A03136生产线平衡分析和瓶颈改善dxc
A03136生产线平衡分析和瓶颈改善dxc

12.瓶颈效应(xiàoyìng):是指瓶子颈部流量的大小限制了倒水时 的水
第十四页,共62页。
13.瓶颈的不良影响: A.工序的先后关系,会影响后续工序进度: B.工序间的平行关系,那么(nà me)会影响产品配套
第十五页,共62页。
二、平衡改善法那么(nà me)及本卷须知 1.平衡改善法那么(nà me)-ECRS法那么(nà me)
第七页,共62页。
第二节、消费线平衡(pínghéng)剖析与改善
一、平衡剖析用语 1.节拍(jiépāi)(PITCH TIME):节拍(jiépāi)是指在规那么时间内完成预定产量, 各工序完成单位成品所需的作业时间。其计算公式: 节拍(jiépāi)=有效出勤时间/[消费方案量X〔1+不良率〕] 例:每月的义务天数为20天,正常义务时间每班次为480分钟,该企业实行 每天2班制,假定该企业的月消费方案量为19200个,不良率为0%,请问该 企业的消费节拍(jiépāi)是多少? 答:节拍(jiépāi)时间=有效出勤时间/[消费方案量X〔1+不良率〕] =480X2X20/[19200X〔1+0%〕] =60秒/个
第二十一页,共62页。
3.平衡改善进程中应本卷须知: A.需求异常(yìcháng)工具和机器的作业要素可分配在同一公用设备工序内 B.作业要素相反或前后相近的应尽量分配在同一工序 C.不相容的作业尽量不分在同一工序 D.必要时可对关键作业,添加操作人数或改用更有效的工具/设备以延伸其作业 时间,提高平衡率 E.消费线补进新手时,因新手对义务不熟习,在配置上需特别留意,否那么会构成 严重的不平衡致使产量大幅下降。 F.采用ECRS法那么中止改善时的优先顺序为:〝取消〞不用要的举措或工序 〔第一选择〕;〝兼并〞庞大举措〔次选〕;〝重排〞作业工序或举措〔第三 选择〕;〝简化〞复杂举措或工序〔最后选择〕
(07)线平衡分析与瓶颈改善

安敏 ·《工业工程与生产效率改善》
1、追求线平衡的目的和意义
L B ine alancing 线平衡 线平衡是对生产线的全部工序进行负荷分析,通过调整 工序间的负荷分配使之达到能力平衡,最终提高生产线的整 体效率。这种改善工序间能力平衡的方法又称为瓶颈改善。
线平衡分析及瓶颈改善的主要目的是: ☆ 提高人员及设备的生产效率
颈就是生产的最短木板,从根本上限制生产能力、生产进度和生产效率。
•TOC理论: • 以色列物理学家艾利·高德拉特(Eliyahu Goldratt)博 士创造的Theory of Constraints理论(简称TOC理论,也称为 制约理论)。其实,TOC理论的哲学基础并不奥秘,就是我们熟 悉的“水桶理论”,也就是“决定木桶盛水量多少的是最短的 那块木板”。高德拉特从系统的角度出发,强调提高系统的有 效产出、降低库存、减少运作费用。
3、线平衡改善的判断标准
一般来说,平衡损失率在 5~15% 以内 是可以接受的,否则就要进行改善。
安敏 ·《工业工程与生产效率改善》
4、线平衡分析的基本步骤
(1)确定分析对象的范围:对象生产线和对象工序; (2)把握分析对象的现状; (3)明确标准工时或观测各工序纯工时; (4)制作工序作业速度分析图(棒形图); (5)计算生产线平衡率和平衡损失率; (6)研究分析结果,制定改进方案。
安敏 ·《工业工程与生产效率改善》
瓶颈管理-生产线平衡与瓶颈改善
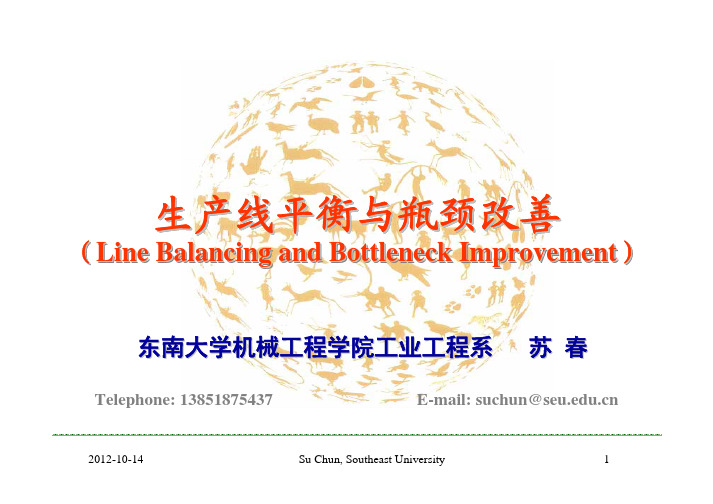
2012-10-14
Su Chun, Southeast University
16
生产线平衡分析的常用术语
1. 生产节拍(cycle time): 节拍表征生产线在规定时间内完成预定产量的能力,即各工 序完成单位产品加工所需的作业时间。
节拍=有效出勤时间/[完成产量 *(1+不良率)]
