电渣重熔技术在中国的应用和发展
电渣炉

浏览字体:大中小电渣重熔摘要:本文阐述了目前国内电渣炉的使用状况,希望对冶金企业的设备改造有一些帮助。
关键词:电渣重熔炉;结晶器;模糊控制;恒电流;恒熔速。
1.前言当前,随着国家建设、航空航天及国防建设的不断发展,市场对各种高品质精细钢材的需求不断增加,电渣重熔炉的重要性日见明显,国内大部分电渣重熔炉的生产多极为繁忙,经济效益明显,但由于大部分电渣重熔炉的建造期多为70年代左右,其设备从整体上看较为陈旧,特别是控制系统更为落后,控制精度(工作电流、工作电压、冶*率、熔速等稳定性)较差,直接影响了电渣锭的质量,制约了其经济效益的进一步提高。
电渣重熔炉是对已炼成的钢或合金进行再精炼的一种电炉设备。
从发热原理来说,电渣重熔炉是一种电阻熔炼炉。
自耗电极是用被熔金属本身制成的。
熔炼电流从变压器经短网到自耗电极,再经熔渣及结晶器平台上的导电板返回。
熔炼电流在通过高电阻熔渣时产生高温熔化自耗电极,金属熔滴穿过熔渣滴入金属熔池,被水冷结晶器冷却凝结成锭坯。
在此过程中金属熔滴与熔渣充分接触,产生强烈的冶金化学反应,使金属得到精炼。
2.电渣重熔炉设备电渣重熔炉通常由三部分组成:机械系统、供电系统、控制系统。
2.1机械系统包括:电极升降立柱、电极横臂、电极旋转升降机构、电极夹头、假电极、结晶器平台(或小车)、水冷结晶器、排烟除尘等。
电渣炉的机械系统从机械结构上分有单支臂和双支臂两种。
单支臂结构方式一次性设备投资较低,但是,当冶炼坯锭较大时,由于电极行程很长,因而要求厂房高度较高,所以,当炉子容量要求较大时,设备造价虽低,但是总投资却不少;加之自耗电极较长,制作和冶炼操作都很困难,所以,单支臂结构方式一般只适合于容量较小的电渣重熔炉。
双支臂结构方式虽然设备的一次性投资较高,但由于电极行程短,厂房高度低,操作灵活,通过支臂交换,可生产较大的电渣锭,所以,在一般情况下,应采用双支臂结构方式。
电极升降立柱通常为钢板焊接而成箱型框架式结构,用以支撑固定电极横臂和电极旋转升降机构。
第二讲 电渣重熔

世界各国电渣技术研究中心
乌克兰巴顿电焊研究院 俄罗斯电热设备科学院вниэто 美国联邦矿业局Albany冶金研究中心 加拿大哥伦比亚大学电渣实验室 德国Max Plank研究所等 东北大学钢铁冶金研究所 特殊钢研究室 钢铁研究总院冶金工艺所
三、电渣重熔工艺
1.电渣工艺制定的基本原则 2.电渣工艺参数的分类 3.钢锭结晶质量的衡量方法 4.工艺参数对目标参数的影响 5.电渣重熔参数的优化匹配 6.ESR过程工艺参数的变化及工艺控制模型
(2)基本控制参数
渣制度:
渣系、渣量GS或渣池深度Hs
电制度:
重熔电流、重熔电压
脱氧制度:
重熔过程向结晶器中加入脱氧剂种类、数量和方法
冷却水制度:
结晶器、底水箱冷却水的压力、流量、进水温度
(3) 目标参数
金属熔池形状及尺寸 极间距离Hem与电极埋入深度He 电极熔化速度Vm 渣池温度Tsl 渣皮厚度δs 电耗We 冷却水出口温度tw.o 局部冷却凝固时间LST 二次晶间距LⅡ
传统浇铸法与电渣重熔钢锭结构的比较
由于结晶器中的金属受到底部和侧面的强制水冷,冷 却速度很大,使金属的凝固只在很小的体积内进行, 使得固相和液相中的充分扩散受到抑制,减少了成分 偏析并有利于夹杂物的重新分配,图4 显示了用传统 的浇铸法和ESR方法生产H13热模具钢中铬和钼的比 较。同时,这种凝固方式可有效的控制结晶方向,可 以获得趋于轴向的结晶组织。因而可以看出重熔钢锭 具有以下的理想结构: 1一致的化学成分 2没有杂质、有害元素及非金属夹杂 3整个钢锭具有基本一致的结晶组织,消除了微观偏析 和气孔。
3)自下而上的顺序凝固条件保证了重熔金属锭 结晶组织均匀致密
图3 显示了传统的浇铸法与电渣重熔所获得的钢锭的 组织的区别,铸模里大量的钢液同时凝固导致了偏 析,偏析的程度取决于多相组织凝固的结晶行为,局 部非金属夹杂的累积及显微缝隙和缩孔是不可避免 的。 在电渣重熔过程中电极的熔化和熔融金属的结晶是同 时进行的。钢锭的上端始终有液态金属熔池和发热的 渣池,既保温又有足够的液态金属填充凝固过程中因 收缩产生的缩孔,可以有效的消除一般钢锭常见的疏 松和缩孔。同时金属液中的气体和夹杂也易于上浮, 所以钢锭的组织致密、均匀。
电渣冶金的发展历程、现状及趋势
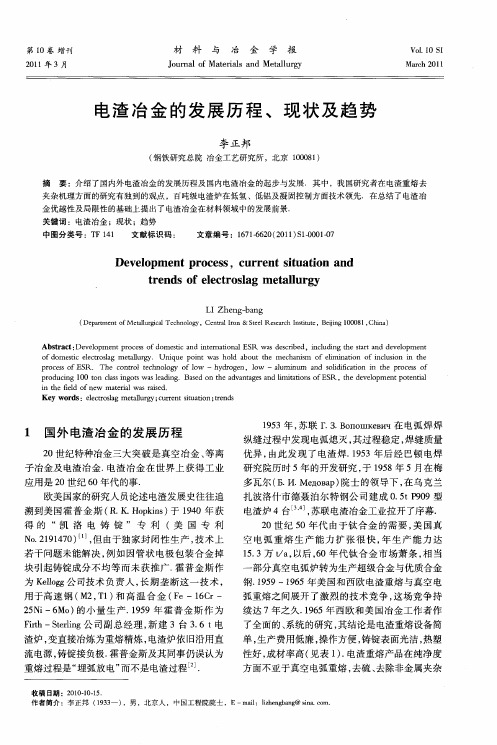
模型 、物质传 递模 型 ( 力学模 型 、 热 薄膜及渗透
理论 为基 础 的新传 质模 型 ) 热塑 性模 型. 和 A Mthl和 F SS ac 等 人成 功地把 热传 . icel .. urz t 递 模 型与现代 凝 固理论 结合 起来 ,用热 传递 模 型
( . . aO 电焊研究所推广了电渣熔铸异形铸 EO H T ) 件 E C和 双 极 串 联 电渣 焊 E WB 两 项 新 技 术 , S S 中国、 日 、美国、西德、加拿大相继在电渣熔 本 铸上有突破.电渣技术从焊接领域扩大到冶金领 域 ,再扩大到铸造行业 .
i h ed o e mae a wa as d n t ef l fn w tr l sr i . i i e
Ke r y wo ds: ee tos g m e al gy; ure iua o te s lcr l tlur c r ntst t n;r nd a i
关键词 :电渣冶金 ;现状 ;趋 势
中图分类号 :T 4 F1 1 文献标 识码 : 文章编号 :17 - 2 (0 1 S —0 1 7 6 16 0 2 1 ) 100 - 6 0
De eo m e o e s,c r e tst a i n a v lp ntpr c s u r n iu to nd
1. 53万 t , / 以后 , a 6 O年代钛合金市场萧条 , 当 相
一
块引起铸锭成分不均等而未获推广. 霍普金斯作
为 K l g 司技 术 负 责 人 , eog公 l 长期 垄 断 这 一 技 术 , 用 于高 速 钢 ( , 1 和 高 温 合 金 ( e一1C M2 T ) F 6 r一 2 N 一6 ) 小 量 生 产 .9 9年 霍 普 金 斯 作 为 5 i Mo 的 15
2024版电渣重熔技术新进展PPT教案

