切削热的产生与切削温度的测量
第5章 切削热与切削温度
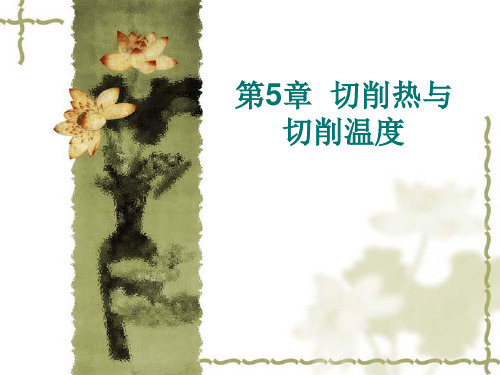
切屑 50%~86% 28%
工件 3%~9% 52.5%
刀具 10%~40% 14.5%
周围介质 1% 5%
表5-1 切屑、工件、刀具中切削热的分布
5.2 切削温度的测量方法
切削温度的测定方法很多,有热电偶法、辐射测温法等。但目前广为应 用的是热电偶法。它具有简单、可靠,使用方便的优点。 5.2.1 热电偶法 热点偶法包括自然热点偶法和人工热电偶法。 1.自然热电偶法 切削过程中,工件、刀具通常是由两种不同的金属材料组成的。在刀 具与切屑和刀具与工件接触区总存在着相当高的切削温度,称为热电偶 的热端;离接触区较远的工件与刀具处一般保持在室温状态,称为热电 偶的冷端。可用导线将工件与刀具的冷端接到仪表上,即可将切削热电 势显示和记录下来。根据事先作出热电偶的标定曲线(温度与毫伏值的 对应关系曲线),即可求得刀具与切屑和刀具与工件接触面的平均温度, 即切削温度。
(a)测量刀具前面某点的温度示意图 (b)测量工件加工面某点的温度示意图 图5-4 用人工热电偶法测量刀具和工件温度
5.2.2 辐射测温法 辐射测温法是一种非接触 式测量方法。它是利用高 温辐射能量来测量工件表 面温度的。作为测量用的 传感器有光电传感器及热 敏电阻传感器两种。如图55所示为用光电传感器测量 刀具与切屑接触面温度分 布的示意图。光电传感器 可以用锗光电二极管或硫 化铅光电池。在刀片上打 一个小的锥孔,一直通到 刀具的前面上,从切屑底 面测定辐射能,通过标定 求得切屑底面该点的温度。
5.4 影响切削温度的主要因素 切削温度的高低,取决于切削热产生的多少和散热 条件的好坏。下面分析几个主要因素对它的影响。 1.工件材料对切削温度的影响 2.切削用量对切削温度的影响 1)切削速度 2)进给量 3)背吃刀量
切削热与切削温度

( (
度左 图 ) 自 然 热 电 偶 法 测 温
度右 图 ) 人 工 热 电 偶 法 测 温
2.切削温度分布
切削温度的分布规律如下: ▲(1)刀—屑接触面摩擦大,热量不易传散,故产生的温度值最
高。 ▲(2)切削区域的最高温度点是在前面上离切削刃有一定距离的
地方,这是摩擦热沿刀面不断增加的缘故。 ▲ (3)剪切区中,在剪切面上各点的变形功大致相同,故各点处
实 验 公 式
3.刀具几何参数的影响
(1)前角增大,切削变形和摩擦均减小,产生的热量 均减少,使切削温度下降。但前角过大,楔角减小,散热 条件变差,切削温度反而升高。因此,在前角增大总会有 一个产生最低温度的最佳值。
(2)主偏角减小,使切削变形和摩擦增加,产生的切 削热增加,但主偏角减小后,因刀头体积增大,切削宽度 增大,故散热条件改善,故切削温度下降。
温度值较接近,但垂直剪切面方向的温度梯度很大。 ▲ (4)切屑底层上的温度梯度很大。 ▲ (5)工件材料塑性越大,切削温度分布越均匀;材料脆性越大,
最高温度点离刀刃越近。 ▲(6)材料导热系数越低,刀具前、后面上的温度越高。 ▲(7)切屑带走热量最多,它的平均温度高于刀具和工件上的平
均温度。
切削温度的分布
刀具的磨损达到一定数值后,磨损对切削温度的影响会 增大,随着切削温度的提高,影响就越显著,实验表明, VB≥0.4mm时,切削温度会显著增高。
金属切削加工
1.3 影响切削温度的主要因素
在切削时影响产生热量和传散热量的因素主要有:工件 材料、切削用量、刀具几何参数、刀具的磨损和切削液等。
1.工件材料 2.切削用量
工件材料的强度、硬度越高,塑 性越大,切削力就越大,产生的热 就多,切削温度就高。
切削热和切削温度的关系
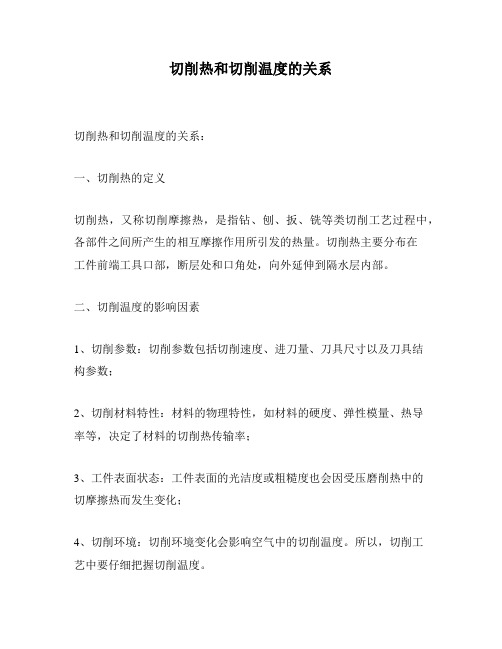
切削热和切削温度的关系
切削热和切削温度的关系:
一、切削热的定义
切削热,又称切削摩擦热,是指钻、刨、扳、铣等类切削工艺过程中,各部件之间所产生的相互摩擦作用所引发的热量。
切削热主要分布在
工件前端工具口部,断层处和口角处,向外延伸到隔水层内部。
二、切削温度的影响因素
1、切削参数:切削参数包括切削速度、进刀量、刀具尺寸以及刀具结
构参数;
2、切削材料特性:材料的物理特性,如材料的硬度、弹性模量、热导
率等,决定了材料的切削热传输率;
3、工件表面状态:工件表面的光洁度或粗糙度也会因受压磨削热中的
切摩擦热而发生变化;
4、切削环境:切削环境变化会影响空气中的切削温度。
所以,切削工
艺中要仔细把握切削温度。
三、切削温度的控制
1、采用合理的切削参数:提高切削速度可以有效减少切削热,调节进刀量可以避免过多的刀具磨损和加大刀具的寿命;
2、采用合理的切削环境:在低温的切削环境中,切削热能够更快地排出,从而降低切削温度;
3、把握切削工件表面温度:切削前,可以根据工件表面温度调整切削参数,使切削温度不过高;
4、利用切削润滑液:切削时,可以使用切削润滑液,它可以对切削前端起到良好的润滑作用,减少切削温度;
5、正确使用刀具:正确使用刀具可以减少不必要的刀具消耗,从而降低切削热,减少切削温度。
四、切削温度的临界值
切削温度的临界值取决于切削材料的性能,一般情况下,普通工件的切削温度临界值一般设定为1000~3000℃,钢材切削的临界值在1500~2500℃,高硬度合金的切削温度不宜超过500℃。
如果切削温度超过了临界值,会导致工件裂痕、烧伤和工具烧毁等问题。
机械制造技术基础 第二章 第五节 切削热及切削温度
