大型储罐倒装施工液压提升工法
筒式钢制储罐液压提升倒装技术施工工法(2)
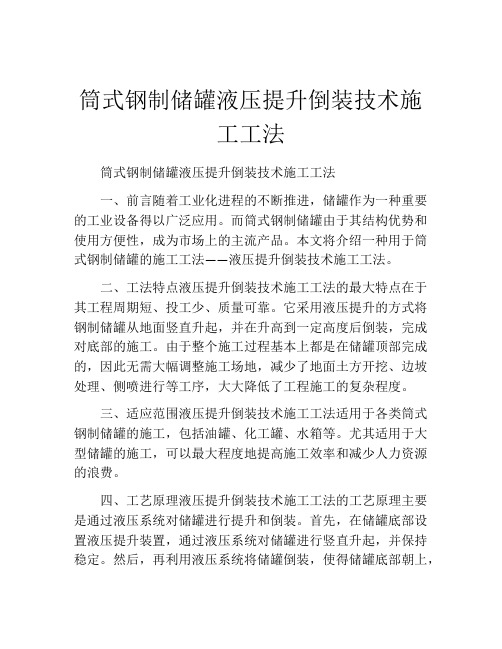
筒式钢制储罐液压提升倒装技术施工工法筒式钢制储罐液压提升倒装技术施工工法一、前言随着工业化进程的不断推进,储罐作为一种重要的工业设备得以广泛应用。
而筒式钢制储罐由于其结构优势和使用方便性,成为市场上的主流产品。
本文将介绍一种用于筒式钢制储罐的施工工法——液压提升倒装技术施工工法。
二、工法特点液压提升倒装技术施工工法的最大特点在于其工程周期短、投工少、质量可靠。
它采用液压提升的方式将钢制储罐从地面竖直升起,并在升高到一定高度后倒装,完成对底部的施工。
由于整个施工过程基本上都是在储罐顶部完成的,因此无需大幅调整施工场地,减少了地面土方开挖、边坡处理、侧喷进行等工序,大大降低了工程施工的复杂程度。
三、适应范围液压提升倒装技术施工工法适用于各类筒式钢制储罐的施工,包括油罐、化工罐、水箱等。
尤其适用于大型储罐的施工,可以最大程度地提高施工效率和减少人力资源的浪费。
四、工艺原理液压提升倒装技术施工工法的工艺原理主要是通过液压系统对储罐进行提升和倒装。
首先,在储罐底部设置液压提升装置,通过液压系统对储罐进行竖直升起,并保持稳定。
然后,再利用液压系统将储罐倒装,使得储罐底部朝上,方便底部的施工。
整个过程中,液压系统对储罐的支撑和稳定起到了核心作用。
五、施工工艺液压提升倒装技术施工工法的施工工艺包括以下几个阶段:1. 地基处理:为保证储罐的施工安全和稳定,首先需要对地基进行处理,包括强化地基、加固地基等。
2.安装液压提升装置:在储罐底部安装液压提升装置,并进行调试和检验,确保其正常工作。
3. 施工准备工作:对储罐上方进行支撑和加固,同时将需要使用的工具和材料准备齐全。
4. 液压提升:利用液压系统将储罐竖直升起,在升高到一定高度后保持稳定。
5. 倒装施工:通过液压系统将储罐倒装,使得底部朝上,方便底部的施工。
6. 完成施工:在储罐底部完成所需的施工工序,包括焊接、防腐等,并进行必要的质量检验。
六、劳动组织液压提升倒装技术施工工法需要充分组织和合理调配劳动力,包括施工现场的工人、操作液压系统的技术人员以及管理人员等。
大型储罐液压提升倒装法施工技术简介精选全文完整版
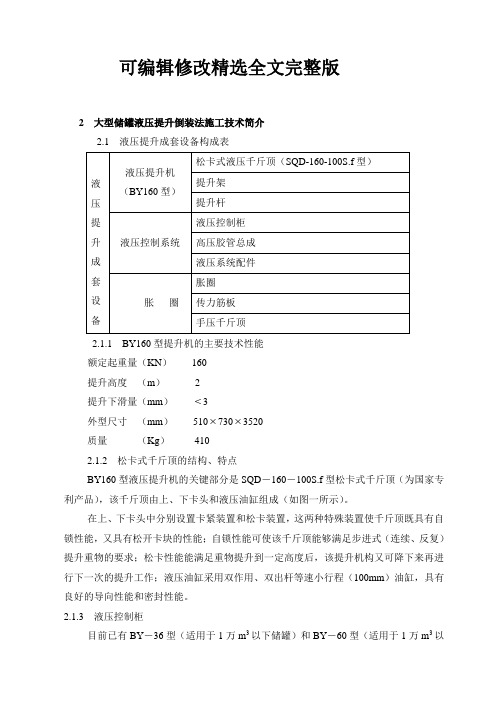
可编辑修改精选全文完整版2 大型储罐液压提升倒装法施工技术简介2.1 液压提升成套设备构成表2.1.1 BY160型提升机的主要技术性能额定起重量(KN)160提升高度(m) 2提升下滑量(mm) 3外型尺寸(mm)510 730 3520质量(Kg)4102.1.2 松卡式千斤顶的结构、特点BY160型液压提升机的关键部分是SQD-160-100S.f型松卡式千斤顶(为国家专利产品),该千斤顶由上、下卡头和液压油缸组成(如图一所示)。
在上、下卡头中分别设置卡紧装置和松卡装置,这两种特殊装置使千斤顶既具有自锁性能,又具有松开卡块的性能;自锁性能可使该千斤顶能够满足步进式(连续、反复)提升重物的要求;松卡性能能满足重物提升到一定高度后,该提升机构又可降下来再进行下一次的提升工作;液压油缸采用双作用、双出杆等速小行程(100mm)油缸,具有良好的导向性能和密封性能。
2.1.3 液压控制柜目前已有BY-36型(适用于1万m3以下储罐)和BY-60型(适用于1万m3以上储罐)两种液压控制柜,其主要技术性能见下表:2.1.4 胀圈胀圈有两方面的作用:一是保证罐体的圆度;二是设置提升支座,通过传力筋板来带动罐体上升,保证提升时的刚度。
胀圈一般采用型钢进行分段制作,用手压千斤顶沿储罐内壁胀紧。
2.2 液压提升倒装法施工工艺简介2.2.1 液压提升倒装法原理本工艺利用液压提升装置(成套设备)均布于储罐内壁圆周处,先提升罐顶及罐体的首层壁板,然后逐层提升组焊罐体的各层壁板。
采用自锁式液压千斤顶和提升架、提升杆组成的提升装置(液压提升机),通过液压控制系统,使液压千斤顶进油时,通过上、下卡头卡紧并举起提升杆和胀圈,从而带动罐体(包括罐顶)向上提升;当千斤顶回油时,其上卡头随活塞杆回程,此时其下卡头自动卡紧提升杆不会下落。
千斤顶如此反复运动使提升杆带着罐体不断上升,直到预定高度。
当下圈壁板组对焊接后,打开液压千斤顶的上、下卡头装置,松开上、下卡头将提升杆及胀圈下降到下一层壁板下部胀紧,焊好传力筋板,再进行提升。
大型储罐倒装法施工液压提升原理及应用

( i i gP t l m E g er gC nt ci o,t.K rma 3 0 0, hn ) X n a er e n i ei o s u t nC .Ld , aa y8 4 0 C ia jn ou n n r o
Ab t c :hs p p rito u e h rn il fte u sd d wn c ntu t n tc n lg fh d a l die iig frlr e soae s a tT i a e nrd c ste picpe o pie o o srci e h oo y o y rui rv n lt o ag trg r h o c fn
第4 1卷
第 7期
重Байду номын сангаас拽
ElcrcW edn c ie e t ligMa hn i
Vo . l No7 1 . 4
21 0 1年 7月
J L 0l u2 1
型储 罐 柳 装 懑 施 液 崖 捷 井 原 理 虚 扁
杨 建 强
