非标单列圆锥滚子轴承套圈磨削工艺改进
圆锥滚动轴承外圈制造工艺改进
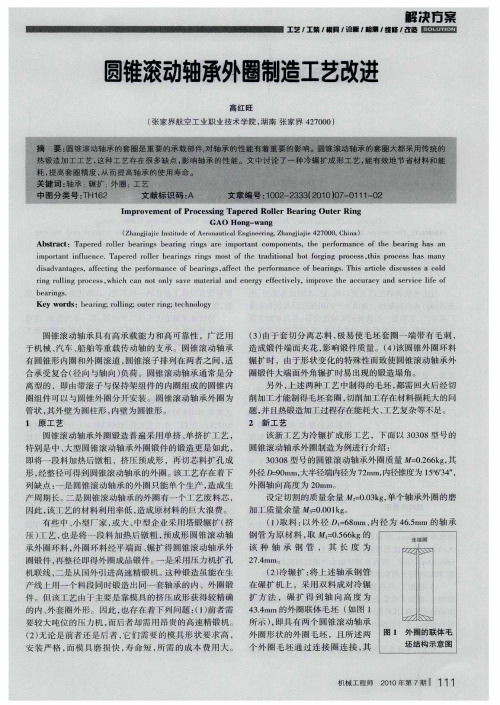
rn o ln r c s , ih c n n to l a e mae i la d e e g f c i e y mp o e t e a c r c n e v c i f i g r li g p o e s wh c a o n y s v t ra n n r y ef tv l ,i r v h c u a y a d s r i e l e o e f b ai g . e rn s
锯 决方 案
工艺 /r / -甍 誓具 , 诌曩 / l 篮俗 , 遁 目雹雹圆 麓I , l
圆锥滚动轴承外圈制造工艺改进
高 红 旺
( 张家界航空工业职业技 术学院 , 湖南 张 家界 4 7 0 2 0 0)
I po e m r v me fPr c s i p r d Ro l r Be r ng Ou e n nto o e sng Ta e e le a i t r Ri g
圈锻件 , 再整 径 即得 外 罔 成 品锻件 。 是采 用 压 力机 扩 孔 一
该新 工 艺 为冷 辗 扩 成形 工 艺 ,下 面 以 3 3 8型 号 的 00
圆锥 滚动 轴 承 外圈 制造 为例进 行 介绍 : 3 38型号 的圆 锥滚 动 轴 承外 圈 质 量 M= . 6 g其 00 O 6 k, 2
2 新 工艺
圆锥滚 动轴 承外 圈锻 造 普遍 采 用 单挤 、 挤 扩 工艺 , 单 特别 是 中 、 型 圆锥 滚 动轴 承 外 圈锻 件 的 锻造 更 是 如 此 , 大 即将一 段 料 加 热后 镦 粗 ,挤 压 预成 形 ,再 切 芯 料 扩 孔成 形 , 整 径可 得 到 圆锥滚 动轴 承 的外 圈 。 工 艺存 在 着下 经 该 列 缺点 : 是 圆锥 滚 动轴 承 的外 圈 只能 单 个 生产 , 成 生 一 造 产 周期 长 。 二是 圆 锥滚 动轴 承 的 外 圈有 一 个工 艺废 料 芯 , 因此 , 工艺 的材 料利 用率 低 , 成 原 材料 的巨大 浪 费 。 该 造 有 些 中 、 型 厂 家 , 大 、 型企 业 采 用塔 锻 辗 扩 ( 小 或 中 挤 压 )二 , 是 将 一 段 料 加 热 后镦 粗 , 成 形 圆 锥 滚 动轴 _艺 也 I 预 承 外 圈环 料 , 圈环 料 经平 端 面 、 扩 得 圆锥 滚动 轴 承 外 外 辗
磨削加工对滚动轴承套圈工作表面的影响和解决方式

磨削加工对滚动轴承套圈工作表面的影响和解决方式【摘要】对于轴承来讲,其在我国工业生产领域占有十分重要的地位,是大多数机械设备运行的基础保障,同时也是机械设备构成的基础零部件。
因此可以说,轴承的质量同我国工业生产之间存在密切的关联。
在进行轴承生产、加工过程中,包含很多环节,其中,磨削加工是整体流程的最终工序,影响着滚动轴承的工作面。
本文简要论述了形成磨削变质层的原理,探讨了滚道表面变质层的特点及类别,并提出相应的处理措施,目的在于进一步提高滚动轴承的生产、加工质量,保证机械设备的安全、稳定运转。
【关键词】磨削加工;滚动轴承;套圈;工作表面;影响;处理方式在工业生产中,滚动轴承有着十分重要的作用,影响着生产的质量及效率。
其是机械设备的基础零部件,假如轴承的表面存在质量问题,那么就会缩短轴承的使用年限,对整体生产工艺也会造成危害。
因此,相关工作人员需要对滚动轴承套圈的磨削加工工艺进行深入研究,提高加工水平。
以下简要针对其相关内容进行分析,仅供参考。
1.形成磨削变质层的原理对于磨削加工来讲,其是借助砂轮的高速旋转对轴承的表面实施切割工艺。
砂轮的表面通常是由较为细小的磨砂构成的,磨砂的形状较不规则,在转动期间,速率相对较快。
进行生产加工过程时,砂轮通常会对轴承表面进行挤压、摩擦,从而对轴承形成作用力,使轴承表面发生形变。
因为在日常工作转动过程中,轴承与砂轮间相对速度较快,则会产生较多热量,再加之砂轮本身的导热特性较差,因此切削液较难流入磨削部位,则温度很难传递出去,使零件的温度提高,甚至严重的可以使温度提高到800℃-1000℃左右。
进而引起滚动轴承的表面组织出现改变,使滚道发生变质问题,影响工作质量及效率。
2.滚道表面变质层的特点及类别2.1磨削热导致的变质层一般来讲,因为磨削热导致的变质层可以被划分成以下几个类别:其一,表面氧化层。
在对轴承进行磨削加工时,因为高速旋转引发热量提高,在空气的影响下,钢材质表面很容易形成铁氧化层,此氧化层的厚度对磨削加工的质量有着十分关键的作用,地位极为重要;其二,非晶态组织层。
轴承套圈工艺改进技术专题报告1
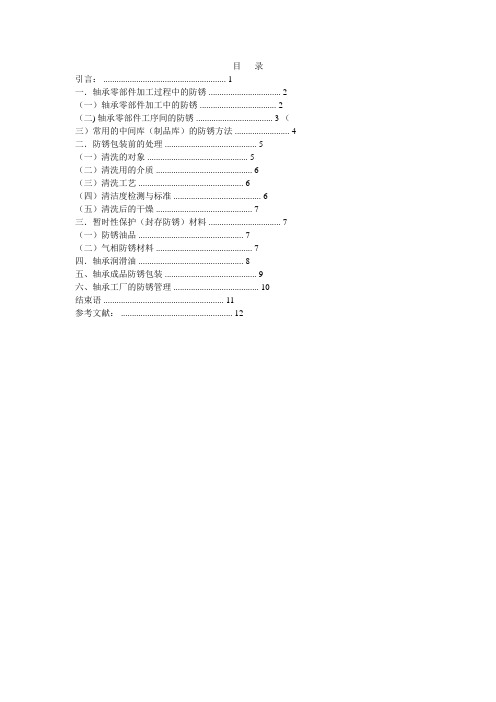
