汽车工装夹具设计一般流程
工装治具的设计与制作及管控流程

工装治具的设计与制作及管控流程1 目的将工装治具用于生产助定位作业,使生产之工序顺畅,防止制程之问题发生,确保生产顺利,提高生产效率,从而满足客户的品质要求,且达成公司的质量目标。
2 适用范围适用于建荣公司生产之制程。
3 治具设计的工作及注意事项3.1 明确了解工艺规程及产品效果图而设计治具之目标,应明确产品的生产性,根据设计策划、工艺规程和产品图纸进行设计。
务必注明产品的零件号、工件穴号、治具名称、制造的数量、要用的型号和规格以及其它特殊说明。
根据工艺规程可以了解工件的定位基准和夹紧面、本工序详细的加工要求、原始尺寸及技术条件和公差、加工余量、定位基准的精度和光洁度、工件的材料硬度和处理、以及表面处理的情况等。
务必了解各工序之间的相互关系,如在本工序之前的有关表面的尺寸和光洁度等。
根据产品图纸可以了解工件的全貌及尺寸,各个表面化的尺寸精度、光洁度及技术条件、检查工艺规程所规定的要求是否正确合理,确认治具状态。
3.2 确定设计方案就是根据生产性,所用的设备,工件的技术要求和使用要求,来确定治具的结构型式。
在考虑设计方案时,一般应依照下列要求:1)确定定位方式,包括确定定位之工件的结构及工件排位/排模之间距(一般来说,定位基准是工艺人员按产品之工艺要求指定的,必须注意治具上的产品在喷漆过程中要喷到油漆,但喷漆人员和治具的设计人员共同检讨提出好的意见)。
2)确定夹紧力的方向和作用点。
3)确定动力来源.4)确定单件夹紧还是多件夹紧。
5)确定单工位还是多工位。
6)根据上述几点方案,选择合适的夹紧装置和结构。
4 定位基准的选择4.1、在定位时,每个工件在治具中的位置是不确定的,对同一批工件来说,各件的位置也将是不一致的。
工件位置的这种不确定性,工件有几个自由度,沿坐标轴的移动自由度和绕坐标轴的转动自由度。
未定位前的工件是自由体,因此,为了使工件在治具中有一个正确位置,必须对影响工件加工表面位置精度的自由度加以限制。
(完整版)汽车焊装夹具设计
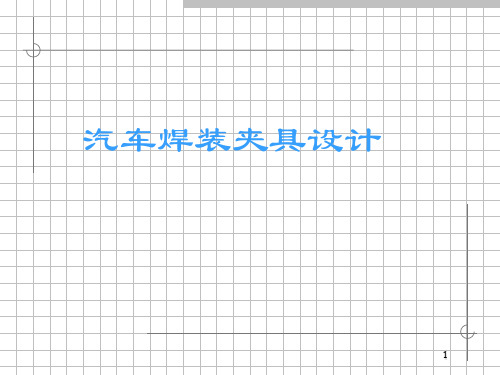
热处理
HRC40-45 HRC40-45 HRC40-45
HRC40-45
21
四、零件加工流程
名称
规格
LOCATE PIN (定位小 工件,与环形磁铁 MGI-RI结合使用)
BASE HANGER
TURNING DEVICE
TURNING BLOCK
旋转
腔体
LIFTER COVER
LIFTER JOINT
18
四、零件加工流程
3)加工前的二次验证 (1)工件与编程所用的图纸是否一致 (2)工件原点是否与编程一致 (3)加工时正面与反面所用的坐标是否一致 (4)打孔时所使用的刀具是否是程序所用刀具 4)加工后的验证 检查完成情况与图纸是否一致,有无遗漏。
19
四、零件加工流程
2、加工标准
工件名称
项目
BASE
引出单元中的序号,整理单元的零 部件明细表,展开明细表中的部件, 整合相同的零件,并对标准件和国 标件进行说明。
过滤明细表,完成零件图的明细表 设置。
13
三、二维转图及尺寸标注
2、尺寸标注 夹具总图上应标注:夹具轮廓尺寸、操作高度、卡
兰线(应该与汽车坐标线统一)、坐标基准、坐标 基准孔、各部件的安装位置、气缸位置、所有定位 尺寸坐标基准孔应相对于坐标线标注。出图内容包 括三向视图及轴测图。 单元中的非标件需要出零件图,并标注公差、表面 加工精度等相关技术要求。 一般要求:加工型面不得超过±0.07mm
并使图形处于正视图方向。 完成主视图的二维转化,再选择转
化其他方向视图及轴侧图。 选择要转化的零件并激活,将非标
准件转化为二维视图。 调入标准图框,将视图装入标准图
框中。
汽车工装夹具设计标准

工装夹具设计标准版次:OR目录一、底板1、夹具底板要求采用Q235-A板材和型材焊接而成,底板的焊缝采用非连续焊缝,焊缝高度为5mm,焊缝长度大于600mm采用间断焊,每条焊缝长度不小于125mm,焊缝总长度不小于焊接总长度的1/2.焊缝要求牢固,光滑平整,不允许有夹渣、气孔等缺陷,底板焊接后应经热处理退火消除应力.2、夹具的底板加工后的厚度为20~30mm;注意:为了方便运输,底板的宽度尺寸应小于2200 mm 底板周边的槽钢开口向外,中间加强用的槽钢间距不宜大于1000mm.3、长度尺寸L<1280mm,宽度尺寸B<500mm 或台面面积<0.64平方米,底板加工后的厚度为20mm,槽钢为10号槽钢;脚轮选用∶科顺4-4109-929-BRK4和4-4108-929承重1080公斤.4、长度尺寸1280≤L<1600mm,宽度尺寸500≤B<700mm 或0.64平方米<台面面积<1.12平方米,底板加工后的厚度为20mm,槽钢为14b号槽钢;脚轮选用∶科顺4-5109-929-BRK4和4-5108-929承重1360公斤.5、长度尺寸1600≤L<2000mm,宽度尺寸700≤B<800mm 或1.12平方米<台面面积<1.6平方米,底板加工后的厚度为25mm,槽钢为16号槽钢;脚轮选用∶科顺4-6109-929-BRK4和4-6108-929承重1640公斤或7-10609-979-BRK1和7-10608-979承重5448公斤.6、长度尺寸L>2000mm 或台面面积>1.6平方米,底板加工后的厚度为30mm,槽钢为20号槽钢.7、如果是旋转夹具,则底板采用60mm 60mm 5mm的方钢管.8、如果是涂胶架,则采用50mm 50mm 4mm的方钢管.9、底板的上表面即安装基准面的平面度为IT8级,表面粗糙度.10、底板的加工基准边基准边一般长60mm,宽5mm.设计布置图如下:11、底板上测量基准孔主要是三座标检测用设计形式如下:其中3-φ10H7的基准孔为通孔,3-φ30的沉头孔深2mm.加工时应随底板的安装基准面一次性加工而成.基准孔至少要三个,它的布置必须是非直线,而且形成的三角形的区域尽量大,应该布置在支撑块的支座形成的多边形的外部,同时应考虑三座标在夹具装配完成后检测探头的可接近性.12、底板的安装基准面上若需刻坐标网格线,坐标网格线的深度0.2 mm,宽度线距为100或200mm,并在刻线的两端刻上坐标号,坐标号应与汽车产品图上的坐标号相一致.