( 疆 石 油 建设 有 限 责任 公 司 , 疆 克拉 玛依 8 4 0 ) 新 新 300
收 稿 日期 : 1 - 3 0 ; 稿 日期 :0 l o 一 4 2 10—9 收 0 2 1- 7 o 作 者 简 介 : 建强( 7 ) , 杨 1 , 甘肃渭通人 , 9 男 高级工程师 , 硕
士, 要从事储罐焊接质量管理工作。 主
型储罐倒 装 法施 工 的关键 技 术掌 握不 到位 , 使倒 致
t kw i ekyo eus eoncnt co cnl yf 謦 sr et k i l i nl io l g t ¥ adsnho i t n a ,h hit e t pi dw osutnt ho g ra ta n , c d gaa s fin a  ̄ n ycrnz i , n c sh f h d ri e o ol og a n u n ys li s b f ao
钢制内浮顶储油罐液压提升倒装施工方法
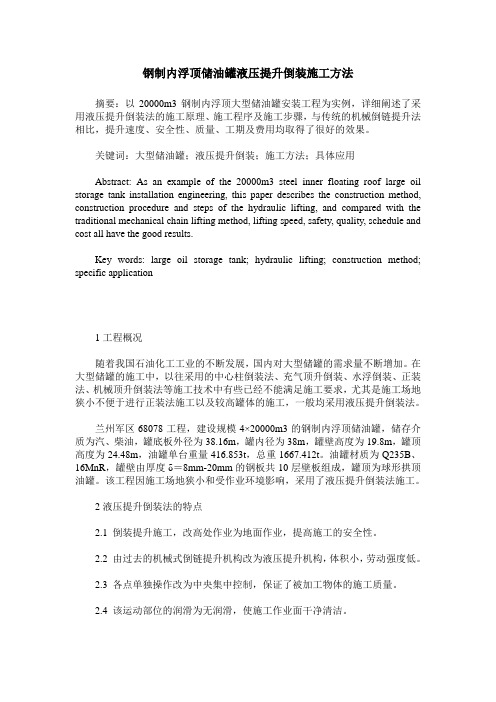
钢制内浮顶储油罐液压提升倒装施工方法摘要:以20000m3钢制内浮顶大型储油罐安装工程为实例,详细阐述了采用液压提升倒装法的施工原理、施工程序及施工步骤,与传统的机械倒链提升法相比,提升速度、安全性、质量、工期及费用均取得了很好的效果。
关键词:大型储油罐;液压提升倒装;施工方法;具体应用Abstract: As an example of the 20000m3 steel inner floating roof large oil storage tank installation engineering, this paper describes the construction method, construction procedure and steps of the hydraulic lifting, and compared with the traditional mechanical chain lifting method, lifting speed, safety, quality, schedule and cost all have the good results.Key words: large oil storage tank; hydraulic lifting; construction method; specific application1工程概况随着我国石油化工工业的不断发展,国内对大型储罐的需求量不断增加。
在大型储罐的施工中,以往采用的中心柱倒装法、充气顶升倒装、水浮倒装、正装法、机械顶升倒装法等施工技术中有些已经不能满足施工要求,尤其是施工场地狭小不便于进行正装法施工以及较高罐体的施工,一般均采用液压提升倒装法。
兰州军区68078工程,建设规模4×20000m3的钢制内浮顶储油罐,储存介质为汽、柴油,罐底板外径为38.16m,罐内径为38m,罐壁高度为19.8m,罐顶高度为24.48m,油罐单台重量416.853t,总重1667.412t。
大型储罐液压提升倒装法施工技术

论大型储罐液压提升倒装法施工技术摘要本文主要介绍了大型储罐液压提升倒装工艺原理、施工工序、提升架和胀圈的设计及液压千斤顶数量的确定,归纳了该施工方法独具的优点和推广应用前景。
主题词油罐液压传动装置安装技术1. 前言随着我国石油化工工业的不断发展,国内对大型储罐的需求量不断增加。
多年来储灌主要采用中心柱法、气吹法、水浮正装法进行储罐施工,由于储罐逐渐向大型化发展,有些施工技术已不能满足施工要求,在大型储罐的建造中正在用液压提升倒装法取代以往采用的其它施工方法。
液压提升倒装法的技术要求并不苛刻,安全可靠、施工手段用料少、安装速度快、对储罐的各种建造参数易于调控。
避免了气吹法出现的冒顶和吹偏事故的风险,是目前比较理想一种储罐建造施工新方法。
2. 工艺原理和施工工序2.1、液压提升工艺原理利用均布在储罐内侧的提升架,在其上安装有起重作用的上、下限位单向卡头,其中上卡头带有液压油缸,动力来自中央控制台,高压油经软管送至双座拥油缸(上卡头),通过换向阀实现油缸的往复动作。
活塞干是空心的,中间穿有钢制提升杆,在油缸往复运动时,可自动完成提升杆的步进式工作。
提升杆带动提升架上的滑板,滑板沿提升架上的轨道移动,在滑板上装有两开托板,用托板上提与罐壁下部临时固定的胀圈,是第一圈壁板随胀圈上升岛预定高度,组焊第二圈壁板,然后将上、下卡头松开,胀圈降至第二圈壁板下部胀紧、固定,如此往复,使罐体提升,实现倒装法施工工艺要求。
2.2、松卡式液压千斤顶工作原理松卡式液压千斤顶工作原理就是由一个液压泵带动多个立柱上的千斤顶,千斤顶中间有一个圆钢芯(直径约为40mm,长为3m,圆钢下端有一个钢托,和圆钢连在一起,靠它托起壁板),千斤顶卡住圆钢,带动圆钢向上升,每升一次的行程为100mm(根据不同的型号,行程有所不同),每一次行程结束时,千斤顶里有一个锁紧圆钢的装置,不至于圆钢下落,也就是说壁板不下落,千斤顶再回到原来的状态,再起升,再回落,往复运动,直至把圆钢提升到我们需要的高度(环缝对口状态)。
大型储罐液压顶升倒装施工工法(2)

大型储罐液压顶升倒装施工工法大型储罐液压顶升倒装施工工法一、前言大型储罐的制作和安装是工业项目中重要的环节之一,传统的安装方式需要大量的人力和时间,同时存在一定的安全隐患。
为了提高施工效率和安全性,大型储罐液压顶升倒装施工工法应运而生。
本文将详细介绍该工法的特点、适应范围、工艺原理、施工工艺、劳动组织、机具设备、质量控制、安全措施、经济技术分析和工程实例。