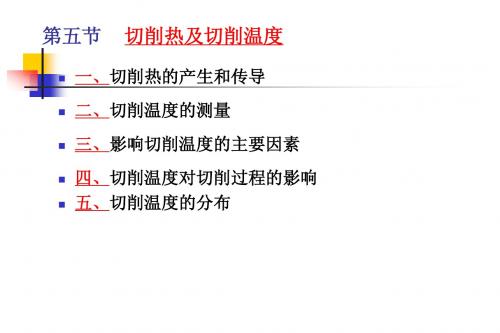
四、切削温度对切削过程的影响
1、切削温度对工件材料被切削性能的影响 切削温度较高,切削区工件材料的强度会降低;同时切削速度较高时(即
切削温度较高),应变速率增大,又会使切削区工件材料的强度增大。最终的 影响结果取决这正反两方面的主、次地位。 通常,切削温度较高,切削区工件材料的强度会降低,材料的被切削性能 好,表现为切削力有下降趋势。 2 、对刀具材料的影响 适当提高切削温度,可提高刀具材料的强度、韧性。所以,硬度高,但强 度、韧性差的刀具材料易采用较高切削速度,这样不易崩刃(如:陶瓷、金刚 石、 立方氮化硼)。 3、 对工件尺寸精度的影响 工件、刀杆受热膨胀,使切削加工后零件尺寸精度及形状精度降低,精 加工时必须注意。 4、利用切削温度自动控制切削速度或进給量。 5、也可同时用切削温度与切削力作为控制型号,控制刀具磨损。
第Ⅰ变形区——切屑的弹、塑性变形功,产生的热为qs。 第Ⅱ变形区——切屑与前刀面的摩擦功,产生的热为qr 。 第Ⅲ变形区——刀具后刀面与工件的摩擦功。 2、切削热的传导 ⑴ 切削热的传导 切削塑性金属,为研究问题方便,忽略后刀面与工件摩擦产生的热,则切削热分别由刀具(qτ)、 切屑(qc)、工件(qw)及周围介质传出(比例较小忽略),具体比例如下: qc=R1. qs+R2.qr qτ=(1-R2) qr qw=(1-R1) qc 其中 :R1—剪切热传入切屑的比例 ;R2 —摩擦热传入切屑的热 。 ⑵ 影响热传导的的主要因素: ① 工件材料的导热系数↑ qc ↑、 qw ↑,则切削区的温度θ↓ ② 刀具材料导热系数↑ qτ ↑,则切削区的温度θ↓ ③ 刀、屑接触时间 ↑ 则切削区的温度θ ↑ ⑶ 影响 R1、R2大小的因素 ① R1:通常V ↑、ac ↑ R1 ↑
切削热与切削温度
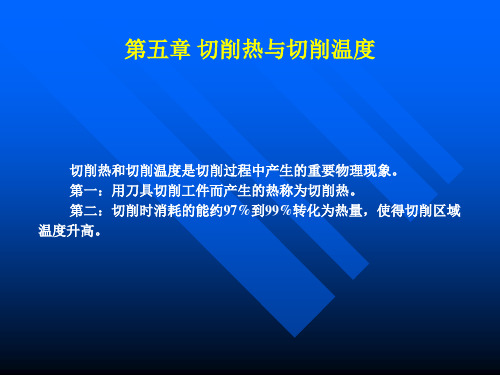
2.主偏角 主偏角加大后,切削刃的工作长度缩短,切削热相对地集 中;但刀尖角减小,使散热条件变差,切削温度将上升。
目前应用较广的是自然热电偶法和人工热电偶法。
补充: 辐射温度计法:任何物体都会有红外线辐射,它表现的是物体的温度。 温度越高辐 射越大。用红外线接收器作传感器,经数字滤波放大,再函数计算,显示出数字。 热电偶法原理:把两种化学成分不同的导体的一端连接在一起,使它们的另一端处 于室温状态(称为冷端),那么,当连在一起的一端受热时(称为热端)在冷热端 之间就会产生一定的电动势,称为电势,把毫伏表或电位差计接在两导体冷端之间 便可测量出热电势的值。实验研究表明,热电势值的大小取决于两种导体材料的化 学成分及冷热端之间的温度差。当组成热电偶的两种材料一定时,经过标定可得到 热电势的值与冷热端温度差之间的关系。
• 5.1切削热的产生与传出 • 来源:切削热来源于切削层金属发生弹性、塑性变形 所产生的热及切屑与前刀面、工件与后刀面之间的摩 擦。 • 切削热产生于三个变形区,切削过程中三个变形区内 产生切削热的根本原因是,切削过程中变形与摩擦所 消耗的功,绝大部分转化为切削热。
• • •
•
•
•
假定主运动所消耗的功全部转化为热能,则单位时间内产生的切削热: Pc = Fcνc Pc—每秒钟内产生的切削热 Fc—主切削力 νc—切削速度 切削热由切屑、工件、刀具及周围介质传导出去。 影响散热主要因素: ⑴工件材料的导热性能 工件材料的导热系数高,由切屑和工件散出的 热就多,切削区温度就较低,刀具寿命提高;但工件温升快,易引起工 件热变形(铜和铝)。工件材料的导热系数小,切削热不易从工件方面 散出,加剧刀具磨损(不锈钢)。 ⑵刀具材料的导热性能 刀具材料的导热系数高,切削热易从刀具散出, 降低了切削区温度,有利于刀具寿命的提高(YG类硬质合金)。 ⑶周围介质 采用冷却性能好的切削液及采用高效冷却方式能传导出较 多的切削热,切削区温度就较低。采用喷雾冷却法使切削液雾化后汽化, 将能吸收更多的切削热,使切削温度降低。 ⑷切屑与刀具的接触时间 外圆车削时,切屑形成后迅速脱离车刀而落 入机床的容屑盘中,切屑传给刀具的热量相对较少;钻削或其它半封闭 式容屑的加工,切屑形成后仍与刀具相接触,传导给刀具的热相对较多。
切削热与切削温度分析

二、温度分布(温度பைடு நூலகம்)
工件:低碳钢;刀具前角30度,后角7度; 切削用量:Vc=22.8mm/min,厚度为0.6mm;干切削。
二、温度分布(温度场)
三、影响切削温度的主要因素
(1)切削用量的影响 ----切削速度
随着切削速度 的提高,切削层金 属塑性变形产生的 热量来不及传到工 件与刀具就被切屑 带走了,因此VC提 高1倍,切削温度 仅增加20~33%。
问题:看图说明前角和主偏角对T的影响
四、切削温度对工件、刀具和切削过程的影响
1. 切削温度对工件材料强度和切削力的影响 2. 切削温度对刀具材料的影响 3. 切削温度对工件尺寸精度的影响 4. 利用切削温度自动控制切削速度和进给量 5. 利用切削温度与切削力控制刀具磨损
三、影响切削温度的主要因素
(1)切削用量的影响 ----进给量f
f 增大,使切 屑的平均变形减少 切屑与前刀面的接 触区长度增加,改 善了散热条件。因 此 , f 提高一倍, 切削温度仅提高10
三、影响切削温度的主要因素
(1)切削用量的影响 ----背吃刀量ap
ap增大,产生的 热量成倍增加。但 是刀刃的工作长度 也增加一倍,大大 改善了散热条件因 此, ap提高一倍切 削温度仅提高3%
