铸件气孔的产生
铸件气孔产生原因及防治方案

气体在金属中的溶解和析出是一个可逆过程,随着温度的升高气体的溶解度增大,温度下降,其溶解度减小,气体析出增加。
气体的外界环境分压力降低时,气体在金属中的溶解度降低,气体也将析出。
气体的析出有三种形式。
第一种气体原子从金属内部扩散到金属表面,脱离吸附状态。
这种形式由于金属液的冷却速度快,粘度大,很难进行。
第二种气体原子与金属内部某元素形成化合物,以非金属夹杂物的形式析出。
第三种气体原子在金属内部形成气体分子,以气泡的形式析出。
如果气泡不能逸出金属液的表面,则将在金属内部形成气孔。
铸件中的气泡就是这样形成的。
在铸造过程中,气孔是由于型壳的透气性不良(没有烧透,材料选择错误,透气性差等),浇注时产生的大量气体不能及时排出,留在铸件内形成孔洞。
气孔不仅减少铸件的有效截面积,且使局部造成应力集中,成为裂纹源,尤其是成串存在的小气泡群,不仅增加缺口的敏感性,使金属强度下降,而且降低零件的疲劳强度。
气孔通常分为析出性气孔、反应性气孔和侵入性气孔。
1、析出性气孔。
金属液在冷却和凝固的过程中,因气体溶解度下降,析出的气体来不及排除,铸件由此而产生的气孔,称为析出性气孔。
这类气孔的特征是:在大型铸件截面上呈大面积分布,而靠近冒口、热节等温度较高区域则分布较密集。
通常金属含气量较多时,气孔形状呈裂纹状;含气量较多时,气孔较大,圆球状。
常发生在同一炉或同一浇包浇注的一批铸件中。
产生析出性气孔的气体,主要是氢气,其次是氮气。
影响析出性气孔形成的因素有:1)、金属液原始含气量。
金属液原始含气量越高,气孔越易形成,静置时间过短,金属溶液内的气体来不及排到熔液表面。
2)、冷却速度。
铸件冷却速度越快,气孔越不易形成。
3)、合金成分。
合金液态收缩大、结晶温度范围大的合金,则容易产生气孔或气缩孔。
4)、气体种类。
气体的扩散速度越快,气孔越不易形成。
2、反应性气孔。
金属液与铸型之间或在金属液内部发生化学反应产生的气体来不及排出,所产生的气孔,称为反应性气孔。
分析铸造过程气孔生成的原因及对策

分析铸造过程气孔生成的原因及对策铸造过程中气孔生成的原因及对策分析铸造是一种重要的金属加工方法,可用于生产各种形状的金属制品。
然而,在铸造过程中,气孔的生成是一个常见的问题,它可能会影响到铸件的质量和性能。
本文将分析铸造过程中气孔生成的原因,并提出相关的对策。
一、原因分析1. 铸造材料的问题在铸造过程中,铸造材料的纯度、含气量和化学成分会直接影响气孔的生成。
杂质和气体在熔融金属中的存在可能会形成气泡,并在凝固过程中被包裹在铸件内部。
此外,如果铸造材料中的挥发性成分含量过高,也容易导致气孔的生成。
2. 模具设计和制造的问题模具的设计和制造不当也是气孔生成的原因之一。
设计不合理的浇口和冷却系统会导致金属在流动过程中吸入空气,形成气孔。
模具的材质和表面处理也会对气孔的生成产生影响,表面粗糙度过高或使用粘结性差的涂料可能会导致铸件表面气孔的形成。
3. 浇注工艺的问题浇注工艺是影响气孔生成的关键因素之一。
浇注温度、浇注速度和浇注角度等工艺参数的控制不当可能导致金属流动不畅,气泡无法完全排出,从而形成气孔。
此外,如果铸件内部存在复杂的几何形状,也会增加气泡在凝固过程中的积累和无法排出的可能性。
二、对策措施1. 提高铸造材料的质量为了减少气孔的生成,需要选用高纯度的铸造材料,并控制好化学成分和气体含量。
可以通过加入脱气剂来减少金属中的气体含量,同时加入合适的合金元素可以改善金属的流动性和凝固性能。
2. 优化模具设计和制造合理的模具设计可以改善金属流动状态,减少气体吸入的可能性。
浇口的设计应考虑到金属的流动路径和速度,确保金属在流动过程中尽量少吸入空气。
此外,模具的材质应选用适合的材料,并进行表面处理以提高其抗粘性和耐腐蚀性能。
3. 控制好浇注工艺参数合理控制浇注温度、浇注速度和浇注角度等参数可以使金属流动顺畅,减少气泡的生成。
同时,在铸造过程中可采用自动浇注系统和真空吸气设备来排除金属中的气体。
对于复杂几何形状的铸件,可以采用分次浇注或采用喷浇工艺来减少气孔的生成。
压铸件气孔的成因和解决办法
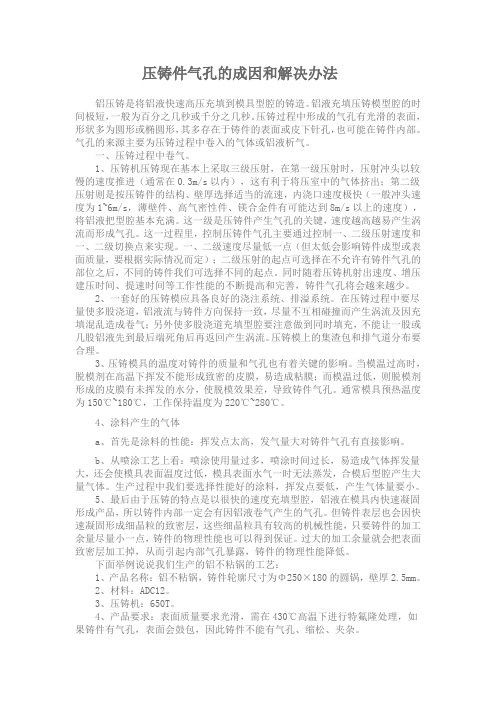
压铸件气孔的成因和解决办法铝压铸是将铝液快速高压充填到模具型腔的铸造。
铝液充填压铸模型腔的时间极短,一般为百分之几秒或千分之几秒。
压铸过程中形成的气孔有光滑的表面,形状多为圆形或椭圆形,其多存在于铸件的表面或皮下针孔,也可能在铸件内部。
气孔的来源主要为压铸过程中卷入的气体或铝液析气。
一、压铸过程中卷气。
1、压铸机压铸现在基本上采取三级压射,在第一级压射时,压射冲头以较慢的速度推进(通常在0.3m/s以内),这有利于将压室中的气体挤出;第二级压射则是按压铸件的结构、壁厚选择适当的流速,内浇口速度极快(一般冲头速度为1~6m/s,薄壁件、高气密性件、镁合金件有可能达到8m/s以上的速度),将铝液把型腔基本充满。
这一级是压铸件产生气孔的关键,速度越高越易产生涡流而形成气孔。
这一过程里,控制压铸件气孔主要通过控制一、二级压射速度和一、二级切换点来实现。