目录
• 电渣重熔技术概述 • 电渣重熔技术新进展 • 关键设备与工艺优化 • 实验研究及案例分析 • 未来发展趋势与挑战 • 总结与展望
01
电渣重熔技术概述
定义与原理
定义
电渣重熔技术是一种利用电流通过熔渣产生的热量来熔 化金属电极,并在水冷结晶器中凝固成锭的冶金工艺。
数据处理与结果分析
数据收集与整理
收集实验过程中的电压、 电流、温度等关键参数, 以及金属成分、组织等数 据。
数据处理
对收集的数据进行清洗、 整理和分析,提取有用信 息。
结果展示
通过图表、图像等形式展 示实验结果,便于分析和 比较。
案例展示及讨论
案例选择
选择具有代表性的电渣重熔实验 案例,如不同金属材料的重熔、
电渣重熔技术应用领域
介绍了电渣重熔技术在航空航天、能源、化工等领域的应用实例,突显其重要性和广泛应用 前景。
学生自我评价与反思
知识掌握程度
通过本次课程学习,我对电渣重熔技术的基本原理、新进展和应用 领域有了更深入的了解,掌握了相关知识和技能。
学习方法与效果
在学习过程中,我采用了多种学习方法,如阅读文献、听讲座、与 同学讨论等,取得了良好的学习效果。
原理
该技术基于电流的热效应,当电流通过具有高电阻的熔 渣时,产生大量热量使金属电极熔化,熔化的金属液滴 通过熔渣进入结晶器,在水冷作用下凝固成锭。
发展历程及现状
01 20世纪初
电渣重熔技术的起源,最初用于 生产特殊钢。
02 20世纪50年代
该技术得到快速发展,开始应用 于生产大型锻件和铸件。
03 21世纪初至今
03 余热回收技术
利用电渣重熔过程中产生的余热,进行回收利用, 提高能源利用效率。
2024年电渣重熔市场需求分析

电渣重熔市场需求分析1. 引言电渣重熔是一种重要的废钢利用方式,通过高温熔化废钢中的电渣,将其分离出来,以得到回收利用的金属和其他有价值的组分。
近年来,电渣重熔市场需求快速增长,本文将对电渣重熔市场需求进行详细分析,并探讨相关影响因素。
2. 市场需求情况电渣重熔市场需求的增长主要受以下几个方面的影响:2.1 工业发展需求随着全球工业化进程的加快,各行各业对金属原材料的需求大幅增加。
废钢经过电渣重熔可以得到高纯度的金属,满足不同工业领域对金属的需求,如建筑、汽车制造、机械制造等。
这种高效的废钢利用方式可以节约大量的原材料,因此受到工业领域的青睐。
2.2 环保要求推动随着人们对环境保护意识的不断提高,废钢的回收利用成为重要的环保举措。
相比于传统的废钢处理方式,电渣重熔可以有效减少废钢的排放量,减轻对环境的污染,因此得到环保机构的支持和推动。
2.3 技术进步带动需求增长电渣重熔技术的不断进步和成本的下降,进一步推动了市场需求的增长。
新一代的电渣重熔设备具有更高的熔化效率和更低的能耗,可以满足大规模废钢处理的需求。
同时,相关配套设备和工艺的改进也提升了电渣重熔的生产效率和产品质量,进一步吸引了投资者的关注。
3. 市场发展趋势基于对电渣重熔市场需求的分析,可以得出以下几个市场发展趋势:3.1 国内市场需求稳步增长中国是全球最大的钢铁生产和消费国,废钢资源丰富。
随着经济发展和工业化进程,国内对金属原材料的需求持续增加,将推动电渣重熔市场的发展。
同时,政府对于环保和资源利用的要求也将进一步推动电渣重熔市场的发展。
3.2 技术升级不断推动市场变革电渣重熔技术的不断进步将带动市场迈向更高效、更环保的方向。
随着熔炼效率和产品质量的不断提升,电渣重熔将在废钢处理领域占据更大的市场份额。
同时,新材料的需求也将推动电渣重熔市场的发展。
3.3 多元化应用的拓展电渣重熔的应用不仅局限于金属回收,还可以用于其他领域。
例如,电渣重熔可以将废钢中的有害物质进行杀灭和稳定化处理,还可以提取出废钢中的其他有价值组分,如铜、铝等。
电渣重熔工模具钢及电渣熔铸技术
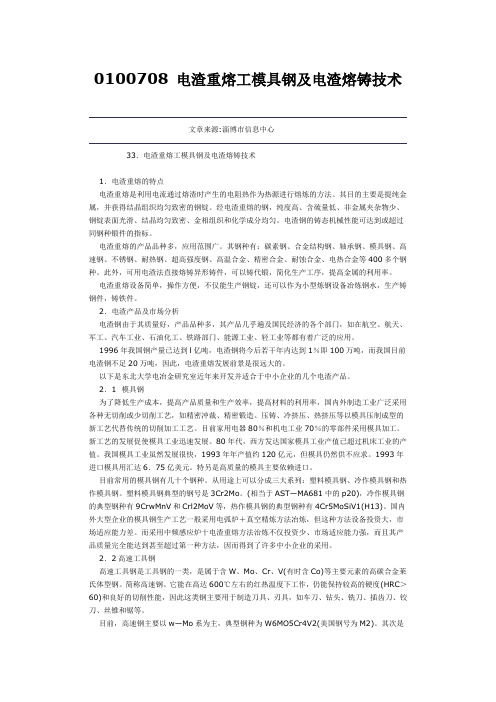
0100708 电渣重熔工模具钢及电渣熔铸技术文章来源:淄博市信息中心33.电渣重熔工模具钢及电渣熔铸技术1.电渣重熔的特点电渣重熔是利用电流通过熔渣时产生的电阻热作为热源进行熔炼的方法。
其目的主要是提纯金属,并获得结晶组织均匀致密的钢锭。
经电渣重熔的钢,纯度高、含硫量低、非金属夹杂物少、钢锭表面光滑、结晶均匀致密、金相组织和化学成分均匀。
电渣钢的铸态机械性能可达到或超过同钢种锻件的指标。
电渣重熔的产品品种多,应用范围广。
其钢种有:碳素钢、合金结构钢、轴承钢、模具钢、高速钢、不锈钢、耐热钢、超高强度钢、高温合金、精密合金、耐蚀合金、电热合金等400多个钢种。
此外,可用电渣法直接熔铸异形铸件,可以铸代锻,简化生产工序,提高金属的利用率。
电渣重熔设备简单,操作方便,不仅能生产钢锭,还可以作为小型炼钢设备冶炼钢水,生产铸钢件,铸铁件。
2.电渣产品及市场分析电渣钢由于其质量好,产品品种多,其产品几乎遍及国民经济的各个部门,如在航空、航天、军工、汽车工业、石油化工、铁路部门、能源工业、轻工业等都有着广泛的应用。
1996年我国钢产量已达到l亿吨,电渣钢将今后若干年内达到1%即100万吨,而我国目前电渣钢不足20万吨,因此,电渣重熔发展前景是很远大的。
以下是东北大学电冶金研究室近年来开发并适合于中小企业的几个电渣产品。
2.1 模具钢为了降低生产成本,提高产品质量和生产效率,提高材料的利用率,国内外制造工业广泛采用各种无切削或少切削工艺,如精密冲裁、精密锻造、压铸、冷挤压、热挤压等以模具压制成型的新工艺代替传统的切削加工工艺。
目前家用电器80%和机电工业70%的零部件采用模具加工。
新工艺的发展促使模具工业迅速发展。
80年代,西方发达国家模具工业产值已超过机床工业的产值。
我国模具工业虽然发展很快,1993年年产值约120亿元,但模具仍然供不应求。
1993年进口模具用汇达6.75亿美元。
特另是高质量的模具主要依赖进口。
高品质特殊钢绿色高效电渣重熔关键技术的开发和应用

