24对电击棒多晶硅还原炉的简介
多晶硅还原对棒

多晶硅还原对棒是一种常见的材料,通常用于生产硅单晶或多晶硅材料。
它是用于化学气相沉积(CVD)过程中的硅生长的关键材料。
以下是对多晶硅还原对棒的解释:
1. 材料组成:多晶硅还原对棒通常由高纯度的多晶硅颗粒组成。
这些颗粒具有良好的结晶性和热稳定性,适用于在高温环境中进行CVD过程。
2. 用途:多晶硅还原对棒是用于硅生长过程中的还原材料。
在CVD过程中,气态硅前体化合物(如氯化硅或三氯硅)与氢气反应,生成固态硅,该过程通常在高温炉中进行。
多晶硅还原对棒的作用是提供足够的硅原子,以便在基板表面沉积硅材料。
3. 物理特性:多晶硅还原对棒通常以棒状形式出现,其外观和物理特性取决于制造过程和规格。
它们通常具有一定的直径和长度,以适应不同的反应室或炉子。
此外,它们需要具有足够的热稳定性,以在高温条件下保持其形状和结构。
4. 制备:多晶硅还原对棒通常是通过化学气相沉积(CVD)的方法制备的。
在CVD过程中,气态硅前体化合物和氢气通过化学反应生成固态硅,该过程涉及到多晶硅还原对棒的供应和控制。
多晶硅还原对棒在半导体工业中具有广泛的应用,用于制备硅片、太阳能电池和其他硅基元件。
通过控制CVD过程中的多晶硅还原对棒的使用,可以实现对硅材料的精确生长和控制,以满足不同应用的要求。
多晶硅 还原炉 产能

多晶硅还原炉产能多晶硅还原炉是制造多晶硅的主要设备之一,其产能通常受到多种因素的影响,包括设备规格、工艺条件、操作方式等。
以下是对多晶硅还原炉产能的详细分析:1.设备规格多晶硅还原炉的规格包括炉体尺寸、电热元件结构、加热功率等。
这些因素直接决定了还原炉的生产能力。
一般来说,还原炉的尺寸越大、加热功率越高,其产能也会相应提高。
1.工艺条件工艺条件包括反应温度、反应压力、气体流量等。
这些因素对还原炉的产能也有重要影响。
在适宜的工艺条件下,多晶硅的合成反应更加充分,还原炉的生产能力也会相应提高。
1.操作方式操作方式包括装料方式、加热方式、冷却方式等。
不同的操作方式对还原炉的产能也会产生影响。
例如,采用先进的装料方式可以增加物料在炉内的停留时间,提高还原反应的效率;采用高效的加热方式可以保证炉内温度的均匀性,提高产品质量;采用快速的冷却方式可以减少产品在高温下的热损伤,提高产品性能。
1.物料质量物料质量包括硅原料的纯度、颗粒度等。
硅原料的纯度越高、颗粒度越均匀,其反应活性也会相应提高,有利于提高还原炉的产能。
1.能耗成本多晶硅还原炉的能耗成本也是影响其产能的一个重要因素。
在保证产品质量和产量的前提下,降低能耗成本可以提高企业的经济效益。
综上所述,多晶硅还原炉的产能受到多种因素的影响,包括设备规格、工艺条件、操作方式、物料质量和能耗成本等。
为了提高还原炉的产能,可以从以下几个方面进行优化:1.选用合适的设备规格,根据实际生产需求进行选型配置。
2.优化工艺条件,通过试验和计算确定最佳的反应温度、反应压力和气体流量等参数。
3.改进操作方式,采用先进的装料方式、加热方式和冷却方式,提高生产效率和产品质量。
4.提高物料质量,加强对硅原料的质量控制,提高其纯度和颗粒度等指标。
5.降低能耗成本,采用先进的节能技术和设备,提高能源利用效率。
在生产实践中,可以通过对以上因素的综合考虑,制定出适合企业实际情况的生产方案,实现多晶硅还原炉的高效生产。
多晶硅还原炉电气系统的设计和应用

多晶硅还原炉电气系统的设计和应用首先,多晶硅还原炉电气系统的设计需要考虑到设备的工作原理和要求。
多晶硅还原炉主要是通过还原炉中的燃料将硅矿石加热至高温,以便将硅矿石中的杂质还原为气体或溶解在液态硅中,从而得到纯净的多晶硅。
