加工余量和切削参数表
数控切削参数表

碳素结构钢的力学性能(GB700-88)注:A、B、C为质量等级,D级为优质级。
铣削加工常用切削速度经验值(m/min)铣削时的切削速度铣削加工每齿进给量推荐值 (mm/z)数控铣削每齿进给量经验值H13~H7孔加工方式余量(孔长度小于5倍直径)注:当孔径≤30mm、直径余量≤4mm和孔径>30~80mm、直径余量≤6mm时,采用一次扩孔或一次镗孔。
H7与H8级精度孔加工方式及余量(在实体材料上加工) (mm)注:在铸铁上加工直径为30mm与32mm的孔可用Ф28与Ф30钻头钻一次。
按H7与H8级精度加工已预先铸出或热冲出的孔 (mm)注:1.如果铸出的孔有很大的加工余量时,则第一次粗镗可分为两次或多次; 2.如果只进行一次半精镗,由其加工余量为表中“半精镗”和“粗铰或二次半精镗”加工余量之和。
平面精铣、磨削加工方式余量(mm)注:1. 精铣时,最后一次行程前留的雨量应该≥0.5mm。
2. 热处理零件磨削的加工余量系将表中值乘以1.2。
高速钢钻头加工钢件的切削用量高速钢钻头加工铝件的切削用量高速钢钻头扩孔、钻孔的切削用量 (mm/r)高速钢铰刀铰孔的切削用量攻螺纹切削速度 (m/min)钻孔的进给量镗孔切削用量硬质合金端面铣刀的铣削用量不锈钢的铣削用量不锈钢的铣削用量硬质合金车刀粗车外圆及端面的进给量注:1、加工断续表面及有冲击的工件时,表内进给量应乘系数K=0.75~0.85;2、在无外皮加工时,表内进给量应乘第数K=1.1;3、加工耐热钢及其合金时,进给量不大于1mm/r;4、加工淬硬钢时,进给量应减小。
当钢的硬度为44~56HRC时,乘系数K=0.8;当钢的硬度为57~62HRC时,乘系数K=0.5。
5、可转位刀片的允许最大进给量不应超过其刀尖圆弧半径数值的80%。
硬质合金外圆车刀半精车的进给量(参考值) mm/r注:rε=0.5mm,用于12×12以下刀杆,rε=1mm,用于30×30以下刀杆,rε=2mm,用于30×45及以上刀杆。
加工余量参数表

附录三加工余量参数表表 1 粗车、半精车外圆的加工余量(单位:mm)注:加工带凸台的零件时,其加工余量要根据零件的全长和最大直径来确定。
表 2 精车外圆的加工余量(单位:mm)1.舍五入)。
这时的粗车外圆的公差等级为14 级。
2. 决定加工余量用轴的长度计算与装夹方式有关。
3. 粗车外圆的公差带相当于h12~h13。
注:1. 在单件或小批生产时,本表的余量值应乘上系数,并化成一位小数,如×=,采用(四舍五入)。
2. 决定加工余量用轴的长度计算与装夹方式有关。
3. 磨前加工公差相当于h11。
表 4 精车端面的加工余量(单位:mm)1. d2. 表中的公差系指尺寸L 的公差。
表 5 磨端面的加工余量(单位:mm)注: 1. 加工有台阶的轴时,每台阶的加工余量应根据该台阶的d 及零件的全长分别选用。
2. 表中的公差系指尺寸L 的公差。
加工孔直径钻用车刀 扩孔钻粗铰精铰的直径第一次第二次镗以后3- - - - 3H7 4- - - - 4H7 5-- - - 5H7 6- - --6H7 8-- -8H7 10- --10H712--12H7 13- -13H7 14--14H715- -15H7 16--16H718- -18H7 20-20H7 22-22H724-24H7 25-25H726-26H7 28-28H7302830H7 3232H7 3535H73838H7 4040H74242H7 4545H74848H7 5050H760 3060H7 70 3070H780 3080H790 30-90H7 100 30-100H7120 30-120H7 140 30-140H716030-160H7 180 30-180H7注: 1. 在铸铁上加工直径到 15mm 的孔时,不用扩孔钻扩孔。
2. 在铸铁上加工直径为 30 到 32mm 的孔时,仅用直径为 28 与 30mm 的钻头钻一次。
各种机加工工时计算表

1200.00 0.833333333
0.2-0.3 0.15 26.0 1379
>>>>>>>往复式平面粗磨理论工时计算<<<<<<<
零件参数
砂轮、机床参数
工件材料
淬火钢 砂轮直径 mm
400
磨削形式
零件装置在夹具中或用千 分表校准
**当加工孔径较大 时,ap取大值;加 工孔径较小,且加 工精度要求较高 时,ap取小值
钢、铸钢 刀具材料 精镗 刀具类型 5 刀具直径 mm 20 推荐切削参数范围 0.6-1.2 1.00 8 509 请输入实际切削参数 3.00 0.60 1.00 600.00 0.3
刀具参数
硬质合金 镗刀块 5.00
4.00 20 1273
>>>>>>>高速钢铰刀铰孔理论工时计算<<<<<<<
零件参数
材料种类
材料性能
孔直径 mm
铰
刀具直径 mm 待加工孔深度 mm
切削深度 mm 铰削余量 mm 实际每转进给量 实际主轴转速 理论工时 min
推荐切削参数 中硬铸铁 铰削余量 mm
175HBS 每转进给量 f mm 6.00 切削速度 m/min 6.0 主轴转速 10.0
材料种类 孔直径 mm
深度 mm
钻
零件参数
不锈钢 刀具直径 mm
12.50 每转进给量 mm
20.00
切削速度 主轴转速
m/min
请输入实际切削参数
推荐切削参数范围 8 ~ 20
数控加工的切削用量

数控加工的切削用量2009-6-11 9:42:00 来源:作者:余英良,于辉阅读:1418次我要收藏1 切削用量选择1.1 数控加工花键轴的切削用量为了保证零件的加工精度,零件分为粗车加工和精车加工。
