间歇反应釜
间歇反应釜的工作原理

间歇反应釜的工作原理
间歇反应釜是一种常见的化工设备,它主要用于进行高温高压的化学反应。
其工作原理是通过加热和加压的方式,使反应物在一定时间内进行化学反应,然后通过减压和冷却的方式,将反应产物分离出来。
间歇反应釜的主要组成部分包括釜体、加热器、冷却器、搅拌器、压力传感器、温度传感器等。
在进行化学反应时,首先将反应物加入到釜体中,然后通过加热器加热,使反应物达到所需的温度。
同时,通过压力传感器控制釜体内的压力,使其达到所需的反应压力。
在反应过程中,搅拌器不断搅拌反应物,使其充分混合,促进反应的进行。
当反应时间到达设定值时,通过减压阀将釜体内的压力降低,使反应产物从釜体中流出。
此时,通过冷却器将反应产物冷却,使其凝固成固体或液体,然后进行分离和提取。
间歇反应釜的工作原理简单明了,但在实际应用中需要注意一些问题。
首先,反应物的加入量和反应时间需要根据具体的反应条件进行调整,以保证反应的充分进行。
其次,釜体内的压力和温度需要严格控制,以避免反应失控或产生危险。
最后,反应产物的分离和提取需要进行精细的操作,以保证产物的纯度和质量。
间歇反应釜是一种重要的化工设备,其工作原理简单明了,但在实际应用中需要注意一些问题。
只有在严格控制反应条件和操作过程
的情况下,才能保证反应的成功和产物的质量。
间歇反应釜的工作原理
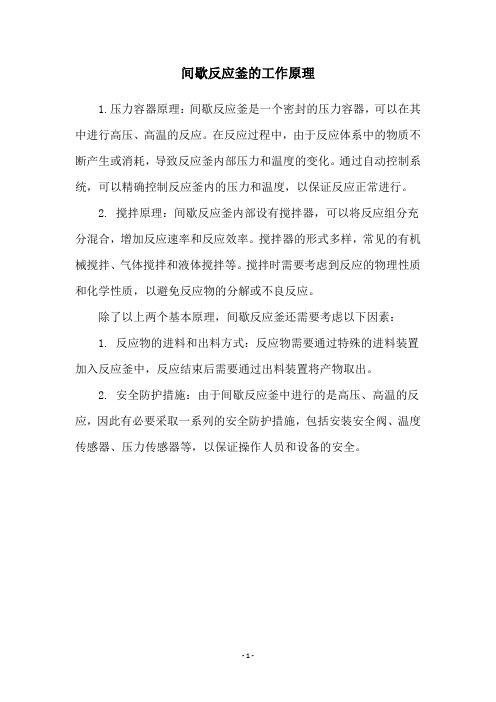
间歇反应釜的工作原理
1.压力容器原理:间歇反应釜是一个密封的压力容器,可以在其中进行高压、高温的反应。
在反应过程中,由于反应体系中的物质不断产生或消耗,导致反应釜内部压力和温度的变化。
通过自动控制系统,可以精确控制反应釜内的压力和温度,以保证反应正常进行。
2. 搅拌原理:间歇反应釜内部设有搅拌器,可以将反应组分充分混合,增加反应速率和反应效率。
搅拌器的形式多样,常见的有机械搅拌、气体搅拌和液体搅拌等。
搅拌时需要考虑到反应的物理性质和化学性质,以避免反应物的分解或不良反应。
除了以上两个基本原理,间歇反应釜还需要考虑以下因素:
1. 反应物的进料和出料方式:反应物需要通过特殊的进料装置加入反应釜中,反应结束后需要通过出料装置将产物取出。
2. 安全防护措施:由于间歇反应釜中进行的是高压、高温的反应,因此有必要采取一系列的安全防护措施,包括安装安全阀、温度传感器、压力传感器等,以保证操作人员和设备的安全。
- 1 -。
间歇反应釜操作实习报告
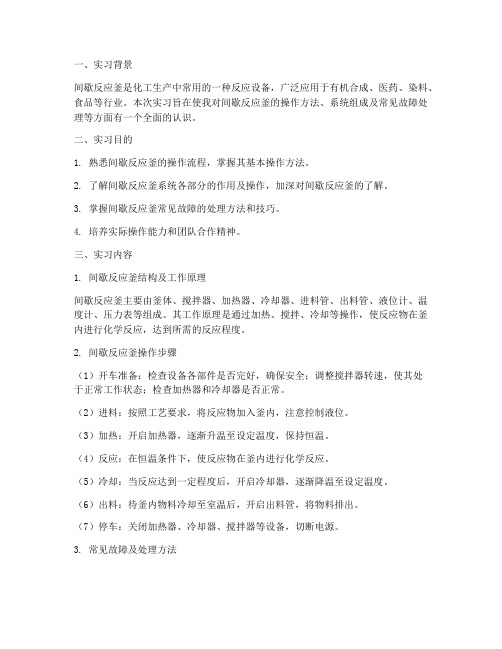
一、实习背景间歇反应釜是化工生产中常用的一种反应设备,广泛应用于有机合成、医药、染料、食品等行业。
本次实习旨在使我对间歇反应釜的操作方法、系统组成及常见故障处理等方面有一个全面的认识。
二、实习目的1. 熟悉间歇反应釜的操作流程,掌握其基本操作方法。
2. 了解间歇反应釜系统各部分的作用及操作,加深对间歇反应釜的了解。
3. 掌握间歇反应釜常见故障的处理方法和技巧。
4. 培养实际操作能力和团队合作精神。
三、实习内容1. 间歇反应釜结构及工作原理间歇反应釜主要由釜体、搅拌器、加热器、冷却器、进料管、出料管、液位计、温度计、压力表等组成。
其工作原理是通过加热、搅拌、冷却等操作,使反应物在釜内进行化学反应,达到所需的反应程度。
2. 间歇反应釜操作步骤(1)开车准备:检查设备各部件是否完好,确保安全;调整搅拌器转速,使其处于正常工作状态;检查加热器和冷却器是否正常。
(2)进料:按照工艺要求,将反应物加入釜内,注意控制液位。
(3)加热:开启加热器,逐渐升温至设定温度,保持恒温。
(4)反应:在恒温条件下,使反应物在釜内进行化学反应。
(5)冷却:当反应达到一定程度后,开启冷却器,逐渐降温至设定温度。
(6)出料:待釜内物料冷却至室温后,开启出料管,将物料排出。
(7)停车:关闭加热器、冷却器、搅拌器等设备,切断电源。
3. 常见故障及处理方法(1)液位异常:可能是液位计失灵或进料管堵塞。
