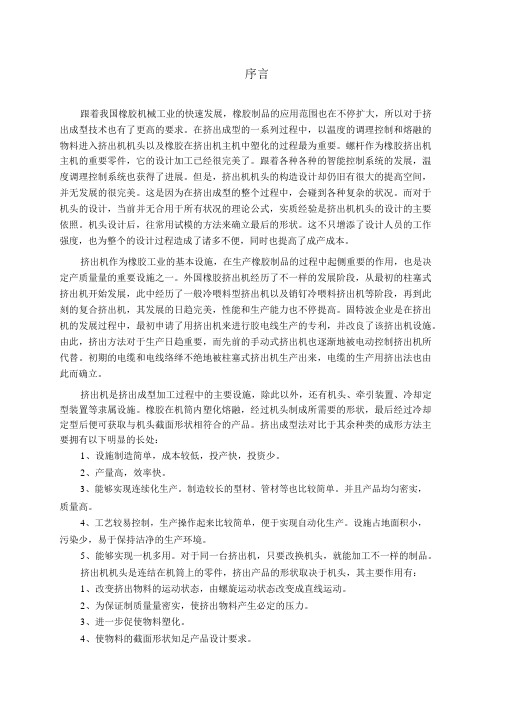
序言跟着我国橡胶机械工业的快速发展,橡胶制品的应用范围也在不停扩大,所以对于挤出成型技术也有了更高的要求。
在挤出成型的一系列过程中,以温度的调理控制和熔融的物料进入挤出机机头以及橡胶在挤出机主机中塑化的过程最为重要。
螺杆作为橡胶挤出机主机的重要零件,它的设计加工已经很完美了。
跟着各种各种的智能控制系统的发展,温度调理控制系统也获得了进展。
但是,挤出机机头的构造设计却仍旧有很大的提高空间,并无发展的很完美。
这是因为在挤出成型的整个过程中,会碰到各种复杂的状况。
而对于机头的设计,当前并无合用于所有状况的理论公式,实质经验是挤出机机头的设计的主要依照。
机头设计后,往常用试模的方法来确立最后的形状。
这不只增添了设计人员的工作强度,也为整个的设计过程造成了诸多不便,同时也提高了成产成本。
挤出机作为橡胶工业的基本设施,在生产橡胶制品的过程中起侧重要的作用,也是决定产质量量的重要设施之一。
外国橡胶挤出机经历了不一样的发展阶段,从最初的柱塞式挤出机开始发展,此中经历了一般冷喂料型挤出机以及销钉冷喂料挤出机等阶段,再到此刻的复合挤出机,其发展的日趋完美,性能和生产能力也不停提高。
固特波企业是在挤出机的发展过程中,最初申请了用挤出机来进行胶电线生产的专利,并改良了该挤出机设施。
由此,挤出方法对于生产日趋重要,而先前的手动式挤出机也逐渐地被电动控制挤出机所代替。
初期的电缆和电线络绎不绝地被柱塞式挤出机生产出来,电缆的生产用挤出法也由此而确立。
挤出机是挤出成型加工过程中的主要设施,除此以外,还有机头、牵引装置、冷却定型装置等隶属设施。
橡胶在机筒内塑化熔融,经过机头制成所需要的形状,最后经过冷却定型后便可获取与机头截面形状相符合的产品。
挤出成型法对比于其余种类的成形方法主要拥有以下明显的长处:1、设施制造简单,成本较低,投产快,投资少。
2、产量高,效率快。
3、能够实现连续化生产。
制造较长的型材、管材等也比较简单。
并且产品均匀密实,质量高。
木塑异型材挤出机头流道设计
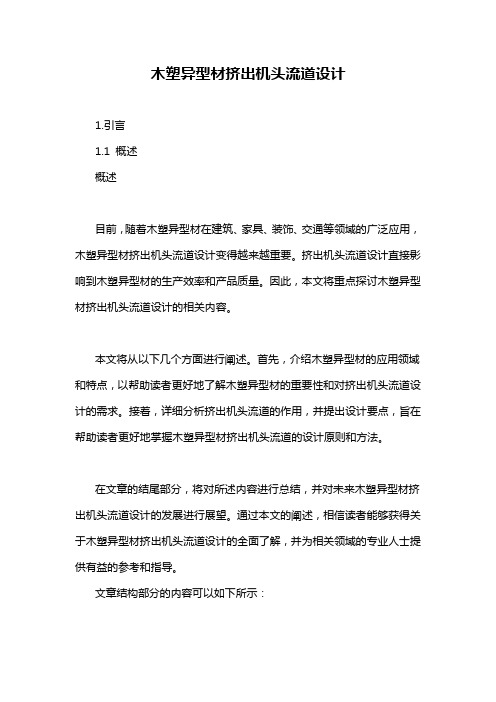
木塑异型材挤出机头流道设计1.引言1.1 概述概述目前,随着木塑异型材在建筑、家具、装饰、交通等领域的广泛应用,木塑异型材挤出机头流道设计变得越来越重要。
挤出机头流道设计直接影响到木塑异型材的生产效率和产品质量。
因此,本文将重点探讨木塑异型材挤出机头流道设计的相关内容。
本文将从以下几个方面进行阐述。
首先,介绍木塑异型材的应用领域和特点,以帮助读者更好地了解木塑异型材的重要性和对挤出机头流道设计的需求。
接着,详细分析挤出机头流道的作用,并提出设计要点,旨在帮助读者更好地掌握木塑异型材挤出机头流道的设计原则和方法。
在文章的结尾部分,将对所述内容进行总结,并对未来木塑异型材挤出机头流道设计的发展进行展望。
通过本文的阐述,相信读者能够获得关于木塑异型材挤出机头流道设计的全面了解,并为相关领域的专业人士提供有益的参考和指导。
文章结构部分的内容可以如下所示:1.2 文章结构本篇文章主要围绕"木塑异型材挤出机头流道设计"展开讨论,其结构主要分为引言、正文和结论三个部分。
引言部分将首先对文章的背景和意义进行概述,介绍木塑异型材的应用领域以及其中存在的挑战。
接着,会简要介绍文章的结构和各个章节的内容,为读者提供整体的框架。
正文部分将重点探讨木塑异型材的特点及其应用前景,包括其在建筑、家具等领域的优势和潜在的市场需求。
同时,还会深入分析木塑异型材的制造工艺和挤出机头流道设计对产品性能的影响,以及目前面临的技术难题和研究进展。
在挤出机头流道设计章节中,我们将详细介绍挤出机头流道的作用和原理,阐述其对木塑异型材生产过程中塑料熔融、挤压和整形的重要性。
