分离过程节能
Aspen plus 节能分离过程
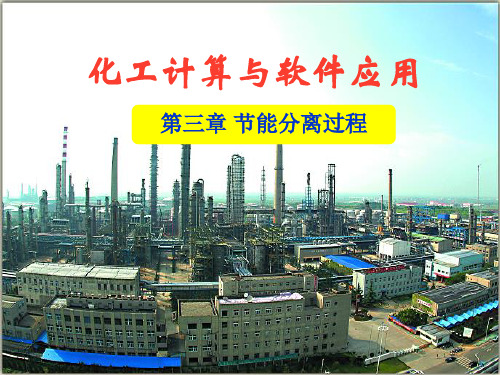
南 京 工 业 大 学 包 宗 宏
8/47
3.1.2热集成网络分析 Aspen能量分析器软件采用过程系统最优化的方法进行过程 热集成的设计,其核心是窄点技术。 它主要是对过程系统的整体进行优化设计,包括冷热物流之 间的恰当匹配、冷热公用工程的类型和能级选择;加热器、冷 却器及系统中的一些设备如分离器、蒸发器等设备在网络中的 合适放置位置;节能、投资和可操作性的三维权衡;
3/47
南 京 工 业 大 学 包 宗 宏
3.1.1 冷热流体换热 例3-1.乙醇与苯双塔双压精馏系统内冷热流体换热。 在例2-19中,设计了一个双塔双压精馏分离乙醇与苯共沸物 的流程:
B5 RECYC
163 C
69.8 C
2RECYC
215.2 KW
B4
-1894.2 kw
D1
-869.1 kw 73 C
3.3 多效蒸发 丙烯腈装置废水双效蒸发模拟流程图:
南 京 工 业 大 学 包 宗 宏
消耗蒸汽27850 kg/h,蒸发水分61580 kg/h。可以算出, 双效蒸发装置1kg蒸汽蒸发了2.21 kg水分,与单效蒸发流 19/47 程相比,节省蒸汽118%。
3.4 精馏过程 3.4.1 多效精馏 多效精馏是利用高压塔顶 蒸汽的潜热向低压塔的再沸器 提供热量,高压塔顶蒸汽同时 被冷凝的热集成精馏系统。根 据进料与压力梯度方向的一致 性,多效精馏可以分为: ①并流结构,即原料分配 南 京 到各热集成塔进料;
包 宗 宏
16/47
3.4.2 多效蒸发 例3-4。某丙烯腈装置废水流率74332.1 kg/h,其中含有丙烯 腈聚合物(以C6H8N2O计算)816 kg/h,温度113℃,压力 600 kPa。 要求通过蒸发把废水中的水份蒸出83%,冷凝后的净化水作为 工艺循环水使用,使浓缩液中的丙烯腈聚合物浓度达到5.9% 以上。
戊烷分离流程及节能技术

77一、生产戊烷所要使用的原料及方法戍烷属于一种重要的化工产品,生产戍烷时,可使用天然气凝析油、油田轻烃、直馏汽油、加氢装置产出的轻质石脑油、重整加氢后的混合烃以及乙烯设备裂解产出的副产品和环戊二烯等。
现阶段,生产戍烷时,主要使用以下两种方法:(1)加氢除烯烃。
使用此方法时,采用的是在裂化后的C5馏分中加氢催化剂的方法来生产戍烷,使用这种方法生产的戍烷的纯度基本上都在98%以上,此时,则可使用分离法生产纯度高于98%的正戍烷和异戊烷。
(2)普通精馏。
普通精馏则要使用物理方法来生产戍烷,使用这种方法生产戍烷操作流程相对较为简单,不需要再单独去去除硫以及烯烃等,同时使用该方法也不会产出其他产物。
使用该方法依据的原理是根据正戍烷以及异戊烷之间的沸点差来分离戍烷,正戍烷与异戍烷之间的沸点差相对较大,两者间的沸点差为8.2℃,尚无共沸点,分离戍烷时,可使用含量较高的原料(正戍烷、异戍烷)和含量较低原料(硫化物、C5烯烃)完成物理分离方可。
使用该方法生产戍烷,操作方法相对简单且生产成本低廉,优点明显,使用该方法可生产出纯度高于95%的正戊烷以及异戊烷。
二、戍烷分离流程1.国内某炼油厂的戍烷分离流程该炼油厂根据自身的轻烃组成情况,选出含量较高的正戍烷、异戍烷原料以及含量较低的硫化物、C5烯烃原料,通过分馏法生产正戊烷以及异戊烷。
在上述原料的组合中正戍烷的含量为19.97%,异戊烷的含量为22.59%,C4以下组合的含量为9.5741%,C6以上的重烃组合的含量为47.8119%。
具体的分离流程如下所示:原材料进入脱重塔后,原材料中所含的碳六重组分会被分流出来,剩余的馏分将会进入至脱轻塔内将碳四以下的轻组分分离出来,这时剩余的馏分则会进入产品塔内部,进而则会分离出正戊烷以及异戍烷。
使用该分离方法分离戍烷时,只需要很小的压力即可,所以,生产戍烷都会使用低压容器,这样不但可以节省投资成本,并且这种方法也比较实用,具有很高的经济价值。
化工分离过程节能的现状与发展
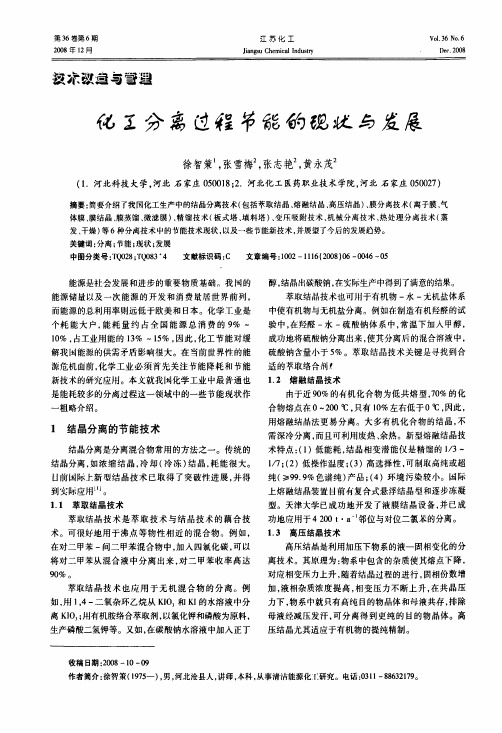
第36卷第6期2008年12月江苏化工J i angs u C hem i cal I n du s t ryV01.36N o.6D ec.2008技求教造与营鲤亿互分禹也程爷锚的琵拔与崖展徐智策1,张雪梅2,张志艳2,黄永茂2(1.河北科技大学,河北石家庄050018;2.河北化工医药职业技术学院,河北石家庄050027)摘要:简要介绍了我国化工生产中的结晶分离技术(包括萃取结晶、熔融结晶、高压结晶)、膜分离技术(离子膜、气体膜、膜结晶、膜蒸馏、微滤膜)、精馏技术(板式塔、填料塔)、变压吸附技术、机械分离技术、热处理分离技术(蒸发、干燥)等6种分离技术中的节能技术现状,以及一些节能新技术,并展望了今后的发展趋势。
关键词:分离;节能;现状;发展中图分类号:'1"0028;'r Q083+4文献标识码:C文章编号:1002—1116(2008)06—0046一05能源是社会发展和进步的重要物质基础。
我闷的能源储量以及一次能源的开发和消费最居世界前列,而能源的总利用率则远低于欧美和日本。