二、工法特点大型储罐液压顶升倒装施工工法具有以下几个特点:高效、安全、灵活。
相比传统的制作、安装方式,该工法能够大大缩短施工周期,减少人力投入,提高施工效率。
同时,在施工过程中,采用液压顶升倒装技术,增加了施工的安全性,减少了人员伤害的风险。
此外,该工法能够适应各类大型储罐的制作和安装,广泛应用于石油、化工、液化气等领域。
三、适应范围大型储罐液压顶升倒装施工工法适用于直立式、卧式、顶升式、碎片式等各种类型的大型储罐。
无论是钢质储罐还是混凝土储罐,该工法都能胜任。
四、工艺原理该工法通过液压顶升倒装技术来实现大型储罐的制作和安装。
首先,在施工现场安装并连接液压缸和支撑装置。
然后,在顶部安装储罐底板,并使用液压缸进行顶升。
当储罐底部离地面一定高度后,通过倒装机具进行翻转,将储罐翻倒至正确位置。
最后,完成储罐的各项安装和连接工作。
五、施工工艺该工法的施工过程分为以下几个阶段:场地准备,液压顶升和倒装,储罐连接和测试。
在场地准备阶段,需要进行场地清理和平整,确保施工现场的安全和清洁。
在液压顶升和倒装阶段,通过液压顶升和倒装机具将储罐翻转至正确位置。
在储罐连接和测试阶段,完成各项管路的连接和测试工作。
六、劳动组织大型储罐液压顶升倒装施工工法的劳动组织主要包括工程经理、工程师、操作工等。
工程经理负责施工计划的制定和协调;工程师负责施工过程的监督和技术支持;操作工负责施工机具和设备的操作和维护。
七、机具设备该工法所需的机具设备包括:液压顶升机具、倒装机具、吊车、钢管脚手架、焊接设备等。
超高层大型液压提升管道倒装法施工工法(2)
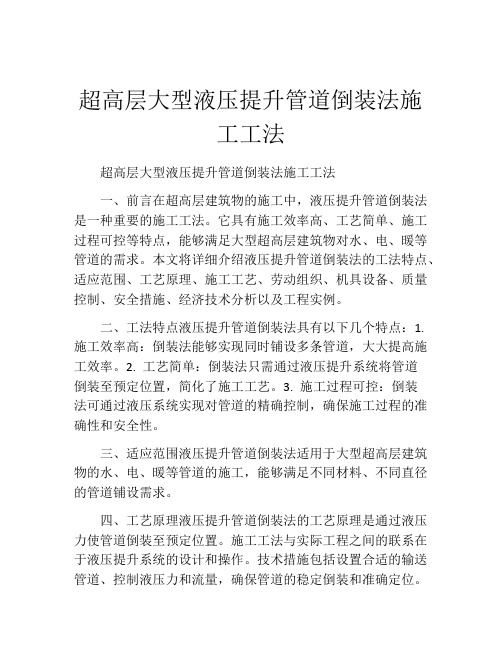
超高层大型液压提升管道倒装法施工工法超高层大型液压提升管道倒装法施工工法一、前言在超高层建筑物的施工中,液压提升管道倒装法是一种重要的施工工法。
它具有施工效率高、工艺简单、施工过程可控等特点,能够满足大型超高层建筑物对水、电、暖等管道的需求。
本文将详细介绍液压提升管道倒装法的工法特点、适应范围、工艺原理、施工工艺、劳动组织、机具设备、质量控制、安全措施、经济技术分析以及工程实例。
二、工法特点液压提升管道倒装法具有以下几个特点:1. 施工效率高:倒装法能够实现同时铺设多条管道,大大提高施工效率。
2. 工艺简单:倒装法只需通过液压提升系统将管道倒装至预定位置,简化了施工工艺。
3. 施工过程可控:倒装法可通过液压系统实现对管道的精确控制,确保施工过程的准确性和安全性。
三、适应范围液压提升管道倒装法适用于大型超高层建筑物的水、电、暖等管道的施工,能够满足不同材料、不同直径的管道铺设需求。
四、工艺原理液压提升管道倒装法的工艺原理是通过液压力使管道倒装至预定位置。
施工工法与实际工程之间的联系在于液压提升系统的设计和操作。
技术措施包括设置合适的输送管道、控制液压力和流量,确保管道的稳定倒装和准确定位。
五、施工工艺液压提升管道倒装法的施工阶段包括准备工作、管道铺设、液压提升、管道定位等。
具体过程如下:1.准备工作:确定管道的布置、尺寸和材料,并对现场进行清理,为管道铺设做准备。
2. 管道铺设:通过吊装、滚动等方式将管道铺设至预定位置,进行必要的固定和连接。
3. 液压提升:通过液压系统施加压力,实现管道的倒装,同时控制液压力和流量,确保倒装的平稳进行。
4. 管道定位:通过准确的液压控制,将管道准确定位至预定位置,进行固定和连接。
六、劳动组织液压提升管道倒装法的劳动组织主要包括施工人员、机械操作人员、监理人员等。
其中施工人员负责管道的布置、铺设和连接;机械操作人员负责操作液压系统进行管道倒装;监理人员负责对施工过程进行监督和检查。
机电安装工程新技术11:大型储罐施工技术
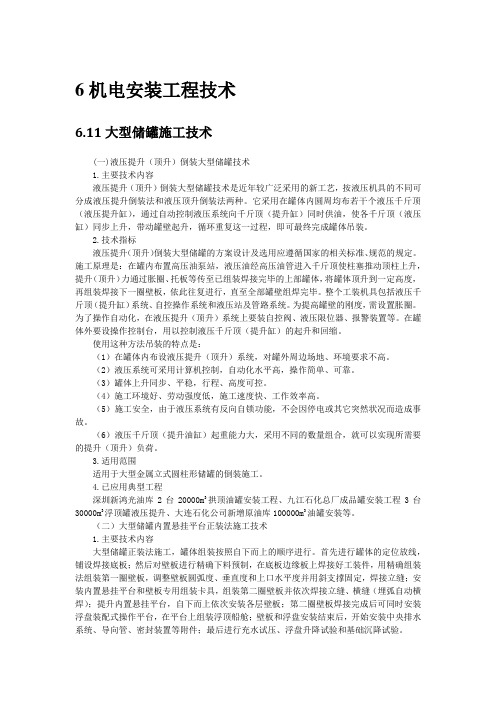
6机电安装工程技术6.11大型储罐施工技术(一)液压提升(顶升)倒装大型储罐技术1.主要技术内容液压提升(顶升)倒装大型储罐技术是近年较广泛采用的新工艺,按液压机具的不同可分成液压提升倒装法和液压顶升倒装法两种。
它采用在罐体内圆周均布若干个液压千斤顶(液压提升缸),通过自动控制液压系统向千斤顶(提升缸)同时供油,使各千斤顶(液压缸)同步上升,带动罐壁起升,循环重复这一过程,即可最终完成罐体吊装。
2.技术指标液压提升(顶升)倒装大型储罐的方案设计及选用应遵循国家的相关标准、规范的规定。
施工原理是:在罐内布置高压油泵站,液压油经高压油管进入千斤顶使柱塞推动顶柱上升,提升(顶升)力通过胀圈、托板等传至已组装焊接完毕的上部罐体,将罐体顶升到一定高度,再组装焊接下一圈壁板,依此往复进行,直至全部罐壁组焊完毕。
整个工装机具包括液压千斤顶(提升缸)系统、自控操作系统和液压站及管路系统。
为提高罐壁的刚度,需设置胀圈。
为了操作自动化,在液压提升(顶升)系统上要装自控阀、液压限位器、报警装置等。
在罐体外要设操作控制台,用以控制液压千斤顶(提升缸)的起升和回缩。
使用这种方法吊装的特点是:(1)在罐体内布设液压提升(顶升)系统,对罐外周边场地、环境要求不高。
(2)液压系统可采用计算机控制,自动化水平高,操作简单、可靠。
(3)罐体上升同步、平稳,行程、高度可控。
(4)施工环境好、劳动强度低,施工速度快、工作效率高。
(5)施工安全,由于液压系统有反向自锁功能,不会因停电或其它突然状况而造成事故。
(6)液压千斤顶(提升油缸)起重能力大,采用不同的数量组合,就可以实现所需要的提升(顶升)负荷。