因此,电气系统的设计需要能够提供足够的电力供应,同时保证设备的稳定运行和生产效率。
多晶硅还原炉电气系统包括供电系统、控制系统和安全系统。
供电系统主要包括高压电源、变压器、开关设备和电缆等。
高压电源需要提供稳定的高压电源,以满足还原炉的工作需求。
变压器用于将高压电源变换为适合还原炉工作的电压。
开关设备用于控制电流的开关和保护。
电缆需要选择适用于高温和高压环境的特殊电缆,以确保电力传输的安全可靠。
控制系统用于控制还原炉的温度、电流和气体流量等参数,以保持设备的稳定运行和生产效率。
控制系统主要包括温度控制系统、电流控制系统和气体控制系统。
温度控制系统需要能够精确监测还原炉的温度,并通过调节电流和气体流量等参数来控制温度。
电流控制系统需要能够实时监测和调节还原炉的电流,以保持设备的工作状态稳定。
气体控制系统需要能够控制还原炉中的气体流量和分布,以确保杂质的还原和排除。
安全系统是多晶硅还原炉电气系统的重要组成部分,用于保护设备和人员的安全。
安全系统主要包括火灾报警系统、漏电保护系统和过载保护系统等。
火灾报警系统能够监测还原炉中的火焰和烟雾,并及时报警,以便采取相应的应急措施。
漏电保护系统能够监测还原炉电路的漏电情况,并在发生漏电时切断电源,以保护人员的安全。
过载保护系统能够监测还原炉电路的负载情况,并在过载时切断电源,以保护设备的安全。
在实际应用中,多晶硅还原炉电气系统的设计和应用需要根据具体的生产需求和设备参数进行调整。
通过合理设计和应用电气系统,可以有效地提高多晶硅还原炉的生产效率和稳定性,同时确保设备和人员的安全。
因此,多晶硅还原炉电气系统的设计和应用是多晶硅生产过程中不可忽视的重要环节。
多晶硅还原炉工作原理

多晶硅还原炉工作原理
多晶硅还原炉是用来生产多晶硅的设备,在工业上被广泛应用于太阳能电池制造等领域。
其工作原理如下:
1. 原料准备:将硅石经过选矿、破碎、洗选等处理,得到纯度较高的硅岩粉末。
同时,将还原炉内的冷却剂和硼酸等添加剂预先准备好。
2. 充填原料:将硅岩粉末从进料口注入还原炉内,确保炉内原料的密实程度和均匀性。
3. 预热阶段:启动加热设备,通过燃烧产生的高温燃气,使还原炉内的温度逐渐升高。
预热阶段的目的是为了加速反应速度,提高整个还原过程的效率。
4. 昇温反应:当还原炉内温度达到一定程度后,硅岩粉末会与炉内残留的冷却剂和硼酸等添加剂发生化学反应,生成高纯度的多晶硅。
反应过程中释放出的气体通过底部的排气孔排出,同时新的冷却剂从顶部加入以保持反应炉内的温度。
5. 冷却:当反应结束后,关闭加热设备,依靠自然冷却使炉内温度逐渐降低。
然后打开还原炉的出料口,取出经过冷却的多晶硅块。
6. 清洗:取出的多晶硅块通常还会进一步进行酸洗等处理,以去除杂质和提高其纯度。
通过以上的工作原理,多晶硅还原炉能够高效地将硅岩粉末转化为高纯度的多晶硅,在太阳能电池等领域发挥着重要作用。
24对电击棒多晶硅还原炉的简介
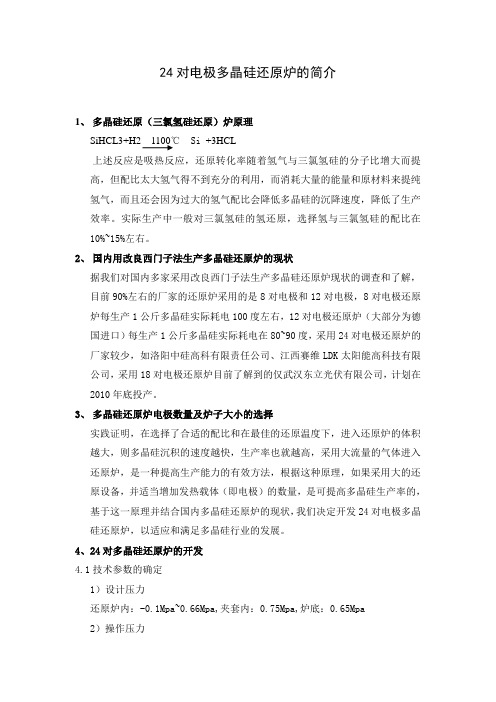
24对电极多晶硅还原炉的简介1、多晶硅还原(三氯氢硅还原)炉原理SiHCL3+H2 1100℃ Si +3HCL上述反应是吸热反应,还原转化率随着氢气与三氯氢硅的分子比增大而提高,但配比太大氢气得不到充分的利用,而消耗大量的能量和原材料来提纯氢气,而且还会因为过大的氢气配比会降低多晶硅的沉降速度,降低了生产效率。
实际生产中一般对三氯氢硅的氢还原,选择氢与三氯氢硅的配比在10%~15%左右。