在粗、精车零件装夹方式与刀具选择的基础上,选定零件数控加工的切削参数如下:在数控精车车削加工中,零件轮廓轨迹的加工余量为0.8÷2=0.4 mm。
主轴转速、背吃刀量等的选择参见表1。
表1 数控加工花键轴工序卡及切削用量1.2 数控加工轴承座的切削用量为了保证零件的加工精度,零件分为粗车加工和精车加工。
在粗、精车零件装夹方式与刀具选择的基础上,选定零件数控加工的切削参数如下:在数控精车车削加工中,零件轮廓轨迹的加工余量为0.8÷2=0.4 mm。
主轴转速、背吃刀量等的选择参见表2。
表2 数控加工轴承座工序卡及切削用量2 相关内容概述金属切削加工的目的,就是用各种类型的金属切削刀具把J:件毛坯上的多余部分从毛坯上剥离开来,得到图样所要求的零件形状和尺寸。
图1 车削加工中切削用量nextpage 2.1 切削用量切削用量是指机床在切削加工时的状态参数。
切削用量包括切削速度、进给速度和背吃刀量。
参见图1。
2.1.1 切削速度切削刃上的切削点相对于工件运动的瞬时速度称为切削速度。
切削速度的单位为m/min。
切削速度与机床主轴转速之问进行转换的关系为:(1)2.1.2 进给速度是刀具在单位时间内沿进给方向上相对于工件的位移量,单位为mm/min。
2.1.3 背吃刀量己加工表面和待加工表面之问的垂直距离。
背吃刀量的计算公式为:(2)式(1)、式(2)中n为主轴(工件)转速,d为工件直径,dω、dm见图1。
在切削加工中,切削速度、进给速度和背吃刀量3个参数是相互关联的。
粗加工中,为提高效率,一般采用较大的背吃刀量。
此时切削速度和进给速度相对较小;在半精加工和精加工阶段,一般采用较大的切削速度、较小的进给量和背吃刀量,以获得较好的加工质量。
加工中心刀具切削用量表

线速度(米/分钟) 铝 高速钢铣刀 镀层硬质合金铣刀 硬质合金铣刀
加工中心刀具切削用量表
45# 60 100~300 100~300
淬硬钢 15~20
60
铸铁 15~20
30
15~20 60 30
S(转速)=线速度×1000/(直径×3.14) F(进给量)=刃数×每刃切削量×转速
每刃切削量 粗加 ~ 0.05
例:20MM硬质合金4刃铣刀精铣45#钢,线速度取60。每刃切0.05。则转速=60×1000/(20×3.14) =955,进给量=4×0.05×955=191。
以上是比较笼统的概括,适用于大多数铣刀、钻头、镗刀(不包括绞刀)加工工艺的计算。在实 际加工中还要针对不同实际情况做出调整。如:工件形状、余量大小、冷却条件、刀具磨损等。
每刃切削量参数的选择:如果太小小于0.02,那不是在切削,是在磨刀,如果太大大于0.2,那也 不是切削,是在撞击。所以并非转速越高,进给量越小越好切削,刀具必须处在一个合理的运动 状态下,才是均质、稳定的切削。
刀具加工中,对刀具寿命影响最大的是线速度,刀具商提供刀具的同时,应该会提供一份刀具针 对各种材料的线速度表,但刀具供应商的参数是在理想状态下得到的,在实际加工中,得打个 7~8折的。
车床加工基本时间计算参考表

工时定额的组成:1.批量加工的单件加工工时=基本时间+辅助时间+布置工作地时间+休息与生理需要的时间2.单件加工时:在以上的基础上加上相应的准备时间3.单件工时定额Td:单件时间td=tj+tf+tb+tx◆ 基本时间tj: 直接改变对象尺寸、开关、相对位置、状态或材料性质所用时间;◆ 辅助时间tf: 为实现工艺过程必须进行的各种辅助动作所用时间。
如装卸工件、操作要、改变切削用量、试切和测量工件、引进及退回刀具等动作所用时间。
辅助时间的的确定方法随生产类型不同而不同。
大批大量生产时,为了使辅助时间规定得合理,须将辅助动作分解成单一动作,再分别查表求得各分解动作的时间,最后予以综合;对于中批生产则可根据以往的统计资料确定;在单件小批生产中,一般用基本时间的百分比进行估算。
基本时间和辅助时间的总和称为作业时间◆ 布置工地时间tb:作班内照管工作地所耗的时间,调整更换刀具、修整砂轮、润滑擦试机床、清理切屑等。
一般按作业时间的2%~5%估算。
◆ 休息和生理时间tx:工作班内满足生理需要所耗的时间。
一般按作业时间的2%估算。
以上四部分时间总和就是单件时间td=tj+tf+tb+tx注意:因本厂每天有30分钟的休息时间,所以休息与生理需要时间tx不需计算在内;布置工地时间tb:车工,铣工按4%计算。
所以单件时间td=tj+tf+tb 组成在成批生产中,每一批工件的开始和终了时,工人需要做以下工作:A、开始时,要熟悉工艺文件,领取毛坯、材料,领取和安装刀具和夹具,调整机床及其他工艺装备等;B、终了时,要拆下和归还工艺装备,送交成品等。
这两部分所用时间叫做准备时间tz,设有N件产品,那分摊到每一个工件上的准备时间为tz/N,将这部分时间加到单件时间上去。
成批生产的单件核算时间:th=td+tz/N大批大量生产时,每个工作地始终完成某一道固定工序,tz/N接近0,故不考虑。
th=td。
4.缩减辅助时间。
在单件时间中占的比重较大。
机加工加工工时计算

1、该表中每一种加工方式的理论工时为单道工步的切削时间,仅用于参考,总的切削时间为所有工步切削时间的2、总加工成本可以参考以下计算公式: C总 = 单位时间机床的切削成本 * 切削时间 + 单位时间机床非切削成本3、如果表中须输入的前提参数与实际有区别,可以在理论工时的基础上乘以难度系数,推荐难度系数为1.0~3.0**工件直径为上道工序所留尺寸**当加工孔径较大时,ap取大值;加工孔径较小,且加工精度要求较高时,ap取小值切削参数选择原则:切削用量不仅是在机床调整前必须确定的重要参数,而且其数值合理与否对加工质量、加工效率、生产成本等有所谓“合理的”切削用量是指充分利用刀具切削性能和机床动力性能(功率、扭矩),在保证质量的前提下,获得高的一制订切削用量时考虑的因素切削加工生产率在切削加工中,金属切除率与切削用量三要素ap、f、v均保持线性关系,即其中任一参数增大一倍,都可使生产率然而由于刀具寿命的制约,当任一参数增大时,其它二参数必须减小。