根据客户需求13、底板上应最少有横竖各一条测量基准槽,其截面宽度为10 mm 、深度为5 mm、一边为直角的倒梯形槽当边长大于2米时应平行对称布置两条,间距一般为1米.根据客户需求设计图示如下:14、安装螺钉如无特殊要求均采用级内六角螺钉.15、吊环螺钉:当夹具重量小于1吨时用M16;1~2吨时用M24;2吨以上用M30 底板上仅制孔,不装吊环螺钉.二、调平机构16、底板固定在地面的方式有可调式地脚螺钉.17、在任何情况下,采用的各种固定方式都不能引起设备的几何精度发生变化.18、在一些手动设备特殊的情况下,可以采用1个支撑的固定方式.19、对于底板尺寸小于 1.2m 1.2m,需要使用3个支撑,并且足够保证固定.3个支撑的布置采取三角形,以保证设备的最佳稳定性.20、对于底板尺寸超过1.2m1.2m,选取支撑的规则如下:尺寸在1.2m和2m内————————————————— 4支撑尺寸在2m和4m内—————————————————— 6支撑优先选用“通用标准库”中的TOPZ0001/TOPZ0002/TOPZ0003、TOPZ1003/TOPZ2003各种高度的支承座或L形安装座或支承过渡座.四、基准球座及测量安装座1、优先选用“通用标准件库”中的TOPC0002/TOPR0002.2、基准球座至少要三个,应该布置在支撑块的支座形成的多边形的外部.它的布置必须是非直线,而且形成的三角形的区域尽量大.3、基准球座也不能布置在机器人焊钳或手工焊钳的运动轨迹上.4、测量安装座的布置应保证ROMER可接近,且不与焊钳,焊钳的吊挂装置等发生干涉,数量根据具体夹具形式来定.“通用标准件库”中备有ROMER的模型,可进行检测位置的模拟.5、在一些情况下, 如果夹具允许,测量球可直接布置在底板上如:包边设备,样架等.五、调整垫a)优先选用“通用标准件库”中的TOPD.b)调整垫的理论设计厚度和数量一般根据客户的需求而定.如神龙汽车有限公司焊接夹具一般要求一组调整垫的数量不能多于3片c)调整垫的常用规格为:、、、1、2、4、5mm.1、使用导向板是为了防止放错工件小件 ,便于装件等.工件边缘与导向板之间的距离为2mm,导向板的调整范围为±5mm,工件刚好脱离定位销时,靠近导向板的工件边缘规定为导向板的弯曲位置.2、焊钳导向处的材料为铬锆铜CuCrlZr,同时要考虑焊钳导向板和支座之间的绝缘;即加绝缘垫和绝缘套筒等推荐板厚:最小16mm手持移动式焊点导向板由于要减轻焊点导向板的重量,推荐使用CESTILENE HD 1000R苹果绿色材料;推荐板厚:最小20mm焊钳导向板示意图焊钳导向板导槽优先选用V形,也可采用U形.在V/U形槽边缘加工530°导角作为预留磨损量一般为5mm左右 .绝缘垫和绝缘套筒的材料一般采用不易破碎的胶木,推荐使用树脂胶木.固定式焊钳导向板一般安装在装配钢板的下面,与钢板表面平行,距离为2-5mm.七、限位块推荐选用U形限位块,用于大翻板或者定位销、螺柱导套等处,定位精度比较高,且重复定位比较稳定.既可保证夹紧后压头与支承块的间隙,也可在夹紧部件倾斜布置时,保证压头的几何位置.参考“通用标准件库”的TOPX.八、绝缘垫片材质为尼龙10101、优先选用“通用标准件库”中的TOPJ2、绝缘垫片有M6、 M 8两种垫片M6螺栓绝缘套代码为TOPJ1001-H=H=8、10、12、18四种规格M8螺栓绝缘套代码为TOPJ2001-H=H=10、12、18、20四种规格φ8销绝缘套代码为TOPJ2001-H=H=10、12、16、18、20五种规格九、可调机构一定位销1、与主定位销不平行的定位销必须采用伸缩销.2、优先选用“通用标准件库”中定位销TOPDX.3、定位销工作表面形式:圆柱形、菱形、削扁、带缺口如下图4、选用材料:20Cr热处理:渗碳淬火,渗碳深度1.2mm直径小于12mm-1.5mm直径大于12mm,表面硬度要求HRC48-52.5、装在磁场内的定位销选用材料为不锈钢,仅对工作表面进行渗氮处理;6、定位销直径:主定位销直径=定位孔名义直径-0.2mm辅定位销直径=定位孔名义直径-0.5mm定位销的加工公差: 0 /-7、定位销的工作表面:定位销截面可以是圆形、菱形、削扁或圆形带缺口的.如下图二定位销座定位销座推荐的形式,如下图:定位销直A B C D E *F I R S T U 2012903095,202047,515161420 40209540117,203047,520262240 60301140117,303057,5252632△注意:定位销座销孔不得为盲孔.三设计形式定位销设计安装形式应为二维或三维可调型.十、压头和支撑块1、厚度- 18 ± 1 mm.- 最小 37 +1/0 mm------用于与外观零件接触的支撑块和夹紧器压头门外板,顶盖,等....支撑块和压头的厚度相同.2、材料42 CrMo ,热处理方式:工作表面采用淬火淬火深度:2 mm,表面硬度可达到HRC 55.对于外观零件的压头如:侧围,门,顶盖…在现场调试后进行热处理,火焰淬火和水冷却.3、特殊情况接触铝制零件的压头和支撑块:- 表面抛光: Ra 0,2 mm- 周边圆角: r 5 mm 仅对厚度 37 mm .4、压头压紧方式1压头的压紧力一般要求垂直于工件的厚度方向.具体如下图:1个锁止自由度 2个锁止自由度2夹紧器正常情况下夹紧钢板,压头所允许的最大倾角15°.5、支撑块和压头的可调支撑块设计时应确保在功能方向的一维或二维可调,特殊情况可设计为三维可调,另外在设计支撑块或压头时应尽可能选取平面处,尽量不要选取复杂的型面做为定位支撑面.压头与压紧臂在设计时应尽可能分开可调,不要做成一体.十一、外购件的选择1、脚轮向荣、科顺;无油轴套嘉善;电机采用SEW或FLANDER产品;2、气缸类1常用的气缸有:普通型、封闭式、耳环式、销钉缸四种.一般选用SMC公司的产品特殊情况下也可选用FESTO的气缸,比如要求单独发信号时.若客户无要求,可选用国产气动元件品牌:如烟台FAST等耳环式夹紧气缸优先选用CK1A型.吊具气缸采用锁紧气缸CAN系列和CLS系列.