3.适用范围适用于大型金属立式圆柱形储罐的倒装施工。
4.已应用典型工程深圳新鸿光油库2台20000m3拱顶油罐安装工程、九江石化总厂成品罐安装工程3台30000m3浮顶罐液压提升、大连石化公司新增原油库100000m3油罐安装等。
(二)大型储罐内置悬挂平台正装法施工技术1.主要技术内容大型储罐正装法施工,罐体组装按照自下而上的顺序进行。
大型储罐液压顶升施工方法
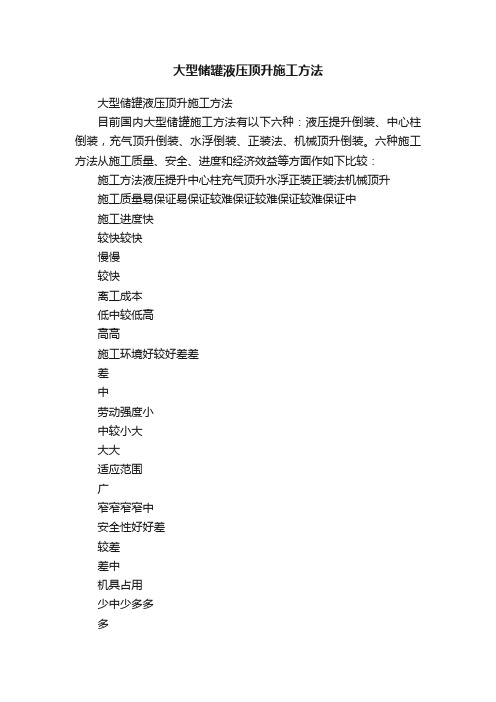
大型储罐液压顶升施工方法大型储罐液压顶升施工方法目前国内大型储罐施工方法有以下六种:液压提升倒装、中心柱倒装,充气顶升倒装、水浮倒装、正装法、机械顶升倒装。
六种施工方法从施工质量、安全、进度和经济效益等方面作如下比较:施工方法液压提升中心柱充气顶升水浮正装正装法机械顶升施工质量易保证易保证较难保证较难保证较难保证中施工进度快较快较快慢慢较快离工成本低中较低高高高施工环境好较好差差差中劳动强度小中较小大大大适应范围广窄窄窄窄中安全性好好差较差差中机具占用少中少多多多场地占用少多少少多中液压提升倒装法介于几种施工方法之间,其特点一是适应范围广,理论上可适用于任意大小的储罐,二是操作控制简单、可靠、危险性小,因此已经越来越多的被采用,其主要缺点是目前成套设备价格较贵,设备购置一次性投入较大。
1 .液压顶升法,是倒装法的一种形式,其安装步骤与程序是:下图2 .液压提升方法:在先期施工的罐底板上安装数个固定垫墩 (400mm 高 , 间距 3-4 米), 然后组装第一层壁板和顶盖板, 沿罐内壁400mm 处均布数台(根据计算确定)液压提升机,以提升机的滑动托架托住固定在罐内壁的胀圈下部, 操纵液压提升机的控制柜,集中控制各液压机的动作 , 液压提升机提升扒杆时 , 同时也将罐体提升 , 升至下一带壁板高度时 , 可进行一带壁板组装 , 然后落下扒杆、胀圈 , 再进行下一带提升组装 , 直到整个油罐倒装完毕。
3 .施工技术2 罐底板预制:按设计排板图编号下料,并按号堆放好。
下料时要注意考虑焊接收缩量 50 毫米。
罐底板下好料后,反面要按要求防腐,编号应在正面,使其在罐底铺设时能够按号施工。
罐底边缘板和中幅板最少宽度和长度必须符合图纸和规范要求,尺寸要严格控制,防止变形过大。
2 罐壁板预制“壁板下料、滚圆,为了保证壁板预制质量,壁板下料采用半自动切割机切割。
壁板经卷板机滚圆,并用样板检查合格后方可下机。
卷制后的壁板应放在壁板胎具上保存、运输,防止变形。
大型储罐液压顶升倒装施工技术
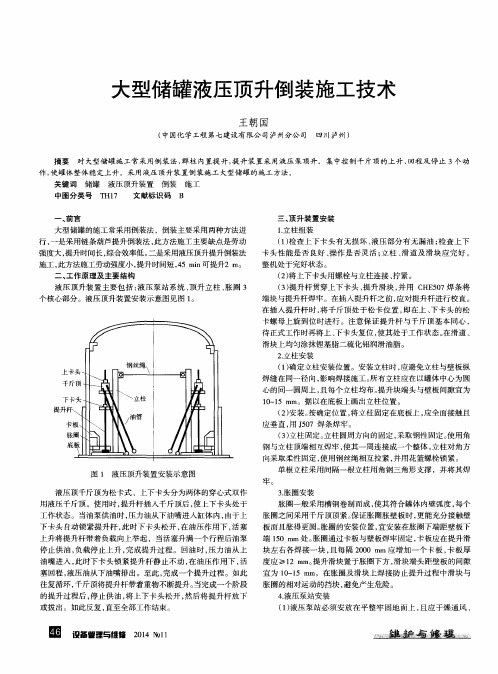
胀 圈的相对运 动的挡块 , 避免产生危险 。
4 . 液压泵站安装 ( 1 ) 液压泵站必 须安放在平整 牢固地面上 , 且应干燥通 风 、
田 设 备 管 理 与 维 修2 0 1 4 N o l l
j缝 盎 翅 一
高温渣 浆泵轴承故 障分析及处理
焊缝在同一径 向 , 影响焊接施工。 所有立柱应在 以罐体中心为圆 心的 同一圆周上 , 且每个立柱均布。 提升块端头与壁板间隙宜为 1 0 ~ 1 5 mm。据 以在底板上画出立柱位置 。
提
( 2 ) 安装 。 按确定位 置 , 将立柱固定在底板上 , 应全面接触且 应垂直 , 用J 5 0 7焊条焊牢。
二、 工 作 原 理 及 主 要结 构
( 1 ) 检查上下卡头有无损 坏 、 液压部分有无漏 油 ; 检查上下 卡 头性能是否 良好 、 操作是 否灵活 ; 立柱 、 滑道及 滑块应 完好 。 整机处于完好状态 。
( 2 ) 将 上 下 卡 头用 螺 栓 与立 柱 连 接 、 拧 紧。
卡螺母 上旋到位时进行 。注意保证提升杆 与千斤顶基本 同心 ,
待正式工作 时再将上 、 下卡头复位 , 使其处 于工作状 态。 在滑道 、 滑块上均匀涂抹锂基脂二硫化钼润滑油脂 。
2 . 立 柱 安 装
( 1 ) 确 定 立 柱 安 装 位 置 。安 装 立 柱 时 , 应 避 免立 柱 与壁 板 纵
大型储罐液压顶 升倒装施工技术
王朝 国
( 中国化 学工程 第七建设有 限公 司泸州分公 司 四川泸州)
摘要 关键词 对大型储罐施 工常采用倒装法 , 群柱 内置提升 , 提升装置采用液压 泵顶升 。集中控 制千斤顶的上升 、 回程 及停止 3个动 储罐 液压顶升装置 倒装 施工
浅谈储罐液压顶升倒装法施工技术
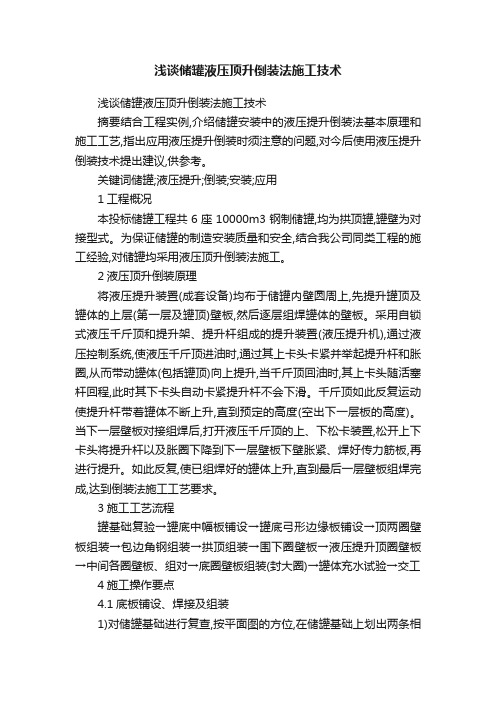
浅谈储罐液压顶升倒装法施工技术浅谈储罐液压顶升倒装法施工技术摘要结合工程实例,介绍储罐安装中的液压提升倒装法基本原理和施工工艺,指出应用液压提升倒装时须注意的问题,对今后使用液压提升倒装技术提出建议,供参考。
关键词储罐;液压提升;倒装;安装;应用1工程概况本投标储罐工程共6座10000m3钢制储罐,均为拱顶罐,罐壁为对接型式。
为保证储罐的制造安装质量和安全,结合我公司同类工程的施工经验,对储罐均采用液压顶升倒装法施工。
2液压顶升倒装原理将液压提升装置(成套设备)均布于储罐内壁圆周上,先提升罐顶及罐体的上层(第一层及罐顶)壁板,然后逐层组焊罐体的壁板。
采用自锁式液压千斤顶和提升架、提升杆组成的提升装置(液压提升机),通过液压控制系统,使液压千斤顶进油时,通过其上卡头卡紧并举起提升杆和胀圈,从而带动罐体(包括罐顶)向上提升,当千斤顶回油时,其上卡头随活塞杆回程,此时其下卡头自动卡紧提升杆不会下滑。
千斤顶如此反复运动使提升杆带着罐体不断上升,直到预定的高度(空出下一层板的高度)。
