硝酸工艺流程图
硝酸工业制法学生
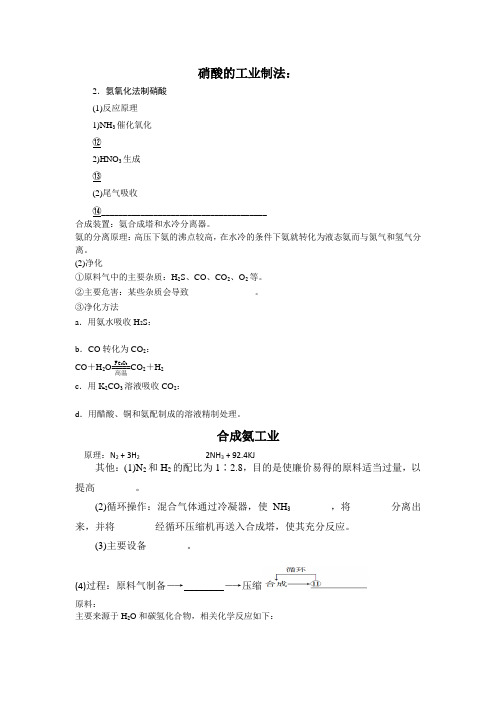
硝酸的工业制法:2.氨氧化法制硝酸 (1)反应原理 1)NH 3催化氧化⑫______________________________________ 2)HNO 3生成⑬______________________________________ (2)尾气吸收⑭______________________________________ 合成装置:氨合成塔和水冷分离器。
氨的分离原理:高压下氨的沸点较高,在水冷的条件下氨就转化为液态氨而与氮气和氢气分离。
(2)净化①原料气中的主要杂质:H 2S 、CO 、CO 2、O 2等。
②主要危害:某些杂质会导致_______________。
③净化方法a .用氨水吸收H 2S :________________________________ b .CO 转化为CO 2: CO +H 2O =====Fe 2O 3高温CO 2+H 2 c .用K 2CO 3溶液吸收CO 2:_____________________________________ d .用醋酸、铜和氨配制成的溶液精制处理。
合成氨工业原理:N 2 + 3H 2 2NH 3 + 92.4KJ其他:(1)N 2和H 2的配比为1∶2.8,目的是使廉价易得的原料适当过量,以提高________。
(2)循环操作:混合气体通过冷凝器,使NH 3________,将________分离出来,并将________经循环压缩机再送入合成塔,使其充分反应。
(3)主要设备________。
(4)过程:原料气制备―→________―→压缩原料:主要来源于H 2O 和碳氢化合物,相关化学反应如下:C +H 2O=====高温CO +H 2 CO +H 2O=====高温催化剂CO 2+H 2 CH 4+H 2O=====高温催化剂CO +3H 2 CH 4+2H 2O=====高温催化剂CO 2+4H 2 CO + H 2O(g) === CO 2 + H 2(3)催化剂使用催化剂可加快化学反应速率,但不影响化学平衡⇒采用以铁为主的催化剂。
硝酸镁法制取浓硝酸(年产3万吨)

课程设计(论文)任务书设计题目:硝酸镁法制取浓硝酸(年产3万吨)学院:专业:班级:学生:指导教师:系主任: (签名)一、设计要求:1、根据设计题目,进行生产实际调研或查阅有关技术资料,选定合理的流程方案和设备类型,并进行简要论述。
(字数不小于8000字)2、设计说明书内容:封面、目录、设计题目、概述与设计方案简介、工艺方案的选择与论证、工艺流程说明、专题论述、参考资料等。
3、图纸要求:工艺流程图1张(图幅2号);设备平面或立面布置图1张(图幅3号))。
二、进度安排:三、指定参考文献与资料《过程装备成套技术设计指南》(兼用本课程设计指导书)、《过程装备成套技术》、《化工单元过程及设备课程设计》摘要浓硝酸是重要的化工基本原料。
在化工、轻工、冶金、国防等工业有广泛的用途;“硝酸镁法”生产浓硝酸工艺属于间接法, 是以硝酸镁溶液为脱水剂, 将浓度为45%一60%的稀硝酸精馏制取浓度为98.2%以上的浓硝酸的生产工艺。