2、国内用改良西门子法生产多晶硅还原炉的现状据我们对国内多家采用改良西门子法生产多晶硅还原炉现状的调查和了解,目前90%左右的厂家的还原炉采用的是8对电极和12对电极,8对电极还原炉每生产1公斤多晶硅实际耗电100度左右,12对电极还原炉(大部分为德国进口)每生产1公斤多晶硅实际耗电在80~90度,采用24对电极还原炉的厂家较少,如洛阳中硅高科有限责任公司、江西赛维LDK太阳能高科技有限公司,采用18对电极还原炉目前了解到的仅武汉东立光伏有限公司,计划在2010年底投产。
3、多晶硅还原炉电极数量及炉子大小的选择实践证明,在选择了合适的配比和在最佳的还原温度下,进入还原炉的体积越大,则多晶硅沉积的速度越快,生产率也就越高,采用大流量的气体进入还原炉,是一种提高生产能力的有效方法,根据这种原理,如果采用大的还原设备,并适当增加发热载体(即电极)的数量,是可提高多晶硅生产率的,基于这一原理并结合国内多晶硅还原炉的现状,我们决定开发24对电极多晶硅还原炉,以适应和满足多晶硅行业的发展。
4、24对多晶硅还原炉的开发4.1技术参数的确定1)设计压力还原炉内:-0.1Mpa~0.66Mpa,夹套内:0.75Mpa,炉底:0.65Mpa2)操作压力还原炉内:0.6Mpa,夹套内:0.6~0.75Mpa,炉底:0.6Mpa 3)设计温度还原炉内筒体:320℃,夹套:150℃,炉底:180℃4)操作温度还原炉内筒体:300℃,夹套:145℃,炉底:150℃5)介质内筒体:H2,SiHCL3,SiCL4,夹套:水,炉底:水※原方案采用导热油冷却以便更好地利用余热热源,经调查采用导热油冷却因渗透性大会对炉内多晶硅产生污染,影响产品纯度和质量,还是选择用水冷却。
多晶硅还原炉电气系统的设计和应用

多晶硅还原炉电气系统的设计和应用多晶硅是一种重要的半导体材料,在太阳能电池等领域有着广泛的应用。
多晶硅的生产过程中,还原炉是至关重要的设备之一、而为了确保还原炉的正常运行,电气系统的设计和应用至关重要。
本文将重点介绍多晶硅还原炉电气系统的设计和应用。
首先是供电系统。
供电系统主要是为还原炉提供电源,保证其正常运行。
多晶硅还原炉通常以三相电形式供电,采用高压输电方式。
电源的选择要考虑到设备的功率需求,同时也要保证稳定的电压和电流输出,以确保还原炉的性能和安全。
其次是控制系统。
控制系统是多晶硅还原炉电气系统的核心部分,用于对设备的温度、压力、流量等参数进行监控和控制。
控制系统通常包括PLC(可编程逻辑控制器)、DCS(分布式控制系统)、传感器、执行机构等。
通过采集和处理传感器的信号,控制系统可以实现对多晶硅还原炉各个过程参数的实时监测和控制,提高生产的稳定性和自动化水平。
最后是安全系统。
安全系统主要用于保障多晶硅还原炉在运行过程中的安全性。
安全系统通常包括火灾报警系统、气体检测系统、过压过流保护系统等。
这些系统可以通过传感器和监控装置实时监测并报警,一旦出现异常,可以及时采取措施以防止事故的发生,保护操作人员和设备的安全。
多晶硅还原炉电气系统在多晶硅生产中起着重要的作用。
其设计和应用的目的是提高生产效率、保障产品质量、确保操作人员和设备的安全。
合理的电气系统设计和选用稳定可靠的设备可以有效地提高还原炉的稳定性和自动化水平,降低生产成本,提高经济效益。
总之,多晶硅还原炉电气系统的设计和应用是多晶硅生产过程中不可或缺的一部分。
通过科学合理的设计和稳定可靠的设备选择,可以提高多晶硅生产的效率和质量,加强生产工艺的控制和自动化程度,提高生产经济效益,实现可持续发展。
多晶硅还原炉对棒材质

多晶硅还原炉对棒材质多晶硅还原炉是一种用于生产多晶硅棒材的设备。
多晶硅棒材是半导体材料的重要组成部分,广泛应用于电子、光电、太阳能等领域。
多晶硅还原炉通过还原法将硅矿石转化为多晶硅,具有高效、低能耗的特点,成为多晶硅生产的关键设备之一。
多晶硅棒材是由多晶硅材料制成的圆柱形棒状材料。
多晶硅具有优良的半导体特性,因此被广泛应用于电子行业。
