电镀工艺注意要点
电镀工艺注意要点

成品表面处理总结电镀分为蒸镀(真空电镀)和水电镀A.电镀1.电镀之定义电镀(electroplating)被定义为一种电沉积过程(electrodepos- ition process),就是利用电解的方式使金属附着于物体表面,以形成均匀、致密、结合力良好的金属层的。
简单的理解,是物理和化学的变化或结合。
其目的是在改变物体表面之特性或尺寸。
例如赋予产品以金属光泽而美观大方。
2.电镀之目的电镀的目的是在基材上镀上金属镀层(deposit),改变基材表面性质或尺寸。
例如赋予金属光泽美观、物品的防锈、防止磨耗、提高导电度、润滑性、强度、耐热性、耐候性、热处理之防止渗碳、氮化、尺寸错误或磨耗之另件之修补。
电镀原理3.电镀件的结构设计注意点:1) 基材最好采用电镀级ABS材料,ABS电镀后覆膜的附着力较好,同时价格也比较低廉。
2) 塑件表面质量一定要非常好,电镀无法掩盖注射的一些缺陷,而且通常会使得这些缺陷更明显。
3) 电镀件镀层厚度对配合尺寸的影响电镀件的厚度按照理想的条件会控制在0.02mm左右,但是在实际的生产中,可能最多会有0.08mm的厚度,所以在有滑动配合的位置上,单边的间隙要控制在0.3mm以上,才能达到满意的效果,这是我们对电镀件配合时需要作的关注。
4) 表面凸起最好控制在0.1~0.15mm/cm,尽量没有尖锐的边缘。
5) 如果有盲孔的设计,盲孔的深度最好不超过孔径的一半,负责不要对孔的底部的色泽作要求。
6) 要采用适合的壁厚防止变形,最好在1.5mm以上4mm以下,如果需要作的很薄的话,要在相应的位置作加强的结构来保证电镀的变形在可控的范围内。
7) 在设计中要考虑到电镀件变形,由于电镀的工作条件一般在60度~70度的温度范围下,在吊挂的条件下,结构不合理,变形的产生难以避免,所以在塑件的设计中对水口的位置要作关注,同时要有合适的吊挂的位置,防止在吊挂时对有要求的表面带来伤害。
另外最好不要在塑件中有金属嵌件存在,由于两者的膨胀系数不同,在温度升高时,电镀液体会渗到缝隙中,对塑件结构造成一定的影响。
电镀注意事项(大处理)

电镀注意事项
一、装冷冻机(未装前以冰块暂用)
温度控制25~30℃
二、阳极锌板
①锁紧,经常查看消耗后有否松动;
②清洗表面,以钢刷除去氧化膜;
③面积缺时要适时补足更新(看表面积)。
三、镀液
①注意液位是否充足到位;
②至少半个月翻缸一次,除去底部残渣;
③阳极加装过滤阳极袋,阳极袋一周清洗一次;
④准备一槽予备槽液,以便逐槽大处理,3个月至半年必须大处理一次;
⑤每3天清洗一次过滤机滤布,增加一套过滤布备用轮换;
⑥每天做波美度、试片、PH例行检测;
⑦每天3次测温,温度不要超过30℃;
⑧霍尔槽以1.2A,5分钟看试片状况,以硫酸盐、硼酸之加入,把试片调到
更佳状况。
斜线区要均匀不发黑才是正常。
⑨防止异物污染镀液(如专用水瓢等…)
四、电流
①测试输出与输入是否相当,最好能做到分条之电流检测;
②注意电流、电压在正常生产下,数值有否异常;
③经常检查阳、阴极线路各接触部分,如松动、氧化、发热造成导电不良。
五、镀液大处理步骤
①取1~3ML/L双氧水加入充分搅拌30分钟;
②取1~3g/L锌粉,一边搅拌一边加入锌粉,充分搅拌30分钟;
③取3~5g/L活性碳(活性碳不用粉状,使用直径2mm左右粒状),先加入三
分之一量加入搅拌30分钟后,再加三分之一量加入搅拌30分钟,最后将余量全部加入充分搅拌60分钟;
④静止镀液4~6小时后翻缸过滤;
⑤取样做霍尔槽试片检测,追加之主盐成分(必要时加1~2ML/L微量添加剂)
——霍尔槽测试;
⑥电解1~2小时后试镀生产,电解电压开至0.5~1V。
电镀工序质量控制
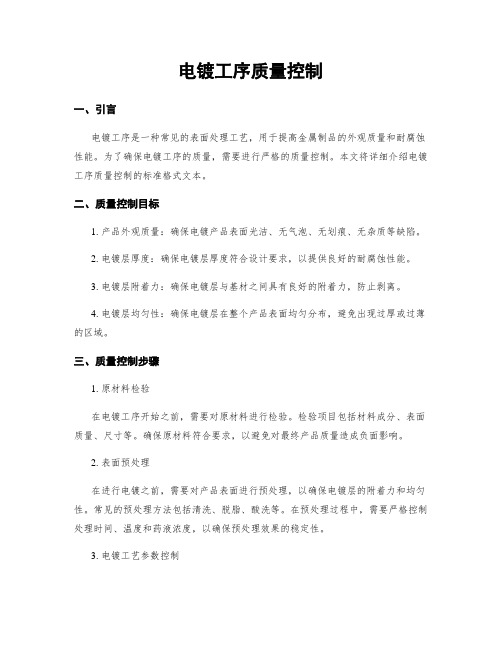
电镀工序质量控制一、引言电镀工序是一种常见的表面处理工艺,用于提高金属制品的外观质量和耐腐蚀性能。
为了确保电镀工序的质量,需要进行严格的质量控制。
本文将详细介绍电镀工序质量控制的标准格式文本。
二、质量控制目标1. 产品外观质量:确保电镀产品表面光洁、无气泡、无划痕、无杂质等缺陷。
2. 电镀层厚度:确保电镀层厚度符合设计要求,以提供良好的耐腐蚀性能。
3. 电镀层附着力:确保电镀层与基材之间具有良好的附着力,防止剥离。
4. 电镀层均匀性:确保电镀层在整个产品表面均匀分布,避免出现过厚或过薄的区域。
三、质量控制步骤1. 原材料检验在电镀工序开始之前,需要对原材料进行检验。
检验项目包括材料成分、表面质量、尺寸等。
确保原材料符合要求,以避免对最终产品质量造成负面影响。
2. 表面预处理在进行电镀之前,需要对产品表面进行预处理,以确保电镀层的附着力和均匀性。
常见的预处理方法包括清洗、脱脂、酸洗等。
在预处理过程中,需要严格控制处理时间、温度和药液浓度,以确保预处理效果的稳定性。
3. 电镀工艺参数控制电镀工艺参数对电镀层的质量有着重要影响。
在电镀过程中,需要控制以下参数:- 电镀液成分:包括金属盐类、添加剂等。
需要确保电镀液成分的稳定性和纯度。
- 电流密度:控制电流密度可以影响电镀层的厚度和均匀性。
需要根据产品要求进行合理的调整。
- 电镀时间:电镀时间决定了电镀层的厚度。
需要根据产品要求进行精确控制。
- 电镀温度:电镀温度对电镀层的质量有一定影响。
需要根据电镀液的要求进行合适的温度控制。
4. 质量检验在电镀工序完成后,需要对产品进行质量检验。
常见的检验项目包括外观检查、厚度测量、附着力测试等。
通过质量检验,可以确保产品符合要求,并及时发现和解决质量问题。
五、质量控制记录为了追溯和总结电镀工序的质量控制情况,需要进行质量控制记录。
记录内容包括原材料检验记录、预处理参数记录、电镀工艺参数记录、质量检验记录等。
通过记录,可以及时发现和解决质量问题,并为后续工序的改进提供参考依据。
电镀工序质量控制

电镀工序质量控制一、引言电镀工序是一种常见的表面处理工艺,用于改善金属制品的外观和性能。
为了确保电镀工序的质量,需要进行严格的质量控制。
本文将详细介绍电镀工序质量控制的标准格式文本。
二、工艺流程电镀工序的质量控制需要从工艺流程的各个环节入手,确保每个环节的操作符合标准要求。
1. 前处理前处理包括清洗、脱脂、酸洗等环节。
在清洗环节,应使用适当的清洗剂,确保金属表面干净无油污。
在脱脂环节,应使用合适的脱脂剂,去除金属表面的油脂。
在酸洗环节,应选择适当的酸洗液,去除金属表面的氧化物和杂质。
2. 镀液配制镀液的配制需要严格按照配方进行,确保镀液的成分和比例准确无误。
在配制过程中,应注意安全操作,避免镀液的误配或污染。
3. 电镀操作电镀操作是电镀工序的核心环节,需要控制电流密度、镀液温度、镀液搅拌速度等参数。
在电镀操作过程中,应定期检测电流密度、镀液温度等参数,确保其稳定在合理范围内。
4. 后处理后处理包括洗涤、中和、干燥等环节。
在洗涤环节,应使用纯净水彻底清洗掉残留的镀液。
在中和环节,应使用适当的中和剂,中和残留的酸碱物质。
在干燥环节,应使用适当的设备,确保金属制品干燥无水痕。
三、质量控制措施为了确保电镀工序的质量,需要采取一系列的质量控制措施。
1. 检测设备应配备适当的检测设备,包括电流密度计、温度计、PH计等,用于监测电镀工序中的关键参数。
这些设备应定期校准,确保其准确度和稳定性。
2. 检测方法应建立合适的检测方法,用于检测电镀工序的关键指标。
例如,可以使用电子显微镜检测镀层的厚度和均匀性,使用化学分析方法检测镀液中的成分和浓度等。
这些检测方法应经过验证,确保其准确可靠。
3. 技术标准应建立详细的技术标准,规定电镀工序中各个环节的操作要求和质量要求。
这些技术标准应与相关行业标准或国家标准相一致,并经过实践验证。
4. 人员培训应对从事电镀工序的操作人员进行培训,使其熟悉工艺流程、掌握操作要点和质量控制方法。
电镀工艺金属字施工注意事项

电镀工艺金属字施工注意事项
嘿!今天咱们来聊聊电镀工艺金属字施工的那些注意事项呀!这可太重要啦!