处理方法:检查液位计,若失灵则更换;检查进料管,若堵塞则疏通。
(2)温度异常:可能是加热器或冷却器故障。
处理方法:检查加热器或冷却器,若故障则维修或更换。
(3)压力异常:可能是釜内反应剧烈或安全阀故障。
处理方法:降低反应速率或检查安全阀,若故障则维修或更换。
四、实习体会通过本次实习,我对间歇反应釜的操作方法、系统组成及常见故障处理等方面有了更深入的了解。
以下是我的一些体会:1. 间歇反应釜操作过程中,要严格按照工艺要求进行,确保反应效果。
反应器(反应釜)的结构和工作原理

反应器(反应釜)的结构和工作原理反应器是一种实现反应过程的设备,用于实现液相单相反应过程和液液、气液、液固、气液固等多相反应过程。
器内常设有搅拌(机械搅拌、气流搅拌等)装置。
在高径比较大时,可用多层搅拌桨叶。
在反应过程中物料需加热或冷却时,可在反应器壁处设置夹套,或在器内设置换热面,也可通过外循环进行换热。
第一部分:按操作方式分1、间歇釜式反应器或称间歇釜操作灵活,易于适应不同操作条件和产品品种,适用于小批量、多品种、反应时间较长的产品生产。
间歇釜的缺点是:需有装料和卸料等辅助操作,产品质量也不易稳定。
但有些反应过程,如一些发酵反应和聚合反应,实现连续生产尚有困难,至今还采用间歇釜。
间歇操作反应器系将原料按一定配比一次加入反应器,待反应达到一定要求后,一次卸出物料。
连续操作反应器系连续加入原料,连续排出反应产物。
当操作达到定态时,反应器内任何位置上物料的组成、温度等状态参数不随时间而变化。
半连续操作反应器也称为半间歇操作反应器,介于上述两者之间,通常是将一种反应物一次加入,然后连续加入另一种反应物。
反应达到一定要求后,停止操作并卸出物料。
间歇反应器的优点是设备简单,同一设备可用于生产多种产品,尤其适合于医药、染料等工业部门小批量、多品种的生产。
另外,间歇反应器中不存在物料的返混,对大多数反应有利。
缺点是需要装卸料、清洗等辅助工序,产品质量不易稳定。
2、连续釜式反应器,或称连续釜可避免间歇釜的缺点,但搅拌作用会造成釜内流体的返混。
在搅拌剧烈、液体粘度较低或平均停留时间较长的场合,釜内物料流型可视作全混流,反应釜相应地称作全混釜。
在要求转化率高或有串联副反应的场合,釜式反应器中的返混现象是不利因素。
此时可采用多釜串联反应器,以减小返混的不利影响,并可分釜控制反应条件。
大规模生产应尽可能采用连续反应器。
连续反应器的优点是产品质量稳定,易于操作控制。
其缺点是连续反应器中都存在程度不同的返混,这对大多数反应皆为不利因素,应通过反应器合理选型和结构设计加以抑制。
间歇反应釜的工作原理
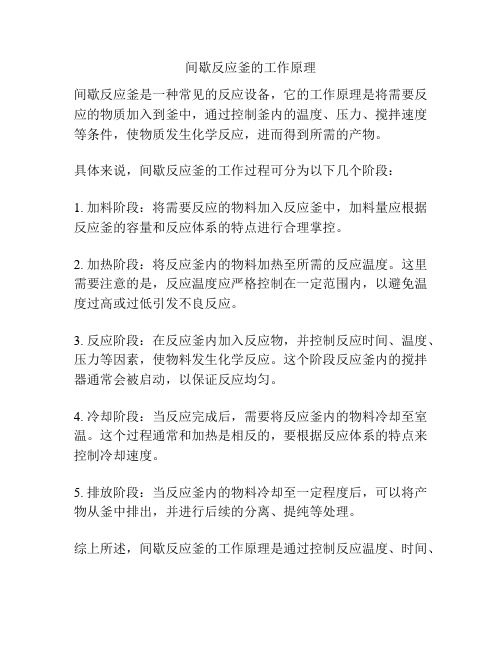
间歇反应釜的工作原理
间歇反应釜是一种常见的反应设备,它的工作原理是将需要反应的物质加入到釜中,通过控制釜内的温度、压力、搅拌速度等条件,使物质发生化学反应,进而得到所需的产物。
具体来说,间歇反应釜的工作过程可分为以下几个阶段:
1. 加料阶段:将需要反应的物料加入反应釜中,加料量应根据反应釜的容量和反应体系的特点进行合理掌控。
2. 加热阶段:将反应釜内的物料加热至所需的反应温度。
这里需要注意的是,反应温度应严格控制在一定范围内,以避免温度过高或过低引发不良反应。
3. 反应阶段:在反应釜内加入反应物,并控制反应时间、温度、压力等因素,使物料发生化学反应。
这个阶段反应釜内的搅拌器通常会被启动,以保证反应均匀。
4. 冷却阶段:当反应完成后,需要将反应釜内的物料冷却至室温。
这个过程通常和加热是相反的,要根据反应体系的特点来控制冷却速度。
5. 排放阶段:当反应釜内的物料冷却至一定程度后,可以将产物从釜中排出,并进行后续的分离、提纯等处理。
综上所述,间歇反应釜的工作原理是通过控制反应温度、时间、
压力、搅拌等条件,使物质发生化学反应,最终得到所需的产物。
化工仿真间歇反应釜课件

❖ 我们前面学习的离心泵、列管换热器、精馏 操作、吸收解吸仿真操作,他们共同的特点 是什么?