高品质特殊钢绿色高效电渣重熔关键技术的开发和应用
为了满足现代工业高品质钢材生产的需求,特殊钢的电渣重熔技术逐渐成为了钢材生产领域的研究热点。
然而,传统的电渣重熔技术存在较多的问题,如能源消耗大、设备投资高、环境污染等,因此对于该技术进行改进和创新,提高其经济和环保效益具有重要意义。
本文将介绍一种绿色高效的电渣重熔关键技术,其开发和应用对于特殊钢的生产将起到一定的推动作用。
一、技术原理
该技术采用的是新型高压电弧电源,可靠性高、电弧稳定耐用、能量损失少、导电性能好,同时配合高频水冷孔,使得渣池稳定,温度控制更加精确。
另外,该技术将电渣重熔与真空冶炼相结合,使得钢水中的不良元素被彻底去除,并减少了钢水在再次冷却后的气孔产生。
此外,通过对炉体进行特殊的防护处理,增加了炉体的使用寿命和稳定性,从而减少了维护和更换的成本。
二、关键技术
1.高压电弧电源技术
改变了传统电弧电源中的变压器结构,采用了新颖的强场构造,使得电弧能够在更小电流下稳定工作,同时将弧气进行高效冷却,减少了能量损失,能够作为电渣重熔的能源供应。
2.真空冶炼技术
通过在电渣重熔的过程中加入真空冶炼工艺,彻底去除钢水中的不良元素,从而提高了钢材的质量和使用寿命。
3.倍增孔设计技术
新型的电渣重熔设备中采用了特殊的倍增孔设计,使得渣池稳定,温度更易控制,进一步提高了钢材的质量。
三、应用前景
新型的电渣重熔技术不仅能够提高特殊钢材的质量,同时还具有较高的经济效益和环保效益。
该技术可应用于航空、航天、核电等高端领域,提高了产品的安全性、可靠性和使用寿命,拓展了特殊钢市场的应用范围,具有较广的市场前景和应用潜力。
电渣重熔

电渣重熔免费编辑添加义项名材料电渣重熔钢(electroslag remelting)是利用电流通过熔渣时产生的电阻热作为热源进行熔炼的方法。
中文名称电渣重熔外文名称electroslag remelting主要目的提纯金属热源主要目的其主要目的是提纯金属并获得洁净组织均匀致密的钢锭。
经电渣重熔的钢,纯度高、含硫低、非金属夹杂物少、钢锭表面光滑、洁净均匀致密、金相组织和化学成分均匀。
电渣钢的铸态机械性能可达到或超过同钢种锻件的指标。
电渣钢锭的质量取决于合理的电渣重熔工艺和保证电渣工艺的设备条件。
主要产品电渣重熔的产品品种多,应用范围广。
其钢种有:碳素钢、合金结构钢、轴承钢、模具钢、高速钢、不锈钢、耐热钢、超高强度钢、高温合金、精密合金、耐蚀合金、电热合金等400多个钢种。
此外,可用电渣法直接熔铸异形铸件,可以铸代锻,简化生产工序,提高金属的利用率。
主要作用电渣熔铸工艺从根本上解决了一般铸造工艺的主要矛盾,它综合了电渣重溶-获得高冶金质量的金属和铸造-浇铸异型零件精化毛坯的长处,并具有与普通冶炼的变形金属相近的致密组织以及无各向异性的特点。
与普通锻件相比,电渣熔铸件的各项性能指标完全达到同钢种的变型金属指标,甚至还避免了锻件的一些不足之处。
应用成果近些年来,电渣熔铸新工艺逐渐引起了国内外工程技术界的重视,许多工业部门在加紧研究和使用电渣熔铸产品。
在发展这项新工艺方面,原苏联、日本和美国的研究成果较多,其次是西德、捷克斯洛伐克、英国、瑞典和法国。
东北大学电冶金研究室在发展电渣熔铸新工艺以及研制使用它的异型件方面取得了以下成果:?电渣熔铸冷轧辊、阀体、三通管、厚壁中空管、石油裂解炉管、齿轮毛坯、各种模具(包括冲压模具)和柴油机曲轴等。
目前,国外著名的电渣炉制造厂家,如美国的CONSARC、德国的ALD和奥地利的INTECO等公司均采用基于PLC和工控机的2级计算机控制系统,能实现整个重熔过程的设备和工艺的全自动控制。
电渣炉重熔技术的发展趋势及在高品质钢锭生产中的应用