首先呢,在施工前一定要做好充分的准备工作哇!你得把施工场地打扫干净呀,可不能有灰尘和杂物啥的捣乱呢!还有材料的选择,哎呀呀,这可不能马虎!一定要选质量好的金属材料和电镀液呀,不然施工出来的效果可就大打折扣啦!
施工过程中呢,温度和时间的控制那是相当关键呀!温度太高或者太低,时间太长或者太短,都会出问题的哟!比如说温度过高,金属字可能会变形呢!时间不够,电镀层可能就不均匀啦!这可咋办?所以得时刻盯着,小心谨慎呐!
还有啊,操作手法也很重要呢!工人师傅们的手艺得精湛呀,每一个步骤都要做到位哇!涂抹电镀液的时候要均匀,不能这儿多那儿少的,不然出来的效果能好看吗?
施工环境也不能忽视哟!通风要好,不然那些化学气味可不好受呢!而且湿度也得注意,太潮湿了可不行呀!
另外,安全问题更是重中之重啊!施工人员得戴好防护装备,保护好自己呀!这可不是闹着玩的,万一出点啥意外,那可不得了哇!
施工完成后,还得仔细检查一遍哟!看看有没有瑕疵,有没有漏镀的地方呀!有问题及时处理,可别等到客户发现了才着急哟!
总之哇,电镀工艺金属字施工可不是一件简单的事儿,每个环节都得小心再小心,注意再注意呢!只有这样,才能做出让人满意的金
属字呀!。
电镀过程中注意事项

电镀过程中注意事项
在电镀过程中,需要注意以下事项:
1.安全防护:电镀液通常会含有有害的化学物质,因此必须佩戴适当的防护装备,如手套、护目镜和防护服,以防止物质对皮肤和眼睛的伤害。
2.通风换气:电镀液会产生有害气体,必须在通风良好的环境下操作,以避免吸入有毒气体对身体的损害。
3.正确操作:根据镀层材料和工艺要求,按照正确的操作步骤进行电镀。
必须严格控制电流、电压和镀液温度,以确保良好的镀层质量。
4.清洁工作区域:电镀过程中会产生一些废液和废料,必须及时清理,以防止堆积和相互污染。
5.避免交叉污染:不同材料的电镀需分别进行,以防止交叉污染产生不良的化学反应和镀层质量。
6.严谨的测量和记录:必须准确测量电流、电压和镀液温度等参数,并记录下来,以方便后续调整和品质控制。
7.保养和维护:定期清洁和保养电镀设备,及时更换耗损的电极和滤网,以保持设备和镀液的良好工作状态。
请注意,在进行电镀工艺时,最好寻求专业技术人员的指导和协助,以确保操作的安全性和结果的质量。
电镀工序质量控制
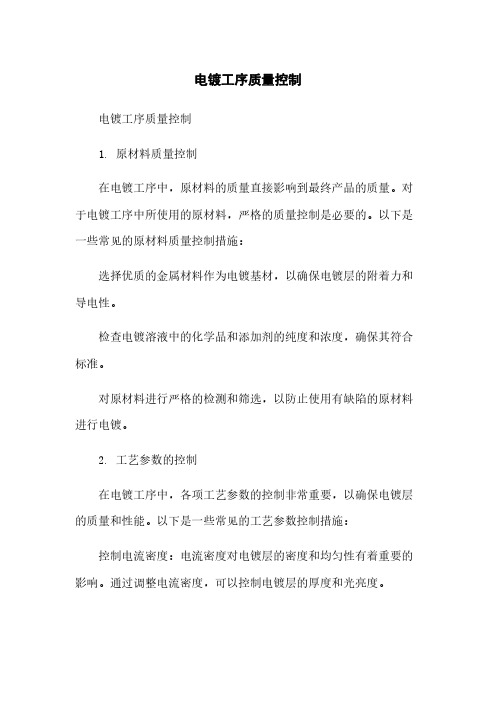
电镀工序质量控制电镀工序质量控制1. 原材料质量控制在电镀工序中,原材料的质量直接影响到最终产品的质量。
对于电镀工序中所使用的原材料,严格的质量控制是必要的。
以下是一些常见的原材料质量控制措施:选择优质的金属材料作为电镀基材,以确保电镀层的附着力和导电性。
检查电镀溶液中的化学品和添加剂的纯度和浓度,确保其符合标准。
对原材料进行严格的检测和筛选,以防止使用有缺陷的原材料进行电镀。
2. 工艺参数的控制在电镀工序中,各项工艺参数的控制非常重要,以确保电镀层的质量和性能。
以下是一些常见的工艺参数控制措施:控制电流密度:电流密度对电镀层的密度和均匀性有着重要的影响。
通过调整电流密度,可以控制电镀层的厚度和光亮度。
控制电镀时间:电镀时间对电镀层的厚度和光亮度也有重要影响。
根据产品要求,控制电镀时间可以确保电镀层的质量。
控制溶液温度:溶液温度对电镀层的结晶性和光亮度有影响。
通过控制溶液温度,可以调整电镀层的性能。
3. 检测和检验方法在电镀工序中,检测和检验是保证质量的重要环节。
以下是一些常见的检测和检验方法:外观检查:通过目视检查产品的外观,检查是否存在气泡、凹陷、划痕等缺陷。
厚度测量:使用合适的测量工具测量电镀层的厚度,以确保其符合产品要求。
附着力测试:通过进行剥离或划槽测试,评估电镀层与基材的附着力。
导电性测试:使用导电度计测试电镀层的导电性能,以确保其满足要求。
4. 持续改进和培训电镀工序的质量控制是一个不断改进的过程。
定期进行质量分析和评估,找出存在的问题,并采取相应的改进措施。
为工作人员提供培训和技能提升,以提高他们的质量意识和操作技能,也是保证电镀质量的重要环节。
在电镀工序中,质量控制是非常重要的。
通过对原材料质量的控制,调整工艺参数,使用合适的检测和检验方法,以及进行持续改进和培训,可以确保电镀产品的质量和性能。
只有通过科学的质量控制措施,才能生产出高质量的电镀产品。
电镀工序质量控制

电镀工序质量控制电镀是一种将金属表面覆盖上一层金属或合金的工艺,常用于改变金属表面的物理、化学性质,以增加其耐腐蚀性、改善导电性、提高外观等。
电镀工序中的质量控制对于保证电镀产品的质量和性能至关重要。
本文将对电镀工序质量控制的关键点进行详细介绍。
一、电镀工序质量控制的基本要求电镀工序质量控制的基本要求包括以下几个方面:(1)工艺参数的控制:包括电流密度、镀液温度、镀时间等参数的控制,以保证电镀层的均匀性和致密性。
(2)化学成分的控制:需要对镀液中的成分进行监控,保持其在一定范围内的稳定,以确保电镀层的质量。
(3)表面处理的控制:包括除油、除锈、除杂等表面处理工艺的控制,以保证金属表面的干净度和光洁度,为电镀提供良好的基础。
(4)设备设施的控制:必须保证电镀设备的运行稳定,设施的完善和维护,确保工艺参数的准确控制。
(5)人员操作控制:对电镀工艺的熟悉程度和操作规程的合理执行对质量的控制也起着重要作用。
二、电镀工序质量控制的关键点1. 镀液的配制与稳定控制镀液是电镀工序中的重要组成部分,其质量直接影响电镀层的质量。
因此,正确配制和稳定控制镀液的化学成分和pH值是保证电镀质量的关键点。
配制镀液时需要根据镀液的性质和电镀材料的要求来确定成分的比例,并严格按照配方进行。