间歇反应釜的工业背景
❖ 思考: ❖ 化工生产过程与其他生产过程的本质区别是?
工业背景
❖ 化工生产过程与其他生产过程的本质区别是
有化学反应发生。 ❖ 化学反应过程是化工生产的核心。其所用设
备——反应器是化工生产中的关键性设备,
❖ 釜式反应器的特点:
釜式反应器在化工生产中具有较大的灵活性, 能进行多品种的生产,即适用于间歇操作过 程,又可单釜或多釜串联适用于连续操作过 程。它具有适用的温度和压力范围宽,操作 弹性大,连续操作时温度、浓度易控制,产 品质量均一等特点。但若应用在转化率要求 较高的场合时,则需要较大的容积。
间歇反应釜
❖ 特点:反应在一个密闭体系内进行,反应物料 和催化剂一次性加入,反应过程中与外界无 物质交换。
❖ 应用: 溶液体系,固液反应体系如:液相光 催化反应,常见的有机合成。
❖ 优点:快速,简单; ❖ 缺点:温度低,对液相体系通过搅拌可以保持
体系均匀和催化剂与反应物的良好接触,但 对气相反应不易做到。
间歇反应釜的结构
工序共有三种原料,多硫化钠(Na2Sn)、 邻硝基氯苯(C6H4ClNO2)及二硫化碳 (CS2)。
二硫化碳
邻硝基氯苯
多硫化钠
将中❖打 ( 反计 。将当来计开7应量待制沉中5自量搅完℃罐反在降备罐拌毕以V1应罐0料及X后上温5中0工沉,—)度1的序淀、利将1,升原1的罐V用产关高0料X二V加品闭至0℃静X硫2热压加90,置中0化1蒸出热让℃4、的碳汽反分。反,V原、将应钟X应逐料邻0,釜后持渐利2硝反!,、续打用基应通V进开重氯X物过行冷力0苯温离3。却输中、度心水送多升泵,至硫高输将间化至送最歇钠反至终翻分应反反应别温应应釜注度釜温入度控
第三章间歇釜式反应器知识讲解

数
需要设备的总容积为:
Q0t '
V
mVm
如果反应器容积V的计算值很大,可选用几个小的反应器
若以m表示反应釜的个数,
则每个釜的容积:Vm=V/m=Q0t’/( m)
为便于反应器的制造和选用,釜的规格由标准(GB 9845-88) 而定。在选择标准釜时,应注意使选择的容积与计算值相当或 略大。如果大,则实际生产能力较要求为大,富裕的生产能力 称为反应器的后备能力,可用后备系数δ来衡量后备能力的大
解: 每台锅每天操作批数: β=24/17=1.41 每天生产西维因农药数量:
1000×1000÷300=3330Kg(GD)
需要设备总容积: mVm=(3330/1.41)×200×10-3/12.5=37.8m3
取Va为10 m3的最大搪瓷锅4台。
δ=(4-3.78)/3.78×100%=5.82%
10
(3)反应体积VR
• 反应体积是指设备中物料所占体积,又称有效体积。
确定反应器的容积V的前提是确定反应器的有效容 积(反应容积)VR。
如果由生产任务确定的单位时间的物料处理量为Q0,
操作时间为t’(包括反应时间t和辅助操作时间t0 ),则
反应器的有效容积:
VR=Q0 t'
其中 t’ = t + t0
11
(4)*设备装料系数
实际生产中,反应器的容积要比有效容积大,以保 证液面上留有空间。
• 反应器有效体积与设备
实际容积之比称为设备
装料系数,以符号
表示,即:
=VR/V。其值视具体
情况而定
条
件
无搅拌或缓慢搅 拌的反应釜
带搅拌的反应釜
易起泡或沸腾状 况下的反应
间歇反应釜实训报告小结
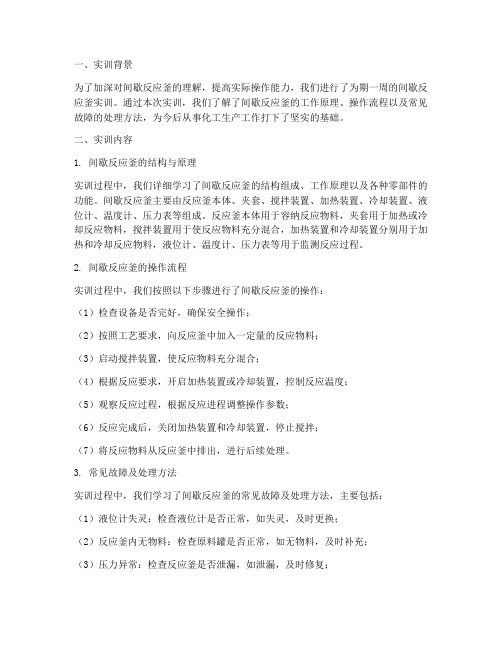
一、实训背景为了加深对间歇反应釜的理解,提高实际操作能力,我们进行了为期一周的间歇反应釜实训。
通过本次实训,我们了解了间歇反应釜的工作原理、操作流程以及常见故障的处理方法,为今后从事化工生产工作打下了坚实的基础。
二、实训内容1. 间歇反应釜的结构与原理实训过程中,我们详细学习了间歇反应釜的结构组成、工作原理以及各种零部件的功能。
间歇反应釜主要由反应釜本体、夹套、搅拌装置、加热装置、冷却装置、液位计、温度计、压力表等组成。
反应釜本体用于容纳反应物料,夹套用于加热或冷却反应物料,搅拌装置用于使反应物料充分混合,加热装置和冷却装置分别用于加热和冷却反应物料,液位计、温度计、压力表等用于监测反应过程。
2. 间歇反应釜的操作流程实训过程中,我们按照以下步骤进行了间歇反应釜的操作:(1)检查设备是否完好,确保安全操作;(2)按照工艺要求,向反应釜中加入一定量的反应物料;(3)启动搅拌装置,使反应物料充分混合;(4)根据反应要求,开启加热装置或冷却装置,控制反应温度;(5)观察反应过程,根据反应进程调整操作参数;(6)反应完成后,关闭加热装置和冷却装置,停止搅拌;(7)将反应物料从反应釜中排出,进行后续处理。
3. 常见故障及处理方法实训过程中,我们学习了间歇反应釜的常见故障及处理方法,主要包括:(1)液位计失灵:检查液位计是否正常,如失灵,及时更换;(2)反应釜内无物料:检查原料罐是否正常,如无物料,及时补充;(3)压力异常:检查反应釜是否泄漏,如泄漏,及时修复;(4)搅拌装置故障:检查搅拌装置是否正常,如故障,及时更换或维修。
三、实训心得体会1. 提高了实际操作能力:通过本次实训,我们掌握了间歇反应釜的操作流程,熟悉了各种操作参数的调整,为今后从事化工生产工作打下了坚实的基础。
2. 增强了安全意识:在实训过程中,我们深刻认识到安全操作的重要性,严格遵守操作规程,确保了实训过程的安全。
3. 培养了团队协作精神:实训过程中,我们学会了与他人沟通、协作,共同完成实验任务,提高了团队协作能力。
间歇反应釜单元工艺流程