因其流程短、投资省并且无稀硝酸生成,产品质量好而被大多数浓硝酸生产企业采用。
关键词:浓硝酸;硝酸镁;稀硝酸;间接法目录摘要 (Ⅰ)前言 (1)第一章浓硝酸的制造概述 (1)1. 1 产品浓硝酸 (1)1. 1. 1 物理性质 (2)1. 1. 2 化学性质 (2)1. 1. 3 产品标准 (3)1. 2 脱水剂硝酸镁 (4)第二章工艺流程论证 (5)2.1工业上制取浓硝酸的三种方法 (5)2.1.1直接合成法 (5)2.2.2超共沸酸精馏法 (6)2.2.3加脱水剂法 (6)2.2工艺条件简述 (10)2.2.1稀硝酸的浓度 (10)2.2.2 硝酸镁溶液的浓度 (10)2.2.3 配料比 (10)2.2.4 回流比 (11)2.2.5 操作温度 (11)2.2.6 操作压力 (11)2.2.7 空塔速度和喷淋密度 (11)2.3硝镁法浓硝酸生产工艺流程简介 (11)2.4硝酸生产装置的布置 (12)第四章典型机器设备选型与论证 (13)4.1硝酸浓缩塔的设计 (13)4.1.1 浓缩塔结构 (14)4.1.2 浓缩塔材质的选用 (14)4.1.3 浓缩塔的强度计算 (15)4.2硝酸镁加热器 (16)4.3硝酸镁溶液蒸发器 (17)4.4硝酸镁分离器 (17)4.5漂白塔 (17)4.6硝酸冷凝器和冷却器 (18)总结 (18)参考文献 (19)致谢 (20)前言浓硝酸(HNO3浓度98%)是一种重要的基础化工原料,广泛用于化工、冶金、医药、染料、农药等领域。
(完整版)制药工艺流程图
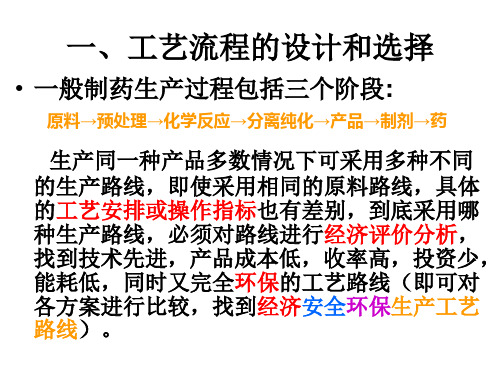
例1:混酸硝化氯苯制备混合硝基氯苯
4硝%混 化;酸温氯组度苯成:与8:混0H℃酸N;中O硝3H4化7N%O时3、间的H:摩2S3尔Oh;配4 4硝比9%化为、废1:H1酸.21O中, 含硝酸<1.6%,含混合硝基氯苯为获得混合硝 基氯苯量的1%。
反应特点:氯苯、硝基氯苯与混酸不互溶。 反应结束两相分层,混酸中尚有少量硝基氯苯 及未完全反应的硝酸;同时,废酸中含有大量 不 硝参 酸加 及反回应收的混H酸2层SO中4;的如硝何基充氯分苯利和用H未2SO反4是应决的 定合成工艺的关键。
⑷∵固液非均相反应,反应液冷 却后,其中的固体应滤除∴在反 应器下部设过滤器 ∵溶剂等沸点较高,可采用真空 过滤
图4-15 氟化反应过程的工艺流程示意图
3、工艺流程设计中应考虑的技术问题
⑴ 生产方式的选择
连续生产 产品的生产方式 间歇生产
联合生产方式
⑵ 提高设备利用率
产品的生产过程都是由一系列单元操作或单元反应过程 所组成的,在工艺流程设计中,保持各单元操作或单 元反应设备之间的能力平衡,提高设备利用率, 是设计者必须考虑的技术问题
其原则如下:
1. 反应中间产物不易变质时,工艺流程采用 不同生产能力的容器,在两步反应中间增 设贮槽,使整个工艺生产连续化;
2. 反应中间产物易变质时,工艺流程采用相 同生产能力的容器,实行生产周期长的多 釜生产,生产周期短的少釜生产的原则;
⑶物料的回收与利用