当下一层壁板对接组焊后,打开液压千斤顶的上、下松卡装置,松开上下卡头将提升杆以及胀圈下降到下一层壁板下壁胀紧、焊好传力筋板,再进行提升。
如此反复,使已组焊好的罐体上升,直到最后一层壁板组焊完成,达到倒装法施工工艺要求。
3施工工艺流程罐基础复验→罐底中幅板铺设→罐底弓形边缘板铺设→顶两圈壁板组装→包边角钢组装→拱顶组装→围下圈壁板→液压提升顶圈壁板→中间各圈壁板、组对→底圈壁板组装(封大圈)→罐体充水试验→交工4施工操作要点4.1底板铺设、焊接及组装1)对储罐基础进行复查,按平面图的方位,在储罐基础上划出两条相互垂直的中心线,储罐安装过程中不得损坏基础。
2)底板的下表面进行喷砂除锈,涂刷第一道环氧煤沥青漆时,应注意每块板的边缘50mm的范围内不刷,待漆层表干后涂刷第二环氧煤沥青漆,直到漆层实干后并经检验合格,方可用于底板的铺设;。
大型钢制储罐液压提升倒装法施工工法(2)

大型钢制储罐液压提升倒装法施工工法大型钢制储罐液压提升倒装法施工工法一、前言大型钢制储罐在工业领域中扮演着重要的角色,而其施工过程中涉及到储罐的倒装与安装,是一个关键的环节。
大型钢制储罐液压提升倒装法施工工法作为一种先进的施工工艺,在现代化工程中得到了广泛应用,本文将对该工法的特点、适应范围、工艺原理、施工工艺、劳动组织、机具设备、质量控制、安全措施与经济技术分析进行详细介绍。
二、工法特点大型钢制储罐液压提升倒装法施工工法具有以下特点:1. 施工速度快:液压提升倒装技术使得储罐的倒装过程更加高效,大大缩短了施工周期。
2. 施工质量高:倒装法使得储罐在施工过程中减少了变形和应力集中的可能性,提高了储罐的使用寿命。
3. 施工安全性较高:液压倒装法能够实现储罐的稳定倒装,减少了倒装过程中的安全风险。
4.施工精确度高:倒装法能够精确控制液压力的大小,保证储罐倒装的平稳进行。
5. 施工成本相对较低:相对于传统的借助起重设备的倒装法,液压倒装法更加经济实用。
三、适应范围大型钢制储罐液压提升倒装法施工工法适用于各类规模较大的储罐倒装,可以广泛应用于石化、化工等行业中。
四、工艺原理大型钢制储罐液压提升倒装法施工工法是基于以下工艺原理:1. 液压原理:利用液压油将大型钢制储罐升起并倒装,通过液压系统控制液压力与速度,实现储罐的稳定倒装。
2. 倒装原理:储罐倒装可以使得罐底焊缝更容易进行焊接,同时减少变形可能性,提高施工质量。
五、施工工艺大型钢制储罐液压提升倒装法施工工艺主要包括以下阶段:1. 预处理阶段:包括施工场地的准备,对储罐进行清洗、除氧等处理,确保施工环境的洁净与安全。
2.铺垫阶段:放置铺垫物,为液压提升倒装提供良好的基础。
3. 提升阶段:利用液压系统将大型钢制储罐升空,通过倒装装置将储罐倒置,实现底部焊接。
4. 固定阶段:对储罐进行固定,防止其倾斜或下滑。
5. 检测与清理阶段:对倒装焊接部位进行检测,以确保焊缝质量;清理施工现场。
拱顶贮罐液压提升倒装法施工新工法
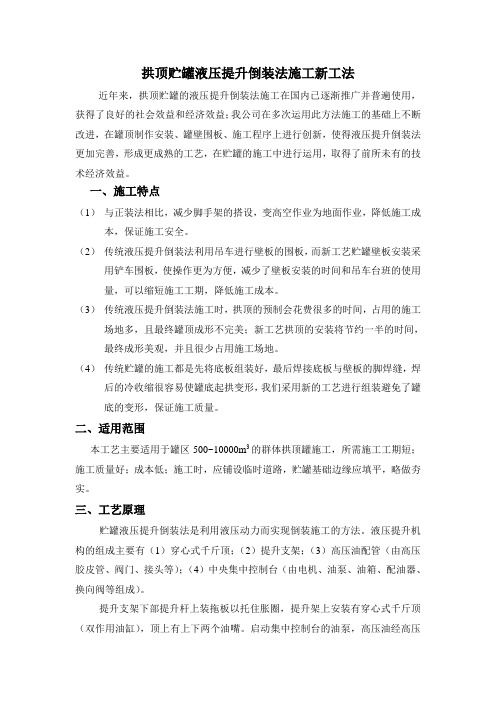
拱顶贮罐液压提升倒装法施工新工法近年来,拱顶贮罐的液压提升倒装法施工在国内已逐渐推广并普遍使用,获得了良好的社会效益和经济效益;我公司在多次运用此方法施工的基础上不断改进,在罐顶制作安装、罐壁围板、施工程序上进行创新,使得液压提升倒装法更加完善,形成更成熟的工艺,在贮罐的施工中进行运用,取得了前所未有的技术经济效益。
一、施工特点(1)与正装法相比,减少脚手架的搭设,变高空作业为地面作业,降低施工成本,保证施工安全。
(2)传统液压提升倒装法利用吊车进行壁板的围板,而新工艺贮罐壁板安装采用铲车围板,使操作更为方便,减少了壁板安装的时间和吊车台班的使用量,可以缩短施工工期,降低施工成本。
(3)传统液压提升倒装法施工时,拱顶的预制会花费很多的时间,占用的施工场地多,且最终罐顶成形不完美;新工艺拱顶的安装将节约一半的时间,最终成形美观,并且很少占用施工场地。
(4)传统贮罐的施工都是先将底板组装好,最后焊接底板与壁板的脚焊缝,焊后的冷收缩很容易使罐底起拱变形,我们采用新的工艺进行组装避免了罐底的变形,保证施工质量。
二、适用范围本工艺主要适用于罐区500~10000m3的群体拱顶罐施工,所需施工工期短;施工质量好;成本低;施工时,应铺设临时道路,贮罐基础边缘应填平,略做夯实。
三、工艺原理贮罐液压提升倒装法是利用液压动力而实现倒装施工的方法。
液压提升机构的组成主要有(1)穿心式千斤顶;(2)提升支架;(3)高压油配管(由高压胶皮管、阀门、接头等);(4)中央集中控制台(由电机、油泵、油箱、配油器、换向阀等组成)。
提升支架下部提升杆上装拖板以托住胀圈,提升架上安装有穿心式千斤顶(双作用油缸),顶上有上下两个油嘴。
启动集中控制台的油泵,高压油经高压油管从下油嘴进入缸内,由于上卡头自动锁住提升杆,此时下卡头松开,在油压作用下,油缸内活塞上升,通过提升杆拖住胀圈使罐体上升,千斤顶的每次行程为100mm。
回油时,高压油从上油嘴进入,此时下卡头自动抱紧提升杆,静止不动。
大型拱顶油罐液压提升倒装法
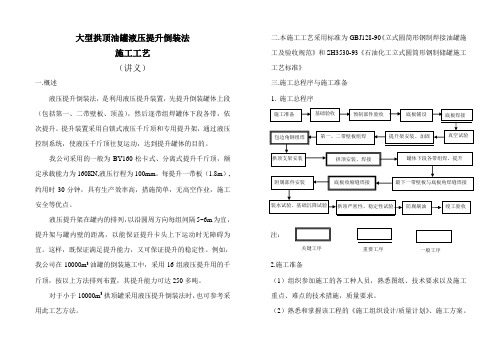
大型拱顶油罐液压提升倒装法施工工艺(讲义)一.概述液压提升倒装法,是利用液压提升装置,先提升倒装罐体上段(包括第一、二带壁板、顶盖),然后逐带组焊罐体下段各带,依次提升。
提升装置采用自锁式液压千斤顶和专用提升架,通过液压控制系统,使液压千斤顶往复运动,达到提升罐体的目的。
我公司采用的一般为BY160松卡式、分离式提升千斤顶,额定承载能力为160KN,液压行程为100mm。