多晶硅棒材通常用于制造太阳能电池、集成电路等产品。
多晶硅还原炉是制造多晶硅棒材的核心设备,其主要作用是将硅矿石经过还原反应转化为多晶硅。
多晶硅还原炉主要由炉体、加热装置、还原剂供给装置、排气装置等部分组成。
炉体是多晶硅还原炉的主要部件,通常采用陶瓷材料制成,具有良好的耐高温性能和导热性能。
加热装置通过提供高温环境,使得硅矿石能够发生还原反应。
还原剂供给装置用于提供还原剂,常用的还原剂有氢气、甲烷等。
排气装置用于排除反应产生的废气和杂质。
多晶硅还原炉的工作原理是通过高温环境下的还原反应将硅矿石转化为多晶硅。
在高温下,硅矿石与还原剂发生反应,生成气态的二氧化硅和固态的多晶硅。
随着反应的进行,固态的多晶硅逐渐沉积在棒材上,形成多晶硅棒材。
多晶硅还原炉具有高效、低能耗的特点。
由于采用了高温环境和合适的还原剂,反应速度较快,可以大大提高生产效率。
同时,多晶硅还原炉的能耗较低,可以减少生产成本和能源消耗。
在多晶硅棒材的生产过程中,多晶硅还原炉起到了至关重要的作用。
它不仅可以提高生产效率,降低能耗,还可以保证多晶硅棒材的质量。
通过控制还原剂的供给量和反应温度等参数,可以获得高纯度、低杂质的多晶硅棒材。
总之,多晶硅还原炉是制造多晶硅棒材的关键设备之一。
它通过高温环境下的还原反应将硅矿石转化为多晶硅,具有高效、低能耗的特点。
在多晶硅棒材的生产过程中,多晶硅还原炉起到了至关重要的作用,可以提高生产效率,降低能耗,并保证产品质量。
随着科技的不断进步,相信多晶硅还原炉将会在半导体材料生产领域发挥越来越重要的作用。
多晶硅还原炉

专利名称:多晶硅还原炉
专利类型:实用新型专利
发明人:吴锋,黄金发,韩秀娟申请号:CN202120443526.2申请日:20210301
公开号:CN216191105U
公开日:
20220405
专利内容由知识产权出版社提供
摘要:本实用新型公开了多晶硅还原炉。
该多晶硅还原炉包括:炉体;以及炉顶,所述炉顶设在所述炉体的顶部,所述炉顶的内表面设有热反射涂覆层。
该多晶硅还原炉的炉顶内表面设有热反射涂覆层,由此,可以有效地将热量反射至硅棒顶部,从而提高硅棒顶部的温度,使该部分硅棒的温度与硅棒整体一致,对该部分硅棒的沉积起到积极作用,进而有效提高产品的良率。
申请人:江苏鑫华半导体材料科技有限公司
地址:221004 江苏省徐州市经济技术开发区杨山路66号
国籍:CN
代理机构:北京清亦华知识产权代理事务所(普通合伙)
代理人:肖阳
更多信息请下载全文后查看。
- 1、下载文档前请自行甄别文档内容的完整性,平台不提供额外的编辑、内容补充、找答案等附加服务。
- 2、"仅部分预览"的文档,不可在线预览部分如存在完整性等问题,可反馈申请退款(可完整预览的文档不适用该条件!)。
- 3、如文档侵犯您的权益,请联系客服反馈,我们会尽快为您处理(人工客服工作时间:9:00-18:30)。
24对电极多晶硅还原炉的简介
1、多晶硅还原(三氯氢硅还原)炉原理
SiHCL3+H2 1100℃ Si +3HCL
上述反应是吸热反应,还原转化率随着氢气与三氯氢硅的分子比增大而提高,但配比太大氢气得不到充分的利用,而消耗大量的能量和原材料来提纯氢气,而且还会因为过大的氢气配比会降低多晶硅的沉降速度,降低了生产效率。
实际生产中一般对三氯氢硅的氢还原,选择氢与三氯氢硅的配比在10%~15%左右。
2、国内用改良西门子法生产多晶硅还原炉的现状
据我们对国内多家采用改良西门子法生产多晶硅还原炉现状的调查和了解,目前90%左右的厂家的还原炉采用的是8对电极和12对电极,8对电极还原炉每生产1公斤多晶硅实际耗电100度左右,12对电极还原炉(大部分为德国进口)每生产1公斤多晶硅实际耗电在80~90度,采用24对电极还原炉的厂家较少,如洛阳中硅高科有限责任公司、江西赛维LDK太阳能高科技有限公司,采用18对电极还原炉目前了解到的仅武汉东立光伏有限公司,计划在2010年底投产。