(2)刀具几何参数的影响 ----主偏角
主偏角减小时,致使 切削宽度增大,刀 尖角增大,刀具散 热条件改善,有利 于降低切削温度。
三、影响切削温度的主要因素
■ (3)工件材料的影响
工件材料的强度、硬 度越高,切削力越大,切 削时消耗的功也越多,产 生的切削热也越多,切削 温度也就越高。
三、影响切削温度的主要因素
切削热和切削温度

切削热和切削温度切削过程中产生的切削热对刀具磨损和刀具寿命具有重要影响,切削热还会使工件和刀具产生变形、残余应力而影响加工精度和表面质量。
一、切削热的产生与传导切削热来源于两个方面,一是切削层金属发生弹性和塑性变形所消耗的能量转换为热能;二是切屑与前刀面、工件与后刀面间产生的摩擦热。
切削过程中的三个变形区就是三个发热区域。
切削过程中所消耗能量的98%~99%都将转化为切削热。
切削热由切屑、工件、刀具及四周的介质(空气,切削液)向外传导。
影响散热的主要因素是:(1)工件材料的导热系数工件材料的导热系数高,由切屑和工件传导出去的热量增多,切削区温度就低。
工件材料导热系数低,切削热传导慢,切削区温度就高,刀具磨损就快。
(2)刀具材料的导热系数刀具材料的导热系数高,切削区的热量向刀具内部传导快,可以降低切削区的温度。
(3)四周介质采纳冷却性能好的切削液能有效地降低切削区的温度。
车削加工时产生的切削热多数被切屑带走,切削速度越高,切削厚度越大,切屑带走的热量越多;传给工件的热量次之,约为30%;传给刀具的热量更少,一般不超过5%。
钻削时,由于切屑不易从孔中排出,故被切屑带走的热量相对较少,只有30%左右,约有50%的热量被工件汲取。
二、切削温度的测量测量切削温度的方法许多,有热电偶法、辐射热计法、热敏电阻法等。
目前常用的是热电偶法,它简洁、牢靠、使用便利。
1. 自然热电偶法;2. 人工热电偶法。
三、影响切削温度的主要因素1.切削用量对切削温度的影响、、增大,单位时间内材料的切除量增加,切削热增多,切削温度将随之上升。
但、和对切削温度的影响程度不同,切削速度对切削温度的影响最为显著,次之,最小,缘由是:增大,前刀面的摩擦热来不及向切屑和刀具内部传导,所以对切削温度影响最大;增大,切屑变厚,切屑的热容量增大,由切屑带走的热量增多,所以对切削温度的影响不如显著;增大,刀刃工作长度增大,散热条件改善,故对切削温度的影响相对较小。
切削热与切削温度
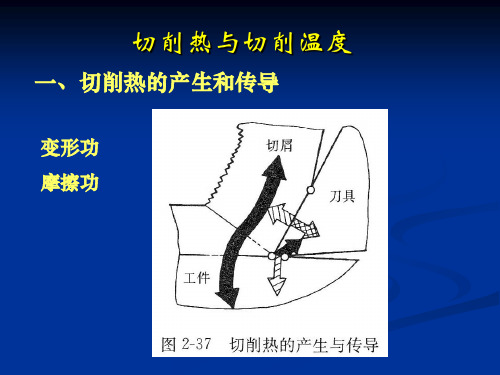
3. 刀具磨损原因 高速钢刀具) (1)磨粒磨损 (高速钢刀具) ) 切屑、工件的硬度虽然低于刀具的硬度, 切屑、工件的硬度虽然低于刀具的硬度,但其结 构中经常含有一些硬度极高的微小的硬质点, 构中经常含有一些硬度极高的微小的硬质点,能在 刀具表面刻划出沟纹,这就是磨粒磨损。 刀具表面刻划出沟纹,这就是磨粒磨损。 硬质点有碳化物(如 硬质点有碳化物 如Fe3C、TiC、VC等)、氮化物 、 、 等、 (如TiN、Si3N4等)、氧化物 如Si02、A12O3等)和金 如 、 、氧化物(如 和金 属间化合物。 属间化合物。
氧化磨损: 氧化磨损: 空气不易进入刀—屑接触区。氧化磨损最容易在主、 空气不易进入刀 屑接触区。氧化磨损最容易在主、 屑接触区 副切削刃的工作边界处形成,在这里划出较深的沟槽, 副切削刃的工作边界处形成,在这里划出较深的沟槽, 造成“边界磨损” 造成“边界磨损”。
温度对磨损的影响
(3)刀具角度的影响 γo ↑ → θ ↓ ; γo ↑ ↑ → θ ↑ 切削热集中↑ 散热↓→ κr ↑ → bD ↓ → 切削热集中↑ → 散热↓→ θ ↑
(4)刀具磨损的影响:刀钝以后,摩擦加剧 )刀具磨损的影响:刀钝以后, 的影响: (5)切削液的影响:冷却效果明显 )切削液的影响 切削液的作用: 切削液的作用: (1)冷却作用 )冷却作用 (2)润滑作用 )润滑作用 (3)清洗作用 )清洗作用 (4)防锈作用 )防锈作用
五、切削温度对工件、刀具和切削过程的影响 切削温度对工件、 1. 切削温度对工件材料强度和切削力的影响 2. 切削温度对刀具材料的影响 3. 切削温度对工件尺寸精度的影响 4. 利用切削温度自动控制切削速度和进给量 5. 利用切削温度与切削力控制刀具磨损
刀具磨损与刀具寿命
第五章 切削热与切削温度
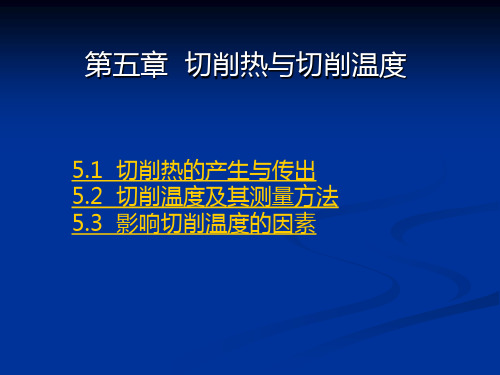
不同的切削加工方法,切削热由切削、刀具、工件和 周围介质传导出去的比例也不同。例如,车削加工时,切 削带走的切削热约为50%-80%,40%-10%传入车刀, 9%-3%传 入工件,1%传入周围介质(如空气)。切削速度越高,进 给量(切削厚度)越大,由切屑带走的热量就越多。 钻削加工时,约有28%的切削热由切削带走,15%传入 钻头,52%传入工件,5%传入周围介质。
5.2
切削温度及其测量方法
切削温度一般是指刀具与工件接触区域的平均温度。 切削温度的测量是实验研究的重要技术,是研究各 种因素对切削温度影响大小的依据。此外,切削温度理 论计算的准确性也需要通过实测数据来校验。 切削温度的测量方法很多,可归纳为以下情况:
单车刀法 自然热电偶法 双车刀法 热电偶法 插入刀具法
2. 主偏角
主偏角对切削温度的影响如 图5.11所示。随主偏角的增 大,切削温度升高。这是因 为主偏角增大,一方面使切 削刃工作长度缩短,切削热 相对集中,同时刀尖角减小 ,散热条件变差,因此切削 温度升高。
3. 负倒棱
及刀尖圆弧半径