同时,我们将提供一些具体的设计要点,包括流道结构、流道形状、流道尺寸等方面的考虑因素,以帮助读者更好地理解并应用于实际设计中。
结论部分将对全文进行总结,再次强调木塑异型材挤出机头流道设计的重要性和挑战,总结已有的研究成果和改进方向,并展望未来的研究方向和发展前景。
挤出机机头

上述三种机头的特征对比
管材机头尺寸设计
8、螺旋芯棒模头
优点: 1) 熔体能沿着口模的圆周均匀分布, 在制品上没有流动痕迹( 结合线) , 制品在圆 周方向上的厚度公差和各种性能均匀; 2) 压 力降和流动阻力较低, 在较高的产量下挤出物 的温度较低; 3) 机械应力和热应力较低,制品 有良好的机械强度; 4) 模头结构坚固, 适合高 粘度材料的吹塑成型, 同时, 机头的装拆操作
2.芯棒 1)芯棒的外径 芯棒的外径由管材的内径决定, 根据生产经验: d= D-2e 式中 d一芯棒的外径(mm); D一口模的内径(mm); e一口模与芯棒的单边间隙(mm), e =(0.83-0.94)t t一材料壁厚(mm)。
2)定型段、压缩段L2和收缩角 a、芯棒定型段的长度与L1相等或稍长。 b、L2可按下面经验公式计算: L2=(1.5-2.5)D0 式中 L2一芯棒的压缩段长度(mm); D0一塑料熔体在过滤板出口处的流道 直径(mm)。 c、芯模收缩角: 低粘度塑料 =45°-60° 高粘度塑料 =30°-50°
的环隙截面积之比,反映出塑料熔体的压实
程度。 低粘度塑料ε =4-10 高粘度塑料 ε =2.5-6.0
7管材挤出机的机头
分类
1)直通式机头
2)直角式机头
3)旁侧式机头
1)直通式机头 结构简单、制造容易、成本低、料流阻 力小等优点;但这种机头的缺点是在生产外 径 大的管材时芯模加热困难,分流器支架 造成的接缝处管材强度低。适用于加工RPVC、 SPVC、 PA、PC、PE和PP等塑料管材,一般 用于挤小口径的管材。
3、挤出机头设计原则
1.内腔呈流线型 :为了使塑料熔体能沿着机
头中的流道均匀平稳地流动而顺利挤出 (表面粗
第三章 挤出成型工艺与模具结构
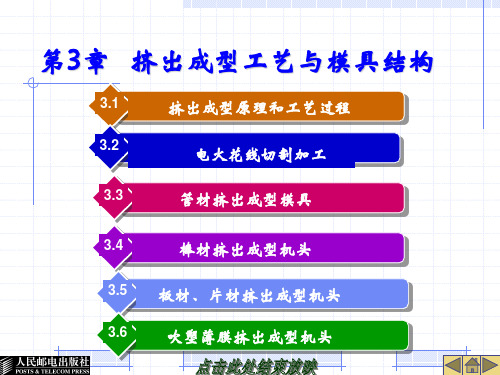
3.机头与挤出机的连接
常用国产挤出机与机头的连接形式如图3-3、 图3-4所示。 在图3-3中,机头以螺纹联接在机头法兰上, 机头法兰以4~6个铰链螺钉与机筒法兰连接固定。 图3-4所示为挤出机与机头的又一种连接形 式。机头以8个内六角螺钉与机头法兰连接固定, 机头法兰与机筒法兰由定位销定位,机头外圆与 机头法兰内孔配合,保证机头与挤出机的同心度。
3.3.3 管材定径套的结构类型及尺寸
管材的定径方法 : 1、外径定型法:(1)内压法 (2) 真空吸附法 。 2、内径定型法
3.4 棒材挤出成型模具
棒材是指截面为圆形的实心塑料型材, 塑料棒材的原材料一般是工程塑料,如尼龙、 聚甲醛、聚碳酸脂、ABS、聚砜、玻璃纤维 增强塑料等。棒材机头的螺杆长径比为2 5~120,除了生产玻璃纤维增强塑料外, 可以设置50~80目的过滤网。
3.1.1 挤出成型原理和特点 1.挤出成型原理
首先将粒状或粉状塑料加入料斗中,在旋转 的挤出机螺杆的作用下,加热的塑料通过沿螺杆 的螺旋槽向前方输送。在此过程中,塑料不断接 受料筒的外加热和螺杆与塑料之间、料筒与塑料 之间的剪切摩擦热,逐渐熔融呈黏流态,然后在 挤压系统的作用下,塑料熔体通过具有一定形状 的挤出模具,从而获得具有一定截面形状的塑料 型材,如图3-1所示。
3.6 吹塑薄膜挤出成型机头
薄膜是目前广泛使用的塑料挤出产品, 薄膜的厚度一般为0.01~0.25mm。薄膜的常 用生产方法是吹塑成型,就是由挤出机机头 挤出塑料管坯,同时从机头中心通入压缩空 气,将管坯吹成所需直径的薄膜。吹塑法可 以加工软、硬聚氯乙烯、聚乙烯、聚丙烯、 聚苯乙烯、聚酰胺等塑料薄膜。
2.挤出成型的特点