行程超过400mm的气缸必须安装防尘护套.2CNOMO标准缸的选用原则:客户要求;一个零件上有多个方向和多个支撑,尤其是在装焊厚度较厚的零件时.3、手动夹紧器GOOD HAND ;优先选用:GH-701-D, GH-701-K, GH-702-D, GH-702-K;GH-304-CM, GH-305-CM, GH-304-EM, GH-305-EM, GH-304-HM, GH-305-HM.十二、钢板间隙1、一般情况e≤ 1.5mm焊接: 压头/支撑块间的间隙 =标准厚度e 1+ 6% +0其中标准厚度e=压头和支撑块之间所有零件的厚度之和2、包边:包边机的理论厚度凹模和镶块间=标准厚度 1+ 6% ++其中标准厚度e=凹模和镶块间之间所有零件的厚度之和3、板厚较厚零件e>1.5 mm压头/支撑块间的间隙 =标准厚度e 1+ 6% +0其中标准厚度e=压头和支撑块之间所有零件的厚度之和十三、焊接夹具的通用公差1、支撑面,压头和定位块的公差 : ± 0,20 mm2、固定和活动定位销的公差在带气压的工作条件下 : ± 0,10 mm 参照零件的位置.3、底板的参考坐标点 : 平行度 = 0,05 mm 在共同的区域.4、对于焊接设备上同时加工几个部件的情况,它们之间定位销,支撑面的最大偏差不超过 0,20 mm .5、焊接或其他方式的底板的平面度和曲率,在长度小于1000时最大不超过0,05,在长度大于1000时最大不超过0,1 .验收的必要条件:至少有4个支脚. 供应商负责提供所需的布置以满足这个条件.6、水平面上定位孔与定位孔之间的公差为±0.02mm,粗糙度为.7、所有的定位孔与基准面的公差为±0.05mm,粗糙度为.8、翻转机构的重复到位精度为±.9、精度孔的同心度、平行度、垂直度的精度容许误差在0.02mm以下.十四、焊接检具的通用公差1、通用公差 :± 0.20 mm2、定位基准支撑和定位销的位置公差:± 0,10 mm3、基准平台的平行度:= 0,05 mm4、对于同一规格型号的多个检具,它们之间的偏差不能超过0.20 mm.5、焊接的机器检测平台或其它平台的平面度及平整度,长度小于1000的,最大不得超过0,05;长度超过1000的,最大不得超过0,1.检测平台用4脚支撑.必须遵守验收条件.6、用于建立车身坐标系的基准小球:球度:0.05mm,基准球空间位置度:0.1mm.7、基准球位置坐标值的确定方法:用定位元素拟合车身坐标系,在此拟合坐标系中确定基准球位置坐标值,作为基准球的理论坐标值.在以后的所用过程中,使用基准球心理论坐标值建立车身坐标系.十五、制图(一)尺寸标注要求设计基准和加工基准统一的原则.(二)图幅图面一般用A3、A4两种图幅,必要情况下可用更大图幅.A3图纸采用横向,A4图纸采用竖向.(三)各种安装面及非安装面光洁度的要求一般安装面的表面光洁度至少,非安装面的光洁度为,底板上大的非安装面达到即可.(四)各种材料热处理技术要求:1 45钢调质处理技术要求:1、热处理:HB220-2502、未注形位公差按照 GB/T1184-H3、未注线性公差按照 GB/T1804-m4、孔口、锐边倒角 1×45°5、表面发黑2 45钢淬火处理技术要求:1、热处理:HRC40-452、未注形位公差按照 GB/T1184-H3、未注线性公差按照 GB/T1804-m4、孔口、锐边倒角 1×45°5、表面发黑3 Q235钢焊接技术要求:1、本件为焊接件,焊接质量符合机械工程用焊接标准2、型材表面为非加工面3、焊后非加工面,焊接加工至.4、未注焊缝均为连续焊缝,焊缝高度5mm,焊缝长度大于600mm时采用间断焊,每条焊缝长度不小于125mm,焊缝总长度不小于焊接总长度的1/25、焊接无缺陷,牢固,焊后打磨,焊缝光滑6、焊后退火消除焊接应力7、未注形位公差按照 GB/T1184-H8、未注线性公差按照 GB/T1804-m9、孔口、锐边倒角 1×45°10、非工作表面喷底漆防锈漆及面漆4 底板孔位图通用技术要求:1、底板基准A上以相互垂直的基准B、C为基准刻出座标网络线,网络线的间距100±,线深,线宽,网格间的平行度和垂直度的允差为,在网格线对应位置标记座标号;2、螺纹孔与螺纹孔、螺纹孔与销孔的尺寸公差为±;销孔与销孔之间的尺寸公差为±;销孔与基准面之间的尺寸公差为±;与基准边的角度公差为±5′.3、锐边倒钝5 20Cr材料技术要求:1、渗碳淬火1.5mm,HRC48-522、未注形位公差按照 GB/T1184-H3、未注线性公差按照 GB/T1804-m4、锐边倒角 1×45°5、表面发黑五图样与工件在图纸中的表达方式要求总图、部件图上应标注:夹具轮廓尺寸、操作高度、坐标线尽量与汽车坐标线统一、坐标基准、坐标基准孔、各部件的安装位置、汽缸位置、所有定位尺寸坐标基准孔应相对于坐标线标注,在图中按汽车产品件在汽车中的实际位置建立汽车坐标;同时按夹具的基础建立坐标系.在夹具上有产品图的摆放位置,并用细双点划线绘出.设计时应注意焊点的坐标位置,必须留有充分的焊钳工作空间位置,便于施焊.用双点划线表示焊钳的外形.六、左右对称件制图的原则一般左右对称件,仅绘制右件图,在2D图中注明“注:TOP--右件图号如图所示,TOP--左件图号与之对称”.七、常用材料及标准件对应的国标号Q235-A GB/T 700-1988 热轧槽钢GB/T 707-1988热轧钢板和钢带 GB/T 709-1988 热轧扁钢 GB/T 704-1988热轧圆钢、方钢 GB/T 702-1986、GB/T 705-1989热轧等边角钢GB/T 9787-1988 热轧不等边角钢GB/T 9788-1988结构用和输送流体用无缝钢管 GB/T 8162-1999内六角螺钉 GB/T 内六角平端紧定螺钉 GB/T 77-2000六角头螺栓全螺纹 GB/T5783-2000 吊环螺钉 GB/T 825-1988平垫圈 GB/T 弹簧垫圈 GB/T 93-1987内螺纹圆柱销 GB/T十六、夹具编号原则T O P0713-001000即:TOP0713-0010002007年公司所接的第13个项目中的第一个分项夹具总图T O P0713-027000第27个分项夹具总图T O P0713-027100第27分项夹具的 100组件图120组件图 120150组件图 150160组件图 160T O P0713-027120120组件中的部件图 121122123对于夹具中的水、电、气部分图及目录分配图号为:001—— 020具体分配号参照部门设计编号标准底板分配号为:025—— 050。