负倒棱 在(0-2)f范围内变化、刀尖圆弧半径 在0-1.5mm范围内变化时,基本不影响切削温度。因为负倒 棱宽度及刀尖圆弧半径的增大,一方面使塑性变形增大, 切削热随之增加;另一方面这两者都能使刀具的散热条件 有所改善,传出的热量也有所增加,两者趋于平衡,所以 对切削温度的影响不大。
刀具材料的导热系数大时,切削区的热量容易从刀具方 面传导出去,也能降低切削区的温度。例如,YG类硬质合金 的导热系数普遍大于YT类硬质合金的导热系数,且抗弯强度 较高,所以在切削导热系数小、热强性好的不锈钢和高温合 金时,在缺少新型高性能硬质合金的情况下,多采用YG6X、 YG6A等牌号的YG类硬质合金。 采用冷却性能较好的切削液也能有效的降低切削温度。 采用喷雾冷却法使切削液雾化后汽化,将能吸收更多的切削 热而使切削温度降低。此外,切削与刀具的接触时间也影响 切削温度。例如,外圆车削时,切削形成后迅速脱离车刀而 落入机床的容屑盘中,传给刀具的切削热就减少了;但在进 行半封闭式容屑的钻削加工时,切屑形成后仍较长时间与道 具接触,由切屑所带走的切削热再次传给刀具,使得切削温 度升高。
第三节__切削热和切削温度
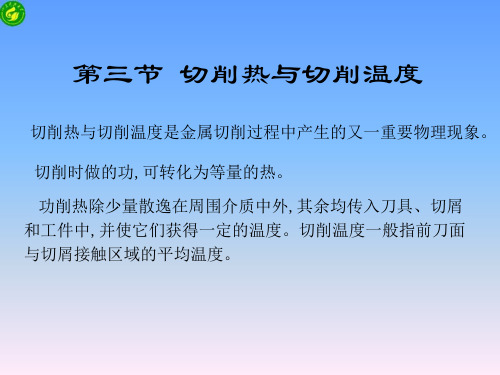
三、影响切削温度的主要因素
切削温度高低取决于两个方面:产生的热量和散热速度。 产生的热量少,散热速度高,则切削温度低;或者上述之一起主导作 用,也会降低切削温度。 因而,凡是能影响产生的热量和散热速度的因素均会影响切削温度的高低
学习目的
通过对切削热的来源、切削温度的分布及影响因素进行
研究,以便控制切削热和切削温度对切削过程的影响。
学习内容
一、切削热的来源及传出 二、切削区的温度及其分布 三、影响切削温度的主要因素
一、切削热的来源及传出
1、切削热来源
1)被切削的金属在刀具的作用下,发生弹性和塑性变形而耗功, 这是切削热的一个重要来源。 2)切屑与前刀面之间的摩擦耗功产生出大量的热量。 3)工件与后刀面之间的摩擦耗功产生出大量的热量。 因此,切削时共有三个发热区域 剪切面 切屑与前刀面接触区 后刀面与过渡表面接触区
所以,切削热的来源就是切屑变形功和前、后刀面的摩擦功。
根据切削理论,切削变形和摩擦而产生的热量.
在剪切面上的塑性变形产生的热量最多。 单位时间内产生的切削热的计算公式
Q —单位时间内产生的切削热(J/s); Fc—主切削力(N); Vc—切削速度(m/s)。
注:该公式中忽略了进给运动所消耗的功率,且假定主运动所消耗的功全部转化为热能。
3)实际意义: 从降低切削温度的角度出发,切削用量的选择原则:为提高切削效率, 应优先选用较大的背吃刀量,其次增加进给量,最后确定刀具和机床性 能允许的最大切削速度。
切削热
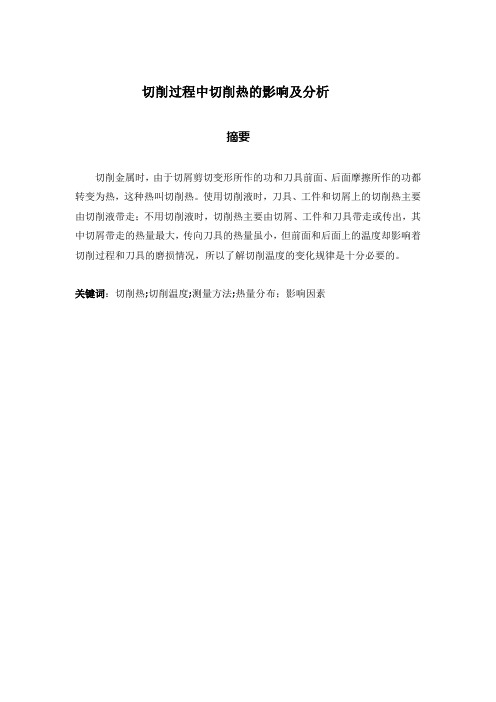
切削过程中切削热的影响及分析摘要切削金属时,由于切屑剪切变形所作的功和刀具前面、后面摩擦所作的功都转变为热,这种热叫切削热。
使用切削液时,刀具、工件和切屑上的切削热主要由切削液带走;不用切削液时,切削热主要由切屑、工件和刀具带走或传出,其中切屑带走的热量最大,传向刀具的热量虽小,但前面和后面上的温度却影响着切削过程和刀具的磨损情况,所以了解切削温度的变化规律是十分必要的。
关键词:切削热;切削温度;测量方法;热量分布;影响因素目录1切削热的产生 (1)2切削热的测量 (2)2.1.热电偶法 (2)2.2自然热电偶法 (5)2.3人工热电偶法 (5)2.4半人工热电偶法 (5)2.5等效热电偶法 (6)2.6.切屑颜色与切削温度的关系 (6)2.7光热辐射法 (7)2.8其他因素 (8)3切削热的影响因素 (8)3.1、切削用量的影响 (8)3.2、刀具几何参数的影响 (9)3.3、刀具磨损的影响 (11)3.4、切削液的影响 (11)3.5工件材料 (11)3.6其他因素 (11)4切削热的分布 (12)5对工件的影响 (13)6 解决措施 (13)7 切削热的利用 (14)结论 (17)致谢 (18)参考文献 (19)1切削热的产生切削热被切削的金属在刀具的作用下,发生弹性和塑性变形而耗功,这是切削热的一个重要来源。
此外,切屑与前刀面、工件与后刀面之间的摩擦也要耗功,也产生出大量的热量。
因此,切削时共有三个发热区域,即剪切面、切屑与前刀面接触区、后刀面与过渡表面接触区,如图示,三个发热区与三个变形区相对应。
所以,切削热的来源就是切屑变形功和前、后刀面的摩擦功。
切削塑性材料时,变形和摩擦都比较大,所以发热较多。
切削速度提高时,因切屑的变形减小,所以塑性变形产生的热量百分比降低,而摩擦产生的热量百分比增高。
切削脆性材料时,后刀面上摩擦产生的热量在切削热中所占的百分比增大。
切削热来源于三个变形区切屑变形功刀具切屑间摩擦功刀具工件间摩擦功切削热产生比例Q=Qs+Qγ+Qα 根据切削条件:切塑性金属时切屑为带状切屑,塑性变形和前刀面的摩擦比较厉害,切屑为带状切屑,塑性变形和前刀面的摩擦比较厉害, Qs+QX占主导切脆性金属时切屑为崩碎切屑,后刀面摩擦占百分比↑,所以Q 切屑为崩碎切屑,后刀面摩擦占百分比↑,所以Qα占主导速度较高时切屑的变形↓,塑性变形产生的热百分比↓ 摩擦热占切屑的变形↓,塑性变形产生的热百分比↓,摩擦热占百分比↑ 百分比↑ ,Qγ+Qα占主导速度较低时切屑的变形↑ 塑性变形Q 切屑的变形↑,塑性变形Qs占主导2切削热的测量尽管切削热是切削温度上升的根源,但直接影响切削过程的却是切削温度,切削温度一般指前刀面与切屑接触区域的平均温度。