(1)连续成型,生产量大,生产率高,成 本低。 (2)塑件截面恒定,形状简单。 (3)塑件内部组织均衡紧密,尺寸比较稳 定准确。 (4)适用性强,除氟塑料以外,几乎能 加工所有热塑性塑料和部分热固性塑料。
挤出机机头设计原则和参数选择 韩兵
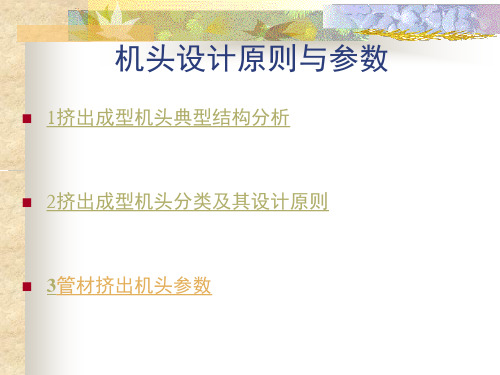
2.管材挤出机头零件的设计 (1) 口模
口模是成型管材外表面的零件,其 结构如图8-6所示。口模内径不等于塑料 管材外径,因为从口模挤出的管坯由于 压力突然降低,塑料因弹性恢复而发生 管径膨胀,同时,管坯在冷却和牵引作 用下,管径会发生缩小。这些膨胀和收 缩的大小与塑料性质、挤出温度和压力 等成型条件以及定径套结构有关,目前 尚无成熟的理论计算方法计算膨胀和收 缩值,一般是根据要求的管材截面尺寸, 按拉伸比确定口模截面尺寸。所谓拉伸 比是指口模成型段环隙横截面积与管材 横截面积之比。
L2=(1.5~2.5)D0
(8-4)
式中D0——栅板出口处直径。 芯模直径d1可按下式计算;
d1=d—2δ
(8-5)
式中δ—芯模与口模之间间隙;
d—口模内径。
由于如上所述塑料熔体挤出口模后的膨胀 与收缩,使δ不等于制品壁厚,δ可按下式计 算式:中k—经验系 数 ,kt k=1.(168~-61).20;
5.机头体 用来组装机头各零件及挤出机连接。 6.定径套 使制品通过定径套获得良好的表面粗糙度,正确 的尺寸和几何形状。 7.堵塞 防止压缩空气泄漏,保证管内一定的压力。
挤出成型机头分类及其设计原则
1.分类 由于挤出制品的形状和要求不同,因此要有相应
的机头满足制品的要求,机头种类很多,大致 可按以下三种特征来进行分类: (1)按机头用途分类 可分为挤管机头、吹管机头、挤板机头等;
2.设计原则
为了使挤出制品具有外观光洁性、尺寸准确性、形状与位置精确 准确性、单位长度的质量和物理力学性能等,一般遵循下面几个原 则:
(1)流道呈流线型 为使物料能沿着机头的流道充满并均匀地被挤 出,同时避免物料发生过热分解,机头内流道应 呈流线型,不能急剧地扩大或缩小,更不能有死 角和停滞区,流道应加工得十分光滑,表面粗糙 度应在Ra 0.4um以下。 (2)足够的压缩比 满足具体制品对机头压力的要求从而使制品密 实和消除因分流器支架造成的结合缝,根据制品 和塑料种类不同,应设计足够的压缩比。
挤出机机头设计

前言随着我国橡胶机械工业的快速发展,橡胶制品的应用范围也在不断扩大,因此对于挤出成型技术也有了更高的要求。
在挤出成型的一系列过程中,以温度的调节控制和熔融的物料进入挤出机机头以及橡胶在挤出机主机中塑化的过程最为重要。
螺杆作为橡胶挤出机主机的重要部件,它的设计加工已经很完善了。
随着各种各样的智能控制系统的发展,温度调节控制系统也取得了进展。
然而,挤出机机头的结构设计却仍然有很大的提升空间,并没有发展的很完善。
这是因为在挤出成型的整个过程中,会遇到各种复杂的情况。
而对4、工艺较易控制,生产操作起来比较简单,便于实现自动化生产。
设备占地面积小,污染少,易于保持清洁的生产环境。
5、可以实现一机多用。
对于同一台挤出机,只需更换机头,就能加工不同的制品。
挤出机机头是连接在机筒上的零件,挤出产品的形状取决于机头,其主要作用有:1、改变挤出物料的运动状态,由螺旋运动状态改变为直线运动。
2、为保证制品质量密实,使挤出物料产生一定的压力。
3、进一步促进物料塑化。
4、使物料的截面形状满足产品设计要求。
1挤出机机头设计要求概述1.1挤出机机头通用设计原则挤出机机头要遵循一定的合理的原则来进行相关设计,总结起来讲,主要有以下几个原则:1、为缩短清洗时间和组装时间,挤出机机头的零部件要尽量少,而且要注意各个零部件的相互配合以及对中性。
2、要尽量减少机头中相关的连接环节。