1.木桶定律: 一个木桶盛水多少,不取决于最高的那块木板,而是取决于 最短的那块木板。
2.木桶定律的三个推论: A. 只有桶壁上所有木板都足够高,木桶才
能盛更多的水。 B. 其它木板中,高出最低木板的部分是没有
意义的,并且高出越多、浪费越大。 C. 提高木桶容量最有效的办法:设法增加最
低木板的高度。
1
提纲
生产线平衡的基本概念 生产线平衡分析的常用术语 生产线平衡分析的基本方法 生产线平衡案例分析
2012-10-14
Su Chun, Southeast University
2
生产线平衡的基本概念
2012-10-14
Su Chun, Southeast University
3
木桶定律
29
生产线平衡分析的基本方法
工序工时改善的基本手段
9 减少动作次数 9 双手操作 9 缩短移动距离 9 简化动作顺序 9 采用辅助工具 9 减少换装时间 9…
2012-10-14
Su Chun, Southeast University
30
生产线平衡分析的基本方法
ECRS法则
符号
名称
说明
E
取消 Eliminate
出料
入料
2012-10-14
生产线平衡分析与改善套路
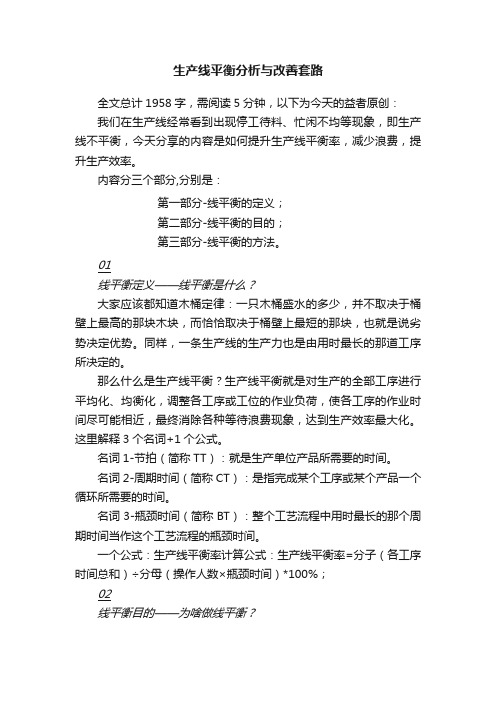
生产线平衡分析与改善套路全文总计1958字,需阅读5分钟,以下为今天的益者原创:我们在生产线经常看到出现停工待料、忙闲不均等现象,即生产线不平衡,今天分享的内容是如何提升生产线平衡率,减少浪费,提升生产效率。
内容分三个部分,分别是:第一部分-线平衡的定义;第二部分-线平衡的目的;第三部分-线平衡的方法。
01线平衡定义——线平衡是什么?大家应该都知道木桶定律:一只木桶盛水的多少,并不取决于桶壁上最高的那块木块,而恰恰取决于桶壁上最短的那块,也就是说劣势决定优势。
同样,一条生产线的生产力也是由用时最长的那道工序所决定的。
那么什么是生产线平衡?生产线平衡就是对生产的全部工序进行平均化、均衡化,调整各工序或工位的作业负荷,使各工序的作业时间尽可能相近,最终消除各种等待浪费现象,达到生产效率最大化。
这里解释3个名词+1个公式。
名词1-节拍(简称TT):就是生产单位产品所需要的时间。
名词2-周期时间(简称CT):是指完成某个工序或某个产品一个循环所需要的时间。
名词3-瓶颈时间(简称BT):整个工艺流程中用时最长的那个周期时间当作这个工艺流程的瓶颈时间。
一个公式:生产线平衡率计算公式:生产线平衡率=分子(各工序时间总和)÷分母(操作人数×瓶颈时间)*100%;02线平衡目的——为啥做线平衡?改善生产线平衡的目的简单来讲就2个:1、资源利用最大化,提升生产效率;2、消除人员等待现象,提升员工士气。
03线平衡方法——怎样做线平衡?工业工程师都应该学过ECRS四大原则,取消、合并、重排、简化;取消不必要的动作,无法取消的想办法合并,重新排列工序,简化作业方法。
生产线平衡采用的方法就是ECRS四大原则。
具体来说,生产线平衡改善,第一步首先要缩短瓶颈时间-提升单位产量;缩短瓶颈的具体方法有三种:1、前后分担转移:相邻间工序工序耗时长的工序,部分作业转移给工序耗时较短的工序;2、作业改善压缩:对瓶颈工序进行作业方法改善,实现工序工时缩短;举个例子:比如以前手机充电要有线接头,现在的无线充电技术,可以省力省时,缩短手机充电操作时间;3、加人改变CT:如果工序时间太长,可以增加人改善工序周期时间,但实际改善中,要求谨慎评估加人改变CT的方法;生产线平衡改善第二步:减少作业人员-产量不变,人员减少;具体方法也有三种:1、工序拆解去除:针对用时最短的工序,进行作业分割转移给其他临近工序,去除该用时最短的工序;2、合并省略工序:在不影响节拍的前提下,可以直接将用时最短的工序与其他临近工序合并,省去该用时最短的工序;3、改善作业合并:先对用时最短的工序进行进一步消除浪费的改善,缩短作业时间,再将该工序合并至其他临近工序,合并该用时最短的工序;一般生产线平衡改善就这两步,先缩短瓶颈时间;再减少作业人员。