金属切削过程中的切削热及切削温度的影响因素研究
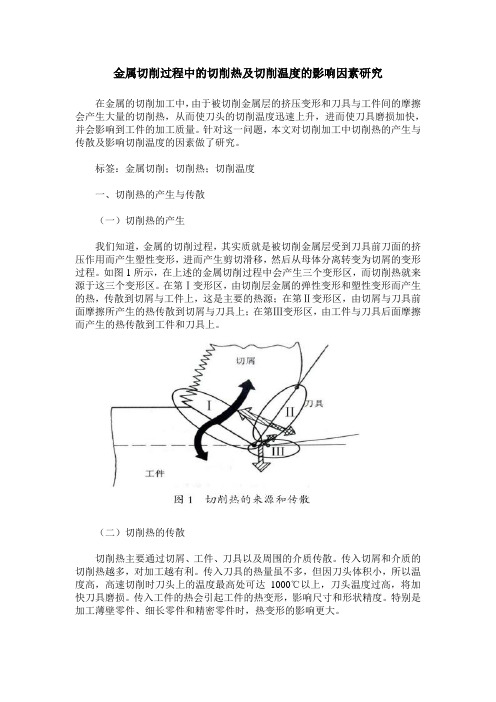
金属切削过程中的切削热及切削温度的影响因素研究在金属的切削加工中,由于被切削金属层的挤压变形和刀具与工件间的摩擦会产生大量的切削热,从而使刀头的切削温度迅速上升,进而使刀具磨损加快,并会影响到工件的加工质量。
针对这一问题,本文对切削加工中切削热的产生与传散及影响切削温度的因素做了研究。
标签:金属切削;切削热;切削温度一、切削热的产生与传散(一)切削热的产生我们知道,金属的切削过程,其实质就是被切削金属层受到刀具前刀面的挤压作用而产生塑性变形,进而产生剪切滑移,然后从母体分离转变为切屑的变形过程。
如图1所示,在上述的金属切削过程中会产生三个变形区,而切削热就来源于这三个变形区。
在第Ⅰ变形区,由切削层金属的弹性变形和塑性变形而产生的热,传散到切屑与工件上,这是主要的热源;在第Ⅱ变形区,由切屑与刀具前面摩擦所产生的热传散到切屑与刀具上;在第Ⅲ变形区,由工件与刀具后面摩擦而产生的热传散到工件和刀具上。
(二)切削热的传散切削热主要通过切屑、工件、刀具以及周围的介质传散。
传入切屑和介质的切削热越多,对加工越有利。
传入刀具的热量虽不多,但因刀头体积小,所以温度高,高速切削时刀头上的温度最高处可达1000℃以上,刀头温度过高,将加快刀具磨损。
传入工件的热会引起工件的热变形,影响尺寸和形状精度。
特别是加工薄壁零件、细长零件和精密零件时,热变形的影响更大。
影响热传导的主要因素是工件和刀具材料的导热能力以及周圍介质的状况。
一般情况下,切削热大部分由切屑带走和传入工件,以保证刀具的正常切削。
各部分传热的比例取决于具体的切削条件。
例如,不使用切削液,以中等切削速度车削钢料外圆时,切削热的50%~86%由切屑带走,10%~40%传入工件,3%~9%传入车刀,1%左右传入空气。
和上述条件一样,钻削钢料时,散热条件差,切削热的28%左右由切屑带走,约15%传入工件,约52%传入钻头,5%左右传入周围介质。
二、切削温度及影响切削温度的因素(一)工件材料材料的强度、硬度越高,切削时消耗的功率就多,产生的切削热也多,温度就越高。
3.3 切削热与切削温度
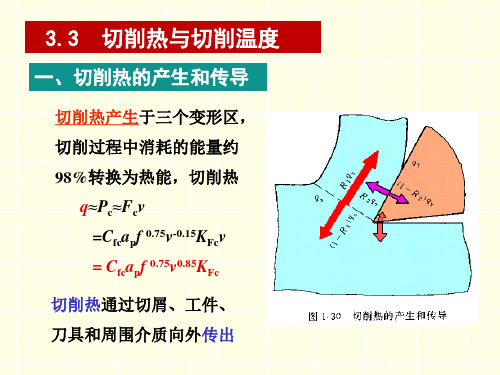
3.3 切削热与切削温度一、切削热的产生和传导切削热产生于三个变形区,切削过程中消耗的能量约98%转换为热能,切削热q≈P c≈F c v=C fc a p f 0.75v-0.15K Fc v=C fc a p f 0.75v0.85K Fc切削热通过切屑、工件、刀具和周围介质向外传出二、切削温度的分布红外胶片法测得切钢料的温度场,分析归纳切削温度分布规律:1.剪切区等温线与滑移线相近OM线温度比OA线上温度高剪切滑移相等的地方温度相等,剪切变形是切削热的第一来源2.前后刀面最高温度点不在刀刃上切屑上最高温度比剪切区温度高切屑底层温度比上层温度高摩擦是切削热的又一来源三、影响切削温度的主要因素切削温度θ 一般指前刀面与切屑接触区内的平均温度两个方面:切削热的产生与传出(一)切削用量的影响由实验得出切削温度经验公式如下θ=C θ v z θf y θa p x θ式中系数及指数见表1-4,由表中数据看出:z θ在0.3~0.5之间,y θ在0.15~0.3,x θ在0.05~0.1切削用量↑时切削温度↑,其中v 对θ影响最大,进给量f 的影响比v 小,背吃刀量a p 的影响很小。
(二)刀具几何参数的影响1. 前角γ的影响γ↑→变形程度↓→F↓q ↓→θ ↓但γ>20°时,因散热面积↓,对θ的影响减小2. 主偏角κr的影响κr ↑,切削宽度aw↓,散热面积↓→θ↑3. 负倒棱和刀尖圆弧半径的影响bγ1 、rε↑,切屑变形程度↑→q ↑同时散热条件改善,两者趋于平衡对θ影响很小(三)工件材料的影响强度硬度、塑性和韧性越大,切削力越大,切削温度升高。
导热率大,散热快,温度下降(四)刀具磨损的影响后刀面磨损增大,切削温度升高; VB达一定值影响加剧; v越高刀磨损对θ影响越显著(五)切削液的影响浇切削液对↓切削温度↓刀具磨损↑加工质量有明显效果。
热导率比热容和流量越大,本身温度越低冷却效果越显著。
第五章切削热和切削温度

工件材料预热至500—800℃经常达到800~900℃,切削力下降却不多。 这也间接证明,切削温度对剪切区域内工 件 材料强度影响不大。
5. 利用切削温度自动控制切削速度或进给量
利用切削温度来控制机床的转速,保持切削温度在最佳 范围内,以提高生产率及工件表面质量。
切削热的传导
切削热传散出去的途径主要是切屑、工件、刀 具和周围介质(如空气、切削液等),影响热传导的 主要因素是工件和刀具材料的导热系数以及周围介质 的状况。
切削热的来源就是切屑变形热 Q 变 和前、后刀面的摩擦热 Q 摩
其产生与传出的关系为:
Q Q 变 Q 摩 Q 屑 Q 刀 Q 工 Q 介
由于后刀面上的摩擦通常远远小于前刀面上 的摩擦,同时进给运动所作的功也远远小于 主运动所作的功。因此,为了简化问题便于 分析,我们忽略后刀面上的摩擦功和进给运 动所作的功,并假定主运动所作的功全部转 化成了热量,则可以得到单位时间内产生的 切削热的公式:
Pm Fzv
式中:Pm——每秒钟产生的切削热,J/s; Fz——切削力,N; v——切削速度,m/s。
第一节、切削热的产生与传导
