无损检测工艺流程图文稿
无损检测工艺规程范本(液体渗透)实用文档系列
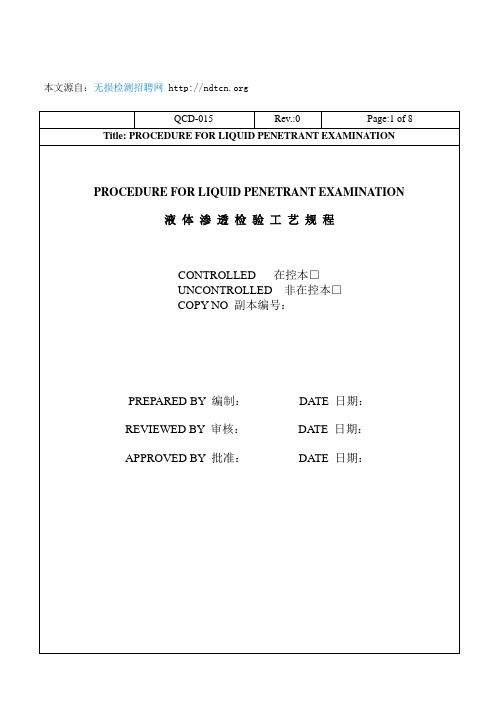
Title: PROCEDURE FOR LIQUID PENETRANT EXAMINATION 1. General 1.1 This procedure is applied to dye liquid penetrant examination of metal material and weldment for ASME Code items. 1.2 This procedure is only suitable for detecting the defects that are open to the surface of material or weldment. 1.3 This procedure shall be demonstrated to the satisfaction of the AI prior to implementation. 2. Personnel 2.1 The personnel engaged in the penetrant examination shall be qualified and certified in accordance with the requirement of NJBST Co., Ltd.’s“Written Practice for NDE Personnel Training Examination, Qualification and Certification”(No.:QCD-011). 3. Penetrant Materials 3.1 The penetrant materials is intended to include all penetrants, solvents or cleaning agents, developers, etc, used in the examination process. 3.2 The liquid penetrant examination materials shall be designated and recommended, as shown in Table 3.2. The materials used for examination shall be the same type. Intermixing of penetrant materials from different families or different manufacturers is not permitted. Table 3.2 Manufacturer Material Model Shanghai Penetrant HD-RS
无损检测渗透探伤(PT)工艺流程

无损检测渗透探伤(PT)工艺流程第七章渗透检测工艺渗透检测工艺基本步骤:1、表面准备和预清洗(洗涤剂清洗,温度75℃~95℃时,10~15分钟)2、施加渗透剂(10~50℃下,渗透时间≥10min)3、多余渗透剂的去除4、干燥(不得大于50℃,干燥时间5~10min)5、施加显像剂(自显像时间10~120min,其他显像时间一般不少于7min)6、观察与评定(显像剂施加后7~60min内进行)7、后清洗及复验渗透检测的时机选择:1、机加工和热处理等操作,可能产生表面缺陷,渗透检测则应在这些工序后进行。
对有延迟裂纹倾向的材料,至少应在焊后24小时进行焊接接头的渗透检测。
2、表面处理工艺(喷漆、镀层、阳极化、涂层、氧化、喷丸和研磨)的操作,渗透检测应在这些工序前进行,表面处理后需机加工的,对该加工部位再次进行渗透检测。
3、工件要求腐蚀检测时,应在腐蚀工序后进行。
4、在役工件的渗透检测应去除表面积炭和油漆层。
但阳极化层可不去除。
表面准备和预清洗渗透检测成功与否,取决于被检表面的状况(污染程度及粗糙度)。
所有污染物都会阻碍渗透剂进入缺陷,清洗污染物的过程中的残留物反过来也能同渗透剂反应,影响渗透检测的灵敏度。
被检表面的粗糙度影响渗透检测效果。
内容:清理固体污染物+液体污染物固体污染物:铁锈、氧化皮、腐蚀产物、焊接飞溅、焊渣、毛刺、油漆及涂层等液体污染物:防锈油、机油、润滑油及有机组分的其它液体,强酸强碱及包括卤素在内的有化学活性的残留物基本要求:1、任何可影响渗透检测的污染物必须清除干净,不得损伤受检工件的工作功能:例如:不得用钢丝刷打磨铝、镁、钛等软合金。