因此,在制订切削用量时,三要刀具寿命切削用量三要素对刀具寿命影响的大小,按顺序为v、f、ap。
因此,从保证合理的刀具寿命出发,在确定切削用量加工表面粗糙度精加工时,增大进给量将增大加工表面粗糙度值。
因此,它是精加工时抑制生产率提高的主要因素。
二刀具寿命的选择原则切削用量与刀具寿命有密切关系。
在制定切削用量时,应首先选择合理的刀具寿命,而合理的刀具寿命一般分最高生产率刀具寿命和最低成本刀具寿命两种,前者根据单件工时最少的目标确定,后者根据工序成本最选择刀具寿命时可考虑如下几点:根据刀具复杂程度、制造和磨刀成本来选择。
复杂和精度高的刀具寿命应选得比单刃刀具高些。
对于机夹可转位刀具,由于换刀时间短,为了充分发挥其切削性能,提高生产效率,刀具寿命可选得低对于装刀、换刀和调刀比较复杂的多刀机床、组合机床与自动化加工刀具,刀具寿命应选得高些,尤应车间内某一工序的生产率限制了整个车间的生产率的提高时,该工序的刀具寿命要选得低些;当某工序大件精加工时,为保证至少完成一次走刀,避免切削时中途换刀,刀具寿命应按零件精度和表面粗糙度三切削用量制定的步骤背吃刀量的选择进给量的选择切削速度的确定校验机床功率四提高切削用量的途径采用切削性能更好的新型刀具材料;在保证工件机械性能的前提下,改善工件材料加工性;改善冷却润滑条件;改进刀具结构,提高刀具制造质量。
钨钢铣刀切削参数表【免费下载】

钨钢(硬质合金)具有硬度高、耐磨、强度和韧性较好、耐热、耐腐蚀等一系列优良性能,特别是它的高硬度和耐磨性,即使在500℃的温度下也基本保持不变,在1000℃时仍有很高的硬度。
钨钢铣刀常常被用于数控加工中心、CNC雕刻机,这种刀具硬度为维氏10K,仅次于钻石,但是即使再坚硬的刀具也是不可避免的会被磨损,从而导致使用寿命缩短,所以掌握钨钢铣刀切削参数对于加工厂来说很重要。
切削材料模具钢料(30≤硬度HRC≤40)刃径(d) 转速(S) 进刀(F) 切削量(H)1 16000 500 0.022 13000 1500-1800 0.044 12000 2500-2800 0.066 9000-10000 3000 0.088 8000 3000 0.110 6000 3000 0.112 5000 3500 0.12-0.15切削材料黄铜(硬度HRC≤30 铍铜硬度HRC35-42)刃径(d) 转速(S) 进刀(F) 切削量(H)1 16000 800-1000 0.03-0.052 14000 1800-2000 0.07-0.084 13000 2500 0.1-0.156 12000 2800-3000 0.38 8000 3000-3500 0.310 7000 3500 0.412 6500-7000 3500 0.4注解:1、以上参数是以高速加工中(主轴转速最高20000)的钨钢铣刀为准,它的表面硬度一般是HRC45-55(洛氏硬度)左右。
2 、平铣刀和圆铣刀(球刀)切削参数差不多,都可以参考上表。
3 、高速加工中一般用来加工一些比较小的零件和产品,所以它使用的刀具比较小,而且很少使用“飞刀”,也即合金铣刀。
4 、高速加工的理念就是:转速高,切削快,切削量少。
5、平时所说的钨钢一般指的就是硬质合金。
钨钢,又称为硬质合金,是指至少含有一种金属碳化物组成的烧结复合材料。
碳化钨,碳化钴,碳化铌、碳化钛,碳化钽是钨钢的常见组份。
孔加工的切削参数表格(精)

孔加工的切削参数及加工余量
1)孔加工的切削参数
表1~表4中列出了部分孔加工切削用量,供选择时参考。
表1 高速钢钻头加工钢件的切削用量
表2 高速钢钻头加工铸铁的切削用量
表3 高速钢铰刀铰孔的切削用量
表4 镗孔切削用量
2)孔加工的加工余量
表5中列出在实体材料上的孔加工方式及加工余量,供选择时参考。
表5 在实体材料上的孔加工方式及加工余量
4.攻螺纹的加工工艺
1)底孔直径的确定
攻螺纹之前要先打底孔,底孔直径的确定方法如下:对钢和塑性大的材料
D孔=D-P
对铸铁和塑性小的材料
D孔=D-(1.05~1.1)P
式中:D孔—螺纹底孔直径,mm;
D─螺纹大径,mm;
P─螺距,mm。
2)盲孔螺纹底孔深度
盲孔螺纹底孔深度的计算方法如下:
盲孔螺纹底孔深度=螺纹孔深度+0.7d
式中:d─钻头的直径,mm。
切削余量、基本公示计算

确定切削用量及基本工时切削用量一般包括切削深度、进给量及切削速度三项。
确定方法是先确定切削深度、进给量、在确定切削速度。
6.1 工序2数据计算本工序为粗车〔车端面、外圆、镗孔〕。
材料为45钢,Rm=670MPa,锻件有外皮,机床为C6140型卧式车床,共建装夹在自定心卡盘。
选用刀具为YT5硬质合金可转位刀;由表1.30*得C6140机床的中心高200mm ,选刀杆尺寸1625B H mm mm ⨯=⨯,刀片厚度,刀具形状为卷屑槽带倒棱型前面刀,前角012γ=︒,后角06α=︒,主偏角90r κ=︒,副偏角,10r κ=︒,刃倾角0s λ=︒,刀尖圆弧半径 0.8r mm ε=。
切端面2mm ,粗车外圆至86.5Φ。
〔1〕切端面1〕.确定切削深度p a :端面单边加工余量为2mm ,考虑模锻公差后其最大单边余量3.2mm ,取=2p a mm 。
2〕.确定进给量f : 由表1.4*,在粗车钢料、刀杆尺寸为1625B H mm mm ⨯=⨯、3p a mm ≤、工件直径60~100mm 时,0.6~0.9/f mm r =,根具机床C6140〔表〕选择机床的横向进给量0.64/f mm r =。