一、二级速度尽量低一点(但太低会影响铸件成型或表面质量,要根据实际情况而定);二级压射的起点可选择在不允许有铸件气孔的部位之后,不同的铸件我们可选择不同的起点。
同时随着压铸机射出速度、增压建压时间、提速时间等工作性能的不断提高和完善,铸件气孔将会越来越少。
2、一套好的压铸模应具备良好的浇注系统、排溢系统。
在压铸过程中要尽量使多股浇道,铝液流与铸件方向保持一致,尽量不互相碰撞而产生涡流及因充填混乱造成卷气;另外使多股浇道充填型腔要注意做到同时填充,不能让一股或几股铝液先到最后端死角后再返回产生涡流。
压铸模上的集渣包和排气道分布要合理。
3、压铸模具的温度对铸件的质量和气孔也有着关键的影响。
当模温过高时,脱模剂在高温下挥发不能形成致密的皮膜,易造成粘膜;而模温过低,则脱模剂形成的皮膜有未挥发的水分,使脱模效果差,导致铸件气孔。
通常模具预热温度为150℃~180℃,工作保持温度为220℃~280℃。
4、涂料产生的气体a、首先是涂料的性能:挥发点太高,发气量大对铸件气孔有直接影响。
铸件产生皮下气孔的原因都有哪些

对于铸件产生的皮下气孔,令许多加工铸件的操作人员感到十分苦恼。
皮下气孔的产生,大多因为铸造过程中各环节或者工序由于操作不当而产生的综合反应。
产生铸件皮下气孔的成因相对复杂,而且影响因素有很多,所以需要操作人员特别引起重视。
下面我们就来具体介绍一下铸件产生皮下气孔的原因都有哪些?一、原材料方面1、进行铸件的时候避免选用含钛、含铝高的原材料以及高合金钢、不锈钢等。
2、对于锈蚀、氧化严重、油污的原材料,需要进行清理后再使用。
3、对于材料表面有潮湿、带水的情况,需要干燥后使用。
4、材料的长度要控制在750px—1000px左右。
二、铁水熔炼方面1、原材料在装炉时,一定要紧实,减少空间,主要是为了减少铁水吸气和氧化。
2、在铁水熔化过程中,要进行检查,避免铁水长时间与空气接触而产生吸气和氧化。
3、熔化好的铁水,高温等待时间不超过10—15分钟,避免成为“死水”的可能性。
4、避免使用不符合标准的增碳剂。
三、孕育剂方面1、使用前需要经过300—400℃的烘烤,去除其内部吸附的水分以及结晶水。
2、孕育剂的力度在5—10mm,含铝量要<1%。
四、浇注方面1、大、小包一定要烘干、烘透,禁止使用湿包装,严禁使用铁水烫包代替烘干。
2、提高浇注温度,高温快浇,浇注温度提高30—50℃,可以使气孔发生率大大降低。
浇注时让铁水充满直交道,中间不断流,抵制界面气体侵入。
3、小包铁水温度低于1350℃,应回炉提温后使用。
4、加强挡渣、蔽渣,氧化皮要及时进行清除,防止其带入型腔。
五、混砂方面1、严格控制型砂水分不大于3.5%。
2、选用优质膨润土和煤粉。
3、每天混砂结束,要将多余型砂回收,并彻底清理和打扫混砂机。
六、模具和造型方面1、模具分型面在设计与生产时要注意设置排气孔槽或排气道及暗气室,主要为了减轻气体压力。
2、在模具上需要增设暗气室,其作用也是为了减轻气体压力。
3、在横浇道或砂芯上面洒冰晶石粉。
铸件气孔产生的原因
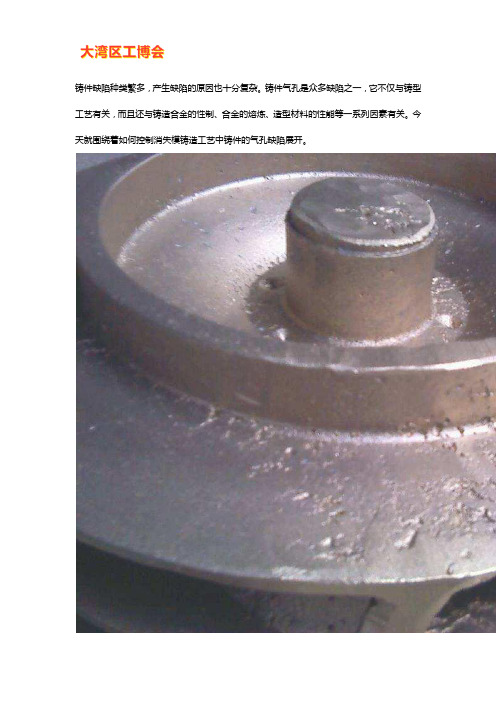
铸件缺陷种类繁多,产生缺陷的原因也十分复杂。
铸件气孔是众多缺陷之一,它不仅与铸型工艺有关,而且还与铸造合金的性制、合金的熔炼、造型材料的性能等一系列因素有关。
今天就围绕着如何控制消失模铸造工艺中铸件的气孔缺陷展开。
1、选择适宜的模型材料采用共聚泡沫模型材料,由于共聚物是拉链式分解,一次性气化程度高,液相比例小,小分子气体很容易从涂层溢出,白模密度在强度和光洁度保证的前提下尽可能小一些,减少发气总量,浇注系统采用空心直浇道并加设过滤器,对金属液进行机械挡渣、吸附梳流,使充型更平稳。
2、浇注系统及保温冒口的使用内浇道的开设要利于合金的顺利平稳快速充型,不形成死角区,在铸件的顶部设置大气压力保温冒口,集渣补缩于一体,相关部位设置随形隔砂冷铁,实现铸件的顺序凝固,把金属液内的气体、渣质及气化残留物快浮到冒口部位,减少气孔、渣孔、缩孔产生的几率。
3、提高涂料的透气性耐火骨料的粒度要适宜,采用复合粘结剂悬浮剂,配制的涂料具有高低温强度好、耐磨损、易涂刷、不开裂、排气能力强、透气性好、烧结均匀、开箱易脱落剥离,不与金属液润湿剂及化学反应,一般铸件涂刷2遍,涂层厚度2mm左右。
消失模涂料的质量管理十分关键。
在大量生产时,定期检查涂料的透气性,及时调整骨料的粒度。
由于涂料的粘结剂、悬浮剂中含有机物质,夏秋季节特别应该注意涂料的发酵酶变,合格的铸件离不开最佳的涂料,控制涂料的质量不可轻心。
4、浇注温度要适宜由于消失模的充型过程中药放热汽化泡沫,钢铁的浇注温度较砂型铸造高30-50℃。
金属液与泡沫的热作用受热浇注温度的制约,浇注温度适宜热解充分,模样的热解产物主要呈小分子气态,在负压场的作用下容易排除型腔,当浇注温度低时,模样的热解不充分,液相残留物会堵塞涂料层,热解气体排出受阻,型腔内形成反压力,充型流动性由此下降,再加上凝固速度快,液体附近的气渣来不及浮集到冒口内,生成气孔的几率增大,当然浇注温度要与冶炼的材料匹配,以避免因温度高或底而产生的其他铸造缺陷。