目录引言: (1)一.轴承零部件加工过程中的防锈 (2)(一)轴承零部件加工中的防锈 (2)(二) 轴承零部件工序间的防锈 ................................... 3 (三)常用的中间库(制品库)的防锈方法 . (4)二.防锈包装前的处理 (5)(一)清洗的对象 (5)(二)清洗用的介质 (6)(三)清洗工艺 (6)(四)清洁度检测与标准 (6)(五)清洗后的干燥 (7)三.暂时性保护(封存防锈)材料 (7)(一)防锈油品 (7)(二)气相防锈材料 (7)四.轴承润滑油 (8)五、轴承成品防锈包装 (9)六、轴承工厂的防锈管理 (10)结束语 (11)参考文献: (12)深沟球轴承轴承内外圈磨加工工艺过程改进作者:刘圣斌指导老师:余军合宁波大学科学技术学院摘要:通过改进轴承内外圈磨工工艺过程和使用的设备,可以使产品磨加工工艺过程和在制品周转更加合理,解决了冷却水、精研油、清洗煤油交叉相混现象,降低了生产成本,降低社会劳动生产时间的同时提高了社会劳动生产率和产品质量。
进一步扩大了轴承产品的竞争优势。
关键字:深沟球轴承;内圈、外圈、磨削、工艺一、轴承介绍:轴承是一种精度高、互换性很强的标准零件,因此,为获得高的生产效率和产品质量,常采用专用加工设备。
达克公司公司专业化生产深沟球轴承,对内外圈的磨加工工艺过程进行了多次改进,提高了工效和产品质量。
1原设备及工艺存在的问题原内、外圈磨超工艺如下:外圈:磨端面(MB7480)→退磁、清洗→磨外径(M1080,MG10200)→支外径磨外沟道(3MZ146)→退磁、清洗→支外径超精外沟道(四轴超精机)。
内圈:磨端面(MB7480)→退磁、清洗→磨内圈挡边(M1050,MGT1050)→支内沟道磨内沟道(3MZ133)→退磁、清洗→支内沟道磨内径(3MZ203)→退磁、清洗→支内圈挡边超精内沟道(四轴超精机)。
立轴圆台平面磨床(MB7480)弊端:此磨床分磨削套圈两个端面,套圈磨第一端面后需要退磁清洗,再磨第二端面,再退磁清洗。
圆锥孔滚子轴承内滚道磨加工夹具的改进
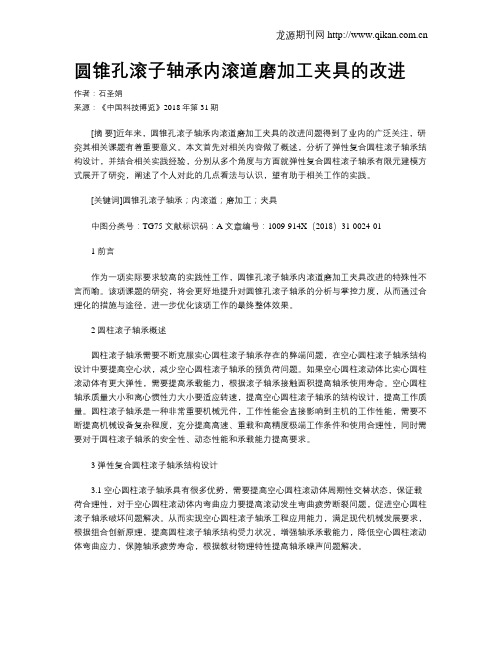
圆锥孔滚子轴承内滚道磨加工夹具的改进作者:石圣娟来源:《中国科技博览》2018年第31期[摘要]近年来,圆锥孔滚子轴承内滚道磨加工夹具的改进问题得到了业内的广泛关注,研究其相关课题有着重要意义。
本文首先对相关内容做了概述,分析了弹性复合圆柱滚子轴承结构设计,并结合相关实践经验,分别从多个角度与方面就弹性复合圆柱滚子轴承有限元建模方式展开了研究,阐述了个人对此的几点看法与认识,望有助于相关工作的实践。
[关键词]圆锥孔滚子轴承;内滚道;磨加工;夹具中图分类号:TG75 文献标识码:A 文章编号:1009-914X(2018)31-0024-011 前言作为一项实际要求较高的实践性工作,圆锥孔滚子轴承内滚道磨加工夹具改进的特殊性不言而喻。
该项课题的研究,将会更好地提升对圆锥孔滚子轴承的分析与掌控力度,从而通过合理化的措施与途径,进一步优化该项工作的最终整体效果。
2 圆柱滚子轴承概述圆柱滚子轴承需要不断克服实心圆柱滚子轴承存在的弊端问题,在空心圆柱滚子轴承结构设计中要提高空心状,减少空心圆柱滚子轴承的预负荷问题。
如果空心圆柱滚动体比实心圆柱滚动体有更大弹性,需要提高承载能力,根据滚子轴承接触面积提高轴承使用寿命。
空心圆柱轴承质量大小和离心惯性力大小要适应转速,提高空心圆柱滚子轴承的结构设计,提高工作质量。
圆柱滚子轴承是一种非常重要机械元件,工作性能会直接影响到主机的工作性能,需要不断提高机械设备复杂程度,充分提高高速、重载和高精度极端工作条件和使用合理性,同时需要对于圆柱滚子轴承的安全性、动态性能和承载能力提高要求。
3 弹性复合圆柱滚子轴承结构设计3.1 空心圆柱滚子轴承具有很多优势,需要提高空心圆柱滚动体周期性交替状态,保证载荷合理性,对于空心圆柱滚动体内弯曲应力要提高滚动发生弯曲疲劳断裂问题,促进空心圆柱滚子轴承破坏问题解决。
从而实现空心圆柱滚子轴承工程应用能力,满足现代机械发展要求,根据组合创新原理,提高圆柱滚子轴承结构受力状况,增强轴承承载能力,降低空心圆柱滚动体弯曲应力,保障轴承疲劳寿命,根据教材物理特性提高轴承噪声问题解决。
圆锥滚子轴承套圈内外同套锻造工艺及其控制