(07)线平衡分析与瓶颈改善

线平衡
线平衡与瓶颈改善同样应在 之 间进行,这样才能真正提高生产能力平衡, 间进行,这样才能真正提高生产能力平衡,最大 限度地降低中间在库、提高效率。 限度地降低中间在库、提高效率。
各工段
安敏 ·《工业工程与生产效率改善》 《工业工程与生产效率改善》
(1)肢体使用原则 )
轻松有节奏
(1)双手同时开始、结束动作 )双手同时开始、 2) (2)双手动作对称反向 (3)以最低等级的动作进行作业 ) (4)动作姿势稳定 ) (5)连续圆滑的曲线动作 ) (6)利用物体惯性 ) (7)减少动作注意力 ) (8)动作有节奏 )
安敏 ·《工业工程与生产效率改善》 《工业工程与生产效率改善》
线平衡分析与瓶颈改善
1、追求线平衡的目的和意义 、 2、线平衡率的计算方法 、 3、线平衡改善的判断标准 、 4、线平衡分析的基本步骤 、 5、改善线平衡的六大方法 、 6、瓶颈工序改善 、 7、动作分析与动作要素 、 8、工序作业改善的动作经济原则 、 9、工序作业改善的 、工序作业改善的ECSR原则 原则 10、线平衡改善的有效利用 、
工序1 工序 100件 100件/H 100% 标准产量奖金 个别效率合格
工序2 工序 125件 125件/H 125% 125%奖金 奖金 个别效率高
工序3 工序 80件 80件/H 80% 0 个别效率低
工序4 工序 100件 100件/H 80% 0 个别效率低
达成率
资源类瓶颈 1. 目标是平衡物流,而不是平衡(生产)能力; 2. “非瓶颈”资源的充分利用不仅不能提高有效产出, 而且还会使库存和搬运增加; 3. 让一项资源充分开动运转起来(利用)同使该项资源带来效益(活力)不能划等号; 4. 瓶颈环节损失1小时,相当于整个系统损失1小时,而且是无法补救的 ; 5. 非瓶颈环节上节约1小时,毫无实际意义; 6. 瓶颈制约了生产系统的有效产出和库存;
生产线平衡分析及效率化
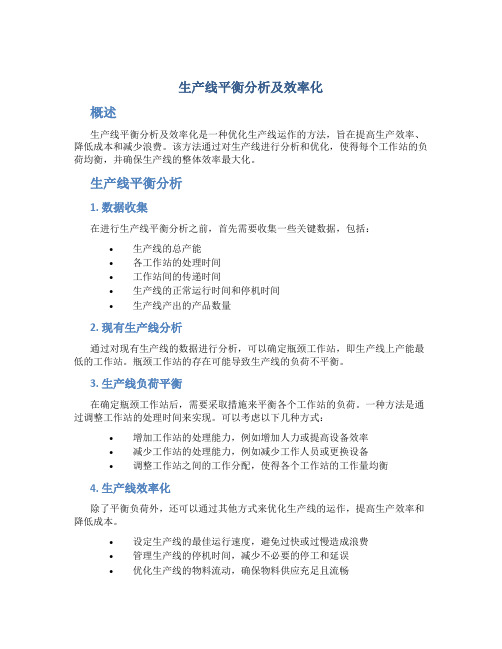
生产线平衡分析及效率化概述生产线平衡分析及效率化是一种优化生产线运作的方法,旨在提高生产效率、降低成本和减少浪费。
该方法通过对生产线进行分析和优化,使得每个工作站的负荷均衡,并确保生产线的整体效率最大化。
生产线平衡分析1. 数据收集在进行生产线平衡分析之前,首先需要收集一些关键数据,包括:•生产线的总产能•各工作站的处理时间•工作站间的传递时间•生产线的正常运行时间和停机时间•生产线产出的产品数量2. 现有生产线分析通过对现有生产线的数据进行分析,可以确定瓶颈工作站,即生产线上产能最低的工作站。
瓶颈工作站的存在可能导致生产线的负荷不平衡。
3. 生产线负荷平衡在确定瓶颈工作站后,需要采取措施来平衡各个工作站的负荷。
一种方法是通过调整工作站的处理时间来实现。
可以考虑以下几种方式:•增加工作站的处理能力,例如增加人力或提高设备效率•减少工作站的处理能力,例如减少工作人员或更换设备•调整工作站之间的工作分配,使得各个工作站的工作量均衡4. 生产线效率化除了平衡负荷外,还可以通过其他方式来优化生产线的运作,提高生产效率和降低成本。
•设定生产线的最佳运行速度,避免过快或过慢造成浪费•管理生产线的停机时间,减少不必要的停工和延误•优化生产线的物料流动,确保物料供应充足且流畅•采用先进的工艺和设备,提高生产线的技术水平和自动化程度•采取精益生产的原则,消除生产线上的浪费和无效操作效果评估进行生产线平衡分析和效率化之后,需要对生产线进行效果评估,以验证改进措施的有效性。
可以考虑以下几个指标:•生产线的总产量是否增加•生产线的负荷是否更均衡•生产线的运行时间是否有所改善•生产线的停机时间是否减少•生产成本是否有所降低结论生产线平衡分析及效率化是优化生产线运作的一种有效方法,可以提高生产效率、降低成本和减少浪费。
通过收集数据、分析现有生产线并采取相应措施来平衡负荷和优化生产线的运作,可以实现生产线的最大效益。