金属切削过程的三个变形区就是产生切削热的三个热 源(图)。在这三个变形区中,刀具克服金属弹、塑性变形抗 力所作的功和克服摩擦抗力所作的功,绝大部分转化为切削 热。
图5-1 切削热的产生与传导
切削热的来源主要有三个方面, (一)切屑与前刀面之间的摩擦所消耗的摩擦功。 (二)工件与后刀面之间的摩擦所消耗的摩擦功。 (三)切削层金属在刀具的作用下发生弹性变形和塑性变形
高,超过了刀具的热硬性极限温度时,刀具的硬度 就会明显下降,产生剧烈的磨损,从而失去切削能 力,使切削工作无法完成。 • 当切削温度超过一定限度后,刀具材料的硬度会显 著下降,因而失去切削性能,刀具很快磨钝不能使 用。 • 高速钢刀具材料的耐热性为600℃左右,超过该温 度刀具失效。硬质合金刀具材料耐热性好,在高温 800~1000℃时,强度反而更高,韧性更好。因此 适当提高切削温度,可防止硬质合金刀具崩刃,延 长刀具寿命。
第5章 切削热分析
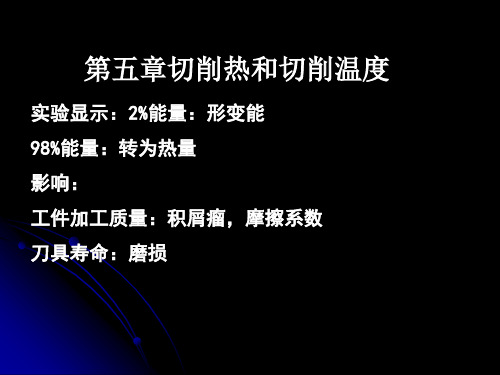
实验显示:2%能量:形变能 98%能量:转为热量 影响: 工件加工质量:积屑瘤,摩擦系数 刀具寿命:磨损
一、切削热的来源与传散
来源: 1.在刀具的切削作用下,切削层金属发生弹性变形和塑性变形。 2.切屑与前刀面,工件与后刀面间消耗的磨擦功,也将转换为热能。
切屑 刀具
工件
切削热的产生和传出
4、工件材料对切削温度的影响
(1)工件材料的硬度和强度越高,切削时所消耗的功就越多产生的切削热也多。 (2)合金结构钢的强度普遍高于45钢,而导热系数有一般均低于45钢.所以切削合金 结构时的切削温度一般均高于切削45钢时的切削温度。 (3)不锈钢1cr18Ni9Ti和高温合金GH131不但导热系数低,而且在高温下仍能保持较 高的强度和硬度,所以切削这种类型的材料时,切削温度比切削其他材料要高得多。
切削温度测定原理与切削温度分布
自然热电偶法采用自然热电偶法的测温装置是利用刀具和工件分别 作为自然热电偶的两极,组成闭合电路测量切削温度。刀具引出端 用导线接入毫伏计的一极,工件引出端的导线通过起电刷作用的铜 顶尖接入毫伏计的另一极。。
切削温度与热电势毫伏值之间的对应关系 可通过切削温度标定得到。根据切削实验 中测出的热电势毫伏值,可在标定曲线上 查出对应的温度值。
3.在剪切区域中,垂直剪切面方向上的温度梯度很大。
切削过程中消耗的功率98~99%转换为热 能,因此近似认为单位时间内产生的切 削热q等于切削功率Pc
q Pc Fcvc
q
CF c
ap
f
v K 0.75 0.85
c
Fc
结论:影响力从大到小依次是ap,v,f
传散: 切削热由切屑.刀具.工件和周围介质传出的比率大致如下:
2.3切削热与切削温度
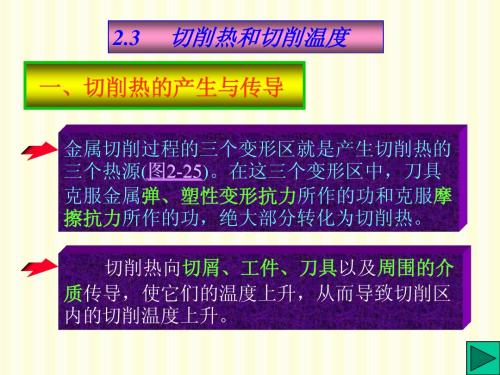
在金属切削过程中, 在金属切削过程中,正确的使用切削 液可以减少摩擦; 液可以减少摩擦;降低切削温度和切削 力;减少切屑与道具的粘结抑制积屑瘤 和鳞刺得生长;提高零件的便面质量; 和鳞刺得生长;提高零件的便面质量; 保证加工精度和提高生产效率。 保证加工精度和提高生产效率。
切削液的作用 (1)冷却作用 ) (2)润滑作用 )
(5)切削液 )
利用切削液的润滑功能 降低摩擦系数,减少切削热 的产生,也可利用它的冷却 功用吸收大量的切削热,所 以采用切削液是降低切削温 度的重要措施。
刀具主后面磨损 时,后角减小,后面 与工件间摩擦加剧。 刃口磨损时,切屑形 成过程的塑性变形加 剧,使切削温度增大。
图
前角与切削温度的关系
六、切削液
切削液的选用
•按工件材料选用 加工钢等塑性材料时,需要切削液;加工 按工件材料选用 铸铁等脆性材料时,不用切削液。 •按刀具材料选用 高速钢刀具耐热性差,粗加工时应选用以 按刀具材料选用 冷却作用为主的切削液,以降低切削温度;在精加工时应使 用润滑性能好的极压切削油或高浓度的极压乳化液,以提高 加工表面质量。硬质合金刀具由于耐热性好,一般不用切削 液; •按加工方法选用 对半封闭、封闭加工,选用极压乳化液或 按加工方法选用 极压切削油,以对切削区进行冷却、润滑和对切屑冲洗。磨 削加工时,由于磨削区温度很高,磨屑会破坏已磨削表面质 量,要求切削液具有良好的冷却、清洗、排屑和防锈性能,一 般选用乳化液。
切削液的添加剂
为改善切削液 性能所加入的化学 物质,称为添加剂。 物质,称为添加剂。 用以改善在较低温度 下切削液的极压添加剂 极压添加剂
比油性添加剂 能耐较高的温度。 能耐较高的温度。
3.表面活性剂 表面活性剂
切削热及切削温度
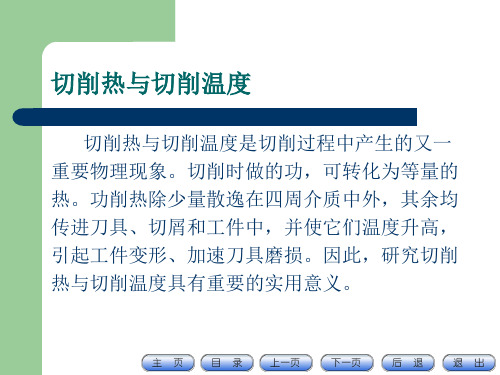
2、切削温度影响因素
(1)切削用量
的影响:通常在 车床上利用测温 装置求出切削用 量对切削温度的 影响关系,并可 整理成下列一般 公式:
2、切削温度影响因素
由上可知:切削速度对切削温度影响最大,随切 削速度的进步,切削温度迅速上升。进给量对切 削温度影响次之,而背吃刀量ap变化时,散热面 积和产生的热量亦作相应变化,故ap对切削温度 的影响很小。
切削热与切削温度
切削热与切削温度是切削过程中产生的又一 重要物理现象。切削时做的功,可转化为等量的 热。功削热除少量散逸在四周介质中外,其余均 传进刀具、切屑和工件中,并使它们温度升高, 引起工件变形、加速刀具磨损。因此,研究切削 热与切削温度具有重要的实用意义。
一、切削热的产生和传导
1、切削热的产生 切削热是由切削功转变而来的。如