化学工业是个耗能大户,能耗量约占全国能源总消费的9%~10%,占工业用能的13%~15%,因此,化工节能对缓解我国能源的供需矛盾影响很大。
在当前世界性的能源危机面前,化学工业必须首先关注节能降耗和节能新技术的研究应用。
本文就我园化学工业中最普通也是能耗较多的分离过程这一领域中的一些节能现状作一粗略介绍。
l结晶分离的节能技术结晶分离是分离混合物常用的方法之一。
传统的结晶分离,如浓缩结晶,冷却(冷冻)结晶,耗能很大。
E j前国际上新型结晶技术已取得了突破性进展,并得到实际应用¨1。
1.1萃取结晶技术萃取结晶技术是萃取技术与结品技术的藕合技术。
可很好地用于沸点等物性相近的混合物。
例如,在对二甲苯一间二甲苯混合物中,加入四氯化碳,可以将对二甲苯从混合液中分离出来,对二甲苯收率高达90%。
化工节能技术第五章第一讲
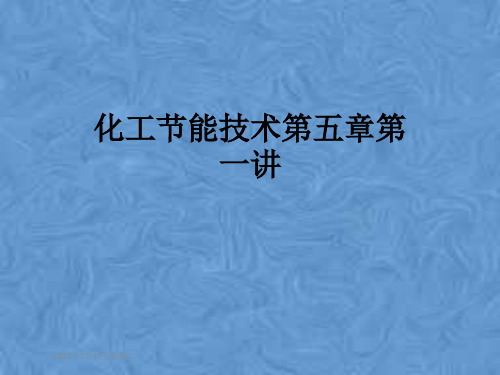
蒸气进入冷凝器中被全部冷
凝,因此塔顶馏出液组成及
回流液组或均与第1层板的上
升蒸气组成相同,即
y1=xD=已知值 由于离开每层理论板的
气液两相是互成平衡的,故
可由y1用气液平衡方程求得x1。 由于从下一层(策2层)板的上
升蒸气组成y2与x1符合精馏段 操作关系,故用精馏段操作
线方程可
y2
R R 1
x1
(1)热量充分回收利用:据调查炼化企业,小于1000C的余 热占57%,1200C-2000C的占37%,大于2000C的占6%。一般 1500C以下的低温余热占一半以上,如何加以利用是值得 研究的。
(2)减少蒸馏过程所需能耗:在很大程度上取决于回流比 大小,可能的条件下,尽量减少操作回流比。
(3)严格控制产品的质量规格:不盲目的追求高纯度。
5.1 蒸馏过程能量消耗及节能
精馏过程能耗较大,如原油精馏燃料消耗占全厂的15%40%。
精馏系统能量利用率低,95%左右被塔顶冷凝器的冷却水 带走,能量利用率仅5%左右。
涉及的能量项:原料带入;加热热源输入;塔顶回流带 入;塔顶产品带出;冷却水带出;塔底产品带出;热损 失,七项。
5.1 蒸馏过程能量消耗及节能
在精馏系统中,塔顶蒸汽用热泵提高它的温位,并作为再沸 器的热源,有效的回收蒸汽的冷凝潜热,用于过程本身,提 高了热效率。因此,热泵精馏是一种很有前途的有效节能技 术。
用于化工生产中的热泵,主要是蒸汽压缩式热泵,低温蒸汽 借助于压缩装置来提高其温位。
分为两类:机械压缩式热泵,螺杆式压缩机或离心式透平压 缩机。由于压缩比大,余热温位提高较大,热泵精馏多采用 此种型式;蒸汽喷射式热泵,利用0.8MPa以上的较高压蒸汽 从喷嘴处高速喷出,所产生的卷带抽吸作用,降低温位的蒸 汽吸入,混合后以0.4MPa以下的低蒸汽从喷射器中喷出,作 为热原使用,设备简单,但节能效果不如压缩式热泵。
精馏过程的节能降耗

精馏过程的节能降耗精馏过程在化工产业中是一项重要的分离技术,但是它也是能耗较高的过程。
为了降低能耗,节能降耗已经成为精馏技术的一个重要研究方向。
本文将介绍几种精馏过程的节能降耗技术。
首先,提高精馏塔的热效率是提高精馏过程的一个关键。
一种常见的做法是引入换热器网络来最大程度地利用出塔冷凝液和进塔蒸汽之间的热量传递。
这种方法可以降低所需的蒸汽量,从而降低了能耗。
此外,还可以使用多效精馏、热泵或采用废热回收技术进一步提高热效率。
其次,提高精馏过程的物质效率也是节能降耗的一个重要途径。
物质效率是指在精馏过程中使用的干燥剂或者吸附剂能够更有效地去除杂质,从而减少能耗。
通过改进精馏塔的操作条件,如温度、压力和液体流速等参数,可以提高物质效率。
同时,使用高效的精馏填料或者塔板也能够提高分离效果,减少杂质的含量。
此外,使用先进的辅助技术可以进一步降低精馏过程的能耗。
例如,在精馏过程中引入膜分离技术可以减少能源消耗。
膜分离技术是一种基于材料表面或孔隙的选择性渗透性原理分离混合物的方法。
与传统的溶剂萃取或者蒸馏技术相比,膜分离技术具有能耗低、操作简单、体积小等优点。
通过将膜分离技术与精馏过程相结合,可以实现更高效的分离效果。
最后,优化精馏过程的操作策略也是节能降耗的一个重要途径。
通过优化参数设定和控制策略,可以使精馏过程更加稳定和高效。
例如,采用先进的控制算法,如模型预测控制或者模糊控制算法,可以实现对精馏过程的快速响应和精确控制,从而降低了能耗和运行成本。
总的来说,精馏过程的节能降耗是一个涉及多个方面的工程问题。
通过提高热效率、物质效率,使用先进的辅助技术和优化操作策略,可以有效地降低精馏过程的能耗。
这些节能降耗技术不仅可以减少环境污染,还可以提高精馏过程的经济效益。
因此,精馏过程的节能降耗在工业应用中具有重要的意义。
乙烯生产工艺流程及设备认知 深冷分离中的节能措施

设置中间再沸器和中间冷凝器 中间换热器设置图
设置中间再沸器和中间冷凝器
在精馏塔中精馏段适当位置增设中间冷凝器提供 部分低质的冷量(如冷却水),可降低塔顶高品位 制冷剂的用量。
利用热泵实现从低温到高温的热量传递 闭式热泵
利用热泵实现从低温到高温的热量传递
(a)
开式热泵
(b)
小
结
1. 设置中间再沸器和中间冷凝器 2. 逐级分凝,多股进料 3. 利用热泵实现从低温到高温的
热量传递
深冷分离中的 节能措施
在深冷分离过程中,可以采 取哪些节能措施呢?