电渣炉重熔技术的发展趋势及在高品质钢锭生产中的应用摘要:本文介绍了电渣炉重熔技术的种类及发展趋势,研究了电渣炉重熔技术在高品质钢锭生产中的应用情况,结果表明:电渣炉重熔在大、中型锻件所需的钢锭生产中,处于优势地位。
关键词:电渣炉;重熔技术;钢锭The Application of Remelting Technology of Electric Slag Surnace in Production of High-quality Steel IngotZhao qiangsong1,Zhang jingchao1,Guo ziqiang1(1. No.6 Institute of Project Planning and Research of Engineering Group Co.,Ltd,Zhengzhou 450007,Henan,China)Abstract:The types of remelting technology of electric slag surnace and the trend of development were introduced.The application of remelting technology of electric slag surnace in high-quality steel ingot was studied. Experimental results show that remelting technology of electric slag surnace is dominant in steel ingot demanded for large and medium forge piece.Key words:electric slag surnace;remelting technology; steel ingot电渣炉重熔技术是对钢锭有更高品质要求时采用的一种熔炼设备,在冶金系统的特殊钢厂比较常见,而在机械行业以前很少用到这种熔炼设备,近些年在机械行业的应用是越来越多,随着国家经济的大发展,电力、冶金、交通、石化、基础机械和国防等行业对高品质钢锭的需要会越来越大。
电渣重熔技术在中国的应用和发展
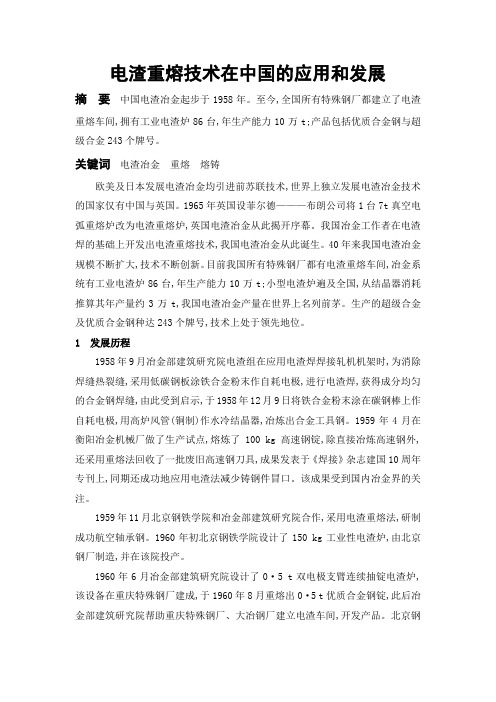
电渣重熔技术在中国的应用和发展摘要中国电渣冶金起步于1958年。
至今,全国所有特殊钢厂都建立了电渣重熔车间,拥有工业电渣炉86台,年生产能力10万t;产品包括优质合金钢与超级合金243个牌号。
关键词电渣冶金重熔熔铸欧美及日本发展电渣冶金均引进前苏联技术,世界上独立发展电渣冶金技术的国家仅有中国与英国。
1965年英国设菲尔德———布朗公司将1台7t真空电弧重熔炉改为电渣重熔炉,英国电渣冶金从此揭开序幕。
我国冶金工作者在电渣焊的基础上开发出电渣重熔技术,我国电渣冶金从此诞生。
40年来我国电渣冶金规模不断扩大,技术不断创新。
目前我国所有特殊钢厂都有电渣重熔车间,冶金系统有工业电渣炉86台,年生产能力10万t;小型电渣炉遍及全国,从结晶器消耗推算其年产量约3万t,我国电渣冶金产量在世界上名列前茅。
生产的超级合金及优质合金钢种达243个牌号,技术上处于领先地位。
1 发展历程1958年9月冶金部建筑研究院电渣组在应用电渣焊焊接轧机机架时,为消除焊缝热裂缝,采用低碳钢板涂铁合金粉末作自耗电极,进行电渣焊,获得成分均匀的合金钢焊缝,由此受到启示,于1958年12月9日将铁合金粉末涂在碳钢棒上作自耗电极,用高炉风管(铜制)作水冷结晶器,冶炼出合金工具钢。
1959年4月在衡阳冶金机械厂做了生产试点,熔炼了100 kg高速钢锭,除直接冶炼高速钢外,还采用重熔法回收了一批废旧高速钢刀具,成果发表于《焊接》杂志建国10周年专刊上,同期还成功地应用电渣法减少铸钢件冒口。
该成果受到国内冶金界的关注。
1959年11月北京钢铁学院和冶金部建筑研究院合作,采用电渣重熔法,研制成功航空轴承钢。
1960年初北京钢铁学院设计了150 kg工业性电渣炉,由北京钢厂制造,并在该院投产。
1960年6月冶金部建筑研究院设计了0·5 t双电极支臂连续抽锭电渣炉,该设备在重庆特殊钢厂建成,于1960年8月重熔出0·5 t优质合金钢锭,此后冶金部建筑研究院帮助重庆特殊钢厂、大冶钢厂建立电渣车间,开发产品。
电渣重熔技术
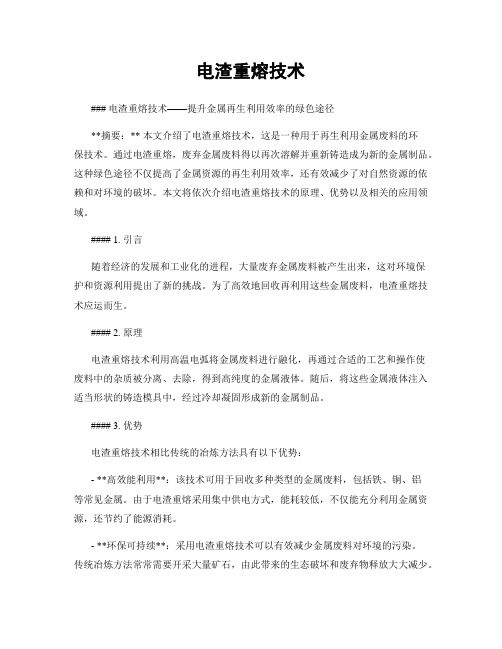
电渣重熔技术### 电渣重熔技术——提升金属再生利用效率的绿色途径**摘要:** 本文介绍了电渣重熔技术,这是一种用于再生利用金属废料的环保技术。
通过电渣重熔,废弃金属废料得以再次溶解并重新铸造成为新的金属制品。
这种绿色途径不仅提高了金属资源的再生利用效率,还有效减少了对自然资源的依赖和对环境的破坏。
本文将依次介绍电渣重熔技术的原理、优势以及相关的应用领域。
#### 1. 引言随着经济的发展和工业化的进程,大量废弃金属废料被产生出来,这对环境保护和资源利用提出了新的挑战。
为了高效地回收再利用这些金属废料,电渣重熔技术应运而生。
#### 2. 原理电渣重熔技术利用高温电弧将金属废料进行融化,再通过合适的工艺和操作使废料中的杂质被分离、去除,得到高纯度的金属液体。
随后,将这些金属液体注入适当形状的铸造模具中,经过冷却凝固形成新的金属制品。
#### 3. 优势电渣重熔技术相比传统的冶炼方法具有以下优势:- **高效能利用**:该技术可用于回收多种类型的金属废料,包括铁、铜、铝等常见金属。
由于电渣重熔采用集中供电方式,能耗较低,不仅能充分利用金属资源,还节约了能源消耗。
- **环保可持续**:采用电渣重熔技术可以有效减少金属废料对环境的污染。
传统冶炼方法常常需要开采大量矿石,由此带来的生态破坏和废弃物释放大大减少。
- **灵活性和精确度高**:电渣重熔工艺可根据废料的种类和质量要求进行调整,生产出的金属产品具有更高的精确度和可定制性,满足不同领域的应用需求。
#### 4. 应用领域**4.1** 金属制造业:电渣重熔技术广泛应用于金属制造领域,如钢铁冶炼、铸造等,进一步提高了金属制品的质量和物理性能。
**4.2** 建筑业:通过电渣重熔技术,废旧钢筋、废旧铝材等建筑废料得以有效回收,并重新利用于新建筑项目中,减少了资源浪费。
**4.3** 汽车制造业:废弃汽车零部件可以通过电渣重熔技术得到再利用。
这不仅降低了车辆制造的成本,还缓解了废弃物的压力。
国外电渣重熔概况 -东北特钢集团0522

国外电渣重熔新技术
快速电渣重熔的优点是,在保证质量的前提下,熔化速 率是传统电渣重熔的3~10倍,具有很高的生产率。可 以用交换电极的方法,用大断面电极坯料连续生产出各 种小断面规格的电渣钢圆型材、方型材及六角材。由于 具有抽锭功能,并配备了切割装置,在拉坯过程中,电 渣锭的长度可以根据用户需求进行切割,具有很强的生 产灵活性,产品趋于近终成形。另外,电渣钢的成材率 高于传统的电渣重熔。图为因泰克公司为意大利瓦尔布 鲁纳公司制作的快速电渣重熔设备。(见图1~4)。
东北特钢集团
1 前言
东北特钢抚顺基地除引进一台6t保护气氛电渣炉外(已与 ALD公司签订合同),近期还将引进一台12t和一台30t保 护性气氛电渣炉。为了对世界上最先进的电渣炉及电渣重 熔的工艺技术有更加深入全面的了解,出于对引进电渣炉 选型和确定工艺的需要,东北特钢先后与乌克兰科学院巴 顿电焊研究所及世界上著名的CONSARC(康萨克) 公司、ALD公司及INTECO(因泰克)公司等特种 冶金设备制作厂家分别进行了几轮技术交流。派专家到德 国和奥地利的电渣钢生产厂家和电渣冶炼设备设计制作厂 家进行了实地考察。并与因泰克公司正式签订了20t和 100t两台气密型保护气氛电渣炉的订货合同。 东北特钢集团
ESR with two power circuit –ESR TC
1 4 2 5 6
7
3
1电极 图5 1电极 2 熔池 3 钢锭 4 渣池 5 电流导电环 7 水冷结晶器 6 绝缘材料
国外电渣重熔新技术
传统的电渣重熔受渣池温度和钢锭表面质量的影响,熔 化速率、熔池深度及钢锭的凝固速度的控制受到很大的 限制。熔化速率偏低,电渣锭表面质量就会出现问题。 而当今很多质量要求高的产品,需要低的熔化速率,浅 平的金属熔池及快的结晶速度,这些要求是传统的电渣 重熔无法实现的。比如传统的电渣重熔生产含铬2~3% 的轧辊辊坯合格率很高。
电渣重熔新技术的研究现状及发展趋势