铸造气孔解决方法
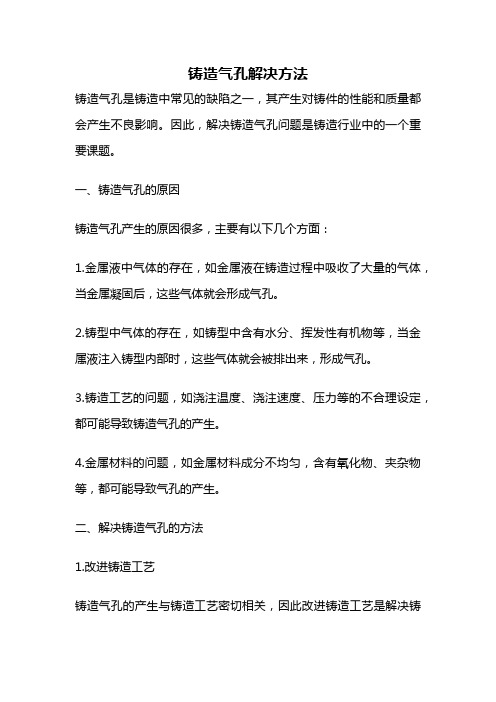
铸造气孔解决方法铸造气孔是铸造中常见的缺陷之一,其产生对铸件的性能和质量都会产生不良影响。
因此,解决铸造气孔问题是铸造行业中的一个重要课题。
一、铸造气孔的原因铸造气孔产生的原因很多,主要有以下几个方面:1.金属液中气体的存在,如金属液在铸造过程中吸收了大量的气体,当金属凝固后,这些气体就会形成气孔。
2.铸型中气体的存在,如铸型中含有水分、挥发性有机物等,当金属液注入铸型内部时,这些气体就会被排出来,形成气孔。
3.铸造工艺的问题,如浇注温度、浇注速度、压力等的不合理设定,都可能导致铸造气孔的产生。
4.金属材料的问题,如金属材料成分不均匀,含有氧化物、夹杂物等,都可能导致气孔的产生。
二、解决铸造气孔的方法1.改进铸造工艺铸造气孔的产生与铸造工艺密切相关,因此改进铸造工艺是解决铸造气孔问题的首要措施。
具体来说,可以采取以下措施:(1)提高浇注温度,减少金属液中气体的溶解度,从而减少气孔的产生。
(2)控制浇注速度和压力,使金属液充分填充铸型,减少气孔的产生。
(3)改进浇注系统,减少金属液的冲击和喷溅,从而减少气孔的产生。
2.改进金属材料金属材料的成分和质量对铸造气孔的产生也有很大的影响。
因此,改进金属材料也是解决铸造气孔问题的重要措施。
具体来说,可以采取以下措施:(1)改进金属材料的制备工艺,减少夹杂物、氧化物等的产生。
(2)优化金属材料的成分和配比,使其成分均匀,减少气孔的产生。
3.改进铸型和模具铸型和模具的质量对铸造气孔的产生也有很大的影响。
因此,改进铸型和模具也是解决铸造气孔问题的重要措施。
具体来说,可以采取以下措施:(1)优化铸型设计,使其能够充分填充金属液,减少气孔的产生。
(2)加强铸型的密封性,减少铸型中气体的存在,从而减少气孔的产生。
(3)采用高质量的模具材料,减少模具中气体的存在,从而减少气孔的产生。
4.采用热处理技术热处理技术可以改变铸件中的组织结构,从而减少气孔的产生。
具体来说,可以采用以下热处理技术:(1)固溶处理:将铸件加热到一定温度,使其中的溶质均匀分布,从而减少气孔的产生。
树脂砂铸造铸件产生气孔的原因及防止

树脂砂铸造铸件产生气孔的原因及防止概述:面对不断增长着的生产优质铸件的压力,同时又面临缺少有专长的劳动力的局面。
时至今日,国内越来越多的公司(或企业)选择由粘土砂干型铸造工艺转为呋喃树脂砂铸造工艺。
与粘土砂干型铸造工艺相比,呋喃树脂砂铸造工艺具有下述优点:铸件表面质量好、尺寸精度高、废品率低,适用范围广、对工人技术水平要求低,大大减轻了工人的劳动强度和改善工作环境,生产率提高40-60%。
但在生产过程中,也存在着一些问题,如果不加以重视和解决,势必会带来不必要的经济损失。
因此,我们在树脂砂生产技术方面,作了一些工作与探索,为我铸造车间进一步扩大业务,拓宽产品范围,作出了努力,本文主要论述的是树脂砂铸造铸件产生气孔的原因及防止。
关键词:呋喃树脂砂气孔防止气孔是树脂砂铸造中最常见的缺陷之一,采用自硬树脂砂造型工艺尽管铸件气孔缺陷大为减少,但如果工艺、熔炼、浇注等措施不当,气孔缺陷也时有发生。
气孔(气眼、气泡、呛火)主要在铸件内部、表面或近于表面处于有大大小小不等的光滑孔眼,形状有圆的、长的及不规则的、有单个的、也有聚集片的,颜色为白色或带一层暗包,有时覆有一层氧化皮。
目前,比较常用树脂砂铸造灰铸、球铁、合金铸铁、碳钢以及低碳合金钢,都会产生气孔,从铸件的气孔来看,主要有侵入性气孔、析出性气孔、反应性气孔等,它们对铸件的质量有不同的影响,但影响大多比较的大,甚至造成铸件的报废,因此,我们要想方设法的去防止、控制、阻止它的产生。
1 气体的来源在树脂砂铸造铸件中,铸件产生气孔是比较常见的,主要是由各种气体形成的,想要更好的去防止、控制、阻止它的产生,就必须找到气体的来源,它的来源主要在熔炼、铸型、材料、浇注等过程中产生。
1.1 熔炼过程[1]熔炼过程中气体的来源,如表一所示,主要来自各种炉料的锈湿以及周围气氛中的水分、氮、氧、以及Co2、Co、So2、H2及有机物燃烧产生的碳氢化合物等。
表一熔炼过程中气体的来源气体种类气体来源氢1、炉料中的水分、氢氧化合物、有机物。
压铸件气孔产生的原因

压铸件气孔产生的原因产生气孔的原因有以下几点:一、氢气残留。
原材料里面还有氢气,坩埚及环境还有湿气,导致气体加热产生氢气夹裹在原材料里面,容易产生针状气孔。
二、压射室充满度不高。
压射室充满度不高会导致压射室内含空间过大,铝汤在压射前,出现回流撞击,产生涡流。
气泡是模具温度及铝温太高,容易产生气泡。
氢气,压射缸卷起,流道卷起,型腔内压力卷起,水蒸气产生气孔这些都是模具气孔的主因。
产生原因:1、金属液在压射室充满度过低(控制在45%~70%),易产生卷气,初压射速度过高。
2、模具浇注系统不合理,排气不良。
3、熔炼温度过高,含气量高,熔液未除气。
4、模具温度过高,留模时间不够,金属凝固时间不足,强度不够过早开模,受压气体膨胀起来。
5、脱模剂、注射头油用量过多。
6、喷涂后吹气时间过短,模具表面水未吹干。