3〕.确定切削速度v :根据表1.10*,用YT15硬质合金车刀加工Rm=600~700MPa 钢料,3p a mm ≤,0.75/f mm r ≤,切削速度109/min v m =。
切削速度修正系数:0.8sv k =,0.65tv k =,0.81rv k =, 1.15Tv k =, 1.0Mv kv k k ==。
故1090.80.650.81 1.1552.8/min v m =⨯⨯⨯⨯=,1000100052.5185.8/min 90v n r d ππ⨯===⨯。
按C6140机床转速〔表4.2-8〕选择160/min 2.67/n r r s ==,则由1000nn dπ=得实际切削速度45.2/min v m =。
刀具切削参数表

对长度与直径比(l/d)超过5倍的刀具在加工中应降低转速与进给率,并减少吃
倍数(l/d) 参数比例 转数S 进给率F Ar(切深)
1-5倍 100% 100% 100%
6倍 70% 70% 70%
7倍 60% 60% 60%
8-10倍 50%↓ 50%↓ 50%↓
6.球刀加工时应根据工件不同要求进行参数选择,参阅《模具加工工艺规范》
0.1
外观型腔面平坦部位尽可能避免采用球刀光刀,避开零切削区。方法:采用圆鼻刀或球 加工方式优选 机床选用最底限 电蚀及数控工艺选用 筋加工方式 等高铣 II级精度 优先电蚀 优先数控 II级精度 优先电蚀 优先数控
7.刀具夹持部分最小长度与刀具直径比例原则:
序号 1 2 3 4 刀具直径 Φ 20-Φ 32 Φ 10-Φ 20 Φ 5-Φ 10 Φ 3-Φ 5
切削线速度 主轴转速 进给速度 金属去除率 端铣飞刀计算 N=Vc*1000/(p*Dc) rpm Vf=fz*N*Zn mm/min Q=ap*ae*Vf/1000 CM3
Vc=p*Dc*N/1000 m/min(切削线速度可参考刀具商
端铣飞刀计算
Dc刀具切削位置直径 ap轴向切削深度(可参考刀具商推荐值) ae 径向切削深度(可参考刀具商推荐值) Fz每齿进给量(可参考刀具商推荐值) Zn刀具齿数 以32日立飞刀为例计算
*895*.4=716
*1342* .2=536.8 *N *Zn mm/min
De*N/1000 m/min
*1000/(p*De) rpm
√ap(Dc2-ap) N*Zn mm/min
Dc*N/1000 m/min (可参考刀具商推荐值)
1000/(p*Dc) rpm
CNC加工参数表
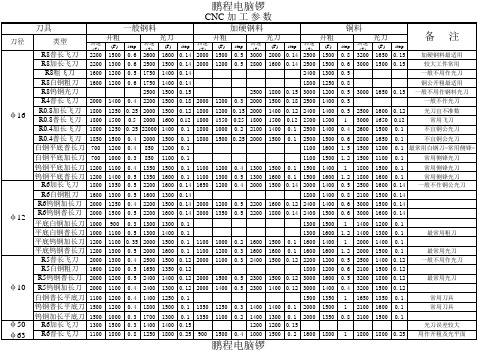
一般钢料
光刀
1600 0.14 2000 1500 0.14 2000 1400 0.14 1400 0.14 1500 0.15 1500 0.18 2000 1500 0.12 1800 1600 0.12 1800 0.1 0.1 0.1 0.1 0.1 1100 1200 1300 1200 1200 1350 1800 1800 1500 1200 1100 1500 1200
φ 35 φ 31R5 φ 32 Φ 30R5
1500 0.16 1800 1500 0.18 2000 1500 0.1 2000 1250 0.16 1800 1500 0.18 2000 1600 0.18 2000 1600 0.18 2400 1500 0.15 2100 1600 0.1 2100 1100 1000 1000 2400 2400 1600 1650
1600 0.1 1500 1500 0.14 2000 1800 1600 0.12 2400 1800 0.14 2400 1300 1300
1600 0.1 1600 0.14 1500 0.14 1500 0.14 1600 0.14 1200 1300 1400 0.1 0.1 0.1
φ 12
2500 0.3 2000 1200 0.15 2000 1350 0.25 1800 1000 0.2 2100 15.15 3000 1500 0.18 2500 1400 0.12 2400 1500 0.12 2500 1400 1500 0.1 0.1 2500 2500 1100 1100
加硬钢料
开粗
1200 0.25 1800 1200 0.3 1800 1250 0.3 1800 1300 0.25 1650 1000 1400 0.2 0.3 1650 1800
加工余量参数表
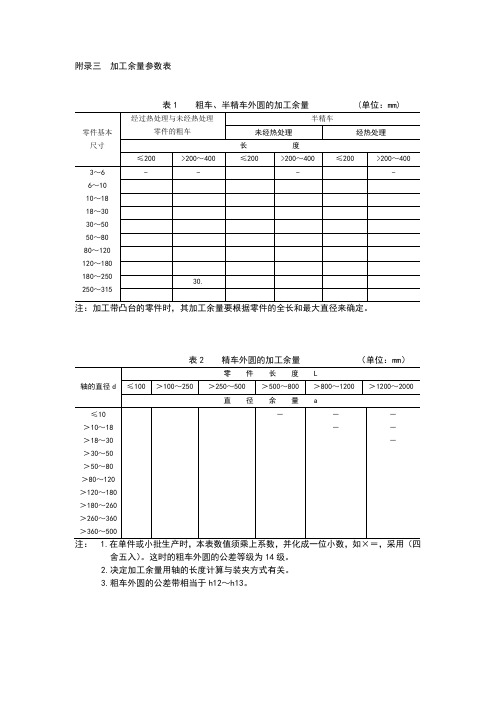
附录三加工余量参数表表1 粗车、半精车外圆的加工余量 (单位:mm)注: 1.在单件或小批生产时,本表数值须乘上系数,并化成一位小数,如×=,采用(四舍五入)。
这时的粗车外圆的公差等级为14级。
2.决定加工余量用轴的长度计算与装夹方式有关。
3.粗车外圆的公差带相当于h12~h13。
表3 磨削外圆的加工余量 (单位:mm)舍五入)。
2.决定加工余量用轴的长度计算与装夹方式有关。
3.磨前加工公差相当于h11。
注:1.加工有台阶的轴时,每台阶的加工余量应根据该台阶的d及零件的全长分别选用。
2.表中的公差系指尺寸L的公差。
表5 磨端面的加工余量 (单位:mm)注:1.加工有台阶的轴时,每台阶的加工余量应根据该台阶的d及零件的全长分别选用。
2.表中的公差系指尺寸L的公差。
2.在铸铁上加工直径为30到32mm的孔时,仅用直径为28与30mm的钻头钻一次。
3.用磨削作为孔的最后加工方法时,精镗以后的直径根据表1-23查得。