在工艺流程设计中,充分考虑物料的回收与再利用, 以降低原辅材料消耗,提高产品收率,是降低产品成本的 重要措施。
一、工艺流程的设计和选择
• 一般制药生产过程包括三个阶段:
原料→预处理→化学反应→分离纯化→产品→制剂→药
生产同一种产品多数情况下可采用多种不同 的生产路线,即使采用相同的原料路线,具体 的工艺安排或操作指标也有差别,到底采用哪 种生产路线,必须对路线进行经济评价分析, 找到技术先进,产品成本低,收率高,投资少, 能耗低,同时又完全环保的工艺路线(即可对 各方案进行比较,找到经济安全环保生产工艺 路线)。
a2o工艺流程图
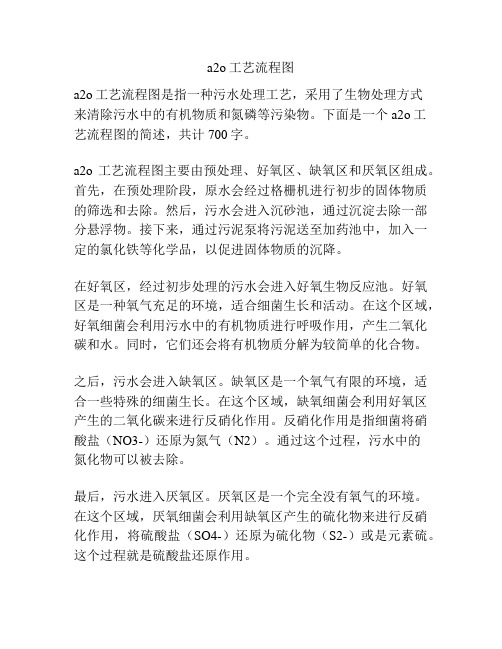
a2o工艺流程图a2o工艺流程图是指一种污水处理工艺,采用了生物处理方式来清除污水中的有机物质和氮磷等污染物。
下面是一个a2o工艺流程图的简述,共计700字。
a2o工艺流程图主要由预处理、好氧区、缺氧区和厌氧区组成。
首先,在预处理阶段,原水会经过格栅机进行初步的固体物质的筛选和去除。
然后,污水会进入沉砂池,通过沉淀去除一部分悬浮物。
接下来,通过污泥泵将污泥送至加药池中,加入一定的氯化铁等化学品,以促进固体物质的沉降。
在好氧区,经过初步处理的污水会进入好氧生物反应池。
好氧区是一种氧气充足的环境,适合细菌生长和活动。
在这个区域,好氧细菌会利用污水中的有机物质进行呼吸作用,产生二氧化碳和水。
同时,它们还会将有机物质分解为较简单的化合物。
之后,污水会进入缺氧区。
缺氧区是一个氧气有限的环境,适合一些特殊的细菌生长。
在这个区域,缺氧细菌会利用好氧区产生的二氧化碳来进行反硝化作用。
反硝化作用是指细菌将硝酸盐(NO3-)还原为氮气(N2)。
通过这个过程,污水中的氮化物可以被去除。
最后,污水进入厌氧区。
厌氧区是一个完全没有氧气的环境。
在这个区域,厌氧细菌会利用缺氧区产生的硫化物来进行反硝化作用,将硫酸盐(SO4-)还原为硫化物(S2-)或是元素硫。
这个过程就是硫酸盐还原作用。
通过这些处理过程,a2o工艺可以将污水中的有机物质和氮磷等污染物进行有效的去除。
最终,经过a2o工艺处理后的清水可以被重新利用,或者直接排放到河流或海洋中。
总结起来,a2o工艺流程图中包括了预处理、好氧区、缺氧区和厌氧区。
通过这些处理过程,a2o工艺可以有效去除污水中的有机物质和氮磷等污染物。
a2o工艺在污水处理领域具有广泛的应用前景,可以为国内外的城市和工业区域提供可持续发展的水资源管理解决方案。
年产30万吨双压法稀硝酸工艺设计

年产30万吨稀硝酸工艺设计一、稀硝酸生产的主要原理解氨接触氧化法制硝酸的总反应式为:NH3+2O2===HNO3+H2O,反应可分三步进行:氨的接触氧化过程:在催化剂的作用下,将氨氧化为一氧化氮,其反应式为:4NH3+5O2====4NO+6H2O (1)一氧化氮氧化过程:将前一过程中生成的NO进一步氧化成NO2,其反应式为:2NO+O2====2NO2 (2)氮氧化物的吸收过程:用水吸收二氧化氮,从而得到产品硝酸,其反应式为:3NO2+H2O====2HNO3+NO (3)用此工艺可生产浓度为45%~60%的稀硝酸。