部件数量减少的同时不但可以节约成本,也2、流道中截面积大的区域流速也低,熔融的物料在这样的区域滞留的时间也就越长,这会引起像PE这样的热敏感型混合物料的降解。
针对这类材料,要服从最小流道体积原则,可以通过减小缝隙挤出机机头分配流道的方法,以便缩短挤出机机头的轴向长度。
3、机头流道中要避免物料流动方向的突变,也要防止截面积突变,即流道中不能有死角,所以各个位置的半径不能小于 3mm。
4、在设计挤出机机头的平行成型区时,要消退流道端部的可逆的形变,且要根据生产的产品的性质和所加工熔融物料来进行设计。
挤出成型工艺与设备概述

15
(3)排气式双螺杆挤出机造粒法
•
将树脂和纤维分别加入排气式双螺杆挤出机的加料孔
和进丝口,玻璃纤维被左旋螺杆及捏合装置所破碎,在料
简内纤维和树脂混合均匀,经过排气段除去混料中的挥发
性物质,进一步塑炼后经口模挤出料条,再经冷却、干燥
10.挤出成型工艺与设备
1
挤 出 成 型 工 艺 是 生 产 热 塑 性 复 合 材 料 (Fiber Reinforced Thermo Plastics 简称FRTP)制品的主要 方法之一。
工艺过程:先将树脂和增强纤维制成粒料,然后再 将粒料加入挤出机内,经塑化、挤出、冷却定型而成 制品。
2
• 应用: 广泛用于生产各种增强塑料管、棒材、异形断面型材等。
8
机头
3
4
5
2
6
1
玻璃纤维通过型芯中的导纱孔进入机头型腔与熔融的 树脂混合。
9
型芯构造形式
分瓣式
套管式
迷宫式
10
牵引和切粒
• 牵引和切粒一般是在一台机器上完成,牵引机构是由两 对牵引辊完成,第一对牵引辊的牵引速度比第二对辊低, 从而保证两道牵引辊之间有一定的张力,防止料条堆积, 但张力不能过大,否则会将料条拉断。 切粒是用切刀将料条连续不断地切成所需要长度的粒料。
18
10.2 影响FRTP性能的因素
1 基体树脂对FRTP性能影响 不同的热塑性树脂,性能差别很大,用纤维增强后,
其效果也有很大差别。
1)力学性能提高2—3倍以上 2)提高热变形温度 3)产品尺寸稳定提高 4)降低线膨胀系数1—3倍 5)对于吸水率的影响 不一 6)耐疲劳性能、抗蠕变性能 7)防止开裂、改善电性能 FRTP的耐化学腐蚀性能主要取决于树脂的品种
挤出成型工艺及模具设计

湿法挤出一般采用柱塞式挤出机,材料 的塑化是借助溶剂使其变为可流动态的。
根据挤出时加压方式的不同,可分为 连续式和间歇式两种。 (1)连续式挤出采用螺杆式挤出机,加压是
通过螺杆进行的。 (2)间歇式挤出采用柱塞式挤出机进行,借
道表面粗糙度Ra值应小于16~32μm。
(4) 机头内应有分流装置和适当的压缩区 机头内应设置分流器和分流器支架等
一类分流装置,如图4-4所示。 另外,机头中设计一段压缩区域,以
增大熔体的流动阻力,消除熔接痕。
(5) 机头成型区应有正确的截面形状 设计机头成型区时,应尽量减小离模
膨胀效应和收缩效应的影响。 设计机头时: 第一:要对口模进行适当的形状和尺寸补
其优点为:生产率高; 定径精度高; 料流稳定均匀; 成型质量也较高; 熔体的流动阻力较小;
缺点为:
3. 旁侧式挤管机头与直角式相似,如
图4.7所示,其结构更为复杂,熔体流动阻
图4.7 旁侧式机头
1、8、10、12 测 温孔; 2 口模; 3 型芯; 4、7 外加热圈; 5 调节螺钉; 6 机头体; 9 连接体; 11 内加热圈
第4章 挤出成型工艺及模具设计
4.1 挤出成型原理及其工艺特性 4.2 挤出成型模具概述 4.3 管材挤出成型模具 4.4 棒材挤出成型机头 4.5 板材、片材挤出成型机头 4.6 异型材挤出成型模具
4.1 挤出成型原理及其工艺特性
4.1.1 挤出成型原理及其特点 4.1.2 挤出成型工艺过程 4.1.3 挤出成型工艺参数
b.挤出成型 将挤出机预热到规定温度后,启动电
机带动螺杆旋转输送物料,同时向料筒中 加入塑料。
管材挤出成型的机头结构及设计.