间歇反应釜单元工艺流程英文回答:Intermittent reaction kettle is a common unit operation in chemical engineering. It is used for carrying out chemical reactions in a batch-wise manner. The process flow of an intermittent reaction kettle can be divided into several steps.1. Charging: The first step is to charge the reactants into the kettle. This can be done manually or using automated systems depending on the scale of the operation. The reactants are usually measured and added in the desired quantities.2. Mixing: Once the reactants are charged, the mixing process begins. The kettle is equipped with agitators or stirrers that ensure proper mixing of the reactants. The mixing time and speed can be adjusted based on the reaction requirements.3. Heating/Cooling: After the mixing is complete, the kettle is heated or cooled to the desired temperature. This step is crucial for initiating or controlling the reaction. Heating or cooling can be achieved using steam, hot water,or cooling water depending on the process requirements.4. Reaction: Once the desired temperature is reached, the reaction takes place. The reaction time can vary depending on the nature of the reaction and the desired product. During this step, the reaction progress is monitored using various analytical techniques.5. Product Separation: After the reaction is complete, the product needs to be separated from the reaction mixture. This can be done through various techniques such as filtration, distillation, crystallization, or centrifugation.6. Discharging: Once the product is separated, it is discharged from the kettle. This can be done manually or using automated systems. The product is then collected andfurther processed or stored as required.中文回答:间歇反应釜是化工工程中常见的单元操作。
间歇反应釜工艺流程
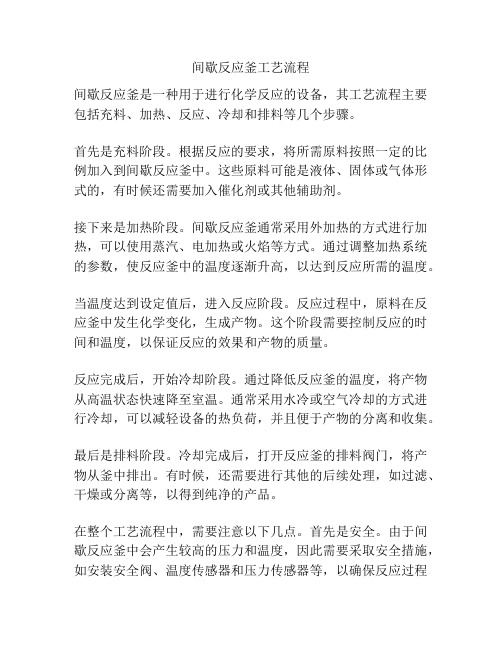
间歇反应釜工艺流程间歇反应釜是一种用于进行化学反应的设备,其工艺流程主要包括充料、加热、反应、冷却和排料等几个步骤。
首先是充料阶段。
根据反应的要求,将所需原料按照一定的比例加入到间歇反应釜中。
这些原料可能是液体、固体或气体形式的,有时候还需要加入催化剂或其他辅助剂。
接下来是加热阶段。
间歇反应釜通常采用外加热的方式进行加热,可以使用蒸汽、电加热或火焰等方式。
通过调整加热系统的参数,使反应釜中的温度逐渐升高,以达到反应所需的温度。
当温度达到设定值后,进入反应阶段。
反应过程中,原料在反应釜中发生化学变化,生成产物。
这个阶段需要控制反应的时间和温度,以保证反应的效果和产物的质量。
反应完成后,开始冷却阶段。
通过降低反应釜的温度,将产物从高温状态快速降至室温。
通常采用水冷或空气冷却的方式进行冷却,可以减轻设备的热负荷,并且便于产物的分离和收集。
最后是排料阶段。
冷却完成后,打开反应釜的排料阀门,将产物从釜中排出。
有时候,还需要进行其他的后续处理,如过滤、干燥或分离等,以得到纯净的产品。
在整个工艺流程中,需要注意以下几点。
首先是安全。
由于间歇反应釜中会产生较高的压力和温度,因此需要采取安全措施,如安装安全阀、温度传感器和压力传感器等,以确保反应过程的安全性。
其次是控制。
利用自动控制系统,通过监测、调节和控制温度、压力和流量等参数,保证反应的稳定性和可控性。
再次是操作。