3、多晶硅还原炉电极数量及炉子大小的选择
实践证明,在选择了合适的配比和在最佳的还原温度下,进入还原炉的体积越大,则多晶硅沉积的速度越快,生产率也就越高,采用大流量的气体进入还原炉,是一种提高生产能力的有效方法,根据这种原理,如果采用大的还原设备,并适当增加发热载体(即电极)的数量,是可提高多晶硅生产率的,基于这一原理并结合国内多晶硅还原炉的现状,我们决定开发24对电极多晶硅还原炉,以适应和满足多晶硅行业的发展。
4、24对多晶硅还原炉的开发
4.1技术参数的确定
1)设计压力
还原炉内:-0.1Mpa~0.66Mpa,夹套内:0.75Mpa,炉底:0.65Mpa
2)操作压力
还原炉内:0.6Mpa,夹套内:0.6~0.75Mpa,炉底:0.6Mpa 3)设计温度
还原炉内筒体:320℃,夹套:150℃,炉底:180℃
4)操作温度
还原炉内筒体:300℃,夹套:145℃,炉底:150℃
5)介质
内筒体:H
2,SiHCL
3
,SiCL
4
,夹套:水,炉底:水
※原方案采用导热油冷却以便更好地利用余热热源,经调查采用导热油冷却因渗透性大会对炉内多晶硅产生污染,影响产品纯度和质量,还是选择用水冷却。
6)电极(发热体)数量
48根/台,长度2800mm,温度:1190℃~1120℃
4、2技术指标
1)每生产1公斤多晶硅还原电耗<75度
2)一个生产周期180小时,产量4800KG
3)单晶硅芯10mm,高2800mm,成品棒粗160mm左右
4、3材料及结构的确定
1)还原炉钟罩材料
内筒体:316L,夹套:Q345R
2)炉底材料
底板:316L,底座板Q345R
3)电极材料
无氧铜
4、4还原炉结构
还原炉结构见图
主要由炉体钟罩和炉底、电极及支座所组成,炉体钟罩和炉底之间用快开螺栓进行连接,炉底可直接支承在车间楼板上或用裙座进行支承。
为保证炉内维持最佳反应温度(1100℃)和降低炉体内筒体及炉底的壁温,炉体钟罩和炉底都设有水夹套冷却。
为了强化冷却效果,夹套内都设有螺旋导流板。
为观察炉内硅沉积情
况,炉体上安装有窥视孔。
为防止多晶硅附着在炉体内筒体壁面上,所有内表面应进行抛光处理。
还原炉筒体与炉底大垫片材料采用改性PTFE(聚四氟乙烯)。
电极材料采用无氧铜,电极棒与石墨底座结合部分(头部)进行镀银处理。
见电极组件图。
5、24对电极还原炉突出特点
5.1采用JB4732-95《钢制压力容器-分析设计标准》进行计算、设计,使结构趋于合理,用材经济适宜,降低设备造价。
5.2进气口布局合理:特别是进气口采用我公司专有产品螺旋流喷嘴喷入炉内,并对炉内流场和气体旋流方向以及进气速度进行模拟试验,确定最佳流场和气流方向及气流速度。
使炉内气体形成旋流湍动,消除了边界层和气体分布不均匀的现象,有利于还原反应的进行,提高了氢与三氯氢硅的转化率。
采用螺旋流喷嘴进气另一个优点是提高了多晶硅的表面质量,使多晶硅棒表面光滑,无起凸和凹坑现象(见多晶硅产品相片)。
5.3国内多晶硅还原炉电极棒长一般在2.2~2.5米左右,我们设计的电极棒长2.8米,即可在同样能源耗量下,可增产10%左右。
5.4 24对电极棒还原炉同8对电极棒和12对电极棒还原炉相比,每生产1公斤多晶硅分别节电20度和10度左右,充分显示了24对电极还原炉的节电幅度和降低多晶硅的生产成本及提高多晶硅产品利润率的效果。
6、相片
6.1多晶硅还原炉外形
6.2多晶硅还原炉炉底
6.3多晶硅还原炉车间布置
6.4多晶硅产品。