目
CONTENTS
录
01 设置中间再沸器和中间冷凝器 02 逐级分凝,多股进料 03 利用热泵实现从低温到高温
的热量传递
01
设置中间Байду номын сангаас沸器和 中间冷凝器
设置中间再沸器和中间冷凝器 脱甲烷塔中间再沸器流程
设置中间再沸器和中间冷凝器
在精馏塔中提馏段适当位置增设中间再沸器提供 部分低质的热量(如废热),可降低塔底高品位加 热介质的用量。
02
逐级分凝,多股进料
逐级分凝,多股进料
脱甲烷塔流程
1-冷箱换热器; 2-气液分离罐; 3-脱甲烷塔; c,e,g,i-脱甲烷塔四股进料; j-富氢; k-甲烷; l-甲烷(分子筛再生用载气); m-甲烷(燃料); p-乙烷(裂解原料)
03
利用热泵实现从低温 到高温的热量传递
利用热泵实现从低温到高温的热量传递
在精馏过程中,塔顶用外来冷剂制冷,从塔 顶移出热量;塔底又要用外来热剂供热。
化工分离过程(总复习)
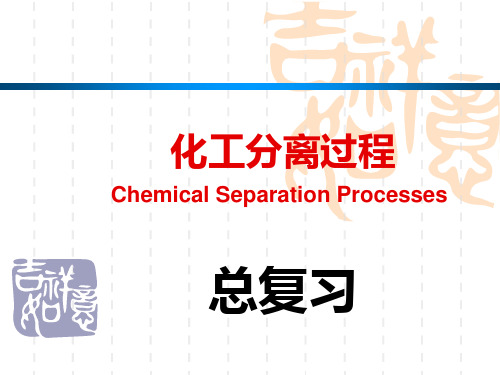
1.3 多组分多级分离过程分析与简捷计算
萃取精馏过程S作用可归纳为以下几点: (1)溶液性质的影响,最好为与1形成正偏差,与2形成 负偏差的体系; (2)溶剂浓度的影响(稀释作用)使原溶液中各组分的 作用减弱,S量要大(一般xS为0.6~0.8)。
3、萃取精馏过程溶剂选择的原则及三种选择方法 4、萃取精馏流程及萃取精馏塔的分段
总复习
习题课大纲
1 重要知识点回顾
1.1 绪论 1.2 单级平衡过程 1.3 多组分多级分离过程分析与简捷计算 1.4 多组分多级分离的严格计算 1.5 分离设备的处理能力和效率 1.6 分离过程的节能 1.7 其它分离技术和分离过程的选择
2 考试题型 3 自由交流环节
2
1.1 绪论
33
1.3 多组分多级分离过程分析与简捷计算
(2)共沸组成的计算(简单过程)
已知共沸压力 P,求:T、xi
5、萃取精馏塔内流量分布、和浓度分布特点 6、萃取精馏操作设计的特点
32
1.3 多组分多级分离过程分析与简捷计算
7、共沸物的特征和共沸组成的计算
(1)共沸物的特征:
s s 12 1P P 1 2 2 1
a 共沸点对应共沸组成x=y;
b 过了共沸点,轻、重组分互换;
c 原料组成在共沸点一侧,可得一纯组分和一共沸物。
分离媒介分为能量媒介(ESA)和物质媒介(MSA)。 速率分离过程——借助某种推动力(如浓度差、压力 差、温度差、电位差等)的作用,某些情况下在选择性透
过膜的配合下,利用各组分扩散速度的差异而实现混合物
的分离操作。
4
1.2 单级平衡过程
1、相平衡的定义和条件
相平衡 :混合物或溶液形成若干相,这些相保
第六章 分离过程的节能

➢ 例如,1994年,美国4万多个精馏塔所消耗的
能量相当于每天190,000m3(120万桶)石 油,占全国能耗的3%。
➢ 由此可见,精馏节能具有重要意义。
如何降低能耗?
➢ 要降低分离过程的能耗,提高其热力学效率,
就应该采取措施减小过程的有效能损失。有效 能损失是由于过程的不可逆性引起的。
Bsep /(Wnet )
Wnet Bsep T0Sirr
6.2 精馏的节能技术
一般精馏过程的不可逆性表现在:
➢(1)在流体流动时产生压力降; ➢(2)塔内上升蒸汽与下降液体直接接触
进行热交换时有温差,再沸器和冷凝器 中传热介质与物料之间存在温差;
➢(3)上升蒸汽与下流液体进行传质过程
时,两相浓度与平衡浓度的差异。
分离过程中有效能损失的主要形式
(1)由于流体流动阻力造成的有效能损失; (2)节流膨胀过程的有效能损失; (3)由于热交换过程中推动力温差存在造成的有
效能损失; (4)由于非平衡的两项物流在传质设备中混合和
接触传质造成的有效能损失。
节省能耗的措施有哪些?
➢ 首先是选取适宜的分离方法,这是节能的关键
化 为
在等摩尔进料下,无因次最小功的最大值是 0.6931 。
对于分离产品不是纯组分的情况:过程的最小分离功等于原料分离成纯组分的最 小分离功减去产品分离成纯组分所需的分离功。 可见,产品纯度越低,所需最 小分离功越小。
分离成非纯产品时所需最小功小于分离成纯产品时所需最小功。
二、分离低压下的液体混合物
该式表明,稳态过程最小分离功等于物流的有效能增量。
6.1.3 热力学效率和净功消耗
➢ 热力学效率是用来衡量有效能的利用率。 ➢ 分离过程热力学效率的定义为:分离最小功与实际分
传质分离过程的强化、节能与创新

思维来 推 动新 的工程 实践 。
这次 会议 的召 开得到 各方 面热烈 响应 ,共 收到
论文 1 1篇 ,主要 包 括传 质 分 离理 论 与过 程 模 拟 , 4
而且 由于 很多传 质分 离设 备 的能耗很 大 ,而设备 强
化 的结果 往往就 是节 能 ,两者是 密切 相关 。解决 强 化 与节能 的根本 途径 要依 赖创新 ,也 就是要 用新 的
产 上 的不确定 性 ,因此 在工业设 备设 计及 放大等 方 面仍 然依 靠 中试数 据 ,或者采取 加大 安全 因素 ,或 者 根据 过去经 验运 作 ,因而缺 乏创新 提高 ,这就 意
关键 的单 元 。它覆 盖 面 广 ,从 化 工 、石 化 、生 化 、 能源 、材 料 、环保 到资源 开发 利用 、轻工 、海 水淡 化 、信息 等领 域 ;而且规 模 的幅度很 宽 ,从整个 传 质分 离 系统 、宏观 的传质 分离设 备 到细观 的纳 米尺
度 的传质 分离过 程 。与此 同时 ,高科 技也 提 出特 殊
实验测 定做得 较 多 ,例 如传 质效率 及有关 参数 的经 验 关联 等 ,但 对传 质过 程 的深 入 了解 做得 较少 。由
要求 ,促 使传 质分 离工程 面 临新 的发展 ,如分 离各
种 生化物 质 、超高 纯度 的分离 、分 离难 以分离 的体 系 、微量 分离 处理 等 。 但是 我们 也应该 看 到 ,我 国现 有 的传 质 分离设
第 6 3卷
第 1期
化
工 学
报
Vo. NO 1 63 .1
精馏过程的节能优化综合ppt课件
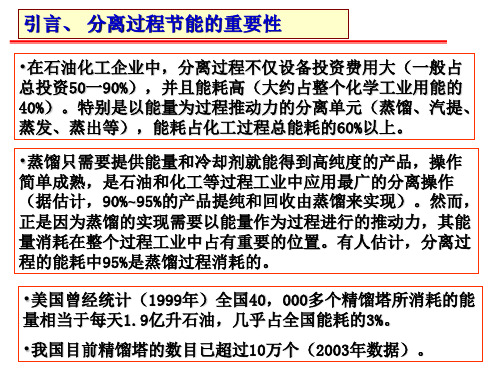
空气源空调(热泵)致热模式
室内(高 温热源)
冷空气 (5℃)
高压液体
冷凝器 (50℃)
热空气 (35℃)
高压蒸汽
节流阀
致冷剂(氟利昂)循环
压缩机
低压液体
低压蒸汽
室外(低 冷空气 温热源) (-5℃)
蒸发器 (-10℃)
冷空气 (-8℃)
空调的效率(COP)主要由什么确定?