操作人员需要熟悉设备的使用方法和操作流程,遵循操作规程,正确使用和维护设备,以确保反应过程的顺利进行。
总结起来,间歇反应釜工艺流程包括充料、加热、反应、冷却和排料等几个关键步骤。
在实际操作中,需要注意安全、控制和操作等方面的要求,以保证反应的顺利进行和产物的质量。
间歇反应釜实习报告
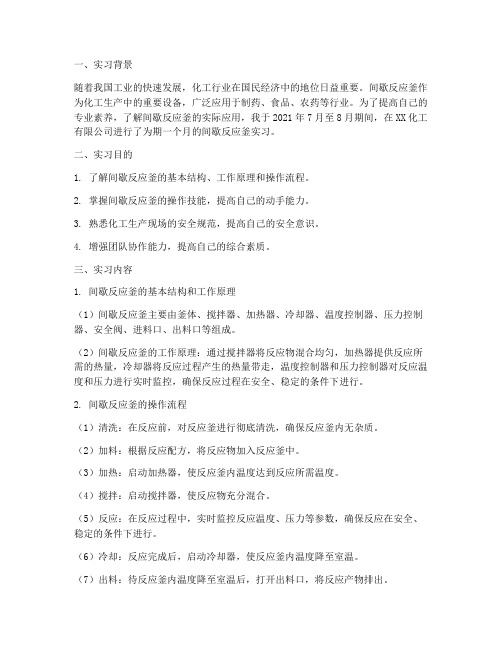
一、实习背景随着我国工业的快速发展,化工行业在国民经济中的地位日益重要。
间歇反应釜作为化工生产中的重要设备,广泛应用于制药、食品、农药等行业。
为了提高自己的专业素养,了解间歇反应釜的实际应用,我于2021年7月至8月期间,在XX化工有限公司进行了为期一个月的间歇反应釜实习。
二、实习目的1. 了解间歇反应釜的基本结构、工作原理和操作流程。
2. 掌握间歇反应釜的操作技能,提高自己的动手能力。
3. 熟悉化工生产现场的安全规范,提高自己的安全意识。
4. 增强团队协作能力,提高自己的综合素质。
三、实习内容1. 间歇反应釜的基本结构和工作原理(1)间歇反应釜主要由釜体、搅拌器、加热器、冷却器、温度控制器、压力控制器、安全阀、进料口、出料口等组成。
(2)间歇反应釜的工作原理:通过搅拌器将反应物混合均匀,加热器提供反应所需的热量,冷却器将反应过程产生的热量带走,温度控制器和压力控制器对反应温度和压力进行实时监控,确保反应过程在安全、稳定的条件下进行。
2. 间歇反应釜的操作流程(1)清洗:在反应前,对反应釜进行彻底清洗,确保反应釜内无杂质。
(2)加料:根据反应配方,将反应物加入反应釜中。
(3)加热:启动加热器,使反应釜内温度达到反应所需温度。
(4)搅拌:启动搅拌器,使反应物充分混合。
(5)反应:在反应过程中,实时监控反应温度、压力等参数,确保反应在安全、稳定的条件下进行。
(6)冷却:反应完成后,启动冷却器,使反应釜内温度降至室温。
(7)出料:待反应釜内温度降至室温后,打开出料口,将反应产物排出。
3. 安全规范(1)进入反应釜区域前,必须穿戴好个人防护用品,如安全帽、防护眼镜、防护手套等。
(2)操作过程中,严禁触摸高温、高压设备。
(3)遇到紧急情况,立即停止操作,并采取相应措施进行处理。
四、实习收获1. 通过实习,我对间歇反应釜的基本结构、工作原理和操作流程有了深入的了解。
2. 在实际操作过程中,提高了自己的动手能力,掌握了间歇反应釜的操作技能。
第三章间歇釜式反应器

使反应物混合均匀,强化传质传热
3.传热装置,主要是夹套和蛇管,用来
输入或移出热量,以保持适宜的反应 温度
4.传动装置,是使搅拌器获得动能以强
化液体流动。ຫໍສະໝຸດ 5.轴密封装置,用来防止釜体与搅拌 轴之间的泄漏
6.工艺接管,为适应工艺需要
2
3
3.1.2间歇釜式反应器的特点及其应用
• 操作周期又称工时定
额或操作时间,是指 • 例如萘磺化制取2-萘磺酸
生产每一批料的全部 的操作周期:
操作时间,即从准备 • 检查设备
投料到操作过程全部 完成所需的总时间t’ , 操 作 时 间 t’ 包 括 反 应
• •
加萘 加硫酸及升温
时 间 t 和 辅 助 操 作 时 • 反应
15分 15分
25分 160分
小,若标准釜的容积为Va,那么,
Va V 100 % Vma Vm 100 %
V
Vm
14
• 思考 • 选用个数少而容积大的设备有利还是选用
个数多而容积小的设备有利 ?
15
3、计算示例
物料处理量FV一般由生产任务确定,辅助时间t0视实 际操作情况而定,反应时间t可由动力学方程确定, 也可由实验得到。由以上数据可求VR、V、m、Vm以 及δ等
5
3.2.1间歇釜式反应器的容积与数量
确定反应器的容积与数量是车间设计的基础, 是实现化学反应工业放大的关键 1、求算反应器的容积与数量需要的基础数据
6
(1)每天处理物料总体积VD和单位时间的物
料处理量为FV
VD
=
GD
GD每天所需处理的物料总重量 ρ物料的密度
FV=VD/24
釜式反应器—理想间歇操作釜式反应器的计算

tr=3.18(h) tr=8.5(h) tr=19.0(h)
热量衡算:单位时间、整个体积、基准0℃ 进入反应器的物料带入的热量:0
非 离开反应器的物料带出的热量:0
恒 温
发生反应的热效应热量: (Hr )(rA )VRdt
过 程
反应器内的物料和外界交换的热量: KA(Tw T )
反应器内累积的热量: mt c pt dT
绝热操作:
(T
T0 )
(H r )nA0 mt c pt
(xA
xA0 )
简化: (T T0 ) (xA xA0 )
反应体积的计算
1.反应器的有效体积VR
VR V0 (t t)
V0 —— 每小时处理的物料体积,m3/h; t —— 达到要求的转化率所需要的反应时间,h; t′—— 辅助时间,h。
2. 反应器的体积V
V VR
m 若用多釜并联操作时,反应釜数: V
V
3. 反应釜结构尺寸:
V 0.785D 2 H
D —— 筒体的直径; H —— 筒体的高度。
理想间歇操作釜式反应器的计算
理想间歇操作釜式反应器简称为BR,是指一次 性加料、一次性出料、在反应进行过程中既不加 料也不出料的釜式反应器
温
过
B
程
1/(-RA)
面积 t
A
cA0
0
XA1
XA2
XA
• 已知:在间歇釜中己二酸和己二醇以等摩尔比反应生产醇酸
树脂。(-rA)=kcA2kmol(A)/L.min) k=1.97L/(kmol.min)
• CA0=0.004kmol/L t´=1h =0.75若每天处理2400kg己二酸
• 求xA=0.5,0.6,0.8,0.9时,所需反应时间.