轴承套圈锻造加工的主要 目的是 : ①获得与产品形状相近的毛 坯, 从 而 提高 金属 材料 利 用 率 , 减少 机 械加 工 量 ; ② 消 除金 属 内在 缺 陷, 改善金属组织 , 使金属流线分布合理 , 致密度好 , 从而提高轴承 使 用 寿命 。 根据锻造时金属的温度高低 , 将锻造分为热锻 、 冷锻和温锻三 大类 : 将 金 属 加 热 到再 结 晶温 度 以上 的锻 造加 工 叫热 锻 ; 金 属 在 室 温下 的变 形 叫冷 锻 ; 而介 于 两 者之 间 的金 属 变形 叫温 锻 。现 在大 量 采用 的加 工 方法 还是 热 锻 。 热 锻 轴承 套 圈的 生产 过程 主 要包 括 三个 环节 : 加热 、 下 料 和锻 造 成形 。锻 造 成形 是 套 圈 锻 造 生 产 的 中心 环 节, 其 形式 很 多 , 我 国大 量 采 用 的是 三 大类 工 艺 : 锤上锻 、 平 锻 机 锻 造和 压 力机 锻造 。 压 力机 锻造 后 , 要 经过 扩孔 机 辗扩 成形 , 以提 高锻 件质量 、 精度和生产率 , 有时为了进一步提高锻件 的尺寸和几何精 度, 为后续工序的 自动化创造条件 , 需要再加精整f 或整形) 工序 。最 后是 退 火工 艺 以便 机 加工 日 。 2 压力 机上 锻 造轴 承套 圈 的优 点 在 压力 机 上锻 造 轴承 套 圈 , 除一 些 小型 锻 件在 压 力 机上 直 接锻 造 成 形外 , 一般 将 压 力 机 与扩 孔 机 联 起来 , 组 织 流 水作 业一 火 锻 造 流水线 , 由压 力机 提 供 扩 孔 前 的毛 坯 , 这 样 降 低 了对 压 力 机 锻 造 的 要求, 扩大 其 能加 工锻 件 的尺 寸 范 围 , 充 分 利 用 了辗 扩工 艺 的 优点 , 因而提 高 了生 产效 率 , 提 高 了锻 件 的尺 寸 精度 和 内在质 量 。压 力 机 锻 造轴 承 套 圈 的优 点 有 : 2 . 1锻件质量高 :金属在型模中被挤压成形 ,内部组织均匀致 密, 锻件表面光洁, 尺寸精度高 。经辗扩后的锻件, 有 的直接将套圈 的滚道辗出 , 金属流线符合轴承的工作要求 , 因而提高 了轴承的寿
滚动轴承套圈数控车削缺陷分析及改进措施

序言目前,国内轴承行业的轴承套圈已经采用先进的数控车削加工技术。
生产实践中发现,轴承套圈在数控车削加工过程中,由于受到各种因素的影响,加工出来的工件不仅达不到规定的技术要求,还会出现各种各样的质量问题,从而造成不合格品甚至废品。
因此,必须进行质量分析,找出质量问题产生的原因,采取相应的纠正预防措施。
滚动轴承套圈数控车削加工过程中的常见缺陷有:车刀纹粗大、垫伤、漏工序、工件放偏、车削瘤、滚道留筋、振纹、倒角异常、挡边低及崩刀等。
有些缺陷出现在表面,很容易被发现,例如车刀纹粗大、漏工序等,可以将缺陷件挑出来后进行返工,经检验合格后流转至下道工序;有些缺陷如垫伤、倒角异常及挡边低等,必须将缺陷件挑出来做报废处理;另外一些缺陷,例如工件放偏、车削瘤及滚道留筋等,不容易被发现,若流入下道工序,则会带来质量隐患,甚至会导致产品报废。
下面以实例分析方式,对滚动轴承套圈数控车削加工过程中产生的缺陷进行原因分析并加以整理归纳,提出相应的改进措施。
缺陷分析与改进措施2.1 工件车刀纹粗大轴承套圈车削完成后,发现端面有非常明显的粗大车刀纹(见图1)。
产生这种缺陷的主要原因是车削刀具选用不合理,如刃口形状、角度不正确(如刀头太尖等),甚至刃口有缺陷;进刀速度快,进给量选择不合理;主轴的间隙大,车削过程中产生振动;材料硬度不合格,如果套圈锻件太硬或太软,则也会出现刀纹粗大问题。
图1端面车刀纹粗大针对该问题采取的改进措施如下。
1)选择合适的车削刀具、合理的进刀速度,调整机床主轴间隙在合适的范围。
2)要求轴承套圈锻件球化退火后硬度在合格范围之内(如GCr15轴承钢退火硬度为8 8~94HRB),这样可避免因硬度不合格而导致的车削刀纹粗大问题。
3)改善机床的刚度,避免机床、工件及刀具在车削过程中产生振动。
4)对于端面有明显车刀纹的轴承套圈,挑出来做报废处理,决不能流入下道工序。
2.2 工件垫伤数控车削后的轴承套圈端面或外径某部位有明显的凹坑,称为车削垫伤。
我国轴承套圈超精研技术的改进要点

我国轴承套圈超精研技术的改进要点我曾经在《怎么样提高高精度轴承的超精质量?》一文中写到:“超精加工主要要提高和改善被加工工件表面的微观质量,这些微观质量包括粗糙度、沟形、圆度和金属条纹的走向。
”轴承套圈沟道超精研工序主要是为了降低被加工沟道的粗糙度,这是最基本的要求,无论是最原始的棍棒超精机还是采用无心支撑结构的自动化超精机,原理大同小异,都是如此。
高水平的和低档的轴承套圈超精研设备的主要区别是轴承套圈沟道形状精度的改善程度和被加工工件表面应力状态的差异。
轴承套圈沟道形状精度的改善主要取决于三个方面:首先,要约束超精前的轴承沟道磨加工形状的基础精度,轴承沟道的基准精度和位置精度在磨削工序也要精确地控制,因为这些需要约束的被加工工件的磨削工序的精度及其对超精加工的结果的影响是不容忽视的;其次,超精研设备的制造精度也会对被超精工件沟道表面形状的变化起到很大的影响,品质较差的超精机非但不能够改善磨削工序形成的形状精度,反而会破坏磨削工序形成的形状精度;第三,超精余量的大小不仅与超精加工的节拍有关,而且也与轴承沟道超精后的表面质量有关系。