解决压铸件气孔的办法:先分析出师什么原因导致的气孔,再来取相应的措施。
(1)干燥、干净的合金料。
(2)控制熔炼温度,避免过热,进行除气处理。
(3)合理选择压铸工艺参数,特别是压射速度。
调整高速切换起点。
(4)顺利填充有利于型腔气体排出,直浇道和横浇道有足够的长度(>50mm),有利于合金液平稳流动和气体有机会排出。
可改变浇口厚度、浇口方向、在形成气孔的位置设置溢流槽、排气槽。
溢流品截面积总和不能小于内浇口截面积总和的60%,否则排渣效果差。
(5)选择性能好的涂料及控制喷涂量。
预防措施:1、调整压铸工艺参数、压射速度和高压射速度的切换点。
2、修改模具浇道,增设溢流槽、排气槽。
3、降低缺陷区域模温,从而降低气体的压力作用。
4、调整熔炼工艺、5、延长留模时间,调整喷涂后吹气时间。
6、调整脱模剂、压射油用量。
气孔是压铸件中常见多发的缺陷之一。
气孔呈圆形或扁平椭圆形气泡状,直径为1mm至20mm不等,内表面光滑,覆有一层氧化层,通常分散在加工表面下。
一、气孔缺陷的成因01 金属杂质过多原材料或回收料中含有较多的氧化物和其他杂质,一些杂质(如氧化物、氢化物、油脂)在熔炼过程中会释放气体。
检测铸件气孔的方法

检测铸件气孔的方法一、引言在我国的铸造行业中,铸件气孔是一个常见的问题。
气孔的存在不仅影响铸件的外观质量,还会对其使用性能产生严重影响。
为了确保铸件的质量,对铸件气孔的检测至关重要。
本文将对铸件气孔的成因、危害以及常用的检测方法进行介绍,以帮助大家更好地了解和解决这一问题。
二、铸件气孔的成因及危害铸件气孔主要是由于铸造过程中,金属液与型砂、芯砂等固体粒子发生反应产生的气体在凝固过程中无法及时排出而在铸件内部形成的。
铸件气孔的存在会使铸件的强度、硬度、耐磨性等性能降低,同时还容易导致铸件在使用过程中出现裂纹、变形等现象。
三、检测铸件气孔的常用方法1.肉眼观察:通过肉眼直接观察铸件表面和断面,观察是否存在气孔。
这种方法适用于较大型的铸件,但对于微小气孔和内部气孔难以发现。
2.低倍显微镜检测:使用低倍显微镜观察铸件的表面和断面,可以较准确地检测到微小气孔。
但低倍显微镜检测仍然难以发现内部气孔。
3.超声波检测:利用超声波在铸件中的传播特性,检测铸件内部是否存在气孔。
这种方法无损检测,适用于各种类型的铸件,但对于形状复杂、厚度变化的铸件检测效果有所降低。
4.射线检测:通过射线对铸件进行透射,观察射线底片上是否存在气孔。
这种方法适用于厚壁、大型铸件的检测,但射线对人体有一定危害,需采取防护措施。
5.渗透检测:将渗透剂涂抹在铸件表面,通过检测气孔处渗透剂的扩散情况来判断气孔的存在。
这种方法适用于表面光滑、无油污的铸件,但对于内部气孔和微小气孔检测效果较差。
四、各种检测方法的优缺点对比1.肉眼观察和低倍显微镜检测:优点是操作简便、成本低,适用于大型铸件的表面气孔检测。
缺点是难以发现微小气孔和内部气孔。
2.超声波检测:优点是无需破坏铸件,可以检测到内部气孔。
缺点是对形状复杂、厚度变化的铸件检测效果有所降低,且对微小气孔检测效果较差。
3.射线检测:优点是适用于厚壁、大型铸件的检测,检测精度较高。
缺点是射线对人体有一定危害,需采取防护措施。
压铸件气孔的成因和解决方法2

压铸件气孔的成因和解决方法2一. 人的因素:1. 脱模剂是否噴得太多?因脱模济发气量大,用量过多时,浇注前未燃尽,使挥发气体被包在铸件表层。
所以在同一条件下,某些工人操作时会产生较多的气孔的原因之一。
选用发气量小的脱模济,用量薄而均匀,燃净后合模。
2 未经常清理溢流槽和排气道?3 开模是否过早?是否对模具进行了预热?各部位是否慢慢均匀升温,使型腔、型芯表面温度为150℃~200℃。
4 刚开始模温低时生产的产品有无隔离?5 如果无预热装置时是否使用铝合金料慢速推入型腔预热或用其它方法加热?6 是否取干净的铝液,有无将氧化层注入压室?7 倒料时,是否将勺子靠近压室注入口,避免飞溅、氧化或卷入空气降温等。
8 金属液一倒入压室,是否即进行压射,温度有无降低了?。
9 冷却与开模,是否根据不同的产品选择开模时间?10 有无因怕铝液飞出(飞水),不敢采用正常压铸压力?更不敢偿试当增加比压。
?11 操作员有无严格遵守压铸工艺?12 有无采用定量浇注?如何确定浇注量?二. 机(设备、模具、工装)的因素:主要是指模具质量、设备性能。
1 压铸模具设计是否合理,会否导致有气孔?压铸模具方面的原因:1.浇口位置的选择和导流形状是否不当,导致金属液进入型腔产生正面撞击和产生旋涡。
(降低压射速度,避免涡流包气)2.浇道形状有无设计不良?3.内浇口速度有无太高,产生湍流?4.排气是否不畅?5.模具型腔位置是否太深?6.机械加工余量是否太大?穿透了表面致密层,露出皮下气孔?压铸件的机械切削加工余量应取得小一些,一般在0.5mm左右,既可减轻铸件重量、减少切削加工量以降低成本,又可避免皮下气孔露出。
余量最好不要大于0.5mm,这样加工出来的面基本看不到气孔的,因为有硬质层的保护。
2 排气孔是否被堵死,气排不出来?3 冲头润滑剂是否太多,或被烧焦?这也是产生气体的来源之一。