拨叉工艺规程及铣端面的工装夹具设计
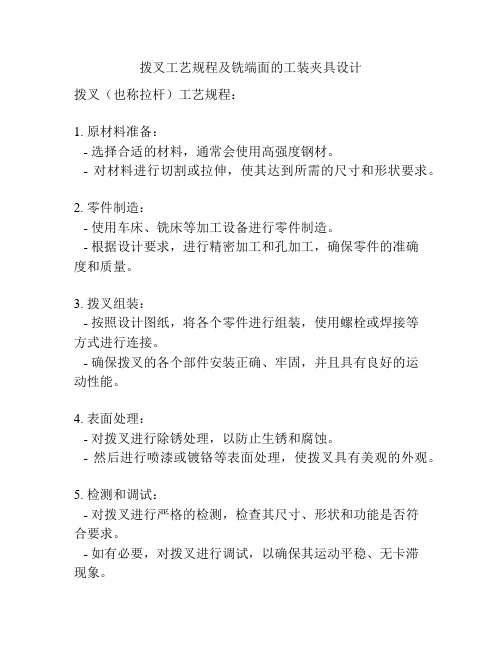
拨叉工艺规程及铣端面的工装夹具设计拨叉(也称拉杆)工艺规程:1. 原材料准备:- 选择合适的材料,通常会使用高强度钢材。
- 对材料进行切割或拉伸,使其达到所需的尺寸和形状要求。
2. 零件制造:- 使用车床、铣床等加工设备进行零件制造。
- 根据设计要求,进行精密加工和孔加工,确保零件的准确度和质量。
3. 拨叉组装:- 按照设计图纸,将各个零件进行组装,使用螺栓或焊接等方式进行连接。
- 确保拨叉的各个部件安装正确、牢固,并且具有良好的运动性能。
4. 表面处理:- 对拨叉进行除锈处理,以防止生锈和腐蚀。
- 然后进行喷漆或镀铬等表面处理,使拨叉具有美观的外观。
5. 检测和调试:- 对拨叉进行严格的检测,检查其尺寸、形状和功能是否符合要求。
- 如有必要,对拨叉进行调试,以确保其运动平稳、无卡滞现象。
铣端面的工装夹具设计:1. 确定夹具类型:- 根据铣削端面的形状和尺寸,选择合适的夹具类型,如机械夹具、气动夹具等。
2. 设计夹具结构:- 根据铣削端面的特点和工艺要求,设计夹具的结构。
- 确定夹具的定位装置、夹紧装置和支撑装置等部件,并确保其具有足够的刚性和稳定性。
3. 定位装置设计:- 根据铣削端面的形状和尺寸,设计合适的定位装置,以确保工件在夹具中的准确定位。
- 可使用V型槽或定位销等装置来实现准确定位。
4. 夹紧装置设计:- 根据铣削端面的形状和尺寸,设计夹紧装置来夹紧工件。
- 可使用夹紧螺钉、夹紧卡等装置,并确保夹紧力均匀、稳定。
5. 支撑装置设计:- 为了防止工件在铣削过程中发生振动或变形,设计适当的支撑装置。
- 可使用支撑块、支撑杆等装置,并确保其对工件施加适当的支撑力。
6. 安全考虑:- 在夹具设计中,必须考虑到安全因素,确保夹具的使用过程中不会对操作人员或设备造成危险。
- 可使用防护罩、安全开关等措施来提高安全性。
以上是拨叉工艺规程及铣端面的工装夹具设计的概述,具体的规程和设计细节可以根据具体情况进行调整和补充。
汽车零部件制造工艺流程简介
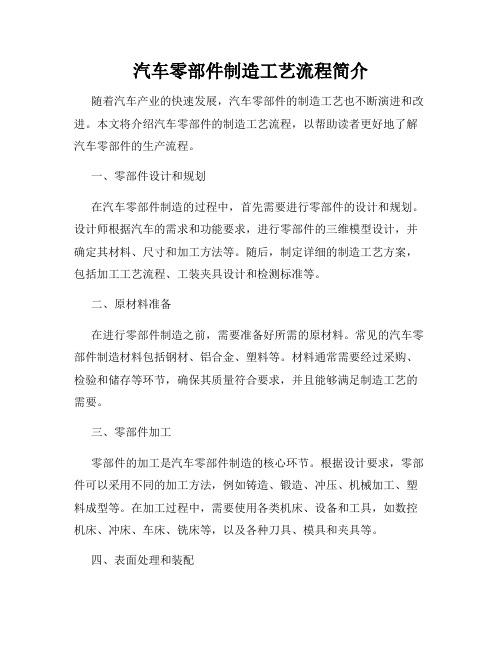
汽车零部件制造工艺流程简介随着汽车产业的快速发展,汽车零部件的制造工艺也不断演进和改进。
本文将介绍汽车零部件的制造工艺流程,以帮助读者更好地了解汽车零部件的生产流程。
一、零部件设计和规划在汽车零部件制造的过程中,首先需要进行零部件的设计和规划。
设计师根据汽车的需求和功能要求,进行零部件的三维模型设计,并确定其材料、尺寸和加工方法等。
随后,制定详细的制造工艺方案,包括加工工艺流程、工装夹具设计和检测标准等。
二、原材料准备在进行零部件制造之前,需要准备好所需的原材料。
常见的汽车零部件制造材料包括钢材、铝合金、塑料等。
材料通常需要经过采购、检验和储存等环节,确保其质量符合要求,并且能够满足制造工艺的需要。
三、零部件加工零部件的加工是汽车零部件制造的核心环节。
根据设计要求,零部件可以采用不同的加工方法,例如铸造、锻造、冲压、机械加工、塑料成型等。
在加工过程中,需要使用各类机床、设备和工具,如数控机床、冲床、车床、铣床等,以及各种刀具、模具和夹具等。
四、表面处理和装配在零部件加工完成后,往往需要进行表面处理,以提高其性能和表观质量。
表面处理的方法包括镀铬、热处理、喷涂、电泳涂装等。
这些处理方法能够增加零部件的耐腐蚀性、耐磨性和装饰性。
随后,根据需要,零部件可能需要进行装配工艺,即将不同的零部件组装成完整的汽车零部件。
五、质量控制和检测在汽车零部件制造过程中,质量控制和检测是必不可少的环节。
制造厂商会制定严格的质量控制标准,确保零部件的质量符合设计要求和客户需求。
同时,生产过程中会进行各种检测手段,如尺寸测量、材料分析、硬度测试和功能测试等,以及非破坏性检测方法,如超声波检测和X射线检测等,以确保零部件的质量和可靠性。
六、包装和出厂最后,经过质量控制和检测的零部件会进行包装,并准备出厂。
包装通常根据零部件的特点和运输方式进行选择,以保证零部件在运输过程中的安全和防护。
零部件出厂后,会按照订单和合同进行交付,以供汽车厂商进行装配和生产。
夹具设计流程概要

工装夹具设计流程
Locating principle for FAW-VW product design关于FAW-VW产品的定位原则:
• 4. 定位销法向定位,沿产品坐标系三维调整,定位销轴线角度<3°角的可以忽略。定位块型面 角度>15°要二维调整。
• The locating direction of locating pin should be consistent to the part‘s normal and can be adjusted in three directions。The locating surface with an angle of over 15°to the part‘s surface shoule be adjusted in two directions。
17
上海德珂斯机械自动化技术有限公司
工装夹具设计流程
夹具设计案例2(Fixture case 2):
NMC project Rear door GEO fixture.
1 manual X gun and 1 manual C gun weld 44 welding points. 19 Units. 1 operator.
9、定位销及其基座三维可调、定位型面二维可调,调整垫片按通用标准。
14
上海德珂斯机械自动化技术有限公司
工装夹具设计流程
九、设计人员对气缸的常提问题
1、气缸的重复精度是多少? 气缸的重复精度见下:
‘a’方向公差±0.1 ‘b’方向公差±0.05 ‘c’方向公差±0.05 夹紧位置的角度公差为 ±10’ ,负载过长会导致定位块或夹紧块超 出正常调整范围之外.