假如我们的轴承产品没有对轴承的噪音和轴承的寿命提出特殊的要求,假如我们的轴承产品仅仅满足于参与国内外市场的低价格竞争,假如我们的轴承产品不想走出国门或者不想替代进口产品,那么,使用低价位的超精研设备是可以的。
因为,在中低档产品的轴承市场上,中国的轴承企业打了很多顽强的战役,在空调类家电市场和电机市场,我们的微型和小型轴承取得了不俗的销售业绩,这些成绩的取得也部分得益于我国轴承加工设备的发展和进步。
而在我国高精尖产品领域,大量的高附加值高利润轴承还是依靠进口。
我国生产的最好的轴承设备,即使出口到国外,也只是应用在普通轴承生产线上;部分大陆境内的外资和合资的轴承加工企业采购国内的轴承设备,也主要用在中低档轴承的生产线上。
迄今为止,我国高水平的进口轴承设备所占的比率很小,部分原因是由于高水平的进口轴承设备的价格普遍高于国产的轴承设备,其主要原因还是国内大部分企业生产的轴承精度和效率要求偏低,在引进更好水平的进口轴承设备方面的要求还不是特别强烈。
圆锥滚子轴承内圈挡边磨削工艺的改进
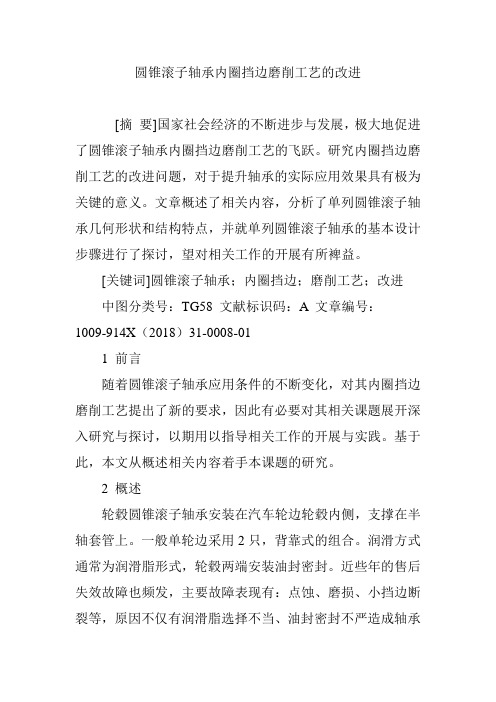
圆锥滚子轴承内圈挡边磨削工艺的改进[摘要]国家社会经济的不断进步与发展,极大地促进了圆锥滚子轴承内圈挡边磨削工艺的飞跃。
研究内圈挡边磨削工艺的改进问题,对于提升轴承的实际应用效果具有极为关键的意义。
文章概述了相关内容,分析了单列圆锥滚子轴承几何形状和结构特点,并就单列圆锥滚子轴承的基本设计步骤进行了探讨,望对相关工作的开展有所裨益。
[关键词]圆锥滚子轴承;内圈挡边;磨削工艺;改进中图分类号:TG58 文献标识码:A 文章编号:1009-914X(2018)31-0008-011 前言随着圆锥滚子轴承应用条件的不断变化,对其内圈挡边磨削工艺提出了新的要求,因此有必要对其相关课题展开深入研究与探讨,以期用以指导相关工作的开展与实践。
基于此,本文从概述相关内容着手本课题的研究。
2 概述轮毂圆锥滚子轴承安装在汽车轮边轮毂内侧,支撑在半轴套管上。
一般单轮边采用2只,背靠式的组合。
润滑方式通常为润滑脂形式,轮毂两端安装油封密封。
近些年的售后失效故障也频发,主要故障表现有:点蚀、磨损、小挡边断裂等,原因不仅有润滑脂选择不当、油封密封不严造成轴承运转过程过热、材料选择问题等等,而且有一部分原因体现在产品选型和设计开发过程中的问题,如为追求动载荷过大,滚子数量选择过多;大小挡边结构设计不合理等,本文重点介绍单列圆锥滚子轴承在设计过程中的一些步骤及注意事项。
3 单列圆锥滚子轴承几何形状和结构特点圆锥滚子轴承主要由内圈、外圈、滚子以及保持架组成。
圆锥滚子轴承有以下特点。
(1)圆锥滚子的内圈滚道、外圈滚道以及滚子的母线沿长线应与旋转轴线相交一点,便于滚子沿着滚道的每点作纯滚动运动。
(2)圆锥滚子轴承的内外圈滚道是有倾斜角的,使轴承具备了承受轴向载荷和径向载荷的能力。
外滚道和中心线角度大小与承受轴向载荷和径向载荷的能力有着密切的关系,内外圈的滚道与滚子之间的线接触使其具备很高的承载能力。
这个特点在很多的场合得到了应用,尤其汽车车桥,如:汽车轮毂轴承、主减速器轴承、差速器轴承等。
圆锥滚子轴承套圈双端面磨削加工工艺的探讨
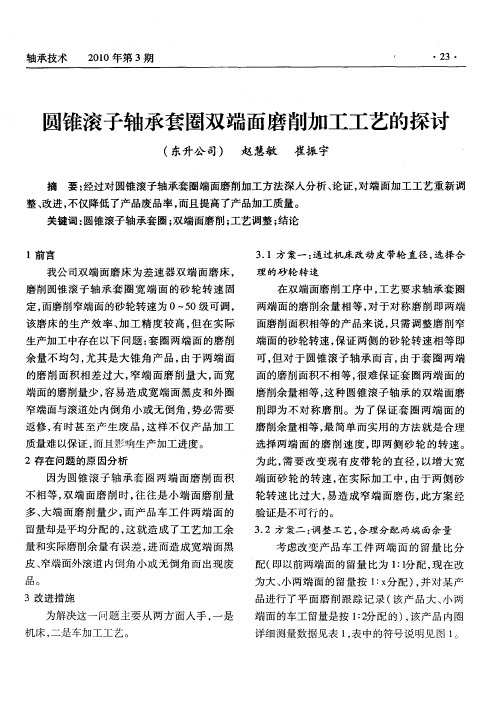
3改进措 施
品进行 了平 面 磨 削 跟 踪 记 录 ( 产 品大 、 两 该 小 端 面 的车工 留量 是按 1玢 配 的 )该 产 品 内 圈 : ,
详 细测 量数 据见 表 1 表 中 的符号说 明见 图 1 , 。
为解决 这 一 问题 主要 从 两 方 面 人 手 , 是 一
机床, 二是 车加 工工 艺 。
验证 是不 可行 的。
3 2方 案二 : 整 工 艺 , . 调 合理 分配 两端 面余 量
因为 圆锥 滚 子 轴 承 套 圈 两 端 面磨 削 面 积
不相 等 , 端 面磨 削 时 , 往 是 小 端 面 磨 削 量 双 往 多 、 端 面磨 削量 少 , 大 而产 品 车 工 件 两 端 面 的 留量却是 平均 分 配 的 , 就 造 成 了工 艺 加 工 余 这
窄端 面与 滚道 处 内倒 角 小 或 无 倒 角 , 必 需 要 势
返修 , 时 甚 至 产 生 废 品 , 样 不 仅 产 品加 工 有 这 质量难 以保 证 , 而且影 响生产 加工 进度 。
2存 在 问题 的原 因分析
可, 对于 圆锥滚子轴承而 言, 但 由于套圈两端