4 浇口位置和导流形状,有无金属液先封闭分型面上的排溢系统?5 内浇口位置是否不合理,通过内浇口后的金属立即撞击型壁、产生涡流,气体被卷入金属流中?6 排气道位置不对,造成排气条件不良?7 溢气道面积是否够大,是否被阻塞,位置是否位於最后充填的地方?模具排气部位是否经常清理?避免因脱模剂堵塞而失去排气作用。
铸件气孔 -回复
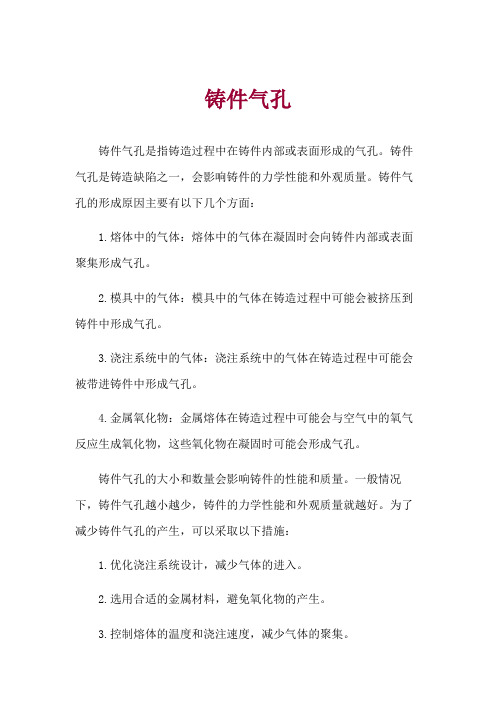
铸件气孔
铸件气孔是指铸造过程中在铸件内部或表面形成的气孔。
铸件气孔是铸造缺陷之一,会影响铸件的力学性能和外观质量。
铸件气孔的形成原因主要有以下几个方面:
1.熔体中的气体:熔体中的气体在凝固时会向铸件内部或表面聚集形成气孔。
2.模具中的气体:模具中的气体在铸造过程中可能会被挤压到铸件中形成气孔。
3.浇注系统中的气体:浇注系统中的气体在铸造过程中可能会被带进铸件中形成气孔。
4.金属氧化物:金属熔体在铸造过程中可能会与空气中的氧气反应生成氧化物,这些氧化物在凝固时可能会形成气孔。
铸件气孔的大小和数量会影响铸件的性能和质量。
一般情况下,铸件气孔越小越少,铸件的力学性能和外观质量就越好。
为了减少铸件气孔的产生,可以采取以下措施:
1.优化浇注系统设计,减少气体的进入。
2.选用合适的金属材料,避免氧化物的产生。
3.控制熔体的温度和浇注速度,减少气体的聚集。
4.采用真空铸造或压力铸造等先进工艺,减少气体的产生。
铸件气孔的检测方法包括目视检查、X射线检测、超声波检测等。
一旦发现铸件气孔,需要进行修补或重新铸造。
铸件渣气孔的产生与预防

铸件渣气孔的产生与预防铸造工业网铸件渣气孔主要产生于八个方面一、熔炼中产生的炉渣(氧化物)二、炉衬材料耐高温不够而产生的熔渣。
三、出炉温度太低,氧化物、夹杂物没有浮出液面。
四、包衬料耐高温不够产生的二次熔渣。
五、金属液太粘,微观气体和微观夹杂物、氧化物无法上浮。
六、钢水初脱氧表面化、终脱氧轻视化,没有炉外精炼净化处理。
七、浇注前没有足够的镇静时间。
八、浇注时冲力太大,浇杯断流,浇道冲沙,涂料脱落等。
铸件渣气孔的杜绝(预防)方法世界上一-切事故预防大于解决手段,铸件渣气孔同样如此,重在预防渣气孔的产生,下面略谈预防方法:一、熔炼产生的炉渣·氧化物的预防1、熔炉材料必须剔除:泥沙,杂质有条件最好抛丸一下再下炉。
2、熔炼炉有条件的最好安装炉盖,既加速炉炼,又省电,防止氧化金属液。
3、熔炼中在不影响加料的情况下,不要除渣(注意:炉渣是最好的保温材料和防止氧化的保护层)。
4、熔炼出炉温度坚持高温出炉低温浇注原则。
5、铸钢熔炼温度到位时进行初脱氧(分多次沉入法脱氧)。
6、终脱氧必须同钢水炉外精炼净化同时进行。
7、冲满钢包后必须用烘烤过的除渣剂覆盖保温镇静2-3分钟。
8、浇注前观察钢包内有无火星飞溅,若有说明脱氧不彻底,必须用铝线补充脱氧直到没有火星飞溅,方可浇筑。
二、炉衬料必须选择耐高温(省略)三、熔炼温度必须坚持高温出炉低温浇注1、铸钢:碳钢1650℃以上,低合金钢1680℃以上,高合金钢1700℃以上。
2、铸铁:球铁1550℃以上,灰铸铁1520℃以上。
四、包衬料预防二次熔渣1、包衬实必须耐高温,建议使用石川牌包衬材料有保障。
2、钢包必须时常修复,剔除掛渣、冷钢(铁)。
3、修补时必须敲打结实、平滑、烘烤到位,充分彻底。
五、增强钢(铁)水流动性,使微观气体、夹杂物、氧化物尽快浮出液面。
六、钢水终脱氧+炉外精炼净化,彻底清除微观氧体,微观夹杂物,氧化物,使钢水洁净无杂。
1、终脱氧剂用量视气候而定,炉外精炼净化剂用量千分之一。
压铸件气孔的成因和解决办法

压铸件气孔的成因和解决办法-标准化文件发布号:(9456-EUATWK-MWUB-WUNN-INNUL-DDQTY-KII压铸件气孔的成因和解决办法铝压铸是将铝液快速高压充填到模具型腔的铸造。
铝液充填压铸模型腔的时间极短,一般为百分之几秒或千分之几秒。
压铸过程中形成的气孔有光滑的表面,形状多为圆形或椭圆形,其多存在于铸件的表面或皮下针孔,也可能在铸件内部。
气孔的来源主要为压铸过程中卷入的气体或铝液析气。
一、压铸过程中卷气。
1、压铸机压铸现在基本上采取三级压射,在第一级压射时,压射冲头以较慢的速度推进(通常在s以内),这有利于将压室中的气体挤出;第二级压射则是按压铸件的结构、壁厚选择适当的流速,内浇口速度极快(一般冲头速度为1~6m/s,薄壁件、高气密性件、镁合金件有可能达到8m/s以上的速度),将铝液把型腔基本充满。
这一级是压铸件产生气孔的关键,速度越高越易产生涡流而形成气孔。
这一过程里,控制压铸件气孔主要通过控制一、二级压射速度和一、二级切换点来实现。
一、二级速度尽量低一点(但太低会影响铸件成型或表面质量,要根据实际情况而定);二级压射的起点可选择在不允许有铸件气孔的部位之后,不同的铸件我们可选择不同的起点。
同时随着压铸机射出速度、增压建压时间、提速时间等工作性能的不断提高和完善,铸件气孔将会越来越少。
2、一套好的压铸模应具备良好的浇注系统、排溢系统。
在压铸过程中要尽量使多股浇道,铝液流与铸件方向保持一致,尽量不互相碰撞而产生涡流及因充填混乱造成卷气;另外使多股浇道充填型腔要注意做到同时填充,不能让一股或几股铝液先到最后端死角后再返回产生涡流。