每提升一带板(1.8m),约用时30分钟,具有生产效率高,措施简单,无高空作业,施工安全等优点。
液压提升架在罐内的排列,以沿圆周方向每组间隔5~6m为宜,提升架与罐内壁的距离,以能保证提升卡头上下运动时无障碍为宜。
这样,既保证满足提升能力,又可保证提升的稳定性。
例如,我公司在10000m3油罐的倒装施工中,采用16组液压提升用的千斤顶,按以上方法排列布置,其提升能力可达250多吨。
对于小于10000m3拱顶罐采用液压提升倒装法时,也可参考采用此工艺方法。
二.本施工工艺采用标准为GBJ128-90《立式圆筒形钢制焊接油罐施工及验收规范》和SH3530-93《石油化工立式圆筒形钢制储罐施工工艺标准》三.施工总程序与施工准备1. 施工总程序注:2.施工准备(1)组织参加施工的各工种人员,熟悉图纸、技术要求以及施工重点、难点的技术措施,质量要求。
(2)熟悉和掌握该工程的《施工组织设计/质量计划》、施工方案。
关键工序重要工序一般工序(3)准备相应的施工用的工、卡具,包括吊装卡具、组对卡具、胎具、脚手架、梯子等。
(4)施工用的测量工具,如50米盘尺、板尺(1米)、磁力线坠(3米)、水平仪、地规等。
(5)对参加焊接施工的焊工按规定进行培训考核,并准备相应的防护用具。
四.基础验收油罐基础验收,主要是对基础的直径、标高、方位、基础表面的锥度及其平整度等外形尺寸进行验收。
1.基础的中心标高允许偏差为±20mm。
2.支承罐壁的基础表面,其高差应符合下列规定:(1)有环梁时,每10m弧长内任意两点的高差不得大于7mm,整个圆周长度内任意两点的高差不得大于13mm。
大型储罐的工工法

⼤型储罐的⼯⼯法⼤型储罐液压顶升、⾃动焊、倒装施⼯⼯法陕西化建⼯程有限责任公司中油吉林化建⼯程有限公司王智杰何丹杨峰斌李丽红1.前⾔随着我国经济的快速发展和⼈民⽣活⽔平的不断提⾼,能源消耗急剧增长,⽯油和成品油的需求剧增。
⽬前我国已变成⽯油进⼝⼤国,⽯油已成为国家重要的战略物资,它直接关系到我国的经济发展、社会稳定和国家安全,增加原油储备迫在眉睫,因此,我国对国家⽯油储备库和成品油库的建设给予了⾼度的重视。
⼤型⽴式钢制储罐是⾮常重要的储运设备,越来越多地被应⽤于原油、成品油等储运⼯程中,其中⽴式圆筒形拱顶储罐和浮顶储罐最为普遍。
因此,⽴式圆形储罐的制作安装也不断更新发展。
⼤型储罐的预制、罐体提升及焊接是储罐制安的主要⼯序,直接影响储罐制安的施⼯质量。
同时,储罐制安⼯作中,主要的⼯作量集中在焊接⼯序上。
在当今施⼯⾏业,⾃动焊技术已经渗⼊到储罐制安⼯艺中,但⾃动焊机以储罐“正装”为基准进⾏设计。
我公司在⼤型储罐制安中,为了减少⾼空作业量,减少脚⼿架的投⼊等,习惯于“倒装法”作业。
为此,我公司技术⼈员与焊机⼚进⾏多次研讨,将适⽤于“正装法”的悬挂式“横焊机”改造成适⽤“倒装法”的轨道式“横焊机”,同时,在罐体提升过程中,为了更稳、更快,⽤“液压顶升”设备代替了原来的电动倒链。
将⾃动焊、液压顶升等先进的施⼯⼯艺融⼊到“倒装法”施⼯⼯艺之中,另外在⾃动焊⽅⾯采⽤⾃⾏研发的了“单⾯焊双⾯成型”技术。
本施⼯⼯艺,经过实践证明安全、可靠、先进。
罐体的焊接质量能够满⾜规范要求,同时克服了“正装法”的⼀些不⾜,是⼀项值得在同⾏业推⼴的施⼯⼯法。
2.⼯法特点2.1⼤型⽴式储罐主体制作安装⽅法有“正装法”和“倒装法”两种,本施⼯⼯法是以“倒装法”为基础研发的。
2.2本施⼯⼯法主要是将⾃动焊接技术及液压顶升技术应⽤于储罐的“倒装法”施⼯⼯艺中。
2.3本施⼯⽅法主要是将“正装法”的“埋弧横焊机”进⾏了改造,即从“悬挂式”改造成“轨道式”,使之与“倒装法”相适应。
大型储罐液压提升倒装工法汇总

大型储罐液压提升倒装施工工法目录1. 前言-------------------------------------------------------------------12. 施工工艺及操作要点-----------------------------------------------------23. 施工计划与劳动力组合--------------------------------------------------104. 机具配备--------------------------------------------------------------125. 质量控制--------------------------------------------------------------136. 安全技术措施----------------------------------------------------------147. 技术经济分析----------------------------------------------------------168.应用实例---------------------------------------------------------------161. 前言大型储罐制作安装工程,液压提升倒装法施工工艺已被施工单位广泛应用。
2004年,我公司购置了一套SQD-160型罐体液压装置,为在公司范围内推广应用,特编制本工法。
基本原理:在储罐组焊过程中,利用液压提升装置均布于储罐内壁圆周处,提升罐体壁板及罐顶,逐层组焊储罐壁,采用行程放大式液压提升机和中心控制盘组成的液压提升系统,工作时,提升机上的油泵带动液压提升机顶轴不断上升,绷紧钢丝绳,直到顶定高度,当下一层壁板对接后,液压油缸将胀圈下降到下一层壁板下部胀紧,焊好限位筋板,如此反复,使已组焊好的罐体上升,直到最后一带壁板焊完。