然而,生产线平衡分析和效率化是一个持续不断的过程,需要持续跟踪和评估生产线的运行情况,并根据需要进行调整和改进。
生产线平衡分析和瓶颈改善课程

生产线平衡分析和瓶颈改善课程生产线平衡分析和瓶颈改善课程介绍生产线平衡分析和瓶颈改善是现代生产管理领域中的重要内容。
在市场竞争日益激烈的背景下,企业需要通过优化生产线,提高生产效率和产品质量,降低成本,从而提高竞争力。
因此,生产线平衡分析和瓶颈改善课程成为企业管理者和生产管理人员必备的培训项目。
课程目标生产线平衡分析和瓶颈改善课程旨在帮助学员理解生产线平衡的概念、原则和方法,并学会如何识别和消除生产线中的瓶颈,以提高生产线的总体效能。
课程将向学员提供相关工具和技术,帮助他们在实际工作中应用所学知识。
课程内容1. 生产线平衡的基本概念- 生产线平衡的定义和重要性- 生产线平衡的目标和原则- 生产线平衡和产能计划的关系2. 生产线平衡方法- 产能评估和需求预测- 工序时间测量和工序分析- 均衡方法和工作站平衡- 循序平衡线和非循序平衡线3. 瓶颈和瓶颈理论- 瓶颈的概念和特征- 瓶颈对生产线的影响- 瓶颈理论的原理和运用4. 瓶颈分析和瓶颈改善- 识别和分析瓶颈- 瓶颈改善的策略和方法- 瓶颈的管理和控制5. 实例分析和案例研究- 生产线平衡分析和瓶颈改善的实际案例- 学员将参与分组讨论和解决实际问题的案例研究课程形式为了更好地帮助学员掌握所学知识和技能,课程将采用多种教学形式和教学方法,包括讲座、案例分析、小组讨论、模拟练习和工厂参观等。
通过这些交流和互动的方式,学员将有机会亲身体验并实践所学内容。
受益人群这门课程适用于企业管理者、生产管理人员和其他对生产线平衡分析和瓶颈改善感兴趣的人士。
无论是在制造业还是在服务行业,都可以从课程中受益。
课程对参与者的角色与职务没有特定要求,只要对生产线平衡和瓶颈改善有兴趣,并且希望在工作中提高效率和竞争力,都可以报名参加。
结语生产线平衡分析和瓶颈改善课程旨在帮助企业实现生产线的优化和升级,从而提高竞争力和市场份额。
通过研究和实践,学员将掌握生产线平衡分析和瓶颈改善的核心概念和方法,并能够灵活应用于实际工作中。
线平衡分析与瓶颈改善
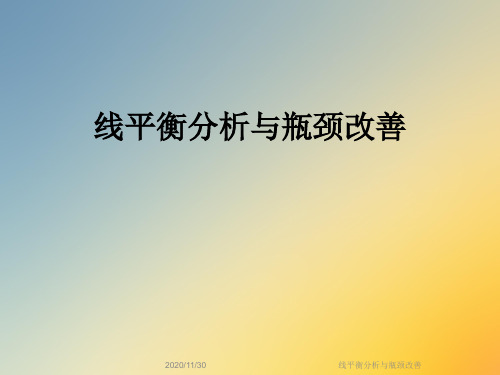
以及工程分析和设计的原理和方法,对该系统所取得的成果进行确定,预测和评价。
•1.2 工业工程的目标:
目标:
工业工程的目标就是设计一个生产系统及该系统的控制方法,使它以最低的成本生产 具有
特定质量水平的某种或几种产品,并且这种生产必须是在保证工人和最终用户的健康和安 全
条件下进行。
线平衡分析与瓶颈改善
2.使用秒表法测量得出的标准工时包含以下几个要素:
•观测时间
•评比因数
•宽放标准
线平衡分析与瓶颈改善
观测时间采集方法:
1. 采取适当的方位,方式及态度进行观测(斜前方2m)事先在纪录表格上记录下要观 测的作业要素及其他必要事项。 2. 多次观测,减少偶然因素的发生。即当所测的数据稳定时纪录的数据。(10times) 3. 不允许随便修改记录的时间值。 4. 去除异常值。 5. 计算平均值,得出观测时间。
•目录:
•1.工业工程概述:
1.1 工业工程的定义 1.2 工业工程的目标 1.3 工业工程的发展史
•2.标准工时基本知识介绍:
2.1 标准工时的定义 2.2 测量标准工时的基本方法
•3.线平衡分析与瓶颈改善:
3.1 线平衡的定义和意义 3.2 生产线平衡的相关概念 3.3 生产线平衡的计算 3.4 生产线平衡的改善原则 3.5 生产线平衡的改善方法
教育
等领域。
线平衡分析与瓶颈改善
•2.标准工时基本知识介绍:
2.1 标准工时的定义
定义:
在正常的操作条件下,熟练工人以标准的作业方法及合理的劳动强度和速度完成符合
质量
要求的某项工作所需作业时间。
利用动作分析、程序分析、操作分析获得最佳的程序和方法,再利用时间研究的基本