密封面不得进行酸蚀处理等。
2、表面准备和预清洗范围:检测部位四周25mm。
▲通常情况下,焊缝、轧制件、铸件、锻件的表面状态,是可以满足渗透检验要求的。
▲如果焊缝、轧制件、铸件、锻件的表面出现不规则,影响渗透探伤效果。
则应用打磨方法或机械加工方法进行表面处理。
无损检测流程图

起重机无损检测的一般流程
B1.资料审查
资料审查应包括下列内容:
B1.1产品合格证、质量证明书、竣工图。
B1.2设备的运行记录,有关运行参数,使用环境,载荷变化情况,以及运行中出现的异常情况等资料。
B1.3检验资料、历次检验检测报告和记录。
B1.4有关修理和改造的文件
B2.技术准备
检测开始前,应作好以下准备工作:
B2.1现场勘察,了解设备的现场情况,确定实施检测的条件。
目视检查设备使用中产生的宏观缺陷,尤其是主要受力部位。
B2.2制定相应检测方案并经过设备使用单位确认。
使用单位应积极配合,提供安全可靠的检测现场。
B2.3检测仪器的选择与确定。
确保现场可安全实施的便携检测仪器。
校准需要校准的仪器设备。
B2.4检测人员与资质的确定。
B3.检测
根据检测方案确定检测方法与实施的流程
B3.1起重机械无损检测方法实施的一般流程为:(见下框图)
B3.2现场检测记录
检测数据应记录完整并保存,填写检测原始记录表。
B3.3根据缺陷所在部位及材料对检测数据进行分析,评估缺陷的安全性,得出无损检测评估结论。
并出具相应无损检测报告书。
无损检测工艺方案
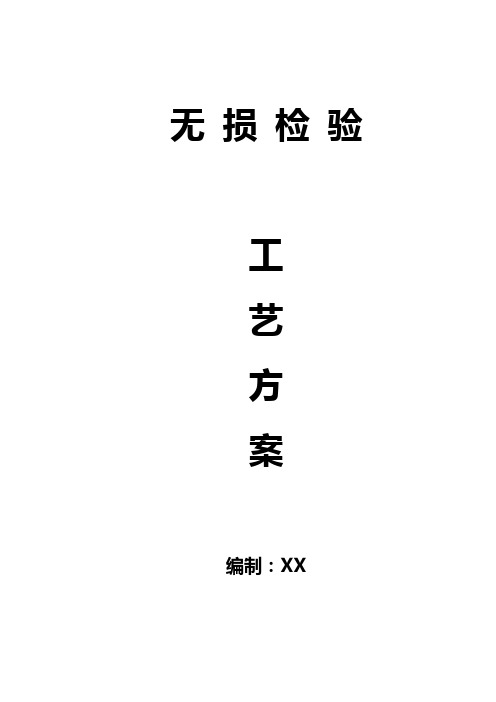
无损检验工艺方案编制:XX目录总则工程概况编制依据检测工序检测人员的资格要求检测部位的状态射线检验方案着色检验方案磁粉检验方案检验记录、报告及底片检测人员的数量检测主要设备、材料质量保证措施安全施工保证措施1.总则本方案是用于XX工程施工过程中无损检测的指导性文件。
施工过程中遇到本方案未涉及问题的处理参见设计图纸和相关技术标准。
2.工程概况XX位于上海市漕泾化学工业园区内,装置共分为生产车间、管廊、罐区1、罐区2、装桶间、装卸站台等6个区域,该工程的无损检测特点为:管道焊口小,底片编号复杂,施工质量要求高,拍片难度大.3.编制依据1)德希尼布天辰公司提供的拜尔涂料系统上海有限公司聚异氰酸酯装置安装工程的招标文件及附图2)德希尼布天辰公司提供的工艺管道施工图3)德希尼布天辰公司提供的管道安装布置及设计说明4)GB50235 工业金属管道工程施工及验收规范。
5)JB4730 压力容器无损检验6)GB50236 现场设备、工业管道焊接工程施工及验收规范7)GB 4792 放射卫生防护基本标准8)GB 6417 金属熔化焊焊缝缺陷分类及说明9)GB 9445 无损检测人员技术资格鉴定规则4.检测工序无损检测工序如图1所示图1:无损检测工序图5.检验人员1)从事射线检验的人员,必须持有国家有关部门颁发的,并与其工种和级别相适应的资格证书,同时,亦需持有国家卫生防护部门颁发的射线安全操作资格证书。
2)底片评判人员必须具有Ⅱ、Ⅲ级资格证书。
6.检测部位的状态1)焊缝及热影响区的表面质量(包括余高高度)应经外观检查合格。
表面的不规则状态在底片上的图象应不掩盖焊缝中的缺陷或与之相混淆,否则应做适当的修正。
2)多层多道手工施焊的横焊焊缝其余高应进行打磨,以满足焊缝质量评定的要求。
7.射线检验方案1)执行标准与合格等级a)JB4730 压力容器无损检验检验质量AB级合格级别Ⅱ级。
b)本方案不包括管子厚度大于8mm 的焊缝的射线检验。
无损检测工艺规程(对接焊缝射线)-17页文档资料
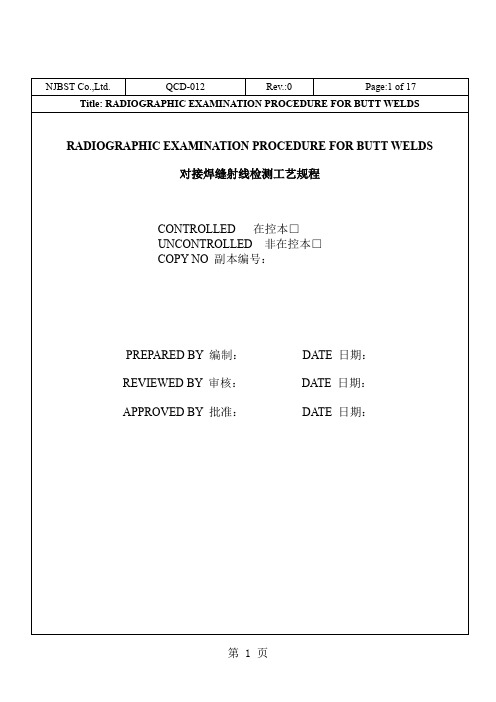
1.1 This procedure is applied to the x-ray radiographic examination of butt welds for pressure vessels constructed in accordance with ASME Code SectionⅧDiv1.
2.3 According to the respective responsibility range, all examiners shall complete the examination conforming to the referencing ASME Code Sections, standards and written instructions. They shall assure the working quality.