压铸模上的集渣包和排气道分布要合理。
3、压铸模具的温度对铸件的质量和气孔也有着关键的影响。
当模温过高时,脱模剂在高温下挥发不能形成致密的皮膜,易造成粘膜;而模温过低,则脱模剂形成的皮膜有未挥发的水分,使脱模效果差,导致铸件气孔。
通常模具预热温度为150℃~180℃,工作保持温度为220℃~280℃。
压铸件内部气孔产生的原因

压铸件内部气孔产生的原因
压铸是一种常见的金属铸造工艺,广泛应用于各种行业。
然而,在压铸过程中,气孔是常见的缺陷之一,它对压铸件的质量和性能有很大的影响。
本文将详细分析压铸件内部气孔产生的原因,并提供一些防止气孔产生的建议。
一、气孔产生的原因
1.金属液中气体含量高
金属液在熔炼、浇注过程中会吸收大量的气体,这些气体在金属液中形成气泡。
当气泡无法从金属液中逸出时,就会随着金属液进入压铸件内部,形成气孔。
2.模具温度过高
模具温度过高会导致金属液在模具内的流动性增加,使得气体更容易进入金属液中。
同时,高温还会降低气体在金属液中的溶解度,使得气泡更容易形成和长大。
3.模具设计不合理
模具设计不合理也是导致气孔产生的原因之一。
例如,浇口位置不当、模具排气不良等都会使得气体无法顺利排出,从而形成气孔。
4.操作不当
操作不当也是导致气孔产生的原因之一。
例如,浇注速度过快、浇注温度过低等都会使得气体难以从金属液中逸出,从而形成气孔。
二、防止气孔产生的建议
1.控制金属液中的气体含量
通过采用真空熔炼、离心熔炼等方法降低金属液中的气体含量,从而减少气孔的产生。
2.控制模具温度
合理控制模具温度,避免温度过高或过低,从而减少气孔的产生。
3.优化模具设计
优化模具设计,确保浇口位置得当、模具排气通畅,从而减少气孔的产生。
压铸件内部气孔产生的原因

压铸件内部气孔产生的原因
压铸件内部气孔的产生原因可以有多种,下面列举了几种常见的原因:
1. 模具设计不合理:模具的进气和排气系统设计不合理,导致在铸件充型过程中无法有效地排出空气,从而形成气孔。
2. 原材料含气量高:铸件采用的原材料中含气量较高,当材料在充型过程中受到高压挤压时,气体会被压入铸件内部形成气孔。
3. 润滑剂残留:在模具内涂抹润滑剂时,如果残留过多或没有合适地分布均匀,会在铸件内形成气孔。
4. 入砂速度过快:当铸模进沙速度过快时,砂芯内的空气没有足够时间流出,造成铸件内部气孔。
5. 砂芯设计不合理:砂芯的结构设计不合理,或者砂芯制作过程中存在缺陷,会导致充型过程中无法排出空气,形成气孔。
6. 炉前处理不当:在熔化和浇铸过程中未能有效去除熔融金属中的杂质和气体,导致铸件内产生气孔。
这些都是可能导致压铸件内部气孔产生的常见原因,通过优化设计、改进工艺和加强质量管理,可以减少气孔的产生。
浅谈铸件气孔的产生及其防止措施

浅谈铸件气孔的产生及其防止措施气孔是铸造生产中常见的铸件缺陷之一。
在铸件的废品中,据统计,由于气孔导致的铸件废品占废品总数的三分之一左右。
气孔是气体聚集在铸件表面、皮下和内部而形成的空洞。
气孔的孔壁光滑,无一定的形状、尺寸和位置。
气孔有各种类型,其产生的原因各不相同,按气体来源,一般将气孔分为三类:侵入性气孔、析出性气孔和反应性气孔。
一、侵入性气孔由于浇注过程中液态金属对铸型激烈的热作用,使型砂和芯砂中的发气物(水分、粘接剂等)气化、分解和燃烧,生成大量气体,加上型腔中原有的气体,这些气体部分侵入液态金属内部而不能逸出所产生的孔洞,称为侵入性气孔。
1.侵入性气孔的形成条件由于浇注时铸型在液态金属的高温作用下产生大量气体,从而使液态金属和铸型界面上的气体压力骤然增加,气体可能侵入液态金属,也有可能从型砂或冒口、出气孔中排出型外,只有在满足下列条件的情况下型(芯)砂中的气体才会侵入液态金属即P气>p液+p阻+p腔式中p气:液态金属和砂型界面的气体压力;P液:液态金属的静压力(p液=ρgh)P阻:气体侵入液态金属时,由于液态金属表面张力而引起的阻力P腔:型腔中液态金属液面上的气体压力2.防止侵入性气孔的主要方法和工艺措施(1)降低砂型(芯)界面的气体压力是最有效的手段。
如选用透气性好,发气量低的造型材料;控制型砂的水分及其它发气附加物;应用发气量低、发气速度慢、发气温度高的粘结剂;砂型(芯)排气要畅通,增加出气孔,提高铸型的排气能力;浇注后及时引火。
引火后可听到气体的爆燃声和砂箱周围燃烧的火焰,砂箱移开后,可看到下部潮湿的痕迹。
说明有大量的气体产生如H2、O2、CO、H2S等气体。
(2)适当提高浇注温度,延迟凝固时间,使侵入的气体有充分的时间从液态金属中上浮和逸出。
(3)加快浇注速度,增加上砂型高度,使有效压力头增加,提高液态金属的静压力。
(4)浇注系统在设置时,应注意液态金属流的平稳,浇注千万不能中断,防止气体卷入金属液中。
铸件气孔和沙眼的区别

铸件气孔和沙眼的区别铸件是工业生产中常见的一种零部件制造技术,而铸件气孔和沙眼则是在铸件加工过程中常见的缺陷问题。
本文将从多个方面对铸件气孔和沙眼进行比较,以便更好地理解它们的区别。
铸件气孔是指在铸件表面或内部产生的气体聚集而形成的孔洞。