同时,稳定控制镀液中各种成分的浓度和pH值,通过定期监测和调整,保持其在合适的范围内,以保证电镀层的均匀性和致密性。
2. 表面处理工艺的控制表面处理是电镀工艺中的重要环节,其质量直接影响电镀层与基材间的结合力和电镀层的外观质量。
因此,在表面处理工艺中需要注意以下几点:(1)除油处理:要确保基材表面没有油脂、蜡质等污物的存在。
可以采用机械除油或溶剂清洗等方法进行除油处理,但需避免对基材表面造成损伤。
(2)除锈处理:要确保基材表面没有氧化膜、锈迹等杂质的存在。
可以采用机械除锈、酸洗等方法进行除锈处理,但需避免对基材表面造成损伤。
(3)除杂处理:要确保基材表面没有杂质、异物等的存在。
电镀工序质量控制要点
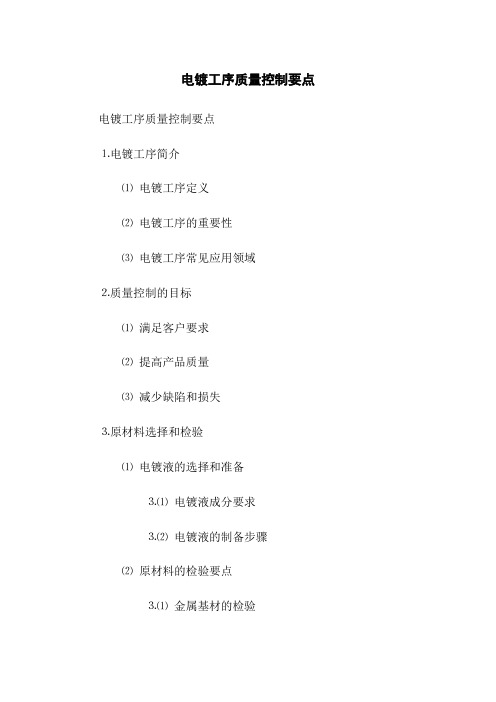
电镀工序质量控制要点电镀工序质量控制要点
⒈电镀工序简介
⑴电镀工序定义
⑵电镀工序的重要性
⑶电镀工序常见应用领域
⒉质量控制的目标
⑴满足客户要求
⑵提高产品质量
⑶减少缺陷和损失
⒊原材料选择和检验
⑴电镀液的选择和准备
⒊⑴电镀液成分要求
⒊⑵电镀液的制备步骤
⑵原材料的检验要点
⒊⑴金属基材的检验
⒊⑵化学试剂的检验
⒋设备和工艺参数控制
⑴电镀槽的选择和清洁
⑵工艺参数的控制
⒋⑴温度控制
⒋⑵酸碱度控制
⒋⑶电流密度控制
⒋⑷时间控制
⒌工艺操作规范
⑴操作人员培训和持证上岗
⑵作业指导书制定和更新
⑶工艺操作步骤
⒌⑴预处理步骤
⒌⑵电镀步骤
⒌⑶后处理步骤
⒍质量检验和控制
⑴检验设备和方法
⒍⑴厚度测量
⒍⑵膜性能检测
⒍⑶外观检查
⑵检测频率和抽样要求
⑶缺陷分析和处理
⒎废物处理和环境保护
⑴废水处理
⒎⑴废水收集和分离
⒎⑵废水净化处理
⑵废液处理
⒎⑴废液收集和分离
⒎⑵废液处理方法
⒏记录和文档管理
⑴生产记录的填写和保留
⑵异常处理和纠正措施的记录
⑶文档的管理和归档
附件:
⒈电镀工序操作指导书
⒉电镀液验收记录表
⒊检验设备操作手册
法律名词及注释:
⒈《环境保护法》- 中国法律,用于管理和保护环境资源,促进可持续发展。
⒉《质量管理体系认证准则》- ISO 9001标准,用于指导企业建立和落实质量管理体系,确保产品质量符合要求。
⒊《废物管理条例》- 中国法律,用于规范废物处理和管理,保护环境和人类健康。
2024年电镀工序质量控制(三篇)
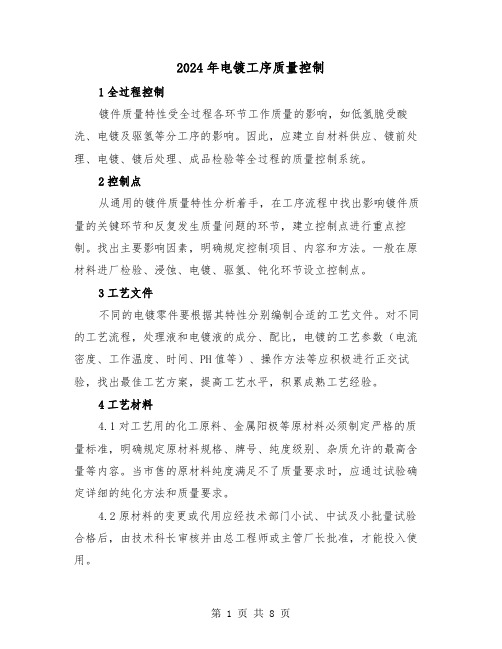
2024年电镀工序质量控制1全过程控制镀件质量特性受全过程各环节工作质量的影响,如低氢脆受酸洗、电镀及驱氢等分工序的影响。
因此,应建立自材料供应、镀前处理、电镀、镀后处理、成品检验等全过程的质量控制系统。
2控制点从通用的镀件质量特性分析着手,在工序流程中找出影响镀件质量的关键环节和反复发生质量问题的环节,建立控制点进行重点控制。
找出主要影响因素,明确规定控制项目、内容和方法。
一般在原材料进厂检验、浸蚀、电镀、驱氢、钝化环节设立控制点。
3工艺文件不同的电镀零件要根据其特性分别编制合适的工艺文件。
对不同的工艺流程,处理液和电镀液的成分、配比,电镀的工艺参数(电流密度、工作温度、时间、PH值等)、操作方法等应积极进行正交试验,找出最佳工艺方案,提高工艺水平,积累成熟工艺经验。
4工艺材料4.1对工艺用的化工原料、金属阳极等原材料必须制定严格的质量标准,明确规定原材料规格、牌号、纯度级别、杂质允许的最高含量等内容。
当市售的原材料纯度满足不了质量要求时,应通过试验确定详细的纯化方法和质量要求。
4.2原材料的变更或代用应经技术部门小试、中试及小批量试验合格后,由技术科长审核并由总工程师或主管厂长批准,才能投入使用。
4.3采购进厂的原材料都要经过严格的质量证明文件的验收和取样分析检验,验收合格才能入库。
4.4应根据原材料性质分别保管,不同规格、不同纯度的原材料不能混放。
易燃、易爆的化工原料要由专门的管理制度和隔离存放制度,存放库应有合乎要求的通风散热条件,并备有相应的消防措施。
电镀中使用的剧毒品要存放专门的剧毒品库,一定要双人双锁制管理,其中一人为厂保卫部门的分管人员,应建立严格的入库、保管、领料制度。
5镀前处理5.1待镀零件应按镀覆前的技术要求进行验收,不符合要求的应予拒收。
5.2为减小由于机械加工、研磨、成型、冷矫正等工序产生的残余应力,防止电镀时开裂,抗拉强度大于或等于1034Mpa的黑色金属零件,镀前必须进行消除应力热处理,处理温度必须低于该种材料的回火温度(一般至少低于回火温度30?C),但不能低于消除应力的温度。
电镀车间注意事项(三篇)
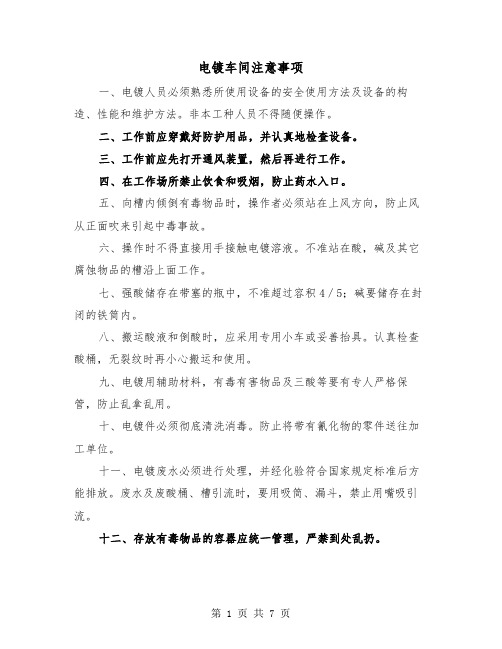
电镀车间注意事项一、电镀人员必须熟悉所使用设备的安全使用方法及设备的构造、性能和维护方法。
非本工种人员不得随便操作。
二、工作前应穿戴好防护用品,并认真地检查设备。
三、工作前应先打开通风装置,然后再进行工作。
四、在工作场所禁止饮食和吸烟,防止药水入口。
五、向槽内倾倒有毒物品时,操作者必须站在上风方向,防止风从正面吹来引起中毒事故。
六、操作时不得直接用手接触电镀溶液。
不准站在酸,碱及其它腐蚀物品的槽沿上面工作。
七、强酸储存在带塞的瓶中,不准超过容积4/5;碱要储存在封闭的铁筒内。
八、搬运酸液和倒酸时,应采用专用小车或妥善抬具。
认真检查酸桶,无裂纹时再小心搬运和使用。
九、电镀用辅助材料,有毒有害物品及三酸等要有专人严格保管,防止乱拿乱用。
十、电镀件必须彻底清洗消毒。
防止将带有氰化物的零件送往加工单位。
十一、电镀废水必须进行处理,并经化验符合国家规定标准后方能排放。
废水及废酸桶、槽引流时,要用吸筒、漏斗,禁止用嘴吸引流。