2.2 The NDE LevelⅠshall receive the necessary instruction or supervision from a certified NDE LevelⅡor LevelⅢExaminer. The NDE LevelⅡshall receive the instruction or supervision from a NDE LevelⅢExaminer.
3. Equipment , Tools and Materials
The LevelⅡExaminer shall select the equipment, tools and materials to assure that they are in compliance with the following conditions and the requirement of the examination instruction.
无损检测工艺——无损检测工艺资料文档
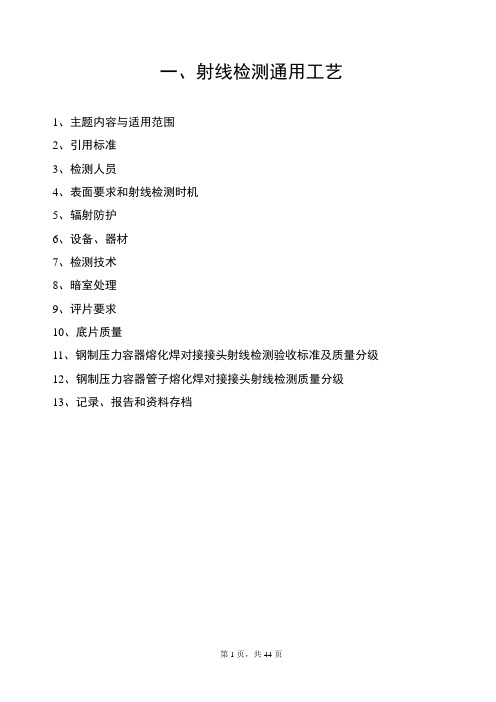
一、射线检测通用工艺1、主题内容与适用范围2、引用标准3、检测人员4、表面要求和射线检测时机5、辐射防护6、设备、器材7、检测技术8、暗室处理9、评片要求10、底片质量11、钢制压力容器熔化焊对接接头射线检测验收标准及质量分级12、钢制压力容器管子熔化焊对接接头射线检测质量分级13、记录、报告和资料存档1主题内容与适用范围1.1 本规程规定了钢制压力容器熔化焊对接焊接接头射线检测应具备的人员资格、所用器材、检测工艺和验收标准等。
1.2 本规程依据JB/T4730.2-2021标准的要求编写。
适用于板厚2~200mm的碳素钢、低合金钢、不锈钢制压力容器和钢管熔化焊对接接头的X射线AB级检测技术和质量分级要求。
满足《容规》和GB150的要求。
1.3 检测工艺卡是本规程的补充,由Ⅱ级检测人员按合同要求进行编写。
2 引用标准JB/T 4730-2021 承压设备无损检测GB 16357-1996 工业X射线探伤放射卫生防护标准GB 18871-2021 电离辐射防护与辐射源安全防护要求JB/T 7902-1999 线型像质计JB/T 7903-1999 工业射线照相底片观片灯HB 7684-2000 射线照相用线型像质计GB/T 19384-2021 无损检测工业射线照相胶片3 检测人员3.1 检测人员必须经过技术培训,按《特种设备无损检测人员考核与监督管理规则》进行考核,取得与其工作相适应的资格证书的人员担任。
3.2 从事射线检测的人员上岗前应进行辐射安全知识的培训,并取得放射工作人员证。
3.3 从事评片的人员应每年检查一次视力,校正视力不低于1.0。
4 表面要求和射线检测时机4.1 在射线检测之前,对焊接接头的表面应经外观检测并合格。
焊接接头表面的不规则状态在底片上的影像不得掩盖或干扰缺陷影像,否则应对表面作适当修磨。
4.2 一般射线检测应在焊后进行,对有延迟裂纹倾向的材料,至少应在焊接完成24h后进行。
无损检测工艺流程
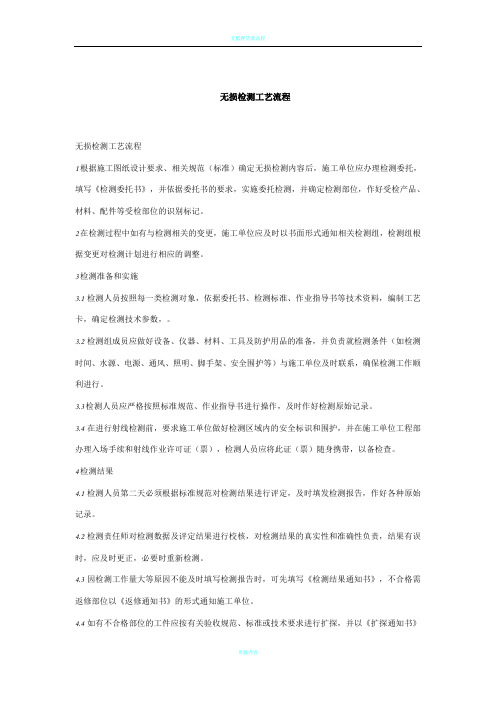
无损检测工艺流程无损检测工艺流程1根据施工图纸设计要求、相关规范(标准)确定无损检测内容后,施工单位应办理检测委托,填写《检测委托书》,并依据委托书的要求,实施委托检测,并确定检测部位,作好受检产品、材料、配件等受检部位的识别标记。
2在检测过程中如有与检测相关的变更,施工单位应及时以书面形式通知相关检测组,检测组根据变更对检测计划进行相应的调整。
3检测准备和实施3.1检测人员按照每一类检测对象,依据委托书、检测标准、作业指导书等技术资料,编制工艺卡,确定检测技术参数,。
3.2检测组成员应做好设备、仪器、材料、工具及防护用品的准备,并负责就检测条件(如检测时间、水源、电源、通风、照明、脚手架、安全围护等)与施工单位及时联系,确保检测工作顺利进行。
3.3检测人员应严格按照标准规范、作业指导书进行操作,及时作好检测原始记录。
3.4在进行射线检测前,要求施工单位做好检测区域内的安全标识和围护,并在施工单位工程部办理入场手续和射线作业许可证(票),检测人员应将此证(票)随身携带,以备检查。
4检测结果4.1检测人员第二天必须根据标准规范对检测结果进行评定,及时填发检测报告,作好各种原始记录。
4.2检测责任师对检测数据及评定结果进行校核,对检测结果的真实性和准确性负责,结果有误时,应及时更正,必要时重新检测。