力是影响切削温度的重要因素,而工件材料的强度(包括硬度)直接决定了单位切 削力,所以工件材料强度(包括硬度)增大时,产生的切削热增多,切削温度升高。 工件材料的导热系数则直接影响切削热的导出。 4、刀具磨损的影响
在后刀面的磨损值达到一定数值后,对切削温度的影响增大;切削速度愈高,影 响就愈明显。合金钢的强度大,导热系数小,所以切削合金钢时刀具磨损对切削温 度的影响,就比切碳素钢时大。 5、切削液的影响
2、切削热的传导
Q传出=Q切屑+Q工件+Q刀具+Q介质 切削热产生以后,由切屑、工件、刀具及周期介质(如空气)传出。
各部分传出的比例取决于工件材料、切削速度、刀具材料及几何角度 等。车削时的切削热主要是由切屑传出的。用高速钢切削钢材时,约 有50%~80%的切削热由切屑带走,10%~40%的热传入工件, 3%~9%的热传给刀具,传给介质的热仅有1%左右。传入刀具的热最 虽不是很多,但由于刀具切削部分体积很小,因此,引起刀具温度升 高较快(高速切削时,刀头温度可达1000℃以上),从而加速刀具的磨 损。 传入工件的热量可使工件的温度升高,引起工件材料膨胀变 形,从而产生形状和尺寸误差,降低加工精度。传入切屑和介质的热 量越多,对加工越有利,因此,在切削加工中应设法减小切削热,改 善散热条件,以减小高温对刀具和工件的不良影响。
切削热与切削温度
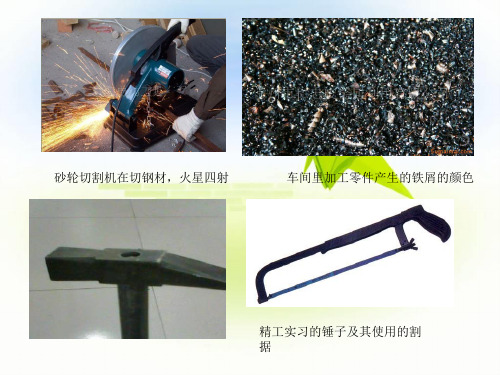
⑶周围介质 采用冷却性能好的切削液及采 用高效冷却方式能传导出较多的切削热, 切削区温度就较低。采用喷雾冷却法使切 削液雾化后汽化,将能吸收更多的切削热, 使切削温度降低。 ⑷切屑与刀具的接触时间 外圆车削时,切 屑形成后迅速脱离车刀而落入机床的容屑 盘中,切屑传给刀具的热量相对较少;钻 削或其它半封闭式容屑的加工,切屑形成 后仍与刀具相接触,传导给刀具的热相对 较多。
砂轮切割机在切钢材,火星四射
车间里加工零件产生的铁屑的颜色
精工实习的锤子及其使用的割 据
切削热与切削温度
1:什么是切削热与切削温度 2:切削热的产生和传出 3:切削温度的测量和分布 4:影响切热:在切削加工过程中,由于被切削材 料层的变形、分离及刀具和被切削材料间 的摩擦而产生的热量。 切削温度:切削过程中切削区域的温度(一 般指前刀面与切屑接触区域的平均温度)。 尽管切削热是切削温度上升的根源,但直 接影响切削过程的却是切削温度。
2:切削用量 (1).切削速度 提高切削速度,切削温度将显著上升。
• 原因一:切削速度提高,单位时间 的金属切除率成正比增多,消耗的 功增大,切削热也会增大,由切屑,
工件与刀具间发生强烈摩擦而产生大量切削热;
故使切削温度上升。 • 原因二:由于切削速度很高,在很短的时间内切屑底层的热来不及向 切屑内部传导,而大量积聚在切屑底层,使切削温度显著升高。 • 注意:随着切削速度的提高到一定程度,切屑流加快,切削产生的热 量来不及传到刀具和工件上就被切屑带走,另外,随着切削速度提高, 切屑变形程度也相应减小,因此切削温度不会随切削速度成倍增长, 从实验结果来看,切削温度大约增加20%—30%
切削热的计算
如果忽略进给运动所消耗的功,并假定主运动所消耗的功全 部转化为热能,则单位时间内产生的切削热能,则单位时 间内产生的切削热可由下式计算
切削温度及其测量方法
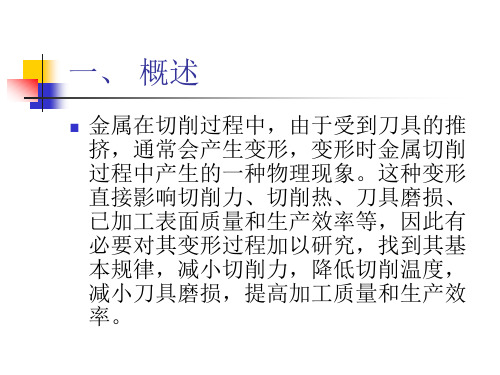
三、 切屑变形
研究切削过程的目的在于找出切屑的变 形规律,要说明这些规律,就必须给些 切屑变形程度的表示方法。
切削层金属变形主要是剪切滑移变形, 应此我们用相对滑移来表示切削层变形 程度。
1、 相对滑移
由材料力学知,剪切变形可用相对滑移 来表示。假定平行四边形OHNM受到剪切 变形后成为OGPM,其相对滑移ε可写成 ε =△S/ △y
二、 第一变形区的变形
正如图3.4所示,图中OA、OB、OM均为等应力线, OA线上的应力达最דmax。
当切削层金属的某点P向切削刃逼近到达点1位置时, 由于OA线上的剪切应力ד
已达到材料屈服强度דs,故 点1流动到点2,2’2则为滑移 量。由于塑性变形过程中材料 的强化,不同等应力线上的应 力将依次逐渐增大。OM线上 的应力已达到最大值דmax。
在DA、CB线的两侧还会产生一系列滑移线,但都分别交于D、C处。
图3.2(b)所示情况与 图3.2 (a)的区别仅在于: 切削时,工件上DB线以下还 有基体材料的阻碍,故DB线 以下的材料将不发生剪切滑 移变形即剪切滑移只在DB线 以上沿DA方向进行,DA就 是切削过程的剪切滑移。
当然,由于刀具有前角 及工件间有摩擦作用,剪切 滑移变形会比较复杂罢了。
KC =
Fc AD
N
mm2
式中AD ----切削面积(mm2)
切削力的经验公式
用测力仪测出切削力,再将实验数据加以适当处理,
可以得到切削力的经验公式。切削力的经验公式通常是
以切削深度ap和进给量f为变量的幂函数,其形式如下:
Fc
9.81CFc ap xFc
f
v K yFc nFc
பைடு நூலகம்
- 1、下载文档前请自行甄别文档内容的完整性,平台不提供额外的编辑、内容补充、找答案等附加服务。
- 2、"仅部分预览"的文档,不可在线预览部分如存在完整性等问题,可反馈申请退款(可完整预览的文档不适用该条件!)。
- 3、如文档侵犯您的权益,请联系客服反馈,我们会尽快为您处理(人工客服工作时间:9:00-18:30)。
切削热的产生与切削温度的测量
切削热和由此产生的切削温度是金属切削过程中的一个重要物理现象。