十二、存放有毒物品的容器应统一管理,严禁到处乱扔。
十三、氰化镀槽的操作人员,下班时应用消毒液对手、脸各部进行消毒。
未经消毒处理的个人防护用品不准带到其它场所。
十四、工作完后,要切断电源气源,盖好镀槽,关闭风机,做好清洁,将工件堆放整齐。
十五、电镀生产中碱性溶液应用较多,如化学除油、电解除油、氧化及有色金属精密件去氧化等。
碱液对人的皮肤和衣服有较强的黏附性及腐蚀性,腐蚀时有灼热的感觉。
在生产中使用碱溶液时,应掌握如下的安全操作知识。
1、操作温度(除氧化溶液外)一般不宜超过80℃,以免碱液蒸汽雾粒外逸,影响操作环境和伤害工人的皮肤和衣服。
2、操作时,工件进出溶液的速度应缓慢,严防碱液溅出伤害人体。
3、氧化,发黑溶液升温时,用铁棍将其表面硬壳破碎,防止内压作用溅出的碱液伤人。
4、碱液粘在皮肤或衣服时,应立即用水冲洗干净。
皮肤可用2%左右的醋酸或2%的硼酸溶液中和清洗干净,待皮肤干燥后涂以甘油、医用凡士林、羊毛脂或橄榄油等。
做电镀细节需注意
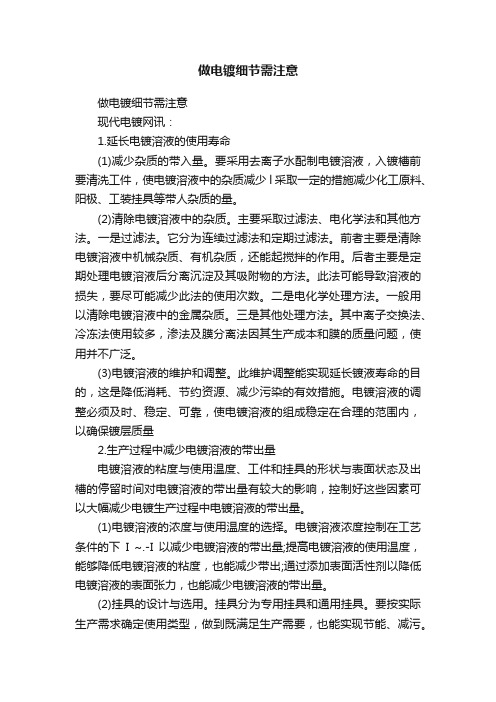
做电镀细节需注意做电镀细节需注意现代电镀网讯:1.延长电镀溶液的使用寿命(1)减少杂质的带入量。
要采用去离子水配制电镀溶液,入镀槽前要清洗工件,使电镀溶液中的杂质减少l采取一定的措施减少化工原料、阳极、工装挂具等带人杂质的量。
(2)清除电镀溶液中的杂质。
主要采取过滤法、电化学法和其他方法。
一是过滤法。
它分为连续过滤法和定期过滤法。
前者主要是清除电镀溶液中机械杂质、有机杂质,还能起搅拌的作用。
后者主要是定期处理电镀溶液后分离沉淀及其吸附物的方法。
此法可能导致溶液的损失,要尽可能减少此法的使用次数。
二是电化学处理方法。
一般用以清除电镀溶液中的金属杂质。
三是其他处理方法。
其中离子交换法、冷冻法使用较多,渗法及膜分离法因其生产成本和膜的质量问题,使用并不广泛。
(3)电镀溶液的维护和调整。
此维护调整能实现延长镀液寿命的目的,这是降低消耗、节约资源、减少污染的有效措施。
电镀溶液的调整必须及时、稳定、可靠,使电镀溶液的组成稳定在合理的范围内,以确保镀层质量2.生产过程中减少电镀溶液的带出量电镀溶液的粘度与使用温度、工件和挂具的形状与表面状态及出槽的停留时间对电镀溶液的带出量有较大的影响,控制好这些因素可以大幅减少电镀生产过程中电镀溶液的带出量。
(1)电镀溶液的浓度与使用温度的选择。
电镀溶液浓度控制在工艺条件的下I ~.-I以减少电镀溶液的带出量;提高电镀溶液的使用温度,能够降低电镀溶液的粘度,也能减少带出;通过添加表面活性剂以降低电镀溶液的表面张力,也能减少电镀溶液的带出量。
(2)挂具的设计与选用。
挂具分为专用挂具和通用挂具。
要按实际生产需求确定使用类型,做到既满足生产需要,也能实现节能、减污。
同时,挂具的表面耍尽可能光滑,无毛刺、桔皮等缺陷。
(3)出槽停留时间的控制。
适当延长工件出槽后在空中的停留时间可以有效减少电镀溶液的带出量。
3.工件的清洗要采用清洗效率高、清洗水量少和可回收利用工件带出液的清洗方法。
电镀工艺的设计,应采用低浓度电镀溶液,并要采取有效措施减少电镀溶液的带出量。
电镀工作心得
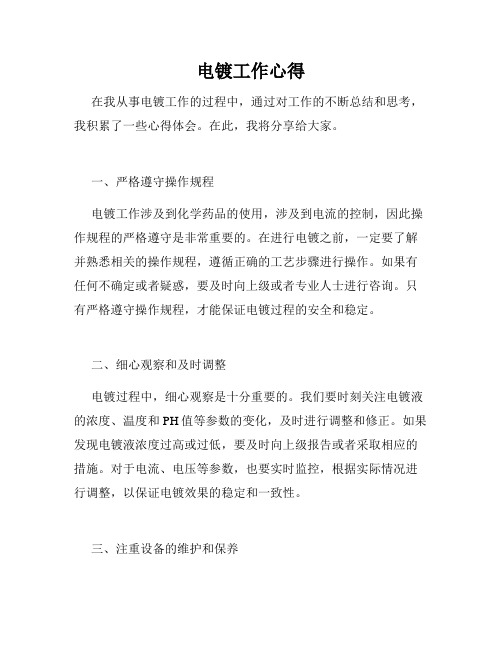
电镀工作心得在我从事电镀工作的过程中,通过对工作的不断总结和思考,我积累了一些心得体会。
在此,我将分享给大家。
一、严格遵守操作规程电镀工作涉及到化学药品的使用,涉及到电流的控制,因此操作规程的严格遵守是非常重要的。
在进行电镀之前,一定要了解并熟悉相关的操作规程,遵循正确的工艺步骤进行操作。
如果有任何不确定或者疑惑,要及时向上级或者专业人士进行咨询。
只有严格遵守操作规程,才能保证电镀过程的安全和稳定。
二、细心观察和及时调整电镀过程中,细心观察是十分重要的。
我们要时刻关注电镀液的浓度、温度和PH值等参数的变化,及时进行调整和修正。
如果发现电镀液浓度过高或过低,要及时向上级报告或者采取相应的措施。
对于电流、电压等参数,也要实时监控,根据实际情况进行调整,以保证电镀效果的稳定和一致性。
三、注重设备的维护和保养电镀工作涉及到各种设备的使用,因此设备的维护和保养是非常重要的。
首先要保持设备的清洁,定期进行设备的检查和维修,以确保设备的正常运转。
同时,还要定期更换电镀液,清洗电极和槽体等,杜绝电镀液污染和杂质的产生。
只有保持设备的良好状态,才能提高电镀的效率和质量。
四、加强团队协作在电镀工作中,团队的协作是非常重要的。
要加强与同事之间的交流与合作,相互之间要互相支持和帮助。
特别是在处理一些复杂或者特殊情况时,要积极向同事请教和寻求帮助,共同解决问题。
只有建立良好的团队合作氛围,才能更好地完成工作任务。
五、持续学习和提升电镀工作是一个不断学习和提升的过程。
我们要保持学习的热情,积极参加培训和学习机会,了解最新的电镀技术和工艺。
同时,我们还要与同行业的专家和同行进行交流和合作,互相学习和促进。
只有不断提升自己的专业水平,才能在电镀工作中不断进步。
六、安全第一电镀工作涉及到化学品和电流的使用,安全是最重要的。
我们要时刻保持警惕,遵循操作规程,正确佩戴个人防护装备。
在使用化学品时,要注意防护措施,避免火灾和化学品泄漏等事故的发生。
电镀过程中的注意事项
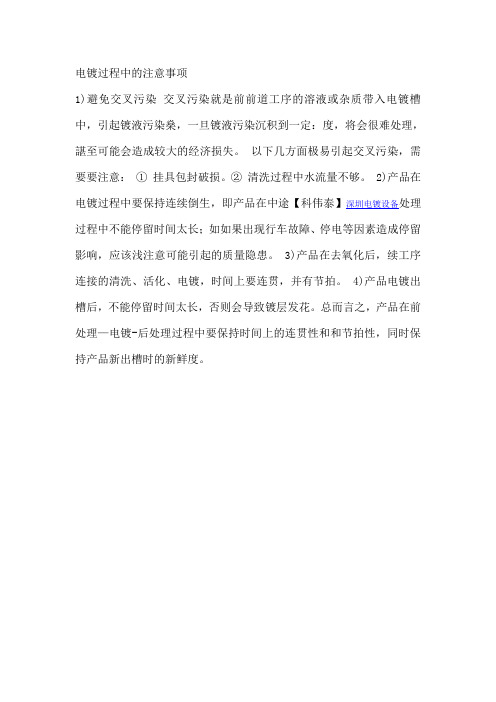
电镀过程中的注意事项
1)避免交叉污染交叉污染就是前前道工序的溶液或杂质带入电镀槽中,引起镀液污染燊,一旦镀液污染沉积到一定:度,将会很难处理,諶至可能会造成较大的经济损失。
以下几方面极易引起交叉污染,需要要注意:① 挂具包封破损。