4.3因检测工作量大等原因不能及时填写检测报告时,可先填写《检测结果通知书》,不合格需返修部位以《返修通知书》的形式通知施工单位。
4.4如有不合格部位的工件应按有关验收规范、标准或技术要求进行扩探,并以《扩探通知书》的形式通知施工单位。
5底片质量;5.1所有底片上,定位和识别标记影像应显示完整、位置正确。
5.2底片评定范围内的黑度D应符合AB级要求:2.0-4.0之间。
5.3底片本底灰雾度D0<0.3。
5.4底片的像质计灵敏度应符合JB/T4730-2005《承压设备无损检测标准》要求。
5.5底片评定范围内不应存在干扰缺陷影像识别的水迹、划伤、斑纹等伪缺陷影像。
无损检测工艺方案(定稿)学习资料

本方案适用于东明石化集团公司10万吨/年离子莫烧碱装置安装工程的工艺管道、容器及钢结构等的无损检测。
无损检测方法有射线检测(RT)、超声波检测(UT)和磁粉检测(MT)渗透检测(PT),按要求选择相应的方法。
1 编制依据及执行标准1.1 GB50235-97《工业金属管道工程施工及验收规范》1.2 GB50236-98《现场设备、工艺管道焊接工程施工及验收规范》1.3 SH3501-2002《石油化工有毒、可燃介质管道工程施工及验收规范》1.4 GB16357-1996《工业X射线探伤放射卫生防护标准》1.5 GB50205-2001《钢结构工程施工及验收规范》1.6 JB/T4730.1~4730.6-2005《承压设备无损检测》1.7 GB11345-89《钢焊缝手工超声波探伤方法和探伤结果分级》2 检测方法、检测比例及评定标准东明石化集团公司10万吨/年离子莫烧碱装置安装工程检测比例按规范及施工图要求执行,选用何种检测方法按施工技术要求及委托书决定,其评定标准为JB/T4730.1~4730.6-2005《承压设备无损检测》或GB11345-89《钢焊缝手工超声波探伤方法和探伤结果分级》。
3 检测人员的要求及配置3.1 检测人员必须是经培训并按照国家质量监督检验检疫总局文件“国质检锅[2003]248号”《特种设备无损检测人员考核与监督管理规则》进行考核取得Ⅰ、Ⅱ、Ⅲ级检验资格证,才能从事与所持资格证级别相应的无损检测工作,并负相应的技术责任。
3.2 检测人员的校正视力不得低于1.0,应按规定体检合格后才能上岗。
从事渗透检测工作的人员,不得有色盲、色弱。
3.3 根据该工程安装工作量及其工期,配置相应的各级别无损检测人员,以满足顾客要求为主,及时完成检测任务。
4 设备的配置4.1 X射线机:4台4.2 超声波检测仪:1台4.3 磁粉探伤仪:1台4.4 观片灯:2台4.5 黑度计:1台4.6 铝合金及镀铬渗透检测对比试块1套,A1-30/100型磁粉检测试片一套4.7 承压设备超声波检测试块:CSK-ⅠA、ⅢA试块一套;钢结构: RB-3试块一块4.8 切片刀:1把5 工件表面要求射线检测:焊缝表面的不规则状态在底片上的影象应不掩盖焊缝中的缺陷或与之相混淆,否则应做适当的修磨。
无损检测工作流程
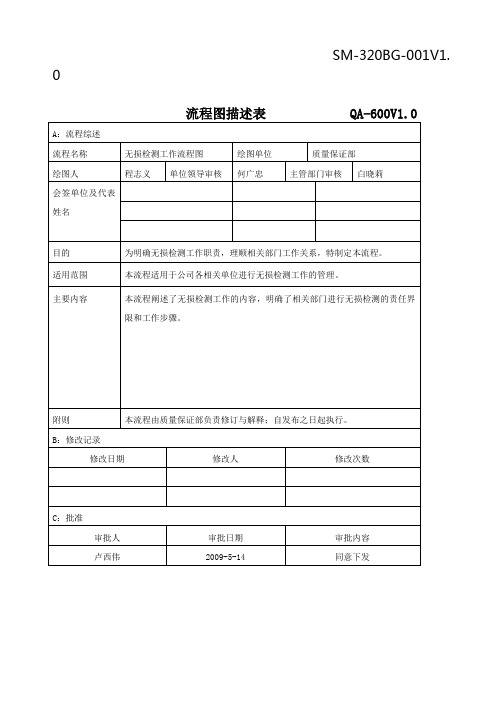
本流程阐述了无损检测工作的内容,明确了相关部门进行无损检测的责任界限和工作步骤。
附则
本流程由质量保证部负责修订与解释;自发布之日起执行。
B:修改记录
修改日期
修改人
修改次数
C:批准
审批人
审批日期
审批内容
卢西伟
2009-5-14
同意下发
D:业务说明
业务名称
职责人
确认时间
责任部门
业务目标
QA-600-010
制定无损检测技术规范
无损检测工程师
产品开工前
质量保证部
按照相关标准,制定无损检测技术规范,明确无损检测技术总体要求。
QA-600-020
设计图纸
设计师
图纸设计阶段
技术中心
保证设计图纸/文件符合标准要求
QA-600-030
无损检测工艺及无损检测标准审核
无损检测工程师
图纸设计阶段
技术通知会签时
质量保证部
工艺路线划分时
各制造中心
划分无损检测工艺路线,明确无损检测工序。
QA-600-070
无损检测技术准备
无损检测工程师
图纸发布后,产品开工前5个工作日完成
质量保证部
对图纸进行分析,做好产品无损检测技术准备,保证无损检测工艺可行。
QA-600-080
编制无损检测文件
无损检测工程师
图纸发布后,产品开工前5个工作日完成
按照无损检测技术规范,对设计图纸(含技术通知)进行审核。
QA-600-040
满足标准要求?