生产线平衡分析及瓶颈改善

现场案例某企业某条生产线每月的工作天数为22天,正常工作时间每天为8小时,该生产线做A产品有5个工序,第1个工序(装配1)为28秒,第2个工序(装配2)为34秒,第3个工序(测试)为31秒,第4个工序(总装)为40秒,第4个工序(包装)为24秒),现在客户给了18000个/月的A产品订单,该生产线要如何完成任务?因为每天完不成819台的任务,该生产线的组长找人事部招了1个新员工,让这个新员工在生产线上5个工序来回帮忙,哪里做不过来就到哪里帮忙做。
生产部经理不接受生产线组长这种增加人手的做法,要求进行改善,在不增加人工成本的情况下满足客户的订单需求。
运作思路及具体工作第一步:明确改善目的和对象是否因生产量变动(增产或减产)而进行改善;是否为了提高生产率、减少作业人员;改善针对某条生产线、某段工序还是整个流程。
第二步:测量对象各工序的时间秒表法(正常的作业速度,测试20个以上工序时间,取平均值)第三步:衡量生产线平衡情况1、生产线平衡率水准平衡率<85%,水准差,90%>平衡率≥85%,良好;平衡率≥90%,属于优秀2、客户需求节拍:生产线瓶颈工时要小于客户需求节拍A产品平衡率=生产线各工序时间总和/(瓶颈工时*人员数)=(28+34+31+40+24)/(40*5)=78.5%客户需求节拍=有效出勤时间/[生产计划量*(1+不良率)]=22*8*3600/18000=35.2秒注:瓶颈工时40,客户需求节拍35.2s第四步:明确增值和非增值时间增值时间:物料加工、产品组装,质量控制及对产品有利包装。
非增值时间:包括取料距离大于60厘米,弯腰,走动,物料的质量造成的过程返工缺料的等待,停机,工装夹具的维修时间,物料和半成品的运输等。
(非增值时间:指工作中没有能改变产品特性,但目前又是不可获缺的工作,即工序中没有必要或是由于现有设备和工艺无法满足产品质量要求而设置的工作。
)第五步:通过ECRS法则改善平衡在确保人员和物料正常后,采用ECRS法则改善案例中ECRS运用符号名称说明E取消Eliminate总装中,物料放在员工身后的地上,员工弯腰取料浪费3秒时间。
生产线平衡分析改善

纯作业时间的总和
×100
节拍时间×工序(人员)数
注意 ① 节拍时间从1天的生产数量求得(参照节拍时间TT计算法)
② 但是如果瓶颈工序大于用①计算得出的值,则以瓶颈工序的作业时间为节拍时间值。
■ 平衡损失率(BD値) BD值(%)=100-生产线均衡损失率
8
一.二. 生产线平衡分析
生产线平衡计算(例)
49
以上 谢谢
D
E
产出
20
三. 瓶颈改善
瓶颈的不良影响
B. 工序间的平行关系,会影响产品配套
A
B
平行关系:
C
影响整体工作的完成和配套 产出
D
E
21
三. 瓶颈改善
基本原则和方法:基本方法图示
改进 工具夹具
作业 拆解分割
提高 设备效率
瓶颈 改善
增加 作业人员
提高 作业技能
调整 作业人员
22
三. 瓶颈改善
基本原则和方法:ECRS分析法
7
打胶水 2
4
插线
插变压 插线
7 30
插线 20
5
功能检
功能检 拆线
16 5
贴断电 4
外观检 8
6 外观检 贴条码 2
包装
6
24 1 37 1 45 2 16 1
改善后
电装7人柔性线
工位 岗位名 作业内 动作时 标准时 人员
序号 称
容 间(秒)间(秒) 配置
打变压 10 打电源 7
1
打室内 1 打线 外线
18
三. 瓶颈改善
识别瓶颈
瓶颈效应:是指瓶子颈部流量的大小限制了倒水时的水量
工序“瓶颈”示意图
生产线平衡分析和瓶颈改善63页PPT
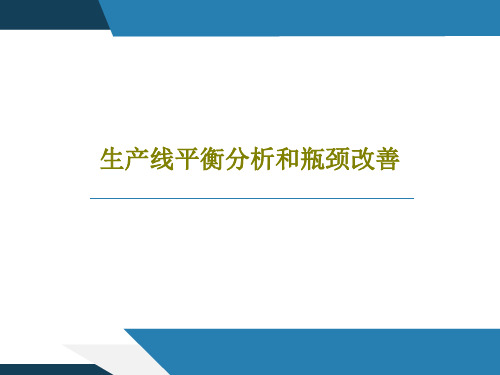
1、最灵繁的人也看不见自己的背脊。——非洲 2、最困难的事情就是认识自己。——希腊 3、有勇气承担命运这才是英雄好汉。——黑塞 4、与肝胆人共事,无字句处读书。——周恩来 5、阅读使人充实,会谈使人敏捷,写作使人精确。——培根
生产线平衡分析和瓶颈改善