电渣重熔新技术的研究现状及发展趋势电渣重熔技术是一种重要的金属再生利用技术,可以有效地回收废旧金属,并在节能减排、资源循环利用方面发挥重要作用。
随着新技术的不断涌现,电渣重熔技术也在不断发展。
本文将从研究现状和未来发展趋势两个方面进行讨论。
一、电渣重熔技术的研究现状1. 传统电渣重熔技术传统电渣重熔技术是指利用电熔炉将金属渣进行加热熔化,使其成为液态金属,然后进行分离纯化的工艺流程。
这种技术在废旧金属回收利用领域已经有着长期的应用历史,主要适用于较为简单的金属合金回收。
传统电渣重熔技术在对复杂金属渣的处理方面存在效率不高、能耗较大、操作成本高等问题。
2. 新型电渣重熔技术随着科技的发展,新型电渣重熔技术不断涌现。
以高温等离子体技术为代表的新型电渣重熔技术,可以通过强电场和高温等离子体作用,实现金属渣的高效分解和还原,从而提高了金属回收率,减少了能耗和废气排放。
利用先进的智能控制系统和传感器技术,结合人工智能和大数据分析等手段,对电渣重熔过程进行精准监控和优化调控,也成为了当前的研究热点。
二、电渣重熔技术的发展趋势1. 资源综合利用未来电渣重熔技术将更加注重资源综合利用,不仅仅局限于金属的回收,还将考虑非金属元素的回收利用。
采用高效分离技术,将金属和非金属进行有效分离,实现资源的最大化回收。
2. 精准智能化控制未来电渣重熔技术将朝着智能化和自动化方向发展,通过引入先进的传感器和智能控制系统,实现对电渣重熔过程的精准监控和模型预测,确保生产过程的稳定性和产品质量的一致性。
3. 节能减排未来电渣重熔技术将致力于进一步降低能耗和减少环境污染。
采用新型高效电熔炉、恒温技术和废气处理技术,减少电渣重熔过程中的能源消耗和废气排放,实现绿色环保生产。
随着科技的不断进步和创新,电渣重熔技术必将迎来更加辉煌的发展。
通过持续深入的研究和不断改进技术手段,电渣重熔技术将为金属再生利用领域注入新的活力,为推动资源循环利用和实现绿色可持续发展做出更大的贡献。
真空电渣重熔炉发展前景的探讨

1 真 空电渣重 熔炉 在真 空 电炉 中的地位
属, 如熔 炼 耐热钢 、 不锈 钢 、 工具 钢和轴 承钢 等 ; 用 应 熔贵金 属 , 如钛 、 、 、 、 、 , 有铀 等 。 锆 钨 钼 钽 铌 还
真 空 电炉包括 有 : 真空 电阻 炉 、 空感 应 炉 、 真 真 空 电弧 炉 、 空 电子 束 炉 和 真空 电渣 重熔 炉 等 。其 真 中真空 电阻 炉主要 用 于真空 热处理 、 空钎焊 、 空 真 真 干燥 、 真空脱 气 和真 空 烧 结 等领 域 。其 他 几 种 真 空
第3 3卷第 1 期
・
特 殊钢
电渣重熔市场分析报告

电渣重熔市场分析报告1.引言1.1 概述概述部分的内容如下:电渣重熔是一种重要的金属再生利用技术,通过对废旧金属材料进行处理,提取其中有价值的金属资源。
在现代工业中,电渣重熔技术已经成为金属回收利用行业的重要环节,对资源节约和环保做出了积极贡献。
本报告旨在对电渣重熔市场进行全面、深入的分析研究,以期为相关产业提供可靠的市场参考和发展方向。
通过对市场规模、需求情况、竞争格局和发展趋势进行分析,帮助企业和投资者更好地把握市场动态,制定有效的市场战略。
随着全球经济的快速发展和环保意识的提升,电渣重熔市场将面临新的机遇和挑战。
本报告将对市场的发展趋势和未来发展方向进行展望,为行业未来的发展提供建议和指导。
1.2 文章结构文章结构部分的内容可以包括对整篇文章的章节安排和每个章节内容的简要说明。
例如,可以介绍引言部分主要包括概述、文章结构、目的和总结等内容;正文部分主要包括电渣重熔市场概况、市场需求分析和竞争格局等内容;结论部分主要包括主要发现、市场发展趋势以及建议与展望等内容。
这样的内容可以帮助读者了解整篇文章的组织结构和内容概要,让他们在阅读时更好地把握文章的主题和重点。
1.3 目的:本报告旨在对电渣重熔市场进行全面的分析,包括市场概况、需求分析和竞争格局,以期为相关企业、投资者和决策者提供准确、全面的市场情报和发展趋势,帮助他们制定合理的市场策略和决策,同时也为行业内部的企业提供参考,促进行业的健康发展和竞争力的提升。
希望通过本报告的编写和发布,能够为电渣重熔市场的进一步发展和壮大提供有益的参考和指导。
1.4 总结总结:通过对电渣重熔市场的深入分析,我们发现市场需求持续增长,竞争格局逐渐加剧。
随着工业发展和环保意识提高,电渣重熔技术将迎来更多的应用和发展机遇。
在未来,我们建议相关企业加强技术创新,优化产品结构,提高企业竞争力,把握市场机遇,实现持续稳定的发展。
同时,政府部门也应加强监管和政策支持,促进市场环境的良性发展,确保市场的健康和稳定。
2024年电渣重熔市场发展现状

电渣重熔市场发展现状简介电渣重熔是一种将废弃的电渣通过高温高压处理再生利用的工艺,目前在全球范围内得到广泛应用。
本文将对电渣重熔市场的发展现状进行分析和讨论。
1. 市场规模电渣重熔市场在近年来经历了快速增长。
据研究机构统计数据显示,2019年全球电渣重熔市场规模达到XX亿美元,预计到2025年将超过XX亿美元。
这说明电渣重熔市场具有巨大的发展潜力。
2. 市场驱动因素电渣重熔市场的发展受到多个因素的驱动。
2.1 环保需求电渣重熔技术可以有效地处理废弃的电渣,减少对环境的污染。
随着全球环保意识的增强,政府和企业对环保要求的提高,对电渣重熔市场的需求也在不断增长。
2.2 资源回收电渣重熔可以将废弃的电渣回收再利用,实现资源的循环利用。
尤其是对于稀有金属等有限资源的回收,电渣重熔技术具有重要意义。
这也促使电渣重熔市场的快速发展。
2.3 工业发展随着工业领域的发展,产生的废弃电渣数量也在增加。
电渣重熔技术为工业企业提供了一种高效、经济的废渣处理方式。
这对于提高生产效率和降低成本具有重要作用,推动了电渣重熔市场的发展。
3. 市场现状目前,电渣重熔市场呈现以下几个特点:3.1 技术创新随着科技的不断进步,电渣重熔技术也在不断创新。
高温高压处理设备的改进和智能化水平的提升,使得电渣重熔工艺更加高效、稳定。
同时,新型材料的应用也为电渣重熔提供了更多的可能性。
3.2 区域发展不平衡电渣重熔市场在全球范围内呈现区域发展不平衡的现象。
发达国家在电渣重熔技术和设备方面具有明显优势,市场规模较大。
而一些发展中国家则在电渣重熔领域存在技术和设备的瓶颈,市场发展相对较慢。
3.3 产业链协作电渣重熔市场的发展需要产业链各环节的协作。
从废渣收集、运输到处理再利用,各环节的协作对于提高效率、降低成本至关重要。
一些企业通过建立废渣回收网络,形成完整的产业链,推动电渣重熔市场的发展。
4. 发展趋势电渣重熔市场的发展展示出以下几个趋势:4.1 自动化和智能化随着技术的发展,电渣重熔设备将趋向于自动化和智能化。
电渣重熔冶炼技术