60年代后,硝酸生产的技术特点是,采用大型化组,适当的提高操作压力。
采用高效设备,降低原料及能量消耗,决尾气中氮氧化物的污染问题。
二、工艺条件的确定催化剂:铂系催化剂氨氧化工艺条件1. 温度在不同温度下,氨氧化后的反应生成物也不同。
低温时,主要生成的是氮气。
650℃时,氧化反应速率加快,氨氧化率达90%;700~1000℃时,氨氧化率为95%~98%。
温度高于1000℃时,由于一氧化氮分解,氨氧化率反而下降。
在650~1000℃范围内,温度升高,反应速率加快,氨氧化率也提高。
但是温度太高,铂损失增大,同时对氧化炉材料要求也更高。
因此一般常压下,氧化温度取750~850℃,加压氧化取870~900℃为宜。
2. 压力氨氧化反应实际上可视为不可逆反应,压力对于NO产率影响不大,但加压反有助于反应速度的提高。
在工业生产条件下,加压时氧化率比常压时氧化率低1%~2%。
尽管加压可导致氨氧化率降低,但由于反应速度的提高可使催化剂的生产强度增大。
尤其是压力提高可大大节省NO氧化和NO2吸收所用的昂贵不锈钢设备。
生产中究竟采用常压还是加压操作,应视具体条件而定。
一般加压氧化采用0.3~0.5MPa压力,国外有采用1.0MPa。
由于本设计选用全中压法,操作压力选为0.45MPa。
3. 接触时间混合气体在铂网区的停留时间称为接触时间。
A2O工艺的流程与原理、变形工艺与改良工艺

什么是A2/O工艺?A2/O是Anaerobic[ˌænəˈrəʊbɪk](厌氧)-Anoxic[æ'nɒksɪk](缺氧)-Oxic ['ɒksɪk](好氧)的英文缩写。
A2/O工艺是流程比较简单的“同步脱氮除磷工艺”。
A2/O基础工艺流程图厌氧池原水和沉淀池回流污泥(含磷污泥)一同进入厌氧池,厌氧段主要功能是将原水有机物进行氨化、回流污泥中的聚磷菌释磷。
厌氧池中的溶解氧的含量严格来说必须控制在0.2mg/L以下。
溶解氧升高的原因可能有:进水COD过低、原水中DO的含量过高、沉淀池回流污泥停留时间过短等。
①氨化作用:又叫脱氨作用,指微生物分解有机氮化物产生氨的过程。
②释磷:聚磷菌把细胞内聚磷酸盐分解(同时将磷释放到泥液中),从中获得能量(产生ATP),利用ATP(三磷酸腺苷-生物体内最直接的能量来源)吸收污水中的易降解的有机物(如,乙酸酐)摄入细胞内,以聚β-羟基丁酸(PHB)的形式储存于细胞内做碳能源存贮物,作为好氧段吸磷的能源。
缺氧池缺氧池中的反硝化细菌以污水中未分解的含碳有机物为碳源,将好氧池内通过内循环回流进来的硝态氮还原为N₂而释放。
在脱氮工艺中,除起反硝化去除硝态氮的作用外,同时也去除部分BOD。
还有水解反应,提高可生化性的作用;溶解氧DO控制在0.5mg/L以下。
回流比R≤50%时,脱氮效率η很低;R<200%,η随R的上升而显著上升;当R>200%后,η上升比较缓慢,一般混合液回流比控制在200%~400%。
厌氧和缺氧池均需防止污泥沉淀,避免底部产生死角和污泥淤积。
池容小的可以考虑水力搅拌,例如用循环泵;池容大的需要使用机械搅拌。
曝气池去除BOD、硝化和吸收磷等均在曝气池进行。
有200%~400%混合液回流至缺氧池。
主要参数:溶解氧DO一般为2~3mg/L。