The disposal of locating and clamping point obey the FAW-VW design principle——RPS locating reference system,all the locating and clamping points use the RPS points as possible;The main benchmark are RPS H and F,RPS 1H and 1F are the first main benchmark。
工装研发流程
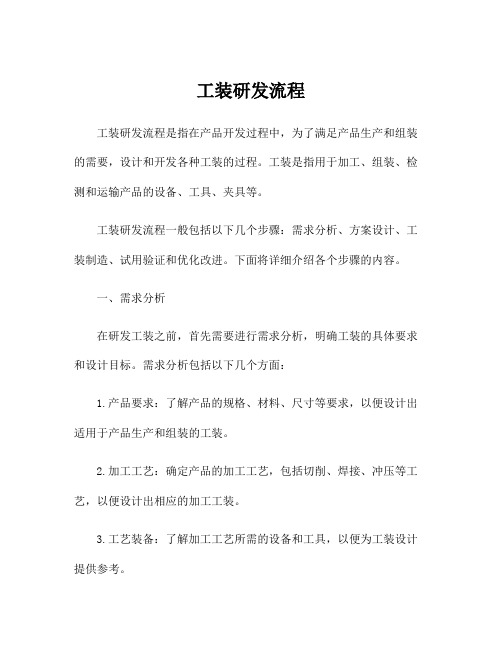
工装研发流程工装研发流程是指在产品开发过程中,为了满足产品生产和组装的需要,设计和开发各种工装的过程。
工装是指用于加工、组装、检测和运输产品的设备、工具、夹具等。
工装研发流程一般包括以下几个步骤:需求分析、方案设计、工装制造、试用验证和优化改进。
下面将详细介绍各个步骤的内容。
一、需求分析在研发工装之前,首先需要进行需求分析,明确工装的具体要求和设计目标。
需求分析包括以下几个方面:1.产品要求:了解产品的规格、材料、尺寸等要求,以便设计出适用于产品生产和组装的工装。
2.加工工艺:确定产品的加工工艺,包括切削、焊接、冲压等工艺,以便设计出相应的加工工装。
3.工艺装备:了解加工工艺所需的设备和工具,以便为工装设计提供参考。
4.产能需求:确定产品的生产数量和周期,以便设计出能满足生产需求的工装。
5.质量要求:了解产品的质量要求,包括尺寸精度、表面光洁度等,以便设计出符合质量要求的工装。
二、方案设计在需求分析的基础上,进行方案设计。
方案设计需要考虑到工装的结构、功能、材料和制造工艺等方面。
具体包括以下几个步骤:1.结构设计:设计工装的整体结构,包括固定装置、夹具、支撑结构等,以便保证工装的稳定性和可靠性。
2.功能设计:确定工装的具体功能,包括定位、夹持、传递等功能,以便满足产品生产和组装的需求。
3.材料选择:选择适合工装的材料,包括金属、塑料、橡胶等,以便满足工装的强度、刚度和耐磨性等要求。
4.制造工艺:确定工装的制造工艺,包括数控加工、成型、焊接等,以便保证工装的加工精度和质量。
三、工装制造在方案设计完成后,需要进行工装的制造。
具体包括以下几个步骤:1.零部件制造:根据方案设计,制造各个工装零部件,包括机械零件、电气元件等。
2.组装调试:根据方案设计将各个零部件进行组装,并进行调试,以保证工装的稳定性和性能。
3.表面处理:对工装的表面进行处理,包括喷涂、镀铬等,以便提高工装的耐磨性和美观度。
4.配件采购:采购工装所需的配件和紧固件,确保工装的正常运行。
焊装夹具设计

四、零件加工流程
5.检测方法 夹具的装配需要用到较多测量工具和测量方法,
我们对一些常用的检测方法归类如下: 利用高度尺来检测型面的位置,销距,画线等。 利用验距台来检测销空距离 利用游标卡尺检测板厚,两面间的距离以及深度 利用万能角度尺测量角度及距离 利用角尺来测垂直和定位 利用千分尺来测量直径 利用便携式三坐标检测装配精度 利用固定式三坐标检测、画线
2、根据设计纲领、数模|、产品图、参考车工艺、 焊接工艺流程,初步确定夹具数量;
3、根据工艺路线、夹具数量进行工艺平面布置图 的设计;
4、初选焊钳图库; 5、工位节拍、安全管理及详细工艺方案; 6.物流要求。 夹具公司根据整车厂提供资料将完成夹具的设计制 造,如下图所示
3
一、工艺分析流程
数模
焊接图、涂胶图等
7
二、夹具三维建模
首先根据车身三维数模截取零件截面, 然后将零件截 面图读入到夹具设计单元中。 结合设计基准书、夹具夹持方案、MLP、MCP分析 单元数量及分布方向, 夹具操作高度、控制方式, 各 单元定位销的类型、定位面的组成、压紧方式分析 确定各单元的结构组成部件, 选用标准件、国标件的 类型及数量。 设置软件参数后, 进入标准件库, 选择合适的标准件, 包括压块、定位块、定位销托、气缸等。 完成标准件选择后, 进入到草图平面, 绘制非标件, 包 括GAUAGE、CLAMP及自制件等 。 改变气缸的尺寸约束, 检查夹具的干涉情况。
LIFTER LOCK
LIFTER SHAFT
TEMPLATE
材料 20Cr
Q235-A 45 HT200
Q235-A Q235-A Q235-A 45 45
热处理 渗碳(渗碳深度0.5-0.8)表面淬 火HRC58-60
汽车制造工程的核心技术及四大工艺流程开发体系

总装工艺虚拟验证
总装工艺设计输入
工艺开发输出
产品概念报告
VBOM
三维数模
二维装配图
装配技术要求
总装工艺开发的主要内容
生产性核心工艺装备
阶梯增长的生产性核心工艺装备的建设投入: 装配厂的工具与输送系统 冲压设备与模具 焊装夹具 涂装设备
$
制造体系是汽车制造企业的核心动力. 制造战略是汽车企业运营战略中最重要部分之一. 制造成本是汽车企业的最主要的成本之一. 制造的固定资产是汽车企业的最大投资之一. 制造的柔性是汽车企业的柔性. 制造的人力资源占公司的总资源的70%.
产品设计输入
冲压工艺规划
冲压工艺设计
冲压工艺虚拟验证
工艺开发输出
冲压工艺虚拟验证
冲压工艺开发的主要内容
产品概念报告
冲压件质量标准
工艺设计标准
DL图
工艺数模
冲压制造要求
……
焊装工艺开发的主要内容
焊装工艺设计
工艺开发输出
产品设计输入
焊装工艺虚拟验证
焊装工艺方案: 产能目标 焊装节拍分析报告 焊装车间物流方案 焊装线规划方案:生产纲领及生产工艺过程/生产线型式及设备选用/焊接夹具及检具开发/生产场地及面积/质量控制策略 技改方案及投资预算 项目实施的人员配置培训规划 结构性能分析报告 焊装质量目标:焊点合格率 /间隙 & 阶差合格率 /白车身合格率/白车身AUDIT分数
设计工程
工程开发与产品验证
产品概念报告
涂装质量标准
工艺设计标准
标杆三维数模
涂装工艺开发的主要内容
产品设计输入
涂装工艺设计
工艺开发输出
涂装工艺作业要求 前处理、电泳工艺要求 涂装打胶图 PVC喷涂区域图 喷漆部位设计图 涂装车间材料消耗清单 涂装新材料开发报告
夹具设计步骤

一、机床夹具设计要求1.保证工件加工的各项技术要求要求正确确定定位方案、夹紧方案,正确确定刀具的导向方式,合理制定夹具的技术要求,必要时要进行误差分析与计算。
2.具有较高的生产效率和较低的制造成本为提高生产效率,应尽量采用多件夹紧、联动夹紧等高效夹具,但结构应尽量简单,造价要低廉。
3.尽量选用标准化零部件尽量选用标准夹具元件和标准件,这样可以缩短夹具的设计制造周期,提高夹具设计质量和降低夹具制造成本。
4.夹具操作方便安全、省力为便于操作,操作手柄一般应放在右边或前面;为便于夹紧工件,操纵夹紧件的手柄或扳手在操作范围内应有足够的活动空间;为减轻工人劳动强度,在条件允许的情况下,应尽量采用气动、液压等机械化夹紧装置。
5.夹具应具有良好的结构工艺性所设计的夹具应便于制造、检验、装配、调整和维修。
二、机床夹具设计的内容及步骤1.明确设计要求,收集和研究有关资料在接到夹具设计任务书后,首先要仔细阅读加工件的零件图和与之有关的部件装配图,了解零件的作用、结构特点和技术要求;其次,要认真研究加工件的工艺规程,充分了解本工序的加工内容和加工要求,了解本工序使用的机床和刀具,研究分析夹具设计任务书上所选用的定位基准和工序尺寸。