(4)机头体(模体)。机头 体相当于模架,用来安装 固定机头的各零部件。机 头体需与挤出机料筒紧密 连接,连接处应密封以防 塑料熔体泄漏。 (5)调节螺钉。调节螺钉用 来控制口模与芯模之间的 环隙大小和同轴度,以保 证挤出制品壁后均匀。通 常调节螺钉的数量4~8个, 视口模的尺寸而定。
(6)定径套。离开口模后的塑料熔体 虽已具有给定的截面形状,但因其 仍处于粘流状态从而产生变形,为 此需要用定径套对其进行冷却定型, 以使制品固化,并获得良好的质量、 准确的尺寸和几何形状。 (7)橡皮塞。橡皮塞的作用是防止压 缩空气泄漏,保证管内具有一定的 压力。
单管挤出机头实景
双管挤出机头实景
一. 管材挤出成型机头的作用
管材挤出机头主要有下述四种作用: (1)使物料由料筒内的螺旋运动变为直线运动。
(2)产生必要的成型压力,保证制品密实。
(3)使物料通过机头得到进一步塑化。
(4)通过机头成型所需断面形状的塑料制品。
二.管材挤出成型机头的结构组成
(1)口模和芯模。口模用 来成型制品的外表面, 芯模用来成型制品的内 表面。因此,口模和芯 模的定型部分决定了制 品的横载面形状和尺寸。
直角式机头
3.侧向机头(弯管式):来自挤出机的料流 (material flow)先流过一个弯形流道再进 入机头一侧,料流包芯棒后沿机头轴向方向 流出。这种设计可使管材的挤出方向与挤出 机呈任意角度,亦可与挤出机螺杆轴线相平 行。适合大口径管的高速挤出,但机头结构 比较复杂,造价较高。
侧向机头(弯管式)
五. 管材挤出成型机头的简单结构设计
2.1.2 口模内径
(1)经验公式: d1=D/BZ
(2)按拉伸比:
(BZ 为补偿系数)
I
挤出机头口模设计-PPT

3.模具的吊装
2.吊装方式 1)水平尺寸大于拉杆水平距离时,采用侧面滑
入(中小型模具) 2)模具厚度小于拉杆水平间距,将模具长方向
平行拉杆轴线方向,吊入后再旋转90度。 3)整体吊装: 4)分体吊装:起重设备受限时,可采用;先定
筛孔直径 1-2.5mm
熔体压力损失小、结构紧凑,易于装拆、清理 适于流动性好和热稳定性好的聚烯烃类大口径管 材。
螺旋供料机头
星形螺旋供料机头 环形螺旋供料机头
槽深变浅 芯模与外壁间距增大,保证流速一致,均匀 无芯棒支架,无熔接痕。
复式机头
三管机头
小型薄壁管
2.管材挤出机头参数确定
1.成型段长度 口模平直部分长度L1 作用:增加料流阻力,使管材更密实;使 料流稳定均匀,消除熔接痕 L1=(0.5-3.0)ds, L1=nt
成型段长度:棒材直径的4-15倍
无分流锥棒材机头
有强力冷却作 用的定型模
定型模
绝热垫
• 机头压缩角影响表面粗 糙度а=30-60°,出口扩
张角β =45°以下。
• 机头口模定型长度 L= (4-10)d,太短,会挤
出胀大明显,太长,阻
力过大卡滞
大家应该也有点累了,稍作休息
大家有疑问的,可以询问和交流 ‹#›
3)内定径 管材与定径棒直接接触,冷却定径 ,内应力均匀,保证尺寸精度和表面粗糙度
3.管材定型装置
(2)定径模尺寸
长度:管材尺寸、塑料性能、挤出速度、冷 却效果、热传导性能有关
过长—牵引阻力大;过短—冷却不 足易变形
RPVC ds300内,3-6ds, 35mm10ds; PO2-5ds 直径:外定径大0.8-1.2%;内定径大2-4% 锥度:出口直径略小于入口
挤出成型工艺及模具设计

2020/3/31
2020/3/31
三、管材挤出机机头的设计
常用的挤管机头有:直通式、直角式和旁侧式
直通式挤管机头
1-芯棒 2-口模 3-调节螺钉 4-分流器支架 5-分流器 6-加热器 7机头体
2020/3/31
2020/3/31
2020/3/31
挤出机头结构
1-管材 2-定型模 3-口 模 4-芯棒 5-调节螺钉 6-分流器 7-分流器支架 8-机头体 9-过滤网 10电加热圈
④ 压缩角 低粘度塑料45~ 60° ,高粘度塑料30 ~ 50° 。
2020/3/31
(3) 分流器和分流器支架 ① 分流器设计需确定的尺寸