过低,氧化不彻底;过高,容易污泥老化。
进入沉淀池的处理水要保持一定浓度的溶解氧,减少停留时间,防止产生缺氧状态,造成反硝化使污泥上浮,厌氧状态,造成污泥释磷;但溶解氧浓度也不宜过高,以防循环混合液对缺氧反应器的干扰。
20万吨年双加压法制造稀硝酸
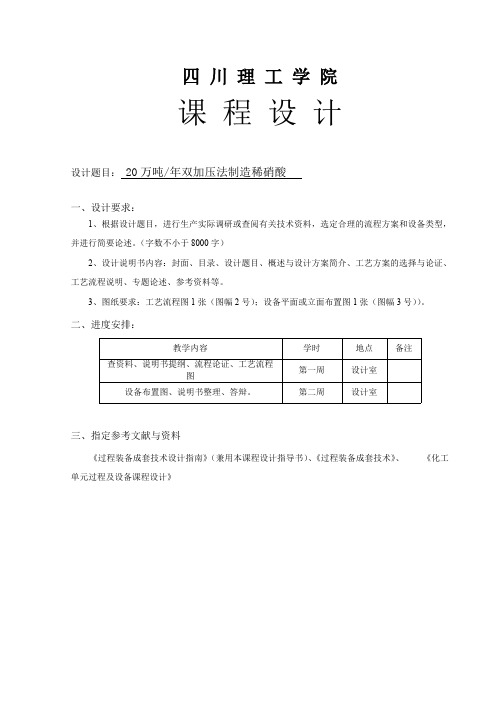
四川理工学院课程设计设计题目:20万吨/年双加压法制造稀硝酸一、设计要求:1、根据设计题目,进行生产实际调研或查阅有关技术资料,选定合理的流程方案和设备类型,并进行简要论述。
(字数不小于8000字)2、设计说明书内容:封面、目录、设计题目、概述与设计方案简介、工艺方案的选择与论证、工艺流程说明、专题论述、参考资料等。
3、图纸要求:工艺流程图1张(图幅2号);设备平面或立面布置图1张(图幅3号))。
二、进度安排:教学内容学时地点备注查资料、说明书提纲、流程论证、工艺流程第一周设计室图设备布置图、说明书整理、答辩。
第二周设计室三、指定参考文献与资料《过程装备成套技术设计指南》(兼用本课程设计指导书)、《过程装备成套技术》、《化工单元过程及设备课程设计》摘要硝酸是化学工业中的重要产品之一,用途十分广泛。
本文对国内外硝酸工业的发展进行了比较全面的总结,对不同的硝酸生产工艺流程进行了比较,分析了各个工艺的优点和缺点。
稀硝酸生产分为常压法、综合法、中压法、高压法、双加压法5种工艺。
与其它方法相比,双加压法生产硝酸的氧化压力适中,吨酸铂耗少,吸收压力高,对氮的氧化物吸收有利,产酸浓度高,氨耗低,酸尾排放的NOx含量低。
双加压法的这些优点,使其在硝酸工业生产中占据了主导地位。
关键词:双加压法;稀硝酸;工艺流程;目录摘要 (Ⅰ)前言 (Ⅱ)第一章硝酸生产工艺简介 (1)1.1 世界硝酸生产概况 (1)1.2 国内硝酸生产概况 (1)第二章工艺流程论证 (3)2.1 常用硝酸生产工艺 (3)2.1.1 常压法 (3)2.1.2 全压法 (3)2.1.3 综合法与双加压法 (3)2.2 硝酸生产工艺之间比较 (3)2.3 稀硝酸生产流程的确定 (5)2.3.1 双加压法稀硝酸工艺流程 (5)2.3.2 主要反应方程式 (6)第三章物料衡算与能量衡算 (8)3.1 物料衡算 (8)3.1.1 反应器(氧化) (8)3.2 能量衡算 (10)3.2.1 压缩机(透平机) (10)第四章典型机械设备的选型与论证 (12)4.1 主要设备 (12)4.2 典型压缩机选型与论证 (12)4.3 典型设备选型与论证 (13)总结 (14)参考文献 (15)致谢 (16)附录 (17)前言目前国内外工业化生产稀硝酸几乎全部采用氨氧化法,根据氨氧化的压力和水吸收氧化氮的压力,稀硝酸生产分为常压法、综合法、中压法、高压法、双加压法5种工艺。
硝酸工艺流程图

除催化剂 旋分器
T=300-330℃ 热气冷却器
中间产物 道生系统
(结晶脱氧产物)
P=30MPA
喷淋式反 应器
除脱氨产物 过滤系统
T=190-220℃ 结晶器
捕集器
旋分器
残渣
复合肥
成品储斗
包装成袋
5欢迎。下载
精品文档
欢迎您的下载, 资料仅供参考!