2.确定夹具的结构方案1)确定定位方案,选择定位元件,计算定位误差。
2)确定对刀或导向方式,选择对刀块或导向元件。
3)确定夹紧方案,选择夹紧机构。
4)确定夹具其他组成部分的结构形式,例如分度装置、夹具和机床的连接方式等。
5)确定夹具体的形式和夹具的总体结构。
在确定夹具结构方案的过程中,应提出几种不同的方案进行比较分析,选取其中最为合理的结构方案。
3.绘制夹具的装配草图和装配图夹具总图绘制比例除特殊情况外,一般均应按1:1绘制,以使所设计夹具有良好的直观性。
总图上的主视图,应尽量选取与操作者正对的位置。
绘制夹具装配图可按如下顺序进行:用双点划线画出工件的外形轮廓和定位面、加工面;画出定位元件和导向元件;按夹紧状态画出夹紧装置;画出其他元件或机构;最后画出夹具体,把上述各组成部分联结成一体,形成完整的夹具。
汽车变速器操纵盖工艺及工装夹具设计

摘要本次设计的主要内容是操纵盖加工工艺规程及2.094++-φ孔钻孔夹具的设计。
操纵盖主要是用在汽车变速器上面,其主要加工表面及控制位置为长度为97的底部大端面和2.094++-φ以及825Hφ。
由零件要求分析可知,保证2.094++-φ孔的精度尺寸的同时应该尽量保证其与底部大端面的垂直度,这对于后工序装配和总成使用上来说都有重要影响。
所以,工序安排时,采取以97的底部大端面粗定位夹紧加工后,对2.094++-φ孔进行钻削加工同时成型。
因其粗糙度为Ra12.5,可通过钻、绞孔来满足。
对于钻825Hφ孔时,主要以操纵盖的97的底部大端面定位,控制其自由度,以达到加工出来的产品满足要求并且一致性好的目的。
本文的研究重点在于通过对操纵盖的工艺性和力学性能分析,对加工工艺进行合理分析,选择确定合理的毛坯、加工方式、设计高效、省力的夹具,通过实践验证,最终加工出合格的操纵盖零件。
【关键词】操纵盖加工工艺夹具设计夹具AbstractThe connecting rod is one of the main driving medium of diesel engine, this text expounds mainly the machining technology and the design of clamping device of the connecting rod. The precision of size, the precision of profile and the precision of position , of the connecting rod is demanded highly , and the rigidity of the connecting rod is not enough, easy to deform, so arranging the craft course, need to separate the each main and superficial thick finish machining process. Reduce the function of processing the surplus , cutting force and internal stress progressively , revise the deformation after processing, can reach the specification requirement for the part finally .【Keyword】Connecting rod Deformination Processing technology Design of clamping device目 录摘要 ..................................................................... 3 Abstract . (4)第一章 绪 论 (4)第二章 零件的分析 (5)2.1、零件的作用 (5)2.2、零件的工艺分析 (5)第三章 毛坯的确定以及毛坯图和零件图的绘出 (8)3.1、分析毛坯的制作以及其组成 (8)3.2、加工余量和工序、毛坯尺寸的确定 (9)第四章 操纵盖的工艺规程的设计 (10)4.1、确定定位基准 (10)4.2、工艺路线的确定 (11)4.3、选择加工设备及刀、夹、量具 (13)4.4 确定切削用量及基本工时 (13)4.4.1粗铣、精铣97,高74底部大端面 (13)4.4.2 粗铣、精铣∮32顶部端面 (13)4.4.3钻∮018.0014++底孔∮13,绞∮13孔至尺寸 (13)4.4.4钻、绞2.0094++-φ直孔 (13)4.4.5钻、绞孔至尺寸762G φ- (20)4.4.6锪平∮20凸台至尺寸 (13)4.4.7钻、攻M8X1.25-6H 螺纹孔底孔∮7,攻M8牙 (13)4.4.8粗镗、半精镗∮25H8深8孔至尺寸 (13)第五章 钻孔夹具的设计 ....................................................................................... 错误!未定义书签。
汽车行业产品开发流程
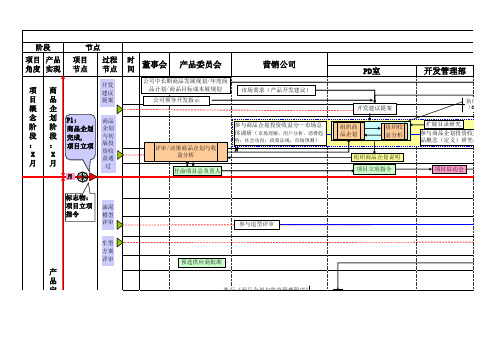
产品定
投资
义完成, 收益
项目工
分析
程启动
报告
月
标志物: 项目工程 启动指令
开
发
设
数字
计
样车
阶
段
执行《商品企划与收益管理程序》
车型方案批准 评审、决策商品 N
收益分析
Y
批准 拟定供应商批准
移行判定
组织项目策划—项目目
组
标、可行性分析]项目
织
计划、项目组织机构
详
细
投
资
收
益
分
析
整车目标成本达成活动展开
项目工程启动指令
造
B0
图
确
认
完
成
生产系统(工
厂
艺员参)
区
物
流
方
案
及
制
车
造
间
系
内
统
部
人
物
员
流
需
方
求
案
计
划
收、
运
质量门核查与确认
品质保证计划实施
外制专用
ET0样车VES评审
ET0质量核查 ET1启动品质确认
收、 运 输、 安 装、 调 试
PT车试装计划 内制件生产准备
手 模工 夹取 具样 制 造
工 装 夹 具 预 验 收 与 进 场 安全 装、 序 调取 试样
组织ET1启动确认会
: X 月
下发 开模 指令
项
ET1
目
样车
实
VES
施
评审
阶
段
OTS
P4: ET完成,
认可 完成
PT阶
工装、夹具流程
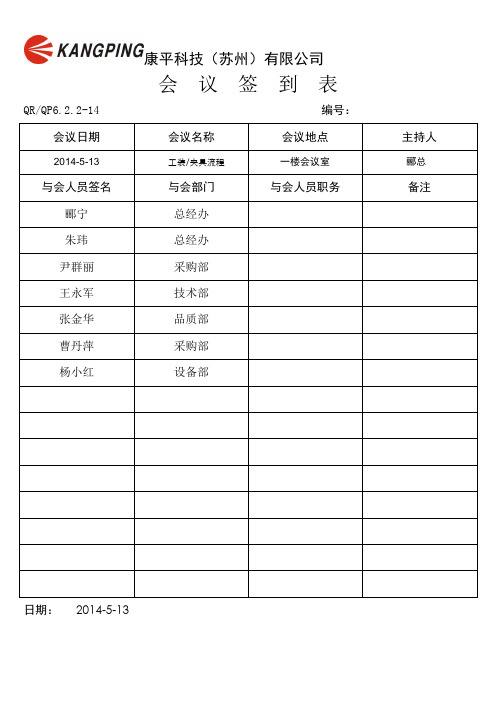
供应商还应做好售后服工作。
6.若是有老模具及测试夹具需要修改或定做,请设备部人员把相关资料准备齐全,采购部通知供应商到我司确认后并回复交期。
记录人:曹丹萍
记录日期:2014-5-13
会议内容:关于新品整套工装/夹具的流程,(从采购部接申请到工装/夹具能正常使用)
1.采购部接到设备部工装申请单(申请单需附整套外形3D图纸,整机1台)后,把相关资料发给供应商。(供应商必须办理借用手续)
2.供应商提供工装/夹具图纸到我司,采购提前一天通知到设备部,设备部安排时间及相关人员(设备,工艺,工程及供应商)确认图纸,无误后签字确认。
以上两项应在5个工作日内完成,特殊情况除外。
3.图纸确认完毕,采购把供应商回复的交期告知各部门并跟催。