这些气孔通常是由于铸造过程中的气体无法完全逸出而产生的。
气孔通常呈现出圆形或椭圆形,大小不一,分布不均匀。
铸件气孔会对铸件的力学性能和密封性能产生负面影响,因此是需要避免的缺陷。
与之相比,沙眼是指铸件表面或内部的砂粒聚集而形成的孔洞。
沙眼通常是由于铸造过程中铸型内的砂粒无法完全融化或燃烧而形成的。
沙眼的形状和大小也不一,分布不均匀。
与气孔相比,沙眼对铸件的力学性能和密封性能的影响相对较小,但仍然是需要处理的缺陷。
铸件气孔和沙眼在形成原因上有所不同。
铸件气孔主要是由于铸造过程中的气体无法完全逸出,导致气体在铸件中聚集形成气孔。
这可能是由于熔融金属中的气体(如氧、水蒸气等)无法完全排出,或者是由于砂芯中的气体无法逸出。
而沙眼则主要是由于铸造过程中铸型内的砂粒无法完全融化或燃烧,残留在铸件中形成沙眼。
铸件气孔和沙眼在外观上也有所不同。
铸件气孔通常呈现出圆形或椭圆形的孔洞,其壁面光滑。
而沙眼则通常呈现出不规则形状的孔洞,其壁面粗糙。
在检测和修复方面,铸件气孔和沙眼也有不同的方法。
对于铸件气孔的检测,常用的方法包括X射线检测、超声波检测和射线检测等。
修复气孔的方法通常包括焊接、热处理和热补等。
而对于沙眼的检测,常用的方法包括目视检测、磁粉检测和渗透检测等。
修复沙眼的方法通常包括打磨、填补和重新铸造等。
铸件气孔和沙眼在对铸件性能影响方面也有所不同。
铸件气孔的存在会降低铸件的强度和韧性,并且容易成为应力集中的起始点,从而导致铸件的断裂。
而沙眼的存在对铸件的力学性能影响较小,但会影响铸件的外观质量,降低铸件的密封性能。
铸件气孔和沙眼是铸件加工中常见的缺陷问题。
它们在形成原因、外观特征、检测方法和对铸件性能的影响等方面都有所不同。
铸件常见的缺陷与产生原因
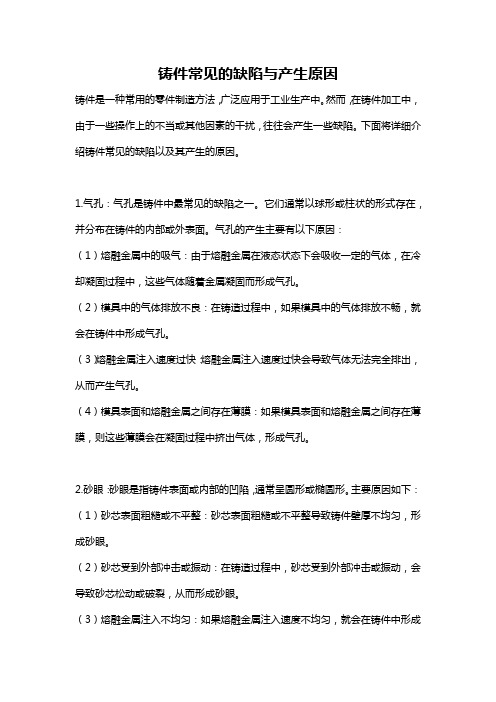
铸件常见的缺陷与产生原因铸件是一种常用的零件制造方法,广泛应用于工业生产中。
然而,在铸件加工中,由于一些操作上的不当或其他因素的干扰,往往会产生一些缺陷。
下面将详细介绍铸件常见的缺陷以及其产生的原因。
1.气孔:气孔是铸件中最常见的缺陷之一。
它们通常以球形或柱状的形式存在,并分布在铸件的内部或外表面。
气孔的产生主要有以下原因:(1)熔融金属中的吸气:由于熔融金属在液态状态下会吸收一定的气体,在冷却凝固过程中,这些气体随着金属凝固而形成气孔。
(2)模具中的气体排放不良:在铸造过程中,如果模具中的气体排放不畅,就会在铸件中形成气孔。
(3)熔融金属注入速度过快:熔融金属注入速度过快会导致气体无法完全排出,从而产生气孔。
(4)模具表面和熔融金属之间存在薄膜:如果模具表面和熔融金属之间存在薄膜,则这些薄膜会在凝固过程中挤出气体,形成气孔。
2.砂眼:砂眼是指铸件表面或内部的凹陷,通常呈圆形或椭圆形。
主要原因如下:(1)砂芯表面粗糙或不平整:砂芯表面粗糙或不平整导致铸件壁厚不均匀,形成砂眼。
(2)砂芯受到外部冲击或振动:在铸造过程中,砂芯受到外部冲击或振动,会导致砂芯松动或破裂,从而形成砂眼。
(3)熔融金属注入不均匀:如果熔融金属注入速度不均匀,就会在铸件中形成砂眼。
3.烧穿:烧穿是指铸件表面和内部出现灰黑色的烧结区域,通常由于铸件在熔融金属中停留时间过长而产生。
其原因主要有以下几点:(1)浇注温度过高:熔融金属温度过高会使铸件在浇注过程中停留时间过长,从而导致烧穿。
(2)浇注时间过长:浇注时间过长会使熔融金属在铸件中停留时间过长,产生过多的热量,最终导致烧穿。
(3)熔融金属中的杂质:熔融金属中的杂质会降低其流动性,导致熔融金属在铸件中停留时间过长并产生烧穿。
4.冷隔:冷隔是指铸件中出现的冷却不良区域,通常呈灰白色或深灰色。
其产生的原因主要有以下几点:(1)注浆速度过快:如果注浆速度过快,就会使熔融金属无法充分填充模具的细小缝隙,从而导致冷隔的形成。
压铸件气孔产生的原因及改进
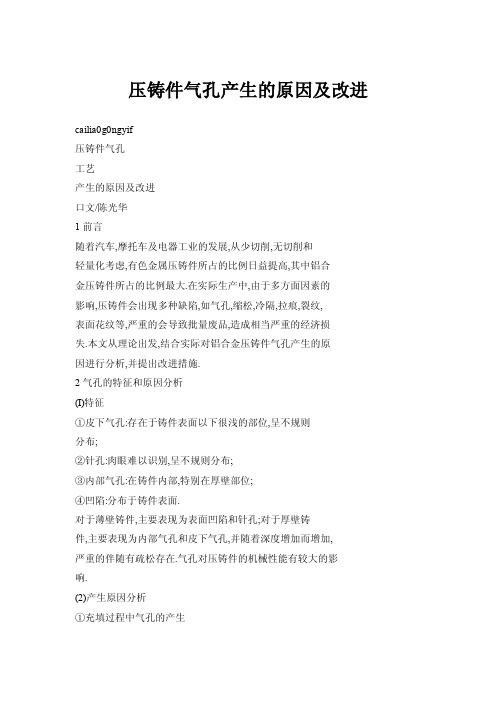
压铸件气孔产生的原因及改进cailia0g0ngyif压铸件气孔工艺产生的原因及改进口文/陈光华1前言随着汽车,摩托车及电器工业的发展,从少切削,无切削和轻量化考虑,有色金属压铸件所占的比例日益提高,其中铝合金压铸件所占的比例最大.在实际生产中,由于多方面因素的影响,压铸件会出现多种缺陷,如气孔,缩松,冷隔,拉痕,裂纹,表面花纹等,严重的会导致批量废品,造成相当严重的经济损失.本文从理论出发,结合实际对铝合金压铸件气孔产生的原因进行分析,并提出改进措施.2气孔的特征和原因分析(I)特征①皮下气孔:存在于铸件表面以下很浅的部位,呈不规则分布;②针孔:肉眼难以识别,呈不规则分布;③内部气孔:在铸件内部,特别在厚壁部位;④凹陷:分布于铸件表面.对于薄壁铸件,主要表现为表面凹陷和针孔;对于厚壁铸件,主要表现为内部气孔和皮下气孔,并随着深度增加而增加,严重的伴随有疏松存在.气孔对压铸件的机械性能有较大的影响.(2)产生原因分析①充填过程中气孔的产生压力铸造的特点是高速高压,这也是压力铸造区别于其它铸造工艺的基本特征.