面的磨 削 面积不 相 等 , 难 保 证 套 圈两 端 面 的 很 磨 削余 量相 等 , 种 圆锥 滚 子 轴 承 的双 端 面磨 这 削即 为不 对 称 磨 削。 为 了 保 证 套 圈两 端 面 的 磨 削余 量相 等 , 简单 而 实 用 的方 法 就 是 合 理 最 选择 两 端 面 的磨 削 速 度 , 即两 侧 砂 轮 的转 速 。 为 此 , 要 改 变 现 有 皮 带 轮 的直 径 , 需 以增 大 宽 端 面砂 轮 的 转 速 , 实 际 加 工 中 , 在 由于 两 侧 砂 轮转 速 比过 大 , 易造 成 窄 端 面磨 伤 , 方 案 经 此
圆锥滚子轴承内圈大挡边油沟车加工工艺改进

圆锥 滚 子轴 承 内圈 油 沟 的加 工 质 量 不仅 影 响 套 圈 的磨 削 加 工 , 而 且 会 对 成 品轴 承 的 质 量 产 生
强度 大 , 差 错 率高 ; ( 6 ) 受 刀具 材料 的 限制 , 不 适 宜 于淬 火后 工 件 油沟 的加 工 。
影响…。随着轴承技术 的发展 , 对 圆锥 滚子轴承 内圈大挡边油沟 的加工质 量要求越来越 高, 主要 表现为油沟深度尺寸 和坐标 尺寸要求越来越 小, 表面粗糙度要求越来 越高。因此 , 在分析传 统圆 锥 滚 子轴 承 内圈 大挡边 油 沟 ( 简称油沟) 加工 方 法 的基础上 , 需要采用更加合理的设备和刀具 , 以提
高油 沟 的加工 质量 。
1 传 统 的 油 沟 加 工 方 法
圆锥滚子轴承内圈油沟传统加工设备及刀具 为普通车床 + 手磨 成形刀具 。采用 普通 C A 6 1 4 0 车床 , 手工刃磨 油沟 刀 , 手摇 纵 向刀架进 给加 工 ( 图1 ) 。传 统 加工 方 法 在 实 际应 用 中存 在 以下 不
摘要: 分析 圆锥滚子 轴承 内圈大挡边油沟传统加 工方 法存 在的不足 , 详 细介绍 了采用数控机床 和成形刀具加 工 大挡边 油沟的方法 , 实例 验证 了改进后工艺方法 的优 点。
关键 词 : 圆锥滚子轴 承 ; 大挡边油沟 ; 数控车床 ; 成 形车刀
中图分类 号 : T H 1 3 3 . 3 3 2 ; T G 7 1 2 文献标志码 : B 文章编 号: 1 0 0 0— 3 7 6 2 ( 2 0 1 3 ) 0 2— 0 0 2 5— 0 3
此, 只能靠刀具本身的角度来控制油沟的角度 , 而
《 轴 承) ) 2 0 1 3 . N o . 2
预防轻系列圆锥滚子轴承套圈热处理变形的措施_杨文生
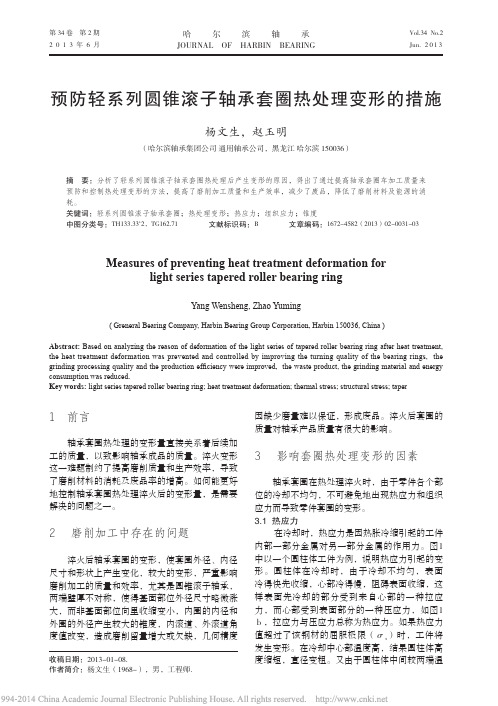
轴承套圈在热处理淬火时,由于零件各个部 位的冷却不均匀,不可避免地出现热应力和组织 应力而导致零件套圈的变形。 3.1 热应力 在冷却时,热应力是因热胀冷缩引起的工件 内部一部分金属对另一部分金属的作用力。图1 中以一个圆柱体工件为例,说明热应力引起的变 形。圆柱体在冷却时,由于冷却不均匀,表面 冷得快先收缩,心部冷得慢,阻碍表面收缩,这 样表面先冷却的部分受到来自心部的一种拉应 力,而心部受到表面部分的一种压应力,如图1 b,拉应力与压应力总称为热应力。如果热应力 值超过了该钢材的屈服极限(σ s)时,工件将 发生变形。在冷却中心部温度高,结果圆柱体高 度缩短,直径变粗。又由于圆柱体中间较两端温
要控制在1.33~1.50m/s。系统压力过大,进给量 过快会产生较大的挤压力,会使轴承套圈在热处 理时释放车加工的残余应力,造成工件变形量的 增加。 (2)控制好车加工过程中的几何形状精度, 夹具安装找正要精确,椭圆度、壁厚差、锥度等 几何形状精度要在技术条件要求范围内尽量好一 些。 (3)车加工的产品尺寸要控制在尺寸公差的 中间值。尺寸散差要小。锻件的留量,退火的硬 度,刀具切削刃的磨损都会造成车加工工件尺寸 散差增大。尺寸散差过大,会使磨削加工尺寸偏 差很难控制,影响磨加工的产品质量。 (4)根据轴承套圈淬火变形的规律,在车加 工时应预留出锥度变形的空间。一般情况下, 截面非对称轴承套圈的变化规律是:远离基面的 直径尺寸会有不同程度地发生收缩,内外圈皆是 如此,而且系列代号越轻﹑幅面越宽的产品变形 越大。因此在车加工精车时,考虑淬火后变形的 问题可参考表1的抽检结果数值。以圆锥滚子轴 承内圈(见图 4)为例:精车内滚道的实际锥角 β1,要比成品设计角度β略小Δ β,β1=β-Δ β。精 车内径时,要人为地加工出非基面端内径尺寸比 基面端的内径尺寸略大的锥度,两端面内径尺寸 的差值为Δ d,d1=d+Δ d。因Δ β在实际测量中, 量表的读值显示的是距离,所以Δ β ≈Δ d /2。 Δ d 应根据套圈直径尺寸的大小、系列代号的宽 窄、轻重等不同条件选取。对于50mm≤ d ≤80 mm,80mm≤D≤250mm的圆锥轴承圈,Δ d 值可取在0.07~0.3mm之间。通常情况下,取值 的规律是直径越大,系列越轻、越宽的套圈, Δ d 取值越大。余下一定程度的变形量,可以在 磨加工过程中消除。此方法以应用多年,有效地 减少了车工变形对磨工的影响。
轴承套圈磨加工工艺过程改进