无损检测工程师
图纸设计阶段
质量保证部
保证设计图纸(含技术通知)/文件符合标准要求。
QA-600-050图纸返回
无损检测PXUT-350+简易操作步骤与报告-焊缝、锻件、钢板
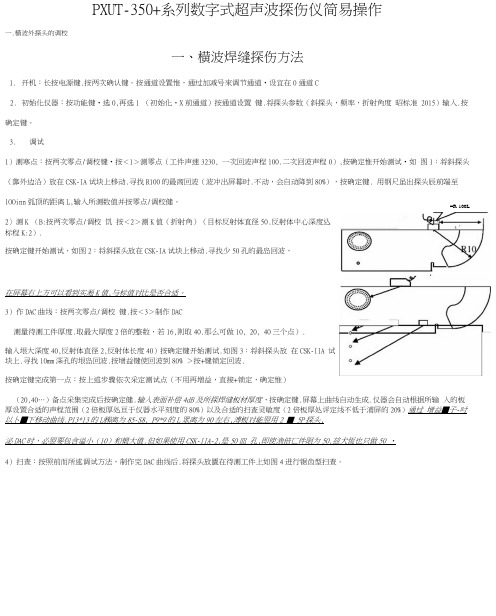
PXUT-350+系列数字式超声波探伤仪简易操作一.横波外探头的调校一、横波焊缝探伤方法1.开机:长按电源键.按两次确认键。
按通道设置惟,通过加减号來调节通道•设宜在0通道C2.初始化仪器:按功能键•选0,再选1 (初始化・X前通道)按通道设置键.将探头参数(斜探头,频率,折射角度昭标准2015)输入.按确定键。
3.调试1)测寒点:按两次零点/调校键•按<1>测零点(工件声速3230, 一次回波声程100.二次回波声程0),按确定惟开始测试•如图1:将斜探头(靠外边沿)放在CSK-IA试块上移动.寻找R100的最商回波(波冲出屏幕时.不动,会自动降到80%),按确定键. 用钢尺虽出探头辰前端至lOOinn弧顶的距离L,输入所测数值并按零点/调校健。
=R-100L 2〉测K (B:按两次零点/调校饥按<2>测K值(折射角)(目标反射体直径50.反射体中心深度込标程K:2).按确定键开始测试,如图2:将斜探头放在CSK-IA试块上移动.寻找少50孔的最岛回波,在屏幕右上方可以看到实淞K值,与标值对比是否合适。
3)作DAC曲线:按两次零点/调校键.按<3>制作DAC测量待测工件厚度.取最大厚度2倍的整数,若16,则取40.那么可做10, 20, 40三个点).输入垠大深度40,反射体直径2,反射体长度40)按确定键开始测试.如图3:将斜探头放在CSK-IIA 试块上.寻找10mm深孔的垠岛回波.按增益键使回波到80% >按+键锁定回波.按确定键完成第一点:按上述步骤依次采定测试点(不用再増益,直接+锁定,确定惟)(20,40…)备点采集完成后按确定健.输入表面补偿4dB及所探焊缝板材厚度、按确定键.屏幕上曲线自动生成.仪器会自动根据所输入的板厚设置合适的声程范围(2倍板厚处亘于仪器水平刻度的80%)以及合适的扫査灵敏度(2倍板厚处评定线不低于浦屏的20%)通过增益■子-吋以卜■下移动曲线.P13*13的L㈱离为85-S8, P9*9的L眾离为90左右,溥板对能翌用2 ■ 5P探头,泌DAC时,必翌要包含谥小(10)和锻大值.但如果使用CSK-IIA-2,是50皿孔,即使漁倍匸件限为50,兹犬恆也只做50 •4)扫查:按照前而所述调试方法,制作完DAC曲线后.将探头放匱在待测工件上如图4进行锯齿型扫查。
无损检测et流程
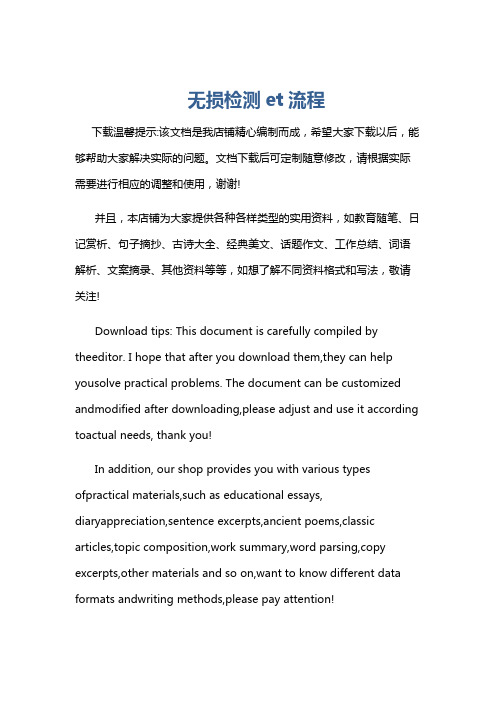
无损检测et流程下载温馨提示:该文档是我店铺精心编制而成,希望大家下载以后,能够帮助大家解决实际的问题。
文档下载后可定制随意修改,请根据实际需要进行相应的调整和使用,谢谢!并且,本店铺为大家提供各种各样类型的实用资料,如教育随笔、日记赏析、句子摘抄、古诗大全、经典美文、话题作文、工作总结、词语解析、文案摘录、其他资料等等,如想了解不同资料格式和写法,敬请关注!Download tips: This document is carefully compiled by theeditor. I hope that after you download them,they can help yousolve practical problems. The document can be customized andmodified after downloading,please adjust and use it according toactual needs, thank you!In addition, our shop provides you with various types ofpractical materials,such as educational essays, diaryappreciation,sentence excerpts,ancient poems,classic articles,topic composition,work summary,word parsing,copy excerpts,other materials and so on,want to know different data formats andwriting methods,please pay attention!无损检测 et 流程一、检测前准备阶段在进行无损检测之前,需要进行一系列准备工作。