1、纪律是管理关系的形式。——阿法 纳西耶 夫 2、改革如果不讲纪律,就难以成功。
3、道德行为训练,不是通过语言影响 ,而是 让儿童 练习良 好道德 行为, 克服懒 惰、轻 率、不 守纪律 、颓废 等不良 行为。 4、学校没有纪律便如磨房里没有水。 ——夸 美纽斯
5、教导儿童服从真理、服从集体,养 成儿童 自觉的 纪律性 ,这是 儿童道 德教育 最重要 的部分 。—— 陈鹤琴
生产线平衡改善方案

生产线平衡改善方案生产线平衡改善方案生产现场遇到的问题: 排拉流程不合理,流水线生产不平衡,线上出现有的员工等待、有的员工堆积从而影响了流水线产量的下降或者达不到标准产量的要求。
员工的工位物料布置不合理,操作动作不经济,造成工序操作时间波动,影响工位的操作效率,尤其是瓶颈工位直接制约整条流水线的产量的提高。
方案的目的: 制定新的排拉流程,使流水线生产均衡化,提高流水线的产量。
改善各工位,特别是瓶颈工位的布料布置和操作动作,使工位操作标准化,培训工人掌握标准操作,提高工位的操作效率。
方案改善的步骤确定新的排拉流程。
1.1项目技术员提供X产品的《标准作业指导书》、原有《排拉流程图》、《产量报表》《标准产能》交项目主管。
1.2项目技术员现场测试现有X产品的工位操作时间和工位与工位之间的距离。
交项目主管。
(工作测定标准表格) 1.3项目主管指导、协调项目技术员完成所需求的资料。
1.4项目主管根据以上资料数据制定X产品的《工艺流程图》、《流水线平整图》找出瓶颈工位和设计新的《排拉流程图》交项目主管和项目经理审核。
1.5项目经理协调各成员按要求完成资料和数据收找出和改善瓶颈工位。
2.1项目主管和项目技术员一起现场对瓶颈工位进集。
2.行动作分析和物料布置分析,将工序分到更细的操作单元并测试每个动作的时间。
(最好用相机将工位操作全程拍摄,再做动作分析)。
2.2项目主管制定《动作分析图》和《双手作业分析图》,设计工作位置物料布置和操作动作方法制定改善后的《动作分析图》和《双手作业流程图》。
交项目经理审核。
2.3项目经理主持召开头脑风暴会议。
充分讨论(必要时到现场讨论)新的《工艺流程图》《排拉流程图》、工位的《动作分析图》《双手作业流程图》的改善合理性最终确定;确定准备制作改善所需的设施;确定何时进行改善试验。
3.改善过程设施的准备和制作。
3.1项目经理协调改善过程所需的工具、夹具等设施的到位。
3.2项目主管跟进改善设施的制作、试用、签收。
- 1、下载文档前请自行甄别文档内容的完整性,平台不提供额外的编辑、内容补充、找答案等附加服务。
- 2、"仅部分预览"的文档,不可在线预览部分如存在完整性等问题,可反馈申请退款(可完整预览的文档不适用该条件!)。
- 3、如文档侵犯您的权益,请联系客服反馈,我们会尽快为您处理(人工客服工作时间:9:00-18:30)。
A03136生产线平衡分析和瓶颈改善dxc
11.瓶颈的常见表现: • 整体进度缓慢,生产效率下降; • 出现产品零部件不能配套的现象; • 一些工序加班赶货,而另一些则很轻松; • 一些工序的半成品堆积过多,而另一些则很少; • 个别工序在等材料、设备,其他工序进展正常; • 个别生产线流动停止,出现在制品滞留时间过长情况。
学习改变命运,知 识创造未来
A03136生产线平衡分析和瓶颈改善dxc
三、平衡改善的实施步骤: 第一步:明确改善目的和对象: • 是否因为生产量变动(增产或减产)而进行的改善 • 是否为了提高生产率、减少作业人员 • 改善对象是一条生产线、某段工序还是整个流程 第二步:了解、分析生产现状及相关人员的工作状况:
学习改变命运,知 识创造未来
A03136生产线平衡分析和瓶颈改善dxc
•案例分析
生产线平衡步骤: 计算产距时间(Takt time) 画优先图(制作工艺流程图) 决定周期时间(CT=Takt time) 确定理论工位数 排程 计算效率
学习改变命运,知 识创造未来
A03136生产线平衡分析和瓶颈改善dxc