使用球 轴承套 圈沟道 自动超精机 (M 31, 3 Z20
3 z l) M 36 取代四轴超精机, 以陶瓷材料为支承材料 , 外圈采用无心支承方式 , 内圈采用 内孔定心方式 , 端面夹紧, 有两个加工工位 , 实现粗 , 精超一次完成 , 超精后工件沟道圆度、 粗糙度得到较好改善。 增加外圈外径修磨工序 , 去除工件支 承造成
l 原设备及 工艺存在 的问题
原内、 外圈磨超工 艺如下 。 外圈: 磨端面 ( B40 退磁 、 M 78 ) 清洗 _磨 外 径 +
( 18 , G 00 ) M 00 M 1 0 _支外径磨外沟道(M 16 - 2 3 Z4)+ 退磁、 清洗_支外径超精外沟道 ( + 四轴超精机) 。 内圈: 磨端面( B40 _ 退磁、 M 78 )÷ 清洗 磨 内圈 挡 边 ( 15 , G 1 0 - 支 内沟 道 磨 内 沟 道 M 00 M T0 ) + 5 ( M 13 _ 退 磁、 洗 _ 支 内 沟 道 磨 内 径 3 Z3 ) ÷ 清 + (M 23 _ 退磁、 3 Z0)÷ 清洗- 支 内圈挡边超精 内沟道 + ( 四轴 超精机 ) 。 使用立轴 圆台平面磨床 ( B40 , M 78 )要分别磨 削套圈两 个端面, 套圈磨第一端面后需要退磁清 洗, 再磨第二端面, 再退磁清洗。如果对 工件端面 磨 削量大小控制 不均 , 就会使 磨削 后沟 位置 受到影 响 , 磨削工序 产生 沟 道黑皮 , 时 , 造成 同 电磁 工作 台 如有脏物或工件定位不平将造成磨后工件的端面 平行度增 大, 沟时沟道对基准端面的平行度增 磨 大, 此类工 件影响到成品轴承旋 转精度和运转噪 声。使用该设备加工工件周期长、 效率低、 劳动强 度大 。
提高轴承商品零件在磨削加工中的质量
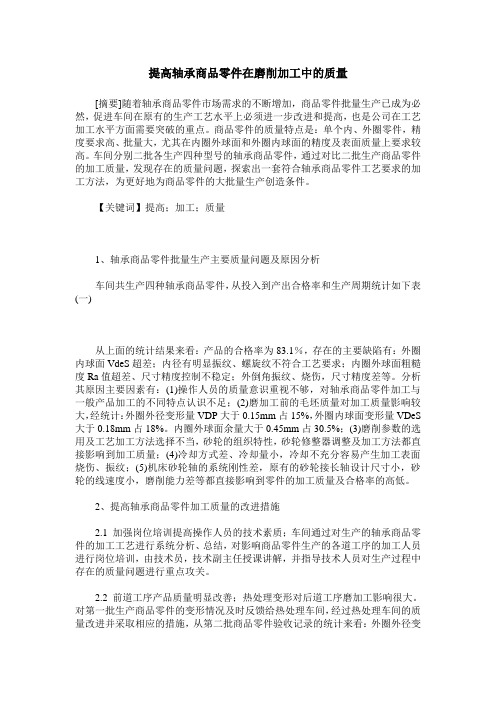
提高轴承商品零件在磨削加工中的质量[摘要]随着轴承商品零件市场需求的不断增加,商品零件批量生产已成为必然,促进车间在原有的生产工艺水平上必须进一步改进和提高,也是公司在工艺加工水平方面需要突破的重点。
商品零件的质量特点是:单个内、外圈零件,精度要求高、批量大,尤其在内圈外球面和外圈内球面的精度及表面质量上要求较高。
车间分别二批各生产四种型号的轴承商品零件,通过对比二批生产商品零件的加工质量,发现存在的质量问题,探索出一套符合轴承商品零件工艺要求的加工方法,为更好地为商品零件的大批量生产创造条件。
【关键词】提高;加工;质量1、轴承商品零件批量生产主要质量问题及原因分析车间共生产四种轴承商品零件,从投入到产出合格率和生产周期统计如下表(一)从上面的统计结果来看:产品的合格率为83.1%,存在的主要缺陷有:外圈内球面VdeS超差;内径有明显振纹、螺旋纹不符合工艺要求;内圈外球面粗糙度Ra值超差、尺寸精度控制不稳定;外倒角振纹、烧伤,尺寸精度差等。
分析其原因主要因素有:(1)操作人员的质量意识重视不够,对轴承商品零件加工与一般产品加工的不同特点认识不足;(2)磨加工前的毛坯质量对加工质量影响较大,经统计:外圈外径变形量VDP大于0.15mm占15%,外圈内球面变形量VDeS 大于0.18mm占18%。
内圈外球面余量大于0.45mm占30.5%;(3)磨削参数的选用及工艺加工方法选择不当,砂轮的组织特性,砂轮修整器调整及加工方法都直接影响到加工质量;(4)冷却方式差、冷却量小,冷却不充分容易产生加工表面烧伤、振纹;(5)机床砂轮轴的系统刚性差,原有的砂轮接长轴设计尺寸小,砂轮的线速度小,磨削能力差等都直接影响到零件的加工质量及合格率的高低。
2、提高轴承商品零件加工质量的改进措施2.1 加强岗位培训提高操作人员的技术素质;车间通过对生产的轴承商品零件的加工工艺进行系统分析、总结,对影响商品零件生产的各道工序的加工人员进行岗位培训,由技术员,技术副主任授课讲解,并指导技术人员对生产过程中存在的质量问题进行重点攻关。
轴承套圈锻造工艺的优化_丁海军
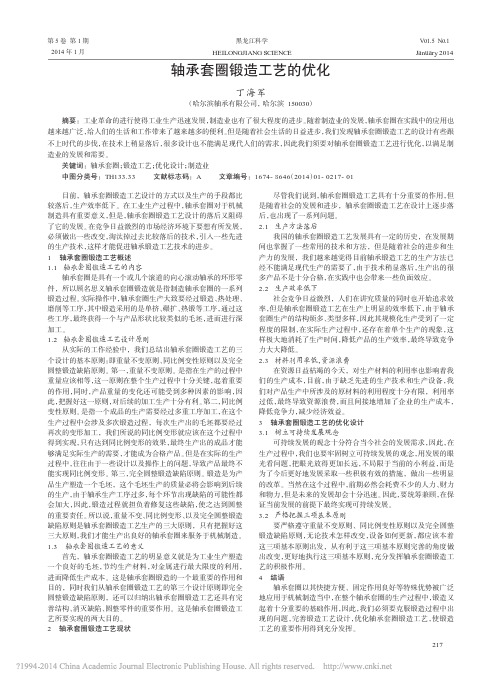
第5卷第1期2014年1月黑龙江科学HEILONGJIANG SCIENCEVo1.5No.1January2014目前,轴承套圈锻造工艺设计的方式以及生产的手段都比较落后,生产效率低下。
在工业生产过程中,轴承套圈对于机械制造具有重要意义,但是,轴承套圈锻造工艺设计的落后又阻碍了它的发展。
在竞争日益激烈的市场经济环境下要想有所发展,必须做出一些改变,淘汰掉过去比较落后的技术,引入一些先进的生产技术,这样才能促进轴承锻造工艺技术的进步。
1轴承套圈锻造工艺概述1.1轴承套圈锻造工艺的内容轴承套圈是具有一个或几个滚道的向心滚动轴承的环形零件,所以顾名思义轴承套圈锻造就是指制造轴承套圈的一系列锻造过程。