② 清洗过程中水流量不够。
2)产品在电镀过程中要保持连续倒生,即产品在中途【科伟泰】深圳电镀设备处理过程中不能停留时间太长;如如果出现行车故障、停电等因素造成停留影响,应该浅注意可能引起的质量隐患。
3)产品在去氧化后,续工序连接的清洗、活化、电镀,时间上要连贯,并有节拍。
4)产品电镀出槽后,不能停留时间太长,否则会导致镀层发花。
总而言之,产品在前处理—电镀-后处理过程中要保持时间上的连贯性和和节拍性,同时保持产品新出槽时的新鲜度。
电镀工序质量控制要点
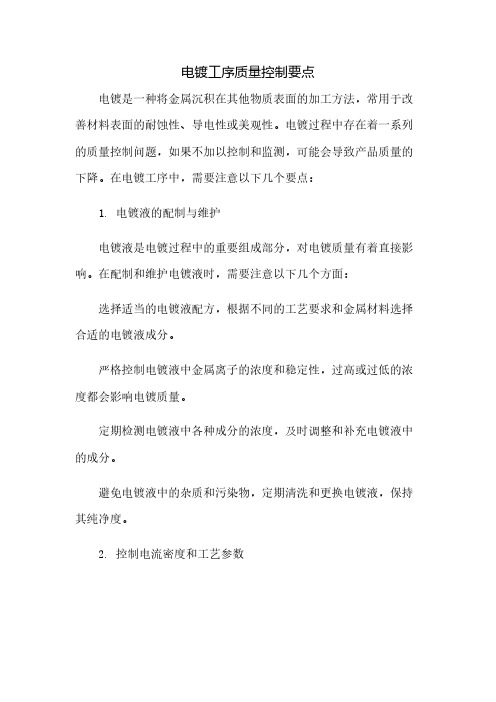
电镀工序质量控制要点电镀是一种将金属沉积在其他物质表面的加工方法,常用于改善材料表面的耐蚀性、导电性或美观性。
电镀过程中存在着一系列的质量控制问题,如果不加以控制和监测,可能会导致产品质量的下降。
在电镀工序中,需要注意以下几个要点:1. 电镀液的配制与维护电镀液是电镀过程中的重要组成部分,对电镀质量有着直接影响。
在配制和维护电镀液时,需要注意以下几个方面:选择适当的电镀液配方,根据不同的工艺要求和金属材料选择合适的电镀液成分。
严格控制电镀液中金属离子的浓度和稳定性,过高或过低的浓度都会影响电镀质量。
定期检测电镀液中各种成分的浓度,及时调整和补充电镀液中的成分。
避免电镀液中的杂质和污染物,定期清洗和更换电镀液,保持其纯净度。
2. 控制电流密度和工艺参数电镀质量很大程度上取决于电流密度和工艺参数的控制。
合理的电流密度可以提高电镀层的均匀性和致密性,在工艺过程中需要注意以下几个方面:确定适当的电流密度范围,避免过高或过低的电流密度对电镀层质量的影响。
控制电镀时间,避免电镀时间过长导致电镀层过厚或过多产生杂质。
控制电极与工件之间的距离和角度,保证电流的均匀分布和工件表面的一致性电镀。
3. 监测和控制电镀层的厚度及均匀性电镀层的厚度和均匀性是衡量电镀质量的重要指标,在电镀过程中需要进行监测和控制,包括以下几个方面:使用合适的测量仪器,如表面粗糙度仪、电子显微镜等,对电镀层的厚度进行测量和分析。
定期检查电镀层的均匀性,避免出现过度电镀或不足电镀的情况。
针对不同的工件形状和面积,采取不同的电镀工艺和参数,保证电镀层的均匀性和一致性。
4. 质量检验与记录质量检验是电镀过程中的关键环节,通过严格的质量检验可以及时发现和纠正质量问题,确保产品质量的稳定。
在质量检验中需要注意以下几个方面:发展合适的质量检验方法,包括外观检查、厚度测量、粗糙度测试、耐蚀性评估等。
建立详细的质量记录,包括每个工件的电镀工艺参数、检验结果、不合格品的处理等信息。
关于电镀产品生产过程注意事项
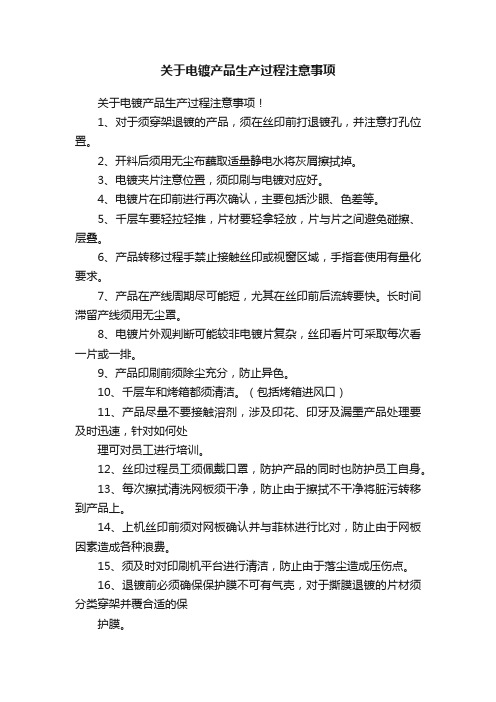
关于电镀产品生产过程注意事项关于电镀产品生产过程注意事项!1、对于须穿架退镀的产品,须在丝印前打退镀孔,并注意打孔位置。
2、开料后须用无尘布蘸取适量静电水将灰屑擦拭掉。
3、电镀夹片注意位置,须印刷与电镀对应好。
4、电镀片在印前进行再次确认,主要包括沙眼、色差等。
5、千层车要轻拉轻推,片材要轻拿轻放,片与片之间避免碰擦、层叠。
6、产品转移过程手禁止接触丝印或视窗区域,手指套使用有量化要求。
7、产品在产线周期尽可能短,尤其在丝印前后流转要快。
长时间滞留产线须用无尘罩。
8、电镀片外观判断可能较非电镀片复杂,丝印看片可采取每次看一片或一排。
9、产品印刷前须除尘充分,防止异色。
10、千层车和烤箱都须清洁。
(包括烤箱进风口)11、产品尽量不要接触溶剂,涉及印花、印牙及漏墨产品处理要及时迅速,针对如何处理可对员工进行培训。
12、丝印过程员工须佩戴口罩,防护产品的同时也防护员工自身。
13、每次擦拭清洗网板须干净,防止由于擦拭不干净将脏污转移到产品上。
14、上机丝印前须对网板确认并与菲林进行比对,防止由于网板因素造成各种浪费。
15、须及时对印刷机平台进行清洁,防止由于落尘造成压伤点。
16、退镀前必须确保保护膜不可有气壳,对于撕膜退镀的片材须分类穿架并覆合适的保护膜。
17、退镀烘烤必须充分,不可残留水分。
18、退镀后打定位孔,打孔前须覆膜。
19、更换网版须做好标记区分。
20、对于印刷尺寸管控可定量比对菲林等。
21、丝印、电镀注意正反面。
22、清洗架须固定好。
23、现场5S保障等。
23 物料流转以及烘烤前须进行再次确认。
电镀处理中的电镀操作技巧

电镀处理中的电镀操作技巧电镀操作是一项对于金属表面工艺处理非常重要的步骤,通过对金属表面进行镀层处理,能够增强金属的耐腐蚀、抗磨损、导电、导热等特性,同时也可以起到美观、装饰、防腐等作用。
但是,电镀操作技术也是非常复杂的,需要考虑到多个因素的影响,常见的问题如镀层质量不佳、脱落、变色、回弹、氢脆等问题也给电镀生产造成了不少的困扰。
因此,下面将会从以下几个方面分析电镀操作技巧,以期能够帮助大家更好地进行电镀处理。
一、处理前的准备工作1. 镀件清洗:在电镀处理之前,必须对被镀件进行充分的清洗处理,以使被镀件表面没有污物和油污,保证金属表面能够被电镀涂层充分的吸附。
其中,清洗液的选择需要考虑到清洗的表面材料、性质、硬度等因素,常见的清洗液有酸、碱、碱性电解液、有机溶剂、酒精、丙酮等。
对于大型和重量较大的被镀件,需要使用洗车机或高压水枪进行清洗处理。
2. 镀件处理:在进行电镀处理之前,还需要对被镀件进行一些表面处理,以便于金属板材表面附着性更好。
其中,处理方法可以包括:磨光、抛光、喷砂、喷丸、沙光明处理等。
3. 原辅材料的质控:电镀处理的质量主要取决于原辅材料的质量,所以在进行电镀处理前,一定要对原辅材料进行质控,并对不合格的原材料及时淘汰。