电渣重熔冶炼技术电渣重熔冶炼技术是一种先进的冶金技术,其主要应用于金属材料的回收和再利用。
该技术利用电弧加热,将废旧金属材料熔化,通过电渣的作用,将杂质分离出来,得到高纯度的金属材料,从而实现资源的有效利用和环境的保护。
一、电渣重熔冶炼技术的原理电渣重熔冶炼技术是利用电弧加热将废旧金属材料熔化,通过电渣的作用,将杂质分离出来,得到高纯度的金属材料。
在电渣重熔冶炼过程中,电极和金属材料之间形成的电弧产生高温,将金属材料熔化。
同时,电极和金属材料之间的电流产生电渣,电渣起到了隔离空气和杂质的作用,使金属材料被分离出来,从而得到高纯度的金属材料。
二、电渣重熔冶炼技术的应用1. 废旧金属材料的回收和再利用废旧金属材料中含有很多有价值的金属元素,如铁、铜、铝等。
这些金属元素可以通过电渣重熔冶炼技术进行回收和再利用,从而实现资源的有效利用和环境的保护。
2. 金属材料的精炼和纯化电渣重熔冶炼技术可以将金属材料中的杂质分离出来,得到高纯度的金属材料。
这一过程可以对金属材料进行精炼和纯化,提高其质量和性能。
3. 金属材料的合金化电渣重熔冶炼技术可以将不同种类的金属材料进行熔合,形成合金材料。
这些合金材料具有更好的性能和应用价值,可以广泛应用于冶金、机械制造、航空航天等领域。
三、电渣重熔冶炼技术的优点1. 能够回收和再利用废旧金属材料,实现资源的有效利用。
2. 能够精炼和纯化金属材料,提高其质量和性能。
3. 能够将不同种类的金属材料进行熔合,形成合金材料,具有更好的性能和应用价值。
4. 能够实现无污染生产,保护环境。
四、电渣重熔冶炼技术的发展趋势随着社会经济的快速发展,金属材料的需求量越来越大。
电渣重熔冶炼技术的应用将会越来越广泛,发展前景十分广阔。
未来,电渣重熔冶炼技术将会更加智能化、自动化,实现无人化生产。
同时,电渣重熔冶炼技术将会与其他领域的技术相结合,形成更加高效、环保、节能的新型冶金技术,为人类的发展和进步做出更大的贡献。
电渣重熔的发展及其趋势

电渣重熔的发展及其趋势李孝根内蒙古科技大学材料与冶金学院09冶金2班 0961102226摘要:简要地回顾了电渣重熔工艺在近几十年的发展与创新。
对电渣重熔技术发展过程中的一些重要工艺,如快速重熔、保护气氛下的电渣重熔等进行了简单的描述。
这些技术在改善传统电渣冶金工艺局限性的同时,进一步发挥了电渣重熔的优越性,使电渣重熔显示了更宽广的应用前景。
并简要地讨论了电渣重熔工艺在21世纪的发展趋势。
关键词:电渣重熔导电结晶器电渣快速重熔保护气氛下的电渣重熔Development and Tendency of Electroslag RemeltingAbstract :The development and achievement of technology of Electroslag Remelting (ESR) in near decades has been reviewed briefly in this text. Some important technologies in the evolution of ESR,such as Electroslag Rapid Remeltiong (ESRR) ,Electroslag Remelting under gases ,etc. were introduced briefly . With the development of these techniques,which avoid some disadvantages existing in the traditiongal ESR,the ESR is entitled to wider range application. And the development trend of the technology of ESR in the 21th century is discussed.Key Words :ESR ,Current conductive mold(CCM) ,ESRR ,ESR under gases 前言电渣重熔是一种在世界范围内广泛应用于优质钢生产的重熔工艺。
电渣重熔