问题:能否用其它热源?
空气源空调(热泵)致冷模式
通常所说的节能主要指降低能量消耗或操作费用。任何过程 节能是基于系统热力学分析提出的(热力学第一定律和第二 定律),节能不仅表现在数量上,更表现在品位上,同时要 明确节能和节钱的概念。
分离过程的优化包括分离方法的选择、流程结构的优化和操 作参数的优化等。优化的目标通常是系统的经济性,还包括 多个目标的优化(安全性、操作性、对环境的影响等)。优 化不仅可能节能,同时一定节钱。
3-1 热泵精馏
热泵精馏举例:分离丙烯—丙烷混合物
普通精馏系统:
常压沸点: 丙烯(-47.5℃ 丙烷(-42.1℃ )
(1)塔为什么带压操作? (2)塔为什么操作回流比很 高? (3)塔采用何种冷却介质和 加热介质? (4)要得到常压丙烯气体产 品,需要哪些步骤?
(5)要得到常压丙烷气体产品, 需要哪些步骤? (6)为什么可以考虑采用热泵 精馏?如何实现?
引言、 分离过程节能的重要性
•在石油化工企业中,分离过程不仅设备投资费用大(一般占 总投资50一90%),并且能耗高(大约占整个化学工业用能的 40%)。特别是以能量为过程推动力的分离单元(蒸馏、汽提、 蒸发、蒸出等),能耗占化工过程总能耗的60%以上。
•蒸馏只需要提供能量和冷却剂就能得到高纯度的产品,操作 简单成熟,是石油和化工等过程工业中应用最广的分离操作 (据估计,90%~95%的产品提纯和回收由蒸馏来实现)。然而, 正是因为蒸馏的实现需要以能量作为过程进行的推动力,其能 量消耗在整个过程工业中占有重要的位置。有人估计,分离过 程的能耗中95%是蒸馏过程消耗的。
化工工艺中常见的节能降耗技术措施

化工工艺中常见的节能降耗技术措施1. 废热回收利用:通过采用热交换器、蒸汽再压缩装置等设备,将工艺过程中产生的废热进行回收利用,用于加热介质或蒸汽发生器,减少能源消耗。
2. 低温余热利用:利用低温余热发电,采用有机废热发电技术,将废热转换为电能,提高能源利用效率。
3. 薄膜分离技术:通过采用薄膜分离技术,如膜渗透、膜蒸馏等,实现分离过程的能耗降低,减少工艺流程中的能量损失。
4. 质量热法:通过调整工艺参数,如温度、压力等,改变反应速率和产物选择性,实现能耗降低和产物质量的提高。
5. 溶剂替代与回收:通过选择更加环保的溶剂替代有机溶剂,减少溶剂使用量;采用溶剂回收技术,对废溶剂进行回收再利用,实现能源和原料的节约。
6. 设备能耗优化:对化工设备进行技术改造,如采用节能设备、降低过程能耗等,减少能源消耗。
7. 生产工艺优化:通过对生产工艺流程进行优化,如缩短反应时间、改进催化剂、改变传质方式等,实现能耗降低和产物质量的提高。
8. 生物技术应用:在某些化工生产过程中,可以引入生物技术,如微生物发酵、酶催化等,利用生物催化剂替代传统化学催化剂,实现能耗降低和反应选择性的提高。
9. 智能化控制系统:采用智能化控制系统,对化工工艺过程进行精确控制和优化调节,减少能耗和废品产生,提高生产效率。
10. 能源管理与优化:建立完善的能源管理体系,监测和分析能源消耗情况,并进行能源使用的优化调整,提高能源利用效率。
通过采取以上节能降耗技术措施,可以在化工工艺中减少能源消耗、降低生产成本,提高资源利用效率和环境友好性。
这些技术措施的应用可以帮助化工企业实现可持续发展,并推动绿色化工产业的发展。
化工分离过程(第20讲)(61分离的最小功和热力学效率)

6.1.1 等温分离的最小功
n 1,zi,1, H1 n2,zi,2, H2
n z ,H m 1 , i , m 1 m 1
n ,H m ,zi,m m
Q W
图6-1 连续稳定分离系统
进出系统物流变量:n,zi,H,S,Q 系统对环境作功:W
6
6.1.1 等温分离的最小功
n1,zi,1, H1 n2,zi,2, H2
分离气体混合物的最小功
13
6.1.1 等温分离的最小功
P185 例6-1
环境温度为 294.4K ,压力 101.3kPa ,在该环境条件下 将流率为 600 kmol/h 的丙烯 - 丙烷的混合气体连续分离成相 同温度、压力下的产品。 已知混合气体中含丙烯 0.60 (摩尔分数)。 分离要求为: ①含丙烯 99%(摩尔) 和含丙烷 95%(摩尔)的两个物流; ②产品为纯丙烯和纯丙烷; 确定所需最小功。
物质的混合是不可逆过程,能够自发完成,因此, 其逆过程——分离必然要消耗能量才能进行。
热力学第二定律: 完成同一变化的任何可逆过程所需的功相等。
因此,分离所需的最小功可通过假想的可逆过程计算。 最小功的数值决定于要分离的混合物的组成、压力和温度 以及分离所得产品的组成、压力和温度。
4
6.1 分离的最小功和热力学效率
化工分离过程
Chemical Separation Processes
第六章 分离过程的节能
第六章 分离过程的节能
是耗能较多的一个部门,我国化工能耗约占全国能源消耗 总量的 12.7%,折合标准煤为 7848 吨。若以每万元产值能 耗平均值计,为全国万元产值能耗平均的2.3倍。而在化学 工业中分离系统能耗更大,特别是精馏单元操作,且余热 量也大。据英、美等国统计,精馏单元操作能耗约占全国 能耗量的3%。 因此,要发展化学工业,开创化学工业的新局面,节 能问题极为重要。确定具体混合物分离的最小能耗,了解 影响能耗的因素,寻求接近此极限能耗的实际分离过程是 很有意义的。
分离过程发展的趋势

分离过程发展的趋势分离过程发展的趋势是指在化工工艺中,不同物质之间的分离操作的趋势和发展方向。