二、电镀过程中的技巧1. 电镀液的选择:根据被镀件的材质和性质等因素,选择合适的电镀液进行电镀处理。
通常来说,电镀液可以分为镀铬、镀镍、镀铜、镀金等多个种类。
2. 正确的电镀参数设置:电镀参数的设置非常重要,对于电镀涂层质量具有直接的影响。
主要参数包括电压、电流密度、电镀时间、温度等。
在设置电镀参数时,可以采取试镀的方式进行,以保证电镀过程中参数的准确性和正确性。
3. 电极摆放:在电镀液中,电镀液的流速、流向、电极间距等参数都能影响到电镀涂层的质量,所以在进行电镀处理时,需要注意对电极的摆放,以保证电镀涂层的质量。
4. 镀件的搭接和避孔处理:在进行电镀涂层处理时,需要注意搭接和避孔处理,以防止暴露的部分出现氢脆和缩孔等现象。
电镀工序质量控制要点
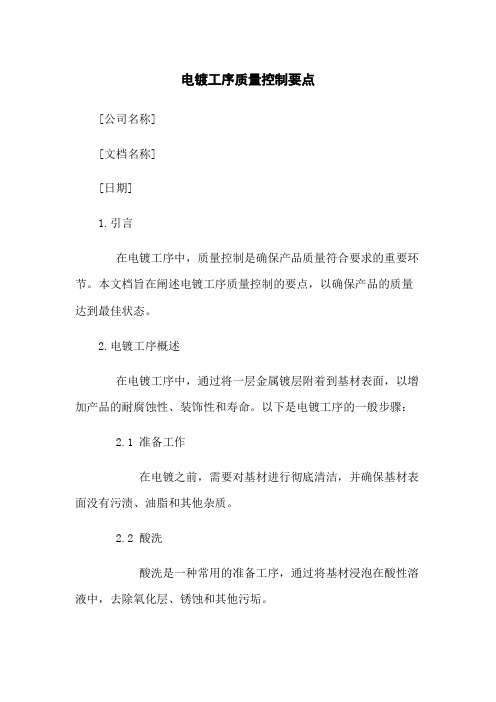
电镀工序质量控制要点[公司名称][文档名称][日期]1.引言在电镀工序中,质量控制是确保产品质量符合要求的重要环节。
本文档旨在阐述电镀工序质量控制的要点,以确保产品的质量达到最佳状态。
2.电镀工序概述在电镀工序中,通过将一层金属镀层附着到基材表面,以增加产品的耐腐蚀性、装饰性和寿命。
以下是电镀工序的一般步骤:2.1 准备工作在电镀之前,需要对基材进行彻底清洁,并确保基材表面没有污渍、油脂和其他杂质。
2.2 酸洗酸洗是一种常用的准备工序,通过将基材浸泡在酸性溶液中,去除氧化层、锈蚀和其他污垢。
2.3 电镀在完成准备工作和酸洗后,基材将被浸入包含金属离子的电解液中,利用电化学反应在基材表面形成金属镀层。
2.4 后处理在电镀完成后,产品需要经过清洗、干燥和其他后处理步骤,以确保镀层的质量和外观符合要求。
3.质量控制要点为确保电镀工序的质量,以下是需要注意的关键要点:3.1 原料选用选择高质量的电镀液、酸洗液以及清洗剂等原料,以确保电镀工序的稳定性和可靠性。
3.2 工艺参数控制控制电镀液中的温度、PH值、电流密度等工艺参数,确保电镀反应正常进行,并避免出现不良的镀层现象。
3.3 设备维护定期检查和维护电镀设备,确保设备的正常运行,避免设备故障对产品质量造成影响。
3.4 检测方法使用适当的检测方法,如厚度测量、粗糙度测量、附着力测试等,对电镀层进行检测,以确保产品的质量满足要求。
3.5 记录和分析对每一批次的电镀产品进行记录,并进行质量分析,以检查是否存在潜在的问题,并采取相应的纠正措施。
4.附件在本文档中,附件提供了进一步的信息和辅助材料,以帮助理解和实施电镀工序质量控制。
附件:- 电镀液成分表- 酸洗工艺流程图- 后处理工艺参数表5.法律名词及注释在本文档中,涉及的法律名词及其注释如下:- 电镀工序:根据相关法律法规的规定,对金属产品进行表面处理,以增加其耐腐蚀性、装饰性等特性的工序。
- 酸洗工艺:通过在酸性溶液中对金属基材进行浸泡和处理,去除氧化层、锈蚀和其他污垢的工艺。
电镀之相关注意事项(精)

電鍍之相關注意事項
1.素材射出后,為避免素材粘附模具之防銹油或射出時噴灑之離型
劑,故建議要超音波震蕩清洗或以甲苯等溶劑擦拭,以便去除油污,避免底涂覆著不良。
2.若底涂采用烘箱熱烘式,建議時間為170℃下2小時,適用一般尼
龍加玻纖(或礦粉)之底漆,例如祥元MB-100等,烘干後之厚度約為20-30μ。
3.若底漆采用UV灯照射式,底漆喷涂後,建议先进烘箱烘烤100℃
下8分钟,用以挥发底漆内之溶剂,再以UV灯照射,使用底漆有日本藤倉VB-7654等,烘干後之厚度约为20-30μ。
4.目前之客户,其面漆皆采用真空铝蒸著电镀(将铝加热後汽化,
均匀附著於欲电镀品之表面),电镀完成後之厚度约为5-8μ。
电镀操作规程
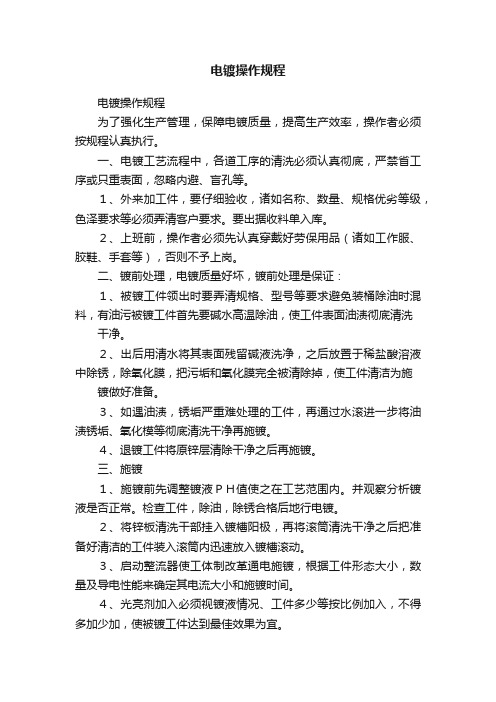
电镀操作规程电镀操作规程为了强化生产管理,保障电镀质量,提高生产效率,操作者必须按规程认真执行。
一、电镀工艺流程中,各道工序的清洗必须认真彻底,严禁省工序或只重表面,忽略内避、盲孔等。
1、外来加工件,要仔细验收,诸如名称、数量、规格优劣等级,色泽要求等必须弄清客户要求。
要出据收料单入库。
2、上班前,操作者必须先认真穿戴好劳保用品(诸如工作服、胶鞋、手套等),否则不予上岗。
二、镀前处理,电镀质量好坏,镀前处理是保证:1、被镀工件领出时要弄清规格、型号等要求避免装桶除油时混料,有油污被镀工件首先要碱水高温除油,使工件表面油渍彻底清洗干净。
2、出后用清水将其表面残留碱液洗净,之后放置于稀盐酸溶液中除锈,除氧化膜,把污垢和氧化膜完全被清除掉,使工件清洁为施镀做好准备。
3、如遇油渍,锈垢严重难处理的工件,再通过水滚进一步将油渍锈垢、氧化模等彻底清洗干净再施镀。
4、退镀工件将原锌层清除干净之后再施镀。
三、施镀1、施镀前先调整镀液PH值使之在工艺范围内。
并观察分析镀液是否正常。
检查工件,除油,除锈合格后地行电镀。
2、将锌板清洗干部挂入镀槽阳极,再将滚筒清洗干净之后把准备好清洁的工件装入滚筒内迅速放入镀槽滚动。
3、启动整流器使工体制改革通电施镀,根据工件形态大小,数量及导电性能来确定其电流大小和施镀时间。
4、光亮剂加入必须视镀液情况、工件多少等按比例加入,不得多加少加,使被镀工件达到最佳效果为宜。
5、电镀电流根据工件类型、大小而定,以工件边角、边缘我有气泡产生为宜,对难镀工件如有盲孔或形态复杂件,不能采取中电冲击,先镀内再镀外部烧焦部分的方法。
6、锌板入槽前必须将上面干结附着物用钢刷清除干净后加阳极套入槽。
极棒上铜缘要用布蕉盐酸擦去,酸液不能流入镀液中,不能用镀液清洗,以免铜杂质进入溶液。
7、镀完后及时将锌板取出,掉入槽内物件及时打捞起来。