4.用金刚石细镗作为孔的最后加工方法时,精镗以后的直径根据表1-24查得。
5.如仅用一次铰孔,则铰孔的加工余量为本表中粗铰与精铰的加工余量总和。
2.在铸铁上加工直径为30、32mm的孔时,仅用直径为28、30mm的钻头钻一次。
3.用磨削作为孔的最后加工方法时,精镗以后的直径根据表1-23查得。
4.用金刚石细镗作为孔的最后加工方法时,精镗以后的直径根据表1-24查得。
5.如仅用一次铰孔,则铰孔的加工余量为本表中粗铰与精铰的加工余量总和。
注:1.当加工在热处理极易变形的、薄的轴套及其他零件时,应将表中的加工余量数值乘以。
2.如被加工孔在以后必须作为基准孔时,其公差应按7级公差来制定。
3.在单件、小批生产时,本表的数值应乘以,并化成一位小数。
例如×=,采用(四舍五入)。
表9 平面加工余量 (单位:mm)注:1.如几个零件同时加工时,长度及宽度为装置在一起的各零件长度或宽度及各零件间的间隙之总和。
数控加工参数表

一、主轴转速n(r/m i n)主轴转速一般根据切削速度V来选定,计算公式为:n=1000V/(π×d)式中,d为刀具直径(mm),V为刀具切削速度(m/min)。
对于球头铣刀,工作直径要小于刀具直径,故其实际转速应大于计算转速n。
表1铣刀的切削速度V(单位:m/min)二、进给速度Vf(mm/min)Vf = fz×z×n式中n为主轴转速,z为铣刀齿数,fz为每齿进给量(mm/齿).每齿进给量fz的选取主要取决于工件材料的力学性能、刀具材料、工件表面粗糙度等因素。
工件材料的强度和硬度越高,fz越小;反之则越大。
硬质合金铣刀的每齿进给量高于同类高速钢铣刀。
工件表面粗糙度要求越高,fz就越小。
1.铣削加工表2 铣刀每齿进给量fz(单位:mm/齿)2.镗削加工表3 镗孔切削用量3、攻螺纹攻螺纹前底孔直径的确定:攻米制螺纹螺距P<1mm:d0=d-PP>1mm:d0=d-(~)P式中P —螺距(mm)d0 —钻头直径(mm)d—螺纹公称直径(mm)攻不通孔螺纹钻孔深度=所需螺孔深度- d表4 攻普通螺纹前的底孔直径表5 攻英制螺纹前的底孔直径表6 攻螺纹切削速度(单位:m/min)4、钻孔加工表7 用高速钢钻头钻孔切削用量(f单位:mm/r)5、铰孔加工铰孔属于精加工工序,加工过程中应合理选择铰刀的类型及材质,高速钢铰刀属于通用铰刀,硬质合金铰刀一般用于加工钢、铸钢、灰铸铁和冷硬铸铁。
为了达到较高的孔径精度和表面质量,应采用较低的切削速度和进给量并合理选择切削液。
铰孔前应留有铰削余量,一般为~底孔直径=铰刀直径-(~)mm铰削加工时切削速度V取3~15m/min进给量f取~r注意:在正式加工之前应试铰,并检验孔径及粗糙度是否符合要求。
三、切削液的选择注:以上各表是加工中心和数控铣床常用的加工参数,供参考。
切削参数表

FSaeapFSaeapFSae ap FSaeapF S ae apD12330043507.50.23600600070.25330092000.10.180070000.080.05 D83300650050.183600800050.25350095000.10.180085000.080.05 D633008500 3.50.1335009000 3.50.23200110000.070.0780085000.060.05 D432001200020.0830001200020.153000120000.050.0570090000.050.05 D33000125001.50.062600120000.0350.03570095000.030.05D2D1.5D1D12R0.53800500070.223800630070.3300085000.220.22850800070.06320085000.250.3 D8R0.53800720040.23800800040.25350095000.20.2850850050.06320095000.250.3 D6R0.53500850030.133200950030.253300110000.20.2850850030.063000100000.20.22 D4R0.532001200020.0830001200020.23000120000.150.157********.063000130000.170.17 R6250055000.350.3300072000.350.3285085000.220.22300085000.350.35 R4300075000.350.25300085000.350.3285090000.220.223000100000.320.32 R3300095000.30.22800100000.30.253000110000.180.183000120000.270.27 R23000120000.250.182800120000.220.183000120000.180.182600130000.230.23 R1.52200130000.150.122800135000.150.152500135000.170.17 26ER0.8300016500.20.228501800160.1300018000.30.3 21ER2 21ER0.8300018000.20.188501800100.1300018000.30.3 17ER0.8 16BR8320050000.250.25350050000.380.38CNC 钢料 切削参数表(高速机)Vc =150-300 Fz =0.15Vc =160-280 Fz =0.13Vc =50-350 Fz =0.09底面/侧面精加工Vc =260 Fz =0.03Vc =200-260 Fz =0.13PL面仿形精加工刀具开粗半精加工仿形精加工 1 当刀具长度在直径的5倍以内下列参数适用.