分离过程是化工工艺中的重要环节,其目的是将混合物中的组分分离出来,以获取纯净的产品或实现组分之间的进一步转化。
随着科技的发展和人们对环境保护及资源利用的要求,分离过程的发展也面临着趋势的变化。
一、高效节能高效节能是分离过程发展的主要趋势之一。
传统的分离过程通常存在能源消耗大、工艺流程复杂、产品纯度不高等问题,因此,如何在保证分离质量的前提下降低能源消耗成为研究的热点。
随着新材料、新工艺的引入,分离设备的效率得到了提高,能耗也有了明显的减少。
例如,膜分离技术具有分离效率高、能耗低、设备体积小等特点,已经开始在生物工程、化工、环保等领域得到广泛应用。
二、多功能集成多功能集成是分离过程发展的另一个趋势。
传统的分离过程通常需要多个独立的分离单元进行操作,增加了设备的大小和复杂度。
而通过多功能集成,可以将多个分离单元进行整合,使得不同的分离操作可以在同一个设备中完成。
这样不仅可以节省空间和设备投资,还可以提高生产效率和产品质量。
例如,膜分离技术可以与吸附、吸附溶剂回收、结晶等技术结合,实现多功能的分离操作。
三、绿色环保绿色环保是分离过程发展的重要趋势。
随着人们对环境污染和资源浪费的关注度提高,传统的分离过程所使用的有机溶剂和化学试剂已经不能满足环保要求。
因此,如何开发低污染的分离剂和环保型分离工艺成为了研究的重点。
一种重要的解决方案是开发水相或水溶剂的分离工艺。
与有机溶剂相比,水相分离具有成本低、对环境污染小等优势。
此外,新型分离技术如超临界流体萃取、微悬浮浓缩等也被广泛研究和应用,以实现低污染、高效率的分离过程。
四、自动化和智能化自动化和智能化是分离过程发展的趋势之一。
随着自动化和智能化技术的不断进步,分离过程中的控制和操作更加方便快捷。
自动化技术可以实现对分离过程的实时监控和数据记录,并可以通过集成计算机控制系统来实现过程的控制和优化。
炼油分离过程大型化关键技术系统集成与节能

机 。作 为 平 台的 建 设 方 , 津 市 制 造 业 信 息 化 生 产 力促 进 天
中 心 欢 迎 天 津 市 越 来 越 多 的软 件 企 业 加 入 进 来 , 同打 造 共 Sa S软 件 运 营 的 产 业 链 ,生 产 力 中心 和 奥 林 科 技 将 共 同 a 为 天津 市 的软 件 企 业 提 供 和 创 造 优 良的 发 展 条 件和 环境 。 据悉 , 目前 已经 有 多 家 天津 本 地 的 骨 干 软 件 企 业 加 入 进 来 , 平 台 已经 开 始 为 客 户 提供 应用 服 务 。 除 了货 代 软 该 件 , 台还 设置 了供 应 链 管 理 软 件 、 贸 管 理 软 件 、 户 关 平 外 客 系 管理 软 件 、 力 资 源 管 理软 件 等 众 多软 件 应用 。 人 图 1 公 共 服 务 平 台 结 构 图 如 今 S a 已成 为 国 际 上 软 件 行 业 的 主流 发 展 方 向 , aS 天津 市 中 小 企业 信 息 化 公 共 服 务 平 台 的 出现 , 疑 为 天津 无 快 速 二 次 开 发 , 大 缩短 建 设 周 期 。 大 iOS为 ADP开 发 的 S a B a S应 用 提 供 了大 规 模 运 行 的 系统环境 , 同时 提 供 了 与 第 3方 服 务 ( 网 络 传 真 、 信 、 如 短 市 的软 件 企业 提供 了 新 的 一 轮 商 机 , 将 给 天 津 市 的企 事 也 业 单 位 信 息 化 普 及 创 造 了更 好 的 条件 。 ●
Байду номын сангаас
近 5年 来 天 津 大学 精 馏 技 术 国 家 工 程 研 究 中 心 已 建
立 了 扎 实 的 工 作 基 础 , 著 降 低 了 过 程 工 业 能 耗 , 得 了 显 取
精馏过程的节能研究
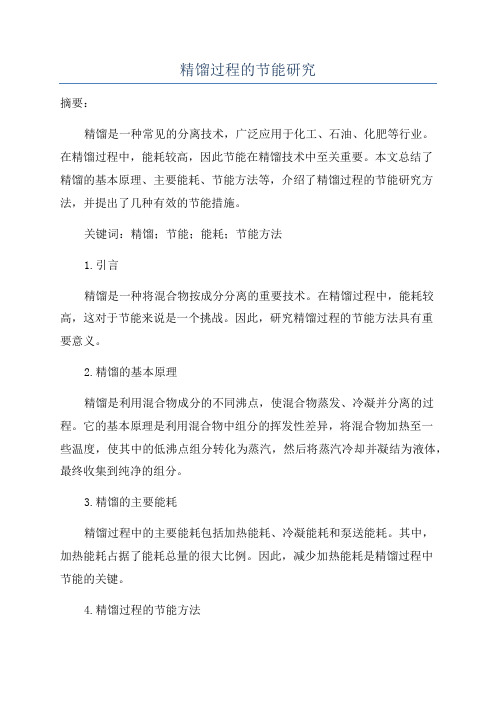
精馏过程的节能研究摘要:精馏是一种常见的分离技术,广泛应用于化工、石油、化肥等行业。
在精馏过程中,能耗较高,因此节能在精馏技术中至关重要。
本文总结了精馏的基本原理、主要能耗、节能方法等,介绍了精馏过程的节能研究方法,并提出了几种有效的节能措施。
关键词:精馏;节能;能耗;节能方法1.引言精馏是一种将混合物按成分分离的重要技术。
在精馏过程中,能耗较高,这对于节能来说是一个挑战。
因此,研究精馏过程的节能方法具有重要意义。
2.精馏的基本原理精馏是利用混合物成分的不同沸点,使混合物蒸发、冷凝并分离的过程。
它的基本原理是利用混合物中组分的挥发性差异,将混合物加热至一些温度,使其中的低沸点组分转化为蒸汽,然后将蒸汽冷却并凝结为液体,最终收集到纯净的组分。
3.精馏的主要能耗精馏过程中的主要能耗包括加热能耗、冷凝能耗和泵送能耗。
其中,加热能耗占据了能耗总量的很大比例。
因此,减少加热能耗是精馏过程中节能的关键。
4.精馏过程的节能方法(1)改善设备结构:优化精馏塔的结构,减少内部分布的不均匀性,提高传质效率和分离效果。
在塔体设计上,可以采用结构紧凑的塔板,增加塔板间隙,减小压降,提高塔板效率。
(2)改进传热方式:采用高效的传热方式,如采用波纹板式换热器、加快传热介质的速度等,提高传热效率,减少能耗。
(3)优化操作条件:合理选择操作条件,如适当降低温度、降低进料浓度等,以减少能耗。
此外,可合理控制回流比、调整塔压和温度等操作参数,以提高精馏的效果。
(4)采用节能设备:在精馏过程中,采用一些节能设备,如多级补热、换热器、回收利用部分废热等,来降低能耗。