4.工装完成送到我司,采购提前通知设备部,设备部人员安排验收。若是工装需试模,设备部人员安排时间并提前通知采购及相关人员,采购通知供应商到我司参与试模,有问题当场沟通并解决。
5.最终试模确认无误,确认结果需一式两份(所有相关人员签字确认),采购部和设备部各一份。
康平科技(苏州)有限公司
会议签到表
QR/QP6.2.2-14编号:
会议日期
会3
工装/夹具流程
一楼会议室
郦总
与会人员签名
与会部门
与会人员职务
备注
郦宁
总经办
朱玮
总经办
尹群丽
采购部
王永军
技术部
张金华
品质部
曹丹萍
采购部
杨小红
设备部
日期:2014-5-13
会议题目:
工装/夹具流程
工装夹具模具控制流程图

注:
与本程序相关的所有内容, 均由技术部 组织。相关部门和人员必须积极配合。
4. 制作/试用
内部制作/外加工
5. 工装夹具验证
检验员/生产部 1. 由工装/夹具管理员统一标 识、建帐、建立履历卡。 2. 所有工装夹具, 必须由工装 /夹具车间进行装拆、 调试, 合 格后交车间操作工使用。 3. 统一整齐存放于公司工装 夹具库,保持清洁,并相隔一 定距离,以免碰伤;贮存时必 须标识明确,对待修、更改、 报废的,必须隔离存放且有明
9. 模具/工装夹具更新
生产部
10. 模具/工装夹具报废
生产部
应经生产部经理和生产车 间负责人确认。
11. 资料归档
生产部/检验员 由工装/夹具管理员归档保存,包括: 1.工装/夹具(含专用检具)验证记录 2.工装/夹具台帐 3.工装/夹具履历表 4.工装/夹具制作清单及跟踪记录 5.工装/夹具报损再制审批单 14-1/1
工装夹具必须存放在通风、无腐蚀 的场所,管理员必须经常进行检查 和维护保养,如发现没有涂防锈油 等现象,应及时给予保养,避免锈 蚀,影响精度。 由管理员负责,对工装夹具的使用 和维修情况,记录于“工装/夹具履 历表”中,作为其更新换代的依据。 生产部生技课 由操作工负责提供末检记录数据。 根据“工装夹具履历表”中的记录, 及其使用寿命,管理员应及时编制 和实施“更新计划” ,确保不影响正 常生产进度。
工装夹具模具控制程序
作业流程及规定
新产品由技术部组织, 相关部门 和人员必须积极配合。 1. 工装夹具模具的设计 技术部 1. 由技术部负责, 组织生产部经理 及车间主任,结合实际操作对夹具 方案进行评审。 2. 评审合格, 则投入制作; 否则, 重新进行设计开发和评审,直至 达成一致意见。 2. 设计方案评审 技术部/生产部 1. 由检验员负责对该工装夹 具试生产的产品(取样 3 至 5 件)进行全尺寸和全性能检 验, 并对照图纸判断所加工的 产品是否合格; 将相关检验报 告报告技术部主管审批。 2. 由技术部根据检验员对试 制产品的检验结果, 确定该工 装夹具是否合格。 1. 不论内、 外部加工, 均由技术部 组织, 并对制作的进度负责。 若委 托供方制作,应对其制作进度进 行监控。 2. 制作完毕后,由生产车间安排 试生产,以验证其适用性。 3. 若该工装夹具合格, 或被技 术部偏差接受, 则可交生产部 正式投入使用, 否则, 应重新 整改和试制。
工装夹具设计的基本方法和步骤
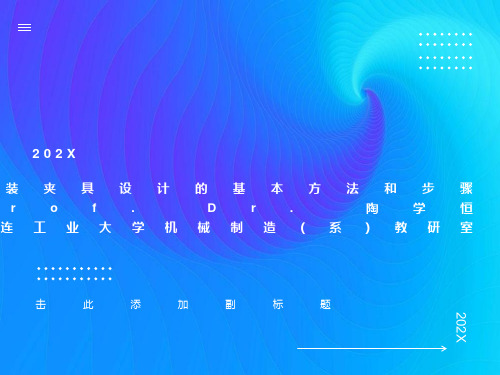
能提高生产效率
04
工艺性能好
05
使用性能好
06
经济性好
07
进行工装夹具的设计和使用,是能够使得零件迅速而准确地安装于夹具中的确定位置,夹具定位
安装于加工设备的确定位置。因此,使用夹具加工零件时,能使零件迅速而准确地处于加工位置,从而保证零件的加工质量满足要求,这就是夹具在生产中得到广泛运用的主要原因。
这三项原则是相互制约的,因此,夹紧力设计时应综合考虑,选择更佳的加紧方案,也可用计算机辅助设计。一般来讲: 对粗加工用的夹具,选用较大的夹紧力,主要考虑零件的不移动原则; 对精加工用的夹具,选用较小的夹紧力,主要考虑零件的不变形和不振动原则。
2-3-2 夹紧点的选择 夹紧点的选择是达到最佳夹紧状态的首要因素,正确选择夹紧点后,才能估算出所需要的夹紧力,选的不当不仅增大夹具变形,甚至不能夹紧零件。 夹紧点的选用原则: 尽可能使夹紧点和支承点对应,使夹紧力作用在支承上,可减少变形; 夹紧点选择应尽量靠近加工表面,不致引起过大的夹紧变形。 可以采取减少夹紧变形的措施: 如增加辅助支承和辅助夹紧点、分散着力点和增加压紧件的接触面积、利用对称变形等等。
2-3-1 零件在夹具中定位后的夹紧三原则: a) 零件在工装夹具中定位后的不移动原则: 选择夹紧力的方向指向定位基准(第一基准),且夹紧力的大小应足以平衡其它力的影响,不使零件在加工过程中产生移动。 b) 零件在工装夹具中定位后的不变形原则: 在夹紧力的作用下,不使零件在加工过程中产生精度所不允许的变形,必须选择合适的夹紧部位及压块和零件的接触形状,同时压紧力应合适。 c) 零件在工装夹具中定位后的不振动原则: 提高支承和夹紧刚性,使得夹紧部位靠近零件的加工表面,避免零件和夹紧系统的振动。
其它的尺寸(夹具上与设计图样无关的),若需要保证其配合精度要求,是可以采取配作加工的加工手段,同样能够达到夹具的使用精度要求,从而保证用该夹具加工的零件,其最终尺寸和位置精度都满足设计要求。
夹具设计04-验收流程

基本信息01工装信息零件号、总成号、工程更改级别、年型、图号、工装编号、首次送样日期、工装制造完成日期、大型外形尺寸、估计重量、是概念设计还是正式生产02评审组AME、AQE、PE、其他03供方信息设计方、制造方、制造地点出来的样子长下面这样:基本信息好了,我们进入正式评审的三个阶段了。
工装设计检查表01安全/人机工程1.1 整个工装设计是否已经考虑对锐边的处理,避免毛刺和锋利的边缘。
1.2 加紧装置、铰链,或其他可移动的细节部位是否注意防止对操作员的伤害。
1.3 加紧装置需有防止掉落的保护。
1.4 工装在动作过程中是否会对人身产生危险?02设计概念2.1 工装设计是否便于零件的装和拆,以及三坐标的检测。
03定位销3.1 定位销的是否与工件上的孔相适合,公差范围是否合理?3.2 定位销自身的固定是否采用了合适的拧紧的方式?3.3 是否有活动的定位销,定位销的活动距离是否合理,活动过程是否会产生干涉?3.4 如果用快速夹驱动定位销,则快速夹的行程和夹紧力能否满足要求?3.5 定位销是否与电极基座绝缘?3.6 定位块的定位强度能否满足长期生产的需要?04压紧块4.1 压紧块是否提供足够的压紧力?4.2 压紧块打开过程中是否会产生碰撞或干涉?4.3 压紧块与夹手或气缸的力臂配置是否合适?若不适合,采取什么措施?05底板5.1 底板强度是否足够安全支撑所有部件?5.2 底板在使用过程中是否会产生形变?5.3 旋转底板与旋转台配合的连接是否安全?5.4 旋转底板与旋转台配合的旋转位置是否在工装的中心上?06旋转台6.1 旋转台的高度、宽度是否合适?6.2 旋转台是否能够提供足够的支撑力?6.3 新旋转台的设计是否考虑可调?可以适合不同工装切换?07整体性能7.1 是否优先采用了机械防错?08可改装性8.1 工装是否能够被改装以使其能被用于相对的另一侧产品(左侧产品/右侧产品)?09图纸要求9.1 设计图纸的工装说明表中是否包含:零件状态,检具状态,材料,明细表,版本号,更改记录等信息。
设计焊接工装夹具的流程与步骤,一文搞定!