切记!刀具长度不可大过直径的9倍2 当刀具长度在直径的5倍以上时需将F/S值下调10%;Ae/Ap减小30%4 工件锐角处需做过渡圆角;钢料为R2、铜料为R1 石墨为R0.6n=主轴转数(公式套用)3 工件在精加工之前需保证余量均匀;不可让刀具产生过大的切削负荷 代码诠释:D =刀具直径 R =刀角半径F =进给速率 S =主轴转数Vc =线性切削速度 (m/min) Fz =每齿切削量(mm/tooth)Ae =径向进给量 (mm) Ap =轴向进给量(mm)加工参数的注意事项:Dv n c ⨯⨯=π1000FSaeapFSaeapFSaeapFSaeapF S ae apD12320043507.50.23200600070.25300060000.10.180060000.080.05 D83000600050.173200600050.25300060000.10.175060000.080.05 D6280060003.50.132006000 3.50.2300060000.070.0775060000.060.05 D43000600020.152********.050.0570060000.050.05 D326006000 1.50.08220060000.0350.0357*******.030.05 D12R0.53500600070.23200600070.3300060000.20.22800600070.06300060000.250.28 D8R0.53800600040.173200600040.3300060000.20.2800600050.06300060000.250.28 D6R0.52800600030.130********.25300060000.20.2800600030.06280060000.20.22 D4R0.52600600020.152********.150.15700600020.05250060000.150.18 R6250060000.350.3320060000.30.3300060000.220.22300060000.350.35 R4300060000.350.25320060000.30.3300060000.220.22300060000.320.32 R3280060000.30.2300060000.250.25280060000.180.183********.280.28 R2220060000.220.15265060000.150.152********.150.152********.220.22 R1.5200060000.120.1180060000.150.15200060000.180.18R1 30ER53500160016.50.4535001600160.4 26ER0.835001650150.435001650150.35300016500.20.228501800160.1300018000.250.25 21ER235001800130.4535001800130.4CNC 钢料 切削参数表(低速机)开粗半精加工仿形精加工制表:刘亚超 2009-06-15审核:加工参数的注意事项:2 当刀具长度在直径的5倍以上时需将F/S值下调10%;Ae/Ap减小30%3 工件在精加工之前需保证余量均匀;不可让刀具产生过大的切削负荷底面/侧面精加工PL面仿形精加工Vc =130-160 Fz =0.22Vc =110-200 Fz =0.15Vc =80-200 Fz =0.1Vc =150-200 Fz =0.035Vc =160-200 Fz =0.13刀具n=主轴转数(公式套用)4 工件锐角处需做过渡圆角;钢料为R2、铜料为R1 石墨为R0.6代码诠释:D =刀具直径 R =刀角半径F =进给速率 S =主轴转数Vc =线性切削速度 (m/min) Fz =每齿切削量(mm/tooth)Ae =径向进给量 (mm) Ap =轴向进给量(mm)1 当刀具长度在直径的5倍以内下列参数适用.切记!刀具长度不可大过直径的9倍Dv n c ⨯⨯=π100017ER0.83200185090.43500185090.35300018500.20.28501850100.1300018000.250.25 16BR8300050000.250.25350050000.350.35 12BR6300055000.220.22350055000.350.35FSaeapFSaeapFSaeapFSaeapFSaeapD124500750060.454000750060.35320080000.120.1285070000.10.1 D84500900040.454000900040.35350092000.120.1285085000.10.1 D64000950030.34000950030.33500110000.10.185088000.10.12000115000.050.1 D435001100020.2535001100020.253200120000.10.180090000.10.11500130000.050.1 D3300012500 1.50.2300012500 1.50.153000130000.080.0870*******.050.081500130000.050.08 D228001300010.1530001300010.132500145000.050.0565*******.050.0812********.050.06 