5.精馏过程的节能研究方法(1)实验研究:通过实验对比不同条件下的能耗指标,分析各种因素对能耗的影响,优化操作条件,并提出相应的改进方法。
(2)模拟仿真:利用模拟软件对精馏过程进行仿真,探究不同操作条件下的能耗情况,并通过改变操作参数等方式来降低能耗。
(3)优化设计:通过数学方法建立精馏过程的数学模型,结合优化算法进行优化设计,以降低能耗为目标,寻找最优操作条件。
过程热力学分析及节能
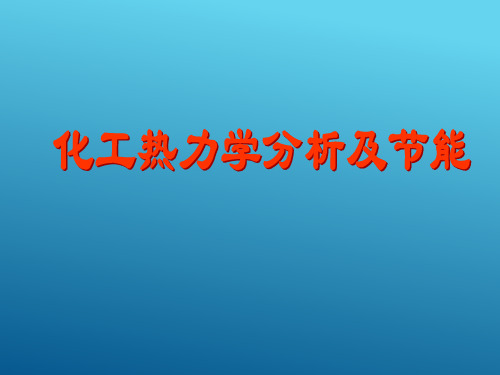
在管道中每输送1kg蒸汽,若保温不良,则其热损失为2129.7 kJ,这就是说,2129.7kJ的热量通过卡诺热机可提供612.10kJ的 功。此冷凝过程的理想功也为612.10kJ,验算如下:
Wid h T0S h1 h2 T0 S2 S1
2740 .3 610.63 2981.7907 6.8833
Sg m j S j
j
out
mi Si in S f
i
根据热力学第一定律
H Q WS 因此 对于理想气体等温混合过程 H 0, WS 0,
即
Q0 S f 0
Sg m j S j
j
out
mi Si in S f
等温混合过程对于每个组分而言,是等温膨胀过程;反之,等 温
i
分离过程对于每个组分而言,是等温压缩过程。混合过程是自发 过程,理想功大于零;分离过程是非自发过程,理想功小于零。 例 3 欲将0.10133MPa(1atm)、25℃的空气分离成相同 温度、压力下的纯氮和纯氧,至少需要消耗多少功?
[解] 设空气中氮的摩尔分数为0.79,氧的摩尔分数为0.21, 根据式(5—19a),对1mol空气分离最小功为
具有作功的能力,在冷凝成水的过程中将蒸汽的作功能力损耗掉
。试计算1kg蒸汽处于0.4154MPa、145℃下冷凝成同样压力和温 度的水时的热损失与损耗功。已知大气温度为25℃。 [解 ] 焓和熵为 查附表3(饱和水蒸气温度表)可得145 ℃饱和蒸汽的
h1 2740 .3kJ kg
1
s1 6.883kJ kg 1 K 1 s1 1.7907 kJ kg 1 K 1
热力学第一定律:
第6章 分离过程的节能化学培训

x
Li
xi
L为全塔平均温度下进料 的黏度, mPa s;为相对挥发度。
Van Winkle关系式
E MV 0.07Dg
式中:
0.14
Sc
0.25
Re
0.08
Dg为 表 面 张 力 系 数 Dg , L /( LU v ); L为 液 体 黏 度N , s / m2
第一节 气液传质设备的效率
6.1.1 气液传质设备的级效率及影响因素 6.1.2 气液传质设备级效率计算方法 6.1.3 气液传质设备的选择
气液传质设备的效率及影响因素 1)效率的表示方法 理论板与实际板比较
理 论 板
气液两相完全混合,板上浓度均一。
实 际 板
板上液相浓度径向分布,液体入口处浓度 高,进入的气相各点浓度不相同。
假设:液流主体在垂直方向完全混合。
Ei , OG
y i , j yi , j 1 yi*, j yi , j 1
yi*, j与x i , j成 平 衡
d. 填 料 塔 的 等 板 高 HETP 度
H ETP 填 料 层 高 / 度 理论板数
等板高度小,填料层传质效率高。
2) 效率的影响因素
1 Lv )] SC 2 Lf
N L (4.127 108 DL )
1 1 1 N OG N G AN L A L kV
1
2
(0.213F 0.15)t L
• 计算EOG:E
OG
1 e N OG
• 计算Zc,查图得EMV: • 查图6-6、6-7得雾沫夹带量,并求Ea。
陶瓷规整波纹填料
金属丝网波纹填料BX型的HETP为0.2-0.25m,
戊烷分离的典型工艺流程及节能技术
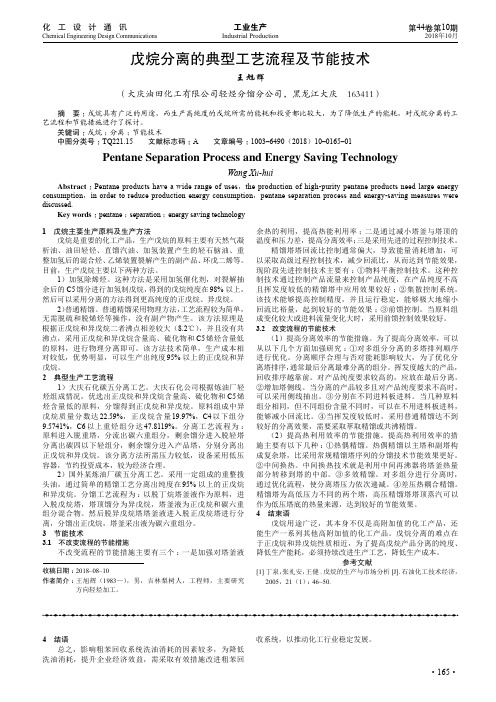
工业生产化 工 设 计 通 讯Industrial ProductionChemical Engineering Design Communications·165·第44卷第10期2018年10月4 结语总之,影响粗苯回收系统洗油消耗的因素较多,为降低洗油消耗,提升企业经济效益,需采取有效措施改进粗苯回收系统,以推动化工行业稳定发展。
1 戊烷主要生产原料及生产方法戊烷是重要的化工产品,生产戊烷的原料主要有天然气凝析油、油田轻烃、直馏汽油、加氢装置产生的轻石脑油、重整加氢后的混合烃、乙烯装置裂解产生的副产品、环戊二烯等。
目前,生产戊烷主要以下两种方法。
1)加氢除烯烃。
这种方法是采用加氢催化剂,对裂解抽余后的C5馏分进行加氢制戊烷,得到的戊烷纯度在98%以上,然后可以采用分离的方法得到更高纯度的正戊烷、异戊烷。
2)普通精馏。
普通精馏采用物理方法,工艺流程较为简单,无需脱硫和脱烯烃等操作,没有副产物产生。
该方法原理是根据正戊烷和异戊烷二者沸点相差较大(8.2℃),并且没有共沸点,采用正戊烷和异戊烷含量高、硫化物和C5烯烃含量低的原料,进行物理分离即可。
该方法技术简单,生产成本相对较低,优势明显,可以生产出纯度95%以上的正戊烷和异戊烷。
2 典型生产工艺流程1)大庆石化碳五分离工艺。
大庆石化公司根据炼油厂轻烃组成情况,优选出正戊烷和异戊烷含量高、硫化物和C5烯烃含量低的原料,分馏得到正戊烷和异戊烷。
原料组成中异戊烷质量分数达22.59%,正戊烷含量19.97%,C4以下组分9.5741%,C6以上重烃组分达47.8119%。