企业无损检测通用工艺文件

企业无损检测通用工艺文件1、内容与适用范围2、引用标准3、检测人员资格及防护4、检测设备、器材和材料5、检测部位表面准备6、检测时机7、检测工艺及技术8、暗室处理9、底片质量10、检测结果的评定和质量等级分类11、检测记录、报告和资料存档1 内容与适用范围1.1 本规程规定了焊缝射线检测人员应具备的资格、所用器材、检测工艺和验收标等。
1.2 本规程依据JB/T4730-2005的要求编写。
适用于2-45㎜钢制承压设备的熔化焊对接接头和壁厚大于等于2㎜的钢制承压设备管子及压力管道的熔化焊环向列接接头X射线,AB级检测技术。
满足《压力容器安全技术监察规程》和GB150-2011的要求。
1.3 检测工艺是本规程的补充,由II级人员按要求编写,其参数有具体规定。
2 引用标准JB/T4730-2005 《承压设备无损检测》GB150-2011 《钢制压力容器》GB16357-1996 《工业X射线探伤放射卫生防护标准》JB/T7902-1999 《线型像质计》JB/T7903-1999 《工业射线照相底片观片灯》3 检测人员资格及防护3.1 检测人员必须经过技术培训,按《特种设备无损检测人员考核与监督管理规则》的要求取得相应的无损检测资格。
3.2 射线检测人员未经矫正或经矫正的视力应不低于5.0,从事评片人员应每年检查一次。
3.3 从事射线检测人员上岗前,应进行辐射安全知识的培训,并取得放射工作人员证。
3.4 射线防护应符合GB16357-1996。
4 检测设备、器材和材料4.1 射线机和能量的选择4.1.1 现使用设备见表1表1制造厂型号有效焦点(mm) 透照厚度范围( mm) 备注日本EX-300GH-3C l.0³2.5 2-45 定向比利时SITE-X SCU286 5³0.5 2-40 周向4.1.2 X射线照相应尽量选用较低的管电压。
在采用较高管电压时,应保证适当的曝光量。
- 1、下载文档前请自行甄别文档内容的完整性,平台不提供额外的编辑、内容补充、找答案等附加服务。
- 2、"仅部分预览"的文档,不可在线预览部分如存在完整性等问题,可反馈申请退款(可完整预览的文档不适用该条件!)。
- 3、如文档侵犯您的权益,请联系客服反馈,我们会尽快为您处理(人工客服工作时间:9:00-18:30)。
无损检测工艺流程集团文件版本号:(M928-T898-M248-WU2669-I2896-DQ586-M1988)无损检测工艺流程无损检测工艺流程1根据施工图纸设计要求、相关规范(标准)确定无损检测内容后,施工单位应办理检测委托,填写《检测委托书》,并依据委托书的要求,实施委托检测,并确定检测部位,作好受检产品、材料、配件等受检部位的识别标记。
2在检测过程中如有与检测相关的变更,施工单位应及时以书面形式通知相关检测组,检测组根据变更对检测计划进行相应的调整。
3检测准备和实施3.1检测人员按照每一类检测对象,依据委托书、检测标准、作业指导书等技术资料,编制工艺卡,确定检测技术参数,。
3.2检测组成员应做好设备、仪器、材料、工具及防护用品的准备,并负责就检测条件(如检测时间、水源、电源、通风、照明、脚手架、安全围护等)与施工单位及时联系,确保检测工作顺利进行。
3.3检测人员应严格按照标准规范、作业指导书进行操作,及时作好检测原始记录。
3.4在进行射线检测前,要求施工单位做好检测区域内的安全标识和围护,并在施工单位工程部办理入场手续和射线作业许可证(票),检测人员应将此证(票)随身携带,以备检查。
4检测结果4.1检测人员第二天必须根据标准规范对检测结果进行评定,及时填发检测报告,作好各种原始记录。
4.2检测责任师对检测数据及评定结果进行校核,对检测结果的真实性和准确性负责,结果有误时,应及时更正,必要时重新检测。
4.3因检测工作量大等原因不能及时填写检测报告时,可先填写《检测结果通知书》,不合格需返修部位以《返修通知书》的形式通知施工单位。
4.4如有不合格部位的工件应按有关验收规范、标准或技术要求进行扩探,并以《扩探通知书》的形式通知施工单位。
5底片质量;5.1所有底片上,定位和识别标记影像应显示完整、位置正确。