在充填过程中包含着力学,热学和流体力学现象,压力,压射速度,金属温度的变化,使这一过程变得相当复杂.压铸填充过程从理论上分为三个阶段:第一阶段,金属液高速进入型腔,冲击内浇口对面型壁,并沿型壁向其它方向迅速扩展形成壳体;第二阶段,随后进入的金属液继续充满型腔; 第三阶段,型腔内金属液在压射增压的作用下迅速压实冷却. 以上三个阶段虽然从理论上反映了充填过程,但对于充填过程中金属流态没有充分的分析.然而铸件缺陷大多是在这一过程中产生的.在金属液被压射进型腔,冲击内浇口对面型壁并向各方向扩展形成壳体的过程中,产生飞溅和涡流,尤其在铸件的拐角处,冲击涡流更容易产生.随着压射速度的增大,冲击飞溅更加严重,还会提前封堵排气槽和分型面,不能有效地将气体排出.这些残存在型腔中的气体很容易引发气孔产生.②金属液中的气体导致气孔产生在合金熔炼过程中,液态金属与炉气接触,气体在金属液中溶解,其中容易溶解且危害最大的是氢气,及其来自空气和炉气中的水蒸气.在一定的压力下,金属液的温度越高,氢在金属液中的溶解度越高,金属液中的含氢量也越大.溶解于金属液中的氢,随着金属液温度降低,在金属结晶过程中析出,来不及排出型腔的气体有可能形成气孔.③型腔表面涂料的挥发以及涂料喷涂不均匀也会引起气孔产生.3改进措施(I)浇注和排溢系统①在浇注系统中,对产生气孔影响较大的是内浇口.在设计时应注意以下几点:金属液从铸件厚壁处充填;金属液进入型腔后不能立刻封闭分型面和排溢系统;尽量减少金属液对内浇口对面型壁和型芯的冲击;尽可能采用单个内浇口,以免金属液相互冲击,形成涡流和飞溅.②根据金属液流态分析,结合溢流槽设置,在合适部位开排气槽,将型腔中的气体排出.③与排气槽配合,开设溢流槽,不但可将气体和冷污金属排出型腔,还能控制金属液的充填流态,减少或防止涡流形成.(2)压铸工艺在满足成型要求的条件下,尽量采用低温,低压射速度,以减少冲击,飞溅和涡流形成.(3)金属液熔炼在保证化学成分符合要求的情况下,尽量避免炉温过高和保温时间过长,严格执行精炼工艺,对回炉料的配比严格控制, 并进行表面去污处理和预热.(4)选用挥发性低的涂料,并保证喷涂均匀.4结论从以上分析可看出,因起压铸件气孔产生的原因是多方面的,需从压铸机性能,模具设计,压铸工艺等方面进行分析和改进,才能保证产品质量的稳定和提高.2002.5.HEA VYTRuCK'重型汽车>回。
- 1、下载文档前请自行甄别文档内容的完整性,平台不提供额外的编辑、内容补充、找答案等附加服务。
- 2、"仅部分预览"的文档,不可在线预览部分如存在完整性等问题,可反馈申请退款(可完整预览的文档不适用该条件!)。
- 3、如文档侵犯您的权益,请联系客服反馈,我们会尽快为您处理(人工客服工作时间:9:00-18:30)。
型芯怎么防止铸件气孔的产生
用什么办法才能防止型芯的干燥..树脂砂芯因浇注时会产生气体从而导致铸件产生气孔最终导致铸件打废品..
1、防止侵入气孔的措施
(1)提高砂型和砂芯的透气性,控制砂型的紧实度砂型和砂芯的透气性越差,紧实度越高,侵入气孔产生的倾向性越大。
应严格控制砂型的紧实度和透气性。
在保证砂型强度的条件下,尽量降低砂型的紧实度。
采用面砂加粗背砂的方法是提高砂型透气性的有效措施。
(2)控制气体产生的速度严格控制型砂和芯砂中发气物质的加入量,控制湿型的分。
干型应保证烘干质量,并及时浇注,停放时间不要过长。
冷铁或芯铁应保证表面清洁、干燥。
浇口圈和冒口圈应烘干后使用。
(3)提高砂型和砂芯的排气能力铸型上扎排气孔帮助排气,保持砂芯排气孔的畅通,铸件顶部设置出气冒口。
采用合理的浇注系统。
(4)适当地提高浇注温度提高浇注温度可使侵入气体有充足的时间排出。
浇注时应控制浇注高度和浇注速度,保证金属液平稳地流动和充型。
(5)提高金属液的熔炼质量尽量降低铁水中的含硫量,保证铁水的流动性。
防止金属液过分氧化,减小气体排出的阻力。
2、防止卷入气孔的措施
尽量降低浇包与浇口的距离,控制浇注液流的大小,使金属液平稳流动和充型。
正确设计浇口杯的形状和尺寸,用扁圆形浇口杯替代圆锥形浇口杯,避免金属液直接进入直浇道。
横浇道可设计挡渣挡气装置,可采用开放式浇注系统。
对小型铸件或薄壁铸件不应浇注太快。
同时,提高金属液的熔炼质量对防止卷入气孔的产生具有很重要的作用。
3、防止析出气孔的措施
炉料进炉前,对炉料应进行清理,保证炉料的清洁,可采用烘干和喷丸处理,去除炉料表面的氧化皮、油污和水分。
合理地选择熔炼设备和熔炼工艺,对要求比较高的铸件,可采用真空熔炼工艺。
严格控制炉料的配比,尽量降低废钢的用量。
采用各种脱气方法(如浮游气泡脱气、冷凝脱气)对金属液进行精炼,如铝合金熔炼应在铝液上面加覆盖剂并进行精炼;阻止气体析出,如铝合金铸件采用冷铁加速铸件的冷却。
使金属液在压力下结晶,可以有效地阻止气体析出,从而避免析出气孔的形成。
4、防止反应气孔的措施
钢液脱氧要完全,严格控制型砂的水分和透气性,避免在潮湿环境中浇注钢或铝铸件。
对于球墨铸铁除了减少铁水中的含气量外,在保证球化质量的前提下,尽量降低镁的含量,同时,严格控制砂型的水分。
提高浇注温度对防止皮下气孔非常有效。
保持金属液流动充型的稳定性,适当提高浇注温度,采用慢浇工艺。