致力为企业和个人提供合同协议,策划案计划书,学习资料等等 打造全网一站式需求
6欢迎。下载
洗氨塔 氨产品
洗氨水至氨 水站
2欢迎。下载
三、尿素工艺流程图 液氨
精品文档
液氨过滤器
液氨缓冲槽
输送换热
尿
素
二氧化碳
压缩
合
成
塔
一段分解
成
品
造粒塔
蒸发浓缩
闪蒸
第
二段分解
一
尿
冷
素
冷凝
却
器
第二冷凝液
送脱盐水站
解吸水解
尾气吸收塔
一段吸收塔 氨冷塔
3欢迎。下载
四、硫酸工艺流程图
空气
ห้องสมุดไป่ตู้空气过滤器
精品文档
干燥塔
主风机
氨尾 气混 合器
1欢迎。下载
精品文档
二、合成氨工艺流程图
废料器压缩机
加氨脱硫
一段炉 炉
二段转化炉
脱
废触煤
烟气
空气压缩机
除
废热锅炉
二
低变分离器
低变炉
高变炉
工
排
氧
化
碳
工艺冷凝液
低压汽提塔
快锅
废触媒
排污水
20万吨年双加压法制造稀硝酸

60年代后,硝酸生产的技术特点是,采用大型化组,适当的提高操作压力。采用高效设备,降低原料及能量消耗,解决尾气中氮氧化物的污染问题。与其他生产方法相比,双加压法的氧化压力适中,吨酸铂耗少,吸收压力高,对氮的氧化物吸收有利,产酸浓度高,氨耗低,酸尾排放的NOx含量低,是一种可供选择的先进的硝酸生产方法。
3706
3977
4300
5447
6670
7600
9670
表1-22006-2010年我国各种硝酸生产方法的产能情况
生产方法
2006年
2007年
2010(估计)
产能×104
比例/%
产能×104
比例/%
产能×104
比例/%
常压法
1180
17.7
1180
16.7
1180
12.2
综合法
1220
18.3
1220
2.3.2主要反应方程式6
第三章物料衡算与能量衡算8
3.1物料衡算8
3.1.1反应器(氧化)8
3.2能量衡算10
3.2.1压缩机(透平机)10
第四章典型机械设备的选型与论证12
4.1主要设备12
4.2典型压缩机选型与论证12
4.3典型设备选型与论证13
总结14
参考文献15
致谢16
附录17
前 言
目前国内外工业化生产稀硝酸几乎全部采用氨氧化法,根据氨氧化的压力和水吸收氧化氮的压力,稀硝酸生产分为常压法、综合法、中压法、高压法、双加压法5种工艺。我国的硝酸生产工艺已由常压法、综合法、中压法发展为高压法和双加压法,双加压法生产稀硝酸工艺是当今世界最为先进的稀硝酸生产工艺。
氨氧化生产硝酸
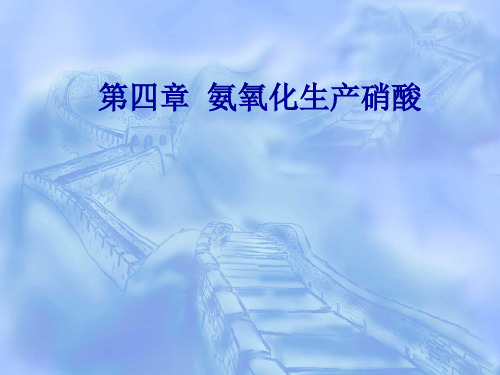
4.2.5 硝酸尾气处理 目前除去NOX的方法归纳起来可分为溶液吸收法、固体 吸附法和催化还原法。
溶液吸收法 脱除效果 残余NOX ppm 设备规模 投资费用 操作费用 NOX回收 较差 200~400 很庞大 一般 一般 含硝盐类 固体吸附法 很高 <100 很庞大 较贵 一般 NOX 催化还原法 很高 <100 较紧凑 一般 较高 破坏
表4-7 在不同温度条件下氨-空气燃烧的浓度极限(VOL)
温度、 4.4.3 温度、压力和接触时间 (1)温度:如果过低,则催化剂活性低 (2)压力:常压下氨的氧化用3~4层铂网。 (3)接触时间:接触时间应适当,太长或者太短都会降低氧 化率。