分离工艺流程为:原料进入脱重塔,分流出碳六重组分,剩余馏分进入脱轻塔分离出碳四以下轻组分,剩余馏分进入产品塔,分别分离出正戊烷和异戊烷。
该分离方法所需压力较低,设备采用低压容器,节约投资成本,较为经济合理。
2)国外某炼油厂碳五分离工艺。
采用一定组成的重整拨头油,通过简单的精馏工艺分离出纯度在95%以上的正戊烷和异戊烷。
- 1、下载文档前请自行甄别文档内容的完整性,平台不提供额外的编辑、内容补充、找答案等附加服务。
- 2、"仅部分预览"的文档,不可在线预览部分如存在完整性等问题,可反馈申请退款(可完整预览的文档不适用该条件!)。
- 3、如文档侵犯您的权益,请联系客服反馈,我们会尽快为您处理(人工客服工作时间:9:00-18:30)。
分离工程
3.3分离过程与设备的节能 分离过程与设备的节能 塔设备节能:降低压降、减少回流比、预热进料、 塔设备节能:降低压降、减少回流比、预热进料、塔顶 余热利用、使用串联塔、采用热泵、采用中间再沸器和中间 余热利用、使用串联塔、采用热泵、 冷凝器等 。 精馏过程节能: 精馏过程节能: 精馏是分离互溶液体的最常用方法,也是化工中最大的 精馏是分离互溶液体的最常用方法, 耗能操作。精馏过程具有热力学不可逆性,其原因是: 耗能操作。精馏过程具有热力学不可逆性,其原因是:①具 有压力梯度的动力传递; 有压力梯度的动力传递;②一定温度梯度的热量传递或不同 温度流体的混合; 温度流体的混合;③一定浓度梯度的质量传递或不同化学位 物流的直接混合。减小压力降、减少温度差、 物流的直接混合。减小压力降、减少温度差、减少传质过程 两相浓度与平衡浓度的差别将有助于节能。 两相浓度与平衡浓度的差别将有助于节能。
多 效 精 馏
分离工程
利用外 部制冷 剂、压 缩塔顶 蒸汽、 蒸汽、 闪蒸塔 底流体
热 泵 精 馏
利用膨胀阀和压缩机改变冷凝和沸腾温度
分离工程
中 间 再 沸 器 与 冷 凝 器
分离工程
塔 顶 蒸 汽 发 电
分离工程
节能的基本经验法则: 节能的基本经验法则: (1)分离同样量的物质,机械分离过程需要的能量比 )分离同样量的物质, 传质分离过程要小得多,所可将机械分离过程作为预处理。 传质分离过程要小得多,所可将机械分离过程作为预处理。 (2)优先使浓度低的组分发生相变; )优先使浓度低的组分发生相变; (3)优先选择分离因子高的方案; )优先选择分离因子高的方案; (4)优先选用能量分离剂; )优先选用能量分离剂; (5)优先选用相变潜热较低的分离剂; )优先选用相变潜热较低的分离剂; (6)平衡分离过程能耗小于速率分离过程; )平衡分离过程能耗小于速率分离过程; (7)避免过度分离; )避免过度分离; (8)适当多地采用多级或组合分离; )适当多地采用多级或组合分离;
分离工程
第十章 分离过程节能
中北大学化工与环境学院 2011年 2011年
分离工程
1概述 1.1能源及其分类 1.1能源及其分类 能源是指可以直接或通过转换,为人类生产与生活提 能源是指可以直接或通过转换,为人类生产与生活提 供能量和动力的物质资源。 供能量和动力的物质资源。 世界能源大会推荐的能源类型有:固体燃料(如煤、 世界能源大会推荐的能源类型有:固体燃料(如煤、 焦炭等)、液体燃料(石油、酒精等)、气体燃料( 焦炭等)、液体燃料(石油、酒精等)、气体燃料(天然 )、液体燃料 )、气体燃料 气、煤气、氢气等)、水力、电能、核能、太阳能、风能、 煤气、氢气等)、水力、电能、核能、太阳能、风能、 )、水力 地热能、海洋能、生物质能等。 地热能、海洋能、生物质能等。 这些能源能够根据人类的需要转化为热能、机械能、 这些能源能够根据人类的需要转化为热能、机械能、 电能、光能、声能及化学能等各种形式而加以利用。 电能、光能、声能及化学能等各种形式而加以利用。
分离工程
节能潜力可从不同角度分析: 节能潜力可从不同角度分析: (1)从单位产值能耗估计节能潜力 我国GDP单耗比发达国家高1 我国GDP单耗比发达国家高1-3倍。 GDP单耗比发达国家高 (2)从提高能源利用率看节能潜力 目前,我国能源利用效率为32%,比发达国家低10个 目前,我国能源利用效率为32%,比发达国家低10个 32%,比发达国家低10 百分点。基数大,每提高1个百分点,可省150万吨标煤。 150万吨标煤 百分点。基数大,每提高1个百分点,可省150万吨标煤。 (3)从主要产品单位能耗的差距分析节能潜力 合成氨与乙烯高出1 合成氨与乙烯高出1倍;烧碱高40%;电石高20%。 烧碱高40%;电石高20%。 40%;电石高20 (4)从主要耗能设备技术水平分析节能潜力 工业锅炉平均热效率55%-60%,发达国家在80%。 工业锅炉平均热效率55%-60%,发达国家在80%。 55%-60%,发达国家在80
分离工程
3.2流程节能 流程节能 多组份混合物分离顺序的合理选择有助于节能降耗。 多组份混合物分离顺序的合理选择有助于节能降耗。 以精馏过程为例介绍。除简单塔外,可采用多段进料、 以精馏过程为例介绍。除简单塔外,可采用多段进料、侧 线采出、侧线气提和热耦合等方式构成复杂塔及塔系, 线采出、侧线气提和热耦合等方式构成复杂塔及塔系,综 合利用能源。 合利用能源。 简单塔分离顺序的合成,分离 种混合物 种混合物, 种流程 种流程。 简单塔分离顺序的合成,分离4种混合物,5种流程。 确定精馏塔分离顺序的经验法则: 确定精馏塔分离顺序的经验法则:①按相对挥发度递 减的顺序逐个从塔顶分离出各组分; 减的顺序逐个从塔顶分离出各组分;②最困难的分离放在 最后; 各塔的馏出液与釜液的摩尔数尽量接近; 最后;③各塔的馏出液与釜液的摩尔数尽量接近;④分离 很高回收率的组分放在最后; 很高回收率的组分放在最后;⑤进料中含量高的组分提前 分离。互相矛盾,需综合考虑。 分离。互相矛盾,需综合考虑。