间歇反应釜的操作规程

间歇反应釜的操作规程1. 引言间歇反应釜是一种常用的化工设备,广泛应用于化学反应、物质合成、催化剂活化等领域。
本文档旨在介绍间歇反应釜的操作规程,以确保操作人员的安全和设备的正常运行。
2. 设备准备在操作间歇反应釜之前,需要做好设备准备工作,包括: - 确保反应釜内外清洁,并检查是否有异物。
- 检查仪表和安全装置是否正常工作。
- 准备所需的原料、试剂和辅助设备。
3. 操作步骤3.1. 开机准备•启动冷却系统,并确保其正常工作。
•检查加热系统和搅拌系统是否正常工作。
3.2. 导入原料•检查原料是否符合操作要求,如纯度、浓度等。
•打开原料进料阀门,将原料注入到反应釜中。
3.3. 加热和反应•设置反应釜的温度和压力参数,注意不要超出设备规定的范围。
•启动加热系统,将反应釜内的温度逐渐升高至设定值。
•同时启动搅拌系统,保持反应物均匀搅拌。
3.4. 反应控制•监测反应温度、压力和搅拌速度,确保其符合设定值。
•根据反应过程中的实际情况,调整温度、压力和搅拌速度,保持反应的稳定进行。
3.5. 反应结束•根据反应的需要,合理控制反应时间。
•在反应达到设定时间后,停止加热系统和搅拌系统,结束反应。
3.6. 放空和清洗•打开放空阀门,将反应釜内的气体排出。
•用适当的溶剂对反应釜进行清洗,确保设备干净。
4. 安全注意事项在操作间歇反应釜时,应注意以下安全事项: - 严格按照操作规程操作,不得随意更改参数。
- 穿戴正确的个人防护装备,如防护眼镜、手套等。
- 注意反应物的性质和特点,避免发生意外事故。
- 定期维护和检查设备,确保设备的安全可靠性。
5. 总结通过本文档的介绍,我们了解了间歇反应釜的操作规程,包括设备准备、操作步骤和安全注意事项。
在操作间歇反应釜时,操作人员应严格遵守操作规程,确保操作的安全和设备的正常运行。
间歇反应釜的实习报告

一、实习背景随着我国化工产业的快速发展,间歇反应釜在化工生产中扮演着重要角色。
为了更好地了解间歇反应釜的工作原理、操作方法以及在实际生产中的应用,我于近期在XX化工有限公司进行了为期一个月的实习。
以下是实习报告。
二、实习目的1. 了解间歇反应釜的工作原理、结构及性能;2. 掌握间歇反应釜的操作方法及安全注意事项;3. 熟悉间歇反应釜在实际生产中的应用;4. 培养实际操作能力,提高综合素质。
三、实习内容1. 间歇反应釜的基本知识(1)间歇反应釜的定义:间歇反应釜是一种在反应过程中,反应物和产物不能连续进出反应器的反应器。
(2)间歇反应釜的分类:根据反应釜的形状、材质、容积等因素,可分为多种类型,如立式反应釜、卧式反应釜、搪瓷反应釜等。
(3)间歇反应釜的组成:主要由釜体、搅拌装置、加热装置、冷却装置、进料装置、出料装置、安全装置等组成。
2. 间歇反应釜的操作方法(1)开启设备:先开启冷却水、蒸汽等,然后开启搅拌装置。
(2)投料:按照工艺要求,将反应物投入反应釜中。
(3)加热:根据工艺要求,调节加热装置,使反应釜内温度达到预定值。
(4)搅拌:开启搅拌装置,使反应物充分混合,保证反应均匀。
(5)反应:在反应过程中,密切观察反应釜内温度、压力等参数,确保反应正常进行。
(6)冷却:反应结束后,关闭加热装置,开启冷却装置,使反应釜内温度降至室温。
(7)出料:待反应釜内温度降至室温后,开启出料装置,将产物排出。
(8)清洗:反应釜使用完毕后,进行清洗,为下次使用做好准备。
3. 间歇反应釜的安全注意事项(1)操作人员必须熟悉设备性能、操作方法及安全注意事项。
(2)操作过程中,密切关注反应釜内温度、压力等参数,确保反应正常进行。
(3)操作过程中,严格遵守安全操作规程,防止意外事故发生。
(4)设备出现故障时,立即停止操作,及时上报,确保设备安全。
四、实习收获1. 通过实习,我对间歇反应釜的工作原理、结构及性能有了更深入的了解。
间歇反应釜仿真实习报告

间歇反应釜仿真实习报告一、实习背景随着我国化工产业的快速发展,间歇反应釜在化工生产中的应用越来越广泛。
间歇反应釜是一种常见的化工反应设备,主要用于进行各种化学反应,如合成、聚合、转化等。
为了提高化工生产的安全性和效率,减少事故发生,有必要对间歇反应釜的操作人员进行严格的培训。
此次实习,我有幸参加了间歇反应釜仿真培训,通过模拟实际生产过程中的各种工况,提高了我的操作技能和安全意识。
二、实习内容1. 熟悉间歇反应釜的工艺流程在仿真培训中,我首先了解了间歇反应釜的工艺流程,包括原料的准备、加料、加热、反应、冷却、卸料等环节。
通过对工艺流程的学习,我掌握了间歇反应釜各部分的作用及操作方法,加深了对间歇反应釜的了解。
2. 学习间歇反应釜的操作方法在仿真培训过程中,我学习了间歇反应釜的操作方法,包括启动、停止、调节温度、压力、液位等参数。
通过实际操作,我掌握了间歇反应釜的操作技巧,提高了操作熟练度。