1 电渣重熔概念电渣重熔(ESR)是利用电流通过电渣层产生电阻热来熔化自耗电极的合金母材,液体金属以熔滴形式经渣层下落至水冷结晶器中的金属熔池内,即渣洗清洁钢液,钢锭由下而上逐步结晶。
电渣重熔一般是在大气中进行,也可用氩气保护。
电渣重熔后并不能降低气体和夹杂物的含量,只是降低大颗粒夹杂物含量,并且使夹杂物弥散分布使夹杂物的有害作用降低至最低。
电渣重熔获得成份均匀、组织致密、质量高的钢锭。
重熔时合金得到进一步精炼,夹杂物去除是通过渣洗和在熔池中上浮。
合金的持久性能和塑性都得到提高,消除或减轻了各种宏观和显微缺陷。
如果需要进一步降低钢中气体需要进一步的真空自耗处理。
电渣设备简单,投资省。
最简单地说电渣重熔就是采用了电焊的原理。
电渣炉机械结构设计简单,但是传动机构采用滚珠丝杠比较流行。
目前,国外著名的电渣炉制造厂家,如美国的CONSARC、德国的ALD和奥地利的INTECO 等公司均采用基于PLC和工控机的2级计算机控制系统,能实现整个重熔过程的设备和工艺的全自动控制。
东北大学从20世纪90年{BANNED}始研制以液压传动或滚珠丝杠传动为核心的新型机械设备,以工控机和PLC为硬件,以专家控制为软件的智能化计算控制系统的新一代电渣炉,目前已有近20台设备成功应用于国内的工业生产中,使用效果良好。
2 电渣炉设备组成电渣炉通常有三部分组成:机械系统、供电系统、控制系统。
电渣炉的机械系统从机械结构上分为双支臂和单支臂两种;它主要由结晶器平台、支撑立柱、横臂(含升降旋转台车)、电极升降机构、电极夹持器、、假电极等组成;目前,电渣炉的升降机构大部分采用丝杠传动和钢丝绳传动两种;丝杠传动相对钢丝绳传动而言,较为平稳,对小型电渣炉尤其合适;但是,丝杠传动在电极升降调节时,其丝杠与丝母由于制造、安装的误差,使其在传动时有一定的间隙,限制了它的响应速度,影响了系统的调节精度;因此,少量新型电渣炉采用了液压驱动电极升降;液压驱动具有响应速度快、调节平稳、系统控制准确等优点,但由于增加了液压系统,造价相对较高。
电渣焊发展现状及其合理应用范围
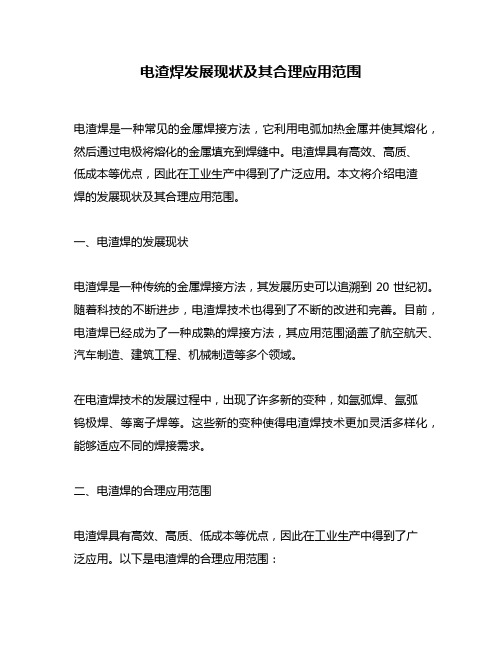
电渣焊发展现状及其合理应用范围电渣焊是一种常见的金属焊接方法,它利用电弧加热金属并使其熔化,然后通过电极将熔化的金属填充到焊缝中。
电渣焊具有高效、高质、低成本等优点,因此在工业生产中得到了广泛应用。
本文将介绍电渣焊的发展现状及其合理应用范围。
一、电渣焊的发展现状电渣焊是一种传统的金属焊接方法,其发展历史可以追溯到20世纪初。
随着科技的不断进步,电渣焊技术也得到了不断的改进和完善。
目前,电渣焊已经成为了一种成熟的焊接方法,其应用范围涵盖了航空航天、汽车制造、建筑工程、机械制造等多个领域。
在电渣焊技术的发展过程中,出现了许多新的变种,如氩弧焊、氩弧钨极焊、等离子焊等。
这些新的变种使得电渣焊技术更加灵活多样化,能够适应不同的焊接需求。
二、电渣焊的合理应用范围电渣焊具有高效、高质、低成本等优点,因此在工业生产中得到了广泛应用。
以下是电渣焊的合理应用范围:1. 金属结构的焊接电渣焊适用于各种金属结构的焊接,如钢结构、铝合金结构、铜结构等。
在建筑工程中,电渣焊被广泛应用于钢结构的焊接,其焊接效果优良,能够满足建筑工程的要求。
2. 汽车制造电渣焊在汽车制造中也得到了广泛应用。
汽车制造中需要对车身进行焊接,电渣焊能够满足这一需求。
同时,电渣焊还可以用于汽车零部件的焊接,如发动机、变速器等。
3. 机械制造在机械制造领域,电渣焊也是一种常见的焊接方法。
它可以用于各种机械零部件的焊接,如轴承、齿轮、机床等。
同时,电渣焊还可以用于修复机械零部件,提高机械设备的使用寿命。
4. 航空航天电渣焊在航空航天领域也得到了广泛应用。
航空航天领域对焊接质量要求极高,电渣焊能够满足这一要求。
同时,电渣焊还可以用于航空航天零部件的修复,提高零部件的使用寿命。
总之,电渣焊是一种成熟的金属焊接方法,其应用范围涵盖了多个领域。
在合理应用范围内,电渣焊能够提高生产效率,降低生产成本,提高产品质量,为工业生产做出了重要贡献。
- 1、下载文档前请自行甄别文档内容的完整性,平台不提供额外的编辑、内容补充、找答案等附加服务。
- 2、"仅部分预览"的文档,不可在线预览部分如存在完整性等问题,可反馈申请退款(可完整预览的文档不适用该条件!)。
- 3、如文档侵犯您的权益,请联系客服反馈,我们会尽快为您处理(人工客服工作时间:9:00-18:30)。
电渣重熔技术在中国的应用和发展摘要中国电渣冶金起步于1958年。
至今,全国所有特殊钢厂都建立了电渣重熔车间,拥有工业电渣炉86台,年生产能力10万t;产品包括优质合金钢与超级合金243个牌号。
尖键词电渣冶金重熔熔铸欧美及日本发展电渣冶金均引进前苏联技术,世界上独立发展电渣冶金技术的国家仅有中国与英国。
1965年英国设菲尔德 ------------ 布朗公司将1台7t真空电弧重熔炉改为电渣重熔炉,英国电渣冶金从此揭开序幕。
我国冶金工作者在电渣焊的基础上开发出电渣重熔技术,我国电渣冶金从此诞生。
40年来我国电渣冶金规模不断扩大,技术不断创新。
目前我国所有特殊钢厂都有电渣重熔车间,冶金系统有工业电渣炉86台,年生产能力10万t;小型电渣炉遍及全国,从结晶器消耗推算其年产量约3万t,我国电渣冶金产量在世界上名列前茅。
生产的超级合金及优质合金钢种达243个牌号,技术上处于领先地位。
1发展历程1958年9月冶金部建筑研究院电渣组在应用电渣焊焊接轧机机架时,为消除焊缝热裂缝,采用低碳钢板涂铁合金粉末作自耗电极,进行电渣焊,获得成分均匀的合金钢焊缝,由此受到启示,于1958年12月9日将铁合金粉末涂在碳钢棒上作自耗电极,用高炉风管(铜制)作水冷结晶器,冶炼出合金工具钢。
1959年4月在衡阳冶金机械厂做了生产试点,熔炼了100 kg高速钢锭,除直接冶炼高速钢外,还采用重熔法回收了一批废旧高速钢刀具,成果发表于《焊接》杂志建国10周年专刊上,同期还成功地应用电渣法减少铸钢件冒口。
该成果受到国内冶金界的矢注。
1959年11月北京钢铁学院和冶金部建筑研究院合作,采用电渣重熔法,研制成功航空轴承钢。
I960年初北京钢铁学院设计了150 kg工业性电渣炉,由北京钢厂制造,并在该院投产。
1960年6月冶金部建筑研究院设计了0 • 5 t双电极支臂连续抽锭电渣炉,该设备在重庆特殊钢厂建成,于I960年8月重熔出0 • 51优质合金钢锭,此后冶金部建筑研究院帮助重庆特殊钢厂、大冶钢厂建立电渣车间,开发产品。
北京钢铁学院帮助大连钢厂、上钢五厂建立设备,并推广电渣冶金技术。
1961年11月冶金部在重庆召开了第1届全国电渣冶金会议,总结了批量生产经验,并推荐双支臂电极交替连续抽锭及单臂固定式两种炉型,成立了全国电渣冶金协调组。
1963年11月国家科委发布《科学技术发展10年规划》,冶金部负责9项,第5项为:电渣冶金。
1963年底冶金部将建筑研究院电渣组人员及设备调入钢铁研究院,成立电渣专业组,继续用同位素方法研究电渣过程去除夹杂机理,并研究新炉型——三相电渣炉,为太原钢铁公司5 - 5t三相电渣炉、齐齐哈尔10t三相电渣炉、上钢三厂板坯电渣炉的建立提供技术设计。
1960年北京钢铁学院建成5 kg密封式氨气保护电渣炉,1964年与抚顺钢厂合作建成200 kg密封式氨气保护电渣炉(真空电渣炉)。
同时进行了电渣重熔过程中渣池内的电弧放电及去除夹杂机理的深入研究。
从1960年开始东北工学院电冶金教研室在电渣重熔工艺参数优化匹配计算及电渣重熔热平衡计算方面做了系统的研究,并提供诺模图供合理选择工艺参数。