❖分流器的角度α
低粘度塑料30°~80°, 高粘度塑料取30°~60°。
❖分流锥长度L3
L3 =(1~1.5) D0
❖分流器头部圆角半径r
取0.5~2mm
2020/3/31
② 分流器支架
① 支承分流器及芯棒,另外起搅拌物料的作用。 ② 小型机头,分流器和分流器支架可以做成一个整体。 ③ 为了消除塑料通过分流器后形成的接合线,分流器支架
上的分流肋应做成流线型,一般3~8根。 ④ 分流器支架设有进气孔和导线孔,用以通入压缩空气和
内装置电热器时导入导线。
2020/3/31
2020/3/31
④机头内设有调节装置
调节熔体流量、口模和芯棒侧隙、挤出压力、成型温度、 挤出速度等。
⑤合理选择材料
机头的零件要承受熔体的压力作用,所以要有足够的强度 。必要时对连接零件进行强度校核。
与熔体接触的零件要有足够的耐磨性和耐腐蚀性,必要时 表面要镀铬处理。主要零件进行调质处理,硬度45~ 50HRC。
挤出成型机头的设计要点是什么

挤出成型机头的设计要点是什么
挤出成型机是一种常见的塑料加工设备,而挤出成型机头则是整个挤出成型机中非常关键的部件之一。
挤出成型机头的设计直接影响着挤出成型的效率和产品质量。
下面将探讨一下挤出成型机头的设计要点。
首先,挤出成型机头的材质选择非常重要。
由于挤出过程中会受到高温高压的影响,挤出成型机头必须选择耐高温、耐腐蚀的材料。
常见的挤出成型机头材质包括不锈钢、硬质合金等。
合适的材质可以保证挤出成型机头在长时间高强度工作下不易损坏,延长使用寿命。
其次,挤出成型机头的结构设计也至关重要。
挤出成型机头通常包括进料口、螺杆、模具口等部件。
合理的结构设计可以确保料料均匀并且顺畅地挤出,避免产生气泡、流痕等缺陷。
同时,挤出成型机头的结构设计也需要考虑易于清洁和维护,以便日常操作和维护。
另外,挤出成型机头的温控系统也是设计中需要考虑的重点之一。
挤出成型机头需要能够精确控制温度,以确保挤出材料能够在适宜的温度下顺利挤出,避免由于温度不当而导致产品质量下降或者机头过热而损坏的情况发生。
因此,优秀的挤出成型机头设计应该考虑到温控系统的稳定性和精确度。
最后,挤出成型机头的流道设计也是设计要点之一。
挤出成型机头需要经过精密的流道设计,以确保挤出材料的均匀性和稳定性。
一个优秀的流道设计可以减少流变效应对挤出过程的干扰,提高挤出效率和产品质量。
综上所述,挤出成型机头的设计要点包括材质选择、结构设计、温控系统和流道设计等方面。
只有在这些方面都考虑到位,才能设计出性能稳定、效率高的挤出成型机头,为挤出成型工艺提供强有力的支持。
1。
挤出成型机头的设计要点
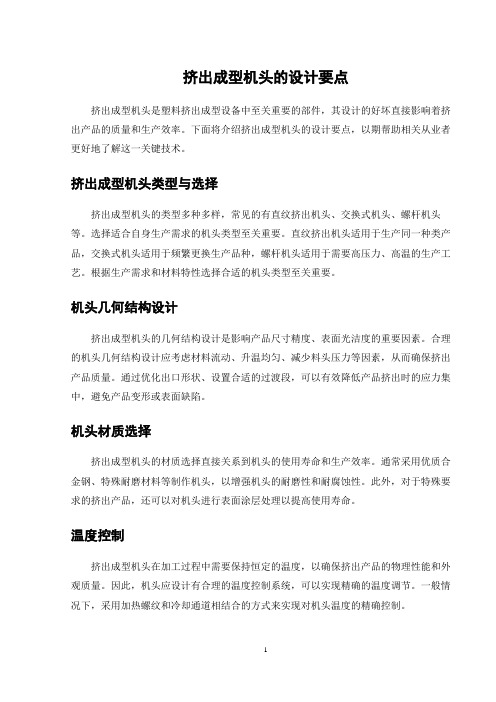
挤出成型机头的设计要点挤出成型机头是塑料挤出成型设备中至关重要的部件,其设计的好坏直接影响着挤出产品的质量和生产效率。
下面将介绍挤出成型机头的设计要点,以期帮助相关从业者更好地了解这一关键技术。
挤出成型机头类型与选择挤出成型机头的类型多种多样,常见的有直纹挤出机头、交换式机头、螺杆机头等。
选择适合自身生产需求的机头类型至关重要。
直纹挤出机头适用于生产同一种类产品,交换式机头适用于频繁更换生产品种,螺杆机头适用于需要高压力、高温的生产工艺。
根据生产需求和材料特性选择合适的机头类型至关重要。
机头几何结构设计挤出成型机头的几何结构设计是影响产品尺寸精度、表面光洁度的重要因素。
合理的机头几何结构设计应考虑材料流动、升温均匀、减少料头压力等因素,从而确保挤出产品质量。
通过优化出口形状、设置合适的过渡段,可以有效降低产品挤出时的应力集中,避免产品变形或表面缺陷。
机头材质选择挤出成型机头的材质选择直接关系到机头的使用寿命和生产效率。
通常采用优质合金钢、特殊耐磨材料等制作机头,以增强机头的耐磨性和耐腐蚀性。
此外,对于特殊要求的挤出产品,还可以对机头进行表面涂层处理以提高使用寿命。
温度控制挤出成型机头在加工过程中需要保持恒定的温度,以确保挤出产品的物理性能和外观质量。