四、镀后钝化1、钝化是关键所在,首先检查工件镀后亮度情况,是否平整,有无烧焦,如有问题拒绝出亮钝化。
- 1、下载文档前请自行甄别文档内容的完整性,平台不提供额外的编辑、内容补充、找答案等附加服务。
- 2、"仅部分预览"的文档,不可在线预览部分如存在完整性等问题,可反馈申请退款(可完整预览的文档不适用该条件!)。
- 3、如文档侵犯您的权益,请联系客服反馈,我们会尽快为您处理(人工客服工作时间:9:00-18:30)。
成品表面处理总结电镀分为蒸镀(真空电镀)和水电镀A.电镀1.电镀之定义电镀(electroplating)被定义为一种电沉积过程(electrodepos- ition process),就是利用电解的方式使金属附着于物体表面,以形成均匀、致密、结合力良好的金属层的。
简单的理解,是物理和化学的变化或结合。
其目的是在改变物体表面之特性或尺寸。
例如赋予产品以金属光泽而美观大方。
2.电镀之目的电镀的目的是在基材上镀上金属镀层(deposit),改变基材表面性质或尺寸。
例如赋予金属光泽美观、物品的防锈、防止磨耗、提高导电度、润滑性、强度、耐热性、耐候性、热处理之防止渗碳、氮化、尺寸错误或磨耗之另件之修补。
电镀原理3.电镀件的结构设计注意点:1) 基材最好采用电镀级ABS材料,ABS电镀后覆膜的附着力较好,同时价格也比较低廉。
2) 塑件表面质量一定要非常好,电镀无法掩盖注射的一些缺陷,而且通常会使得这些缺陷更明显。
3) 电镀件镀层厚度对配合尺寸的影响电镀件的厚度按照理想的条件会控制在0.02mm左右,但是在实际的生产中,可能最多会有0.08mm的厚度,所以在有滑动配合的位置上,单边的间隙要控制在0.3mm以上,才能达到满意的效果,这是我们对电镀件配合时需要作的关注。
4) 表面凸起最好控制在0.1~0.15mm/cm,尽量没有尖锐的边缘。
5) 如果有盲孔的设计,盲孔的深度最好不超过孔径的一半,负责不要对孔的底部的色泽作要求。
6) 要采用适合的壁厚防止变形,最好在1.5mm以上4mm以下,如果需要作的很薄的话,要在相应的位置作加强的结构来保证电镀的变形在可控的范围内。
7) 在设计中要考虑到电镀件变形,由于电镀的工作条件一般在60度~70度的温度范围下,在吊挂的条件下,结构不合理,变形的产生难以避免,所以在塑件的设计中对水口的位置要作关注,同时要有合适的吊挂的位置,防止在吊挂时对有要求的表面带来伤害。
另外最好不要在塑件中有金属嵌件存在,由于两者的膨胀系数不同,在温度升高时,电镀液体会渗到缝隙中,对塑件结构造成一定的影响。
8) 要避免采用大面的平面。
塑料件在电镀之后反光率提高,平面上的凹坑、局部的轻微凹凸不平都变得很敏感,最终影响产品效果。
这种零件可采用略带弧形的造型。
9) 要避免直角和尖角。
初做造型和结构的设计人员往往设计出棱角的造型。
但是,这样的棱角部位很容易产生应力集中而影响镀层的结合力。
而且,这样的部位会造成结瘤现象。
因此,方形的轮廓尽量改为曲线形轮廓,或用圆角过渡。
造型上一定要要求方的地方,也要在一切角和棱的地方倒圆角R=0.2~0.3 mm。
10) 不要有过深的凹部,不要有小孔和盲孔,这些部位不仅电镀困难,而且容易残存溶液污染下道工序的溶液。
像旋钮和按钮不可避免的盲孔,应从中间留缝。
11) 要考虑留有时装挂的结点部位.结点部位要放在不显眼的位置。
可以用挂钩、槽、缝和凸台等位置作接点。
12) 厚度不应太薄,也不要有突变。
太薄的零件在电镀过程中受热或受镀层应力的影响容易变形.厚度的突变容易造成应力集中,一般来说厚度差不应超过两倍。
13) 标记和符号要采用流畅的字体,如:圆体、琥珀、彩云等。
因多棱多角不适于电镀。
流畅的字体容易成形、电镀后外观好。
文字凸起的高度以0.3~0.5为宜,斜度65度。
14) 如果能够采用皮纹、滚花等装饰效果要尽量采用,因为降低电镀件的反光率有助于掩盖可能产生的外观缺陷。
15) 尽量不要采用螺纹和金属嵌件,以免电镀时为保护螺纹、嵌件而增加工序。
1.局部电镀要求的实现在我们的设计中常常要求在塑件表面的不同部位实现不同的效果。
我们通常采用以下四个方法来实现这种效果:1).拆成小件。
不同的效果部位分别做成一个小零件,最后装配在一起。
在形状不太复杂并且组件有批量的条件下的情况下,开一套小的模具注射的费用会形成比较明显的价格优势,2).加绝缘油墨。
如果是在不影响外观的局部要求不电镀,通常可以采用加绝缘油墨后进行电镀的方法进行加工,这样喷涂了绝缘油墨的部位就会没有金属覆膜,达到要求。
其实这是我们在设计中常常涉及到的一个部分,因为电镀后的制件会变硬变脆,是我们不希望得到的结果,所以尤其在按键这类的制件上它的拐臂是我们不希望被电镀上的部分,因为我们需要它有充分的弹性,局部电镀在这个时候就非常必要。
在另外的情况下也常用到,类似于PDA这类的轻巧的制品,一般电路板直接固定在塑胶壳体上,为了防止对电路的影响,通常在同电路有接触的部分均进行绝缘处理,这时多采用油墨的方式来进行电镀前对局部的处理。
3).类似双色注塑的工艺。
一般如果有双色注射机,可以将ABS和PC分不同的阶段注射,制成塑件后进行电镀处理,在这样的条件下,由于两种塑胶对电镀液的不同附着力导致ABS的部分有电镀的效果而PC的部分没有电镀的效果,达到要求。
4). 二次注射。
就是将制件分成两个部分,首先将一个部分进行注射后进行电镀处理,将处理后的制品再装入另外一套模具中进行二次注射得到最终的样品。