学习改变命运,知 识创造未来
A03136生产线平衡分析和瓶颈改善dxc
2.提高生产线平衡效率的意义 • 缩短每一制品装配时间,增加单位时间的生产量,降低生产成
本 • 减少工序间的在制品, 减少现场场地的占用 • 减少工程之间的预备时间,缩短生产周期 • 消除人员等待现象,提升员工士气 • 改变传统小批量作业模式,使其达到一个流生产。 • 可以稳定和提升产品品质 • 提升整体生产线效率和降低生产现场的各种浪费
善
工序 1 2 3 4 5 工序
23
学习改变命运,知 识创造未来
A03136生产线平衡分析和瓶颈改善dxc
•并行作业,增加人员
•拆解去除
1人
作业 作
业
作
时
业
间
时
2人
间
作业
工序 1 2 3 4 5
工序 1 2 3 4 5
学习改变命运,知 识创造未来
A03136生产线平衡分析和瓶颈改善dxc
•作业改善后合并
学习改变命运,知 识创造未来
A03136生产线平衡分析和瓶颈改善dxc
三、生产线平衡的定义及意义 1.为何位的作业负荷或工作量,使各工序的作 业时间尽可能相近或相等,最终消除各种等待浪费现象 ,达到生产效率最大化。它是生产流程设计与作业标准 化中最重要的方法。通过平衡生产,可以加深理解“一 个流”生产模式及熟悉“单元生产”的编制方法,它是 一切新理论与新方法的基础。
• 生产系统的目标是平衡物流,而不是平衡生产能力; • “非瓶颈”资源的充分利用不仅不能提高有效产出,而且还
会使库存和搬运增加; • 瓶颈环节损失1小时,相当于整个系统损失1小时,而且是
无法补救的 ; • 非瓶颈环节上节约1小时,毫无实际意义; • 瓶颈制约了生产系统的有效产出和库存;
学习改变命运,知 识创造未来
学习改变命运,知 识创造未来
A03136生产线平衡分析和瓶颈改善dxc
•稼动损失时间与平衡损失时间的区别
•节拍=33
•瓶颈时间 •=29.2
•此部 •分是 •稼动 •损失 •时间
•此部 •分是 •平衡 •损失 •时间
学习改变命运,知 识创造未来
A03136生产线平衡分析和瓶颈改善dxc
10.瓶颈的(Bottle Neck)定义:阻碍企业流程更大程度增加 有效产出或减少库存和费用的环节谓之瓶颈,瓶颈可能是 有形的,也可能是无形的。
•重排
作
作
业
业
时
时
间
间
工序 1
2
3
4
5
工序 1
2
3
4
5
学习改变命运,知 识创造未来
A03136生产线平衡分析和瓶颈改善dxc
2-1. 平衡改善的基本原则和方法: 通过调整作业工序的作业内容来使作业时间相近或减少这一偏差。 A.首先考虑对瓶颈工序进行改善,作业改善方法可参照程序分析、动 作分析、工装自动化等工程方法和手段 B.将瓶颈工序的作业内容分割给其它工序。 C.合并相关工序,重新排布生产线。 D.分解作业时间较短的工序,把它安排到其它工序中去。 E.增加作业员,只要平衡率提高了,人均产量就提高了,单位成本也随 之下降。
答:节拍时间=有效出勤时间/[生产计划量X(1+不良率)]
=480X2X20/[19200X(1+0%)]
=60秒/个
学习改变命运,知 识创造未来
A03136生产线平衡分析和瓶颈改善dxc
2.传送带速度CV:
传送带速度是指流水线的皮带传递速度,一般情况下,采用一定的 距离作好标记,然后测定其时间,进而得出流水线传送带的实际速 度,计算公式:CV=间隔标记距离/所耗时间。采用流水线作业的 企业,传送带的速度与作业效率、疲劳程度以及能否完成产量有密 切的关系。理想的传送带速度是恰好能完成预定产量的同时又能减 少作业员的身心疲劳。理想的传送带速度的计算公式:CV=间隔标 记距离/节拍时间,因此在现场生产管理过程中,只要把流水线的 皮带速度调成理想的传送带速度即可。
学习改变命运,知 识创造未来
•产距时间:TAKT TIME
Takt Time = Demand Rate(需求速度
)
Takt Time 工作时间
=
生产量
目标:按需求生产 !