因此,机头应设计有合理的温度控制系统,可以实现精确的温度调节。
一般情况下,采用加热螺纹和冷却通道相结合的方式来实现对机头温度的精确控制。
清洁与维护挤出成型机头在生产过程中容易受到塑料材料残渣的堵塞,因此需要定期清洁和维护。
清洁机头时应谨慎操作,避免损坏机头表面,影响其挤出产品的质量。
定期检查机头的磨损情况,并根据需要进行及时更换。
综上所述,挤出成型机头的设计要点包括机头类型选择、几何结构设计、材质选择、温度控制以及清洁与维护等方面。
只有全面考虑这些因素,合理设计和维护机头,才能确保挤出产品的质量和生产效率,提高生产制造的竞争力。
(第20讲)第四章 第九节 其它挤出机头设计

福建工程学院《塑料成型工艺及模具设计》
第四章 塑料挤塑成型模具
四、塑料网挤出机头 管状塑料网机头:由可分别单独旋转的芯棒和口模外 管状塑料网机头:由可分别单独旋转的芯棒和口模外 组成,口模和芯棒分别开设有相应的半圆孔( 圈组成,口模和芯棒分别开设有相应的半圆孔(或其它 形状孔),其余部分互相密合, ),其余部分互相密合 形状孔),其余部分互相密合,熔体仅能中半圆孔中挤 出(图4-9-6)。
模唇运动:当上、下模唇半圆孔对正时, 模唇运动:当上、下模唇半圆孔对正时,挤出为圆形线 正好形成网的结点,错开时,挤出的为网眼间的网线。 条,正好形成网的结点,错开时,挤出的为网眼间的网线。
福建工程学院《塑料成型工艺及模具设计》 第四章 塑料挤塑成型模具
四、塑料网挤出机头 塑料网孔形式:改变上、下模唇往复运动的方向、速 塑料网孔形式:改变上、下模唇往复运动的方向、 挤出速度则可形成不同的网型( 度、挤出速度则可形成不同的网型(图4-9-5)。
四、塑料网挤出机头 塑料网:分片状和管状塑料网。 塑料网:分片状和管状塑料网。 片状塑料网机头:由上下两片模唇组成, 片状塑料网机头:由上下两片模唇组成,模唇分别设有 相应的半圆孔(或其它断面形状的孔),且相互紧密接触, ),且相互紧密接触 相应的半圆孔(或其它断面形状的孔),且相互紧密接触, 下模唇可单独或同时做方向相反的往复运动。 上、下模唇可单独或同时做方向相反的往复运动。
塑料网孔形式:改变芯棒和口模圈的回转方向、 塑料网孔形式:改变芯棒和口模圈的回转方向、回转速 挤出速度则可形成不同的网型( 度、挤出速度则可形成不同的网型(图4-9-5)。
福建工程学院《塑料成型工艺及模具设计》 第四章 塑料挤塑成型模具
四、塑料网挤出机头 管状塑料网机头:图4-9-7所示;挤出设备见图4-9-8。 管状塑料网机头: 所示;挤出设备见图4
- 1、下载文档前请自行甄别文档内容的完整性,平台不提供额外的编辑、内容补充、找答案等附加服务。
- 2、"仅部分预览"的文档,不可在线预览部分如存在完整性等问题,可反馈申请退款(可完整预览的文档不适用该条件!)。
- 3、如文档侵犯您的权益,请联系客服反馈,我们会尽快为您处理(人工客服工作时间:9:00-18:30)。
k''wm
(11-
2)
于为是,根据k公式(m11-12)和k上'式' ,k被表示 3
(11-3)
11.2.3.管材挤出成型机头工艺参数的确定
又根据公式 k ' 4k 可得 m3
(11-4)
k'' 3m9 k' 4m8
上式表明了 缝形口模k’’和圆形口模的K
材
均可
均可
11.2.3.管材挤出成型机头工艺参数的确定
1.口模定型段长度L值的确定
图11-7挤管机头属于环隙孔,对于环隙 孔内径大于3/5外径时,物料的流动形式 属于一维的特殊形式.
薄片形缝隙口模
w
ph 2L
,rw
6Q wh 2
通过rw k''wm
式可得:
11.2.3.管材挤出成型机头工艺参数的确定
11.2.2 管材挤出成型机头典型结构
11.2.3 管材挤出成型机头工艺参数的确 定
11.2.4 管材定型套设计
11.2.1. 概述
挤管成型模具包括机头和定型模.塑料 的制品断面形状为圆形管材形状.图( 11-2)
图(11-3)为spvc机头典型结构及挤 出spvc管材的典型生产工艺过程.