D1.52300135000.50.122200135000.50.12000150000.050.05600125000.050.0510********.030.05 D11800150000.050.05850150000.030.03D12R0.54500800060.454000800060.4320080000.150.258507500 6.50.1 D8R0.54500900040.454000900040.4350095000.150.228508500 4.50.1 D6R0.54000950030.34000950030.33500110000.10.228509000 3.50.1 D4R0.535001100020.335001100020.33000120000.10.28009000 2.50.1 D3R0.5280012500 1.50.2300012500 1.50.253000125000.080.15700100001.50.08R4450085000.70.4400085000.50.4350085000.220.22 R3400092000.50.4400092000.40.43500100000.220.22Vc =160-200 Fz =0.1Vc =110-300 Fz =0.2Vc =110-300 Fz =0.15Vc =150-320 Fz =0.1半精加工仿形精加工底面/侧面精加工细小工件/骨位精加工CNC 铜料电极 切削参数表刀具开粗Vc =150-200 Fz =0.05制表:刘亚超 2009-06-15审核:n=主轴转数(公式套用)4 工件锐角处需做过渡圆角;钢料为R2、铜料为R1 石墨为R0.6Ae =径向进给量 (mm) Ap =轴向进给量(mm)加工参数的注意事项:1 当刀具长度在直径的5倍以内下列参数适用.切记!刀具长度不可大过直径的9倍2 当刀具长度在直径的5倍以上时需将F/S值下调10%;Ae/Ap减小30%3 工件在精加工之前需保证余量均匀;不可让刀具产生过大的切削负荷 代码诠释:D =刀具直径 R =刀角半径F =进给速率 S =主轴转数Vc =线性切削速度 (m/min) Fz =每齿切削量(mm/tooth)Dv n c ⨯⨯=π1000R1.53000130000.30.23200130000.250.23000130000.170.171800120000.10.1 R12500150000.10.11300135000.080.08 R0.51350150000.050.05850150000.050.05FSaeapFSaeapFSaeapFSaeapFSaeapD12500070006 1.54500700060.6350070000.150.285055000.150.12 D640009000314500900030.5350095000.120.1585070000.120.12130088000.060.1 D436001100020.5535001100020.353500120000.10.1580085000.10.11200100000.060.1 D3320012000 1.50.35320012000 1.50.33000130000.10.12700100000.10.11000120000.060.06 D226001300010.230001300010.252800140000.080.1650120000.080.0810********.050.05 D11800160000.050.05850150000.030.03D6R0.540009500314500950030.5350095000.120.158507000 3.50.12 D4R0.535001100020.5540001100020.353500120000.10.158008500 2.50.1 D3R0.5320012000 1.50.35300012000 1.50.253000125000.10.12700100001.50.1R4450085000.80.8450085000.80.6350085000.20.2 R3400092000.50.6420092000.50.43500100000.20.2 R2350095000.450.3400095000.40.353500120000.150.151********.080.08 R1.53000125000.350.253200125000.30.23000130000.150.151600120000.080.08 R12500150000.10.11300135000.050.05 R0.51350160000.050.05850150000.050.05底面/侧面精加工细小工件/骨位精加工Vc =110-300 Fz =0.25Vc =110-300 Fz =0.2Vc =150-300 Fz =0.15Vc =150-200 Fz =0.15Vc =160-200 Fz =0.1刀具开粗半精加工仿形精加工制表:刘亚超 2009-06-15审核:CNC 石墨电极 切削参数表4 工件锐角处需做过渡圆角;钢料为R2、铜料为R1 石墨为R0.6Ae =径向进给量 (mm) Ap =轴向进给量(mm)加工参数的注意事项:1 当刀具长度在直径的5倍以内下列参数适用.切记!刀具长度不可大过直径的9倍2 当刀具长度在直径的5倍以上时需将F/S值下调10%;Ae/Ap减小30%3 工件在精加工之前需保证余量均匀;不可让刀具产生过大的切削负荷 代码诠释:D =刀具直径 R =刀角半径F =进给速率 S =主轴转数Vc =线性切削速度 (m/min) Fz =每齿切削量(mm/tooth)n=主轴转数(公式套用)Dv n c ⨯⨯=π1000制表:刘亚超 2009-06-15审核:。