实际操作中,轴承套圈生产大致要经过锻造、热处理、磨削等工序,其中锻造采用的是单挤、碾扩、热锻等工序,通过这些工序,最终获得一个与产品形状比较类似的毛坯,进而进行深加工。
1.2轴承套圈锻造工艺设计原则从实际的工作经验中,我们总结出轴承套圈锻造工艺的三个设计的基本原则:即重量不变原则、同比例变性原则以及完全圆整锻造缺陷原则。
第一,重量不变原则。
是指在生产的过程中重量应该相等,这一原则在整个生产过程中十分关键,起着重要的作用,同时,产品重量的变化还可能受到多种因素的影响,因此,把握好这一原则,对后续的加工生产十分有利。
第二,同比例变性原则。
是指一个成品的生产需要经过多重工序加工,在这个生产过程中会涉及多次锻造过程,每次生产出的毛坯都要经过再次的变形加工,我们所说的同比例变形就应该在这个过程中得到实现,只有达到同比例变形的效果,最终生产出的成品才能够满足实际生产的需要,才能成为合格产品。
但是在实际的生产过程中,往往由于一些设计以及操作上的问题,导致产品最终不能实现同比例变形。
第三,完全圆整锻造缺陷原则。
锻造是为产品生产塑造一个毛坯,这个毛坯生产的质量必将会影响到后续的生产,由于轴承生产工序过多,每个环节出现缺陷的可能性都会加大,因此,锻造过程就担负着修复这些缺陷,使之达到圆整的重要责任。
轴承外圈加工工艺设计及改进朱鹏
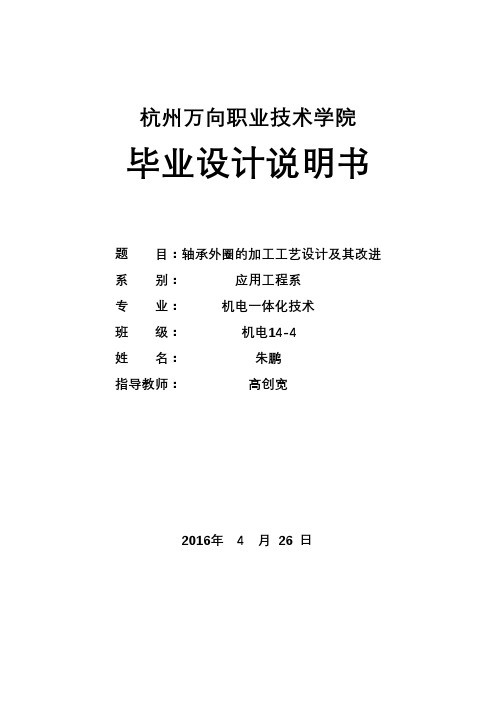
杭州万向职业技术学院毕业设计说明书题目:轴承外圈的加工工艺设计及其改进系别:应用工程系专业:机电一体化技术班级:机电14-4姓名:朱鹏指导教师:高创宽2016年 4 月26 日毕业设计原创性声明本人所呈交的毕业设计说明书是本人在导师的指导下进行的设计工作所取得的成果。
据我所知,除设计中已经注明引用的内容外,本设计不包含其他个人已经发表的成果。
对本设计的研究做出重要贡献的个人和集体,均已在设计说明书中作了明确说明并表示谢意。
作者签名:日期:目录1.零部件功能与结构 (4)1.1滚动轴承工作原理 (4)1.2滚动轴承功能(作用) (4)1.3滚动轴承结构分析 (4)2.轴承外圈零件图 (5)3.轴承外圈零件工艺分析 (5)4.轴承外圈加工工艺设计 (5)4.1加工工艺路线拟定 (5)4.2填写工艺卡 (6)5.轴承外圈加工工序设计 (6)5.1工序二:车外圆Φ52.27×7滚道Φ40.74×3.8轴承 (6)5.2工序三:车外圆Φ52.27×8滚道Φ48.7×15轴承 (8)6.轴承外圈加工的改进 (10)设计总结 (12)参考文献 (13)致谢 (14)附件1-1 (15)附件2 (16)1.零件功能与结构1.1滚动轴承工作原理滚动轴承借助于在内、外圈之间滚动体的滚动实现力的传递。
内圈紧配合于轴颈上,外圈与所配合装置之间允许有少许的转动。
当轴转动时,内圈随轴颈回转,并引导滚动体一面绕其轴心自转;一面沿内外圈滚道公转。
轴承有径向间隙和轴向游隙,以保证滚动体能自由转动。
滚动体与内、外圈之间的相对运动属于纯滚动。
保持架用于维持各滚动体之间的相对位置,防止歪斜和相互碰撞,保证滚动体能沿滚道均匀分布。
1.2滚动轴承功能(作用)滚动轴承用于支承轴及轴上零件,并保持轴的正常工作位置和旋转精度。
1.3滚动轴承结构分析滚动轴承属于轴套类零件,一般由内圈、外圈、滚动体和保持架组成。
圆锥滚子加工技术的优化改进
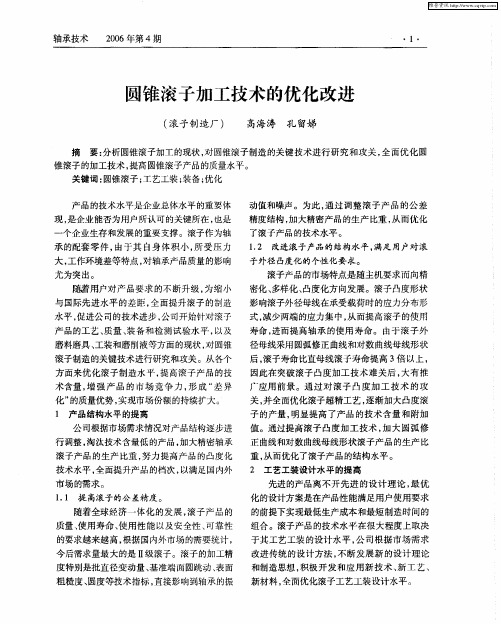
随着全球经济一 体化 的发展 , 滚子产 品的
质量、 使用寿命 、 使用性能 以及安全性 、 可靠性
的前提下实现最低生产成本 和最短制造时间的
组合 。滚子产 品的技术水平在很大程度上取决
于其工艺工装 的设计水平 , 司根据市场需求 公 改进传统的设计方法 , 不断发展新 的设计理论 和制造思想 , 积极开发和应用新技术、 新工 艺 、 新材料 , 全面优化滚子工艺工装设计水平。
1 产 品结 构水 平的提 高
广应用前景 。通过对滚子 凸度加 工 技术 的攻
关, 并全面优化滚子超精工艺 , 逐渐加大凸度滚
子 的产量, 明显提高 了产 品的技术含量和附加
公 司根据市场需求情况对产品结构逐步进 行调整, 淘汰技术含量低 的产品, 加大精密轴承 滚子产品的生产 比重 , 努力提高产品的凸度化 技术水平 , 全面提升产品的档次 , 以满足国内外
个企业生存和发展的重要支撑 。滚子作为轴
承 的配套零件 , 由于其 自身体积小 , 受压 力 所
大, 工作环境差等特点, 对轴承产品质量的影响
尤 为突 出。
子 外径 凸度化 的个性 化要 求 。
滚子产品的市场特点是随主机要求而向精
随着用户对产 品要求的不 断升级 , 为缩小 与国际先进水平 的差距, 全面提升滚子 的制造 水平 , 促进公司的技术进步 , 公司开始针对滚予
市 场 的需 求 。
1 1 提 高滚子的公 差精度 。 .