5.混合电镀效果对设计的要求我们在设计中常常采用高光电镀和蚀纹电镀的效果共同作用在一个制品上得到特殊的设计效果,通常在设计中建议采用较小的蚀纹,这样效果会比较好,但这样的设计时,为了不会使蚀纹的效果被电镀所掩盖,有时会电镀两层后就不进行电镀,这样的后果是电镀第二层的镍会比较容易氧化变色,影响设计的效果。
电镀效果介绍1.高光电镀高光电镀的效果的实现通常要求模具表面良好抛光,注射出的塑件采用光铬处理后得到的效果。
2.亚光电镀亚光电镀的效果的实现通常要求模具表面良好抛光,注射出的塑件采用亚铬处理后得到的效果。
2.珍珠铬珍珠铬电镀的效果的实现通常要求模具表面良好抛光,注射出的塑件采用珍珠铬处理后得到的效果。
4.蚀纹电镀蚀纹电镀的效果的实现通常要求模具表面处理出不同效果的蚀纹方式后,注射出的塑件采用光铬处理后得到的效果。
5.局部电镀通过采用不同的方式使得成品件的表面局部没有电镀的效果,与有电镀的部分形成反差,形成独特的设计风格。
6.彩色电镀通过采用不同的电镀溶液,在电镀后塑件表面沉积的金属会反射出不同的光泽,形成独特的效果。
1.金属表面处理1.1铁和钢概述由于铁金属表面处理的方法非常多,特性也不甚相同。
一般厂内设备之零件,依需求状况选择适当之表面处理。
例如一般机架施以喷漆处理,螺栓螺帽以染黑处理,固定机板或底座以镀镍处理,滑动轨道或滑动杆可依所需强度施以镀铬或镀硬铬处理,露光台之Lamp house则以氮化处理。
各种表面处理的不同点如下表格:铁金属热处理:一表面硬化热处理:由于铁金属热处理的方法非常多,特性也不甚相同滑动面用耐磨耗材料硬度使用实例:二表面电镀处理电镀是表面处理很普遍被采用的方式,为耐蚀、耐磨或装饰等用途,在金属或非金属表面上,利用电气沉积金属的表面技术。
三钢铁化学镍处理钢铁化学镍处理亦称为无电镀镍处理,适合广泛用以取代传统`的电镀镍处理,运用在各种铁金属表面之防锈、防蚀处理,并且能增加被处理物表面的美观,提高价值感。
钢铁化学镍处理的原理乃利用溶液化学还原反应而在金属表面生成一镀膜。
其主要其主要特点为:处理后之金属的表面平滑,耐蚀、耐磨且复杂形状的被处理物,亦可得到均匀的镀层膜。
硬度达HRC51以上,热处理可达硬度HRC70,予以取代镀硬铬。
膜厚可要求在5µ至数条内。
附着力佳,且可镀在铁、钢、铜、铝、ABS胶或陶瓷上。
磨擦系数仅为0.03﹝为硬铬的1/3,与铸铁相同﹞。
成本高昂,溶液寿命短。
与电镀镍比较之优缺点如下:优点:皮膜孔隙少且厚度均匀,厚度较薄但比较硬,可以用在非导材料。
缺点:沉积速度慢,含有磷硼化合物,融点较低且较脆。
1.2铝和铝合金概述铝常用的表面处理方法:1. 抛光:克服缺陷去毛刺和使表面光亮的作用。
2.喷砂:喷砂的目的是用来克服和掩盖铝合金在机械加工过程中产生的一些缺陷以及满足客户对产品外观的一些特殊要求。
有玻璃砂、钨砂等,呈现不同感觉。
类似毛玻璃的粗燥质感,细的砂型同样可以表现出高档的产品。
3.电镀:比较常见,同时有打磨后电镀的处理工艺见第4章电镀(见200页电镀)4.车纹。
是模具成型后再次加工的处理方式,使用车床加工出纹路。
成体表现为非常规则的纹理特征。
5.擦纹。
有叫做拉丝。
表现相似于车纹,都是表面形成流畅的连续纹路,不同的是,车纹表现为环状纹路,擦纹表现为直线6.批花。
我们经常看到有些金属铭牌,上面的产品或者公司标示有倾斜或者直体丝状条纹,此为批花工艺7.批边。
类似抛光、电镀效果,但是加工方式不同,效果不同。
加工方式为机械加工,呈现极亮的光芒效果8.氧化(上色):氧化的用途分两方面:增强物理特性;可以达到上色目的。
9.钻石切割一拉丝拉丝可根据装饰需要,制成直纹、乱纹、螺纹、波纹和旋纹等几种。
直纹拉丝是指在铝板表面用机械磨擦的方法加工出直线纹路。
它具有刷除铝板表面划痕和装饰铝板表面的双重作用。
直纹拉丝有连续丝纹和断续丝纹两种。
连续丝纹可用百洁布或不锈钢刷通过对铝板表面进行连续水平直线磨擦(如在有靠现装置的条件下手工技磨或用刨床夹住钢丝刷在铝板上磨刷)获取。
改变不锈钢刷的钢丝直径,可获得不同粗细的纹路。
断续丝纹一般在刷光机或擦纹机上加工制得。
制取原理:采用两组同向旋转的差动轮,上组为快速旋转的磨辊,下组为慢速转动的胶辊,铝或铝合金板从两组辊轮中经过,被刷出细腻的断续直纹。
乱纹拉丝是在高速运转的铜丝刷下,使铝板前后左右移动磨擦所获得的一种无规则、无明显纹路的亚光丝纹。
这种加工,对铝或铝合金板的表面要求较高。
波纹一般在刷光机或擦纹机上制取。
利用上组磨辊的轴向运动,在铝或铝合金板表面磨刷,得出波浪式纹路。
旋纹也称旋光,是采用圆柱状毛毡或研石尼龙轮装在钻床上,用煤油调和抛光油膏,对铝或铝合金板表面进行旋转抛磨所获取的一种丝纹。
它多用于圆形标牌和小型装饰性表盘的装饰性加工。
螺纹是用一台在轴上装有圆形毛毡的小电机,将其固定在桌面上,与桌子边沿成60度左右的角度,另外做一个装有固定铝板压茶的拖板,在拖板上贴一条边沿齐直的聚酯薄膜用来限制螺纹宽度。
利用毛毡的旋转与拖板的直线移动,在铝板表面旋擦出宽度一致的螺纹纹路。
二喷砂A.喷砂(Sand Blasting)处理喷砂(Sand Blasting)处理在金属表面的应用是非常普遍的。
目的是用来克服和掩盖铝合金在机械加工过程中产生的一些缺陷以及满足客户对产品外观的一些特殊要求。
原理只是将加速的磨料颗粒向金属表面撞击,而达至除金秀、去毛刺、去氧化层或作表面预处理等,它能改变金属表面的光洁度和应力状态。
常用的砂材有玻璃砂、金刚砂、钢珠、碳化硅等喷砂工艺的好处喷砂工艺可分为气压喷枪及叶轮抛丸两种,而喷砂工艺的优点在于它能够除披峰、去除在压铸、冲压、火焰切割和锻压后的毛刺,对较薄工件及有毛孔的毛刺效果更好,它可清理砂铸过程残余的砂粒、清理铸铁件或钢材的锈渍、清理热处理、烧悍、热锻、辗压等热工序后的除氧化皮。