1964年6月在重庆召开了第2届全国电渣冶金会议。
这时全国工业电渣炉已达21台,生产钢种54个,会议研究了三相电渣炉问题,拟定电渣重熔各项技术经济指标,提出电渣重熔生产车间化。
电渣钢的优良质量受到用户支持,一机部得悉电渣钢轴承用于汽车,使用寿命较电炉钢提高了3倍的情况,决定给各特殊钢厂提供20台1 800 kVA 电渣炉变压器。
有衬电渣炉是我国开创的电渣冶金新分支。
江西南昌江东机床厂于I960年采用单相单电极炉底导电式有衬电渣炉,冶炼合金钢。
1960年北京钢铁学院帮助北京量具刃具厂建立了单相双极有衬电渣炉,1961年又试验成功了三自耗电极三相有衬电渣炉,分别在北京带钢厂和北京钢丝厂进行工业性生产。
三相有衬电渣炉在北京钢丝厂成功地生产30多年,取得了巨大经济效益;1972年昆明工学院在西南地区推广有衬电渣炉时,改进单相双极有衬电渣炉,采用Bifilar供电在炉底接零线,从而解决了双电极熔化不均匀的问题,于1982年双自耗电极单相有衬电渣炉项目获国家发明奖。
此外70代东北工学院在东北地区推广单相单极炉底导电式有衬电渣炉。
熔炼合金钢及回收废料取得成效。
早在1962年冶金部建筑研究院成功地用凝壳式有衬电渣炉冶炼出超低碳不锈钢,1964年获国家新产品一等奖。
1965年8月在大连钢厂召开了第3届电渣冶金交流会,研究了电渣重熔冶金质量问题,公布了钢研院抽检各厂轴承钢ZGCr15的结果,以重特综合质量最佳。
1969年9月在匹兹堡召开的第2届国际电渣冶金会议上前苏联、美国发布了电渣熔铸消息,展示产品照片,引起了轰动。
其实我国冶金工作者早在1967年就已掌握了电渣熔铸技术。
1971年钢铁研究院与武汉设计院合作设计了15 t双极串联板坯电渣炉(5000 kVA),钢铁研究院与太原钢铁公司采用双极串联电渣炉重熔出超低碳00NiCr7Mo13Ti 耐蚀合金板,不经开坯直接上板轧机。
实践证明采用单相双极串联生产板坯功率因数高(cos①=0 • 9),热源集中,同样功率下生产率可提高一倍,电耗降低1/3,金属熔池浅平,有利于轴向结晶。
电耗高,生产率低是世界各国电渣重熔存在的普遍问题,钢铁研究院与本溪钢铁公司采用低氟高电阻渣(CaO-MgO-AI2O3-SiO2-15%CaF2取代低电阻的传统渣(70%CaF2・30%AI203)同时设定渣成分,偏离共晶点,利用渣皮凝固过程选择结晶形成绝缘渣皮,解决了国际上至今尚未解决的分流问题。
重熔渗碳轴承钢比电耗由1 775 kWh/t降至936 kWh/t,重熔生产率由180 kg/h提高到373 kg/h,本溪钢铁公司1982年至1992年累计节电240万kWh,钢铁研究院和本溪钢铁公司获国家发明奖。
重庆特殊钢厂采用高电阻CT渣,大冶钢厂采用白云石渣,东北工学院和抚顺钢厂合作采用工艺参数匹配都获得显著节电效果。
1965年上海重型机器厂建立了1台三相百吨电渣炉,后因自耗电极采用螺丝联接,在重熔时掉块,影响铸锭质量,被拆除。
上海重型机器厂与北京钢铁学院合作,于1981年创建了200 t级电渣炉,结晶器直径2 • 8 m,若抽锭可生产240 t的大锭,这是目前世界上最大的电渣炉,实际生产锭重已达205 t。
德国萨尔钢厂Saarstahl GmbH电渣炉,其结晶器直径为2 • 2 m,重熔最大锭重为165 t。
前苏联在新西柏利亚曾建250 t 电渣炉,延续10年之久,终因技术原因而终止。
最近美国Consarc公司提供日本一台大电渣炉,锭重为100 t。
1983年电渣冶金协调组由大冶钢厂任组长,钢铁研究总院和齐齐哈尔钢厂任副组长,在齐齐哈尔钢厂召开第4届电渣冶金交流会,研究了电渣重熔进一步降低电耗,提高成材率,发展电渣冶金以及防止环境污染等问题;同时研究了在消化齐钢引进德国Loybold-Heraus公司F850-10-U基础上,吸收同轴导电,有载无级调压及微机控制等技术以改造国内电渣炉。
1985年12月在成都无缝钢管厂召开了第5届电渣冶金技术交流会。
这时,全国特殊钢厂有工业电炉66台,实产优质合金钢及超级合金5 • 4万t,全国电渣冶金重熔平均电耗由1980年1 850kWh/t降至1985年1 578 kWh/t。
各特殊钢厂在品种开发上获得多次奖励。
1988年4月在美国圣地亚哥召开的第9届国际真空冶金会议上,对1961-1988年全世界对特种熔炼做出突出贡献的36个单位授奖,中国占3个,它们是:北京钢铁学院、钢铁研究总院、上海重型机器厂;对38名有突出贡献的个人授奖,中国有5人:傅杰、李正邦、朱觉、刘海洪和林宗棠。
并争取到第10届国际真空冶金会议于1990年在中国召开。
1990年8月在潍坊召开了第6届全国电渣冶金交流会,总结了30年来的成果,强调了电渣冶金应走出结晶器与冶金流程相结合发展,即要发展中间包电渣力a 热,电渣热封顶,电渣浇注,电渣离心浇注,电渣精密铸造,电渣转注等。
2中国电渣冶金重大成就2.1 200 t级电渣炉最成功的大型电渣炉是德国Loybold-Hereaus公司为萨尔钢厂(SaarstahlGmbH建的FB45/165G炉子,供电用可控硅变频电源0〜10 Hz短网感抗cos①〜0 -98,1971年建成以来生产正常,炉子负荷饱满,缺点是变频设备庞大昂贵,且原件老化快,据悉已多次更换元件。
上海重型机器厂与北京钢铁学院合作,于1981年建成200 t级电渣炉,1982年国家鉴定后即为秦山30万kW核电站提供了124件毛坯。
炉子由3根立柱呈等边三角形布置,每根立柱上有可上下移动、左右旋转的支臂,其端头夹持电极,夹持双极串联(Bifilar)回路,重熔6根耗电极分别由3个5 200 kVA 单相变压器供电,变压器二次线抽零、3根抽零线同接引锭板,6根①500 mm的自耗电极同插入一个0)2 800 mm结晶器,液渣引燃,通电即可开始重熔,采用抽锭装置,可用短结晶器抽长锭,重熔过程3个旋转支臂可轮流更换电极这种电渣炉3个变压器接三相电网,有利于电力平衡,双极串联可以降低回路感抗提高设备功率因数,cosQ>0 • 87〜0・96,因双极串联两极间有效电阻RS增大,从而提高电效率nE=RS/(RS+2 r)(lr为短网电阻之总和)。
设两路供电电网,防止长时间重熔断电,水路有两路水源,有深水井可控制夏天进水温度〉25C ,并有磁化水处理装置,有抽风排烟除尘系统及烟气净化处理设备,无疑是一台设计精巧、功能齐备、动作灵活的电渣炉,在世界上实属罕见。
前苏联新西伯利亚电热厂250 t电渣炉失败、韩国釜LU国际公司熔炼92 t锭出现偏析严重皆因工艺未掌握。
18年来上海重型机器厂摸索出一套成熟的工艺,在工艺上的创新是:低氢控制,凝固控制和低铝控制。
2.2 电渣熔铸我国冶金工作者在1966年就对铸态电渣锭进行热处理与性能测试,得到肯定的结论。
1967年就掌握了电渣熔铸变断面铸件工艺,如输入功率随断面变化及金属铸件收缩引起铸件与底板分离问题。
李正邦等提出立式电渣熔铸涡轮盘方案柱状晶交界面沿中心线,垂直于铸件厚度方向,避幵涡轮盘受力方向。
获国家发明奖。
朱觉教授一直倡导钢水电渣浇注,赵沛、刘海洪电渣浇注空心管成功地置取心棒,徐卫国感应电渣浇注,林功文、李正邦电渣离心浇铸利用动态效应细化晶粒均属冶金科技前沿的新突破。
2.3 电渣重熔理论研究2.3.1 电渣重熔去除夹杂物机理电渣重熔净化金属、显著地去除非金属夹杂物,但对其机理各国研究者持有不同观点。
前苏联Q. B・JIaT am和日本真殿统认为,电渣重熔去除夹杂物的主要原因是夹杂物自金属熔池浮升进入渣池。