4.4.4 硝酸生产常见事故模式 (1)NH3和空气在接触设备、混合器、管道内生成易爆的混合 气体发生爆炸。 (2)生产车间、厂区内聚集有大量氨和氧化氮气体,使职工中 毒。 (3)生成亚硝酸盐-硝酸盐易在鼓风机、透平压缩机,反应器和 接触设备的点火部件管道等处发生爆炸。 (4)当浓缩器燃烧室内加入过量液体或气体燃料时,稀硝酸浓 缩工段会形成易爆的气体 (5)当氧气冲出或氧气进入被有机物质污染的设备时,在未经 脱酯处理以及沾有油污的设备和管道表面可能发生燃烧。 (6)氧气和硝酸与有机物接触或与含有棉花,石蜡等有机物质 的石棉衬垫和填料接触而发生燃烧。 (7)由于浓硝酸和混酸有机物质接触引起燃烧和爆炸。 (8)液体氧化氮与氨混合而发生爆炸。
为了解决这个问题,氨氧化物必须很快冷却下来, 使其中水分尽快冷凝,但要求一氧化氮尽量少氧化成 二氧化氮,如果浓度不高,溶解在水中的氧化物量也 就较少了,这个过程是在所谓快速冷却设备中进行的, 对冷却器的选择应是传热系数大的高效设备,以实现 短时间完成气体冷却和水蒸汽冷凝。
表4-1 氮氧化物脱除方法的比较
精细化工第三章-工艺流程图-xs

图1-3 氯苯硝化制 备硝基氯苯 最简单的物 料流程图
图1-4 氯苯硝化制备硝 基氯苯用框图表 示的物料流程图 CB-氯苯 NCB-硝基氯苯 基准-㎏· -1 h
物料流程图 应该编入初 步设计说明 书
4. 带控制点的工艺流程图-定量的图
初步设计阶段带控制点的工艺流程图
施工图设计阶段带控制点的工艺流程图 ⑴ 带控制点的工艺流程图基本要求 ⑵带控制点的工艺流程图的图面要求
初步设计阶段在施工图设计阶段一般需要绘制的工艺流程图生产工艺流程设计的基本程序工艺路线的选择确定工艺流程的组成和顺序绘制工艺流程框图绘制工艺流程示意图绘制物料流程图绘制初步设计阶段带控制点的工艺流程图绘制施工阶段带控制点的工艺流程图二工艺流程设计方法工艺流程设计中的方案比较产物收率原料单耗能量单耗产品成本设备投资操作费用等均可作为方案比较的评判标准工艺流程中的流程完善根据单元操作或单元反应过程所产生的污染物确定相应的污染治理方案等根据单元操作或单元反应所涉及的主要设备标明进料和出料的名称数量组成及工艺条件根据单元操作或单元反应过程的温度热效应等确定传热设备和载能介质的技术规格根据单元操作或单元反应过程的参数显示和控制方式确定仪表和自动控制方案根据单元操作或单元反应过程的燃烧爆炸毒害等确定相应的安全技术措施工艺流程设计中应考虑的技术问题生产方式的选择主要的技术问题产品的生产方式可采用连续生产间歇生产或联合生产方式间歇生产方式是精细化工的主要生产方式使用较多当产品的生产规模较大生产水平要求较高时尽可能采用连续生产方式
2. 工艺流程设计的任务
用图和必要的文字说明表示原料变成产品的全过程。
(1)确定工艺流程的组成-确定各生产过程的具体内容、顺序和组合方式 (2)确定载能介质的技术规格和流向 (3)确定操作条件和控制方法 (4)确定安全技术措施 (5)绘制不同深度的工艺流程图
硝酸预氧化法提金
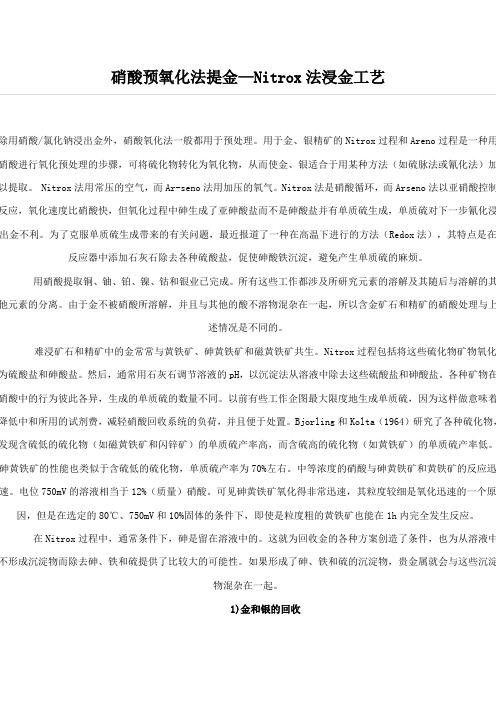
硝酸预氧化法提金—Nitrox法浸金工艺除用硝酸/氯化钠浸出金外,硝酸氧化法一般都用于预处理。
用于金、银精矿的Nitrox过程和Areno过程是一种用硝酸进行氧化预处理的步骤,可将硫化物转化为氧化物,从而使金、银适合于用某种方法(如硫脉法或氰化法)加以提取。
Nitrox法用常压的空气,而Ar-seno法用加压的氧气。
Nitrox法是硝酸循环,而Arseno法以亚硝酸控制反应,氧化速度比硝酸快,但氧化过程中砷生成了亚砷酸盐而不是砷酸盐并有单质硫生成,单质硫对下一步氰化浸出金不利。