值 。通过提高滚子 凸度加工技术 , 加大圆弧修
正曲线和对数曲线母线形状滚子产品的生产 比 重, 从而优化了滚子产 品的结构水平 。
2 工艺工 装设 计水 平 的提 高
- 1、下载文档前请自行甄别文档内容的完整性,平台不提供额外的编辑、内容补充、找答案等附加服务。
- 2、"仅部分预览"的文档,不可在线预览部分如存在完整性等问题,可反馈申请退款(可完整预览的文档不适用该条件!)。
- 3、如文档侵犯您的权益,请联系客服反馈,我们会尽快为您处理(人工客服工作时间:9:00-18:30)。
非标单列圆锥滚子轴承套圈磨削工艺改进
文章简要分析了某非标单列圆锥滚子轴承套圈的结构特点及加工难点,根据在加工中出现的问题,论述了问题产生的原因及有效的解决方法,优化了磨削加工工艺。
标签:非标;单列圆锥滚子轴承;磨削加工工艺
1 概述
单列圆锥滚子轴承套圈结构较简单,一般需要经过锻造、车加工、热处理、磨加工等加工工序来实现其尺寸、精度和性能要求,而合理的磨削加工工艺在满足产品精度要求的同时,提高生产效率方面显得尤为重要[1]。
2 轴承套圈的结构特点及加工难点
某非标单列圆锥滚子轴承的结构如图1所示,其中图(a)为轴承装配图,图(b)和图(c)分别为内、外圈零件图。
由图1可知:轴承套圈为轻、窄薄壁轴承,且内、外圈滚道角度及内圈大挡边锥面与大端面的夹角均较大。
目前国内圆锥滚子轴承的加工工艺已基本成熟,但薄壁轴承套圈因其宽度小,径向和轴向刚性差,抵抗外力的能力差,易产生变形,在车加工过程中易产生加持变形,在热处理过程中易产生淬火应力变形,在磨削加工过程中因磨削热、磨削力作用易造成的磨削应力变形,这些都将导致零件的尺寸精度、形位精度等难以达到图纸要求,废品率较高,而大锥角圆锥滚子轴承在磨削加工工艺过程中,易出现磨削内滚道时砂轮无法磨削到靠近大挡边一侧的滚道边缘而造成内滚道留边的现象。
3 存在的问题及解决方案
3.1 变形问题
在各加工工序中,最大变形来自于热处理产生的淬火应力变形,其主要影响轴承套圈大端面的翘曲变形,此型号轴承在试制过程中,热后件套圈大端面翘曲变形高达0.5mm,而端面在磨削过程中起到端面定位基准的作用,因此在加工中采用加大磨削留量的方式来改善热后的变形量,使磨削后零件能达到产品要求的各项精度。
因此在工艺制定时,增大了磨削留量,将磨削加工工艺过程中常采用的两次循环磨削改为三次磨削循环以提高精度,即将原有的粗磨、细磨工序改为及粗磨、细磨及精磨工序。
外圈的磨削加工通常采用大端面定位,支撑外径磨削外径(支外磨外)、支撑外径磨削外滚道(支外磨内)的加工方式,因此大端面的精度将影响其他各面的精度,而外径的精度将影响外滚道的精度,据此,制定外圈的磨削加工工艺流程为:粗磨双端面→粗磨外径→粗磨外滚道→→磁粉探伤→稳定处理→细磨双端面→细磨外径→细磨外滚道→精磨双端面→精磨外径→精磨外滚道→超精外滚
道、抛光外径。
内圈的磨削加工通常采用大端面定位,支撑内滚道磨削内滚道(支外磨外)、支撑内滚道磨削内径(支外磨内)的加工方式,因此大端面的精度将影响其他各面的精度,而内滚道的精度将影响内径的精度,据此,制定工艺流程为:粗磨双端面→粗磨内滚道→粗磨大挡边→粗磨内径→磁粉探伤→稳定处理→细磨双端面→细磨内滚道→细磨大挡边→细磨内径→精磨双端面→精磨内滚道→精磨大挡边→精磨内径→超精内滚道、大挡边。
3.2 内滚道留边问题
在磨削此型号单列圆锥滚子轴承内圈滚道过程中,出现了砂轮端面剐蹭大挡边的现象,若避免此现象发生,必将导致磨削内滚道时,砂轮无法磨削到靠近大挡边一侧的滚道边缘而造成内滚道留边的现象。
经分析,导致此问题产生的原因是由于此型号内滚道角度较大,大挡边锥面与内圈大端端面夹角也较大,即内滚道与大挡边锥面夹角较小,而目前国内磨削内滚道的设备上可采用的砂轮直径Ds均较大(通常Ds为600mm),大挡边越程槽的设计尺寸M2max(内圈滚道素线与越程槽的交点至大挡边素线的距离)已不满足大锥角圆锥滚子轴承的加工工艺需求,因此导致此现象发生。
大挡边越程槽是大挡边与滚道之间的过渡结构,是车加工、磨加工内圈滚道和大挡边时的退刀槽,也起到容纳滚子大端倒角及储存润滑油的作用,若大挡边越程槽尺寸过大,会导致内滚道的有效长度减小,减弱轴承的承载能力,若越程槽尺寸过小,将导致磨削内滚道时产生留边现象,当小到不足以容纳滚子倒角时,会引起滚子运转不灵活并加剧磨损,最终影响成品套圈装配后的装配性能及轴承的使用寿命等,因此应合理设计和控制大挡边越程槽的尺寸[2]。
在单列圆锥滚子轴承设计时,M2max通常根据洛阳轴承研究所文件:ZYB9-93《圆锥滚子轴承设计方法》选取,据此文件选取此型号的M2max值为:M2max=0.7mm,经实践证明,此数值不适用于国内设备选用大尺寸砂轮磨削大锥角轴承的实际加工情况,易产生留边现象。
而大锥角圆锥滚子轴承磨削不产生留边的条件[3]为:
式中:M2max为大挡边越程槽的尺寸;λ为内圈大挡边锥面与端面的夹角;β为内滚道与中心线的夹角;DS为内滚道磨床砂轮直径;d2为大挡边直径;r’7min 为大挡边倒角径向坐标的最小极限尺寸;a为大挡边所在的边缘点在内滚道上的投影长度。
由图1可知:λ=13°41′39″,β=13°28′,DS=600,d2=264,di=254.108,r’7min=0.3,由上式(1)可知:M2max?0.8105,因此应优化大挡边越程槽尺寸M2max的设计值。
3.3 其他问题
3.3.1 磨削加工留量分配。
由于磨削留量较大,若细磨后,内滚道与内径的壁厚变动量(即壁厚差Ki)控制不好,在精磨工序,若滚道留量较大,内径留量较少,很容易导致磨削内径时,内径圆度达不到图纸要求的精度,即出现内径磨不圆的现象,原因是磨削内径时以内滚道为基准作为支撑面,若细磨壁厚差控
制不好,磨削内径很难改变原始偏心位置,若内径留量足够,内径精度则能达到工艺要求,否则很容易因内径留量不足造成的大批量报废。
因此,在制定磨削加工工艺时,應合理制定粗、细、精磨的磨削量,选择合理的磨削参数,在控制变形和精度的同时,缩短生产周期,提高效率。
3.3.2 磨削加工尺寸稳定性。
此型号轴承在磨削加工过程中,出现过细磨后达到精度要求,但过段时间套圈发生变形,破坏了原有精度的现象,后采取在细磨工序后增加二次回火稳定工序,达到了改善磨削后变形的问题。
4 结束语
通过分析某非标单列圆锥滚子轴承的结构特点及加工难点,结合在加工中出现的问题,论述了问题产生的主要原因及有效的解决办法,优化了磨削加工工艺,为此类单列圆锥滚子轴承的磨削加工工艺的制定提供了一定的参考性。
参考文献
[1]吴丽丽,县鹏宇.轻、窄系列圆锥滚子轴承套圈磨加工工艺分析[J].轴承,2012(11):20-21.
[2]王江山.大锥角圆锥滚子轴承内圈越程槽设计对轴承性能的影响[J].金属加工(热加工),2013(S1):185-187.
[3]陈德富.大锥角圆锥滚子轴承内圈大挡边越程槽尺寸的设计[J].轴承,2010(08):8-9.。