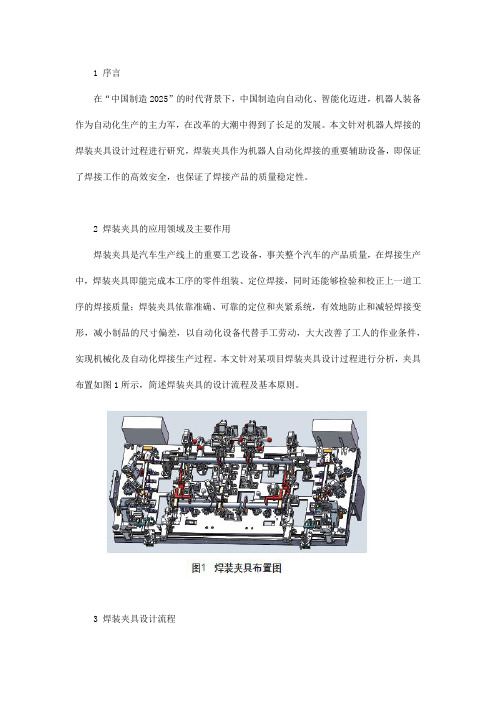
1 序言在“中国制造2025”的时代背景下,中国制造向自动化、智能化迈进,机器人装备作为自动化生产的主力军,在改革的大潮中得到了长足的发展。
本文针对机器人焊接的焊装夹具设计过程进行研究,焊装夹具作为机器人自动化焊接的重要辅助设备,即保证了焊接工作的高效安全,也保证了焊接产品的质量稳定性。
2 焊装夹具的应用领域及主要作用焊装夹具是汽车生产线上的重要工艺设备,事关整个汽车的产品质量,在焊接生产中,焊装夹具即能完成本工序的零件组装、定位焊接,同时还能够检验和校正上一道工序的焊接质量;焊装夹具依靠准确、可靠的定位和夹紧系统,有效地防止和减轻焊接变形,减小制品的尺寸偏差,以自动化设备代替手工劳动,大大改善了工人的作业条件,实现机械化及自动化焊接生产过程。
本文针对某项目焊装夹具设计过程进行分析,夹具布置如图1所示,简述焊装夹具的设计流程及基本原则。
3 焊装夹具设计流程3.1 焊装夹具设计依据设计依据是以客户提供的产品三维模型、产品图样、产品技术要求和有关技术要求等输入信息,在设计焊装夹具之前,应了解产品结构特征、工艺需要等信息,并结合企业自身的加工制作水平进行设计。
认真分析用户提供的产品图样,将各零部件的基准定位信息记录并标记,如图2所示,方便在后续设计中查阅。
3.2 设计前准备工作在正式开始焊装夹具设计之前,应根据之前分析图样得到的信息,在产品三维模型上,将产品需要焊接的位置标记焊缝位置分布,如图3所示,以免在设计过程中丢漏焊缝,造成设计时间延误。
根据产品图样的定位信息,确定产品在焊装夹具底板上的摆放位置,在满足支撑定位的前提下,尽量使产品里夹具底板近一些,方便产品靠近夹具底板一侧焊缝在变位机旋转180°时,机器人可以更好的焊接姿态进行焊接;同时确定焊接所采用的焊枪型号,并要求提供焊枪的完整数模,将焊枪以合理的角度摆放至产品焊缝上,直观的反应焊接过程,一般每条焊缝放置两把焊枪,位于焊缝两端,焊枪布置应与产品对接面有45°夹角,如图4所示,与焊缝走向有75°夹角,如图5所示。
工装夹具设计管理流程
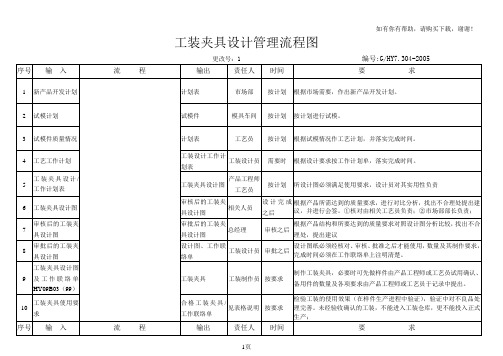
报废申请单
市场部长
即时
市场部部长对报废申请进行审核。
20
报废申请单
报废申请单
总经理
即时
总经理审批。
21
报废申请单
报废清单
工装保管员
按要求
编制报废清单归档保存,工装保管员在工装清单备注栏及时注销。
编制/日期:审核/日期:批准/日Байду номын сангаас:
22、相关记录
22.1工装(新、改)验收确认单编号:G/HY7.3B08-
序号
输入
流程
输出
责任人
时间
要求
11
工装夹具管理规定
工装(新、改)验收确认单
工装保管员
样件生产后
登记工装清单、进仓单,数量准备,放置妥当并标识清楚。
12
合格工装夹具
工装出仓单
工装保管员
按需要
登记出仓单,并签收。
13
合格工装夹具
夹具标识
(存卡)
工装保管员
按规定
1登记工装清单;
②上架定置堆放并标识(存卡);
③易生锈的上防锈油,精度较高的应存放工具柜内。
14
生产计划安排
工装夹具管理规定
生产车间带班、线长
生产前
领用时登记工装夹具进出仓登记表,签名确认。
15
工装夹具管理规定
试用情况表
产品工程师工艺员
生产中
对工装夹具的使用情况进行检查监督并进行指导。收集使用意见加以改进完善。
16
工装夹具管理规定
工装夹具管理规定
7
审核后的工装夹具设计图
审批后的工装夹具设计图
总经理
审核之后
根据产品结构和所要达到的质量要求对照设计图分析比较,找出不合理处,提出建议