3. 学习间歇反应釜的事故处理方法在实际生产过程中,间歇反应釜可能会出现各种事故,如超压、超温、泄漏等。
在仿真培训中,我学习了间歇反应釜的各种事故处理方法,掌握了事故发生的原因和预防措施,提高了应对突发事故的能力。
4. 分析间歇反应釜的运行数据通过对间歇反应釜的运行数据进行实时分析,可以了解设备的运行状态,预防事故的发生。
在仿真培训中,我学习了如何分析间歇反应釜的运行数据,如温度、压力、液位等参数,提高了我的数据分析能力。
三、实习收获通过参加间歇反应釜仿真培训,我收获颇丰。
首先,我熟悉了间歇反应釜的工艺流程和操作方法,为实际工作中的操作奠定了基础。
其次,我学会了间歇反应釜的事故处理方法,提高了应对突发事故的能力。
最后,我掌握了分析间歇反应釜运行数据的方法,为设备运行管理提供了有力支持。
四、实习总结此次间歇反应釜仿真培训,使我受益匪浅。
我深刻认识到,熟练掌握间歇反应釜的操作方法和事故处理技巧是保证生产安全、提高生产效率的关键。
间歇反应釜控制的难点与策略

间歇反应釜控制的难点与策略间歇反应釜控制的难点主要在:1、复杂性、时滞性和非线性(1)聚合反应的生产过程伴随着物理化学反应、生化反应、相变过程及物质和能量的转换和传递,因而是一个十分复杂的工业生产过程;(2)所用反应釜容积量大、釜壁厚,因此是一个热容量大、纯滞后、时间长的被控对象;(3)随着反应的进行,各传热媒体的传热系数成非线性变化,并且对各种外界环境的变化比较敏感;加上反应过程增益变化也会很大,甚至增益的变化方向都是不一样的,而且随着反应的进行,釜的传热系数也会随着发生不规则的变化。
所以,这些因素的存在,致使该反应过程变得异常的复杂,致使夹套内的冷却液量与釜内温度之间的变化产生严重的非线性,而冷水量直接影响釜内温度是否满足工艺要求。
2、难控性(1)反应过程中由于化学反应放热的复杂性和非线性,各传热媒体的传热系数成非线性变化,并对各种外部干扰的影响较敏感,使得控制有一定的难度,(2)反应过程中如果热量移去不及时、不均匀,会使反应温度一直上升,极易因局部过热而照成“飞温”现象,产生爆聚;反之,如果热量移去过多,会造成反应温度一直下跌,形成僵釜现象,造成反应停止,而聚合反应好坏的主要因素就是反应釜温度控制的好坏,温度的变化将直接影响产品的质量和产量,所以此过程的温度控制是重点也是难点。
(3)反应工艺以及反应设备的约束及外界环境对反应影响的不确定性也使得控制难度的增加。
3、建模难间歇反应过程化学反应机理较为复杂,尤其是聚合反应过程涉及物料、能量的平衡,反应动力学等,加上外界条件如原料纯度、催化剂类型、原料添加量的变化、热水温度、循环冷却液的流量变化对系统的影响较大,推导机理模型较为困难,又由于化学反应防热过程的复杂性和非线性,随着反应的进行,各转热媒体的传热系数不规则变化对各种外部干扰影响较为敏感,依照机理法和最小二乘法等传统的建模方法,要建立反应过程的精确数学模型非常困难。
变论域模糊控制。
化工仿真—间歇反应釜课件

编写仿真程序:根据 建立的数学模型,编 写仿真程序,实现间 歇反应釜仿真的计算 和模拟。
确定仿真参数和边界条件
确定反应温度、压力、物料配比等参数 设定反应釜的进出口流量和温度 确定反应釜内壁的热传导系数和热容 设定反应釜内的搅拌转速和功率
编写仿真程序
确定仿真目标:确定间 歇反应釜仿真的具体目 标,如模拟反应过程、 优化反应条件等。
未来展望:随着科技的不断进步,间歇反应釜仿真技术有望在工业生产中发挥更加重要的作用, 需要进一步研究和探索。
对化工仿真技术的未来发展的展望和建议
化工仿真技术将不断升级和完善,提高模拟的真实性和准确性。 化工仿真技术将与人工智能、大数据等先进技术结合,实现智能化仿真。 化工仿真技术将拓展应用领域,不仅局限于化工行业,还将应用于其他工业领域。 化工仿真技术需要加强人才培养和技术交流,提高技术水平和应用能力。
间歇反应釜仿真 的实现过程
建立数学模型
确定仿真目标:确定 间歇反应釜仿真的具 体目标,如模拟反应 过程、优化反应条件 等。
建立反应动力学模型: 根据化学反应原理, 建立反应动力学模型, 描述反应速率和反应 进程。
确定模型参数:根据 实验数据或经验公式 ,确定模型参数,如 反应速率常数、活化 能等。
缺点:对于某些复杂的化学反应,模拟 精度可能会受到影响,需要不断调整和 优化模型。
改进方向:加强模型精度和稳定性,提 高模拟结果的可靠性和准确性。同时, 拓展应用领域,为更多类型的间歇反应 提供仿真支持。
化工仿真技术的 发展前景和挑战
化工仿真技术的发展前景
化工仿真技术将更加智能化,提高预测精度和可靠性
仿真结果分析和优化方案