- 1、下载文档前请自行甄别文档内容的完整性,平台不提供额外的编辑、内容补充、找答案等附加服务。
- 2、"仅部分预览"的文档,不可在线预览部分如存在完整性等问题,可反馈申请退款(可完整预览的文档不适用该条件!)。
- 3、如文档侵犯您的权益,请联系客服反馈,我们会尽快为您处理(人工客服工作时间:9:00-18:30)。
大型储罐倒装施工液压提升工法目录1工法特点 (2)2工艺原理 (2)3使用范围 (2)4施工程序 (2)5操作要点 (3)6施工机具 (6)7劳动组织 (7)8质量、安全控制 (7)9经济效益分析 (7)10工程应用 (7)本工法是对原有工艺方法的提高和创新,在受力方式、动力源、可靠性、经济性等方面有新的进步。
1工法特点倒装法施工,改高处作业为地面作业。
改顶升方式为提升方式,使受力由受压改为受拉。
机械机构改为液压机构,出力大,机构小。
个别控制改为中央控制。
运动部分改润滑为无润滑。
改连续提升为步进提升,提升高度(理论上)不受限制。
改刚性受力为球面自位式弯矩卸载机构。
机械效率、体积重量、出力、安全等都较原施工方法提高。
2工艺原理倒装法原理金属圆柱形储罐主体由三部分组成:罐底、壁板、罐顶。
罐体高度主要由各节壁板形成。
正装法的程序是:罐底→各层壁板→罐顶。
罐体越来越高,必须高处作业。
倒装法的程序是:罐底→罐顶→上层壁板→提升→下层壁板→提升→各层壁板。
主体施工全部地面作业,不仅安全、工效高,而且节省了吊机、脚手架等费用。
罐顶和上层壁板的提升必须用胀圈。
胀圈按罐内径作为若干段,每两段间用千斤顶胀紧在罐壁上,并焊接筋板来保证胀圈向罐体的传力。
提升机构提升胀圈,则将罐顶及上层壁板升起。
焊完下层壁板再将胀圈装到下层壁板上。
重复工作,直至完成全部壁板施工。
液压提升原理动力来自中央控制台,其中包括电机、油泵、油箱、换向阀、安全阀、压力表、按扭盘、配油器、16组截止阀等。
高压油经软管送至双作用油缸,通过换向阀实现油缸的往复动作。
活塞杆是空心的,中间穿一提升杆。
在油缸的上、下各有一个自位单向卡头(是本局的专利技术,专利号:.8),在油缸往复运动时,可自动完成提升杆的步进式工作。
提升杆拉动滑板,滑板沿支架的轨道移动。
在滑板上装有两块托板,用托板提动胀圈,使罐体提升,实现倒装工艺要求。
滑板与支承架轨道间采用无润滑衬板。
支承架应有一定的高度、强度和刚度。
3使用范围本工法可用于金属圆柱形储罐的倒装施工,容积自1000m3至20000m3。
可以对接,或搭接罐壁。
可以是拱顶罐浮顶罐或内浮顶罐。
此提升原理也可用于车间内大吨位设备的吊装。
4施工程序图1施工程序图5操作要点提升支架使用数量提升支架额定出力200kN,不同容积的储罐依提升支架的间距和单台支架的负荷选择。
中小型储罐依间距选择,大型储罐最后提升重量很大,一般依负荷选择。
例如,标准设计的1000m3拱顶罐,选用5台,两提升支架间的间距为6.5m,单台荷载重为9t。
10000m3内浮顶罐最大荷重210t,选用10台支架时间距为9.24m。
间距太大会造成胀圈变形,一般以不大于8m为宜,选用14台时,间距6.6m,单台负荷为15t。
提升支架的平面布置提升支架应均匀布置在罐壁内侧,尽量靠近壁板,以减少支架的弯矩。
中央控制台置于罐中心,由高压橡胶软管连接各油缸的上下油孔。
支架的稳定性影响整个罐体提升的稳定,必须平稳垂直固定,并用两根斜支承和一根连到中心的径向水平拉杆,使所有支架呈辐射形连接。
这种布置方式即可使单个支架有足够的刚度,又使所有支架形成封闭系统,充分保证提升系统的稳定性。
使用时逐个进行空载试验,检查油缸往复动作、提升杆步进、上下卡头是否可靠,提升杆与滑板的运动,以及中央控制台和油管是否正常工作。
胀圈的制作胀圈是倒装法必不可少的措施,依罐壁内径分段制作,各段用螺栓连接成几大段,大段间用千斤顶把胀圈胀紧在罐壁上。
一般2000m3罐可预制6段,用3个千斤顶;10000m3罐可预制12大段,用6个千斤顶。
胀圈截面取方形,依受力情况计算。
胀紧后用传力筋板分段把胀圈焊在罐壁上,其部位最好在提升架的位置。
底板的安装;根据各罐安装的顺序,底板安装前,应对其下表面进行防腐(搭接范围内空出)。
底板铺设前,应在验收合格的基础上画出十字中心线,当土建标注的中心偏差较大时(但在允许范围之内),应调整到最小。
底板铺设应根据加工制作提供的配板图,由罐底中心向四周顺序进行。
首先铺设位于中心位置的一块,其位置要准确,不应有纵横轴线旋转误差,中心轴的水平误差一般不应大于2mm。
中心底板铺好后,将基础上表面的十字中心线,反至底板表面,找出中心,并作出明显标志。
对设有弓形边板的底板,中幅板应搭在弓形边板的上部。
铺板时,应保证设计要求的搭接宽度,搭接处两板之间的最大间隙不应大于lmm,在三层底板重叠处,应将上层底板切角或打磨。
在铺板过程中,先将板端短缝点焊。
5.4.2底板的焊接焊接应从底板中心开始,先焊短缝,再隔条点焊长缝,然后焊接。
无论是焊接短缝还是长缝,均采用分段退焊的方法,焊工均匀分布,同时施焊。
5.4.3底板尺寸的测量、画线和余量切割拉尺测量底板半径,测量尺寸按下式确定:R1iR+∆+=2测式中:R——底板设计半径;i——设计坡度(‰);Δ——底板与壁板之间的焊接收缩量和边缘板与中幅板之间的焊缝收缩量,一般纵向收缩为0.65mm/m。
测量底板周长的同时,画出底板圆周线,并将余量切除。