分离工程 2分离的最小功和热力学效率
分离最小功表示了分离过程能耗的下限,与组成、 分离最小功表示了分离过程能耗的下限,与组成、压 力及温度等因素有关。可逆时最小。 力及温度等因素有关。可逆时最小。最小分离功的大小标 志着物质分离的难易程度。评价不同方案时, 志着物质分离的难易程度。评价不同方案时,最小功具有 重要的意义。 重要的意义。
分离工程
1.2节能的潜力与意义 1.2节能的潜力与意义 化学工业的特点之一就是, 化学工业的特点之一就是,煤、石油、天然气等,既 石油、天然气等, 是化学工业的能源又是化学工业的原料。化学工业成为工 是化学工业的能源又是化学工业的原料。 业部门中的第一用能大户。 业部门中的第一用能大户。 节能就是应用技术上可行、经济上合理、环境和社会 节能就是应用技术上可行、经济上合理、 可以接受的方法,来合理有效地利用能源。节能并不是少 可以接受的方法,来合理有效地利用能源。 用能源,而其实质是充分有效地发挥能源的作用。 用能源,而其实质是充分有效地发挥能源的作用。 节能潜力有两种:一种是节能总潜力;二是可实现的 节能潜力有两种:一种是节能总潜力; 节能潜力。前者是技术极限值,重点讨论可实现的节能潜 技术极限值, 节能潜力。前者是技术极限值 力。
分离工程
1.3节能的途径 1.3节能的途径 能耗水平是由自然条件、经济体制、经济因素、 能耗水平是由自然条件、经济体制、经济因素、管理 水平、政策倾向、社会因素、技术水平及人的观念等有关。 水平、政策倾向、社会因素、技术水平及人的观念等有关。 将这些因素归纳为结构节能、管理节能和技术节能。 将这些因素归纳为结构节能、管理节能和技术节能。 结构节能:产业、产品、企业、地区结构等。 结构节能:产业、产品、企业、地区结构等。 管理节能:宏观调控和企业经营管理。 管理节能:宏观调控和企业经营管理。 技术节能:工艺节能(分离工程、反应工程)、流程 技术节能:工艺节能(分离工程、反应工程)、流程 )、 节能、化工单元操作设备节能( 节能、化工单元操作设备节能(泵、压缩机、换热设备、 压缩机、换热设备、 蒸发设备、塔设备、分离设备等) 系统节能( 蒸发设备、塔设备、分离设备等)及系统节能(从宏观系 统合理用能的角度出发,所进行的节能工作)。 统合理用能的角度出发,所进行的节能工作)。
分离工程 3技术节能途径
3.1工艺节能 工艺节能 就是通过选择和设计合适的分离过程来节能, 就是通过选择和设计合适的分离过程来节能,包括选 择合适的分离方法与分离助剂。 择合适的分离方法与分离助剂。 研发更加高效的分离工艺也是节能的重要途径。举例: 研发更加高效的分离工艺也是节能的重要途径。举例: 二氧化碳的脱除,热碳酸钾法--NHD。 二氧化碳的脱除,热碳酸钾法-- -- 。 采用多种分离过程的组合可以比只采用一种分离方法 过程能耗低,但往往以增加设备投资为代价。 过程能耗低,但往往以增加设备投资为代价。但只要总体 来讲经济效益明显,就可采用。桔皮直接干燥;压榨-- 来讲经济效益明显,就可采用。桔皮直接干燥;压榨-- 多效蒸发--干燥空气再利用等。 多效蒸发--干燥空气再利用等。 --干燥空气再利用等
分离工程
能源是经济发展的源动力,是现代文明的物质基础。 能源是经济发展的源动力,是现代文明的物质基础。 由于能源消费急剧增加,造成能源供应紧张; 由于能源消费急剧增加,造成能源供应紧张;容易被 利用的能源资源有限, 利用的能源资源有限,世界各国都在寻求各种方法更加有 效地开发和利用能源。 效地开发和利用能源。 能源的分类方法很多, 来源分为来自地球以外天体 能源的分类方法很多,按来源分为来自地球以外天体 的能量(主要是太阳,煤炭、石油、天然气、水能、 的能量(主要是太阳,煤炭、石油、天然气、水能、风能 及海洋能)、地球本身蕴藏的能量(地热能及原子核能) 及海洋能)、地球本身蕴藏的能量(地热能及原子核能) )、地球本身蕴藏的能量 及地球与其它天体之间相互作用而产生的能量(潮汐能); 及地球与其它天体之间相互作用而产生的能量(潮汐能); 转换和利用层次分为一次能源 自然界存在)、 分为一次能源( )、二次能 按转换和利用层次分为一次能源(自然界存在)、二次能 源(电、蒸汽、煤气、焦炭等)及终端能源;按使用状况 蒸汽、煤气、焦炭等)及终端能源; 分为常规能源和新能源;清洁能源和非清洁能源。 分为常规能源和新能源;清洁能源和非清洁能源。
分离工程
节能的意义: 节能的意义: 节能是保持人类社会可持续发展的重要措施, 节能是保持人类社会可持续发展的重要措施,科学发 展观的内涵:以人为本,全面、协调、可持续发展。 展观的内涵:以人为本,全面、协调、可持续发展。 的内涵 节能有利于环境保护。(灰尘、硫有其它污染物) 节能有利于环境保护。(灰尘、硫有其它污染物) 。(灰尘 节能也就意味着节省宝贵的化工原料(资源)。 节能也就意味着节省宝贵的化工原料(资源)。 节能可促进生产。(生产更多的产品) 节能可促进生产。(生产更多的产品) 。(生产更多的产品 节能可降低生产成本,增加利润,提高企业竞争力。 节能可降低生产成本,增加利润,提高企业竞争力。 节能可促进管理的改善和技术的进步。 节能可促进管理的改善和技术的进步。