仿真结果:间歇反应釜的物料转化率、反应时间、温度等关键参数的模拟结果 结果分析:对比实际生产数据,分析仿真结果的准确性和可靠性 优化方案:根据仿真结果,提出针对性的优化措施,提高间歇反应釜的生产效率和产品质量 实施方案:详细说明优化方案的实施步骤和注意事项
反应釜间歇反应过程温度控制特点

反应釜间歇反应过程温度控制特点反应釜是一种广泛应用于化学、医药、食品、冶金等领域的设备,其采用了间歇反应的方式进行化学反应。
在反应釜内,温度是一个至关重要的控制因素,能够影响到反应的速率、产物的选择和质量,甚至是反应是否能够成功实施。
因此,在间歇反应过程中,温度控制是一个非常重要和特殊的问题。
首先,反应釜间歇反应过程温度控制的特点之一是瞬时性。
由于反应釜是一个封闭的体系,外部热量输入量是不稳定的。
在反应釜内,化学反应会放出大量的热能,进而会导致反应釜内部的温度急剧上升。
因此,必须采取一定的措施,及时地调节反应釜内的温度以保证反应的稳定进行。
其次,反应釜间歇反应过程温度控制的特点之二是持续性。
由于反应釜内的反应是间歇式的,因此每次进行反应之前都需要保持反应釜内部的温度恒定。
当反应开始后,反应釜内的温度会急剧上升,此时需要通过冷却系统来降低温度,以保证反应稳定进行。
一旦反应结束,还需要及时地恢复反应釜内的温度到初始状态,以方便下次反应的开始。
最后,反应釜间歇反应过程温度控制的特点之三是灵活性。
反应釜内的化学反应需要合理选取不同的反应条件,包括反应时间、反应温度、反应物浓度等参数。
因此,温度控制系统需要具备良好的控制灵活性,以便根据反应物和反应条件的不同需要进行调整和优化。
总之,反应釜间歇反应过程温度控制是一个非常关键和特殊的问题,必须采取一定的措施来确保反应的稳定性和成功性。
在使用反应釜进行化学反应时,必须深刻理解温度控制的特点,采取相应的措施,才能够取得优异的反应效果和结果。
- 1、下载文档前请自行甄别文档内容的完整性,平台不提供额外的编辑、内容补充、找答案等附加服务。
- 2、"仅部分预览"的文档,不可在线预览部分如存在完整性等问题,可反馈申请退款(可完整预览的文档不适用该条件!)。
- 3、如文档侵犯您的权益,请联系客服反馈,我们会尽快为您处理(人工客服工作时间:9:00-18:30)。
间歇反应釜
了解塔的结构,开车前,开车时,停车后的要求,注意事项,操作规程以及工艺参数的调整等。
1反应釜的结构
一)反应釜由反应容器、搅拌器及
传动系统、冷却装置、安全装
置、加热炉等组成。
1、釜体、釜盖采用
1Cr18Ni9Ti不锈钢加工制成,
釜体通过螺纹与法兰联接,釜
盖为正体平板盖,两者由周向
均布的主螺栓、螺母紧固联接。
2、反应釜主密封口采用A型
的双线密封,其余密封点均采
用圆弧面与平面、圆弧面与圆
弧面的线接触的密封形式,依
靠接触面的高精度和光洁度,达到良好的密封效果。
3、釜体外装有桶型碳化硅炉芯,电炉丝穿于炉芯中,其端头由炉壳侧下部穿出,通过接线螺柱,橡套电缆与控制器相连。
4、釜盖上装有压力表,爆破膜安全装置,汽液相阀,温度传感器等,便于随时了解釜内的反应情况,调节釜内的介质比例,并确保安全运行。
反应釜的结构2
5、联轴器主要由具有很强磁力的一对内、外磁环组成,中间有承压的隔套。
搅拌器由伺服电机通过联轴器驱动。
控制伺服电机的转速,便可达到控制搅拌转速的目的。
6、隔套上部装有测速线圈,连成一体的搅拌器与内磁环旋转时,测速线圈便产生感应电动势,该电势与搅拌转速相应,该电势传递到转速表上,便可显示出搅拌转速。
7、磁联轴器与釜盖间装有冷却水套,当操作温度较高时应通冷却水,以及磁钢温度太高而退磁。
8、轴承采用1Cr18Ni9Ti不锈钢
轴承或高强电化石墨,耐摩损,且维修周期长。
开车前的准备•a、准备必要的开车工具,如扳手、管钳等;
•b、确保减速机、机座轴承、釜用机封油盒内不缺油;
•c、确认传动部分完好后,点动电机,检查搅拌轴是否按顺时针方向旋转,严禁反转;•d、用氮气(压缩空气)试漏,检查锅上进出口阀门是否内漏,相关动、静密封点是否有漏点,并用直接放空阀泄压,看压力能否很快泄完
开车时的要求
•a、按工艺操作规程进料,启动搅拌运行;
•b、反应釜在运行中要严格执行工艺操作规程,严禁超温、超压、超负荷运行;凡出现超温、超压、超负荷等异常情况,立即按工艺规定采取相应处理措施。
禁止锅内超过规定的液位反应;
•c、严格按工艺规定的物料配比加(投)料,并均衡控制加料和升温速度,防止因配比错误
或加(投)料过快,引起釜内剧烈反应,出现超温、超压、超负荷等异常情况,而引发设备安全事故。
•d、设备升温或降温时,操作动作一定要平稳,以避免温差应力和压力应力突然叠加,使设备产生变形或受损;
•e、严格执行交接班管理制度,把设备运行与完好情况列入交接班,杜绝因交接班不清而出现异常情况和设备事故。
停车时要求
按工艺操作规程处理完反应釜物料后停搅拌,并检查、清洗或吹扫相关管线与设备,按工艺操作规程确认合格后准备下一循环的操作。