顶层壁板的安装壁板安装前应在底板上面画出壁板安装位置线,沿画线圆周每500~700mm设一垫块。
垫块采用槽钢[,长150mm左右。
垫块与底板点焊,在其上表面画出壁板安装线,在画线两侧点焊挡板。
倒装法施工,首先安装顶层壁板。
在吊车的配合下,按照排板依次将壁板吊装就位,一边吊装,一边点焊纵缝(留出有安装余量的一道纵缝不点焊)。
对口间隙应符合设计要求。
待该层壁板全部吊装组对完成以后,在内侧沿焊缝自上而下,每500mm左右点焊一块弧型板。
错边量应满足要求。
壁板纵缝先焊外侧,内侧清根后施焊。
除活口以外的其他纵缝全部焊完后,应拉尺测量壁板周长。
周长的实际尺寸应该是理论尺寸加最后活口焊接收缩量,加顶部包边角钢焊接收缩量和下部环缝焊接收缩量。
第二层壁板的安装及提升顶层壁板和顶板安装之后,即可安装第二层壁板,方法同顶层壁板,并留出一道活口不焊,在第二层壁板吊装的同时,在罐内组对和安装胀圈。
按照的要求,调整提升设备,然后提升。
提升时,用中央控制台按扭盘按上升扭,完成一步提升,再按下降扭,使油缸活塞复位。
第二步提升同第一步操作。
在提升高度差较大时,关闭其它油缸,单独提升局部较低部位的油缸,至平高时停止提升。
一步步提升直至使顶层壁板高出下层壁板30~50mm,在下层壁板外侧,错升点焊限位挡板,使上下层壁板对接。
为了保证对口间隙均匀一致,在环缝之间加垫板,垫板应与设计要求的对口间隙相同。
当上下壁板不等厚时,应保证内侧平齐。
用提升机构调整环缝间隙,其方法是依间隙大小,逐个支架进行调整。
调整时关闭油泵,释放下卡头,手动拧开油缸下回路阀门,油缸在重力下向下移动,并及时关闭。
反复调节,直至符合要求。
环缝组对时,应在内侧每500mm左右点焊一块矩形板,以防止环缝的焊接变形,纵缝内则自上而下,每500mm左右点焊弧形板。
第二层板安装后,将胀圈落下与底部连接,方法与顶层壁板相同。
纵缝和环缝焊完后,应按设计要求对壁板的几何尺寸和焊缝质量进行检验。
其余各层壁板的安装检验合格后,按照上述方法和步骤安装第三层、第四层壁板,直至最后一层壁板的安装结束。
最后一层壁板的纵缝及上部环缝焊接后,将胀圈落下与底部连接,开启提升机,使罐升高160~200mm,拆除垫块,在底层壁板安装线内外设挡板,使壁板就位。
底层壁板与底板的环向内外角焊缝,由数名焊工均匀对称分布于罐内外,采用分段退焊法,沿同一方向同时施焊。
罐体试验5.8.1底板的真空试漏试漏前,应清除罐内杂物和焊缝上的药皮及铁锈,采用真空法,对全部底板焊缝进行试漏,真空度不应低于300mm汞柱。
对靠近壁板的焊缝(此处无法真空试漏),则用磁粉探伤或渗透探伤的方法进行试验。
5.8.2罐体充水试验、浮盘升降试验基础沉降观测罐体充水试验前,应将下部各开孔暂时封闭,将罐顶透光孔打开,向罐内充水,充水至最高操作液位后,稳压48h。
检查和记录罐体沉降量,检查纵缝和环缝有无渗漏,检查浮盘升降情况和密封性能。
在充水过程中,水温不应低于5℃,当水温低于5℃时,应采取加温措施。
5.8.3罐壁罐顶的严密性试验、强度试验和稳定性试验按国家或行业现行标准的有关规定执行。
罐体焊接工艺及焊缝检验储罐的焊接技术要求和焊接质量检验,按施工图纸和有关规定进行。
为保证贮罐的焊接质量,达到设计对焊接质量的要求,开工前,除对焊工进行培训和考试外,尚须根据储罐的材质、厚度、焊接材料、接头形式以及焊接设备制定焊接工艺评定,确定最佳的焊接工艺参数。
根据施焊位置、板厚、坡口形式及焊接材料等选择相应的焊接工艺参数,对电流、电压、和焊接速度加以控制,从而获得良好的焊接质量。
焊接前检查组装质量,消除坡口面及坡口两侧20mm范围内的铁锈、水分和油污,并充分干燥。
定位焊及工卡具的焊接,应与正式焊接相同。
焊接程序为:(1)罐底中幅板焊接,先短横缝,后长纵缝;(2)罐底边缘板外缘300mm对接焊缝焊接;(3)壁板的纵缝焊接;(4)包边角钢与壁板焊接,顶圈环缝焊接;(5)罐顶板焊接;(6)罐顶板与包边角钢间的环缝焊接;(7)顶部第二层壁板的纵缝焊接;(8)两层壁板间环缝焊接;(9)重复;焊缝焊接;(10)底层罐壁板纵缝焊接;(11)罐底与罐壁板连接的角环焊缝焊接(内外同时焊接);(12)边缘板剩余对接焊缝焊接;(13)罐底边缘板与中幅板之间的收缩缝焊接。
返修的焊缝,应按原规定的方法进行探伤,并应达到合格标准。
焊接的修补必须按照焊接工艺进行,同一部位的返修次数,不宜超过二次,当超过二次时,须经施工单位技术总负责人批准。
焊缝检验焊缝检验按国家或行业现行标准执行(如SYJ1016—82《立式圆筒形钢制焊接油罐设计技术规定》,HGJ201—83圆筒形钢制焊接储罐施工验收规范))。
6施工机具按现行有关标准对储罐几何形状尺寸进行检查,对焊缝进行外观和无损检验。
质量控制点如下:(l)下料尺寸复验或半成品尺寸复验;(2)组装尺寸检测,坡口尺寸检测;(3)焊接质量检验;(4)罐体试验,重点检查底板真空试漏、充水试验,罐顶严密试验和强度试验等。
安全控制点如下;(l)提升支架的稳定性检验;(2)上、下卡头可靠性检查;(3)胀圈及筋板焊接质量检查;(4)罐体试验时严格按程序操作。
9经济效益分析与机械顶升相比,节电68%,减轻自重80%,机械效益提高80%,制造成本降低5l%,提升速度提高20%,降低成本15%,人工费节约10%,施工工期比工期定额减少75%。
施工安全、稳定性好,工作中设备无噪声,集中液压控制便于操作。
10工程应用1993年在北京乙烯工程东方化工厂罐区四台10000m3常压内浮顶罐的施工中,使用16台液压提升支架。
第一次提升,用3h。
由于操作逐渐熟练,以后各节约1h左右。