5.2底片评定范围内的黑度D应符合AB级要求:2.0-4.0之间。
5.3底片本底灰雾度D0<0.3。
5.4底片的像质计灵敏度应符合JB/T4730-2005《承压设备无损检测标准》要求。
5.5底片评定范围内不应存在干扰缺陷影像识别的水迹、划伤、斑纹等伪缺陷影像。
5.6资料的归档:所有检测工程结束后,检测报告和底片图纸及各种原始记录应整理交公司存档,若用户需要,也可交用户保管,底片保存期为7年。
5.7随时接受并积极配合业主、监理、施工单位、质量监督部门进行的监督检查,并提供所需的检测资料和相关材料。
射线检测通用工艺规程射线检测通用工艺规程1.主题内容与适用范围本规程规定了焊缝射线人员具备的资格、所用器材、检测工艺和验收标准等内容。
本规程依据JB/T4730-2005的要求编写。
适用于本公司板厚在2~30 mm钢制压力容器及壁厚T≥2mm钢管对接焊接接头的X射线AB级检测技术。
满足《压力容器安全技术监察规程》 GB150、GB151 的要求。
检测工艺卡内容是本规程的补充,由Ⅱ级人员按本规程等要求编写,其参数规定的更具体。
2.引用标准、法规JB/T4730-2005《承压设备无损检测》GB150-1998《钢制压力容器》GB151-1999《管壳式换热器》GB18871-2002《电离辐射防护及辐射源安全基本标准》GB16357-1996《工业X射线探伤放射卫生放护标准》JB/T7902《线型象质计》《特种设备无损检测人员考核与监督管理规则》《压力容器安全技术监察规程》.3.一般要求3.1射线检测人员必须经过技术培训,按《特种设备无损检测人员考核与监督管理规则》考核并取得与其工作相适应的资格证书。
≮1.0。
评片人员还应辨别出400mm距离处高0.5mm、间距0.5mm的一组印刷字母。
3.2辐射防护射线防护应符合GB18871、GB16357的有关规定。
3.3胶片和增感屏3.3.2 增感屏:采用前屏为0.03mm、后屏为0.03~0.10mm的铅箔增感屏。
.3.3.3 胶片和增感屏在透照过程中应始终紧密接触。
3.4象质计3.4.1 底片影像质量采用Fe线型像质计测定。
其型号和规格应符合JB/T7902的规定。
象质计型号一般按下表4选定。
但对透照外径≤100mm 钢管环缝时采用JB/T4730附录F的专用象质计。
3.4.2 底片的象质计灵敏度选用按透照厚度及不同的透照方法选择表1至表3中要求达到的象质丝号。
3.4.3 透照厚度W:射线照射方向上材料的公称厚度。
多层透照时, 透照厚度为通过的各层材料公称厚度之和。
焊缝两侧母材厚度不同时,以薄板计。
表1 象质计灵敏度值-单壁透照、象质计置于源侧 (AB级)表2 象质计灵敏度值-双壁双影透照、象质计置于源侧 (AB级)表3 象质计灵敏度值-双壁单影或双壁双影透照、象质计置于胶片侧 (AB级)表43.4.4 象质计的使用象质计一般应放在工件源侧表面焊接接头的一端(在被检区长度的1/4左右位置),金属丝应横跨焊缝,细丝置于外侧。
当一张胶片上同时透照多条焊接接头时,象质计应放置在透照区最边缘焊缝处。
3.4.5 透照外径≤100mm小径管焊缝时可选用通用线型象质计或JB/T4730附录F的专用象质计,金属丝应横跨焊缝放置。
3.5散射线屏蔽背部散射线及无用射线应采用常规方法屏蔽。
为验证背部散射线的影响,在每个暗盒背向工件侧贴一个“B”铅字标记(高13mm厚度1.6mm)。
若在底片的黑色背影上出现B的较淡影象,就说明背散射防护不良,应予重照。
但若较淡背影上出现较黑的影象,则不作为底片质量判废依据。
3.6标记透照部位标记由定位标记和识别标记构成。
焊缝透照定位标记包括搭接标记和中心标记。
局部检测时搭接标记称为有效区段标记。
当铅质标记用数字表示时,可不用中心标记。
识别标记包括产品编号、焊缝编号、底片编号和透照日期。
返修部分还应有返修标记R1,R2…..(其数码表示返修次数)标记一般应放置在距焊缝边缘至少5mm以外,所有标记影像不应重叠, 且不应干扰有效评定范围内的影像。
定位标记3.7观片灯和评片要求观片灯的亮度至少应能观察最大黑度为4.0的底片,且观片窗口的漫射光亮度可调,并备有遮光板,对不需观察或透光量过强部分屏蔽。
评片应在评片室进行。
评片室应整洁,安静,温度适宜,光线应暗且柔和。
3.7.3 评片人员在评片前应经历一定的暗适应时间。
底片评定范围为焊缝及两恻5mm宽的区域。