数控加工参数表

数控加工参数表 The manuscript was revised on the evening of 2021一、主轴转速n(r/min)主轴转速一般根据切削速度V来选定,计算公式为:n=1000V/(π×d)式中,d为刀具直径(mm),V为刀具切削速度(m/min)。
对于球头铣刀,工作直径要小于刀具直径,故其实际转速应大于计算转速n。
表1铣刀的切削速度V(单位:m/min)二、进给速度V f (mm/min)Vf = fz×z×n式中n为主轴转速,z为铣刀齿数,f z为每齿进给量(mm/齿).每齿进给量fz的选取主要取决于工件材料的力学性能、刀具材料、工件表面粗糙度等因素。
工件材料的强度和硬度越高,f z越小;反之则越大。
硬质合金铣刀的每齿进给量高于同类高速钢铣刀。
工件表面粗糙度要求越高,f z就越小。
1.铣削加工表2 铣刀每齿进给量f z (单位:mm/齿)2.镗削加工表3 镗孔切削用量3、攻螺纹攻螺纹前底孔直径的确定:攻米制螺纹螺距P<1mm:d0=d-PP>1mm:d0=d-(~)P式中P —螺距(mm)d0 —钻头直径(mm)d—螺纹公称直径(mm)攻不通孔螺纹钻孔深度=所需螺孔深度- d表4 攻普通螺纹前的底孔直径表5 攻英制螺纹前的底孔直径表6 攻螺纹切削速度(单位:m/min)4、钻孔加工表7 用高速钢钻头钻孔切削用量(f单位:mm/r)5、铰孔加工铰孔属于精加工工序,加工过程中应合理选择铰刀的类型及材质,高速钢铰刀属于通用铰刀,硬质合金铰刀一般用于加工钢、铸钢、灰铸铁和冷硬铸铁。
为了达到较高的孔径精度和表面质量,应采用较低的切削速度和进给量并合理选择切削液。
铰孔前应留有铰削余量,一般为~底孔直径=铰刀直径-(~)mm铰削加工时切削速度V取3~15m/min进给量f取~r注意:在正式加工之前应试铰,并检验孔径及粗糙度是否符合要求。
三、切削液的选择注:以上各表是加工中心和数控铣床常用的加工参数,供参考。
刀具基本切削参数表
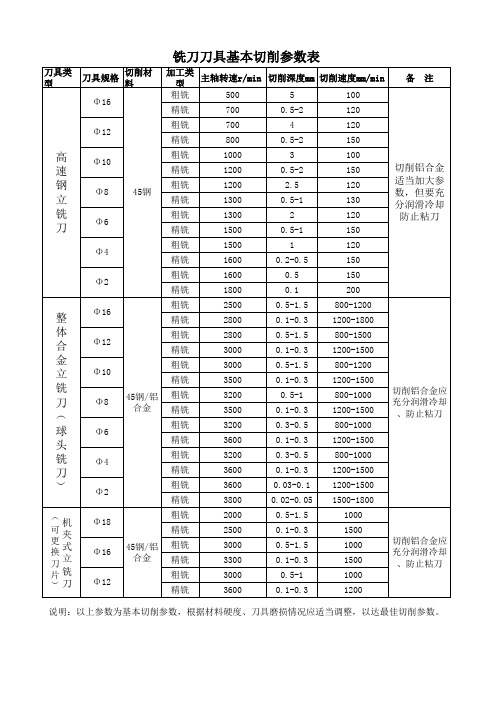
120
防止粘刀
精铣
1500
0.5-1
150
粗铣
1500
1
120
精铣
1600
0.2-0.5
150
粗铣
1600
0.5
150
精铣
1800
0.1
200
粗铣
2500
0.5-1.5
800-1200
精铣
2800
0.1-0.3
1200-1800
粗铣
2800
0.5-1.5
800-1500
精铣
3000
0.1-0.3
1200-1500
说明:以上参数为基本切削参数,根据材料硬度、刀具磨损情况应适当调整,以达最佳切削参数。
刀具类 型
高 速 钢 立 铣 刀
整 体 合 金 立 铣 刀 (
球 头 铣 刀 )
(机
可 更 换 刀
夹 式 立
片铣
)刀
刀具规格
切削材 料
Φ16
Φ12
Φ10
Φ8
45钢
Φ6
Φ4
Φ2
Φ16
Φ12
Φ10
Φ8
45钢/铝 合金
Φ6
Φ4
Φ2
Φ18
Φ16
45钢/铝 合金
Φ12
铣刀刀具基本切削参数表
加工类 型
主轴转速r/min
1500 1000 1500 1000
切削铝合金应 充分润滑冷却 、防止粘刀
精铣
3600
0.1-0.3
1200
说明:以上参数为基本切削参数,根据材料硬度、刀具磨损情况应适当调整,以达最佳切削参数。
铣刀刀具基本切削参数表
加工余量
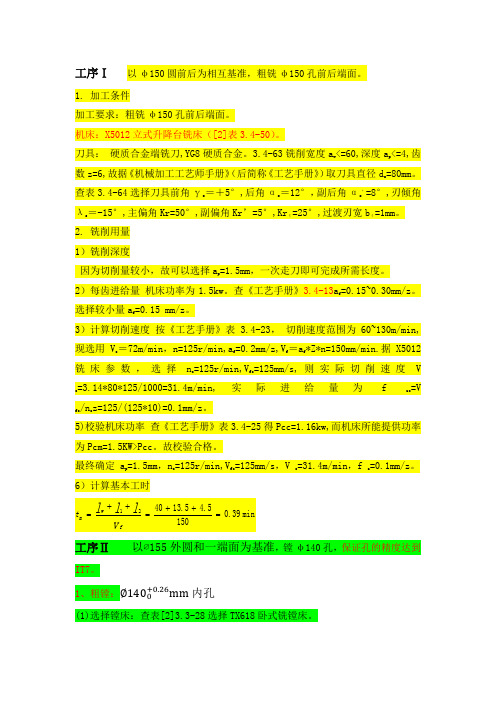
1) 铣削深度 查[2]表3.4-43因为切削量较小,故可以选择ap=0.5mm,一次走刀即可完成所需长度。
2) 每齿进给量 机床功率为1.5kw。查[2]表3.4-13af=0.15~0.30mm/z。由于是对称铣,选较小量af=0.15mm/z。
查《工艺手册》表30-25,寿命T=180min
由表3.2-3得:kMv=1.0,klv=1.0,故V'表=13.5 m/min×1.0×1.0=13.5 m/min.
查Z5040机床说明书,取n=245r/min.实际切削速度为
由表[2]3.2-5得:
kMT=kMF=0.94,故F=6460*0.94=6072N,
T=58*0.94=54.5 N·m
工序Ⅶ: 和∅155一端面为基准,钻圆柱面上两小孔,2X ,保证两孔间距离为32±0.1mm。
1.选择钻床查表[2]3.2-57选Z512-A立式钻床。
加工刀具为:钻孔—ø7.2mm直柄小麻花钻。
2.确定钻削用量
(1)确定进给量
查[2]表3.2-10得:取f=0.4mm/r, 根据表3.2-8,按钻头强度所允许的进给量f'>1.22mm/r, 由于机床进给机构允许的轴向力Fmax=15690N(由机床说明书查出)。
2. 铣削用量
1)铣削深度
因为切削量较小,故可以选择ap=1.5mm,一次走刀即可完成所需长度。
2)每齿进给量 机床功率为1.5kw。查《工艺手册》3.4-13af=0.15~0.30mm/z。选择较小量af=0.15mm/z。
3)计算切削速度 按《工艺手册》表3.4-23,切削速度范围为60~130m/min,现选用Vc=72m/min,n=125r/min,af=0.2mm/z,Vf=af*Z*n=150mm/min.据X5012铣床参数,选择nc=125r/min,Vfc=125mm/s,则实际切削速度Vc=3.14*80*125/1000=31.4m/min,实际进给量为fzc=Vfc/ncz=125/(125*10)=0.1mm/z。