A03136生产线平衡分析和瓶颈改善dxc
KQ34-4琴键开关产品装配任务明细表
序
任务描述
时间
紧前任务
01 底座装静触片
6.5
3.瓶颈工时:指生产线所有工序中所用人均工时最长的工序,通常指 一道工序,有时也指几道工序。
学习改变命运,知 识创造未来
A03136生产线平衡分析和瓶颈改善dxc
3.总瓶颈站工时:指瓶颈站工时乘以生产线作业人数的总和。 4.周程时间:是指单个产品从前到后所有工序所费时间的总和。 5.平衡率: 其计算公式=生产线各工序时间总和/(瓶颈工时X人员数) 6.平衡损失:其计算公式=1-平衡率 7.平衡损失时间:其计算公式=∑(瓶颈工时-工位工时) 8.稼动损失时间:其计算公式=(节拍-瓶颈时间)X总人数 9.稼动损失率:其计算公式=稼动损失时间/(节拍X总人数)X100%,平 衡损失时间与稼动损失时间是两个不同的概念,平衡损失时间是瓶颈 工时与各工位工时时间差的总和,而稼动损失时间是工序生产节拍与 瓶颈工时时间差的总和,它们之间的关系如下图所示:
如各工位或工序的良品率有多高?人员出勤状况、产品加工的难易 度、品质事故的发生点等。 第三步:了解产品工艺流程并分解各工程的作业要素:根据工程分析图 了解加工作业内容,依据作业拆分原则拆分各工程的作业要素。 第四步:对各作业要素进行时间观测
学习改变命运,知 识创造未来
A03136生产线平衡分析和瓶颈改善dxc
学习改变命运,知 识创造未来
A03136生产线平衡分析和瓶颈改善dxc
3.平衡改善过程中应注意事项: A.需要同样工具和机器的作业要素可分配在同一专用设备工序内 B.作业要素相同或前后相近的应尽量分配在同一工序 C.不相容的作业尽量不分在同一工序 D.必要时可对关键作业,增加操作人数或改用更有效的工具/设备以 缩短其作业时间,提高平衡率 E.生产线补进新手时,因新手对工作不熟悉,在配置上需特别注意,否 则会造成严重的不平衡致使产量大幅下降。 F.采用ECRS法则进行改善时的优先顺序为:“取消”不必要的动作 或工序(第一选择);“合并”微小动作(次选);“重排”作业 工序或动作(第三选择);“简化”复杂动作或工序(最后选择)
2.木桶定律的三个推论
A.只有桶壁上所有木板都足够高,木桶才能盛满水
B.所有木板高出最低木板的部分是没有意义的,而且高出越多, 浪费就越大
C.提高木桶容量最有效的办法就是设法加高最低木板的高度
学习改变命运,知 识创造未来
A03136生产线平衡分析和瓶颈改善dxc
二、生产线平衡与木桶定律的关系 “生产线平衡”与“木桶定律”非常相似:生产线的最 大产能不是取决于作业速度最快的工位,而恰恰取决于 作业速度最慢的工位,最快与最慢的差距越大,产能损 失就越大。 制造现场,各个车间或小组之间,彼此的管理水平、产 能等往往是不等的,企业现场管理的整体水平并不取决 于最优秀的车间单位而是取决于最差的车间单位,同理 ,对一条生产线来言,其产量、效率高低也是如此。
学习改变命运,知 识创造未来
A03136生产线平衡分析和瓶颈改善dxc
12.瓶颈效应:是指瓶子颈部流量的大小限制了倒水时的水
学习改变命运,知 识创造未来
A03136生产线平衡分析和瓶颈改善dxc
13.瓶颈的不良影响: A.工序的先后关系,会影响后续工序进度:
B.工序间的平行关系,则会影响产品配套
无
02 装扣板和扣簧
4.5
01
03 装联锁片[铁]*2
5.5
02
04 装长动触片*2
7.5
03
05 装长动触片*1
5
04
06 装卡板*2
3.5
05
07 装卡板+零档卡板
3.5
06
08 装盖板
5
07
09 分塔簧+装塔簧
11.5
08
10 压塔簧
S
简化
经过取消、合并、重排后的必要工序,应考虑能否
Simplify 采用最简单的方法或设备替代,以节省人力和时间
• 以上ECRS法则,具体可通过下列图片来说明生产中如何运用改善:
学习改变命运,知 识创造未来
A03136生产线平衡分析和瓶颈改善dxc
•作业改善压缩
•分割转移
作
业
作