3.8黑度计采用TD-210型黑度计和仪器自带的黑度片。
黑度计误差应大小不超过0.05mm。
3.9表面要求和射线检测时机3.9.1 检测前对接焊接接头的表面应经外观检测并合格。
表面的不规则状态应不不掩盖或干扰缺陷影象,否则应对表面作适当修整。
3.9.2 射线检测应在焊后进行。
对有延迟裂纹倾向的材料,至少应在焊后24小时方可检测。
4.检测技术4.1 透照布置,透照方式容器局部检测部位应优先选择焊缝交叉部位以及开孔区将被其他元件覆盖的焊缝,拼接封头,拼接管板,拼接补强圈的对接焊缝。
应根据工件特点和技术条件的要求选择适宜的透照方式。
在可实施的情况下应选用单壁透照方式,当单壁透照不可实施时方可采用双壁透照方式。
4.1.2 周向曝光源置于圆筒形容器环焊缝的中心,一次曝光检测整条环焊缝,焦距F为D/2+2(mm),当胶片长300mm时,L3或Leff选用260mm。
4.1.3 透照方向透照时射线束中心应垂直指向透照区中心,需要时也可选用有利于发现缺陷的方向透照。
4.1.4 一次透照长度一次透照长度应以透照厚度比K进行控制。
AB级检测技术纵向对接焊接接头K≤1.03,环向对接焊接接头K≤1.1。
整条环向对接焊接接头所需的透照次数可参照 JB/T4730.2附录D的曲线图确定4.2曝光条件4.2.1 应根据每台X光机、胶片和增感屏制作曝光曲线表,以此作为曝光范围,曝光量一般应≥15mA.min。
4.3胶片处理按胶片使用说明书的规定、采用手工冲洗。
4.4底片的质量?4.4.1 底片上, 定位和识别标记影像应显示完整、位置正确,且不得掩盖受检焊缝的影像。
4.4.2 底片评定范围内的黑度D:2.0≤D≤4.0。
4.4.4 底片上的象质计灵敏度应符合有关规定。
4.4.6 底片有效评定区域内不得有胶片处理不当或其它妨碍底片准确评定的伪缺影像。
4.5质量分级4.5.1 根据对接焊接接头中存在缺陷的性质、数量和密集程度,其质量分为Ⅰ、Ⅱ、Ⅲ、Ⅳ级。
Ⅰ级对接焊接接头内不允许存在裂纹、未熔合、和未焊透。
Ⅱ级、Ⅲ级对接焊接接头内不允许存在裂纹、未焊透和未熔合。
Ⅲ级者为Ⅳ级。
4.5.2 圆形缺陷的质量分级圆形缺陷用圆形缺陷评定区进行质量分级评定,圆形缺陷评定区为一个与焊缝平行的矩形,其尺寸见表5。
圆形缺陷评定区应选在缺陷最严重的区域。
表5 缺陷评定区表6 缺陷点数换算表表7 各级别允许的圆形缺陷点数Ⅰ级的对接焊接接头和母材公称厚度T≤5mm的Ⅱ级对接焊接接头,不计点数的缺陷在圆形缺陷评定区内不得多于10个,超过时对接焊接接头质量等级应降低一级。
表8 不计点数的缺陷尺寸4.5.6 条形缺陷的质量分级长宽比大于3的气孔、夹渣、夹钨等缺陷定义为条形缺陷,条形缺陷按表9的规定进行分级评定。
表9 条形缺陷的分级4.6 综合评级4.6.1 在圆形缺陷评定区内同时存在圆形缺陷和条形缺陷时,应进行综合评级。
4.6.2 综合评级的级别如下确定:对圆形缺陷和条形缺陷分别评定级别,将两者级别之和减一作为综合评级的质量级别。
4.7射线检测记录、报告和资料存档射线检测现场原始记录及检测位置图由Ⅰ、Ⅱ级检测人员按规定填写并签字认可。
4.7.2 底片评定记录由Ⅱ级人员初评、复评并签字认可。
射线检测报告应准确、完整,并经Ⅱ级以上相应责任人员签字认可。
超声波检测通用工艺规程1.主要内容与适用范围本规程规定了焊缝超声检测人员具备的资格、仪器、探头、试块、检测技术方法和质量分级等。
本规程适用于本公司生产的厚度为6mm~30mm钢制承压设备全熔化焊的超声检测。
不适用于铸钢及奥氏体钢焊缝,外径小于159mm的钢管对接焊缝,内径小于或等于250mm或内外径之比小于80%的纵向焊缝检测。
本规程按JB4730的要求编写,符合《容规》和GB150等要求。
检测工艺卡是本规程的补充,由Ⅱ级人员按本规程等要求编制,其检测参数规定的更具体。
2.引用标准、法规JB/T4730-2005《承压设备无损检测》GB150-1998《钢制压力容器》JB/T9214-1999《A型脉冲反射式超声波探伤系统工作性能测试方法》JB/T10061-1999《A型脉冲反射式超声波探伤仪通用技术条件》JB/T10062-1999《超声探伤用探头性能测试方法》3.检测人员3.1检测人员必须经过培训,按《特种设备无损检测人员考核与监督管理规则》的要求。
经理论和实践考试合格,取得相应等级资格证书的人员担任。