大量的切削热使切削区域的温度升高,直接影响刀具的磨损和寿命,并影响工件的加工精度和表面质量。
切削温度也可作为自动化生产中监控因素,所以研究切削热和切削温度变化规律对生产时间有重要的意义。
(一)切削热的产生和传出被切金属层在刀具的作用下发生弹性变形和塑性变形,这是切削热的一个来源。
同时,切屑与前刀面、工件与后刀面间消耗的摩擦功也将转化为热能,这是切削热的又一个来源
(见图1)。
如果忽略后刀面上的摩擦功和进给运动所消耗的功,并假定主运动所消耗的功全部转化为热能,则单位时间内产生的切削热可算出:
Qc=Fzvc
式中Qc--每秒钟内产生的切削热,单位为J/s ;
Fz--主切削力,单位为N;
vc--切削速度,单位为m/s。
图1 切削热的产生和传出
(二)切削温度及其测量方法
切削温度一般是指刀具与工件接触区域的平均温度。
切削温度测量的方法很多,如图2所示。
目前比较常用的测量切削温度的方法是热电偶法和光热辐射法。
下面将分别进行阐述。
t 红外线F 板彳成胶片[法
r 热敏顔料法
热緻电饱达 域热计法
I 金属纽飙观察法
图2 切削温度的测量方法
1. 热电偶法
热电偶法又分为自然热电偶法和人工热电偶法(见表
1)。
表1
自然热电偶与人工热电偶比较
切別臥度测宦法
「单牟刀法
r fl 然热电偶法
「热电侧法*
I 人工热砸偶法
'插入匸件法
『福射热计法
PhS 电池法
锯光电二极仰法
图3 自然热电偶法测温示意图
1.铜顶尖2•铜销3.车床主轴尾部4.工件5.刀具
图4 人工热电偶法测温示意图
a)测前刀面温度b)测工件温度
要想知道前刀面上的温度,还需应用传热学的原理和公式进行推算。
应用人工热电偶法测温,并辅以传热学计算所得到的刀具、切屑和工件的切削温度分布情况(见图5)。
图5 切削温度的分布
a )刀具、工件和切屑中温度分布
b )刀具前刀面上温度分布 加工条件:刀具 YT20 vc=600m/min 加工条件:工件 30Mn4 ap=3mm f=0.25mm/r
由图5可以看出切削温度的分布规律:
(1) 前刀面上温度最高处并不在切削刃口处,而在离刃口有一定距离的位置,工件材料 塑性越大,距离刃口越远,反之越近。
这是因为热量沿前刀面有个积累过程,这也是刀具磨 损严重之处;
(2) 切屑底层的温度梯度最大,说明摩擦热集中在切屑底层与前刀面接触处。
2. 光热辐射法
除了热电偶测温法,采用观察刀具或零件切削前后金相组织变化的方法也能判定切削温 度,但这两种方法并不直观,而且观察和分析的工作量较大。
近来也更多的是使用红外线测 温仪或光能电池测量切削温度。
热像仪就是利用红外线原理来测量切削温度的,它是通过非 接触探测红外热量,并将其转换生成热图像和温度值,进而显示在显示器上,并可以对温度 值进行计算的一种检测设备。
如图6是用热像仪测温的现场演示图。
图1-30是利用热像仪的 配套软件采集到的切削温度场图,软件可以将切削过程以红外影像采集下来,在确定准确的 发射率情况下,设定播放速度,调节播放位置,对采集切削过程的温度分布进行测量和绘制。
b)
a)
至切削刃81^7mm
图7 测得温度场图
3. 切屑颜色与切削温度的关系
在生产实践中,可以通过切削加工时切屑的颜色来判断刀尖部位的大致温度。
以车削碳 素结构钢为例,随着切削温度的提高,切屑颜色变化过程顺序为:银白色一黄白色一金黄色 -紫色一浅蓝色-深蓝色。
其中,银白色切屑反映的切削温度约为 200 r 左右,金黄色切屑 反映的切削温度约400C 左右,深蓝色切屑反映的切削温度约 600C 左右。
(三)影响切削温度的主要因素 1. 工件材料
工件材料的强度、硬度越高,切削时消耗的功就越多,产生的切削热越多,切削温度就 越高。
工件材料的热导率越大,通过切屑和工件传出的热量越多,切削温度下降越快。
2. 刀具几何参数
BWM»[ « uf
( --- ) ----------- )— r^iA
图6 用热像仪现场测温
lr Mi ff
A^WI I M
十
1
前角增大,切削变形减小,产生的热量少,切削温度降低;但过大的前角会减少散热体 积,当前角大于20° ~25°时,前角对切削温度的影响减少。
主偏角减小,使切削宽度增大, 散热面积增加,切削温度下降,如图 8、图9所示。
8 前角对切削温度的影响
图9 主偏角对切屑温度的影响
3. 切削用量
对切削温度影响最大的切削用量是切削速度,其次是进给量,而背吃刀量的影响最小,
这是因为当切削速度vc 增加时,单位时间内参与变形的金属量增加而使消耗的功率增大, 切 削温度升高;当f 增加时,切屑变厚,由切屑带走的热量增多,故切削温度上升不甚明显; 当ap 增加时,产生的热量和散热面积同时增大,故对切削温度的影响也小,如图 10
所示。
600
50()
400
3
°°20a 3Cf
45° MT 75*
主偏角妣
1
图10 切削用量对切削温度的影响
a )切削速度的影响
b )进给量的影响
c )背吃刀量的影响
4. 其他因素
刀具后刀面磨损量增大时,加剧了刀具与工件间的摩擦,使切削温度升高,切削速度越 高,刀具磨损对切削温度的影响就越显著(见图 11)。
浇注切削液对降低切削温度、减少刀 具磨损和提高已加工表面质量有明显的效果。
切削液的润滑作用可以减少摩擦,减小切削热 的产生。
图11
不同切削速度下后刀面磨损与切削温度的关系
a)
[2W ~
1000 -咖
70fl
二 □
=
4-
1
1 ■
4 '
5召
20 W 40
60 韻 100 150 300
^?1fn in in)
r
二二
b)。