为了克服单质硫生成带来的有关问题,最近报道了一种在高温下进行的方法(Redox法),其特点是在反应器中添加石灰石除去各种硫酸盐,促使砷酸铁沉淀,避免产生单质硫的麻烦。
用硝酸提取铜、铀、铂、镍、钴和银业已完成。
所有这些工作都涉及所研究元素的溶解及其随后与溶解的其他元素的分离。
由于金不被硝酸所溶解,并且与其他的酸不溶物混杂在一起,所以含金矿石和精矿的硝酸处理与上述情况是不同的。
难浸矿石和精矿中的金常常与黄铁矿、砷黄铁矿和磁黄铁矿共生。
Nitrox过程包括将这些硫化物矿物氧化为硫酸盐和砷酸盐。
然后,通常用石灰石调节溶液的pH,以沉淀法从溶液中除去这些硫酸盐和砷酸盐。
各种矿物在硝酸中的行为彼此各异,生成的单质硫的数量不同。
以前有些工作企图最大限度地生成单质硫,因为这样做意味着降低中和所用的试剂费,减轻硝酸回收系统的负荷,并且便于处置。
Bjorling和Kolta(1964)研究了各种硫化物,发现含硫低的硫化物(如磁黄铁矿和闪锌矿)的单质硫产率高,而含硫高的硫化物(如黄铁矿)的单质硫产率低。
砷黄铁矿的性能也类似于含硫低的硫化物,单质硫产率为70%左右。
中等浓度的硝酸与砷黄铁矿和黄铁矿的反应迅速。
电位750mV的溶液相当于12%(质量)硝酸。
可见砷黄铁矿氧化得非常迅速,其粒度较细是氧化迅速的一个原因,但是在选定的80℃、750mV和10%固体的条件下,即使是粒度粗的黄铁矿也能在1h内完全发生反应。
硝酸工业制法学生

硝酸的工业制法:2.氨氧化法制硝酸 (1)反响原理 1)NH 3催化氧化⑫______________________________________ 2)HNO 3生成⑬______________________________________ (2)尾气吸收⑭______________________________________ 合成装置:氨合成塔和水冷别离器。
氨的别离原理:高压下氨的沸点较高,在水冷的条件下氨就转化为液态氨而与氮气和氢气别离。
(2)净化①原料气中的主要杂质:H 2S 、CO 、CO 2、O 2等。
②主要危害:某些杂质会导致_______________。
③净化方法a .用氨水吸收H 2S :________________________________ b .CO 转化为CO 2: CO +H 2O=====Fe 2O 3高温CO 2+H 2 c .用K 2CO 3溶液吸收CO 2: _____________________________________d .用醋酸、铜和氨配制成的溶液精制处理。
合成氨工业原理:N 2 + 3H 2 2NH 3 + 92.4KJ其他:(1)N 2和H 2的配比为1∶2.8,目的是使廉价易得的原料适当过量,以提高________。
(2)循环操作:混合气体通过冷凝器,使NH 3________,将________别离出来,并将________经循环压缩机再送入合成塔,使其充分反响。
(3)主要设备________。
(4)过程:原料气制备―→________―→压缩原料:主要来源于H 2O 和碳氢化合物,相关化学反响如下: C +H 2O=====高温CO +H 2 CO +H 2O=====高温催化剂CO 2+H 2 CH 4+H 2O=====高温催化剂CO +3H 2 CH 4+2H 2O=====高温催化剂CO 2+4H 2 CO + H 2O(g) === CO 2 + H 2(3)催化剂使用催化剂可加快化学反响速率,但不影响化学平衡⇒采用以铁为主的催化剂。