11.2.1. 概述
❖ 了解各种挤出机头的各组成机构及其功 能;
❖ 交接各种挤出机头的工作原理。
第11章 挤出成型及机头设计 教本学章重重点点
❖ 管材挤出机头设计; ❖ 板材与片材挤出机头设计; ❖ 异性材挤出机头设计。
第11章 挤出成型及机头设计 本章难点
❖ 各种挤出机头的设计 ❖ 读懂各种挤出机头的结构图
第11章 挤出成型及机头设计
11.1.2 挤出成型机头设计原理
机头设计原则: 1 、机头流道呈光滑流线型,以减少流动
阻力,使物料沿着机头流道充满并均匀地 挤出,同时避免物料发生过热分解. 2 、为使制品密实和消除因分流器支架造 成的分流痕迹,物料应有足够的压缩比. 3 、要考虑塑料各物理性能和生产工艺性 能对制品断面形状和尺寸的影响,设计正 确合理的机头断面形状和尺寸.
w6Qh2 k& ' ——系数,相当于圆型口模的
k ' 'w ——窄缝流道之宽(按环隙缝平
均直径换算)
h ——窄缝流动的缝隙高(即薄壁 管机头口模的圆环单面间隙)
11.2.3.管材挤出成型机头工艺参数的确定
熔得体,在缝Q隙流k道'' 2的mw流1(动hm m可2由2p式)mrLwm
11.2.2.管材挤出成型机头典型结构
常见的管材挤出成型机头有以下三种形 式。
1、直通式机头,又称平式机头,如图( 11-4),机头内的熔料挤出方向与挤 出机螺杆轴线方向平行或一致,它是 最简单,最经济,最常用的机头。缺点 是分流器支架产生的分流痕迹难以消除 。
11.2.2.管材挤出成型机头典型结构
11.1.1 挤出成型机头典型结构分析
机头挤出成型模具的主要部件,它有下 述四种作用:
(1) 使物料由螺旋运动变为直线运动 ;
(2)产生必要的成型压力,保证制品密 实;
(3)使物料通过机头得到进一步塑化; (4)通过机头成型所需要的断面形状;
11.1.1 挤出成型机头典型结构分析
我们以管材为例,分析机头的组成 零件及各组成零件的作用. 管材机头主要由下面一些零件组成(见 图11-1)
现将三种机头的特性列于表(11-1)
11.2.2.管材挤出成型机头典型结构
表11-1 机头特性表
直通机头 直教机头 侧式机头
机头熔料方 与螺杆轴 与螺杆轴线 与螺杆轴线
向
线一致 垂直
平行
机头结构 简单
复杂
复杂
分流器支架 有
无
无
定型长度 应该长 不需太长 不需太长
芯模加热 较困难 容易
容易
挤出口径
小口径管 大、小口径 大小、口径
2、直角式机头,又称十字机头或弯机头 ,如图(11-5)、机头内的熔料挤出方 向成90直角,可以有效地消除分流器所 产生的分流痕,提高产品质量,缺点是 芯模设计,加工,安装困难。
11.2.2.管材挤出成型机头典型结构
3、侧式机头,又称管式机头,如图( 11-6),由挤出机的熔料到机头要 经过两次转向(90°或45 ° ),并以 平行于螺杆轴线的方向挤出,优点是 加强了溶料塑化,提高了产品质量, 适于生产大口径管。缺点是结构复杂 ,模具成本高。
11.1 挤出成型机头概论 11.2 管材挤出成型及机头设计 11.3 板材和片材挤出成型及机头设计 11.4 吹塑薄膜挤出成型机头设计 11.5 电线电缆挤出成型及机头设计 11.6 导型材挤出成型及机头设计 11.7 思考题
11.1 挤出成型机头概论 11.1.1 挤出成型机头典型结构分析 11.1.2 挤出成型机头设计原理
11.1.2 挤出成型机头设计原理
4 、在在满足强度条件下,机头结构应紧凑并 便于装配和拆卸,连接处应严密,防止漏料 ,其形状尽量对称,使传热均匀.
5 、由于机头磨损大,应合理选用材料,常选 用硬度教高,耐磨,耐腐蚀,高温不变形的 钢材及合金钢,有的甚至需要镀铬来提高其 耐磨性和抗腐蚀能力.
11.2 管材挤出成型及机头设计 11.2.1 概述
挤出成型及机头设计
第11章 挤出成型及机头设计
本章基本内容
❖ 挤出机头概述 ❖ 管材挤出机头设计 ❖ 板材与片材挤出机头设计 ❖ 吹塑薄膜挤出机头设计 ❖ 电线电缆挤出机头设计 ❖ 异型材挤出机头设计
第11章 挤出成型及机头设计
学习目的与要求
❖ 掌握挤出模(机头)的概念和总体结构 ;
❖ 掌握各种组成挤出机头零件名称和结构 ;
1、口模
口模用以成型制品的外表面。
2、芯模 芯模用以成型制品的内表面。
11.1.1 挤出成型机头典型结构分析
3、分流器 熔融塑料通过分流器分流形成管状制品 的胚形,并在剪切力的作用下进一步加 热塑化.
4 、分流器支架
5 、滤网板
11.1.2 挤出成型机头设计原理
我们可以将机头依次人为的分为几个部分: 1 、入口部分 2 、展开部分 3 、分流部分和压缩部分 4 、定型部分
管材挤出成型过程: 熔融塑料由挤出机挤出后,经过滤网板
,分流器,被分流器支架分成若干股,然 后再汇合,最后进入芯模和口模形成的环 形通道挤出连续的管胚,硬管在定型模和 冷却装置的作用下冷却成型,经牵引切割 装置成为所需产品,软管可不需定型模。 直接由冷却装置冷却定型,再由牵引,切 割,卷取装置收卷为所需产品。